氰化锌粉置换规范讲义
锌粉置换技术操作规程
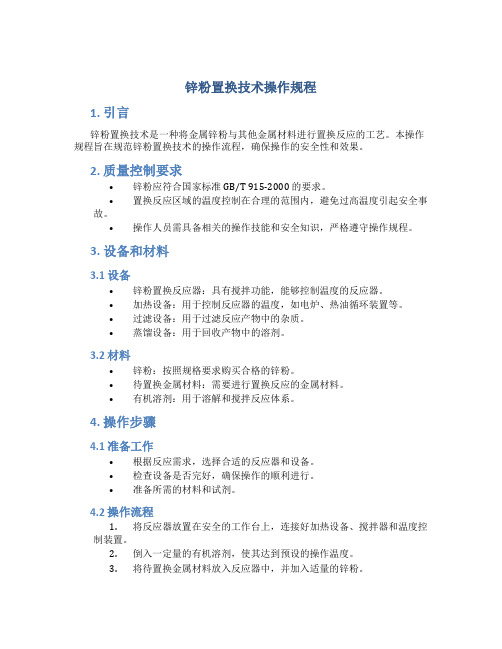
锌粉置换技术操作规程1. 引言锌粉置换技术是一种将金属锌粉与其他金属材料进行置换反应的工艺。
本操作规程旨在规范锌粉置换技术的操作流程,确保操作的安全性和效果。
2. 质量控制要求•锌粉应符合国家标准 GB/T 915-2000 的要求。
•置换反应区域的温度控制在合理的范围内,避免过高温度引起安全事故。
•操作人员需具备相关的操作技能和安全知识,严格遵守操作规程。
3. 设备和材料3.1 设备•锌粉置换反应器:具有搅拌功能,能够控制温度的反应器。
•加热设备:用于控制反应器的温度,如电炉、热油循环装置等。
•过滤设备:用于过滤反应产物中的杂质。
•蒸馏设备:用于回收产物中的溶剂。
3.2 材料•锌粉:按照规格要求购买合格的锌粉。
•待置换金属材料:需要进行置换反应的金属材料。
•有机溶剂:用于溶解和搅拌反应体系。
4. 操作步骤4.1 准备工作•根据反应需求,选择合适的反应器和设备。
•检查设备是否完好,确保操作的顺利进行。
•准备所需的材料和试剂。
4.2 操作流程1.将反应器放置在安全的工作台上,连接好加热设备、搅拌器和温度控制装置。
2.倒入一定量的有机溶剂,使其达到预设的操作温度。
3.将待置换金属材料放入反应器中,并加入适量的锌粉。
4.启动搅拌器和加热设备,调整温度和搅拌速度,保持反应体系的均匀和稳定。
5.根据反应体系的不同,反应时间可在几分钟到数小时之间。
操作人员应根据实际情况进行调整。
6.反应结束后,关闭加热设备和搅拌器,待体系冷却至安全温度后停止操作。
7.将反应产物倒入过滤设备中,去除其中的杂质。
8.倘若需要回收溶剂,可将产物放入蒸馏设备中进行蒸馏,以得到纯净的溶剂。
5. 操作注意事项1.操作人员应严格遵守相关的安全规定,佩戴防护设备,避免发生化学品飞溅和热伤害。
2.当搅拌器启动时,应确保操作空间内没有其他杂物,避免发生搅拌器与其他物体的碰撞。
3.反应体系的温度应逐渐升高,避免突然升温引起温度梯度过大,导致反应剧烈。
氰化镀锌——精选推荐
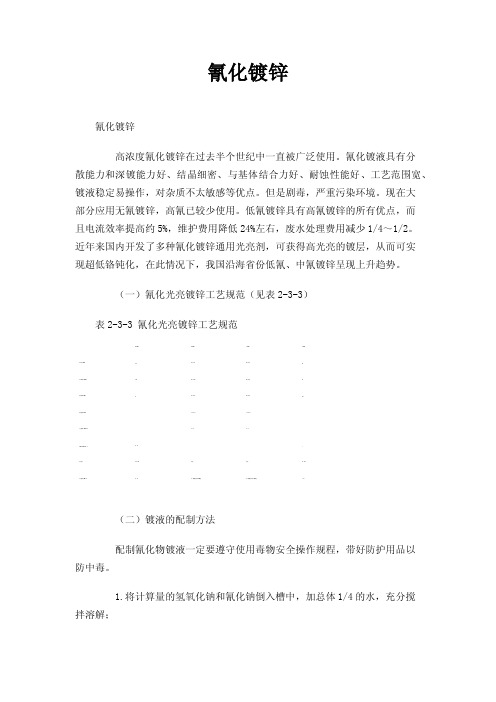
氰化镀锌氰化镀锌高浓度氰化镀锌在过去半个世纪中一直被广泛使用。
氰化镀液具有分散能力和深镀能力好、结晶细密、与基体结合力好、耐蚀性能好、工艺范围宽、镀液稳定易操作,对杂质不太敏感等优点。
但是剧毒,严重污染环境。
现在大部分应用无氰镀锌,高氰已较少使用。
低氰镀锌具有高氰镀锌的所有优点,而且电流效率提高约5%,维护费用降低24%左右,废水处理费用减少1/4~1/2。
近年来国内开发了多种氰化镀锌通用光亮剂,可获得高光亮的镀层,从而可实现超低铬钝化,在此情况下,我国沿海省份低氰、中氰镀锌呈现上升趋势。
(一)氰化光亮镀锌工艺规范(见表2-3-3)表2-3-3 氰化光亮镀锌工艺规范000000000(二)镀液的配制方法配制氰化物镀液一定要遵守使用毒物安全操作规程,带好防护用品以防中毒。
1.将计算量的氢氧化钠和氰化钠倒入槽中,加总体1/4的水,充分搅拌溶解;2.将计算量的氧化锌调成糊状,在不断搅拌下慢慢加入热槽液中,搅至完全溶解。
3.稀至总体积,加入硫化钠,搅拌10min让其充分反应,除去重金属杂质;4.按使用说明书要求加入某种光亮剂,充分搅匀,用0.5~1A/dm2的低电流密度电解处理3~4h,试镀合格后即可投产。
(三)镀液组成和工艺规范的影响1.氧化锌提供被沉积的金属离子,浓度高则电流效率高,而阴极极化降低,分散能力下降,凸出部位易烧焦,允许电流密度的上限值反而降低。
锌含量与氰化物浓度有关,微氰镀液锌控制在7.5~9g/L;低氰镀液锌为10~12g/L;中氰镀液锌14~18g/L,高氰镀液锌30~35g/L。
锌含量偏低,分散能力好,但电流效率下降。
2.氰化钠高、中氰镀液中氰化钠是络合剂,在镀液锌以Zn(CN)42-形式存在。
而低氰镀液主络合剂是氢氧化钠,锌以Zn(OH)42-形式存在。
在低氰镀液中氰化钠的存在对改善镀液和镀层性能起着重要作用。
因为氰化钠有表面活性作用,容易吸附在阴极/镀液界面上,故电极表面上氰根的浓度远大于溶液本体的浓度,导致阴极化增大,结晶细密,厚度均匀,还能增强结合力,所以少量氰化钠可作为改善镀层质量的介质。
氰化厂生产工艺操作规程
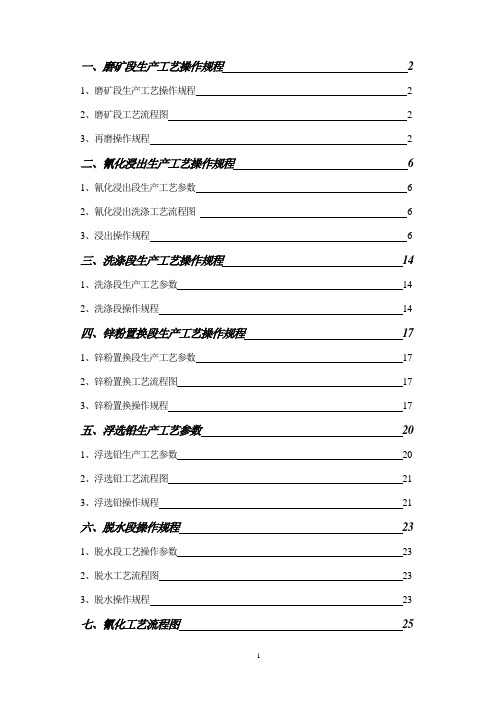
一、磨矿段生产工艺操作规程 21、磨矿段生产工艺操作规程 22、磨矿段工艺流程图 23、再磨操作规程 2二、氰化浸出生产工艺操作规程 61、氰化浸出段生产工艺参数 62、氰化浸出洗涤工艺流程图 63、浸出操作规程 6三、洗涤段生产工艺操作规程141、洗涤段生产工艺参数142、洗涤段操作规程14四、锌粉置换段生产工艺操作规程171、锌粉置换段生产工艺参数172、锌粉置换工艺流程图173、锌粉置换操作规程17五、浮选铅生产工艺参数201、浮选铅生产工艺参数202、浮选铅工艺流程图213、浮选铅操作规程21六、脱水段操作规程231、脱水段工艺操作参数232、脱水工艺流程图233、脱水操作规程23七、氰化工艺流程图25一、磨矿段生产工艺操作规程1、磨矿段生产工艺参数:1)根据公司计划决定年湿金精矿处理量。
2)磨矿的调浆浓度35±20%3)旋流器分级浓度25±10%,溢流浓度18±10%,底流浓度75±10%。
4)球磨机钢球补加量按(0.9—1.5)公斤/吨湿矿补加。
5)钢球规格φ40mm。
6)磨矿细度-400目一般占90%以上。
(特殊矿类除外)以上各工艺参数特殊矿物要按生产调度单执行。
2、磨矿段工艺流程图3、再磨矿操作规程1) 加料调浆岗位(1)起重机操作规程①起重机应由专人操作,操作者应熟悉掌握安全操作规程。
②开车前,必须对起重机进行空负荷运转,并检查下列项目:a.按钮能否可靠的控制升降机运行。
b.限位器动作是否灵活可靠。
c.运转时有无异常响声或气味。
d.钢丝绳能否在卷筒上正确缠绕。
e.检查电子称是否良好,数字清楚无误。
f.如遇不正常情况,应及时排除,然后才能使用。
g.钢丝绳是否破股断丝。
③起重机使用时,严禁超负荷使用,每次起动时宜先点动按钮,使重物拉紧钢丝绳后再进行起吊。
④限位器是防止吊钩起升或下降超过极限位置而发生事故的保险装置,不应作为行程开关经常使用,更不得拆除。
锌粉置换岗位安全操作规程
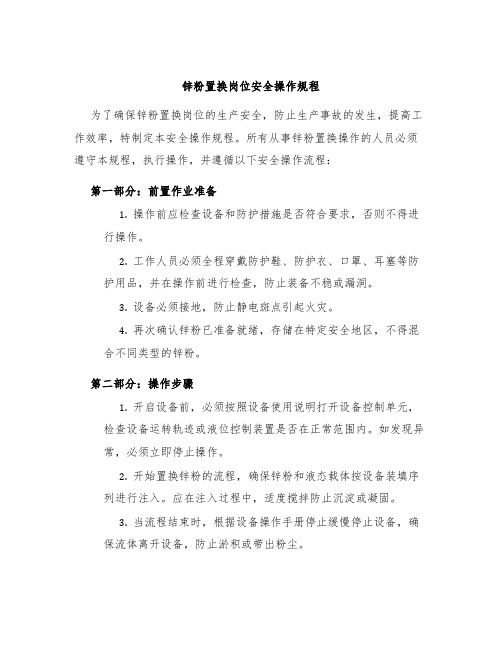
锌粉置换岗位安全操作规程为了确保锌粉置换岗位的生产安全,防止生产事故的发生,提高工作效率,特制定本安全操作规程。
所有从事锌粉置换操作的人员必须遵守本规程,执行操作,并遵循以下安全操作流程:第一部分:前置作业准备1.操作前应检查设备和防护措施是否符合要求,否则不得进行操作。
2.工作人员必须全程穿戴防护鞋、防护衣、口罩、耳塞等防护用品,并在操作前进行检查,防止装备不稳或漏洞。
3.设备必须接地,防止静电斑点引起火灾。
4.再次确认锌粉已准备就绪,存储在特定安全地区,不得混合不同类型的锌粉。
第二部分:操作步骤1.开启设备前,必须按照设备使用说明打开设备控制单元,检查设备运转轨迹或液位控制装置是否在正常范围内。
如发现异常,必须立即停止操作。
2.开始置换锌粉的流程,确保锌粉和液态载体按设备装填序列进行注入。
应在注入过程中,适度搅拌防止沉淀或凝固。
3.当流程结束时,根据设备操作手册停止缓慢停止设备,确保流体离开设备,防止淤积或带出粉尘。
第三部分:事故处理程序1.确保所有人员在事故发生后立即撤离现场。
2.在可能的情况下,关闭主要的配电线路或紧急停止设备运转。
3.在发现透泄或火灾时,应使用适当的灭火设备,同时通知相关部门进行应急处理。
4.在事故处理过程中,必须保持通信畅通,及时报告上级主管和其他相应部门,维护工作场所的安全。
第四部分:紧急救援程序1.当事故发生时,必须立即拨打紧急电话。
2.当事故发生时,应立即采取措施制止事故发生,并在救援人员到达前进行现场隔离。
3.确保救援人员在到达现场后,始终保持通信畅通,及时报告现场情况并协助救援人员处理事故。
结束语为确保生产安全,本规程对锌粉置换操作进行了安全全程控制。
每位工人都必须遵守规程,建立安全实践方法,积极与时俱进,不断改进工作方式。
如果您对此规程有任何疑问,请立即向主管或安全干事了解详情,避免发生不可挽回的事故。
重庆科技学院贵金属冶金学PPT课件8.从常规氰化浸出液中置换金银

按照置换金的反应计算, 1g金理论上仅需需0.19g锌 ,但实际却要高出此数值数十倍。
锌置换的原理
(3) 金与氧气的反应 锌置换Au(CN)2-的过程产出金,这实际上是氰化浸金的 逆过程。因此如溶液中有O2的存在,可能会使已置换出来的金 溶解进入溶液。
因此,为了减少锌耗和防止金的返溶,加锌置换 金之前,应当将溶液中的氧除去。
锌置换的原理
为防止锌置换金银时白色沉淀的生成,进行置换 金银的氰化贵液要有足够浓度的碱和氰化物。 预先脱氧是防止白色沉淀生成最有效的措施。因 为,氰化贵液脱氧后,大大减少了锌的氧化,即减少 了溶液中锌的总浓度,从而可以在相对较低的氰化物 浓度下进行锌的置换。 锌置换过程是电化学反应过程,在阳极区锌被氧 化失去电子,而在阴极区,金、氧和水被还原得到电 子。氰化物溶液中如果存在铅离子,对锌置换金起着 促进作用,因铅的电位比锌的更正,用可溶性铅盐 (如 硝酸铅或乙酸铅)处理锌时,铅被还原成海绵铅。
从常规氰化浸出液中置换金银
自发展氰化法到Biblioteka 近为止,锌置换沉淀法是从氰化物溶 液中沉淀贵金属主要的,实际上也是唯一的方法。目前,这 种方法在黄金生产工业中仍保持领先地位。然而,饭年来越 来越广泛地推广以采用离子交换树脂和活性炭为基础的吸附 法。使用这种方法的可能性极其广泛,而且可以预料,随着 时间的推移,这种方法的作用将会显著增大。
锌置换的原理
锌的一些副反应:
(1) 锌与水的反应 在碱性溶液中,水被还原成H2的半电池反应为: 2H2O+2e=H2+2OH(8-3) E0=-0.83V 与锌在氰化物溶液中的标准电位(-1.26V)相比,锌有可能将氰 化液中的H2O置换成H2 析出,即: Zn+4CN-+2H2O=Zn(CN)42- +H2 +2OH(8-4)
金矿石氰化浸出锌粉置换提金工艺回收率计算规范(送审稿)_百度.

ICSH :YS金矿石氰化浸出锌粉置换提金工艺理论回收率计算方法Calculation methods of gold recovery rateOf cyanide leaching and zinc dust precipitation (送审稿中华人民共和国工业和信息化部发布YS/T××× -20××前言本标准由中国黄金协会提出。
本标准由全国黄金标准化技术委员会归口。
本标准由长春黄金研究院负责起草。
本标准主要起草人:XXX 、 XXX 、郑晔、赵明福。
目次前言 (I)1 范围 . (1)2 术语和定义 (1)3 氰化浸出锌粉置换提金工艺理论回收率计算方法 ............ 2 3.1氰化浸出锌粉置换提金原则工艺流程及取样点设置 . ............... 2 3.2回收率计算方法 (5)金矿石氰化浸出锌粉置换提金工艺理论回收率计算方法 1 范围本标准规定了金矿石氰化浸出锌粉置换提金工艺过程理论回收率计算方法。
本标准适用于金矿石、浮选金精矿,或金矿石、浮选金精矿经焙烧、生物氧化及其它工艺预处理后,氰化浸出锌粉置换提金工艺过程。
2 术语和定义下列术语和定义适用于本标准。
2.1 金矿石 Gold ore指含有金的矿石。
2.2 氰原 Gold-bearing material(gold ore or gold concentrates before cyanide leaching进入氰化浸出作业前的含金物料,在本标准中指直接氰化的金矿石、浮选金精矿,或金矿石、浮选金精矿经焙烧、生物氧化及其它工艺预处理后得到的含金物料。
2.3 氰化浸出 Cyanide leaching在含氧的氰化物溶液中溶解金的过程。
2.4 洗涤 Washing使含金溶液与固体分离的过程。
2.5 锌粉置换 Zinc dust precipitation在含金的贵液中加入锌粉,通过锌与金的置换反应使金沉淀的方法。
几种氰化法的介绍

几种氰化法提金介绍1.氰化法提金概述氰化法提金是以氰化物的水溶液作溶剂,浸出含金矿石中的金,然后再从含金浸出液中提取金的方法。
氰化法提金主要包括如下两个步骤:(1)氰化浸出:在稀薄的氰化溶液中,并有氧(或氧化剂)存在的条件下,含金矿石中的金与氰化物反应生成一价金的络合物而溶解进入溶液中,得到浸出液。
以氰化钾为例,反应式为:4Au+8KCN+2H2O→4KAu(CN)2+4KOH氰化浸出金的工艺方法有槽浸氰化法和堆浸氰化法两类。
槽浸氰化法是传统的浸金方法,又分渗滤氰化法和搅拌氰化法两种;堆浸法是近20年来才出现的新技术,主要用于处理低品位氧化矿。
自1887发现氰化液可以溶金以来,氰化法浸出至今已有近百年的生产实践,工艺比较成熟,回收率高,对矿石适应性强,能就地产金,所以至今仍是黄金浸出生产的主要方法。
(2)沉积提金:从氰化浸出液中提取金。
工艺方法有加锌置换法(锌丝置换法和锌粉置换法)、活性炭吸附法(炭浆法CIP和炭浸法CIL)、离子交换树脂法(树脂矿浆法RIP 和RIL)、电解沉积法、磁炭法等。
锌粉(丝)置换法是较为传统的提金方法,在黄金矿山应用较多;炭浆法是目前新建金矿的首选方法,其产金量占世界产金量的50%以上;其余方法在黄金矿山也正日渐得到应用。
2.渗滤氰化法渗滤氰化法是氰化浸出的工艺方法之一,是基于氰化溶液渗透通过矿石层而使含金矿石中的金浸出的方法,适用于砂矿和疏松多孔物料。
渗滤氰化法的主要设备是渗滤浸出槽,见图1。
渗滤浸出槽通常为木槽、铁槽或水泥槽。
槽底水平或稍倾斜,呈圆形、长方形或正方形。
槽的直径或边长一般为5~12米,高度一般为2~2.5米,容积一般为50~150吨。
图1渗滤氰化法的工艺过程:(1)装入矿砂及碱:要求布料均匀,粒度一致,疏松一致。
有干法和湿法两种装法。
干法适于水分在20%以下的矿砂,可用人工或机械装矿。
湿法是将矿浆用水稀释后,用砂泵扬送或沿槽自流入槽内。
(2)渗滤浸出:装料完毕后即可把氰化液送入槽中。
锌粉置换岗位安全操作规程示范文本

锌粉置换岗位安全操作规程示范文本In The Actual Work Production Management, In Order To Ensure The Smooth Progress Of The Process, And Consider The Relationship Between Each Link, The Specific Requirements Of EachLink To Achieve Risk Control And Planning某某管理中心XX年XX月锌粉置换岗位安全操作规程示范文本使用指引:此操作规程资料应用在实际工作生产管理中为了保障过程顺利推进,同时考虑各个环节之间的关系,每个环节实现的具体要求而进行的风险控制与规划,并将危害降低到最小,文档经过下载可进行自定义修改,请根据实际需求进行调整与使用。
1.上班前必须穿戴好劳保用品,班中严禁喝酒、吃食品,严禁酒后上班。
2. 与贵液及锌粉接触时,应佩戴乳胶手套和防尘口罩。
3. 随时检查运行设备的温度、润滑情况及有无异常声响、震动和气味。
4. 进入岗位围栏内检修设备或做接触含金物料的工作时,必须通知保安,保安到场后方可进行。
5. 进入脱氧塔或中间槽作业时使用36V以下安全照明灯或手电筒,不得使用220V照明灯具;且需两人以上进行,一人作业,一人监护;并佩戴好防毒面具。
设备及电器的防护装置必须齐全,否则职工有权拒绝操作。
检修、擦拭运转设备时严禁戴手套。
严禁用水冲洗电机、配电箱及开关按钮;电路湿水、受潮的设备严禁开启。
检修设备时,应切断配电箱内电源,并挂上“禁止合闸”标牌。
10. 贫液快速检测、接触王水等危化品时,应穿戴好劳保,做好防护,按操作规程进行操作。
请在此位置输入品牌名/标语/sloganPlease Enter The Brand Name / Slogan / Slogan In This Position, Such As Foonsion。
某金矿全泥氰化锌粉置换厂工艺流程技术改造实践

某金矿全泥氰化锌粉置换厂工艺流程技术改造实践摘要:该矿石属少硫化矿物石英脉含金矿石,金属矿物主要为黄铁矿;脉石矿物主要为石英,其次为长石、方解石、云母等。
矿石中的金元素以自然金的形式产出,并且以裂隙金为主,属于易氰化浸出矿石。
经过现场工业生产调试结果证明,采用全泥氰化—锌粉置换工艺流程代替浮选处理该矿石是正确的,尾矿品位由0.57g/t降到0.20g/t,金的回收率由82.87%提高到92.16%,提高了企业的经济效益。
关键词:全泥氰化-锌粉置换、浮选、代替、回收率、经济效益Abstract: The ore is a sulfide mineral quartz vein ore less, metal minerals is mainly pyrite; major gangue mineral is quartz, feldspar, calcite, followed by mica. Of gold in Ores by natural gold in the form of output elements, and fissure gold, is easy to cyanide leaching of ores. After the industrial production debugging results show that, using the all sliming cyanidation - zinc powder replacement process for flotation treatment of the ore is correct, tailing grade from 0.57g/t to 0.20g/t, the gold recovery rate from 82.87% to92.16%, increasing economic benefits of enterprises.Key words: all slime cyanidation - zinc powder replacement; flotation; replace; recovery rate; economic benefit该金矿自1998年建成投产以来,选矿技术人员围绕着如何提高选矿技术指标和经济效益,对选矿工艺流程进行了多次的变更和革新。
氰化法提金的基本原理
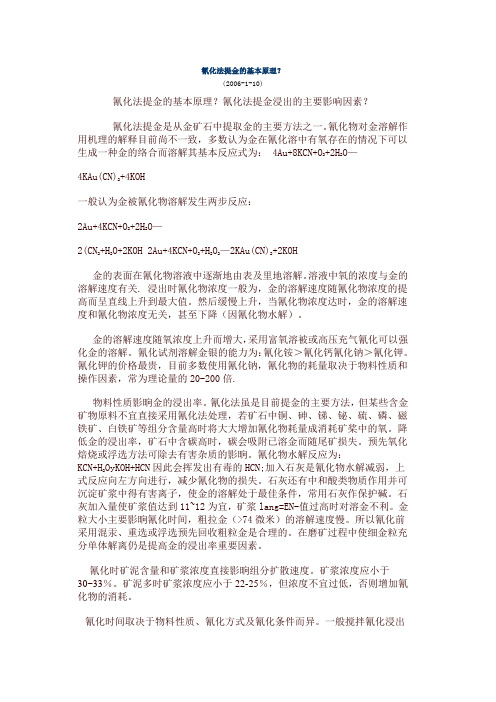
氰化法提金的基本原理?(2006-1-10)氰化法提金的基本原理?氰化法提金浸出的主要影响因素?氰化法提金是从金矿石中提取金的主要方法之一。
氰化物对金溶解作用机理的解释目前尚不一致,多数认为金在氰化溶中有氧存在的情况下可以生成一种金的络合而溶解其基本反应式为: 4Au+8KCN+O2+2H2O—4KAu(CN)2+4KOH一般认为金被氰化物溶解发生两步反应:2Au+4KCN+O2+2H2O—2(CN2+H2O+2KOH 2Au+4KCN+O2+H2O2—2KAu(CN)2+2KOH金的表面在氰化物溶液中逐渐地由表及里地溶解。
溶液中氧的浓度与金的溶解速度有关. 浸出时氰化物浓度一般为,金的溶解速度随氰化物浓度的提高而呈直线上升到最大值。
然后缓慢上升,当氰化物浓度达时,金的溶解速度和氰化物浓度无关,甚至下降(因氰化物水解)。
金的溶解速度随氧浓度上升而增大,采用富氧溶被或高压充气氰化可以强化金的溶解。
氰化试剂溶解金银的能力为:氰化铵>氰化钙氰化钠>氰化钾。
氰化钾的价格最贵,目前多数使用氰化钠,氰化物的耗量取决于物料性质和操作因素,常为理论量的20-200倍.物料性质影晌金的浸出率。
氰化法虽是目前提金的主要方法,但某些含金矿物原料不宜直接采用氰化法处理,若矿石中铜、砷、锑、铋、硫、磷、磁铁矿、白铁矿等组分含量高时将大大增加氰化物耗量成消耗矿桨中的氧。
降低金的浸出率,矿石中含碳高时,碳会吸附已溶金而随尾矿损失。
预先氧化焙烧或浮选方法可除去有害杂质的影晌。
氰化物水解反应为:KCN+H2OyKOH+HCN因此会挥发出有毒的HCN;加入石灰是氰化物水解减弱,上式反应向左方向进行,减少氰化物的损失。
石灰还有中和酸类物质作用并可沉淀矿浆中得有害离子,使金的溶解处于最佳条件,常用石灰作保护碱。
石灰加入量使矿浆值达到11~12为宜,矿浆lang=EN-值过高时对溶金不利。
金粒大小主要影晌氰化时间,粗拉金(>74微米)的溶解速度慢。
氰化法提金工艺

氰化法提金工艺—锌粉置换篇传统的氰化法提金工艺主要包括浸出、洗涤、置换(沉淀)三个工序。
①浸出——矿石中固体金溶解于含氧的氰化物溶液中的过程。
②洗涤——为回收浸出后的含金溶液,用水洗涤矿粒表面以及矿粒之间的已溶金,以实现固液分离的过程。
③置换——用金属锌从含金溶液中使其还原、沉淀,回收金的过程。
20世纪以来,从氰化矿浆中回收金是先进行矿浆的洗涤,然后进行贵液的澄清、除气。
从澄清的贵液中沉淀金,一直沿用锌粉置换法。
20世纪60年代以来才发展起来的向矿浆中加入活性炭的“炭浆法”发展很快。
随着对离子交换剂应用的研究,采用离子交换树脂从氰化液或氰化矿浆中吸附金的方法亦具有重要的实用价值。
在氰化液的溶剂萃取提金方面也作过一些研究。
当往氰化含金液中加人硫酸时,可用异戊醇来萃取金,萃取率随硫酸浓度的升高而增加。
如在2mol/L的硫酸液中进行萃取,还可使金与砷、铁等杂质分离。
使用氧代烷氧基磷酸酯从氰酸盐碱性液中萃取金,萃取指标令人满意;使用亚硫酸钠反萃取也获得了较好的结果等等。
1.氰化浸金用含氧的氰化物溶液把矿石中的金溶解出来的过程叫氰化浸出。
目前,无论从工艺、设备、管理或操作等方面都已日臻完善。
如前所述,金在含有氧的氰化物溶液中的溶解,实质上是一个电化学腐蚀过程。
浸出过程中主要使用的药剂是氰化物和保护碱两种。
1)氰化物工业上用于氰化法浸出金的氰化物主要有氰化钾(KCN)、氰化钠(NaCN)、氰化钙金鹏矿业机械有限公司 1[Ca(CN)2]和氰化铵(NH4CN)四种。
在生产中常用的氰化物是氰化钠,它是一种剧毒的白色粉末,商品氰化钠一般压制成球状或块状。
工业上也有用氰熔体作为浸出药剂的。
它是将氰化钙、食盐和焦炭混合后在电炉中熔化而成的一种混合物。
除了含40%-45%的Ca(CN)2和NaCN以外,还含有一些对氰化过程有害的杂质,如可溶性硫化物、碳以及一些不溶性杂质等。
其特点是价格便宜,但用量大,约为氰化钠的2-2.5倍。
锌粉置换岗位安全操作规程

锌粉置换岗位安全操作规程一、前言为确保岗位工作人员的人身安全和生产设备的安全运行,有效预防事故的发生,特制定本《锌粉置换岗位安全操作规程》。
二、岗位概述锌粉置换岗位是指负责进行锌粉置换工作的工作岗位。
三、岗位职责1.对锌粉进行置换操作,保证生产持续进行;2.配合相关部门进行设备维护、保养和检修;3.发现设备故障和异常情况时及时上报并采取相应措施;4.严格按照操作规程进行操作,确保操作的安全性和有效性;5.积极参与各类安全培训和应急演练。
四、操作规程4.1 岗位操作流程1.确保工作场所的通风设备正常运行;2.穿戴好相应的防护设备,包括帽子、耳塞、防护服、手套等;3.检查置换设备的运行状态,确保其正常运转;4.开始锌粉置换操作,按照设备操作手册中的规定进行操作;5.在操作过程中,严禁私自更改设备工艺参数,如有需要,应及时向主管或相关技术人员报告;6.操作完成后,关闭相关设备,清理工作现场,保持设备及周边环境的整洁;7.及时上报操作记录及异常情况,并配合相关部门的后续处理工作。
4.2 安全注意事项1.严禁在暴露的锌粉中使用明火作业,以免引发火灾或爆炸;2.进入操作区域前,应先检查设备是否处于停止状态,确保人员和设备的安全;3.操作人员应根据个人身体条件,选择适合的防护用品;4.操作过程中应保持安静,避免拆卸、安装设备时产生的噪音干扰到其他工作人员;5.发现设备异常时应立即停止操作,并向主管或相关技术人员报告。
4.3 紧急情况处理1.发生火灾时,应迅速切断有关设备的电源,启动应急消防设备并报警;2.发生爆炸时,应立即躲避到安全地带,避免受伤后及时报警并向主管汇报;3.发现有毒气体泄漏时,应立即切断气源并撤离现场,然后报警并向主管汇报。
五、安全培训和演练1.每位岗位工作人员入职时应接受相应的安全培训,包括锌粉置换岗位的相关操作规程和安全注意事项;2.定期组织安全培训和演练,提高工作人员的安全意识和应急处理能力;3.对岗位工作人员进行定期安全考核,确保其了解和掌握相关操作规程和安全知识。
氰化锌粉置换规范讲义.
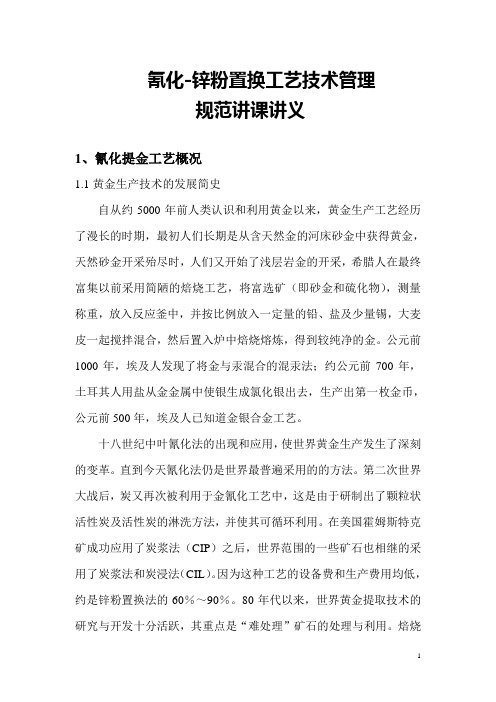
氰化-锌粉置换工艺技术管理规范讲课讲义1、氰化提金工艺概况1.1黄金生产技术的发展简史自从约5000年前人类认识和利用黄金以来,黄金生产工艺经历了漫长的时期,最初人们长期是从含天然金的河床砂金中获得黄金,天然砂金开采殆尽时,人们又开始了浅层岩金的开采,希腊人在最终富集以前采用简陋的焙烧工艺,将富选矿(即砂金和硫化物),测量称重,放入反应釜中,并按比例放入一定量的铅、盐及少量锡,大麦皮一起搅拌混合,然后置入炉中焙烧熔炼,得到较纯净的金。
公元前1000年,埃及人发现了将金与汞混合的混汞法;约公元前700年,土耳其人用盐从金金属中使银生成氯化银出去,生产出第一枚金币,公元前500年,埃及人已知道金银合金工艺。
十八世纪中叶氰化法的出现和应用,使世界黄金生产发生了深刻的变革。
直到今天氰化法仍是世界最普遍采用的的方法。
第二次世界大战后,炭又再次被利用于金氰化工艺中,这是由于研制出了颗粒状活性炭及活性炭的淋洗方法,并使其可循环利用。
在美国霍姆斯特克矿成功应用了炭浆法(CIP)之后,世界范围的一些矿石也相继的采用了炭浆法和炭浸法(CIL)。
因为这种工艺的设备费和生产费用均低,约是锌粉置换法的60%~90%。
80年代以来,世界黄金提取技术的研究与开发十分活跃,其重点是“难处理”矿石的处理与利用。
焙烧法在处理难处理矿的预处理的中普遍得到了应用。
1949年加拿大的大耶洛奈夫首先使用流化床焙烧法焙烧浮选精矿以来,许多国家和地区都建立了金精矿焙烧工厂。
1988年美国默克尔建立了第一座金矿石非酸性加压氧化厂,这种方法适合处理含碳酸盐高的矿石。
更新一代的预氧化技术是微生物湿法化学氧化(细菌氧化)。
随着金矿石难处理性的增大和环保日益严格的要求,人们正寻求能用于酸性介质以避免氧化后产物的碱性氰化处理所需要的高中和费用的浸出剂,以及相应的氰化提金技术。
虽至今仍未实现工业应用,但这毕竟是提金技术的一个重要发展方向。
微生物浸出是利用微生物(细菌)的氧化作用选择性溶解矿石中某组分的工艺过程,既可以用来提取金属,也可以用来除去矿石中的有害干扰组分。
锌粉置换技术操作规程(最新版)
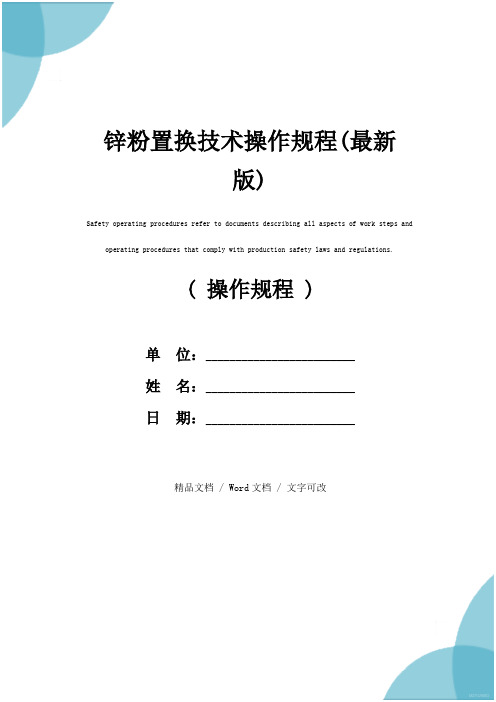
( 操作规程 )单位:_________________________姓名:_________________________日期:_________________________精品文档 / Word文档 / 文字可改锌粉置换技术操作规程(最新版)Safety operating procedures refer to documents describing all aspects of work steps and operating procedures that comply with production safety laws and regulations.锌粉置换技术操作规程(最新版)1.工艺要求1.1工序产品的质量要求1.1.1.金置换率99.5%,银置换率99%。
1.1.2.氰化贫液含金品位≤0.02mg/L,贫液快速检测样做到粉白。
1.1.3.金泥:含Au品位根据贵液而定。
1.1.4氰根浓度≥0.6g/l。
1.1.5锌粉的添加1.1.5.1根据贵夜流量均匀、连续、稳定添加(工段通知);1.1.5.2锌粉添加量<0.25kg/t矿(40—50g/m³);(生产量根据原料金品位、银品位、尾液指标,按工段通知确定执行)1.1.5.3贫液含金品位<0.03mg/l为合格;1.1.5.4金板框拆除前高压空气吹出水份4—6小时,金泥水份<45%为合格;1.1.5.5泥板框拆除前高压空气吹出水份3—5小时,矿泥水份<25%为合格;1.2原料及溶剂标准1.2.1.锌粉粒径:-325目95%。
1.2.2.锌粉用量:依据快速检测结果来调整。
1.3工艺技术条件1.3.1氰化贫液品位≤0.02mg/L。
1.3.2氰化贵液CN¯:1.0~1.2‰,温度≥15℃,pH值10.5~11。
1.3.3脱氧塔负压0.090MPa以上。
1.3.4贵液中悬浮物0.1mg/L。
3.置换板框运行作业程序:第一步准备:①运行的板框压力升至0.5MPa、流量下降至规定流量减2m³、置换泵电机运行频率50HZ、工段通知停运或发生其他特殊情况,以上情况,申请拆除板框;②提前24小时做好书面计划,由生产科审批,并通知相关人员,做好准备工作;③倒备用板框的准备:人员、挂浆用的锌粉50kg、清理混料筒的工具等;第二步启动:①板框打回流(若需清理混料筒,则需停车),停止加锌粉;②按次序缓缓打开备用板框进、出口阀门,在此过程中检查板框无异常(如有喷漏液体、出口跑混等异常情况,关闭阀门后通知相关人员及时处理);③按次序缓缓关闭运行板框进、出口阀门,把流量调至最大;④记录开启板框的相关数据,板框开始运行;第三步挂浆:①具备挂浆的条件:脱氧塔真空表示数≥0.08kpa、锌粉50kg、流量最大、混料筒运行正常、脱氧塔液位2/3;②挂浆量:0.9—1.1kg/㎡(过滤面积);挂浆时间10—15分钟;③挂浆标准:均匀连续、短时间、大流量、锌粉平均分布在滤布的表面上;④挂浆结束2—3分钟,化验室取贫液样,化验金品位≤0.05mg/l 为正常(出现问题,及时处理);⑤打开生产阀门,关闭回流阀,调节变频器,至正常流量;开启锌粉给料机,按要求添加锌粉;第四步运行①随着板框的运行,板框阻力升高,流量会下降,要随机调节变频器,保持流量达标稳定;②严格按要求添加锌粉,避免贫液跑高;③非特殊情况,锌粉岗位打回流,不要停车,以避免因停车造成浆层脱落,引起贫液跑高或额外挂浆而浪费锌粉;④与化验室保持密切联系,及时获取贫液指标,发现问题,立即打回流,避免造成尾液跑高的事故发生;第五步停运(倒板框):①达到工艺条件后,按程序把板框倒换过,老板框停运;②及时接好高压空气管道,吹出金泥水份:吹出时间≥6小时,注意事项为:及时调节,风量的大小要适宜;③拆出的金泥水份≤45%;4.操作规程4.1操作前准备4.1.1检查各电机设备运转是否正常,润滑性能是否良好,调整贵液泵进出口阀门,向泵内进液排气,达到开车状态。
- 1、下载文档前请自行甄别文档内容的完整性,平台不提供额外的编辑、内容补充、找答案等附加服务。
- 2、"仅部分预览"的文档,不可在线预览部分如存在完整性等问题,可反馈申请退款(可完整预览的文档不适用该条件!)。
- 3、如文档侵犯您的权益,请联系客服反馈,我们会尽快为您处理(人工客服工作时间:9:00-18:30)。
氰化-锌粉置换工艺技术管理规范讲课讲义1、氰化提金工艺概况1.1黄金生产技术的发展简史自从约5000年前人类认识和利用黄金以来,黄金生产工艺经历了漫长的时期,最初人们长期是从含天然金的河床砂金中获得黄金,天然砂金开采殆尽时,人们又开始了浅层岩金的开采,希腊人在最终富集以前采用简陋的焙烧工艺,将富选矿(即砂金和硫化物),测量称重,放入反应釜中,并按比例放入一定量的铅、盐及少量锡,大麦皮一起搅拌混合,然后置入炉中焙烧熔炼,得到较纯净的金。
公元前1000年,埃及人发现了将金与汞混合的混汞法;约公元前700年,土耳其人用盐从金金属中使银生成氯化银出去,生产出第一枚金币,公元前500年,埃及人已知道金银合金工艺。
十八世纪中叶氰化法的出现和应用,使世界黄金生产发生了深刻的变革。
直到今天氰化法仍是世界最普遍采用的的方法。
第二次世界大战后,炭又再次被利用于金氰化工艺中,这是由于研制出了颗粒状活性炭及活性炭的淋洗方法,并使其可循环利用。
在美国霍姆斯特克矿成功应用了炭浆法(CIP)之后,世界范围的一些矿石也相继的采用了炭浆法和炭浸法(CIL)。
因为这种工艺的设备费和生产费用均低,约是锌粉置换法的60%~90%。
80年代以来,世界黄金提取技术的研究与开发十分活跃,其重点是“难处理”矿石的处理与利用。
焙烧法在处理难处理矿的预处理的中普遍得到了应用。
1949年加拿大的大耶洛奈夫首先使用流化床焙烧法焙烧浮选精矿以来,许多国家和地区都建立了金精矿焙烧工厂。
1988年美国默克尔建立了第一座金矿石非酸性加压氧化厂,这种方法适合处理含碳酸盐高的矿石。
更新一代的预氧化技术是微生物湿法化学氧化(细菌氧化)。
随着金矿石难处理性的增大和环保日益严格的要求,人们正寻求能用于酸性介质以避免氧化后产物的碱性氰化处理所需要的高中和费用的浸出剂,以及相应的氰化提金技术。
虽至今仍未实现工业应用,但这毕竟是提金技术的一个重要发展方向。
微生物浸出是利用微生物(细菌)的氧化作用选择性溶解矿石中某组分的工艺过程,既可以用来提取金属,也可以用来除去矿石中的有害干扰组分。
难浸金矿往往是因为金属中硫化矿对金形成包裹的原因,细菌氧化可以破坏这些金属硫化矿,从而提高金的氰化浸出率。
对金属硫化矿通常采用氧化铁硫杆菌或嗜热硫杆菌。
细菌冶金的问题包括细菌的采集、分离和培养以及为了适应建厂地区的环境对细菌进行训化。
这种方法处理复杂含矿我国处于世界领先水平。
但采用细菌浸出对矿石的要求是有条件的,如果矿石中含硫很高并含有铜等有价金属,采用该方法会产生大量的硫酸盐和稀酸,不但硫、铜、砷等无法回收,还要用大量的石灰进行中和,产生大量的渣,增加了渣堆场的容积。
从已投入生产的几个企业来看,综合回收和经济效益并不理想。
压热氧化浸出就是通过提高温度和通氧气来增大有价金属或有害金属在浸出剂中的溶解度,从而加速浸出反应的过程。
这一方法使难浸金矿中硫化物及含砷化合物被氧化成硫酸和砷酸盐,使金粒暴露出来便于氰化浸出。
压热氧化浸出是在压力为20kg/cm2。
温度为180℃~200℃的条件下进行的。
对设备材料、机械加工、自动化仪表及控制、操作技术水平都有较高要求。
我国在镍冶金方为得到广泛应用,但在黄金冶炼方为尚处在研究阶段。
本方法只适用于原矿,不适于选矿的精矿。
尽管有人提出催化氧化法以降低浸出温度和压力,但对材料、配套设备、自动化仪表及控制综合研究不足,没有达到预期的效果,因规模小,经济效益也不好。
造琉捕金适应性更为广泛,尤其针对难处理矿各元素回收率高,不使用氰化钠等更能适应严格的环保要求。
1.2黄金生产工艺概述矿石的破碎与细碎,以及精矿的细磨,主要是为了解离金、含金矿物以及其他有经济价值的金属,最佳细碎粒度受各种经济因素的限制,如金的回收率,加工费用和细碎费用之间的平衡。
物料破碎分为三段:粗碎至150~125mm,中碎至100~25mm,细碎至20~5mm。
矿石主要采用各种破碎机,如鄂式破碎机、圆筒破碎机、锤碎机等。
1.2.2 筛分与分级筛分是为了从破碎后的矿石中,分出细粒产品。
按目的不同,可分为预先筛分、检查筛分、准备筛分和最终筛分。
筛分可实现一下功能:(1)跟据后续加工过程按粒极分别处理的要求,对物料进行分级。
(2)从矿浆和溶液中通过筛分过程分离出吸附剂。
(3)用于尾矿构筑中尾矿的分级。
1.2.3 选矿在金的提取流程中,选矿作为一种颗粒金回收的方法,或在氰化之前作为“预富集”手段而被广泛应用,其主要作用是:(1)通过重选或混汞回收游离金和与重矿物伴生的金。
(2)用浮选法剔除部分品味低但对下步金提取会产生副面影响的组分,如消耗氰化物的硫化物、吸附金的含炭物质、耗酸的碳酸盐。
(3)优先浮选,例如金、含金黄铁矿、砷黄铁矿的分离。
1.2.4 预氧化处理用常规浸出法处理时,金回收率低,或是试剂消耗过高的矿可采用预氧化处理的方法,使金变得适合于氰化浸出。
局部氧化适合于钝化难处理矿石,解离出与特定矿物伴生的金,或是解离出在硫化物中的、在优先氧化部位的金。
全部氧化通常用于嵌布细粒金的,或完全与之伴生的硫化物矿。
焙烧氧化法用来处理含硫化物、砷化物、炭质及碲化矿物的矿石和精矿,在世界范围内以应用了几十年。
而且被证明是可行的方法。
生物氧化以被用于处理含硫化物和砷化物的浮选精矿,尽管氧化速度较慢,但与焙烧法和加压氧化法比较,具有费用低、有利于环保因此有一定的推广价值。
所有湿法冶金中,金的提取都采用浸出步骤以获得提取回收金的含金溶液,目前仍采用稀的碱性氰化物溶液作为溶解金的浸出溶液。
金的氰化浸出有两种基本方法:搅拌浸出和堆浸。
这两种方法提金原理相同,所不同的只是矿石的最终处理粒度及浸出作业不同。
(1)搅拌浸出搅拌浸出是在混合搅拌槽中进行的,一般要求矿石粒度达80%<150μm(100目)和80%<4μm(400目)之间。
矿石和氰化物溶液皆在动态中将金浸出。
浸出时用空气或机械搅拌使固体保持悬浮状态。
影响氰化浸出的因素较多,标准氰化浸出工艺条件下,矿将浓度为35%~50%,pH值用石灰调至9.5~11.5之间、氰化物浓度为0.02%~0.1%,通空气或纯氧以保持浸出时足够的溶解氧(通常条件下,氧在水中最高溶解度为5~10mg/L)温度21~45℃,浸出时间24~40h。
(2)堆浸堆浸工艺是先将破碎后的矿石堆放于不透水的底垫上,然后将氰化溶液喷洒到矿堆的顶部,氰化物溶液渗透过矿石堆并将金浸出来。
一般情况下,堆浸时矿石粒度为10~25mm,堆浸时间60~90d,金的浸出率一般为70%。
固液分离在提金过程中有着重要意义,浸出矿浆经固液分离才能获得供下一步回收金用的澄清贵液,而为了提高金的回收率,需对固液分离后的固体进行洗涤,以尽量回收固体部分所夹带的含金溶液。
生产中用倾析、过滤法和流态化法(试验采用流态化洗涤塔代替浓密机进行洗涤和液固分离。
由于流态化洗涤塔系运用逆流原理,传质效率高,可以使洗涤过程得到强化。
)进行浸出矿浆固液的分离与洗涤。
倾析法分为连续倾析法和渐断倾析法两种。
前者在澄清器或浓密机中进行,后者多在几台单层或多层浓密机中以连续逆流方式进行。
矿浆或者浑浊溶液分离还能涉及到多种化学药品及其组合应用。
这些药品包括pH调整剂(如氢氧化钠、氢氧化钙、及硫酸)、絮凝剂、凝结剂及粘度调整剂。
它们都会对下步过程有明显影响。
从浸出液或通过中间富集及纯化阶段回收金,是应用化学的或电解的还原过程实现的。
对于稀的浸出液,一般直接采用锌粉置换沉淀方法回收金,但电积法不适用,因为在稀溶液中电流效率很低而且处理体积很大的浸出液需要很大的电解槽;因此,一般都采用锌粉置换的工艺。
1.2.8 精练提纯金银有火法、化学法和电积法。
目前采用电积法,其特点是操作简单、原材料消耗少、效率高、产品纯度高、劳动条件好,且能综合回收铂族金属。
其次采用化学提纯法,如硫酸浸煮法、硝酸分银法和王水分金法等,主要用于某些特殊原料和特定流程中。
火法为古老的金银提纯方法,目前一般不在使用。
1.2.9 废物处理/处置废料可用解毒法或回收有价值废料组分的处理办法。
一般步骤是:○1试剂回收和循环;○2金属的回收;○3去毒性。
前两步骤主要用于提高经济效益,并可能去处一部分毒性,改善环境。
当废物含毒物量超过法规允许的范围时,或者废物需要在工艺过程中有效循环使用时去毒是非常必要的。
1.3氰化浸出锌粉置换的理论基础在含氧的氰化物溶液中金的溶解,称为氰化浸出。
贵金属金和银是化学性质很稳定的元素,它很难氧化,在绝大多数的溶剂中也不会溶解。
人类在十八世纪中叶就发现了金、银和铜等金属能够溶解于氰化物的水溶液中,同时也确定了有空气存在的作用和温度对溶解速度的影响。
金对电子就有很强的亲合力,因此它的电离氧化过程需要很大的能量。
在氰化过程中,金在形成络合离子之间,先转化成离子状态,然后再形成金的络合离子。
Au →e A u ++同样,对于银:在氰化物溶液中,当有氰存在时,金溶解可以用下面的反应方程式表示:或反应式分两步进行:如果用热力学反应式,金的溶解则可以写成:-=+2)(2e 242CN Au CN Au —— 250550308-=∆F 卡;-=++OH O O H 2e 2)(2122气 184890298-=∆F 卡; )(21)(2122气溶液O O = 19730298-=∆F 卡; 以上三式相加:455170208-=∆F 卡;这个反应的平衡常数 33103.2⨯=K 。
对于银在氰化物溶液中得溶解,反应方式与金相似,而401970208-=∆F 卡和29109.2⨯=K 。
为了使金、银得到较快的溶解速度,合理的条件既不单是溶解氧的浓度,也不单是游离氰化物的浓度,而是两者浓度的比值。
因此,如果只是片面的强调充气而忽视了游离氰化物的浓度,或者加入过量的氰化物,而溶液中的氧含量低于理论值,对提高金、银的浸出速度都是成效不大的,都会造成充气动力或氰化物的浪费。
当向溶液中加入锌后,金被锌置换转换化为金属状态而析出,同时锌溶解于碱性的氰化物溶液中。
锌置换的过程是电化学反应过程,金的沉淀是由于生成电偶的结果,该电偶为锌——铅电偶,锌为阳极,铅为阴极。
铅的来源除矿石含有外,主要是向锌的产品中加入的铅或置换过程中加入可溶性铅盐。
金氰络合离子在电偶电流的作用下,必然向阳极移动与锌作用,使锌以氰锌络合离子状态进入溶液中,而金被还原沉淀出来,其反应式为:锌同时也部分溶解于碱性的氰化物溶液中其反应过程为:水解离过程产生氢离子,其反应式为:氢离子在阴极还原析出2H ,反应式为:综合以上反应,可得出下列反应式:当溶液中有氧存在时,锌被氧化:↓=++222)(21n OH Zn O H O Z (白色) 在低浓度氰化物溶液中,氢氧化锌和氰化锌沉淀会沉积在锌的表面妨碍金的置换,所以金的置换过程中,要保持溶液中有一定的氰化物和碱的浓度,避免2)(OH Zn 和2)(CN Zn 的生成,使金的置换过程顺利进行。