试模确认流程
试模操作规程
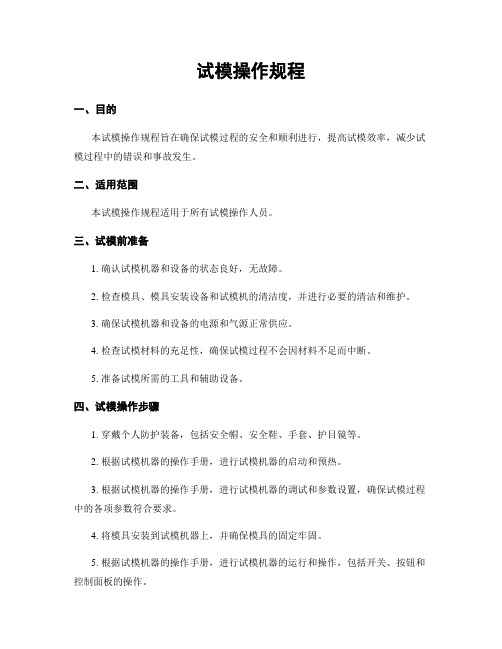
试模操作规程一、目的本试模操作规程旨在确保试模过程的安全和顺利进行,提高试模效率,减少试模过程中的错误和事故发生。
二、适用范围本试模操作规程适用于所有试模操作人员。
三、试模前准备1. 确认试模机器和设备的状态良好,无故障。
2. 检查模具、模具安装设备和试模机的清洁度,并进行必要的清洁和维护。
3. 确保试模机器和设备的电源和气源正常供应。
4. 检查试模材料的充足性,确保试模过程不会因材料不足而中断。
5. 准备试模所需的工具和辅助设备。
四、试模操作步骤1. 穿戴个人防护装备,包括安全帽、安全鞋、手套、护目镜等。
2. 根据试模机器的操作手册,进行试模机器的启动和预热。
3. 根据试模机器的操作手册,进行试模机器的调试和参数设置,确保试模过程中的各项参数符合要求。
4. 将模具安装到试模机器上,并确保模具的固定牢固。
5. 根据试模机器的操作手册,进行试模机器的运行和操作,包括开关、按钮和控制面板的操作。
6. 观察试模过程中的各项指标和参数,如温度、压力、速度等,确保其在设定范围内。
7. 定期检查试模机器和设备的运行状态,如有异常及时处理。
8. 在试模过程中,严禁将手或其他物体伸入试模机器内部,以免发生事故。
9. 在试模过程中,如发现异常情况或有安全隐患,应立即停止试模并报告上级。
10. 试模完成后,关闭试模机器和设备,并进行清理和维护。
五、安全注意事项1. 在试模过程中,严禁戏弄、嬉闹或进行其他不相关的行为,以免影响操作安全。
2. 在试模过程中,严禁将手或其他物体伸入试模机器内部,以免发生夹伤或其他伤害。
3. 在试模过程中,严禁随意更改试模机器的参数设置,以免引发故障或事故。
4. 在试模过程中,如发现异常情况或有安全隐患,应立即停止试模并报告上级。
5. 在试模过程中,应随时保持警惕,注意观察试模机器和设备的运行状态,如有异常及时处理。
六、事故应急处理1. 如发生试模过程中的事故,应立即停止试模并采取紧急措施,确保人员安全。
试模作业指导书
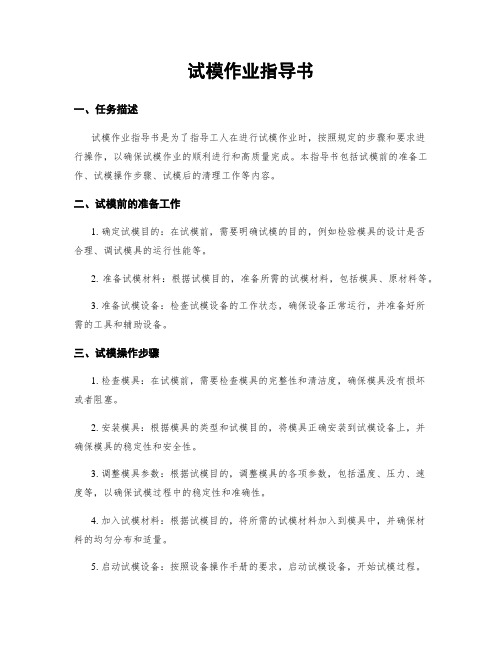
试模作业指导书一、任务描述试模作业指导书是为了指导工人在进行试模作业时,按照规定的步骤和要求进行操作,以确保试模作业的顺利进行和高质量完成。
本指导书包括试模前的准备工作、试模操作步骤、试模后的清理工作等内容。
二、试模前的准备工作1. 确定试模目的:在试模前,需要明确试模的目的,例如检验模具的设计是否合理、调试模具的运行性能等。
2. 准备试模材料:根据试模目的,准备所需的试模材料,包括模具、原材料等。
3. 准备试模设备:检查试模设备的工作状态,确保设备正常运行,并准备好所需的工具和辅助设备。
三、试模操作步骤1. 检查模具:在试模前,需要检查模具的完整性和清洁度,确保模具没有损坏或者阻塞。
2. 安装模具:根据模具的类型和试模目的,将模具正确安装到试模设备上,并确保模具的稳定性和安全性。
3. 调整模具参数:根据试模目的,调整模具的各项参数,包括温度、压力、速度等,以确保试模过程中的稳定性和准确性。
4. 加入试模材料:根据试模目的,将所需的试模材料加入到模具中,并确保材料的均匀分布和适量。
5. 启动试模设备:按照设备操作手册的要求,启动试模设备,开始试模过程。
6. 观察试模过程:在试模过程中,及时观察模具的运行情况和试模效果,发现异常情况及时处理。
7. 记录试模数据:在试模过程中,记录关键的试模数据,包括温度、压力、时间等,以备后续分析和评估使用。
8. 结束试模操作:试模完成后,按照设备操作手册的要求,住手试模设备,并进行必要的清理工作。
四、试模后的清理工作1. 清理模具:试模完成后,需要对模具进行清洁和保养,包括清除残留材料、润滑模具等。
2. 清理试模设备:对试模设备进行清洁和维护,确保设备的正常使用和延长设备的使用寿命。
3. 整理试模数据:整理试模过程中记录的数据,进行分析和评估,并根据需要进行改进和优化。
五、注意事项1. 操作安全:在试模过程中,要严格遵守安全操作规程,确保人员和设备的安全。
2. 质量控制:在试模过程中,要注意质量控制,确保试模产品符合要求。
试模流程

试模流程1.0目的:明确项目工作职责权限,规范其工作流程。
2.0适用范围:3.0职责;3.1项目系;3.1.1 负责《模具确认表》中收集基本信息,制作初步《机种资料》;3.1.2 根据《机种资料》,申购试模材料及色粉;3.1.3 检查模具装配图、零件图、并对照客户打合内容核对图面,不符处及时与设计担当确认;3.1.4 根据T1试模日期,跟踪新模进度,(核对制模课I-M3系统计划与现场进度),并熟悉模具结构,对计划变动之状况,及时联络客户,并重新确定T1日期;3.1.5 根据T1试模日期,结合实际进度,提前一天开出《试模申请单》;3.1.6 T1样板试作前,将客户图面登记后交ISO受控并分发给相关部门;3.1.7 负责现场试模状况,跟踪、对模具问题、产品问题做详细记录,作为T1修正依据,并于次日以《模具修正/变更履历表》形式附一啤样板交样板文员,下发给模具PMC,模具课安排对模具进行维修;以对设计结果进行验证;3.1.8.a T1试做后,如产品成型条件正常,由项目工程师填写《样板检查通知单》,并附3啤条件正常样板交测量房测数,并将每次测数报告保存工程资料上;以对设计结果进行验证。
3.1.8.b T1试作后,对需二次加工(喷油、印刷、烫金绘雕等)之部品,由项目工程师联络丝喷课安排喷油治具制作,油漆样品申购、印刷鸿墨样品申购,印刷菲林、网板、钢板、治具制作、烫金治具制作,烫金纸申购等,并作如T2样板二次加工准备;3.1.8.c T1试作后,项目工程师须联络本课包装技术员,对每个部品设计包装方式(分国内、国外及厂内半成品周转等);3.1.8.d T1试作后,项目工程师对所得样板进行评估,将合格样板交样板文员处理;项目样板文员须将样板整理标识后,填表写《样板寄送单》递送给营业,由营业转交给客户,并将客户签名回传之《样板寄送单》复印一份给营业,产品每次客户回传《样板寄送单》须存档;3.1.8.f 每次模具试作后,如模具存在问题,项目工程师须对照试模结果进行《模具修正/变更履历表》的填写,现场跟进模具修改进度;适时填写《试模申请单》对修改后的模具进行试作直至模具产品均符合客户要求;3.1.9 项目文员对每套模具按模具编号及产品编号统计试模次数,对超过目标之模具及时通知项目工程师及主管,便于组织专题会议提出解决方案;3.1.10 项目文员负责对部门所需物料之申购;3.1.11 样板文员负责整理,保存每套模具之客户资料(修正及变更等);3.1.12 所有模具及移管模具的变更,项目工程师从营业处接到客户变更后,须以《模具变更/修正履历表》的形式,附一啤样板,交样板文员,下发模具PMC安排模具进行相应变更,对于只变更二次加工之部分,联络丝喷打样,并将变更后样品送给营业交客户确认变更部品取得客户承认之后,须通知样板文员填写《塑工程变更通知书》,下发相关部门,并将原件存放在每套模具File中;3.1.13 项目工程师负责已OK模具之相关资料整理,召开量产会议;3.1.14 负责对所有需二次加工部品之治具制作,辅料申购及二次加工打样;3.1.15 负责新产品之《包装指示》书制作;3.2 设计系负责客户变更及公司内部变更之相应模具图而变更;3.3 模具课3.3.1 负责所有模具按项目所发资料修正;3.3.2 模具PMC负责对所有模具进度的跟踪,对异常之情况以书面资料或邮件方式提供给项目工程师;3.4 计划课3.4.1 负责对试模料、色料等申请的受理及进度跟踪、试模料的发放;3.4.2 负责对项目所有《试模申请单》的机台安排;3.5采购课负责对项目系之申购物料进行采购;3.6 营业课3.6.1 负责项目呈送之样板递送;3.6.2 负责客户修模联络,变更联络,打样联络信息之传递;3.6.3 负责《模具OK单》的填写及安排量产或交模。
试模操作规程
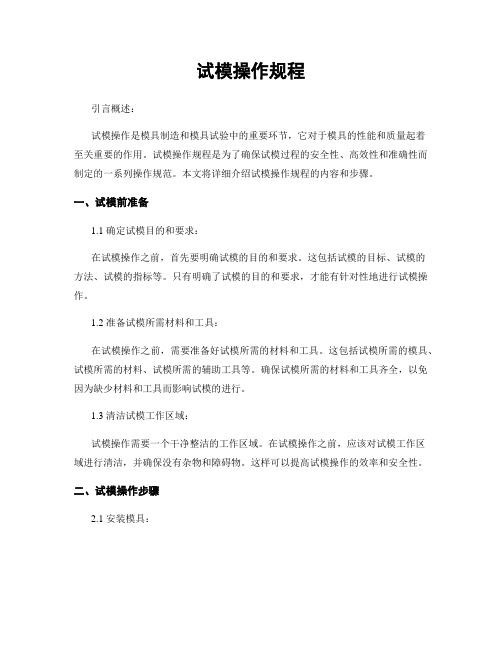
试模操作规程引言概述:试模操作是模具制造和模具试验中的重要环节,它对于模具的性能和质量起着至关重要的作用。
试模操作规程是为了确保试模过程的安全性、高效性和准确性而制定的一系列操作规范。
本文将详细介绍试模操作规程的内容和步骤。
一、试模前准备1.1 确定试模目的和要求:在试模操作之前,首先要明确试模的目的和要求。
这包括试模的目标、试模的方法、试模的指标等。
只有明确了试模的目的和要求,才能有针对性地进行试模操作。
1.2 准备试模所需材料和工具:在试模操作之前,需要准备好试模所需的材料和工具。
这包括试模所需的模具、试模所需的材料、试模所需的辅助工具等。
确保试模所需的材料和工具齐全,以免因为缺少材料和工具而影响试模的进行。
1.3 清洁试模工作区域:试模操作需要一个干净整洁的工作区域。
在试模操作之前,应该对试模工作区域进行清洁,并确保没有杂物和障碍物。
这样可以提高试模操作的效率和安全性。
二、试模操作步骤2.1 安装模具:试模操作的第一步是安装模具。
根据试模的要求和模具的类型,选择合适的安装方式。
在安装模具之前,要检查模具的完整性和可用性,确保模具没有损坏和缺陷。
2.2 调整模具参数:根据试模的要求和模具的特点,调整模具的参数。
这包括模具的开合速度、模具的温度、模具的压力等。
通过合理调整模具的参数,可以提高试模的效率和准确性。
2.3 进行试模操作:根据试模的要求和试模操作规程,进行试模操作。
这包括模具的开合、模具的注塑、模具的冷却等。
在试模操作过程中,要注意操作的安全性和准确性,确保试模的顺利进行。
三、试模后处理3.1 清洁模具:试模操作之后,应该及时清洁模具。
清洁模具可以去除试模过程中产生的杂质和残留物,保持模具的清洁和良好状态。
同时,清洁模具也有利于下一次试模的进行。
3.2 检查模具质量:试模操作之后,应该对模具的质量进行检查。
这包括模具的尺寸精度、模具的表面质量、模具的使用寿命等。
通过检查模具的质量,可以评估试模的效果和模具的性能。
试模作业指导书
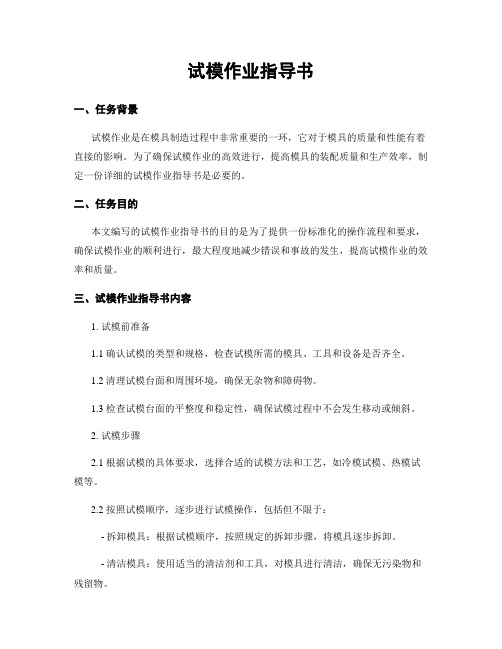
试模作业指导书一、任务背景试模作业是在模具制造过程中非常重要的一环,它对于模具的质量和性能有着直接的影响。
为了确保试模作业的高效进行,提高模具的装配质量和生产效率,制定一份详细的试模作业指导书是必要的。
二、任务目的本文编写的试模作业指导书的目的是为了提供一份标准化的操作流程和要求,确保试模作业的顺利进行,最大程度地减少错误和事故的发生,提高试模作业的效率和质量。
三、试模作业指导书内容1. 试模前准备1.1 确认试模的类型和规格,检查试模所需的模具、工具和设备是否齐全。
1.2 清理试模台面和周围环境,确保无杂物和障碍物。
1.3 检查试模台面的平整度和稳定性,确保试模过程中不会发生移动或倾斜。
2. 试模步骤2.1 根据试模的具体要求,选择合适的试模方法和工艺,如冷模试模、热模试模等。
2.2 按照试模顺序,逐步进行试模操作,包括但不限于:- 拆卸模具:根据试模顺序,按照规定的拆卸步骤,将模具逐步拆卸。
- 清洁模具:使用适当的清洁剂和工具,对模具进行清洁,确保无污染物和残留物。
- 检查模具:对拆卸下来的模具进行全面检查,包括模具的表面状况、零件的完整性等。
- 维修模具:如有需要,对模具进行必要的维修和更换,确保模具的完好性和正常使用。
- 组装模具:按照试模顺序,逐步组装模具,确保各零件的正确安装和紧固。
- 调试模具:对组装好的模具进行调试,确保模具的运行正常、无卡阻和其他问题。
- 试模测试:按照试模要求,进行试模测试,包括模具的开合、产品的成型等。
- 试模记录:记录试模过程中的关键信息和数据,如试模时间、试模结果等。
3. 试模安全措施3.1 确保试模过程中的安全性,如佩戴适当的防护用具,如手套、护目镜等。
3.2 严格遵守操作规程和安全操作流程,禁止操作人员擅自调整或更改试模设备和工具。
3.3 注意模具的重量和尺寸,避免因操作不当导致模具滑落或破损。
3.4 在试模过程中,及时清理模具周围的杂物和残留物,保持工作环境整洁。
试模操作规程

试模操作规程一、目的和范围本操作规程的目的是确保试模操作的安全性和有效性,保护设备和人员的安全,提高试模效率。
适用于所有试模操作人员。
二、术语和定义1. 试模:指在生产前对模具进行调试和测试的过程。
2. 模具:指用于制造产品的工具或设备。
3. 试模操作人员:指负责进行试模操作的工作人员。
三、试模前准备1. 确认试模工作的目标和要求。
2. 检查模具的完整性和清洁度,确保没有损坏或杂物。
3. 准备所需的试模材料和工具。
四、试模操作步骤1. 确保试模操作区域的安全,清理杂物,确保地面干净整洁。
2. 穿戴个人防护装备,包括安全帽、安全鞋、防护眼镜等。
3. 检查试模设备的电源和气源是否正常,确保设备工作正常。
4. 按照试模工作要求,调整模具的位置和固定方式。
5. 检查模具的温度和润滑情况,确保模具处于适宜的工作状态。
6. 启动试模设备,按照操作要求进行试模操作。
7. 监控试模过程中的温度、压力等参数,及时调整设备参数。
8. 在试模过程中,注意观察模具的运行情况,及时发现并处理异常情况。
9. 试模结束后,关闭试模设备,清理工作区域,归位工具和材料。
10. 填写试模操作记录,包括试模时间、参数、异常情况等信息。
五、安全注意事项1. 在试模操作过程中,严禁随意触碰设备和模具,以免发生意外伤害。
2. 严禁在试模操作区域内吸烟或使用明火。
3. 在试模操作前,必须熟悉试模设备的操作流程和安全规定。
4. 在试模过程中,如发现设备异常或模具损坏,应立即停止操作并报告上级。
5. 试模操作人员必须经过专业培训并持有相关证书。
六、常见问题及解决方法1. 试模过程中出现模具卡料:停止设备运行,检查模具和材料,清理卡料,重新开始试模。
2. 试模过程中出现模具温度过高:检查冷却系统是否正常工作,调整冷却水流量和温度。
3. 试模过程中出现模具不闭合或不平整:检查模具固定和调整机构,重新调整模具位置。
4. 试模过程中出现模具润滑不良:检查润滑系统是否正常工作,添加或更换润滑剂。
试模工作流程

2.5模具上线。
2.6按照试创模记录表所列的生产参数,进行试创模参数预设及生产。
2.7由生产人员(班长)将试模中的生产参数依次填写在试创模记录表所对应表格内,并由工艺人员签字确认。
2.8试模过程中,工艺人员要随时掌握试模产品的状况,及时调整试模参数,以便在最短时间内试创制出符合要求的产品。
2.13模具正式编入正常生产模具序列,并由生产车间按计划安排进行生产或入库、保管、维护等。
3.0修改与修订
4.1 2014年6月27日第1次草拟。
1.0目的
1.1规范模具的试模工作流程。
2.0试模流程
2.1接受试模任务单。任务单由技术科该模ห้องสมุดไป่ตู้设计人员出具,总工签字批准后发出。任务单内应有产品基本的参数要求如:重量、尺寸、颜色、大约承重、密封性等。
2.2根据任务单确定模具件数、模具名称。
2.3根据任务单确定该模具配置(预埋件)后交计划安排试模生产。
2.9符合要求的产品应由工艺人员召集技术科模具设计人员、总工、生产厂长、质检人员进行工艺评审。
2.10产品经检测、评判不合格,继续执行2.7、2.8、2.9项规定步骤。
2.11产品经检测、评判合格,以上相关人员应在试模记录表内会签。并签署试创模结论。做好模具交接。
2.12工艺科将该模具试创模记录表存档,完成模具交接手续。
科学试模的基本流程
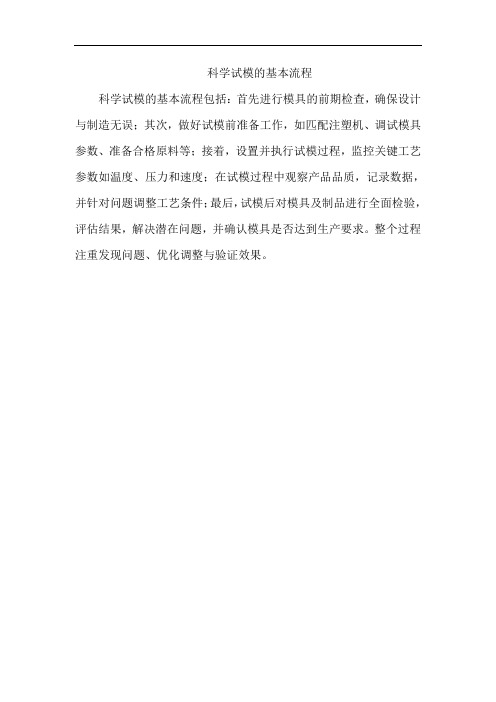
科学试模的基本流程
科学试模的基本流程包括:首先进行模具的前期检查,确保设计与制造无误;其次,做好试模前准备工作,如匹配注塑机、调试模具参数、准备合格原料等;接着,设置并执行试模过程,监控关键工艺参数如温度、压力和速度;在试模过程中观察产品品质,记录数据,并针对问题调整工艺条件;最后,试模后对模具及制品进行全面检验,评估结果,解决潜在问题,并确认模具是否达到生产要求。
整个过程注重发现问题、优化调整与验证效果。
试模操作流程

试模操作流程试模主要分四部分:(1)试模前模具的检查(2)试模前的准备工作和调试(3)试模时的注意事项(4)试模后模具的检收一、试模前模具的检查模具做好后,需要对模具进行试模前的检查,以发现模具设计和制造中的问题,以便及时纠正,其具体步骤如下:(1)注塑模的外观检查1.成型零件、浇注系统等与熔料接触的表面应光滑、平整、无塌坑、伤痕等缺陷。
2.模具的闭合行程,安装于机器的各配合部位尺寸、脱模方式、开模距离、模具工件要求等应符合设备的相关条件。
3.模具上应有生产号和合模标志,各种接头、阀门、附件、备件应齐全。
4.各滑动零件的配合间隙应符合要求,起止位置定位正确,镶件紧固应紧固牢靠。
5.对于注塑腐蚀性较强的注塑模,其模具型腔的表面应镀铬和防腐处理。
6.模具的外观部分不应当有锐角,大、中型模具应有起吊用的吊孔、吊环。
7.互相接触的承压零件,应有合理的承压面积和承压方式,避免直接承受挤压。
8.模具的稳定性良好,有足够强度,工作时应受力匀衡,行动平稳。
(2)模具的空运转检查模具安装好后,必须经过空运转检查,经便进一步发现问题,进而解决问题。
1.将模具缓缓合拢,合模后各结合面均应接触紧密,不得出现间隙。
2.开模时顶出脱模机构应保证顺利脱模,以便取出塑件和浇注系统废料。
3.活动型芯,顶出及导向部分等运动时应滑动平稳、灵活、动作协调可靠。
4.检查各锁紧机构、应能可靠、稳妥地锁紧,各紧固件不得有任何松动现象。
5.各气动、液动控制系统动作正确,不泄漏、不产生过大振动,各阀门工作正常。
6.冷却系统的水路应畅通,不漏水,各种控制阀门控制正常。
试模流程
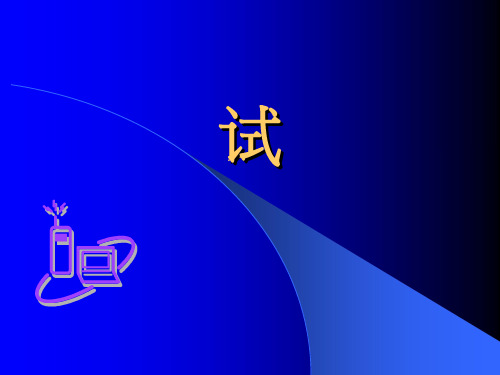
B. 試模中注意事項:
1.模具于試模中最忌不正常之成型方式調整.壓力、劑量、 溫度等皆須在可承載的條件內.尤其在尺寸規格內,而有 縮水現象下,每每有加多劑量的調機模式是試模之大忌, 亦是模具殺手作為. 2.試模是在尋找模具的不正確的結構,不正確的尺寸及一 切的錯誤.因而,一切作為都必須以正常的量產的行為行 之.故此,在以尺寸為基准的條件下尋得正確的成型條件. 3.試模所得塑件若有各樣缺點,應以變更模具為優先考慮, 而非作不正常調機去取得樣品而造成量產時良率不足.
15. 若成品表面是否有異常現象是否有確認模具上有 相同現象 16. 有咬花現象時是否有與咬花樣板核對 17. 有刻字、印刷時是否有與黑白稿核對并確認是否正確 18. 確認結合線的位置及不當的位置 19. 是否有進膠噴痕、流痕現象 20. 是否有銀絲現象,并確認原料干燥烘烤情形 21. 是否有將試模完的樣品交代后續處理事項(噴漆、組 立、廢料銷毀……)
D. 確認材料
1.材料是否正确. 2.材料是否已干燥. 3.材料是否是新料
三、试 模 中
A. 試模步驟:
1.模具上機后正確接通水(油)管,并先行加熱 2.正確調整模具開模距離及頂針頂出長度.在頂針回位后 檢查所有斜銷是否回位,確認無誤后方可關模,否則須請 模具廠人員到現場確認并改善之. 3.估算模具之注塑量,并以其值的20%作為第一模的劑量之 標准.
三、试 模 后
1. 保壓取消打出的未飽模成品 2PCS 2. 水口 3. 尺寸上限樣品 2PCS及成型條件 4. 尺寸下限樣品 2PCS及成型條件 5. 較佳成型條件樣品 2PCS及成型條件 6. 試模后模具保養 7. 試模問題檢討
試模作業
二 、试 模 前 前
A. 试模必备五大要素:
新项目模具试模流程
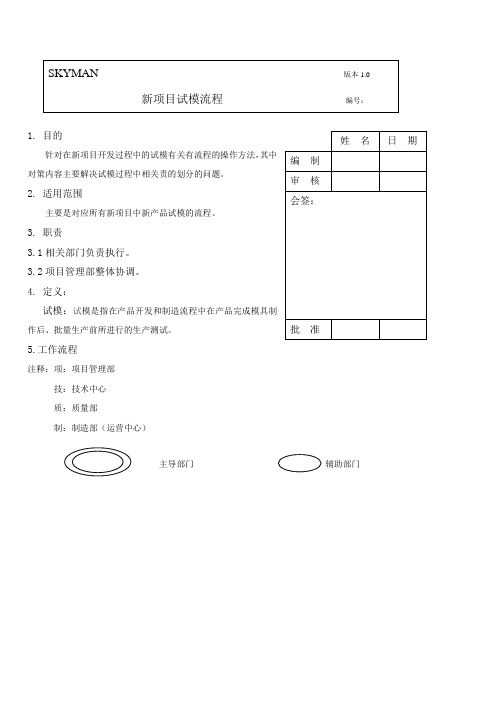
1.目的针对在新项目开发过程中的试模有关有流程的操作方法,其中对策内容主要解决试模过程中相关责的划分的问题。
2. 适用范围主要是对应所有新项目中新产品试模的流程。
3. 职责3.1相关部门负责执行。
3.2项目管理部整体协调。
4. 定义:试模:试模是指在产品开发和制造流程中在产品完成模具制作后、批量生产前所进行的生产测试。
5.工作流程注释:项:项目管理部技:技术中心质:质量部制:制造部(运营中心)主导部门辅助部门6.备注说明1.原则上一个产品的整套模具须在一个工作日内完成一轮试模。
在试模的过程中,如发现模具本身或者零件有异常,技术中心需要在短时间内给出明确的判断,且在一个工作日内做好整改方案。
2.试模完成确认是指产品质量得到质量认可,模具状态制造部门认可。
3.试模计划应提前一周下发到制造部,特殊情况需事前当面联络。
4.试模原则上应整线和4小时倍数安排,特殊情况由制造部安排。
附件1发行版本:No.1 重庆天人汽车车身制造有限公司试模联络单发行时间项目信息项目名称B211 客户长安紧急程度急项目代表电话技术代表电话供应商供应商联系人/电话试模产品信息序号产品件号名称工序工序名称机械吨位需求工段希望时间1 1234 5234编制:批准试模安排试模安排生产协调员:时间:备注:如试模零件较多,可以附页附件2发行版本:No.1 重庆天人汽车车身制造有限公司模具试模确认表项目:模具厂家:零件名称零件编号:模具编号:确认时间:试模情况和外观及产品质量结果制造/日期:质检/时期:模具质量检查评估意见技术项目:。
试模操作规程
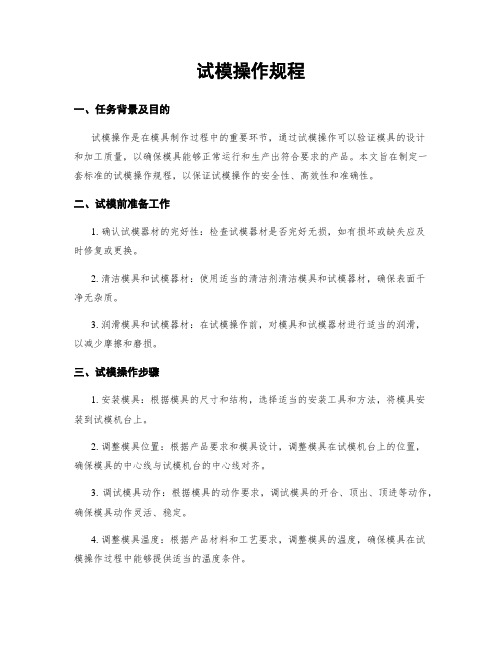
试模操作规程一、任务背景及目的试模操作是在模具制作过程中的重要环节,通过试模操作可以验证模具的设计和加工质量,以确保模具能够正常运行和生产出符合要求的产品。
本文旨在制定一套标准的试模操作规程,以保证试模操作的安全性、高效性和准确性。
二、试模前准备工作1. 确认试模器材的完好性:检查试模器材是否完好无损,如有损坏或缺失应及时修复或更换。
2. 清洁模具和试模器材:使用适当的清洁剂清洁模具和试模器材,确保表面干净无杂质。
3. 润滑模具和试模器材:在试模操作前,对模具和试模器材进行适当的润滑,以减少摩擦和磨损。
三、试模操作步骤1. 安装模具:根据模具的尺寸和结构,选择适当的安装工具和方法,将模具安装到试模机台上。
2. 调整模具位置:根据产品要求和模具设计,调整模具在试模机台上的位置,确保模具的中心线与试模机台的中心线对齐。
3. 调试模具动作:根据模具的动作要求,调试模具的开合、顶出、顶进等动作,确保模具动作灵活、稳定。
4. 调整模具温度:根据产品材料和工艺要求,调整模具的温度,确保模具在试模操作过程中能够提供适当的温度条件。
5. 调整模具压力:根据产品材料和工艺要求,调整模具的压力,确保模具在试模操作过程中能够提供适当的压力条件。
6. 进行试模操作:根据产品要求,进行试模操作,观察模具动作是否正常,产品是否符合要求。
7. 检查模具和产品:试模操作完成后,对模具和产品进行检查,检查模具是否有损坏或磨损,产品是否符合要求。
8. 记录试模数据:记录试模操作的相关数据,包括模具温度、模具压力、产品尺寸等,以便后续分析和改进。
四、安全注意事项1. 严格遵守试模操作规程:试模操作人员必须严格按照试模操作规程进行操作,不得随意更改或省略步骤。
2. 使用个人防护装备:试模操作人员应佩戴适当的个人防护装备,如安全帽、防护眼镜、防护手套等,确保人身安全。
3. 避免触摸运动部件:在试模操作过程中,严禁触摸模具的运动部件,以免发生意外伤害。
试模流程图
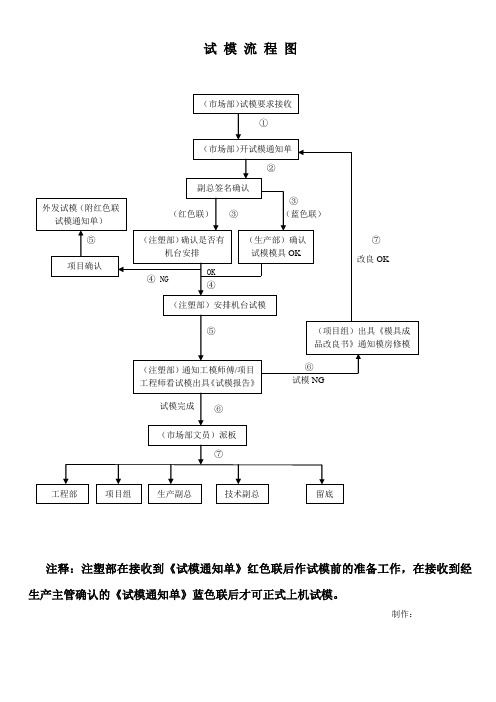
试模流程图注释:注塑部在接收到《试模通知单》红色联后作试模前的准备工作,在接收到经生产主管确认的《试模通知单》蓝色联后才可正式上机试模。
制作:试模操作程序生产前对模具采取新模具试运作,具体操作如下:试模主要分四部分:(1)试模前模具的检查(2)试模前的准备工作和调试(3)试模时的注意事项(4)试模后模具的检收一、试模前模具的检查模具做好后,需要对模具进行试模前的检查,以发现模具设计和制造中的问题,以便及时纠正,其具体步骤如下:(1)注塑模的外观检查1.成型零件、浇注系统等与熔料接触的表面应光滑、平整、无塌坑、伤痕等缺陷。
2.模具的闭合行程,安装于机器的各配合部位尺寸、脱模方式、开模距离、模具工件要求等应符合设备的相关条件。
3.模具上应有生产号和合模标志,各种接头、阀门、附件、备件应齐全。
4.各滑动零件的配合间隙应符合要求,起止位置定位正确,镶件紧固应紧固牢靠。
5.对于注塑腐蚀性较强的注塑模,其模具型腔的表面应镀铬和防腐处理。
6.模具的外观部分不应当有锐角,大、中型模具应有起吊用的吊孔、吊环。
7.互相接触的承压零件,应有合理的承压面积和承压方式,避免直接承受挤压。
8.模具的稳定性良好,有足够强度,工作时应受力匀衡,行动平稳。
(2)模具的空运转检查模具安装好后,必须经过空运转检查,经便进一步发现问题,进而解决问题。
1.将模具缓缓合拢,合模后各结合面均应接触紧密,不得出现间隙。
2.开模时顶出脱模机构应保证顺利脱模,以便取出塑件和浇注系统废料。
3.活动型芯,顶出及导向部分等运动时应滑动平稳、灵活、动作协调可靠。
4.检查各锁紧机构、应能可靠、稳妥地锁紧,各紧固件不得有任何松动现象。
5.各气动、液动控制系统动作正确,不泄漏、不产生过大振动,各阀门工作正常。
6.冷却系统的水路应畅通,不漏水,各种控制阀门控制正常。
二,试模前的准备工作及调试试模是为了检查模具制作的质量好坏,能否生产出合格产品来。
1.试模前,应检查所用原料是否符合要求,不符合要求的应进行处理或更换;欲试之原料先行干燥,PE、PP、POM不需干燥其余均要,利用新料试才标准。
试模流程
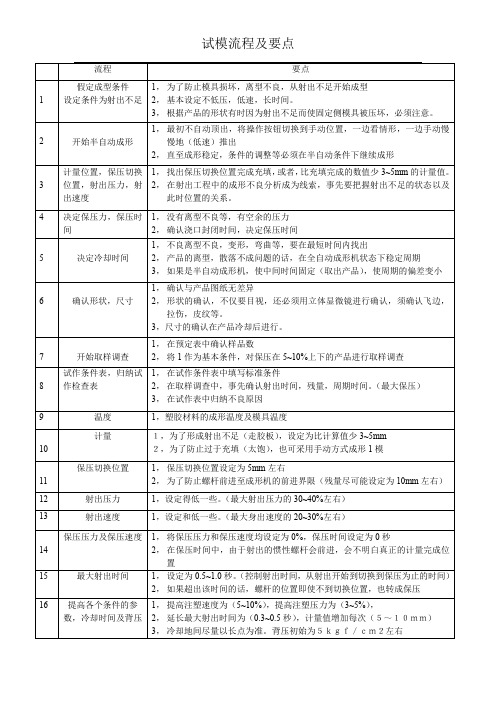
16
提高各个条件的参数,冷却时间及背压
1,提高注塑速度为(5~10%),提高注塑压力为(3~5%),
2,延长最大射出时间为(0.3~0.5秒),计量值增加每次(5~10mm)
3,冷却地间尽量以长点为准。背压初始为5kgf/cm2左右
13
射出速度
1,设定和低一些。(最大身出速度的20~30%左右)
14
保压压力及保压速度
1,将保压压力和保压速度均设定为0%,保压时间设定为0秒
2,在保压时间中,由于射出的惯性螺杆会前进,会不明白真正的计量完成位置
15
最大射出时间
1,设定为0.5~1.0秒。(控制射出时间,从射出开始到切换到保压为止的时间)
10
计量
1,为了形成射出不足(走胶板),设定为比计算值少3~5mm
2,为了防止过于充填(太饱),也可采用手动方式成形1模
11
保压切换位置
1,保压切换位置设定为5mm左右
2,为了防止螺杆前进至成形机的前进界限(残量尽可能设定为10mm左右)
12
射出压力
1,设定得低一些。(最大射出压力的30~40%左右)
1,不良离型不良,变形,弯曲等,要在最短时间内找出
2,产品的离型,散落不成问题的话,在全自动成形机状态下稳定周期
3,如果是半自动成形机,使中间时间固定(取出产品),使周期的偏差变小
6
确认形状,尺寸
1,确认与产品图纸无差异
2,形状的确认,不仅要目视,还必须用立体显微镜进行确认,须确认飞边,拉伤,皮纹等。
流程
要点
1
假定成型条件
设定条件为射出不足
1,为了防止模具损坏,离型不良,从射出不足开始成型
试模程序要点

试模程序要点一、前言当我们接到一副新模具需打样试模时,我们总是渴望能早一些试出一个结果且祷求过程顺利以免浪费工时并造成困扰。
但在此我们必须提醒二点:第一、模具设计师及制造技师有时也会发生错误,在我们试模时若不提高警觉,可能会因小的错误而产生大的损害。
第二、试模的结果是要保证以后生产的顺利。
若在试模过程中没有遵循合理的步骤及做适当的记录,即无法保障量产时的顺利进行。
我们更强调的是「模具运用顺利的话将迅速增加利润的回收,否则所造成的成本损失会更甚于模具本身的造价」。
二、试模前的注意事项1. 了解模具的有关资料:最好能取得模具的设计图面,详予分析,并约得模具技师参加试模工作。
2. 先在工作台上检查其机械配合动作:要注意有否刮伤,缺件及松动等现象,模向滑板动作是否确实,水道及气管接头有无泄漏,模具之开程若有限制的话也应在模上标明。
以上动作若能在挂模前做到的话,就可避免在挂模时发现问题,再去拆卸模具所发生的工时浪费。
3. 当确定模具各部动作得宜后,就要选择适合的试模射出机,在选择时应注意(a)射出容量(b)导杆的宽度(c)最大的开程(d)配件是否齐全等。
一切都确认没有问题后则下一步骤就是吊挂模具,吊挂时应注意在锁上所有夹模板及开模之前吊钓不要取下,以免夹模板松动或断裂以致模具掉落。
模具装妥后应再仔细检查模具各部份的机械动作,如滑板、顶针、退牙结构及限制开关等之动作是否确实。
并注意射料嘴与进料口是否对准。
下一步则是注意合模动作,此时应将关模压力调低,在手动及低速的合模动作中注意看及听是否有任可不顺畅动作及异声等现象。
4. 提高模具温度:依据成品所用原料之性能及模具之大小选用适当的模温控制机将模具之温度提高至生产时所须的温度。
俟模温提高之后须再次检视各部份的动作,因为钢材因热膨胀之后可能会引起卡模现象,因此须注意各部的滑动,以免有拉伤及颤动的产生。
5.若工厂内没有推行实验计划法则,我们建议在调整试模条件时一次只能调整一个条件,以便区分单一条件变动对成品之影响。
工程试模规范流程
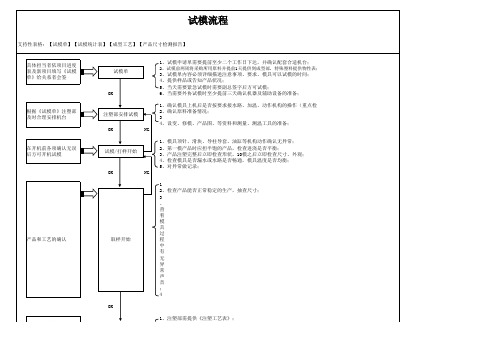
支持性表格:】
具体担当者依项目进度 表及新项目填写《试模 单》给关系者会签 OK
1、试模申请单需要提前至少二个工作日下达,并确认配套合适机台; 试模单
2、试模前两周将采购所用原料并提前1天提供到成型部,特殊塑料提供物性表;
3、试模单内容必须详细描述注意事项、要求、模具可以试模的时间; 4、提供样品或告知产品状况; 5、当天需要紧急试模时需要副总签字后方可试模; 6、当需要外协试模时至少提前三天确认机器及辅助设备的准备; 1、确认模具上机后是否按要求接水路、加温、动作机构的操作(重点检 2、确认原料准备情况; 3、T0、T1及必要时通知模具担当人、项目部等相关人员到场试模; 4、设变、修模、产品图、等资料和测量、测温工具的准备; NG 1、模具顶针、滑块、导柱导套、油缸等机构动作确认无异常; 2、第一模产品时应担半饱的产品,检查进浇是否平衡; 3、产品注塑完整后立即检查形状,10模之后立即检查尺寸、外观; 4、检查模具是否漏水或水路是否畅通,模具温度是否均衡; 5、对异常做记录; NG 1、正式取样前需要有缺料状态的80%、50%、饱和及涨模的状态; 2、检查产品能否正常稳定的生产,抽查尺寸; 3、查看模具过程中有无异常声音; 4、确认成型工艺的稳定、合理性;
根据《试模单》注塑部 及时合理安排机台
注塑部安排试模 OK
在开机前各项确认无误 后方可开机试模
试模/打样开始
OK
产品和工艺的确认
取样开始
OK 1、注塑部需提供《注塑工艺表》; 2、非正常高压高速工艺调试3模产品以便检查模具极限情况并保留样品; 3、保留正常工艺下的5模产品包括水口,标签张贴试模日期和次数; 4、通知钳工对模具分型面刷红丹并对试模异常做记录;
完成《试模单》所有要 求
基本塑模试模流程
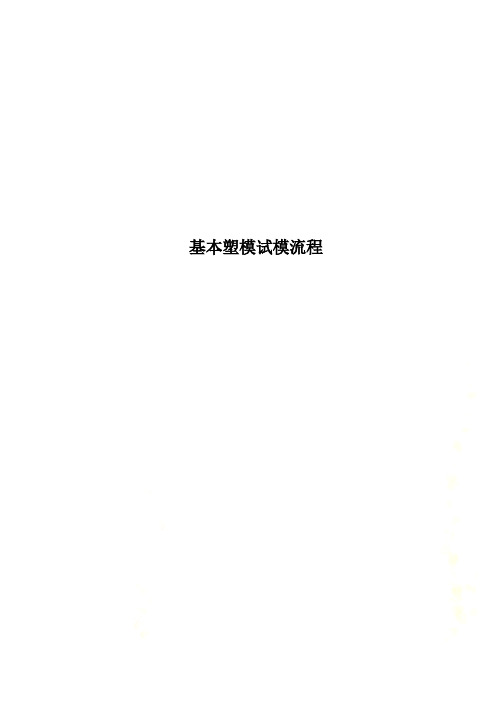
基本塑模试模流程D 基本试模程序请记住: 试模的目的是为了找出模具上的缺陷并加以修改,以适应后续的批量生产.第一步: 设定料筒温度 (根据材料供应商)• 须使用感应器测量实际熔体温度. 第二步: 设定模具温度(根据材料供应商)• 须使用感应器测量实际模腔温度.• 同时测量模腔各点温度是否平衡.要求: 温差<5°C, 最好<2°C ;否则须检查模具冷却系统.模具温度设定 °C第三步: 在无保压和保压时间的前提下,作短射填充试验(一级速度), 找出压力切换点( 即产品打满95% 的螺杆位置). 目的:• 把握熔体流动状态; 验证浇口是否平衡( 注意: 模温不均匀,对于尤其是热敏性材料及浇口很小的情况下,些微的模温差异都会造成自然平衡流道的不平衡).• 查看熔体最后成型位置排气状况, 决定是否需要优化排气系统第四步: 找出优化的注射速度(一级) , 即: 转压注射压力最低时的注射速度. 例如:• 同时获得实际注射压力( 注意:设定的注射压力必须时刻大于实际显示的射压 )- 实际注射压力取决于负载; 在其他条件不变的情况下取决于压力切换点和注注射速度 mm/s注射压力 Bar• 查看流动状态(是否有喷射等) ,产品表观以及注射压力是否过大决定是否需要流道尺1寸,浇口尺寸和位置等. .料筒温度设定 °C0,1 0,12 0,14 0,16 0,18 0,2 350 315 280 245 210 175 注射时间 [s] 注射速度 [mm/s] 注射压力 [b ar 优化设定区域 材料 注射压力 (bar) 保压压力 (bar) 模腔压力(bar) PS 700 - 1600 300 - 600 200 - 400 ABS 800 - 1600 400 - 900 350 - 550 PP 700 - 1600 300 - 600 200 - 400 PA 700 - 1600 500 - 700 350 - 700 POM 800 - 1800 800 - 1000 600 - 800 PC 1000 - 1800 600 - 1000 400 - 600 PMMA 1000 - 1600 600 - 1000 400 - 800 PC/ABS 800 - 1700 600 - 800 350 - 500 PBT 700 - 1600 500 - 800 400 - 700如图: 各种材料的一般压力范围第五步: 找出保压时间 (即浇口冷凝时间) . 每次取2模产品,然后称重(不含料头).保压时间就是产品重量开始稳定的时间. 每次加0.5s (小产品的话可以取小)保压时间 (s) 第一模产品重(g) 第二模产品重(g) 保压时间 (s) 第一模产品重(g) 第二模产品重(g)1 41.5 4.52 52.5 5.53 63.5 6.5保压时间=重量稳定时的时间+0.5秒• 保压时间太短: 会造使熔体从模腔内倒流,从而造成产品重量,尺寸,料垫的不稳定以及产品凹陷,空洞.• 保压时间太长: 实际上就是冷却时间, 反而会造成产品内部应力从而产生变形,裂纹等问题第六步: 找出设定的冷却时间: 不断降低冷却时间直至产品不出现缺陷的最短时间.• 通过下面的公式估算冷却时间. 如果实际找出的冷却时间和估算值相比过长, 则需考虑是否需要进行冷却系统的改进.• 查看产品各部分冷却状况是否一致, 以决定哪部分需要强化或弱化冷却.第七步: 找出保压压力(一级) :(1) 首先找出最低保压压力: 产品刚出现充模不足,凹陷,内应力,尺寸偏小等问题时的保压压力.(2) 然后找出最高保压压力: 产品刚出现毛刺,内应力,脱模不良,尺寸扁大等问题时的保压压力.• 理想的保压压力= (Plh + Phh)/2• 分析最大保压和最低保压的范围, 并通过可能的模具修改来使他们的范围尽量扩大.• 在最低保压和最高保压之间每隔100bar 或50bar(取决于最低最高保压之间的范围)取值; 然后在取的保压压力下各生产2模;研究保压和尺寸之间的关系,以决定可接受的保压压力Ph 或修改模具尺寸.Ph =Tc = Plh = Phh = a ... 对 PC 2,17 PA 6, PBT, PE-LD 2,64 ABS, PS, SAN, PA 6.6 2,82 PE-HD, PMMA 3,00 PP 3,67 POM 4,18 ²s a ⨯≈τ第八步: 记录并保存以上工艺参数; 修模.第九步: 修模后重新试模•尽量采用和上一次相同的工艺参数. . . . . . . . . . .. ……第十步: ( 在模具修改完毕后) 在确定的参数基础上生产2小时, 取产品50模一模一模称重并测量某一或几个关键尺寸,研究重量和尺寸之间的关系, 确定可接受的重量控制偏差.•根据如下”产品模重变动范围和参数变动范围的关系”确定批量生产时参数控制范围模重偏差0.05% 0.1% 0.2% 0.4%预塑时间± 0.04s ± 0.06s 0.08s 0.13s注射时间± 0.02s ± 0.02s ± 0.04s ± 0.06s周期± 0.5% ± 0.5% ± 1% ± 1%预塑停止位置± 0.1mm ± 0.1mm ± 0.2mm ± 0.3mm料垫± 0.1mm ± 0.1mm ± 0.2mm ± 0.3mm熔体温度± 2°C ± 2°C ± 3°C ± 5°C模具温度± 1°C ± 1°C ± 2°C ± 4°C料筒温度± 1°C ± 1°C ± 2°C ± 4°C下料口温度± 1°C ± 2°C ± 3°C ± 4°C热流道温度± 1°C ± 2°C ± 3°C ± 4°C油温± 1°C ± 1°C ± 2°C ± 2°C室温± 2°C ± 2°C ± 3°C ± 4°C模腔压力± 30 ± 40 ± 60 ± 80填充压力± 10 ± 20 ± 30 ± 40保压压力± 10 ± 10 ± 15 ± 20背压± 5 bar ± 5 bar ± 10 ± 10模腔填充差异± 1% ± 1% ± 2% ± 5%转压压力± 10 ± 20 ± 30 ± 40螺杆转速± 10 ± 15 ± 20 ± 30熔体温度峰值±±±±转压时熔体温度±±±±附录一:试模时的注意点1. 试模前必须确认:(1)材料: 正确的材料; 清洁; 干燥彻底.(2)设备: 机床料斗,附机及所有管道,接头清洁.(3)模具: 清洁2. 选择合理的螺杆直径(即合理的机床大小):依据: (1) 一模产品的料量应占机床最大料量的30%-60%.(2) 材料在料筒内的停留时间不能超过供应商提供的最大停留时间.3. 螺杆转速的设定:原则: 尽量慢(也可使用材料供应商提供的设定范围).太快容易造成熔体过度剪切从而破裂降解, 塑化不均, 卷入气体等缺陷底线: 使预塑时间略短于冷却时间.4. 背压的设定:原则: 推荐使用材料供应商提供的背压.倾向于大的螺杆背压目标: 减小熔体塑化时的轴向差异,减少气体,塑使化均匀.---背压太小:塑化不均; 气泡; 冷料; 混色不均; 塑化时间不稳等---背压太大:材料降解; 螺杆磨损加剧; 预塑时间长; 流涎; 塑化时间不稳等5. 后松退的设定:(1) 松退量:原则: 一般以不流涎为基本原则. 对于粘度大的材料,如PC, 一般要求松退足够,如最少6mm, 以使下次注射时止回阀能够很好的关闭,从而保证料垫稳定.(2) 松退速度:原则: 尽量低. 以比螺杆旋转时后退的速度略快为底线.6. 关于多级注射, 多级保压:只有当模具无法修改而产品依然有问题时, 才考虑使用.说明: 此处的压力均为螺杆头处的压力, 若使用液压缸压力,则大致为它的1/10(根据客户习惯选择压力类型)附录二:常见模具问题造成的产品缺陷1. 浇口:(1) 尺寸过小: 注射压力过大; 喷射纹; 真空泡; 充模不足; 凹陷; 流动纹; 浇口处银纹; 浇口处晕斑;; 浇口处裂纹; 熔接痕; 麻点等(2) 位置不正确:a. 流动不稳定: 喷射纹; 流动时裹气等b. 浇口过早冷却: 真空泡; 充模不足; 凹陷等(3) 形状不正确: 浇口切割不良等(4) 浇口不平衡: 填充不平衡.2.流道:(1)尺寸过小: 注射压力过大; 真空泡; ; 凹陷; 流动纹; 熔接痕; 麻点等(2)流道不光滑: 流道粘模; 流动不稳定; 混入气体等(3)冷却不充分: 流道冷却时间长; 流道粘模等3. 排气:(1)不充分: 熔体流动末端烧焦; 充填不足; 注射压力过大等(2)尺寸过大: 排气槽位置毛边.4. 冷却系统:(1)冷却不充分(冷却效率低): 冷却时间过长(2)冷却不平衡: 产品变形.5.顶出系统:(1)顶出过长: 顶出痕过深; 顶针处滑痕等(2)顶出不平衡: 产品顶出时变形; 顶针损坏等(3)顶出不畅: 顶出时造成真空; 顶出位置未放在阻力最大处等6. 型腔:表面不光滑: 压花不均; 表面花纹; 光泽不好等。
试模标准动作流程
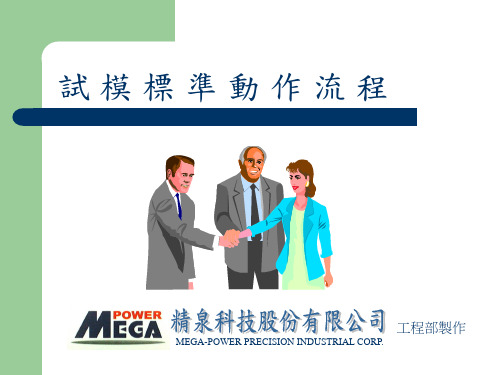
射膠行程計量
100*10 12.56*1.06*0.8 *0.8+3(殘量) =(1000/10.68)*0.8+3 ≒ 77(mm)
* 射出效率一般以80%計
2-4 短射
找出模具澆道至澆口的極限位置。 依照產品結構設定各個流動軌跡位置。 找出因注澆而產生的應力、變形、噴痕、流痕、焦化、 光澤不均、頂白、縮水、毛邊等不良現象是如何產生。 將短射過程之成品以數位相機拍攝存檔。(附圖J)
(以壓力為設定之基準) 第一段:保壓第一段壓力設定低一點,以解決毛邊問題。 第二段:保壓第二段壓力設定高一點,以解決縮水及尺寸 問題。 第三段:保壓第三段壓力設定低一點,以解決殘留應力所 造成的變形問題。
【附圖L】
保壓設定低會產生的不良 充填不足 縮水 尺寸太小 收縮太大(尺寸不安定)
保壓設定高會產生的不良 毛邊 變型(殘留應力太大) 尺寸太大 成品PL面會有小毛邊 過度充填 離模不良
3-1 射出速度設定的標準
(以速度%為設定的標準) 以速度%為設定的標準) 第一段:通常都用在充填澆道與流道,設定時使用中速到高速。 第二段:通常都用在充填澆口(gate)附近,一般用低速設定,太快會有噴 痕、起瘡(小gate時)的現象,但太慢也有充填不佳的現象。 第三段:通常都用高速設定,目的在防止唱片痕(波紋)及改善會膠線。 第四段:通常用中速或較低速度設定,目的在防止毛邊及瓦斯燒焦(因排氣 不良所造成)。 PS. 在close loop的系統中,射出壓力會隨著射出速度設定的快慢而自動調整。
殘留應力造成變形 離模不良 變形
毛邊
2
保
3
1
力
壓
四、試模後溝通與檢討
試模是尋找問題(確定是在成型哪個過程產生的) 並能找出正確解決方法。 試模是依據正確解決方法修改模具確保成型時能擁 有最大的成型調整空間。 依據前述觀念要求模具廠作對的修改。