铁路货车轮轴新组装轮对组装轴承压装作业指导书
铁路货车轮轴检修作业指导书
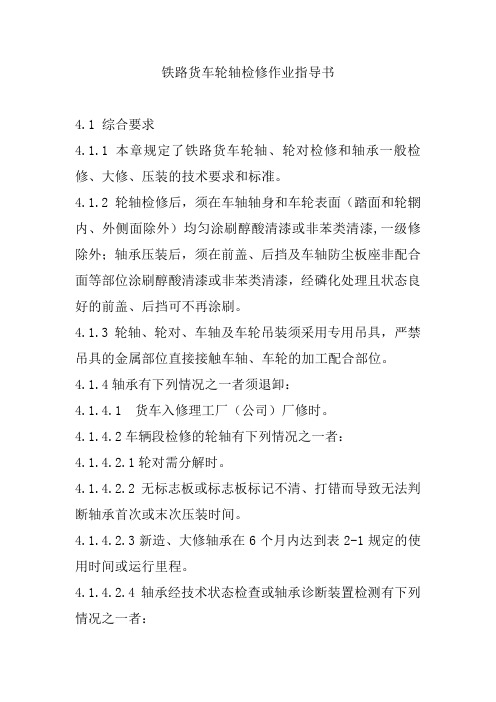
铁路货车轮轴检修作业指导书4.1 综合要求4.1.1 本章规定了铁路货车轮轴、轮对检修和轴承一般检修、大修、压装的技术要求和标准。
4.1.2 轮轴检修后,须在车轴轴身和车轮表面(踏面和轮辋内、外侧面除外)均匀涂刷醇酸清漆或非苯类清漆,一级修除外;轴承压装后,须在前盖、后挡及车轴防尘板座非配合面等部位涂刷醇酸清漆或非苯类清漆,经磷化处理且状态良好的前盖、后挡可不再涂刷。
4.1.3轮轴、轮对、车轴及车轮吊装须采用专用吊具,严禁吊具的金属部位直接接触车轴、车轮的加工配合部位。
4.1.4轴承有下列情况之一者须退卸:4.1.4.1 货车入修理工厂(公司)厂修时。
4.1.4.2车辆段检修的轮轴有下列情况之一者:4.1.4.2.1轮对需分解时。
4.1.4.2.2无标志板或标志板标记不清、打错而导致无法判断轴承首次或末次压装时间。
4.1.4.2.3新造、大修轴承在6个月内达到表2-1规定的使用时间或运行里程。
4.1.4.2.4轴承经技术状态检查或轴承诊断装置检测有下列情况之一者:(1)轴承(包括外圈、前盖、后挡、轴端螺栓等)有裂纹、碰伤、松动、变形和其他异状。
(2)密封罩、密封座、油封、密封组成有裂纹、碰伤、松动、变形,密封组成高于外圈端面,SKF 197726、353130B、353132A(352132A)、353132B(353132X2-2RS)型轴承密封组成中骨架与油封脱胶影响密封性能。
(3)轴承密封失效,有甩油、混砂、混水或油脂变质现象。
(4)转动轴承有异音、卡滞或其他不正常现象。
(5)轴承的轴向游隙大于0.75 mm;(6)电焊作业导致电流通过轴承。
(7)空车脱轨轮轴的同一转向架上的所有轴承,车辆颠覆或重车脱轨后的全车轴承。
(8)轮轴上遭受水浸或火灾的轴承。
(9)发生热轴故障或车辆滚动轴承故障轨边声学诊断系统(TADS)预报需退卸的轴承。
(10)使用时间达到 20 年的国产 RD 2型 40 钢车轴上的轴承。
铁路货车轮对和滚动轴承组装及检修规则

4.1轮对组装范围4.1.1轮对新组装:轮对新组装是以新制车轮及车轴按新制(原型)技术标准组装的轮对。
4.1.2轮对重新组装:轮对重新组装是以旧车轮和旧车轴(拼修)、旧车轮和新车轴(换轴)及新车轮和旧车轴(换轮)按厂修技术标准组装的轮对。
4.2轮对组装要求4.2.1 同一车轴上必须组装同型号、同材质的车轮(除另有规定者外,不同国家或不同厂家制造的车轮不得混装)。
4.2.2轮对应以同型号的车轴和车轮相组装。
当车轮与车轴型号不同时,轮对型号以车轴型号为准,组装规定如下:4.2.2.1 D型车轮可组装在轮座直径为197mm及以下的E 型车轴上;4.2.2.2 E型车轮可组装在轮座直径为192mm及以上的D 型车轴上。
4.2.3 向同一车轴上组装的两个车轮轮辋宽度相差不得超过5mm,其内侧距离应按最小轮辋宽度的规定执行;轮辋宽度小于127mm的车轮不得再组装使用。
4.2.4轮对退轮检查后,其原车轮与原车轴不得重新组装。
4.2.5轮座和轮毂孔旋配技术要求4.2.5.1轮对组装时,轮毂孔及轮座应在相同环境温度下同温8小时后进行加工、测量、选配和组装。
4.2.5.2轮座与轮毂孔采取过盈配合,配合过盈量按轮座直径的o.8‰~1.5‰执行;4.2.5.3轮毂孔和轮座的直径尺寸必须符合规定限度,并且同一车轴上两端的轮座直径相差不得超过3mm。
4.2.5.4 轮座加工后的圆度不得超过O.020mm,内外侧的直径差不得超过O.1mm,并且大端必须在内侧。
4.2.5.5 轮座的终加工可采用磨削或滚压工艺,采用滚压工艺做为终加工时,轮座经车削加工表面粗糙度必须达到Ra3.2μm后方可进行滚压加工,经磨削或滚压加工后表面粗糙度应达到Ra1.6μm,但由于压装工艺的原因,为保证压装力曲线合格,轮座表面粗糙度可放宽到Ra2.0μm。
4.2.5.6轴身直径不得大于轮座直径,轮座与轴身过渡部分的圆弧半径必须符合图纸规定,过渡部分的表面粗糙度必须达到Ra6.3μm。
铁路货车轮轴新组装轮对组装轴承压装作业指导书
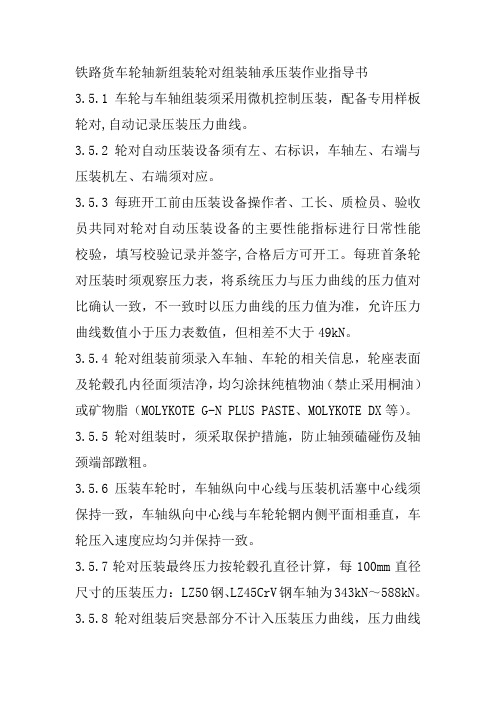
铁路货车轮轴新组装轮对组装轴承压装作业指导书3.5.1车轮与车轴组装须采用微机控制压装,配备专用样板轮对,自动记录压装压力曲线。
3.5.2轮对自动压装设备须有左、右标识,车轴左、右端与压装机左、右端须对应。
3.5.3每班开工前由压装设备操作者、工长、质检员、验收员共同对轮对自动压装设备的主要性能指标进行日常性能校验,填写校验记录并签字,合格后方可开工。
每班首条轮对压装时须观察压力表,将系统压力与压力曲线的压力值对比确认一致,不一致时以压力曲线的压力值为准,允许压力曲线数值小于压力表数值,但相差不大于49kN。
3.5.4轮对组装前须录入车轴、车轮的相关信息,轮座表面及轮毂孔内径面须洁净,均匀涂抹纯植物油(禁止采用桐油)或矿物脂(MOLYKOTE G-N PLUS PASTE、MOLYKOTE DX等)。
3.5.5轮对组装时,须采取保护措施,防止轴颈磕碰伤及轴颈端部蹾粗。
3.5.6压装车轮时,车轴纵向中心线与压装机活塞中心线须保持一致,车轴纵向中心线与车轮轮辋内侧平面相垂直,车轮压入速度应均匀并保持一致。
3.5.7轮对压装最终压力按轮毂孔直径计算,每100mm直径尺寸的压装压力: LZ50钢、LZ45CrV钢车轴为343kN~588kN。
3.5.8轮对组装后突悬部分不计入压装压力曲线,压力曲线须符合附件3规定。
3.5.9压力曲线等不合格时,应及时分解轮对。
分解时,车轴的中心线与压力机活塞的中心线应保持一致,并采取保护措施,防止轴颈蹾粗和磕碰伤,车轮压退时的最大压应力不超过车轴材质的下屈服强度。
3.5.10不得将分解的原车轮与原车轴原位进行第二次压装,在原车轴、车轮表面无损伤的情况下,可重新选配其他新加工过的合格车轮、车轴进行压装。
分解后有拉伤的车轮、车轴须重新加工,清除缺陷后方可使用。
若车轴经重新加工后须对再加工部位进行复合磁化荧光磁粉探伤检查。
3.5.11轮对压装压力曲线图表(车统-57)须与轮轴卡片(车统-51)装订在一起一并传递、保存,且车统-51、车统-57与轮对实物相符;同一条轮对的不合格压装压力曲线和合格曲线记录一并保存。
轮对轴箱、轴承组装作业指导书

轮对轴箱、轴承组装作业指导书标准化轮对轴箱、轴承组装岗位安全风险提示1.工作时必须穿防砸皮鞋,作业过程中工作人员不得站在钢轨上,防止车轮碾伤、配件砸伤。
2.穿戴好安全帽,防止组装机碰撞头部。
3.严格按照操作规程进行作业,防止设备故障。
类别:段修(A2修)系统:走行装置部件:轮对及轴箱轮对轴箱、轴承组装作业指导书适用车型:22B、25B、25G、25K、25T作业人员:轮对组装工2名作业时间:5分钟/条工装工具: 1. 轮对轴箱组装机;2. 塑料袋;3. 电子秤;4. 铜棒;5. 喷壶。
作业材料:1. 白手套;2. 变压器油;3. 铁道车辆轴承Ⅳ型润滑脂/SHC-100型专用油脂;4. 干净棉布。
参考资料:《铁路客车轮对和滚动轴承轴箱组装及检修规则》铁运〔2013〕191号安全防护及注意事项:警告——工作时必须穿防砸皮鞋,作业过程中工作人员不得站在钢轨上,防止车轮碾伤、配件砸伤。
注意——穿戴好安全帽,防止组装机碰撞头部。
基本技术要求:1.注意——每日开工前做好组装机的校验工作,并记录。
2.注意——注油量要符合《客车轴承注油脂量表》[附件]要求。
3.注意——组装过程中车轴与轴箱内径中心轴必须保持同心,防止轴承拉伤轴颈。
4. 注意——轻拿轻放,防止配件碰伤。
作业环境与作业位置:轮对组装间质检组必查抽检项目:必查:轮对、轴箱、轴承组装抽检:轴承组装核对编号及厂家型号、材质第 1 页 共 4 页轮对轴箱、轴承组装作业指导书序号 作业项目工具及材料作业程序及标准作业图示1工前准备电子称、塑料袋、轮对轴箱组装机1.1作业前,应先了解当班组装计划,穿戴好安全帽、防砸皮鞋等防护用具。
1.2检查作业工具、材料是否齐全。
1.3每日开工前,通过传送带将待组装轮对按顺序排列在组装线上,轮对摆放到位[图1],检查轮对轴箱组装机各部状态,检查油脂状况,要求无杂质、无混水、混油,状态良好,并校验轮对轴箱组装机注油量,油脂实测值与设定值误差不得超过15g ,注油脂量设定值满足轴承注油脂量要求[附件],填写油脂称重记录、设备日常点检记录等台账,各项检查无异常方准开工。
铁路货车轮轴新组装轴承压装限度
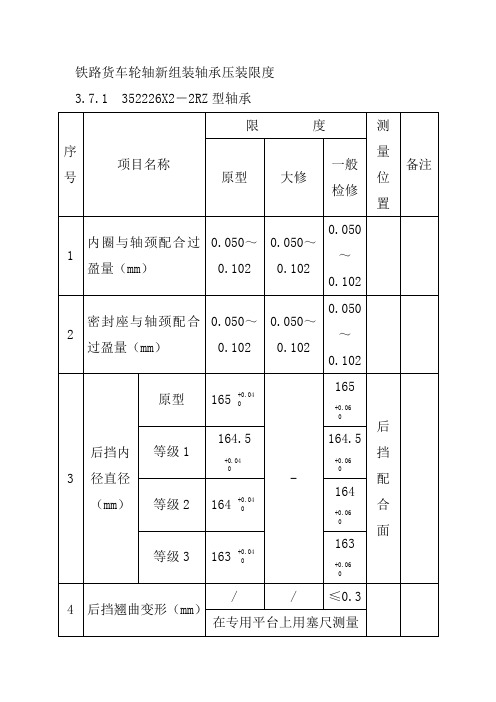
铁路货车轮轴新组装轴承压装限度3.7.1 352226X2-2RZ型轴承序号项目名称限度测量位置备注原型大修一般检修1 内圈与轴颈配合过盈量(mm)0.050~0.1020.050~0.1020.050~0.1022 密封座与轴颈配合过盈量(mm)0.050~0.1020.050~0.1020.050~0.1023 后挡内径直径(mm)原型165 +0.04-165+0.06后挡配合面等级1164.5+0.04164.5+0.06等级2 164 +0.04164+0.06等级3 163 +0.04163+0.064 后挡翘曲变形(mm)/ / ≤0.3 在专用平台上用塞尺测量5 后挡内径圆度(mm)/ / ≤0.16 后挡与防尘板座的配合过盈量(mm)0.018~0.0850.010~0.0850.010~0.0857 压装力(kN)58.8~24558.8~24558.8~2458 压装终止贴合压力(kN)392~4419 压装后的轴向游隙(mm)0.075~0.500.075~0.500.075~0.5410 测轴向游隙推(拉)力(N)294~490294~490294~49011 轴端螺栓拧紧力矩(N·m)216~226216~226216~2263.7.2 SKF 197726型轴承序号项目名称限度(mm)测量位置备注原型大修一般检修1轴承内圈与轴颈配合过盈量(mm )0.050~0.1020.050~0.1020.050~0.1022密封座与轴颈配合过盈量(mm ) 0.050~0.1020.050~0.102 0.050~0.1023 后挡内径直径(mm ) 原型165 +0.04-165 +0.06后挡配合面等级1 164.5+0.04164.5 +0.06 0等级2164 +0.040 164 +0.060 等级3163 +0.04163 +0.060 4 后挡翘曲变形(mm )//≤0.3在专用平台上用塞尺测量5 后挡内径圆度(mm ) //≤0.16后挡与防尘板座配合过盈量(mm )0.018~0.085 0.018~0.085 0.018~0.0857 压装力(kN ) 58.8~24558.8~24558.8~2458 终止贴合压力(kN ) 392~441 9压装后轴向游隙(mm )0.025~0.5080.025~0.540 0.025~0.54010 测轴向游隙推(拉)力(N )294~490 294~490294~49011 轴端螺栓拧紧力矩(N ·m )216~226216~226216~2263.7.3 353130A 型和353130X2-2RZ 型轴承序号项 目 名 称限 度测量 位置 备注原型 大修一般检修 1内圈与轴颈配合过盈量(mm )0.051~0.101 0.051~0.101 0.051~0.1012密封座与轴颈配合过盈量(mm )0.051~0.1010.051~0.1010.051~0.101适用于353130X2-2RZ 型 3 后挡内径直径(mm )原型180 +0.04-180 +0.06后挡配合面等级1 179.5+0.04 0179.5+0.06 0等级2179+0.04 0179+0.06 04后挡翘曲变形(mm )/ /≤0.3在专用平台上用塞尺测量序号项目名称限度测量位置备注原型大修一般检修5 后挡内径圆度(mm)/ / ≤0.16 后挡与防尘板座的配合过盈量(mm)0.018~0.0850.010~0.0850.010~0.0857 压装力(kN)58.8~245 58.8~24558.8~2458 压装终止贴合压力(kN)392~4419 压装后的轴向游隙(mm)0.10~0.540.10~0.540.10~0.541 0 测轴向游隙推(拉)力(N)294~490294~490294~4901 1 轴端螺栓拧紧力矩(N·m)315~345315~345315~3453.7.4 353130B(C353130)型和CTBU150(SKF ITALY V OR-7030A)型轴承序号项目名称限度测量位置备注原型大修一般检修1 内圈与轴颈配合过盈量(mm)0.051~0.1010.051~0.1010.051~0.1012 后挡内径直径(mm)原型180 0-0.1-180 +0.02-0.10后挡配合面等级1 179.5 0-0.1179.5+0.02-0.10等级2 179 0-0.1179 +0.02-0.103 后挡翘曲变形(mm)/ / ≤0.3 在专用平台上用塞尺测量4 后挡内径圆度(mm)/ / ≤0.15 后挡与防尘板座配合过盈量(mm)0.058~0.1850.058~0.1850.058~0.1856 压装力(kN)58.8~245 58.8~24558.8~2457 终止贴合压力(kN)313.6~352.8313.6~352.8313.6~352.88 压装后轴向游隙(mm)0.05~0.450.05~0.450.05~0.459 测轴向游隙推(拉)力(N)294~490 294~490294~49010 轴端螺栓拧紧力矩(N·m)315~345 315~345315~3453.7.5 F-808997.TAROL150/250-B-TVP型轴承序号项目名称大修限度备注公制英制1 内圈与轴颈配合过盈量(mm)0.051~0.1012密封座与轴颈配合过盈量(mm)0.051~0.1013 后挡与防尘板座的配合过盈量(mm)0.018~0.0854 压装后的轴向游隙(mm)≤0.5 保证轴承手动旋转灵活。
铁路货车轮轴四级检修作业指导书

铁路货车轮轴四级检修作业指导书4.5.1 基本作业条件4.5.1.1基本工序主要包括轴承修程判定,轴承退卸,轮对外观技术状态检查,轮对(车轴)清洗除锈,轮对分解,车轴穿透探伤检查,车轴检修,轮对(车轴)荧光磁粉探伤,车轮检修,车轴与车轮选配,轮对压装,车轮轮缘踏面加工,轮对尺寸检测,轴颈、防尘板座擦拭,轴承与轴颈、后挡与防尘板座检测与选配,轴颈、防尘板座涂脂,轴承压装,轴承压装到位检测,刻打标志板,轴承附件组装,轴向游隙检测,轴承磨合测试,轮轴涂漆,轮轴检查,轮轴支出。
4.5.1.2 主要工装设备固定式轴承退卸机、轮对(车轴)清洗除锈机、轮对(车轴)荧光磁粉探伤机、超声波探伤仪、数控车轮车床、轮对退卸压力机、数控车床、外圆磨床、成型磨床、数控立式车床或数控镗床、轮对自动压装机或轮对自动组装单元(含专用样板轮对)、轴承附件清洗装置、轴端标记刻打机、微控轴承压装机、标志板刻打机、轴端螺栓智能力矩扳机、轴承磨合机。
4.5.1.3 主要检测器具车轴全长及轴肩距测量尺、车轴圆弧检查样板、轴端螺栓孔螺纹塞规、轴端三孔位置度综合量规、游标深度尺(深度游标卡尺)、粗糙度测量仪、粗糙度比较样块、外径千分尺、车轮检查器、轮径尺(仪)、轮对内侧距检测尺,轮位差测量尺,车轮滚动圆跳动测量器、内径千分尺(表)、标准样环、前盖、后挡检测样板(尺)、轴承轴向游隙检测仪、力矩扳手。
4.5.2 技术要求4.5.2.1 轮轴收入4.5.2.1.1车辆段建立《轮轴卡片》(车统-51A),车辆工厂(公司)建立《轮轴卡片》(车统-51D)。
4.5.2.1.2检查轮轴信息,确定轴承修程。
4.5.2.2 轴承退卸须符合第4.4.2.2条要求。
4.5.2.3 轮对技术状态检查4.5.2.3.1清除各部位表面的油漆及锈垢,车轴外露表面须露出基本金属面。
4.5.2.3.2按规定对轮对车轴施行复合磁化荧光磁粉探伤检查和超声波探伤检查。
4.5.2.3.3检查轮对表面状态,测量轮对内侧距离、车轮直径、轮辋厚度、轮缘厚度等各部尺寸,并确定施修范围。
轮对轴承总组装作业指导书
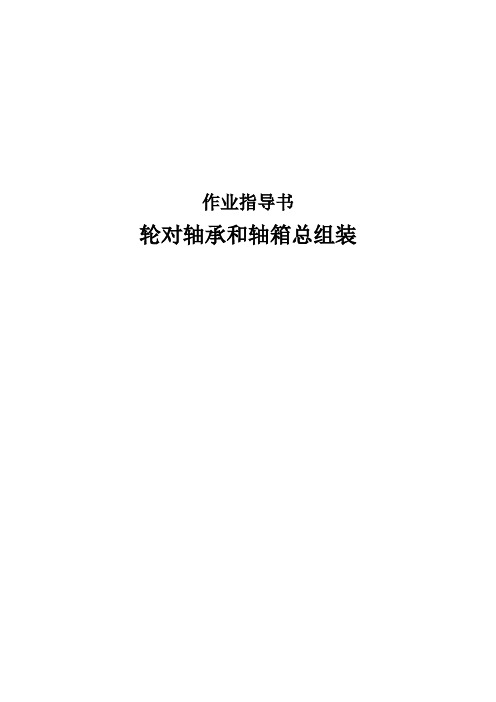
作业指导书轮对轴承和轴箱总组装轮对轴承和轴箱总组装作业指导书重要质量标准作业要点作业流程操作人员需持证上岗并,配齐劳动防护用品,温度清洁度达标作业者防护用品穿戴整齐、工具准备齐全第一步:工前准备轴承各部间隙需符合新轮规标准按顺序检测轴承各部间隙第二步;测量内圈外径,径向轴向间隙,按照检修标准做好检查,检测按照顺序作好各工位准备工作第四步;总装所需配件检查选配准备按照检修标准各工位依顺序组装严格按照标准操作第四步;轴箱轴承压装做到工完料净场地清按要求填写好各项记录表格第五步:完工清理安全风险提示1. 钻出车底时仔细观察,小心高空坠物;2. 车下作业防止磕碰、摔伤。
目次1.工前准备 (1)2.发放轴承 (2)3.测量组装后内圈外径 (3)4.测试轴承转动 (4)5.组装后径向间隙测量 (5)6.轴箱检测 (7)7.轴箱内孔刷油 (8)8.轴箱配件选配 (9)10.轴承入库发放 (14)11.开工轴承脂称量校验 (15)12.轴箱轴承压装 (16)13.完工轴承脂称量校验 (19)14.完工清理 (20)轮对及轴箱装置检修作业指导书类别:A2修系统:轮对及轴箱装置部件:轮对轴箱轮对轴承和轴箱总组装作业指导书适用车型:22、25B、25G、25K、19K、25T作业人员: 4名轮轴装修工作业时间: 40分钟工装工具:1、塞尺、外径千分尺、内径量表、深度游标卡尺、 M22h级螺纹环规、电子称、接盘、毛刷、粉笔2、轮对轴承组装机械手、轴承运输小车、YAG-50激光雕刻机作业材料:Ⅳ型轴承油脂、变压器油、轴承、轴箱作业场所:轮轴组装间环境要求:工作间内空气清洁度、地面清洁度符合要求;工作间内的温度为16℃-30℃,相对湿度≤60%。
操作规程:参考资料:1.《铁路客车轮轴组装检修及管理规则》(铁总运〔2013〕191号)安全防护及注意事项:警告—— 1.职工劳动保护着装规范,穿劳保皮鞋,防止滑倒受伤。
2.组装过程中应防止配件砸伤手脚。
【参考文档】轴承装配作业指导书-优秀word范文 (10页)
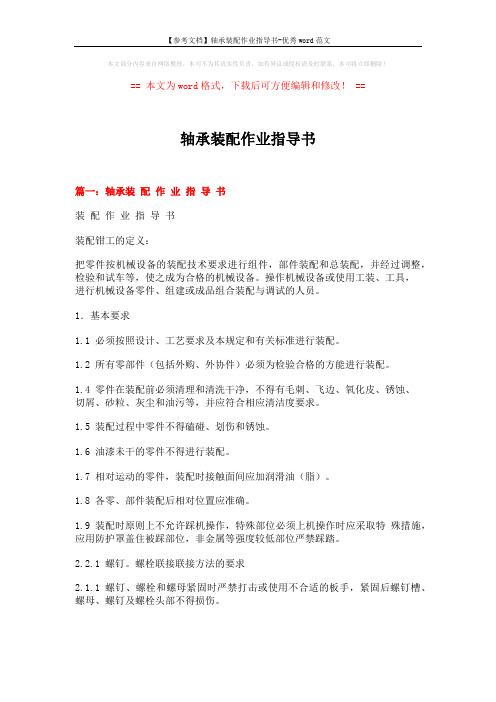
本文部分内容来自网络整理,本司不为其真实性负责,如有异议或侵权请及时联系,本司将立即删除!== 本文为word格式,下载后可方便编辑和修改! ==轴承装配作业指导书篇一:轴承装配作业指导书装配作业指导书装配钳工的定义:把零件按机械设备的装配技术要求进行组件,部件装配和总装配,并经过调整,检验和试车等,使之成为合格的机械设备。
操作机械设备或使用工装、工具,进行机械设备零件、组建或成品组合装配与调试的人员。
1.基本要求1.1 必须按照设计、工艺要求及本规定和有关标准进行装配。
1.2 所有零部件(包括外购、外协件)必须为检验合格的方能进行装配。
1.4 零件在装配前必须清理和清洗干净,不得有毛刺、飞边、氧化皮、锈蚀、切屑、砂粒、灰尘和油污等,并应符合相应清洁度要求。
1.5 装配过程中零件不得磕碰、划伤和锈蚀。
1.6 油漆未干的零件不得进行装配。
1.7 相对运动的零件,装配时接触面间应加润滑油(脂)。
1.8 各零、部件装配后相对位置应准确。
1.9 装配时原则上不允许踩机操作,特殊部位必须上机操作时应采取特殊措施,应用防护罩盖住被踩部位,非金属等强度较低部位严禁踩踏。
2.2.1 螺钉。
螺栓联接联接方法的要求2.1.1 螺钉、螺栓和螺母紧固时严禁打击或使用不合适的板手,紧固后螺钉槽、螺母、螺钉及螺栓头部不得损伤。
2.1.2 有规定拧紧力矩要求的紧固件,应采用力矩扳手按规定拧紧力矩紧固。
未规定拧紧力矩的螺栓,其拧紧力矩可参考附录2的规定。
2.1.3 同一零件用多个螺钉或螺栓紧固时,各螺钉(螺栓)需顺时针、交错、对称逐步拧紧,如有定位销,应从靠近定位销的螺钉或螺栓开始。
2.1.4 用双螺母时,应先装薄螺母后装厚螺母。
2.1.5 螺钉、螺栓和螺母拧紧后,螺钉、螺栓一般应露出螺母1-2个螺距。
2.1.6 螺钉、螺栓和螺母拧紧后,其支承面应与被紧固零件贴合。
2.2 键连接2.2.1 平键与固定键的键槽两侧面应均匀接触,其配合面间不得有间隙。
轴承安装、拆卸技术手册及作业指导书

大型养路机械轮对车轴E轴无轴箱轴承拆卸与安装技术手册一、目的指导大型养路机械轮对车轴E轴无轴箱轴承的检修、更换;二、引用标准和文件《轮对车轴轴承维护与保养的补充说明》《铁路货车轮轴组装检修及管理规则》《DKL-48k连续式三枕捣固稳定车检修规则》铁姆肯厂家《车轴轴承安装与维护手册》三、轴承压装3.1 一般要求1.轴承压装应该在指定的区域内完成。
该区域应清洁、明亮,周边不允许安排会产生尘土、铁屑、油污等生产工序。
2.轴承压装使用的设备、工装、计量器具等应保持清洁,且校验时间在有效期内。
3.轴承及附件、轮对及检测器具须同室存放,放置时间应不少于8h;不能同室存放时,存放处温差不应超过5℃。
3.2 轴承压装器械1.轴承压装机应带有安全阀,能短时间内保持规定的压力,确保轴承贴合完毕,并确保从测量仪器读取的压力处于正确的吨位范围、压装到位。
2.轴承压装应采用能打印压装曲线的轴承压装机,压装时应保证压装机活塞中心线与轴颈中心线保持一致。
压装机开始起动压装,直到压力表显示的压力陡然上升,达到规定的贴合力,并保压3-5s。
3.3 轴承压装参数3.4 压装步骤3.4.1 检查轴承状态1.当新轴承从仓库中拿出来时,不需要清洗掉原始的润滑剂保护层。
2.不得拿掉插入轴承孔内的硬纸板,该纸板压装过程中会自动退出。
3.轴承压装前,应对轴承进行外观检查,确认无错、缺零件和其他异常现象,车轴轴端中心孔及螺栓孔内无铁屑和污物。
重点检查密封有无变形、移位等异常。
3.4.2检查车轴在安装轴承之前,应对车轴进行检查,以确保轴承的顺利安装。
1.轴颈、轴肩和圆角处应有加工光滑和磨光的表面,并且无尖角、毛刺、刻痕、划痕和锈蚀。
2.检查轴颈、轴肩以及圆角,以确保车轴的尺寸处于规定的公差内,一边使轴承获得正确的过盈配合。
3.在安装车轴之前,如果车轴以备磁化,则应先消磁。
3.4.3轴承压装1.压装前,记录下轴承外圈的序列号,并核对后档所刻序列号与轴承外圈序列号一致!2.轴承压装前中隔圈不得偏离轴心位置。
铁路货车轮轴新组装作业指导书
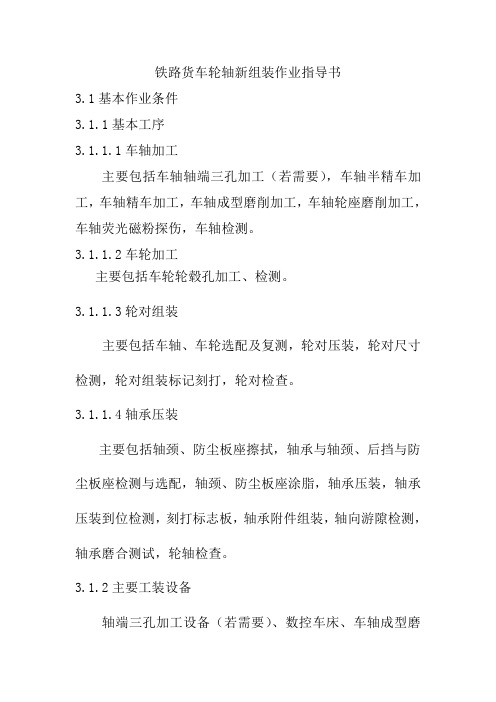
铁路货车轮轴新组装作业指导书3.1基本作业条件3.1.1基本工序3.1.1.1车轴加工主要包括车轴轴端三孔加工(若需要),车轴半精车加工,车轴精车加工,车轴成型磨削加工,车轴轮座磨削加工,车轴荧光磁粉探伤,车轴检测。
3.1.1.2车轮加工主要包括车轮轮毂孔加工、检测。
3.1.1.3轮对组装主要包括车轴、车轮选配及复测,轮对压装,轮对尺寸检测,轮对组装标记刻打,轮对检查。
3.1.1.4轴承压装主要包括轴颈、防尘板座擦拭,轴承与轴颈、后挡与防尘板座检测与选配,轴颈、防尘板座涂脂,轴承压装,轴承压装到位检测,刻打标志板,轴承附件组装,轴向游隙检测,轴承磨合测试,轮轴检查。
3.1.2主要工装设备轴端三孔加工设备(若需要)、数控车床、车轴成型磨床、车轴外圆磨床、车轴荧光磁粉探伤机、数控立式车床或数控立式镗床、轮对自动压装机或轮对自动组装单元(含专用样板轮对)、轴端标记刻打机、微控轴承压装机、标志板刻打机、轴端螺栓智能力矩扳机、轴承磨合机、轮对分解压力机、轴承退卸机。
3.1.3主要检测器具车轴全长及轴肩距测量尺、车轴圆弧检查样板、轴端螺栓孔螺纹塞规、轴端三孔位置度综合量规、深度游标卡尺、粗糙度测量仪、粗糙度比较样块、外径千分尺、内径千分尺(表)、标准样环、车轮踏面形状检查样板、轮径尺(仪)、车轮检查器、轮对内侧距检测尺、轮位差测量尺、车轮滚动圆跳动测量器、轴承轴向游隙检测仪、力矩扳手。
3.2车轴加工3.2.1 半精加工车轴外观技术状态检查3.2.1.1建立《轮轴卡片》(车统-51),核对车轴制造信息。
3.2.1.2车轴外表面无残留氧化黑皮,无可见裂纹,无影响后续加工的锈蚀,轴身部位均匀涂刷醇酸清漆或非苯类清漆。
3.2.1.3车轴不得存在精加工时无法消除的刀痕和损伤。
3.2.1.4车轴中心孔、轴端螺栓孔须进行检查,符合图样要求。
3.2.1.5车轴轴身、轮座与轴身过渡部分的圆弧半径须符合图样要求,表面粗糙度须达到Ra3.2μm。
【2018-2019】轴承装配作业指导书-优秀word范文 (10页)
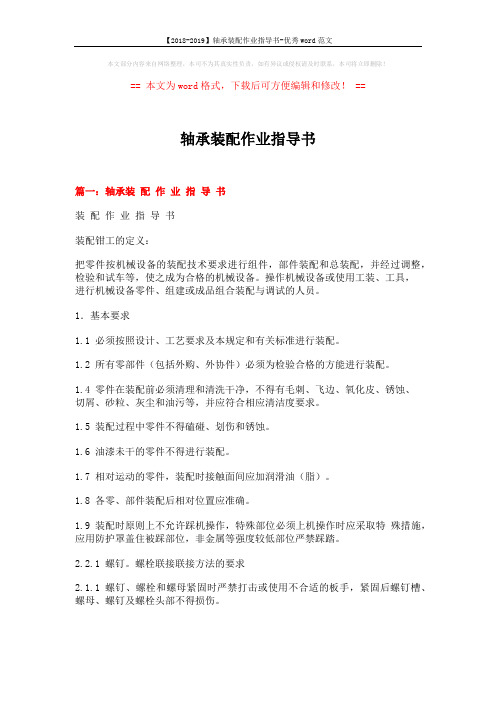
本文部分内容来自网络整理,本司不为其真实性负责,如有异议或侵权请及时联系,本司将立即删除!== 本文为word格式,下载后可方便编辑和修改! ==轴承装配作业指导书篇一:轴承装配作业指导书装配作业指导书装配钳工的定义:把零件按机械设备的装配技术要求进行组件,部件装配和总装配,并经过调整,检验和试车等,使之成为合格的机械设备。
操作机械设备或使用工装、工具,进行机械设备零件、组建或成品组合装配与调试的人员。
1.基本要求1.1 必须按照设计、工艺要求及本规定和有关标准进行装配。
1.2 所有零部件(包括外购、外协件)必须为检验合格的方能进行装配。
1.4 零件在装配前必须清理和清洗干净,不得有毛刺、飞边、氧化皮、锈蚀、切屑、砂粒、灰尘和油污等,并应符合相应清洁度要求。
1.5 装配过程中零件不得磕碰、划伤和锈蚀。
1.6 油漆未干的零件不得进行装配。
1.7 相对运动的零件,装配时接触面间应加润滑油(脂)。
1.8 各零、部件装配后相对位置应准确。
1.9 装配时原则上不允许踩机操作,特殊部位必须上机操作时应采取特殊措施,应用防护罩盖住被踩部位,非金属等强度较低部位严禁踩踏。
2.2.1 螺钉。
螺栓联接联接方法的要求2.1.1 螺钉、螺栓和螺母紧固时严禁打击或使用不合适的板手,紧固后螺钉槽、螺母、螺钉及螺栓头部不得损伤。
2.1.2 有规定拧紧力矩要求的紧固件,应采用力矩扳手按规定拧紧力矩紧固。
未规定拧紧力矩的螺栓,其拧紧力矩可参考附录2的规定。
2.1.3 同一零件用多个螺钉或螺栓紧固时,各螺钉(螺栓)需顺时针、交错、对称逐步拧紧,如有定位销,应从靠近定位销的螺钉或螺栓开始。
2.1.4 用双螺母时,应先装薄螺母后装厚螺母。
2.1.5 螺钉、螺栓和螺母拧紧后,螺钉、螺栓一般应露出螺母1-2个螺距。
2.1.6 螺钉、螺栓和螺母拧紧后,其支承面应与被紧固零件贴合。
2.2 键连接2.2.1 平键与固定键的键槽两侧面应均匀接触,其配合面间不得有间隙。
铁路货车轮轴轴承检修作业指导书

铁路货车轮轴轴承检修作业指导书4.6.1轴承一般检修4.6.1.1 基本作业条件4.6.1.1.1 基本工序清洗及分解,刻写编号,外圈除锈、磁粉探伤及清洗,零件外观检查及手工修磨,尺寸检测,刻写(打)一般检修标记,清洗及组装。
4.6.1.1.2 主要工装设备轴承密封组成分解设备、轴承零部件清洗设备、外圈除锈设备、外圈喷淋设备、外圈磁粉探伤机、轴承零部件退磁机、轴承清洗设备、密封组成或内油封组成或外油封组成压装设备、轴承注脂及匀脂机、标记刻写(打)设备。
4.6.1.1.3 主要检测器具电子秤、轴承游隙测量设备、轴承检测仪、扭矩测量机。
4.6.1.1.4 作业环境(1)轴承一般检修须在独立的生产场所内进行。
(2)轴承零部件检测间、存放间及组装间须封闭,温度和相对湿度应符合附件4的规定。
(3) 24h内轴承检测间、存放间及组装间的落尘量应符合附件4的规定。
(4)轴承检测间的温度、相对湿度应每天检查并记录;落尘量定性检查每周不少于2次,定量检查每月进行1次,且在定性检查合格后的第二天进行。
4.6.1.1.5 工序控制(1)须做到一般检修品、待大修品、报废品及不同型号的检修品相隔离。
(2)建立轴承一般检修工艺流水线,主要包括轴承清洗及分解线、轴承检测及修理线、轴承组装线。
(3)须执行原套原位检修,除密封座和中隔圈外,禁止轴承外圈、内圈及滚子进行互换和拼修。
(4)轴承搬运、清洗及检修过程中零部件不得磕碰伤,保持架不得脱落。
4.6.1.2 技术要求4.6.1.2.1 轴承清洗及分解(1)轴承清洗须采用对轴承零件无腐蚀作用的清洗介质。
(2)内圈组件的清洗温度须不大于80℃,清洗时须防止保持架磕碰伤和离心力对保持架的冲击。
(3)轴承清洗后,零件表面无明显油垢。
(4)轴承零件清洗后须进行防锈处理。
(5)分解后的油封、密封罩、密封组成(不含密封座)须报废。
4.6.1.2.2 编号轴承分解后内圈、外圈须编号,要求准确、清晰;同一套轴承两内圈组件与外圈原滚道须一一对应,不得错位。
轮对总组装综合要求作业指导书
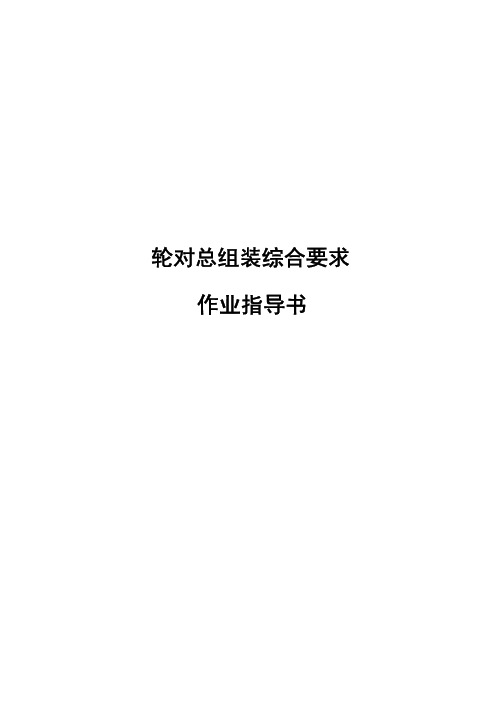
轮对总组装综合要求作业指导书标准化轮对总组装岗位安全风险提示1.工作时必须穿防砸皮鞋,作业过程中工作人员不得站在钢轨上,防止车轮碾伤。
2.测量前要对各种仪表量具进行校验,符合要求方可测量。
类别:段修(A2修)系统:走行装置部件:轮对及轴箱轮对总组装综合要求作业指导书适用车型:22B、25B、25G、25K、25T作业人员:轮对组装工2名作业时间:作业材料:工装工具: 1. 空调机;2. 干湿度计;3. 测试板;4. 轴承运输小车。
参考资料:《铁路客车轮对和滚动轴承轴箱组装及检修规则》铁运〔2013〕191号安全防护及注意事项:注意——严把组装环境要求关。
基本技术要求:1 注意——轴承组装前清洁度标准符合《轴承组装前清洁度标准》[表1]要求。
2 注意——轴箱及其附件组装前清洁度标准符合《轴箱及其附件组装前清洁度标准》[表2]要求。
3 注意——室内温度16~30℃,室内相对湿度≤60%。
作业环境与作业位置:轮对组装间质检组必查抽检项目:必查:无抽查:无第 1 页 共 4 页轮对总组装综合要求作业指导书序号 作业项目工具及材料作业程序及标准作业图示1 温度要求空调机 温度计每日对轴承检测间的温度进行1次检测并填写环境检测记录。
[图1]工作间内的温度:室内温度16~30℃,测量时将摄氏温度计置于室内无日晒、热源和风流动处。
检测间与轮对总组装间温差不超过5℃。
图1 温度测量仪2湿度要求干湿度计 去湿机每日对轴承检测间的相对湿度进行1次检测并填写环境检测记录。
[图2] 组装间内的湿度:室内相对湿度≤60%,测量时将湿度计置于室内无日晒、热源和风流动处。
图2 湿度计序号作业项目工具及材料作业程序及标准作业图示3 环境清洁度要求白布测试板3.1定性检查空气清洁度。
每周对轮对组装间空气清洁度定性检查不少于2次。
目视要求:轴承检测、组装、存放工作间内的空气中不得有明显飘尘,在专用测试板上不得有明显落灰层。
白布检查:以洁净的棉白细布擦拭时,不得有明显污迹。
铁路货车轮轴新组装车轮加工车轴车轮选配作业指导书
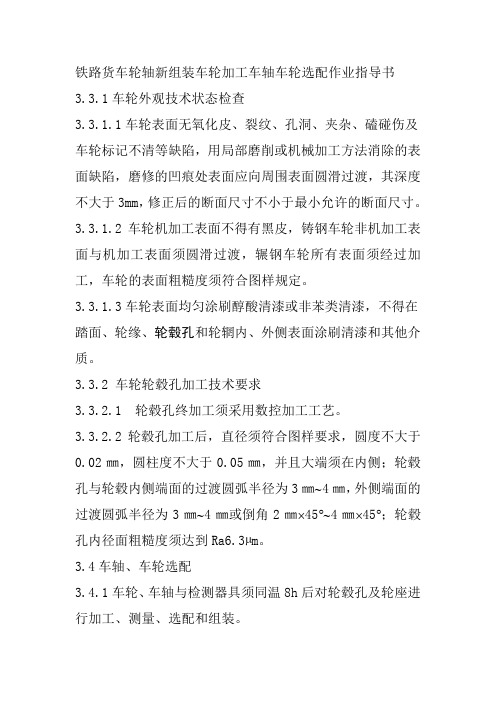
铁路货车轮轴新组装车轮加工车轴车轮选配作业指导书3.3.1车轮外观技术状态检查3.3.1.1车轮表面无氧化皮、裂纹、孔洞、夹杂、磕碰伤及车轮标记不清等缺陷,用局部磨削或机械加工方法消除的表面缺陷,磨修的凹痕处表面应向周围表面圆滑过渡,其深度不大于3mm,修正后的断面尺寸不小于最小允许的断面尺寸。
3.3.1.2车轮机加工表面不得有黑皮,铸钢车轮非机加工表面与机加工表面须圆滑过渡,辗钢车轮所有表面须经过加工,车轮的表面粗糙度须符合图样规定。
3.3.1.3车轮表面均匀涂刷醇酸清漆或非苯类清漆,不得在踏面、轮缘、轮毂孔和轮辋内、外侧表面涂刷清漆和其他介质。
3.3.2 车轮轮毂孔加工技术要求3.3.2.1 轮毂孔终加工须采用数控加工工艺。
3.3.2.2轮毂孔加工后,直径须符合图样要求,圆度不大于0.02㎜,圆柱度不大于0.05㎜,并且大端须在内侧;轮毂孔与轮毂内侧端面的过渡圆弧半径为3㎜~4㎜,外侧端面的过渡圆弧半径为3㎜~4㎜或倒角2㎜⨯45︒~4㎜⨯45︒;轮毂孔内径面粗糙度须达到Ra6.3µm。
3.4车轴、车轮选配3.4.1车轮、车轴与检测器具须同温8h后对轮毂孔及轮座进行加工、测量、选配和组装。
3.4.2同一车轴上须组装同型号、同材质的车轮,轮对型号以车轴型号为准。
3.4.3同一车轴上组装的两个车轮轮辋宽度差不大于3㎜。
3.4.4同一车轮相互垂直的直径差不大于0.5mm;同一车轴上的两车轮直径差不大于1mm。
3.4.5轮座与轮毂孔采取过盈配合,配合过盈量为轮座直径的0.8‰~1.5‰。
3.4.6轮座与轮毂孔选配后对二者关键尺寸进行逐项复查、确认。
3.4.7选配、复测前须将车轴轮座、车轮轮毂孔擦拭干净,按规定位置测量轮座与轮毂孔直径、圆度及圆柱度。
3.4.7.1轮座直径按图3-1所示位置分别测量Ⅰ、Ⅱ两截面,每个截面测量两点,测量位置均须相差90°,两点算术平均值为每个截面轮座直径,Ⅰ、Ⅱ两截面轮座直径的算术平均值为轮座直径,任一截面两点轮座直径之差的1/2为轮座圆度,Ⅰ、Ⅱ截面轮座直径之差的1/2为轮座圆柱度,轮座直径不允许在全长范围内向轮座引入部端逐渐增大。
【精品文档】轴承装配作业指导书-word范文 (10页)

本文部分内容来自网络整理,本司不为其真实性负责,如有异议或侵权请及时联系,本司将立即删除!== 本文为word格式,下载后可方便编辑和修改! ==轴承装配作业指导书篇一:轴承装配作业指导书装配作业指导书装配钳工的定义:把零件按机械设备的装配技术要求进行组件,部件装配和总装配,并经过调整,检验和试车等,使之成为合格的机械设备。
操作机械设备或使用工装、工具,进行机械设备零件、组建或成品组合装配与调试的人员。
1.基本要求1.1 必须按照设计、工艺要求及本规定和有关标准进行装配。
1.2 所有零部件(包括外购、外协件)必须为检验合格的方能进行装配。
1.4 零件在装配前必须清理和清洗干净,不得有毛刺、飞边、氧化皮、锈蚀、切屑、砂粒、灰尘和油污等,并应符合相应清洁度要求。
1.5 装配过程中零件不得磕碰、划伤和锈蚀。
1.6 油漆未干的零件不得进行装配。
1.7 相对运动的零件,装配时接触面间应加润滑油(脂)。
1.8 各零、部件装配后相对位置应准确。
1.9 装配时原则上不允许踩机操作,特殊部位必须上机操作时应采取特殊措施,应用防护罩盖住被踩部位,非金属等强度较低部位严禁踩踏。
2.2.1 螺钉。
螺栓联接联接方法的要求2.1.1 螺钉、螺栓和螺母紧固时严禁打击或使用不合适的板手,紧固后螺钉槽、螺母、螺钉及螺栓头部不得损伤。
2.1.2 有规定拧紧力矩要求的紧固件,应采用力矩扳手按规定拧紧力矩紧固。
未规定拧紧力矩的螺栓,其拧紧力矩可参考附录2的规定。
2.1.3 同一零件用多个螺钉或螺栓紧固时,各螺钉(螺栓)需顺时针、交错、对称逐步拧紧,如有定位销,应从靠近定位销的螺钉或螺栓开始。
2.1.4 用双螺母时,应先装薄螺母后装厚螺母。
2.1.5 螺钉、螺栓和螺母拧紧后,螺钉、螺栓一般应露出螺母1-2个螺距。
2.1.6 螺钉、螺栓和螺母拧紧后,其支承面应与被紧固零件贴合。
2.2 键连接2.2.1 平键与固定键的键槽两侧面应均匀接触,其配合面间不得有间隙。
轴承安装、拆卸技术手册及作业指导书
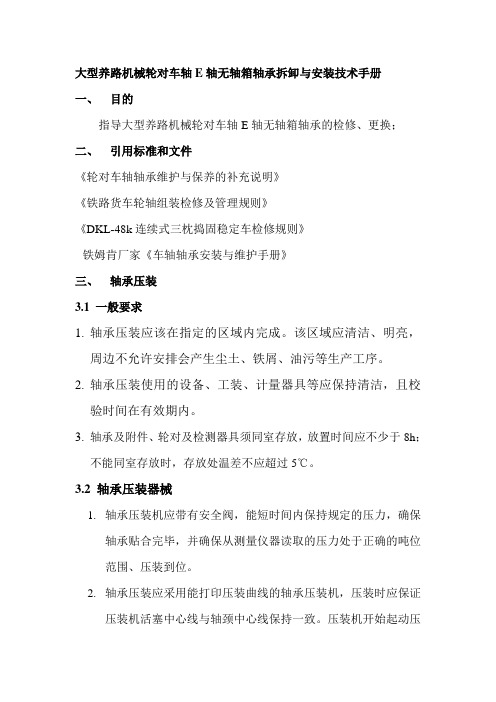
大型养路机械轮对车轴E轴无轴箱轴承拆卸与安装技术手册一、目的指导大型养路机械轮对车轴E轴无轴箱轴承的检修、更换;二、引用标准和文件《轮对车轴轴承维护与保养的补充说明》《铁路货车轮轴组装检修及管理规则》《DKL-48k连续式三枕捣固稳定车检修规则》铁姆肯厂家《车轴轴承安装与维护手册》三、轴承压装3.1 一般要求1.轴承压装应该在指定的区域内完成。
该区域应清洁、明亮,周边不允许安排会产生尘土、铁屑、油污等生产工序。
2.轴承压装使用的设备、工装、计量器具等应保持清洁,且校验时间在有效期内。
3.轴承及附件、轮对及检测器具须同室存放,放置时间应不少于8h;不能同室存放时,存放处温差不应超过5℃。
3.2 轴承压装器械1.轴承压装机应带有安全阀,能短时间内保持规定的压力,确保轴承贴合完毕,并确保从测量仪器读取的压力处于正确的吨位范围、压装到位。
2.轴承压装应采用能打印压装曲线的轴承压装机,压装时应保证压装机活塞中心线与轴颈中心线保持一致。
压装机开始起动压装,直到压力表显示的压力陡然上升,达到规定的贴合力,并保压3-5s。
3.3 轴承压装参数3.4 压装步骤3.4.1 检查轴承状态1.当新轴承从仓库中拿出来时,不需要清洗掉原始的润滑剂保护层。
2.不得拿掉插入轴承孔内的硬纸板,该纸板压装过程中会自动退出。
3.轴承压装前,应对轴承进行外观检查,确认无错、缺零件和其他异常现象,车轴轴端中心孔及螺栓孔内无铁屑和污物。
重点检查密封有无变形、移位等异常。
3.4.2检查车轴在安装轴承之前,应对车轴进行检查,以确保轴承的顺利安装。
1.轴颈、轴肩和圆角处应有加工光滑和磨光的表面,并且无尖角、毛刺、刻痕、划痕和锈蚀。
2.检查轴颈、轴肩以及圆角,以确保车轴的尺寸处于规定的公差内,一边使轴承获得正确的过盈配合。
3.在安装车轴之前,如果车轴以备磁化,则应先消磁。
3.4.3轴承压装1.压装前,记录下轴承外圈的序列号,并核对后档所刻序列号与轴承外圈序列号一致!2.轴承压装前中隔圈不得偏离轴心位置。
LZ22轴承压装作业指导书

作业指导书轴承压装目 次一、作业介绍 (3)二、作业流程示意图 (4)三、作业程序、标准及示范 (5)1.班前准备 (5)2.开工准备 (5)3.工序控制 (5)4.轴承压装 (5)5.设备故障处置 (7)6.质量反馈处置 (7)7.完工要求 (7)五、附件 (9)1.限度表 (9)2.轴承压装机日常性能校验记录 (9)一、作业介绍作业地点:车辆段检修车间轮轴轴承压装间。
适用范围:适用于铁路货车RD2、RE2A、RE2B轮轴三级修的轴承压装作业。
上道工序:轴颈防尘板座涂脂。
下道工序:轴承压装后检查。
人员及工种要求:本岗位作业须由轮轴钳工完成,作业人员上岗前要进行岗前培训,并持有《岗位培训合格证》,上岗人员须持证上岗。
作业要点:劳动防护用品穿戴整齐;开工前全面检查工具、材料状态确认性能良好无故障;检查测量具计量检定不过期;左右两端轴承压装作业人员合作共同完成轴承的压装作业;压装过程左端作业人员将轴号信息告知右端作业人员;完工进行整理,清扫场地。
二、作业流程示意图三、作业程序、标准及示范1.班前准备按规定穿戴好劳动保护用品,参加班前点名会。
2.开工准备2.1按《工装设备、检测器具、工具及材料》清单检查工装工具、样板量具及材料状态,须齐全、良好;对自动检测试验类设备按规定进行日常或季度性能校验。
发生异常情况时通知工长处理。
2.2检查压装工作间环境质量。
轴承压装间的温度必须不低于10℃。
检测和选配前,轴承及附件、轮对及检测器具须同室存放,放置时间应不少于8小时;不能同室存放时,存放处温差不应超过5K。
3.工序控制轴承压装前,检查轴颈、防尘板座油脂涂抹情况,油脂涂抹须均匀、不漏涂。
发现油脂涂抹不均匀或漏涂时,通知上道工序处理。
4.轴承压装4.1检查轮对、轴承及后档4.1.1检查轴承及附件外观质量,确认无错、缺零件和其他异常现象。
4.1.2轴承外圈、密封装置、后挡不得有缺损、变形或磕碰伤。
4.1.3 353130B轴承塑钢隔圈使用新品,应完好,无断裂等缺陷。
- 1、下载文档前请自行甄别文档内容的完整性,平台不提供额外的编辑、内容补充、找答案等附加服务。
- 2、"仅部分预览"的文档,不可在线预览部分如存在完整性等问题,可反馈申请退款(可完整预览的文档不适用该条件!)。
- 3、如文档侵犯您的权益,请联系客服反馈,我们会尽快为您处理(人工客服工作时间:9:00-18:30)。
铁路货车轮轴新组装轮对组装轴承压装作业指导书
3.5.1车轮与车轴组装须采用微机控制压装,配备专用样板轮对,自动记录压装压力曲线。
3.5.2轮对自动压装设备须有左、右标识,车轴左、右端与压装机左、右端须对应。
3.5.3每班开工前由压装设备操作者、工长、质检员、验收员共同对轮对自动压装设备的主要性能指标进行日常性能校验,填写校验记录并签字,合格后方可开工。
每班首条轮对压装时须观察压力表,将系统压力与压力曲线的压力值对比确认一致,不一致时以压力曲线的压力值为准,允许压力曲线数值小于压力表数值,但相差不大于49kN。
3.5.4轮对组装前须录入车轴、车轮的相关信息,轮座表面及轮毂孔内径面须洁净,均匀涂抹纯植物油(禁止采用桐油)或矿物脂(MOLYKOTE G-N PLUS PASTE、MOLYKOTE DX等)。
3.5.5轮对组装时,须采取保护措施,防止轴颈磕碰伤及轴颈端部蹾粗。
3.5.6压装车轮时,车轴纵向中心线与压装机活塞中心线须保持一致,车轴纵向中心线与车轮轮辋内侧平面相垂直,车轮压入速度应均匀并保持一致。
3.5.7轮对压装最终压力按轮毂孔直径计算,每100mm直径尺寸的压装压力: LZ50钢、LZ45CrV钢车轴为343kN~588kN。
3.5.8轮对组装后突悬部分不计入压装压力曲线,压力曲线
须符合附件3规定。
3.5.9压力曲线等不合格时,应及时分解轮对。
分解时,车轴的中心线与压力机活塞的中心线应保持一致,并采取保护措施,防止轴颈蹾粗和磕碰伤,车轮压退时的最大压应力不超过车轴材质的下屈服强度。
3.5.10不得将分解的原车轮与原车轴原位进行第二次压装,在原车轴、车轮表面无损伤的情况下,可重新选配其他新加工过的合格车轮、车轴进行压装。
分解后有拉伤的车轮、车轴须重新加工,清除缺陷后方可使用。
若车轴经重新加工后须对再加工部位进行复合磁化荧光磁粉探伤检查。
3.5.11轮对压装压力曲线图表(车统-57)须与轮轴卡片(车统-51)装订在一起一并传递、保存,且车统-51、车统-57与轮对实物相符;同一条轮对的不合格压装压力曲线和合格曲线记录一并保存。
3.5.12轮对组装合格后须刻打轮对组装标记,标记刻打符合轮轴及零部件标记第5.1.4条规定。
3.5.13轮对组装后检测要求
3.5.13.1轮对轮位差不大于3㎜。
3.5.13.2轮对内侧距离1353±2㎜,其任意三处差不大于l ㎜。
3.5.13.3轮对内侧距离不符合规定尺寸时不得压调。
3.5.13.4同一车轮相互垂直的直径差不大于0.5mm;同一轮
对的两车轮直径差不大于1mm,同一轮对的两车轮滚动圆相对于轴中心线的径向跳动不大于0.6mm。
3.6轴承压装
3.6.1 轴承压装须在清洁的工作间内进行。
压装间的温度应不低于10℃。
检测和选配前,轴承及附件、轮对及检测器具须同室存放,放置时间应不少于8h;不能同室存放时,存放处温差不应超过5K。
3.6.2 每班开工前由轴承压装机操作者、工长、质检员、验收员共同对轴承压装机的主要性能指标进行日常性能校验,填写日常性能校验记录并签字,合格后方可开工。
每班首条压装时须观察压装机压力表,将系统压力与压力曲线贴合压力对比确认应一致,如不一致时,系统压力与计算机显示值相差不超过10kN。
3.6.3 同一轮对上须压装同型号、同厂家的轴承。
3.6.4 轴承压装前,须对轮对实物进行检查核对,确认车轴制造单位代号、车轴制造顺序号、车轴制造时间等信息,保证与轮轴卡片一致。
3.6.5 轴承压装前,须进行外观质量检查,确认无错、缺零件和其他异常现象,车轴轴端中心孔及螺栓孔内无铁屑和污物。
3.6.6 轴承压装前,须将轴颈、防尘板座擦拭干净,按图3-2所示和表 3-1位置测量轴颈直径、圆柱度和防尘板座直径。
3.6.6.1车轴轴颈直径须测量Ⅰ、Ⅱ两个截面,每个截面测量两点,测量位置均须相差90°,两点算术平均值为每个截面车轴轴颈直径,Ⅰ、Ⅱ两截面轴颈直径的算术平均值为车轴轴颈直径,Ⅰ、Ⅱ截面轴颈直径之差的1/2为轴颈圆柱度,轴颈直径不允许在全长范围内向轴颈端部方向逐渐增大。
3.6.6.2防尘板座直径测量Ⅲ截面,测量两点,测量位置须相差90°,两点算术平均值为防尘板座直径。
图 3-2 轴颈、防尘板座直径测量位置示意图表3-1 测量位置距轴端距离范围表
单位:mm
轴型 A B C
RF225~30 140~160 5~10
RE2B25~30 140~160 5~10
RD2 25~30 130~150 5~10
3.6.7 轴承压装前,须对轴承制造单位提供记录中的轴承内圈内径尺寸进行复查、确认,根据车轴轴颈尺寸选配轴承,配合过盈量须符合规定。
3.6.8 轴承压装前须根据车轴防尘板座尺寸选配后挡,配合过盈量须符合规定。
3.6.9 轴承压装前须用乙醇或汽油擦拭车轴轴颈、轴颈根部、轴颈后肩、防尘板座;先在轴颈根部、轴颈后肩、防尘板座配合面上均匀涂刷厚度约为0.5mm的PR-1型车轴轴颈卸荷槽专用防锈脂,再在轴颈上均匀涂刷厚度约为0.5mm的Ⅱ号防锈极压锂基脂。
3.6.10 353130B型轴承塑钢隔圈组装
3.6.10.1 轴承压装前,先将塑钢隔圈与后挡组装,再将其与轴承内圈组装。
3.6.10.2 轴承压装时,应保证塑钢隔圈、后挡及轴承内圈不分离,避免损坏塑钢隔圈;分离时须检查,符合要求方可重新组装和压装。
3.6.10.3 压装到位的轴承如退卸,塑钢隔圈须报废。
3.6.11 353132A(352132A)型轴承防护隔圈组装
3.6.11.1 轴承压装前,应先将后挡与防护隔圈组装在一起。
3.6.11.2 轴承压装时,先将组装在一起的后挡和防护隔圈放在车轴轴颈上,轴承压装过程中将组装在一起的后挡和防护隔圈组装在轴承内侧内圈上。
3.6.11.3 压装到位的轴承如退卸,防护隔圈无裂损或无变形的可重复使用。
3.6.12 353132B(353132X2-2RS)型轴承塑钢连接圈组装
3.6.12.1 轴承压装前,塑钢连接圈应按方向,先与后挡配合面组装在一起,再将其与轴承内侧内圈组装在一起。
3.6.12.2 轴承压装时,应保证塑钢连接圈、后挡及轴承内圈不分离。
3.6.12.3 压装到位的轴承如退卸,塑钢连接圈无裂损或无变形的可重复使用。
3.6.13 轴承压装须采用能打印压装曲线的固定式微控轴承压装机,压装时应保证轮对轴向定位且压装机活塞中心线与轴颈中心线保持一致。
3.6.14 轴承压装前中隔圈不得偏离轴心位置。
3.6.15 轴承压装过程中应旋转轴承外圈,保持其旋转灵活;卡滞时须停止压装,退卸检查。
轴承的压装力及终止贴合压力须符合规定,并保压3s 及以上。
3.6.16 轴承压装后须进行轴承压装到位检查。
见表3-2。
表3-2 轴承压装后外侧内圈(密封座)端面到车轴端面距离
推荐值表 轴承型号 范围备注
353132A (352132A )、353132B 4.9~负值表示密封座端面
在车轴端面以外 353130B 8.4~352226X2-2RZ 、SKF 197726-14.4
3.6.17 轴承压装后须左右旋转3圈~5圈,转动须灵活,不得有卡阻。
3.6.18 轴承压装后,须在294N ~490N 轴向推(拉)力下检
测轴承的轴向游隙,轴向游隙须符合规定。
3.6.19 轴承压装后,轴端须组装轴承前盖、标志板、防松片、轴端螺栓,并对轴端螺栓用施封锁施封。
3.6.20 轴端螺栓紧固后防松片的所有止耳须撬起,每组两个止耳中至少有一个须贴靠在轴端螺栓的六方平面上,防松片只可使用一次。
3.6.21 标志板须使用0.5mm~1mm的软性不锈钢板按要求制作,组装前须按规定刻打标记,标记刻打须准确、清晰。
3.6.22 施封锁上须有装用单位和施封锁制造单位代号、“D”(或“E”、“F”)代号标记,施封锁锁闭后手拉不得开锁。
3.6.23 轴端螺栓须为35钢制品,螺栓头部带有锻造的35钢标记、制造年标记、制造单位代号标记。
3.6.24 螺栓组装前须进行外观检查,螺栓不得有锈蚀、毛刺、滑扣、弯曲、拉长、裂纹等。
3.6.25 螺栓组装时须在螺纹部位涂少量润滑脂,宜用智能力矩扳机均匀紧固,拧紧力矩须符合规定。
3.6.26 轴端螺栓用智能力矩扳机紧固后每班首、末件须用力矩扳手进行最小扭力矩复验。
3.6.27 轴承压装后,进行转速不低于200r/min,时间不少于5min的磨合测试。
轴承转动时不应有异音,应使用测温仪测试轴承温升,宜使用专用诊断测试仪器测试轴承状态,并。