胀接工艺规程
胀接工艺
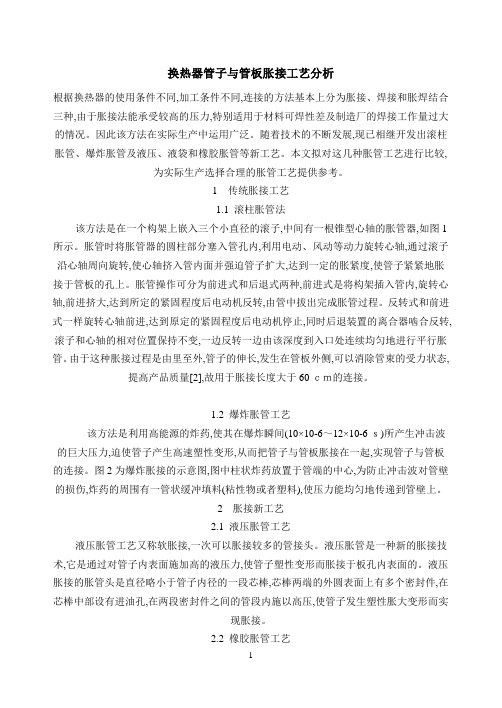
换热器管子与管板胀接工艺分析根据换热器的使用条件不同,加工条件不同,连接的方法基本上分为胀接、焊接和胀焊结合三种,由于胀接法能承受较高的压力,特别适用于材料可焊性差及制造厂的焊接工作量过大的情况。
因此该方法在实际生产中运用广泛。
随着技术的不断发展,现已相继开发出滚柱胀管、爆炸胀管及液压、液袋和橡胶胀管等新工艺。
本文拟对这几种胀管工艺进行比较,为实际生产选择合理的胀管工艺提供参考。
1传统胀接工艺1.1 滚柱胀管法该方法是在一个构架上嵌入三个小直径的滚子,中间有一根锥型心轴的胀管器,如图1所示。
胀管时将胀管器的圆柱部分塞入管孔内,利用电动、风动等动力旋转心轴,通过滚子沿心轴周向旋转,使心轴挤入管内面并强迫管子扩大,达到一定的胀紧度,使管子紧紧地胀接于管板的孔上。
胀管操作可分为前进式和后退式两种,前进式是将构架插入管内,旋转心轴,前进挤大,达到所定的紧固程度后电动机反转,由管中拔出完成胀管过程。
反转式和前进式一样旋转心轴前进,达到原定的紧固程度后电动机停止,同时后退装置的离合器啮合反转,滚子和心轴的相对位置保持不变,一边反转一边由该深度到入口处连续均匀地进行平行胀管。
由于这种胀接过程是由里至外,管子的伸长,发生在管板外侧,可以消除管束的受力状态,提高产品质量[2],故用于胀接长度大于60cm的连接。
1.2 爆炸胀管工艺该方法是利用高能源的炸药,使其在爆炸瞬间(10×10-6~12×10-6s)所产生冲击波的巨大压力,迫使管子产生高速塑性变形,从而把管子与管板胀接在一起,实现管子与管板的连接。
图2为爆炸胀接的示意图,图中柱状炸药放置于管端的中心,为防止冲击波对管壁的损伤,炸药的周围有一管状缓冲填料(粘性物或者塑料),使压力能均匀地传递到管壁上。
2胀接新工艺2.1 液压胀管工艺液压胀管工艺又称软胀接,一次可以胀接较多的管接头。
液压胀管是一种新的胀接技术,它是通过对管子内表面施加高的液压力,使管子塑性变形而胀接于板孔内表面的。
胀接工艺规程

胀接工艺规程1.主题内容与适用范围本规程规定了管板胀接的有关技术内容,适用于管板的胀接。
1.1胀接操作人员2.1胀接操作人员必须经过有关部门技术培训,考试合格后方能上岗操作。
2.2胀接操作人员应掌握设备的使用性能,熟悉产品图样,工艺文件及标准要求。
2.3胀接操作人员应认真作好胀接场地的管理工作,对所用工、量检具应能正确使用,妥当保管。
3.胀接管孔的技术要求3.1用气油等熔清洗胀接管孔壁上的油污,再用细砂布沿孔壁园周方向打磨残留锈蚀,并去除管孔边缘毛刺,打磨后,管孔壁的表面粗糙度不得大于12.5米。
3.2清理后的管孔壁不得有纵向刻痕,个别管孔允许有一条螺旋形或环向刻痕,刻痕深度不得超过0.5mm。
宽度不得超过1mm,刻痕至管孔边缘的距离不得少于4mm。
3.3胀接管孔尺寸及公差应符合表2规定。
表2 单位mm管子公称外径7 9.52 12.7 15.88 19 25 32 管孔直径7.1 9.75 12.85 16.1 19.2 25.2 32.2管孔允许偏差+0.03-0.02+0.054.胀接器及胀接设备检查4.1胀杆及滚柱材料应符合GB1298-2008<碳素工具钢技术条件>的规定。
4. 2胀接器的胀杆及滚柱的工作表面粗糙度不大于12.5微米,胀杆的锥度应在1:20-1:40之间,滚柱的锥度应在1:4-1:80之间。
4.3胀管器的滚柱工作表面硬度不低于HRC52,胀杆工作表面硬度应比滚柱工作表面硬度高HRC6-10。
4.4胀管器的胀杆全长直线度不大于0.1mm。
4.5胀管器壳体上的滚柱巢孔中心线应与壳体轴心斜线,其夹角a。
4.6胀管器的滚柱数量不宜少于4个。
4.7胀管器转速一般不得超过60r/min。
4.8胀杆和滚柱工作表面应无刻痕、压坑、碰伤等缺陷。
4.9胀杆和滚柱的配合程度应良好,滚柱与检查环规间的最大间隙a不大于0.2mm(图3)4.10胀管器检查合格后,涂以润滑脂待用。
5.穿管5.1管子的两个胀接端穿入管孔时能自由伸入,管子必须装正,不得歪斜。
换热器通用胀接工艺

胀管通用工艺规程一、胀接说明1 胀接胀接是换热管与管板的主要联接形式之一,它是利用胀管器伸入换热管管头内,挤压管子端部,使管端直径扩大产生塑性变形,同时保持管板处在弹性变形范围内。
当取出胀管器后,管板孔弹性变形,管板对管子产生一定的挤紧压力,使管子与管板孔周边紧紧地贴合在一起,达到密封和固定连接的目的。
由于管板与管子的胀接消除了弹性板与塑性管头之间的间隙,可有效地防止壳程介质的进入而造成的缝隙腐蚀。
当使用温度高于300℃时,材料的蠕变会使挤压残余应力逐渐消失,连接的可靠性难以保证。
因此,在这种工况下,或预计拉脱力较大时,可采用管板孔开槽的强度胀接。
胀接又分为贴胀和强度胀。
2 胀管率胀管率是换热管胀接后,管子直径扩大比率。
贴胀与强度胀的主要区别在于对管子胀管率 (管子直径扩大比率) 的控制不同,对冷换设备换热管来说,强度胀要求的胀管率H为1~2.1%,而贴胀要求的胀管率H为0.3~0.7%。
3 贴胀贴胀是轻度胀接的俗称,贴胀是为消除换热管与管板孔之间的缝隙,以防止壳程介质进入缝隙而造成的间隙腐蚀。
由于贴胀时胀管器给管子的胀紧力较小,管子径向变形量也就比较小。
因此换热管与管板孔之间的相对运动的摩擦力就比较小,所以它不能承受较大的拉脱力,且不能保证连接的可靠性,仅起密封作用。
贴胀时,管孔不需要开槽。
4 强度胀强度胀是指管板与换热管连接处的密封性和抗拉脱强度均由胀接接头来保证的连接方式。
强度胀接的管板孔要求开胀管槽,一般开两道胀管槽。
以使管子材料在胀接时嵌入胀管槽内,由此来增加其拉脱力。
特别是当使用温度高于300℃时,材料的蠕变会使挤压残余应力逐渐消失,连接的可靠性下降,甚至发生管子与管板松脱,这时采用强度胀接,其抗拉脱力就比贴胀要大得多。
胀管前应用砂轮磨掉表面污物和锈皮,直至呈现金属光泽,清理锈蚀长度应不小于管板厚度的2倍。
管板硬度应比管子硬度高HB20~30,以免胀接时管板孔产生塑性变形,影响胀接的紧密性。
胀接工艺守则

胀接工艺守则1总则管板和换热管是换热器的主要受压元件,二者之间的连接处是换热器的关键部位。
而胀接是实现换热管与管板连接的方法之一,胀接质量的好坏对换热器的正常运作起着关键作用。
2胀接型式和方法胀接型式按胀接进度可分为贴胀和强度胀2.1贴胀是为消除换热管与管板直径缝隙的轻度胀接,其目的是为了小处缝隙腐蚀和提高焊缝的抗疲劳性能,贴胀后胀接接头的抗拉脱力应达到IMPa 以上;2.2强度胀是包装换热管与管板连接的密封性能及抗拉脱轻度的胀接。
强度胀接后胀接接头的抗拉脱力应达到4MPa以上;2.3胀接方法按胀接工艺的不同可分为机械胀和柔性胀接(橡胶胀、液压胀、液袋式液胀等)。
3胀管器的选用胀管器主要根据换热管的直径、管板厚度、胀接长度及胀接特点来确定,通常有胀接器生产厂家按胀接条件选定。
4换热管与管板硬度测定4.1胀接的远离是胀接时硬度较低的管子产生塑性变形,而硬度较高的管板产生弹性形变,胀接后塑性变形管子收到弹性变形额管板孔壁的挤压而使管子和管板紧密地结合在一起,因此在试胀前应首先测定管子与管板的硬度值是否相匹配;4.2换热管与管板的材料应有适当的硬度差,管板硬度应大于换热管的硬度,其差值最好达到HB30以上,否则胀接后管子的回弹量接近或大于管板的回弹量而造成胀接接头不紧,如果二者硬度差相差很小时,应对管子端部进行退火处理,管子端部退火处理长度一般为管板厚度加IOOmmO5试胀5.1正式胀接之前应进行试胀。
试胀的目的是验证胀管器质量的好坏,验证预定的管子与管板孔的结构是否合理,检验胀接部位的外观质量及接头的密封性能,测试胀接接头的抗拉脱力,孕照合适的胀管率,以便制定合理的产品胀接工艺;5.2试胀应在试胀工艺试板上进行,试板应与产品管板的材料、厚度、管孔大小一致,试板上孔的数量应不少于5个,其管孔的排列形式应与产品管孔排列形式一致,试胀所用管子的材料、规格应与产品用换热器一致,但长度可以不一致,一般为管板厚度加50mm;5.3试胀前应根据胀管率计算公式推送出换热管胀接后的内件尺寸,胀管率计算公式可按我国锅炉规程中给出的公式计算:H=(dι-d2-δ)∕d3×100%δ一一胀前管孔直径与管子外径之差5.4胀管率应在0.9%~2.2%之间选取,胀管率小于0.9%为欠胀,管子胀后为产生足够的塑性变形,不能保证资金质量;胀管率大于2.2%为过胀,管子胀后产生过大的塑性变形,加工硬化现象严重,容易导致管子处理裂纹等缺陷,管板也可能产生塑性变形而使胀后的管板不能有效的回弹,从而影响胀接接头的性能。
胀接通用工艺

胀接通用工艺1. 总则:本通用工艺适用于管壳式换热器管板与管子的胀接。
2 胀管前准备2.1 管端及管板必须清理干净,不得有油渍污物、毛刺、铁屑、锈蚀等杂物;管孔表面不得有影响紧密性的缺陷,如贯通的纵向或螺旋状刻痕等。
2.2 测量管板厚度,检查所领的胀管器是否符合要求。
2.3 准备润滑油及冷却用油。
3 胀管长度3.1 胀接连接时,其胀接长度不得伸出管板背面(壳程侧),换热管的胀接部分与非胀接部分应圆滑过渡,不得有急剧的棱角。
4 胀管率ρ对于钢管和钢管板,ρ=12~18%为强度胀接;ρ=7~10%为紧密胀接;ρ=3~7%为贴合胀接,不能保证联接强度和严密度。
过大的ρ会使管壁加工硬化严重,甚至发生裂纹,胀接强度也会降低。
如果管子直径较大,管子的金属材料较软,且管板的金属材料较硬时,则选取较大的胀管率。
其值可按下式计算:ρ=(d K-d N-e)/Do×100%式中:d K——管子胀接后的内径d N——管子胀接前的内径e—胀接前管子与管板的间隙(即管子胀前外径)Do—胀接前管板孔径5 胀接过程5.1 为减少管板胀后变形,推荐按梅花状的顺序定位胀。
5.2 对大直径,(D N>1000)特别是薄管板,为避免胀后变形,在定位胀前,将两管板保持与管子垂直,测量四点,其中两管板间距之差不得超过:D N<1000时2mm;D N≥1000时3mm。
两管板按上述要求调好后,靠近中心处临时用拉杆若干根将两管板拉紧,再按上述步骤胀接。
5.3 胀接过程中允许施用润滑油,但一定要防止润滑油带入管板孔内。
5.4 胀管时,一旦过胀,发现管子胀裂,需更换管子,管子抽出后,修磨管板孔。
管孔最大直径应不大于Do+1㎜。
5.5 管子全部胀完后,应逐根检查管口是否有漏胀。
如果管头超差应用钻头锪到允许范围,见下表6 胀管质量要求:6.1 胀口内壁光滑平整,无凹陷擦伤、重皮、起毛。
6.2 胀口扩大部分的过渡区应无明显棱角,不准出现裂纹。
锅炉安装胀接工艺

胀接工艺1 胀接前的准备工作1.1 炉管退火(详见4 炉管退火工艺)。
1.2 管端、管孔的清理及管端打磨1.3 管端的清理及打磨a、管端的胀接表面存在的锈蚀点、氧化皮、纵向沟纹及退火进沾上的铅点等缺陷,在胀接前进行清理打磨。
b、管端的打磨常用机械打磨和手工打磨,机械打磨采用角式砂轮机对管端进行打磨处理,手工打磨用锉刀将管端打磨光滑,消除缺陷后,再用砂布沿圆弧方向精磨。
c、胀管前,管子胀接端应磨锉至出现金属光泽,磨削量要控制好,打磨后管壁厚度不得小于公称壁厚的90%,管端打磨长度至少为管孔壁厚加50mm,且不应有起皮、凹痕、裂纹和纵向刻痕等缺陷。
d、磨锉合格后的管端,在装管前应用外径千分尺测量胀接段外径,应测量几处,取其平均值,并作好记录。
磨锉后管口应包扎好,若因某种原因不能立即胀管,应妥善保护,防止管端生锈。
e、距管口100mm内管端内壁必须用钢丝刷和刮刀将锈层及退火时沾的铅点清理掉,以免在胀管时,造成测量误差,影响胀管率的计算准确性。
锈层、铅点对胀管器的磨损比较严重。
1.4 管孔的清理、检查及修整a、安装前,对汽包管孔必须逐个进行清理和测量,并做好记录。
b、除油、除锈。
用棉纱将防锈油及管孔上的污垢去掉,再用细砂纸沿圆周方向将锈层磨净,使管孔露出金属光泽。
c、测量管孔(1)管孔直径、椭圆度及不柱度。
采用内径千分尺或精度为0.02mm的游标卡尺,沿汽包外壁方向测量管孔的直径及椭圆度。
(2)测量方法是管孔直径的十字线方向,互成90°分别测出直径的两个数值。
(3)应逐个测量管孔,并按排号、管孔号记录在展开图上。
测得的两个方向上的直径差值即为椭圆度。
(4)应测量管孔的不柱度。
用上述量具在汽包内壁方向测出管孔直径,再与沿外壁方向测得数值相比较,其锥度大小可由沿外壁测得的直径与沿内壁方向测得的直径之差除以壁厚计算出来。
(5)记录时,汽包上的管孔编号应与展开图上的编号一致。
d、管孔检查中应注意事项:(1)管孔环形或螺旋形沟纹深度不应大于0.5mm,宽度不得大于1mm,沟纹至管孔边缘距离不应小于4mm。
锅炉安装胀接工艺
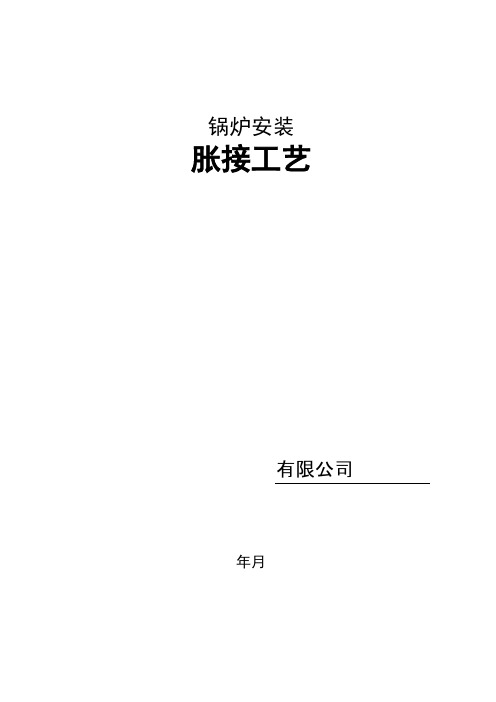
锅炉安装胀接工艺有限公司年月锅炉安装胀接工艺1总则1.1是为了保证锅炉胀管的施工方法与要求的统一,以确保锅炉安装质量,特制定本工艺。
1.2对于工作压力W2.5MPa的锅炉胀管施工应采用外径控制法胀管工艺;对于热水锅炉及工作压力〉2.5MPa的锅炉胀管施工应采用内径控制法胀管工艺。
1.3对腐蚀、尺寸超差、设备本身先天性不足,不能达到本工艺要求的部分,应提出措施,并取得锅炉安全监察部门同意后施工。
1.4胀管工作中应注意安全施工,并应特别注意照明(行灯采用安全电压)及通风等方面的安全技术工作。
1.5引进的高参数胀接式锅炉胀管施工时,可结合制造厂安装指导书参照本工艺执行。
2编写依据2.1《蒸汽锅炉安全技术监察规程》(劳部发[1996]276号)2.2《热水锅炉安全技术监察规程》(1997)2.3GB50273-1998《工业锅炉安装工程施工及验收规范》2.4GB50235-1997《工业管道工程施工及验收规范》2.5GB50236-1998《现场设备、工业管道焊接施工及验收规范》2.6GB50184-1993《工业金属管道工程质量验收评定标准》2.7JB/T9618-1999《工业锅炉胀接技术条件》3胀管专用工具的要求与检查3.1胀管器3.1.1多年来国内各锅炉厂在供应锅炉时大都随带胀管器,各厂的胀管器大同小异,基本都属自进式串联翻边胀管器。
这种胀管器在使用时缺陷较多,使翻边深度很难控制,造成胀口的翻边深度不是太深,就是太浅。
如图1所示,并有翻边后管孔与管子有硬翻边间隙。
如图2所示,是造成漏口较多、补胀率高的主要原因之一。
3.1.2采用带有止推环的翻边胀管器时,工作前可根据对流管的直径选择胀管器,并根据汽包直径调整好止推环高度。
当翻边深度达到规范要求时,止推环就顶在汽包内壁上,这时胀管器只能做旋转扩张,不能直线前进,每一个胀口的翻边深度与角度都能达到规范要求,确保了翻边质量,克服了串联式胀管器易发生翻边根部压不实的弊病。
换热器通用胀接工艺 精品
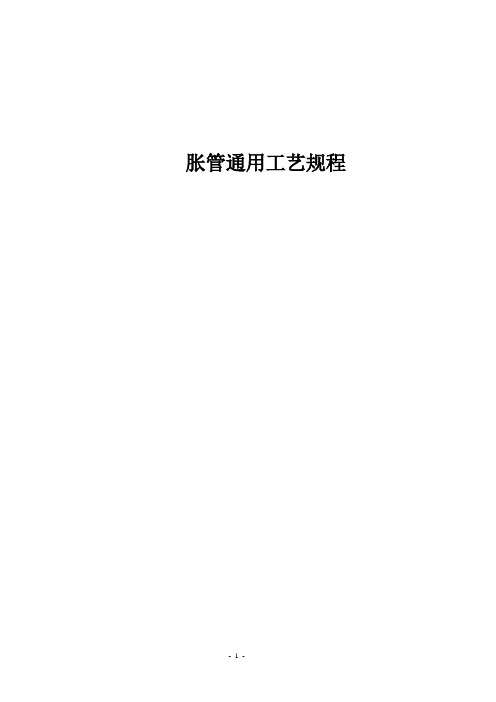
胀管通用工艺规程一、胀接说明1 胀接胀接是换热管与管板的主要联接形式之一,它是利用胀管器伸入换热管管头内,挤压管子端部,使管端直径扩大产生塑性变形,同时保持管板处在弹性变形范围内。
当取出胀管器后,管板孔弹性变形,管板对管子产生一定的挤紧压力,使管子与管板孔周边紧紧地贴合在一起,达到密封和固定连接的目的。
由于管板与管子的胀接消除了弹性板与塑性管头之间的间隙,可有效地防止壳程介质的进入而造成的缝隙腐蚀。
当使用温度高于300℃时,材料的蠕变会使挤压残余应力逐渐消失,连接的可靠性难以保证。
因此,在这种工况下,或预计拉脱力较大时,可采用管板孔开槽的强度胀接。
胀接又分为贴胀和强度胀。
2 胀管率胀管率是换热管胀接后,管子直径扩大比率。
贴胀与强度胀的主要区别在于对管子胀管率 (管子直径扩大比率) 的控制不同,对冷换设备换热管来说,强度胀要求的胀管率H为1~2.1%,而贴胀要求的胀管率H为0.3~0.7%。
3 贴胀贴胀是轻度胀接的俗称,贴胀是为消除换热管与管板孔之间的缝隙,以防止壳程介质进入缝隙而造成的间隙腐蚀。
由于贴胀时胀管器给管子的胀紧力较小,管子径向变形量也就比较小。
因此换热管与管板孔之间的相对运动的摩擦力就比较小,所以它不能承受较大的拉脱力,且不能保证连接的可靠性,仅起密封作用。
贴胀时,管孔不需要开槽。
4 强度胀强度胀是指管板与换热管连接处的密封性和抗拉脱强度均由胀接接头来保证的连接方式。
强度胀接的管板孔要求开胀管槽,一般开两道胀管槽。
以使管子材料在胀接时嵌入胀管槽内,由此来增加其拉脱力。
特别是当使用温度高于300℃时,材料的蠕变会使挤压残余应力逐渐消失,连接的可靠性下降,甚至发生管子与管板松脱,这时采用强度胀接,其抗拉脱力就比贴胀要大得多。
胀管前应用砂轮磨掉表面污物和锈皮,直至呈现金属光泽,清理锈蚀长度应不小于管板厚度的2倍。
管板硬度应比管子硬度高HB20~30,以免胀接时管板孔产生塑性变形,影响胀接的紧密性。
胀管工艺规程
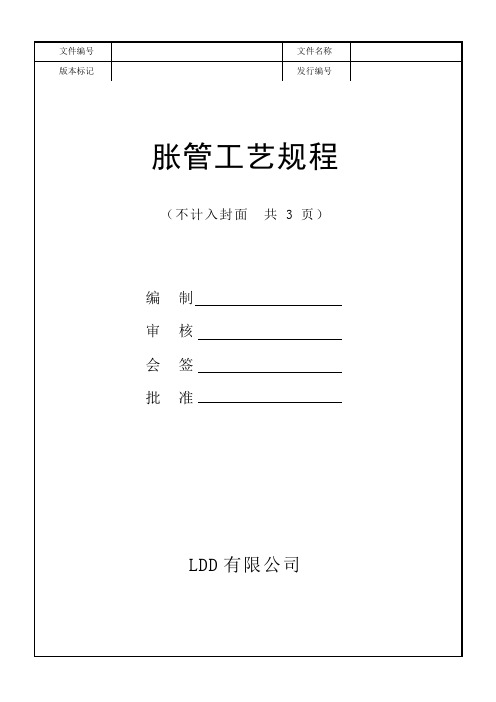
(不计入封面 共3页)
编制
审核
会签
批准
LDD有限公司
一、胀接管子的技术要求
1、胀接管子外表面不得有重皮、压扁、裂纹等表面缺陷,胀接管端不得有纵向刻痕。如有横向刻横、麻点等缺陷时,缺陷深度不超过管子公称壁厚的10%。
2、胀接管子的端面倾斜度应不大于管子公称外径的1.5%,且最大不超过1mm。
10.21~10.3
12.22~12.32
14.23~
14.35
17.25~17.38
23.28~23.46
铜管规格
16X1.5
16X1.8
不锈钢管规格
12~13.35
12.64~12.78
胀管后内径
12.24~
10.32
14.26~14.37
23.89~24.08
3)胀接时每胀完15-20个管口,应对胀管器进行清洗,检查有无损伤,反之更换。
4、胀管率控制
①强度胀:换热管材料为铜、铜合金及不锈钢时,胀管率一般控制在0.5%~1.2%范围内,超胀不得超过2.0%;换热管材料为10钢或20钢时,胀管率一般控制在0 7%~2.1%范围内,超胀不得超过2.8%;换热管材料为黄铜时,胀管率一般控制在1%~1.8%范围内,超胀不得超过2.5%。
4)同一胀口漏水,补胀次数不应多于2次,补胀后重新进行水压试验。对于补胀后仍有漏水且胀管率大于超胀指标的管子应换管重胀。(在割除不合格的管子时,必须注意不损伤管孔壁)
5)应有专人负责记录胀接和水压试验结果,以作为验收依据并备案。
2、胀管率检验
1)每面管板按5%均布随机测量胀后换热管内径,且不少于20根,对少于20根的全部进行测量,比较理论胀管内径值,对于欠胀的管头进行补胀,补胀前应测量胀口内径,确定合适的补胀量,以免超胀。
胀接工艺规程

xxxxxx有限公司换热器管板与换热管机械胀接工艺规程1、主题内容与适用范围本工艺规定了“管板”“折流板”“管子”的胀前预处理、胀接方法和胀接密封效果的检验及泄漏处理以及胀后清理的工艺方法。
本工艺适用于管壳式换热器中钢制管板和铜制换热管的机械强度胀接。
2、胀前预处理2.1管板、折流板、换热管胀前应用钢玉砂布清除孔口周边及管口内外边缘的锐边和毛刺。
2.2管板、折流板表面和有油迹的管子应做脱脂处理,对油脂浓重部位,用丙酮或四氯化碳喷射或刷洗,然后用无油压缩气体吹干。
2.3孔内和胀槽边缘有毛刺的管板孔,须用相应尺寸的铰刀铰光,然后用无油压缩气体吹净切削。
2.45钢制折流板、拉杆、定距管应喷砂去除表面氧化层或用钢玉砂布除锈,也可用HP-2金属清洗剂作化学除锈钝化处理。
有色材料折流板脱脂用四氯化碳或洗涤剂溶液进行清洗晾干。
2.5凡经加工的管件,如翅片管、U形管、螺旋管应按图纸要求逐根进行压力试验,不漏为合格。
2.6管件长度要按设计或工艺尺寸下料,不留余量,锯口用专用刀具或锉刀去毛刺、倒角。
2.7管子两端即按设计及工艺文件要求范围内应用管端磨光机或180目以上细钢玉砂布做抛光处理,然后用无油压缩气体吹除磨料粉末。
2.8管板、管子在预处理过程中应用木质工位器具保护,避免磕碰划伤。
2.9所有经预处理后的零件,均用塑料布覆盖防尘。
3、胀接方法3.1接管应尽量采用带有扭矩控制仪的电动或风动胀管机。
3.2按管子规格和管板厚度选择合适规格的胀管器。
胀接中一般用洗涤剂溶液润滑,胀后及时清洗掉管子材质的颗粒物以减少胀管工具的损坏,并注意检查胀针和胀杆的磨损情况,必要时及时调换。
若发生断杆卡壳情况,应慎重从胀接前端用笔管径小一定尺寸的、硬度合适的圆钢通入管内将断杆和胀套、胀针一起打出,切忌损伤管内壁,造成内漏的质量事故。
3.3为了避免管端和管孔的抛光面再次被氧化,施胀与清理的时间间隔不得超过24小时。
3.4先胀4~5根管子掌握适当胀大量(参看3.5)。
换热器通用胀接工艺

引言概述换热器通用胀接工艺是一种常用的换热器连接工艺,用于将换热器管束与壳体有效连接,确保换热器的正常运行。
本文将对换热器通用胀接工艺进行详细介绍,包括工艺原理、工艺步骤、工艺优点及适用范围。
正文内容1.工艺原理1.1胀接原理换热器通用胀接工艺是通过利用金属材料的可塑性,在管束与壳体之间形成一定的力学连接,实现换热器部件之间的良好密封和传热效果。
胀接工艺利用管束内放置胀接管,通过在管束两端施加一定的胀接力,使得管束与壳体之间产生形变,从而实现紧密连接。
1.2胀接原理的基本要求胀接工艺的基本要求是确保换热器的密封性、传热效果以及结构强度。
在进行胀接前,需要进行严格的材料选择和设计计算。
一方面,胀接材料需要具备较好的抗腐蚀性能和耐高温性能,以适应不同工况下的换热器应用。
另一方面,根据换热器的工作压力和温度等参数,合理设计胀接力的大小,确保胀接的牢固性和可靠性。
2.工艺步骤2.1前期准备换热器通用胀接工艺需要进行一系列的前期准备工作。
首先是对换热器的设计进行分析和评估,确定胀接的适用性和可行性。
其次是根据设计要求选取合适的胀接材料,并对材料进行检测和验收。
然后进行胀接工艺的参数计算和工艺方案设计。
最后是制定胀接施工方案,并准备必要的工艺设备和工具。
2.2胀接施工在施工过程中,首先需要对换热器进行清洗和检查,确保管束表面光洁无污染。
接下来将胀接管按照设计要求放置于管束两端,并进行包封和固定。
然后通过工艺设备施加一定的胀接力,使得胀接管与管束和壳体发生变形,实现胀接连接。
胀接力的施加需要控制力量和速度,避免过度胀接导致破裂或松动。
2.3检测和验收胀接施工完成后,需要进行严格的检测和验收。
主要包括外观检查、胀接质量检测和尺寸测量。
外观检查主要是检查管束与壳体之间的连接是否紧密,无裂纹、变形等缺陷。
胀接质量检测可采用无损检测方法,如超声波、放射线等,检测胀接处的内部质量。
尺寸测量则是对管束直径、壳体孔径等尺寸进行测量,确保符合设计要求。
强度胀接工艺规程

强度胀接工艺规程文件编号:HN/ZQM-7-15本规程适用于换热管与管板的连接,保证换热管与管板的密封性能和抗拉脱强度。
引用标准GB151-1999一、适用范围设计压力小于等于4MPa设计温度小于等于300℃操作中应无剧烈的振动,无过大的温度变化及无明显的应力腐蚀。
二、结构型是及尺寸结构型式按下图胀贴用于≤ 用于≥用于厚管板及避免间隙腐蚀的场合结构尺寸按下表≤1416~2530~38 45~57换热管外径d伸出长度L 3+2 4+25+2槽深K 不开槽0.5 0.6 0.8三、一般要求1、最小胀接长度应取下列二者的最小值1.1管板名义厚度减去3mm1.2 50mm2、当有要求时,管板名义厚度减去3mm与50mm之间的差值可采用贴胀;或管板名义厚度减去3mm的全长胀接。
3、换热器的换热管与管板的胀接可选用柔性胀接方法,如液压胀、橡胶胀、机械胀,选用机械胀接应控制胀管率以保证胀紧度。
4、柔性胀接可分为贴胀和强度胀接,贴胀时管板孔内表面可不开槽。
强度胀接管孔内应开矩形槽。
5、换热管材料的硬度值一般须低于管板的硬度值,有应力腐蚀时,不应采用管头局部退火的方式来降低换热管的硬度。
6、换热管管端外表面应除锈至呈金属光泽,其长度不宜小于二倍的管板厚度,不应有起皮、皱纹裂纹、切口和偏斜等缺陷。
7、换热管与管板胀接时,管孔应严格垂直于管板紧密面,其垂直度允差,按GB1184—80《形状和位置公差》第9级公差等级选取,管孔表面粗糙度Ra值不大于12.5μm,管孔表面不得有影响胀接紧密性的缺陷,如贯通的纵向或螺旋状刻痕等。
8、胀接部位的换热管和管板孔表面,应清理干净不得留有影响胀接连接质量的毛刺、铁屑、锈斑油污。
9、胀接连接时,其胀接长度不得伸出管板背面(壳程侧),换热管的胀接部位与非胀接部分应圆滑过渡,不得有急剧的棱角突变。
四、胀接1、胀管机:检查胀管器及胀珠位置尺寸,应符合图样及工艺要求。
2、换热管穿入管板后,逐根进行胀接。
换热器通用胀接工艺
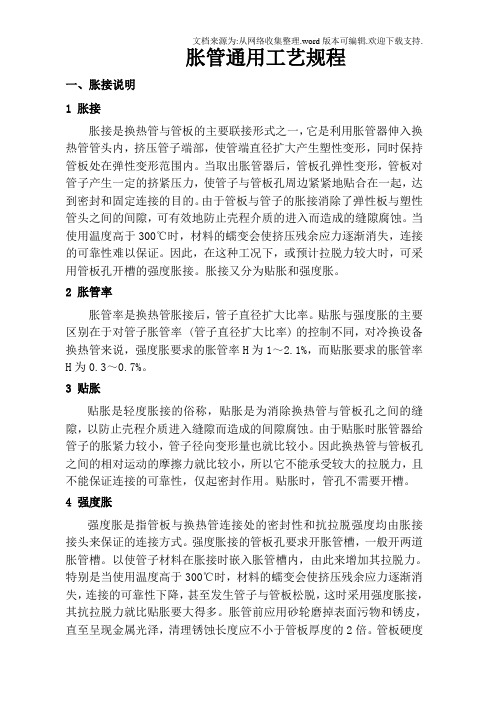
胀管通用工艺规程一、胀接说明1 胀接胀接是换热管与管板的主要联接形式之一,它是利用胀管器伸入换热管管头内,挤压管子端部,使管端直径扩大产生塑性变形,同时保持管板处在弹性变形范围内。
当取出胀管器后,管板孔弹性变形,管板对管子产生一定的挤紧压力,使管子与管板孔周边紧紧地贴合在一起,达到密封和固定连接的目的。
由于管板与管子的胀接消除了弹性板与塑性管头之间的间隙,可有效地防止壳程介质的进入而造成的缝隙腐蚀。
当使用温度高于300℃时,材料的蠕变会使挤压残余应力逐渐消失,连接的可靠性难以保证。
因此,在这种工况下,或预计拉脱力较大时,可采用管板孔开槽的强度胀接。
胀接又分为贴胀和强度胀。
2 胀管率胀管率是换热管胀接后,管子直径扩大比率。
贴胀与强度胀的主要区别在于对管子胀管率 (管子直径扩大比率) 的控制不同,对冷换设备换热管来说,强度胀要求的胀管率H为1~2.1%,而贴胀要求的胀管率H为0.3~0.7%。
3 贴胀贴胀是轻度胀接的俗称,贴胀是为消除换热管与管板孔之间的缝隙,以防止壳程介质进入缝隙而造成的间隙腐蚀。
由于贴胀时胀管器给管子的胀紧力较小,管子径向变形量也就比较小。
因此换热管与管板孔之间的相对运动的摩擦力就比较小,所以它不能承受较大的拉脱力,且不能保证连接的可靠性,仅起密封作用。
贴胀时,管孔不需要开槽。
4 强度胀强度胀是指管板与换热管连接处的密封性和抗拉脱强度均由胀接接头来保证的连接方式。
强度胀接的管板孔要求开胀管槽,一般开两道胀管槽。
以使管子材料在胀接时嵌入胀管槽内,由此来增加其拉脱力。
特别是当使用温度高于300℃时,材料的蠕变会使挤压残余应力逐渐消失,连接的可靠性下降,甚至发生管子与管板松脱,这时采用强度胀接,其抗拉脱力就比贴胀要大得多。
胀管前应用砂轮磨掉表面污物和锈皮,直至呈现金属光泽,清理锈蚀长度应不小于管板厚度的2倍。
管板硬度应比管子硬度高HB20~30,以免胀接时管板孔产生塑性变形,影响胀接的紧密性。
换热器管子与管板接头胀接工艺守则

换热器管子与管板接头胀接工艺守则换热器管子与管板接头胀接工艺守则本守则规定了压力管子与管板的胀接方法和技术要求,适用于GB150、GB151及《固容规》涉及的强度胀、焊后胀,胀后焊结构的产品。
胀接操作人员胀接操作人员必须经过有关部门技术培训,考试合格后方能上岗。
胀接操作人员应掌握所用胀接设备的使用性能,熟悉产品图样、工艺文件及标准要求。
此外,胀接操作人员应认真做好胀接场地的管理工作,对所用工、量、检具能正确使用和妥善保管。
胀接设备与胀管器胀接设备与胀管器应能满足胀接技术条件及有关标准要求。
胀接设备一般有如下几种:无自动控制胀管率装置的机械式胀管机、液压驱动扭矩自动控制胀管率的胀管机、微机控制胀管率的机械式胀管机和液压橡胶柔性胀管机。
上述胀接设备可视产品情况选择使用。
胀管器按用途一般分为12°~15°扳边胀管器、90°扳边胀管器和无扳边胀管器。
胀管器按胀柱数量一般分为3个胀柱胀管器和5个胀柱胀管器,应优先选用5胀柱胀管器。
90°扳边胀管器一般有普通90°扳边胀管器与90°无声扳边胀管器之分,应优先选用无声扳边胀管器。
胀接管子的技术要求胀接管子的外表面不得有重皮、裂纹、压扁等缺陷,胀接管端不得有纵向刻痕。
如有横向刻痕、麻点等缺陷时,缺陷深度不得超过管子公称壁厚的5%。
胀接管子的端面倾斜度△f 应不大于管子公称外径的1.5%,且最大不超过1mm。
管端硬度宜低于管板硬度,若管端硬度大于管板硬度时,应进行退火处理。
硬度检查应符合下列规定:用于胀接的管子按每个炉批号管子总数的1%取样,且不少于3个;用于管板的钢板,每个炉批号取1个试样;样坯切取位置及方向应符合GB2975的规定;硬度测试可在切取的试样上进行,亦可在管板和胀接管端上直接进行;测试前,应将测点处的氧化皮、锈蚀、油污清除掉,使之露出金属光泽;当在试样上进行时,试验方法、试样尺寸及表面要求应符合GB231的规定。
胀接工艺守则

胀接工艺守则GREENS编制:日期:批准:日期:1 主题内容与适用范围本守则规定了工业锅炉管子与锅筒或管板的胀接方法和技术要求。
本守则适用于介质出口压力不大于2.5MPa且以水为介质的快装或组装出厂的工业锅炉。
2 引用标准GB231 金属布氏硬度试验方法GB2975 钢材力学及工艺性能试验取样规定GB3087 低中压锅炉用无缝钢管GB/T8163 输送流体用无缝钢管JB/T1611 锅炉管子制造技术条件JB/T9619 工业锅炉胀接技术条件3 胀接操作人员3.1 胀接操作人员必须经过有关部门技术培训,考试合格后方能上岗。
3.2 胀接操作人员连续脱岗半年,应重新进行技术培训,经考试合格后,方可回岗操作。
3.3 胀接操作人员应掌握所用胀接设备的使用性能,熟悉锅炉产品图样、工艺文件及标准要求。
3.4 胀接操作人员应认真做好胀接场地的管理工作,对所用工、量、检具能正确使用和妥善保管。
4 胀接设备与胀管器4.1 胀接设备与胀管器应能满足胀接技术条件及有关标准要求。
4.2 胀管器可直接用于手工胀接。
4.3.1 胀管器按用途一般分为:a.12°~15°扳边胀管器;b.90°扳边胀管器;c.无扳边胀管器。
4.3.2 胀管器按胀柱数量一般分为:a.3个胀柱1个翻边柱胀管器;b.4个胀柱2个翻边柱胀管器;应优先选用4个胀柱胀管器。
5 胀接管子的技术要求5.1 胀接管子应符合GB3087或GB/T8163的规定。
5.2 胀接管子的外表面不得有重皮、裂纹、压扁等缺陷,胀接管端不得有纵向刻痕,如有横向刻痕、麻点等缺陷时,缺陷深度不得超过管子公称壁厚的10%。
5.3 水管锅炉胀接管子的制造偏差应符合JB/T1611的规定,锅壳锅炉胀接管子的长度尺寸应根据锅壳两端管板间实际长度确定。
5.4 胀接管子的端面△f应不大于管子公称外径的1.5%,且最大不超过1mm(见图书1)。
5.5 管端硬度宜低于管板(或锅筒)硬度,若管端硬度大于管板(或锅筒)硬度时,应进行退火处理。
胀接工艺流程

胀接工艺流程发泡工艺是一种常见的工业制造方法,可以将材料在加热的过程中产生气泡,从而实现材料的膨胀和变形。
它广泛应用于制造汽车、航空器、家具、建筑材料等领域。
胀接工艺是发泡工艺的一种,它通过将两个或多个材料胀接在一起,形成一个坚固的结合。
胀接工艺通常在制造材料需要具备一定的柔韧性和耐冲击性时使用。
胀接工艺的流程主要包括以下几个步骤:第一步,材料准备。
在胀接工艺中,通常会使用发泡材料和基底材料。
发泡材料有多种选择,如聚乙烯、聚丙烯等。
基底材料可以是金属、塑料、木材等。
在进行胀接之前,需要对材料进行清洁,确保表面无油污和杂质。
第二步,设计模具。
根据胀接的需求,设计相应的模具。
模具通常由金属制成,可以根据需要进行定制。
模具的设计要考虑到胀接后的材料形状和尺寸。
第三步,准备发泡材料。
将发泡材料按照一定比例混合,并加入发泡剂。
混合过程通常使用机械搅拌器进行,确保混合均匀。
然后将混合好的材料倒入模具中。
第四步,加热胀接。
将装有发泡材料的模具放入加热设备中,通常是使用加热炉进行加热。
加热的温度和时间根据材料的种类和厚度来确定。
在加热过程中,发泡材料会产生气泡,从而使材料膨胀和变形。
第五步,冷却和固化。
待胀接材料膨胀完毕后,将模具从加热设备中取出,待其冷却和固化。
冷却的时间取决于材料的种类和厚度,通常需要几分钟到几小时不等。
第六步,去除模具。
待材料冷却固化后,将模具从材料中取出。
通常需要用一把工具小心地撬起模具,从而不损坏材料。
第七步,加工和整理。
胀接后的材料可能需要进行加工和整理。
加工可以包括切割、打磨、抛光等,以得到预期的形状和尺寸。
整理包括清理表面杂质和修饰外观,使材料更具美观性和实用性。
胀接工艺流程清楚明了,但实际操作时也需要注意一些细节。
例如,在混合发泡材料时要确保混合均匀,否则可能会导致胀接后的材料质量不稳定。
另外,加热温度和时间的控制也是关键,如果温度过高或时间过长,可能导致材料过度膨胀或变质。
此外,使用合适的模具和合适的加工工具也对胀接后的材料质量和外观有很大影响。
不锈钢管胀接工艺

不锈钢管胀接工艺
一、胀接工艺介绍
不锈钢管胀接工艺是一种常用的连接方式,它通过利用不锈钢管的弹
性和塑性来实现管道的连接。
该工艺具有结构简单、操作方便、效率
高等优点,广泛应用于建筑、化工、石油等领域。
二、胀接工艺流程
1.准备工作
首先需要准备好所需的材料和工具,包括不锈钢管、胀接头、切割机、钳子等。
2.切割管道
将要连接的两根不锈钢管分别放在切割机上进行切割,保证两端平整
且无毛刺。
3.安装胀接头
将胀接头插入其中一根管道中,并轻轻拧动以确保其与管道紧密贴合。
4.使用钳子进行胀口处理
将另一根管道插入胀接头内部,并使用钳子逐渐扭转直到其完全卡住。
注意力度适中,过度扭转会导致胀口变形或者破裂。
5.检测连接质量
使用手感或者外观检查连接处是否牢固并且没有漏气现象。
三、胀接工艺注意事项
1.选择合适的胀接头,确保其与管道直径相同。
2.切割管道时,要使用专业的切割机,并且保证两端平整无毛刺。
3.在进行胀口处理时,要注意力度适中,过度扭转会导致胀口变形或者破裂。
4.检测连接质量时,要仔细检查是否牢固并且没有漏气现象。
四、总结
不锈钢管胀接工艺是一种常用的连接方式,具有结构简单、操作方便、效率高等优点。
在进行该工艺时需要注意选择合适的胀接头、使用专
业的切割机进行管道切割、注意力度适中以及仔细检查连接质量。
通
过以上步骤可以实现不锈钢管的快速连接,并达到牢固可靠的效果。
胀管工艺规程
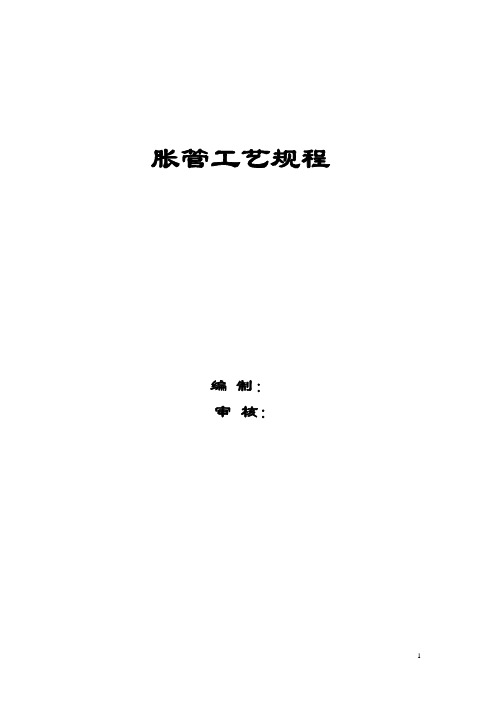
+15% -10%
±0.8% ±10%
±1%
+12% -10%
抽查区域应不小于管板中心角 60。范围内管孔孔径,允许抽查区域
内有 4%管孔直径偏差比表 1-2 中数值大 0.15mm。
换热管与换热板的管孔允许偏差
表 1-2
类别 换热器外径(mm)
19
25 32
38
45
57
Ⅰ 换热管允许偏差(mm) ±0.2 ±0.2 ±0.3 ±0.3 ±0.3 ±0.45
2
换热管的允许偏差 表 1-1
材料
标准
碳 GB8163-87
钢
外径×厚度
(mm)
19×2 25×2 25×2.5 32×3 38×3 45×3
57×3.5
Ⅰ级换热器 外径偏差 壁厚偏差 (mm) (mm)
±0.2 ±0.3
+12% -10%
Ⅱ级换热器 外径偏差 壁厚偏差 (mm) (mm)
±0.4 ±0.45
19.40
+0.20 0
25.40
+0.2 0
32.50
+0.30 0
38.50
+0.30 0
45.50
+0.40 0
57.70
+0.40 0
2、对工艺评定的要求 实施本工艺时,必须按照正确方法完成下列工艺评定: (1)换热器与管板接头焊接工艺评定。 (2)换热器与管板接头贴胀工艺评定。 3、对管子与管板结合部位的清理
8
胀管工艺规程
编 制: 审 核:
1
管子与管板“焊、胀”连接工艺
一、原理及适用条件 本工艺的实施步骤是焊-胀。它巧妙地运用胀接过程的超压过载技 术,通过对管与管板的环形焊缝进行复胀,造成应变递增而应力不增加, 即让该区域处于屈服状态,在焊缝的拉伸残余应力场中,留下一个压缩 残余应力体系。两种残余应力相互叠加的结果,使其拉伸残余应力的峰 值大减;二次应变又引起应力的重新分布,结果起到调整和均化应力场 的效果,最终将残余应力的峰值削弱到预定限度以下。 本工艺适用于管子与管板的胀、焊并用连接型列管式换热器的工厂 或现场加工。管板厚度范围为 16~100mm,材质为碳钢者,就符合 GB150-98 第二章 2.2 条的规定,若采用 16Mn 时,就分别符合 GB3247 — 88 和 GBI51 — 99 中 的 有 关 规 定 ; 换 热 管 束 应 符 合 GB8163 、 GB9948-88、GB6479-86、GB5310-85 的规定。 二、焊、胀工艺 (一)准备工作 1、对换热管和管板的质量检查 (1)管子内外表面不允许有重皮、裂纹、砂眼及凹痕。管端头处不 得有纵向沟纹,横向沟纹深度不允许大于壁厚的 1/10。 管子端面应与管子轴线垂直,其不垂直度不大于外径的 2%。 (2)换热管的允许偏差应符合表 1-1 要求。 (3)管孔表面粗糙度 Ra 不大于 12.5μm,表面不允许纵向或螺旋 状刻痕。管孔壁面不得有毛刺、铁屑、油污。 (4)管孔的直径允许偏差应符合表 1-2 规定。
换热器通用胀接工艺
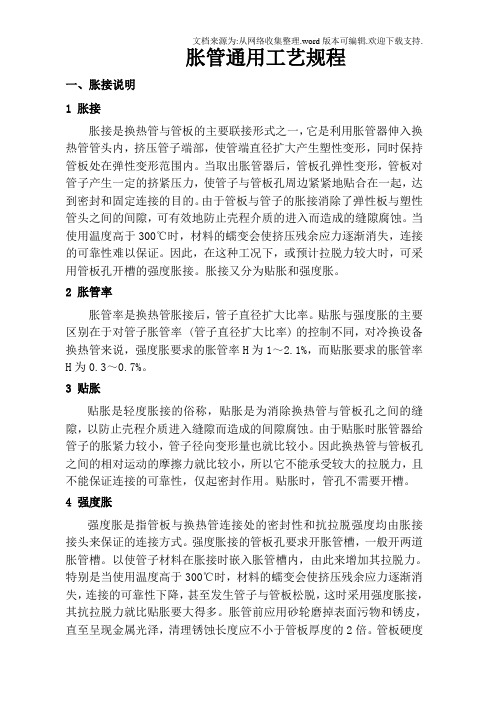
胀管通用工艺规程一、胀接说明1 胀接胀接是换热管与管板的主要联接形式之一,它是利用胀管器伸入换热管管头内,挤压管子端部,使管端直径扩大产生塑性变形,同时保持管板处在弹性变形范围内。
当取出胀管器后,管板孔弹性变形,管板对管子产生一定的挤紧压力,使管子与管板孔周边紧紧地贴合在一起,达到密封和固定连接的目的。
由于管板与管子的胀接消除了弹性板与塑性管头之间的间隙,可有效地防止壳程介质的进入而造成的缝隙腐蚀。
当使用温度高于300℃时,材料的蠕变会使挤压残余应力逐渐消失,连接的可靠性难以保证。
因此,在这种工况下,或预计拉脱力较大时,可采用管板孔开槽的强度胀接。
胀接又分为贴胀和强度胀。
2 胀管率胀管率是换热管胀接后,管子直径扩大比率。
贴胀与强度胀的主要区别在于对管子胀管率 (管子直径扩大比率) 的控制不同,对冷换设备换热管来说,强度胀要求的胀管率H为1~2.1%,而贴胀要求的胀管率H为0.3~0.7%。
3 贴胀贴胀是轻度胀接的俗称,贴胀是为消除换热管与管板孔之间的缝隙,以防止壳程介质进入缝隙而造成的间隙腐蚀。
由于贴胀时胀管器给管子的胀紧力较小,管子径向变形量也就比较小。
因此换热管与管板孔之间的相对运动的摩擦力就比较小,所以它不能承受较大的拉脱力,且不能保证连接的可靠性,仅起密封作用。
贴胀时,管孔不需要开槽。
4 强度胀强度胀是指管板与换热管连接处的密封性和抗拉脱强度均由胀接接头来保证的连接方式。
强度胀接的管板孔要求开胀管槽,一般开两道胀管槽。
以使管子材料在胀接时嵌入胀管槽内,由此来增加其拉脱力。
特别是当使用温度高于300℃时,材料的蠕变会使挤压残余应力逐渐消失,连接的可靠性下降,甚至发生管子与管板松脱,这时采用强度胀接,其抗拉脱力就比贴胀要大得多。
胀管前应用砂轮磨掉表面污物和锈皮,直至呈现金属光泽,清理锈蚀长度应不小于管板厚度的2倍。
管板硬度应比管子硬度高HB20~30,以免胀接时管板孔产生塑性变形,影响胀接的紧密性。
- 1、下载文档前请自行甄别文档内容的完整性,平台不提供额外的编辑、内容补充、找答案等附加服务。
- 2、"仅部分预览"的文档,不可在线预览部分如存在完整性等问题,可反馈申请退款(可完整预览的文档不适用该条件!)。
- 3、如文档侵犯您的权益,请联系客服反馈,我们会尽快为您处理(人工客服工作时间:9:00-18:30)。
胀接工艺胀接工艺1胀接前的准备工作1.1受热面管子安装前的检查,应符合下列要求1.1.1管子表面不应有重皮、裂纹、压扁和严重锈蚀等缺陷。
当管子表面有刻痕、麻点等其他缺陷时,其深度不应超过管子公称壁厚的10%。
1.1.3对流管束应作外形检查及矫正,校管平台应平整牢固,放样尺寸误差不应大于1mm,矫正后的管子与放样实线应吻合,局部间隙不应大于2mm,并应进行试装检查。
1.1.4受热面管排列应整齐,局部管段与设计安装位置偏差不宜大于5mm。
1.1.5胀接管口的端面倾斜度不应大于管子公称外径的1.5%,且不大于1mm。
1.1.6受热面管子应作通球检查,通球后的管子应有可靠的封闭措施,通球直径应符合表4-1的规定。
表4-1通球直径(mm)注:1、Dw—管子公称外径;Dn—管子公称内径;2、试验用球一般采用不易产生塑性变形的材料制造。
试验用球一般应用钢材或木材制成,不宜用铝等易产生塑性变形材料,通球所用的球要逐个编号,严格管理,防止球遗忘于管内,对完成通球检查的管子临时封堵。
做好通球记录。
1.2管子的硬度测定,每根管子的两端均应测试硬度,常用的硬度测定方法有布氏硬度(HB)和洛氏硬度(HRC)等。
1.3管子端头退火1.3.1胀接管子的锅筒(锅壳)和管板的厚度应不小于12mm。
胀接管孔间的距离不应小于19 mm。
外径大于102 mm的管子不宜采用胀接。
1.3.2胀接管子材料宜选用低于管板硬度的材料。
若管端硬度大于管板硬度时,应进行退火处理。
管端退火不得用煤炭作燃料直接加热,管端退火长度不应小于100 mm。
1.3.3管子胀端退火时,受热应均匀,退火温度应控制在600~650℃之间,并应保持10~15min,退火时间应为100~150min,退火后的管端应有缓慢冷却的保温措施。
1.4胀接管孔的质量应符合下列要求1.4.1胀管管孔的表面粗糙度Ra不应大于12.5μm,且不应有凹痕,边缘毛刺和纵向裂痕,少量管孔的环向或螺旋形刻痕深度不应大于0.5mm,宽度不应大于1mm,刻痕至管孔边缘的距离不应小于4mm。
1.4.2胀管管孔的允许偏差应符合表4-2表4-2胀接管孔的直径与允许偏差(mm)1.5胀管器、胀管机选择1.5.1胀管动力有手动、电动、风动、液压传动等多种,大中型锅炉胀接多采用电动胀管机。
1.5.2胀管器的规格选择胀管器盖板上应有产品规格钢印,并附有说明书和质量证明等技术文件,其说明书应明确该胀管器可胀接管子的规格。
使用前还应根据对锅筒和管子的检测结果,对胀管器的可适用性进行检查。
方法是:1.5.2.1将胀杆向里推进,使胀珠尽量向外,形成的切圆的直径应大于管子的终胀内径;1.5.2.2胀珠的长度应与钢筒的壁厚相适应,翻边终胀的胀管器直胀珠的长度,应是锅筒壁厚加管端伸入锅筒两倍的长度。
例如胀接Ф32~Ф63.5管子与壁厚50mm的锅筒胀接,选胀管器胀珠直段的长度应是50+18±2=68±2mm。
1.5.3拆解胀管器进行检查1.5.3.1胀杆胀珠不直度应小于0.1mm;1.5.3.2胀杆的锥度应为1/20~1/25,胀珠的锥度应是1/40~1/50(即胀杆与胀珠锥度比2:1);1.5.3.3胀杆和胀珠的表面必须光洁、无沟纹斑痕、起皮等缺陷,其工作表面粗糙度Ra≤12.5μm;1.5.3.4胀珠的工作表面硬度应不低于HRC52,胀杆的工作表面硬度应比胀珠工作表面硬度高HRC6~10;1.5.3.5同一胀管器各巢孔的倾斜应一致,斜度应为a=1.5°~2.5°向左斜,错列式翻边胀珠巢不需斜度,巢孔锥度与胀珠锥度相匹配,胀壳上的胀珠巢与胀珠间隙,新的胀管器为0.2~0.3mm,旧的不大于0.7mm。
1.5.4对胀管器组装体进行检查1.5.4.1将胀杆全推入胀管器内进行检查:翻边胀管器,胀珠应转动灵活,胀珠不从珠巢中脱落;串列式翻边胀管器,翻边珠与直胀珠轴向总间隙应小于1mm。
1.5.4.2自进式胀管器胀杆顺时转动胀杆,胀杆向里推进,同时胀珠能自动均匀平稳扩胀,逆时针转动胀杆时胀杆能轻松退出。
1.5.4.3用直尺测量胀杆推进或迟出量,用油标卡尺测量各胀珠外扩或内缩直径是否均匀,是否与胀杆伸缩量成固定的正比例。
2试胀及胀接工艺规程的制订2.1胀接前应进行试胀工作,以检查胀管的质量和管材的胀接性能。
在试胀工作中,要对试样进行比较性检查,检查胀口部分是否有裂纹,胀接过渡部分是否有剧烈变化,喇叭根部与管孔壁的结合状态是否良好等,然后检查管孔壁与管子外壁的接触表面的印痕和啮合状况。
根据检查结果,确定合理的胀管率。
需在安装现场进行胀接的锅炉出厂时,锅炉制造单位应提供适量同钢号的胀接试件(胀接试板应有管孔)。
2.2施工单位应根据锅炉设计图样和试胀结果制订胀接工艺规程。
胀管操作人员应经过培训,并严格按照胀接工艺规程进行胀管操作。
2.3电动胀管机试验检验内容2.3.1胀接消除间隙阶段电流值;2.3.2固定胀管,即消除间隙后,再将管径扩胀0.2~0.3mm阶段的电流值;2.3.3翻边扩胀阶段的电流值2.3.4试验胀管内孔每扩大1mm,胀杆进伸实际深度,和实际旋转的圈数;2.3.5试胀中应准确控制2.3.1~2.3.4条款的数据,以便实际胀管参照这些数据进行操作。
2.4要求连续试胀,不断测量和记录,将每一个胀口的胀前管孔径、管内径及管与孔间隙扩胀量等准确详实记录。
2.5水压试验检查试胀口,将试胀板的胀口翻边的一侧密封,按锅炉水压强度试验的压力,对试胀口进行水压试验。
如果水压试验发现泄漏,应拆开封闭进行复胀,并做复胀记录,再做水压试验,直至水压试验合格。
2.6试胀外观检查:观察胀口有无单边偏挤、胀口内不光滑、翻边有台阶、切口或裂纹、过渡段不自然等缺陷。
2.7解剖胀口检查胀口啮合与胀缩情况。
将试胀合格和不合格的胀口分别用机械切开(不能用乙炔割开)检查各种胀口管外径与管孔壁啮合情况,测量管壁减薄值,通过比较管孔切开前后的直径变化判断管孔回弹实况。
2.8分析以上试胀检查记录,对材料的胀接性能、机具操作参数、胀管操作工艺程序、合理的胀管率控制值等作出鉴定,写出书面试胀工艺评定,用以指导锅炉胀管施工。
3胀接的技术要求3.1胀接前,应清除管端和管孔的表面油污,并打磨至发生金属光泽;管端的打磨长度应至少为管孔壁厚加50mm。
打磨后,管壁厚度不得小于公称壁厚的90%,且不应有起皮、凹痕、裂纹和纵向刻痕等缺陷。
3.2胀接管端应根据打磨后的管孔直径与管端外径的实测数据进行选配,胀接管孔与管端的最大间距应符合表4-3的规定。
3.3胀接时,环境温度宜为0℃以上。
3.4胀管应符合下列要求表4-3胀接管孔与管端的最大间隙(mm)表4-4管端伸出管孔的长度(mm)3.4.2管端装入管孔后,应立即进行胀接。
3.4.3其准管固定后,宜从中间分向两边胀接。
3.4.4胀管率应按测量管子内径在胀接前后的变化值计算(以下简称内径控制法),或按测量紧靠锅筒外壁处管子胀完后的外径计算(以下简称外径控制法)。
当采用内径控制法时,胀管率Hn应控制在1.3%~2.1%的范围内;当采用外径控制法时,胀管率Hw应控制在1.0%~1.8%的范围内,并分别按下列公式计算:Hn=(d1―d2―δ)÷d3×100%HW=( d4-d3)÷d3×100%式中 Hn—采用内径控制法时的胀管率;HW—采用外径控制法时的胀管率;d1—胀完后的管子实测内径(mm);d2—未胀时的管子实测内径(mm);d3—未胀时的管孔实测内径(mm);d4—胀完后紧靠锅筒外壁处管子实测内径(mm);δ—未胀时管孔的管子实测外径之差(mm)3.4.5管口应翻边,翻边起点宜与锅筒表面平齐,翻边角度宜为12°~15°。
3.4.6胀管器滚柱数量不宜少于4只;胀管应用专用工具测量。
4胀接的质量及检验4.1胀接后,管端不应有起皮、皱纹、裂纹,切口和偏斜等缺陷。
在胀接过程中,应随时检查胀口的胀接质量,及时发现和消除缺陷。
4.2为了计算胀管率和检查胀管质量,施工单位根据实际检查和测量结果,做好胀接记录。
4.3胀接全部完毕后,必须进行水压试验,检查胀口的严密性。
5胀口补胀及胀管率的控制5.1经水压试验确定需补胀的胀口,应在放水后立即进行补胀,补胀次数不宜多于2次。
5.2胀口补胀前应复测胀口内径,并确定补胀值。
补胀值应按测量胀口内径在补帐前后的变化值计算。
其补胀率应按下式计算:ΔH=(d3―d2)÷d1×100%式中ΔH—补胀率d3—补胀后的管子内径(mm);d2—补胀前的管子实测内径(mm);d1—未胀时的管孔实测内径(mm);补胀后,胀口的累计胀管率应为补胀前的胀管率与补胀率之和,当采用内径控制法时,累计胀管率宜控制在1.3%~2.1%范围内;当采用外径控制法时,累计胀管率宜控制在1.0%~1.8%的范围内。
5.3胀管率超出控制范围时,超胀的最大胀管率:当肛用内径控制法控制时,不得超过2.6%;当采用外径控制法控制时,不得超过2.5%;在同一锅筒上的超胀管口数量不得大于胀接总数的4%,且不得超过15个。
5.4扩胀量的控制方法。
原则是利用试胀结果,例如:扩胀量与电流或扩胀与胀杆进行伸量的比例关系,控制扩胀量,实际操作还要边胀接边测量,随时调整扩胀值,不能盲目操作,造成不可弥补的胀接缺陷。
5.5翻边调整。
扩胀时原翻边会有所变化,当扩胀到预定值时,停止进胀,胀管器3~5圈达到调整翻边和光滑胀口内表面的目的。
5.6对扩胀结果测量记录。
各个胀口扩胀后,对胀管内径进行测量,按实测数据核算胀管率,将实测值和胀管率填入胀管记录作为交工依据。
6胀接常见缺陷和预防纠正措施胀接常见缺陷和预防纠正措施见表4-5~4-7。
表4-5胀接常见缺陷和预防纠正措施胀接缺陷特征及不良后果原因分析预防和纠正措施1外观一般缺陷人、机、料、法、环有针对性、对症采取预防纠正措施1.1翻边有裂纹,严重时可影响胀接使用寿命人:管端处理不当料:材质不均匀有裂纹环:胀接温度低A、管端伸入锅筒不能过长B、端头修磨C、插管前超声波抽查管端缺陷D、环境温度0℃以上或对管端预热翻边1.2胀口内壁环向擦痕或起皮、麻坑等胀管器胀珠破损A、适当润滑B、清洗检查胀珠硬度和光洁度C、必要时更换胀管器1.3未胀与受胀过渡段明显1.4受胀内壁有纵向突起条纹直胀珠末端过渡段短且无过渡圆角在一个位置起始胀接旋转不均匀A、检查胀珠下部过渡段必要时人工修磨此部分B、转换角度起胀C、不进胀转胀管器1.5翻边转角和直段交接部1)挤压双层台严重时影响胀口严密性2)有切痕,严重时影响管端寿命机:翻边胀珠与直胀珠有间隙机:直胀珠与翻边胀珠接触直径不等A、如使用串列胀管器时检查直胀珠与翻边珠间隙应小于0.5mmB、用错列式三珠翻边胀管器C、减缓翻边速度表4-6胀接常见缺陷和预防纠正措施胀接缺陷特征及不良后果原因分析预防和纠正措施2整体或部分漏分原因复杂补胀,限胀率1.3%~2.1%(内控法)2.1管子受胀与未胀部分外径变化不明显扩胀量不足A、确定胀管率的大小要经试验鉴定B、扩胀达到预定胀管率,不可随意少胀C、审查胀接记录,确认欠胀的补充扩胀2.2管与孔接触面有杂物,材料有纵向沟纹对管与孔检查处理不严A、检查处理沟纹打磨与清洗管端和保持管与孔间隙不被污染B、适当补充扩胀(以不过胀为限)2.3沿圆周方向胀接不均匀,管壁略呈棱形或三角形进胀速度快,胀珠数量少A、机械胀管机应平稳旋转缓慢进胀B、不进胀空转动胀管器或少量扩胀碾压管壁2.4沿轴线方向胀接不均匀,胀口有锥度管孔呈锥体或胀管器与胀杆锥度不标准A、胀管圆锥度应符合允许偏差否则应处理合格再胀接B、胀珠锥度与胀杆锥度比应1:2,如不适宜更换胀管器C、少量扩胀碾压管壁,纠正锥状2.5单边偏挤。