永磁铁氧体预烧料的生产工艺是怎样的
永磁铁氧体生产工艺

永磁铁氧体生产工艺永磁铁氧体是一种具有高磁性和高温稳定性的磁性材料,广泛应用于电机、发电机、传感器等领域。
永磁铁氧体的生产工艺一般包括以下几个步骤:1. 原料准备:永磁铁氧体的主要原料是氧化铁、氧化钡、氧化钴等化合物,需要按照一定的比例进行配料,同时还需要添加一定的助磁剂和其他添加剂。
配料完成后,将原料送入球磨机进行混合研磨,以提高混合度和颗粒粒度的均匀性。
2. 造粒压制:将研磨后的混合粉末送入造粒机进行压制成形。
常用的造粒方法有干压造粒和湿压造粒两种。
干压造粒是将混合粉末在模具中进行压制,形成预定形状的颗粒;湿压造粒则是在添加一定的液体和黏结剂的情况下进行造粒,然后通过干燥将颗粒固化。
3. 烧结和烧结控制:将压制成形的颗粒送入高温炉进行烧结。
在烧结过程中,由于高温作用,颗粒之间的颗粒间结合力增强,形成致密的材料,颗粒内部排列有序。
烧结温度和时间的控制对于材料的性能具有重要影响,需要进行精确控制。
4. 后处理:烧结后的材料还需要通过一些后处理工艺来进一步提高其性能。
常见的后处理方法包括磁化处理、热处理和磁场处理等。
磁化处理是将材料置于强磁场中进行磁化,以提高材料的磁性能;热处理则是利用高温进行退火或淬火等处理,以改变材料的晶体结构和性能;磁场处理则是利用磁场对材料进行预处理,提高材料的磁性能。
5. 检验和包装:经过上述工艺步骤后,对生产出的永磁铁氧体进行质量检验,包括磁性能测试、密度测试、外观检查等。
合格的产销售前,还需要进行包装和存储,以保证产品的质量和使用寿命。
以上是永磁铁氧体的基本生产工艺,不同厂家和产品可能会有所差异,但总体上都是通过原料准备、造粒压制、烧结和后处理等环节来完成材料的制备。
随着技术的不断发展,工艺也在不断改进和优化,以提高材料的性能和生产效率。
铁氧体磁铁制造工艺流程

铁氧体磁铁制造工艺流程铁氧体磁铁制造工艺流程一、概述铁氧体磁铁是一种常见的永磁材料,具有高磁能积、高矫顽力、高稳定性等优点,广泛应用于电机、声学器件、传感器等领域。
本文将介绍铁氧体磁铁的制造工艺流程。
二、原材料准备1. 铁氧体粉末:选择适当的铁氧体粉末是制造高质量铁氧体磁铁的关键。
常用的粉末有SrFe12O19、BaFe12O19等。
2. 粘结剂:粘结剂可以增加粉末之间的黏着力,提高成型后的强度和韧性。
常用的粘结剂有聚乙烯醇(PVA)、聚乙烯(PE)等。
3. 溶剂:溶剂用于稀释粘结剂,使其易于涂覆在粉末表面。
常用的溶剂有水、丙酮等。
4. 添加剂:添加剂可以改善材料性能,如增加导电性能或防腐蚀性能。
常用的添加剂有氧化铁、钛酸酯等。
三、成型1. 压制:将铁氧体粉末和粘结剂混合均匀后,采用压制工艺将其压成所需形状的坯料。
压制时需要控制压力和温度,以确保坯料的致密性和稳定性。
2. 烧结:将压制好的坯料置于高温炉中进行烧结。
烧结过程中,粉末颗粒之间会发生化学反应,形成致密的晶体结构。
同时,粘结剂也会被热分解并挥发出去。
烧结温度和时间需要根据具体材料而定。
四、加工1. 切割:将烧结好的铁氧体坯料切割成所需尺寸的小块。
2. 磨削:对切割好的小块进行表面处理和修整,以获得平整光滑的表面。
3. 磁化:通过电流或强磁场对铁氧体磁铁进行磁化处理。
在这个过程中,材料内部会产生一定方向上的自发极化,并形成一个稳定的磁场。
五、检测和质量控制1. 磁性检测:通过磁性测试仪器检测铁氧体磁铁的磁场强度、剩磁、矫顽力等指标。
2. 外观检测:对铁氧体磁铁进行外观检查,检查是否有裂纹、毛刺等缺陷。
3. 包装和贮存:将合格的铁氧体磁铁进行包装,并在干燥、无尘的环境中储存。
同时,要注意避免与其他磁性物品接触,以免影响其性能。
六、结语以上就是铁氧体磁铁制造工艺流程的详细介绍。
在实际生产中,需要根据具体情况进行调整和改进,以确保产品质量和生产效率。
永磁铁氧体的制备工艺
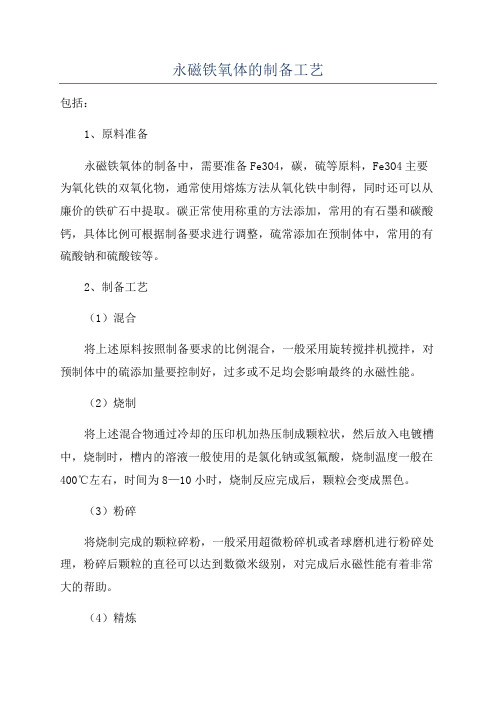
永磁铁氧体的制备工艺
包括:
1、原料准备
永磁铁氧体的制备中,需要准备Fe3O4,碳,硫等原料,Fe3O4主要为氧化铁的双氧化物,通常使用熔炼方法从氧化铁中制得,同时还可以从廉价的铁矿石中提取。
碳正常使用称重的方法添加,常用的有石墨和碳酸钙,具体比例可根据制备要求进行调整,硫常添加在预制体中,常用的有硫酸钠和硫酸铵等。
2、制备工艺
(1)混合
将上述原料按照制备要求的比例混合,一般采用旋转搅拌机搅拌,对预制体中的硫添加量要控制好,过多或不足均会影响最终的永磁性能。
(2)烧制
将上述混合物通过冷却的压印机加热压制成颗粒状,然后放入电镀槽中,烧制时,槽内的溶液一般使用的是氯化钠或氢氟酸,烧制温度一般在400℃左右,时间为8—10小时,烧制反应完成后,颗粒会变成黑色。
(3)粉碎
将烧制完成的颗粒碎粉,一般采用超微粉碎机或者球磨机进行粉碎处理,粉碎后颗粒的直径可以达到数微米级别,对完成后永磁性能有着非常大的帮助。
(4)精炼。
永磁铁氧体的制备工艺

永磁铁氧体的制备工艺一、原料选取1.氧化物原料:通常使用Fe2O3、Fe3O4作为铁源,Co3O4作为钴源。
2.氮化物原料:一般使用氮化铁作为氮源。
3.稀土原料:利用稀土元素的高磁晶各向异性,常使用氧化稀土和相应的稀土钴化合物作为稀土源。
二、配料1.按照化学计量比例将各种原料精细研磨,并通过筛网分选得到均匀的粉末。
2.将各种原料粉末按照一定比例进行混合,通常由铁源、稀土源和钴源组成。
三、烧结1.将混合粉末充分搅拌均匀,并进行压片成坯。
通常采用等静压方法,在模具中施加一定压力,使混合粉末在模具中成型。
2.将坯体进行预烧处理,去除一部分有机物质,并形成初步的金属氧化物。
3.进行烧结处理,将坯体加热至一定温度下,使金属氧化物发生化学反应,形成金属间化合物和磁性颗粒。
4.控制烧结温度和时间,以保证产生足够的磁晶各向异性和颗粒尺寸的增长。
四、后处理1.针对烧结后的材料进行磨削、超声清洗等处理,以去除表面的污染物和不良颗粒。
2.进行磁化处理,通过外加磁场将材料磁化,使其具有永久磁性。
3.进行磁性能测试,进行磁感强度、矫顽力和剩余磁感应强度等性能测试,并根据需要对材料进行优化。
永磁铁氧体的制备工艺繁多,其中最常用的是传统的陶瓷工艺和后来发展起来的粉末冶金工艺。
陶瓷工艺制备的永磁铁氧体具有较高的矫顽力和剩余磁感应强度,但磁晶各向异性较低;而粉末冶金工艺制备的永磁铁氧体具有较高的磁晶各向异性,但矫顽力和剩余磁感应强度较低。
目前,研究人员正在努力寻找新的制备工艺,以获得更优异的永磁铁氧体性能。
综上所述,永磁铁氧体的制备工艺包括原料选取、配料、烧结和后处理等步骤。
这些工艺在生产过程中需要严格控制参数和条件,以获得理想的微观结构和磁性能。
随着技术的不断发展,相信永磁铁氧体的制备工艺还会不断创新和改进,以满足不同领域对其性能的需求。
铁氧体生产工艺
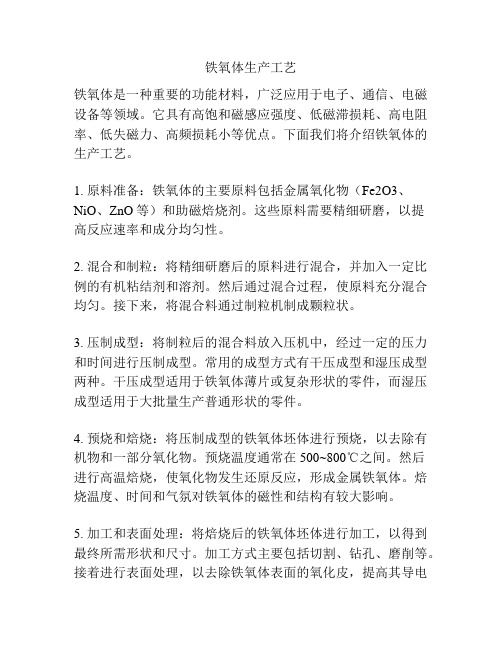
铁氧体生产工艺铁氧体是一种重要的功能材料,广泛应用于电子、通信、电磁设备等领域。
它具有高饱和磁感应强度、低磁滞损耗、高电阻率、低失磁力、高频损耗小等优点。
下面我们将介绍铁氧体的生产工艺。
1. 原料准备:铁氧体的主要原料包括金属氧化物(Fe2O3、NiO、ZnO等)和助磁焙烧剂。
这些原料需要精细研磨,以提高反应速率和成分均匀性。
2. 混合和制粒:将精细研磨后的原料进行混合,并加入一定比例的有机粘结剂和溶剂。
然后通过混合过程,使原料充分混合均匀。
接下来,将混合料通过制粒机制成颗粒状。
3. 压制成型:将制粒后的混合料放入压机中,经过一定的压力和时间进行压制成型。
常用的成型方式有干压成型和湿压成型两种。
干压成型适用于铁氧体薄片或复杂形状的零件,而湿压成型适用于大批量生产普通形状的零件。
4. 预烧和焙烧:将压制成型的铁氧体坯体进行预烧,以去除有机物和一部分氧化物。
预烧温度通常在500~800℃之间。
然后进行高温焙烧,使氧化物发生还原反应,形成金属铁氧体。
焙烧温度、时间和气氛对铁氧体的磁性和结构有较大影响。
5. 加工和表面处理:将焙烧后的铁氧体坯体进行加工,以得到最终所需形状和尺寸。
加工方式主要包括切割、钻孔、磨削等。
接着进行表面处理,以去除铁氧体表面的氧化皮,提高其导电性和表面光洁度。
6. 检测和筛选:对铁氧体产品进行磁性、电学和物理性能的检测。
检测内容包括磁感应强度、磁滞回线、矫顽力、电阻率、介电常数等。
根据产品质量要求,对合格产品进行筛选和分级。
7. 包装和储存:对合格的铁氧体产品进行包装和标识,并存放在干燥、通风的仓库中。
在储存过程中要防止产品受潮、受尘和受污染,以保证其性能不受影响。
以上就是铁氧体的生产工艺,生产铁氧体需要精细的原料准备、混合和制粒、压制成型、预烧和焙烧、加工和表面处理、检测和筛选、以及包装和储存等步骤。
通过这些工艺步骤的合理配合,可以制得具有优良性能的铁氧体产品。
永磁铁氧体预烧料的加工工艺及方法

永磁铁氧体预烧料的加工工艺及方法永磁铁氧体(Permanent Magnet Ferrite)是一种常用的磁性材料,具有高磁感应强度、优良的耐腐蚀性和热稳定性等特性。
在制备永磁铁氧体磁体之前,需要首先制备永磁铁氧体预烧料,然后通过烧结等工艺将其转化为磁体材料。
原料选择与准备:永磁铁氧体预烧料的主要成分为铁氧体和结合剂。
铁氧体的主要成分有镍、锌、尤其是氧化铝和钡等。
结合剂可以选择有机物或无机物,如聚乙烯醇(PVA)、羟丙基甲基纤维素醚(HPMC)等。
这些原料需要根据成品永磁铁氧体的性能要求选择,并进行准备。
混合:将原料按照一定比例进行混合。
混合可以采用机械搅拌、称重、喷洒等方法。
通过混合可以保证各种成分得到均匀分布,确保后续工艺的顺利进行。
均化:将混合后的原料进行均化处理。
均化是为了消除原料中的团聚现象,使颗粒得到更好的分散状况。
常用的均化方法有机械研磨、超声波均化等。
湿法制粒:将均化后的原料与添加一定量的水或有机溶剂进行混合,形成可塑性较好的湿混合物。
然后通过制粒机等设备对湿混合物进行制粒。
制粒的目的是使混合物得到更好的成型性和流动性。
干燥:将制粒后的永磁铁氧体预烧料进行干燥,以去除水分或溶剂。
干燥的方法可以有自然干燥、烘箱干燥、真空干燥等。
干燥的温度和时间需要根据具体情况确定。
细粉磁性颗粒制备:将干燥后的永磁铁氧体预烧料粉末进行进一步处理,制备细粉磁性颗粒。
常用的制备方法有磁力分选、水力分选等。
此过程的主要目的是提高预烧料颗粒的磁性能和均匀性。
综上所述,永磁铁氧体预烧料的制备工艺包括原料选择与准备、混合、均化、湿法制粒、干燥、细粉磁性颗粒制备等环节。
这些工艺步骤的顺序和参数需要根据具体情况进行调整和优化,以确保永磁铁氧体预烧料的质量和性能。
同时,制备过程中需要严格控制工艺参数,确保原料的均匀分布和颗粒的一致性。
最终,制备出的永磁铁氧体预烧料可以通过烧结等工艺转化为磁体材料,用于生产各种永磁铁氧体磁体产品。
永磁铁氧体预烧料的生产工艺是怎样的
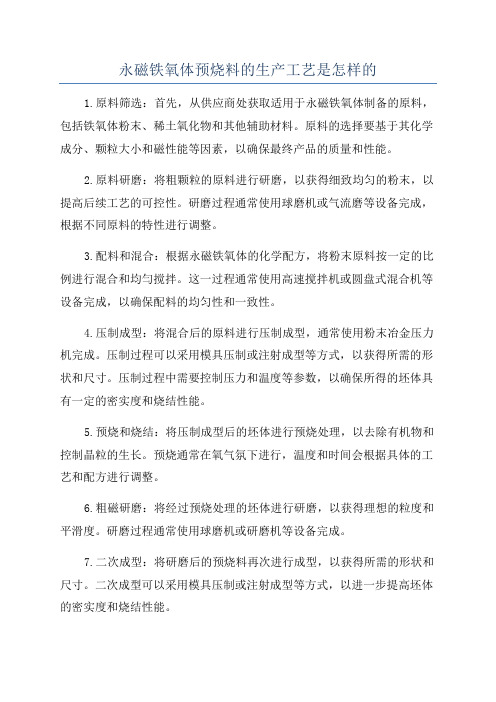
永磁铁氧体预烧料的生产工艺是怎样的1.原料筛选:首先,从供应商处获取适用于永磁铁氧体制备的原料,包括铁氧体粉末、稀土氧化物和其他辅助材料。
原料的选择要基于其化学成分、颗粒大小和磁性能等因素,以确保最终产品的质量和性能。
2.原料研磨:将粗颗粒的原料进行研磨,以获得细致均匀的粉末,以提高后续工艺的可控性。
研磨过程通常使用球磨机或气流磨等设备完成,根据不同原料的特性进行调整。
3.配料和混合:根据永磁铁氧体的化学配方,将粉末原料按一定的比例进行混合和均勻搅拌。
这一过程通常使用高速搅拌机或圆盘式混合机等设备完成,以确保配料的均匀性和一致性。
4.压制成型:将混合后的原料进行压制成型,通常使用粉末冶金压力机完成。
压制过程可以采用模具压制或注射成型等方式,以获得所需的形状和尺寸。
压制过程中需要控制压力和温度等参数,以确保所得的坯体具有一定的密实度和烧结性能。
5.预烧和烧结:将压制成型后的坯体进行预烧处理,以去除有机物和控制晶粒的生长。
预烧通常在氧气氛下进行,温度和时间会根据具体的工艺和配方进行调整。
6.粗磁研磨:将经过预烧处理的坯体进行研磨,以获得理想的粒度和平滑度。
研磨过程通常使用球磨机或研磨机等设备完成。
7.二次成型:将研磨后的预烧料再次进行成型,以获得所需的形状和尺寸。
二次成型可以采用模具压制或注射成型等方式,以进一步提高坯体的密实度和烧结性能。
8.最后烧结:将经过二次成型的坯体进行最后的烧结处理,以实现晶粒的长大和晶界的固相扩散,得到具有优良磁性能和物理性能的成品。
烧结过程通常在氧气氛下进行,温度和时间也会根据具体需求进行调整。
9.检测和包装:对最后烧结的永磁铁氧体进行物性和磁性能的检测,以确保产品符合要求。
合格的产品将经过清洗、包装和标识等工艺,最终通过质检合格后进入市场。
总结:永磁铁氧体预烧料的生产工艺包括原料筛选、原料研磨、配料和混合、压制成型、预烧和烧结、粗磁研磨、二次成型、最后烧结、检测和包装等多个步骤。
永磁铁氧体加工工艺和方法
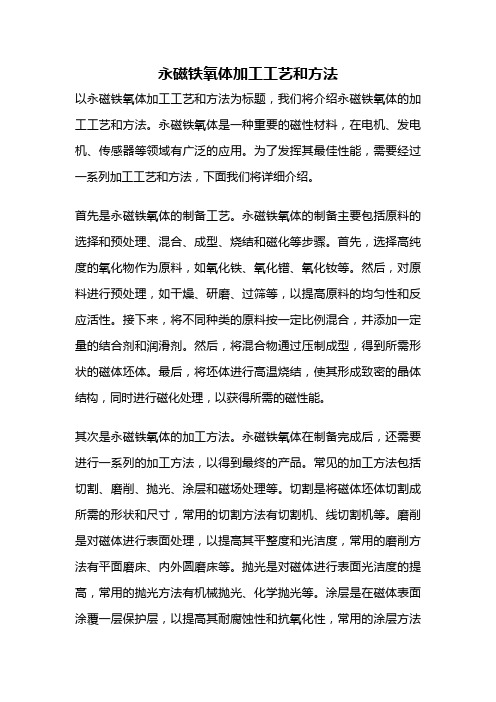
永磁铁氧体加工工艺和方法以永磁铁氧体加工工艺和方法为标题,我们将介绍永磁铁氧体的加工工艺和方法。
永磁铁氧体是一种重要的磁性材料,在电机、发电机、传感器等领域有广泛的应用。
为了发挥其最佳性能,需要经过一系列加工工艺和方法,下面我们将详细介绍。
首先是永磁铁氧体的制备工艺。
永磁铁氧体的制备主要包括原料的选择和预处理、混合、成型、烧结和磁化等步骤。
首先,选择高纯度的氧化物作为原料,如氧化铁、氧化镨、氧化钕等。
然后,对原料进行预处理,如干燥、研磨、过筛等,以提高原料的均匀性和反应活性。
接下来,将不同种类的原料按一定比例混合,并添加一定量的结合剂和润滑剂。
然后,将混合物通过压制成型,得到所需形状的磁体坯体。
最后,将坯体进行高温烧结,使其形成致密的晶体结构,同时进行磁化处理,以获得所需的磁性能。
其次是永磁铁氧体的加工方法。
永磁铁氧体在制备完成后,还需要进行一系列的加工方法,以得到最终的产品。
常见的加工方法包括切割、磨削、抛光、涂层和磁场处理等。
切割是将磁体坯体切割成所需的形状和尺寸,常用的切割方法有切割机、线切割机等。
磨削是对磁体进行表面处理,以提高其平整度和光洁度,常用的磨削方法有平面磨床、内外圆磨床等。
抛光是对磁体进行表面光洁度的提高,常用的抛光方法有机械抛光、化学抛光等。
涂层是在磁体表面涂覆一层保护层,以提高其耐腐蚀性和抗氧化性,常用的涂层方法有喷涂、浸渍等。
磁场处理是通过施加外部磁场,对磁体进行磁化处理,以提高其磁性能,常用的磁场处理方法有直流磁场处理、交变磁场处理等。
在进行永磁铁氧体加工工艺和方法时,还需要注意一些关键技术。
首先是原料的选择和配比,不同种类和比例的原料会影响磁体的磁性能。
其次是成型工艺的控制,包括压制力、压制速度和保压时间等参数的控制,这些参数会影响磁体的致密度和形状。
再次是烧结工艺的控制,包括烧结温度、烧结时间和气氛等条件的控制,这些条件会影响磁体的晶体结构和磁性能。
最后是磁场处理的控制,包括磁场强度、磁化时间和磁化方向等参数的控制,这些参数会影响磁体的磁化程度和磁性能。
永磁铁氧体预烧料的生产工艺是怎样的

永磁铁氧体预烧料的生产工艺是怎样的以优质铁鳞为原料,采用链篦机——回转窑干法生产工艺,生产Y30H-1型锶永磁铁氧体预烧料。
经过烘干、球磨后的铁鳞,与一定配比的碳酸锶、高岭土进行配料、强混、造球后,送入链篦机进行烘干、氧化处理。
链篦机采用回转窑的尾气对物料进行烘干,以及将物料中的FeO氧化为Fe2O3,将物料中三氧化二铁的成份进行大比例的提高。
完成链篦机烘干、氧化后的球状物料,送入回转窑经过1200℃进行高温煅烧处理。
在回转窑中,物料中的碳酸锶和碳酸钙会在高温中发生分解反应,然后再与Fe2O3生成产品——SrO(Fe2O3)6。
项目生产过程中发生的化学反应如下:链篦机中的氧化反应:4FeO +O2 = 2Fe2O3?回转窑中的分解反应:SrCO3 =(高温)SrO+CO2↑回转窑中产品的生成反应:SrO+ 6Fe2O3=(高温)SrO(Fe2O3) 61、原料来源铁鳞由汽车运输至本项目厂区铁鳞堆场进行散放堆存。
项目外购的袋装碳酸锶、高岭土全部在车间内暂存库房内堆存。
2、原料处理项目需要对铁鳞进行初步筛分、烘干、冷却、球磨机初磨、配料、配料后强混球磨等工段,为项目三条生产线提供合格的原材料。
具体处理步骤如下:(1)铁鳞筛分项目铁鳞堆场内设置了一台孔径为75px的粗筛,除去铁鳞中较大的杂质。
根据现场勘查,筛除的杂质主要为热轧厂铁鳞沉淀池中混杂的砖头、废弃角钢等固废。
(2)铁鳞烘干窑烘干经过筛分后的合格铁鳞经3m高的斗提机输送至烘干窑中,通入煤气燃耗后进行烘干处理,将含水率为10%的铁鳞烘干到含水1%左右。
斗提机进料口,会产生车间粉尘(G1),采用集气罩收集后送入SMC4-30型布袋除尘器处理,除尘系统回收的粉尘送强混球磨机进行研磨。
烘干过程中将产生烘干烟气(G2),主要污染物为粉尘。
烘干烟气经烟气管道收集送旋风除尘系统处理,除尘系统回收的粉尘送强混球磨机进行研磨。
(3)铁鳞烘干窑后冷却筒烘干窑后冷却筒与项目烘干窑对接,烘干后的铁鳞直接进入冷却筒进行冷却处理。
永磁铁氧体预烧料的加工工艺及方法

永磁铁氧体预烧料的加工工艺及方法永磁铁氧体预烧料的加工过程实际上是碳酸钡(BaCO3)或碳酸锶(SrCO3)与铁红(Fe2O3)经过高温下的固相反应充分生成六角形的铁氧体晶粒的过程。
固相反应是否完善、充分,晶粒形状是否完整,对材料的质量有很大影响。
同时预烧料的优劣在铁氧体磁铁的生产中至关重要,质量差的预烧料是无法生产出高性能铁氧体磁铁。
目前我们公司生产的铁氧体预烧料有:异方性锶料、等方性普通粒料、自动车料三种。
决定永磁铁氧体预烧料性能优劣主要有以下几个方面:○1材料○2配方○3工艺手段及控制方法一、材料在永磁铁氧体预烧料生产中首先要选择合适的原材料,选择时主要考虑:原料纯度、含杂质情况、原料化学活动性、颗粒度等几个方面。
1、铁红(Fe2O3):永磁铁氧体预烧料的主料,应选择纯度>97%以上,最好在98%以上。
目前我公司使用印度铁红有98.5%、98%、97.5%、96%四种,用量最大为97.5%铁红。
台湾铁红纯度98.5%、比利时铁红纯度99%。
2、碳酸钡(BaCO3)或碳酸锶(SrCO3):永磁铁氧体预烧料的主料,纯度应大于96%。
最好大于98%以上。
目前我公司使用为纯度97%。
3、添加剂:在预烧时增加添加剂主要目的是为了改善材料的结构灵敏度,弥补某一特性。
永磁铁氧体常用的添加剂有:SiO2、CaCO3、SrSO4等,具体作用在配方中再做介绍。
4、含杂质情况:杂质含量中二氧化硅(SiO2)含量应该在0.5%以下,最好在0.1%以下。
氯离子含量最好在0.15%以下(此杂质对铁氧体性能影响很大,直接影响产品收缩率、反应气氛,应在烧结低温部分将其挥发排除)。
5、化学活动性:就铁红、铁磷、铁矿砂三种生产永磁铁氧体原料而言,铁红的化学活动性优于其他两种。
我公司目前全部使用铁红生产,另外纯度大的铁红化学活动性优于纯度小的铁红。
4、颗粒度:原料的粒度最好在1um以下,颗粒度太大往往影响固相反应的充分发生。
5、原料密度:原料的压密程度(密度)同样对预烧料的烧结有较大影响,密度大的铁红在混料过程中更加容易混料均匀、铁红与碳酸锶能充分接触;预烧过程中会增加铁氧体的生成比例。
永磁铁氧体预烧料的加工工艺及方法
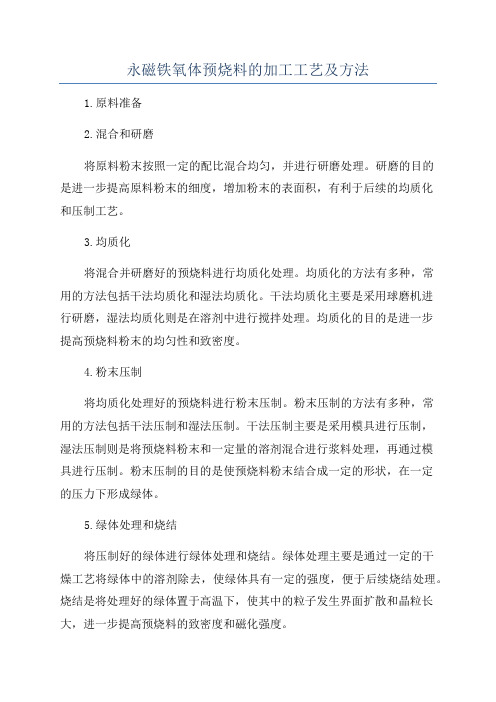
永磁铁氧体预烧料的加工工艺及方法1.原料准备2.混合和研磨将原料粉末按照一定的配比混合均匀,并进行研磨处理。
研磨的目的是进一步提高原料粉末的细度,增加粉末的表面积,有利于后续的均质化和压制工艺。
3.均质化将混合并研磨好的预烧料进行均质化处理。
均质化的方法有多种,常用的方法包括干法均质化和湿法均质化。
干法均质化主要是采用球磨机进行研磨,湿法均质化则是在溶剂中进行搅拌处理。
均质化的目的是进一步提高预烧料粉末的均匀性和致密度。
4.粉末压制将均质化处理好的预烧料进行粉末压制。
粉末压制的方法有多种,常用的方法包括干法压制和湿法压制。
干法压制主要是采用模具进行压制,湿法压制则是将预烧料粉末和一定量的溶剂混合进行浆料处理,再通过模具进行压制。
粉末压制的目的是使预烧料粉末结合成一定的形状,在一定的压力下形成绿体。
5.绿体处理和烧结将压制好的绿体进行绿体处理和烧结。
绿体处理主要是通过一定的干燥工艺将绿体中的溶剂除去,使绿体具有一定的强度,便于后续烧结处理。
烧结是将处理好的绿体置于高温下,使其中的粒子发生界面扩散和晶粒长大,进一步提高预烧料的致密度和磁化强度。
6.后处理将烧结好的永磁铁氧体进行针对性的后处理。
后处理的方法有多种,常用的方法包括磨削、磨抛、镀和包覆等。
后处理的目的是进一步提高永磁铁氧体的表面光洁度和耐腐蚀性,提高其使用寿命和性能稳定性。
综上所述,永磁铁氧体预烧料的加工工艺包括原料准备、混合和研磨、均质化、粉末压制、绿体处理和烧结以及后处理等步骤。
每个步骤都对于最终的永磁铁氧体性能具有重要影响,因此在实际加工过程中需要科学合理地控制每个步骤的工艺参数,并不断优化工艺流程,以提高预烧料的致密度和磁化强度。
烧结永磁铁氧体的生产流程

烧结永磁铁氧体的生产流程烧结永磁铁氧体是一种常用的永磁材料,具有高磁导率和良好的磁性能。
它广泛应用于电机、发电机、传感器等领域。
下面将介绍烧结永磁铁氧体的生产流程。
1. 原料准备烧结永磁铁氧体的主要原料包括氧化铁、氧化钡、氧化钴、氧化镨等。
这些原料需要进行粉碎、混合和筛分,确保粒度均匀一致。
2. 成型将混合后的原料通过成型机械进行成型。
常用的成型方式有压制和注塑。
压制是将原料粉末放入模具中,施加高压使其成型。
注塑则是将原料粉末与有机物混合,通过注射机将混合物注入模具中。
3. 烧结成型后的永磁铁氧体坯体需要进行烧结处理。
烧结是将坯体放入高温炉中,在一定的温度和气氛条件下进行加热处理。
烧结的目的是使粉末颗粒发生颗粒与颗粒之间的结合,形成致密的块状材料。
4. 磨削和加工经过烧结处理后的永磁铁氧体坯体需要进行磨削和加工。
磨削是将坯体表面进行抛光,使其表面光滑。
加工则是根据具体产品要求进行切割、钻孔等加工工序。
5. 磁化磨削和加工后的永磁铁氧体需要进行磁化处理。
磁化是将材料置于强磁场中,使其具有一定的磁性。
磁化可以通过电流磁化和恒温磁化两种方式进行。
6. 检测和质量控制生产过程中需要对烧结永磁铁氧体进行检测和质量控制。
常用的检测方法包括磁性测试、化学成分分析、显微结构观察等。
通过这些检测方法可以确保产品的质量符合要求。
7. 成品包装和储存经过检测合格的烧结永磁铁氧体需要进行包装和储存。
常用的包装方式有真空包装、防潮包装等。
包装完毕后,成品需要存放在干燥、通风的仓库中,避免湿气和腐蚀物质对产品的影响。
烧结永磁铁氧体的生产流程包括原料准备、成型、烧结、磨削和加工、磁化、检测和质量控制以及成品包装和储存等环节。
通过严格的生产流程和质量控制,可以生产出高质量的烧结永磁铁氧体,满足不同领域的需求。
干湿法永磁铁氧体预烧料的生产方法[发明专利]
![干湿法永磁铁氧体预烧料的生产方法[发明专利]](https://img.taocdn.com/s3/m/0aebb32f08a1284ac9504321.png)
专利名称:干湿法永磁铁氧体预烧料的生产方法专利类型:发明专利
发明人:邱新明
申请号:CN201210267113.9
申请日:20120730
公开号:CN103172387A
公开日:
20130626
专利内容由知识产权出版社提供
摘要:本发明涉及一种干湿法永磁铁氧体预烧料的生产方法,其特征在于,包括以下步骤:(1)铁红原料焙烧处理;(2)混料湿磨;(3)脱水;(4)烘干;(5)震动粉碎;(6)预加水后造球烧结;(7)冷却并粗粉碎。
本发明所述的方法生产的永磁铁氧体预烧料的磁性能达到了FB6H的水平,而在永磁铁氧体预烧料内添加少量La(镧)Co(钴)后可将磁性能做到日本TDK公司的FB9系列以上水平,且本发明生产的产品的产量在以湿法为基础的相同规格生产线相比可提高40%左右,能源消耗可降低50%,产生的经济效益可提高2-3倍。
申请人:江苏熙友磁电科技有限公司
地址:214211 江苏省无锡市宜兴市和桥镇鹅洲南路
国籍:CN
代理机构:南京纵横知识产权代理有限公司
更多信息请下载全文后查看。
- 1、下载文档前请自行甄别文档内容的完整性,平台不提供额外的编辑、内容补充、找答案等附加服务。
- 2、"仅部分预览"的文档,不可在线预览部分如存在完整性等问题,可反馈申请退款(可完整预览的文档不适用该条件!)。
- 3、如文档侵犯您的权益,请联系客服反馈,我们会尽快为您处理(人工客服工作时间:9:00-18:30)。
永磁铁氧体预烧料的生产工艺是怎样的
以优质铁鳞为原料,采用链篦机——回转窑干法生产工艺,生产Y30H-1型锶永磁铁氧体预烧料。
经过烘干、球磨后的铁鳞,与一定配比的碳酸锶、高岭土进行配料、强混、造球后,送入链篦机进行烘干、氧化处理。
链篦机采用回转窑的尾气对物料进行烘干,以及将物料中的FeO氧化为Fe2O3,将物料中三氧化二铁的成份进行大比例的提高。
完成链篦机烘干、氧化后的球状物料,送入回转窑经过1200℃进行高温煅烧处理。
在回转窑中,物料中的碳酸锶和碳酸钙会在高温中发生分解反应,然后再与Fe2O3生成产品——SrO(Fe2O3)6。
项目生产过程中发生的化学反应如下:
链篦机中的氧化反应:4FeO +O2 = 2Fe2O3?
回转窑中的分解反应:SrCO3 =(高温)SrO+CO2↑
回转窑中产品的生成反应:SrO+ 6Fe2O3=(高温)SrO(Fe2O3) 6
1、原料来源
铁鳞由汽车运输至本项目厂区铁鳞堆场进行散放堆存。
项目外购的袋装碳酸锶、高岭土全部在车间内暂存库房内堆存。
2、原料处理
项目需要对铁鳞进行初步筛分、烘干、冷却、球磨机初磨、配料、配料后强混球磨等工段,为项目三条生产线提供合格的原材料。
具体处理步骤如下:
(1)铁鳞筛分
项目铁鳞堆场内设置了一台孔径为75px的粗筛,除去铁鳞中较大的杂质。
根据现场勘查,筛除的杂质主要为热轧厂铁鳞沉淀池中混杂的砖头、废弃角钢等固废。
(2)铁鳞烘干窑烘干
经过筛分后的合格铁鳞经3m高的斗提机输送至烘干窑中,通入煤气燃耗后进行烘干处理,将含水率为10%的铁鳞烘干到含水1%左右。
斗提机进料口,会产生车间粉尘(G1),采用集气罩收集后送入SMC4-30型布袋除尘器处理,除尘系统回收的粉尘送强混球磨机进行研磨。
烘干过程中将产生烘干烟气(G2),主要污染物为粉尘。
烘干烟气经烟气管道收集送旋风除尘系统处理,除尘系统回收的粉尘送强混球磨机进行研磨。
(3)铁鳞烘干窑后冷却筒
烘干窑后冷却筒与项目烘干窑对接,烘干后的铁鳞直接进入冷却筒进行冷却处理。
冷却筒通过对筒体喷淋水进行间接冷却,冷却废水(W1)经冷却水收集槽、收集管道收集后,送循环水处理站处理后循环使用。
冷却筒后出料口会产生粉尘(G3),由集气罩收集后送入SMC4-30型布袋除尘器处理,除尘系统回收的粉尘送强混球磨机进行研磨。
(4)铁鳞冷却后物料输入工段
铁鳞冷却后,经螺旋输送机送至5m高的斗提机下端,由斗提机送至容量为100t的铁鳞料仓暂存,铁鳞料仓为密闭状态。
斗提机下端进料口会产生粉尘(G4),由集气罩收集后送入SMC4-30型布袋除尘器处理,除尘系统回收的粉尘送强混球磨机进行研磨。
(5)铁鳞球磨
来自铁鳞料仓的铁鳞经密闭进料管道进入铁鳞球磨机进行研磨处理,将铁鳞研磨为粒径在30μm左右的细微粉末。
铁鳞球磨机研磨后的粉料,经过人工手推车装料后运输,并配以电动行车输送至铁鳞粉料仓。
铁鳞球磨机进、出料口会产生粉尘(G5),由集气罩收集后送入SMC4-30型布袋除尘器处理,除尘系统回收的粉尘送强混球磨机进行研磨。
(6)配料、强混球磨
来自铁鳞粉料仓的铁鳞粉、碳酸锶、高岭土分别进入混料机进行混料处理。
为保证铁鳞、碳酸锶及高岭土均匀混合。
项目将配料完成后的物料,由封闭式螺旋输送机送至强混球磨机进行强混磨,并细磨到粒径小于或等于20μm级别。
完成强混球磨工段后,项目原料工序提供的物料由人工手推车装料运输,并配以电动行车输送至三条生产线的高位料仓暂存。
配料机进料口会产生车间粉尘(G6),强混球磨机进出料口都会产生粉尘(G7),三条生产线的三个高位料仓在进料时会产生粉尘(G8)。
在上述三个产尘源分别加设集气罩,收集后的废气送入SMC4-30型布袋除尘器处理,除尘系统回收的粉尘送强混球磨机进行研磨。
3、造球工序
项目三条生产线的原料料仓,分别由各个生产线的螺旋输送机送至造球机加水(水料配比为13:100)湿润后造球。
4、煅烧工序
主要包括链篦机烘干、氧化处理工段,及回转窑煅烧工段。
(1)链篦机工段
三条生产线中,完成造球后的物料,由各个生产线的斗提机送至链篦机进行烘干氧化处理。
造球完成后的球状物料中含有一定量的FeO,链篦机采用回转窑的尾气对物料进行烘干,以及将物料中的FeO氧化为Fe2O3,将物料中三氧化二铁的成份进行大比例的提高。
此反应过程中所需的氧由引风机引入空气提供。
每条生产线中的链篦机会产生含尘烟气(G9),1#主厂房内2台链篦机烟气分别进入2套旋风除尘系统进行处理后通过35m高的排气筒排放,2#主厂房内1台链篦机烟气进入1套布袋除尘器处理后通过35m高的排气筒(与1#主厂房同一根)排放,回收的烟尘返回强混球磨机进行研磨。
(2)回转窑煅烧工段
三条生产线中,每条线中的链篦机与回转窑无缝对接,经过链篦机处理后的物料直接进入回转窑中,通入煤气在1200℃左右的高温下进行煅烧,煅烧时间约为6小时。
回转窑煅烧过程中,SrCO3先被分解为SrO和CO2,然后SrO在高温条件下与Fe2O3生成SrO(Fe2O3)6。
回转窑煅烧过程中会有CO2废气产生。
回转窑烟气返回链篦机。
5、半成品螺旋冷却筒冷却工段
三条生产线中,煅烧后的半成品由密封料槽直接送至螺旋冷却筒冷却(两设备之间高差1.5m),冷却筒通过筒体喷淋水冷却,冷却废水(W2)经冷却水收集槽、收集管道收集后,送循环水处理站处理后循环使用。
6、成品球磨
三条生产线中,螺旋冷却筒直接与成品球磨机进料口无缝对接,完成煅烧工序后的球状物料直接球磨机进行研磨处理,并细磨到粒径为21~50μm级别。
研磨后的成品由人工手推车运输,并配以电动行车输送至成品料仓暂存。
由于本项目成品自身比重大(4.1~4.3g/cm3),成品中的高岭土起到了很好的粘结剂的作用。
因此,项目成品球磨过程中不易起尘。
7、成品检验及包装入库
在三条生产线中,研磨后的产品通过检测,合格产品经自动称量、包装机进行成品包装,由于本项目成品自身比重大(4.1~4.3g/cm3),成品中的高岭土起到了很好的粘结剂的作用,再加上成品装袋工序采用了密封口自动装袋方式,因此也不会大量起尘。