轮对压配合时的压装与分解
铁路货车轮对和滚动轴承组装及检修规则

4.1轮对组装范围4.1.1轮对新组装:轮对新组装是以新制车轮及车轴按新制(原型)技术标准组装的轮对。
4.1.2轮对重新组装:轮对重新组装是以旧车轮和旧车轴(拼修)、旧车轮和新车轴(换轴)及新车轮和旧车轴(换轮)按厂修技术标准组装的轮对。
4.2轮对组装要求4.2.1 同一车轴上必须组装同型号、同材质的车轮(除另有规定者外,不同国家或不同厂家制造的车轮不得混装)。
4.2.2轮对应以同型号的车轴和车轮相组装。
当车轮与车轴型号不同时,轮对型号以车轴型号为准,组装规定如下:4.2.2.1 D型车轮可组装在轮座直径为197mm及以下的E 型车轴上;4.2.2.2 E型车轮可组装在轮座直径为192mm及以上的D 型车轴上。
4.2.3 向同一车轴上组装的两个车轮轮辋宽度相差不得超过5mm,其内侧距离应按最小轮辋宽度的规定执行;轮辋宽度小于127mm的车轮不得再组装使用。
4.2.4轮对退轮检查后,其原车轮与原车轴不得重新组装。
4.2.5轮座和轮毂孔旋配技术要求4.2.5.1轮对组装时,轮毂孔及轮座应在相同环境温度下同温8小时后进行加工、测量、选配和组装。
4.2.5.2轮座与轮毂孔采取过盈配合,配合过盈量按轮座直径的o.8‰~1.5‰执行;4.2.5.3轮毂孔和轮座的直径尺寸必须符合规定限度,并且同一车轴上两端的轮座直径相差不得超过3mm。
4.2.5.4 轮座加工后的圆度不得超过O.020mm,内外侧的直径差不得超过O.1mm,并且大端必须在内侧。
4.2.5.5 轮座的终加工可采用磨削或滚压工艺,采用滚压工艺做为终加工时,轮座经车削加工表面粗糙度必须达到Ra3.2μm后方可进行滚压加工,经磨削或滚压加工后表面粗糙度应达到Ra1.6μm,但由于压装工艺的原因,为保证压装力曲线合格,轮座表面粗糙度可放宽到Ra2.0μm。
4.2.5.6轴身直径不得大于轮座直径,轮座与轴身过渡部分的圆弧半径必须符合图纸规定,过渡部分的表面粗糙度必须达到Ra6.3μm。
HXD3型电力机车车轮压装概述

HXD3型电力机车车轮压装概述摘要:介绍了HXD3型电力机车轮对基础结构,阐述了检修过程中轮对压装应急处理办法,分析了新造与检修车轮压装曲线的区别,轮对从新造到C6修周期内经过多次拆解与压装,基本不会影响轮对装配的质量。
关键词:应急办法;过程简介;对比分析。
1引言对机车轮对组装技术条件研究,轮对压装应急处理办法,新造与检修阶段车轮拆卸、压装的操作过程和相关压装曲线对比分析,验证了轮对经过多次拆装后的质量仍可满足机车正常运用安全。
2轮对压装简介随着我国轨道交通事业的发展,轮对压装是轮对加工中的一道重要工序,车轮与车轴采用过盈配合,无键连接,其压装质量的优劣直接关系到车辆运行安全。
根据TB/T1463-2015可知,轮对的压装分4种。
HXD3系列大都为注油压装。
3HXD3型轮对结构简介HXD3型电力机车轮对的车轴采用JZ50钢的实心轴,车轮为J11或J2的整体辗钢材质,车轮踏面采用JM3磨耗型踏面,车轮与车轴过盈量为0.26mm~0.33mm,毂孔直径约为250mm,过盈量与毂孔直径的比值=1.03‰~1.31‰,新造的滚动圆直径1250mm,轮对内侧距未负载状态为1353。
[1]4轮对压装应急处理办法HXD3型电力机车进行高级修的检修过程中,因车轮拆卸导致的车轴拉伤报废概率大致在0.98%左右,结合车轮与车轴的拆卸、检修及压装的简要步骤,分析车轴拉伤报废的原因如下。
4.1车轮拆卸拉伤的原因车轮拆卸过程中造成车轴拉伤的原因主要有三点,其一,就是接磨,是车轮与车轴形成的夹角而导致接磨;其二,就是硬拉伤,车轴与车轮之间的拉伤;未等到液压油渗出,毂孔涨开,就启动反拔机,所造成的;其三,有异物拉伤,比如在轮对运用中因振动过大造成有的注油孔螺堵丢失,导致灰尘进入车轮油槽,拆卸过程中,灰尘挤入车轮与车轴结合面造成拉伤。
4.2压装应急处理办法车轮压装过程,需进行清洁、尺寸测量、注油压力设置、压装曲线检查等相关工作,保证车轮压装不会出现因杂质、尺寸不符合技术要求等问题导致压装不合格。
铁路货车轮轴新组装轮对组装轴承压装作业指导书
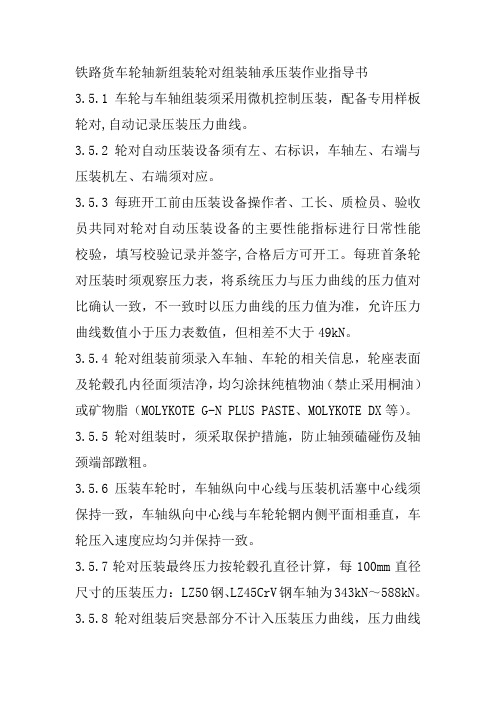
铁路货车轮轴新组装轮对组装轴承压装作业指导书3.5.1车轮与车轴组装须采用微机控制压装,配备专用样板轮对,自动记录压装压力曲线。
3.5.2轮对自动压装设备须有左、右标识,车轴左、右端与压装机左、右端须对应。
3.5.3每班开工前由压装设备操作者、工长、质检员、验收员共同对轮对自动压装设备的主要性能指标进行日常性能校验,填写校验记录并签字,合格后方可开工。
每班首条轮对压装时须观察压力表,将系统压力与压力曲线的压力值对比确认一致,不一致时以压力曲线的压力值为准,允许压力曲线数值小于压力表数值,但相差不大于49kN。
3.5.4轮对组装前须录入车轴、车轮的相关信息,轮座表面及轮毂孔内径面须洁净,均匀涂抹纯植物油(禁止采用桐油)或矿物脂(MOLYKOTE G-N PLUS PASTE、MOLYKOTE DX等)。
3.5.5轮对组装时,须采取保护措施,防止轴颈磕碰伤及轴颈端部蹾粗。
3.5.6压装车轮时,车轴纵向中心线与压装机活塞中心线须保持一致,车轴纵向中心线与车轮轮辋内侧平面相垂直,车轮压入速度应均匀并保持一致。
3.5.7轮对压装最终压力按轮毂孔直径计算,每100mm直径尺寸的压装压力: LZ50钢、LZ45CrV钢车轴为343kN~588kN。
3.5.8轮对组装后突悬部分不计入压装压力曲线,压力曲线须符合附件3规定。
3.5.9压力曲线等不合格时,应及时分解轮对。
分解时,车轴的中心线与压力机活塞的中心线应保持一致,并采取保护措施,防止轴颈蹾粗和磕碰伤,车轮压退时的最大压应力不超过车轴材质的下屈服强度。
3.5.10不得将分解的原车轮与原车轴原位进行第二次压装,在原车轴、车轮表面无损伤的情况下,可重新选配其他新加工过的合格车轮、车轴进行压装。
分解后有拉伤的车轮、车轴须重新加工,清除缺陷后方可使用。
若车轴经重新加工后须对再加工部位进行复合磁化荧光磁粉探伤检查。
3.5.11轮对压装压力曲线图表(车统-57)须与轮轴卡片(车统-51)装订在一起一并传递、保存,且车统-51、车统-57与轮对实物相符;同一条轮对的不合格压装压力曲线和合格曲线记录一并保存。
轮对、轴承和轴箱分解作业指导书
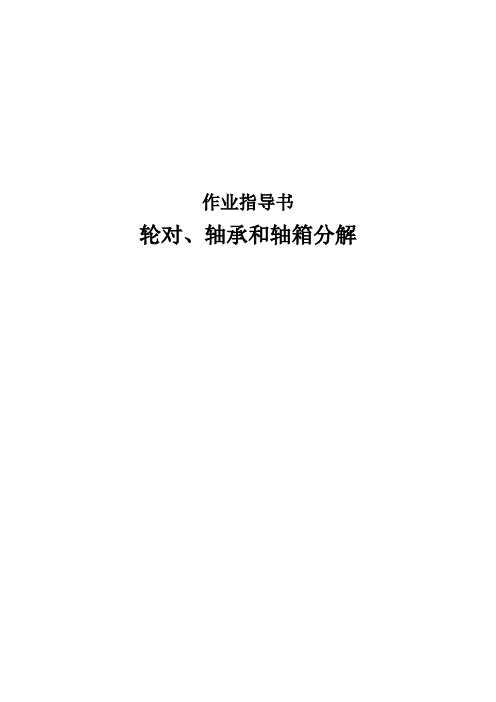
轴箱回按钮和轴箱升或降按钮,将轴
箱、轴承(不包括轴承内圈)从轴颈
上慢慢地分离出来,轴箱托架及轴箱
一直回到起始位。[图 3]
图 2 启动轴箱拉按钮,使托架对准轴箱底部 图 3 将轴箱及轴承从轴颈上平稳退卸
3
轮对、轴承和轴箱分解及轴承清洗作业指导书
序号 作业项目 工具及材料
作业方法及标准
作业图示
2.2 按轴箱升按钮,将轴箱、轴承升
送带
作业场所:轮轴分解工位
2.紫铜棒、温度计
环境要求:室内地面清洁,无油泥、杂物,通风良好。
操作规程: 参考文件: 1.《铁路客车轮轴组装检修及管理规则》(铁总运〔2013〕191号)
安全防护及注意事项: 1. 警告——职工劳动保护着装规范,穿劳保皮鞋,防止滑倒受伤。 2. 警告——分解过程中应防止配件砸伤手脚。 基本技术要求: 1. 用分解机械手将轴箱、轴承(不包括轴承内圈)从轴颈上平稳取下,禁止野蛮操作损伤轴承; 2. 轴承清洗后清洁度质量要求:目视轴承各件表面及沟角处不得有油污、水分、灰尘、纤维物及其它污垢;手感 轴承各件表面不得有颗粒物存在。 3. 外圈组件的清洗液温度≤90°C,在溶液中停留时间≤10min,清洗时须防止零部件磕碰伤。
作业方法及标准
作业图示
2 2.分解
2.1 将轮对分解线上的待分解轮对
送入分解机械手转稿上,按转镐上升
按钮,将轮对升起,然后再按转镐旋
转按钮,将轮对旋转 90°,将轮对一
端的轴箱对准分解机械手,按轴箱拉
轴箱分解机械 按钮,使机械手的轴箱托架对准轴箱
手
下部[图 2],按下轴箱升按钮,上
升轴箱托架刚好在轴箱底平齐,点动
作业指导书
轮对、轴承和轴箱分解
轮对压装过程中几个关键工艺参数的分析

轮对压装过程中几个关键工艺参数的分析摘要:铁路客车轮对承受着车辆的全部载荷,并在负重的条件下沿轨道作高速运转,轮对压装作为重要工序之一,其参数直接影响着行车安全。
本文分析了轮对压装的工艺过程中的几个关键参数,阐述了压装过程中易产生的问题,分析了产生这些问题的原因。
关键词:轮对;工艺;参数轮对是铁路客车最主要的零部件之一,而轮对组装的质量是保证车辆在高速运行中安全的至关重要的环节,车轴、车轮经过几道工序的加工,最后冷压组装,轮轴的加工质量好坏直接影响到轮轴压装环节的合格与否。
通过对压装环节主要质量问题的分析,我们找到了引起这些问题的原因,并在相应生产工序中采取措施,加强了工艺管理。
1. 影响轮对一次压装合格率的因素轮轴压装合格与否是用压装曲线来判别的,所以压装曲线记录仪的灵敏度也直接影响着轮对一次压装合格率。
同时,为了保证所需的联接强度及防止轮对联接部分的应力过高,必须正确选择过盈量。
但在实践中只满足过盈量的选取值,并不能取得理想的压力曲线和终止压装力,它还受到配合表面几何形状误差等因素的制约。
1.1 轮座、轮毂孔锥度对压装合格率的影响通常,在车轮轮毂孔上加工0.04的正向锥度,车轴轮座上加工0.10的正向锥度,以保证曲线形状及终止压装力合格。
在轮对压装过程中,由于轮座、轮毂孔锥度不一致,轮轴配合表面各部位的尺寸(沿径向方向)都不相等,因而沿轴向方向每一横截面的过盈量也不相等。
如果轮座与轮毂孔圆锥度较大且方向一致时,在开始压装时,会出现压力小或没压力,而压装一定量的长度时随过盈量的增加压力迅速增大,造成曲线的长度不够。
1.2 测量误差对轮对压装合格率的影响由于外径干分尺和百分表本身的不确定度(外径千分±0.006 mm,百分表±0.O25mm),再加上选配时测量部位和测量温度及湿度的影响,对过盈量的选取值形成累积误差,不能反映轮轴尺寸的真实值,直接影响过盈量选取的准确性,导致轮对一次压装合格率下降。
锥度车轴轮对压装分析

锥度车轴轮对压装分析摘要我国轨道车辆转向架造、修普遍采用轮轴冷压装工艺, 基于基轴制(或基孔制)采用过盈配合,选配车轮轮毂孔、车轴轮座直径后, 均匀涂抹润滑介质后压装,通过压装过程产生的位移--压力曲线判定配合标准。
但冷压装轮对在退卸时往往产生车轴、车轮拉伤现象,致使车轴、车轮报废。
锥度车轴车轮压装的轮对,可以很好避免该项问题的发生。
锥度车轴轮对的压装需解决的是如何在制造过程中保证压装曲线符合标准要求。
通过以往车轴加工经验,分析、实践锥度车轴的加工过程和参数指标控制方法。
建立力学模型,分析锥度车轴压装过程中车轴车轮配合直径变化对压力变化产生的影响,制定压装过程中达到符合要求的压装曲线的控制方法。
关键词转向架锥度车轴轮对压装曲线1问题的提出目前,部分轨道交通车辆在运营维护过程中为便于更换车轮及降低车轴损伤率,提出车轴轮座、车轮轮毂孔须采用锥度配合的冷压装组装。
锥度车轴轮对压装技术标准依托于《EN 13260 铁路应用-轮对与转向架-轮对-产品要求》及《UIC 813 为动车和拖车提供轮对的技术说明--公差和组装》。
基于国内普速客车以及高速动车组转向架等干线铁路客车轮对成熟、完备的轮对冷压装制造工艺技术,以及理论计算压装力及压装速度等参数,进行理论探讨。
2工艺性分析2.1锥度车轴加工与检测锥度车轴压装以轮对冷压工艺为基础,采取基轴制,先计算得出满足要求过盈量,选配确认车轮内孔直径与车轴轮座直径后,均匀涂抹润滑介质,用压力机一一对应进行压装。
检测、选配、压装时应使轮轴处于同一温度下进行,压装后压装曲线是唯一的检验依据。
锥度车轴压装的关键因素是过盈量的选取,其决定压装曲线走势。
过盈量的选取要保证提供足够的配合力,使轮对在运用中不发生相对运动,保证运行的安全。
故尺寸范围内,选取合适的过盈量进行车轴单件加工、检测,是首先需要解决的问题。
加工1:300锥度轮座无技术难点,加工前进行砂轮修型后,参照既有工艺可完成轮座精磨削加工。
轮对压配合时的压装与分解

轮对压配合时的压装与分解摘要:轮对是转向架的重要组成部分。
通过了解轮对压装的基本工艺的基础上,并进一步分析圆柱度,过盈量,压入速度和润滑剂等关键因素对轮对压装质量的影响。
通过分析关键因素的影响,有助于提高轮对压装质量,从而为转向架安全工作提供重要保障。
关键词:转向架;轮对压装;关键因素1前言轮对本身的结构并不复杂,但是由于它承担的任务多且重要,因此它的加工制造以及组装要求都非常高。
尤其是轮对的组装对于转向架的运行表现起到关键性的作用,组装稍有差错容易引发列车停车,甚至脱轨等重大事故。
通过对轮对组装过程的分析,可以更好地保证轮对正常使用,保障列车行驶安全。
2轮对压装工艺简介轮对本身结构较为简单,但是其对压装的要求却十分严格。
目前常见压装根据压装方式不同可以分为普通压装和注油压装两种方式。
其中普通压装根据压装温度不同可以分为热压装和冷压装。
热压装是将车轮内孔进行加热使其膨胀后再进行压装,其主要是针对过盈量较大的情况下使用。
热压装工艺设备一般较为复杂,一次投入成本较高,压装合格率较高,可提高车轴的使用寿命,止推试验效率低。
冷压装是直接通过压装机将车轮压到车轴上的方式,其主要是针对过盈量较小的情况下使用。
冷压装设备较为简单,一次性投入成本较低,但压装合格率一般,对操作要求较高,操作不当容易“戗轴”,对车轴寿命有一定影响,止推试验效率高。
而注油压装是在车轮上开注油孔,在压装过程中通过注入高压油,在车轮和车轴接触面之间形成一层油膜进行压装,其主要是针对车轴表面要求较高时使用。
注油压装设备较为复杂,操作难度较大,加工难度大,但压装过程允许停顿且不限时间,可以在一定范围内自由调整车轮位置。
这三种压装工艺目前都在使用,都有各个的优缺点。
这三种压装工艺的选择主要根据车轮和轮轴的结构以及压装的具体要求来决定的。
目前使用最为广泛使用的还是冷压装工艺。
3轮对压装影响因素在轮对冷压装过程中,影响压装效果主要包括过盈量,圆柱度,压入速度和润滑剂等因素。
轮对压装

摘要:本文主要介绍的是轮对的组装过程和轮轴联结质量及其分析等问题。
引言:车辆轮对是由两个同类型和同材质的车轮与一根车轴按规定压力和规定尺寸紧压配合组装成的一个整体。
他承受着车辆的全部载荷,并在负重的条件下沿轨道作高速运转。
因此,要求能圆滑的滚动并坚固耐用,以确保行车的安全、平稳。
对于快速客车来讲,车辆轮对还需包括两个同类型筒材质的制动盘组成,按规定的压力和尺寸紧压配合在车轴上,以提高整个车辆的制动力。
轮对的制造是指将车轴及车轮、制动盘的毛胚经机械加工后组装成轮对,并最后对整个轮对进行加工、检查等全部工作而言,轮对制造的工艺过程如下:车轴、车轮、制动盘是靠过盈时显得紧配合联接,并采用压装法。
紧配合联接不需用键和螺钉,便能传递较大的扭矩和承受轴向载荷,因而在相同的载荷下,能减小零件的尺寸,节省金属材料。
零件的紧配合联接,也可用热装或冷装法来实现。
热装和冷装系利用加热或冷却相互配合中的某一零件,使过盈量暂时消除,以便自由的完成两者的组装,待恢复至室温后,即形成过盈而达到紧配合联接。
由于热装法及冷装法难以检查轮对组装后的质量,所以目前尚未应用于轮对组装,而压装法能根据压力及自动记录器及压力表所示出的压力曲线及压入力大小来鉴定联接的可靠程度。
因此在车辆制造中轮对的紧配合联接目前均采用压装法。
轮对的组装轮对组装的技术要求:轮对的组装质量,直接关系到行车安全,因此在组装前后应严格按下列要求进行检查。
(1)车轴、车轮、制动盘组成应符合按规定程序审批的图纸及技术条件的要求车轴座及制动盘座部的表面粗糙度应达到Ra≤1.6um,而相应的轮毂孔的表面粗糙度应达到Ra≤6.3um。
为使车轮、制动盘易于压入车轴,在车轴的轮座及制动盘座靠近外侧均应旋成锥形,作为导入部分,长度分别为(12+40)mm、(10+20)mm 。
其小端直径较大端直径小1mm,轮座与制动盘座其余部分均应旋成圆柱形,在这一部分全长内的圆柱度不得超过0.05mm,大端必须靠近轴中央一端,圆度不得超过0.02mm,直线度不得超过0.015mm;轮座、盘座加工时,应向轴中央方向加旋,轮座长为186mm,盘座长为180mm。
试论动车组轮对压装工艺项点
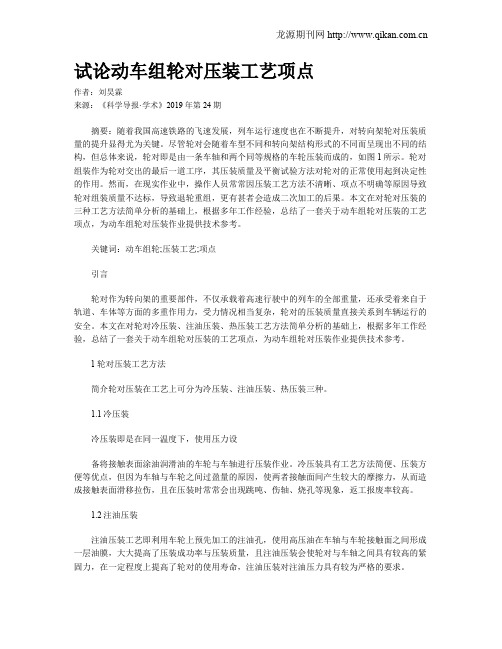
试论动车组轮对压装工艺项点作者:刘昊霖来源:《科学导报·学术》2019年第24期摘要:随着我国高速铁路的飞速发展,列车运行速度也在不断提升,对转向架轮对压装质量的提升显得尤为关键。
尽管轮对会随着车型不同和转向架结构形式的不同而呈现出不同的结构,但总体来说,轮对即是由一条车轴和两个同等规格的车轮压装而成的,如图1所示。
轮对组装作为轮对交出的最后一道工序,其压装质量及平衡试验方法对轮对的正常使用起到决定性的作用。
然而,在现实作业中,操作人员常常因压装工艺方法不清晰、项点不明确等原因导致轮对组装质量不达标,导致退轮重组,更有甚者会造成二次加工的后果。
本文在对轮对压装的三种工艺方法简单分析的基础上,根据多年工作经验,总结了一套关于动车组轮对压装的工艺项点,为动车组轮对压装作业提供技术参考。
关键词:动车组轮;压装工艺;项点引言轮对作为转向架的重要部件,不仅承载着高速行驶中的列车的全部重量,还承受着来自于轨道、车体等方面的多重作用力,受力情况相当复杂,轮对的压装质量直接关系到车辆运行的安全。
本文在对轮对冷压装、注油压装、热压装工艺方法简单分析的基础上,根据多年工作经验,总结了一套关于动车组轮对压装的工艺项点,为动车组轮对压装作业提供技术参考。
1轮对压装工艺方法简介轮对压装在工艺上可分为冷压装、注油压装、热压装三种。
1.1冷压装冷压装即是在同一温度下,使用压力设备将接触表面涂油润滑油的车轮与车轴进行压装作业。
冷压装具有工艺方法简便、压装方便等优点,但因为车轴与车轮之间过盈量的原因,使两者接触面间产生较大的摩擦力,从而造成接触表面滑移拉伤,且在压装时常常会出现跳吨、伤轴、烧孔等现象,返工报废率较高。
1.2注油压装注油压装工艺即利用车轮上预先加工的注油孔,使用高压油在车轴与车轮接触面之间形成一层油膜,大大提高了压装成功率与压装质量,且注油压装会使轮对与车轴之间具有较高的紧固力,在一定程度上提高了轮对的使用寿命,注油压装对注油压力具有较为严格的要求。
轮对压装工艺过程浅析

轮对压装工艺过程浅析作者:林路路宋宇晗来源:《中国科技博览》2019年第11期[摘要]随着城市轨道交通的蓬勃发展,城轨车辆运行的平稳性及安全性受到越来越多的人的关注。
轮对组成作为转向架的核心组成部分,其组装质量直接关系到了列车的运行安全。
轮对组成采用压装的工艺方法,利用过盈配合使车轴与车轮之间紧密连接,本文针对目前城轨转向架的轮对压装过程,总结压装过程中的关键工艺要点,为转向架轮对压装质量提升提供参考。
[关键词]城轨转向架,轮对压装,工艺要点,质量提升中图分类号:U270.331.1 文献标识码:A 文章编号:1009-914X(2019)11-0298-011、引言随着我国经济的快速稳定发展,越来越多的城市为缓解城市拥堵开始修建城市轨道交通网络。
转向架作为城轨车辆的走行部,组装质量要求更是严格。
转向架上的轮对组成直接与轨道接触,最先受到轮轨间的作用力,尤其是运行过程中的硬性冲击。
轮对压装的难度系数大,质量管控要求高,本文通过浅析目前城轨转向架轮对压装的一般过程,找出压装过程中着重注意的关键工艺要点,提高轮对压装效率。
2、轮对组成结构由于城轨车辆运行速度一般限制于80km/h~120 km/h之间,速度等级不高,车轮材质往往选择CL60钢材,车轴材质选择LZ50钢材。
车轮上与钢轨相接触的部分称为轮辋。
轮辋上与钢轨相接触的表面称为踏面,目前采用的一般为LMA型磨耗踏面。
踏面一侧凸起的部分称为轮缘,轮缘位于钢轨的内侧,可防止轮对滚动脱轨,并起导向作用。
车轮上与车轴相结合的部分称为轮毂。
轮毂与轮辋用轮辐连接。
轮辐可以是连续的圆盘,称为辐板。
为了进一步缓和轮轨间的硬性冲击,缓冲作用力,部分城轨车辆采用空心车轴进行轮对组成,以达到减少簧下质量减少冲击作用的效果,轮对组成如图1所示。
3、压装方法车轴与车轮间采用压装方法来实现彼此间的过盈配合。
过盈配合产生的过盈量可以实现半径方向产生接触面的强压力,并依靠接触面的强压力产生静摩擦力实现扭矩及轴向力的传递。
轮对压装机全解
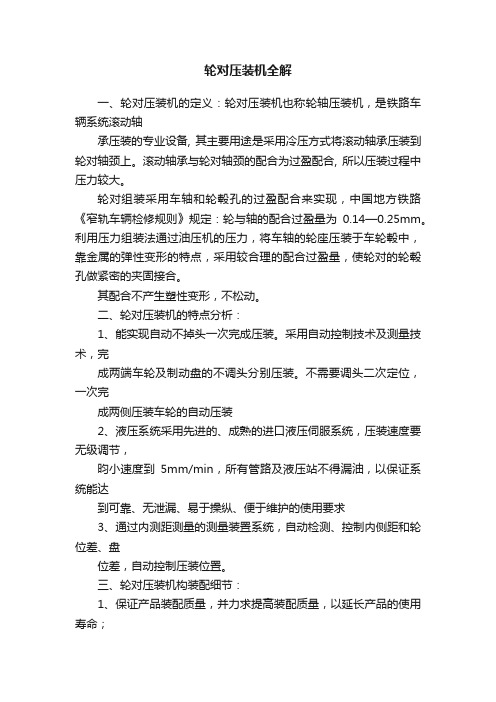
轮对压装机全解一、轮对压装机的定义:轮对压装机也称轮轴压装机,是铁路车辆系统滚动轴承压装的专业设备, 其主要用途是采用冷压方式将滚动轴承压装到轮对轴颈上。
滚动轴承与轮对轴颈的配合为过盈配合, 所以压装过程中压力较大。
轮对组装采用车轴和轮毂孔的过盈配合来实现,中国地方铁路《窄轨车辆检修规则》规定:轮与轴的配合过盈量为0.14—0.25mm。
利用压力组装法通过油压机的压力,将车轴的轮座压装于车轮毂中,靠金属的弹性变形的特点,采用较合理的配合过盈量,使轮对的轮毂孔做紧密的夹固接合。
其配合不产生塑性变形,不松动。
二、轮对压装机的特点分析:1、能实现自动不掉头一次完成压装。
采用自动控制技术及测量技术,完成两端车轮及制动盘的不调头分别压装。
不需要调头二次定位,一次完成两侧压装车轮的自动压装2、液压系统采用先进的、成熟的进口液压伺服系统,压装速度要无级调节,昀小速度到5mm/min,所有管路及液压站不得漏油,以保证系统能达到可靠、无泄漏、易于操纵、便于维护的使用要求3、通过内测距测量的测量装置系统,自动检测、控制内侧距和轮位差、盘位差,自动控制压装位置。
三、轮对压装机构装配细节:1、保证产品装配质量,并力求提高装配质量,以延长产品的使用寿命;2、合理安排装配工序,尽量减少钳工装配工作量;3、提高装配工作效率,缩短装配周期;4、尽可能减少车间的作业面积,力争单位面积上具有最大生产率。
压装机由机体、液压站和控制台三部分组成,液压站和控制台相对主机应该就近布置,现场的钢轨与机体上的导轨应该联结平整。
四、轮对压装机使用须知:1、开机前对设备的导轨进行润滑、检查各个机械部件运转状态是否正常。
2、开机前检查各开关等是否有损坏,继电器接触是否良好等,发现损坏需及时更换。
在保养过程中保持各开关的有效动作位置,若发生变化要及时调整。
3、每天开机前检查计算机主机、显示器、打印机的电源线已经连接;开机后检查测试系统是否有计算机病毒或木马程序运行侵害。
轮对压装标准关键技术研究

参考文献
[1]徐国明影响轮对压装质量的因数[J].《机车车辆工艺》.1984.02
[2]冯绍艳机车轮对组装标准对比研究[J].《机车车辆工艺》.201》.2002.02
压装前需测量车轮轮毂孔及车轴轮座的大端直径符合,并确认过盈量满足要求。在批量生产过程中,根据技术要求及实际操作经验,可将过盈量确定在要求范围的中值偏上,并将车轴及车轮加工的尺寸范围减小以达到轮轴任意配和便可满足要求。由于测量工具的精度及磨损、测量方式及准确度等原因,轮轴测量直径易出现测量误差,导致过盈量不满足实际压装需求。在实际生产中需要对测量的工具,如千分尺、千分表等测量器具进行校准并定期检定,尽量避免工具误差;人工测量车轮及车轴尺寸时可选取多截面,且每个界面在不同角度测量多组数据进行比对,减少人为测量误差。
车轮加工后压人端定大小的圆角且圆角与轮毂孔的相切点须处理圆滑过渡使车轮易于压人轮毂由于机械切削加工特性过渡位置处易产生挤压变形棱边划痕等情况压装前需将车轴轮座包含引入部分车轮轮毂孔包含引人部分进行充分处理清除上面的毛刺高点粒状或线状杂质等
轮对压装标准关键技术研究
轮对承受着轨道车辆全部载荷,需要在高负载工况下进行高速转动。车轮与车轴压装作为关键工序,保证各项压装参数,控制轮轴压装质量是轮对生产控制的重点。
浅谈高速动车组欧系日系轮对压装工艺

浅谈高速动车组欧系日系轮对压装工艺摘要:本文介绍了高速动车组转向架轮对压装中常用的压装工艺,并结合国内较为成熟的车型CRH2A动车组轮对为模型,对欧系和日系轮对压装工艺进行对比分析,并就现场生产中的压装工艺选用给出了合理化建议。
关键词:高速动车组;轮对压装;压装工艺;油压;冷压前言轮对作为直接传递轮轨作用力的最为关键的走行装置在整个车辆系统中的作用至关重要。
目前,国内动车组轮对的制造检修依据主要分为欧标和日标两大类,故本文就以国内较为成熟的车型CRH2A动车组轮对为模型,对欧系和日系轮对压装工艺进行对比分析。
1.轮对压装工艺运用现状1.1 压装方法轮对压装方法主要分为:注油压装和普通压装。
普通压装又分为冷压装和热压装。
轮对注油压装是指压装时,在车轴轮座和车轮毂孔之间注入高于它们接触应力的高压油,使之形成油膜,随着轮座和毂孔接触面积的增加,高压油不断渗透,使整个轮对压装过程在被油膜隔开的情况下进行。
而与之对应的即为普通压装,分为热压和冷压,热压即将整体车轮或轮心加热,使轮毂孔膨胀后装在车轴上,而在常温下成为过盈配合的装配方法,而冷压就是一直通过压力机在过盈状态下将车轮或轮心装到车轴上。
1.2 压装工艺路线动车组轮对压装一般遵循以下工艺路线:轮、轴同温—轮座、毂孔尺寸测量—轮座打磨—润滑剂涂抹—轮对选配—轮对压装(欧系、日系不同)—压装后检查—检压—轮对标记—超声波探伤—其它工序。
图1 日系轮对注油压装曲线目前在CRH2A的新造检修中,日系轮对采用注油压装,见图1,压装起始阶段也是使用冷压方式,将毂孔套压进车轴,同时关注压装力曲线变化,待曲线出现下降,见图中A点,此时即为注油槽开始进入压装部,A—B段为注油槽部通过压装部,待注油槽全部通过,压力回升,此时注油槽部位完全与车轴贴合,暂停压力机,连接油泵对注油孔注油,高压油泵压力表目标值设定为140MPa,油压变化范围控制在(120MPa-150MPa)之间,待轮毂端面渗出高压油时,再次开启压力机注入高压油继续压装,最后轮毂孔与轮座到达压装位置,此时油膜完全隔开轮毂、轮座接触面,压力降为0,作业完成。
高铁轮对压装工艺的研究

高铁轮对压装工艺的研究作者:吕惠来源:《中国科技博览》2016年第16期单位代码:91140100666633795J中图分类号:U270.6 文献标识码:A 文章编号:1009-914X(2016)16-0070-01车轴、车轮加工的工艺、内部探伤和表面探伤确保了轮对连接的准确性,压装后轮对的内侧距、轮位和制动盘盘距等参数必须符合相关的规定来保证滚动平稳性。
高铁轮对除了承受一定的装配力,还要承受复杂的静载荷、动载荷以及在制动时由闸瓦的摩擦产生的热应力,因此对轮对的强度有很髙的要求。
同时轮对作为簧下重量,在轮轨线路产生了很大的动载荷,随着机车速度的提髙,这种动载荷的影响会越来越大。
因此为提高行车的安全性能,就要尽可能减轻簧下重量,选择材料性能良好的轮对部件材料,同时要保证轮对组装的质量和过盈配合面良好的应力应变状态。
在轮对压装的过程中,车轮和车轴配合面处的应力应变状态会发生改变,在轮对的微小结构特征处如圆角、倒角和过渡圆弧等会有应力集中的现象,它是轮对微动损伤和疲劳裂纹形成的主要源头。
因此,本文提出轮对过盈配合面应力应变状态的研究。
在保证压装曲线合格的情况下,也要保证配合面良好的状态。
并结合现有的铁路标准,为构建完善的轮对压装质量评价体系提供理论基础。
意大利D Benuzzi和G Donzella等提出一种预测车轴和车轮压装曲线的方法。
测量摩擦样品直接取自车轴和车轮。
为了改变接触表面的润滑条件,他们开发出一种能够适应轴向试验机的新装置,它可以实现接触压力和滑动速度的变化。
基本尺寸相同的轴和孔的相互结合,叫做配合。
由于轴和孔的实际尺寸并不相同,轴和孔的配合表现出不同的配合性质,当孔的实际尺寸减去轴的实际尺寸的代数差值为负即为过盈。
高铁轮对采用过盈配合,主要用于孔轴零件的紧配合。
因结构简单,对中性好并能承受人的载荷;同时由于不需要紧固件的联接,进而避免了釆用键槽定位而削弱,零件强度的缺点,因此在实际生产制造中普遍采用过盈配合做周向定位和传递扭矩。
轮对压装知识分享

轮对压装影响车辆轮对组装质量的因素压装曲线轮对是窄轨车辆的重要部件,其质量的好坏,直接影响到行车安全。
作为轮对生产的重要环节——轮对的组装应引起我们的高度重视。
轮对组装采用车轴和轮毂孔的过盈配合来实现,中国地方铁路《窄轨车辆检修规则》规定:轮与轴的配合过盈量为0.14—0.25mm。
利用压力组装法通过油压机的压力,将车轴的轮座压装于车轮毂中,靠金属的弹性变形的特点,采用较合理的配合过盈量,使轮对的轮毂孔做紧密的夹固接合。
其配合不产生塑性变形,不松动。
鉴于车辆轮对受力复杂,使用年限长,加之轮对在制动时闸瓦和车轮磨擦产生的高热传导的轮毂会引起轮毂孔的膨胀,轴颈运转热传导到轮座会引起轮座膨胀等情况《窄轨车辆检修规则》规定压装的最终压力按轮毂孔直径计算,每100mm最小不得低于30吨,最大不得超过50吨;压力机应同时具备压力表及自动记录仪器,保持作用良好,曲线与压力表吨数差不超过5吨;正常合格的压装曲线,在压装全过程中其压力应当是均匀增长。
由于压装力的大小及压力曲线的开头直接关系到轮对的压装质量,而影响压装力和压力曲线形状的因素又较多,现仅就实际工作中易产生的几个因素加以分析。
一、轮座与轮毂孔压旋削加工时的几个形位公差对压装力的影响。
(一)配合表面粗糙度对压装力的影响机床转速的快慢,进刀量的多少对工件表面粗糙度都有一定的影响,而在测量轮座、轮毂孔尺寸时,测点均系表面波峰值,在压装过程中,波峰值被擦平,对过盈量会产生一定的影响,使得配合的结合力减小,影响压装质量,因此在组装工艺中规定:轮毂孔加工后粗糙度为Ra1.6um,轮座的粗糙度为Ra1.6um,Ra值的过大或过小,都会导致压装过程中出现跳“吨”现象。
(二)圆锥度对压装力的影响为保证压装曲线逐渐上升,组装过程中沿轴线接触面的过盈值应相对稳定或趋于上升,过盈值的选取应以测量压装接触长度的中点的数值为宜,因此,如果轮座与轮毂孔圆锥度较大且方向一致时,在开始压装时,会出现压力小或没压力,而压装一定量的长度时随过盈量的增加压力迅速增大,造成曲线的长度不够;如果前端过盈量大,在压装开始时,压力上升迅速,末端过盈量小,不能继续“长吨”甚至出现“降吨”,同样造成压力曲线不合格。
CRH3动车轮对压装选配_王守杰王全先孙建军杨霄

轮对是由 1 根车轴和 2 个相同的车轮组成,在 轮轴结合部位采用过盈配合。 研究表明, 轮轴配 合部位的应力状态对车轴的疲劳强度有重要的影 响,因此,轮对压装质量的好坏很大程度上决定 了机车运行状况的好坏。 目前判断轮对压装是否 合格的唯一依据就是压装曲线。 轮轴压装过程中, 车轴的轮座部分在压装力的作用下沿车轮轮箍孔 移动,在压装配合面产生弹性和塑性变形, 当压 装力克服了压装配合面上正压力产生的摩擦阻力 时,车轴和轮箍孔表面产生相对移动, 从而实现 轮轴的压装。 在压装过程中, 可以通过压力表所
轮毂最大 等效应力 / MPa 202. 987 203. 644 204. 568 205. 748 207. 126
图1
轮对二维轴对称模型
0. 07 0. 09 0. 11
2
过盈量对轮对压装的影响
0. 13
国家标准规定过盈量取值范围为轮座直径的 0. 8 ‰ ~ 1. 5 ‰ , 轮 座 直 径 为 198 mm , 因 此 过 盈量的范围为 0. 158 4 mm ~ 0. 297 mm , 在此范 围内取几 组 过 盈 量 , 在 不 考 虑 轮 毂 轮 座 公 差 且 摩擦因数取相 同 数 值 的 情 况 下 , 得 到 表 1 中 几 组数据。
Hale Waihona Puke *安徽省省属企业自主创新科技计划项目 ( 12010202144 )
— 72 —
《起重运输机械》
2014 ( 2 )
1
有限元模型的建立
表1 过盈量 / mm 0. 178 2 0. 217 8 0. 257 4 0. 297 0
过盈量对轮对压装的影响 车轴最大等效 应力 / MPa 154. 800 189. 167 223. 522 253. 182 最大压装力 / kN 740. 23 904. 70 1 069. 10 1 210. 30
轮对压装工艺分析

轮对压装工艺分析作者:杨廷琦曹振山纪炜来源:《科学与信息化》2019年第04期摘要轮对组成承载着整个车辆的载荷,是车辆走行部的重要组成部分,直接影响到车辆运行的安全性与稳定性。
本文从轮对的压装工艺着手,分析轮对压装质量保证及质量提升。
关键词轮对组成;压装工艺;质量提升1 研究背景随着高速动车组的不断发展,列车运行速度在不断刷新。
高速度运行的动车组列车受到的振动成倍增加,导致走行部轮对受到的硬性冲击不断增强。
轮对组成作为走行部的重要零件,主要负责承载列车重量,承受轨道对轮对的冲击,利用与轨道的黏着力产生驱动力及制动力等。
轮对组成的质量决定了列车运行的安全与稳定,本文从轮对压装工艺着手,分析讨论提升轮对压装质量的关键点[1]。
2 轮对组成结构轮对组成分为动车车轮以及拖车车轮,主要区别在于是否均有驱动装置。
本文主要对轮对压装工艺进行探究,动车轮对组成与拖车轮对组成在轮对压装方面不存在差异性,本文以拖车轮对组成作为研究对象进行分析。
拖车轮对组成主要由车轴、车轮、制动盘、轴箱组成等部分构成[2]。
3 压装工艺分析3.1 压装工艺简介轮对压装工艺有三种不同的类型,分别为注油压装,冷压装,热压装。
注油压装工艺即利用车轮上预先加工的注油孔,使用高压油在车轴与车轮接触面之间形成一层油膜,使整个压装过程被油膜隔开;热压装工艺即车轮进行均匀加热处理,以热涨效应抵消车轮孔与轴径之间的过盈量;冷压装即是在同一温度下,使用压力设备将接触表面涂油润滑油的车轮与车轴进行压装作业。
3.2 轮对注油压装工艺根据轮对材质及结构的差异性,采用不同的压装工艺。
本文介绍的动车组轮对压装采用注油压装工艺操作方法,由于油膜的作用提高了压装成功率与压装质量,且注油压装会使轮对与车轴之间具有较高的紧固力,在一定程度上提高了轮对的使用寿命[3]。
轮对注油压装在轮对组装压力机上完成,组装前首先对轮对及车轴配合处清洁处理,保证接触面无灰尘、无损伤。
将轮对及车轴放置于压力机的位置,向注油口中注入高压油,注油油压约为(120~150)MPa,压装力小于900kN。
轮轴冷压装问题的分析及解决

0 . 0 2 mm,不许有非正 常刀痕沟槽 。轴座的配合表
1 . 轮对冷 压装工 艺路线简 介
工艺路 线 为 :压装 前的 准备 ( 车轮 车 轴的加
工 )一 轮轴 在 压 装 机 上 装 夹 定位 一轮 轴 压 装 。 从 工
面选用磨削加工 ,其表面粗糙度值按 = 1 . 6 m 控
氟乙烯 ,车 削加 工成 。导 向套作用是 压装时 引导
露
冷 加 工 - -
3 1
T n 薏
轮 、轴 对 中 ,保证 同心 ,防止 配 合面 被 擦 伤 。保 护 套作 用 是避 免 轴端 面 直 接 受 力造 成 塑性 变 形 。导 向 套 与保 护 套使 用方 法 如 图4 所 示 ,天 车 吊装 车 轴 放 焊 接件 工 装 ,工 装 制 作好 后 ,先 试 用 工 装 ,找 到
采用 图5 定位工装控制内侧距) ,压装过程 中不许
停机。
_ — —
图5 工装设计 图
工装使用方法 ( 见 图6 ) :先在车 轴上安装
1 J ~] r ] 厂 。 。 。 ] 『 — —1 r 1 f _ _ ]
轴端导向套
广 r l q l , I
LL
护 套 、导 向套 ,用 油 压 机先 压 入 一端 车 轮 ,再 压
故。
轮和车轴采用过盈 配合 ( H7 / u 6 ),两车轮 内侧距
一
般要求控制在 ( L±2 )mm。轮 对 的 组 装 一 般 采
用轮轴压装机冷压装 ,压装过程 中对压装力和压装 曲线有严格要求 ,如不符合标准需重新选配压 装。 另外除了保证轮对压装的质量和精度外 ,还应控制 压装速 度来提高生产效率 。冶金车辆属于重载 型车 辆且使 用环境恶劣 ,轮对承受着车辆的全部载荷 , 并且保证其在钢轨上的运 行和转 向,轮对对车辆 的 整体性 能起着至关重要的作用 ,因此要严格把控轮
轮对压装工艺要点分析

轮对压装工艺要点分析作者:安迪徐华祥宋宇晗来源:《青年生活》2019年第18期摘要:轮对是轨道列车的重要组成部分,也是影响车辆运行安全的关键零部件,主要由一根车轴及两个车轮组成。
轮轴采用过盈配合连接,依靠过盈量传递扭矩和轴向力。
轮对采用压装工艺压装到车轴处,实现两者的过盈配合。
本文对轮对压装工艺进行论述,从压装过程中压装曲线、压装力、过盈量等多方向分析,提出压装过程中的关键工艺要点及注意要点。
关键词:轮对组成,压装工艺,关键项点1.研究背景铁路运输是我国重要的客运及货运方式,随着近些年经济的快速发展,轨道行业更是飞速发展。
轨道车辆主体由车体,转向架,制动系统,驱动系统,车辆设备等部分组成,其中转向架作为车辆的走行部结构,承担着支持车体载荷,提供驱动、制动功能以及自导向能力。
轮对作为转向架的关键部件,直接与轨道接触,为车辆安全运行提供了不可或缺的作用。
轮对与车轴压装组成,结合处过盈配合,依靠连接面产生的弹性、塑性变形,使轮对与车轴实现紧密连接。
2.轮对结构轮对组成由一条车轴与两个车轮配合组装而成。
车轴主要包括轴颈、轮座、防尘板座等组成。
轴颈承载车辆并传递载荷;轮座与车轮配合,作为结合面,通常采用锥体结构;防尘板座是轴颈与轮座的过渡部分,避免应力集中。
车轴采用碳素钢材质,热处理及机械加工处理。
为了减轻簧下质量,部分车轴采用空心车轴。
车轮由踏面、轮缘、轮辋、轮毂和辐板组成。
踏面是车轮与轨道接触的部分,现多采用LMA磨耗型踏面;轮缘是保证车辆在轨道上运行不脱离的部分;轮毂是车轮与车轴配合的部分。
车轮车轴组成如图1所示。
3.压装过程选择合适的车轴车轮进行压装,车轴与车轮结合处打磨去除毛刷,表面涂抹植物油润滑。
将车轮车轴放置恒温间8小时,实现温度的恒定。
车轮的压装采用冷压法进行,首先将车轴吊运至车轴支架处,调节车轴高度尺寸,使车轴纵向中心线水平。
然后吊运车轴套在车轴上,调节车轮状态,使车轴与车轮纵向中心线重合,进行预压装。
轮对组装常见故障及原因浅析

轮对组装常见故障及原因浅析摘要:货车轮对组装是轮对四级修的关键环节,轮对组装质量是决定列车安全可靠运行的关键,也是维护货运安全的保证。
本文结合压装曲线对常见的轮对组装故障及压装不合格分解后出现的轮座、轮毂孔拉伤原因进行了简要分析,并提出相关质量保证措施。
关键词:轮对组装;原因分析;压装曲线;保证措施1.前言轮对是车辆转向架的关键部件,如果轮对组装质量未能满足要求,车辆在运行过程中就会出现车轴和车轮的松动,内侧距超差等现象,其直接后果是造成列车脱轨事故,更会直接影响铁路干线的安全畅通。
因此,轮对组装质量关键性、重要性不言而喻。
2.轮对组装机理分析及相关工艺要求货车轮对组装采用过盈配合冷压装,在组装过程中,当压装力克服了压装配合面上径向压力产生的摩擦力时,两者间完成于水平方向产生的相对移动,从而实现轮对的组装。
压装压力曲线图是评价压装合格与否的重要条件,轮对压装时,压装压力曲线形状及终点压装力主要与配合面粗糙度、过盈量、几何形状、润滑等因素有关,曲线合格与否为多因素共同作用的结果而非单一因素造成。
压装压力曲线不合格将导致轮对进行退卸返工,分解的原车轮与原车轴不得原位进行第二次压装,须重新选配其他车轮。
且在退卸车轮过程中可能会产生车轴轮座和车轮轮毂孔内的表面拉伤,造成车轴和车轮的报废,在造成了配件材料、生产工时的浪费的同时,也影响了车间的生产节奏和生产安排,同时也会对操作工的心理造成一定的不利影响。
3.常见压装曲线不合格的产生原因及预防措施3.1压装不合格的主要表现形式及原因分析(1)压装力高于理论最大值或低于最小值,即“吨大”、“吨小”。
车轴轮座与车轮轮毂孔间为过盈配合,一般来说过盈量对压装力影响最大,轮座压入轮毂孔过程中,两者接触面上会形成垂直于接触面的径向压力,压装力与过盈量成正比关系;过盈量越大,配合面径向正压力越大,轮对组装过程中配合面的摩擦力越大,那么就可能出现轮座拉伤或吨大等问题。
反之,轮对组装过程中可能会出现吨小或曲线平直问题,从而对轮对在货车车辆运输运用过程中的安全可靠性失去保证。
- 1、下载文档前请自行甄别文档内容的完整性,平台不提供额外的编辑、内容补充、找答案等附加服务。
- 2、"仅部分预览"的文档,不可在线预览部分如存在完整性等问题,可反馈申请退款(可完整预览的文档不适用该条件!)。
- 3、如文档侵犯您的权益,请联系客服反馈,我们会尽快为您处理(人工客服工作时间:9:00-18:30)。
轮对压配合时的压装与分解
发表时间:2018-08-06T14:11:57.477Z 来源:《基层建设》2018年第18期作者:黄兵亮张尧包继文
[导读] 摘要:轮对是转向架的重要组成部分。
通过了解轮对压装的基本工艺的基础上,并进一步分析圆柱度,过盈量,压入速度和润滑剂等关键因素对轮对压装质量的影响。
中车兰州机车有限公司甘肃兰州 730050
摘要:轮对是转向架的重要组成部分。
通过了解轮对压装的基本工艺的基础上,并进一步分析圆柱度,过盈量,压入速度和润滑剂等关键因素对轮对压装质量的影响。
通过分析关键因素的影响,有助于提高轮对压装质量,从而为转向架安全工作提供重要保障。
关键词:转向架;轮对压装;关键因素
1前言
轮对本身的结构并不复杂,但是由于它承担的任务多且重要,因此它的加工制造以及组装要求都非常高。
尤其是轮对的组装对于转向架的运行表现起到关键性的作用,组装稍有差错容易引发列车停车,甚至脱轨等重大事故。
通过对轮对组装过程的分析,可以更好地保证轮对正常使用,保障列车行驶安全。
2轮对压装工艺简介
轮对本身结构较为简单,但是其对压装的要求却十分严格。
目前常见压装根据压装方式不同可以分为普通压装和注油压装两种方式。
其中普通压装根据压装温度不同可以分为热压装和冷压装。
热压装是将车轮内孔进行加热使其膨胀后再进行压装,其主要是针对过盈量较大的情况下使用。
热压装工艺设备一般较为复杂,一次投入成本较高,压装合格率较高,可提高车轴的使用寿命,止推试验效率低。
冷压装是直接通过压装机将车轮压到车轴上的方式,其主要是针对过盈量较小的情况下使用。
冷压装设备较为简单,一次性投入成本较低,但压装合格率一般,对操作要求较高,操作不当容易“戗轴”,对车轴寿命有一定影响,止推试验效率高。
而注油压装是在车轮上开注油孔,在压装过程中通过注入高压油,在车轮和车轴接触面之间形成一层油膜进行压装,其主要是针对车轴表面要求较高时使用。
注油压装设备较为复杂,操作难度较大,加工难度大,但压装过程允许停顿且不限时间,可以在一定范围内自由调整车轮位置。
这三种压装工艺目前都在使用,都有各个的优缺点。
这三种压装工艺的选择主要根据车轮和轮轴的结构以及压装的具体要求来决定的。
目前使用最为广泛使用的还是冷压装工艺。
3轮对压装影响因素
在轮对冷压装过程中,影响压装效果主要包括过盈量,圆柱度,压入速度和润滑剂等因素。
在冷压装工艺中,判断轮对组装是否合格的标准主要是通过查看压装压力曲线是否符合规范。
通过分析这些因素对压装压力曲线的影响,对于压装工作有一定的指导意义。
3.1过盈量对压装效果的影响
由于车轮和车轴在转动过程中是不能有相对运动的,因此车轮和车轴配合应采用过盈配合。
对于冷压工艺,过盈量对于压装效果起到至关重要的作用。
过盈量不足则会造成压装过程中无压力反应,车轮和车轴之间容易产生相对转动。
而过盈量过大则会在压装过程容易擦伤车轴,对车轴的寿命有影响。
在国标中,规定的过盈量取值为轮座直径的0.8‰~1.5‰。
压装压力一般是随着过盈量的增加而增加。
在实际操作中,存在着过盈量达到了规定值的下限,但是压装压力值显得偏小。
其主要是由于在实际测量过程是存在误差的,造成了过盈量误判。
在过盈量到了规定值的上限值,最后较容易出现实际压力超出了规定压力值。
因此对于过盈量在边界值的情况,测量要多次取平均降低误差,同时在压装操作过程中要更为注意。
此外在组装之前,可尽量将车轮和车轴的过盈量规定中间值附近靠拢,可降低压装过程中的要求。
3.2压入速度对压装效果的影响
在压装过程,对于压入速度控制有较高的要求。
由于车轮和车轴的压装是属于过盈压装,压装过程中两者需要一定的时间去适应彼此之间的压力。
如果压入速度过快,两者对于压力不能够及时适应,容易造成冲击从而在局部造成擦伤。
如果压入速度过于缓慢,虽然两者可以较好适应施加的压力,但是容易造成两者长久性变形,不能够较好地贴合。
3.3圆柱度对压装效果的影响
圆柱度指的是任一垂直截面最大尺寸与最小尺寸差。
圆柱度的大小关系着车轮和车轴贴合面接触效果以及受力是否均匀。
圆柱度越大,容易在压装过程中产生局部轴向残余应力,最终导致压装压力增大。
由于残余应力的存在,在使用过程会加速车轴的疲劳进而降低使用寿命。
虽然圆柱度是不可避免的,但是在压装过程可以利用其特性来解决末端压力压力降低和压力曲线末端平直的问题。
3.4润滑剂对压装效果的影响
润滑剂的使用时改善车轮与车轴之间贴合面处的摩擦因数,可以有效防止车轴擦伤。
润滑剂的使用一方面与润滑剂的种类有关,另一方面还与使用量有关。
润滑剂要能够保证良好的润滑性能,可以形成较为稳定的油膜,具备较高的熔点和较好的承载抗磨性能。
目前广泛使用的二硫化钼润滑剂能够较好地满足这些要求。
需要注意的是压装过程中润滑剂量的控制。
润滑剂不足,易导致润滑不充分,压装力较大时易造成擦伤。
润滑剂过多,又容易造成压装快完成时,积油过多导致压力下降过多而造成不合格。
因此在压装过程中要注意压力曲线的变化,如果压力陡升则可以通过增加润滑剂进行解决。
4基本情况分析
对车轮车轴材质进行分析,车轮选用ER9材质,车轴选用EA1N材质,进行金相、化学成分检测均符合要求。
从车轴轮座表面缺陷宏观形态分析,是典型的压入损伤特征,即在压装时,轮座(轮毂孔)表面的金属因异常挤压发生轴向滑移,表面金属层被破坏,最终在末端形成金属堆积。
缺陷形态呈鱼鳞片带状分布,在鱼鳞片带的终端形成大小不同的金属挤压包。
其原因主要是车轴轮座和车轮轮毂孔表面在压装过程中,配合面未形成良好的润滑油膜或者润滑油膜被破坏,造成压入过程中异常挤压,滑动摩擦转变成“黏着摩擦”所致。
在车轮车轴材质、过盈量、粗糙度和润滑油脂等均符合要求的情况下,影响润滑油膜的形成或破坏的因素,还可能与车轮和车轴压装引入时不正有关。
当车轮和车轴引入不正时,一方面在压入起始阶段,车轮在车轴表面存在极小面积或线接触,造成局部接触应力过大导致油膜未形成,在压力机轴向推力的作用下,车轴表面剪应力超过材料屈服强度引起“啃轴”,在压装曲线上表现出过高的起吨压力值且压力曲线异常波动。
缺陷存在多处,单个缺陷均有大有小,在轮座表面分散分布,同时存在纵向贯通轮座的情况。
对压退后的车轮、车轴实物端口进行检查分析,发现在车轮轮毂孔端口和车轴引导角表面存在分散缺陷,在表面多处存在高点、毛刺,在压装时随之压入,造成多处拉伤。
当缺
陷较小时,对车轴表面接触压应力影响较小,因此在压装曲线上表面为合格。
综合以上分析,在材质、过盈量、粗糙度和润滑油脂等因素均符合要求的情况下,影响轮对压装损伤的因素有:(1)车轮和车轴引入不正问题,一方面表现在车轴和压装机活塞杆不在同一轴线上,造成车轴偏斜,另一方面车轮压装引导套设计不合理,未起到引导的作用,造成车轮偏斜;(2)车轮轮毂孔端口和车轴引导角表面存在缺陷,主要与压装前对车轴引导角和轮毂孔端口处理不良有关。
5结束语
通过分析可以得知,轮对压装过程是一个十分复杂的过程,可以了解到每个因素对压装的影响。
因此在实际组装过程中,可以综合考虑上述的影响因素,从而制定出相应的解决措施。
同时在实际操作中要细心仔细,及时发现异常并找到解决措施,从而提高组装合格率。
参考文献:
[1]邱杰.润滑工艺对轮对压装质量影响机理及其试验研究[D].武汉理工大学,2015.
[2]郑佳宝.轮对过盈配合面应力应变状态的研究[D].武汉理工大学,2013.
[3]韩建斌.轮对压装曲线记录及其自动判断系统的研究[D].武汉理工大学,2012.
[4]张忠.过盈量在轮对压装中的重要性分析[J].机械工程师,2010(01):148-149.
[5]张元涛,张顺启.关于轮对压装工艺参数优化设计的探讨[J].铁道车辆,2006(07):29-30+46.。