液压缸装配出厂试验规范
液压油缸出厂检验报告

实验、泄漏实验、行程检测、外观检测等出厂实验,实验结果符合要求,质量合格,准予出厂。
备注:“√”为符合产品指标值。
测量时油液温度: 45℃
检验员:
审核:
批准:
1430 21 M22*1.5 螺纹连接
出厂编号
GD20120151-GD20120153
出厂时间
2012.3.20
实验测量值
序号 实验项目
产品指标值
被试产品编号
1
2
3
2012.3.28 检01 3
结果 报告
备注
1 试运行 全行程往复运动数次,完全排除缸内空气。 √
√
√
√
2
起动压力 特性实验
压力逐渐升高,记录下最低起动压力。
2
2
2√Leabharlann 3耐压实验1.5倍的工作压力,保压2min,无渗漏、 变形、松动。
无
无
无
√
低压0.5Mpa(缸径>32mm)或1Mpa (缸径≤32mm)往复3次,停留10s,
各部分无渗漏。(低压泄漏)
无
无
无
√
4 泄漏实验
加压到工作压力,经活塞至未加压腔无 泄漏。(内泄漏)
无
无
无
√
起动、耐压、泄漏实验时,活塞杆密封
********厂
液压油缸出厂检验报告
报告编号:2012032
产品名称
前门油缸 型号规格 GGK1-90/50*1430
检验日期
订货单位
检验员编号
检验根据
GB/T 15622-2005《液压缸实验方法》
检验数量
缸径(mm)
90
杆径(mm)
50
液压缸验收试验规程
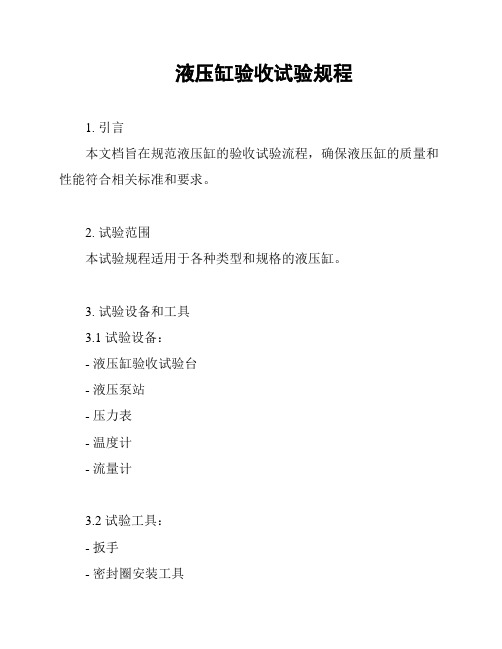
液压缸验收试验规程1. 引言本文档旨在规范液压缸的验收试验流程,确保液压缸的质量和性能符合相关标准和要求。
2. 试验范围本试验规程适用于各种类型和规格的液压缸。
3. 试验设备和工具3.1 试验设备:- 液压缸验收试验台- 液压泵站- 压力表- 温度计- 流量计3.2 试验工具:- 扳手- 密封圈安装工具- 液压油4. 试验内容4.1 外观检查- 检查液压缸的表面是否有明显的划痕、变形或油渍等。
- 检查液压缸的连接接头是否完好无损。
4.2 尺寸和封装检查- 检查液压缸的尺寸是否符合设计要求。
- 检查密封圈的封装是否正确,无泄漏。
4.3 工作性能测试- 连接液压缸至试验台,进行负荷承载能力测试。
- 测试液压缸的工作性能,包括行程、速度、压力等。
5. 试验要求5.1 外观检查合格标准:- 无明显的划痕、变形或油渍等。
- 连接接头完好无损。
5.2 尺寸和封装检查合格标准:- 尺寸符合设计要求。
- 密封圈封装正确,无泄漏。
5.3 工作性能测试合格标准:- 负荷承载能力测试通过。
- 工作性能符合设计要求。
6. 试验记录和报告6.1 试验记录:- 对每项试验内容进行记录,包括试验时间、试验结果等。
6.2 试验报告:- 根据试验记录编制试验报告,详细描述试验过程和结果。
7. 安全注意事项7.1 操作人员必须熟悉试验设备的使用方法和安全操作规程。
7.2 在试验过程中,需特别注意保护个人安全,避免液压压力过高造成危险。
7.3 如果试验过程中发现异常情况,应立即停止试验,并进行必要的维修和调整。
以上为液压缸验收试验规程的简要介绍,旨在为试验人员提供操作指南和质量标准。
具体的试验细节和要求应根据实际情况和相关标准进行补充和确认。
液压缸检验规范

1双作用液压缸检验标准
1.1出厂检验项目、内容、方法和要求
1.1.1全检项目(每一台产品上进行的检验)
序号
检验项目
试验方法
检验要求
1
空载运转
被试缸在无载工况下,全行程上进行5次试运转。活塞运源自平稳2最低启动压力
在空载运行时,从无杆腔逐渐施加压力,测其活塞的最低启动压力。
V
其他
Pn≤10MPa
Pn>10 MPa
Pn≤10 MPa
Pn>10 MPa
0.75MPa
0.09Pn
0.5MPa
0.06Pn
0.45MPa
0.06Pn
0.3MPa
0.04Pn
3
耐压试验
在被测缸无杆腔和有杆腔分别施加公称压力Pn的1.5倍(当Pn﹥16MPa时,应为1.25倍)将活塞分别停留在行程的两端,保持2min进行试验
不允许有外部渗油、爬升等不正常现象
2
耐压试验
在被测柱塞缸的柱塞处全部伸出位置,调节溢流阀使缸内的压力为额定压力的1.5倍,保压2min进行试验
1.不得有外部渗漏
2.全部零件均不得有永久变形
3
外部渗漏
全行程运行换向20次,然后测量柱塞杆处的渗漏量
≤0.025mL
2.1.2抽检项目(液压油缸的抽检数量为每批产品的2%,但不得少于2台,若抽检中有不合格项目,则对此项目应加倍复试,如仍不合格,则对该批产品全检)
序号
检验项目
试验方法
检验要求
1
最低启动压力
在无负荷情况下,调节溢流阀逐渐升压至柱塞开始运动时,测量柱塞缸内的压力,即为最低启动压力
≤0.56MPa
2
液压缸出厂实验项目及方法

最低启动压力 不得超过规定值
必检
3
耐压试验
将被试液压缸活塞分别停在缸两端 (但作用液压缸处于行程极限位置),分 别向工作腔输入工称压力1.5倍的油液, 保压2min以上来自不得有外渗漏 及永久变形等现象
必检
4
泄漏试验
①内泄漏:将被测液压缸工作腔输入公 称压力的油液,测定径活塞泄至未加压腔 的泄漏量 ②外泄漏:在进行启动压力特性试验、 耐压试验、耐久试验、内泄漏试验时,测 量活塞杆密封处的泄漏量,各结合面处不 得有渗漏现象
必检
韶关液压唐山分公司
液压缸出厂实验项目及方法
序号 试验项目 实验方法 要 求 必要性
1
试运转
调整系统压力,使被试液压缸能在 无负载工况下启动,并全程往复运动 数次,排尽缸内的空气
不得有外渗漏 等不正常现象
必检
2
启动压力 特性试验
试运转后,在被测液压缸空载工况下, 调节溢流阀,使无杆腔压力逐步升高 (双活塞杆液压缸,两腔均可),至液 压缸启动时,记录下压力表测量的被测 液压缸工作腔的活塞在启动时压力值即 为最低启动压力
漏油量或单位时间内沉 降量,应符合设计要求
必检
5
耐久试验
在额定压力下,将被试液压缸以设计 要求最高速度连续运行,速度误差± 10%,一次连续运行8h以上,在试验期 间,被试液压缸的零件均不得进行调整, 记录累计行程
正常运转
抽检
6
行程试验
将被试液压缸活塞或柱塞停在两端极 限位置,测量其行程长度
符合设计要求
液压缸装配作业规程

液压缸装配作业规程1、装配前检查。
检查清点所有的零部件是否齐全。
检查所有零部件是否符合图纸要求及检验是否合格等其他相关要求。
目测密封槽各棱角、槽底是否符合要求。
测量各尺寸是否符合要求。
2、装配前准备。
各零部件去毛刺、清洗,并无任何杂质附在零部件表面。
密封件装配倒角、密封槽等处应圆滑。
对要求有防松螺钉或开口销防松的,按图纸要求配钻螺纹孔或开口销孔。
配钻后应严格去尖角、毛刺、铁屑。
支承导向环的切口角度应控制在与轴向成25°左右,切口间隙应控制在2mm以内,切后去飞边、毛刺。
活塞杆放在适当的工装上不得损坏表面。
目测表面有无磕碰、划伤等表面缺陷。
螺纹及倒角处毛刺、铁屑等应清除干净。
3、冲洗、清洗。
各零件(密封件除外)放入干净煤油内清洗干净,使清洁度达到要求。
较长、直径较大的缸筒在冲洗台架上对缸筒内壁进行循环喷洗。
4、装配。
转运到装配作业区域(必须在装配作业区进行装配,以确保装配时,外界环境不造成污染,),再进行装配前的冲洗。
液压缸各零件清洗完后,用干净压缩空气将各零件吹干,无残留煤油,方可进行装配。
●各零件用干净破布(禁止用带丝状物如棉纱等)垫于装配平台,以防颗粒杂质污染液压缸内部各零件。
●领取的密封件禁止浸泡在煤油内,以免加速密封件老化、硬化、膨胀变形,缩短密封件使用寿命。
●保护性装配密封件,禁止用带尖锐刃口的工具撬密封件,损坏密封件。
对于缸筒上油口、卡键槽,以及斯特封形式密封等,在装配密封时要用相应的工装进行装配。
●在装配时要在密封部位涂抹少量液压油。
5、外观保护。
●外露油口用橡胶塞或堵板堵住,以免杂质掉入油缸内。
●外露活塞杆螺纹用橡胶套帽套入,以免碰伤螺纹。
6、检测试验。
进行出厂试验,试验方法应符合GB/T15622-2005,试验指标应符合JB/T10205-2000。
试验合格后,所有联接螺栓(钉),必须重新紧一篇。
●最后,要在液压缸适当位置打上标牌,打印相应参数(工作压力、缸径、活塞杆径、行程,装配日期等)。
液压件入厂检验规范

液压件入厂检验规范
一、液压油:
1.产地、牌号必须与图纸要求一致;
2.必须有产品合格证;
3.油桶摆放按照规定执行;
4.厂内复检项目(抽检):
油的比重(目的:检验含水量;检验设备:比重计);油的粘度:按牌号及国标检验;油的颗粒度(目的:检查油中的杂质;检验设备:颗粒测试仪);
二、油缸:
1.产地、型号必须与图纸要求一致;
2.必须有产品合格证;
3.厂内复检项目:
油缸的安装距及安装孔径;
油缸的行程;
油缸的接口螺纹;
油缸的外观质量;
打压试验;
三、液压泵、液压马达:
1.产地、型号必须与图纸要求一致;
2.必须有产品合格证;。
液压缸各项检验
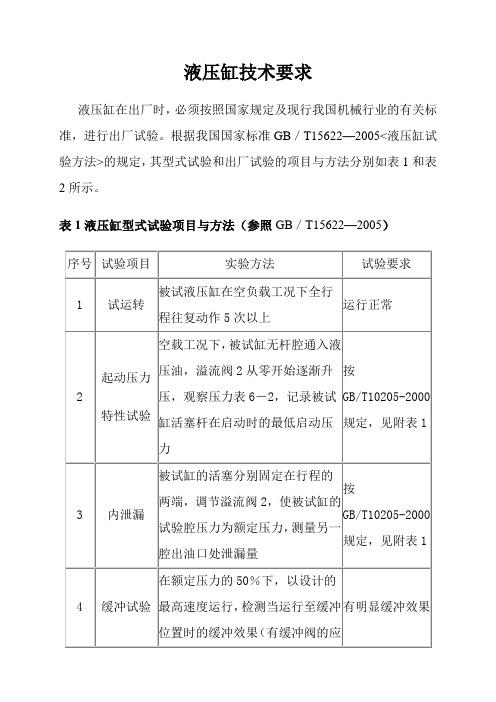
同表1缓冲试验方法
同表1
5
耐压试验
必测
同表1耐压试验方法
同表1
6
外渗漏
必测
同表1外渗漏试验方法
同表1
7
全行程检查
必测
同表1全行程检查试验
同表1
按GB/T10205-2000规定,见附表1
4
缓冲试验
在额定压力的50%下,以设计的最高速度运行,检测当运行至缓冲位置时的缓冲效果(有缓冲阀的应调节缓冲阀)
有明显缓冲效果
5
负载效率
将测力计装在被试缸的活塞杆上。调节溢流阀2,使进入被试缸的液压油的压力逐渐升高,测出不同压力下的负载效率
按GB/T10205-2000规定,见附表1
按设计要求
8Hale Waihona Puke 外泄漏在整个试验过程中,检测活塞杆密封处的泄漏量;检查缸体各静密封处、结合面处和可调节机构处是否有渗漏现象
按GB/T10205-2000规定,见附表1
9
高温试验
被试缸在额定压力下,通入90℃的油液,连续运转一小时以上
正常工作无异常
10
耐久性试验
在额定压力下,使被试液压缸以设计要求的最高速度连续运行,速度误差为士10%。一次连续运行8h以上。在试验期间,被试液压缸的零件均不得进行调整。记录累计行程。
1
试运转
被试液压缸在空负载工况下全行程往复动作5次以上
运行正常
2
起动压力
特性试验
空载工况下,被试缸无杆腔通入液压油,溢流阀2从零开始逐渐升压,观察压力表6-2,记录被试缸活塞杆在启动时的最低启动压力
按GB/T10205-2000规定,见附表1
3
内泄漏
被试缸的活塞分别固定在行程的两端,调节溢流阀2,使被试缸的试验腔压力为额定压力,测量另一腔出油口处泄漏量
液压油缸质量检验规范

液压油缸质量检验规范
前言
本规范用于液压油缸的质量检验,旨在保证液压油缸的质量,提高产品的可靠性和安全性。
检验标准
1. 外观检验
液压油缸的外观应该无裂纹、无变形、无划痕、表面无锈蚀,在装配后应该无泄漏。
2. 尺寸检验
液压油缸的内径、外径、活塞杆直径、活塞杆长度应该符合设计要求。
3. 强度检验
液压油缸在压力测试时,应该承受规定压力2倍的测试压力,无破裂、变形和泄漏等现象。
4. 密封性检验
液压油缸在压力测试时,应该保持规定压力10分钟,没有任何泄漏现象,且在经过密封性试验后活塞杆不会出现损坏。
检验方法
1. 外观检验
使用肉眼或放大镜仔细检查液压油缸表面,如果发现异常,应该进行更加细致的检查。
2. 尺寸检验
使用专业的检测设备,比如游标卡尺、外径千分尺、内景千分尺等,测量液压油缸的相关尺寸。
3. 强度检验
沿对称轴向液压油缸施加试验压力,在压力测试过程中观察液压油缸的变形情况和是否有漏油现象。
4. 密封性检验
涂抹液压油缸需要检验的密封部位,将液压油缸放入水中进行压力测试,观察是否有气泡冒出,检查活塞杆样子并观察密封性。
结论
液压油缸的检验可以保障其质量,减少使用过程中出现的故障,确保液压油缸能够在高压下稳定运行,提高设备的工作效率和安全性。
- 1、下载文档前请自行甄别文档内容的完整性,平台不提供额外的编辑、内容补充、找答案等附加服务。
- 2、"仅部分预览"的文档,不可在线预览部分如存在完整性等问题,可反馈申请退款(可完整预览的文档不适用该条件!)。
- 3、如文档侵犯您的权益,请联系客服反馈,我们会尽快为您处理(人工客服工作时间:9:00-18:30)。
工程液压缸装配
试验出厂工艺规范
一、设备及工量具、装配工装:
1、粗、精洗工作台;外滑环加热装置;无水空压机;烘干机等。
2、各引进套、装配器、整形器等装配工装。
3、各类清洗工具、去毛刺工具、砂纸、油石、抛光膏(粉)、面粉等。
二、准备
1、配套:按装配图上的“零件明细表”领取合格的零件成品、密封件标件等。
未经检查合格的零配件不得进入装配。
2、清理:
A:检查并最终清除所有机加工零件、标准件、塑料件、橡胶件飞边、毛刺、锈迹。
活塞杆应擦拭干净并检查是否有掉铬、碰伤现象,缸筒油口倒角及毛刺应特别注意。
清除时,零件不能有损伤,同时复查各零件外观是否合格;
B:密封件应小心拆除保护装置;
3、清洁:
A:清洗前用压缩空气吹净工作台及待装配零件各部位的异物,再用煤油(密封件不用燃油清洗)或清洗剂清洗干净。
要注意缸筒内孔、缸头各内孔、活塞、导向套各油槽的细小异物;有螺纹的零件应用和好的面团进行粘连去除污物。
B:清洗后要用压缩空气将零件吹干或烘干;
C:采用干式装配的零件进行干燥处理;
D:所有待装配的零件清洗、清理后都要放置在装配点的干净工位器具上;
E:清理、清洗所有装配工具、工装。
4、要求:
A:部装前、自检时严禁带线手套、帆布手套;部装中允许带绵质薄手套。
B:所有零部件必须先行自检,然后通知检验进行检查,合格后方可进行下一步组装。
5、零件检验
装配钳工做好自检工作,再向检验员提请检查。
装配检验员必须按上述要求进行巡检和完工检查。
三、组装
1、组装活塞:分别装配活塞密封组件和支承环;活塞密封(材料为填充PTFE
必须在50°C~60°C的油温中浸泡后才可装配)装配后必须进行整形。
活塞为螺纹式时,将0形圈装入内台阶孔的O形圈槽内。
2、组装导向套:
分别装配轴用组合密封、Y型密封圈、防尘圈(或支承环)和O型圈,组装导向套必须采用干式装配。
3、组装活塞杆:
A:活塞杆小端为卡键式:将活塞杆小端装上O型圈,然后装配活塞组件,再按图纸要求装轴用卡键、卡键帽、轴用挡圈及其它零件。
整体焊接式活塞
杆,须先装导向套组件,再装活塞组件。
B:活塞杆小端为螺纹式:将活塞组件旋入活塞杆上拧紧到位,注意不能损伤O 形圈,然后装锁紧螺母压紧(装配前清除紧定螺钉孔的油脂),装钢球、紧定螺钉(装配前涂紧固胶)。
整体焊接式活塞杆,须先装导向套组件,再装活塞组件。
C:活塞杆杆端为叉头时,最后装叉头。
4、缸体组装:
A:缸体为卡键式:将已组装好的活塞杆装入缸体,再按图纸要求装导向套、孔用卡键、挡环、轴用挡圈及其它零件(注意装配导向套时若O型圈过油口,必须用堵塞堵住油口以免损坏密封件)。
B:缸体为法兰式:将已组装好的活塞杆装入缸体,再按图纸要求装导向套、弹垫、螺钉(螺栓),按装配图拧紧力矩要求拧紧螺钉(螺栓)。
螺钉、螺栓须按拧紧力矩表的拧紧力矩紧固。
特殊油缸按图纸的技术要求执行。
C:缸体为螺纹式:将已组装好的活塞杆装入缸体,再按图纸要求装螺纹式导向套,拧紧。
配钻紧定螺钉孔,清除铁屑,抹紧固胶,装紧定螺钉拧紧。
5、装配过程中的要求
A:保护零件的已加工面的尺寸精度和表面粗糙度,夹持零件要加垫软金属垫块,装拆要用规定的装配工具,在装配的全过程中,不能对零件(组件、部件)进行有损锤击和切削加工,禁止使用如锉刀、刮刀、油石等切削刀具。
个别需要进行配制、配研组装的零件完工后,要在指定的工位清洁被研制零件的各表面。
B:保持各密封件在装配过程中的正确位置和形状,密封件的表面不得出现划伤、拉毛、切边等损伤。
C:保证零部件的配合性质,对过盈配合的固紧零件须注意公差要求,对间隙配合的运动零件要保证运动灵活。
如:关节轴承须转动灵活、衬套须紧固等。
D:配合件和紧固件所用的螺钉、螺母、定位销等在装配时须涂上机油且保证按
图纸上所要求的拧紧力矩要求及其它技术要求,如涂紧固胶等。
定位销的头部要平齐销孔端面。
E:按图纸规定打钢号、钉标牌。
F:装配所用试车接头应每月进行一次螺纹检查,不合格者应及时更换,若使用不合格品的试车接头进行出厂试验,装配检验人员可拒绝进行试车检验。
6、检验
检验人员须对上述装配过程进行严格检查,杜绝野蛮装配。
装配的产品要按图纸的要求对各相关位置和尺寸检查。
如安装距、油口位置、方向及尺寸和缸、杆头的尺寸等。
对于有配管的油缸还要检查配管和油缸的连接是否可靠。
四、出厂试验及检验
A:液压缸出厂试验检验按GB/T7935—2005 《液压元件通用技术条件》、GB/T15622—2005《液压缸试验方法》、JB/T10205—2000《液压缸技术条件》及图纸等技术文件进行试验验收。
B:针对我公司的实际情况,对跑合试验和耐压试验将按批量产品的10%进行抽检,10支以内的按50%抽检。
跑合试验中每支油缸的跑合次数均应达到50次以上,检验人员必须严格测试外泄漏情况。
试验压力、耐压试验、试验时间严格按GB/T15622—2005《液压缸试验方法》执行,以重点观察内泄漏情况。
C:对每支油缸的试验结果必须按有关规定做好记录。
D:经试验合格的产品:放置在倒油架上排净余油,用压缩空气并吹净各部位异物,特别是油口、两端关节轴承部分等,螺纹联接的油口用油塞堵上,法兰联接的油口用油口盖板盖上。
活塞杆外螺纹用橡胶套罩上,耳环孔、关节轴承用防尘盖盖上。
外露部分按规定涂上防锈油经检验人员检查后方可进入成品库待包装。
E、对试验合格的产品进行完工检验。
主要检查螺纹联接的油口是否用油塞堵上,法兰联接的油口是否用油口盖板盖上,活塞杆外螺纹是否用橡胶套罩上,关节轴承是否用防尘盖盖上,外露部分是否按规定涂上防锈油等。