机械加工常用尺寸精度及表面粗糙度
各种加工方法的经济精度和表面粗糙度

各种加工方法能够达到的尺寸的经济精度表1 孔加工的经济精度表2 圆锥形孔加工的经济精度表3 圆柱形深孔加工的经济精度表4 花键孔加工的经济精度表5 外圆柱表面加工的经济精度表6 端面加工的经济精度(mm)表7 用成形铣刀加工的经济精度(mm)注:指加工表面至基准的尺寸精度。
表8 同时加工平行表面的经刘精度(mm)注:指两平行表面距离的尺寸精度。
表9 平面加工的经济精度注:1 表内资料适用于尺寸<1m,结构刚性好的零件加工,用光洁的加工表面作为定位和测量基准。
2 端铣刀铣削的加工精度在相同的条件下大体上比圆柱铣刀铣削高一级。
3 细铣仅用于端铣刀铣削。
表10 公制螺纹加工的经济精度表11 花键加工的经济精度表12 齿形加工的经济精度各种加工方法能够达到的形状的经济精度表13 平面度和直线度的经济精度表14 圆柱形表面形状精度的经济精度注:形状精度等级的公差值见附表2、3。
表15 曲面加工的经济精度表16 在各种机床上加工时形状的平均经济精度各种加工方法所能够达到的相互位置的经济精度表17 平行度的经济精度表18 端面跳动和垂直度的经济精度表19 同轴度的经济精度表20 轴心线相互平行的孔的位置经济精度注:对于钻、卧镗及组合机床的镗孔偏差同样适用于铰孔。
表21 轴心线相互垂直的孔的位置经济精度注:在镗空间的垂直孔时,中心距误差可按上式相应的找正方法选用。
各种加工方法能够达到的零件表面粗糙度表22 各种加工方法能够达到的零件表面粗糙度各类型面的加工方案及经济精度表23 外圆表面加工方案表24 孔加工方案表25 平面加工方案——机械篇标准公差及形位公差附表1 标准公差值注:基本尺寸小于1mm时,无IT14至IT18。
13 22-4-25 10:32附表2 平面度、直线度公差值附表3 圆度、圆柱度公差值附表4 平行度、垂直度、倾斜度公差值附表5 同轴度、对称度、圆跳动、全跳动公差值参考文献1 《金属机械加工工艺人员手册》修订本上海科学技术出版社1981年2 《机械制造工艺学》顾崇衔等编著陕西科学技术出版社1982年3 《航空机械设计手册》第三机械工业部612所编1979年4 《机械制造工艺学课程设计简明手册》华中工学院机械制造工艺教研室编1981年5 《机械工程手册》第46篇机械工业出版社1981年6 《圆柱齿轮加工》上海科学技术出版社1979年切削用量切削用量的选择原则正确地选择切削用量,对提高切削效率,保证必要的刀具耐用度和经济性,保证加工质量,具有重要的作用。
机械加工精度名词解释

机械加工精度名词解释
机械加工精度指的是针对零件或工件加工过程中所要求的尺寸、形状、位置、表面粗糙度等方面的精确度。
精度是指实际测得结果与理论值之间的偏差或误差程度,常用的机械加工精度名词包括以下几个:
1. 尺寸精度:指零件加工后尺寸测量值与设计尺寸之间的偏差。
这是表征零件尺寸准确程度的指标,通常用公差表示。
2. 形状精度:指零件加工后形状特征与设计要求之间的偏差。
例如,平整度、圆度、直线度等,用来描述零件表面的平整程度以及曲线、直线等特征的精确程度。
3. 位置精度:指零件加工后特定特征之间的相对位置偏差。
常用的位置精度名词包括平行度、垂直度、同轴度等,用来描述零件特征在空间中的位置关系。
4. 表面粗糙度:指加工后零件表面的光洁程度。
常用参数包括Ra(平均粗糙度)、Rz(Z向平均粗糙度)等,用来描述零件表面的粗糙度。
这些机械加工精度的指标对于确保零件的质量和功能至关重要,能够影响到零件的装配性能和使用寿命。
机械精度等级标准

机械精度等级标准机械精度等级标准是指机械加工件在尺寸、形位、表面粗糙度等方面的精度等级。
在机械制造领域中,精度等级标准是非常重要的,它直接关系到机械加工件的质量和使用效果。
因此,制定机械精度等级标准是非常必要的。
目前,国际上通用的机械精度等级标准主要有ISO、GB和JIS 等。
其中,ISO是国际标准化组织制定的标准,GB是中国国家标准,JIS是日本工业标准。
这些标准都是根据不同的机械加工件进行制定的,具体的标准内容也有所不同。
下面就分别介绍一下ISO、GB和JIS的机械精度等级标准。
ISO机械精度等级标准主要包括以下几个方面:1.尺寸精度等级:ISO标准规定了从IT01到IT18共18个尺寸精度等级。
其中,IT01是最高精度等级,IT18是最低精度等级。
2.形位精度等级:ISO标准规定了从IT01到IT14共14个形位精度等级。
其中,IT01是最高精度等级,IT14是最低精度等级。
3.表面粗糙度等级:ISO标准规定了从Ra0.1到Ra100共40个表面粗糙度等级。
其中,Ra0.1是最高精度等级,Ra100是最低精度等级。
GB机械精度等级标准主要包括以下几个方面:1.尺寸精度等级:GB标准规定了从IT01到IT18共18个尺寸精度等级。
其中,IT01是最高精度等级,IT18是最低精度等级。
2.形位精度等级:GB标准规定了从IT01到IT14共14个形位精度等级。
其中,IT01是最高精度等级,IT14是最低精度等级。
3.表面粗糙度等级:GB标准规定了从Ra0.1到Ra100共40个表面粗糙度等级。
其中,Ra0.1是最高精度等级,Ra100是最低精度等级。
JIS机械精度等级标准主要包括以下几个方面:1.尺寸精度等级:JIS标准规定了从IT01到IT18共18个尺寸精度等级。
其中,IT01是最高精度等级,IT18是最低精度等级。
2.形位精度等级:JIS标准规定了从IT01到IT14共14个形位精度等级。
机械加工产品公差精度等级标准
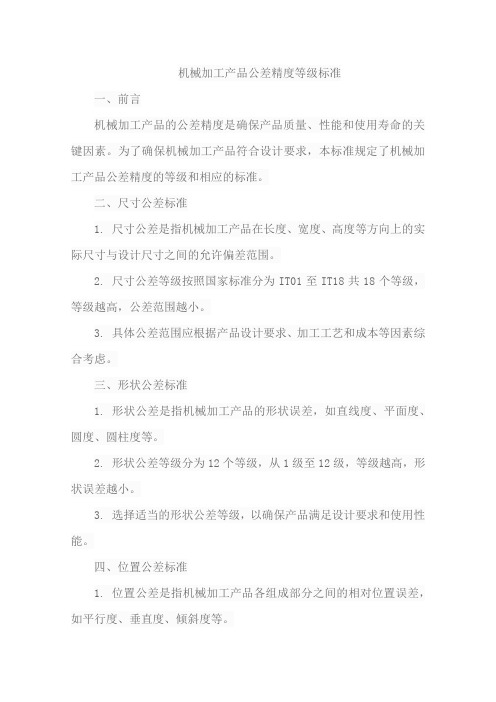
机械加工产品公差精度等级标准一、前言机械加工产品的公差精度是确保产品质量、性能和使用寿命的关键因素。
为了确保机械加工产品符合设计要求,本标准规定了机械加工产品公差精度的等级和相应的标准。
二、尺寸公差标准1. 尺寸公差是指机械加工产品在长度、宽度、高度等方向上的实际尺寸与设计尺寸之间的允许偏差范围。
2. 尺寸公差等级按照国家标准分为IT01至IT18共18个等级,等级越高,公差范围越小。
3. 具体公差范围应根据产品设计要求、加工工艺和成本等因素综合考虑。
三、形状公差标准1. 形状公差是指机械加工产品的形状误差,如直线度、平面度、圆度、圆柱度等。
2. 形状公差等级分为12个等级,从1级至12级,等级越高,形状误差越小。
3. 选择适当的形状公差等级,以确保产品满足设计要求和使用性能。
四、位置公差标准1. 位置公差是指机械加工产品各组成部分之间的相对位置误差,如平行度、垂直度、倾斜度等。
2. 位置公差等级分为11个等级,从1级至11级,等级越高,位置误差越小。
3. 选择适当的位置公差等级,以确保产品装配精度和使用性能。
五、表面粗糙度标准1. 表面粗糙度是指机械加工产品表面微观几何形状的不平度。
2. 表面粗糙度等级分为Ra、Rz、Ry等多种评定参数,每个参数分为不同等级,等级越高,表面越光滑。
3. 选择适当的表面粗糙度等级,以确保产品表面质量和使用性能。
六、材料公差标准1. 材料公差是指机械加工产品所用材料的物理性能、化学成分等与设计要求之间的允许偏差范围。
2. 材料公差标准应根据产品使用环境和性能要求综合考虑,选择符合国家标准和行业标准的材料。
七、热处理公差标准1. 热处理公差是指机械加工产品在热处理过程中产生的尺寸、形状和性能变化与设计要求之间的允许偏差范围。
2. 选择适当的热处理工艺和参数,以确保产品热处理后的稳定性和性能。
八、装配公差标准1. 装配公差是指机械加工产品在装配过程中各零部件之间的相对位置误差和配合间隙。
机械加工表面粗糙度

机械加工表面粗糙度表面粗糙度,是指加工表面具有的较小间距和微小峰谷不平度。
其两波峰或两波谷之间的距离(波距)很小(在1mm以下),用肉眼是难以区别的,因此它属于微观几何形状误差。
表面粗糙度越小,则表面越光滑。
表面粗糙度的大小,对机械零件的使用性能有很大的影响,粗糙度表示方式零件表面经过加工后,看起来很光滑,经放大观察却凹凸不平。
表面粗糙度,是指加工后的零件表面上具有的较小间距和微小峰谷所组成的微观几何形状特征,一般是由所采取的加工方法和(或)其他因素形成的。
零件表面的功用不同,所需的表面粗糙度参数值也不一样。
零件图上要标注表面粗糙度代(符)号,用以说明该表面完工后须达到的表面特性。
表面粗糙度高度参数有3种:1.轮廓算术平均偏差Ra在取样长度内,沿测量方向(Y方向)的轮廓线上的点与基准线之间距离绝对值的算术平均值。
2.微观不平度十点高度Rz指在取样长度内5个最大轮廓峰高的平均值和5个最大轮廓谷深的平均值之和。
3.轮廓最大高度Ry在取样长度内,轮廓最高峰顶线和最低谷底线之间的距离。
目前,一般机械制造工业中主要选用Ra。
Ra值按下列公式计算:Ra=1/l ∫t0|Y(x)|dx或近似为Ra= 1/n ∑|Yi|。
式中,Y为轮廓线上的点到基准线(中线)之间的距离;ι为粗糙度多用于表征钢板,因为钢板涂覆前必须要有一定得粗糙度,否则油漆的咬合力不足,容易脱落。
机械加工表面粗糙度机械加工表面质量,是指零件在机械加工后被加工面的微观不平度,也叫粗糙度,以Ra\Rz\Ry三种代号加数字来表示,机械图纸中都会有相应的表面质量要求,一般是工件表面粗糙度Ra<0.8um的表面时称:镜面。
其加工后的表面质量直接影响被加工件的物理、化学及力学性能。
产品的工作性能、可靠性、寿命在很大程度上取决于主要零件的表面质量。
一般而言,重要或关键零件的表面质量要求都比普通零件要高。
这是因为表面质量好的零件会在很大程度上提高其耐磨性、耐蚀性和抗疲劳破损能力。
机械加工表面粗糙度解释及测量

較低的光潔度對于盡快加工零件和盡量減 少輔助工作量有明顯的經濟效益。何況 在某些用途中﹐一定的粗糙性可以提高 零件的功能﹐有些零件甚至明確規定了 最大和最小粗糙度的值。舉例來說﹐具 有一定粗糙度的表面常常可以增加漆層 或其它涂敷層的黏附性。
有些多功能零件要求很復雜的表面﹐才能 最好地發揮作用。比如發動機的汽缸內 壁必須足夠光滑﹐以便為活塞環提供良 好的密封表面﹐利于壓縮﹐並防止漏氣 。同時﹐表面上還必須具有尺寸﹑數量 和分布都合適的凹點﹐為的是保持潤滑 油。
Ry(ISO,JIS)
全粗糙度高度(最大高度)---Ry(ISO,JIS); Ry=(Peakmax-Valleymin)sampling
length
Ry(DIN)
全粗糙度高度(最大高度)--Ry(DIN); 在各取樣長度內, 求出各Zi, 而在各 Zi中最大值稱為Ry(DIN)=Rmax;
•Rmax對零件表面的劃傷﹑毛刺之類的缺 陷非常敏感﹐很適合于檢驗這樣的狀態 。然而﹐由于生產過程中的個別劃痕或 毛刺往往不具有代表性﹐所以Rmax不適 于監控工序的穩定性
.(Rmax)
Rq
粗糙度幾何(平方)平均值 (Root mean square roughness, Rq)
下圖所示, Rq=(1/N Σyi2)1/2
Rt
最大高度---Rt, 由全體評價長度算出, Rp 和Rv之和. Rt=(PeakmaxValleymin)assessment length
b. Shoe/Skid VS Skidless type stylus 之用法不同: 如圖所示
Shoe/Skid type:滑動器半徑比波峰間隔 (Sm)大很多,使其運動幾乎成一直線。 若Sm過大則可用Shoe來支撐。優點易 於歸零.
表面粗糙度和尺寸公差等级IT
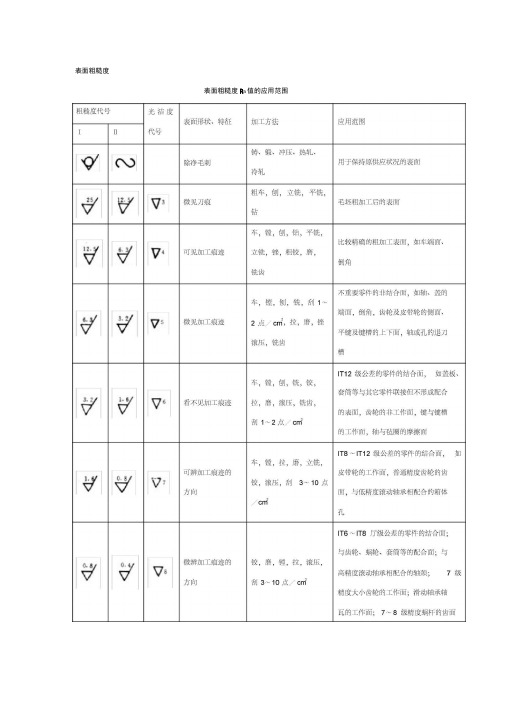
表面粗糙度表面粗糙度R a值的应用范围(旧国标)5,R a的最大允许值取6.3。
因此,在不影响原表面粗糙要求的情况下,取该值有利于加工。
2.粗糙度代号H为第2种过渡方式。
它是取新国标中相应最靠近的上一档的第1系列值,如原光洁度5,R a的最大允许值取3.2。
因此,取该值提高了原表面粗糙度的要求和加工的成本。
尺寸公差等级(IT )公差(1)公差基本术语的含义1)基本尺寸;设计时给定的尺寸,称为基本尺寸。
的基本尺寸2)实际尺寸:零件加工后经测量所得到的尺寸,称为实际尺寸。
3)极限尺寸:实际尺寸允许变化的两个界限值称为极限尺寸。
它以基本尺寸确定。
两个极限值中较大的一个称为最大极限尺寸Dmax (或dmax);较小的一个称为极限尺寸Dmin(或dmin)。
)尺寸偏差;某一尺寸减其基本尺寸所得的代数差,称为尺寸偏差,简称偏差。
实际偏差=实际尺寸一基本尺寸最大极限尺寸减其基本尺寸所得的代数差,称为上偏差;最小极限尺寸减其基本尺寸所得的代数差,称为下偏差;上偏差和下偏差统称为极限偏差。
国家标准规定,孔的上偏差代号为ES,轴的上偏差代号为es;孔的下偏差代号为EI,轴的下偏差代号为ei,则:ES =孔的最大极限尺一孔的基本尺寸cs=轴的最大极限尺寸-轴的基本尺寸EI =孔的最小极限尺寸一孔的基本尺寸ei =轴的最小极限尺寸-轴的奥基本尺寸偏差值可以为正、负或零值。
5)尺寸公差,允许尺寸的变动量称为尺寸公差,简称公差。
公差等于最大极限尺寸与最小极限尺寸的代数差的绝对值;或等于上偏差与下偏差代数差的绝对值。
6)零线:图1a 中示意表明了基本尺寸相向、相互配合的孔与轴之间极限尺寸、尺寸偏差与尺寸公差之间的相互关系,为方便起见,在实际讨论的过程中,通常只画出放大了的孔和轴的公差带,称为公差与配合图解,简称公差带图,如阁l- b 所示。
在公差带图中,确定偏差的一条基准线,即零偏差线,就叩零线,通常零线表示基本尺寸。
正偏差位于零线之上。
表面粗糙度和尺寸公差等级IT
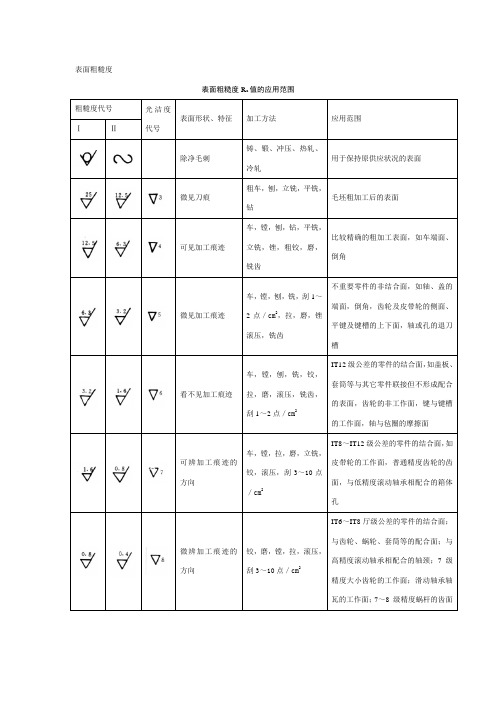
表面粗糙度表面粗糙度R a值的应用范围注:1. 粗糙度代号I为第一种过渡方式。
它是取新国标中相应最靠近的下一档的第1系列值,如原光洁度(旧国标)为▽5,R a的最大允许值取6.3。
因此,在不影响原表面粗糙要求的情况下,取该值有利于加工。
2. 粗糙度代号Ⅱ为第2种过渡方式。
它是取新国标中相应最靠近的上一档的第1系列值,如原光洁度为▽5,R a的最大允许值取3.2。
因此,取该值提高了原表面粗糙度的要求和加工的成本。
尺寸公差等级(IT)公差(1)公差基本术语的含义1)基本尺寸;设计时给定的尺寸,称为基本尺寸。
的基本尺寸2)实际尺寸:零件加工后经测量所得到的尺寸,称为实际尺寸。
3)极限尺寸:实际尺寸允许变化的两个界限值称为极限尺寸。
它以基本尺寸确定。
两个极限值中较大的一个称为最大极限尺寸Dmax(或dmax);较小的一个称为极限尺寸Dmin(或dmin)。
)尺寸偏差;某一尺寸减其基本尺寸所得的代数差,称为尺寸偏差,简称偏差。
实际偏差=实际尺寸一基本尺寸最大极限尺寸减其基本尺寸所得的代数差,称为上偏差;最小极限尺寸减其基本尺寸所得的代数差,称为下偏差;上偏差和下偏差统称为极限偏差。
国家标准规定,孔的上偏差代号为ES,轴的上偏差代号为es;孔的下偏差代号为EI,轴的下偏差代号为ei,则:ES=孔的最大极限尺-孔的基本尺寸cs=轴的最大极限尺寸-轴的基本尺寸EI=孔的最小极限尺寸-孔的基本尺寸ei=轴的最小极限尺寸-轴的奥基本尺寸偏差值可以为正、负或零值。
5)尺寸公差,允许尺寸的变动量称为尺寸公差,简称公差。
公差等于最大极限尺寸与最小极限尺寸的代数差的绝对值;或等于上偏差与下偏差代数差的绝对值。
6)零线:图1a中示意表明了基本尺寸相向、相互配合的孔与轴之间极限尺寸、尺寸偏差与尺寸公差之间的相互关系,为方便起见,在实际讨论的过程中,通常只画出放大了的孔和轴的公差带,称为公差与配合图解,简称公差带图,如阁l-b所示。
尺寸精度与粗糙度

表面粗糙度的测量方法
• 1、比较法:将被测表面与粗糙度标准样块进行比较, 用目测或抚摸、指甲划动等感触判断表面粗糙度的大 小。 • 2、测量仪器:比较显微镜、双管显微镜、干涉显微镜 和轮廓仪等。
6.3 12.5
25
25
25
50 (▽)
50 100
100
计算标准为 4Ra = Ry = Rz
表面粗糙度对零件质量的影响 • • • • 对耐磨性的影响 对疲劳强度的影响 对腐蚀性的影响 对配合性质的影响
•
设计零件时,要根据具体条件选择适当的 表面粗糙度,取值越小,加工越困难成本越高。
表面粗糙度的选用原则
零件的表面质量
零件表面上微小峰谷的高低程度和间距状况, 称为表面粗糙度,也称为微观不平度。 • 基本的表面粗糙度符号: • 切削加工获得的表面: • 用不去除方法获得的表面:
• 表面粗糙度的评定参数 • 1)轮廓算术平均偏差Ra:在取样长度内轮廓偏距绝对值的算术平均值; • 2)微观不平度十点高度Rz:在取样长度内5个最大的轮廓峰高的平均值与5 个 最大的轮廓谷深的平均值之和; • 3)轮廓最大高度Ry:在取样长度内轮廓峰顶线和轮廓谷底线之间的距离。
位置精度 • 指零件的点线面要素 的实际位置相对于理想 位置的准确程度。用位 置公差来控制。国标中 规定了八项位置公差: 平行度、垂直度、倾斜 度、同轴度、对称度、 位置度、圆跳动和全跳 动。
尺寸公差与表面粗糙度

05 总结与展望
总结
尺寸公差与表面粗糙度是机械加工中的重要参数,它 们对产品的性能和可靠性有着显著的影响。
随着科技的不断发展,对尺寸公差与表面粗糙度的要 求也越来越高,这需要我们不断探索新的加工方法和
测量技术,以提高产品的质量和性能。
在实际应用中,应综合考虑尺寸公差与表面粗糙度的 关系,以及它们对产品性能的影响,以制定合理的加
工和测量方案。
展望
随着数字化和智能化技术的不断发展,未来的机械加工将更加依赖于先进的测量技术和数据分析方法。
新的加工方法和材料将对尺寸公差与表面粗糙度提出更高的要求,需要我们不断探索和创新,以适应新 的市场需求。
在未来,尺寸公差与表面粗糙度的研究将更加注重跨学科的合作和交流,以推动相关领域的发展和进步。
测量精度
测量精度对结果的影响很大,因此需要选择精度 合适的测量工具和正确的测量方法,以获得准确 的测量结果。
03 尺寸公差与表面粗糙度的 控制方法
加工工艺控制
加工方法选择
根据零件材料、结构、精度要求等选择合适的加工方 法,如车削、铣削、磨削等。
加工余量分配
合理分配各工序的加工余量,确保最终加工尺寸的精 度。
02
表面粗糙度越高,摩擦系数越大,磨损速度越快,从而影响零
件的耐磨性。
表面粗糙度对零件疲劳强度的影响
03
表面粗糙度越高,应力集中越严重,疲劳裂纹容易形成和扩展,
降低零件的疲劳强度。
尺寸公差对表面粗糙度的影响
尺寸公差越小,表面粗糙度越低
在加工过程中,尺寸公差越小,切削深度、进给量等工艺参数越小,从而减小 表面粗糙度。
热处理工艺
控制零件的热处理工艺,以减小变形和组织不均匀性 对尺寸精度的影响。
表面粗糙度等级常用
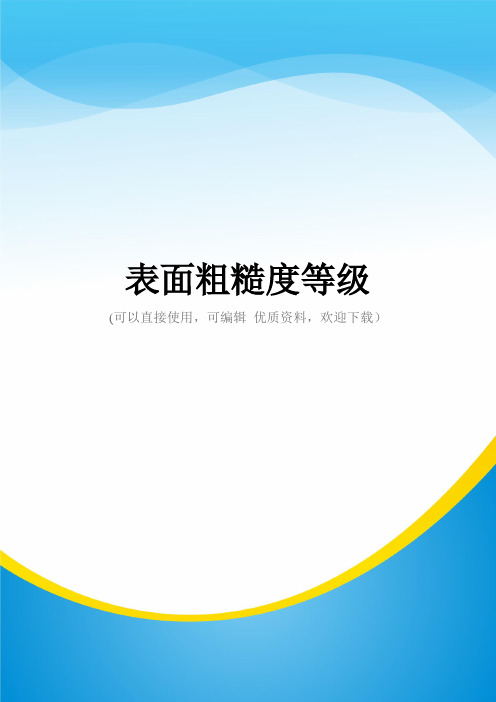
表面粗糙度等级(可以直接使用,可编辑优质资料,欢迎下载)本人从事机械行业多年,为大家提供一些简单的数据:【表面粗糙度等级】【表面粗糙度Ra特征】参数的情况列表如下,如有问题,由时代公司负责解释。
本表还适用于公司TR1系列粗糙度仪。
修改后可测量参数的总数没有变化,仍为13个参数,只是显示在不同的标准中,也就是说:时代粗糙度仪产品参数:涵盖新旧标准参数!(详表面粗糙度有Ra,Rz,Ry 之分,据GB 3505摘录:表面粗糙度参数及其数值(Surface Roughness Parameters and their Values)常用的3个分别是:轮廓算数平均偏差(Ra)--arithmetical mean deviation of the profile;微观不平度十点高度(Rz)--the point height of irregularities;轮廓最大高度(Ry)--maximum height of the profile。
Ra--在取样长度L内轮廓偏距绝对值的算术平均值。
Rz--在取样长度内5个最大的轮廓峰高的平均值与5个最大的轮廓谷深的平均值之和。
Ry--在取样长度L内轮廓峰顶线和轮廓谷底线之间的距离。
如果图面没标注粗糙度选用Ra /Rz /Ry 的情况下默认为Ra。
表面粗糙度是指加工表面具有的较小间距和微小峰谷不平度。
其两波峰或两波谷之间的距离(波距)很小(在1mm以下),用肉眼是难以区别的,因此它属于微观几何形状误差。
表面粗糙度越小,则表面越光滑。
表面粗糙度的大小,对机械零件的使用性能有很大的影响,主要表现在以下几个方面:①表面粗糙度影响零件的耐磨性。
表面越粗糙,配合表面间的有效接触面积越小,压强越大,磨损就越快。
②表面粗糙度影响配合性质的稳定性。
对间隙配合来说,表面越粗糙,就越易磨损,使工作过程中间隙逐渐增大;对过盈配合来说,由于装配时将微观凸峰挤平,减小了实际有效过盈,降低了联结强度。
加工表面粗糙度标准
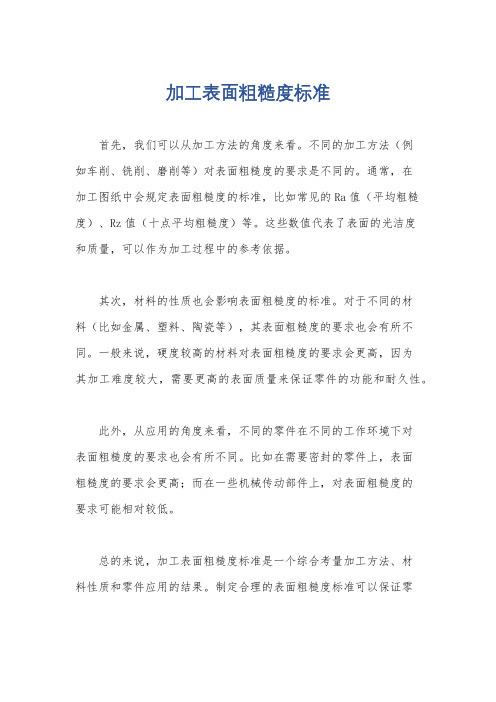
加工表面粗糙度标准
首先,我们可以从加工方法的角度来看。
不同的加工方法(例
如车削、铣削、磨削等)对表面粗糙度的要求是不同的。
通常,在
加工图纸中会规定表面粗糙度的标准,比如常见的Ra值(平均粗糙度)、Rz值(十点平均粗糙度)等。
这些数值代表了表面的光洁度
和质量,可以作为加工过程中的参考依据。
其次,材料的性质也会影响表面粗糙度的标准。
对于不同的材
料(比如金属、塑料、陶瓷等),其表面粗糙度的要求也会有所不同。
一般来说,硬度较高的材料对表面粗糙度的要求会更高,因为
其加工难度较大,需要更高的表面质量来保证零件的功能和耐久性。
此外,从应用的角度来看,不同的零件在不同的工作环境下对
表面粗糙度的要求也会有所不同。
比如在需要密封的零件上,表面
粗糙度的要求会更高;而在一些机械传动部件上,对表面粗糙度的
要求可能相对较低。
总的来说,加工表面粗糙度标准是一个综合考量加工方法、材
料性质和零件应用的结果。
制定合理的表面粗糙度标准可以保证零
件的质量和性能,提高加工效率和降低成本。
因此,在实际加工过程中,需要根据具体情况制定和执行相应的表面粗糙度标准。
机械设计,制图,公差,表面粗糙度标注!机械制造类专用!很全
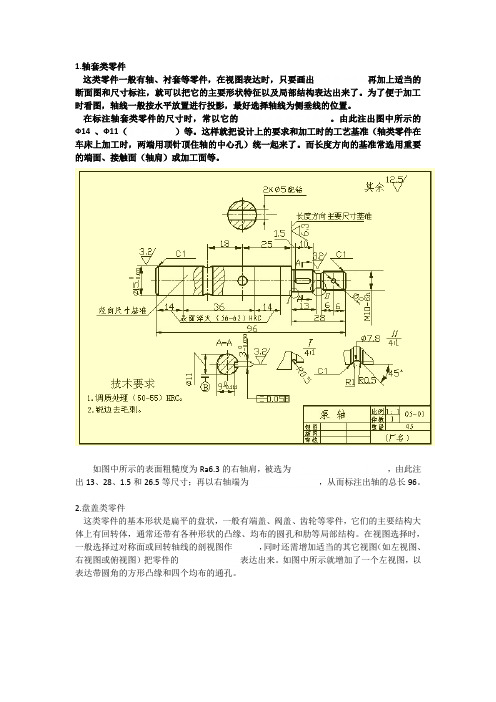
1.轴套类零件这类零件一般有轴、衬套等零件,在视图表达时,只要画出一个基本视图再加上适当的断面图和尺寸标注,就可以把它的主要形状特征以及局部结构表达出来了。
为了便于加工时看图,轴线一般按水平放置进行投影,最好选择轴线为侧垂线的位置。
在标注轴套类零件的尺寸时,常以它的轴线作为径向尺寸基准。
由此注出图中所示的Ф14 、Ф11(见A-A断面)等。
这样就把设计上的要求和加工时的工艺基准(轴类零件在车床上加工时,两端用顶针顶住轴的中心孔)统一起来了。
而长度方向的基准常选用重要的端面、接触面(轴肩)或加工面等。
如图中所示的表面粗糙度为Ra6.3的右轴肩,被选为长度方向的主要尺寸基准,由此注出13、28、1.5和26.5等尺寸;再以右轴端为长度方向的辅助基,从而标注出轴的总长96。
2.盘盖类零件这类零件的基本形状是扁平的盘状,一般有端盖、阀盖、齿轮等零件,它们的主要结构大体上有回转体,通常还带有各种形状的凸缘、均布的圆孔和肋等局部结构。
在视图选择时,一般选择过对称面或回转轴线的剖视图作主视图,同时还需增加适当的其它视图(如左视图、右视图或俯视图)把零件的外形和均布结构表达出来。
如图中所示就增加了一个左视图,以表达带圆角的方形凸缘和四个均布的通孔。
在标注盘盖类零件的尺寸时,通常选用通过轴孔的轴线作为径向尺寸基准,长度方向的主要尺寸基准常选用重要的端面。
3.叉架类零件这类零件一般有拨叉、连杆、支座等零件。
由于它们的加工位置多变,在选择主视图时,主要考虑工作位置和形状特征。
对其它视图的选择,常常需要两个或两个以上的基本视图,并且还要用适当的局部视图、断面图等表达方法来表达零件的局部结构。
踏脚座零件图中所示视图选择表达方案精练、清晰对于表达轴承和肋的宽度来说,右视图是没有必要的,而对于T字形肋,采用剖面比较合适。
在标注叉架类零件的尺寸时,通常选用安装基面或零件的对称面作为尺寸基准。
尺寸标注方法参见图。
4.箱体类零件一般来说,这类零件的形状、结构比前面三类零件复杂,而且加工位置的变化更多。
不同的加工方法可能达到的尺寸精度及表面粗糙度
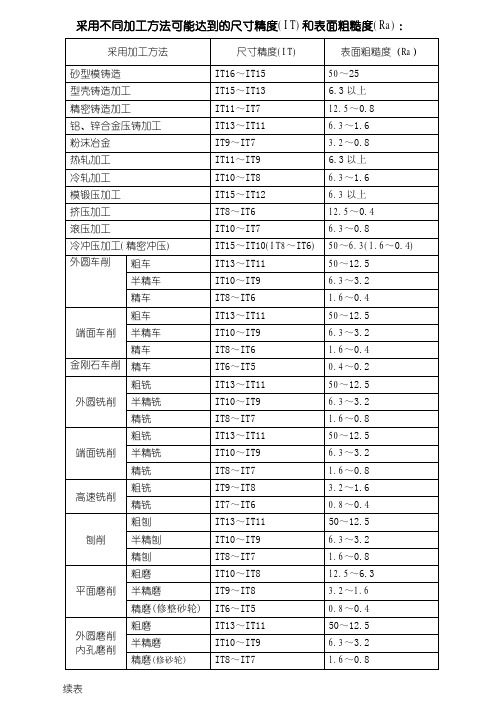
2.基本尺寸小于或等于 1mm 时无 IT14 至 IT18。
0.4~0.2
6.3~0.4
0.05~0.01 0.8~0.2 3.2~0.4 6.3~0.05 0.4~0.2 0.8~0.4 0.8~0.05 0.8~0.4 0.4~0.2 0.4~0.2 0.2~0.1
机械切削加工尺寸未注公差(單位:mm)
公称尺寸
f-精密级
0.5~3
±0.05
>3 ~6
±0.05
50~12.5 25~6.3 50~12.5 6.3~3.2 3.2~1.6 0.8~0.4 25~12.5 6.3~3.2 1.6~0.8 0.8~0.2 12.5~25 6.3~1.6 1.6~0.8 0.8~0.4 0.8~0.1 50~0.8 50~12.5
IT8~IT7 IT10~IT8 IT9~IT8
切削加工:粗加工:IT13~IT11 Ra:50~12.5 ; 半精加工:IT10~IT8 Ra:6.3~1.6 ; 精加工:IT7~IT5 Ra:0.8~0.2 ; 精密加工:IT5 以下 Ra:0.1~0.025 ; 超精加工:IT3 以下 Ra:0.025 以下的最光面.
1.粗糙面(如 Ra:50、25、12.5)的粗加工公差等级:T13~IT11,如粗车、粗铣、粗刨、 粗镗、毛锉、锯断、钻孔、倒角等,适用于没有配合要求的自由面; 2.半光面(如 Ra:6.3、3.2、1.6)的半精加工公差等级:IT10~IT8,如半精车、半精铣、半精镗、 粗磨、扩孔等,适用于接触面、不甚精确定心的配合面; 3.光面(如 Ra:0.8、0.4、0.2)的精加工公差等级:IT7~IT5,如精车、精拉、精铰、精铣、 精磨、座标磨、研磨、抛光等,适用于要求精确定心的重要配合面; 4.最光面(如 Ra:0.1、0.05、0.02)的超精加工公差等级:IT5 以下,如研磨、珩磨、超精磨、抛光、 镜面磨等,适用于高精度、高速运动的零部件的配合表、较重要的装饰面,如镜面模仁等;
零件表面粗糙度与尺寸公差
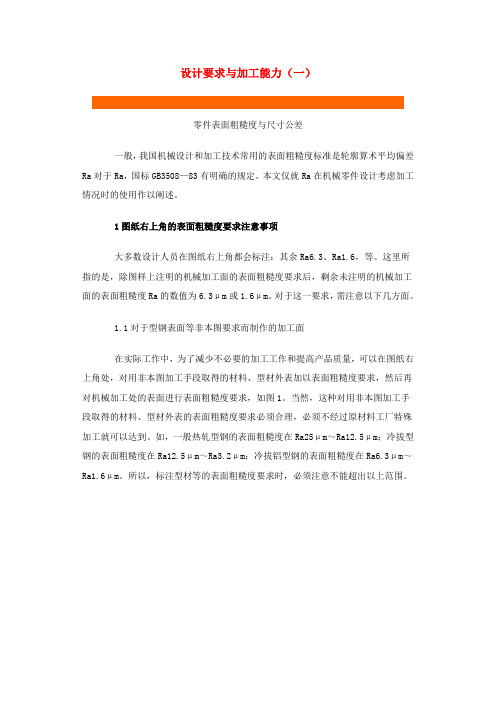
设计要求与加工能力(一)零件表面粗糙度与尺寸公差一般,我国机械设计和加工技术常用的表面粗糙度标准是轮廓算术平均偏差Ra对于Ra,国标GB3508—83有明确的规定。
本文仅就Ra在机械零件设计考虑加工情况时的使用作以阐述。
1图纸右上角的表面粗糙度要求注意事项大多数设计人员在图纸右上角都会标注:其余Ra6.3、Ra1.6,等。
这里所指的是,除图样上注明的机械加工面的表面粗糙度要求后,剩余未注明的机械加工面的表面粗糙度Ra的数值为6.3μm或1.6μm。
对于这一要求,需注意以下几方面。
1.1对于型钢表面等非本图要求而制作的加工面在实际工作中,为了减少不必要的加工工作和提高产品质量,可以在图纸右上角处,对用非本图加工手段取得的材料、型材外表加以表面粗糙度要求,然后再对机械加工处的表面进行表面粗糙度要求,如图1。
当然,这种对用非本图加工手段取得的材料、型材外表的表面粗糙度要求必须合理,必须不经过原材料工厂特殊加工就可以达到。
如,一般热轧型钢的表面粗糙度在Ra25μm~Ra12.5μm;冷拔型钢的表面粗糙度在Ra12.5μm~Ra3.2μm;冷拔铝型钢的表面粗糙度在Ra6.3μm~Ra1.6μm。
所以,标注型材等的表面粗糙度要求时,必须注意不能超出以上范围。
1.2对于用铸造、锻造、焊接等本图要求而制作的毛坯件在使用铸造、锻造、焊接制作毛坯时,尤其是型腔件,对它们的机械加工往往是一部分,而不是全部加工。
此时,设计人员一般在图纸右上角处标上:其余Ra6.3。
这里的Ra6.3μm仅仅是指对型腔件要求进行机械加工部分,除去图纸上已经有表面粗糙度要求的_部分外表面加以表面粗糙度要求而已,并没有对非机械加工部分(如铸造、锻造)的外表加以表面粗糙度要求。
所以,为了不产生混淆,有必要对工件全面要求,就是在对机械加工处的表面进行表面粗糙度要求之前,对用铸造、锻造、焊接等本图要求而制作的毛坯件的外表进行表面粗糙度要求,如图2。
各种加工方法的经济精度和表面粗糙度
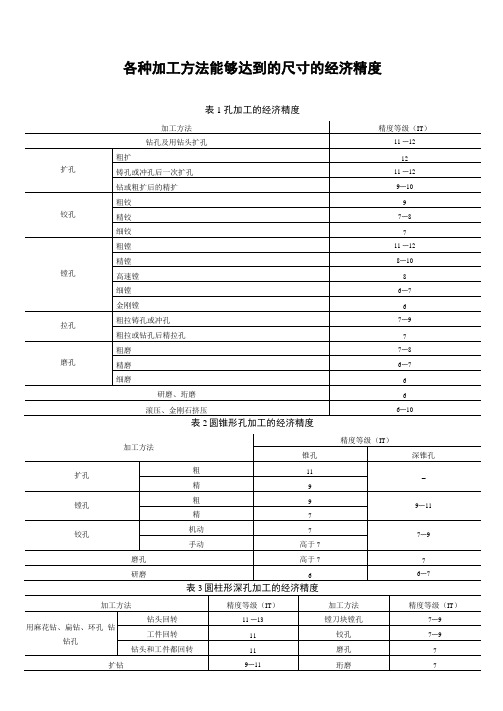
各种加工方法能够达到的尺寸的经济精度表1 孔加工的经济精度表2圆锥形孔加工的经济精度表3圆柱形深孔加工的经济精度6mm7mm91<1m2端铣刀铣削的加工精度在相同的条件下大体上比圆柱铣刀铣削高一级。
3细铣仅用于端铣刀铣削。
11各种加工方法能够达到的形状的经济精度2315各种加工方法所能够达到的相互位置的经济精度表19同轴度的经济精度表20 轴心线相互平行的孔的位置经济精度注:对于钻、卧镗及组合机床的镗孔偏差同样适用于铰孔。
表21轴心线相互垂直的孔的位置经济精度各种加工方法能够达到的零件表面粗糙度表22 各种加工方法能够达到的零件表面粗糙度各类型面的加工方案及经济精度表23外圆表面加工方案标准公差及形位公差附表1标准公差值1mm IT14IT1813 22-2-21 16:331 《金属机械加工工艺人员手册》修订本上海科学技术出版社1981年2 《机械制造工艺学》顾崇衔等编著陕西科学技术出版社1982年3 《航空机械设计手册》第三机械工业部612所编1979年4 《机械制造工艺学课程设计简明手册》华中工学院机械制造工艺教研室编1981年5 《机械工程手册》第46篇机械工业出版社1981年6 《圆柱齿轮加工》上海科学技术出版社1979年切削用量切削用量的选择原则正确地选择切削用量,对提高切削效率,保证必要的刀具耐用度和经济性,保证加工质量,具有重要的作用。
1粗加工切削用量的选择原则:粗加工时加工精度与表面求不高,毛坯余量较大。
因此,选择粗加工的切削用量时,要尽可能保证较高的单位时间金属切除量(金属切除率)和必要的刀具耐用度,以提高生产效率和降低加工成本。
金属切除率可以用下式计算:Z k vfa X1000式中Zw——单位时间内的金属切除量(mm3/s);v --- 切削速度(m/s);f --- 进给量(mm/r);a p -------- 切削深度(mm)。
提高切削速度、增大进给量和切削深度,都能提高金属切除率。
各种加工方法的加工精度

各种加工方法的加工精度一:车削车削中工件旋转,形成主切削运动.刀具沿平行旋转轴线运动时,就形成内、外园柱面。
刀具沿与轴线相交的斜线运动,就形成锥面.仿形车床或数控车床上,可以控制刀具沿着一条曲线进给,则形成一特定的旋转曲面。
采用成型车刀,横向进给时,也可加工出旋转曲面来。
车削还可以加工螺纹面、端平面及偏心轴等.车削加工精度一般为IT8—IT7,表面粗糙度为6.3—1.6μm。
精车时,可达IT6—IT5,粗糙度可达0。
4—0.1μm。
车削的生产率较高,切削过程比较平稳,刀具较简单。
二:铣削主切削运动是刀具的旋转。
卧铣时,平面的形成是由铣刀的外园面上的刃形成的。
立铣时,平面是由铣刀的端面刃形成的。
提高铣刀的转速可以获得较高的切削速度,因此生产率较高.但由于铣刀刀齿的切入、切出,形成冲击,切削过程容易产生振动,因而限制了表面质量的提高。
这种冲击,也加剧了刀具的磨损和破损,往往导致硬质合金刀片的碎裂。
在切离工件的一般时间内,可以得到一定冷却,因此散热条件较好。
按照铣削时主运动速度方向与工件进给方向的相同或相反,又分为顺铣和逆铣。
顺铣铣削力的水平分力与工件的进给方向相同,工件台进给丝杠与固定螺母之间一般有间隙存在,因此切削力容易引起工件和工作台一起向前窜动,使进给量突然增大,引起打刀.在铣削铸件或锻件等表面有硬度的工件时,顺铣刀齿首先接触工件硬皮,加剧了铣刀的磨损。
逆铣可以避免顺铣时发生的窜动现象。
逆铣时,切削厚度从零开始逐渐增大,因而刀刃开始经历了一段在切削硬化的已加工表面上挤压滑行的阶段,加速了刀具的磨损。
同时,逆铣时,铣削力将工件上抬,易引起振动,这是逆铣的不利之处.铣削的加工精度一般可达IT8—IT7,表面粗糙度为6。
3—1。
6μm.普通铣削一般只能加工平面,用成形铣刀也可以加工出固定的曲面。
数控铣床可以用软件通过数控系统控制几个轴按一定关系联动,铣出复杂曲面来,这时一般采用球头铣刀。
数控铣床对加工叶轮机械的叶片、模具的模芯和型腔等形状复杂的工件,具有特别重要的意义。