型材的剖面模数
项目四 钢质船舶规范法结构设计(4)组合型材的剖面设计

3)型材稳定性条件
型材腹板高而薄或面板过宽时, 型材腹板高而薄或面板过宽时,往往面板由于弯 曲压应力作用或腹板受过大的剪切作用而局部失 去稳定性, 去稳定性,因此型材的尺寸搭配应满足这种局部 稳定性的要求。 稳定性的要求。 要求腹板高厚比h/t< ,否则应设置加强筋, 要求腹板高厚比 <75,否则应设置加强筋, 长江实船h/t=50~60。 长江实船 。 经稳定性计算, 型材面板宽厚比 型材面板宽厚比b/δ< , 经稳定性计算,T型材面板宽厚比 <36,实 际可取b=( 际可取 (10~20)δ,折边型材减半。 ) ,折边型材减半。 h、b、t、δ的规定如图 所示。 的规定如图5-8所示 、 、 、 的规定如图 所示。
2.设计步骤 .
型材的剖面设计,就是确定型材剖面尺寸, 型材的剖面设计,就是确定型材剖面尺寸,使型材 满足强度、刚度及稳定性要求。 满足强度、刚度及稳定性要求。 现结合实例,说明组合型材剖面的设计步骤。 现结合实例,说明组合型材剖面的设计步骤。 某长江客货轮, 某长江客货轮,甲板纵桁所必须的剖面模数 W=404cm3,惯性矩 ,惯性矩I=7780cm4,甲板纵桁跨长 , l=7.7m,载荷的平均宽度b 2.35m, l=7.7m,载荷的平均宽度b = 2.35m,设计型材剖面 尺寸。 尺寸。
⑤确定面板尺寸 面板剖面积: 面板剖面积:
w h × t 404 30 × 0.6 f1= − = − = 13.5 − 4 = 9.5 cm 2 h k 30 4.5
⑥决定面板尺寸
δ = (1.2 ~ 2)t = 7.2 ~ 12 mm, 实取δ =8mm
950 b= = = 119 mm, 实取b = 120 mm δ 8 f1
1.首先确定腹板尺寸。 首先确定腹板尺寸。
剖面模数计算

56.00 50.00 50.00 72.00 50.00 50.00 84.00 50.00 50.00 50.00 91.00 91.00 50.00 50.00 50.00 50.00 50.00 50.00 60.00 60.00 50.00 50.00 50.00 50.00 50.00 50.00 50.00 50.00 50.00 50.00 50.00 50.00 50.00
zn
h
5.73 12.68680168
1.165
0.926
2.72
2.04
3.57
1.95
4.42
1.86
5.27
1.77
6.12
1.64
6.97
1.49
L400× 120×12
×23
W=1624.
0.85
12.69
4
662.22 89 cm3
L400×
120×12
×23
W=1624.
0.85
11.43
135.01 156.35 143.10 176.66 198.08 222.24 228.33 254.82 286.55 315.72 288.72 335.45 358.61
395.82 398.97 450.07 497.58 541.77 68.72 99.58 111.09 139.40 155.61 188.68 206.01 252.54 275.21 324.37 348.50 407.54 436.64 517.49 548.87
T型材计算
T型材带板面积
轧制型材计算
L63×40×4 L63×40×5 L63×40×6 L63×40×7 L75×50×5 L75×50×6 L75×50×8 L75×50×10 L90×56×5 L90×56×6 L90×56×7 L90×56×8 L100×63×6 L100×63×7 L100×63×8 L100×63×10 L100×80×6 L100×80×7 L100×80×8 L100×80×10 L110×70×6 L110×70×7 L110×70×8 L110×70×10 L125×80×7 L125×80×8
项目六--6.2.3型材剖面设计实例(精)
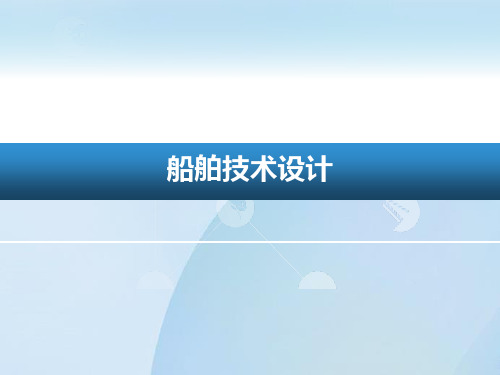
176N / m m2, M 77kN m,N 71kN, Y 235N / m m2,
任务2 优化设计船舶型材剖面
项目六
船舶型材剖面设计
1、计算 W1 和 f 0
W1
M
437.5cm2,f 0
N 9.5cm2 0.85
船舶技术设计
项目六
船舶型材剖面设计 6.2.3 型材剖面设计实例
学习内容: 某船用T型材的剖面优化设计 学习目标: 初步具有优化设计型材剖面的能力
任务2 优化设计船舶型材剖面
项目六
船舶型材剖面设计
例题:
已知条件:
88N / m m2,f 2 18cm2,t0 4m m,l 8m
式中: a1
W1 f ,a2 2 fh f
任务2 优化设计船舶型材剖面
项目六
船舶型材剖面设计
5、第二次近似决定m 因为:
2 f1 f 0.805 2 f2 f N 74.6n / m m2 0.85 f
0.424
则运用式(7-19),可得m=78.4
所以总稳定性可以得到保证。
任务2 优化设计船舶型材剖面
ቤተ መጻሕፍቲ ባይዱ
项目六
船舶型材剖面设计
拓展与思考
案例1:某船T型材主肋骨剖面的优化设计。
设规范对某船货舱主肋骨所要求的剖面模数 [W]=1200cm3 ,要求的剖面惯性矩 [I]=17640cm4 ,已知此货舱舷侧外板 厚度 t2 =18mm,肋距 s=0.78m,主肋骨跨距 l=4.5m,试设 计此主肋骨用T型材的剖面尺寸。
任务2 优化设计船舶型材剖面
第十六讲 型材剖面设计概要

因为K=4,所以 2 3 3 W0 0.75m t0 235.2cm (4)第一次近似计算型材剖面尺寸 2 < 及 < W0 W1 2W0 f 0 < mt0 hopt m t0 28cm 则
2 f m t0 11.2cm2
船体强度与结构设计
初取腹板尺寸为300×4,则
(7)确定面板尺寸
a2 (3a1 1) 0.25(6a1 1) f1 f 12.1cm2 3a2 1
由式(5.3.2)及(5.3.3)决定的n0在9~18之间。 由式(5.3.32)面板宽度为:
b1 2n0 f1 14.8 ~ 20.9cm
船体教研室吴春芳编 Email:qiuyuan_cat@
船体强度与结构设计
3)设计变量的类型
a.结构的剖面几何参数
b.结构的布局参数(如结构的型式,节点位 置,构件间距等) c.结构所用材料的参数 其中a是最常见也是最简单的一类结构优化设计
问题
明确一个标志:设计空间
船体教研室吴春芳编 Email:qiuyuan_cat@
船体教研室吴春芳编 Email:qiuyuan_cat@
船体强度与结构设计
3)可行域 满足所有约束条件的结构设计方案是可以被应 用的设计,称为可行域。 所有可行设计点的集合称为可行域。 构成可行域边界的约束曲面称为临界约束。
x1
0 = ) x h1(
h2(x )=0
0
可行域
0 = ) x ( h
f x min或 max
T
使目标函数 并受到约束
h j X 0
g k X 0
j 1,2,3, J k 1,2,3, K
剖面模数计算
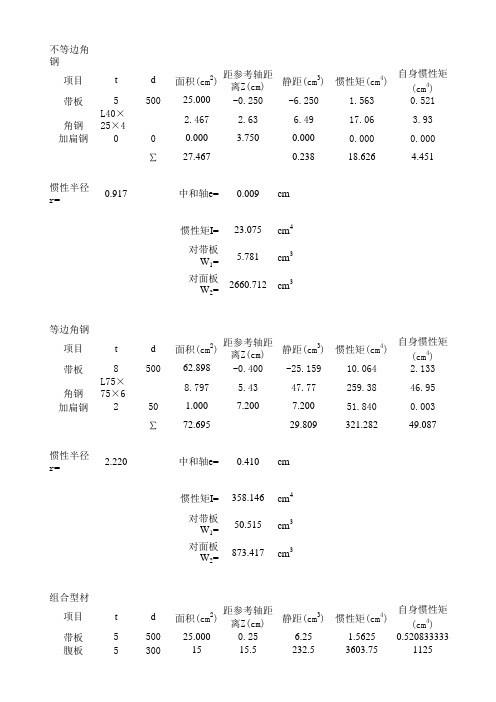
r=
1.151
中和轴e= 0.098 cm
惯性矩I= 36.894 cm4
对带板 W1=
7.526
cm3
对面板 W2=
376.215
cm3
槽钢
项目
t
d
面积(cm2)
距参考轴距 离Z(cm)
静距(cm3)
惯性矩(cm4)
自身惯性矩 (cm4)
带板
10 1100 78.622 -0.500 -39.311
中和轴e= 0.410 cm
惯性矩I= 358.146 cm4
对带板 W1=
50.515
cm3
对面板 W2=
873.417
cm3
组合型材
项目
t
带板
5
腹板
5
d
面积(cm2)
距参考轴距 离Z(cm)
静距(cm3)
惯性矩(cm4)
自身惯性矩 (cm4)
500 25.000
0.25
6.25
1.5625 0.520833333
静距(cm3)
惯性矩(cm4)
自身惯性矩 (cm4)
500 62.898 -0.400 -25.159
10.064
2.133
8.797
5.43
47.77
259.38
46.95
50
1.000
7.200
7.200
51.840
0.003
∑ 72.695
29.809
321.282
49.087
惯性半径
r=
2.220
惯性矩I= 621.146 cm4
对带板 W1=
64.359
型材的剖面模数

1380 1400 1450
1500
1550 1600
1650
1700 1750 1800 1850 1900
1950
2000 2050
2100
2150 2200 2250 2300 2350 2400 2450
具有附连翼板的剖面,(mm)
- 370×14 - 370×15
- 360×28 - 380×26 - 400×24
- 280×12
580
- 280×22
肘板尺寸
折
无折边
有折边 边
55
mm - 280×9.5 - 280×8.0
- 290×9.5 - 290×8.0
折 边 60
- 310×10.5 - 310×8.5
mm
- 315×10.5 - 315×8.5 - 320×10.5 - 320×8.5
- 330×11.0 - 330×9.0
- 200×17
240 - 150×100×12
- 220×15
250 - 180×90×10 -200×11.5 - 200×18
260 - 160×80×14
- 220×16 - 240×14
肘板尺寸
无折边
有折边
- 180×7.0 - 180×6.5
折 边 - 190×7.0 - 190×6.5
- 370×13
肘板尺寸
无折边
有折边
- 370×12.0 -370×9.5
折 边 - 380×12.0 -380×10.0
70 mm
- 390×12.5 -390×10.0
折 - 400×13.0 - 400×10.5 边
型材剖面模数计算

型材剖面模数计算要计算型材剖面的模数,首先需要了解型材的截面形状。
常见的型材包括角钢、圆钢、槽钢、工字钢等,每种型材的截面形状都有所不同。
这些型材的截面形状可以通过几何测量或CAD软件进行测量和绘制。
一般来说,计算型材剖面模数可以通过以下步骤进行:1.测量型材的截面尺寸:使用尺子或卡尺等工具测量型材的截面尺寸,并记录下来。
比如,对于角钢的剖面,可以测量上下边缘的高度和左右边缘的宽度。
2.计算型材的截面面积:根据测量得到的尺寸,可以计算出型材的截面面积。
对于角钢的剖面,可以将上下边缘的高度乘以左右边缘的宽度,得到截面的面积。
3.计算型材的惯性矩:惯性矩是衡量型材在受力时抵抗形变的能力。
计算型材的惯性矩需要使用型材的截面尺寸来进行计算。
惯性矩的计算公式根据型材的截面形状和坐标系的选择有所不同。
对于简单的截面形状,比如矩形、圆形等,可以使用经典的惯性矩计算公式进行计算。
对于复杂的截面形状,可以使用CAD软件进行建模,并通过软件提供的计算工具进行计算。
4.计算型材的模数:型材的模数可以通过将型材的惯性矩除以型材的最远离中性轴的距离得到。
模数的计算结果就是型材在剖面上的抗弯刚度。
模数的大小可以反映型材的强度和刚度。
模数越大,说明型材的强度和刚度越大,能够承受更大的外力而不产生较大的形变。
在实际工程应用中,可以根据型材的截面尺寸和模数来选择合适的型材进行设计。
对于需要承受较大外力的结构,应选择截面积大、模数大的型材,以提高结构的强度和刚度。
对于受力相对较小的部位,可以选择截面积小、模数小的型材,以减小结构的重量和成本。
剖面模数计算方法
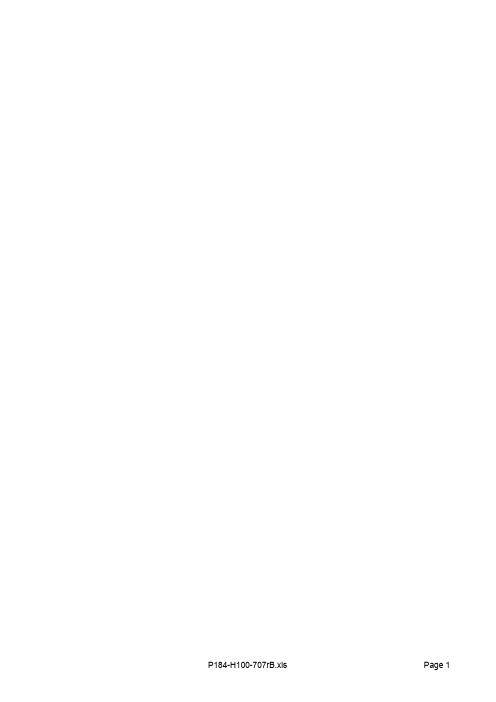
Allowable stress to ABS MODU 2001, part 3, charpter 2, section 1, item 3.3F=Fy/F.S., whereFy = 235 N/mm2 , or 34 ksiF.S. = 1.67 for axial or bending stress2.50 for shear stressHence, F = 140.7 N/mm2 , or 20.4 ksi for axial or bending stress94.0 N/mm2 , or 13.6 ksi for shear stress1. Bulkhead1.1 Wind pressure p = f V k2.c h.c s N/m2wheref = 0.611Vk = 100 knots = 51.44 m/sc s = 1.0c h = 1.1hence p = 1778.4 N/m2or 37.13 lbf/ft21.2 Bulkhead platingPlate panel maximum size (mm)4070 by 690Plate thickness, t (mm)8Bulkhead load to wind pressure p = 1778.4 N/m2or 37.13 lbf/ft2Stress due to lateral perpendicular load:σ = kpb2/t2 wherek = 0.741 for panel size ratio of 5.9 (4070/690)p =37.13lbf/ft2, or0.26 lbf/in2b =690 mmt =8mmHenceσ =1421 lbf/in2, or 1.42ksi OK3Shear stress at support,τ = RF max/A web = 4.49N/mm2, or0.7ksi OK2. Bottom2.1. bottom platingPlate panel maximum size (mm)2650 by 830Plate thickness, t (mm)8Deck load to MODU 2001, w920 kgf/m2, or 188 lbf/ft2Stress due to lateral perpendicular load:σ = kwb2/t2 wherek = 0.718 for panel size ratio of 3.19 (2650/830)w =188lbf/ft2, or 1.31 lbf/in2b =830mmt =8mmHenceσ =10090 lbf/in2, or10.1ksi OK33. APV' lower Supporting StructureAs per contract specification 2.22G, foundations for equipment shall be designed for combined staticand dynamic load of 1.5g vertical and 0.5g horizontal for roll and pitch.According to HYDRALIFT Drawing: T2820-D1157-G0040 APV's arrangement,per WORKING APV' average weight: 2750kg,add 10% variables: 3025kg is to be used in following calculation.3.1 check supporting plate panelThe supporting plate panel, which is supported at four sides, is considered conservatively as plate beam supported at two longer edges.Plate panel concentrated load maximum size (mm)1420 by 760Plate thickness, t (mm) =25.5Deck load to MODU 2001, w =920kgf/m2, or 188 lbf/ft2Max moment due to deck load q: M q =qL/8 =925N.mwhere L =0.76mMax reaction force due to deck loa R q=qL/2=4870NLoad Case 1 (LC1): Heave at 1.5gForce due to static and dynamic load:P = ma,wherem=3025kga=14.7m/s2 (1.5g)P=44467.5NHence,Q=2P = 88935NM1max=Ql1l2/L=16605N.mwhere L=0.76ml1=0.33ml2=0.43mR1max=Ql2/L=50318NForce due to pitch:P=ma,wherem=3025kga= 4.9m/s2 (0.5g)P pitch=14822.5NHence,Q2=2.755*P/5.76 = 7090NThe force acts on plate as a longitudinal tension, as illustrated in sketchLC3: Roll at 0.5g to starboardForce due to roll:P=ma,wherem=3025kga= 4.9m/s2 (0.5g)P=14822.5NHence,Q2=2.755*P/5.76 = 7090NThe force acts on plate as a transverse tension, as illustrated in sketchLC4: Heave at 1.5g, pitch at 0.5g to forward and roll at 0.5g to starboard (LC1+LC2+LC3)moment:BM max=M1max + Mq =17530N.mshear:RF max=R1max + Rq =55188Nlongitudinal tension:TF x =14179Ntransverse tension:TF y =14179Nplate beam modulus:SM=bt2/6 =154cm3where b =142cmt = 2.55cmplate beam area:A1 =bt =362cm2A2 =at =194cm2where a =76cmBending stress,σ = BM max/SM =113.91N/mm2, or16.5ksi OK Shear stress,τ = RF max/A1 = 1.52N/mm2, or0.2ksi OK Longitudinal tension stress:σx = TF x/A2 =0.73N/mm2, or0.1ksi OK Transverse tension stress:σy = TF y/A1 =0.39N/mm2, or0.1ksi OK3.2 Check supporting structurewhere L= 1.42mBM max = (q1+q2)L2/8 =1774kgf.mRFmax = (q1+q2)L/2 = 4997kgf3Bending stress ,σ = BM max/SM = 6.21N/mm2, or0.9ksi OK Shear stress ,τ = RF max/A1 = 6.81N/mm2, or 1.0ksi OKb. Beam A2-B2Similar to beam A1-B1, check beam A2-B2 stress is OK.R B2 =4964kgfc. Beam A3-B3Similar to beam A1-B1, check beam A3-B3 stress is OK.R B3 =2697kgfd. Beam A4-B4Similar to beam A1-B1, check beam A4-B4 stress is OK.R B4 =2482kgfe. Beam A5-B5Similar to beam A1-B1, check beam A5-B5 stress is OK.R B5 =4964kgff. Beam A6-B6Similar to beam A1-B1, check beam A6-B6 stress is OK.R B6 =4964kgfg. Beam A7-B7Similar to beam A1-B1, check beam A7-B7 stress is OK.R B7 =4964kgfh. Beam A8-B8Similar to beam A1-B1, check beam A8-B8 stress is OK.R B8 =4964kgfi. Beam A9-B9Similar to beam A1-B1, check beam A4-B4 stress is OK.R B9 =2482kgfj. Beam C1-D1Similar to beam A1-B1, check beam C1-D1 stress is OK.R C1 =4989kgfR D1 =4989kgfk. Beam C2-D2Similar to beam A1-B1, check beam C2-D2 stress is OK.R C2 =4957kgfR D2 =4957kgfl. Beam C3-D3Similar to beam A1-B1, check beam C2-D2 stress is OK.R C3 =2690kgfR D3 =2690kgf3.2.2 Check transverse girdersMax moment due to force R B1: M B1 = 0.76*1.985*R B1/2.745 =2746kgf.mMax moment due to force R B2: M B2 = 1.42*1.325*R B2/2.745 =3402kgf.mMax moment due to force R B3: M B3 = 2.08*0.665*R B3/2.745 =1359kgf.m Combined moment: BM max =6163kgf.mReaction force: R E1 = 1.985*R B1/2.745 + 1.325*R B2/2.745 + 0.665*R B3/2.745 =6663kgf Reaction force: R F1a = 0.76*R B1/2.745 + 1.42*R B2/2.745 + 2.08*R B3/2.745 =5995kgf hence,RF max =6663kgfBending stress ,σ = BM max/SM =24.00N/mm2, or 3.5ksi OK Shear stress ,τ = RF max/A WEB =8.17N/mm2, or 1.2ksi OKn. Beam E2-F2Similar to beam E1-E1, check beam E2-F2 stress is OK.Reaction force: R F2 =5984kgfDistributed load along the beam length due to bulkhead weight, q = 660kgf/mMax moment due to load q: M q =qL2/8 =622kgf.mMax moment due to force R D1: M D1 = 0.76*1.985*R D1/2.745 =2742kgf.mMax moment due to force R D2: M D2 = 1.42*1.325*R D2/2.745 =3398kgf.mMax moment due to force R D3: M D3 = 2.08*0.665*R D3/2.745 =1355kgf.mCombined moment: BM max =6774kgf.mReaction force: R E3 =7558kgfReaction force: R F3a =6890kgfhence,RF max =7558kgfBending stress ,σ = BM max/SM =26.38N/mm2, or 3.8ksi OK Shear stress ,τ = RF max/A WEB =9.27N/mm2, or 1.3ksi OKDeck load to MODU 2001, w = 920kgf/m2 or 188 lbf/ft2Distributed load along the beam length, q = 0.165*w =151.8kgf/mMax moment due to load q: M q =q*1.4452*(1+1.3/2.745)2/8 =86kgf.mMax moment due to force R B4: M B4 = 1.445*1.3*R B4/2.745 =1699kgf.mMax moment due to force R B5: M B5 = 2.105*0.64*R B5/2.745 =3402kgf.mCombined moment: BM max =4259kgf.mReaction force: R F1b =2424kgfReaction force: R =5146kgfthk(cm)width(cm)sectionarea(cm2)ctr.dist. toplt top(cm)d(cm)I0 (cm4)mom. ofinert.(cm4)SM(cm3)top flg 2.5516.542.075 1.27522.844135.0web1808042.5542666.748997.3btm flg0.816.513.282.950.732077.6 Combined135.27533.7125210.02520 Bending stress ,σ = BM max/SM =16.58N/mm2, or 2.4ksi OK Shear stress ,τ = RF max/A WEB = 6.31N/mm2, or0.9ksi OKDeck load to MODU 2001, w = 920kgf/m2 or 188 lbf/ft2Distributed load along the beam length, q1 = 0.165*w =151.8kgf/mDistributed load along the beam length due to bulkhead weight, q2 = 660kgf/m BM max = (q1+q2)L2/8 =765kgf.mRFmax = (q1+q2)L/2 = 1114kgfHence,R =1114kgfBending stress ,σ = BM max/SM = 2.98N/mm2, or0.4ksi OK Shear stress ,τ = RF max/A WEB = 1.37N/mm2, or0.2ksi OKr. Beam E5-F5Similar to beam F3-E5, check beam E5-F5 stress is OK.Reaction force: R E5b =1185kgfR F5 =1185kgfDeck load to MODU 2001, w = 920kgf/m2 or 188 lbf/ft2Distributed load along the beam length, q = 0.165*w =151.8kgf/mMax moment due to load q: M q =q*0.832*(1+2.66/3.49)2/8 =41kgf.mMax moment due to force R B6: M B6 = 0.68*2.81*R B6/3.49 =2718kgf.mMax moment due to force R B7: M B7 = 1.34*2.15*R B7/3.49 =4098kgf.mMax moment due to force R B8: M B8 = 2.0*1.49*R B8/3.49 =4239kgf.mMax moment due to force R B9: M B9 = 2.66*0.83*R B9/3.49 =1570kgf.mCombined moment: BM max =9829kgf.mReaction force: R E4b =9779kgfBending stress ,σ = BM max/SM =38.27N/mm2, or 5.6ksi OK Shear stress ,τ = RF max/A WEB =11.99N/mm2, or 1.7ksi OK3.2.3 Check longitudinal girdersDeck load to MODU 2001, w = 920kgf/m2 or 188 lbf/ft2Distributed load along the beam length, q = 0.3*w =276kgf/mMax moment due to load q: M q =q*3.5882/2 =1777kgf.mMax moment due to force R F1a +R F1b: M F1 = 0.938*(R F1a+R F1b) =7897kgf.mMax moment due to force R F2: M F2 = 2.193*R F2 =13123kgf.mMax moment due to force R F3a +R F3b: M F1 = 3.588*(R F3a+R F3b) =29041kgf.mCombined moment: BM max =51838kgf.mReaction force: R G1 = q*3.588 + RF1a + RF1b + RF2 + RF3a + RF3b=23397kgfBending stress ,σ = BM max/SM =167.46N/mm2, or24.3ksi OK Shear stress , 1.2τ = RF max/A WEB =65.58N/mm2, or9.5ksi OKDeck load to MODU 2001, w = 920kgf/m2 or 188 lbf/ft2Distributed load along the beam length, q1 = 0.3*w =276kgf/mLoad as Heave at 1.5gForce due to static and dynamic load:P = ma,wherem=3025kga=14.7m/s2 (1.5g)P=44468NHence,q2=2P/L = 6384kgf/mwhere L= 1.42mMax moment due to load q1: M q1 =q1*4.072/2 =2286kgf.mMax moment due to load q2: M q2 =q2*1.422/2 =6437kgf.mMax moment due to force R E4a +R E4b: M E4 = 1.42*(R E4a+R E4b) =21194kgf.mMax moment due to force R E5a +R E5b: M E4 = 4.07*(R E5a+R E5b) =9357kgf.mCombined moment: BM max =39273kgf.mReaction force: R G2 = q1*4.07 +q2*1.42 + R E4a + R E4b + R E5a + R E5b=27413kgf hence,RF =27413kgfBending stress ,σ = BM max/SM =65.74N/mm2, or9.5ksi OK Shear stress ,τ = RF max/A WEB =26.89N/mm2, or 3.9ksi OKv. Beam G3-F5Deck load to MODU 2001, w = 920kgf/m or 188 lbf/ft2Distributed load along the beam length, q1 = 0.165*w =151.8kgf/mDistributed load along the beam length due to bulkhead weight, q2 = 660kgf/m Max moment due to load q1: M q1 =q1*4.072/2 =1257kgf.mMax moment due to load q2: M q2 =q2*4.072/2 =5466kgf.mMax moment due to force R F4: M F4 = 1.42*R F4 =10964kgf.mMax moment due to force R F5: M F5 = 4.07*R F5 =4823kgf.mCombined moment: BM max =22510kgf.mBending stress ,σ = BM max/SM =62.18N/mm2, or9.0ksi OK Shear stress ,τ = RF max/A WEB =11.26N/mm2, or 1.6ksi OK4. APV' Upper Supporting Structure3.1 :P pitch =14822.5NQ1pitch =7733N Load due to a APV's Roll at 0.5g to starboard has calculated as 3.1 :P roll =14822.5NQ1roll =7733N 4.1 Check APV' end box mounting structure on forward transverse bulkhead4.1.1 Check stiffener' flange subjected to tensionAs per "Yield Line Analysis of Bolted Hanging Connections", AISC, Engineering Journal, Vol.14, No.3 1977, For hanger rods, the allowable working load is the smaller of following :P1 = F y t b2(2r)1/2(1+a/b)/LFP2 = F y t b2[r(1+a/b)]1/2/LFwhere F y=235N/mm2t b=13mmr= (F y-F b)/F y =0.401F b=140.7N/mm2a=50mmb=35.5mmLF = 1.7P1 =50388NP2 =22959Nhence,the allowable total force carried by flange[ P ]=22959Nmaximal load forced on stiffener L100x75x13 is P max = 1.5Q1roll = 11600 N < [ P ]OK!4.1.2 Check stiffener subjected to compressionR max =8522N9thk(cm)plt width/sect dep(cm)sectionarea(cm2)ctr.dist. toplt top(cm)d(cm)I0 (cm4)mom. ofinert.(cm4)SM(cm3)att plt0.85644.80.4 2.493.9section-7.515.46 5.9794.6359.7Combined60.26 1.8453.6704.3in3 Bending stress ,σ = BM max/SM =23.83N/mm2, or 3.5ksi OKR max=R F =8738Nthk(cm)plt width/sect dep(cm)sectionarea(cm2)ctr.dist. toplt top(cm)d(cm)I0 (cm4)mom. ofinert.(cm4)SM(cm3)att plt 1.2519.2240.625 3.1196.0section-7.521.06 6.6994.6314.4Combined45.06 3.5510.3965.9in3Bending stress ,σ = BM max/SM =22.61N/mm2, or 3.3ksi OK Shear stress ,τ = RF max/A1 = 4.15N/mm2, or0.6ksi OKC. Check beam L-MR max =11934Nthk(cm)width(cm)sectionarea(cm2)ctr.dist. toplt top(cm)d(cm)I0 (cm4)mom. ofinert.(cm4)SM(cm3)top flg00000.00.0web0.9 2.5 2.25 1.25 1.2 4.8btm flg0.97.5 6.75 2.950.5 1.7Combined9 2.5 6.530.2in3 Bending stress ,σ = BM max/SM =4145.20N/mm2, or601.6ksi OK Shear stress ,τ = RF max/A1 =53.04N/mm2, or7.7ksi OK4.2 Check APV' end box mounting structure on inboard longitudinal bulkheadAs per "Yield Line Analysis of Bolted Hanging Connections", AISC, Engineering Journal, Vol.14, No.3, 1977, For hanger rods, the allowable working load is the smaller of following :P1 = F y t b2(2r)1/2(1+a/b)/LFP2 = F y t b2[r(1+a/b)]1/2/LFwhere F y=235N/mm2t b=19mmr= (F y-F b)/F y =0.401F b=140.7N/mm2a=50mmb=35.5mmLF = 1.7hence,P1 =107634NP2 =49042Nhence,the allowable total force carried by flange[ P ]=49042Nmaximal concentrated load forced on girder T 811x12.5w P max = 3Q2roll = 23199 N < [ P ]OK!4.2.2 Check longitudinal girder' web stability under compression when roll to starboardAs per "Manual of STEEL CONSTRUCTION Allowable Stress Design", AISC,Slenderness ratio Kl/r =450> 200where K =2l =811mmr = 3.61mmAnd C c =(2*3.142E/F y)1/2 =130where E =200000MpaF y =235N/mm2here,Kl/r >C chence,the allowable stress F a = 12*3.142E/(23*(Kl/r)2 = 5.08N/mm2Compression total load forced on Girder' web section Q =12*Q2roll92796N web section area A=19625mm2RF max =92796Nthk(cm)width(cm)sectionarea(cm2)ctr.dist. toplt top(cm)d(cm)I0 (cm4)mom. ofinert.(cm4)SM(cm3)top flg 2.5547.3120.615 1.27565.474578.2web 1.2581.1101.37543.155563.784757.5btm flg 1.911.521.8584.6 6.674705.9Combined243.8426.1234041.73939240.4in3 Bending stress ,σ = BM max/SM =17.91N/mm2, or 2.6ksi OK Shear stress ,τ = RF max/A web =9.15N/mm2, or 1.3ksi OK4.3 Check supporting APV' end box mounting structure on TF-12 transverse bulkheadBending stress ,σ = BM max/SM =72.79N/mm2, or10.6ksi OK Shear stress ,τ = RF max/A web =17.26N/mm2, or 2.5ksi OKthk(cm)width(cm)sectionarea(cm2)ctr.dist. toplt top(cm)d(cm)I0 (cm4)mom. ofinert.(cm4)SM(cm3)top flg 1.310130.65 1.8871.8web 1.3 6.28.06 4.425.8184.0btm flg 1.957.5109.258.4532.948.7web 1.2581013.453.3262.1top flg 1.25121518.025 2.01270.1Combined155.318.8302636.726916.4in3Bending stress ,σ = BM max/SM =74.44N/mm2, or10.8ksi OK Shear stress ,τ = RF max/A web =17.26N/mm2, or 2.5ksi OK。
型材剖面设计

00
0.00 0.00 -0.16 -1.26
腹板1) 0.4 0.2 8.8
0.11 0.968 0.11 0.00 -0.05 -4.26
大翼板 40 0 17
0.22 3.74 0.82 0.00 0.06 3.05
∑1)
30.2
4.708
0.93
Δ= 0.1559 I= 0.20
构 件 及 剖面尺寸 剖 面 积 至参考 静矩 惯性矩 自身惯性 至中和轴 Wi
比面积: 1.剖面模数比面积 2.剖面惯性矩比面积 意义:产生单位剖面模数所需的剖面积.
船舶总体设计
二、型材的强度要求及剖面要素计算
为保证型材有足够 强度,必须使翼板的最大正 应力和腹板上的最大剪应力小于许用应力,即
M
W1
及
NS
ItΒιβλιοθήκη 则首先要建立型材剖面要素与剖面几何尺寸之间 的关系式。
对中和轴的惯性矩:ICA2eCeB#DIV/0!
Δ= ###### I= #DIV/0!
剖面模数:
W1构号件及编 剖(ecIm1面2) ,积 至距参考离
I W 静(矩cm2.2m 惯(性cm矩2m 自矩h身惯性 至距中e和1轴离
Wi
船舶总体设计
如图例4.2.1所示任意两构件的形心分别为a1和a2, 其距离为D,已知各构件的面积分别为A1和A2,对各自 形心轴的惯性矩分别为I1和I2,求该组合剖面对其形 心轴的惯性矩I。
习 题 4 . 2 . 9
船舶总体设计
解:选取小翼板的中和轴为参考轴,则有 1)大翼板剖面积增加1cm2时,则有
构件 编号
及
剖面尺寸
剖面 (cm2)
积
至参考 距离
常用型材参数及计算

常用型材参数及计算常用型材是指在建筑和制造领域中经常使用的各种形状的金属材料,如铝型材、钢管、钢板等。
这些材料通常具有高强度、耐腐蚀、耐磨损和良好的加工性能,广泛应用于建筑、交通运输、机械制造、电子电气、航空航天等领域。
以下是常见的铝型材的参数和计算方法。
1.型材截面尺寸参数(1)尺寸名称:型材截面的尺寸通常由宽度、高度和厚度等参数来描述。
(2)截面形状:常见的截面形状有矩形、方形、圆形、椭圆形、T形、I形等。
(3)面积:型材截面的面积是指截面内的面积。
2.截面惯性矩和截面模量(1) 惯性矩:型材截面的惯性矩是描述截面抵抗弯曲变形能力的重要参数,通常用I表示,单位为mm^4,计算方法为根据截面形状确定相应的公式计算。
(2) 截面模量:型材截面的截面模量是描述截面抵抗拉伸和压缩变形能力的重要参数,通常用W表示,单位为mm^3,计算方法为根据截面形状确定相应的公式计算。
3.弯曲应力和弯曲刚度(1)弯曲应力:在受到弯曲荷载时,型材截面的不同部位会承受不同大小的应力,通过计算得到的弯曲应力可以判断材料的强度是否满足要求。
(2)弯曲刚度:型材截面的弯曲刚度是描述截面抵抗弯曲变形能力的一种参数,可以通过计算得到。
4.抗弯强度和剪切强度(1)抗弯强度:型材的抗弯强度是指在弯曲作用下,截面的最大抵抗能力。
抗弯强度的计算可以通过弯曲应力和截面惯性矩来求解。
(2)剪切强度:型材的剪切强度是指在剪切作用下,截面的最大抵抗能力。
剪切强度的计算可以通过剪切应力和截面模量来求解。
5.设计方法和计算举例(1)设计方法:设计一般遵循强度、刚度和稳定性原则,通过选择合适的材料和类型来满足工程需求。
(2) 计算举例:以铝型材为例,假设型材为矩形截面,宽度为100mm,高度为50mm,厚度为5mm。
根据公式计算出截面面积、惯性矩和模量。
假设受到弯曲荷载后,型材的应力为100MPa,根据公式计算出型材的抗弯强度。
通过以上的参数和计算方法,可以对常用型材进行合理的选择和设计,以满足不同工程需求的强度和刚度要求。
钢结构局部强度计算

钢结构局部强度计算之欧侯瑞魂创作目录绪论41 强度的分类42 载荷的分类43 构件变形的分类54 许用应力与平安因数5第一章杆件的强度和稳定性计算71.1 型材剖面要素的计算71.1.2 型材剖面模数与惯性矩的计算71.2.1 危险点的位置91.2.2 强度设计91.3 压杆的稳定性计算101.3.3 压杆的稳定性计算121.4 杆件抗弯强度计算13第二章板的强度计算162.1 板的分类162.2 刚性板的应力计算16第三章区域详细设计193.1 外板设计193.1.1 船底板193.4.1 尺度间距sb303.4.2 横骨架式舷侧骨架设计30附录一经常使用型材规格表35表1 球扁钢35表2 不等边角钢36表3 不等边不等厚角钢39表4 管形钢质支柱41表5瑞典(INEXA)公司球扁钢43表6 挪威(FUNDIA)公司球扁钢45附录二肘板尺寸47表7 肘板尺寸47附录三参考文献48绪论船体结构设计内容是:选择合适的结构资料和结构形式,决定结构的尺寸和连接方式;在包管结构具有足够强度和平安性的前提下,使其具有最佳的技术经济性和美观性.影响船体结构强度(结构平安性)的因素主要有两方面:载荷效应和资料性能.长期以来,结构的平安性衡量尺度都普遍采取确定性的许用应力法.该法以预先规定的某一计算载荷为基础,利用结构剖面中的计算应力σ与许用应力[σ]相比较来检验强度是否足够.船体结构强度,按作用范围可分为:总强度、区域强度(甲板强度、舱壁强度、底板强度等)和局部强度.船体结构强度,按作用形式可分为:纵向强度、横向强度和扭转强度.1. 作用在船体结构上的载荷,按其对结构的影响可分为:总体性载荷和局部性载荷.a) 总体性载荷:是指引起整个船体变形或破坏的载荷和载荷效应.例如:总纵弯曲的力矩,剪力,应力及纵向扭矩b) 局部性载荷:是指引起局部结构,构件的变或破坏的载荷.例如:水密试验的压力,设备不服衡造成的惯性力,局部振动等.另外,货物,油,水等重力及舷外水压(静水或海浪)既能引起引起局部结构和构件的变形或破坏,又能引起总纵弯曲,扭转甚至船的断裂.2. 作用在船体结构上的载荷,按载荷随时间变更的性质可分为:不变载荷,静变载荷,动变载荷和冲击载荷.a) 不变载荷:是指在作用时间内不改变其大小的载荷.例如:静水载荷(包含静水压力,货物压力,静水弯矩等),水密试验时的水压等.b) 静变载荷:是指载荷在作用时间内有变更,但其变更的最小周期超出该受力结构的固有震动周期若干倍,又称准静态载荷.例如:海浪载荷,液体货物的晃动压力,航行中的甲板上浪等.c) 动变载荷:是指在作用时间内的变更周期与所研究的结构响应的固有振动周期同阶.例如:螺旋桨引起的脉动压力,局部结构的强迫(机械)震动等.d) 冲击载荷:是指在非常短的时间内突然作用的载荷.例如船底砰击(见图).当构件的承载能力不克不及满足载荷对其发生的应力时,该构件的存在形式会发生变更.一般情况下可以分为:屈服和断裂.屈服分为压缩、拉伸和扭转变形.许用应力是由资料自己决定的.比方说钢的密度7.85(g/cm3),抗拉强度b σ×102GPa.极限应力:资料丧失正常工作能力时的应力jx σs σ.脆性资料的极限应力为其抗拉(压)强度b σ.许用应力:为包管构建平安工作,需有足够的平安储备,因此把极限应力除以大于1的平安因数n 作为资料的许用应力,记作[]σ,即[]σ=n jxσ对于塑性资料:[]σ=s s n σ;对于脆性资料:[]σ=b bln σ.式中n s 为屈服平安因数,n bs =1.2~1.5;n b =2.0~2.3. 许用切应力:脆性资料[]τ=(0.8~1.0)[]σ韧性资料[]τ=(0.5~0.8)[]σ第一章 杆件的强度和稳定性计算 1.1 型材剖面要素的计算船体结构中大多数骨架都是焊接在钢板上的,当骨架受力发生变形时,与它连接的板也一起介入骨架抵抗变形。
【全版】项目六表格法确定型材剖面要素推荐PPT

2 1
4、带板处的剖面模数:
4、带板处的剖面模数:
4、带板处的剖面模数:
I W2 h e
任务1 设计船舶型材剖面
项目六 船舶型材剖面设计
复习与思考
参考轴选取的位置不同对结果是否有 影响?
任务1 设计船舶型材剖面
至参考轴距 (离cmZ)i
静矩fi﹒Zi (cm3)
fi
1 2 3 ┇
——
Σ
A
B
C
任务1 设计船舶型材剖面
项目六 船舶型材剖面设计
初始参考轴一般取在翼板的重心轴线处
确定型材剖面要素的表格法
B 确定型材剖面要素的表格法
123、、、剖对翼面中板中和处和轴的轴的剖至惯面翼性模板矩数的::距WI离:C eI e AA eCeB 项参4确确确 4任4确项确熟 项任构任确构表233任24项、 、 、 、 、 、 、 、目考定定定务定目定悉目务件务定件6务目-带带带对翼翼对带1六 轴 型 型 型1型 六 型 用六 1名 1型 名 1六板板板中板板应板选材材材 材材表 称材称型设设设设船处处处船船和处处计处船取剖剖剖 剖剖格 及剖及材计 计 计 计舶的的的舶舶轴的的算的舶的面面面 面面计 尺面尺剖船船船船型剖剖剖型型的剖剖公剖型位要要要 要要算 寸要寸面舶舶舶舶材面面面材材惯面面式面材置素素素 素素型 (素(要型型型型剖模模模剖剖性模模模剖不的的的 的的材 的素mm材材材材面数数数面面矩数数数面mm同表表表 表表要 表计剖剖剖剖设 : : : 设 设 : : : : 设))对格格格格格素格算面面面面计计计计结法法法 法法的 法表果方是法否有影响?
船舶技术设计
项目六 船舶型材剖面设计
6.1.3 表格法确定型材剖面要素 学习内容:
型材模具设计

一、模孔布置1.模具的外形尺寸①模具外形D挤压制品的最大外接圆直径D w是群定模具外径的一个主要参数。
也可以根据挤压筒内径D t来确定该挤压筒所允许的制品的外接圆直径D w,即:D w=(0.80~0.85)D t所以D w=(0.80~0.85)D t=(0.80~0.85)×200=160~170mm取D w=160mm对于较复杂的断面形状,包括薄壁或难挤压金属型材,模具外径的最小值可按以下经验公式确定:D min=(1.45~1.60)D w所以D min=(1.45~1.60)D w=(1.45~1.60)×160=232~256mm取D=250mm②模具厚度H模具厚度H应根据被挤压合金的变形抗力(即挤压力)的大小来考虑。
在保证模具组件(模具、模垫、垫环等)有足够的强度的条件下,模具的厚度应尽量减薄,规格应尽量减少。
但为了安装和调整方便,模具的厚度尺寸应尽可能系列化,便于管理和使用,一般模具的厚度按下述数值(单位:mm)选用:20,25,30,40,50,60,70,80,90,100,110在挤压机设计时,通常选取单位压力位1000MPa时的挤压筒D t作为基本参数来确定模具的厚度,其关系为:H=(0.12~0.22)D t所以H=(0.12~0.22)D t=0.12~0.22)×200=24~44mm取H=40mm2.模孔的合理配置单孔挤压时的模孔布置①具有两个以上对称轴的型材,型材的重心布置在模子中心②具有一个对称轴,如果断面壁厚差不大,应使型材的对称轴通过模子的一个坐标轴,使型材断面的重心位于另一个坐标轴上。
③对于非对称的型材和壁厚差别很大的型材,将型材重心相对模子中心偏移一定距离,且将金属不易流动的壁薄部位靠近模子中心,尽量使金属在变形时的单位静压力相等。
④壁厚差不太大,但断面较复杂的型材,将型材断面外接圆的圆心布置在模子中心。
对于挤压比很大,金属流动困难或流动很不均匀的某些型材,可采用平衡模孔或增加工艺余量的方法。