烟气循环流化床(CFB-FGD)干法脱硫工艺
烟气循环流化床(CFB-FGD)干法脱硫优化调整

C HE N L i a,S HI Ho n g ,Z HANG Yi n g
( H u b e i E l e c t r i c P o w e r R e s e a r c h I n s t i t u t e , Wu h a n 4 3 0 0 7 7 , C h i n a )
艺 。在 这 种形 势下 ,干 法脱硫 工 艺应运 而 生 。
吸 收塔 ,在 此处 高温 烟气 与加 入 的吸收 剂 、循 环脱 硫灰 充分 预混合 ,进 行初 步 的脱硫 反应 ,然 后通 过 吸 收塔底部 的文丘里 管 的加速 ,吸收剂 、循 环脱 硫
灰受 到气 流 的 冲击 作 用 而 悬 浮起 来 ,形 成 流 化 床 ,
f e si a b i l i t y o f o p i t iz m a i t o n nd a a d j u s t m e n t d u r i n g t h e r u n n i n g p r o c e s s f o C F B — F G D s y s t e m.
1 概 述
火 电厂排 放 的二 氧 化硫形 成 的酸雨 已严 重危 害
的 区别 就在 于其所 使 用 的脱 硫 剂是 以干 粉形 态进 入 吸收 塔 ,而 非像 湿法 脱硫一 样使 用 吸收 剂 的浆液 进 行脱 硫 。C F B - F G D基 本工 艺原 理 为 :
火力发电循环流化床半干法脱硫技术简介
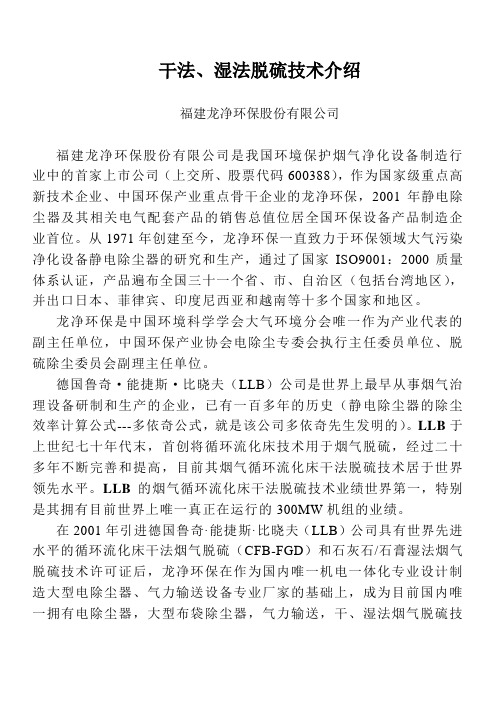
干法、湿法脱硫技术介绍福建龙净环保股份有限公司福建龙净环保股份有限公司是我国环境保护烟气净化设备制造行业中的首家上市公司(上交所、股票代码600388),作为国家级重点高新技术企业、中国环保产业重点骨干企业的龙净环保,2001年静电除尘器及其相关电气配套产品的销售总值位居全国环保设备产品制造企业首位。
从1971年创建至今,龙净环保一直致力于环保领域大气污染净化设备静电除尘器的研究和生产,通过了国家ISO9001:2000质量体系认证,产品遍布全国三十一个省、市、自治区(包括台湾地区),并出口日本、菲律宾、印度尼西亚和越南等十多个国家和地区。
龙净环保是中国环境科学学会大气环境分会唯一作为产业代表的副主任单位,中国环保产业协会电除尘专委会执行主任委员单位、脱硫除尘委员会副理主任单位。
德国鲁奇·能捷斯·比晓夫(LLB)公司是世界上最早从事烟气治理设备研制和生产的企业,已有一百多年的历史(静电除尘器的除尘效率计算公式---多依奇公式,就是该公司多依奇先生发明的)。
LLB于上世纪七十年代末,首创将循环流化床技术用于烟气脱硫,经过二十多年不断完善和提高,目前其烟气循环流化床干法脱硫技术居于世界领先水平。
LLB的烟气循环流化床干法脱硫技术业绩世界第一,特别是其拥有目前世界上唯一真正在运行的300MW机组的业绩。
在2001年引进德国鲁奇·能捷斯·比晓夫(LLB)公司具有世界先进水平的循环流化床干法烟气脱硫(CFB-FGD)和石灰石/石膏湿法烟气脱硫技术许可证后,龙净环保在作为国内唯一机电一体化专业设计制造大型电除尘器、气力输送设备专业厂家的基础上,成为目前国内唯一拥有电除尘器,大型布袋除尘器,气力输送,干、湿法烟气脱硫技术研发、设计、制造、安装综合服务能力的高水平的专业环保企业。
一.烟气循环流化床(CFB-FGD)干法脱硫工艺1.工艺描述1.1工艺流程从工艺流程图表明(见图1):一个典型的CFB-FGD系统由吸收塔、除尘器、吸收剂制备系统、物料输送系统、喷水系统、脱硫灰输送及存储系统、电气控制系统等构成。
简述几种(半)干法工艺原理及特点
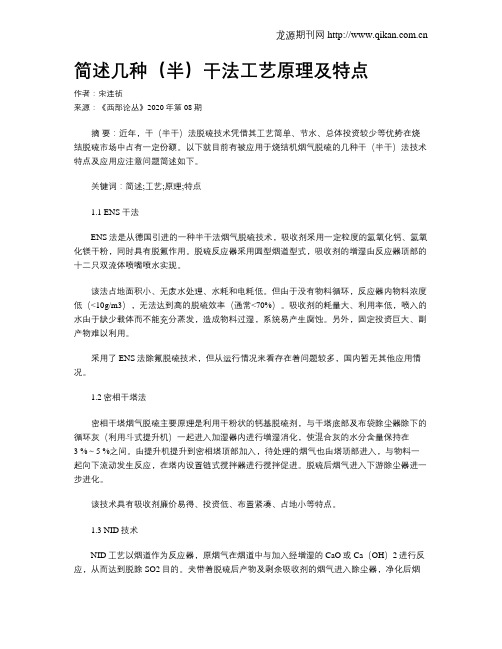
简述几种(半)干法工艺原理及特点作者:宋连祯来源:《西部论丛》2020年第08期摘要:近年,干(半干)法脱硫技术凭借其工艺简单、节水、总体投资较少等优势在烧结脱硫市场中占有一定份额。
以下就目前有被应用于烧结机烟气脱硫的几种干(半干)法技术特点及应用应注意问题简述如下。
关键词:简述;工艺;原理;特点1.1 ENS干法ENS法是从德国引进的一种半干法烟气脱硫技术,吸收剂采用一定粒度的氢氧化钙、氢氧化镁干粉,同时具有脱氟作用。
脱硫反应器采用圆型烟道型式,吸收剂的增湿由反应器顶部的十二只双流体喷嘴喷水实现。
该法占地面积小、无废水处理、水耗和电耗低。
但由于没有物料循环,反应器内物料浓度低(<10g/m3),无法达到高的脱硫效率(通常<70%)。
吸收剂的耗量大、利用率低,喷入的水由于缺少载体而不能充分蒸发,造成物料过湿,系统易产生腐蚀。
另外,固定投资巨大、副产物难以利用。
采用了ENS法除氟脱硫技术,但从运行情况来看存在着问题较多,国内暂无其他应用情况。
1.2密相干塔法密相干塔烟气脱硫主要原理是利用干粉状的钙基脱硫剂,与干塔底部及布袋除尘器除下的循环灰(利用斗式提升机)一起进入加湿器内进行增湿消化,使混合灰的水分含量保持在3 %~5 %之间。
由提升机提升到密相塔顶部加入,待处理的烟气也由塔顶部进入,与物料一起向下流动发生反应,在塔内设置链式搅拌器进行搅拌促进。
脱硫后烟气进入下游除尘器进一步进化。
该技术具有吸收剂廉价易得、投资低、布置紧凑、占地小等特点。
1.3 NID技术NID工艺以烟道作为反应器,原烟气在烟道中与加入经增湿的CaO或Ca(OH)2进行反应,从而达到脱除 SO2目的。
夹带着脱硫后产物及剩余吸收剂的烟气进入除尘器,净化后烟气经烟囱排放,除尘器收集的脱硫灰除部分外排至脱硫灰仓外,大部分经增湿器随新鲜吸收剂返回反应器中,提高了吸收剂的利率。
NID是移动输送床技术,是一种简易的采用烟道作为反应器的烟气脱硫工艺,混合了水的消石灰、脱硫灰在烟道反应器内的停留时间只有1秒左右,因此,脱硫效率较低(一般低于70%)。
烟气循环流化床脱硫CFB-FGD技术使用简介

锅炉的两个装置的基本情况。
2.烟气CFB脱硫工艺简介
无论是Lurgi公司的CFB工艺, Wulff公司的RCFB工艺还是F.L. Smith的GSA工艺,它们在工作原理上都是很类似的。因此我们以Lurgi公司的CFB工艺为基础对烟气CFB脱硫工艺作简单的介绍。
要一台干消化器用来制备消石灰粉,然后用空气斜槽进行输送就可以了,从而
大大简化了工艺流程。
在各种负荷条件下,CFB烟气脱硫系统都能很好地适应.当负荷从100%变化到10%,系统称仍能很好地工作,这使得CFB工艺既能由于调峰机组,又能用于带基本负荷的机组。
CFB工艺所产生的脱硫副产品呈干粉状,非常便于处置。其化学组成与喷雾干燥工艺的副产品相类似,主要CaSO3、CaSO4以及未反应完的吸收剂(Ca(OH)2)等构成。脱硫副产品中是否含有大量的飞灰,则取决于在CFB烟气脱硫系统强是否安装了前级除尘器。CFB烟气脱硫系统的脱硫副产品的处置方法也与喷雾干燥的副产品基本相同。CFB工艺的副产品在加水后会硬化,硬化后的屈服强度可达15-18N/mm2,压实密度为1.28g/cm3,而其渗透率则与黏土类似,约为3X10-11。由此可见该副产品的强度与混凝土接近,很适合作矿井回填、道路基础。如能进一步加以开发,可能成为良好的建材工业的原料。
德国Wulff公司是一个成立较晚的设计和建造烟气CFB脱硫工程的小型企业。它的创始人R. Graf原是Lurgi公司在烟气CFB脱硫技术开发方面的主要负责人。脱离Lurgi公司后自建了Wulff公司,专门从事烟气CFB脱硫技术的开发工作,在Lurgi技术的基础上开发研制了一种叫做回流式烟气循环流化床的烟气CFB脱硫技术,对烟气CFB脱硫技术作了较大的改进,使之更加适用于动力工业(详见后)。
循环流化床烟气脱硫工艺
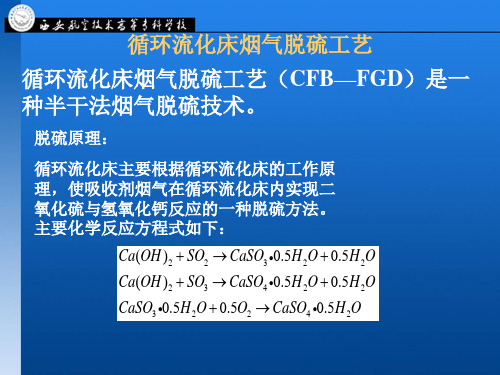
吊顶是现代家庭装修常见的装饰手法。 吊顶既具有美化空间的作用,也是区分室 内空间一种方法。很多情况下,室内空间不能 通过墙体、隔断来划分,那样就会让空间显得 很拥挤,很局促。设计上可以通过天花与地面 来对室内空间进行区分,而天花所占的比例又 很大。吊顶材料可以分为面板和架构龙骨。吊 顶面板分为普通石膏板和防水防潮类面板。龙 骨分为金属龙骨与木龙骨。
现代房产大多是清水房,因此家庭装修的 一个很大的项目就是包门窗套、安装室内门。 中国过去的房子,大多以实用为主,随着室内 装饰的兴起,人们越来越关注房屋空间的美化 和装饰。因此,在门框的基础上,发展成为门 套,即将安装门后剩余的墙壁给包起来,一则 美观漂亮,二则起到对墙壁的保护作用。
2.对已建电厂典型的CFD-FGD工艺布置方式:
1.对新建电厂典型的CFD-FGD工艺布置方 式:
锅炉空气预热器 一级除尘 循环流化床吸收 塔 脱硫除尘器 引风机 烟囱。
一级除尘的目的是:可回收部分经济效益 高的粉煤灰‘减少脱硫灰量。效率可达 70%~90%。
• 在CFD-FGD工艺布置中。通常有以下两 种情况:
• 场地较宽裕时:一级除尘器两个进出口, 吸收塔一个进出口,二级(脱硫除尘器) 两个进出口,或引风机布置在二级除尘 器与引风机之间。
典型工艺系统流程
一个典型的循环流化床烟气脱硫系统是由预除尘 器、吸收剂制备、脱硫塔、脱硫灰再循环、注 水系统、脱硫除尘器以及仪表控制系统等组成。
影响系统脱硫效率的主要因素
• 床料循环倍率 • 流化床床料浓度(一般在5~塔操作温度
CFD-FGD工艺布置
本章小结
干法脱硫工艺
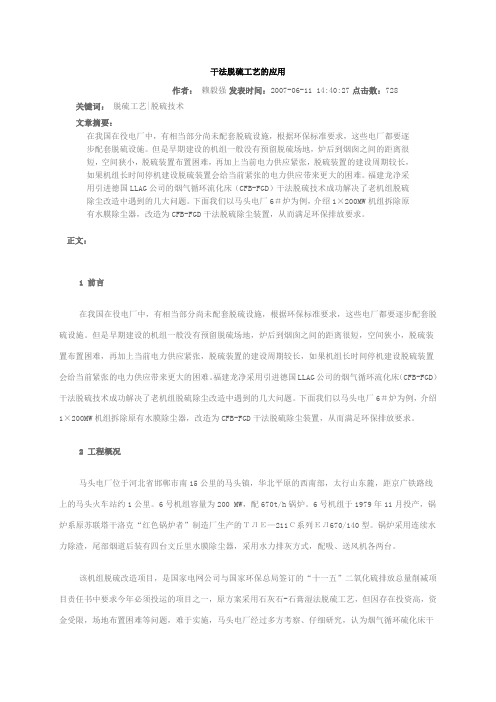
干法脱硫工艺的应用作者:赖毅强发表时间:2007-06-11 14:40:27 点击数:728 关键词:脱硫工艺|脱硫技术文章摘要:在我国在役电厂中,有相当部分尚未配套脱硫设施,根据环保标准要求,这些电厂都要逐步配套脱硫设施。
但是早期建设的机组一般没有预留脱硫场地,炉后到烟囱之间的距离很短,空间狭小,脱硫装置布置困难,再加上当前电力供应紧张,脱硫装置的建设周期较长,如果机组长时间停机建设脱硫装置会给当前紧张的电力供应带来更大的困难。
福建龙净采用引进德国LLAG公司的烟气循环流化床(CFB-FGD)干法脱硫技术成功解决了老机组脱硫除尘改造中遇到的几大问题。
下面我们以马头电厂6#炉为例,介绍1×200MW机组拆除原有水膜除尘器,改造为CFB-FGD干法脱硫除尘装置,从而满足环保排放要求。
正文:1 前言在我国在役电厂中,有相当部分尚未配套脱硫设施,根据环保标准要求,这些电厂都要逐步配套脱硫设施。
但是早期建设的机组一般没有预留脱硫场地,炉后到烟囱之间的距离很短,空间狭小,脱硫装置布置困难,再加上当前电力供应紧张,脱硫装置的建设周期较长,如果机组长时间停机建设脱硫装置会给当前紧张的电力供应带来更大的困难。
福建龙净采用引进德国LLAG公司的烟气循环流化床(CFB-FGD)干法脱硫技术成功解决了老机组脱硫除尘改造中遇到的几大问题。
下面我们以马头电厂6#炉为例,介绍1×200MW机组拆除原有水膜除尘器,改造为CFB-FGD干法脱硫除尘装置,从而满足环保排放要求。
2 工程概况马头电厂位于河北省邯郸市南15公里的马头镇,华北平原的西南部,太行山东麓,距京广铁路线上的马头火车站约1公里。
6号机组容量为200 MW,配670t/h锅炉。
6号机组于1979年11月投产,锅炉系原苏联塔干洛克“红色锅炉者”制造厂生产的ТЛЕ—211С系列ЕЛ670/140型。
锅炉采用连续水力除渣,尾部烟道后装有四台文丘里水膜除尘器,采用水力排灰方式,配吸、送风机各两台。
CFB系列循环流化床烟气脱硫系统

CFB系列循环流化床烟气脱硫系统系统简介循环流化床烟气脱硫技术(Circulating Fluidized Bed Flue Gas Desulfurization,简称CFB-FGD),采用消石灰或石灰作为脱硫剂。
CFB系列循环流化床烟气脱硫装置是国电南自自主开发的干法脱硫装置,该技术国电南自具有自主知识产权,循环流化床烟气脱硫技术(简称CFB-FGD),是采用消石灰或石灰作为脱硫剂,安装在空气预热器和除尘器之间。
工艺原理与工艺流程循环流化床烟气脱硫技术,在空气预热器和除尘器之间安装循环流化床系统,烟气从流化床反应器下部布风板进入反应器,与消石灰颗粒充分混合,SO2、SO3及其它有害气体,如HCl、HF等与消石灰发生反应,生成CaSO3·1/2H2O、CaSO4·1/2H2O和CaCO3等。
反应器内的脱硫剂呈悬浮的流化状态,反应表面积大,传热/传质条件很多,且颗粒之间不断碰撞、反应。
随后夹带着大量粉尘的烟气进入除尘器中,被除尘器收集下来的固体颗粒大部分又返回流化床反应器中,继续参加脱硫反应过程,同时循环量可以根据负荷进行调节。
由于脱硫剂在反应器内滞留时间长,因此使得脱硫效果和吸收剂的利用率大大提高。
另外,工业水用喷嘴喷入反应器下部,以增加烟气湿度降低烟温,从而提高了脱硫效率。
循环流化床烟气脱硫系统主要包括给料系统、反应器系统、物料循环系统、喷水系统、旁路烟道。
技术特点★ 脱硫系统流程简单、占地面积较少。
★ 脱硫工艺适用于已确定的煤种条件并适应燃煤含硫量在一定范围内可能的变动;可满足锅炉负荷从30%到120%范围内变化。
★ 系统运行费用低。
★ 采用易于取得且价廉的石灰石或消石灰作为脱硫剂,且在较低的钙硫比下(钙硫比为1.1~1.2),脱硫效率可达90%以上,系统运行费用低。
★ 采用具有自主产权的干式消化器,保证了脱硫剂的活性。
★ 由于脱硫剂的给料及硫化产物均为干态,设备不存在腐蚀现象。
循环流化床烟气脱硫技术
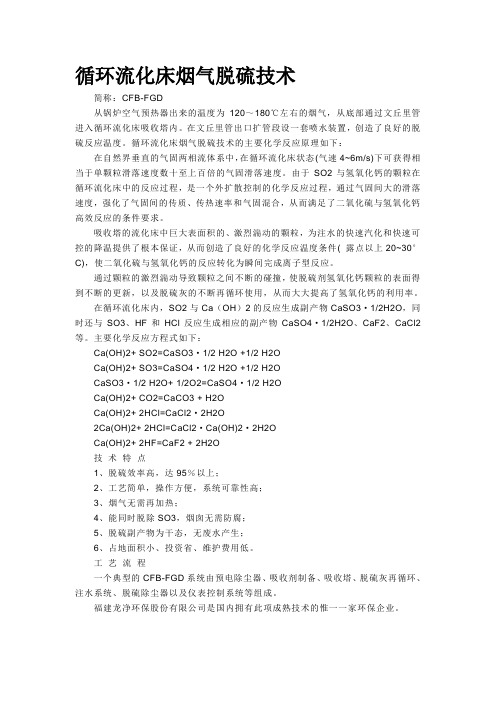
循环流化床烟气脱硫技术简称:CFB-FGD从锅炉空气预热器出来的温度为120~180℃左右的烟气,从底部通过文丘里管进入循环流化床吸收塔内。
在文丘里管出口扩管段设一套喷水装置,创造了良好的脱硫反应温度。
循环流化床烟气脱硫技术的主要化学反应原理如下:在自然界垂直的气固两相流体系中,在循环流化床状态(气速4~6m/s)下可获得相当于单颗粒滑落速度数十至上百倍的气固滑落速度。
由于SO2与氢氧化钙的颗粒在循环流化床中的反应过程,是一个外扩散控制的化学反应过程,通过气固间大的滑落速度,强化了气固间的传质、传热速率和气固混合,从而满足了二氧化硫与氢氧化钙高效反应的条件要求。
吸收塔的流化床中巨大表面积的、激烈湍动的颗粒,为注水的快速汽化和快速可控的降温提供了根本保证,从而创造了良好的化学反应温度条件( 露点以上20~30°C),使二氧化硫与氢氧化钙的反应转化为瞬间完成离子型反应。
通过颗粒的激烈湍动导致颗粒之间不断的碰撞,使脱硫剂氢氧化钙颗粒的表面得到不断的更新,以及脱硫灰的不断再循环使用,从而大大提高了氢氧化钙的利用率。
在循环流化床内,SO2与Ca(OH)2的反应生成副产物CaSO3·1/2H2O,同时还与SO3、HF和HCl反应生成相应的副产物CaSO4·1/2H2O、CaF2、CaCl2等。
主要化学反应方程式如下:Ca(OH)2+ SO2=CaSO3·1/2 H2O +1/2 H2OCa(OH)2+ SO3=CaSO4·1/2 H2O +1/2 H2OCaSO3·1/2 H2O+ 1/2O2=CaSO4·1/2 H2OCa(OH)2+ CO2=CaCO3 + H2OCa(OH)2+ 2HCl=CaCl2·2H2O2Ca(OH)2+ 2HCl=CaCl2·Ca(OH)2·2H2OCa(OH)2+ 2HF=CaF2 + 2H2O技术特点1、脱硫效率高,达95%以上;2、工艺简单,操作方便,系统可靠性高;3、烟气无需再加热;4、能同时脱除SO3,烟囱无需防腐;5、脱硫副产物为干态,无废水产生;6、占地面积小、投资省、维护费用低。
“循环流化床吸收塔(CFB-FGD)”工艺进行烟气脱硫技术

“循环流化床吸收塔( CFB-FGD)”工艺进行烟气脱硫技术摘要:干法烟气脱硫装置所采用的技术是在引进国外先进的干法脱硫工艺循环流化床干法烟气脱硫(CFB-FGD)技术的基础上经不断完善、改进,形成了适合我国国情的干法脱硫技术,它具有结构简单、运行可靠、脱硫效率高(大于90%)、投资小的特点。
循环流化床烟气干法脱硫技术是目前商业应用中单塔处理能力最大、脱硫综合效益最优越的唯一一种干法烟气脱硫技术。
关键词:干法烟气脱硫;循环流化床吸收塔(CFB-FGD);烟气脱硫技术脱硫反应塔内的气固最大滑落速度是否能在不同的烟气负荷下始终得以保持不变,是衡量一个循环流化床干法脱硫工艺先进与否的一个重要指标,也是一个鉴别干法脱硫能否达到较高脱硫率的一个重要指标。
喷入的用于降低烟气温度的水[1],以激烈湍动的、拥有巨大的表面积的颗粒作为载体,在塔内得到充分的蒸发,保证了进入后续除尘器中的灰具有良好的流动状态。
由于流化床中气固间良好的传热、传质效果[2],绝大部分SO2得以去除,加上排烟温度始终控制在高于露点温度20℃以上,因此排烟不需要再加热,同时系统无需采取特殊的防腐处理。
净化后的含尘烟气从吸收塔顶部侧向排出,然后转向进入脱硫除尘器[3],再通过引风机排入烟囱。
经除尘器捕集下来的固体颗粒,通过除尘器下的再循环系统,返回吸收塔继续参加反应,如此循环,多余的少量脱硫灰渣通过物料输送至脱硫灰仓内,再通过罐车运出厂外综合利用。
在循环流化床吸收塔中,Ca(OH)2与烟气中的SO2和几乎全部的SO3,HCl,HF等,完成化学反应,主要化学反应方程式如下:Ca(OH)2+ SO2=CaSO3·1/2 H2O +1/2 H2OCa(OH)2+ SO3=CaSO4·1/2 H2O +1/2 H2OCaSO3·1/2 H2O+ 1/2O2=CaSO4·1/2 H2OCa(OH)2+ CO2=CaCO3 + H2OCa(OH)2+ 2HCl=CaCl2·2H2O(~75℃)(强吸潮性物料)2Ca(OH)2+ 2HCl=CaCl2·Ca(OH)2·2H2O(>120℃)Ca(OH)2+ 2HF=CaF2 + 2H2O(从上述化学反应方程式可以看出,Ca(OH)2应尽量避免在75℃左右与HCl 反应)具有以下工艺及结构特点:1)去除重金属、有机污染物等有害物质利用吸附剂及塔内物料的巨大比表面积,使烟气中的重金属、有机污染物(主要是二噁英(PCDD)和呋喃(PCDF))等大部分被去除。
烟气循环流化床脱硫技术介绍

(1)采用流线型的底部进气结构,保证了吸收塔入口气流分布均匀 为了适应单塔处理大烟气量,必须采用多文丘里管的结构,采用多个文丘里管的
吸收塔,要求进入塔内的烟气流场分布较为均匀,否则因各个文丘里管流速差异较大, 可能导致固体颗粒物从某个喷嘴向下滑落。
为了解决布气不均匀造成塔内固体颗粒分布不均匀的问题,吸收塔进气方式采用 流线型的底部进气结构(见下图 1),避免了两股气流对撞产生涡流,从而保证了吸收 塔入口气流分布均匀。
1 发展历史
德国鲁奇能捷斯公司(LLAG)是世界上最早从事烟气治理设备研制和生产的企 业,已有一百多年的历史(静电除尘器的除尘效率计算公式——多依奇公式,就是该 公司的工程师多依奇先生发明的)。LLAG 在上世纪六十年代首先推出了循环流化床概 念,此后把循环流化床概念应用到四十多个不同的工艺。LLAG 于上世纪七十年代初, 在发明循环流化床锅炉的基础上,首创将循环流化床技术(CFB)用于工业烟气脱硫, 直至九十年代初,是世界上唯一拥有循环流化床干法脱硫技术的公司,经过三十多年 不断完善和提高,目前其烟气循环流化床干法脱硫技术居于世界领先水平。
3) 降低系统运行压降,吸收塔的压降由烟气压降和固体颗粒压降两部分组 成(见下图 3)。由于循环流化床内的固体颗粒浓度(或称固-气比)是保证流化 床良好运行的重要参数,在运行中只有通过控制吸收塔的压降来实现调节床内的固 -气比,以保证反应器始终处于良好的运行工况,从而保证了床内脱硫反应所需的 固体颗粒浓度。
(2) 吸收塔的流化床中巨大表面积的、激烈湍动的颗粒,为注水的快速汽化和
2
快速可控的降温提供了根本保证,从而创造了良好的化学反应温度条件(露点以上 20~30°C),使二氧化硫与氢氧化钙的反应转化为瞬间完成离子型反应,如果没有循环 流化床中大量颗粒的参与,注入的水需要数十倍的空间来完成水份充分的挥发。
脱硫脱硝除尘技术干法脱硫技术(CFB-FGD)

莱特莱德脱硫脱硝脱硫脱硝除尘技术—干法脱硫技术(CFB-FGD)半干法脱硫(CFB-FGD),该工艺分为二级脱硫:在炉膛内喷入石灰石粉脱除部分SO2;在锅炉尾部设置文丘里脱硫塔,并喷入增湿水,有工业污水系统可以直接利用,使未反应的石灰石粉进一步得以利用对烟气进行二次脱硫。
其特点是系统简单、投资小、电负荷低、无废水排放、占地面积也较少。
但是,由于其脱硫反应是在气固两相之间进行,受到传质过程的影响,反应速度较慢,吸收剂利用率较低。
当钙硫比控制在1.5-2.5时,经二级脱硫后,脱硫效率可达80%—90%左右。
烟气脱硫设备技术特点:(1)脱硫效率高:脱硫效率可达90%以上,是目前各种干法、半干法烟气脱硫工艺中最高的,可与湿法工艺相媲美;(2)工程投资费用、运行费用和脱硫成本较低,为湿法工艺的50%~70%。
(3)工艺流程简单,系统设备少,为湿法工艺的40%~50%,且转动部件少,降低了维护和检修费用;(4)占地面积小,为湿法工艺的30%~40%,且系统布置灵活,非常适合现有机组的改造和场地紧缺的新建机组。
(5)能源消耗低,如电耗、水耗等,为湿法工艺的30%~50%。
(6)能有效脱除SO3、氯化物和氟化物等有害气体,其脱除效率远高于湿法工艺,达90%~99%,腐蚀性较小,可不采用烟气再热器,直接使用干烟囱排放烟气。
(7)对锅炉负荷变化的适用性强,负荷跟踪特性好,启停方便,可在30%负荷时投用,对基本负荷和调峰机组均有很好的适用性。
(8)对燃煤硫分的适应性强,可用于0.3%~6.5%的燃煤硫分。
且应用于中低硫煤时(<2%),其经济性优于湿法工艺。
(9)无脱硫废水排放,且脱硫副产品呈干态,不会造成二次污染,对综合利用和处置堆放有利。
烟气循环流化床(CFB-FGD)干法脱硫工艺

烟气循环流化床(CFB-FGD)干法脱硫工艺
gaojilu 发表于2006-2-20 20:40:31
工艺流程
从工艺流程图表明一个典型的 CFB-FGD 系统由吸收塔、除尘器、吸收剂制备系统、物料输送系统、喷水系统、脱硫灰输送及存储系统、电气控制系统等构成。
来自锅炉的空气预热器出来的烟气温度一般为 120~180℃左右,通过一级除尘器(当脱硫渣与粉煤灰须分别处理时),从底部进入吸收塔,在此处高温烟气与加入的吸收剂、循环脱硫灰充分预混合,进行初步的脱硫反应,然后通过吸收塔底部的文丘里管的加速,吸收剂、循环脱硫灰受到气流的冲击作用而悬浮起来,形成流化床,进行第二步充分的脱硫反应。
在这一区域内流体处于激烈的湍动状态,循环流化床内的Ca/S值可达到40~50,颗粒与烟气之间具有很大的滑落速度,颗粒反应界面不断摩擦、碰撞更新,极大地强化了脱硫反应的传质与传热。
在文丘里出口扩管段设一套喷水装置,喷入的雾化水一是增湿颗粒表面,二是使烟温降至高于烟气露点20℃左右,创造了良好的脱硫反应温度,吸收剂在此与SO2充分反应,生成副产物CaSO3·1/2H2O,还与SO3、HF和HCl 反应生成相应的副产物CaSO4·1/2H2O、CaF2、CaCl2等。
净化后的含尘烟气从吸收塔顶部侧向排出,然后进入脱硫除尘器(可根据需要选用布袋除尘器或电除尘器),通过引风机排入烟囱。
由于排烟温度高于露点温度20℃左右,因此烟气不需要再加热,同时整个系统无须任何的防腐。
经除尘器捕集下来的固体颗粒,通过再循环系统,返回吸收塔继续反应,如此循环,少量脱硫灰渣通过物料输送至灰仓,最后通过输送设备外排。
CFB-FGD烟气脱硫、脱硝、调质
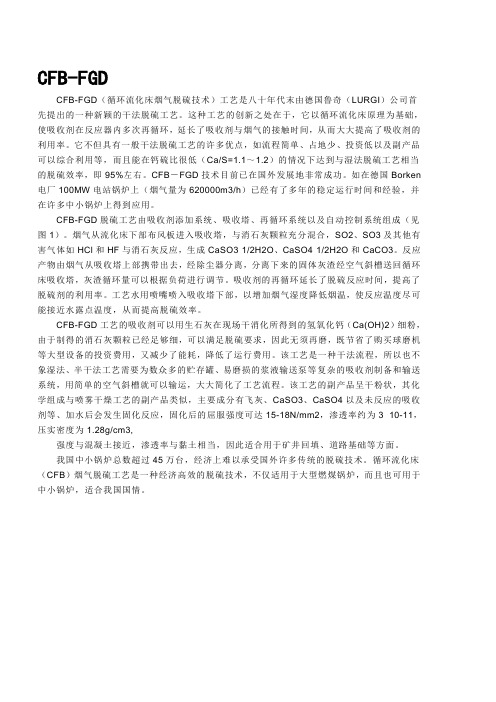
CFB-FGDCFB-FGD(循环流化床烟气脱硫技术)工艺是八十年代末由德国鲁奇(LURGI)公司首先提出的一种新颖的干法脱硫工艺。
这种工艺的创新之处在于,它以循环流化床原理为基础,使吸收剂在反应器内多次再循环,延长了吸收剂与烟气的接触时间,从而大大提高了吸收剂的利用率。
它不但具有一般干法脱硫工艺的许多优点,如流程简单、占地少、投资低以及副产品可以综合利用等,而且能在钙硫比很低(Ca/S=1.1~1.2)的情况下达到与湿法脱硫工艺相当的脱硫效率,即95%左右。
CFB-FGD技术目前已在国外发展地非常成功。
如在德国Borken 电厂100MW电站锅炉上(烟气量为620000m3/h)已经有了多年的稳定运行时间和经验,并在许多中小锅炉上得到应用。
CFB-FGD脱硫工艺由吸收剂添加系统、吸收塔、再循环系统以及自动控制系统组成(见图1)。
烟气从流化床下部布风板进入吸收塔,与消石灰颗粒充分混合,SO2、SO3及其他有害气体如HCl和HF与消石灰反应,生成CaSO3·1/2H2O、CaSO4·1/2H2O和CaCO3。
反应产物由烟气从吸收塔上部携带出去,经除尘器分离,分离下来的固体灰渣经空气斜槽送回循环床吸收塔,灰渣循环量可以根据负荷进行调节。
吸收剂的再循环延长了脱硫反应时间,提高了脱硫剂的利用率。
工艺水用喷嘴喷入吸收塔下部,以增加烟气湿度降低烟温,使反应温度尽可能接近水露点温度,从而提高脱硫效率。
CFB-FGD工艺的吸收剂可以用生石灰在现场干消化所得到的氢氧化钙(Ca(OH)2)细粉,由于制得的消石灰颗粒已经足够细,可以满足脱硫要求,因此无须再磨,既节省了购买球磨机等大型设备的投资费用,又减少了能耗,降低了运行费用。
该工艺是一种干法流程,所以也不象湿法、半干法工艺需要为数众多的贮存罐、易磨损的浆液输送泵等复杂的吸收剂制备和输送系统,用简单的空气斜槽就可以输运,大大简化了工艺流程。
该工艺的副产品呈干粉状,其化学组成与喷雾干燥工艺的副产品类似,主要成分有飞灰、CaSO3、CaSO4以及未反应的吸收剂等、加水后会发生固化反应,固化后的屈服强度可达15-18N/mm2,渗透率约为3×10-11,压实密度为1.28g/cm3,强度与混凝土接近,渗透率与黏土相当,因此适合用于矿井回填、道路基础等方面。
CFB-FGD、NID、RCFB-FGD 三种脱硫工艺的比较
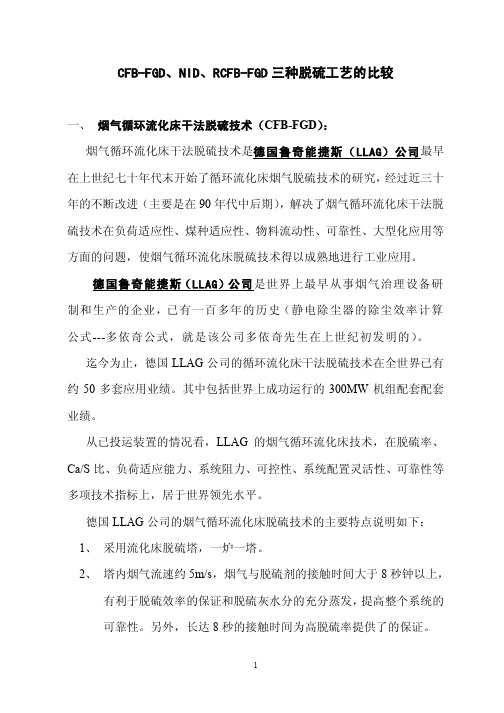
CFB-FGD、NID、RCFB-FGD三种脱硫工艺的比较一、烟气循环流化床干法脱硫技术(CFB-FGD):烟气循环流化床干法脱硫技术是德国鲁奇能捷斯(LLAG)公司最早在上世纪七十年代末开始了循环流化床烟气脱硫技术的研究,经过近三十年的不断改进(主要是在90年代中后期),解决了烟气循环流化床干法脱硫技术在负荷适应性、煤种适应性、物料流动性、可靠性、大型化应用等方面的问题,使烟气循环流化床脱硫技术得以成熟地进行工业应用。
德国鲁奇能捷斯(LLAG)公司是世界上最早从事烟气治理设备研制和生产的企业,已有一百多年的历史(静电除尘器的除尘效率计算公式---多依奇公式,就是该公司多依奇先生在上世纪初发明的)。
迄今为止,德国LLAG公司的循环流化床干法脱硫技术在全世界已有约50多套应用业绩。
其中包括世界上成功运行的300MW机组配套配套业绩。
从已投运装置的情况看,LLAG的烟气循环流化床技术,在脱硫率、Ca/S比、负荷适应能力、系统阻力、可控性、系统配置灵活性、可靠性等多项技术指标上,居于世界领先水平。
德国LLAG公司的烟气循环流化床脱硫技术的主要特点说明如下:1、采用流化床脱硫塔,一炉一塔。
2、塔内烟气流速约5m/s,烟气与脱硫剂的接触时间大于8秒钟以上,有利于脱硫效率的保证和脱硫灰水分的充分蒸发,提高整个系统的可靠性。
另外,长达8秒的接触时间为高脱硫率提供了的保证。
3、将物料和水分开单独加入到吸收塔内,加水的位置位于流化床颗粒浓度最大和湍动能最大的区域,采用单根回流式高压喷嘴,注入到塔内的雾化水的粒径小于200μ,通过气流和以大量激烈湍动的颗粒,促使脱硫反应的降温水得到有效的蒸发。
4、采用回流式高压喷嘴单喷嘴,水泵的出水设计量是喷嘴注水量的数倍,适应烟温变化的能力较强。
5、脱硫灰和吸收剂均从文丘里下部烟气高温段注入,抑制和减少了强吸水性物质的产生,提高了脱硫灰的流动性,解决了脱硫灰过度抱团、黏结的问题。
CFB-FGD

烟气脱硫技术FGD:Flue Gas Desulfurization;循环流化床锅炉CFB:Circulating Fluidized BedCFB-FGD(循环流化床烟气脱硫技术)工艺是八十年代末由德国鲁奇(LURGI)公司首先提出的一种新颖的干法脱硫工艺。
该工艺是一种干法流程,所以也不象湿法、半干法工艺需要为数众多的贮存罐、易磨损的浆液输送泵等复杂的吸收剂制备和输送系统,用简单的空气斜槽就可以输运,大大简化了工艺流程。
这种工艺的创新之处在于,它以循环流化床原理为基础,使吸收剂在反应器内多次再循环,延长了吸收剂与烟气的接触时间,从而大大提高了吸收剂的利用率。
它不但具有一般干法脱硫工艺的许多优点,如流程简单、占地少、投资低以及副产品可以综合利用等,而且能在钙硫比很低(Ca/S=1.1~1.2)的情况下达到与湿法脱硫工艺相当的脱硫效率,即95%左右。
CFB-FGD技术目前已在国外发展地非常成功。
如在德国Borken电厂100MW电站锅炉上(烟气量为620000m3/h)已经有了多年的稳定运行时间和经验,并在许多中小锅炉上得到应用。
CFB-FGD脱硫工艺由吸收剂添加系统、吸收塔、再循环系统以及自动控制系统组成。
烟气从流化床下部布风板进入吸收塔,与消石灰颗粒充分混合,SO2、SO3及其他有害气体如HCl和HF与消石灰反应,生成CaSO3·1/2H2O、CaSO4·1/2H2O和CaCO3。
反应产物由烟气从吸收塔上部携带出去,经除尘器分离,分离下来的固体灰渣经空气斜槽送回循环床吸收塔,灰渣循环量可以根据负荷进行调节。
吸收剂的再循环延长了脱硫反应时间,提高了脱硫剂的利用率。
工艺水用喷嘴喷入吸收塔下部,以增加烟气湿度降低烟温,使反应温度尽可能接近水露点温度,从而提高脱硫效率。
CFB-FGD工艺的吸收剂可以用生石灰在现场干消化所得到的氢氧化钙(Ca(OH)2)细粉,由于制得的消石灰颗粒已经足够细,可以满足脱硫要求,因此无须再磨,既节省了购买球磨机等大型设备的投资费用,又减少了能耗,降低了运行费用。
循环硫化床烟气脱硫技术及工艺设计
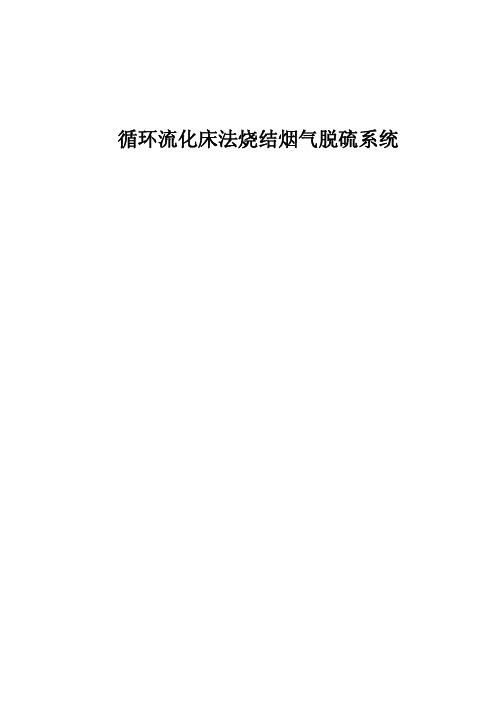
空气污染控制。 2.1.2 国内烧结厂烟气脱硫现状
烧结机是钢铁生产过程的重要设备。烧结工艺将各种粉矿混合伴匀, 布料于烧结带上燃烧,粉矿熔融粘结成烧结矿。混料中加有粉焦或煤粉作 为燃料。燃料燃烧时,穿过料层吸入空气助燃,燃烧产生的废气中含有 SO2 等污染物,SO2 浓度与燃料含硫量有关。从烟气脱硫角度来看,烧结 烟气具有以下特征:1)废气量大;2)烟气温度高;3)SO2 浓度低,总 量大。
一般来说,在人为中排放的 SO2 总量中,火电厂约占一半,工业企 业占 1/3,其余属于交通运输工具移动源和广泛分散的商用民用炉灶。
近 10 几年来,由于国家推行清洁生产,加大环保投入,强化环境管 理的结果,SO2 污染势头有所遏制,但尚未发生根本变化。未来 10 年将 是我国经济持续高速发展时期,如不采取有效措施,SO2 污染可能制约发 展的速度。
半干法的工艺特点是:反应在气、固、液三相中进行,利用烟气显热
-6-
蒸发吸收液中的水份,使最终产物为于粉状,脱硫废渣一般抛弃处置。该 方法既能结合湿法和干法脱硫的优点,实现脱硫效率高、吸收率高,同时 投资少、设备简单。
根据钢铁企业烧结烟气气量较大、SO2 浓度较低等特点,比较以上脱硫 工艺,我们推荐采用半干法的循环流化床工艺进行烧结烟气脱硫。
-2-
二、烧结烟气脱硫状况、技术和工艺推荐
2.1 国内外烧结烟气脱硫现状
2.1.1 国外烟气脱硫现状
国外烧结烟气脱硫的总体状况和技术水平,以日本、美国和德国为代 表。由于日本环保法规严厉,烧结废气含硫较高的各类生产厂几乎都设有 废气脱硫装置,因此其烧结烟气脱硫工艺的应用程度高于美国和德国。
日本烧结厂比较重视环境保护,针对生产过程中产生和散发的灰尘、
在世界上属于一流,在废气脱硫方面,日本在 20 世纪 70 年代就已开发了
- 1、下载文档前请自行甄别文档内容的完整性,平台不提供额外的编辑、内容补充、找答案等附加服务。
- 2、"仅部分预览"的文档,不可在线预览部分如存在完整性等问题,可反馈申请退款(可完整预览的文档不适用该条件!)。
- 3、如文档侵犯您的权益,请联系客服反馈,我们会尽快为您处理(人工客服工作时间:9:00-18:30)。
烟气循环流化床(CFB-FGD)干法脱硫工艺
gaojilu 发表于2006-2-20 20:40:31
工艺流程
从工艺流程图表明一个典型的 CFB-FGD 系统由吸收塔、除尘器、吸收剂制备系统、物料输送系统、喷水系统、脱硫灰输送及存储系统、电气控制系统等构成。
来自锅炉的空气预热器出来的烟气温度一般为 120~180℃左右,通过一级除尘器(当脱硫渣与粉煤灰须分别处理时),从底部进入吸收塔,在此处高温烟气与加入的吸收剂、循环脱硫灰充分预混合,进行初步的脱硫反应,然后通过吸收塔底部的文丘里管的加速,吸收剂、循环脱硫灰受到气流的冲击作用而悬浮起来,形成流化床,进行第二步充分的脱硫反应。
在这一区域内流体处于激烈的湍动状态,循环流化床内的Ca/S值可达到40~50,颗粒与烟气之间具有很大的滑落速度,颗粒反应界面不断摩擦、碰撞更新,极大地强化了脱硫反应的传质与传热。
在文丘里出口扩管段设一套喷水装置,喷入的雾化水一是增湿颗粒表面,二是使烟温降至高于烟气露点20℃左右,创造了良好的脱硫反应温度,吸收剂在此与SO2充分反应,生成副产物CaSO3·1/2H2O,还与SO3、HF和HCl 反应生成相应的副产物CaSO4·1/2H2O、CaF2、CaCl2等。
净化后的含尘烟气从吸收塔顶部侧向排出,然后进入脱硫除尘器(可根据需要选用布袋除尘器或电除尘器),通过引风机排入烟囱。
由于排烟温度高于露点温度20℃左右,因此烟气不需要再加热,同时整个系统无须任何的防腐。
经除尘器捕集下来的固体颗粒,通过再循环系统,返回吸收塔继续反应,如此循环,少量脱硫灰渣通过物料输送至灰仓,最后通过输送设备外排。