机床参考点
机床参考点名词解释

机床参考点名词解释
机床参考点是机械加工中的一个术语,它是一个固定的位置点,用于对机床的运动进行检测和控制。
这个参考点也是机床坐标系的原点,在经过一系列的数据确定以及调整之后,这个原点就会被确定下来。
在接上电之后,这个原点不能独立构建,需要在坐标轴上确定每一个参考点,并通过自动或手动的方式回归到参考点,这样才能建立坐标系。
在选择参考点时,可以根据参数的情况进行考虑,可以选择与机床原点重合或不重合的参考点。
在后期编程加工的过程中建立起来的原点,是机床坐标系中的一个特殊点,必须通过程序才能进行运行。
如果这个元件出现问题,可以通过其他的方式进行补偿,比如刀具的补偿、轴向补偿等等。
当数控机床失去对参考点的记忆时,例如断电后、按下急停开关后、空运行后、超越行程极限等情况下,需要重新回到参考点。
数控机床回参考点的故障分析和排除
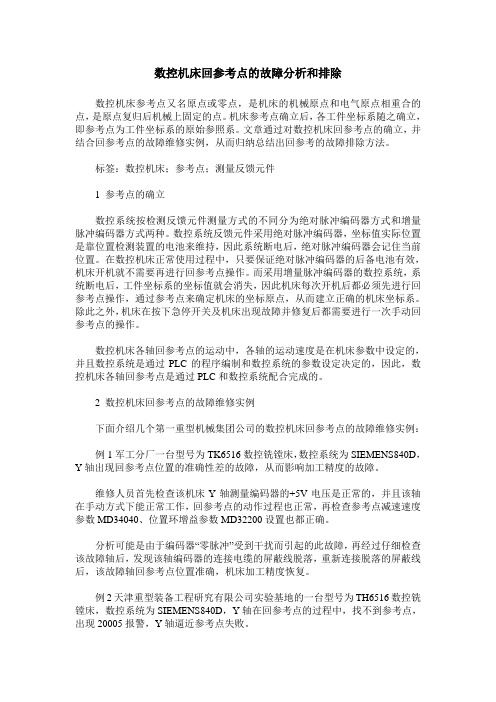
数控机床回参考点的故障分析和排除数控机床参考点又名原点或零点,是机床的机械原点和电气原点相重合的点,是原点复归后机械上固定的点。
机床参考点确立后,各工件坐标系随之确立,即参考点为工件坐标系的原始参照系。
文章通过对数控机床回参考点的确立,并结合回参考点的故障维修实例,从而归纳总结出回参考的故障排除方法。
标签:数控机床;参考点;测量反馈元件1 参考点的确立数控系统按检测反馈元件测量方式的不同分为绝对脉冲编码器方式和增量脉冲编码器方式两种。
数控系统反馈元件采用绝对脉冲编码器,坐标值实际位置是靠位置检测装置的电池来维持,因此系统断电后,绝对脉冲编码器会记住当前位置。
在数控机床正常使用过程中,只要保证绝对脉冲编码器的后备电池有效,机床开机就不需要再进行回参考点操作。
而采用增量脉冲编码器的数控系统,系统断电后,工件坐标系的坐标值就会消失,因此机床每次开机后都必须先进行回参考点操作,通过参考点来确定机床的坐标原点,从而建立正确的机床坐标系。
除此之外,机床在按下急停开关及机床出现故障并修复后都需要进行一次手动回参考点的操作。
数控机床各轴回参考点的运动中,各轴的运动速度是在机床参数中设定的,并且数控系统是通过PLC的程序编制和数控系统的参数设定决定的,因此,数控机床各轴回参考点是通过PLC和数控系统配合完成的。
2 数控机床回参考点的故障维修实例下面介绍几个第一重型机械集团公司的数控机床回参考点的故障维修实例:例1军工分厂一台型号为TK6516数控铣镗床,数控系统为SIEMENS840D,Y轴出现回参考点位置的准确性差的故障,从而影响加工精度的故障。
维修人员首先检查该机床Y轴测量编码器的+5V电压是正常的,并且该轴在手动方式下能正常工作,回参考点的动作过程也正常,再检查参考点减速速度参数MD34040、位置环增益参数MD32200设置也都正确。
分析可能是由于编码器“零脉冲”受到干扰而引起的此故障,再经过仔细检查该故障轴后,发现该轴编码器的连接电缆的屏蔽线脱落,重新连接脱落的屏蔽线后,该故障轴回参考点位置准确,机床加工精度恢复。
数控车床中机床坐标系-机床参考点与工件坐标系的关系
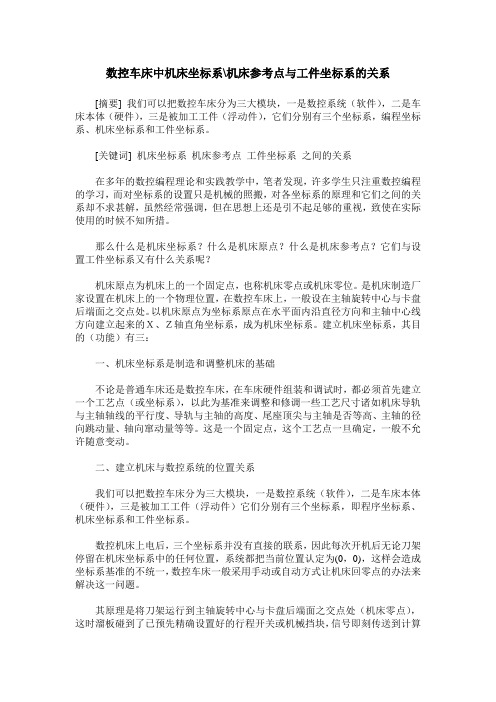
数控车床中机床坐标系\机床参考点与工件坐标系的关系[摘要] 我们可以把数控车床分为三大模块,一是数控系统(软件),二是车床本体(硬件),三是被加工工件(浮动件),它们分别有三个坐标系,编程坐标系、机床坐标系和工件坐标系。
[关键词] 机床坐标系机床参考点工件坐标系之间的关系在多年的数控编程理论和实践教学中,笔者发现,许多学生只注重数控编程的学习,而对坐标系的设置只是机械的照搬,对各坐标系的原理和它们之间的关系却不求甚解,虽然经常强调,但在思想上还是引不起足够的重视,致使在实际使用的时候不知所措。
那么什么是机床坐标系?什么是机床原点?什么是机床参考点?它们与设置工件坐标系又有什么关系呢?机床原点为机床上的一个固定点,也称机床零点或机床零位。
是机床制造厂家设置在机床上的一个物理位置,在数控车床上,一般设在主轴旋转中心与卡盘后端面之交点处。
以机床原点为坐标系原点在水平面内沿直径方向和主轴中心线方向建立起来的X、Z轴直角坐标系,成为机床坐标系。
建立机床坐标系,其目的(功能)有三:一、机床坐标系是制造和调整机床的基础不论是普通车床还是数控车床,在车床硬件组装和调试时,都必须首先建立一个工艺点(或坐标系),以此为基准来调整和修调一些工艺尺寸诸如机床导轨与主轴轴线的平行度、导轨与主轴的高度、尾座顶尖与主轴是否等高、主轴的径向跳动量、轴向窜动量等等。
这是一个固定点,这个工艺点一旦确定,一般不允许随意变动。
二、建立机床与数控系统的位置关系我们可以把数控车床分为三大模块,一是数控系统(软件),二是车床本体(硬件),三是被加工工件(浮动件)它们分别有三个坐标系,即程序坐标系、机床坐标系和工件坐标系。
数控机床上电后,三个坐标系并没有直接的联系,因此每次开机后无论刀架停留在机床坐标系中的任何位置,系统都把当前位置认定为(0,0),这样会造成坐标系基准的不统一,数控车床一般采用手动或自动方式让机床回零点的办法来解决这一问题。
数控机床原点、参考点、工作零点的区别和联系
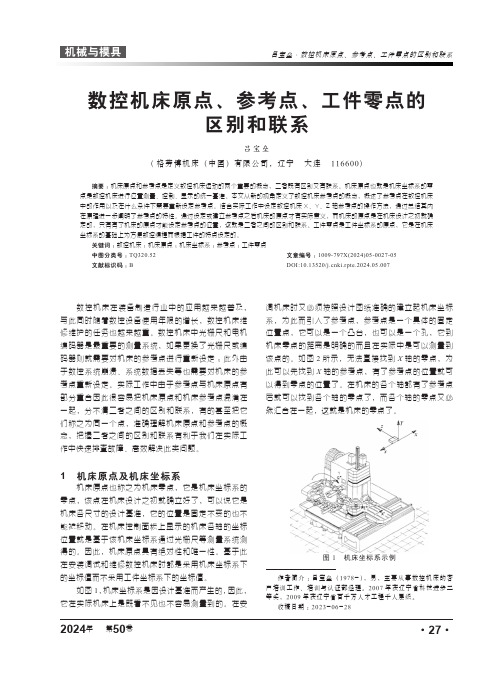
作者简介:吕宝垒(1978-),男,主要从事数控机床的客户培训工作、培训与认证部经理。
2007年获辽宁省科技进步二等奖,2009年获辽宁省百千万人才工程千人层级。
收稿日期:2023-06-28数控机床在装备制造行业中的应用越来越普及,与此同时随着数控设备使用年限的增长,数控机床维修维护的任务也越来越重。
数控机床中光栅尺和电机编码器是最重要的测量系统,如果更换了光栅尺或编码器则就需要对机床的参考点进行重新设定;此外由于数控系统崩溃、系统数据丢失等也需要对机床的参考点重新设定。
实际工作中由于参考点与机床原点有部分重合因此很容易把机床原点和机床参考点混淆在一起,分不清二者之间的区别和联系,有的甚至把它们称之为同一个点,准确理解机床原点和参考点的概念,把握二者之间的区别和联系有利于我们在实际工作中快速排查故障、高效解决此类问题。
1 机床原点及机床坐标系机床原点也称之为机床零点,它是机床坐标系的零点,该点在机床设计之初就确立好了,可以说它是机床各尺寸的设计基准,它的位置是固定不变的也不能被移动。
在机床控制面板上显示的机床各轴的坐标位置就是基于该机床坐标系通过光栅尺等测量系统测得的。
因此,机床原点具有绝对性和唯一性。
基于此在安装调试和维修数控机床时都是采用机床坐标系下的坐标值而不采用工件坐标系下的坐标值。
如图1,机床坐标系是因设计基准而产生的,因此,它在实际机床上是既看不见也不容易测量到的。
在安数控机床原点、参考点、工件零点的区别和联系吕宝垒(格劳博机床(中国)有限公司,辽宁 大连 116600)摘要:机床原点和参考点是定义数控机床运动的两个重要的概念,二者既有区别又有联系。
机床原点也就是机床坐标系的零点是数控机床进行位置测量、控制、显示的统一基准。
本文从新的视角定义了数控机床参考点的概念,概述了参考点在数控机床中的作用以及在什么条件下需要重新设定参考点。
结合实际工作中设定数控机床X、Y、Z 轴参考点的操作方法,通过总结其内在原理进一步阐明了参考点的特性。
机床A1-A2主从轴参考点的方法

机床A1-A2主从轴参考点的方法背景描述:机床是GROB的双轴GM4580,A1-A2是主从轴,A2是主动轴,带距离编码的光栅尺,A1轴是从动轴,不带光栅尺,A1和A2轴电机都是绝对值式编码器。
这是A1轴:这是A2轴:执行作业:更换后A2轴圆光栅后,重新设定A2轴的参考点标定之前这里有几个机床数据需要先说一下:MD30200- 指的是机床的测量系统数量,这台机床的A2轴MD30200=2 (编码器+光栅尺)MD30240[0]-指的是第一测量系统的类型,增量式为1,绝对值式为4,A2轴的MD30240[0]=1说明第一测量系统为增量型,也就是光栅作为第一测量系统,而MD30240[1]=4 说明第二测量系统为绝对值型,也就是编码器作为第二测量系统。
总结就是:GROB设定的A2轴绝对值型编码器对应的机床参数下角标为1,作为第二测量系统;带距离编码的圆光栅对应的机床参数下角标为0,作为第一测量系统。
这是需要注意的知晓的!我们的标定过程是这样的:1. 更换完圆光栅后,机床会有A2 轴未定参考的提示,自动情况是不能回原位的,选择自动-本地模式开始低速回原位,当轴转动超过20°后出现A2轴编码器位置公差超出报警。
报警原因是因为A2轴的圆光栅是带距离编码的,每过20°就会出现一个零脉冲,但是A2圆光栅和A1编码器相差又超过20°因而产生报警,因此需要先将A1轴标定零点,方法同西门子绝对值编码器标零方法。
2. 下一步要保证A2两个测量系统的数值保持一致,查看“诊断”-“轴诊断”-“轴信息”-选择A2轴查看两个测量系统的值这里就会有两个计算方法,一个是让圆光栅值去和编码器保持一致,另一种就是相反,让编码器去和圆光栅保持一致。
1)现以让圆光栅值去和编码器保持一致为例:用第二系统测量值减去第一测量系统值:-191.471-(-32.127)=-159.344。
重要一步:A轴解耦合,将差值-159.344补到A2轴的MD34090[0]中即可,即MD34090[0]+(-159.344)。
数控机床返回参考点控制及常见故障诊断
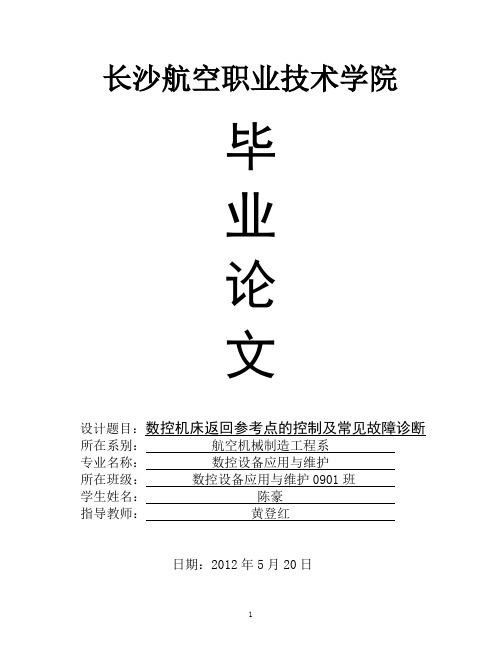
长沙航空职业技术学院毕业论文设计题目:数控机床返回参考点的控制及常见故障诊断所在系别:航空机械制造工程系专业名称:数控设备应用与维护所在班级:数控设备应用与维护0901班学生姓名:**指导教师:***日期:2012年5月20日空军航空维修技术学院毕业设计(论文)任务书数控设备应用与维护专业 0901班姓名陈豪学号 29指导老师:黄登红设计题目:数控机床返回参考点的控制及常见故障诊断设计题号:17设计内容及要求:1.绘制并打印数控机床的挡块式和无挡块式回零控制原理图各一张(2号图纸);2.完成设计说明书编制(不小于4000字);设计说明书内容应包括:分析数控机床返回参考点的必要性;阐述数控机床返回参考点的原理和常见方式;完成返回参考点PLC控制程序编写(使用梯形图)和说明;与返回参考点相关的系统参数及其功能说明;返回参考点的常见故障及解决措施。
联系方式:手机:159****5961电话:*************邮箱:******************数控教研室2011年10月目录摘要 (4)绪论 (5)第一章数控机床返回参考点的必要性 (6)第二章数控机床返回参考点的原理及常见方式 (8)2.1 增量栅格法(挡块式)回参考点原理 (9)2.2 绝对栅格法(无挡块式)回参考点原理 (9)第三章数控机床返回参考点的相关参数及设定 (16)第四章数控机床返回参考点的PMC控制 (20)4.1 可编程控制器(PMC)简介 (20)4.2 数控机床返回参考点的PMC控制 (21)第五章数控机床返回参考点的常见故障分析及诊断.205.1 数控机床不能返回参考点的原因 (20)5.2 数控机床回参考点故障的主要类型错误!未定义书签。
5.3 数控机床回参考点常见故障分析与诊断错误!未定义书签。
5.3.1 增量式(挡块式)回零过程中的常见故障分析及诊断.............. 错误!未定义书签。
5.3.2 绝对式(无挡块式)回零过程中的常见故障分析及诊断............ 错误!未定义书签。
数控机床返回参考点常见故障分析
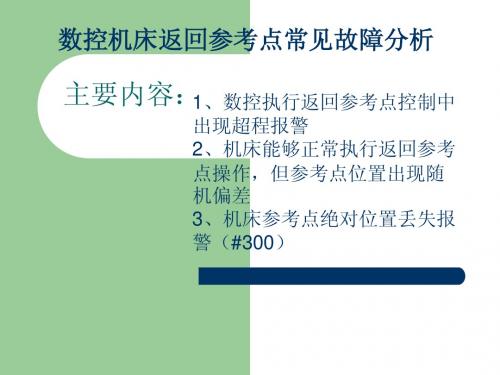
如上述测量的值在规定范围内,说明: 如上述测量的值在规定范围内,说明:
1)减速开关及接线不良,活更换减速开关 或重新接线 2)减速挡块位置不正确,重新调整减速挡块 3)进给伺服电动机内装编码器不良,拆开伺服电动机内 装编码器进行清洗,检查连接电缆及电缆的插座是否 良好 4)全闭环检测装置不良或有灰尘及油污,清洗光栅尺的 长光栅 5)如果只是每天早上首先开机出现,则更换系统的备份 电池 6)伺服放大器或者系统主板不良,则更换不良部件
2、机床能够正常执行返回参考点操作,但 参考点位置出现随机偏差
出现上述测速量超差的原因及处理方法: 1)伺服电动机与丝杠联结松动,紧固伺服电动 机与丝杠的联轴节。 2)丝杠螺母副间隙过大,调整丝杠螺母副的间 隙或者更换整套丝杠螺母副 3)丝杠两端固定或支撑的轴承间隙过大或不良, 调整丝杠两端的轴承间隙或更换轴承
数控机床返回参考点常见故障分析
主要内容: 1、数控执行返回参考点控制中
出现超程报警 2、机床能够正常执行返回参考 点操作,但参考点位置出现随 机偏差 3、机床参考点绝对位置丢失报 警(#300)
1、数控执行返回参考点控制中出现超程报 警
1、机床执行返回参考点控制中出现超程报警 (1)机床返回参考点过程中无减速动作或者一 直以减速移动故障原因 1)减速开关及接线不良 2)减速开关与挡块位置不当 3)减速开关信号系统的I/O接口故障 4)系统本身不良
故障的诊断: 通过系统PMC状态监控画面,检查机床在返回 参考点控制过程中信号是否正常,如果信号不 变化,则为减速开关不良。如果信号变化正常, 则为系统本身故障
(2)机床返回参考点过程中有减速动作 故障原因: 1)机床离参考点位置太近 2)减速挡块与机床超程保护开关太近 3)系统一转信号不良 故障的诊断与处理
浅谈数控机床回参考点及故障分析处理
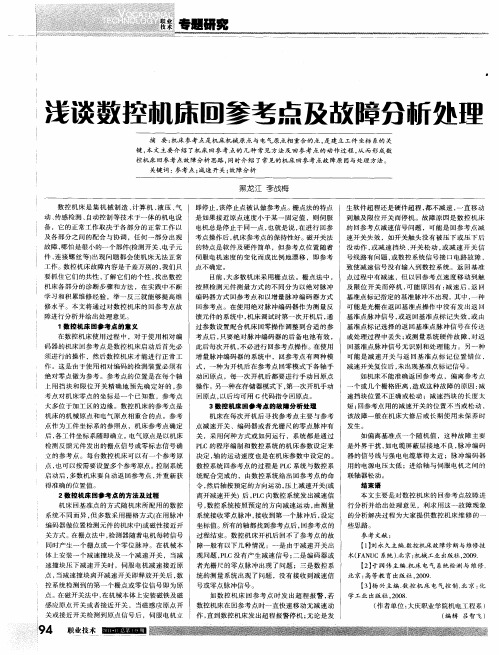
摘 要: 机床 参考点是机床机械 原点与 电气原点 相重合的 点, 是建立工件 坐标 系的关
键, 本文主要介 绍 了机床 回参 考点 的几种 常见方 法及回参 考点 的动作过 程 , 而形成数 从
控机床 回参考点故障分析 思路 , 同时介 绍 了常见的机床 回参 考点故障原 因与处理方法 。
得准 确的位置值 。
关 ,采用何种 方式或如 何运行 ,系统都 是通 过 P C的程 序编制 和数控 系统 的机 床参数 设定来 L
决 定 , 的运动速度 也是在机 床参数 中设定 的。 轴 数 控系统 回参考点 的过程是 P C系统与数控 系 L 统 配合完 成的 ,由数控 系统给 出 回参 考点 的命
速挡块 位置不 正确或松动 ;减 速挡块 的长度 太 短; 回参考点 用的减速 开关的位 置不 当或松 动 , 该 故障一般在 机床大修 后或 长期使用 未保 养 时
发生 。
检测 反馈元件 发 出的栅 点信号 或零标志 信号确
立 的参考点 。每 台数 控机床 可以有一个 参考 原 点 , 可以按需要设 置多个参考原 点。控制 系统 也 启动 后 , 多数 机床要 自动返 回参考点 , 并重新 获
关键 词 : 参考点 ; 减速 开关 ; 故障 分析
黑龙江 李 战梅
数控 机床 是集 机械 制 造 、 计算 机 、 液压 、 气
即停 止 , 该停止点被认 做参考点 。 栅点法 的特点
是 如果接近 原点速度小 于某一 固定值 ,则伺 服 电机 总是停 止于 同一点 , 也就是说 , 在进 行 回参 考 点操作后 , 机床参 考点的保持性好 。磁 开关 法 的特点是软 件及硬件 简单 ,但参 考点位 置 随着 伺 服电机速 度的变化 而成 比例地漂移 ,即参 考 点 不确定 。 目前 , 多数机床采 用栅点 法 。栅 点法 中 , 大 按 照检测元 件测量方 式 的不 同分为 以绝对 脉冲 编 码器方式 回参考点 和 以增量 脉冲 编码 器方 式 回参考点 。在使用绝 对脉 冲编码器作 为测 量反 馈 元件 的系统 中, 床调试 时第 一次 开机后 , 机 通 过参数设 置配合机床 回零操 作调整 到合适 的参 考点后 , 只要绝对 脉冲编码 器的后备 电池有 效 , 此后每次 开机 , 不必进行 回参考 点操作 。在使用
数控车床手动回参考点操作步骤
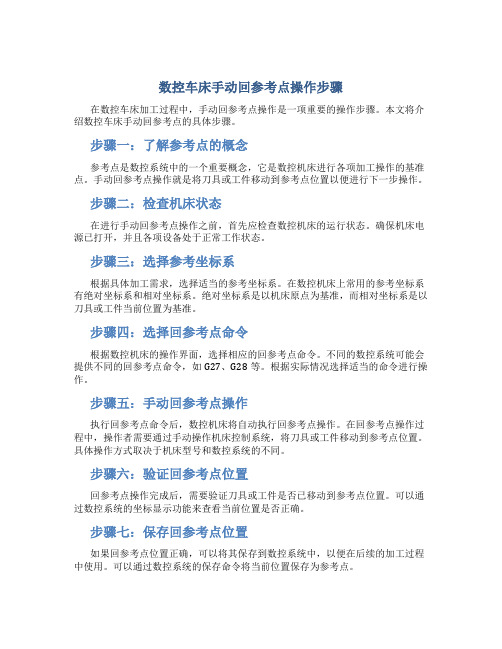
数控车床手动回参考点操作步骤在数控车床加工过程中,手动回参考点操作是一项重要的操作步骤。
本文将介绍数控车床手动回参考点的具体步骤。
步骤一:了解参考点的概念参考点是数控系统中的一个重要概念,它是数控机床进行各项加工操作的基准点。
手动回参考点操作就是将刀具或工件移动到参考点位置以便进行下一步操作。
步骤二:检查机床状态在进行手动回参考点操作之前,首先应检查数控机床的运行状态。
确保机床电源已打开,并且各项设备处于正常工作状态。
步骤三:选择参考坐标系根据具体加工需求,选择适当的参考坐标系。
在数控机床上常用的参考坐标系有绝对坐标系和相对坐标系。
绝对坐标系是以机床原点为基准,而相对坐标系是以刀具或工件当前位置为基准。
步骤四:选择回参考点命令根据数控机床的操作界面,选择相应的回参考点命令。
不同的数控系统可能会提供不同的回参考点命令,如G27、G28等。
根据实际情况选择适当的命令进行操作。
步骤五:手动回参考点操作执行回参考点命令后,数控机床将自动执行回参考点操作。
在回参考点操作过程中,操作者需要通过手动操作机床控制系统,将刀具或工件移动到参考点位置。
具体操作方式取决于机床型号和数控系统的不同。
步骤六:验证回参考点位置回参考点操作完成后,需要验证刀具或工件是否已移动到参考点位置。
可以通过数控系统的坐标显示功能来查看当前位置是否正确。
步骤七:保存回参考点位置如果回参考点位置正确,可以将其保存到数控系统中,以便在后续的加工过程中使用。
可以通过数控系统的保存命令将当前位置保存为参考点。
步骤八:完成手动回参考点操作手动回参考点操作完成后,可以进行下一步加工操作或者进行其它操作。
在整个加工过程中,需要不断重复手动回参考点操作,以确保每个加工步骤都准确无误。
结论手动回参考点操作是数控机床加工过程中的一项重要操作步骤。
正确地执行手动回参考点操作可以确保刀具或工件准确移动到参考点位置,为后续的加工操作提供良好的基础。
操作者应熟悉数控机床的相关操作命令和界面,严格按照操作步骤进行操作,确保操作的准确性和安全性。
任务12 机床零点、参考点以及程序原点、对刀点

项目二数控车床坐标系【教学课题】任务1.2 机床零点、参考点以及程序原点、对刀点【教学目标】通过学习了解机床零点、参考点以及程序原点、对刀点概念以及作用。
【教学重点】程序原点与对刀点概念以及作用。
【教学难点】对刀方法。
【教学方法】1.教法:任务驱动、多媒体演示、启发式讲授及示范2.学法:学中做、做中学【教学准备】多媒体课件、任务单、教学视频等。
【教学时间】2课时【教学过程】一、新课导入二、新知学习点的距离。
机床回到了参考点位置,也就知道了该坐标轴的零点位置,找到所有坐标轴的参考点,CNC 就建立起了机床坐标系。
机床坐标轴的机械行程是由最大和最小限位开关来限定的。
机床坐标轴的有效行程范围是由软件限位来界定的,其值由制造商定义。
知识补充:我们通常机床启动后要“回零”,其实就是回到机床的参考点。
二、工件坐标系、程序原点和对刀点工件坐标系是编程人员在编程时使用的,编程人员选择工件上的某一已知点为原点(也称程序原点),建立一个新的坐标系,称为工件坐标系。
工件坐标系一旦建立便一直有效,直到被新的工件坐标系所取代。
工件坐标系的原点选择要尽量满足编程简单,尺寸换算少,引起的加工误差小等条件。
一般情况下,程序原点应选在尺寸标注的基准或定位基准上。
对车床编程而言,工件坐标系原点一般选在,工件轴线与工件的左端面、右端面、卡爪左端面的交点上。
如下图所示工件轴线与工件的右端面的交点为工件坐标系原点。
对刀点是零件程序加工的起始点,对刀的目的是确定程序原点在机床坐标系中的位置,对刀点可与程序原点重合,也可在任何便于对刀之处,但该点与程序原点之间必须有确定的坐标联系。
可以通过CNC 将相对于程序原点的任意点的坐标转换为相对于机床零点的坐标。
加工开始时要设置工件坐标系,用G50 指令可建立工件坐标系;用G54~G59 及刀具指令可选择工件坐标系。
三、任务实施在车削加工的数控程序中,X轴的坐标值取为零件图样上的直径值,采用直径尺寸编程与零件图样中的尺寸标注一致,这样可避免尺寸换算过程中可能造成的错误,给编程带来很大方便。
机床回参考点命令G27、G28、G29

机床参考点是可以任意设定的,设定的位置主要根据机床加工或换刀的需要。
设定的方法有两种:其一即根据刀杆上某一点或刀具刀尖等坐标位置存入参数中,来设定机床参考点:其二用调整机床上各相应的挡铁位置,也可以设定机床参考点。
一般参考点选作机床坐标的原点,在使用手动返回参考点功能时,刀具即可在机床X、Y、Z坐标参考点定位,这时返回参考点指示灯亮,表明刀具在机床的参考点位置。
返回参考点校验功能(G27)指令程序中的这项功能,用于检查机床是否能准确返回参考点。
格式:G27 X____ Y____ :当执行G27指令后,返回各轴参考点指示灯分别点亮。
当使用刀具补偿功能时,指示灯是不亮的,所以在取消刀具补偿功能后,才能使用G27指令。
当返回参考点校验功能程序段完成,需要使机械系统停止时,必须在下一个程序段后增加M00或M01等辅助功能或在单程序段情况下运行。
自动返回参考点(G28)指令利用这项指令,可以使受控轴自动返回参考点。
格式:G28 X____ Y____ :或G28 Z____ X____ ;或G28 Y____ Z____ ;其中X、Y、Z为中间点位置坐标,指令执行后,所有的受控轴都将快速定位到中间点,然后再从中间点到参考点。
G28指令一般用于自动换刀,所以使用G28指令时,应取消刀具的补偿功能。
从参考点自动返回(G29)指令从参考点自动返回指令G29的形式为:G29 X____ Y____;或G29 Z____ X____ ;或G29 Y____ Z____;这条指令一般紧跟在G28指令后使用,指令中的X、Y、Z坐标值是执行完G29后,刀具应到达的坐标点。
它的动作顺序是从参考点快速到达G28指令的中间点,再从中间点移动到G29指令的点定位,其动作与G00动作相同。
第二参考点返回(G30)指令G30 X____ Y____;或G30 Z____ X____ ;或G30 Y____ Z____;G30为第二参考点返回,该功能与G28指令相似。
数控机床回参考点的探索

数控机床回参考点的探索作者:史晓龙洪超来源:《智能制造》2020年第09期摘要:本文阐述了什么是参考点,参考点与机床原点(零点)之间的关系,回参考点的作用与意义,参考点与位置编码器的之间的关系,针对使用FANUC系统,不同位置编码器的数控机床而采用的有挡块、无挡块和标记点三种设置参考点的方式,给出了具体的设置参数、设置方法和操作步骤,为数控机床操作和调试提供一定的帮助。
关键词:参考点;机床原点;位置编码器;有挡块无挡块标记点1 参考点与机床原点参考点是指数控机床上某一固定位置的特定点。
通常数控系统启动后,首先要做的工作就是回参考点操作,也称回机床原点或回零操作。
回参考点是数控机床的重要功能,也是机床操作人员操作数控机床时最常见的操作。
数控机床在加工零件时,数控系统通过发出各种程序指令来控制刀具和机床的运动。
为了准确地控制运动的方向和移动的距离,就有必要在机床上建立一坐标系作为加工的基准,这个加工基准就是机床坐标系。
因为机床各轴的正方向是统一规定好的,所以只要确定了机床坐标系原点(零点)的位置,也就确定了机床坐标系的位置。
机床坐标系是机床固有的坐标系,是制造和调整机床的基础,坐标系的原点是机床生产厂家在设计机床时就已经确定好的,用户不能随意更改,且机床原点只是一个设计定义的点,不方便被直接测量定位。
那怎样才能找到机床原点的准确位置呢?方法是通过回参考点。
机床参考点是数控机床上人为设置的一个固定位置的点,通常是设在各个轴正方向行程的极限位置处。
这样,只要通过指定机床参考点到机床原点之间的距离,并始终保持二者之间的固定位置关系,就可以通过直接定位参考点位置的同时间接确定机床原点的位置。
确定了机床原点(零点),也就确定了机床坐标系和加工的基准。
机床参考点与机床原点可以是同一点,也可以不是。
通常数控铣削类机床的参考点与机床原点是重合的,分别在 X轴、Y轴和Z轴的正向行程最大极限处。
而数控车床上的参考点与机床原点就不在同一点.机床原点位于卡盘回转中心与端面相交的中心。
机床原点、机床参考点
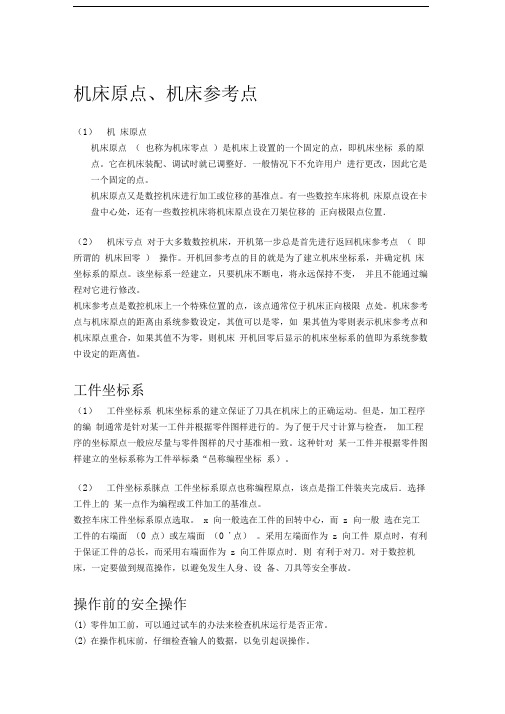
机床原点、机床参考点(1)机床原点机床原点(也称为机床零点)是机床上设置的一个固定的点,即机床坐标系的原点。
它在机床装配、调试时就已调整好.一般情况下不允许用户进行更改,因此它是一个固定的点。
机床原点又是数控机床进行加工或位移的基准点。
有一些数控车床将机床原点设在卡盘中心处,还有一些数控机床将机床原点设在刀架位移的正向极限点位置.(2)机床亏点对于大多数数控机床,开机第一步总是首先进行返回机床参考点(即所谓的机床回零)操作。
开机回参考点的目的就是为了建立机床坐标系,并确定机床坐标系的原点。
该坐标系一经建立,只要机床不断电,将永远保持不变,并且不能通过编程对它进行修改。
机床参考点是数控机床上一个特殊位置的点,该点通常位于机床正向极限点处。
机床参考点与机床原点的距离由系统参数设定,其值可以是零,如果其值为零则表示机床参考点和机床原点重合,如果其值不为零,则机床开机回零后显示的机床坐标系的值即为系统参数中设定的距离值。
工件坐标系(1)工件坐标系机床坐标系的建立保证了刀具在机床上的正确运动。
但是,加工程序的编制通常是针对某一工件并根据零件图样进行的。
为了便于尺寸计算与检查,加工程序的坐标原点一般应尽量与零件图样的尺寸基准相一致。
这种针对某一工件并根据零件图样建立的坐标系称为工件举标桑“邑称编程坐标系)。
(2)工件坐标系脒点工件坐标系原点也称编程原点,该点是指工件装夹完成后.选择工件上的某一点作为编程或工件加工的基准点。
数控车床工件坐标系原点选取。
x 向一般选在工件的回转中心,而z 向一般选在完工工件的右端面(0 点)或左端面(0 '点)。
采用左端面作为z 向工件原点时,有利于保证工件的总长,而采用右端面作为z 向工件原点时.则有利于对刀。
对于数控机床,一定要做到规范操作,以避免发生人身、设备、刀具等安全事故。
操作前的安全操作(1)零件加工前,可以通过试车的办法来检查机床运行是否正常。
(2)在操作机床前,仔细检查输人的数据,以免引起误操作。
数控机床回参考点过程分析、典型模式和故障分析
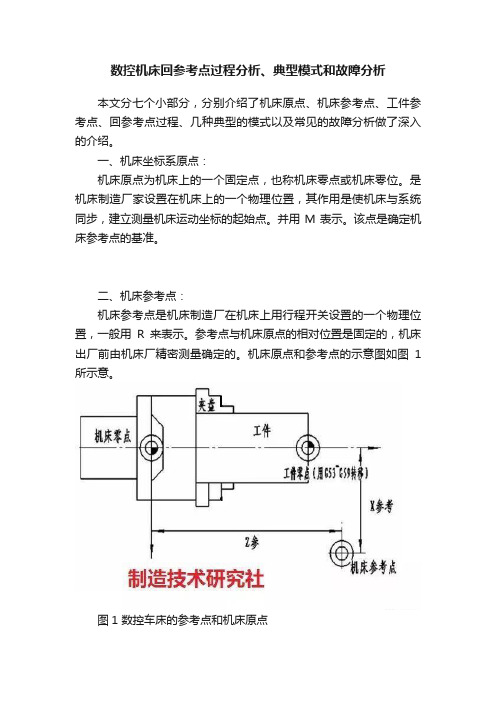
数控机床回参考点过程分析、典型模式和故障分析本文分七个小部分,分别介绍了机床原点、机床参考点、工件参考点、回参考点过程、几种典型的模式以及常见的故障分析做了深入的介绍。
一、机床坐标系原点:机床原点为机床上的一个固定点,也称机床零点或机床零位。
是机床制造厂家设置在机床上的一个物理位置,其作用是使机床与系统同步,建立测量机床运动坐标的起始点。
并用M表示。
该点是确定机床参考点的基准。
二、机床参考点:机床参考点是机床制造厂在机床上用行程开关设置的一个物理位置,一般用R来表示。
参考点与机床原点的相对位置是固定的,机床出厂前由机床厂精密测量确定的。
机床原点和参考点的示意图如图1所示意。
图1 数控车床的参考点和机床原点一般来说,机床坐标系原点或机床零点是通过机床参考点间接确定的。
机床参考点是机床上的一个固定点,其与机床零点间有一确定的相对位置,一般设置在刀具运动的X、Z正向最大极限位置。
展开剩余85%在机床每次通电之后,工作之前,必须进行回机床零点操作,使刀具运动到机床参考点,其位置由机械档块确定。
这样,通过机床回零操作,确定了机床零点,从而准确地建立机床坐标系,即相当于数控系统内部建立一个以机床零点为坐标原点的机床坐标系。
机床坐标系是机床固有的坐标系,一般情况下,机床坐标系在机床出厂前已经调整好,不允许用户随意变动。
对于铣床来说,有的机床参考点就是原点,有的参考点在最大行程位置。
而对于车床来说,参考点和原点不是同一点,这在图1中显示得十分明显。
三、工件坐标系原点:工件坐标系是用来确定工件几何形体上各要素的位置而设置的坐标系,工件原点的位置是人为设定的,它是由编程人员在编制程序时根据工件的特点选定的,所以也称编程原点。
工件坐标系原点和机床原点是有偏移的,所有的编程都是以工件原点作为原点的,在通过G53,G59来指定偏移。
四、机床回参考点过程:机床回参考点过程在往期文章(《端午节,回家就向数控机床回参考点一样,不需要理由,只需要团聚》)中已经详细说明了,这里再简单回顾一下:1)设置回参考点工作方式;2)选择返回参考点的轴并操作该轴返回参考点,该轴以G00快速向参考点运动;3)当随滑板一起运动的撞块压下参考点开关触头,使其内断(ON)转通(OFF)状态后,机床滑板会减速并按参数设定的速度继续移动。
数控机床刀位点对刀点和对刀参考点

数控机床刀位点对刀点和对刀参考点
数控机床刀位点对刀点和对刀参考点
数控机床作为现代数控加工工业中不可或缺的设备之一,其精度和效率的高要求对于数控机床的操作者提出了更高的要求。
而机床的刀位点对刀点和对刀参考点则是数控加工过程中极其重要的概念。
刀位点是指切削刀具在数控机床上被安装在刀架上时的位置,也可以称为工装点。
在数控机床上,刀位点一般用G代码设置,程序中可将其称为T代码,以表示每次的切削刀具的刀尖的相对位置。
而对于要执行特定加工操作的切削刀具,先要将其切换至正确的刀位点,以确保加工的准确性和精度。
而对于对刀点,它又分为机械对刀点和光学对刀点两种类型。
机械对刀点是通过碰撞测量法来确定加工过程中的相应工作空间,而光学对刀点则是通过投影目标的切点位置来实现精确测量,其主要用于精确定位需特殊精度的加工过程中。
相对于机械对刀方法,光学对刀点有更高的精度和可靠性,其操作也更加方便快捷。
刀位点对刀点和对刀参考点除了流畅的操作过程,对于机床加工的精度和效率也起到了至关重要的作用。
现代数控机床的发展趋势意味着
对于其工作功能和精度的不断提高,因此操作者也需要不断调整自身的操作方法,以确保数控加工过程中的精度、效率和安全性。
加工中心参考点的确认方法

加工中心参考点的确立方法所谓加工中心参考点又名原点或零点,是机床的机械原点和电气原点相重合的点,是原点复归后机械上固定的点。
每台机床可以有一个参考原点,也可以据需要设置多个参考原点,用于自动刀具交换(ATC)或自动拖盘交换(APC)等。
参考点作为工件坐标系的原始参照系,机床参考点确定后,各工件坐标系随之建立。
所谓机械原点,是基本机械坐标系的基准点,机械零部件一旦装配完毕,机械原点随即确立。
所谓电气原点,是由机床所使用的检测反馈元件所发出的栅点信号或零标志信号确立的参考点。
为了使电气原点与机械原点重合,必须将电气原点到机械原点的距离用一个设置原点偏移量的参数进行设置。
这个重合的点就是机床原点。
在加工中心使用过程中,机床手动或者自动回参考点操作是经常进行的动作。
不管机床检测反馈元件是配用增量式脉冲编码器还是绝对式脉冲编码器,在某些情况下,如进行ATC或APC过程中,机床某一轴或全部轴都要先回参考原点。
按机床检测元件检测原点信号方式的不同,返回机床参考点的方法有两种。
一种为栅点法,另一种为磁开关法。
在栅点法中,检测器随着电机一转信号同时产生一个栅点或一个零位脉冲,在机械本体上安装一个减速撞块及一个减速开关后,数控系统检测到的第一个栅点或零位信号即为原点。
在磁开关法中,在机械本体上安装磁铁及磁感应原点开关,当磁感应原点开关检测到原点信号后,伺服电机立即停止,该停止点被认作原点。
栅点方法的特点是如果接近原点速度小于某一固定值,则伺服电机总是停止于同一点,也就是说,在进行回原点操作后,机床原点的保持性好。
磁开关法的特点是软件及硬件简单,但原点位置随着伺服电机速度的变化而成比例地漂移,即原点不确定。
目前,几乎所有的机床都采用栅点法。
使用栅点法回机床原点的几种情形如下:1.使用增量检测反馈元件的机床开机后的第一次回机床原点;2.使用绝对式检测反馈元件的机床安装后调试时第一次机床开机回原点;3.栅点偏移量参数设置调整后机床第一次手动回原点。
实验十三机床回参考点实验

实验十三机床回参考点实验一、实验目的1、了解全功能数控机床回参考点功能与建立机床坐标系的概念。
2、掌握SINUMERIK 802D数控系统的回参功能调整。
二、实验设备RS-SY-802D数控机床综合实验系统。
三、实验必备知识1、机床回参考点功能是全功能数控机床建立机床坐标系的必要手段,参考点可以设在机床坐标行程内的任意位置(一般由机床制造厂家设定)。
在数控机床上需要对刀具运动轨迹的数值进行准确控制,所以要对数控机床建立坐标系。
标准坐标系是右手直角笛卡尔坐标系。
右手直角笛卡尔坐标系规定了直角坐标X、Y、Z三者的关系及其正方向用右手定则判定,围绕X、Y、Z各轴的回转运动及其正方向+A、+B、+C分别用右螺旋法则判定。
数控车床坐标系的确定:Z轴坐标是由传递切削动力的主轴所确定,平行于主轴轴线,一般Z轴的正方向为远离主轴的方向。
X轴坐标是沿工件的径向且平行于横向导轨,一般X轴的正方向为远离工件旋转中心的方向。
加工中心坐标系的确定:Z轴坐标是由传递切削动力的主轴所确定,平行于主轴轴线,一般Z轴的正方向为远离工件的方向。
X轴坐标是水平的,一般平行于工件的装夹表面,X轴的正方向由右手直角笛卡尔坐标系判定。
Y轴坐标是由右手直角笛卡尔坐标系来判定。
2、机床回完参考点后,机床坐标系就已建立,参考点通常是坐标系中的某一点,该点不一定是坐标原点。
此时,各种补偿以及偏置生效,机床轴才能根据程序的命令走出正确的坐标值。
3、对于安装了绝对值编码器作位置反馈的机床,由于绝对值编码器具有记忆功能,无需每次开机都作回参考点操作。
而大多数的数控机床则使用增量值编码器作位置反馈,重新开机后的第一件事,便是作回参考点操作,建立坐标系,以避免因此而引起的撞刀现象。
4、在闭环或半闭环的位置编码器中,如圆光栅编码器中一般都有零脉冲信号,光栅中一般都有零位脉冲信号。
安装方式可以有很多种。
5、机床回参考点操作,一般需有一定的硬件支持,除位置编码器以外,一般还须在坐标轴相应的位置上安装一硬件挡块与一行程开关,作为参考点减速开关。
数控机床回不了参考点的故障诊断及修理方法
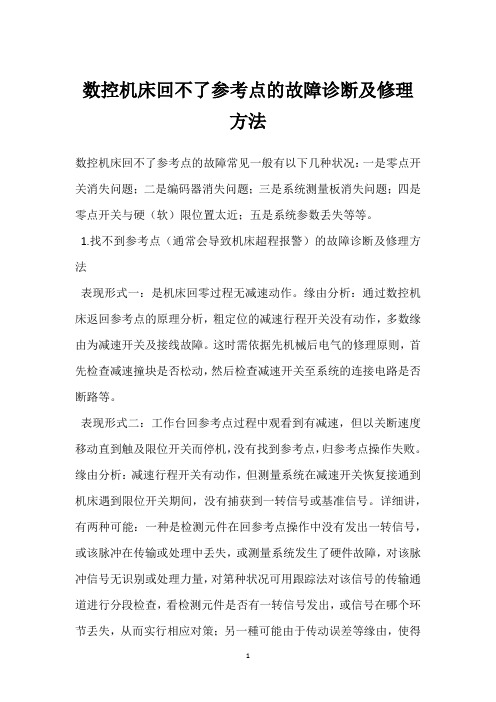
数控机床回不了参考点的故障诊断及修理方法数控机床回不了参考点的故障常见一般有以下几种状况:一是零点开关消失问题;二是编码器消失问题;三是系统测量板消失问题;四是零点开关与硬(软)限位置太近;五是系统参数丢失等等。
1.找不到参考点(通常会导致机床超程报警)的故障诊断及修理方法表现形式一:是机床回零过程无减速动作。
缘由分析:通过数控机床返回参考点的原理分析,粗定位的减速行程开关没有动作,多数缘由为减速开关及接线故障。
这时需依据先机械后电气的修理原则,首先检查减速撞块是否松动,然后检查减速开关至系统的连接电路是否断路等。
表现形式二:工作台回参考点过程中观看到有减速,但以关断速度移动直到触及限位开关而停机,没有找到参考点,归参考点操作失败。
缘由分析:减速行程开关有动作,但测量系统在减速开关恢复接通到机床遇到限位开关期间,没有捕获到一转信号或基准信号。
详细讲,有两种可能:一种是检测元件在回参考点操作中没有发出一转信号,或该脉冲在传输或处理中丢失,或测量系统发生了硬件故障,对该脉冲信号无识别或处理力量,对第种状况可用跟踪法对该信号的传输通道进行分段检查,看检测元件是否有一转信号发出,或信号在哪个环节丢失,从而实行相应对策;另一種可能由于传动误差等缘由,使得一转信号刚错过,在等待下一个一转信号的过程中,坐标轴触及到限位开关,所以只好停机。
对第种状况,可能是零点开关与硬(软)限位置太近,可试着适当调整限位开关或减速开关与参考点位置标记间的距离,即可消退故障。
2.找不准参考点(即返回参考点有偏差)的故障诊断及修理方法表现形式是机床在返回参考点过程中有减速,也有制动到零的过程,但停止位置不精确且无规律,或与参考点正确位置前移或后移一个丝杠螺距(即相当编码器一转的机床位移量的偏差)。
缘由分析:对于前种状况,经常是由于减速开关(参考点开关)或压块松动、低速设置太低、信号干扰等因素造成的,消失后一种状况的缘由是零点开关与硬(软)限位置太近,对于这种故障可适当调整减速开关的位置或修改偏移量参数,使一转信号产生的时刻离减速信号从断到通时相距约半个一转信号产生的周期,即可消退故障。
- 1、下载文档前请自行甄别文档内容的完整性,平台不提供额外的编辑、内容补充、找答案等附加服务。
- 2、"仅部分预览"的文档,不可在线预览部分如存在完整性等问题,可反馈申请退款(可完整预览的文档不适用该条件!)。
- 3、如文档侵犯您的权益,请联系客服反馈,我们会尽快为您处理(人工客服工作时间:9:00-18:30)。
h、根据需要,设定参考点偏移量。
4)、故障举例:
一台三菱M64系统钻削中心,Z轴回参考点时发生过行程报警。
a、 检查参考点检测开关信号,当移动到参考点挡块位置时,能够从“0”变为“1”;
b、 检查栅罩量参数(2028),正常;
各轴返回参考点的方式=0;
各轴的参考计数器容量,根据电机每转的回馈脉冲数作为参考计数器容量设定;
是否使用绝对脉冲编码器作为位置检测器=0 ;
绝对脉冲编码器原点位置的设定=0;
位置检测使用类型=0;
快速进给加减速时间常数、快速进给速度、FL速度、手动快速进给速度、伺服回路增益依实际情况进行设定;
g、重启电源。
2)、无挡块参考点方式调整:
a、设定参数: #2049 = 2 无挡块参考点调整方式;
#2050 = 0 正方向、 = 1 负方向;
b、选择“绝对位置设定”画面,选择手轮或寸动模式;
c、在“绝对位置设定”画面,选择“无碰压”方式;
d、#0绝对位置设定=1 , #2原点设定:以基本机械坐标为准,设定参考点的坐标值;
b、选择“手动”模式,将控制轴移动到参考点附近;
c、输入参数:MD34100,机床坐标位置;
d、激活绝对编码器的调整功能:MD34210=1.绝对编码器调整状态;
e、按机床复位键,使机床参数生效;
f、机床回归参考点;
g、机床不移动,系统自动设置参数:34090. 参考点偏移量;34210. 绝对编码器设定完毕状态,屏幕上显示位置是MD34100设定位置。
是否使用绝对脉冲编码器作为位置检测器: 0. 不是 、1. 是 1815.50021 7021
绝对脉冲编码器原点位置的设定:0. 没有建立、 1. 建立1815.40022 7022
位置检测使用类型:0.内装式脉冲编码器、1. 分离式编码器、直线尺1815.10037 7037
快速进给加减速时间常数16200522
参数内容 系统0i/16i/18i/21i0
所有轴返回参考点的方式: 0. 挡块、 1. 无挡块1002.10076
各轴返回参考点的方式: 0. 挡块、 1. 无挡块1005.10391
各轴的参考计数器容量18210570~0575 7570 7571
每轴的栅格偏移量18500508~0511 0640 0642 7508 7509
最后查到参考点挡块松动,拧紧螺丝后,重新试机,故障排除。
二: 绝对位置检测系统:
1. 发那克系统:
1)、工作原理: 绝对位置检测系统参考点回归比较简单,只要在参考点方式下,按任意方向键,控制轴以参考点间隙初始设置方向运行,寻找到第一个栅格点后,就把这个点设置为参考点。
2)、相关参数:
4、故障举例:
一台西门子810D系统,机床每次参考点返回位置都不一致,从以下几项逐步进行排查:
a、 伺服模块控制信号接触不良;
b、电机与机械联轴节松动;
C、参数点开关或挡块松动;
d、参数设置不正确;
е、位置编码器供电电压不低于4.8V;
f、位置编码器有故障;
g、位置编码器回馈线有干扰;
数控机床参考点的设置与维修
2007-5-15 16:52:00 来源:中国自动化网
摘要: 这里详细地介绍了发那克,三菱,西门子几种常用数控系统参考点的工作原理、调整和设定方法,并举例说明参考点的故障现象,解决方法。
关键词:参考点 相对位置检测系统 绝对位置检测系统
前言: 当数控机床更换、拆卸电机或编码器后,机床会有报警信息:编码器内的机械绝对位置数据丢失了,或者机床回参考点后发现参考点和更换前发生了偏移,这就要求我们重新设定参考点,所以我们对了解参考点的工作原理十分必要。
e、把控制轴移动到参考点附近。
f、#1 = 1,控制轴以 #2050设置方向移动,达到第一个栅格点时停止,把这个点设定为电气参考点。
g、重启电源。
3、 西门子系统(802D、810D、840D为例):
1)、调试;
a、设置参数:
MD34200=0.绝对编码器位置设定;
MD34210=0.绝对编码器初始状态;
2)、相关参数:
参数内容 系统M60 M64
快速进给速度2025
慢行速度2026
参考点偏移量2027
栅罩量2028
栅间隔2029
参考点回归方向2030
3)、设定方法:
a、设定参数:
参考点偏移量=0
栅罩量=0
栅间隔=滚珠导螺快速进给速度、慢行速度、参考点回归方向依实际情况进行设定。
参考点是指当执行手动参考点回归或加工程序的G28指令时机械所定位的那一点,又名原点或零点。每台机床有一个参考点,根据需要也可以设置多个参考点,用于自动刀具交换(ATC)、自动拖盘交换(APC)等。通过G28指令执行快速复归的点称为第一参考点(原点),通过G30指令复归的点称为第二、第三或第四参考点,也称为返回浮动参考点。由编码器发出的栅点信号或零标志信号所确定的点称为电气原点。机械原点是基本机械坐标系的基准点,机械零件一旦装配好,机械参考点也就建立了。为了使电气原点和机械原点重合,将使用一个参数进行设置,这个重合的点就是机床原点。
b、机床重启,手动回到参考点附近;
c、是否使用绝对脉冲编码器作为位置检测器=1 ;
绝对脉冲编码器原点位置的设定=1;
e、机床重启;
f、 由于机床参考点与设定前不同,重新调整每轴的栅格偏移量。
2、三菱系统(M60、M64为例):
1)、无挡块机械碰压方式:
a、设定参数: #2049.= 1 无檔块机械碰压方式;
#2054 电流极限;
b、选择“绝对位置设定”画面,选择手轮或寸动模式,(也可选择自动初期化模式);
C、在“绝对位置设定”画面,选择“可碰压”;
d、#0绝对位置设定=1 , #2原点设定:以基本机械坐标为准,设定参考点的坐标值;
e、移动控制轴,当控制轴碰压上机械挡块,在给定时间内达到极限电流时,控制轴停止并反方向移动。如果b步选择手轮或寸动模式,则控制轴反方向移动移动到第一栅格点,这个点就是电气参考点;如果b步选择“自动初期化”模式,则在第a步还要设置 #2005碰压速度参数和 #2056接近点值,此时控制轴反方向以 #2005(碰压速度)移动到 #2056(接近点)值停止,再以 #2055(碰压速度)向挡块移动,在给定时间内达到极限电流时,控制轴停止并以反方向移动到第一栅格点,这个点就是电气参考点;
快速进给速度14200518~0521
FL速度14250534
手动快速进给速度14240559~0562
伺服回路增益18250517
返回参考点间隙初始方向 0. 正 1. 负10060003 7003 0066
3)、设置方法:
a、设定参数:
所有轴返回参考点的方式=0;
快速进给速度14200518~0521
FL速度14250534
手动快速进给速度14240559~0562
伺服回路增益18250517
3)、பைடு நூலகம்定方法:
a、 设定参数:
所有轴返回参考点的方式=0;
各轴返回参考点的方式=0;
各轴的参考计数器容量,根据电机每转的回馈脉冲数作为参考计数器容量设定;
2)、相关参数:
参数内容 系统0i/16i/18i/21i0
所有轴返回参考点的方式: 0. 挡块、 1. 无挡块1002.10076
各轴返回参考点的方式: 0. 挡块、 1. 无挡块1005.10391
各轴的参考计数器容量18210570~0575 7570 7571
每轴的栅格偏移量18500508~0511 0640 0642 7508 7509
b、重启电源,回参考点。
C、在|报警/诊断|→|伺服|→|伺服监视(2)|,计下栅间隔和栅格量的值。
d、计算栅罩量:
当栅间隔/2<栅格量时,栅罩量=栅格量-栅间隔/2
当栅间隔/2>栅格量时,栅罩量=栅格量+栅间隔/2
e、把计算值设定到栅罩量参数中。
f、重启电源,再次回参考点。
一: 使用相对位置检测系统的参考点回归方式:
1、发那克系统:
1)、工作原理:
当手动或自动回机床参考点时,首先,回归轴以正方向快速移动,当挡块碰上参考点接近开关时,开始减速运行。当挡块离开参考点接近开关时,继续以FL速度移动。当走到相对编码器的零位时,回归电机停止,并将此零点作为机床的参考点。
机床配备的位置检测系统一般有相对位置检测系统和绝对位置检测系统。相对位置检测系统由于在关机后位置数据丢失,所以在机床每次开机后都要求先回零点才可投入加工运行,一般使用挡块式零点回归。绝对位置检测系统即使在电源切断时也能检测机械的移动量,所以机床每次开机后不需要进行原点回归。由于在关机后位置数据不会丢失,并且绝对位置检测功能执行各种数据的核对,如检测器的回馈量相互核对、机械固有点上的绝对位置核对,因此具有很高的可信性。当更换绝对位置检测器或绝对位置丢失时,应设定参考点,绝对位置检测系统一般使用无挡块式零点回归。
是否使用绝对脉冲编码器作为位置检测器=0 ;
绝对脉冲编码器原点位置的设定=0;
位置检测使用类型=0;
快速进给加减速时间常数、快速进给速度、FL速度、手动快速进给速度、伺服回路增益依实际情况进行设定。
b、 机床重启,回参考点。
c、 由于机床参考点与设定前不同,重新调整每轴的栅格偏移量。
是否使用绝对脉冲编码器作为位置检测器: 0. 不是 、1. 是 1815.50021 7021