SolidWorks自顶向下装配设计(自制教程)
自顶向下设计

自顶向下(Top-down)设计方法目前,很多人在利用三维软件进行机械产品设计时,首先设计好各个零部件,然后在组件模式下将这些零部件通过匹配、对齐、插入、相切等约束进行装配。
如果在装配过程中发现干涉现象或者某些零部件根本安装不上去等等,这时需要对零部件进行重新设计与装配,而在装配过程中存在很多父子关系,当修改完某些零件后,会发现以这些零件的点、线、面为基准的其它零件装配不上去,缺失装配基准,这样会造成蝴蝶效应,更严重的是有时候还必须从头开始进行装配,大大延长了设计周期,降低了设计效率。
这是一种传统的自底向上的设计方法,由于事先没有一个很好的规划,没有一个全局的考虑,修改起来特别麻烦,重复工作量大,造成人力和时间的浪费,这对产品快速推出市场有很大的影响。
为了缩短设计周期,提高设计效率,吸音板自动生产线布料机的设计采用了与之相反的一种设计方法即自顶向下的设计方法。
产品的设计尤其是新产品的开发设计是一个复杂的过程,是将产品市场需求映像成产品功能要求、并将产品功能要求映像成几何结构的过程。
要实现该过程,首先要分析产品的功能要求,先设计出初步方案及装配结构草图,得到产品的功能概念模型,再对功能概念模型进行分析,设计计算,确定每个设计参数,将概念模型映像成装配体模型,通过装配体模型传递设计信息,然后各设计小组在此装配体模型的统一控制下,并行地完成各子装配体及零部件的详细设计,最后对设计产品分析,返回修改不满意之处,直至得到满足功能要求的产品。
即要经过概念设计、功能结构设计、产品详细设计及产品分析等阶段,是一自顶向下的设计过程[8],如图3.1所示。
图3.1 自顶向下设计流程Fig.3.1 Top-down design process从图3.1可以看出自顶向下设计方法强调在设计中首先从整体和全局入手,通过装配体模型自顶向下地传递总体设计信息,然后在统一模型的约束下对各个部分进行详细设计。
在整个过程中,可随时对设计进行修改。
solidworkds 自上而下设计 实例

Solidworks是一种常用的计算机辅助设计(CAD)软件,而“自上而下设计”是指从整体到细节逐步推导出设计的过程。
在Solidworks中,自上而下设计可以帮助工程师更好地组织和管理复杂的设计项目,提高设计效率和质量。
1. 介绍Solidworks自上而下设计的概念在Solidworks中,自上而下设计是指在开始进行具体部件设计之前,先从整体结构和功能出发进行设计规划。
通过建立上层装配,确定整体的尺寸、结构和功能要求,再逐步细化为具体的零部件设计。
这种设计方法能够帮助工程师更好地掌握整体设计方向,确保各个部件之间的协调和一致性。
2. Solidworks自上而下设计的优势在实际工程项目中,采用自上而下设计方法可以带来多重优势。
可以更好地协调各个部件之间的关系,避免设计冲突和重复工作。
可以更好地满足整体设计要求,确保各个部件的功能和结构符合整体设计目标。
还可以提高设计的灵活性和可维护性,便于后续的修改和更新。
3. Solidworks自上而下设计的实际应用举一个实际的案例来说明Solidworks自上而下设计的应用。
比如在设计一个复杂的机械装置时,工程师可以首先建立整体的装配结构,确定各个部件之间的相对位置和运动关系。
然后再逐步细化为具体的零部件设计,确保每个部件都能够完美配合整体装配,并满足设计要求。
这样一来,不仅可以更好地管理和控制设计进度,还能够更好地保证设计质量和可靠性。
4. 个人观点和理解在我看来,Solidworks自上而下设计是一种非常值得推荐的设计方法。
它能够帮助工程师更好地把握设计方向,提高设计效率和质量,同时还能够增强设计的可维护性和可扩展性。
在实际应用中,需要结合具体的项目需求和团队协作方式,灵活运用自上而下设计方法,才能发挥其最大的优势。
总结回顾:通过对Solidworks自上而下设计的介绍和应用案例,我们可以看到这种设计方法的重要性和价值所在。
在实际工程项目中,采用自上而下设计方法可以带来诸多优势,提高设计效率和质量。
Solidworks自顶向下装配设计实例
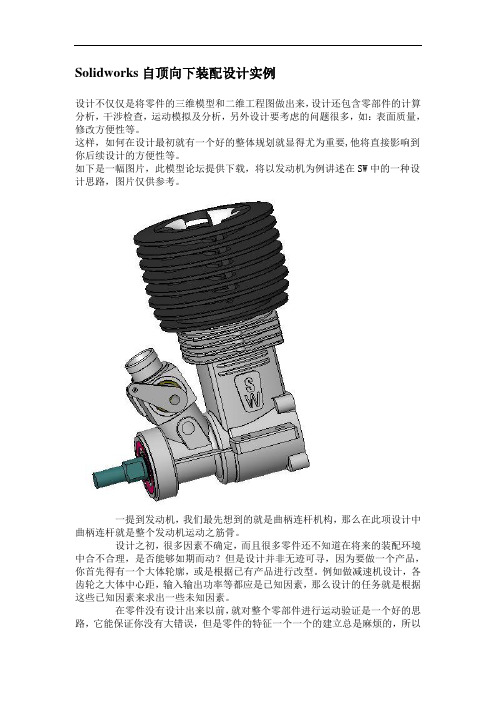
Solidworks自顶向下装配设计实例设计不仅仅是将零件的三维模型和二维工程图做出来,设计还包含零部件的计算分析,干涉检查,运动模拟及分析,另外设计要考虑的问题很多,如:表面质量,修改方便性等。
这样,如何在设计最初就有一个好的整体规划就显得尤为重要,他将直接影响到你后续设计的方便性等。
如下是一幅图片,此模型论坛提供下载,将以发动机为例讲述在SW中的一种设计思路,图片仅供参考。
一提到发动机,我们最先想到的就是曲柄连杆机构,那么在此项设计中曲柄连杆就是整个发动机运动之筋骨。
设计之初,很多因素不确定,而且很多零件还不知道在将来的装配环境中合不合理,是否能够如期而动?但是设计并非无迹可寻,因为要做一个产品,你首先得有一个大体轮廓,或是根据已有产品进行改型。
例如做减速机设计,各齿轮之大体中心距,输入输出功率等都应是已知因素,那么设计的任务就是根据这些已知因素来求出一些未知因素。
在零件没有设计出来以前,就对整个零部件进行运动验证是一个好的思路,它能保证你没有大错误,但是零件的特征一个一个的建立总是麻烦的,所以我们在SW中用线条来代替实体的零件进行运动模拟,以期在设计之初最大程度的减少工作量,而直接看到最终运动结果。
这也如在3D Max在做人物动画时先绘制骨骼,然后再往上赋予肌肉的原理是一样的。
上图的线架构运动模拟是如何建立的?第一步,建立曲轴线模型如图,然后将其存成一个零件。
注意在其曲拐中间部位建立一基准平面,以备后来装配之需。
同时大家也注意到,此图片是用JPEG格式存成的,所以不太清晰,而同类图片(颜色不丰富)的话用GIF格式则效果较好,以下的图片全采用了GIF格式。
第二步,建立连杆线条模型。
第三步,建立活塞线条模型。
本来是可以用一个圆圈代替的,但为了形像一点用了两个圆。
第四步,建立缸套。
简单一点,用一个圆代替。
第五步,建立一装配体,将以上四文件拖入装配体中,注间将拖入的第一个零件高为浮动,我在此先拖入曲轴。
solidworks装配体教程
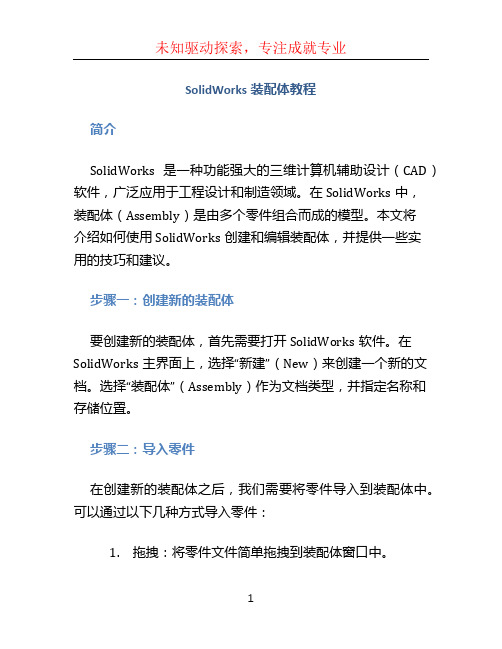
SolidWorks装配体教程简介SolidWorks是一种功能强大的三维计算机辅助设计(CAD)软件,广泛应用于工程设计和制造领域。
在SolidWorks中,装配体(Assembly)是由多个零件组合而成的模型。
本文将介绍如何使用SolidWorks创建和编辑装配体,并提供一些实用的技巧和建议。
步骤一:创建新的装配体要创建新的装配体,首先需要打开SolidWorks软件。
在SolidWorks主界面上,选择“新建”(New)来创建一个新的文档。
选择“装配体”(Assembly)作为文档类型,并指定名称和存储位置。
步骤二:导入零件在创建新的装配体之后,我们需要将零件导入到装配体中。
可以通过以下几种方式导入零件:1.拖拽:将零件文件简单拖拽到装配体窗口中。
2.插入:选择“插入组件”(Insert Component),然后选择要导入的零件文件。
3.复制:可以复制和粘贴之前已经存在于装配体中的零件,以节省导入的步骤。
步骤三:组装零件在导入零件之后,我们需要将它们组装在一起以创建完整的装配体。
可以使用以下工具和技巧进行组装:1.对齐:使用“对齐”(Align)工具将零件的特定面对齐,确保装配体的准确性。
2.关系:使用“关系”(Mate)工具添加关系,如平行、垂直、共线等,以确保零件之间相对位置的正确性。
3.约束:使用“约束”(Constraint)工具对零件进行约束,例如固定、旋转、平移到指定位置等。
步骤四:调整装配体一旦完成零件的组装,可能需要对装配体进行调整以满足设计要求。
以下是一些常用的调整方法:1.改变尺寸:可以通过编辑零件的尺寸来调整装配体的大小和形状。
2.旋转和移动:可以通过旋转和移动零件来调整它们之间的相对位置。
3.更换件号:可以通过更换零件的属性来替换装配体中的零件,并实时预览更改。
步骤五:创建装配剖面有时,我们需要创建装配体的剖面以更好地展示内部结构。
以下是创建装配剖面的步骤:1.选择“标注剖面”(Section View)工具。
SolidWorks装配教程
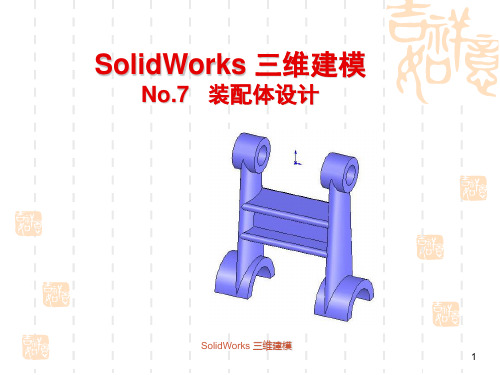
“装配体”工具栏—>
工具—>干涉检查
动态干涉:旋转或移动零部件的过程中,可以进行动 态的干涉检查或动态计算零件间的间隙。
SolidWorks 三维建模 7
装配
6、爆炸视图
作用:分离装配体中的零部件以便查看装配体的构成。 “装配体”工具栏—>爆炸视图,选中”拖动后自动调 整零部件间距”,在图形区全选装配体,单击“应用”
特征驱动阵列(以一个零件上的已有阵列为参考 对零部件实施阵列操作)
SolidWorks 三维建模 5
装配
配合实例:万向联轴节装配体
零件位置: 安装目录\samples\tutorial\AssemblyMates
SolidWorks 三维建模 6
装配
5、干涉检查
静态干涉检查:对装配体中所有的零件或选择的零件 进行检查
SolidWorks 三维建模 8
SolidWorks 三维建模 4
装配
4、调整零件位置
为了准确装配零件,需要将零件在装配前调整到安装位 置附近,朝向要和最终的安装形态大致相同。
移动:工具图标;鼠标左键;三重轴 旋转:工具图标;鼠标右键;三重轴 镜向:插入—>镜向零部件 阵列:插入—>零部件阵列
线性阵列:与零件环境中相同 圆周阵列:与零件环境中相同
SolidWorks 三维建模
No.7 装配体设计
SolidWorks 三维建模 1
装配
装配体设计是将各种零件导入到装配体环境中,利用配 合方式将其安装到正确的位置,使其构成一部件或机器。
1、新建装配体文件
新建—>装配体 零件环境中单击“标准”工具栏中的“装配体”按纽 装配体文件的后缀名为.sldasm。 装配体设计的基本操作步骤如下: (1) 设定装配体的第一个“地”零件,零件的原点固定在装 配环境中的原点位置,做为其他零件的参照。 (2) 将其他零部件调入装配体环境,这些零件未指定装配关 系,可以随意移动和转动,未浮动零件。 (3) 为浮动零件添加配合关系。
solidworks中装配体设计的主要方法
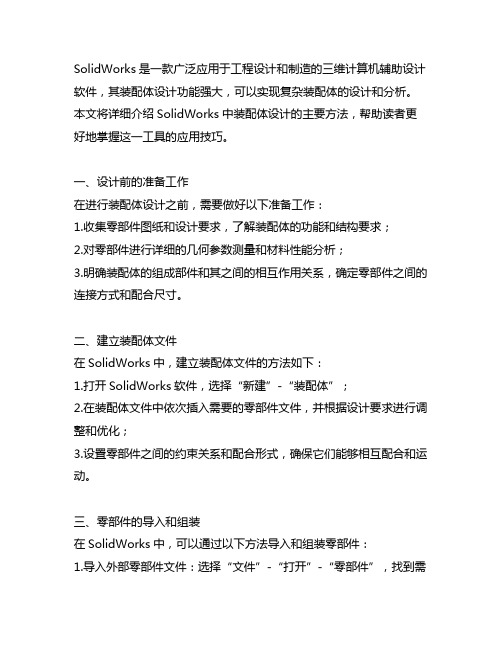
SolidWorks是一款广泛应用于工程设计和制造的三维计算机辅助设计软件,其装配体设计功能强大,可以实现复杂装配体的设计和分析。
本文将详细介绍SolidWorks中装配体设计的主要方法,帮助读者更好地掌握这一工具的应用技巧。
一、设计前的准备工作在进行装配体设计之前,需要做好以下准备工作:1.收集零部件图纸和设计要求,了解装配体的功能和结构要求;2.对零部件进行详细的几何参数测量和材料性能分析;3.明确装配体的组成部件和其之间的相互作用关系,确定零部件之间的连接方式和配合尺寸。
二、建立装配体文件在SolidWorks中,建立装配体文件的方法如下:1.打开SolidWorks软件,选择“新建”-“装配体”;2.在装配体文件中依次插入需要的零部件文件,并根据设计要求进行调整和优化;3.设置零部件之间的约束关系和配合形式,确保它们能够相互配合和运动。
三、零部件的导入和组装在SolidWorks中,可以通过以下方法导入和组装零部件:1.导入外部零部件文件:选择“文件”-“打开”-“零部件”,找到需要导入的零部件文件并打开;2.组装零部件:选择“装配”-“零件”,在装配面上放置导入的零部件,根据设计需求添加轴线和基准面,进行零部件的组装。
四、装配体的约束与驱动在SolidWorks中,对装配体进行约束与驱动的方法如下:1.约束零部件的相对位置:选择“装配”-“关系”-“基本关系”,通过点、面、轴线等对零部件进行约束;2.设置零部件的运动方式:选择“装配”-“驱动件”,设置驱动零部件和被驱动零部件,指定驱动方式和参数。
五、装配体的分析与优化在SolidWorks中,可以对装配体进行分析与优化,以确保设计的合理性和稳定性:1.进行结构分析:选择“评估”-“静态研究”,对装配体进行强度及刚度分析,找出可能存在的问题并进行优化;2.考虑装配体的动态特性:选择“模拟”-“动力学模拟”,对装配体进行运动学和动力学仿真,分析其运动性能和工作稳定性。
基于SolidWorks的自顶向下装配与参数化技术

基 于 S l Wok oi d r s的 自顶 向下装配 与参 数化技术
水俊 峰 吴 宗佳 陈树 晓 吴淑 芳 , , , ,王 宗彦
(. 中 北 大 学 机 械 工 程 与 自动 化 学 院 , 山西 太 原 1 0 0 5 ;2 海 军 9 5 0部 队 2 0所 一 室 ,辽 宁 大连 16 2 ) 301 . 15 4 1 0 3
络 发达 的并 行工 程 和协 同设计 。
带 。TB S的主要 功 能包 括 :① 管 理 功能 :顶层 基本 骨
架 可以被 用 来管 理大 型 的装 配设 计 ,允 许设 计 者 只调
参 数化 设计 是规 格化 、系列 化 产品 设计 的 一种 高
效 、优 质 的设计 方法 。它一般 是 指零 件 、部 件 比较 定
摘要 :介绍 了在 S l Wok oi rs中 自顶向下 的装 配设计过程和实施方 法 ,提出 以 “ d 顶层基 本骨架 ”作 为 自顶向下
设 计 时 信 息 传 递 的 桥 梁 ,并 以 具 体 实 例 实 现 了 装 配 过 程 和 参 数 化 设 计 。
关 键 词 : 自顶 向 下 ; 参 数 化 技 术 ;装 配
品 的性 能 、可维 修性 和 可 回收性 等 。传统 的产 品装 配 大 多 以零 件 几何模 型 为基 础 ,在 零件 详 细几何 模 型 的
基础 上搭 建装 配模 型 ,这 种从 零 件模 型构 建装 配模 型
的方 法称 为 自底 向上 的装 配方 法 。然 而在 实 际 的设 计
的最 基 本 的 பைடு நூலகம் 能 和 要 求 ,在 设 计 顶 层 先 构 造 出 一 个
出顶 层装 配 的基 本骨 架 到 内存 中来 控制 整 个产 品 的设 计 及 其变 更 , 顶层 基本 骨 架包 含 了重 要 的设 计基 准 , 如
详解SolidWorksTop-Down设计
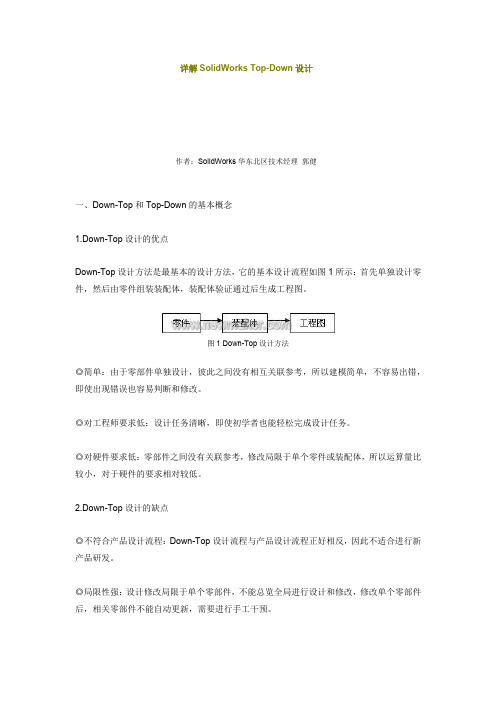
详解SolidWorks Top-Down设计作者:SolidWorks华东北区技术经理郭健一、Down-Top和Top-Down的基本概念1.Down-Top设计的优点Down-Top设计方法是最基本的设计方法,它的基本设计流程如图1所示:首先单独设计零件,然后由零件组装装配体,装配体验证通过后生成工程图。
图1 Down-Top设计方法◎简单:由于零部件单独设计,彼此之间没有相互关联参考,所以建模简单,不容易出错,即使出现错误也容易判断和修改。
◎对工程师要求低:设计任务清晰,即使初学者也能轻松完成设计任务。
◎对硬件要求低:零部件之间没有关联参考,修改局限于单个零件或装配体,所以运算量比较小,对于硬件的要求相对较低。
2.Down-Top设计的缺点◎不符合产品设计流程:Down-Top设计流程与产品设计流程正好相反,因此不适合进行新产品研发。
◎局限性强:设计修改局限于单个零部件,不能总览全局进行设计和修改,修改单个零部件后,相关零部件不能自动更新,需要进行手工干预。
3.Down-Top设计的适用范围◎SolidWorks软件初步引入,对已有2D图样进行三维转化阶段,尤其适合初学者,或者刚刚完成初级/中高级培训的企业。
◎已有产品的变型设计和局部修改,这种针对局部进行的修改适用于Down-Top设计。
4.Top-Down设计的优点Top-Down设计属于SollidWorks的高级设计方法,设计流程如图2所示。
图2 Top-Down设计流程◎符合产品开发流程:由图2可知,Top-Down设计流程与产品研发流程基本一致,符合现有的设计习惯,可以完全融合到产品研发中。
◎全局性强:总图修改后,设计变更能自动传递到相关零部件,从而保证设计一致。
◎效率高:一处修改而全局变化。
在系列零件设计中效率更高:主参数修改→零部件自动更新→所有工程图自动更新,一套新的产品数据自动生成,现在用几个小时就能完成原来几周的工作量。
在SolidWorks中实现自顶向下建模的思路
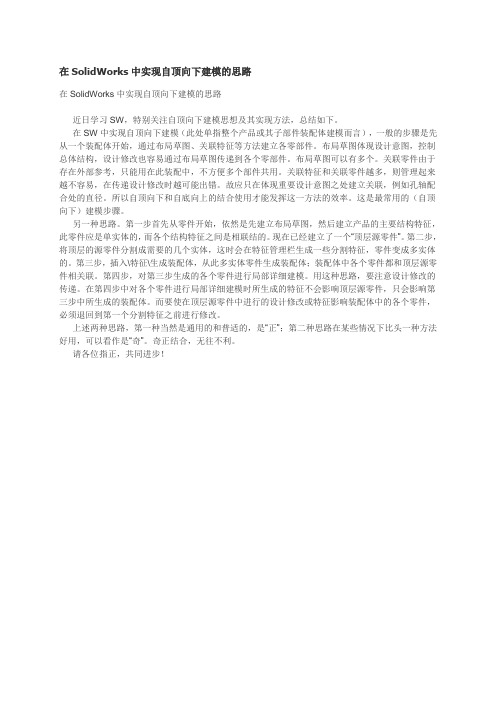
在SolidWorks中实现自顶向下建模的思路在SolidWorks中实现自顶向下建模的思路近日学习SW,特别关注自顶向下建模思想及其实现方法,总结如下。
在SW中实现自顶向下建模(此处单指整个产品或其子部件装配体建模而言),一般的步骤是先从一个装配体开始,通过布局草图、关联特征等方法建立各零部件。
布局草图体现设计意图,控制总体结构,设计修改也容易通过布局草图传递到各个零部件。
布局草图可以有多个。
关联零件由于存在外部参考,只能用在此装配中,不方便多个部件共用。
关联特征和关联零件越多,则管理起来越不容易,在传递设计修改时越可能出错。
故应只在体现重要设计意图之处建立关联,例如孔轴配合处的直径。
所以自顶向下和自底向上的结合使用才能发挥这一方法的效率。
这是最常用的(自顶向下)建模步骤。
另一种思路。
第一步首先从零件开始,依然是先建立布局草图,然后建立产品的主要结构特征,此零件应是单实体的,而各个结构特征之间是相联结的。
现在已经建立了一个“顶层源零件”。
第二步,将顶层的源零件分割成需要的几个实体,这时会在特征管理栏生成一些分割特征,零件变成多实体的。
第三步,插入\特征\生成装配体,从此多实体零件生成装配体;装配体中各个零件都和顶层源零件相关联。
第四步,对第三步生成的各个零件进行局部详细建模。
用这种思路,要注意设计修改的传递。
在第四步中对各个零件进行局部详细建模时所生成的特征不会影响顶层源零件,只会影响第三步中所生成的装配体。
而要使在顶层源零件中进行的设计修改或特征影响装配体中的各个零件,必须退回到第一个分割特征之前进行修改。
上述两种思路,第一种当然是通用的和普适的,是“正”;第二种思路在某些情况下比头一种方法好用,可以看作是“奇”。
奇正结合,无往不利。
请各位指正,共同进步!。
SW-TOPDOWN自顶向下设计

图5变型金刚设计流程
变型金刚的设计采用分割的方法,流程为:首先设计主零件,然后由主零件分割出不同的部分并分派到不同的零件内,对每个子零件进行详细设计,最后组装在一起。当设计变更时,只需修改主零件,所有的子零件会自动更新。
案例二:特种车辆设计(零部件之间相互没有运动或运动很少,但是关联很多且复杂),如图6所示的水泥散装车。
图1Down-Top设计方法
◎简单:由于零部件单独设计修改。
◎对工程师要求低:设计任务清晰,即使初学者也能轻松完成设计任务。
◎对硬件要求低:零部件之间没有关联参考,修改局限于单个零件或装配体,所以运算量比较小,对于硬件的要求相对较低。
图6水泥散装车
水泥散装车采用多体的方法设计主零件,然后把每一个实体(零件)插入到新零件中形成新的零件,然后进行详细设计,最后组装在一起。当设计变更时,只需修改主零件,所有的子零件会自动更新。
优点:所有相关零部件在同一个主零件中完成,这样就不会产生复杂的关联参考,并且修改容易。
缺点:如果零部件之间有复杂的相互运动,或者零部件非常多,这样设计就很困难。
◎系列产品设计:主产品定型后,对产品结构与参数传递进行优化。这样在系列产品设计中,通过修改参数就能自动完成大部分重复设计,从而提高设计效率。
二、Top-Down设计分类
SolidWorks的Top-Down设计方法主要分为三类:关联参考、外部参考法和布局,下面分别进行介绍。
1.关联参考
关联参考法是基础的Top-Down设计设计方法,它通过零部件之间的关联参考来传递设计关联,从而达到修改一个零部件,则相关零部件根据关联自动更新的目的。
◎对工程师要求高:由于参考关联复杂,要求工程师能够熟练操作软件,熟悉产品设计流程和变化趋势。对总工程师的要求更高,如果初始布局不合理,则需要进行大量修改,甚至因为无法修改而导致整体崩溃。
基于Solidworks软件的自顶向下装配设计

课程教育 研究
C 0 u r s e E d u c a t i o n R e s e a r c h
2 0 1 4 年2 月 上旬 刊
基于 S o l i d w 0 r k s 软件 的 自顶向下装配设计
黄 雪云
( 深圳 职 业技 术 学 院机 电工 程 学 院 广东 深圳 5 1 8 0 5 5 )
【 关键词 】 自顶向下 S o l i d wo r k s机械装配设计 【 中图分类号】 G 6 4 【 文献标识码 】 A
1 . 引言
【 文章编号 】 2 0 9 5 — 3 0 8 9 ( 2 0 1 4 ) 0 2 — 0 2 4 8 — 0 1
在 装 配特 征 树 中右 击 “ 气 缸体 骨 架 ” , 选择“ 替 换零 部 件 ” , 浏 览打 设计 之初 . 很 多因素 不确 定 . 而且 还 不 知道 各 零 件在 将 来 的 开 零部件 细 化设 计过 程 中完成 的“ 气缸 体. S L D P RT” . 完成 气缸 体 装配 环境 中是 否合 理 . 是 否 能够如 期 而动 如 果能 在 零件 设计 之 细化模 型替 换 其骨 架模 型 。 重 复上 述 步骤 , 实现 其他 零部 件替 换 , 前. 先 在 装 配状 态 下进 行 骨 架设 计 . 并对 整 个 零部 件 进行 运 动 验 最后 完成如 图 2所 示发 动机 装 配模 型 。 证. 以便 直接 看 到 最终 运动 结果 , 这 样 可 以在设 计之 初 最 大程 度
型. 包括重 要 的装 配参 数和 装 配关 系 将 气 缸体插 入 装 配体 . 并设 体 主 轴颈 孔 的尺 寸约 束 . 并 将机 体主 轴颈 草 图 圆与 曲轴轴 颈 草 图 置 为浮动 . 在 将其 三 个默认 基 准面 与装 配环 境 的相应 基 准面 设置 圆添加 “ 相等” 几何 约束 . 完成关 联设 计 “ 重合 ” 装 配关 系后 设 为 固定 : 将 两个机 体 分 别插 入 装 配体 . 并把 3 . 总 结 前视 基 准 面与 气缸 体 的前视 基 准 面“ 重合 ” . 并根据 规 划设 置机 体 自顶 向下设 计技 术 从 产品 功 能概 念 设 计 开始 .能够 有 效地 与 气缸 体 的装 配 尺 寸 : 随后 依 次插 入 曲轴 、 活 塞、 连杆 . 每插入一 把握设计意图. 使 组 织 结构 清 晰 . 便 于在 各 个子 装 配之 间迅 速 可 个零 件 骨 架时都要 按 整体 规 划设 置相 应的 装 配尺寸 和装 配 关 系 靠地 传 递设 大 限度 的
2.自顶向下装配_UG NX 8.0应用与实例教程(第3版)_[共3页]
![2.自顶向下装配_UG NX 8.0应用与实例教程(第3版)_[共3页]](https://img.taocdn.com/s3/m/cf3686b40b1c59eef8c7b4f6.png)
第7章 装配设计基础图7-2 【装配】工具条在开始进行装配时,必须合理地选取一个“基础组件”。
基础组件应为整个装配模型中最为关键的部分。
在装配过程中,各个添加组件以一定的约束关系和基础组件装配在一起,这样,各个组件和基础组件之间就形成了“父子关系”。
这个基础组件将作为各个组件的装配父对象。
7.1.2 装配方法装配就是在零部件之间创建联系。
装配部件与零部件的关系可以是引用,也可以是复制,因此,装配方式包括多零件装配和虚拟装配两种。
由于多零件装配占用内存较大,运行速度慢,并且零部件更新时,装配文件不再自动更新,因此,很少使用。
而虚拟装配则正好相反,具有占用计算机内存小,运行速度快,存储数据小等优点,并且当零部件更新时,装配文件自动更新。
UG NX 8.0的装配方法主要包括自底向上装配设计、自顶向下装配设计以,及在自底向上和自顶向下的装配方式间来回切换的混合设计。
1.自底向上装配设计自底向上装配设计方法是先创建装配体的零部件,然后,把它们以组件的形式添加到装配文件中。
这种装配设计方法是先创建最下层的子装配件,再把各子装配件或部件装配成更高级的装配部件,直到完成装配任务为止。
因此,这种装配方法要求在进行装配设计前就已经完成零部件的设计。
自底向上装配设计方法包括一个主要的装配操作过程,即添加组件。
图7-3所示为【添加组件】对话框,如果添加的文件已被加载,直接选择文件;如果添加的文件没有被加载,选择【打开】按钮选择文件。
定位方式有4种,包括绝对原点、选择原点、通过约束和移动。
●“绝对原点”方式是通过绝对坐标原点进行定位。
●“选择原点”方式是选择点进行定位。
●“通过约束”方式是使用装配约束定义装配中组件的位置。
●“移动”组件方式是使用“移动”组件选项来移动装配中的组件,可以选择以动态方式移动组件(如使用拖动手柄),也可以创建约束来将组件移到位置上。
2.自顶向下装配自顶向下装配设计主要用于装配部件的上下文中设计,上下文设计指在装配中参照其他零部件对当前工作部件进行设计,即在装配部件的顶级向下产生子装配和零件的装配方法。
使用SOLIDWORKS Treehouse实现复杂电动工具自顶向下设计
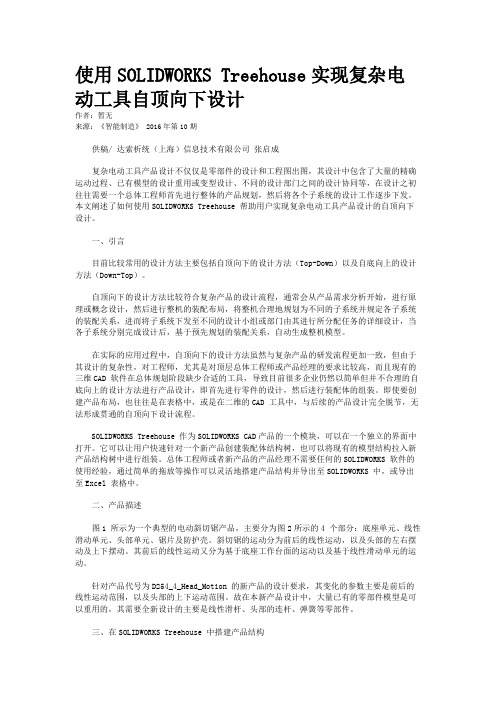
使用SOLIDWORKS Treehouse实现复杂电动工具自顶向下设计作者:暂无来源:《智能制造》 2016年第10期供稿/ 达索析统(上海)信息技术有限公司张启成复杂电动工具产品设计不仅仅是零部件的设计和工程图出图,其设计中包含了大量的精确运动过程、已有模型的设计重用或变型设计、不同的设计部门之间的设计协同等,在设计之初往往需要一个总体工程师首先进行整体的产品规划,然后将各个子系统的设计工作逐步下发。
本文阐述了如何使用SOLIDWORKS Treehouse 帮助用户实现复杂电动工具产品设计的自顶向下设计。
一、引言目前比较常用的设计方法主要包括自顶向下的设计方法(Top-Down)以及自底向上的设计方法(Down-Top)。
自顶向下的设计方法比较符合复杂产品的设计流程,通常会从产品需求分析开始,进行原理或概念设计,然后进行整机的装配布局,将整机合理地规划为不同的子系统并规定各子系统的装配关系,进而将子系统下发至不同的设计小组或部门由其进行所分配任务的详细设计,当各子系统分别完成设计后,基于预先规划的装配关系,自动生成整机模型。
在实际的应用过程中,自顶向下的设计方法虽然与复杂产品的研发流程更加一致,但由于其设计的复杂性,对工程师,尤其是对顶层总体工程师或产品经理的要求比较高,而且现有的三维CAD 软件在总体规划阶段缺少合适的工具,导致目前很多企业仍然以简单但并不合理的自底向上的设计方法进行产品设计,即首先进行零件的设计,然后进行装配体的组装。
即使要创建产品布局,也往往是在表格中,或是在二维的CAD 工具中,与后续的产品设计完全脱节,无法形成贯通的自顶向下设计流程。
SOLIDWORKS Treehouse 作为SOLIDWORKS CAD产品的一个模块,可以在一个独立的界面中打开。
它可以让用户快速针对一个新产品创建装配体结构树,也可以将现有的模型结构拉入新产品结构树中进行组装。
总体工程师或者新产品的产品经理不需要任何的SOLIDWORKS 软件的使用经验,通过简单的拖放等操作可以灵活地搭建产品结构并导出至SOLIDWORKS 中,或导出至Excel 表格中。
sw从上往下的设计方法

sw从上往下的设计方法SW(Structured Walkthrough)从上往下的设计方法是一种软件开发过程中常用的设计方法。
这种方法是一种结构化的设计方法,旨在通过逐步细化和分解问题,从整体到细节,逐步深入设计软件系统的各个部分。
下面我将从多个角度来回答这个问题。
首先,SW从上往下的设计方法强调整体到细节的设计思路。
在设计软件系统时,首先从整体的功能和结构出发,进行系统的总体设计,然后逐步细化到各个模块和子系统的设计,最终得到具体的实现方案。
这种设计方法有助于确保软件系统的整体一致性和高效性。
其次,SW从上往下的设计方法注重模块化和结构化。
通过将系统分解为多个模块,每个模块再进一步分解为子模块,逐级细化,从而实现系统的模块化设计。
这种设计方法有助于降低系统的复杂度,提高系统的可维护性和可扩展性。
此外,SW从上往下的设计方法还强调逐步求精和迭代设计。
在设计过程中,首先完成系统的整体设计框架,然后逐步细化和完善各个模块的设计,不断迭代优化,直至得到最终的设计方案。
这种设计方法有助于在设计过程中及时发现和解决问题,确保系统设计的完整性和合理性。
最后,SW从上往下的设计方法需要充分考虑系统的可行性和实现难度。
在设计过程中,需要综合考虑系统的功能需求、性能要求、技术限制等因素,确保设计方案既能满足用户需求,又能在技术上可行并且具有实现可能性。
总的来说,SW从上往下的设计方法是一种注重整体到细节、模块化和迭代设计的结构化设计方法,能够帮助开发团队高效地设计和实现复杂的软件系统。
solidworks自顶向下设计实例

SolidWorks自顶向下设计实例在SolidWorks中,自顶向下设计是一种非常常见的设计方法,它允许工程师在开始设计时就考虑整体系统,并在之后的设计过程中逐步细化细节。
这种方法非常适合于需要快速响应需求变化的项目,并且能够最大程度地减少设计修订的次数。
在本文中,我将通过一个实际的案例来阐述SolidWorks自顶向下设计的方法和优势。
案例介绍:假设我们要设计一个简单的机械组件,它包括一个齿轮、一个轴和一个连杆。
我们将通过自顶向下设计的方法来完成这个案例。
步骤一:定义整体尺寸和相对位置在开始设计之前,我们首先需要确定整体尺寸和各个零件之间的相对位置。
在SolidWorks中,我们可以通过创建一个装配体,并在装配体中设置零件的大致位置和尺寸来实现这一步骤。
步骤二:创建零件在确定了整体尺寸和位置之后,我们可以开始逐步细化各个零件。
在这个案例中,我们可以先创建齿轮、轴和连杆的三维模型,并在零件中应用装配体中定义的相对位置和尺寸。
步骤三:设计细节在完成了零件的创建之后,我们可以逐步添加细节,比如轴承孔、螺纹等。
此时,因为我们已经在装配体中定义了相对位置,所以这些细节的添加将变得非常简单和直观。
步骤四:装配我们将完成的零件装配到一起,并检查它们之间的相对位置和尺寸是否符合原先定义的要求。
在装配的过程中,因为我们采用了自顶向下的设计方法,所以可以确保各个零件之间的协调性和一致性。
总结回顾:通过上述案例,我们可以看到自顶向下设计方法的优势。
它不仅让我们能够在开始设计时就考虑整体系统,还能够在后续的设计过程中逐步细化细节。
这种方法能够最大程度地减少设计修订的次数,并且能够快速响应需求变化。
在实际工程项目中,自顶向下设计方法非常适用于需要快速迭代和灵活调整的项目。
个人观点和理解:在我看来,自顶向下设计方法是一种非常高效和灵活的设计方法。
它允许工程师在开始设计时就考虑整体系统,避免了后续设计过程中的重大调整和修订。
solid works 教程第4章 装配设计

装配实例
装配关系的编辑
在设计数中单击“配合”前面的“+”符号,打开装配关系 。 选择需要编辑的装配关系,单击鼠标右键,在弹出的快捷 选项中选择【编辑特征】选项,按照需要修改各项配合设 置。
删除装配关系
在设计树中,选择想要删除的配合关系,单击右键,弹出 快捷菜单,选择【删除】选项,或者选中配合关系后按键 盘上的Delete键,出现【删除确认】对话框,单击“是”
零部件的操作
线性零部件阵列
单击【装配体】工具栏中的【线性零部件…】命令按钮
& 提示:若要将阵列中的某个零部件跳过,在激 活“要跳过实例”选项后,再选择要跳过显示的 零部件即可。
零部件的操作
圆周零部件阵列
单击【装配体】工具栏中的【圆周零部件…】命令按钮
零部件的操作
镜像零部件
单击【装配体】工具栏中的【镜像零部件】命令按钮
装配的基本概念
装配体:装配体,它由多个零部件或其他子装配体所组
成的一个组合体。装配体文件的扩展名为“.sldasm”
。 配合:配合是在装配体零部件之间生成几何关系。当零
件被调入到装配体中时,除了第一个调入的之外,其它
的都没有添加配合,位置处于任意的“浮动”状态。在 装配环境中,处于“浮动”状态的零件可以分别沿三个 坐标轴移动,也可以分别绕三个坐标轴转动,即共有六 个自由度。
路径配合:将零部件上所选的点约束到路径。 线性/线性耦合配合:在一个零部件的平移和另一个零部 件的平移之间建立几何关系。 距离配合:允许零部件在距离配合一定数值范围内移动。 角度配合:允许零部件再角度配合一定数值范围内移动。
零部件的装配关系
机械配合
凸轮配合:是一个相切或重合配合类型,它允许将圆柱、基准面、或点与一 系列相切的拉伸曲面相配合。 铰链配合:将两个零部件之间的移动限制在一定的旋转范围内,其效果相当 于同时添加同心配合和重合配合。 齿轮配合:会强迫两个零部件绕所选轴相对旋转,齿轮配合的有效旋转轴包 括圆柱面、圆锥面、轴和线性边线。 齿条小齿轮配合:通过齿条和小齿轮配合,某个零部件(齿条)的线性平移 会引起另一零部件(小齿轮)做圆周旋转,反之亦然。 螺旋配合:将两个零部件约束为同心,还在一个零部件的旋转和另一个零部 件的平移之间添加几何关系。 万向节配合:一个零部件(输出轴)绕自身轴的旋转是由另一个零部件(输 入轴)绕其轴的旋转驱动。
- 1、下载文档前请自行甄别文档内容的完整性,平台不提供额外的编辑、内容补充、找答案等附加服务。
- 2、"仅部分预览"的文档,不可在线预览部分如存在完整性等问题,可反馈申请退款(可完整预览的文档不适用该条件!)。
- 3、如文档侵犯您的权益,请联系客服反馈,我们会尽快为您处理(人工客服工作时间:9:00-18:30)。
SolidWorks 自顶向下装配设计(自制教程)
设计不仅仅是将零件的三维模型和二维工程图做出来,设计还包含零部件的计
算分析,干涉检查,运动模拟及分析,另外设计要考虑的问题很多,如:表面质量,
修改方便性等。
这样,如何在设计最初就有一个好的整体规划就显得尤为重要, 他将直接影响
你后续设计的方便性等。
如下是一幅图片,此模型论坛提供下载,将以发动机为例讲述在SW中的一种设计思路,图片仅供参考。
一提到发动机,我们最先想到的就是曲柄连杆机构,那么在此项设计中曲柄连杆就是整个发动机运动之筋骨。
设计之初,很多因素不确定,而且很多零件还不知道在将来的装配环境中合不
合理,是否能够如期而动?但是设计并非无迹可寻,因为要做一个产品,你首先得
有一个大体轮廓,或是根据已有产品进行改型。
例如做减速机设计,各齿轮之大体
中心距,输入输出功率等都应是已知因素,那么设计的任务就是根据这些已知因素
来求出一些未知因素。
在零件没有设计出来以前,就对整个零部件进行运动验证是一个好的思路,它
能保证你没有大错误,但是零件的特征一个一个的建立总是麻烦的,所以我们在SW 中用线条来代替实体的零件进行运动模拟,以期在设计之初最大程度的减少工作量, 而直接看到最终运动结果。
这也如在3D Max在做人物动画时先绘制骨骼,然后再往上赋予肌肉的原理是
上图的线架构运动模拟是如何建立的??
第一步,建立曲轴线模型如图,然后将其存成一个零件。
注意在其曲拐中间部位建立一基准平面,以备后来装配之需。
同时大家也注意到,此图片是用JP EG格式存成的,所以不太清晰,而同类图
片(颜色不丰富)的话用 GIF 格式则效果较好,以下的图片全采用了 GIF 格
式。
\ Goni. Gn
第二步, 建立连杆线条模型。
本来是可以用一个圆圈代替的,但为了形像一点用了两个圆。
第四步,建立缸套。
简单一点,用一个圆代替。
於点\ '、 k
* P 图I
/臭呼
1
If
\ 1
V' 建立活塞线条模型。
第三步,
件咼为浮动,我在此先拖入曲轴。
童龊語T
删薄一牌I 打形tr 圳liiljw!竝』
i &第六步,为曲轴添加装配几何关系。
其中曲轴原点与装配原点重合,曲轴前视面与装配前视面重合,这样曲轴还留 下一个转动自由度,符合实际运动情况。
将以上四文件拖入装配体中,注间将拖入的第一个零
ion cn
粮寒件s 为浮动
V,
H1号
童】 Nv 调*尢 響
Q
rx lA , 豎警鼎
轲评呈陛
一f
此时如要对零件进行拖动观看运动效果,请用手形工具然后切换至特征树中选择零件,而不要在模型中直接拖拉线条。
把连杆一拖进来就发现其尺寸太大,与整体比例不符,所以对其尺寸进行修
改,
十准面1 \
gck^mcv^yahoo. com. cn
将其余两零件拖进行,同样有比例不协调之嫌,所以将两零件所有尺寸统统改
为25。
両加董疚系 此点^合关
OS
前视和上視之间加入「'平行距离” gdwEcy 配关粟,距离值九80
编辑活塞零件。
!■■■ 0痢骰
h- <$>上视
i 0若视 L 原点 -也苴區11
喉
ESB
;0上 © 右
飞基
也]茎 帥配含址 ■ -電重
:-% M
H 0 重 ____________________ * !-嚥平 1
如图修改零件及设置几何关系。
轄到… 压縮迦 隐眾零部件© 固定① 部件属性…(I )
重合
视
删除
编a 此零件
Sm artH ales 但)
移动零部件dj 吏看配合① 編辑詐迫 _
装配好后如图,但产生了一个问题,线条不能加入运动马达,要加入运动马达 的话必须有体,所以下一步我们还是编辑零件将曲轴端部加入一个拉伸圆柱。
*
草问,白专 i 音 昜脣簷慕上便
/Xi 亦匚 矗7 目 h<.'■:. C'Z fTi
■: n 完成最后线架模拟。
SfilGr) ・ I • I W H 1 k ► H q> H I 和
'1 一# 编辑完零件馳》至莉 配
棋式,选园周边线然 点
击模拟工具栏中" 鮭转
马达"项
后
快
E
^QU
\完此放
\制点播 、
茅用速
・*" ■ . _ _
gdwmcy ",
S 11 1
窿转马达] • ■nW
终止录制
做完以后,可以在此基础上进行各零件的细化设计。
在此不多述特征的建立方法,谨祝大家能用好Solidworks这一优秀的设计工具。
细化零件特征设计后
6
实体模拟动画。