仿金电镀工艺
不掉色的假黄金制作工艺

不掉色的假黄金制作工艺
假黄金,也称镀金,是一种在品质上比较次的金属制品。
不掉色的假黄金制作工艺与普通的镀金工艺不同,它需要用到一些特殊材料。
下面是一种制作不掉色假黄金的工艺:
材料:黄金合金液、金属制品、镀膜材料
工具:电镀设备
步骤:
1. 将金属制品清洗干净,去除表面的铁锈和油污。
2. 在电镀设备中加入黄金合金液,并将金属制品浸入液中。
3. 通过电解作用,将黄金合金液中的金属离子附着在金属制品表面,形成一层金属膜。
4. 将金属制品取出,用清水冲洗干净,然后晾干。
5. 在金属制品表面涂上一层无色透明的镀膜材料,以保护金属层。
这种假黄金制作工艺与传统的镀金工艺相比,主要区别就在于使用的黄金合金液不含钯,而是采用了一些其他的金属材料来进行配比,从而使得制作出的假黄金在使用过程中不会掉色。
仿金电镀.PPt
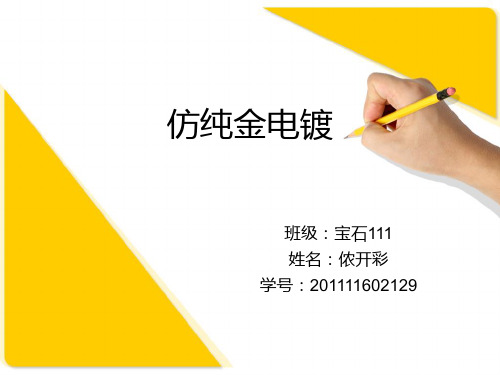
试验事实还表明,合金层中Cu、zn、sn三种金属成分比例 不同,使经BTA钝化后的仿纯金的颜色也不同。 用BTA的钝化工艺,通常使BTA浓度在1~4 g/L,经过一定温 度和时间处理,仿金层可以不用有机涂料封闭,而能镀层颜色来看,并不一定要达到24K的 纯金色。 笔者所采取的是“二步法”,先从三元合金镀液中镀取一 定比例的Cu-Zn-Sn合金,再用一次或二次的钝化处理方法, 得到极似24K纯金色的镀层。
有关仿金镀层颜色的看法
仿金镀层的颜色很难得到纯金的颜色,影响仿金镀层颜色 的因素很多,有工艺中合金成分的比例,电镀仿金前基体的 表面加工状态和光亮镍层的表面状态等,如果固定了基体 金属表面的加工状态和光亮镍镀层的光亮度,整平度之后, 合金层中金属的比例就成了影响仿金层颜色的一个主要因 素。
例如18K,它仅指含金量是75%,其余为别的金属,随着这些 金属不同可以使18K金有不同的颜色。
薛惠平在他的文章中指出„‘1‟,二元合金中铜锌含量不同,则色泽不 同,只有Co70%,Zn30%才能得到金黄色,如果是三元合金,金黄的18K 金色是Cu81%;Zn18%;Sn微量;赤金的24K金色Cu92.5%;Zns7%;Sn 少量。由此看来,Sn的加入,要得到18K金的金黄色,Cu与Zn比例已不 再是70:30了,24K的赤金色,zn的含量更少。
影响三元合金仿金电镀工艺的因素很多,CA依然 是良好的稳定剂,它能扩大电流密度范围,使高低电 流密度处的镀层颜色均匀一致,工艺条件和镀液稳 定。要使镀层达到仿纯金色,还要通过适当的后处 理工序。
三元仿金镀层的后处理
三元仿金层镀后也必须经过严格的水洗、钝化和浸(喷)有机 涂料等工序,才能久不变色。其中采用苯骄三氮哇(BTA)钝 化工艺,有效地提高仿金层的抗变色能力。
仿金电镀工艺
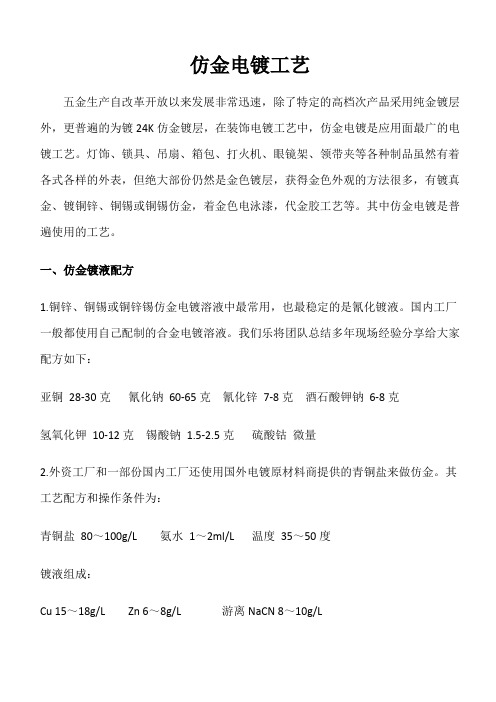
仿金电镀工艺五金生产自改革开放以来发展非常迅速,除了特定的高档次产品采用纯金镀层外,更普遍的为镀24K仿金镀层,在装饰电镀工艺中,仿金电镀是应用面最广的电镀工艺。
灯饰、锁具、吊扇、箱包、打火机、眼镜架、领带夹等各种制品虽然有着各式各样的外表,但绝大部份仍然是金色镀层,获得金色外观的方法很多,有镀真金、镀铜锌、铜锡或铜锡仿金,着金色电泳漆,代金胶工艺等。
其中仿金电镀是普遍使用的工艺。
一、仿金镀液配方1.铜锌、铜锡或铜锌锡仿金电镀溶液中最常用,也最稳定的是氰化镀液。
国内工厂一般都使用自己配制的合金电镀溶液。
我们乐将团队总结多年现场经验分享给大家配方如下:亚铜28-30克氰化钠60-65克氰化锌7-8克酒石酸钾钠6-8克氢氧化钾10-12克锡酸钠1.5-2.5克硫酸钴微量2.外资工厂和一部份国内工厂还使用国外电镀原材料商提供的青铜盐来做仿金。
其工艺配方和操作条件为:青铜盐80~100g/L 氨水1~2ml/L 温度35~50度镀液组成:Cu 15~18g/L Zn 6~8g/L 游离NaCN 8~10g/L二、仿金电镀不仅只是配方中络物和铜、锌、锡三元含量和温度的优选,而更重要是电流和时间的选择,电流分三档不同安培数,三档电流受时间控制,拉开高、中、低阴极电流,先高后低、挂具不停地轻轻的晃动,在电流作用下,镀层由青白→微黄→近24K仿金色三、各成份作用与控制技巧1.氰化钠其含量的增加,一方面有利于Zn(CN)j一的形成,减少锌在镀液析出的量,;另一方面增强了铜氰离子与氰的络合程度,降低铜的析出量。
从我们乐将团队长期控制的经验来看:适量的氰化钠可以使偏红的色彩转黄,也可能转变过头而偏白。
这个依氰化钠量变化而产生颜色的变化过程大家一定要记牢!在新配可调整溶液时,各种离子之间的络合转变并不是马上能完成,为使其中的各种络合离子达到稳态的化学平衡,当加入氰化钠或氢氧化钠后要均匀搅拌络合一段时间,才能对调色效果明显2.氢氧化钠1)是锌的第二络合剂,也是锡的唯一络合剂,锌和锡在合金镀层中所占的比值直接影响色彩。
塑料无氰仿金电镀工艺的加工流程

塑料无氰仿金电镀工艺的加工流程1 前言仿金电镀优良的装饰性受到人们的普遍喜爱。
但国内普遍采用的仿金电镀含氰化物多,毒性大,不仅危害到工人的身体健康,而且污染环境严重,因此,无氰化物的仿金电镀颇受青睐。
氰化物由于有剧毒,废水处理困难,电镀工艺过程难控制等原因,在塑料仿金电镀上的应用受到了限制。
本文针对仿金电镀存在的不足,开展无氰仿金电镀工艺研究。
采用焦磷酸盐作络合剂,柠檬酸盐、氨三乙酸等作辅助络合剂研究出一种无氰仿金电镀工艺,所得仿金镀层为18-22K,且色泽均匀,结合力良好,达到了预期效果。
2 工艺流程塑料除应力→水洗→除油→热水洗→冷水洗→粗化→水洗→除铬膜→水洗→敏化→漂洗→活化→漂洗→化学镀铜→水洗→光亮镀铜→水洗→光亮镀镍→水洗→镀仿金→水洗→钝化→水洗→干燥→封闭→干燥→检验镀前处理、化学镀铜、光亮镀铜、光亮镀镍都采用传统工艺,本文不再叙述。
3 实验结果与讨论3.1 无氰仿金电镀工艺规范经过优化筛选,确定无氰仿金电镀工艺配方如下:3.2 镀液中金属离子浓度对镀层性能影响由表1可知:当铜的含量偏低时,仿金层中锌含量高,镀层偏白;而当铜的含量偏高时,仿金层铜的颜色较深。
锡的含量不可太高,否则仿金层发雾,可能是锡的氢氧化物沉淀。
3.3 添加剂对仿金电镀层外观的影响由表2可知,添加剂的微量加入导致仿金镀层外观的变化。
在正确的添加范围内,仿金层色泽为18-22K。
由实验结果确定添加剂的范围为:0.002~0.006g/L。
3.4 pH值对仿金镀层外观的影响由表3可知,酸值对仿金镀层的影响较大,合适的pH值范围可得到性能优良的仿金镀层。
pH值低时,焦磷酸盐水解成磷酸盐,使溶液浑浊,阳极发生钝化,镀层沉积不上铜和锌,镀层偏红,发灰。
pH值稍高时,铜易析出,而锡的析出受到影响,使得镀层中锡含量偏低,镀层发黄且不光亮。
pH继续升高,锡易析出,镀层色泽黄且光亮。
当pH值高达9.2以上,铜生成碱式盐夹杂在镀层中,导致镀层附着力差、发雾。
仿金电镀工艺
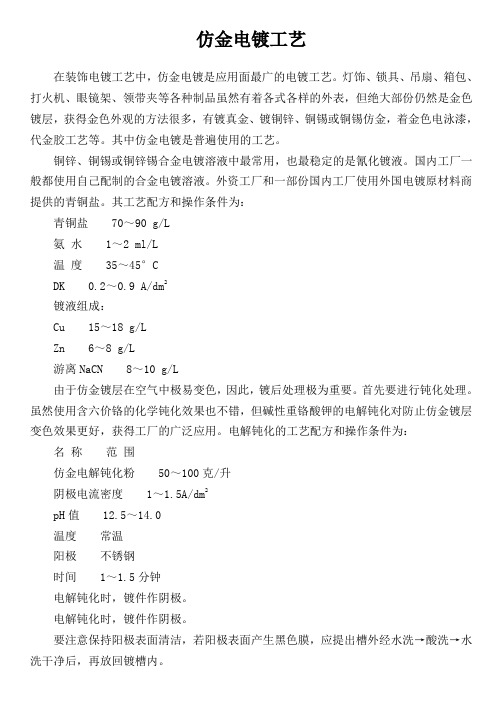
仿金电镀工艺在装饰电镀工艺中,仿金电镀是应用面最广的电镀工艺。
灯饰、锁具、吊扇、箱包、打火机、眼镜架、领带夹等各种制品虽然有着各式各样的外表,但绝大部份仍然是金色镀层,获得金色外观的方法很多,有镀真金、镀铜锌、铜锡或铜锡仿金,着金色电泳漆,代金胶工艺等。
其中仿金电镀是普遍使用的工艺。
铜锌、铜锡或铜锌锡合金电镀溶液中最常用,也最稳定的是氰化镀液。
国内工厂一般都使用自己配制的合金电镀溶液。
外资工厂和一部份国内工厂使用外国电镀原材料商提供的青铜盐。
其工艺配方和操作条件为:青铜盐 70~90 g/L氨水 1~2 ml/L温度 35~45°CDK 0.2~0.9 A/dm2镀液组成:Cu 15~18 g/LZn 6~8 g/L游离NaCN 8~10 g/L由于仿金镀层在空气中极易变色,因此,镀后处理极为重要。
首先要进行钝化处理。
虽然使用含六价铬的化学钝化效果也不错,但碱性重铬酸钾的电解钝化对防止仿金镀层变色效果更好,获得工厂的广泛应用。
电解钝化的工艺配方和操作条件为:名称范围仿金电解钝化粉 50~100克/升阴极电流密度 1~1.5A/dm2pH值 12.5~14.0温度常温阳极不锈钢时间 1~1.5分钟电解钝化时,镀件作阴极。
电解钝化时,镀件作阴极。
要注意保持阳极表面清洁,若阳极表面产生黑色膜,应提出槽外经水洗→酸洗→水洗干净后,再放回镀槽内。
为保证钝化质量,槽液pH值应不低于12.5,电流1A/dm2以上,如为恒电压则5-6V。
钝化后的工件必须经过充分的水洗,再作切水和切油处理。
其工艺流程如下:仿金→水洗→水洗→电解钝化→超声波水清洗→水洗一次→切水→切油。
切水是用切水剂脱去工件表面的水份,因此工件表面变得不亲水,切油是去掉工件表面的不亲水的切水剂,然后烘干喷漆。
24K仿金电镀,这里我要特别提到的是温州技术创新的24K仿金电镀。
24K仿金电镀不仅只是配方中络物和铜、锌、锡三元含量和温度的优选,而更重要是电流和时间的选择,电流分三档不同安培数,三档电流受时间控制,拉开高、中、低阴极电流,先高后低、挂具不停地轻轻的晃动,在电流作用下,镀层由淡白→微黄→近24K金黄色,镀出金色调和罩光漆烘干温度相关。
镀锌层的金黄色钝化(仿金)工艺

镀锌层的金黄色钝化(仿金)工艺1.前言仿金镀层, 通常先镀亮镍层打底或“亮铜-亮镍”作底层, 然后镀上1-2μm 较薄的铜合金, 如氰化物镀铜锌、铜锡或铜锌锡合金的方法, 获得外观装饰性仿金镀层。
近年来推出的镀锌层染色、罩清漆的仿金工艺, 也就是在镀锌层上经金黄色钝化液钝化形成金黄色钝化膜, 水洗后即浸脱水防锈剂, 以固定膜层得到均匀金黄色,再涂覆一层透明而具有一定硬度的有机膜(清漆) 进行保护,从而实现仿金装饰生产。
2.工艺流程钢铁制品→前处理→镀锌→流动水清洗→碱液漂洗→二道流动水清洗→锌层出光→二道流动水清洗→金黄色钝化→流动水清洗→浸脱水防锈剂→流动水清洗→膜层老化→涂覆透明漆→有机膜固化→操作者自检→专职检验成品包装入库。
3.工艺配方3.1出光液:硝酸3%-5%,食盐5%-10%。
3.2钝化液:铬酸3-5g/l,硫酸O.3-O.5g/l,硝酸O.7-0.9g/l,室温,时间10-30s,空停8-10s。
3.3 防锈剂:聚乙烯醇15-25g/l,苯甲酸钠30-50g/l,亚硝酸钠20-30g/l,三乙醇胺50-100g/l,乙醇(1:2)800ml/l。
配制说明:在搪瓷桶内注入计算量的乙醇,并加温至90-95℃, 在不断搅拌下缓慢加入聚乙烯醇, 使之溶解成胶状液体。
冷却至40-50℃, 将计算好的苯甲酸钠、亚硝酸钠及三乙醇胺依次加入,搅拌溶解形成透明液体,或采用市售现成的且适合本工艺的脱水防锈剂。
3.4 涂料:604环氧树脂50%,丙嗣20%,丁醇10%,二甲苯10%环己酮10%或采用市售现成的涂料,如丙烯酸清漆、改性丙烯酸酶类的涂料等。
4.注意事项(1)要获得理想金黄色质量,良好的镀锌层是重要环节。
凡是镀锌层如氰化物、碱性和酸性等锌镀层都可以进行仿金装饰生产。
但是,必须要求镀锌层平整致密、光亮,且镀层夹杂无机、有机杂质要少。
因此,要经常过滤镀液,尽量减少有机杂质和金属杂质的积累, 因为槽液中杂质积累多, 夹杂在镀锌层内的杂质量也多使金黄色钝化膜更易变色。
锌铁合金为底层的仿金电镀全套工艺

锌铁合金为底层的仿金电镀全套工艺!装饰性仿金镀层色泽庄重高雅,深受青睐,已广泛用于家用、五金、仪器、建材及首饰等行业。
仿金电镀溶液有氰化物型及无氰化物型2种。
无氰仿金电镀已逐步替代氰化电镀,但其底层主要用焦磷酸盐镀液和HEDP镀液。
前者成分复杂,分散能力不够,较难控制;后者分散能力和深镀能力较好,溶液稳定,色泽均匀,但光亮度不够。
可见仿金电镀预镀层的选择至关重要。
此外,基体的前处理、仿金镀工艺及其镀后处理的选用亦要得当。
以锌铁合金为底层,对仿金镀全套工艺进行了故障排除方法,收到了良好的效果。
装饰品仿金镀层较薄,耐蚀性极差,用厚铜打底易泛红;采用亮镍打底,仿金镀层光亮、硬度高,不易发花,但成本高;采用光亮铜锡合金-亮镍或暗镍-亮铜-亮镍作底镀层也能满足要求,但操作复杂。
用高耐蚀性全光亮锌铁合金电镀取代镍系作仿金镀底层,不仅镀层光亮度好,防护性能还更优,其生产成本又大大降低。
应用于聚苯乙烯塑料件的仿金电镀技术

4 3 OO
( ・ g L)
3 5
失效 。④ 零件 在进 入活 化液前 ,如 果先 用含S C 0 nI 4
gL H I 0 / 的溶 液进 行预 处理 ,不清 洗直 接 /和 C 0mLL 1 入槽 活化 ,可大大提高 活化效果 ,延 长活化液使 用寿 命。 表2 活化液配方和操作条件
磷酸 胸 ).l氧 钠 妨 0 簟 t 镳 ’ 他 氯 期毒 l 蛸
2 O 5 2 0
 ̄ J L t) 。 离秘 / . ( I m 1 E ,
1 60
舞 啾狮嘲
3 0
聚苯 乙烯是 苯 乙烯 的聚合物 ,是 当今世界 五大通 用塑料之 一 ,外观透 明 ,但产品 发脆 ,通过 加入聚丁 二烯 可制成耐冲 击性聚苯 乙烯 。通过 实验 H P 塑料件 IS
度和足够 的酸度 ,要定 期添 加亚锡 盐和盐酸 ,溶液 分 层 时 ,证 明亚锡 离 子 不 足 ,应 及 时 补 加 1 0~2 / 0gL
S C, ③切 不 可 带 入 六 价 铬 、硝 酸 银 等 氧 化 性 杂 nI 。
质 ,也不得采 用空气搅拌 ,否则会 导致活化液 分解而
( L) ( g・ g・L1 I )
3 1 活 化 .
HIS P 塑料件 浸泡 在体积 比为21 :的丙 酮水 溶液 中 ,时
间为3~5mi。 n
门铰链电镀仿金Cu-Zn合金工艺设计 2课件

一、工艺设计说明书1 摘要1.1 中文摘要摘要:仿金镀层外观有纯金色、18K以及16K金色。
目前国内外广泛应用的仿金镀层,一般采用铜锌合金的方法得到,主要有二元合金(70Cu-Zn,80Cu-Sn)与三元合金(Cu-Zn-Sn)。
三元合金颜色光泽优良,应用最广。
仿金镀层一般要求底层光亮,而仿金镀液不再添加光亮剂。
为装饰用的仿金镀层较薄,一般在1~2um,,只要求在制品表面”着”上一层薄金黄色。
这样薄的铜锌合金镀层耐蚀性极差。
因此,镀层的耐蚀性主要靠电镀底层来解决,采用镀厚铜打底,再度仿金镀层的方法,获得镀层易“泛红“。
故生产中常采用镀亮镍层打底,这样既光亮又有一定硬度,而且表面的仿金层也不易发花。
仿金电镀的镀液有氰化物型、氰化物—焦磷酸盐型、HEDP型和焦磷酸盐型。
后两种无氰镀液组成复杂,分散能力不好,维护困难,应用少,氰化物型最稳定,较易控制,镀得的镀层色泽鲜艳、合格率高并可重复反修。
以中、低氰镀液应用最广。
电镀仿金层后,为防止变色,除进行适当的钝化处理外,还要涂上一层透明的有机膜。
对于一些精巧产品,这层有机膜显得很不协调,因而可在仿金层上再镀一层金。
由于金镀层有良好的稳定性,产品不易变色,美观大方,很受欢迎。
关键词:仿金镀层铜锌合金光亮剂 HEDP型钝化分散能力有机膜1.2 英文摘要Abstract:The appearance of imitation gold plating with pure gold, 18K, and 16K gold. Imitation gold plating is widely used at home and abroad, generally use a copper-zinc alloy obtained by the method, there are binary alloys (70Cu-Zn, 80Cu-Sn) and ternary alloys (Cu-Zn-Sn). Ternary alloy color gloss is excellent, the most widely used. Imitation gold coating generally require the underlying bright, imitation gold plating bath is no longer add brightener. Decorated with imitation gold plating is thin, generally 1 ~ 2um requires only the surface of the work in progress, "" a thin layer of golden yellow. This thin copper-zinc alloy corrosion resistance is poor. Therefore, the corrosion resistance of the coating to solve the underlying by plating, thick copper plating base again, imitation gold plating, coating "flushed". Of production are often plated bright nickel layer of primer, so that both light has a certain hardness, imitation gold surface layer is not easy to blur.Imitation gold plating of the bath of cyanide and cyanide - pyrophosphate type, HEDP and pyrophosphate type. The latter two cyanide plating bath composition is complex, poor dispersion capability, and difficult to maintain, less application cyanide type is the most stable and easier to control, plated coating bright color, high pass rate can repeat antirevisionist the. In, the most widely used low-cyanide plating bath.Electroplating imitation gold layer, in order to prevent discoloration, and in addition to the appropriate passivation treatment, but also coated with a layer of transparent organic film. For delicate products, this layer of organic film look very coordinated, thus imitation gold layer on layer of gold-plated. Gold plating has good stability, the product is not easy to change color, elegant appearance, is very popularKeyword:imitation gold plating copper and zinc alloy brightener HEDP typle passivation disperssion capability orgnic film2、设计依据2.1 工件名称、材质和尺寸门铰链、45#钢、工件最大综合吊挂尺寸长×宽×高:90mm×50mm×10mm表面积:88×2=176 cm22.2 镀层要求采用HEDP(羟基亚乙基二磷酸)仿金电镀工艺2.3 车间任务和生产纲领(1)车间任务本车间负责对45#钢制门铰链进行HEDP(羟基亚乙基二磷酸)仿金电镀工艺(2)生产纲领年产量:每年500万个,每个2个零件,年产量为1000万个零件考虑零件返修和报废,按2%计算,则实际年产量为1020万件2.4 工作制度和年时基数(1)工作制度:采用三班制,一、二班每班工作8小时,第三班采用7小时。
详解仿金电镀工艺配方与操作技巧完整版
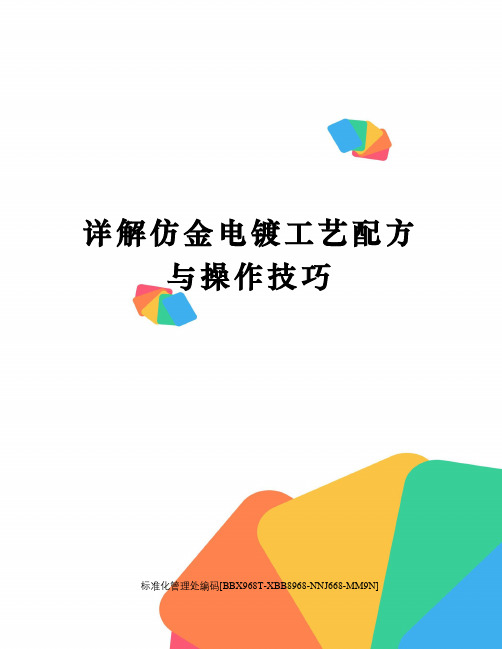
详解仿金电镀工艺配方与操作技巧标准化管理处编码[BBX968T-XBB8968-NNJ668-MM9N]详解仿金电镀工艺配方与操作技巧五金生产自改革开放以来发展非常迅速,除了特定的高档次产品采用纯金镀层外,更普遍的为镀24K仿金镀层,在装饰电镀工艺中,仿金电镀是应用面最广的电镀工艺。
灯饰、锁具、吊扇、箱包、打火机、眼镜架、领带夹等各种制品虽然有着各式各样的外表,但绝大部份仍然是金色镀层,获得金色外观的方法很多,有镀真金、镀铜锌、铜锡或铜锡仿金,着金色电泳漆,代金胶工艺等。
其中仿金电镀是普遍使用的工艺。
一、仿金镀液配方1.铜锌、铜锡或铜锌锡仿金电镀溶液中最常用,也最稳定的是氰化镀液。
国内工厂一般都使用自己配制的合金电镀溶液。
我们乐将团队总结多年现场经验分享给大家配方如下:亚铜 28-30克氰化钠 60-65克氰化锌 7-8克酒石酸钾钠 6-8克氢氧化钾 10-12克锡酸钠 1.5-2.5克硫酸钴微量2.外资工厂和一部份国内工厂还使用国外电镀原材料商提供的青铜盐来做仿金。
其工艺配方和操作条件为:青铜盐 80~100g/L氨水 1~2ml/L温度 35~50度镀液组成:Cu 15~18g/LZn 6~8g/L游离NaCN 8~10g/L二、仿金电镀不仅只是配方中络物和铜、锌、锡三元含量和温度的优选,而更重要是电流和时间的选择,电流分三档不同安培数,三档电流受时间控制,拉开高、中、低阴极电流,先高后低、挂具不停地轻轻的晃动,在电流作用下,镀层由青白→微黄→近24K仿金色三、各成份作用与控制技巧1.氰化钠其含量的增加,一方面有利于Zn(CN)j一的形成,减少锌在镀液析出的量,;另一方面增强了铜氰离子与氰的络合程度,降低铜的析出量。
从我们乐将团队长期控制的经验来看:适量的氰化钠可以使偏红的色彩转黄,也可能转变过头而偏白。
这个依氰化钠量变化而产生颜色的变化过程大家一定要记牢!在新配可调整溶液时,各种离子之间的络合转变并不是马上能完成,为使其中的各种络合离子达到稳态的化学平衡,当加入氰化钠或氢氧化钠后要均匀搅拌络合一段时间,才能对调色效果明显2.氢氧化钠1)是锌的第二络合剂,也是锡的唯一络合剂,锌和锡在合金镀层中所占的比值直接影响色彩。
NY仿金电镀工艺
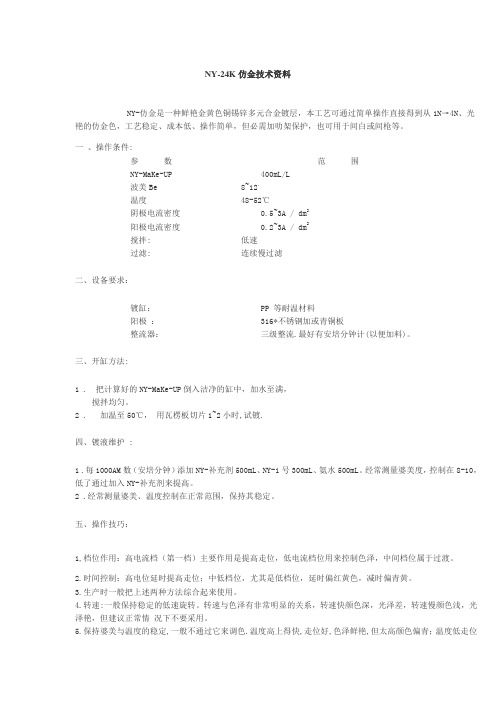
NY-24K仿金技术资料NY-仿金是一种鲜艳金黄色铜锡锌多元合金镀层,本工艺可通过简单操作直接得到从1N→4N、光艳的仿金色,工艺稳定、成本低、操作简单,但必需加叻架保护,也可用于间白或间枪等。
一、操作条件:参数范围NY-MaKe-UP400mL/L波美Be8~12。
温度48-52℃阴极电流密度0.5~3A / dm2阳极电流密度0.2~3A / dm2搅拌:低速过滤:连续慢过滤二、设备要求:镀缸:PP 等耐温材料阳极:316*不锈钢加或青铜板整流器:三级整流.最好有安培分钟计(以便加料)。
三、开缸方法:1 . 把计算好的NY-MaKe-UP倒入洁净的缸中,加水至满,搅拌均匀。
2 . 加温至50℃,用瓦楞板切片1~2小时,试镀.四、镀液维护 :1 .每1000AM数(安培分钟)添加NY-补充剂500mL、NY-1号300mL、氨水500mL。
经常测量婆美度,控制在8-10,低了通过加入NY-补充剂来提高。
2 .经常测量婆美、温度控制在正常范围,保持其稳定。
五、操作技巧:1,档位作用:高电流档(第一档)主要作用是提高走位,低电流档位用来控制色泽,中间档位属于过渡。
2.时间控制:高电位延时提高走位;中低档位,尤其是低档位,延时偏红黄色,减时偏青黄。
3.生产时一般把上述两种方法综合起来使用。
4.转速:一般保持稳定的低速旋转。
转速与色泽有非常明显的关系,转速快颜色深,光泽差,转速慢颜色浅,光泽艳,但建议正常情况下不要采用。
5.保持婆美与温度的稳定,一般不通过它来调色.温度高上得快,走位好,色泽鲜艳,但太高颜色偏青;温度低走位差,光泽差,颜色偏红。
浓度高上得快,走位好, 但太高会影响结合力和光泽,浓度低,色泽不匀,走位差,让它们控制在正常范围。
6.NY-1#是深色调色剂,补加会变红黄色,但过量会很红且走位差。
氨水主要起均色作用,降低色差提高走位,但过量会偏青。
六、后处理要求:1).镀完仿金后,无需再做过酸或电解处理,经过四道水后可直截下保护水缸。
氰化仿金电镀工艺

氰化仿金电镀工艺(一)铜锌合金仿金电镀铜锌合金的仿金镀层很薄,一般只有0.3~1μm,其中含有铜70%~80%、锌约20%~30%。
为了防变色并效果好,还可以添加少量其他一元金属。
仿金镀层的颜色不仅与铜和锌的含量及比例有关,而且与镀液的成分及工艺条件有着密切关系。
镀铜锌合金仿金镀层溶液配方及工艺条件如下:氰化亚铜(CuCN) 75g/L 溶液温度20~22℃氰化锌[Zn(CN)2] 9g/L 电流密度2~10A/dm2氰化钠(总量,NaCN) 55g/L 阳极材料铜(70%)、锌(30%)氰化钠(游离,NaCN) 15~25g/L合金板碳酸钠(Na2CO3)6~25g/L电镀时间视镀层厚度而定氟化钠2~5g/L仿金镀层出镀后,对空气和水中的杂质极其敏感,因此必须用纯净水或无离子水清洗最后一道工序,同时必须马上进行钝化处理。
钝化处理的溶液配方如下:铬酐(Cr03) 2~5g/L 氧化锌(ZnO) 0.8g/L销酸(HN03) 1mL/L 阴离子表面活性剂0.2mL/L所得的钝化膜是一层看不见、透明的薄膜,它不仅可以增加耐蚀性,在存放时可抗色变,同时还可以增加仿金镀层与最后涂刷清漆层之间的附着力。
仿金镀层钝化后必须迅速干燥,最后一次也应用无离子水清洗。
用木屑烘干是一种有效的干燥方法,能够可靠地防止干燥后出现的斑点。
仿金镀层干燥后应马上涂透明清漆,以便隔绝镀层与氧接触,避免由于氧化而颜色变暗的情况出现。
6~12μm的环氧基罩光漆或清漆效果较好,环氧基罩光漆的耐磨性能较好,产品在使用过程中不会变色,漆膜不易破损。
漆膜涂覆后在30~40min内硬化,但要在90~100℃下干燥24h。
这种仿金镀层有沉积速度快、镀层厚度只有0.3~1.0μm、复杂零件上的仿金镀层色泽基本均匀一致而操作简便等特点。
(二)铜锡合金仿金电镀铜锡基合金仿金电镀效果也很好,其溶液的基本配方及工艺条件如下:氰化亚铜(CuCN) 30g/L 氰化钾(总,KCN) 40g/L锡酸钠(Na2Sn03) 15g/L 氰化镍钾[KzNi(CN)4] 5g/L氨基磺酸钠[Na2(NH2S03)2] 10g/L 溶液温度20~30℃氨基磺酸铟[In(NH2S03)2] 6g/L 电流密度3A/din2酒石酸钾钠[NaKC4H46] 20g/L如果在溶液中再添加2g/L苹果酸或柠檬酸,可获得良好的黄铜色泽;若添加10g/L柠檬酸,可得到18K金色;把柠檬酸的含量提高到20g/L时,可以镀得玫瑰金色泽。
工件仿金工艺流程

工件仿金工艺流程一、什么是工件仿金工艺。
工件仿金工艺呢,简单来说,就是让工件看起来像金子一样。
你想啊,金子多贵呀,不是所有东西都能用真金去做的。
比如说一些装饰品、小摆件之类的,要是都用真金,成本可就太高啦。
所以呢,就有了这个仿金工艺。
这工艺就是通过一系列的操作,让那些本来不是金的工件,从外观上看和金子差不多,闪闪发光的,可好看了。
二、仿金工艺的前期准备。
1. 工件的选择。
这可是很重要的一步哦。
不同的工件可能需要不同的处理方式。
比如说,如果是金属材质的工件,像铜或者铁的,那它们的质地就比较硬,在后续的加工中可能就需要更强力的处理手段。
要是一些塑料材质的工件,那就得小心一点啦,因为塑料比较容易变形或者损坏。
而且呢,工件的形状也很关键。
如果是那种有很多复杂花纹或者细小部件的工件,在进行仿金工艺的时候就得格外注意,可不能把这些漂亮的地方给弄坏了。
2. 材料的准备。
要进行仿金工艺,那肯定得有专门的材料呀。
这里面就包括各种化学试剂呢。
像镀液,这可是仿金工艺里的关键材料。
镀液的成分不同,最后仿金的效果也会不一样。
还有一些用来清洗工件的清洁剂,这就像是给工件洗澡一样,得把它身上的脏东西都洗干净了,这样后续的仿金涂层才能更好地附着在上面。
三、仿金工艺的具体流程。
1. 表面处理。
这一步就像是给工件化妆前的打底。
首先要把工件表面的油污、铁锈之类的东西都去掉。
如果是金属工件,可能会用到砂纸打磨,把表面磨得光滑平整。
这就像我们洗脸的时候要把脸洗干净,还得把死皮去掉一样。
然后呢,再用清洁剂进行清洗,确保表面没有任何杂质。
对于一些有特殊要求的工件,可能还需要进行酸洗或者碱洗,这都是为了让工件表面处于最佳的状态,好迎接后面的仿金涂层。
2. 镀底层。
在工件表面处理好之后,就要镀底层了。
这个底层就像是房子的地基一样重要。
一般会先镀一层比较薄的金属,像镍之类的。
这层底层的作用可大了,它可以提高工件的耐腐蚀性,还能让后面的仿金涂层更好地附着。
- 1、下载文档前请自行甄别文档内容的完整性,平台不提供额外的编辑、内容补充、找答案等附加服务。
- 2、"仅部分预览"的文档,不可在线预览部分如存在完整性等问题,可反馈申请退款(可完整预览的文档不适用该条件!)。
- 3、如文档侵犯您的权益,请联系客服反馈,我们会尽快为您处理(人工客服工作时间:9:00-18:30)。
仿金电镀工艺
五金生产自改革开放以来发展非常迅速,除了特定的高档次产品采用纯金镀层外,更普遍的为镀24K仿金镀层,在装饰性电镀工艺中,仿金电镀是应用面最广的电镀工艺。
灯饰、锁具、吊扇、箱包、打火机、眼镜架、领带夹等各种制品虽然有着各式各样的外表,但绝大部份仍然是金色镀层,获得金色外观的方法很多,有镀真金、镀铜锌、铜锡或铜锡仿金,着金色电泳漆,代金胶工艺等。
其中仿金电镀是普遍使用的工艺。
一,仿金镀液配方
1.铜锌、铜锡或铜锌锡仿金电镀溶液中最常用,也最稳定的是氰化镀液。
国内工厂一般都使用自己配制的合金电镀溶液多年现场经验分享给大家配方如下:
亚铜 28-30克
氰化钠 60-65克
氰化锌 7-8克
酒石酸钾钠 6-8克
氢氧化钾 10-12克
锡酸钠 1.5-2.5克
硫酸钴微量
2.国外电镀原材料商提供的青铜盐来做仿金。
其工艺配方和操作条件为:
青铜盐
80~100 g/L
氨水
1~2 ml/L
温度
35~50度
镀液组成:
Cu
15~18 g/L
Zn
6~8 g/L
游离NaCN
8~10 g/L
二,仿金电镀不仅只是配方中络物和铜、锌、锡三元含量和温度的优选,而更重要是电流和时间的选择,电流分三档不同安培数,三档电流受时间控制,拉开高、中、低阴极电流,先高后低、挂具不停地轻轻的晃动,在电流作用下,镀层由青白→微黄→近24K仿金色
三,各成份作用与控制技巧
1. 氰化钠
其含量的增加,一方面有利于Zn(CN)j一的形成,减少锌在镀液析出的量,;另一方面增强了铜氰离子与氰的络合程度,降低铜的析出量。
从长期控制的经验来看:适量的氰化钠可以使偏红的色彩转黄,也可能转变过头而偏白。
这个依氰化钠量变化而产生颜色的变化过程大家一定要记牢!
在新配可调整溶液时,各种离子之间的络合转变并不是马上能完成,为使其中的各种络合离子达到稳态的化学平衡,当加入氰化钠或氢氧化钠后要均匀搅拌络合一段时间,才能对调色效果明显
2. 氢氧化钠
1)是锌的第二络合剂,也是锡的唯一络合剂,锌和锡在合金镀层中所占的比值直接影响色彩。
含量增大,使锌析出占的比值也增大。
如果镀层偏红,补加氢氧化钠有可能使色彩转变成黄色,但其前提条件是溶液中有足够的锌含量和不太高的氰化钠量。
反之,氢氧化钠
含量过低,不利于锌的析出。
为了得到理想的仿金色彩,需要增加超比值的锌含量才能弥补锌析出的不足。
2)另外我们团队要告知大家的是:氢氧化钠过低,还同时不利于锡酸钠的稳定,甚至会逐渐水解转变成偏锡酸杂质沉淀于槽底。
这种反应在槽内是不可逆的,一但没络合好即使之后再如何提高氢氧化钠,偏锡酸都不再溶解恢复为锡酸钠。
3)还有一种情况:当溶液中铜锌比值适当时,有时氢氧化钠过高会使仿金色呈现偏红的土黄色(似黄泥土色)或称为锌红色。
如果将这种锌红色认为是镀层中铜量过高的铜红色,继续补充氢氧化钠或锌量则会步入误区。
此时,应该采用酸性物质来降低氢氧化钠的量,使锌红色转变成金色。
3. 酒石酸钾钠
它是第三络合剂,对铜和锌都有较弱的络合作用。
酒石酸钾钠的加入可以改善仿金镀层的光亮度,特别在稍长时间的电镀过程中,能使镀层保持较好的亮度,起到半光亮剂的作用以及活化阳极作用。
4. 硫酸钴的用量很少,约0.05~0.10 g/L,对仿金色有促进作用,使金色光亮柔和。
四,工艺条件
除了上述这些主盐的影响,工艺条件对仿金电镀也是非常关健的,如:
(1)温度作为调色的辅助手段,温度的升高有利于铜的电解析出,使仿金色彩增加红的色调。
一般宜采取40~50℃,必要时可达60℃,可根据色彩的需要与溶液的组成适当调节。
温度
的升高能提高溶液的导电性,使色彩均匀、亮丽。
但过高的温度会使氰化钠加速分解消耗,不利于溶液的稳定性。
(2)电流密度。
要获得成色足的仿金,要求各金属之间的比值及其与络合剂之间的比值满足于诸金属在某一电位电流析出量达到最佳仿金色的比例,为了电流控制达到重复准确性,以保证色彩的再现性,要使用专用的三档式电流定时控制器。
这种电流控制器包含3
只可调式时间继电器,按既定时间自动开启和关闭分别控制3只调压器,每次将逐步下调的3档既定电压依次输入一只变压器,输出电流经过整流后将3档不同大小的电流按既定电压依次输入仿金槽内。
这种仿金槽的电源装置不同于其他槽的电源装置,3档电流分为冲击电流、过渡电流和仿金电流。
控制和选择好每一档电流的时间和大小至关重要,其中又以最后一档最为重要。
(3)仿金时间。
各档时间的总和在20~30 s,冲击电流时间长度以不引起局部烧焦或光亮度下降为准,仿金电流的时间以获得足够色度的均匀仿金色为准。
3档电流的时间要作合理分配,冲击电流时间不可过长,约占20%~30%之间(以25%为宜);过渡电流时间稍长,约占40%~45%之间(以43%为宜);仿金电流时间要恰到好处,约占30%~35%(以32%为宜)。
在此时间内应获适当的仿金层总厚度,时间过短仿金层过薄可引起局部褪色和变色;时间过长仿金层过厚有损于仿金色彩的鲜艳。
如果在适当的时间内不能出现或充分显示最佳仿金色色彩,在调整各档相应电流也无效时应对仿金镀液进行微调或必要的调整。
冲击电流大小以均匀镀覆于整个零件外表面不出现烧焦,仿金电流大小以获得理想的仿金色为准。