试模流程
试模流程

试模流程1.0目的:明确项目工作职责权限,规范其工作流程。
2.0适用范围:3.0职责;3.1项目系;3.1.1 负责《模具确认表》中收集基本信息,制作初步《机种资料》;3.1.2 根据《机种资料》,申购试模材料及色粉;3.1.3 检查模具装配图、零件图、并对照客户打合内容核对图面,不符处及时与设计担当确认;3.1.4 根据T1试模日期,跟踪新模进度,(核对制模课I-M3系统计划与现场进度),并熟悉模具结构,对计划变动之状况,及时联络客户,并重新确定T1日期;3.1.5 根据T1试模日期,结合实际进度,提前一天开出《试模申请单》;3.1.6 T1样板试作前,将客户图面登记后交ISO受控并分发给相关部门;3.1.7 负责现场试模状况,跟踪、对模具问题、产品问题做详细记录,作为T1修正依据,并于次日以《模具修正/变更履历表》形式附一啤样板交样板文员,下发给模具PMC,模具课安排对模具进行维修;以对设计结果进行验证;3.1.8.a T1试做后,如产品成型条件正常,由项目工程师填写《样板检查通知单》,并附3啤条件正常样板交测量房测数,并将每次测数报告保存工程资料上;以对设计结果进行验证。
3.1.8.b T1试作后,对需二次加工(喷油、印刷、烫金绘雕等)之部品,由项目工程师联络丝喷课安排喷油治具制作,油漆样品申购、印刷鸿墨样品申购,印刷菲林、网板、钢板、治具制作、烫金治具制作,烫金纸申购等,并作如T2样板二次加工准备;3.1.8.c T1试作后,项目工程师须联络本课包装技术员,对每个部品设计包装方式(分国内、国外及厂内半成品周转等);3.1.8.d T1试作后,项目工程师对所得样板进行评估,将合格样板交样板文员处理;项目样板文员须将样板整理标识后,填表写《样板寄送单》递送给营业,由营业转交给客户,并将客户签名回传之《样板寄送单》复印一份给营业,产品每次客户回传《样板寄送单》须存档;3.1.8.f 每次模具试作后,如模具存在问题,项目工程师须对照试模结果进行《模具修正/变更履历表》的填写,现场跟进模具修改进度;适时填写《试模申请单》对修改后的模具进行试作直至模具产品均符合客户要求;3.1.9 项目文员对每套模具按模具编号及产品编号统计试模次数,对超过目标之模具及时通知项目工程师及主管,便于组织专题会议提出解决方案;3.1.10 项目文员负责对部门所需物料之申购;3.1.11 样板文员负责整理,保存每套模具之客户资料(修正及变更等);3.1.12 所有模具及移管模具的变更,项目工程师从营业处接到客户变更后,须以《模具变更/修正履历表》的形式,附一啤样板,交样板文员,下发模具PMC安排模具进行相应变更,对于只变更二次加工之部分,联络丝喷打样,并将变更后样品送给营业交客户确认变更部品取得客户承认之后,须通知样板文员填写《塑工程变更通知书》,下发相关部门,并将原件存放在每套模具File中;3.1.13 项目工程师负责已OK模具之相关资料整理,召开量产会议;3.1.14 负责对所有需二次加工部品之治具制作,辅料申购及二次加工打样;3.1.15 负责新产品之《包装指示》书制作;3.2 设计系负责客户变更及公司内部变更之相应模具图而变更;3.3 模具课3.3.1 负责所有模具按项目所发资料修正;3.3.2 模具PMC负责对所有模具进度的跟踪,对异常之情况以书面资料或邮件方式提供给项目工程师;3.4 计划课3.4.1 负责对试模料、色料等申请的受理及进度跟踪、试模料的发放;3.4.2 负责对项目所有《试模申请单》的机台安排;3.5采购课负责对项目系之申购物料进行采购;3.6 营业课3.6.1 负责项目呈送之样板递送;3.6.2 负责客户修模联络,变更联络,打样联络信息之传递;3.6.3 负责《模具OK单》的填写及安排量产或交模。
试模质量管理作业流程
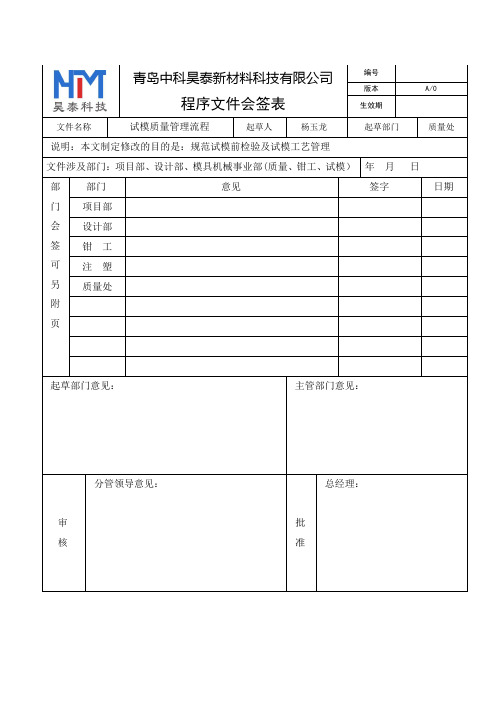
程序文件会签表
编号
版本
A/0
生效期
文件名称
试模质量管理流程
起草人
杨玉龙
起草部门
质量处
说明:本文制定修改的目的是:规范试模前检验及试模工艺管理
文件涉及部门:项目部、设计部、模具机械事业部(质量、钳工、试模)
年月日
部
门
会
签
可
另
附
页
部门
意见
签字
日期
项目部
设计部
钳工
注塑
质量处
起草部门意见:
《月度试模报表》
5.3.6.试模过程中在小批量生产时,工艺员必须检测并记录模具各点的实际温度,模温要求温差不得超过5度;
5.3.7.在完成项目经理要求的样件数量后,工艺员应验证模具动作的可靠性,按照正常生产工艺参数连续空载动作50次验证各项机构动作的可靠性;
5.3.8.试模结束后,工艺员将试模成型工艺参数、模温检测、生产周期、试模问题点记录在试模记录表上;
5.2试模前检验:
5.2.1.工艺员通过试模计划,必须提前了解模具的信息:试模用材料特性、模具的安装方式、模具的外接结构、产品结构及浇注系统等;
5.2.2.模具调至注塑车间,工艺员应在第一时间到现场检查模具外接部件:与注塑料机定位圈规格确认、注塑机顶出位置及顶出孔大小确认、水路及油路联接确认、油路控制确认、模具外围大小确认、热流道温控柜及插座确认;如发现与设备不符者,应立即通知技师整改;
青岛中科昊泰新材料科技有限公司
程序文件
编号
页次
版本
生效期
主题:
试模质量管理流程
工艺员通过试模前的检验确保模具的安装时间最短,有效地组织试模生产,不产生无效装模时间;
试模作业指导书
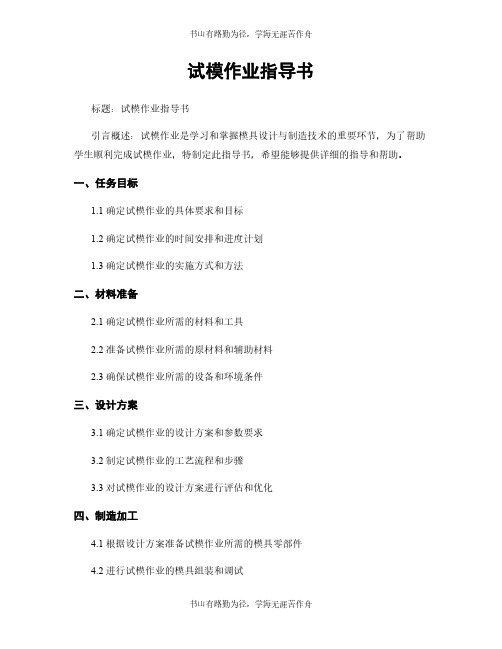
试模作业指导书
标题:试模作业指导书
引言概述:试模作业是学习和掌握模具设计与制造技术的重要环节,为了帮助学生顺利完成试模作业,特制定此指导书,希望能够提供详细的指导和帮助。
一、任务目标
1.1 确定试模作业的具体要求和目标
1.2 确定试模作业的时间安排和进度计划
1.3 确定试模作业的实施方式和方法
二、材料准备
2.1 确定试模作业所需的材料和工具
2.2 准备试模作业所需的原材料和辅助材料
2.3 确保试模作业所需的设备和环境条件
三、设计方案
3.1 确定试模作业的设计方案和参数要求
3.2 制定试模作业的工艺流程和步骤
3.3 对试模作业的设计方案进行评估和优化
四、制造加工
4.1 根据设计方案准备试模作业所需的模具零部件
4.2 进行试模作业的模具组装和调试
4.3 进行试模作业的模具试制和调整
五、试模验证
5.1 进行试模作业的成品检验和评估
5.2 对试模作业的成品进行改进和优化
5.3 对试模作业的过程进行总结和反思
结语:通过本指导书的详细指导和帮助,相信学生们能够更好地完成试模作业,提升模具设计与制造技术的水平和能力。
希望学生们认真学习和实践,取得更好的成绩和收获。
试模流程图

台州大发模具制造有限公司试模流程图<A>通知试模:其它部门【总经理、工程部(设计师)、制造部(制作组长)、品保部】得知需试模,用《内部联系条》把客户编号、模具编号、产品名称、试模胶料、数量等知会制造部文员;<B>试模通知单:制造部文员填写《试模通知单》(并登记于《试模状况记录一览表》上,每月统计公布一次),经审批,分发各单位,统一安排试模(填单前需由品保部工艺员确认试模用物料是否齐全);<C>试模前准备:①品保部工艺员专人负责试模用物料(含胶料、包装等)的出入库, 领用物料需填写《试模用料状况一览表》; ②制作组长派组员与工艺员一起领齐(运送)试模用物料,并由工艺员专人负责烘料;③注塑车间安排机台,并通知品保部工艺员; ④试模前品保部提前安排T01前点检,并填写《模具表现评估表之一(T01前)》;<D>参与试模:①由品保部工艺员通知参与试模人员,参与试模人员需在《试模情况记录表》上签到(《试模情况记录表》由制造部文员专人保管);②新模T01、T1时,制作组长、设计师、品保部人员必须到场;③新模T2以后及修(改)模试模,制作组长及品保部人员必须到场,其它人员视情况而定;<E>试模件处理:①试模件由品保部负责分类管理(试模件放于专用仓库,出入库及用途需记录);②品保部人员负责试模件包装(可请注塑车间人员帮忙);③每次试模品保部必须保留两啤以上完整试模板(含浇口);④品保部负责对试模件进行外观检测及尺寸检测,并填写《模具表现评估表之三(试模件评估)》及《首件检测报告》;⑤林助理负责对试模件送样(含包装要求);<F>试模后现场清理:①注塑车间把模具卸下,放于指定位置,并通知制造部文员;②制造部文员(含叫叉车)通知制作组长把模具拉回制作车间;③水压机、新模用温控箱等工具由品保部专人保管,制作组长领用需写借条;<G>试模记录:①试模相关人员(试模员、品保部、制造部)填写《试模情况记录表》,并交制造部文员专人保管;②品保部跟模人员填写《模具表现评估表之二(试模现场)》;③试模相关人员(试模员、品保部、制造部)如实填写《试模用料状况一览表》,并交制造部文员专人保管;<H>修(改)模事宜:①由品保部、制造部(制作组长)把相关资料(问题点),汇总到林助理处;②由林助理出具《修(改)模通知单》,制造部修(改)模,设计师负责修改模技术支持,制造部负责进度.。
模具试模流程

4品质部检测完将检测结果及数据记录于《样品检测报告》。
5《样品检测报告》由研发部、品质部、项目部共同确认,对检测结果真实性负责。
6产品注塑成型工艺参数在确定试模OK后,由注塑技术员进行记录。
试模报告
样品检测报告
成型工艺参数表
塑胶产品检验规范
产品图纸
005
试模检讨
试模产品
3注塑生产部在试模当日前,完成原料的烘烤和配料。
4为避免其它人员等待浪费时间,注塑部技术员应提前1-2小时进行模具安装与机台调试。
注塑排产
注塑原料
安装好的模具
调试好的机台
上下模作业指导书
003
现场试模
注塑原料
安装好的模具
调试好的机台
工模部
注塑部
品质部
研发部
项目部
2H
1试模加料前应确认料斗内原料已清洗干净。
工程部:
制造部:
项目管理部:
人资行政部:
IT部:
11.编修/审批记录:
版本
编制人
审核人
编制/修订日期
修订内容及理由(摘要)
签批人
A/0
新版发行
04
PMC
PC
计划安排试模所需的机台及物料。
熟练操作办公软件,能独立安排生产计划。
05
品质部
PQE
1负责试模样品的随机抽样检测。
2对抽样样品进行尺寸、结构、外观进行检测,出具检测报告。
3试模问题点对产品质量影响的风险评估,提出改善建议。
4试模问题点改善后的跟进验证。
1熟悉模具结构。
2熟悉注塑原理及成型工艺。
项目部
营销部
客户
富士康内部资料-试模流程PPT课件.ppt

7.打出標准值產品后,模具廠及成型廠試模師依模具狀況及 成品狀況再作出下限值產品并記下成型條件.依此再試作 上限值之產品并記記下成型條件.再將保壓取消打出未保 壓成品.
8.完成三種基本條件之成型品,依其條件各備5件并作記號送 于工程師驗証其所需規格.若須作調整時,亦不會偏離此三 種成型條件規范太多,故可以很快調出工程師所需之式樣. (每次微調完成式樣時,在塑件上須編號且須作成型條件記 錄,方可送樣給工程師確認).
立、废料销毁……)
三、试 模 后
1.保压取消打出的未饱模成品2PCS 2.水口 3.尺寸上限样品2PCS及成型条件 4.尺寸下限样品2PCS及成型条件 5.较佳成型条件样品2PCS及成型条件 6.试模后模具保养 7.试模问题检讨
試模作業
15.若成品表面是否有异常现象是否有确认模具上有 相同现象
16.有咬花现象时是否有与咬花样板核对
17.有刻字、印刷时是否有与黑白稿核对并确认是否正确
18.确认结合线的位置及不当的位置
19.是否有进胶喷痕、流痕现象
20.是否有银丝现象,并确认原料干燥烘烤情形 21.是否有将试模完的样品交代后续处理事项(喷漆、组
D(油),溫度是否先行確認.(查模溫機) 2.射出料管加熱溫度是否有按照原料廠所提供的資料
及要求設定. 3.如果是熱膠道的模具,每個加熱點溫度、作動是否
正常(即溫控器與加熱器是否正常).
4.射出成型機台大小及料管直徑是否與上次試模相同.
5.射嘴與模具的澆口襯套之間是否有漏膠的現象,塑料 在射管中是否停留過久,如果有過久時是否有先行將 料管內的料射出不用.
试
模作业流程
目录
一、試 模 流 程 二、试 模 前 三、试 模 中 四、试 模 后
试模测试试验流程
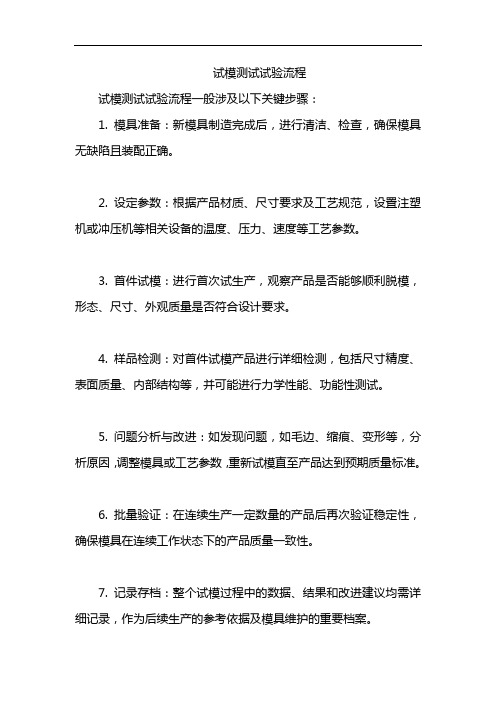
试模测试试验流程
试模测试试验流程一般涉及以下关键步骤:
1. 模具准备:新模具制造完成后,进行清洁、检查,确保模具无缺陷且装配正确。
2. 设定参数:根据产品材质、尺寸要求及工艺规范,设置注塑机或冲压机等相关设备的温度、压力、速度等工艺参数。
3. 首件试模:进行首次试生产,观察产品是否能够顺利脱模,形态、尺寸、外观质量是否符合设计要求。
4. 样品检测:对首件试模产品进行详细检测,包括尺寸精度、表面质量、内部结构等,并可能进行力学性能、功能性测试。
5. 问题分析与改进:如发现问题,如毛边、缩痕、变形等,分析原因,调整模具或工艺参数,重新试模直至产品达到预期质量标准。
6. 批量验证:在连续生产一定数量的产品后再次验证稳定性,确保模具在连续工作状态下的产品质量一致性。
7. 记录存档:整个试模过程中的数据、结果和改进建议均需详细记录,作为后续生产的参考依据及模具维护的重要档案。
erp试模流程步骤
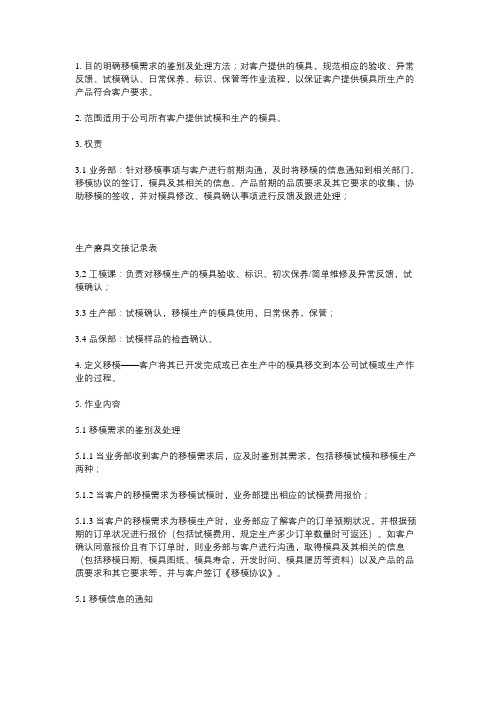
1. 目的明确移模需求的鉴别及处理方法;对客户提供的模具,规范相应的验收、异常反馈、试模确认、日常保养、标识、保管等作业流程,以保证客户提供模具所生产的产品符合客户要求。
2. 范围适用于公司所有客户提供试模和生产的模具。
3. 权责3.1 业务部:针对移模事项与客户进行前期沟通,及时将移模的信息通知到相关部门,移模协议的签订,模具及其相关的信息、产品前期的品质要求及其它要求的收集,协助移模的签收,并对模具修改、模具确认事项进行反馈及跟进处理;生产磨具交接记录表3.2 工模课:负责对移模生产的模具验收、标识、初次保养/简单维修及异常反馈,试模确认;3.3 生产部:试模确认,移模生产的模具使用,日常保养,保管;3.4 品保部:试模样品的检查确认。
4. 定义移模——客户将其已开发完成或已在生产中的模具移交到本公司试模或生产作业的过程。
5. 作业内容5.1 移模需求的鉴别及处理5.1.1 当业务部收到客户的移模需求后,应及时鉴别其需求,包括移模试模和移模生产两种;5.1.2 当客户的移模需求为移模试模时,业务部提出相应的试模费用报价;5.1.3 当客户的移模需求为移模生产时,业务部应了解客户的订单预期状况,并根据预期的订单状况进行报价(包括试模费用,规定生产多少订单数量时可返还)。
如客户确认同意报价且有下订单时,则业务部与客户进行沟通,取得模具及其相关的信息(包括移模日期、模具图纸、模具寿命,开发时间、模具履历等资料)以及产品的品质要求和其它要求等,并与客户签订《移模协议》。
5.1 移模信息的通知5.1.1 当收到客户确认移模试模的信息时,业务部与客户进行沟通,取得试模及产品的成型及外观要求等,以《内部行文》或邮件的方式通知生产和工模课;5.1.2 当签订完成《移模协议》后,业务部将收集的信息以《新产品要求输入及评审单》的方式通知到工程、生产、品保等相关部门;5.2 模具验收5.2.1 发出的客户移模信息给相关部门后,业务部安排时间与工模课去客户处对模具进行初步验收,确认OK 则业务部安排进行移模;5.2.2 针对移模生产的模具还需进行以下处理:5.2.2.1 客户模具送到工厂后,由工模课依客户提供的模具图纸进行模具的验收,并将客户提供的模具图纸存档;5.2.2.2 模具验收合格后,工模课对模具进行初次保养,有需要时进行简单的维修,并将相关信息及时反馈到业务部,业务部依据《客户财产管理程序》建立《客户财产清单》;5.2.2.3 模具验收不合格时,工模课及时将信息反馈到业务部联络客户进行处理。
注塑专业试模现场试模作业流程标准
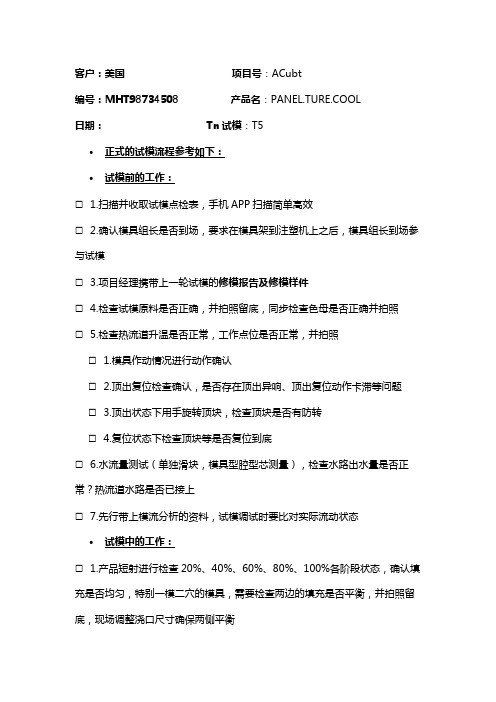
客户:美国项目号:ACubt编号:MHT98734508 产品名:PANEL.TURE.COOL日期:Tn试模:T5•正式的试模流程参考如下:•试模前的工作:□ 1.扫描并收取试模点检表,手机APP扫描简单高效□ 2.确认模具组长是否到场,要求在模具架到注塑机上之后,模具组长到场参与试模□ 3.项目经理携带上一轮试模的修模报告及修模样件□ 4.检查试模原料是否正确,并拍照留底,同步检查色母是否正确并拍照□ 5.检查热流道升温是否正常,工作点位是否正常,并拍照□ 1.模具作动情况进行动作确认□ 2.顶出复位检查确认,是否存在顶出异响、顶出复位动作卡滞等问题□ 3.顶出状态下用手旋转顶块,检查顶块是否有防转□ 4.复位状态下检查顶块等是否复位到底□ 6.水流量测试(单独滑块,模具型腔型芯测量),检查水路出水量是否正常?热流道水路是否已接上□7.先行带上模流分析的资料,试模调试时要比对实际流动状态•试模中的工作:□ 1.产品短射进行检查20%、40%、60%、80%、100%各阶段状态,确认填充是否均匀,特别一模二穴的模具,需要检查两边的填充是否平衡,并拍照留底,现场调整浇口尺寸确保两侧平衡□ 2.用高温高速高压非正常工艺调试,此三模产品用来修模检讨评审用□ 3.对模具进行外观及细节检查,是否符合客户的模具标准,如若对标准不熟悉的最好带上客户的模具标准□ 4.模具问题点的判断基本思路:□ 1.正常出模的零件状态进行检查,确认问题点□ 2.开模后不要顶出,检查产品是否存在异常,确认是否由开模引起的问题。
常见问题有皮纹后粘模拉伤□ 3.顶出2~5mm, 手动慢速顶出,检查有问题的部位,确认是否顶出不平衡、局部粘模、吸腔等问题□ 4.顶出完全后,再检查产品,会否存在产品粘顶块单边跑等问题,取件是否能正常取出□ 5.模具基本试模照片拍摄:□ 1.模具合模状态照片、型腔侧照片、型芯侧照片□ 2.顶出状态、复位状态、开模后不顶出状态等,确认模具动作OK□ 3.热流道系统照片:热流道点位位置、热流道温控点数量、顺序阀浇口□ 4.原料包装袋照片□ 5.其余细节问题点等照片□ 6.对成型完整的零件进行检查,确认产品是否符合数据定义,产品质量是否达到寄样品质要求□7.对比上一轮的修模报告和修模样件,对比问题点关闭率,现场能优化的尽量优化,现场对比后生产本次修模合格率□8.签字封样生产,每件产品背面标识序号,并测量产品重量、检查现场收缩率尺寸,同时拍照留底□9.生产的零件需要安排飞边修剪的,同样需要限样描述清楚,以便修边人员操作□10.依照正常客户需求的零件数量增加5Pcs生产,其中2Pcs作为内部修模检讨用(项目和钳工各1Pcs)其余3Pcs作为品质检查使用(CMM、尺寸检查等)□11.项目自行留底的两模样品需要连同浇口(浇口需要记号笔标注)一起,以便后期分析,如若是潜伏浇口的一样要留存□12.生产实际每次产品数量的一半后测量模温,每20Pcs后检测模温,表面温差控制在±5℃以内□13.模具需要在机器上加温状态空打4小时,空打完成之后再依标准工艺生产5模样件,对比样件情况(模具量产试验需求)□14.记录注塑机参数,并拍照留底,以便后续调取使用•试模后的工作:□ 1.生产完毕后需涂红丹验证合模情况并拍照留底,红丹合模不良的需要通知钳工到现场进行参与□ 2.试模现场问题点会判,需要技术支持的部分,可要求对应项目总监、设计组长等参与支持□ 3.生成试模记录单,并在上面会签,同时扫描到手机APP里存档。
外发试模工作流程图
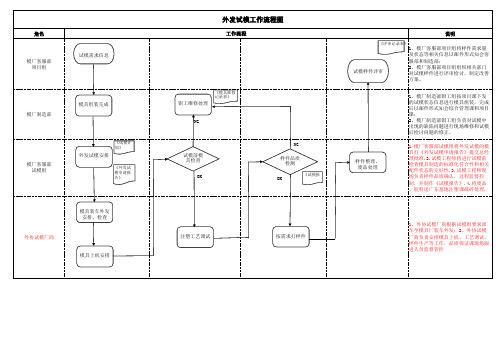
模厂客服部 项目组
试模需求信息
模厂制造部
模厂客服部 试模组
模具组装完成
外发试模安排
《试模计 划》
《外发试 模申请 安排、检查
模具上机安排
外发试模工作流程图
工作流程
钳工维修处理
《模具维修 记录表》
NG
试模前模 具检查
OK
NG
样件品质 检测
《试模报
OK
注塑工艺调试
按需求打样件
1.模厂客服部试模组将外发试模的模 具打《外发试模申请报告》提交总经 理批准.2.试模工程师将进行试模前 检查模具制造的标准化符合性和相关 配件状态的完好性.3.试模工程师现 场负责样件品质确认,过程监督控 制,并制作《试模报告》.4.将废品 、胶料送广东基地注塑课破碎处理.
1、外协试模厂商根据试模组要求派 车至模具厂装车外发;2、外协试模 厂商负责安排模具上机、工艺调试、 样件生产等工作,品质保证课现场跟 进人员监督管控
说明
《评审记录表》
1、模厂客服部项目组将样件需求量
及状态等相关信息以邮件形式知会客
服部和制造部;
试模样件评审
2、模厂客服部项目组组织相关部门 对试模样件进行评审检讨,制定改善
方案。
样件整理、 废品处理
1、模厂制造部钳工组按项目课下发 的试模状态信息进行模具组装,完成 后以邮件形式知会综合管理课和项目 课; 2、模厂制造部钳工组负责对试模中 出现的缺陷问题进行现场维修和试模 后检讨问题的修正。
冲压模具试模报告模板

冲压模具试模报告模板一、试模目的说明试模的目的是什么,例如:检查模具的制造质量、验证模具设计是否合理、确认模具的寿命等。
二、试模条件1.材料:说明试模所使用的材料种类和规格。
2.轧辊:说明轧辊的直径、柔度和工作状况。
3.润滑:说明使用的润滑剂种类和润滑方式。
三、试模装置1.模具尺寸:列出模具的尺寸和毛坯的尺寸。
2.模具材料:说明模具所使用的材料种类和规格。
3.模具结构:用文字或图纸简要描述模具的结构。
4.模具制造:说明模具的加工工艺和加工精度。
四、试模流程1.试模前准备:检查模具和轧辊是否清洁,调整模具的位置和固定方式。
2.试模过程:按照设定的参数进行模具试模,包括试模速度、模具的运动轨迹等。
3.试模结果:记录试模过程中的问题和异常情况,记录试模的周期和次数。
五、试模结果1.表面质量:对试模的毛坯进行外观检查,包括表面是否有划痕、变形等。
2.尺寸精度:对试模的成品进行尺寸测量,检查尺寸是否符合要求。
3.模具使用寿命:记录试模过程中模具的使用寿命,包括可以试模的次数和模具的损耗情况。
六、试模结论根据试模结果,给出对模具的评价和结论,例如:模具质量良好,符合设计要求,或者模具存在一些问题,需要进行修复或改进。
七、优化建议针对试模过程中出现的问题,提出合理的优化意见,包括调整模具的结构、改变模具材料、修改模具的加工工艺等。
八、试模总结对整个试模过程进行总结,包括试模的目的是否达到、试模结果的准确性和稳定性等方面进行评价。
以上是一个冲压模具试模报告的简单模板,可以根据实际情况进行修改和完善。
在撰写报告时,要注意提供足够的数据和细节,客观地记录试模过程和结果,以及给出合理的结论和建议。
五金模具试模报告

五金模具试模报告背景介绍五金模具是指用于制造五金制品的模具,其在五金制造工业中起着至关重要的作用。
试模是在模具制造完成后进行的一项关键测试,目的是验证模具的设计和制造是否符合预期,并对模具进行必要的调整和改进。
试模流程试模流程通常包括以下步骤:1. 准备工作试模之前,需要准备好必要的设备和材料,例如模具、试模机器、模具调整工具、试模材料等。
2. 安装模具将模具正确安装到试模机器上,确保模具与机器之间的连接稳固可靠。
3. 调整模具根据试模的要求,进行必要的模具调整。
这可能包括模具的开合距离、注塑压力、温度等参数的调整,以及模具零件的更换和修正。
4. 准备试模材料根据模具的设计要求,准备好试模所需的材料,例如塑料颗粒、金属板材等。
5. 进行试模将试模材料放入模具中,然后启动试模机器,进行试模操作。
试模操作过程中需要密切观察模具的工作状态,包括模具的开合、注塑过程中的材料流动情况等。
6. 检查试模结果试模完成后,取出试模制品,进行质量检查。
检查的重点包括产品的尺寸精度、表面光洁度、材料的熔融度等。
7. 分析试模问题如果试模结果不符合预期,需要进行问题分析,找出问题的原因。
可能的问题包括模具设计不合理、模具制造质量不达标等。
8. 调整和改进根据试模问题的分析结果,对模具进行必要的调整和改进。
这可能包括模具结构的优化、材料的更换,以及加工工艺的调整等。
9. 重新试模完成模具的调整和改进后,再次进行试模,重复上述步骤,直到试模结果符合预期为止。
试模的意义试模是五金模具制造过程中不可或缺的一环,具有以下重要意义:1.验证模具设计:通过试模可以验证模具的设计是否合理,是否能够满足产品的制造要求。
2.发现问题和缺陷:试模过程中,可以发现模具设计或制造中存在的问题和缺陷,及时进行改进。
3.提高生产效率:通过试模可以调整和优化模具的工作参数,提高生产效率和产品质量。
4.降低成本:试模可以帮助发现并解决模具制造中的问题,避免不必要的资源和材料浪费,从而降低制造成本。
试模、打板作业流程

打板技术要求(工程部填写)
□A 级标准 □B 级标准 □C 级标准
尺寸 □按图纸 □按样板 □客户要求
结构 □按图纸 □按样板 □客户要求
色粉编号
外观 □按样板 □客户要求
包装
油墨
菲林编号
工程部审核
总经理批准
打板令
供应商:
客户/机型:
货仓部 开始交货日期:
月
注塑课 开始生产日期:
月
喷丝课 开始生产日期:
5.1.4 进度跟踪/异常反馈 5.1.4.1 工模部、工程部、注塑课、喷印课都必须按《打板评审表》上 回复的完成时间完成相应的打板任务,当有外界因素制约到本 部门的生产,会导致计划无法按时达成时,必须填写《内部异 常联络单》反馈相关单位,由工程的项目工程师对责任单位进 行跟踪。 5.1.4.2 若按打板顺序,任一单位未及时反馈异常及追踪下游单位导致 无法按时交板,责任由各部门共同承担;若上游及时提报异常, 但责任单位未及时处理将直接追究异常单位的责任,且将给予 经再三追踪仍无处理结果的单位行政处罚措施,并列入当月绩 效考核范围。 5.1.4.3 由工程部的工程师对所跟踪客户/机型,进行打板全程跟进。 5.1.4.4 若客户要求配色方案打板时,则开发部人员需主动至车间指导, 确认。 5.1.4.5 打板过程: A. 若注塑完成打板后,须填写《入库单》将样板入库至样板房; B. 由样板管理员通知喷印课至样板房领素材打板; C. 若有配色上的需要,打板时由喷印课通知开发人员至喷印课现 场指导打板。 D. 参照 5.1.7 执行。
月
特别要求:
本厂机型:
订单数量:
日
完成交货日期:
月
日
完成交货日期:
月
日
注塑模具试模流程
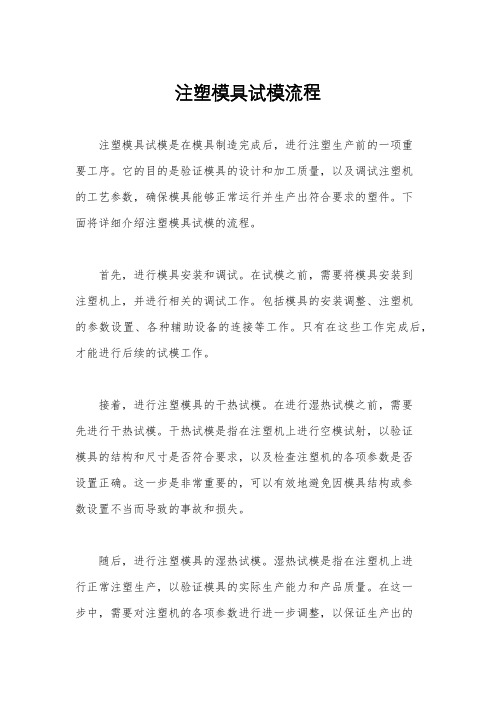
注塑模具试模流程注塑模具试模是在模具制造完成后,进行注塑生产前的一项重要工序。
它的目的是验证模具的设计和加工质量,以及调试注塑机的工艺参数,确保模具能够正常运行并生产出符合要求的塑件。
下面将详细介绍注塑模具试模的流程。
首先,进行模具安装和调试。
在试模之前,需要将模具安装到注塑机上,并进行相关的调试工作。
包括模具的安装调整、注塑机的参数设置、各种辅助设备的连接等工作。
只有在这些工作完成后,才能进行后续的试模工作。
接着,进行注塑模具的干热试模。
在进行湿热试模之前,需要先进行干热试模。
干热试模是指在注塑机上进行空模试射,以验证模具的结构和尺寸是否符合要求,以及检查注塑机的各项参数是否设置正确。
这一步是非常重要的,可以有效地避免因模具结构或参数设置不当而导致的事故和损失。
随后,进行注塑模具的湿热试模。
湿热试模是指在注塑机上进行正常注塑生产,以验证模具的实际生产能力和产品质量。
在这一步中,需要对注塑机的各项参数进行进一步调整,以保证生产出的塑件符合客户的要求。
同时,还需要对模具的冷却系统、顶针系统、脱模系统等进行全面检查,确保模具能够正常运行。
最后,进行塑件的质量检验和调整。
在试模完成后,需要对生产出的塑件进行全面的质量检验,包括尺寸、外观、物理性能等方面。
如果发现有不合格的塑件,需要及时找出问题原因,并对模具或注塑机进行相应的调整和修正。
只有确保生产出的塑件符合要求,才能正式投入生产。
总之,注塑模具试模是注塑生产中非常重要的一环,它直接关系到模具的使用效果和塑件的质量。
只有严格按照试模流程进行操作,并不断优化和改进工艺,才能保证模具生产出高质量的塑件,达到预期的生产效果。
试模流程

2计划员汇总《试模计 划表》
2计划员
2.《试模计划表》 QR-M-项-008 《试模申请单》 QR-M-制-009
3.填写《试模申请 单》
3计划员/项目工程师/制 模组长 3.《试模申请单》 QR-M-制-009 《制造三部(第__周)生产 日计划表 》QR-M-试-015 4.《试模申请单》 QR-M-制-009 5.品质检验员
6.计划员依《制造三部(第__周)生产日计划表》及本日实际到达之模具,安排当 天的试模工作,生产科接收《试模申请单》,同时在表单上面记录模具实际到达制造 三部的时间。 7.1.计划员依据《制造三部(第__周)生产日计划表》判定是否需外协试模,如果 机台排定不能满足待试模具之时间要求,通知项目负责人,协商是改期还是外协试 模。如果项目负责人确认可以改期,与计划员确定时间后,计划员更新汇总的《制造 三部(第__周)生产日计划表》中的待试模时间.如果不能改期,申请外协试模,进 入外协试模流程。改期确认可行后,模具进入待试模状态,计划员安排后续试模。 7.2.因机台数量、机台吨位或类型(如压铸模)不能满足要求,进入外协试模流程。 计划员在《试模申请单》上勾选外协项,制造三部经理审批《外协试模申请单》, 计划员将审批后的《外协试模申请单》下半联给外协采购员,外协采购员凭单联系 经《新制造供方评审流程》评审合格的外协试模供应商,同时依供应商回复时间邮 件通知项目工程师。项目工程师向综合管理部后勤科申请安排车辆,并通知相关部 门分别准备试模所需工具。具体如下:制造三部生产科准备:温控箱,热流道插座,水 管,油管,试模报告表格,测温器,试模材料(提前烘好),纸箱,气泡袋,白电油,布碎, 修批锋刀,胶袋,模温机等;制模科准备:模具总装图,相机,修模工具箱等。相关人 员随模具出厂。 8.生产科按照计划员制定的《制造三部(第__周)生产日计划表》安排每日生产计 划,在每天上班前填写《机台生产安排表》悬挂在机台上,通知到所有装模员每台 机的日生产安排。 9.生产科装模员依据《试模申请单》的要求打样,首样打出后,通知制模科长/跟模 工程师确认。如果为T1试模,制造三部文员需通知相关人员(项目负责人,制模科 长,设计组长/设计工程师可视模具难易程度决定是否参加),现场签到,记录在《模 具现场验收记录表》上,试完模后由制造三部文员做成电子档,其它试模需通知相 关的人员,依《试模申请单》上勾选为准。 10.样品初步判定。如《试模申请单》上写明无需向客户送样,则无需判定人员签 样;如果需要向客户寄样时,项目工程师书面通知制造三部品质QA客户的品质要 求,并在现场签样,品质IPQC 检验员依项目签的限度样件及《试模样件检验作业指 导书》进行检验判定。生产科装模员根据判定结果打样,如果OK,依《制造三部日 生产计划表》上注明的数量打样;如果NG,依《试模申请单》上注明自留数量打 样。试完模后,制造三部文员归档《试模申请单》,并做好试模次数统计工作,将次 数统计在《项目部模具登记表》中。同时,制造三部文员须于当天(如果为晚上试 模,则在第二天上午)内将自留样件依《试模申请单》上对应各部门的数量送至相 关部门人员手中,同时相关人员签收《试模样品签收记录表》,注意自留样件需留 水口并保持自然状态,不要做人工修整,同时将《试模报告》送至相关部门人员手 中,并录入服务器共享档案中。 11.判定OK后可以进行送客户样品打样时,装模员将IPQC判定合格的样件(需贴有QC PASS标签),依《试模样件包装及出货作业指导书》包装好。打包好后需在外箱上 做好标记(模号,数量等),并放置于专用置场。IPQC检验员进行包装和数量确认后封 箱(《试模报告》(如需要时)等放入其中),并在外包装标签上盖合格章。封箱OK 后,IPQC立即通知项目负责人送样。制造三部文员提供一件产品到品质部,由品质 部负责向技术中心测量室提出测量申请,技术中心测量完成后将报告放置在服务器 上共享。
- 1、下载文档前请自行甄别文档内容的完整性,平台不提供额外的编辑、内容补充、找答案等附加服务。
- 2、"仅部分预览"的文档,不可在线预览部分如存在完整性等问题,可反馈申请退款(可完整预览的文档不适用该条件!)。
- 3、如文档侵犯您的权益,请联系客服反馈,我们会尽快为您处理(人工客服工作时间:9:00-18:30)。
异常
将报告提交主管确认
判断修改方向,提出量测数据
取连续生产尺寸ok样品量测 生产10PCS 工程确认尺寸OK后取连续生产 工程协调,制三配合 确认成品相关功能 功能OK后开 30PCS
判断异常原因,提出功能数据 -存档
,<<测ቤተ መጻሕፍቲ ባይዱ联络单>>给品保确认功能
品保确认OK后与生管协调,由生管开M/O量试 开《量试通知单》 注意各制程是否混料
*试模材料暂存现场需标识清楚
试模作业流程
主导 单位
品保 生管 工程 仓库 制造 工程 工程 品保 制三 工程 品保 生管 工程 工程
项目
进料检验 安排机台 试模联络函 发料 架模 试模 量测数据 确认数据 组装成品 测试功能 确认功能 安排机台 量试通知单 各制程品质确认
备注
确认:厚度,宽度(1米取5个点各取左右尺寸)硬度3个点 进料检验OK后 与生管员,生管主管协调,电话+Mail 发行给相关单位《试模联络函>> 工程协调,仓管人员发料 冲压件:钟崇亮 制造配合,制一 :梁鹏程 修复:异常时配合调整模具 制六:肖朝辉 -记录试模,模具调整条件 塑胶 2CAV -存档 -存档 塑胶:李卫东