渐开线非标齿轮滚刀的正确选用
齿轮滚刀使用及检验标准

齿轮滚刀(直槽)使用及检验标准一、齿轮滚刀使用标准 1、滚刀的轴向窜刀滚刀使用过程中,除进行正确的安装、调整外,还应进行轴向窜动,以延长滚刀的使用寿命。
1.1滚刀的起始安装位置如图1-1 滚刀切削区域向齿轮端面的投影图,滚刀实际切削区域长度=切出长度(l 0)+切入部分(l )。
图1-1滚刀切削区域向齿轮端面的投影图切出长度l 0=0*cos tan 0*cos ha βαδ式中0ha ——滚刀的齿顶高; β——被切齿轮的螺旋角; 0α——滚刀刀齿的齿形角; δ——滚刀的安装角。
切入长度l =(2*11)*1cos ra h h δ式中1ra ——被切齿轮齿顶圆半径; 1h ——滚齿时的切入深度; δ——滚刀的安装角。
安装滚刀的初始位置时,应使展成中心位于距切入端端面为l 的位置上,检验计算展成中心与切出端端面距离不小于l 0。
1.2 轴向窜刀的方向滚刀的轴向窜刀,通常应在与被加工齿轮旋转方向相反的方向上进行,如图1-2轴向窜刀的方向。
图1-2 轴向窜刀的方向1.3 轴向窜刀的窜刀量直槽滚刀的窜刀量S 可用下式确定: S=*d*cos dnm c Z πγ式中n ——滚刀头数; m ——滚刀模数;Zd——滚刀圆周齿数;γ——滚刀螺旋升角;dc——(确定窜刀量大小的系数,为4、5、6、7、8、9等整数值)。
推荐轴向窜刀的窜刀量S等于滚刀的轴向齿距Px。
1.4轴向窜刀的时机滚刀轴向窜刀的时机推荐为后刀面磨损约为磨钝标准的25%~30%时,即进行窜刀(单工步未加工完除外)。
在不同的切削条件下,滚刀窜刀量和窜刀时间间隔的最佳数值还要根据实际磨损情况,试验分析后确定。
1.5轴向窜刀的方法我车间滚齿机的轴向窜刀需靠手动完成,基本方法有两种,推荐方法为方法一。
方法一:按照确定窜刀量的各种倍数值,制作垫刀垫圈,通过变换滚刀心轴上垫圈的厚度,使滚刀沿其轴线移动,以改变滚刀对被加工齿轮轴线的位置。
方法二:切削一定数量的齿轮后,将分齿挂轮脱开,并转动滚刀,以达到轴向窜刀的目的。
渐开线齿轮滚刀安全操作及保养规程

渐开线齿轮滚刀安全操作及保养规程渐开线齿轮滚刀是一种用于制造齿轮的工具,其使用需要严格遵守安全操作规程,以确保工作人员的安全和机器的正常运转。
以下是渐开线齿轮滚刀的安全操作及保养规程:一、安全操作规程1.1 备戴个人防护装备使用渐开线齿轮滚刀时,必须备戴个人防护装备。
该装备包括头盔、护目镜、手套、防尘口罩等。
1.2 遵守操作规程使用该设备的人员必须接受专业培训,了解设备的使用方法、注意事项和规章制度。
同时,必须遵守操作规程,不得进行超出设备规定范围的操作。
1.3 安全距离在设备运作时,不允许在设备附近站立或者行动,操作人员必须和机器保持安全距离。
1.4 设备维护定期对渐开线齿轮滚刀进行清洁和保养。
定期检查设备的状态,并使用符合规定的润滑剂进行润滑。
1.5 切勿用手接触齿轮滚刀在设备工作期间,切勿用手接触滚刀或者齿轮。
工作完毕后,必须确认滚刀已经停止转动,才能进入设备操作区域。
二、保养规程2.1 清洁设备要始终保持设备的清洁。
使用设备后,应该用干的布或者刷子清理设备,确保没有残留物质。
2.2 润滑设备渐开线齿轮滚刀必须使用符合规定的润滑剂进行润滑。
机器维护人员必须在设备的特定区域添加润滑剂。
2.3 定期检查设备定期检查设备的状态,必须检查设备是否损坏、松动或脱落。
如发现问题,必须立即采取措施进行修复。
2.4 定期更换磨损部分渐开线齿轮滚刀在使用一定时间后,其零部件和制造配件会出现磨损。
机器维护人员必须在定期检查后更换有磨损的部分,以保证设备的正常运行。
2.5 保护设备保护设备不受到外部因素的影响。
防止接触潮湿、灰尘或其他污染物的材料。
在非使用时间内,应该将设备保持在干燥,洁净的地方。
三、小结渐开线齿轮滚刀的安全操作和正确保养,是确保设备正常运转和人员安全的关键所在。
良好的维护保护和正确的操作方式,可以延长设备使用寿命,减少事故发生的概率,保证人员的安全,提高工作效率。
在设备使用前必须对机器进行详细了解,遵守操作流程和安全规定,尽可能地保护自己和他人的安全。
渐开线圆柱齿轮的传动精度及选用

fi″采用双啮仪测量。fi″反映齿轮的短周期径向误差,由于仪器
结构简单,操作方便,所以在成批生产中广泛使用。
3)齿廓总偏差Fα 在计值范围Lα 内,包容实际齿廓迹线的两条设计齿廓迹线间的距
离,即在图7-7中过齿廓迹线最高、最低点作设计齿廓迹线的两条平行
直线间距离为Fα 。用渐开线检查仪测量。
项目7 渐开线圆柱齿轮的传动精度及选用
齿廓形 状偏差
齿廓倾斜 偏差
实际齿廓迹线
图7-7 渐开线齿廓偏差展开图
形状偏差ffα
在计值范围内,包容实际齿廓迹线的两条与平均齿廓迹线完全相同 的曲线间的距离,且两条曲线与平均齿廓迹线的距离为常数。
滚齿加工示意图
项目7 渐开线圆柱齿轮的传动精度及选用
齿轮传动的四项基本要求及影响因素
齿轮传动的 影响使用要求的误差(或因素) 使用要求
传递运动的 准确性
长周期误差:包括几何偏心和运动偏心分别引起的径向和切向 长周期(一转)误差。两种偏心同时存在,可能叠加,也可能 抵消。这类误差用齿轮上的长周期偏差作为评定指标
与测量齿轮接触,并转过一整圈时出现的中心距最大值和最小值之差。
Fi″的测量用双面啮合综合检查仪(简称双啮仪)进行。如图所
示。
用双啮仪测径向综合偏差
项目7 渐开线圆柱齿轮的传动精度及选用
5)公法线长度变动量Fw Fw是指在齿轮转一周范围内,实际公法线长度最大值与最小值之差,
如图所示。
公法线长度变动量及测量
项目7 渐开线圆柱齿轮的传动精度及选用
知识点1.渐开线圆柱齿轮传动的基本要求
1.传递运动的准确性 要求齿轮在一转范围内,实际速比相对于理论速比的变动量应限
渐开线花键滚刀标准

渐开线花键滚刀标准渐开线花键滚刀是一种常用于机械加工的切削工具,它的标准制定对于保证加工质量和效率具有重要意义。
本文将就渐开线花键滚刀标准进行详细介绍,包括其定义、特点、标准制定的重要性以及相关注意事项。
渐开线花键滚刀是一种用于加工渐开线花键的刀具,其特点是在刀具的刀片上具有特殊的渐开线花键形状,可以实现高效、精确的加工。
在实际生产中,渐开线花键滚刀的标准制定对于保证加工质量和效率具有重要意义。
首先,渐开线花键滚刀的标准制定可以保证加工的精度和一致性。
通过制定标准,可以规范刀具的尺寸、形状、材质等参数,确保每把刀具都符合统一的标准要求,从而保证加工出的零件具有一致的尺寸和形状。
其次,标准化的渐开线花键滚刀可以提高生产效率。
具有统一标准的刀具可以更好地配合加工设备,减少调试时间,提高生产效率。
此外,标准化的刀具还可以降低加工过程中的故障率,减少停机维护时间,进一步提高生产效率。
标准制定对于渐开线花键滚刀的使用和维护也具有重要意义。
通过制定标准化的使用和维护流程,可以确保刀具在使用过程中能够发挥最佳效果,延长使用寿命,降低生产成本。
在使用渐开线花键滚刀时,还需要注意以下几点:首先,要选择适合加工材料和加工工艺的渐开线花键滚刀。
不同的材料和工艺需要选择不同的刀具,以保证加工质量和效率。
其次,要严格按照标准化的使用和维护流程进行操作。
在使用过程中要注意及时清洁、润滑和更换刀具,避免因刀具损坏导致的加工质量下降和生产效率降低。
最后,要定期检查渐开线花键滚刀的使用状况,及时发现问题并进行处理。
定期的检查和维护可以保证刀具的良好状态,延长使用寿命,降低生产成本。
总之,渐开线花键滚刀标准的制定对于保证加工质量和效率具有重要意义。
标准化的刀具可以保证加工精度和一致性,提高生产效率,同时也便于使用和维护。
在实际生产中,我们应该严格遵守标准要求,合理选择、正确使用和定期维护渐开线花键滚刀,以确保加工质量和提高生产效率。
渐开线齿轮变位系数选择的新方法
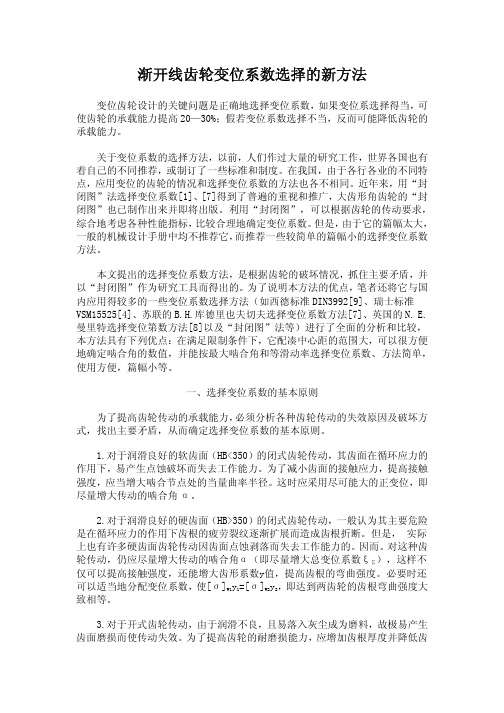
曲线),在该曲线上选取位变系数时,齿轮的最大滑动率是相等的。
从公式(10)还可以看出,η'=η"曲线的基本斜率主要取决于齿数比u的大 小,当然,曲线的具体形状还与齿数Z2、Z1有关。
图 8 为Z1=17,而Z2不同(即u不同)时的η'=η"曲线。可以看出,各曲线的
图2
在图 3 中,曲线组Ⅱ中的每一条曲线即为Z1一定时(如Z1=12,13,……等), 对于不同的Z2所得到的ξ∑B──Z∑变化曲线。而曲线组Ⅰ为ε=1 的曲线与 η'=η"曲线的交点所得的总变位系数ξ∑──Z∑曲线。
图3
从图 3 中可以看出,当小齿轮数Z1一定时,ξ∑B随Z∑的增加而增加,而当Z∑ 一定时,随小齿轮齿数Z1的增大,ξ∑B也不断增大。
渐开线齿轮变位系数选择的新方法
变位齿轮设计的关键问题是正确地选择变位系数,如果变位系选择得当,可 使齿轮的承载能力提高 20—30%;假若变位系数选择不当,反而可能降低齿轮的 承载能力。
关于变位系数的选择方法,以前,人们作过大量的研究工作,世界各国也有 着自己的不同推荐,或制订了一些标准和制度。在我国,由于各行各业的不同特 点,应用变位的齿轮的情况和选择变位系数的方法也各不相同。近年来,用“封 闭图”法选择变位系数[1]、[7]得到了普遍的重视和推广,大齿形角齿轮的“封 闭图”也已制作出来并即将出版。利用“封闭图”,可以根据齿轮的传动要求, 综合地考虑各种性能指标,比较合理地确定变位系数。但是,由于它的篇幅太大, 一般的机械设计手册中均不推荐它,而推荐一些较简单的篇幅小的选择变位系数 方法。
渐开线花键齿轮刀具

齿轮刀具GB/T10095.1、GB/T10095.2《渐开线圆柱齿轮精度》的齿轮。
2.特点及精度:滚刀技术条件按GB/T6084—2001,结构按GB/T6083—2001生产,并作成单头、右旋或左旋,轴向直沟,零度前角。
分为两种基本型式:Ⅰ型为加大直径、长度型,用于AA级滚刀;Ⅱ型为正常直径,长度型,用于AA、A、B、C级四种精度的滚刀。
3.刀具标记及示例订货时注明:名称、产品编号、模数、精度等级、旋向(右旋不注明)、标准号。
例:齿轮滚刀 25100—166 m2 A GB/T6084—20014.规格及主要尺寸参数表1 齿轮刀具(Ⅰ型、AA级) mm表2 齿轮刀具(Ⅱ型AA、A、B、C 级) mm齿轮滚刀 JB2495—781.用途:齿轮滚刀用于加工齿形符合GB1356—78《渐开线圆柱齿轮基准齿形》的齿轮。
2.特点及精度:滚刀结构为单头、右旋或左旋,轴向直沟,零度前角。
滚刀分为AA、A、B、C 级四种精度等级。
3.刀具标记及示例订货时注明:名称、产品编号、模数、精度等级、旋向(右旋不注明)、标准号。
例:齿轮滚刀 25110—044 m2 A 左 JB2495—784.规格及主要尺寸参数表1 齿轮滚刀(A、B、C级) mm表2 齿轮刀具(AA级)mm齿轮滚刀(企业标准)1.用途:齿轮滚刀用于加工齿形符合GB1356—78《渐开线圆柱齿轮基准齿形》的齿轮。
2.特点及精度:滚刀结构为单头、右旋,轴向直沟,零度前角。
滚刀分为AA、A、B、C四种精度等级。
与按GB/T6084制造的滚刀相比,工厂标准滚刀AA级接近GB/T6084的A级;A级基本相当于GB/T6084的B级;B、C级接近GB/T6084的C级。
3.刀具标记及示例订货时注明:名称、产品编号、模数、精度等级。
例:齿轮滚刀 25100—190 m2 A4.规格及主要尺寸参数齿轮滚刀(径节制)企业标准1.用途:齿轮滚刀(径节制)用于加工齿形角为14°30′,齿高系数f=1,径向间隙系数cˊ=0.157的渐开线圆柱齿轮。
机械制造与自动化《5.3齿轮滚刀选用教案》
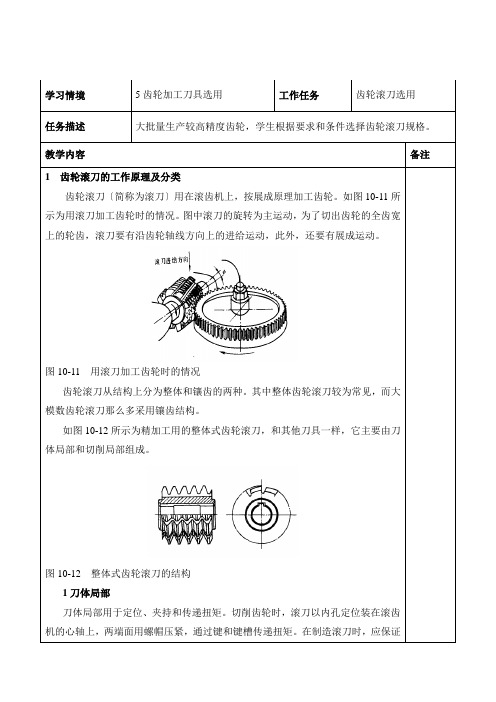
学习情境5齿轮加工刀具选用工作任务齿轮滚刀选用任务描述大批量生产较高精度齿轮,学生根据要求和条件选择齿轮滚刀规格。
教学内容备注1 齿轮滚刀的工作原理及分类齿轮滚刀〔简称为滚刀〕用在滚齿机上,按展成原理加工齿轮。
如图10-11所示为用滚刀加工齿轮时的情况。
图中滚刀的旋转为主运动,为了切出齿轮的全齿宽上的轮齿,滚刀要有沿齿轮轴线方向上的进给运动,此外,还要有展成运动。
图10-11 用滚刀加工齿轮时的情况齿轮滚刀从结构上分为整体和镶齿的两种。
其中整体齿轮滚刀较为常见,而大模数齿轮滚刀那么多采用镶齿结构。
如图10-12所示为精加工用的整体式齿轮滚刀,和其他刀具一样,它主要由刀体局部和切削局部组成。
图10-12 整体式齿轮滚刀的结构1刀体局部刀体局部用于定位、夹持和传递扭矩。
切削齿轮时,滚刀以内孔定位装在滚齿机的心轴上,两端面用螺帽压紧,通过键和键槽传递扭矩。
在制造滚刀时,应保证阿基米德滚刀多采用单头的。
粗加工阿基米德滚刀可以采用多头的。
和单头滚刀相比,多头滚刀可以提高生产率,但用多头滚刀加工时,将产生较大误差〔因其与渐开线滚刀有更大差异〕,并且齿轮每个齿的齿形是由较少的刀齿包络而成,因而齿面的粗糙度也较差。
3阿基米德滚刀的齿形阿基米德滚刀轴向齿形是直线。
标准规定在轴向测量齿形,所以工作图中应给出滚刀的轴向齿形图。
如图10-21所示为直槽阿基米德齿轮滚刀〔前角为零度〕的齿形图,即其前面的齿形。
图10-21 阿基米德齿轮滚刀的轴向齿形图10-21中的齿形角xo α可按下式计算 nx00tg tg cos ααλ= 〔10-4〕式中,0λ为阿基米德滚刀的螺旋升角〔°〕。
轴向齿距0x p 按下式计算 n0n 0x000πcos cos p m z p λλ== 〔10-5〕 式中,0z 为滚刀头数;0n p 为滚刀的法向齿距〔mm 〕。
阿基米德滚刀的齿厚可在法向测量,也可在轴向测量。
对于精加工滚刀,法向齿厚可按下式计算0n S =n 0n S p - 〔10-6〕式中,n S 为被加工齿轮的法向分度圆齿厚〔mm 〕。
齿轮工艺员必备的滚刀知识
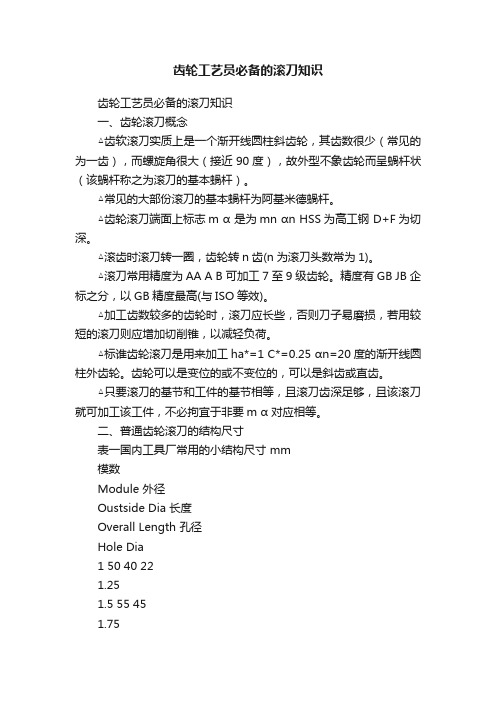
3.75 90 80
4
4.5 90
5 100 100
5.5 112 112 40
6
6.5 118 118
7 125
8 125 132
9 140 150
10 150 170 50
三、滚刀常用材料
1. 钨钢(硬质合金)
2、普通高速钢(M2)
3. 钴高速钢(M35 M42)(SKH55)
4. 粉末冶金高速钢:
板状的
10 DLC(a-C:H) 2500 0.10-0.20 350 黑灰色单层
11 TiAlN
氮铝化钛3300 0.25 -1.3/1.5 900 紫灰色纳米-结构
12 TiAlN
氮铝化钛3300 0.40 -3.0/-3.5 900 蓝灰色
纳米-结构
13 TiAlN
氮铝化钛3500 0.40 -4.0 800 紫灰色单层
6 多晶体金刚石8000-
10000 0.15-0.20 600 浅灰色单层
7 TiAlN
氮铝化钛3300 0.30-0.35 -1.3/-1.5 900 紫灰色纳米-结构
8 TiCN+TiN
碳氮化钛+氮化钛3000 0.40 -4.0 400 金黄色多层,倾斜的
9 TiAlN+ WC/C
氮铝化钛+碳化钨/碳3000 0.15-0.20 -1.7/-2.0 800 深灰色多层的,薄
*依赖于应用于测试条件
五、刀具在使用前后及镀层前后的速度关系表(以一般碳钢为例)
刀具滚削转速m/min 刮削转速m/min
钨钢+镀层150-250 150-180
钨钢磨后不镀120-150 100-120
渐开线非标齿轮滚刀的正确选用

渐开线非标齿轮滚刀的正确选用目前,汽车、拖拉机等行业大量使用齿顶高系数ha*≠1,压力角an≠20°或模数mn为非标准值的渐开线非标齿轮。
为加工此类齿轮,需根据被切齿轮参数确定相应的滚刀参数,并从《复杂刀具订货图册》(以下简称《图册》)中选用正确的非标滚刀。
1 非标滚刀的选用步骤1.1 确定滚刀类型与精度滚刀类型与精度的选择应根据加工设备及工艺而定。
滚刀模数(或径节、周节)和压力角应与被切齿轮相目前,汽车、拖拉机等行业大量使用齿顶高系数h a*≠1,压力角αn≠20°或模数m n为非标准值的渐开线非标齿轮。
为加工此类齿轮,需根据被切齿轮参数确定相应的滚刀参数,并从《复杂刀具订货图册》(以下简称《图册》)中选用正确的非标滚刀。
1 非标滚刀的选用步骤1.1 确定滚刀类型与精度滚刀类型与精度的选择应根据加工设备及工艺而定。
滚刀模数(或径节、周节)和压力角应与被切齿轮相等,螺旋方向最好与被切齿轮相同,加工直齿齿轮时应优先选用右旋滚刀。
1.2 确定滚刀全齿高h对于非全切式滚刀,滚刀全齿高h的计算公式为h≥h1+c*m n+∆h (1)对于全切式滚刀,则有h=h1 (2)式中:h1——被加工齿轮全齿高c*——被加工齿轮顶隙系数mn——被加工齿轮法向模数△h——剃齿或磨齿时因工艺需要而设置的滚刀齿顶加长量,可参考表1选取:1.3 确定滚刀法向齿厚Sn、轴向齿厚Sx和齿顶高ha齿轮滚刀的轴向齿形如图1所示。
其中,Ⅰ型为正常齿形,Ⅱ型为修形齿形。
剃前齿轮滚刀的轴向齿形一般有五种类型(图略)。
剃前和磨前滚刀的齿形通常都有一定修形量。
图1滚刀齿厚和齿顶高有以下两种计算方法:1) 按通用滚刀设计方法的计算公式为S n=πm n/2-∆S'+∆S" (3)S x=S n/cosλ(4)h a=h f1+x n1m n+∆h (5)式中:∆S'——滚刀的加工余量(可参考表2 取值)注:E ss——被切齿轮齿厚极限上偏差∆S"——考虑被切齿轮齿厚偏差而附加的滚刀齿厚增量(可参考表2取值)λ——滚刀分度圆螺旋升角h f1——被切齿轮齿根高x n1——被切齿轮法向变位系数式(4)中滚刀分度圆螺旋升角λ的计算公式为sinλ=m n z[/d e-2h a-0.2(k+δd e)]≈m n z/(d e-2h a) (6)式中:z——滚刀头数de——滚刀齿顶圆直径k——滚刀径向铲背量δde——滚刀外径公差2) 按专用滚刀设计方法的计算公式为S n=e n1min=πm n/2-2x n1m n tanαn-∆S'+∆S" (7)S x=S n/cosλ(8)h a=h f1+∆h (9)式中:e n1min——被切齿轮工序法面齿间宽最小值1.4 确定滚刀修形与齿顶圆弧当被切齿轮无修形要求时,选择剃前或磨前滚刀时无需验算滚刀修形量,其它类型的滚刀则应选用非修形滚刀。
项目7渐开线圆柱齿轮的传动精度及选用知识点1渐开线
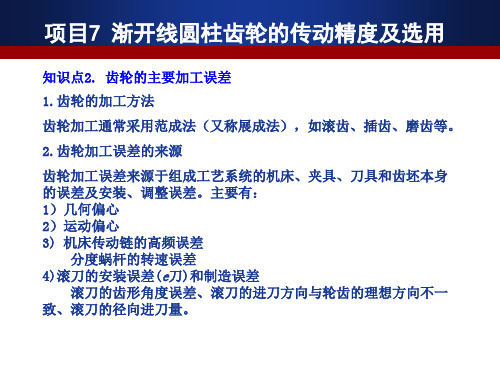
4)滚刀的安装误差(e刀)和制造误差
滚刀的齿形角度误差、滚刀的进刀方向与轮齿的理想方向不一 致、滚刀的径向进刀量。
项目7 渐开线圆柱齿轮的传动精度及选用
几何偏心e1 齿坯几何中心与机床心轴中心不重合,引起加工误差。 运动偏心e2 滚齿时,由于机床分度蜗 轮的偏心,使工作台带动 旋转的齿坯在一转范围内 时快时慢地旋转,导致加 工误差。
“基中心距制”,即在中心距一定的情况下,用控制轮齿的齿厚的方法 获得必要的侧隙。 1)齿侧间隙
2)齿距偏差:k个齿距累积偏差Fpk与齿距累积总偏差Fp Fpk 是指在端平面上,在接近齿高中部的一个与齿轮轴线同心的
圆上,任意k个齿距的实际弧长与理论弧长之差的代数差, 通常,取
k=z/8。齿距累积总偏差Fp指齿轮同侧齿面任意弧段内的最大齿距累积
偏差。齿距偏差反映了一个齿距和一转内任意个齿距的最大变化,它 直接反映齿轮的转角误差,是几何偏心和运动偏心的综合结果。
滚齿加工示意图
项目7 渐开线圆柱齿轮的传动精度及选用
齿轮传动的四项基本要求及影响因素
齿轮传动的 影响使用要求的误差(或因素) 使用要求
传递运动的 准确性
长周期误差:包括几何偏心和运动偏心分别引起的径向和切向 长周期(一转)误差。两种偏心同时存在,可能叠加,也可能 抵消。这类误差用齿轮上的长周期偏差作为评定指标
(360°/z)的径向综合偏差值。如图7-5(b)所示。
fi″采用双啮仪测量。fi″反映齿轮的短周期径向误差,由于仪器
结构简单,操作方便,所以在成批生产中广泛使用。
3)齿廓总偏差Fα 在计值范围Lα 内,包容实际齿廓迹线的两条设计齿廓迹线间的距
离,即在图7-7中过齿廓迹线最高、最低点作设计齿廓迹线的两条平行
齿轮加工中刀具的选择与使用

齿轮加工中刀具的选择与使用加工中心所用的刀具是由通用刀具(又称工作头或刀头)和与加工中心主轴前端锥孔配套的刀柄等组成。
在应用中,要根据加工中心机床的要求、夹具的要求、工件材料的性能、加工工序、切削用量以及其它相关因素正确选用刀具。
刀具选择总的原则是:刀具的安装和调整方便,刚性好,耐用度和精度高。
在保证安全和满足加工要求的前提下,刀具长度应尽可能短,以提高刀具的刚性。
加工中心机床上,各种刀具分别装在刀库中,按程序的规定进行自动换刀。
因此必须采用标准刀柄,以便使钻、镗、扩、铣削等工序用的刀具能迅速、准确地装到机床主轴上。
编程人员应充分了解机床上所用刀柄的结构尺寸、调整方法以及调整范围,以便在编程时确定刀具的径向和轴向尺寸。
加工中心机床所用的刀具必须适应加工中心高速、高效和自动化程度高的特点,其刀柄部分要联接通用刀具并装在机床主轴上,由于加工中心类型不同,其刀柄柄部的型式及尺寸不尽相同。
JT(ISO7388)表示加工中心机床用的锥柄柄部(带有机械手夹持槽),其后面的数字为相应的ISO锥度号,如50、45、和40分别代表大端直径为69.85、57.15和44.45毫米的7:24锥度。
ST(ISO297)表示一般数控机床用的锥柄柄部(没有机械手夹持槽),数字意义与JT类相同。
BT(MAS403)表示用于日本标准MAS403的带有机械手夹持槽联接。
加工中心刀具的刀柄分为整体式工具系统和模块式工具系统两大类。
模块式工具系统由于其定位精度高,装卸方便,连接刚性好,具有良好的抗振性,是目前用得较多的一种型式,它由刀柄、中间接杆以及工作头组成。
它具有单圆柱定心,径向销钉锁紧的联接特点,它的一部分为孔,而另一部分为轴,两者之间进行插入连接,构成一个刚性刀柄,一端和机床主轴连接,另一端安装上各种可转位刀具便构成一个工具系统。
根据加工中心类型,可以选择莫氏及公制锥柄。
中间接杆有等径和变径两类,根据不同的内外径及长度将刀柄和工作头模块相联接。
齿轮刀具的选用方法
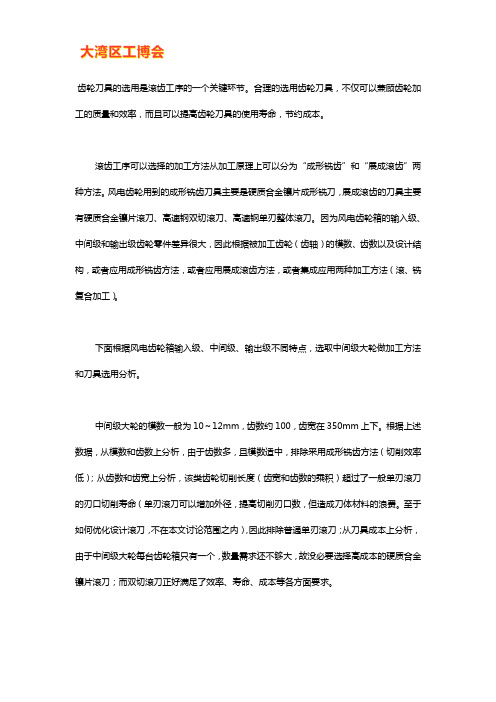
齿轮刀具的选用是滚齿工序的一个关键环节。
合理的选用齿轮刀具,不仅可以兼顾齿轮加工的质量和效率,而且可以提高齿轮刀具的使用寿命,节约成本。
滚齿工序可以选择的加工方法从加工原理上可以分为“成形铣齿”和“展成滚齿”两种方法。
风电齿轮用到的成形铣齿刀具主要是硬质合金镶片成形铣刀,展成滚齿的刀具主要有硬质合金镶片滚刀、高速钢双切滚刀、高速钢单刃整体滚刀。
因为风电齿轮箱的输入级、中间级和输出级齿轮零件差异很大,因此根据被加工齿轮(齿轴)的模数、齿数以及设计结构,或者应用成形铣齿方法,或者应用展成滚齿方法,或者集成应用两种加工方法(滚、铣复合加工)。
下面根据风电齿轮箱输入级、中间级、输出级不同特点,选取中间级大轮做加工方法和刀具选用分析。
中间级大轮的模数一般为10~12mm,齿数约100,齿宽在350mm上下。
根据上述数据,从模数和齿数上分析,由于齿数多,且模数适中,排除采用成形铣齿方法(切削效率低);从齿数和齿宽上分析,该类齿轮切削长度(齿宽和齿数的乘积)超过了一般单刃滚刀的刃口切削寿命(单刃滚刀可以增加外径,提高切削刃口数,但造成刀体材料的浪费。
至于如何优化设计滚刀,不在本文讨论范围之内),因此排除普通单刃滚刀;从刀具成本上分析,由于中间级大轮每台齿轮箱只有一个,数量需求还不够大,故没必要选择高成本的硬质合金镶片滚刀;而双切滚刀正好满足了效率、寿命、成本等各方面要求。
齿轮滚刀
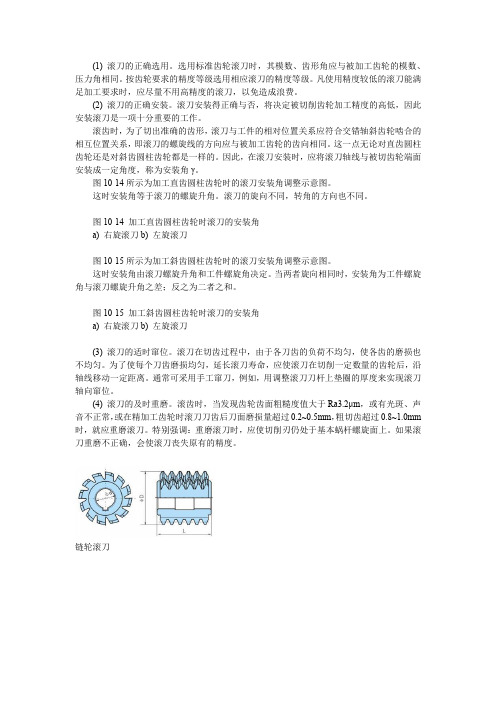
(1) 滚刀的正确选用。
选用标准齿轮滚刀时,其模数、齿形角应与被加工齿轮的模数、压力角相同。
按齿轮要求的精度等级选用相应滚刀的精度等级。
凡使用精度较低的滚刀能满足加工要求时,应尽量不用高精度的滚刀,以免造成浪费。
(2) 滚刀的正确安装。
滚刀安装得正确与否,将决定被切削齿轮加工精度的高低,因此安装滚刀是一项十分重要的工作。
滚齿时,为了切出准确的齿形,滚刀与工件的相对位置关系应符合交错轴斜齿轮啮合的相互位置关系,即滚刀的螺旋线的方向应与被加工齿轮的齿向相同。
这一点无论对直齿圆柱齿轮还是对斜齿圆柱齿轮都是一样的。
因此,在滚刀安装时,应将滚刀轴线与被切齿轮端面安装成一定角度,称为安装角γ。
图10-14所示为加工直齿圆柱齿轮时的滚刀安装角调整示意图。
这时安装角等于滚刀的螺旋升角。
滚刀的旋向不同,转角的方向也不同。
图10-14 加工直齿圆柱齿轮时滚刀的安装角a) 右旋滚刀b) 左旋滚刀图10-15所示为加工斜齿圆柱齿轮时的滚刀安装角调整示意图。
这时安装角由滚刀螺旋升角和工件螺旋角决定。
当两者旋向相同时,安装角为工件螺旋角与滚刀螺旋升角之差;反之为二者之和。
图10-15 加工斜齿圆柱齿轮时滚刀的安装角a) 右旋滚刀b) 左旋滚刀(3) 滚刀的适时窜位。
滚刀在切齿过程中,由于各刀齿的负荷不均匀,使各齿的磨损也不均匀。
为了使每个刀齿磨损均匀,延长滚刀寿命,应使滚刀在切削一定数量的齿轮后,沿轴线移动一定距离。
通常可采用手工窜刀,例如,用调整滚刀刀杆上垫圈的厚度来实现滚刀轴向窜位。
(4) 滚刀的及时重磨。
滚齿时,当发现齿轮齿面粗糙度值大于Ra3.2μm,或有光斑、声音不正常,或在精加工齿轮时滚刀刀齿后刀面磨损量超过0.2~0.5mm,粗切齿超过0.8~1.0mm 时,就应重磨滚刀。
特别强调:重磨滚刀时,应使切削刃仍处于基本蜗杆螺旋面上。
如果滚刀重磨不正确,会使滚刀丧失原有的精度。
链轮滚刀。
渐开线标准齿轮的正确啮合条件
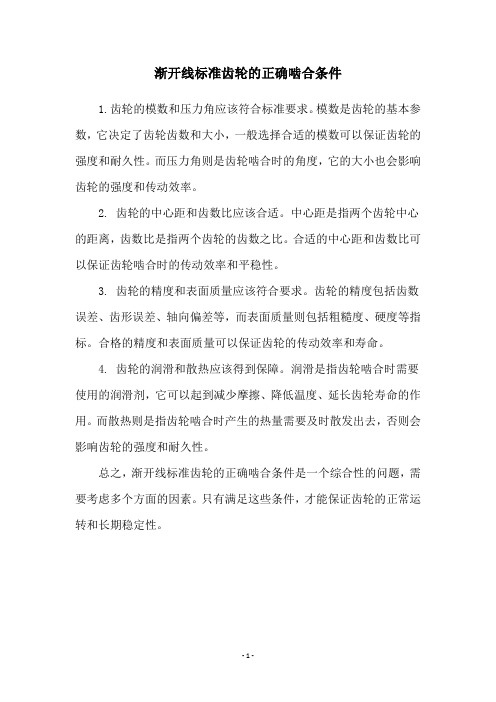
渐开线标准齿轮的正确啮合条件
1.齿轮的模数和压力角应该符合标准要求。
模数是齿轮的基本参数,它决定了齿轮齿数和大小,一般选择合适的模数可以保证齿轮的强度和耐久性。
而压力角则是齿轮啮合时的角度,它的大小也会影响齿轮的强度和传动效率。
2. 齿轮的中心距和齿数比应该合适。
中心距是指两个齿轮中心的距离,齿数比是指两个齿轮的齿数之比。
合适的中心距和齿数比可以保证齿轮啮合时的传动效率和平稳性。
3. 齿轮的精度和表面质量应该符合要求。
齿轮的精度包括齿数误差、齿形误差、轴向偏差等,而表面质量则包括粗糙度、硬度等指标。
合格的精度和表面质量可以保证齿轮的传动效率和寿命。
4. 齿轮的润滑和散热应该得到保障。
润滑是指齿轮啮合时需要使用的润滑剂,它可以起到减少摩擦、降低温度、延长齿轮寿命的作用。
而散热则是指齿轮啮合时产生的热量需要及时散发出去,否则会影响齿轮的强度和耐久性。
总之,渐开线标准齿轮的正确啮合条件是一个综合性的问题,需要考虑多个方面的因素。
只有满足这些条件,才能保证齿轮的正常运转和长期稳定性。
- 1 -。
非标渐开线花键滚刀安全操作及保养规程
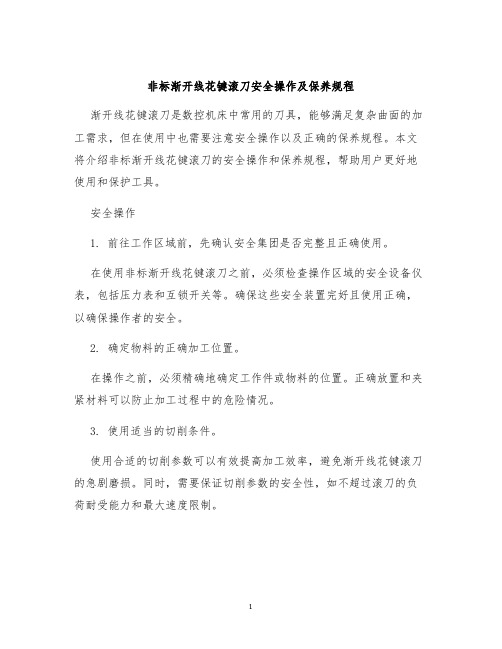
非标渐开线花键滚刀安全操作及保养规程渐开线花键滚刀是数控机床中常用的刀具,能够满足复杂曲面的加工需求,但在使用中也需要注意安全操作以及正确的保养规程。
本文将介绍非标渐开线花键滚刀的安全操作和保养规程,帮助用户更好地使用和保护工具。
安全操作1. 前往工作区域前,先确认安全集团是否完整且正确使用。
在使用非标渐开线花键滚刀之前,必须检查操作区域的安全设备仪表,包括压力表和互锁开关等。
确保这些安全装置完好且使用正确,以确保操作者的安全。
2. 确定物料的正确加工位置。
在操作之前,必须精确地确定工作件或物料的位置。
正确放置和夹紧材料可以防止加工过程中的危险情况。
3. 使用适当的切削条件。
使用合适的切削参数可以有效提高加工效率,避免渐开线花键滚刀的急剧磨损。
同时,需要保证切削参数的安全性,如不超过滚刀的负荷耐受能力和最大速度限制。
4. 确保正确安装和锁定滚刀。
当需要安装或更换滚刀时,必须先关闭电源,等待设备完全停止工作之后才能进行工具的更换过程。
操作者必须按照事先制定的安装操作规程,正确安装和紧固工具,并检查固定螺丝是否松动。
5. 禁止身体接近运动的工具。
在操作过程中,严禁任何人员靠近工具的运动轨迹。
需要安装并识别相应的保护装置来确保操作过程中的安全和生产效率。
6. 尽可能避免异常状态的操作。
如果出现任何异常状况,例如材料错位或搬运设备出现故障,应立即停止机器。
在解决问题之前,必须彻底检查设备的安全状态,清除可能产生的危险来源。
7. 操作完成后关闭电源并恢复安全状态。
当操作完成之后,需要将设备恢复到安全状态。
关闭电源、清理工作区域和检查安全状态等防范措施将确保再次使用非标渐开线花键滚刀时的安全性。
保养规程1. 定期检查滚刀的磨损情况。
滚刀的磨损情况直接影响其效能和加工质量。
要确保最佳使用效果,必须经常检查和评估工具的磨损程度,并在必要时更换滚刀。
2. 适时清洗和润滑滚刀。
清洗和润滑滚刀是必要的工具维护工作。
滚刀的清洗和润滑将延长其使用寿命,并防止可能产生的预期和不良后果。
渐开线非标齿轮滚刀的正确选用

渐开线非标齿轮滚刀的正确选用
齐键
【期刊名称】《工具技术》
【年(卷),期】2001(35)12
【总页数】2页(P34-35)
【关键词】齿轮加工;渐开线非标齿轮滚刀;选用
【作者】齐键
【作者单位】青海东风曲轴有限责任公司
【正文语种】中文
【中图分类】TG721
【相关文献】
1.渐开线滚刀滚齿加工齿轮齿面的数值计算方法 [J], 阎长罡;年立胜;郭毅
2.滚切渐开线直齿圆柱齿轮的双排滚切刀设计 [J], 刘喜平
3.利用加工渐开线齿轮滚刀滚切铣刀容屑槽 [J], 夏春来
4.能切制多个工件的渐开线非标齿轮滚刀的设计 [J], 张范孚
5.渐开线非标准齿轮插齿刀的正确选用 [J], 杨耀锋
因版权原因,仅展示原文概要,查看原文内容请购买。
渐开线花键滚刀 基本型式和尺寸(标准状态:现行)
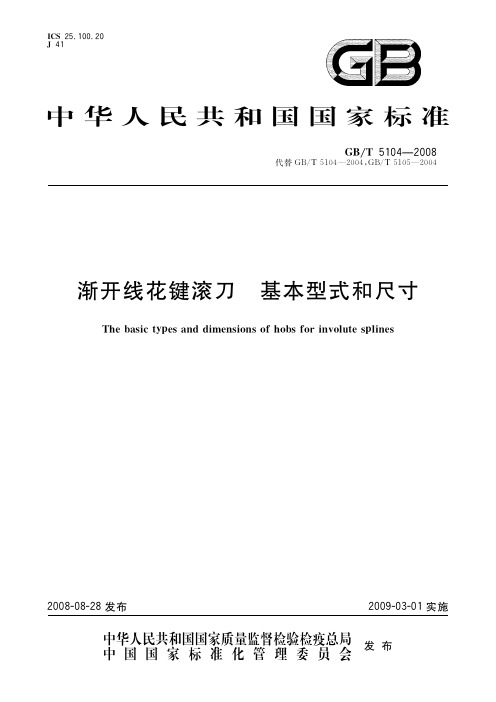
中华人民共和国国家标准
犌犅/犜 5104—2008
代替 GB/T5104—2004,GB/T5105—2004
渐开线花键滚刀 基本型式和尺寸
犜犺犲犫犪狊犻犮狋狔狆犲狊犪狀犱犱犻犿犲狀狊犻狅狀狊狅犳犺狅犫狊犳狅狉犻狀狏狅犾狌狋犲狊狆犾犻狀犲狊
20080828发布
20090301实施
GB/T3478.1 圆 柱 直 齿 渐 开 线 花 键 模 数 基 本 齿 廓 公 差(GB/T3478.1—1995,eqvISO4156: 1981)
GB/T3478.2 圆柱直齿渐开线花键 30°压力角 尺寸表(GB/T3478.2—1995,neqISO4156:1981) GB/T3478.4 圆柱直齿渐开线花键 45°压力角 尺寸表(GB/T3478.4—1995,neqISO4156:1981) GB/T6132 铣 刀 和 铣 刀 刀 杆 的 互 换 尺 寸 (GB/T6132—2006,ISO240:1994,IDT) 3 型 式 和 尺 寸 3.1 压力角为30°渐开线花键滚 刀 的 基 本 型 式 分 两 种:Ⅰ 型 和 Ⅱ 型。 Ⅰ 型 为 平 齿 顶 滚 刀,适 用 于 加 工 平 齿 根 的 外 花 键 ;Ⅱ 型 为 圆 齿 顶 滚 刀 ,适 用 于 加 工 圆 齿 根 的 外 花 键 。 3.2 压 力 角 为30°渐 开 线 花 键 滚 刀 结 构 型 式 和 尺 寸 按 图1 和 表1 的 规 定 ,压 力 角 为45°渐 开 线 花 键 滚 刀 结构型式和尺寸按图1和表2的规定。滚刀的计算尺寸参见附录 A,滚刀的轴向尺寸参见附录 B。 3.3 滚 刀 做 成 单 头 右 旋 (按 用 户 要 求 可 做 成 左 旋 );容 屑 槽 为 平 行 于 滚 刀 轴 线 的 直 槽 。 3.4 键槽的尺寸和偏差按 GB/T6132的规定。 3.5 轴台直径犱1 由制造厂商自定。ⅠΒιβλιοθήκη 犌犅/犜 5104—2008
渐开线齿轮变位系数选择的新方法

面的滑动率。这也要求采用尽可能大的啮合角的正传动,并合理地分配变位系数,
以使两齿轮齿根处的最大滑动率接近或相等(即η'=η")。
4.对于高速或重载的齿轮传动,易产生齿面胶合破坏而使传动失效。除了应 在润滑方面采取措施外,应用变位齿轮时,也应尽可能减小其齿面的接触应力及
我们按滑动率相等的原则(η'=η")分配变位系数。
所谓滑动率,就是两齿面在啮合点的相对切向速度(齿面相对滑动速度)与 该与的切向速度的比值。当一齿轮的齿根与另一齿轮的齿顶啮合时,齿根处的滑
动率达到最大值ηmax。 小齿轮Z1的最大滑动率η'为:
大齿轮Z2的最大滑动率η"为:
若令η'=η"时,则有:
为了兼顾各种齿数的齿轮传动,并考虑到一对齿轮传动的齿数比 u=(Z2/Z1) 不大于 8,对于不同的Z1和Z2,我们规定总变位系数ξ∑不超过图 3 听ABCD折线, 即折线ABCD为ξ∑的限制曲线。这样,当小齿轮的齿数 Z1=12—16 时,若在折 线ABC上选取ξ∑,其重合度ε将略小于 1.2(大于 1.1);而当Z1>17 时,若在折
数比u的大小,用图 10 中的对应斜线分配变位系数,即可保证齿轮的滑动率相等 (或接近)。
图 10
四、选择变位系数线图及应用举例
为了使用方便,将图 7 和 10 图合在一起得图 11,称为选择变位系数线图。 在该图中,由座标原点 0 向左,ξ1为正值,反之为负值。
2.对于润滑良好的硬齿面(HB>350)的闭式齿轮传动,一般认为其主要危险 是在循环应力的作用下齿根的疲劳裂纹逐渐扩展而造成齿根折断。但是, 实际 上也有许多硬齿面齿轮传动因齿面点蚀剥落而失去工作能力的。因而。对这种齿 轮传动,仍应尽量增大传动的啮合角α(即尽量增大总变位系数ξ∑),这样不 仅可以提高接触强度,还能增大齿形系数y值,提高齿根的弯曲强度。必要时还 可以适当地分配变位系数,使[σ]W1y1=[σ]W2y2,即达到两齿轮的齿根弯曲强度大 致相等。
- 1、下载文档前请自行甄别文档内容的完整性,平台不提供额外的编辑、内容补充、找答案等附加服务。
- 2、"仅部分预览"的文档,不可在线预览部分如存在完整性等问题,可反馈申请退款(可完整预览的文档不适用该条件!)。
- 3、如文档侵犯您的权益,请联系客服反馈,我们会尽快为您处理(人工客服工作时间:9:00-18:30)。
渐开线非标齿轮滚刀的正确选用
2007/7/5/09:43 来源:中国刀具信息网
目前,汽车、拖拉机等行业大量使用齿顶高系数h a*≠1,压力角αn≠20°或模数m n为非标准值的渐开线非标齿轮。
为加工此类齿轮,需根据被切齿轮参数确定相应的滚刀参数,并从《复杂刀具订货图册》(以下简称《图册》)中选用正确的非标滚刀。
1 非标滚刀的选用步骤
1.确定滚刀类型与精度
滚刀类型与精度的选择应根据加工设备及工艺而定。
滚刀模数(或径节、周节)和压力角应与被切齿轮相等,螺旋方向最好与被切齿轮相同,加工直齿齿轮时应优先选用右旋滚刀。
2.确定滚刀全齿高h
对于非全切式滚刀,滚刀全齿高h的计算公式为
h≥h1+c*m n+∆h (1)
对于全切式滚刀,则有
h=h1(2)
式中:h1——被加工齿轮全齿高
c*——被加工齿轮顶隙系数
m n——被加工齿轮法向模数
∆h——剃齿或磨齿时因工艺需要而设置的滚刀齿顶加长量,可参考表1选取
3.确定滚刀法向齿厚S n、轴向齿厚S x和齿顶高h a
齿轮滚刀的轴向齿形如图1所示。
其中,Ⅰ型为正常齿形,Ⅱ型为修形齿形。
剃前齿轮滚刀的轴向齿形一般有五种类型(图略)。
剃前和磨前滚刀的齿形通常都有一定修形量。
图1
滚刀齿厚和齿顶高有以下两种计算方法:
a.按通用滚刀设计方法的计算公式为
S n=πm n/2-∆S’+∆S" (3)
S x=S n/cosλ(4)
h a=h f1+x n1m n+∆h (5)
b.式中:∆S’——滚刀的加工余量(可参考表2 取值)
注:E ss——被切齿轮齿厚极限上偏差
c.∆S"——考虑被切齿轮齿厚偏差而附加的滚刀齿厚增量(可参考表2取值)
d.λ——滚刀分度圆螺旋升角
e.h f1——被切齿轮齿根高
f.x n1——被切齿轮法向变位系数
g.式(4)中滚刀分度圆螺旋升角λ的计算公式为
sinλ=m n z[/d e-2h a-0.2(k+δd e)]≈m n z/(d e-2h a) (6)
h.式中:z——滚刀头数
i.d e——滚刀齿顶圆直径
j.k——滚刀径向铲背量
k.δd e——滚刀外径公差
l.按专用滚刀设计方法的计算公式为
S n=e n1min=πm n/2-2x n1m n tanαn-∆S’+∆S" (7)
S x=S n/cosλ(8)
h a=h f1+∆h (9)
m.式中:e n1min——被切齿轮工序法面齿间宽最小值
4.确定滚刀修形与齿顶圆弧
当被切齿轮无修形要求时,选择剃前或磨前滚刀时无需验算滚刀修形量,其它类型的滚刀则应选用非修形滚刀。
当被切齿轮有修形要求时,无论何种类型的滚刀均应选用修形滚刀,并验算修形
量,验算过程可参考有关齿轮刀具设计手册。
当被切齿轮对滚刀齿顶圆角r1有特殊要求时,订货时需与滚刀制造厂协商。
对于在《图册》的备注栏中给出了r1值的大齿顶圆角滚刀,应按复杂刀具设计手册中的有关公式验算被切齿轮与配对齿轮传动时是否会发生过渡曲线干涉;对于备注栏中未标注r1值的滚刀,由于r1较小,因此无需
验算过渡曲线干涉。
5.查《图册》选用滚刀。
根据上述步骤确定的滚刀参数,查阅《图册》,选出所需滚刀。
6.验算滚刀轴向齿厚S x
首先按式(6)估算出λ值,然后按式(4)或(8)验算滚刀轴向齿厚S x。
当按照步骤(3)中方法①和②确定的滚刀参数在《图册》中选不出所需滚刀时,还可按下式对符合以上步骤确定的参数(h a、S x除外)的所有滚刀的a和S x进行验算,若此式成立,则该滚刀可用:S x=[pm n/2-∆S’+∆S"+2(h a-x n1m n-h f1-∆h)tana n]/cosλ(10)
2 应用实例
应用上述方法选用加工解放牌汽车中间轴齿轮3的非标滚刀。
该齿轮为双径节制齿轮,参数见表
3。
滚刀选用步骤如下:
1.当采用滚齿→热处理加工工艺时,应选用A级或B级齿轮滚刀,滚刀径节DP1/DP2=6/8,
a N=20°,螺旋方向为右旋。
2.滚刀全齿高h≥h1+c*m2+∆h=7.62+0.4×
3.175+0=8.89mm。
3.滚刀法向齿厚S n、轴向齿厚S x和齿顶高h a分别为
S n=πm1/2-∆S’+∆S"=25.4π/2×6-0+(0~0.08)=6.65~6.73mm
S x=S n/cosλ=6.65/cosλ~6.73/cosλ(λ待定)
h a=h f1+x n2m2+∆h=3.145+1.3+0=4.445mm
4.被加工齿轮无齿形修形,因此选用非修形、正常齿顶圆角的滚刀。
5.根据以上步骤确定的参数查阅《图册》后,选用代号为G1-DP-26的滚刀,其主要参数见
表4。
6.验算滚刀轴向齿厚S x:
S x=6.65/cos3°36’~6.73/cos3°36’=6.66~6.74mm
计算值与表6中的S x值相符,故所选滚刀符合要求。
加工实践证明,本文介绍的非标滚刀选用方法简单实用,能较好满足生产要求。