螺纹轴加工与工艺
轴的加工工艺包含哪些工艺

轴的加工工艺包含哪些工艺
轴的加工工艺主要包括以下几种:
1. 铣削:利用铣床进行切削加工,通过刀具在工件表面上移动切削下去,以形成所需形状和尺寸;
2. 螺纹加工:利用车床进行螺纹加工,包括内螺纹和外螺纹的加工,常见的加工方法有螺丝刀切削、切割、割头插装和模块化刀具;
3. 磨削:利用磨床进行磨削加工,可以通过砂轮进行切削、抛光、研磨等,以达到高精度、高表面质量的要求;
4. 铰削:用铰刀进行铰削加工,可以对轴孔进行加工,完成对轴部分直径或孔部分倒角的形成;
5. 钻削:用钻床进行钻削加工,通过钻头切削工件,形成孔或孔加工的工艺;
6. 切削:利用车床进行切削加工,通过车刀对工件进行切削,形成外形和尺寸;
7. 光电处理:利用激光或电子束进行材料熔化、汽化,形成孔或加工轴的外形;
8. 焊接:利用焊接设备进行焊接加工,通常是连接两个或多个轴材料;
9. 热处理:通过加热和冷却过程对轴进行热处理,以提高其物理和机械性能;
10. 表面处理:包括镀层、喷涂、阳极氧化等工艺,以提高轴的耐腐蚀性和外观质量。
以上是一些常见的轴加工工艺,具体应根据实际情况选择合适的工艺。
螺纹加工基本常识
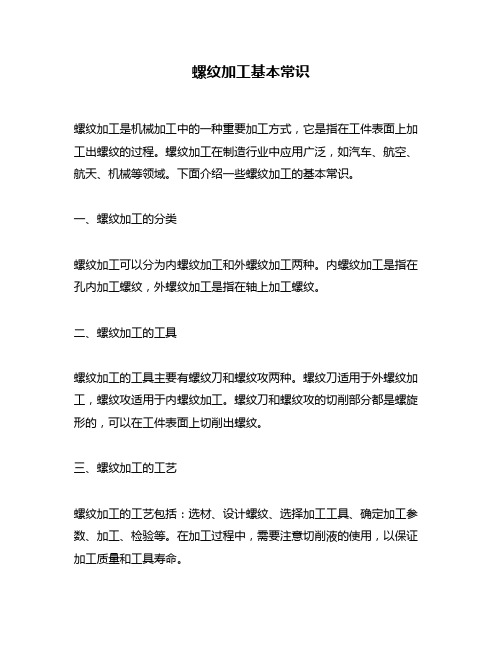
螺纹加工基本常识
螺纹加工是机械加工中的一种重要加工方式,它是指在工件表面上加工出螺纹的过程。
螺纹加工在制造行业中应用广泛,如汽车、航空、航天、机械等领域。
下面介绍一些螺纹加工的基本常识。
一、螺纹加工的分类
螺纹加工可以分为内螺纹加工和外螺纹加工两种。
内螺纹加工是指在孔内加工螺纹,外螺纹加工是指在轴上加工螺纹。
二、螺纹加工的工具
螺纹加工的工具主要有螺纹刀和螺纹攻两种。
螺纹刀适用于外螺纹加工,螺纹攻适用于内螺纹加工。
螺纹刀和螺纹攻的切削部分都是螺旋形的,可以在工件表面上切削出螺纹。
三、螺纹加工的工艺
螺纹加工的工艺包括:选材、设计螺纹、选择加工工具、确定加工参数、加工、检验等。
在加工过程中,需要注意切削液的使用,以保证加工质量和工具寿命。
四、螺纹加工的注意事项
1. 加工前需要对工件进行清洗,以去除表面的油污和杂质,以免影响加工质量。
2. 加工时需要注意切削液的使用,以保证切削液的浓度和温度,以及切削液的流量。
3. 加工时需要注意刀具的选择和切削参数的确定,以保证加工质量和工具寿命。
4. 加工后需要对加工质量进行检验,以保证加工质量符合要求。
总之,螺纹加工是机械加工中的一种重要加工方式,它在制造行业中应用广泛。
在螺纹加工过程中,需要注意选材、设计螺纹、选择加工工具、确定加工参数、加工、检验等方面的问题,以保证加工质量和工具寿命。
数控加工工艺及编程 项目3螺纹轴加工工具刀具选择

螺纹轴加工刀具和工具选择一、车刀选择外圆车刀选择原则与短轴加工时的外圆车刀相同用90度外圆车刀,这里就不在赘述。
分析该螺纹零件。
螺纹为M12的三角外螺纹,我选择三角形外螺纹车刀,刀尖角60度。
割槽刀选用3mm宽的外割槽刀。
二、螺纹车刀特点螺纹车刀是成形刀具,其切削部分的形状应和螺纹牙型轴向剖面的形状相符合,车刀的刀尖角应该等于牙型角。
三角形螺纹的牙型角是60°,理论上三角形螺纹车刀的刀尖角也应该是60°。
但实际生产中,只有高速工具钢三角形螺纹车刀的刀尖角是60°,硬质合金三角形螺纹车刀的刀尖角则应为59°30’左右。
这是因为用硬质合金车刀高速切削时,工件材料受到较大的挤压力,会使牙型角增大约0.5°。
三、螺纹车刀种类1.高速工具钢三角形螺纹车刀(图1)的前角一般取5°~15°,粗车刀的纵向前角一般取15°左右,精车刀的前角一般取6°~10°。
2.硬质合金三角形螺纹车刀(图2)的前角和纵向前角一般都取0°,为了增加切削刃的强度,在车削较高硬度的材料时,两切削刃上可磨出负倒棱。
a)粗车到b)精车刀图1高速钢三角螺纹车刀c)焊接式d)机加式图2 硬质合金三角螺纹车刀三、刀具的刃磨三角螺纹车刀刃磨要求:①根据粗、精车的要求,刃磨出合理的前、后角。
粗车刀前角大、后角小,精车刀则相反;②车刀的左右刀刃必须是直线,无崩刃;③刀头不歪斜,牙型半角相等;④内螺纹车刀刀尖角平分线必须与刀杆垂直;⑤内螺纹车刀后角应适当大些,一般磨有两个后角。
四、割槽刀1)高速工具钢槽刀如图3所示1)前角ϒ0:前角增大能使车刀刃口锋利,切削省力并排屑顺畅,ϒ0=5°~20°;2)主后角α0:可减少车槽刀主后刀面和工件过渡表面间的摩擦,α0=6°~8°;3)副后角α0’:可减少车槽刀两个副后刀面和工件已加工表面间的摩擦,α0'=1~3°。
螺纹轴的加工与分析.

如图2.1,编程中,每次螺纹加工走刀至少有4次基本运动(直螺纹)。
运动①:将刀具从起始位置X向快速(G00方式)移动至螺纹计划切削深度处。
运动②:加工螺纹——轴向螺纹加工(进给率等于螺距)。
运动③:刀具X向快速(G00方式)退刀至螺纹加工区域外的X向位置。
运动④:快速(G00方式)返回至起始位置。
绪
随着计算机技术的高速发展,传统的制造业开始了根本性变革,各工业发达国家投入巨资,对现代制造技术进行研究开发,提出了全新的制造模式。在现代制造系统中,数控技术是关键技术,它集微电子计算机、信息处理、自动检测、自动控制等高薪技术于一体,具有高精度、高效率、柔性自动化等特点,对制造业实现柔性自动化、集体化、智能化起着举足轻重的作用。同时,市场对产品的质量和生产效率提出了越来越高的要求。根据数控车削加工的工艺方法,安排工序的先后顺序,确定刀具的选择和切削用量的选择等设计。一般生产加工中,螺纹的加工方式多采用攻丝这种传统工艺,随着数控技术的发展、软件的创新、控制精度的提高、三轴联动或多轴联动数控系统的产生及其在生产领域的广泛应用,相应的先进加工工艺——螺纹铣削逐渐得以实现,其加工精度、光洁度以及柔性是攻丝无法比拟的,另外其经济性在某种情况下也更优于传统工艺。良好的结构工艺性,可以使零件加工容易,节省工时和材料。而较差的零件零件工艺性,会使加工困难,浪费工时和材料,有时甚至无法加工。因此,零件各加工部位的结构工艺性应符合数控加工的特点。
图1.3
H=0.866Pd2=d–0.6495Pd1=d–1.0825Pα=60°
D、d-内、外螺纹大径D2、d2-内、外螺纹中径D1、d1-内、外螺纹小径P-螺距
2三角螺纹的加工
2.1 螺纹加工概念及加工工艺
第六章 螺纹加工
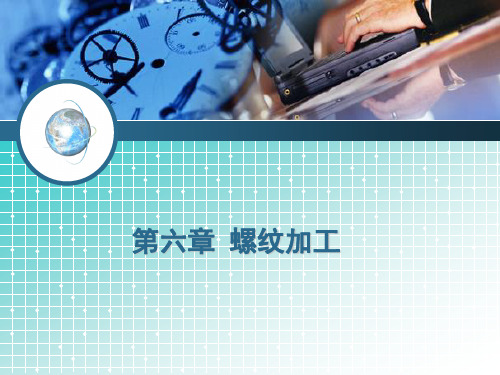
三、梯形螺纹车刀的装夹
螺纹车刀的刀尖应与工件轴线等高,两切削刃夹角的平分 线应垂直于工件轴线,装夹时用梯形螺纹对刀样板校正,以免 产生螺纹半角误差。
四、梯形螺纹车削注意事项
1. 加工梯形螺纹时应采用左右借刀法加工,避免刀具三刃 口同时切削,产生扎刀。 2. 螺纹的牙型角要正确,螺纹牙型两侧面的表面粗糙值要 小。 3. 螺纹加工过程中,应注意不得改变转速,否则会乱牙。
第六章 螺纹加工
在各种机电产品中,螺纹的应用十分广泛,如螺钉、螺 母、螺杆、丝杠等。 用途:它主要用于连接各种机件,也可用来传递运动和载 荷。 主要分类: 按螺纹的牙型——三角形、梯形、锯齿形、圆形等; 按螺纹的外廓形状——圆柱螺纹、圆锥螺纹。
螺纹轴套零件图
第一节 等距螺纹的加工 第二节 多线螺纹的加工 第三节 梯形螺纹的加工
二、运用子程序加工梯形螺纹
上例中的螺纹加工也可用左右切削法,可调用子程序重复 进刀切削。
(下一页续表)
续表
梯形螺纹的加工方法
一、梯形螺纹的一般技术要求
梯形螺纹的轴向剖面形状是等腰梯形。用作传动,精度要 求高,表面粗糙值小,车削梯形螺纹比车削三角螺纹困难。梯 形螺纹的一般技术要求如下: 1. 螺纹的中径必须与基准轴颈同轴,其大径尺寸应小于基 本尺寸。
毛坯为φ45mm×75mm的45钢,用G71、G92指令进行编程, 加工该零件。
实例零件图
一、工艺分析
1. 夹住毛坯φ45mm外圆,伸出大于40mm长→粗车 φ34mm外圆至φ34.5mm→粗车φ24mm外圆至φ24.5mm,精 车外轮廓至尺寸。 2. 换4mm车槽刀加工退刀槽。 3. 换外三角螺纹刀粗、精加工M24×3(1.5)-6g外 螺纹至尺寸。
k :螺纹的牙深。半径值,单位为μm。
双线螺纹零件加工
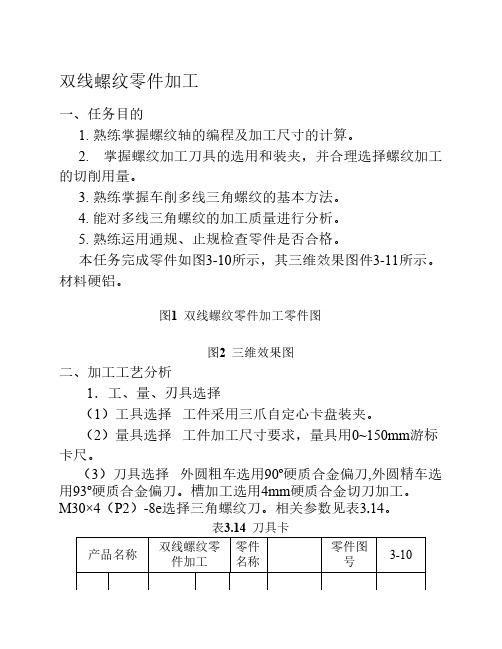
表3.14 刀具卡
产品名称
双线螺纹零 零件 件加工 名称
零件图 号
3-10
序号 刀具号 刀具名 数量 加工 刀尖半径 刀尖方位 备注
称
表面
90º硬
粗车
1 T1 质合金 1 阶梯 0.4mm
3
偏刀
轴
93º硬
精车
2 T2 质合金 1 阶梯 0.2mm
3
偏刀
轴
3
T3
硬质合 金切刀
1
切 槽、 切断
刀宽4mm
车至Ф34外圆公差中值
车Ф42外圆 快速退刀至换刀点 关闭切削液 主轴停 换刀T0202 主轴正转,转速为800r/min,进给量 0.12mm/r 打开冷却液 快速进刀至循环起点 精车循环 快速退刀至换刀点 切削液停 主轴停 换切刀 主轴正转,转速为350r/min,进给量 0.25mm/r 切削液开 快速进刀至第一刀切槽起点 切槽第一刀留0.5mm余量 暂停1s 快速退刀至第一刀切槽起点 快速退刀至第二刀切槽起点 切槽第二刀 暂停1s 车槽底
60º硬质
车外
4
T4 合金螺纹
车刀
1
螺纹
0.2
编制
审核
批
准
共1页
2.加工工艺方案
(1)加工工艺路线
如图3-10所示,根据零件的工艺特点和毛坯尺寸
Ф45×100mm,确定零件加工方案 。
① 采用三爪自定心卡盘装卡,零件伸出卡盘85mm,加工
零件外轮廓至尺寸要求后切断,留0.5 mm余量。设置编程原点
在工件右端面的轴线上。
快速定位至循环起点
N530 G92 X29.2 Z-24.0 螺纹车削循环第一刀,切深
F4.0
杆螺纹轴数控车削加工工艺过程及编程设计
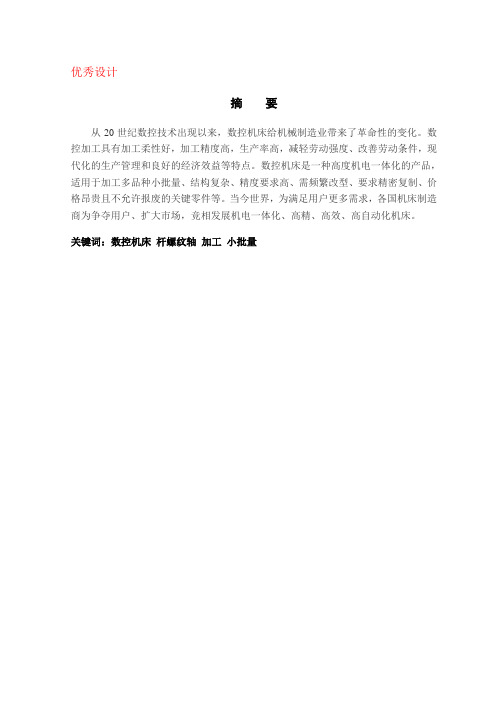
优秀设计摘要从20世纪数控技术出现以来,数控机床给机械制造业带来了革命性的变化。
数控加工具有加工柔性好,加工精度高,生产率高,减轻劳动强度、改善劳动条件,现代化的生产管理和良好的经济效益等特点。
数控机床是一种高度机电一体化的产品,适用于加工多品种小批量、结构复杂、精度要求高、需频繁改型、要求精密复制、价格昂贵且不允许报废的关键零件等。
当今世界,为满足用户更多需求,各国机床制造商为争夺用户、扩大市场,竞相发展机电一体化、高精、高效、高自动化机床。
关键词:数控机床杆螺纹轴加工小批量AbstractSince twentieth Century of numerical control technology, numerical control machine tool to bring a revolutionary change in the mechanical manufacturing industry. NC machining processing with good flexibility, high machining precision, high productivity, reduce labor intensity, improve working conditions, the modernization of production management and good economic benefit etc.. NC machine tool is a kind of mechanical and electrical products, applicable to the processing of many varieties of small batch, complex structure, high precision, need frequent modification, precision replication, expensive and does not allow the scrap key parts etc.. In today's world, to meet the user more demand, machine tool manufacturers for the user, enlarge the market, competing for the development of electromechanical integration, high precision, high efficiency, high automation machine.Keywords: CNC machine tool rod threaded shaft processing small quantities目录摘要 (2)1.引言 (4)2.数控车床概述 (4)2.1数控车床的基本构成及特点 (4)2.1.1数控车床的基本构成 (4)2.1.2数控车床的结构特点 (5)2.2数控车床的分类 (5)2.2.1按数控系统的功能分类 (6)2.2.2按加工零件的基本粪型分类 (6)2.2.3 按数控车床主轴位置分类 (6)2.2.4 按刀架数量分类 (7)2.3数控车床的加工特点 (8)3.数控车削加工工艺编制基础 (9)4. 3.1零件图工艺分析 (9)3.1.1结构工艺性分析 (9)3.1.2精度及技术要求分析 (9)3.2加工方案确定 (10)3.3夹具的选择 (11)3.3.1用于轴类工件的夹具 (11)3.3.2用于盘类工件的夹具 (12)3.4刀具的选择 (12)3.4.1车刀刀片材料的选用 (12)3.4.2车刀类型及其几何参数的选用 (9)3.5切削用量的选择 (17)3.5.1数控车削加工时切削用量的确定方法 (9)3.5.2进给速度的确定 (18)4.杆螺纹轴的加工程序单 (21)参考文献 (25)1.引言机床是制造业的主要生产设备,许多产品的零件都直接或间接的经过机床加工。
11【教案】 项目十一 螺纹轴零件的编程与加工(G92)

一、螺纹加工理论知识1. 螺纹的基本加工参数2. 螺纹起点与终点轴向尺寸由于车螺纹起始时有一个加速过程,结束前有一个减速过程。
在这段距离中,螺距不可能保持均匀,因此车螺纹时,两端必须设置足够的升速进刀段(空刀导入量)δ ,和减速退刀段(空刀导出量) σ2。
01、σ2一般按下式选取:3. 螺纹分层切削深度推荐1、大径:d 公称直径)2、中径:d2= d -2×3/8H=d -0.6495P3、牙高:h=0.6495xP4、小径:d1=D-2h=d-2x (0.6495XP )δ≥2x Pδ2≥(1~1.5二、G92 螺纹切削循环指令1. 直螺纹切削循环格式:G92 X(U)_ Z(W)_ F_ ;X(U)、Z(W):螺纹终点坐标值;F_:螺纹导程R_:圆锥螺纹切削起始点与切削终点的半径差。
注:加工圆柱螺纹时,R= 0;加工圆锥螺纹时,当X向切削起始点坐标小于切削终点坐标时,R为负,反之为正。
2. 例:试编写图所示圆柱螺纹的加工程序。
O0001T0101M03S500G00X200Z200G00X35 Z104起刀位置G92X29.2 Z53F1.5螺纹切削循环X28.6 第二刀X28.2第三刀X28.04切削到尺寸G00X200Z200 回换刀点M05M30三、相关知识1. 螺纹车刀2. 螺纹的测量与检测1)大径的测量螺纹大径的公差较大,一般可用游标卡尺或千分尺测量。
2)螺距的测量螺距一般可用金属直尺测量,可以多测量几个,以减少误差。
3)中径的测量三角形螺纹的中径可用螺纹千分尺来测量。
使用方法与一般的外径千分尺相似,有两个和螺纹牙型角相同的触头,一个呈圆锥体,一个呈凹槽。
有一系列的测量触头可供不同的牙型角和螺距选用。
测量时,螺纹千分尺的俩个触头正好卡在螺纹的牙型面上,所得的读数就是该螺纹中径的实际尺寸。
4)用螺纹环规或螺纹塞规综合检查三角螺纹。
首先应对螺纹的直径、螺距、牙形和表面粗糙度进行检查,再用环规或塞规测量螺纹的尺寸精度,即通端进而止端不进,说明螺纹精度符合要求。
各种螺纹加工工艺分析
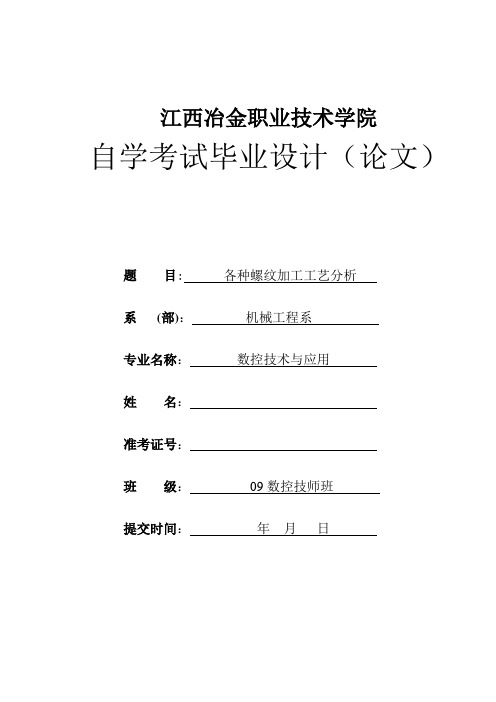
江西冶金职业技术学院自学考试毕业设计(论文)题目: 各种螺纹加工工艺分析系(部):机械工程系专业名称:数控技术与应用姓名:准考证号:班级:09数控技师班提交时间:年月日摘要理想的加工程序不仅应保证加工出符合图样的合格工件,同时应能使数控机床的功能得到合理的应用和充分的发挥。
数控机床是一种高效率的自动化设备,它的效率高于普通机床的2~3倍,所以,要充分发挥数控机床的这一特点,必须熟练掌握其性能、特点、使用操作方法,同时还必须在编程之前正确地确定加工方案.在数控机床加工过程中,由于加工对象复杂多样,特别是轮廓曲线的形状及位置千变万化,加上材料不同、批量不同等多方面因素的影响,在对具体零件制定加工方案时,应该进行具体分析和区别对待,灵活处理。
只有这样,才能使制定的加工方案合理,从而达到质量优、效率高和成本低的目的。
在对加工工艺进行认真和仔细的分析后,制定加工方案的一般原则为先粗后精,先近后远,先内后外,程序段最少,走刀路线最短,由于生产规模的差异,对于同一零件的加工方案是有所不同的,应根据具体条件,选择经济、合理的工艺方案。
关键词:数控机床加工;选择;工艺方案目录引言 (1)一、数控加工工艺 (1)1.1加工工序划分 (1)1.2.数控铣床加工路线 (1)1.3.孔加工定位路线 (2)1.4.工件的安装与夹具的选择 (3)1.5.加工路线的确定 (3)1.6.车螺纹时轴向进给距离的分析 (6)1.7.多头螺纹加工方法及程序设计 (6)1.8.精度较高的孔系加工 (7)二、普通螺纹的分析 (7)2.1.普通螺纹加工尺寸计算分析 (7)2.2.普通螺纹刀具的装刀与对刀 (7)2.3.普通螺纹的编程加工 (7)2.4.普通螺纹的检测 (8)三、多头螺纹的加工 (8)3.1.多头螺纹的基本特性 (8)3.2.多头螺纹的加工方法 (8)3.3.实例分析 (9)3.4.多头螺纹的程序设计 (9)3.5.多头螺纹加工的控制因素 (10)四、轴类零件的加工 (10)4.1.零件图工艺分析 (10)4.2.选择设备 (11)4.3.确定零件的定位基准和装和装夹方式 (11)4.4.确定加工顺序及进给路线 (11)4.5.刀具选择 (11)4.6.切削用量选择 (12)4.7.零件精加工工序 (12)结论 (14)致谢 (15)参考文献 (16)附录 (17)江西冶金职业技术学院09级自考毕业设计(论文)各种螺纹加工工艺分析引言从20世纪中叶数控技术出现以来,数控机床给机械制造业带来了革命性的变化。
复杂螺纹轴类零件的加工工艺分析

成, 内螺纹 通过 钻孔 、 粗镗、 精镗 来完成 。 3 . 对 零件 l 和 零件 2的圆柱 面 配合 ,
3 . 两个零 件分别 有装 配形式 , 两 配合 装配尺 寸和行 为公差 的要 求 。 4 . 网所爪 为舣 合零件 , 包括 件 1 和
1 . 装配 后零 件 1 的 E处和 零 件 2的
还 应保 证 其形状 和位 置精 度 的要 求 。文
圆外轮廓 、 一 个应通过 粗 、 精
车和切槽 来 完成 , 内轮 廓应 通过 钻孔 、 粗
3 . 有 端配 合要求 尺寸 1 2 6 9 1 - 0 . 0 9 。
复杂螺 纹轴类零件 的加工工艺分析
■ 张永 松
摘要: 轴 类零件 是机械 加 工 中经 常遇 到的典型 零件之 一 , 它主要 用来 支承传 动零部件 , 传递 扭矩 和承受 载荷 。一般 由外 匮 l 柱 面、 断
面, 台阶 倒角 沟槽 螺纹 和 中心孔等 要素 构成 。文 章通 过复 杂轴 类零件 的加 工工 艺分析 , 巧 用 了辅 助顶 尖 完成对 该类零 件 的加
外轮 廓时 应分 别使 用粗 精 刀, ; 来 进行 粗
零件 1 零件 2 精加 T。
作者 简介 : 张永松 , 南京交通技 师 学院 。
№
耵。
工艺 分 析
1 . 零件 1 的 主要 加
工部 分包括 四段 圆柱外
径、 一段 圆锥 外径 、 两段 相切 的外 圆弧 、一段椭 配 合件装 配图
反 映轴 类零 件 的加 丁规 律 和共性 。 而轴
类 零件 的精 度要 求 较高 ,所 以在 车削 时 除l r 要 保 让尺 寸 精 度和 表 而 粗糙 度 外 ,
螺纹的加工工艺
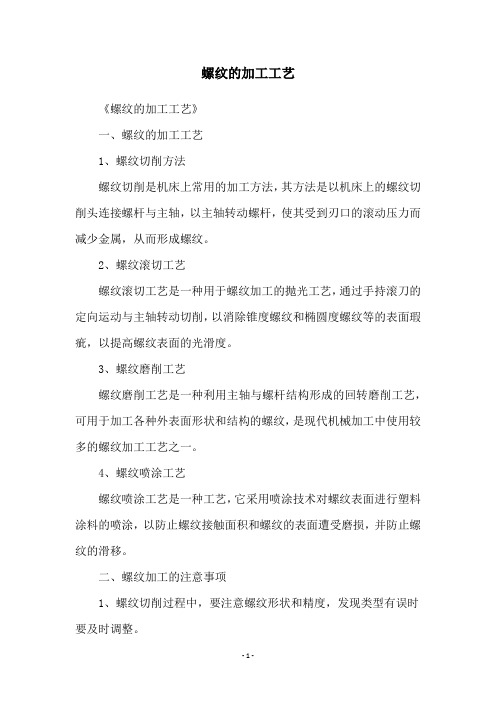
螺纹的加工工艺
《螺纹的加工工艺》
一、螺纹的加工工艺
1、螺纹切削方法
螺纹切削是机床上常用的加工方法,其方法是以机床上的螺纹切削头连接螺杆与主轴,以主轴转动螺杆,使其受到刃口的滚动压力而减少金属,从而形成螺纹。
2、螺纹滚切工艺
螺纹滚切工艺是一种用于螺纹加工的抛光工艺,通过手持滚刀的定向运动与主轴转动切削,以消除锥度螺纹和椭圆度螺纹等的表面瑕疵,以提高螺纹表面的光滑度。
3、螺纹磨削工艺
螺纹磨削工艺是一种利用主轴与螺杆结构形成的回转磨削工艺,可用于加工各种外表面形状和结构的螺纹,是现代机械加工中使用较多的螺纹加工工艺之一。
4、螺纹喷涂工艺
螺纹喷涂工艺是一种工艺,它采用喷涂技术对螺纹表面进行塑料涂料的喷涂,以防止螺纹接触面积和螺纹的表面遭受磨损,并防止螺纹的滑移。
二、螺纹加工的注意事项
1、螺纹切削过程中,要注意螺纹形状和精度,发现类型有误时要及时调整。
2、在执行螺纹滚切工艺时,需要提高滚刀的质量,防止因滚刀质量不佳而影响螺纹的表面质量。
3、在采用螺纹磨削工艺加工螺纹时,宜使用多种磨具,以达到充分的磨削效果。
4、在喷涂螺纹前,要先将螺纹表面进行清洗,使涂料能够附着在螺纹表面,以防止涂料脱落。
车工工艺螺纹加工【共37张PPT】

【2】车内螺纹时,孔径
基准直径 基准平面
基准距离
车螺纹和蜗杆
▪ 【3】标记举例 ▪ ¾“圆锥内螺纹 Rc ¾“(19.05mm) ▪ ¾“圆柱内螺纹 Rp¾“(19.05mm) ▪ ¾“圆锥外螺纹 R¾“(19.05mm) ▪ 锥锥配合
Rc ¾“(19.05mm)/ R¾“(19.05mm) 柱锥配合
【3】螺纹牙型--在通过螺纹轴线的剖面内,螺纹的轮廓形状。 【按线数分】--单线和多线 判定方法:P工XN工= P丝XN丝 车螺纹和蜗杆-螺纹车刀
车螺纹和蜗杆-螺纹车刀
【3】螺纹牙型--在通过螺纹轴线的剖面内,螺纹的轮廓形状。
圆锥内螺纹与圆锥外螺纹的配合。
外螺纹小径--外螺纹的底径。
车螺纹和蜗杆-三角螺纹测量
▪ 【8】螺纹升角ψ--在中径圆柱上,螺旋 线切线与垂直于螺纹轴线的平面之间的夹 角。
▪ tan ψ=P/πd2 ▪ P--螺距 ▪ d2--中径
车螺纹和蜗杆
牙侧
φ
牙底
牙顶
车螺纹和蜗杆
▪ 二、三角螺纹的种类和尺寸计算
▪ 三角螺纹分为 【1】普通螺纹
▪
【2】英制螺纹
▪
【3】管螺纹
▪ 1、普通螺纹特点
▪ 1、单项测量 ▪ 【1】测螺距--钢直尺、螺距规 ▪ 【2】测大、小径--游标卡尺、千分尺 ▪ 【3】测中径--螺纹千分尺、三针测量
(三角螺纹一般不测中径。 ▪ 2、综合测量 ▪ 【1】螺纹塞规--测内螺纹 ▪ 【2】螺纹环规--测外螺纹
车螺纹和蜗杆
左旋 右旋
车螺纹和蜗杆
▪ 【3】螺纹牙型--在通过螺纹轴线的剖面内,螺纹 的轮廓形状。
阶梯螺纹轴的数控加工与工艺

阶梯螺纹轴的数控加工与工艺第1章阶梯螺纹轴的工艺分析1.1阶梯螺纹轴的零件图图1.1阶梯螺纹轴零件图1.1分析图样可知:该零件图为轴类回转体,所要加工的内容主要有圆柱面、半圆球、锥面、螺纹、螺纹退刀槽、内孔等组成,该零件的表面粗糙度、尺寸精度等要求较高,需合理选用切削用量和刀具在加工中予以保证,该零件关键工序是M18的螺纹、Ф18mm至Ф34mm的锥度、内孔及SR6半圆球。
该零件分两次装夹,第一次夹住工件右端车左端,第二次夹住已加工Ф36mm 表面,加工零件右端,加工过程大致应为车两端面、钻中心孔、钻孔、车左端外圆及内孔、平总长、车右端外圆。
1.2毛坯的种类(1)铸件:适用于形状复杂的零件毛坯。
其方法主要是铸造。
(2)锻件:适用于强度要求高、形状比较简单的零件毛坯。
(3)型材:型材有热轧和冷拉两种。
热轧适用于尺寸较大精度较低的毛坯;冷拉适用于尺寸较小、精度较高的毛坯。
(4)焊接件:将型材或钢板等焊接成所需要的零件结构,简单方便,生产周期短,但需要经时效处理后才能进行机械加工。
1.2.1毛坯的选择原则在选择毛坯时应考虑下列因素:(1)材料和机械加工性能。
材料能否在加工设备上顺利加工决定其加工的难易程度,而在切削过程中会产生大量切削热致使工件的性能和组织发生改变。
(2)零件的结构形状和外形尺寸。
选择零件的毛坯时其大小,形状尽可能与零件图相近。
(3)生产纲领大小。
当零件产量较大时,应选择精度和生产率较高的毛坯制造方法。
(4)生产条件。
选择毛坯时,要考虑到毛坯的制造水平,设备加工精度,员工的技术水平经济性等。
(5)充分考虑利用新技术、新工艺、新材料的可能。
为节约材料和能源,发展趋势是少切屑、无切屑毛坯制造。
该零件材料为45钢、属于中小传动轴,应选用Ф45mm的圆钢做毛坯。
1.3表面加工方法的确定任何零件都是由一些简单表面如外圆、内孔、平面和成形表面等进行不同组合而形成的,根据这些表面所要求的精度和表面粗糙度以及零件的结构特点,将每一表面的加工方案确定下来,也就确定了零件的全部加工内容。
B类宏程序加工梯形螺纹的方法和技巧

OCCUPATION2012 03166专业开发D evolopmentB类宏程序加工梯形螺纹的方法和技巧文/陈未峰一、B类宏程序在数控编程中的重要性在数控车削加工中,普通轴类零件的轮廓形状都可以利用G功能指令来完成加工。
但异形曲线和大螺距螺纹大大增加了零件的加工难度,G指令编程不好实现这类零件的有效加工。
例如梯形螺纹较之三角螺纹,螺距和牙型都大,而且精度高,牙型两侧表面粗糙度值较小,这样梯形螺纹车削时,吃刀深、走刀快、切削余量大、切削抗力大,导致梯形螺纹的车削加工难度较大。
与宏程序相比,一般程序的程序字为常量,一个程序只能描述一个几何形状,所以缺乏灵活性和适用性。
而用户宏程序本体中可以使用变量进行编程,还可以用宏指令对这些变量进行赋值、运算等处理,从而可以使用宏程序执行一些有规律变化的动作。
与A类宏程序相似,B类宏程序的变量也是由“#”符号和1至3位数字构成;但B类宏程序的数学运算可直接用数学符号完成,而不需采用G65语句,有效地提高了零件的编程灵活性和加工效率。
因此,使用B类宏程序加工有梯形螺纹的零件,对提高数控编程的效率是非常重要的。
二、球头梯形螺纹零件加工工艺分析1.球头梯形螺纹零件分析如图1所示,球头梯形螺纹轴由球面、曲面、退刀槽和梯形螺纹构成,其螺距为6mm,加工精度要求较高,球面和曲面加工简单。
在FANUC 0i数控系统机床上加工时,利用G73复合固定循环就可以进行有效加工,但由于梯形螺纹螺距较大和加工精度较高,致使梯形螺纹车削时,吃刀深、切削余量大、切削抗力大,车削加工难度较大。
利用普通G功能指令无法高质量、有效地完成该零件的加工,需利用B类宏程序进行切削加工。
2.计算相关尺寸,并查表确定公差该零件上梯形外螺纹为Tr36×6,螺距为6mm,公制梯形螺纹的牙型角为30°,梯形螺纹的牙型如图2所示,各基本尺寸计算结果如下:大径中径d 2=d -0.5P =36-3=33,查表确定其公差,故;牙高h 3=0.5P+ a c =3.5;小径d 3=d-2 h 3=29,查表确定其公差,故;牙顶宽f=0.366P=2.196;牙底宽W=0.366P-0.536a c =2.196-0.268=1.928螺纹中经三针测量法测量,如图3所示,用3.1mm的测量棒测量中径,则测量尺寸为M=d 2+4.864d D -1.866P=32.88,根据中径公差确定公差,则(其中d D 表示测量用量针的直径,P表示螺距)。
任务三螺纹轴的加工工艺与程序编制
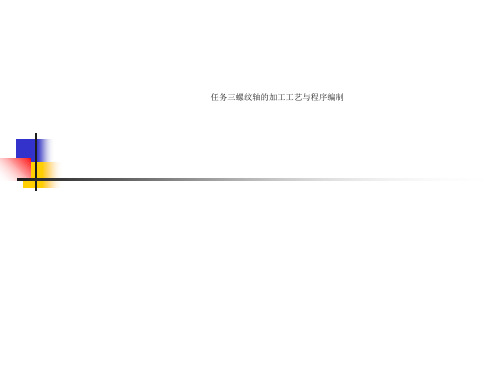
如果X(U)及△i省略,可用相应的正负符号指定刀具退刀量 f:进给量
G75走刀路线
G75应用举例
例:加工如图2.3.9所示四处3mm宽外沟 N3槽0 G00 X32 Z-13;
N40 G75 R1; R:退刀量1mm
G92应用举例
如图所示用G92加工 M20×1.5圆锥螺纹,分四刀 完成。
…… N50G00X28.Z2.; N60G92X19.2Z-22.R-3.F1.5; N70X18.6; N80X18.2; N90X18.04; ……
双头螺纹的加工举例
例4.用G92加工M24×4/2圆柱螺 纹,假设每条螺纹分两刀完成。
半径差。 k:螺纹牙型的高度,用半径值指定,单位为μm, Δd:第一次的切深量,X轴方向的半径值,单位为μm L:螺纹导程
G76 螺纹切削复合循环轨迹
由图可知,其以 斜进法方法分层 切削螺纹,因此 更适合加工螺距 较大、牙型较深 的螺纹。
G76应用举例
用G76加工如图所示的螺纹 …… N230 G00 X 34 Z5; (刀具定位到循环起点) G76 P01060 Q200 R100; (螺纹车削循环,最小切深0.2mm,精加工余
Z
XZ
W
4R
3F 1R
G32
Z
指令G92使用注意事项
① 在螺纹切削期间,按下进给保持时,刀具将在完成 一个螺纹切削循环后再进入进给保持状态。
② 如果在单段方式下执行 G92 循环,则每执行一次循 环必须按四次循环起动按钮。
③ G92 指令是模态指令,当 Z 轴移动量没有变化时, 只需对 X 轴指定移动指令即可重复固定循环。
螺纹及丝杆加工工艺

螺纹及丝杆加工工艺引言螺纹和丝杆作为广泛应用于机械设备中的重要部件,其加工工艺对产品质量和性能具有重要影响。
螺纹加工是一种复杂且精密的加工工艺,要求高精度和良好的表面质量。
本文将介绍螺纹及丝杆加工的工艺流程和常用的加工方法。
工艺流程螺纹及丝杆加工的工艺流程通常包括以下几个步骤:1.材料准备:选择适当的材料进行加工,通常使用具有良好加工性能和耐磨性的材料。
2.车削加工:螺纹及丝杆的加工通常以车削加工为主要方法。
车削加工可以分为粗车和精车两个阶段。
粗车主要是为了去除材料多余的部分,获得近似尺寸的基准圆柱体。
精车则是在基准圆柱体上进行细致修整,以获得准确的螺纹形状和表面质量。
3.螺纹刀具选择:根据加工要求选择适当的螺纹刀具,常见的有螺纹车刀、螺纹铣刀、螺纹切割刀等。
选择刀具时要考虑加工材料的硬度、螺纹尺寸和表面质量要求等因素。
4.加工参数设置:根据加工材料和螺纹尺寸等因素,设置合适的车削速度、进给速度和切削深度等加工参数。
合理的加工参数可以提高生产效率和加工质量。
5.螺纹切削:根据螺纹图样,使用选定的螺纹刀具进行切削加工。
螺纹刀具要正确安装,确保刀具切削刃与工件螺纹轴线的垂直程度,以获得正确的螺纹形状和精度。
6.表面处理:螺纹及丝杆的表面可能会出现一些不良缺陷,如划伤、磨痕等。
为了提高表面质量,通常会进行一些表面处理,如打磨、抛光等。
7.检测和质量控制:对加工后的螺纹及丝杆进行检测,包括测量螺纹尺寸、检查螺纹形状和表面质量等。
必要时,还需进行质量控制,以确保产品符合设计要求。
常用的加工方法冷滚压加工法冷滚压加工是一种常见且有效的螺纹加工方法。
该方法利用特殊的滚齿刀具,将刀具的螺纹牙形与工件螺纹相契合,通过滚动切削来获得精确的螺纹形状。
冷滚压加工法具有以下优点:•高效:较高的生产效率,可一次加工多个螺纹。
•高精度:获得较高的螺纹精度和表面质量。
•节约材料:由于冷滚压不需要切削过多的材料,可以节约原材料。
- 1、下载文档前请自行甄别文档内容的完整性,平台不提供额外的编辑、内容补充、找答案等附加服务。
- 2、"仅部分预览"的文档,不可在线预览部分如存在完整性等问题,可反馈申请退款(可完整预览的文档不适用该条件!)。
- 3、如文档侵犯您的权益,请联系客服反馈,我们会尽快为您处理(人工客服工作时间:9:00-18:30)。
螺纹轴加工与工艺第一章螺纹轴简述工艺分析与设计1.1 螺纹的简述在轴类零件的加工表面,车出螺旋线形状的相等截面和连续凸起部分叫螺纹,按照工件的形状可分为圆柱螺纹和圆锥螺纹;按其错在工件的位置可分为外螺纹、内螺纹,按照截面压型的形状可分为三角形螺纹、矩形螺纹、梯形螺纹、及其他特殊型螺纹,三角形螺纹主要用于两物体的连接、紧固。
按照螺旋线的分类可分为左旋螺纹和右旋螺纹,加工方向的不同所得到的螺旋线方向不同,按螺旋线的数量可分为单线螺纹、双线螺纹及多线螺纹。
按其使用的场合这些种类功能都不同。
1.2数控加工工艺分析和设计数控加工工艺分析的规程是:充分考虑采取各种措施保证产品质量,以最低的成本保证要求的生产率。
在制定工艺规程时,应尽力做到技术上先进,经济上合理并具有良好的生产条件。
制定工艺规程的工作主要包括准备工作、工艺过程的拟定和工序设计三个阶段,其内容步骤如下:(1)分析零件图和产品装配图;(2)选择毛胚;(3)选择定位基准;(4)拟定工艺路线;(5)确定加工余量和工序尺寸;(6)确定切削用量和时间;(7)确定各工序的设备、刀具夹具量具及辅助工具;(8)确定工序的技术要求及检验方法;(9)确定所有准备的合理性;在准备阶段工作的基础上,拟定以工序为单位的加工工艺过程再对每个工序确定详细内容,将所有步骤反复检查修改。
最后对制定的工艺规程进行综合分析与评价,看能否满足所设计的要求。
本设计零件有端面、倒角、圆弧、锥度、槽、螺纹。
该类零件适合数控车床加工,选择华中系列的数控机床。
加工工艺路线的拟定是制造工艺过程的总体布局,其主要任务是选择各个表面的加工方法,确定各个表面的加工顺序以及整个工艺过程中工序的数目,各个工序内容拟定过程中应首先确定各次加工定位基准和装夹方法。
然后再将所需的辅助、任务处理等工序插入相应的顺序中,得到工件的加工工艺路线。
1.2.1工艺基准在零件加工、测量和装配过程中所使用的基准,称为工艺基准。
根据用途的不同可以分为工序基准、定位基准、测量基准和装配基准。
(1)工序基准。
在工序图上,用以标注本工序被加工表面加工后的尺寸、形状、位置的基准称为工序基准。
(2)定位基准。
是指工件在加工过程中,用于确定工件在机床或夹具上的位置的基准。
(3)测量基准。
是指检验工件时,用于测量已加工表面的尺寸及各表面之间位置精度的基准(4)装配基准。
是指机器装配时用以确定零件或部件在机器中正确位置的基准。
1.3华中数控车床的指令功能概述G指令根据功能的不同分成若干组,其中00组的G功能称作非模态G功能,指令只在所规定的程序段中有效,程序段结束时被注销。
其余组的称模态G功能,这些工能一旦被执行,则一直有效,知道被同一组G工能注销为止。
模态G功能组中包含一个默认G 功能(上表中有*记号的G功能),通电时将初始化该功能。
每有共同地址符的不同组G指令代码可以放在同一程序段中,而且与顺序无关。
例如,G90、G17可与G01放在同一程序段。
辅助功能也称M功能,主要用于控制零件程序的走向,以及机床各种辅助功能的开关动作,如主轴转动、停止切削液的开关等。
M代码与G代码一样,也有非模态M功能和模态功能M模态两种形式。
非模态M 功能(当段有效代码),只在书写了改代码的程序段中有效;模态M功能(续效代码),一组可相互注销的M功能,这些功能在被同一组的另一个功能注销前一直有效。
模态M功能组中包含一个默认功能(上表中带有*记号的M功能),系统通电时将初始化该功能。
第二章螺纹轴车削加工工艺2.1螺纹加工方法及工艺2.1.1车削螺纹的方法车削三角螺纹主要方法有直进法、左右车削法、斜进法。
(1)直进发:车削时只朝X方向进给,在几个行程后,把螺纹加工到所需尺寸和表面粗糙度。
适合于高速切削螺距P<3mm的螺纹、脆性材料的螺纹和硬质合金高速车削的螺纹。
(2)左右车削法:车螺纹时,除了朝X方向进行车削外,同时还进行了Z方向左右的微量进给,经过几次车削后,把螺纹加工到尺寸。
适合于螺距P≥3mm螺纹的精车,刚度较低的粗、精车。
(3)斜进法:当螺距较大螺纹槽较深且切削余量较大时,粗车为了加工方便,除了朝X方向进行切削外,同时还进行了Z方向一个方向的微量进给,经过几次车削后,把螺纹加工至尺寸。
适用于螺距P≥3mm螺纹与塑性材料螺纹的粗车。
2.1.2车削三角螺纹切削用量的选择(1)主轴转速用高速钢车刀车削塑性材料的螺纹时,一般选择12~150r/min的低速;用硬质合金车刀车削铸铁等脆性材料的螺纹时,一般选择360r/min的中速;用硬质合金车刀车削塑性材料的螺纹时,一般选择480r/min左右的中速;螺纹直径小、螺距小(P<2mm)时,宜选用较高的转速;螺纹直径大、螺距大时,宜选用较低的转速。
(2)被吃刀量因为螺纹牙型较深,不能一次车削完成,所以在螺纹加工过程中,可分数次进给,直至把螺纹车削到要求的深度。
实际加工螺纹时,由于车刀刀尖半径的影响,螺纹的实际切深有变化。
螺纹车到可在牙底最小削平高度H/8出削平或倒圆角。
则螺纹实际压型高度可按以下方式计算:压型高度:h=2-H/8=0.6595P式中H─螺纹原始三角形高度,H=0.866Pmm。
P─螺距,mm。
装夹外螺纹车刀时,应使刀尖对准工件中心,同时使刀刃夹角中线垂直于工件轴线,装刀时可用样板来对刀。
螺纹车削需要多次切削,每次切削逐渐加深否则刀具寿命也比预期短很多。
为实现每次切削的目的,机床主轴恒定转速旋转,且必须与进给速度保持同步,保证每次切削深度都在螺纹圆柱的同一位置上,最后一次走刀加工出适当的螺纹尺寸、形状、表面质量和公差,并得到合格螺纹。
2.2G32 G82螺纹切削指令运用2.1.1螺纹指令G32【格式】G32X(U) Z(W) R E P F【说明】(1) X、Z:为绝对编程时,有效螺纹终点在工件坐标系中的坐标值。
(2) U、W:为增量编程时,有效螺纹终点相对于螺纹切削起点的坐标增量。
(3) F:螺纹导程,即主轴每转一圈,刀具相对于工件的进给值。
(4) R、E:螺纹切削的退尾量,R表示Z向退尾量;E为X向退尾量,R、E在绝对或增量编程时都是以增量方式指定,R、E前面的符号为正表示沿Z、X正向回退,根据螺纹标准,R一般取2倍的螺距,E去螺纹的牙型高。
(5) P:主轴基准脉冲处距离螺纹切削起始点的主轴转角。
(6)使用G32指令能加工圆柱螺纹、锥螺纹和端面螺纹。
2.1.2螺纹指令G82【格式】G82X(U) Z(W) R E C P F【说明】(1) X、Z:绝对编程时,为螺纹终点C在工件坐标系下的坐标。
(2) U、W:增量编程时,为螺纹终点C相对于循环起点A的坐标增量。
(3) R、E:螺纹车削的退尾量,R、E均为向量,R为Z向回退量,E为X 向回退量。
R、E可以省略,表示不用回退功能。
(4) C:螺纹线数,为0或1时车削单线螺纹。
(5) P:单线螺纹车削时,为主轴基准脉冲处距离车削起始点的主轴转角(缺省值为0);多线螺纹车削时,为相邻螺纹线的车削起始点之间对应的主轴转角。
(6) F:螺纹导程。
第三章轴类零件(螺纹轴)的加工工艺分析3.1 零件工艺图分析轴类零件图如图a所示,毛坯为,材料:#45棒材ø50×85mm。
图3.1(1)零件结构分析如上零件图有圆柱面、圆锥面、圆弧、槽、螺纹、内孔等构成,其中有些尺寸标注精度要求较高。
加工时因注意尺寸偏差,标注要求轮廓清晰完整,毛坯材料为45号钢,毛坯尺寸为ø50mmX85mm。
(2)零件技术要求分析零件的技术要求一般包括各加工表面的加工精度和表面质量,热处理要求,动平衡、去磁等其它技术要求。
切削加工对零件结构工艺性总的要求是使零件安装、加工和测量方便,提高切削效率,减少加工量和易于保证加工质量。
(3)加工难点及处理方案分析上图可知,此零件对平面、粗糙度要求较高。
为提高零件加工尺寸精度,应对图上所给出几个要求较高的地方编程时采用中间值,轮廓线上有圆弧,因此在加工时应该进行刀具半径补偿,以保证轮廓线的准确性。
各个外轮廓表面的粗糙度可采用粗加工然后精加工方案。
以保证尺寸、形状、精度和表面粗糙度。
3.1.2 确定工件的定位与装夹工件的装夹包含两方面内容:一是定位,使工件在机床上相对于刀具占有正确的加工位置,保证加工的精度。
二是夹紧,将定位后的工件固定,使工件定位基准面与夹具上的定位元件的定位表面保持接触,在加工过程中不发生位置变化,保证工件的定位效果。
1工件的装夹方法(1)找正装夹法:找正装夹法是按工件的有关表面或专门划出的线痕作为找正依据,用划针或千分表,逐个地找正工件相对于刀具及机床的位置,然后把工件夹紧。
这种安装方法简单,不需专门设备,但精度不高,生产率低,多用于单件小批量生产。
(2)夹具装夹法:夹具装夹法是靠工件的定位基准面与夹具上定位元件的定位表面相接触,实现工件的迅速定位,并使其夹紧。
这种方法可使同一批工件在夹具中占据一致的加工位置,保证同一批工件的精度稳定,容易获得较高的加工精度和生产率,广泛用于中批以上的生产类型。
2定位中的几种情况(1)完全定位。
工件的留个自由度全部被限制的定位,称为完全定位。
(2)不完全定位。
根据工件的加工要求,并不需要限制工件的全部自由度,这要的定位,称为不完全定位。
(3)欠定位。
根据工件的加工要求,应该限制的自由度没有完全被限制的定位,称为欠定位。
(4)过定位。
同一个自由度被几个支承点重复限制的情况,称为过定位。
3.1.3 切削加工顺序的安排(1)先粗后精先安排粗加工,中间安排半精加工,最后安排修整和精加工。
(2)先主后次先安排零件和工作表面等主要表面的加工,后安排如,紧固螺纹孔等表面加工。
由于次要加工工作量小,又长与主要表面有位置精度要求,所以一般要放在主要表面的半精加工之后,精加工之前进行。
(3)先面后孔对于箱体、支架、连杆、底座等零件,先加工用作定位的平面和孔的端面,然后在加工孔。
这样可以使工件定位夹紧稳定可靠,及于保证孔与平面的位置精度,减小刀具的磨损,同时也给孔加工带来方便。
(4)基面先行用作精基准的表面,首先要加工出来。
所以,第一道工序一般是进行定位面的粗加工和半精加工(有时包括精加工),然后在以精基准面定位加工其他表面。
例如,轴类零件顶尖孔的加工。
综上所诉:此零件的的加工顺序如下:1.先进行左端部分的加工,左端部分先采用G71加工外圆轮廓。
(1)加工左端外圆轮廓仿真加工如下。
图3.22再进行右端部分的加工,右端部分先采用G71加工外圆轮廓。
(1)加工右端外圆轮廓仿真加工如下。
图 3.23切槽和螺纹的仿真加工如下。
(1)采用G81切槽G82切螺纹。
图3.33.4 切削用量的确定确定切削用量的因素有:生产率、加工质量(主要是表面粗糙度)、刀具耐用度、机床功率、切削引起的工艺系统的系统弹性变形和振动等。