生产件批准管理程序
生产件批准管理程序

生产件批准管理程序一、引言在现代工业生产中,生产件的质量和安全性是至关重要的。
为了确保生产件的质量和安全性,制定和执行一套科学合理的生产件批准管理程序是必不可少的。
本文将介绍生产件批准管理程序的相关内容,以期提高生产件的质量和安全性。
二、制定生产件批准管理程序的必要性1.确保生产件符合质量标准:通过制定生产件批准管理程序,可以确保生产件的设计、制造、检验等各个环节都符合质量标准,从而保证生产件的质量。
2.提高生产效率:生产件批准管理程序可以明确生产件的审批流程和时间要求,避免因审批延误而导致生产进度延误,提高生产效率。
3.保障生产件的安全性:生产件批准管理程序可以要求对生产件的材料、工艺、结构等进行全面评估和审查,确保生产件的安全性。
4.提升企业形象:通过严格执行生产件批准管理程序,可以树立企业的质量和安全形象,增强消费者对企业产品的信任度。
三、生产件批准管理程序的主要内容1.生产件设计批准:在设计生产件时,需要制定详细的设计要求和设计流程,明确设计人员的职责和权限,并进行设计评审和备案,确保设计的合理性和可行性。
2.生产件制造批准:在生产件的制造过程中,需要编制详细的制造工艺和制造流程,明确制造人员的职责和权限,并进行制造过程的监控和检验,确保制造的准确性和质量。
3.生产件材料批准:生产件的材料选择至关重要,需要制定严格的材料选择标准,对材料进行全面评估和检测,确保材料的质量和安全性。
4.生产件检验批准:生产件的检验是确保产品质量的重要环节,需要制定详细的检验标准和检验流程,明确检验人员的职责和权限,并进行检验结果的记录和分析,确保产品符合质量标准。
5.生产件变更批准:在生产件的设计、制造、材料等方面发生变更时,需要制定变更的管理程序,明确变更的审批流程和变更的影响评估,确保变更不影响产品的质量和安全性。
四、生产件批准管理程序的执行1.明确责任:制定生产件批准管理程序时,需要明确相关人员的责任和职责,确保每个环节都有专人负责执行。
ppap的管理流程

ppap的管理流程下载温馨提示:该文档是我店铺精心编制而成,希望大家下载以后,能够帮助大家解决实际的问题。
文档下载后可定制随意修改,请根据实际需要进行相应的调整和使用,谢谢!并且,本店铺为大家提供各种各样类型的实用资料,如教育随笔、日记赏析、句子摘抄、古诗大全、经典美文、话题作文、工作总结、词语解析、文案摘录、其他资料等等,如想了解不同资料格式和写法,敬请关注!Download tips: This document is carefully compiled by theeditor. I hope that after you download them,they can help yousolve practical problems. The document can be customized andmodified after downloading,please adjust and use it according toactual needs, thank you!In addition, our shop provides you with various types ofpractical materials,such as educational essays, diaryappreciation,sentence excerpts,ancient poems,classic articles,topic composition,work summary,word parsing,copy excerpts,other materials and so on,want to know different data formats andwriting methods,please pay attention!PPAP(生产件批准程序)管理流程。
1. 提交申请。
供应商向顾客提交生产件批准申请(PPAP),其中包含以下信息:生产件图纸和规范。
生产件批准管理程序

生产件批准管理程序1. 引言生产件批准管理程序是指企业在生产过程中对于产品生产件的批准管理程序,包括了审批流程、技术要求、责任分工等内容。
该程序旨在确保生产件的合规性和质量可控性,保证产品的生产过程符合法律法规和标准要求。
2. 审批流程生产件批准管理程序的审批流程主要包括以下几个环节:2.1 提交申请生产部门在确定所需生产件后,应填写生产件批准申请表,并将其提交给负责审批的相关部门或人员。
申请表应包含以下内容: - 生产件名称、型号和规格; - 单位数量和预计使用时间; - 技术要求和生产要求; - 影响产品质量的关键环节和控制措施; - 需要使用的设备和设施; - 其他相关材料。
2.2 审批审批部门或人员应在收到生产件批准申请后,按照公司制定的流程进行审批。
审批内容主要包括以下方面: - 生产件的技术要求是否符合标准和规范; - 生产件的供应商是否符合质量管理体系要求; - 是否有足够的生产能力和设备来满足生产要求; - 生产件的采购价格和交货时间是否符合预期; - 其他相关信息。
2.3 批准经过审批部门或人员的评估和审核,如果生产件的申请符合各项要求,审批部门或人员应及时发出批准通知,并将批准结果记录在相应的批准文件中。
2.4 档案管理批准部门或人员应将生产件的批准文件进行归档管理,确保相关信息的完整性和可追溯性。
档案管理应包括以下内容: - 生产件的批准文件; - 生产件的技术要求和生产要求; - 生产件的批准通知。
3. 技术要求为了保证生产件的质量和合规性,生产件批准管理程序要求相关部门或人员制定详细的技术要求,包括以下方面: - 生产件的材料要求; - 生产件的尺寸和外观要求; - 生产件的性能指标; - 在生产过程中需要采取的控制措施。
4. 责任分工为了有效执行生产件批准管理程序,企业应明确相关部门或人员的责任。
常见的责任分工包括以下几个方面: - 生产部门负责填写生产件批准申请表,并负责生产过程的监控和质量控制; - 质量部门负责审核和审批生产件批准申请,并对生产件的合规性进行监督和评估; - 采购部门负责与供应商进行沟通和协商,确保生产件的质量和交货时间符合要求; - 档案部门负责管理生产件的批准文件和相关信息。
生产件批准管理程序

2 过程范围
适用于顾客提出的生产件批准要求及对供方的生产件批准要求。
3 术语和定义
3.1 PPAP (Production Part Approval Process)-- 生产件批准程序
3.2 生产件:是指在生产现场用正式生产工装、量具、过程、材料、操作者、环境和过程参数(如:进给量/速 度/时间/压力/温度)制造的零件
H. 仅适用于散装材料: a、新的或现有的供方提供的具有特殊特性的原材料的新货源; b、在没有外观规范的情况下,产品外观属性的更改; c、在相同的过程中变更了参数(属已批准的产品的P-FMEA参数以外部分,包括包装); d、已批准产品的D-FMEA(产品组成、成分等级)以外部分的更改;
I. 试验/检验方法的更改 — 新技术的采用(不影响接受准则)。
2.用于批准的生产件生产时的数量至少300件或一个小时至 一个班的产量,顾客另有规定的除外; 3. 在证实所有的测试结果均符合顾客的要求,及全部所需 文件都具备以后,负责提交的部门将全部文件列入PPAP 提交清单,经开发部部长审核批准后作PPAP提交;
4. 顾客不认可时,负责提交的部门根据客户要求重新提交 相关资料;
NO
顾客
顾客批准 OK
参见流程说明4.3.1;4.3.2
1.新产品开发时,由项目小组负责与顾客联系,确定提交 等级,当无顾客要求时,按等级三提交。并对工程更改进 行确认;
2 .正式投产后的工程更改时,由开发部负责与顾客联系, 确定提交等级,并对工程更改进行确认;
1.开发部应将PPAP要求及负责部门纳入工作计划;
开发部
样件检验
对于首批样品,开发部对尺寸及外观项目进行检验并保存 记录,供方的生产零件的核准由开发部负责;
PPAP生产件批准管理程序

零件重量(质量)
组织必须在PSW上记录要发运的零件重量,除非顾客另有规定,否则一律用千克(kg)表示,并精确到小数点4位(0.0000)。重量不能包括运输时的保护装置、装配辅具或包装材料。为了确定零件重量,组织必须随机选择10个零件分别称重,然后计算并报告平均重量。用于生产实现的每个型腔、模具、生产线或过程都必须至少选取一个零件进行称重。
XX汽车零部件有限公司
文件编号
版本号
A/0
PPAP生产件批准管理程序
制定部门
生效日期
1.目的:
本程序用来确定组织是否已经正确理解了顾客工程设计记录和规范的所有要求,并且在执行所要求的生产节拍条件下的实际生产过程中,具有持续满足这些要求的潜在能力。
2.范围:
适用于生产件的批准整个过程,本程序也适用于我方对供应商提交的要求。
一旦完全满足所有要求的准则,组织则必须在AAR上记录所要求的信息,必须到你的顾客指定的地点提交完成的AAR和代表性的生产产品/零件,并等候处置。按照所要求的提交等级,在最后提交时,AAR(填入零件交接情况和顾客签名)与PSW一起提交。
散装材料要求检查表(仅适用于散装材料PPAP)
对于散装材料,散装材料要求上检查表(见术语)必须经顾客和组织达成一致。所有规定的要求必须满足,除非在检查表上特别指明“没有要求”(NR)。
注:如果对新零件的共通性已经评审,那么相似零件的“零件系统”控制计划是可接受的。
注:有些顾客要求在提交之前进行控制计划的批准,如:顾客在控制计划上签字。(见IATF16949:2016标准要求)
PPAP 生产件批准管理程序

适用于公司用于汽车制造顾客的所有生产和/或服务所需的生产性零组件之批准。
3.0权责
3.1业务部负责接收顾客的生产件批准(PPAP)的要求和向顾客提交PPAP文件、样件;
3.2工程部项目组负责提供生产件样品,组织完成顾客的PPAP相关资料及数据;负责
提出供方生产件批准要求,负责供方生产件的批准;
C、“生产件批准——性能试验结果”报告必须包括以下内容:
a)被试验零件的设计记录更改等级、以及被试验零件的技术规范的编号、日期及更改等级。
b)尚未纳入设计记录中的任何授权的工程更改文件。
c)进行试验的日期。
10)初始过程能力研究:
项目组在提交由顾客或公司自己指定的所有特殊特性之前,必须按《SPC统计过程控制程序》之规定确定初始过程能力或性能的水平是可以接受的。
C初始研究的接收准则:
对于稳定过程,公司在评价初始过程研究结果时,必须采用以下的接收准则。
D非稳定过程:根据不稳定的性质,一个非稳定过程可能不满足顾客的要求。项目组在提交PPAP之前,必须识别、评价和在可能的情况下消除变差的特殊原因;项目组必须将存在的任何不稳定过程通报顾客,且在任何提交之前,必须向顾客提出纠正措施计划。
3.3采购部负责组织供方实施采购件PPAP要求;
3.4品质部负责提供PPAP相关资料及尺寸结果、材料试验、性能试验结果;
4.定义
4.1 PPAP:指Production Part Approval Process(生产件批准程序)的英文简称。
4.2生产件:在生产现场,用生产模具、量具、工艺过程、材料、操作者、环境和过程设置,
5.1.2.提交给顾客批准的生产件必须在第一批产品发运前完成批准,除非顾客放弃该生产件的批准要求(要求顾客签署姓名和日期并记录存档);不论顾客有没有要求公司正式提交生产件,项目组都必须对PPAP文件中所有适用的项目进行评审和更新,以反映生产过程的情况。提交给顾客批准的生产件必须取自重要的和有效的生产过程,该生产过程必须是1小时到8小时的生产,且规定数量至少为300件连续生产的产品/部件,除非顾客或顾客授权的质量代表另有书面规定和要求。
生产件批准管理程序

1.目的:用来确定组织是否已经正确理解了顾客工程设计记录和规范的所有要求,并且在执行所要求的生产节拍条件下的实际生产过程中,具有持续满足这些要求的潜在能力。
2.范围:2.1凡本组织提交顾客的汽车生产件的内部和外部供方现场均适用,顾客有要求时可依其指定的要求来实施提交。
当顾客无特殊要求时,组织按本程序要求实施;2.2有关供方向本组织提交的生产件批准:2.2.1顾客指定本组织的供方随本组织一起PPAP提交;2.2.2本组织要求供方提交。
3.相关文件及术语3.1PPAP:生产件批准程序;3.2AAR:外观件批准报告;3.3PSW:零件提交保证书;3.4生产件:用于PPAP的产品必须取自生产过程(即用正式生产工装、量具、工艺过程、材料、操作者、环境和过程设置),必须是1小时到8小时的生产,且规定的生产数量至少300件连续生产的产品,除非顾客另有规定。
4.职责:4.1市场部负责与顾客沟通,传达顾客现场审核要求,试生产订单的下达,产品交付信息的传递以及PPAP的提交和确认结果沟通;4.2开发部负责试生产过程控制及相关文件资料的修正,资料室存档,工装量产性验收,量产性评审及整改计划,试生产现场操作、检验培训,PPAP内部认可,试生产过程问题点的记录、检查和反馈;PPAP提交的相关文件资料的准备:设计记录、工程更改文件、顾客工程批准、过程流程图、PFMEA、初始过程研究、控制计划、生产件样品、标准样品、检查辅具、顾客特殊要求记录、尺寸结果、外观件批准报告(适用时入材料试验结果、性能试验结果、测量系统分析研究、具有资格的实验室文件、零件提交保证书。
4.3质量部负责进料检验、试生产过程产品质量控制、过程审核、产品审核、不良品统计分析和生产质量保证;4.4制造部负责试生产过程准备(包括生产计划、生产设备、生产人员安排、原辅材料采购以及供方PPAP提交),试生产,生产线配置,常用物流工具准备,业务订单交付,设备的维护和保养,批量生产设备保证,工装量产性改善和试生产现场相关的培训;XX 有限公司程序文件生产件批准管理程序 页次 3/8 文件编号XX/QP0703-09版本号A/05.流程图:主导部门:开发部6.内容:6.1 对于新产品在OTS 认可并试生产有效运行的情况下,由开发部提出PPAP 认可要求,市场 部负责通知顾客产品批准部门并确定现场审核的方式和日期。
生产件批准管理程序

生产件批准管理程序引言生产件批准管理程序是一种重要的管理工具,用于确保生产件在制造过程中符合质量标准和技术要求。
通过严格执行生产件批准管理程序,可以减少生产环节中的错误和缺陷,提高生产效率和产品质量。
本文将介绍生产件批准管理程序的目的、范围、流程和相关责任。
目的生产件批准管理程序的主要目的是确保生产过程中所使用的零件和材料符合质量标准和技术要求,以保证最终产品的质量。
通过严格执行批准管理程序,可以有效地检查和验证供应商提供的生产件,避免使用不合格的零件和材料,减少缺陷和废品的产生,提高产品质量和客户满意度。
范围生产件批准管理程序适用于所有与生产过程相关的零件和材料。
它包括但不限于以下方面:1.材料批准:在开始生产之前,必须对所使用的原材料进行审查和批准。
原材料必须符合质量标准和技术要求,并提供相关的证明文件。
2.供应商管理:生产件的供应商必须符合公司的供应商评估要求。
供应商必须提供相关的质量控制文件和报告,以证明其产品质量和供货能力。
3.零件检验:在生产过程中,必须对使用的零件进行检验,以确保其质量和准确性。
检验方法和标准必须与公司的质量管理体系相一致。
4.批准记录:所有通过批准管理程序的生产件必须有相应的批准记录。
批准记录包括零件的描述、规格、供应商信息和批准日期等。
流程生产件批准管理程序包括以下流程:1.申请批准:生产部门必须在开始使用新的生产件之前,向质量部门提交批准申请。
申请中必须包含零件的描述、规格、供应商信息和批准理由等。
2.审查申请:质量部门对批准申请进行审查,包括对零件的质量标准和技术要求的确认。
如果申请不符合要求,质量部门可以要求申请者提供补充信息或进行修改。
3.零件检验:一旦申请获得批准,生产部门必须对所使用的零件进行检验。
检验可以采用抽样检验或全检验的方式,具体方法由质量部门指定。
4.发布批准:经过检验合格的生产件,质量部门将发布批准记录。
此时,生产部门才可以正式使用该生产件。
生产件批准(PPAP)管理程序
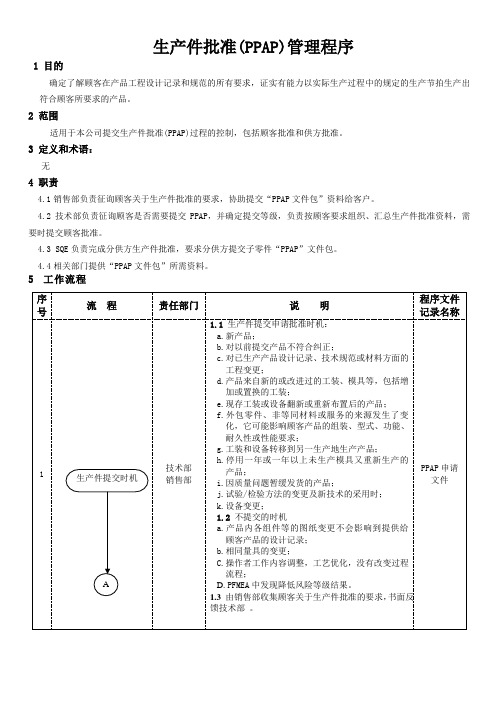
生产件批准(PPAP)管理程序
1 目的
确定了解顾客在产品工程设计记录和规范的所有要求,证实有能力以实际生产过程中的规定的生产节拍生产出符合顾客所要求的产品。
2 范围
适用于本公司提交生产件批准(PPAP)过程的控制,包括顾客批准和供方批准。
3 定义和术语:
无
4 职责
4.1销售部负责征询顾客关于生产件批准的要求,协助提交“PPAP文件包”资料给客户。
4.2技术部负责征询顾客是否需要提交PPAP,并确定提交等级,负责按顾客要求组织、汇总生产件批准资料,需要时提交顾客批准。
4.3 SQE负责完成分供方生产件批准,要求分供方提交子零件“PPAP”文件包。
4.4相关部门提供“PPAP文件包”所需资料。
5工作流程
6顾客的通知
公司有如下情形的制造过程设计的变更,在变更前必须通知顾客,且必须在顾客批准建议的变更后才能实施,并在变更后的一个月内重新提交PPAP。
1.和以前批准的零件或产品相比,使用了其他不同的结构或材料。
2.使用了新的或改进的工装(不包括易损工装)、模具,包括补充的或替换用的工装。
3.在对现有的工装或设备进行设计或重新布置之后进行生产。
4.外包零件、非等同材料或服务的来源发生了变化,它可能影响顾客产品的组装、型式、功能、耐久性或性能要求。
5.工装和设备转移到另一生产地生产产品。
6.停用一年或一年以上未生产模具又重新生产的产品。
7.试验/检验方法的变更及新技术的采用时。
7相关文件
8 相关表单。
PPAP生产件批准管理控制程序

1、目的
本程序规定了生产件批准(PPAP)的一般要求,通过对生产件的批准过程,确保公司对顾客的所有要求正确理解,并有能力按规定的生产节拍提供满足顾客要求的产品。
2、范围
适用于公司范围内所有汽车行业产品及过程。
3、定义
生产件:在生产现场使用正式生产工装、工艺过程、材料、操作者、环境和过程参数制造出来的零部件。
用于批准的生产件必须取自于1-8小时的量产、且生产数量至少为300件连续生产的零部件或由顾客相关部门批准的数量。
4、职责
4.1技术部门负责本程序的控制。
负责产品及工艺设计策划及样件制作过程管理。
4.2质量管理部门提供:负责产品质量校验、试验、性能报告;负责测量系统分析报告;实验室及PSW保证书资料提交。
4.3 各责任部门负责按APQP策划要求准备、提供相应的资料。
采购部门负责供应商PPAP资料提交过程监控,推荐使用本程序规定的方法及资料格式。
5、工作流程及描述
5.1产品和过程批准流程图
5.2工作要点简述
附录:PPAP提交等级表
注:S==公司必须向指定的顾客产品批准部门提交,并在适当的场所,包括制造场所,保留一份记录或文件项目的复印件。
R==公司必须在适当的场所,包括制造场所保存,顾客代表有要求时应易于得到。
*==公司必须在适当的场所保存,并在有要求时向顾客提交。
6、支持性文件
《项目管理程序》
7、记录
8、程序变更记录。
生产件批准(PPAP)管理程序

1.《试产计划》 2.《过程流程图》 3.《过程失效模式及 后果分析》 4.《控制计划》
1.PPAP 产品
生产科 技术科
5.3.4 品质科负责零件提交保证书、测量系
统分析、生产件的全尺寸检验、性能试验结 果、材料试验结果、初期 PPK 研究。
1.《R&R 分析报告》
技术科
● ● 1 个工作周
技术科项目工 程师
4、 作业过程:
过程输入
过程输出
过程绩效
1.APQP 过程 2.顾客 PPAP 提交要求
1.PPAP 样 2.PPAP 文件
1.PPAP 一次通过率≥75%
文件编号 版 本/修 订 号
有限公司
A/0 生 效 日 期
文件名称
页
次
2020-3-1
生产件批准(PPAP)管
理程序
第2页 共 11 页
条款号
A
● 1.《生产件批准启动申请表》
作业方法描述
5.1 生产件批准申请表的提出 5.1.1 除非有顾客放弃的书面通知(需同意人签 名),新产品在正式生产前必须按 PPAP 执 行,新产品由营业部依据《APQP 进度表》提 出启动。
输出
1.《生产件批准启动 申请表》
信息
多功能小 组组长、副 总经理 部长
2、 适用范围: 本程序适用于顾客有要求时本公司向其提交供其进行生产件批准的产品。
3、 定义: 3.1.生产件:生产件是指生产现场使用同批量生产一致的生产工装、设备、量具、制造过程、材料、操作者、操作环境和过程参数来制造的零 件;用于生产件批准的零件必须是来自有效的生产过程,除非顾客另有规定,该过程必须是 1 小时到 8 小时的连续生产,生产量至少为 300 件连续生产的零件。对于每一个生产过程,即对于来自于相同的装配线或生产单元、多个模腔的冲模、压铸模或加工夹具的每一个位置的零 件,都必须进行对代表性样件进行测量及试验。 3.2.标准样品:从试生产过程中随机抽取的能代表生产件的品质水平的样品,与用于生产件批准的样件一起提交给顾客,在顾客批准后返回公 司作为生产标准使用的样品,或者当顾客不签回标准样品时,在提交生产件批准时,由本公司工程师保留的样件,在收到顾客书面的 PPAP 批准后,由本公司工程师签名确认作为生产标准使用的样品,都统称为标准样品。 标准样品必须同用于生产件批准的零件来源于同一次试生产过程,对于每一个生产过程,即对于相同的装配线或生产单元、多个模腔的冲 模、压铸模或加工夹具的每一个位置,都必须包括。
生产件批准(PPAP)管理程序

XXXXXXXX有限公司生产件批准(PPAP)管理程序文件编号:版本:编制:审核:批准:XXXXX有限公司发布生产件批准(P P A P)管理程序1.目的确保正确理解了顾客的所有要求,并依顾客的要求实施产品批准计划,确保提交的资料、产品符合客户之要求。
2. 范围本程序适用于本公司为顾客提供的新产品(各种汽车电子产品主机及喇叭、天线、支架等附件)或因设计、材料、工程、工装模具更改使产品外观、性能参数发生变化时,在第一批产品发运前对产品进行评审和送顾客批准。
3. 规范性引用文件下列文件对于本文件的应用是必不可少的,凡是注日期的引用文件,仅注日期的版本适用于本文件。
凡是不注日期的引用文件,其最新版本(包括所有的修改单)使用于本文件。
XX-61 产品开发控制程序XX-63 项目管理控制程序PPAP手册4.定义4.1 PPAP:生产件批准程序(Production Part Approval Process)。
4.2 生产件(Production Part):是指在生产现场使用生产工装、量具、过程、操作者、环境和过程参数生产的产品。
4.3 生产件批准提交(Production Part Approval Submissions): 是以从有效的生产(Significant Production Run)中抽取特定数量的生产件或生产材料为基础,该生产过程是用生产工装、工艺过程和循环次数来进行的。
该生产过程必须是1 小时到8 小时的量产,除非客户另以书面同意其它数量,否則產出量至少为300件连续生产的零件。
这些用于生产件批准而提交的零件或材料要由组织验证满足所有设计记录上规定的要求。
4.4 PE(Process engineer):工艺工程师4.5 IQC(Input Quality Control):来料品质检验4.6 PQC(Process Quality Control):过程品质控制5. 职责5.1 技术中心5.1.1 技术中心:负责提交可销售产品的设计记录(工程图面、特殊特性清单等)、DFMEA、工程规范、顾客工程批准相关资料、包装规范、IMDS资料、设计变更资料(如有)等;5.1.2 技术中心实验室:负责提交材料测试报告、试验报告、合格实验室文件等;5.2 制造中心:负责生产件样品/标准样品的提交、留存、标识及相关资料的提交,作业指导书的完成与提交;5.3采购物流中心:负责分供方清单的提交;5.4质量管理部:5.4.1 负责送件测试,提供相应的全尺寸与性能测试报告,提供外观件批准报告(AAR),完成量测系统分析(MSA)与初期能力研究(PPK),填写零件提交保证书(PSW)等;5.4.2 负责审核项目管理部收集汇总的所有PPAP资料的符合性,并将审核后的PPAP资料提交给市场营销部;5.5项目管理部:负责依据产品开发控制程序和项目管理控制程序时间节点要求收集汇总所有资料,并组织APQP项目小组成员评审相关资料的符合性;;5.6 营销中心:将产品批准所需资料送交客户审核批准,并将相关信息反馈给质量管理部与项目管理部;5.7 工程部:负责提交过程流程图、PFMEA、控制计划、场地平面布置图(如客户需要)、检查辅具清单等。
生产件批准程序

生产件批准程序一、背景介绍生产件批准程序(Product Approval Process)是企业在生产制造领域中的一种重要管理方式,用于确保生产的产品符合质量标准和技术要求。
该程序通过一系列步骤和程序,确保生产件的合格性,从而减少产品质量问题和生产事故的发生,提高产品的可靠性和用户满意度。
二、程序步骤1. 定义批准标准在生产件批准程序中,首先需要明确批准标准。
批准标准应包括产品质量要求、技术规范、工艺流程、可靠性要求等内容。
企业需要与设计部门、质量部门以及相关技术人员进行沟通,确定产品应达到的标准。
定期检查和修订批准标准是保持符合最新技术和市场需求的重要环节。
2. 提交批准申请一旦产品开发完成,企业应向批准管理部门提交批准申请。
申请内容应包括产品的名称、规格参数、技术要求等相关信息,并附上产品的设计图纸、所需材料清单和技术文件等。
申请时应注意完整准确地提供所需信息,以便批准部门进行评估和审查。
3. 批准评估和审查批准部门将对申请进行评估和审查。
评估内容包括产品的设计合理性、制造可行性、材料可靠性、工艺流程是否符合规范等。
审查内容则包括技术文件的完整性和准确性、相关法规和标准的遵守情况等。
批准部门可以根据需要进行实地考察和测试。
4. 批准决策基于评估和审查的结果,批准部门将作出决策。
如果产品符合批准标准,则将对申请进行批准,并颁发相应的批准文件。
如果产品不符合批准标准,将要求申请人进行相应的改进和调整。
企业还可以附上批准条件和期限,以确保产品质量持续达到标准。
5. 生产执行一旦产品获得批准,企业可以开始进行相应的生产制造工作。
企业应按照批准标准和要求进行生产,确保产品的一致性和合格性。
同时,企业应对生产过程进行严格控制,例如进行过程检查、品质抽检等,确保产品的质量稳定性和一致性。
6. 批准监控和更新对于已经批准的产品,批准部门需要定期进行监控和更新。
监控内容包括产品质量检验、用户反馈、生产数据分析等。
生产件批准程序手册

生产件批准程序手册一、引言生产件批准程序手册是为了确保生产过程的质量控制和监管而制定的指导性文件。
本手册旨在规范生产件批准的流程和要求,提高产品制造的准确性和一致性。
二、适用范围本手册适用于公司内部所有生产件的批准程序,包括但不限于工程图纸、工艺文件、产品样品等。
三、定义和缩写1. 批准:指通过文件或书面形式,确认生产件符合规定要求并获得批准的过程。
2. 生产件:指用于产品制造的所有工程图纸、工艺文件、产品样品等。
3. PERT(Program Evaluation and Review Technique):项目评价与审查技术。
四、生产件批准流程1. 提交申请生产件批准的流程由设计部门发起,向质量控制部门提交申请表格(表格样式参见附录A)和相关资料,包括产品设计图纸、工艺文件等。
2. 技术评审质量控制部门接收申请后,安排技术人员进行评审。
评审内容主要包括生产件的规格、尺寸、材料、工艺要求等方面的符合性。
评审结束后,技术人员根据评审结果进行意见反馈。
3. 修改和重新提交如果评审意见中存在不符合要求的部分,设计部门需要根据意见进行修改,并重新提交申请。
修改完成后,重新按照程序提交申请表格和相关资料。
4. 批准决策质量控制部门根据技术评审结果和修改后的申请资料,对生产件的批准进行决策。
决策包括通过、拒绝或者要求进一步修改与复审。
决策结果由批准委员会签署。
5. 批准公告批准委员会将批准决策结果公告给设计部门和生产部门。
设计部门和生产部门接收公告后,开始生产件的制造和组装工作。
6. 记录和存档所有的生产件批准申请表格、评审意见、决策结果等文件必须进行记录和存档。
记录和存档的方式可参照公司规定的档案管理制度进行。
五、质量控制要求对于每个生产件批准申请,在评审过程中,质量控制部门需注意以下要求:1. 评审人员必须具备相关技术知识和经验,确保评审结果准确可靠。
2. 所有评审意见必须清晰、明确,并按时提交给申请部门。
质量PPAP生产件批准程序管理与实施规范

质量PPAP生产件批准程序管理与实施规范一、引言质量PPAP(Production Part Approval Process)生产件批准程序是一种质量管理方法,用于验证供应商所提供的生产件能否满足客户的要求和期望。
本文旨在探讨质量PPAP生产件批准程序的管理与实施规范,以确保产品质量和顾客满意度。
二、程序管理1. 定义审批流程在管理质量PPAP生产件批准程序前,首先需要明确审批流程。
确定相关的部门和责任人,并规定每个审批节点的职责和审核要求。
审批流程应该全面、透明,并及时进行调整和改进。
2. 指定PPAP团队成立专门的PPAP团队,负责管理和执行PPAP生产件批准程序。
该团队应包括质量工程师、供应链管理人员、技术人员等相关人员,并确保团队成员具备充足的知识和技能,以保证程序的顺利进行。
3. 制定PPAP文档根据客户要求和标准,制定符合质量PPAP要求的文件和记录。
这些文件和记录应包括但不限于控制计划、样品评估报告、测量系统分析和检验结果等。
确保文档的准确性和完整性,以便审批和审核时能提供清晰的信息。
4. 建立供应商评估机制定期对供应商进行评估和审核,以确保其具备满足质量PPAP要求的能力。
评估内容可包括供应商的质量管理系统、生产工艺、设备能力等。
根据评估结果,对供应商进行分类管理,并与其积极进行沟通和协作,以提高供应链的稳定性和质量水平。
三、实施规范1. 产品设计阶段在产品设计阶段,应确保设计团队充分了解PPAP要求,并将其纳入设计规范中。
设计团队应与质量PPAP团队紧密合作,确保设计满足质量要求和客户期望,并为后续的生产件批准做好准备工作。
2. 样品制备与评估样品制备是质量PPAP的关键环节之一。
样品应按照客户要求和标准进行制备,并确保每一项要求都得到满足。
样品评估包括对外观、尺寸、性能等方面进行全面的检验和测试,确保产品的质量和符合性。
3. 测量系统分析在质量PPAP生产件批准程序中,测量系统的准确性和可靠性至关重要。
生产件批准程序

生产件批准程序1. 引言生产件批准程序是指在生产过程中对生产件的核准和批准流程。
该程序旨在确保生产件符合质量和规范要求,并确保产品的一致性和稳定性。
本文档将详细介绍生产件批准程序的具体流程和相关要求。
2. 批准程序概述生产件批准程序包括以下关键步骤:•批准流程定义•生产件批准文件•批准标准和要求•生产件批准流程执行3. 批准流程定义生产件批准流程需要明确定义所有相关人员和部门的角色和职责。
下面是一个基本的生产件批准流程示例:1.设计阶段:设计团队完成生产件的设计和开发,并编写设计文档。
2.样品制作:根据设计文档制作样品,并进行内部评估和测试。
3.样品审批:样品交由质量部门进行审批和评估,确保样品符合质量要求。
4.批准文件准备:根据样品审批结果,编写生产件批准文件。
5.批准文件审批:批准文件交由相关管理部门进行审批。
6.生产准备:生产部门根据批准文件准备生产设备和相关资源。
7.生产件批准:生产部门根据批准文件进行生产,并对生产件进行质量控制和检查。
8.批准结果记录:质量部门记录生产件批准结果并归档。
4. 生产件批准文件生产件批准文件是生产件批准过程中的核心文件。
批准文件包括以下内容:•生产件设计文档:包含生产件的技术规格和设计要求。
•样品评估报告:对样品进行评估和测试的报告,包括各项指标和测试结果。
•生产件批准表:记录生产件批准结果和相关信息的表格。
•相关许可证和证书:包括产品认证、生产许可证等相关文件。
5. 批准标准和要求在批准过程中,需要明确定义生产件的标准和要求。
这些标准和要求通常包括以下几个方面:•技术要求:包括生产件的尺寸、材料性能、外观要求等。
•安全要求:包括生产件的安全性能和使用安全要求。
•环境要求:包括生产件的环境适应性和环境保护要求。
•质量要求:包括生产件的质量控制要求和质量管理要求。
6. 生产件批准流程执行在实际执行生产件批准流程时,需要按照以下步骤进行:1.设计阶段:设计团队根据设计要求完成设计和开发,并编写设计文档。
生产件批准PPAP管理程序

XX-QP-834-04XXX 模具制造有限公司A4(210X297)生产件批准管理程序PPAP制定日期 2016.11.15XX-QP-16版本/版次 A0页次发放范围:总经理、办公室、供销部、品质部、生技部、财务部 编制. 审核 会签 批准办公室 副总 财务部 供销部(销售) 供销部(采购)总经理XXX 模具制造有限公司程序文件目的:1、按顾客要求实施生产件批准计划,以确定顾客的工程设计记录和规范的所有要求都被完全了解,并确定公司按顾客规定的生产节拍来生产顾客需要的产品。
2、范围:适用对顾客要求的生产件批准的控制。
对没有ISO/IATF16949要求的顾客,可以不实施PPAP程序,只需按照顾客的要求提交样品和有关文件。
对A类、B类供应商必须采用同样的批准程序控制。
供应商提交PPAP的项目依据品质部部的要求实施。
3、职责:3.1 技术部负责生产件批准的归口管理,负责联络顾客,向顾客提供生产件批准所需的实物和资料,并向相关部门反映生产件批准的情况。
4、定义:4.1 生产件生产件是指生产现场使用正式的生产工装、量具、过程、材料、操作者、操作环境和过程参数零件。
4.2 标准样品提交给顾客的样品,在顾客批准后返回公司作为生产标准使用。
5、程序5.1必须向顾客提交PPAP批准的情况5.1.1 新的零件或产品(如:以前未曾提供给顾客的某种零件、材料、或颜色)5.1.2 对以前提交的不符合零件的纠正。
要求提交对所有以前的不符合零件的纠正。
“不符合”包括以下内容:a产品性能违反顾客的要求;b产品或能力问题;c供方问题,d替代零件的临时批准;e试验问题5.1.3 关于生产产品/零件编号的设计记录、技术规范、或材料方面的工程变更。
5.2需通知顾客,由顾客决定提交PPAP批准的情况。
公司必须将下列的任何设计和过程更改通知顾客产品批准部门,由顾客决定是否需提交PPAP批准:5.2.1 和以前被批准的零件或产品相比,使用了其他不同的结构或材料。
PPAP(生产件批准)管理程序

页 次
5/5
7.使用表单:
7.1《调机试模记录表》
7.2《PPAP文件汇总表》
7.3《零件提交保证书》
7.4《尺寸检验结果》
7.5《材料试验结果》
7.6《性能试验结果》
7.7《外观件批准报告》
7.8《工装样件认可报告》
7.9《生产件最终批准报告》
送交客户进行批准。
5.9生产件最终批准:
5.9.1本公司通过样品批准程序后,仍应确保往后量产结果仍能符合客户要求。
5.9.2经Titus批准前不得交货,批准结果区分下列3种情况:
a.核准:本公司零组件满足所有规格及要求,可以开始交货。
b.暂时性核准:在限定时间内或数量基准下同意本公司配合生产需求进行交货
等级5——在供应商制造厂备有保证书、工装样件和完整的支持数据以供评审
5.4零件提交保证书:
5.4.1全部要求符合则填入保证书内。
5.4.2当确认全部要求均符合而且所有要求的文件或样品均已备妥,则质量部主管应于保证书签名。
5.4.3工程变更:视工程变更程度,按客户要求重新提出生产件批准申请。
5.5尺寸检验:
c退件:正式量产前应重新送件申请批准。
文件编号
QP-34
版本
V01
文件名称
File Name
PPAP(生产件批准)管理程序
页 次
4/5
作业流程图
控制部门
说明事项
技术部、采购
向供应商采购新模具或要求供应商打样时。
供应商、采购
供应商提交PPAP资料,Titus采购接收。
质量经理、管理代表
质量部、生产部
1.质量部提供样品尺寸量测结果、外观检查结果、功能性测试结果。
- 1、下载文档前请自行甄别文档内容的完整性,平台不提供额外的编辑、内容补充、找答案等附加服务。
- 2、"仅部分预览"的文档,不可在线预览部分如存在完整性等问题,可反馈申请退款(可完整预览的文档不适用该条件!)。
- 3、如文档侵犯您的权益,请联系客服反馈,我们会尽快为您处理(人工客服工作时间:9:00-18:30)。
1.目的:用来确定组织是否已经正确理解了顾客工程设计记录和规范的所有要求,并且在执行所要求的生产节拍条件下的实际生产过程中,具有持续满足这些要求的潜在能力。
2.范围:2.1凡本组织提交顾客的汽车生产件的内部和外部供方现场均适用,顾客有要求时可依其指定的要求来实施提交。
当顾客无特殊要求时,组织按本程序要求实施;2.2 有关供方向本组织提交的生产件批准:2.2.1顾客指定本组织的供方随本组织一起PPAP提交;2.2.2本组织要求供方提交。
3.相关文件及术语3.1 PPAP:生产件批准程序;3.2 AAR:外观件批准报告;3.3 PSW:零件提交保证书;3.4生产件:用于PPAP的产品必须取自生产过程(即用正式生产工装、量具、工艺过程、材料、操作者、环境和过程设置),必须是1小时到8小时的生产,且规定的生产数量至少300件连续生产的产品,除非顾客另有规定。
4.职责:4.1市场部负责与顾客沟通,传达顾客现场审核要求,试生产订单的下达,产品交付信息的传递以及PPAP的提交和确认结果沟通;4.2开发部负责试生产过程控制及相关文件资料的修正,资料室存档,工装量产性验收,量产性评审及整改计划,试生产现场操作、检验培训,PPAP 内部认可,试生产过程问题点的记录、检查和反馈;PPAP提交的相关文件资料的准备:设计记录、工程更改文件、顾客工程批准、过程流程图、PFMEA、初始过程研究、控制计划、生产件样品、标准样品、检查辅具、顾客特殊要求记录、尺寸结果、外观件批准报告(适用时)、材料试验结果、性能试验结果、测量系统分析研究、具有资格的实验室文件、零件提交保证书。
4.3质量部负责进料检验、试生产过程产品质量控制、过程审核、产品审核、不良品统计分析和生产质量保证;4.4制造部负责试生产过程准备(包括生产计划、生产设备、生产人员安排、原辅材料采购以及供方PPAP提交),试生产,生产线配置,常用物流工具准备,业务订单交付,设备的维护和保养,批量生产设备保证,工装量产性改善和试生产现场相关的培训;5.流程图:主导部门:开发部6.内容:6.1对于新产品在OTS认可并试生产有效运行的情况下,由开发部提出PPAP认可要求,市场部负责通知顾客产品批准部门并确定现场审核的方式和日期。
6.2制造部接到开发部的试生产移交通知后即进行生产过程准备,包括制定生产计划表、原辅材料采购、生产设备、生产人员安排等。
6.3制造部负责PPAP试生产或2TP试生产以确保提交的零件出自正式的生产过程;6.4开发部保持与市场部的充分沟通并按“PPAP准备计划”督促各项准备工作就绪以确保PPAP 试生产的成功。
6.5 PPAP提交范围或时机:6.5.1必须在首批产品发运前提交PPAP批准,除非负责顾客批准部门放弃该要求;6.5.2以下情况发生时通知顾客,因顾客可能会决定要求提交PPAP批准:6.5.2.1与以前批准的零件相比使用了其他可选择的结构、材料或加工方法;6.5.2.2使用新的或改进的工装(易损工装除外)、模具、铸模、模型等,包括附加的和替换用的工装;6.5.2.3现有工装或设备经翻新或重新布置后进行生产;6.5.2.4设备或工装转移到不同的工厂或在一个新增的厂址进行生产;6.5.2.5供方零件、非等效材料或服务(如热处理、电镀)的更改,从而影响顾客的装配、成型、功能、性能或耐久性的要求;6.5.2.6在工装停止批量生产达到或超过12个月以后重新启用而生产的产品;6.5.2.7 由内部生产的或供方生产的产品或生产过程的更改;6.5.2.8检验/试验方法的更改-新技术的采用(不影响接受准则);6.5.3下列情况下不要求通知顾客和提交PPAP,但需更新受到影响的PPAP文件;6.5.3.1对配件图纸的更改,内部制造或供方制造但不影响到提供给顾客产品的设计记录;6.5.3.2工装在同一工厂移动(用于等效的设备、过程流程不变、不分解工装)或设备在同一工厂移动(相同的设备、过程流程不变);6.5.3.3设备方面的更改(具有相同的基本技术或方法的过程流程);6.5.3.4重新平衡操作工的作业含量,对过程流程不引起更改;6.6 PPAP试生产或2TP试生产。
6.7 PPAP试生产的产品用来验证产品和过程是否符合生产件的要求并输出相应的PPAP文件。
6.8 生产件批准之必备文件:6.8.1设计记录(包括零件图纸、CAD/CAM数据、规范等);6.8.2授权的工程更改文件:必须具有尚未记入设计记录中但已在产品、零件或工装上体现出来的任何授权的工程更改文件;6.8.3要求的工程批准:在设计记录有规定时,本公司必须具有顾客工程批准的证据;6.8.4“过程流程图”,对于格式如顾客有规定则按顾客要求;6.8.5“PFMEA表”,其执行依《PFMEA管理规定》;6.8.6尺寸结果-“首件(批)样品检验报告”;6.8.7材料/性能/耐久性试验结果总结报告,按照“试验大纲”中规定的试验要求进行材料试验,出具试验报告;对于顾客开发的材料规范和有顾客批准的供方名单的产品,本公司必须从指定的供方采购材料或服务。
6.8.8初始过程研究报告(PPK研究报告),其执行依《数据分析管理程序》:6.8.8.1在提交之前对于顾客或本公司指定为关键或重要的所有产品特性必须确定初始过程能力的可接受水平;6.8.8.2利用X-R图对设备、人力、材料、方法进行评估,对于那些使用X-R图能够研究的产品特性,应根据25组或更多子组的数据并至少包括总数为100以上的单个数据进行短期研究;6.8.8.3质量指数:Ppk-初始过程能力指数,Cpk-稳定过程的能力指数;6.8.8.4初始研究的接受准则:Ppk>1.67,该过程目前能满足顾客要求,批准后即可按控制计划进行生产; 1.33≤Ppk≤1.67,该过程目前可被接受,但是要求进行一些改进,并与顾客取得联系来评审研究结果,如果在批量生产之前仍没有办法改进将要求对控制计划进行更改;Ppk<1.33,该过程目前不能满足接受准则,与顾客代表取得联系,对研究结果进行评审,采取纠正预防措施进行过程改进并对控制计划进行更改;6.8.8.5量产为非稳定过程时应做100%全检并追加SPC管制,直到CPK≥1.33为止,必须优先进行过程改进并形成纠正措施计划文件;6.8.8.6不满足接受准则时的策略:必须提出纠正措施计划(如:过程改进、工装更改和顾客工程要求更改)以及临时修订控制计划(如包括出厂产品100%检验)并经客户批准,持续进行减少变差的努力直到CPK≥ 1.33;6.8.9具有资格试验室的文件要求:组织必须表明试验范围和所委托试验室符合资格的证明文件;6.8.10“控制计划”:其执行依《控制计划管理规定》;6.8.11“零件提交保证书(PSW)”:对于每一顾客零件编号都必须完成一份单独的保证书PSW;6.8.11.1零件重量:必须选择10个零件取其平均重量,单位:kg,精确到小数点后4位。
6.8.12“外观件批准报告(AAR)”:在设计记录中有外观要求的每个零件必须完成一份单独的“外观件批准报告”,通常只适用于带有颜色、表面粒度或表面外观要求的零件;6.8.13生产件样品:组织必须按照顾客的要求或提交要求的规定提供取自生产过程的零件样品;6.8.14标准样品:组织必须保存一件标准样品,与生产件批准记录保存的时间相同或保存在设计记录、控制计划或检验准则要求有标准样品的地方,作为一个基准或检验标准使用,必须对样品加以标识并标出批准的日期;6.8.15检具及检查辅具:本公司必须认证检具及检查辅具与零件尺寸要求一致,如顾客提出要求则必须提交零件的检具、检查辅具及相关文件(如检具清单、检具图纸、量测系统分析报告等);6.8.16包装说明(除非顾客要求):经项目小组评价或顾客批准的“包装规范”,格式可按顾客要求;6.8.17“供应商清单”(除非顾客要求);6.8.18“场地平面布置图”(除非顾客要求);6.8.19功能评估(FE)报告(除非顾客要求);6.8.20顾客的特殊要求:本公司必须有与所有适用的顾客特殊要求相符合的记录。
6.9提交等级:6.9.1提交的等级由顾客确定,如顾客未指定则以等级3为默认等级:等级1--只向顾客提交保证书(若指定为外观项目,还应提交外观件批准报告);等级2--向顾客提交保证书和产品样品及有限的支持数据;等级3--向顾客提交保证书和产品样品及完整的支持数据;等级4--提交保证书和顾客规定的其他要求;等级5--在本公司评审完整的支持数据和零件样品。
6.9.2 PPAP的保存/提交要求:S=必须向指定的顾客产品批准部门提交,本组织只保留复印件。
R=本组织必须在适当的场所,包括制造场所保存,顾客代表有要求时应易于得到。
*=本组织在适当的场所保存,并在有要求时向顾客提交。
6.10质量部要求并审核供方提交的PPAP,采购在组织内代表供方;6.10.1选择供方需符合ISO9001:2000/QS-9000/VDA6.1/TS16949要求;6.10.2供方PPAP评审:6.10.2.1供方在试生产后需提交PPAP;6.10.2.2本公司对供方的PPAP审核后,由质量部主导提供PPAP审核报告,不符合项由制造部采购落实供方整改;6.10.2.3供方经组织认可后方可进入量产。
6.10.3如顾客要求对供方进行认可,则提交“供应商清单”;6.11项目小组在PPAP试生产后进行总结是必不可少的,针对PPAP试生产出现的问题点采取对策尽快实施。
6.12 项目小组在PPAP试生产后必须进行评估试生产的产品和过程是否符合生产件的要求以决定是否提交,内部决定发货需经开发部、质量部和市场部核准,申请特采需经总经理批准。
6.13 市场部负责PPAP的提交和提交后的确认工作(如PPAP提交后的问题反馈和获取顾客PPAP认可报告等),协调开发部等相关部门参与现场验证。
6.14项目小组必须在PPAP试生产后对“控制计划”进行评审和修订,以巩固PPAP试生产的成果和用于量产的控制。
6.15组织在接到顾客批准前决不能按批量发运其产品,如公司内部没有核准提交或顾客没有批准均需重新进行PPAP试生产。
6.16产品提交状态:6.16.1完全批准:该产品满足顾客所有的规范和要求,可根据顾客计划部门的安排按批量发运产品;6.16.2临时批准:允许按限定时间或零件数量运送生产需要的材料;仅当下列情况下可给予临时批准:6.16.2.1已明确了影响生产批准的不合格的根本原因;6.16.2.2已准备了一份包括顾客同意的临时批准计划和临时批准文件,若没能按截止日期或规定的发运量满足已同意的措施计划,则会被拒收;如果没有同意延长临时批准则不允许再发运;6.16.3拒收:提交的样品和文件不符合顾客的要求。