螺纹轴的加工
螺纹加工方法详细讲解
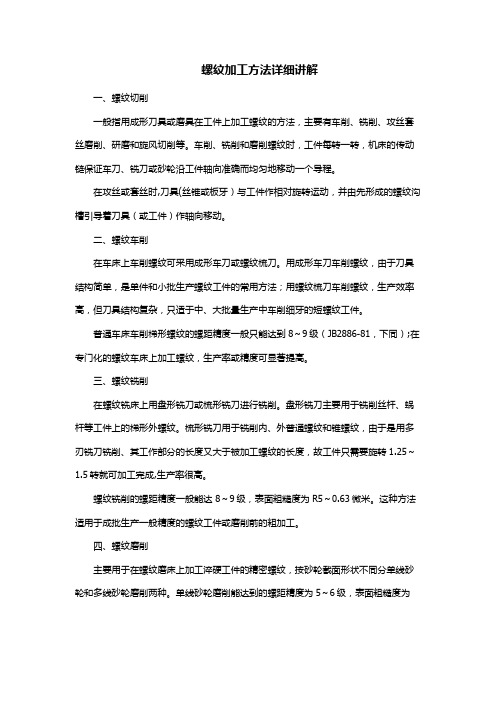
螺纹加工方法详细讲解一、螺纹切削一般指用成形刀具或磨具在工件上加工螺纹的方法,主要有车削、铣削、攻丝套丝磨削、研磨和旋风切削等。
车削、铣削和磨削螺纹时,工件每转一转,机床的传动链保证车刀、铣刀或砂轮沿工件轴向准确而均匀地移动一个导程。
在攻丝或套丝时,刀具(丝锥或板牙)与工件作相对旋转运动,并由先形成的螺纹沟槽引导着刀具(或工件)作轴向移动。
二、螺纹车削在车床上车削螺纹可采用成形车刀或螺纹梳刀。
用成形车刀车削螺纹,由于刀具结构简单,是单件和小批生产螺纹工件的常用方法;用螺纹梳刀车削螺纹,生产效率高,但刀具结构复杂,只适于中、大批量生产中车削细牙的短螺纹工件。
普通车床车削梯形螺纹的螺距精度一般只能达到8~9级(JB2886-81,下同);在专门化的螺纹车床上加工螺纹,生产率或精度可显著提高。
三、螺纹铣削在螺纹铣床上用盘形铣刀或梳形铣刀进行铣削。
盘形铣刀主要用于铣削丝杆、蜗杆等工件上的梯形外螺纹。
梳形铣刀用于铣削内、外普通螺纹和锥螺纹,由于是用多刃铣刀铣削、其工作部分的长度又大于被加工螺纹的长度,故工件只需要旋转1.25~1.5转就可加工完成,生产率很高。
螺纹铣削的螺距精度一般能达 8~9级,表面粗糙度为R5~0.63微米。
这种方法适用于成批生产一般精度的螺纹工件或磨削前的粗加工。
四、螺纹磨削主要用于在螺纹磨床上加工淬硬工件的精密螺纹,按砂轮截面形状不同分单线砂轮和多线砂轮磨削两种。
单线砂轮磨削能达到的螺距精度为5~6级,表面粗糙度为R1.25~0.08微米,砂轮修整较方便。
这种方法适于磨削精密丝杠、螺纹量规、蜗杆、小批量的螺纹工件和铲磨精密滚刀。
多线砂轮磨削又分纵磨法和切入磨法两种。
纵磨法的砂轮宽度小于被磨螺纹长度,砂轮纵向移动一次或数次行程即可把螺纹磨到最后尺寸。
切入磨法的砂轮宽度大于被磨螺纹长度,砂轮径向切入工件表面,工件约转1.25转就可磨好,生产率较高,但精度稍低,砂轮修整比较复杂。
切入磨法适于铲磨批量较大的丝锥和磨削某些紧固用的螺纹。
螺纹轴加工与工艺

螺纹轴加工与工艺第一章螺纹轴简述工艺分析与设计1.1 螺纹的简述在轴类零件的加工表面,车出螺旋线形状的相等截面和连续凸起部分叫螺纹,按照工件的形状可分为圆柱螺纹和圆锥螺纹;按其错在工件的位置可分为外螺纹、内螺纹,按照截面压型的形状可分为三角形螺纹、矩形螺纹、梯形螺纹、及其他特殊型螺纹,三角形螺纹主要用于两物体的连接、紧固。
按照螺旋线的分类可分为左旋螺纹和右旋螺纹,加工方向的不同所得到的螺旋线方向不同,按螺旋线的数量可分为单线螺纹、双线螺纹及多线螺纹。
按其使用的场合这些种类功能都不同。
1.2数控加工工艺分析和设计数控加工工艺分析的规程是:充分考虑采取各种措施保证产品质量,以最低的成本保证要求的生产率。
在制定工艺规程时,应尽力做到技术上先进,经济上合理并具有良好的生产条件。
制定工艺规程的工作主要包括准备工作、工艺过程的拟定和工序设计三个阶段,其内容步骤如下:(1)分析零件图和产品装配图;(2)选择毛胚;(3)选择定位基准;(4)拟定工艺路线;(5)确定加工余量和工序尺寸;(6)确定切削用量和时间;(7)确定各工序的设备、刀具夹具量具及辅助工具;(8)确定工序的技术要求及检验方法;(9)确定所有准备的合理性;在准备阶段工作的基础上,拟定以工序为单位的加工工艺过程再对每个工序确定详细内容,将所有步骤反复检查修改。
最后对制定的工艺规程进行综合分析与评价,看能否满足所设计的要求。
本设计零件有端面、倒角、圆弧、锥度、槽、螺纹。
该类零件适合数控车床加工,选择华中系列的数控机床。
加工工艺路线的拟定是制造工艺过程的总体布局,其主要任务是选择各个表面的加工方法,确定各个表面的加工顺序以及整个工艺过程中工序的数目,各个工序内容拟定过程中应首先确定各次加工定位基准和装夹方法。
然后再将所需的辅助、任务处理等工序插入相应的顺序中,得到工件的加工工艺路线。
1.2.1工艺基准在零件加工、测量和装配过程中所使用的基准,称为工艺基准。
数控车工教案《螺纹轴的加工》(修正)

教案说明本教案内容是《数控车工》(高级)FANUC系统B类宏程序学习后进行的一次综合训练,通过螺纹轴的加工,使学生掌握B类宏程序的应用,能根据图纸要求编制合理的加工工艺,同时进一步提高学生加工螺纹的技能水平及在加工中如何控制工件的尺寸精度及表面质量。
整个教学过程分为两大部分,第一部分为专业理论知识,通过教师展示实习任务,逐步引导学生分析图形,思考加工工艺,填写工艺卡片,编制程序,教师对比点评及模拟加工等多种教学方法,活跃了课堂气氛,激发了学生学习的积极性,为后面的实作训练打下良好的理论基础。
第二部分为专业实作训练,在整个训练中,教师将理论知识转化为现场操作演示,并由学生模仿加工,培养了学生的观察能力和动手能力,再通过学生分组操作练习,教师巡回检查指导,提高了学生的操作水平;最后引导学生对加工工件进行自评、互评,提高了学生分析问题和解决问题的能力,激发了学生学习的兴趣,使学生体验到理实一体化课程的乐趣。
本节教学内容力求充分体现教学内容的基础性、教学方法的灵活性、教师的“做中教”和学生的“做中学”,有机地结合在一起,不仅达到了任务目标,也突破了教学重难点。
在课堂最后,通过教师的综合点评,学生的总结反思、课后作业,进一步巩固了所学知识,并为下次的学习打下良好的基础!《数控车工》一体化教案教案首页教学过程的设计的重视。
三、讲授新课:实习任务展示:《螺纹轴》(项目引领法、提问法、讲授法等)1、实习任务分析:(10)(1)在这个图形中,包括了椭圆,台阶轴、锥度、螺纹退刀槽及螺纹的加工等实习内容,难点在于椭圆编程及螺纹的加工,涉及计算的有椭圆公式的变换、锥度的计算以及螺纹相关尺寸的确定。
PPT本习内容。
提问:1看的不难?2任了级的内容?最点评总结,并正学时表扬。
级进行加工,教师提问:的外圆,第二次掉头夹持工件椭圆的标准方程为:x2/a2+y2/b2=1(其中a和b分别是椭圆的长半根据上图由椭圆原点向编程原点进行转换: x=2*x z=z-20锥度计算:锥度公式:锥度=(d 大—d 小)/L d 大=40螺纹尺寸:车螺纹的导入距离L1≈2*P=3车螺纹的导出距离L2≈2车螺纹前的外圆直径d 杆≈d-0.1P=29.85 螺纹的小径d1≈d-1.2P=28.2mm通过计算,得出了我们需要的数据,接下来就将这些数据正确地用在我们的编程中吧。
数控加工工艺及编程 项目3螺纹轴加工工具刀具选择

螺纹轴加工刀具和工具选择一、车刀选择外圆车刀选择原则与短轴加工时的外圆车刀相同用90度外圆车刀,这里就不在赘述。
分析该螺纹零件。
螺纹为M12的三角外螺纹,我选择三角形外螺纹车刀,刀尖角60度。
割槽刀选用3mm宽的外割槽刀。
二、螺纹车刀特点螺纹车刀是成形刀具,其切削部分的形状应和螺纹牙型轴向剖面的形状相符合,车刀的刀尖角应该等于牙型角。
三角形螺纹的牙型角是60°,理论上三角形螺纹车刀的刀尖角也应该是60°。
但实际生产中,只有高速工具钢三角形螺纹车刀的刀尖角是60°,硬质合金三角形螺纹车刀的刀尖角则应为59°30’左右。
这是因为用硬质合金车刀高速切削时,工件材料受到较大的挤压力,会使牙型角增大约0.5°。
三、螺纹车刀种类1.高速工具钢三角形螺纹车刀(图1)的前角一般取5°~15°,粗车刀的纵向前角一般取15°左右,精车刀的前角一般取6°~10°。
2.硬质合金三角形螺纹车刀(图2)的前角和纵向前角一般都取0°,为了增加切削刃的强度,在车削较高硬度的材料时,两切削刃上可磨出负倒棱。
a)粗车到b)精车刀图1高速钢三角螺纹车刀c)焊接式d)机加式图2 硬质合金三角螺纹车刀三、刀具的刃磨三角螺纹车刀刃磨要求:①根据粗、精车的要求,刃磨出合理的前、后角。
粗车刀前角大、后角小,精车刀则相反;②车刀的左右刀刃必须是直线,无崩刃;③刀头不歪斜,牙型半角相等;④内螺纹车刀刀尖角平分线必须与刀杆垂直;⑤内螺纹车刀后角应适当大些,一般磨有两个后角。
四、割槽刀1)高速工具钢槽刀如图3所示1)前角ϒ0:前角增大能使车刀刃口锋利,切削省力并排屑顺畅,ϒ0=5°~20°;2)主后角α0:可减少车槽刀主后刀面和工件过渡表面间的摩擦,α0=6°~8°;3)副后角α0’:可减少车槽刀两个副后刀面和工件已加工表面间的摩擦,α0'=1~3°。
螺纹轴的加工与分析.

如图2.1,编程中,每次螺纹加工走刀至少有4次基本运动(直螺纹)。
运动①:将刀具从起始位置X向快速(G00方式)移动至螺纹计划切削深度处。
运动②:加工螺纹——轴向螺纹加工(进给率等于螺距)。
运动③:刀具X向快速(G00方式)退刀至螺纹加工区域外的X向位置。
运动④:快速(G00方式)返回至起始位置。
绪
随着计算机技术的高速发展,传统的制造业开始了根本性变革,各工业发达国家投入巨资,对现代制造技术进行研究开发,提出了全新的制造模式。在现代制造系统中,数控技术是关键技术,它集微电子计算机、信息处理、自动检测、自动控制等高薪技术于一体,具有高精度、高效率、柔性自动化等特点,对制造业实现柔性自动化、集体化、智能化起着举足轻重的作用。同时,市场对产品的质量和生产效率提出了越来越高的要求。根据数控车削加工的工艺方法,安排工序的先后顺序,确定刀具的选择和切削用量的选择等设计。一般生产加工中,螺纹的加工方式多采用攻丝这种传统工艺,随着数控技术的发展、软件的创新、控制精度的提高、三轴联动或多轴联动数控系统的产生及其在生产领域的广泛应用,相应的先进加工工艺——螺纹铣削逐渐得以实现,其加工精度、光洁度以及柔性是攻丝无法比拟的,另外其经济性在某种情况下也更优于传统工艺。良好的结构工艺性,可以使零件加工容易,节省工时和材料。而较差的零件零件工艺性,会使加工困难,浪费工时和材料,有时甚至无法加工。因此,零件各加工部位的结构工艺性应符合数控加工的特点。
图1.3
H=0.866Pd2=d–0.6495Pd1=d–1.0825Pα=60°
D、d-内、外螺纹大径D2、d2-内、外螺纹中径D1、d1-内、外螺纹小径P-螺距
2三角螺纹的加工
2.1 螺纹加工概念及加工工艺
第六章 螺纹加工
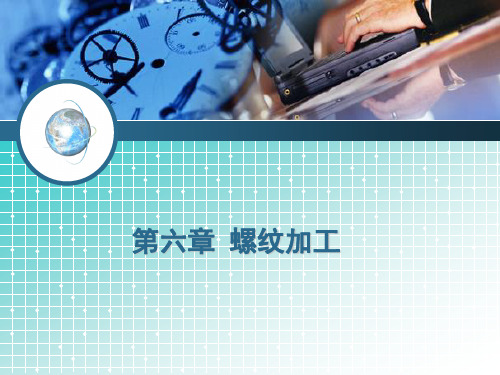
三、梯形螺纹车刀的装夹
螺纹车刀的刀尖应与工件轴线等高,两切削刃夹角的平分 线应垂直于工件轴线,装夹时用梯形螺纹对刀样板校正,以免 产生螺纹半角误差。
四、梯形螺纹车削注意事项
1. 加工梯形螺纹时应采用左右借刀法加工,避免刀具三刃 口同时切削,产生扎刀。 2. 螺纹的牙型角要正确,螺纹牙型两侧面的表面粗糙值要 小。 3. 螺纹加工过程中,应注意不得改变转速,否则会乱牙。
第六章 螺纹加工
在各种机电产品中,螺纹的应用十分广泛,如螺钉、螺 母、螺杆、丝杠等。 用途:它主要用于连接各种机件,也可用来传递运动和载 荷。 主要分类: 按螺纹的牙型——三角形、梯形、锯齿形、圆形等; 按螺纹的外廓形状——圆柱螺纹、圆锥螺纹。
螺纹轴套零件图
第一节 等距螺纹的加工 第二节 多线螺纹的加工 第三节 梯形螺纹的加工
二、运用子程序加工梯形螺纹
上例中的螺纹加工也可用左右切削法,可调用子程序重复 进刀切削。
(下一页续表)
续表
梯形螺纹的加工方法
一、梯形螺纹的一般技术要求
梯形螺纹的轴向剖面形状是等腰梯形。用作传动,精度要 求高,表面粗糙值小,车削梯形螺纹比车削三角螺纹困难。梯 形螺纹的一般技术要求如下: 1. 螺纹的中径必须与基准轴颈同轴,其大径尺寸应小于基 本尺寸。
毛坯为φ45mm×75mm的45钢,用G71、G92指令进行编程, 加工该零件。
实例零件图
一、工艺分析
1. 夹住毛坯φ45mm外圆,伸出大于40mm长→粗车 φ34mm外圆至φ34.5mm→粗车φ24mm外圆至φ24.5mm,精 车外轮廓至尺寸。 2. 换4mm车槽刀加工退刀槽。 3. 换外三角螺纹刀粗、精加工M24×3(1.5)-6g外 螺纹至尺寸。
k :螺纹的牙深。半径值,单位为μm。
《带孔螺纹轴的数控加工》教案

数控车削技术教案教学过程实施仿真模拟()解说演示()各组程序员根据加工方案使用数控仿真软件仿真模拟实现产品加工过程。
要求:()确定工件毛坯的尺寸。
()选择加工的所需刀具。
()完成加工程序的编写与输入。
里忙员将仿真加。
军说产品加工工艺。
a(2)各组由名同学演示仿真加工过程。
4PT:*口艺组由q曰:二。
;:上数控仿真软件的加(1)过程录制视吃壬H SV-I17MMP:!使用数控仿真软件的录屏功能录制加工视频。
ID--/教师通过数控车教学视频,针对教如何婚口工中保证零件的尺寸精度。
:内孔与三角形外螺纹的测量方:内径千分尺的校零与测量。
外径螺纹千分尺的校零与测 —哪加风—学生使用精度控制仿真测试,选取本课题的零件,相互 辩论()各组技术员同学通过视频对比各组加工方案相互辩论,找出其方案所存在的问题。
教师进行点评,并通过刀具磨损动画让学生明白切削中如何使用正确的参数,引导学生改进问题并确定最终加工方案■旦里关sf 通过加工视频对比方案找错。
动画解释切削参数的选择。
方案验证 完成外圆,内孔,外螺纹的测量及磨耗修改,测试成绩被后台记录。
难点 练习()仿真 练习()件进行数控仿真软精度控制 仿真测试数控 仿真软件难点 讲解()视频教学方案实施零件加工)精度检验)任务评价试题自测)总结拓展:)学生将程序通过传输软件传输到数控系统,上机进行带孔螺纹轴的数控加工。
要求:()分钟内独立完成零件加工;()保证零件的尺寸精度;()遵守安全操作规程。
fl监控并到车,HlfD J楼辟;叵画教师使用电子课堂间进行巡褊旨n E ii1■1学生相互测量加工零件的精度写《带孔螺纹轴考核评分表》自动导入到评价系统中。
I*BER3反耶MI吧HUB f”熊4M髀传输软件实现程序传输电子课堂实现车间与机房即时通讯并登录教学平台填在线[见附件),成绩将测试系统学生登录教学平台中的在线测试,选择本课题的相关试题完成自测并提交系统。
在线测试系统教师对本次项目完成的情况进行讲解,总结其中的不足,并布置作业要求学生进行课外拓展,完成其他零件的仿真加工练习教学平台交流拓展附件1:数控车削技术学案课题名称带孔螺纹轴的数控加工上课时间[□□□□]:掌握带孔螺纹轴的工艺分析与精度控制方法。
数控机床编程与操作任务2.7螺纹轴的编程与加工

a)车圆柱螺纹加工循环
b)车圆锥螺纹加工循环
图2-95 G92指令加工路线图
知识准备:三、螺纹车削指令
任务2.7 螺纹轴的编程与加工
3.应用实例
利用G32和G92指令分别编制如图2-96所示的普通三角形圆柱螺纹轴的加工程序。
分析:(1)螺纹导程F为1mm,背吃刀量aP查表2-29可知分3次切削:每次切削深度依次为0.7、 0.4、0.2,从而可得X的坐标依次为29.3、28.9、28.7。
(2)切入切出段δ1、δ2计算。δ1取3mm,δ2=δ1/2=1.5,切削起点Z坐标为3mm,终点Z坐
······
aP=0.2mm 快速退至换刀点
知识准备:三、螺纹车削指令
任务2.7 螺纹轴的编程与加工
4. 螺纹车削复合循环指令G76 1)指令作用 G76指令用于多次自动循环切削螺纹。经常用于加工不带退刀槽的圆柱螺纹和圆锥螺纹。
2)指令格式
G76 P(m)(r)( ) Q(dmin) R(d ) ;
任务2.7 螺纹轴的编程与加工
—机械工业出版社
目录
任务2.7 螺纹轴的编程与加工
过渡页
Transition Page
1
任务导入
2
学习目标
3
知识准备
4
任务实施
5
问题归纳
6
技能强化
2
任务导入
任务2.7 螺纹轴的编程与加工
图2-88 螺纹轴零件图
如图2-88所示螺纹轴零件图,毛坯为φ50mm×200mm的棒料,材料 为45钢,完成螺纹轴零件的编程与加工。
复杂螺纹轴类零件的加工工艺分析

成, 内螺纹 通过 钻孔 、 粗镗、 精镗 来完成 。 3 . 对 零件 l 和 零件 2的圆柱 面 配合 ,
3 . 两个零 件分别 有装 配形式 , 两 配合 装配尺 寸和行 为公差 的要 求 。 4 . 网所爪 为舣 合零件 , 包括 件 1 和
1 . 装配 后零 件 1 的 E处和 零 件 2的
还 应保 证 其形状 和位 置精 度 的要 求 。文
圆外轮廓 、 一 个应通过 粗 、 精
车和切槽 来 完成 , 内轮 廓应 通过 钻孔 、 粗
3 . 有 端配 合要求 尺寸 1 2 6 9 1 - 0 . 0 9 。
复杂螺 纹轴类零件 的加工工艺分析
■ 张永 松
摘要: 轴 类零件 是机械 加 工 中经 常遇 到的典型 零件之 一 , 它主要 用来 支承传 动零部件 , 传递 扭矩 和承受 载荷 。一般 由外 匮 l 柱 面、 断
面, 台阶 倒角 沟槽 螺纹 和 中心孔等 要素 构成 。文 章通 过复 杂轴 类零件 的加 工工 艺分析 , 巧 用 了辅 助顶 尖 完成对 该类零 件 的加
外轮 廓时 应分 别使 用粗 精 刀, ; 来 进行 粗
零件 1 零件 2 精加 T。
作者 简介 : 张永松 , 南京交通技 师 学院 。
№
耵。
工艺 分 析
1 . 零件 1 的 主要 加
工部 分包括 四段 圆柱外
径、 一段 圆锥 外径 、 两段 相切 的外 圆弧 、一段椭 配 合件装 配图
反 映轴 类零 件 的加 丁规 律 和共性 。 而轴
类 零件 的精 度要 求 较高 ,所 以在 车削 时 除l r 要 保 让尺 寸 精 度和 表 而 粗糙 度 外 ,
锥螺纹加工方法

锥螺纹加工方法
锥螺纹加工方法是将螺纹在轴线方向逐渐加大或减小的加工方法。
下面介绍几种常见的锥螺纹加工方法:
1. 割床加工:使用割床进行锥螺纹的加工。
先在工件上切割出初始螺纹,然后使用倒数刀,持续切割或修整螺纹,最后得到锥螺纹。
2. 滚压加工:使用滚压刀具对工件进行加工。
滚压刀具上有一套与工件锥螺纹相对应的刀齿,通过滚动加工来形成螺纹。
3. 铣削加工:使用铣床进行加工。
在铣床上安装相应的刀具,按照螺纹的螺旋线形状进行加工。
4. 砂轮修整加工:使用砂轮进行锥螺纹的修整和细加工。
通过砂轮的修整,使螺纹形状更加准确。
5. 切削液拉削加工:使用切削液拉削机床进行加工。
切削液拉削机床可以按照一定的角度和速度进行螺旋状切削,形成锥螺纹。
总的来说,锥螺纹加工方法主要有割床加工、滚压加工、铣削加工、砂轮修整加工和切削液拉削加工等多种方法,具体选择哪种方法需要根据工件的要求和加工设备的条件来决定。
阶梯螺纹轴的数控加工与工艺

阶梯螺纹轴的数控加工与工艺第1章阶梯螺纹轴的工艺分析1.1阶梯螺纹轴的零件图图1.1阶梯螺纹轴零件图1.1分析图样可知:该零件图为轴类回转体,所要加工的内容主要有圆柱面、半圆球、锥面、螺纹、螺纹退刀槽、内孔等组成,该零件的表面粗糙度、尺寸精度等要求较高,需合理选用切削用量和刀具在加工中予以保证,该零件关键工序是M18的螺纹、Ф18mm至Ф34mm的锥度、内孔及SR6半圆球。
该零件分两次装夹,第一次夹住工件右端车左端,第二次夹住已加工Ф36mm 表面,加工零件右端,加工过程大致应为车两端面、钻中心孔、钻孔、车左端外圆及内孔、平总长、车右端外圆。
1.2毛坯的种类(1)铸件:适用于形状复杂的零件毛坯。
其方法主要是铸造。
(2)锻件:适用于强度要求高、形状比较简单的零件毛坯。
(3)型材:型材有热轧和冷拉两种。
热轧适用于尺寸较大精度较低的毛坯;冷拉适用于尺寸较小、精度较高的毛坯。
(4)焊接件:将型材或钢板等焊接成所需要的零件结构,简单方便,生产周期短,但需要经时效处理后才能进行机械加工。
1.2.1毛坯的选择原则在选择毛坯时应考虑下列因素:(1)材料和机械加工性能。
材料能否在加工设备上顺利加工决定其加工的难易程度,而在切削过程中会产生大量切削热致使工件的性能和组织发生改变。
(2)零件的结构形状和外形尺寸。
选择零件的毛坯时其大小,形状尽可能与零件图相近。
(3)生产纲领大小。
当零件产量较大时,应选择精度和生产率较高的毛坯制造方法。
(4)生产条件。
选择毛坯时,要考虑到毛坯的制造水平,设备加工精度,员工的技术水平经济性等。
(5)充分考虑利用新技术、新工艺、新材料的可能。
为节约材料和能源,发展趋势是少切屑、无切屑毛坯制造。
该零件材料为45钢、属于中小传动轴,应选用Ф45mm的圆钢做毛坯。
1.3表面加工方法的确定任何零件都是由一些简单表面如外圆、内孔、平面和成形表面等进行不同组合而形成的,根据这些表面所要求的精度和表面粗糙度以及零件的结构特点,将每一表面的加工方案确定下来,也就确定了零件的全部加工内容。
任务三螺纹轴的加工工艺与程序编制
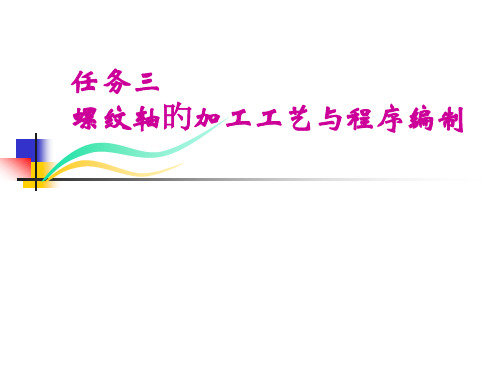
半径差。 k:螺纹牙型旳高度,用半径值指定,单位为μm, Δd:第一次旳切深量,X轴方向旳半径值,单位为μm L:螺纹导程
后数值不允许带小数点,单位为0.001秒(或转)。 G04暂停功能能够用在车槽时旳暂停 钻孔时暂停和车螺纹前主轴转速旳延时暂停。
⑵G01车槽
应用举例:用G01车如图2-52所示旳 槽,槽刀宽为4mm,工件坐标零 点在右端面中心。
…… G00 X22 Z-15; G01 X14 F30; G04 X0.5; 槽底暂停0.5S G01 X22 F100; Z-18; G01 X14 F30; G04 X0.5; 槽底暂停0.5S X22 F100; ……
在安装时,刀具不宜伸出过长,同步刀具旳中心线必 须装得与工件中心垂直,以确保两个副偏角对称。
切断实心工件时,刀具旳主切削刃必须装得与工件中 心等高,不然不能车到中心,而且轻易崩刃,甚至折 断车刀。
刀具旳底平面应平整,以确保两个副后角对称。 假如有顶尖顶住加工时,应在切断前及时移去顶尖,
不然轻易打坏刀具。
螺纹大径(D、d)
螺纹中径(D2、d2) 螺纹大径(D1、d1)
螺纹旳牙型高度( h)
计算公式
P H=0.866P
螺纹大径旳基本 尺寸=公称直径
d2= D2=d-0.6495P d1= D1=d-1.0825P h=0.54P
螺纹车削几何尺寸阐明
(1)高速车削三角形外螺纹时,受车刀挤压后会使螺纹大 径尺寸胀大,所以车螺纹前旳外圆直径,因比螺纹大径 小。根据一般经验公式,螺纹顶径在车外圆时应车小 (0.1~0.13)P(P为螺距)
任务三螺纹轴的加工工艺与程序编制
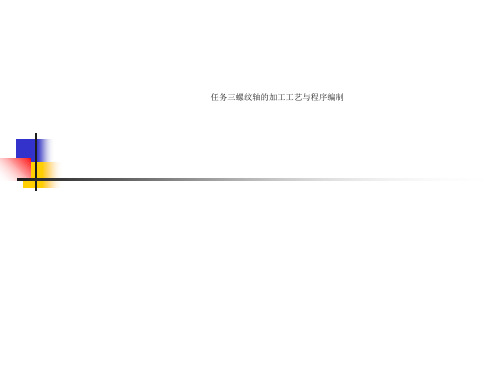
如果X(U)及△i省略,可用相应的正负符号指定刀具退刀量 f:进给量
G75走刀路线
G75应用举例
例:加工如图2.3.9所示四处3mm宽外沟 N3槽0 G00 X32 Z-13;
N40 G75 R1; R:退刀量1mm
G92应用举例
如图所示用G92加工 M20×1.5圆锥螺纹,分四刀 完成。
…… N50G00X28.Z2.; N60G92X19.2Z-22.R-3.F1.5; N70X18.6; N80X18.2; N90X18.04; ……
双头螺纹的加工举例
例4.用G92加工M24×4/2圆柱螺 纹,假设每条螺纹分两刀完成。
半径差。 k:螺纹牙型的高度,用半径值指定,单位为μm, Δd:第一次的切深量,X轴方向的半径值,单位为μm L:螺纹导程
G76 螺纹切削复合循环轨迹
由图可知,其以 斜进法方法分层 切削螺纹,因此 更适合加工螺距 较大、牙型较深 的螺纹。
G76应用举例
用G76加工如图所示的螺纹 …… N230 G00 X 34 Z5; (刀具定位到循环起点) G76 P01060 Q200 R100; (螺纹车削循环,最小切深0.2mm,精加工余
Z
XZ
W
4R
3F 1R
G32
Z
指令G92使用注意事项
① 在螺纹切削期间,按下进给保持时,刀具将在完成 一个螺纹切削循环后再进入进给保持状态。
② 如果在单段方式下执行 G92 循环,则每执行一次循 环必须按四次循环起动按钮。
③ G92 指令是模态指令,当 Z 轴移动量没有变化时, 只需对 X 轴指定移动指令即可重复固定循环。
螺纹及丝杆加工工艺

螺纹及丝杆加工工艺引言螺纹和丝杆作为广泛应用于机械设备中的重要部件,其加工工艺对产品质量和性能具有重要影响。
螺纹加工是一种复杂且精密的加工工艺,要求高精度和良好的表面质量。
本文将介绍螺纹及丝杆加工的工艺流程和常用的加工方法。
工艺流程螺纹及丝杆加工的工艺流程通常包括以下几个步骤:1.材料准备:选择适当的材料进行加工,通常使用具有良好加工性能和耐磨性的材料。
2.车削加工:螺纹及丝杆的加工通常以车削加工为主要方法。
车削加工可以分为粗车和精车两个阶段。
粗车主要是为了去除材料多余的部分,获得近似尺寸的基准圆柱体。
精车则是在基准圆柱体上进行细致修整,以获得准确的螺纹形状和表面质量。
3.螺纹刀具选择:根据加工要求选择适当的螺纹刀具,常见的有螺纹车刀、螺纹铣刀、螺纹切割刀等。
选择刀具时要考虑加工材料的硬度、螺纹尺寸和表面质量要求等因素。
4.加工参数设置:根据加工材料和螺纹尺寸等因素,设置合适的车削速度、进给速度和切削深度等加工参数。
合理的加工参数可以提高生产效率和加工质量。
5.螺纹切削:根据螺纹图样,使用选定的螺纹刀具进行切削加工。
螺纹刀具要正确安装,确保刀具切削刃与工件螺纹轴线的垂直程度,以获得正确的螺纹形状和精度。
6.表面处理:螺纹及丝杆的表面可能会出现一些不良缺陷,如划伤、磨痕等。
为了提高表面质量,通常会进行一些表面处理,如打磨、抛光等。
7.检测和质量控制:对加工后的螺纹及丝杆进行检测,包括测量螺纹尺寸、检查螺纹形状和表面质量等。
必要时,还需进行质量控制,以确保产品符合设计要求。
常用的加工方法冷滚压加工法冷滚压加工是一种常见且有效的螺纹加工方法。
该方法利用特殊的滚齿刀具,将刀具的螺纹牙形与工件螺纹相契合,通过滚动切削来获得精确的螺纹形状。
冷滚压加工法具有以下优点:•高效:较高的生产效率,可一次加工多个螺纹。
•高精度:获得较高的螺纹精度和表面质量。
•节约材料:由于冷滚压不需要切削过多的材料,可以节约原材料。
- 1、下载文档前请自行甄别文档内容的完整性,平台不提供额外的编辑、内容补充、找答案等附加服务。
- 2、"仅部分预览"的文档,不可在线预览部分如存在完整性等问题,可反馈申请退款(可完整预览的文档不适用该条件!)。
- 3、如文档侵犯您的权益,请联系客服反馈,我们会尽快为您处理(人工客服工作时间:9:00-18:30)。
螺纹轴的加工
主讲:耿国卿
一、技能训练目标
目标 1:指令G71、G90的编程方法 目标 2:数控车床的基本操作方法
目标 3:工件的测量方法及量具的使用方法
目标 4: 制定工件的加工工艺
目标 5:螺纹轴的车削加工
二、工作任务描述
1.加工零件项目工作任务名称:
螺纹轴的加工
2.零件类型描述:
第1刀
第2刀
第3刀
第4刀
第5 刀
第6 刀
第7刀
第8 刀
径向进给量(半径值)
每刀切削直径
0.3
29.40.2528.9来自0.2028.5
0.15
28.2
0.15
27.9
0.10
27.7
0.075
27.55
0
27.55
(三)工、量具选择
(四)加工工艺卡片
(四)加工程序
五、任务评价
1)小组内相互检测。教师抽查、指导。 2)问题原因的自我分析及小组讨论。 3)评价项目及评分标准:
(二)数值计算
图中尺寸φ 36,换算成编程尺寸φ 35.981±0.019 mm。 螺纹M30×2的实际大径:d=30-0.2=29.8;走刀次数及径向进给量:可 以参考表6-1分配走刀次数和径向进给量,在最后一刀切削时,实际 小径按计算值27.55,最后一刀为修光空走刀。走刀次数及径向进给 量如下:
零件图
三、任务要求
每2人一小组(自由组合); 两人合作编写加工程序、确定加工工艺及 切削用量; 两人共同完成一个工件的加工任务。工件 手动车断。 写上两人姓名。
四、任务实施
(一)任务分析
根据图纸及任务要求,该工件由外圆、槽和螺纹构成。 工件长度为80mm,为短轴加工,可采用三爪自定心卡盘装夹, 不用顶尖。 工件采取调质处理,切削性能良好,粗车可采用硬质合金车刀, 精车用高速钢车刀。 外圆形状较为复杂,去除余量较大,可采用G71指令编程。螺纹 M30×2的螺距不大,采用直进式加工,指令采用G92。4×2的槽 可选择4mm宽的切槽刀一次完成。 由于尺寸φ 36精度要求较高,且与螺纹M30×2有同轴度要求, 如果先加工完成外圆尺寸后再车螺纹,由于车削螺纹的切削力 较大,有可能引起工件变形,影响工件的同轴度。因此φ 36外 圆先粗车,留精加工余量,等车完螺纹后最后精加工。最后保 证总长,切断。 切削用量:粗车n=500r/min,ap=1mm;精车 n=1000r/min,ap=0.5mm; 车螺纹转速:n=300r/min。 编写工艺卡片。
评分标准:
六、小结
(1)编程格式 (2)对刀方法 (3)编程方法及技巧
七、作业
课后写试验报告:螺纹轴的加工。
谢谢大家!
该零件是使用数控车削加工的基本零件轮廓形状和螺纹;是数控 车削加工中难度较高的基本零件之一。
3.任务内容描述:
已知毛坯材料为45钢,毛坯尺寸为Ф 45mm的棒料。调质处理 220~260HBS。制定零件加工工艺,编写零件加工程序,并在仿 真软件上进行虚拟操作加工。最后使用数控车床进行加工,并对加 工后零件进行检测、评价。