计算齿轮侧隙
侧隙计算

1、曲轴齿轮与惰齿轮A啮合时的法向侧隙计算曲轴齿轮、惰齿轮A均是变位斜齿轮,其标准中心距计算如下:a=m n(z1+z2)/(2cosβ),已知m n=2.5,z1=21,z2=31,β=18°计算得a=68.35mm设计图纸给定安装中心距为69.77~69.82mm,查阅资料得法向侧隙计算公式为:Cn= m n(z v1+z v2)cosαn(invαn′- invαn0′)当量齿数z v1= z1/cos3β=24.42,z v2= z2/cos3β=36.05法向压力角αn=15°αn0′为两齿轮无侧隙安装时的啮合角invαn0′=2tanαn(x t1+ x t2)/(z v1+z v2)+ invαn端面变位系数x t1= x n1cosβ,x t2= x n2cosβ,已知法面变位系数x n1=0.417,x n2=0.176,则,x t1=0.397,x t2=0.167,计算得invαn0′=0.01115αn′为实际安装后的啮合角,设实际安装后的中心距为a′,有这样一个公式:a′cosαn′=a cosαn取a′=69.77mm时,αn′=18.87°,Cn=0.1853mm取a′=69.82mm时,αn′=18.99°,Cn=0.2234mm所以该对齿轮安装后的法向侧隙范围是0.1853~0.2234mm经验公式:J nbmin=2(0.06+0.0005a i+0.03 m n)/3,其中J nbmin为最小法向侧隙,a i为最小安装中心距,计算得J nbmin=0.1133mm2、凸轮轴齿轮与惰齿轮A啮合时的法向侧隙计算凸轮轴齿轮、惰齿轮A均是变位斜齿轮,其标准中心距计算如下:a=m n(z1+z2)/(2cosβ),已知m n=2.5,z1=42,z2=31,β=18°计算得a=95.95mm设计图纸给定安装中心距为96.49~96.54mm,查阅资料得法向侧隙计算公式为:Cn= m n(z v1+z v2)cosαn(invαn′- invαn0′)当量齿数z v1= z1/cos3β=48.84,z v2= z2/cos3β=36.05法向压力角αn=15°αn0′为两齿轮无侧隙安装时的啮合角invαn0′=2tanαn(x t1+ x t2)/(z v1+z v2)+ invαn端面变位系数x t1= x n1cosβ,x t2= x n2cosβ,已知法面变位系数x n1=0.002,x n2=0.176,则,x t1=0.0019,x t2=0.167,计算得invαn0′=0.00722αn′为实际安装后的啮合角,设实际安装后的中心距为a′,有这样一个公式:a′cosαn′=a cosαn取a′=96.49mm时,αn′=16.15°,Cn=0.1005mm取a′=96.54mm时,αn′=16.26°,Cn=0.1357mm所以该对齿轮安装后的法向侧隙范围是0.1005~0.1357mm经验公式:J nbmin=2(0.06+0.0005a i+0.03 m n)/3,其中J nbmin为最小法向侧隙,a i为最小安装中心距,计算得J nbmin=0.1222mm3、惰齿轮B与惰齿轮A啮合时的法向侧隙计算惰齿轮B不是变位齿轮,但可以看成是法面变位系数x n1=0的变位斜齿轮,惰齿轮A是变位斜齿轮,其标准中心距计算如下:a=m n(z1+z2)/(2cosβ),已知m n=2.5,z1=29,z2=31,β=18°计算得a=78.86mm设计图纸给定安装中心距为79.29~79.34mm,查阅资料得法向侧隙计算公式为:Cn= m n(z v1+z v2)cosαn(invαn′- invαn0′)当量齿数z v1= z1/cos3β=33.72,z v2= z2/cos3β=36.05法向压力角αn=15°αn0′为两齿轮无侧隙安装时的啮合角invαn0′=2tanαn(x t1+ x t2)/(z v1+z v2)+ invαn端面变位系数x t1= x n1cosβ,x t2= x n2cosβ,已知法面变位系数x n1=0,x n2=0.176,则,x t1=0,x t2=0.167,计算得invαn0′=0.00743αn′为实际安装后的啮合角,设实际安装后的中心距为a′,有这样一个公式:a′cosαn′=a cosαn取a′=79.29mm时,αn′=16.12°,Cn=0.0390mm取a′=79.34mm时,αn′=16.24°,Cn=0.0678mm所以该对齿轮安装后的法向侧隙范围是0.0390~0.0678mm经验公式:J nbmin=2(0.06+0.0005a i+0.03 m n)/3,其中J nbmin为最小法向侧隙,a i为最小安装中心距,计算得J nbmin=0.1164mm。
齿轮副最大与最小侧隙的计算

Ts1、Ts2—分别为小齿轮、大齿轮的齿厚公差(μm);
Ta—齿轮副的中心距公差(μm);
αn’—齿轮压力角(0)。
≤10
>10-25
>25-60
>60
喷油润滑
10
20
30
30-50
油池润滑
5-10
2.齿轮副最大法向侧隙值的计算
计算齿轮副的最大法向侧隙时,主要考虑齿轮的加工精度。其计算公式如下
Jnmax=Jmin+【(Ts12+Ts22)Xcos2αn+(TaX2Xsinαn)】(1/2)
式中 Jnmax—最大法向侧隙(μm);
式中Jnmin—最小法向侧隙(μm);
a—齿轮副中心距(μm);
α1
△t1、△t2—分别为齿轮、箱体温度与标准温度(200C)之差(0C);
αn’—齿轮副法向啮合角(0);
δ—润滑状况系数(检附表);
mn—齿轮模数。
δ表值
润滑方式
齿轮节圆圆周速度v(m/s)
齿轮副侧隙探讨
一、由最小侧隙推导大小齿轮齿厚上偏差:
二、齿轮副最大侧隙计算
齿轮副最小和最大法向侧隙值计算
2010-04-28 12:16
1.齿轮副最小法向侧隙值的计算
计算齿轮副的最小法向侧隙时,主要考虑齿轮副的热变形和润滑状况的工作条件。其计算公式如下:
Jnmin=2a·(α1△t1-α2△t2)sinαn’+δmn
齿轮侧隙计算公式

齿轮侧隙计算公式齿轮是机械传动中常用的一种元件,它通过齿间啮合的方式来传递动力和扭矩。
齿轮的侧隙是指两个相邻齿面之间的距离,它对齿轮传动的精度和可靠性有着非常重要的影响。
因此,在进行齿轮设计和制造时,需要准确计算齿轮的侧隙。
齿轮侧隙的计算可以通过以下公式来实现:S=Kt(bm+bf+ΔF)其中,S表示齿轮侧隙,Kt表示齿轮侧隙系数,bm表示模数,bf表示齿宽系数,ΔF表示两轮啮合产生的变形力。
首先,我们需要确定齿轮侧隙系数Kt。
对于各种齿轮传动方式(平行轴齿轮、斜齿轮、锥齿轮等),都有相应的侧隙系数值。
在平行轴齿轮啮合时,Kt一般为0.05~0.15;在斜齿轮啮合时,Kt一般为0.07~0.20;在锥齿轮啮合时,Kt一般为0.10~0.20。
接下来,通过计算齿宽系数bf,可以确定齿轮侧隙计算中的第二个参数。
bf分为全齿宽系数和有效齿宽系数两种,通常取全齿宽系数。
bf的计算方法是bf=b/(z*cosα),其中b表示齿宽,z表示齿数,α表示齿轮齿面斜角。
最后,我们需要考虑啮合变形力的影响。
在齿轮啮合过程中,由于齿轮齿面形状、变形等因素,会在齿面产生一定的变形力。
啮合变形力ΔF的计算可以采用有限元法、试验法等方法,在具体的设计中需要根据实际情况进行确定。
通过以上公式和参数计算,我们可以得到准确的齿轮侧隙值。
齿轮侧隙对于齿轮的传动精度和可靠性有着非常重要的作用,因此在齿轮设计和制造过程中,必须非常注重齿轮侧隙的准确计算。
同时,在实际生产中也需要进行严格的监测和测量,保证齿轮的稳定性和可靠性。
齿轮、齿轮副误差及侧隙的代号和定义 (GB11365-89)
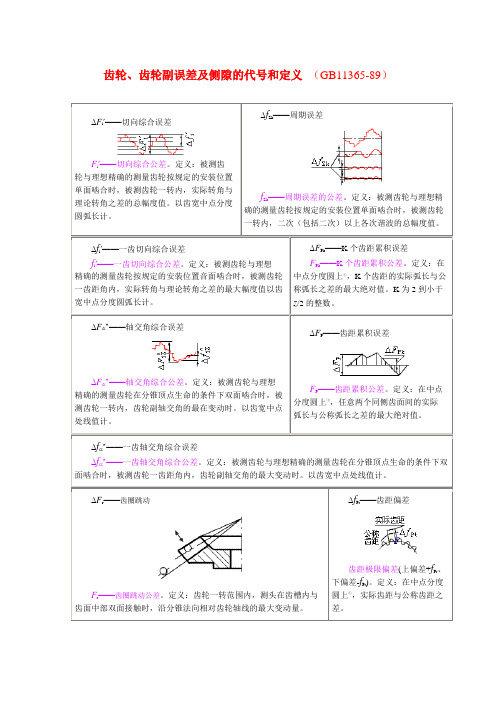
齿轮、齿轮副误差及侧隙的代号和定义(GB11365-89)
之比的百分数即
注:①允许在齿面中部测量。
②齿轮副转动整周期按下式计算:n2=z1/x
式中:n2——大轮转数,z1——小轮齿数,x——大、小轮齿数的最大公约数。
什么是齿轮副的侧隙
指的就是两个齿轮在啮合状态下一个齿轮(一)一个齿(1)和另一个齿轮(二)的一个齿(2)的齿面接触时,这个齿(一中的1号)的另一个齿面和另一个齿轮(二)的和这个齿(一中的1号)相啮合的齿(二中的2号)相邻的齿在分度圆上的间隙,一中的1号齿在二中的两个齿中间,在理论上齿轮副分析中这个侧隙为零,但实际中齿轮运行中会齿型会变大(温度上升)。
要是在常温没侧隙就会咬死,而且为了在齿轮的侧隙上留下空间储油。
在齿型变到最大时也要留有空间给储油。
所以都会有侧隙。
有侧隙也有缺点就是当齿轮副转换转向时会带来回程误差和冲击。
但不同场合的齿轮副的侧隙要求不同,像仪表为了减小回程误差就要小侧隙,而经常转换转向的地方防止冲击过大也要小侧隙。
太小的侧隙容易咬死而且因为储油问题而润滑不良。
而其他地方的侧隙可以大一些,但侧隙太大的问题也不用多
说,肯定不行的。
会有不同的用场会有一些合理的推荐值。
具体数据查询手册。
在装配中多用铅丝法测量侧隙,用一个粗细合适的铅丝让在啮合的两个齿在啮合过程中夹一下,然后测量铅丝变形后的厚度来测量侧隙。
齿轮副侧隙计算方法

润滑方式 油池润滑
喷油润滑
齿 轮 线 速 度%&&+:"
1#"% "%#1#(* (*#1#.%
1$.%
/-8%#& #*""%$0-
"%0(%0’%0#’%"*%$0-
注’0- 为法向模数
#($/-9是考虑齿轮传 动 的 温 度 变 化! 这 时 由 于 齿 轮 和箱体的材料不同!温度不同以及材料的线膨胀系数不 同!而使原侧隙/-8发 生 减 小 #或 增 大$! 所 以! 除 前 述 /-8外! 还需加上/-9的补偿" 所以
;%!$"&&! "理论值# 最 大 法 向 侧 隙/-&8F;/E&8F<=+!;%!.$6<=+(%1&&
;%!.%&&! "理论值# 若考虑加工及安装产生的基节$轴向$轴线平行度 和中心距偏差%则有! 最小法向侧隙/-&,-;%!$":%38% (+,-!-:4
;%!’$" "&&# 最大法向侧隙/-&8F;%!.%7%38% (+,-!-74
%!%"#
3B
% ! 基节极限偏差 3C9
?%!%(%
3C9
&!齿向公差 :’ 接触斑点 按齿高不小于
%!%(% *%D
:’ *%D
按齿长不小于 /%D
%!%"# ?%!%(% %!%(%
/%D
%!%$";%!’$* "&&# /-&8F; "%2+," 72+,( % #<=+"<=+!- 7 %38% (+,-!-
直齿圆柱齿轮变位系数、公法线长度、齿厚、最小法向侧隙的计算

外啮合直齿圆柱齿轮变位系数、公法线长度、齿厚、最小法向侧隙的计算1,直齿圆柱齿轮变位系数计算:Case1:a,此处例子仅计算用齿条型刀具加工时的情况(插齿刀加工见相关手册公式):小结:由此可知本例选取的齿数在不变位的情况也不会产生根切现象。
b,根据下图选择大小齿轮的变位系数和x∑。
本例在P6-P7区间取值。
即齿根及齿面承载能力较高区,进行选择。
因大小齿轮的齿数和为18+19=37。
所以本例选择的变位系数和x∑=0.8。
本例我们的两个齿轮在工作时属于减速运动,所以按减速运动的变位系数分配线图,进行2个齿轮的变位系数的选择。
先按(z1+z1)/2=18.5,作为横坐标,做一条垂线(图中蓝色的线),再按x∑/2=0.4,作为纵坐标,做一条水平线(图中橙色的线),接着沿着L线的趋势,穿过上面2条线的交点做一条射线(图中红色的线)最后按大小齿轮的齿数做相应的垂线(图中紫色的线),即得到需要的各自变位系数。
最后我们选择的变位系数即为:小齿轮x1=0.42,大齿轮x2=0.38。
【基本保障其和与之前x ∑一致,即可】。
c,验算变位后的齿顶厚度:注:一般要求齿顶厚Sa≥0.25m;对于表面淬火的齿轮要求Sa≥0.4m下表中的da的计算见后面的计算表格中的计算公式(因为当齿轮变位后,齿顶圆的计算和未变位齿轮的计算稍有差别-涉及到变位系数和中心距变位系数。
)。
分度圆直径db mm 73.8 77.9齿轮的齿顶圆直径da mm 83.027 86.799齿轮的齿顶压力角αa °27.27 26.17中间值invα0.0215 0.0215中间值invαa 0.0587 0.0347齿顶厚Sα 5.77 7.47判断值0.25m 1.025 1.025判断值0.4m 1.64 1.64小结:计算发现变位后的齿轮齿顶厚满足设计需求。
根据上面确定的变位系数,计算齿轮的中心距变位系数和节圆直径、齿根圆直径、齿顶圆直径。
齿轮侧隙及齿厚偏差自动计算表
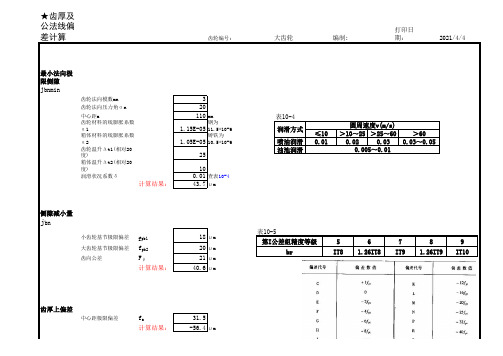
Ess
-66.0 μm
Esi
-176.0 μm
Ess*cosα n0.72Fr*sin αn
计算结果: Esi*cosα n+0.72Fr*s inαn 计算结果:
-75.80997 μm -151.5956 μm
Ewms/(sin αMt*cosβ b) 计算结果 Ewms/(sin αMt*cosβ b)*cos(π /2z)
★齿厚及 公法线偏 差计算
最小法向极 限侧隙
jbnmin
jnmin=1000* a(α1*Δ
t1-α2*Δ
t2)*2*sin
αn+δ
*mn*1000
齿轮法向模数mn
齿轮法向压力角αn
中心距a 齿轮材料的线膨胀系数 α1 箱体材料的线膨胀系数 α2 齿轮温升Δt1(相对20 度) 箱体温升Δt2(相对20 度)
>60
喷油润滑 0.01
0.02
0.03 0.03~0.05
油池润滑
0.005~0.01
表10-5 第I公差组精度等级 br
5
6
7
8
9
IT8 1.26IT8 IT9 1.26IT9 IT10
齿厚公差
齿圈径向跳动公差
径向切深公差
齿厚下偏差
齿距极限偏差Fpt 齿厚上偏差/Fpt 齿厚下偏差/Fpt
Ts=2*tanα n*(Fr^2+br ^2)^0.5 Fr
-180.9787
偶数齿
本表不属 于国家标 准,仅供 注:1 参考.
2 αMt1= 25 3 螺旋角β 8.1094
见标准齿轮 参数计算
4
βb= 0.132949
滑移齿轮间隙计算公式

滑移齿轮间隙计算公式在机械传动系统中,齿轮是一种常见的传动元件,它通过齿轮的啮合来传递动力和转矩。
在齿轮传动系统中,滑移齿轮间隙是一个重要的参数,它直接影响到齿轮传动系统的工作效率和传动精度。
因此,准确地计算滑移齿轮间隙是非常重要的。
滑移齿轮间隙是指两个啮合的齿轮之间的空隙,它的大小会影响到齿轮的传动效果。
通常情况下,滑移齿轮间隙的大小会受到齿轮的制造精度和安装精度的影响。
因此,为了确保齿轮传动系统的正常工作,需要对滑移齿轮间隙进行准确的计算和控制。
滑移齿轮间隙的计算公式可以根据齿轮的模数、齿数、齿顶高和齿根高来确定。
一般情况下,滑移齿轮间隙的计算公式如下:δ = (0.167 × (m1 + m2)) c。
其中,δ表示滑移齿轮间隙的大小,m1和m2分别表示两个啮合齿轮的模数,c表示齿根高的总和。
在实际应用中,可以根据这个公式来计算滑移齿轮间隙的大小,从而确定齿轮传动系统的工作参数。
但是需要注意的是,这个公式只是一个理论计算公式,实际的滑移齿轮间隙的大小还会受到齿轮制造精度、安装精度和工作环境等因素的影响。
因此,在实际应用中,还需要根据具体情况进行调整和修正。
另外,除了滑移齿轮间隙的计算公式之外,还需要注意一些影响滑移齿轮间隙的因素。
例如,在齿轮制造过程中,需要控制好齿轮的模数、齿数、齿顶高和齿根高等参数,以确保齿轮的制造精度。
在齿轮安装过程中,需要保证齿轮的啮合精度和轴向间隙的控制,以确保齿轮传动系统的正常工作。
此外,还需要注意到滑移齿轮间隙的大小会直接影响到齿轮传动系统的工作效率和传动精度。
因此,在实际应用中,需要根据具体的工作要求和工作环境来确定滑移齿轮间隙的大小。
在一些高精度的传动系统中,需要对滑移齿轮间隙进行精确的控制,以确保齿轮传动系统的正常工作。
总之,滑移齿轮间隙的计算公式是确定齿轮传动系统工作参数的重要依据。
通过准确地计算和控制滑移齿轮间隙,可以确保齿轮传动系统的正常工作,提高传动效率和传动精度。
齿轮侧隙及齿厚偏差自动计算表
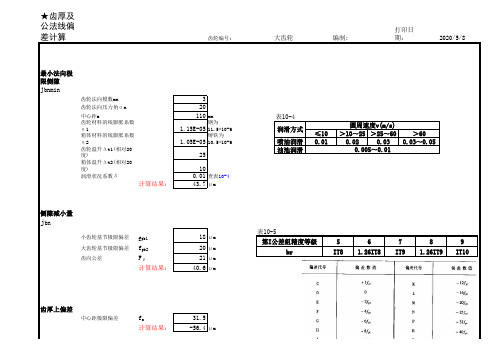
★齿厚及公法线偏差计算齿轮编号:编制:打印日期:最小法向极限侧隙j bnmin j nmin =1000*a(α1*Δt1-α2*Δt2)*2*sin αn+δ*m n *1000齿轮法向模数mn 3齿轮法向压力角αn 20 中心距a 110mm 齿轮材料的线膨胀系数α1 1.15E-05钢为11.5*10-6箱体材料的线膨胀系数α2 1.05E-05铸铁为10.5*10-6齿轮温升Δt1(相对20度)25箱体温升Δt2(相对20度)10润滑状况系数δ0.01查表10-4计算结果:43.7μm 侧隙减小量j bnJn=(F pb 1^2+F pb 2^2+2.104*F β^2)^0.5小齿轮基节极限偏差f pb118μm 大齿轮基节极限偏差f pb220μm 齿向公差F β21μm 计算结果:40.6μm 齿厚上偏差Ess=-((j nmin +J n )/(2cos αn)+fa*tan αn)中心距极限偏差f a 31.5计算结果:-56.4μm 齿厚公差Ts=2*tan αn*(Fr^2+br^2)^0.5齿圈径向跳动公差Fr 56径向切深公差br 145根据分度圆直径从表10-5查取计算计算结果:113.1μm 齿厚下偏差Esi=Ess-Ts 齿距极限偏差Fpt22.0μm 齿厚上偏差/Fpt-2.6-3按齿厚极限偏差表取整齿厚下偏差/Fpt-7.7-8按齿厚极限偏差表取整计算结果:-169.5μm 齿厚上偏差取值:Ess -66.0μm 注:1本表不属于国家标准,仅供参考.齿厚下偏差取值:Esi -176.0μm 2αMt1=25见标准齿轮参数计算3螺旋角β=8.1094公法线平均长度上偏差EwmsEss*cos αn-0.72Fr*sin αn 4βb=0.132949计算结果:-75.80997μm 5齿数z=20大,小齿轮分别计算公法线平均长度下偏差Ewmi Esi*cos αn+0.72Fr*sinαn 计算结果:-151.5956μm 2016/12/20大齿轮表10-4≤10>10~25>25~60>60喷油润滑0.010.020.030.03~0.05油池润滑圆周速度v(m/s)润滑方式0.005~0.01表10-5第I 公差组精度等级56789br IT8 1.26IT8IT9 1.26IT9IT10。
齿轮副的精度指标和侧隙指标讲解

齿轮传动是通过齿轮副实现的,其误差 直接影响齿轮的使用要求。对齿轮副的检验, 是按设计中心距安装后进行的一种综合检验, 从满足齿轮使用要求出发,规定的齿轮副检 验参数有中心距极限偏差和轴线的平行度偏 差,接触斑点,侧隙等。
11.3.1齿轮副的精度 1.中心距极限偏差fa:
因为齿轮为机床主轴箱的传动齿轮,由表11-13 可大致得出齿轮精度在3-8级之间.而 V=πdn1/1000×60=(3.14×2.75×26×1650)/1000×60
=6.2m/s
参考表11-14确定该齿轮为7级精度,表示为
7GB/T100095.1-2001
2确定侧隙和齿厚偏差
中心距 a= m/2(Z1+Z2)=2.75/2(26+56)=112.75mm 由公式11-1得:
轴线平面:包含用两
轴承跨距中较长的一根轴 线和另一轴上的一个轴承 中心所形成的平面。
(2)轴线平行度偏差 f 和 f
轴线平面内的平行度偏差f是在两轴线的公
共平面上测量的,此公共平面是用两轴承跨距中
较长的一个L和另一根轴上的一个轴承来确定的。
如果两个轴承的跨距相同,则用小齿轮轴和大齿
轮轴的一个轴承确定。垂直平面上的平行度偏差
Fr=0.03mm
由11-3 和2-2表查: br=IT9=0.074mm Tsn =√Fr²+br²2tan αn = 0.058mm Esni = Esns-Tsn = - 0.071-0.058= - 0.129mm
f
是在与轴线公共平面相垂直的平面上测量的。
f 和 f的最大推荐值为:
式中,L为轴承跨距,b为齿宽。
(3)接触斑点
接触斑点是指装配好的齿轮副,在轻微的制
浅析机械设计中齿轮传动侧隙的解决方法

浅析机械设计中齿轮传动侧隙的解决方法作者:马博来源:《农家科技下旬刊》2017年第02期摘要:齿轮具有改变运动方向和运动速度,以及传递动力的作用。
齿轮在船舶、能源、制造、汽车等行业领域的设备中广泛地得到应用。
随着各个领域技术的不断更新与发展,对高质量齿轮的制造的要求也越来越高。
为了有效提高齿轮传动的传动率以及精度,文章简要地介绍了在齿轮的传动作用中,通过对齿轮传动侧隙所产生的问题提出了解决侧隙的有效方法。
关键词:传动;侧隙;齿轮;啮合状态;设计问题;放大补偿齿轮从东汉时期的指南车开始被人们逐渐应用,经历了许多年代,齿轮的形式以及作用都在不断地演变和发展。
有齿,并可以相互啮合的机械零部件就是齿轮。
按照齿轮的制造方法可以将齿轮分为烧结齿轮、轧制齿轮、切制齿轮、铸造齿轮等;按照齿线的形状可将齿轮分为曲线齿轮、人字齿轮、斜齿轮、直齿轮等;按照轮齿所处表面可将齿轮分为内齿轮和外齿轮;按照齿轮的外形将能够将齿轮分为蜗杆齿轮、非圆齿轮、锥齿轮、圆柱齿轮等等;再如按照齿廓曲线可将其分为圆弧齿轮、摆线齿轮、开线齿轮等。
齿轮其结构包括模数、周节即齿距、齿厚、齿廓、分度圆、齿根圆、齿顶圆、齿槽即齿间,轮齿等。
一、齿轮传动侧隙的优劣既然文章是对机械设计中齿轮法向侧隙的解决方法进行讨论,那我们就先来了解一下什么是齿轮侧隙。
在2个齿轮互相啮合的状态下,齿轮与齿轮在接触时,第二个齿轮和前一齿轮相互咬合的齿所邻近的齿在分度圆上的间隙称为齿轮侧隙。
在常温的状态下,齿轮与齿轮的啮合如果没有侧隙的存在就会出现咬死的现象。
在实际的齿轮运行中,随着机械工作过程中温度的逐渐上升,理论上应该为零的齿轮侧隙就会随着温度的升高而间隙变大。
因此,侧隙的产生也是正常现象,而且,侧隙中可以保留储油的空间,这些都是齿轮侧隙的特点。
但是,侧隙也会出现在齿轮转向时的回程误差,以至于给齿轮带来冲击影响,这就是齿轮侧隙的劣势所在。
侧隙过于窄小会因储油空间不足导致润滑不良,而且会容易造成齿轮咬死。
齿轮圆周侧间隙测量方法-概述说明以及解释

齿轮圆周侧间隙测量方法-概述说明以及解释1.引言1.1 概述齿轮是一种常见的传动装置,广泛应用于各个领域。
在齿轮传动中,齿轮圆周侧间隙是一个重要的参数,它对传动的精度和可靠性起着关键作用。
齿轮圆周侧间隙是指齿轮齿根与相邻齿轮齿顶之间的距离。
它直接影响齿轮的啮合性能和传动效率。
如果齿轮圆周侧间隙过大,会导致齿轮啮合不稳定,噪声增加,甚至影响传动精度;而如果齿轮圆周侧间隙过小,则容易造成齿轮的磨损和损坏。
因此,准确测量齿轮圆周侧间隙对于齿轮传动的设计、制造和维护至关重要。
然而,由于齿轮圆周侧间隙的特殊性,其测量一直是一个相对复杂的工作。
本文旨在介绍齿轮圆周侧间隙的测量方法。
首先,我们将概述齿轮圆周侧间隙的定义和重要性。
其次,我们将详细讨论影响齿轮圆周侧间隙的因素,以便更好地理解它的测量方法。
最后,我们将总结各种齿轮圆周侧间隙测量方法,并推荐其中的一种方法作为最佳实践。
通过本文的阅读,读者将能够全面了解齿轮圆周侧间隙的测量方法,并在实际应用中选取适合的方法,以确保齿轮传动的正常运行和长期可靠性。
1.2文章结构文章结构部分的内容:本文按照以下结构展开对齿轮圆周侧间隙测量方法进行探讨。
首先,在引言中对文章的研究主题进行了概述,明确了本文的目的和重要性。
然后,在正文中详细介绍了齿轮圆周侧间隙的定义和重要性,以及影响该间隙的因素。
最后,在结论部分对齿轮圆周侧间隙测量方法进行总结,并推荐了一些可行的测量方法。
通过这样的结构安排,本文旨在全面了解齿轮圆周侧间隙的测量方法,为相关领域的研究和实际应用提供参考和借鉴。
1.3 目的本文的主要目的是介绍齿轮圆周侧间隙测量方法,并总结推荐适用的测量方法。
通过深入探讨齿轮圆周侧间隙的定义和重要性,以及其影响因素,旨在帮助读者全面了解并掌握齿轮圆周侧间隙的测量技术。
同时,通过对不同齿轮圆周侧间隙测量方法的比较和总结,旨在为齿轮制造和检测过程中的实际应用提供参考和指导。
具体地,本文的目的包括以下几个方面:1)详细介绍齿轮圆周侧间隙的定义和重要性。
齿轮侧隙计算方法

一、补偿热变形法向侧隙jn1 um-0.052箱体(铝合金)线膨胀系数(α2) 1/℃0.003齿轮线膨胀系数(α1)1/℃0.004箱体温差(Δt2)℃100.005齿轮温差(Δt1)℃100.006法向压力角(αn) 20.007中心距 a mm63.00二、保证齿轮间润滑油膜形成的侧隙jn20.02模数 m 2.00齿数 z32.00发动机转速 n rpm8500.00角速度 ω /s890.12分度圆直径 d mm64.00圆周速度 ν m/s28.48三、 安装、加工补偿系数 k算法1齿轮副安装引起的侧隙减少量 um0.01738925算法2齿轮副安装引起的侧隙减少量 um0.01738867 fpb10.0075fpb20.0075Fβ0.0095fx0.0095fy0.00475四、理论最小侧隙 jnmin考虑润滑、温差、安装-0.01考虑润滑、安装0.04考虑齿厚、中心距、安装等0.02考虑齿厚、温差、中心距、安装等-0.027404五、理论齿厚极限偏差的确定保证最小侧隙量的齿厚实际上偏差 Ess'-0.0308132中心距极限偏差 fa0.03nss-4.1084272对应齿厚公差代号F保证最小侧隙量的齿厚实际下偏差 Esi'-0.0681763齿轮侧隙公差 Ts 0.03736308齿圈径向跳动公差 Fr 0.036切齿进刀公差 br 0.01nsi -9.0901717对应齿厚公差代号J六、理论公法线极限偏差的确定公法线上偏差 Ews -0.0378201公法线下上偏差 Ewi -0.0551996七、实际齿厚偏差由公法线公差反推齿厚偏差公法线上偏差 Ews0-0.011公法线下偏差 Ewi0-0.041齿厚上偏差 Ess0-0.0022718齿厚下偏差 Esi0-0.0341972八、实际齿轮侧隙 jn0实际预期实际中心距偏差 fa00.03-0.03冷态侧隙 上偏差jns0-10.043748470.084791 下偏差jni0-1-0.01625150.024791热态侧隙 上偏差jns0-20.090.132195 下偏差jni0-20.030.072195九、考虑轴承游隙的实际齿侧隙0组游隙上偏差0组游隙下偏差0组游隙齿轮冷态侧隙上偏差0.045548470.0865910组游隙齿轮冷态侧隙下偏差-0.01595150.0250913组游隙上偏差3组游隙下偏差3组游隙齿轮冷态侧隙上偏差0.046248470.0872913组游隙齿轮冷态侧隙下偏差-0.01515150.0258910.00180.00030.00250.0011。
公法线和侧隙关系

公法线和侧隙关系
公法线是描述齿轮齿廓与法线的交点之间的距离,而侧隙则是指齿轮在啮合过程中,为了防止卡死或过载而预留的空隙。
公法线与侧隙之间的关系可以用以下公式表示:
ΔE = ΔW / cosα
其中,ΔE表示侧隙,ΔW表示公法线微小变化量,α表示齿轮压力角。
这
个公式表明,公法线的微小变化量与侧隙的大小成正比,即公法线变化越大,侧隙也越大。
此外,中心距偏差也会影响侧隙。
如果中心距存在偏差,那么两齿轮的啮合中心距会产生偏差,进而导致啮合传动时有侧隙。
这类偏差属于第二类误差引起的偏差,主要来源于减速差速器的箱体两个平行孔之间的距离的偏差。
以上内容仅供参考,建议查阅齿轮设计、制造相关书籍或咨询专业人士以获取更准确的信息。
齿轮啮合的侧隙检测方法
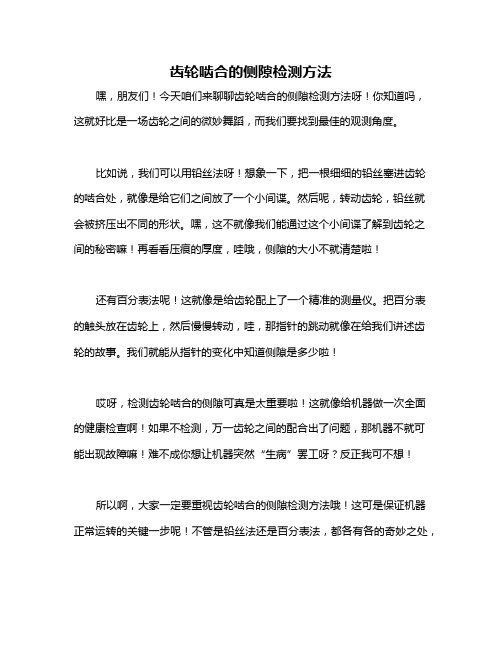
齿轮啮合的侧隙检测方法
嘿,朋友们!今天咱们来聊聊齿轮啮合的侧隙检测方法呀!你知道吗,这就好比是一场齿轮之间的微妙舞蹈,而我们要找到最佳的观测角度。
比如说,我们可以用铅丝法呀!想象一下,把一根细细的铅丝塞进齿轮的啮合处,就像是给它们之间放了一个小间谍。
然后呢,转动齿轮,铅丝就会被挤压出不同的形状。
嘿,这不就像我们能通过这个小间谍了解到齿轮之间的秘密嘛!再看看压痕的厚度,哇哦,侧隙的大小不就清楚啦!
还有百分表法呢!这就像是给齿轮配上了一个精准的测量仪。
把百分表的触头放在齿轮上,然后慢慢转动,哇,那指针的跳动就像在给我们讲述齿轮的故事。
我们就能从指针的变化中知道侧隙是多少啦!
哎呀,检测齿轮啮合的侧隙可真是太重要啦!这就像给机器做一次全面的健康检查啊!如果不检测,万一齿轮之间的配合出了问题,那机器不就可能出现故障嘛!难不成你想让机器突然“生病”罢工呀?反正我可不想!
所以啊,大家一定要重视齿轮啮合的侧隙检测方法哦!这可是保证机器正常运转的关键一步呢!不管是铅丝法还是百分表法,都各有各的奇妙之处,
我们要根据实际情况选择最合适的方法呀,让我们的齿轮能一直欢快地跳着那完美的舞蹈!
我的观点就是:齿轮啮合的侧隙检测绝对不能马虎,要用合适的方法认真对待,这样机器才能长久稳定地运行呀!。
齿轮侧隙及齿厚偏差自动计算表
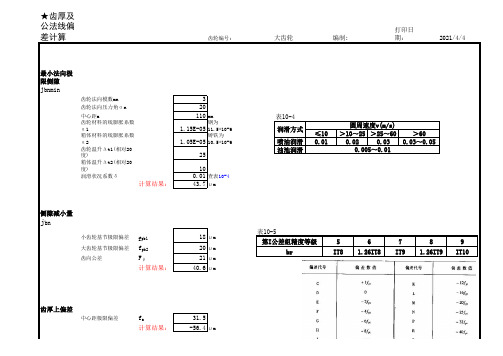
中心距极限偏差
fpb1
fpb2
Fβ 计算结果:
Ess=((jnmin+Jn)/ (2cosα n)+fa*tan αn) fa 计算结果:
18 μm 20 μm 21 μm 40.6 μm
31.5 -56.4 μm
大齿轮
编制:
打印日 期:
2021/4/4
表10-4
润滑方式
≤10
圆周速度v(m/s) >10~25 >25~60
润滑状况系数δ
计算结果:
齿轮编号:
3 20 110 mm
钢为
1.15E-05 11.5*10-6
铸铁为
1.05E-05 10.5*10-6 25 10
0.01 查表10-4 43.7 μm
侧隙减小量
jbn
Jn=(Fpb1^2+ Fpb2^2+2.10 4*Fβ ^2)^0.5
小齿轮基节极限偏差 大齿轮基节极限偏差 齿向公差
-180.9787
偶数齿
本表不属 于国家标 准,仅供 注:1 参考.
2 αMt1= 25 3 螺旋角β 8.1094
见标准齿轮 参数计算
4
βb= 0.132949
5 齿数z= 20
大,小齿轮 分别计算
计算结果 -180.4208
奇数齿
圆棒跨距上 偏差Ems
Ess
-66.0 μm
Esi
-176.0 μm
Ess*cosα n0.72Fr*sin αn
计算结果: Esi*cosα n+0.72Fr*s inαn 计算结果:
-75.80997 μm -151.5956 μm
Ewms/(sin αMt*cosβ b) 计算结果 Ewms/(sin αMt*cosβ b)*cos(π /2z)
- 1、下载文档前请自行甄别文档内容的完整性,平台不提供额外的编辑、内容补充、找答案等附加服务。
- 2、"仅部分预览"的文档,不可在线预览部分如存在完整性等问题,可反馈申请退款(可完整预览的文档不适用该条件!)。
- 3、如文档侵犯您的权益,请联系客服反馈,我们会尽快为您处理(人工客服工作时间:9:00-18:30)。
无侧隙啮合参数未知参数
齿厚、齿距侧隙
参数符号主动齿轮(小)
从动齿轮(大)齿数z 21
40法向模数m n 法向压力角αn 螺旋角β法向变位系数x n 0.047
-0.465齿宽b 齿顶圆直径d a 54.3
96.5齿根圆直径d f 42.35
84.55任意圆直径d x 54.3
96.5中心距a 当量齿数zv 32.82903592
62.53149699当量模数m n 当量压力角αn 当量螺旋角β当量变位系数x n 0.047
-0.465当量分度圆直径d 65.66
125.06当量基圆直径d b 61.89
117.89任意圆压力角α29.30
23.61任意圆直径d'70.97
128.66当量齿轮任意圆直径dx 70.97
128.66
任意圆直径d 54.0696.44
曹德义 2008年11月14.5
70
齿 轮 计 算
2.00
19.5
30.5
2.00
19.50
啮合压力角渐开线函数a b c 啮合压力角弧度端面啮合角理论中心距离中心距变动系数y 中心距变动系数y 中心距变动系数yn 中心距变动系数yn 齿顶高变动系数△y 齿顶高系数ha* 1.428 1.464顶隙系数c*0.2180.145理论啮合线长度端面变位系数x t 0.040-0.401齿顶高h a 2.778 1.826齿根高h f 3.197 4.149齿根圆直径d f 42.3584.55端面模数m t 端面压力角αt 齿顶圆端面压力角αat 33.8727.14任意圆端面压力角αxt 33.8727.14齿顶圆螺旋角βa 33.2731.48任意圆螺旋角βx 33.2731.48分度圆直径d 48.7448792.85节圆直径 d'48.2091.80节圆螺旋角β'30.2230.22基圆直径d b 45.08685.877齿顶圆曲率半径ρa 15.1322.01任意圆曲率半径ρx 15.1322.01理论啮合线长度l 渐开线起始圆直径
45.41688.002导程
259.974495.189基圆螺旋角βb 端面啮合角αt 法向啮合角αn 三角函数invαn 齿顶圆压力角αa 33.8727.14任意圆压力角αx 33.8727.14端面重合度εα轴向重合度εβ总重合度εγ法向齿距p n -0.374-0.374-0.434-0.43420.54169.92733781.840.016
系 数0.3590.3750.1410.35924.5360.0743.016.2832.321.1722.3424.7428.58320.7018.0330.0108
端面齿距p t 基圆齿距p bt 基圆法向齿距p bn 法向齿厚s n 3.208 2.483端面齿厚s t 3.723 2.882齿顶圆端面齿厚s at 0.943 1.271齿顶圆法向齿厚s an 0.788 1.084任意圆端面齿厚s xt 0.943 1.271任意圆法向齿厚s xn 0.788 1.084基圆端面齿厚s bt 4.3927 4.4726基圆法向齿厚s bn 3.8573 3.9276节圆端面齿厚s t' 3.8966 3.2589节圆法向齿厚s n' 3.3671 2.8161当量齿数z v 32.8362.53
节圆端面齿距p t'节圆法向齿距p n'圆周侧隙j wt 法向侧隙j bn 法向侧隙j bn 圆周侧隙j wt 7.2926.7455.9237.21026.23050.05470.044940.044940.0547
备注输入
端面法向
考虑倒棱考虑倒棱
根据节圆齿厚计算根据基圆齿厚计算。