新产品开发试制管理规定
新品试制管理制度
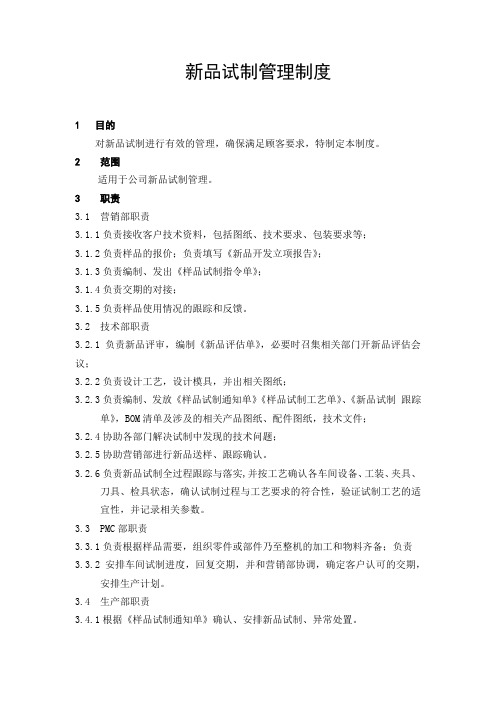
新品试制管理制度1 目的对新品试制进行有效的管理,确保满足顾客要求,特制定本制度。
2 范围适用于公司新品试制管理。
3 职责3.1 营销部职责3.1.1负责接收客户技术资料,包括图纸、技术要求、包装要求等;3.1.2负责样品的报价;负责填写《新品开发立项报告》;3.1.3负责编制、发出《样品试制指令单》;3.1.4负责交期的对接;3.1.5负责样品使用情况的跟踪和反馈。
3.2 技术部职责3.2.1负责新品评审,编制《新品评估单》,必要时召集相关部门开新品评估会议;3.2.2负责设计工艺,设计模具,并出相关图纸;3.2.3负责编制、发放《样品试制通知单》《样品试制工艺单》、《新品试制跟踪单》,BOM清单及涉及的相关产品图纸、配件图纸,技术文件;3.2.4协助各部门解决试制中发现的技术问题;3.2.5协助营销部进行新品送样、跟踪确认。
3.2.6负责新品试制全过程跟踪与落实,并按工艺确认各车间设备、工装、夹具、刀具、检具状态,确认试制过程与工艺要求的符合性,验证试制工艺的适宜性,并记录相关参数。
3.3 PMC部职责3.3.1负责根据样品需要,组织零件或部件乃至整机的加工和物料齐备;负责3.3.2安排车间试制进度,回复交期,并和营销部协调,确定客户认可的交期,安排生产计划。
3.4 生产部职责3.4.1根据《样品试制通知单》确认、安排新品试制、异常处置。
3.4.2各车间负责新品生产或模具的调试,对新品试制质量、新品试制进度负责。
3.4.3车间负责试制过程异常情况的处置和反馈,及时填写、流转《新品试制跟踪单》。
3.5品管部职责3.5.1负责新品检验计划编制,并取得客户认可;3.5.2负责相关量具定制或安排自制;3.5.2负责过程质量的监控与成品检测,出具完整的检测报告,判定样品的合格性。
4 术语和定义4.1新品4.1.1新品系开发新的产品,用于向顾客送样确认或内部试制验证的产品。
4.1.2成熟产品因图纸更改或技术状态变更,需顾客重新确认的产品。
新产品试制流程管理办法
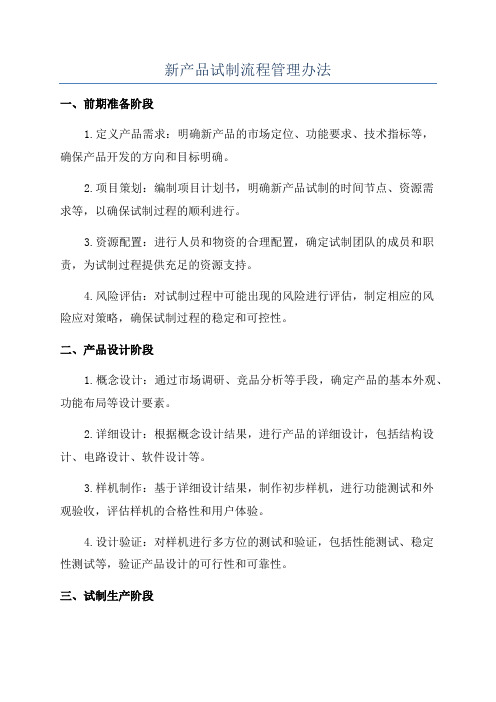
新产品试制流程管理办法一、前期准备阶段1.定义产品需求:明确新产品的市场定位、功能要求、技术指标等,确保产品开发的方向和目标明确。
2.项目策划:编制项目计划书,明确新产品试制的时间节点、资源需求等,以确保试制过程的顺利进行。
3.资源配置:进行人员和物资的合理配置,确定试制团队的成员和职责,为试制过程提供充足的资源支持。
4.风险评估:对试制过程中可能出现的风险进行评估,制定相应的风险应对策略,确保试制过程的稳定和可控性。
二、产品设计阶段1.概念设计:通过市场调研、竞品分析等手段,确定产品的基本外观、功能布局等设计要素。
2.详细设计:根据概念设计结果,进行产品的详细设计,包括结构设计、电路设计、软件设计等。
3.样机制作:基于详细设计结果,制作初步样机,进行功能测试和外观验收,评估样机的合格性和用户体验。
4.设计验证:对样机进行多方位的测试和验证,包括性能测试、稳定性测试等,验证产品设计的可行性和可靠性。
三、试制生产阶段1.试制准备:确认产品设计的最终结果,准备试制所需的物料和工艺流程,确保试制环境的良好条件。
2.试制组织:指定试制团队成员的职责和任务,确保各项工作的协调和合理分工。
3.试制工艺:按照工艺流程进行产品组装、调试、测试等工作,确保产品在试制阶段的合格率和稳定性。
4.试制跟踪:跟踪试制过程中的各项指标,包括产出率、故障率、工时等,及时调整和改进试制过程。
四、试制评估阶段1.试制结果评估:对试制完成的产品进行全面评估,包括性能评估、质量评估、成本评估等,判断试制的效果和价值。
2.试制经验总结:总结试制过程中的经验和教训,归纳并提炼出成功的试制方法和技巧,以便后续的产品开发和试制过程参考。
3.报告撰写:编写试制报告,详细记录试制过程中的各项指标和结果,为产品开发提供参考和决策的依据。
五、试制后续处理阶段1.试制优化:根据试制评估结果,对产品进行优化和改进,提高产品的性能、质量和成本效益。
2.市场推广:根据试制结果和评估报告,制定产品的市场推广策略,进行产品的市场推广和销售。
公司新品开发管理制度内容
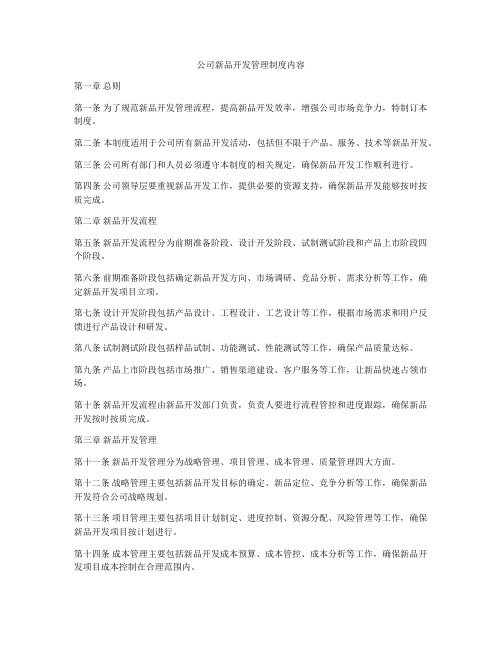
公司新品开发管理制度内容第一章总则第一条为了规范新品开发管理流程,提高新品开发效率,增强公司市场竞争力,特制订本制度。
第二条本制度适用于公司所有新品开发活动,包括但不限于产品、服务、技术等新品开发。
第三条公司所有部门和人员必须遵守本制度的相关规定,确保新品开发工作顺利进行。
第四条公司领导层要重视新品开发工作,提供必要的资源支持,确保新品开发能够按时按质完成。
第二章新品开发流程第五条新品开发流程分为前期准备阶段、设计开发阶段、试制测试阶段和产品上市阶段四个阶段。
第六条前期准备阶段包括确定新品开发方向、市场调研、竞品分析、需求分析等工作,确定新品开发项目立项。
第七条设计开发阶段包括产品设计、工程设计、工艺设计等工作,根据市场需求和用户反馈进行产品设计和研发。
第八条试制测试阶段包括样品试制、功能测试、性能测试等工作,确保产品质量达标。
第九条产品上市阶段包括市场推广、销售渠道建设、客户服务等工作,让新品快速占领市场。
第十条新品开发流程由新品开发部门负责,负责人要进行流程管控和进度跟踪,确保新品开发按时按质完成。
第三章新品开发管理第十一条新品开发管理分为战略管理、项目管理、成本管理、质量管理四大方面。
第十二条战略管理主要包括新品开发目标的确定、新品定位、竞争分析等工作,确保新品开发符合公司战略规划。
第十三条项目管理主要包括项目计划制定、进度控制、资源分配、风险管理等工作,确保新品开发项目按计划进行。
第十四条成本管理主要包括新品开发成本预算、成本管控、成本分析等工作,确保新品开发项目成本控制在合理范围内。
第十五条质量管理主要包括产品质量控制、质量检验、质量跟踪等工作,确保新品质量达标。
第四章新品开发团队第十六条新品开发团队由产品经理、技术工程师、市场营销人员、生产管理人员等组成,各自负责不同的工作。
第十七条产品经理负责新品项目的规划、管理和推动,确保新品开发按计划进行。
第十八条技术工程师负责新品的设计和研发工作,确保新品技术先进、性能稳定。
XXX公司新品试制管理办法 (一)

XXX公司新品试制管理办法 (一)
XXX公司新品试制管理办法
近年来,市场竞争愈发激烈,各种新产品层出不穷,这也促使着各大
企业在研发新品上下足功夫。
而在为市场带来更多新型商品的过程中,企业对新品进行试制几乎是不可或缺的一环。
因此,如何规范企业试
制新产品的过程便显得十分重要。
XXX公司就此制定了一部“新品试制管理办法”。
一、试制前期准备
在试制新产品之前,企业需要制定试制计划和方案,并组织专业技术
人员进行技术指导和评估。
其中,试制计划应该明确试制目的、试制
方法、时间节点以及试制后的评估标准;试制方案则应具体规定试制
的流程、试制的要求和技术标准等。
二、试制过程管理
试制过程管理主要包括原材料采购、制造、组装、调试等各个环节。
在这个过程中,企业要准确掌握试制的进度并确保每个环节的质量。
同时,要对试制过程进行记录,以便后期查找问题和改进试制流程。
三、试制结果评估
试制出来的新产品应进行全面评估,包括功能、质量、成本等各个方面。
如果试制结果不理想,企业可以找到问题并进行改进,直至新产
品达到预期效果为止。
四、试制报告撰写
当试制完成之后,需要撰写试制报告并进行分析。
报告应该包括试制的主要过程、试制结果、问题分析和梳理出后续的改进方向,为公司后续的开发提供借鉴。
通过实施新品试制管理办法,企业在试制新产品时将更加注重流程的规范性、技术的可行性和成本效益。
这样,不仅可以提升企业研发产品的一致性和稳定性,也可以更好地保证企业的竞争力和市场发展。
食品新产品试制管理制度
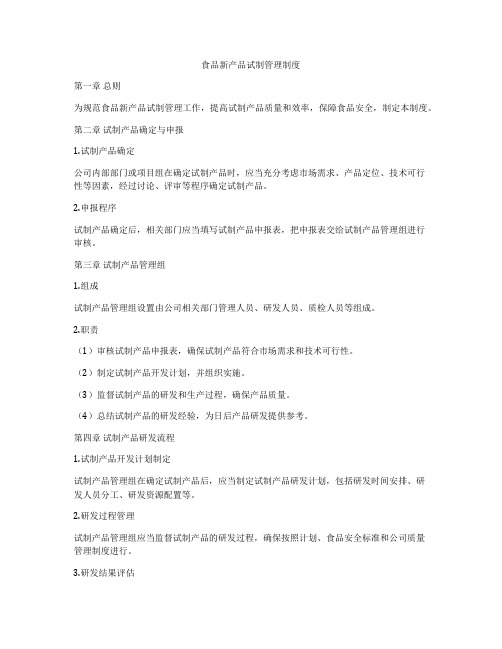
食品新产品试制管理制度第一章总则为规范食品新产品试制管理工作,提高试制产品质量和效率,保障食品安全,制定本制度。
第二章试制产品确定与申报1.试制产品确定公司内部部门或项目组在确定试制产品时,应当充分考虑市场需求、产品定位、技术可行性等因素,经过讨论、评审等程序确定试制产品。
2.申报程序试制产品确定后,相关部门应当填写试制产品申报表,把申报表交给试制产品管理组进行审核。
第三章试制产品管理组1.组成试制产品管理组设置由公司相关部门管理人员、研发人员、质检人员等组成。
2.职责(1)审核试制产品申报表,确保试制产品符合市场需求和技术可行性。
(2)制定试制产品开发计划,并组织实施。
(3)监督试制产品的研发和生产过程,确保产品质量。
(4)总结试制产品的研发经验,为日后产品研发提供参考。
第四章试制产品研发流程1.试制产品开发计划制定试制产品管理组在确定试制产品后,应当制定试制产品研发计划,包括研发时间安排、研发人员分工、研发资源配置等。
2.研发过程管理试制产品管理组应当监督试制产品的研发过程,确保按照计划、食品安全标准和公司质量管理制度进行。
3.研发结果评估试制产品研发完成后,相关部门应当进行研发结果评估,包括产品质量、安全性、市场适应度等。
第五章试制产品生产制造1.生产设备及人员准备试制产品生产前,生产部门应当准备好生产设备和生产人员,并确保生产环境符合食品安全和生产标准。
2.生产过程监督生产过程中,生产部门应当根据试制产品生产标准和质量要求进行生产,并及时记录生产过程中出现的问题。
3.质检验收生产完成后,质检部门应当对产品进行严格的质检验收,确保产品符合食品安全和质量要求。
第六章试制产品品质追踪1.品质跟踪过程试制产品完成生产后,质检部门应当对产品进行品质跟踪,包括产品保存期限、产品存储条件、产品质量变化等情况进行跟踪。
2.品质问题处理对于发现的产品品质问题,应当建立健全的处理流程,及时处理并进行问题分析,确保类似问题不再出现。
新产品开发与试制管理办法
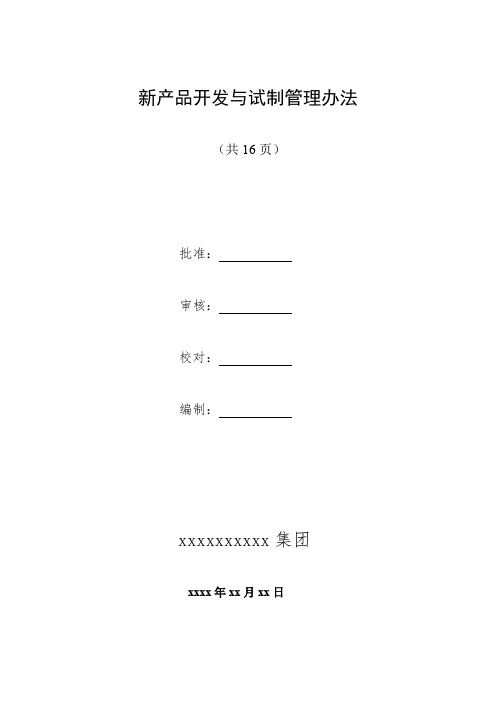
新产品开发与试制管理办法(共16页)批准:审核:校对:编制:xxxxxxxxxx集团xxxx年xx月xx日一、总则1、为使新产品从构思提出到产品试制整个过程的工作有序高效地进行,以保证设计及设计转化的质量,达到新产品的各项性能满足顾客或设计要求,特制定本办法。
2、本办法适用于新产品开发及试制的全过程控制,非标设备及大型专用工装的设计与试制也可参照本办法执行。
但根据设计开发的输入和新产品的复杂程度等的情况,产品开发的程序可适当剪裁,但剪裁必须满足不影响新产品设计开发整个过程的控制且不影响产品的功能、性能及外观。
3、本办法由集团总工程师批准后施行。
二、参考文件科研项目(课题)立项与实施管理办法(试行)三、定义1、新产品:是指在性能、结构、材质或原理等一方面或几方面有重大改进及技术上有突破的产品,2、产品开发:指企业通过对新产品的研制,以扩大和完善产品品种的一系列复杂的系统工作。
四、职责1、市场部门:负责新产品市场需求信息的收集、调研与预测。
2、技术部门:负责新产品设计、提供相关图纸及技术资料;编制新产品试制工艺规范和试制工艺总方案;负责新产品工装夹具、专用工具的设计;负责新产品的样件试验;解决新产品试制中的技术问题。
3、质检部门:负责编制新产品检验作业指导书、新产品试制品质的控制(含原材料、标准件及外购件)。
4、生产部门:负责新产品试制并将试制过程中发现的设计或工艺问题按相关程序及时反馈给技术部门。
5、采购等其他部门:按相关技术要求和材料定额及标准件清单采购,提供必要的配合工作,确保新产品开发及试制工作顺利进行。
五、新产品开发程序1、产品立项1.1市场部门根据客户需求信息、市场调研与预测或产品开发人员根据集团发展战略自主创新提出新产品开发建议,形成《新产品开发项目建议书》(见附件1),经单位(部门)领导审核后报送技术中心科技管理部门。
1.2科技管理部门根据集团发展规划和市场需求情况对所报《新产品开发项目建议书》组织人员进行平衡筛选,筛选结果经技术中心主任审定后形成《项目开题报告》与《项目计划任务书》。
新产品开发管理规定

新产品开发管理规定制度名称:新产品开发管理制度第1章总则第1条目的。
为了加快产品更新换代的速度,推动企业技术进步,加强新产品开发管理工作,特制定本制度。
第2条新产品定义。
本制度所称的新产品是指在结构、材质、工艺等方面比老产品有明显改进,显著提高了产品的性能或扩大了产品使用功能以及采用新技术原理、新设计构思的产品。
第3条新产品开发遵循的原则。
1.新产品要具有先进性、适用性、适销对路等潜在的经济效益和社会效益。
2.新产品要符合产业、产品结构调整方向,以及国家技术政策和技术装备政策要求3.新产品的设计要标准化。
第2章管理职责第4条组织管理。
为了加速企业的新产品开发,有效地进行系统管理,本企业特成立新产品开发委员会。
新产品开发委员会由主任委员、执行秘书及委员构成。
第5条委员人选。
主任委员由主管副总经理担任,执行秘书由行政部经理担任,其他委员依个案性质不同,由主任委员指派公司内现有人员担任。
第6条委员职责。
1.主任委员。
1、负责新产品开发工作事宜。
2、负责召开并主持新产品开发会议。
3、负责指派其他委员。
4、负责拟定及呈报新产品全部投资及利润分析方案。
2.执行秘书。
1、负责拟定开发时间规划和产品开发计划。
2、协助主任委员从事开发会议联络及记录。
3、协助主任委员追踪新产品开发工作。
4、负责提供新产品开发所需材料及物品。
3.销售管理委员。
1、负责有关市场调查。
2、提出产品现有生产厂家及市场信息。
3、提出新产品未来市场需求潜力报告。
4、根据市场调查资料及成本分析资料,拟定销售价格,分析销售渠道及销售预测。
5、编制企划、广告费用预算。
4.生产技术委员。
1、负责提供与新产品有关的设备、原物料。
2、负责新产品试制及生产包装设计技术问题。
3、负责新产品样品试验及品质检查。
4、提出新产品相关成本分析及生产能量、设备投资资料。
5.税务委员。
1、提供新产品在税务上的有关资料,包括以下几个方面。
2、是否属奖励投资项目。
3、营利事业所得税最低百分率。
新产品研发试制管理规定
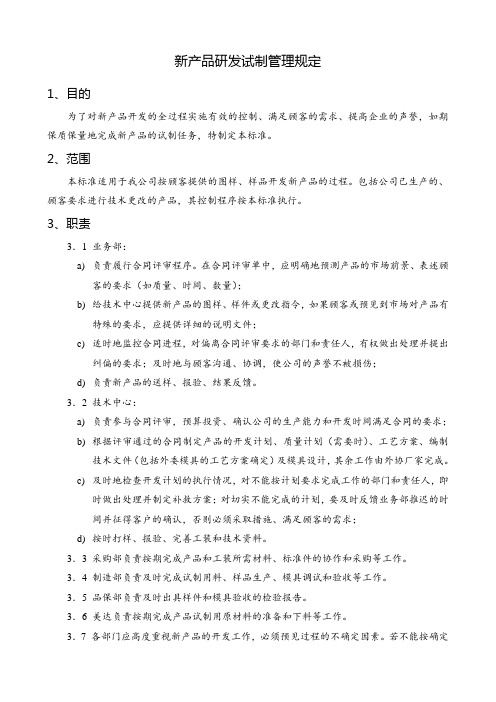
新产品研发试制管理规定1、目的为了对新产品开发的全过程实施有效的控制、满足顾客的需求、提高企业的声誉,如期保质保量地完成新产品的试制任务,特制定本标准。
2、范围本标准适用于我公司按顾客提供的图样、样品开发新产品的过程。
包括公司已生产的、顾客要求进行技术更改的产品,其控制程序按本标准执行。
3、职责3.1 业务部:a)负责履行合同评审程序。
在合同评审单中,应明确地预测产品的市场前景、表述顾客的要求(如质量、时间、数量);b)给技术中心提供新产品的图样、样件或更改指令,如果顾客或预见到市场对产品有特殊的要求,应提供详细的说明文件;c)适时地监控合同进程,对偏离合同评审要求的部门和责任人,有权做出处理并提出纠偏的要求;及时地与顾客沟通、协调,使公司的声誉不被损伤;d)负责新产品的送样、报验、结果反馈。
3.2 技术中心:a)负责参与合同评审,预算投资、确认公司的生产能力和开发时间满足合同的要求;b)根据评审通过的合同制定产品的开发计划、质量计划(需要时)、工艺方案、编制技术文件(包括外委模具的工艺方案确定)及模具设计,其余工作由外协厂家完成。
c)及时地检查开发计划的执行情况,对不能按计划要求完成工作的部门和责任人,即时做出处理并制定补救方案;对切实不能完成的计划,要及时反馈业务部推迟的时间并征得客户的确认,否则必须采取措施、满足顾客的需求;d)按时打样、报验、完善工装和技术资料。
3.3 采购部负责按期完成产品和工装所需材料、标准件的协作和采购等工作。
3.4 制造部负责及时完成试制用料、样品生产、模具调试和验收等工作。
3.5 品保部负责及时出具样件和模具验收的检验报告。
3.6 美达负责按期完成产品试制用原材料的准备和下料等工作。
3.7 各部门应高度重视新产品的开发工作,必须预见过程的不确定因素。
若不能按确定的时间完成的工作均应至少提前三天书面反馈原因,否则承担因此而带来的任何不良结果。
4、定义5、程序5.1 新产品开发工作流程图:业务部负责提供产品图样、样件及合同评审单技术中心负责技术经理或技术中心主任外协单位或技术中心负责外协单位或模具车间负责,采购部负责标准件和材料模具车间负责、制造部协同完成模具车间 、技术中心检查各项工作是否已完成技术下发样件通知单、制造部组织完成、品保部业务部负责 模具、技术、品保、制造部验收模具模具车间负责日常管理和维护5.2业务部负责把通过合同评审的各项要求和图样等资料提供给技术中心。
ISO9001新产品试制试产管理办法
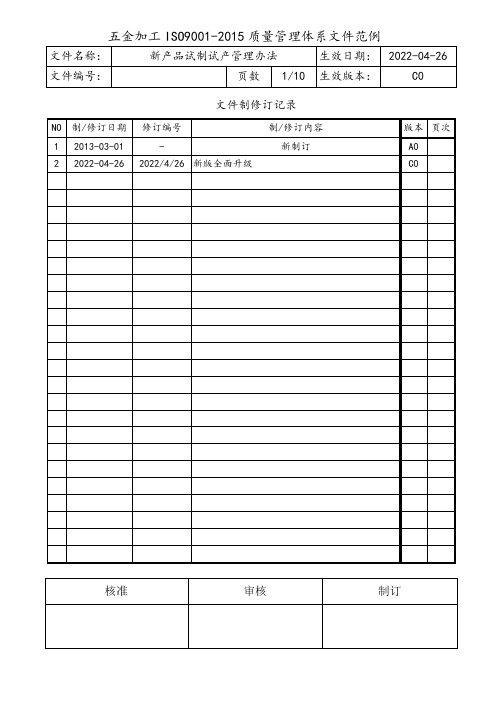
文件制修订记录1.0目的本标准规定了新产品试制试产以及产品重大设计更改试制试产或产品改进试产全过程的管理要求。
2.0范围公司产品。
3.0职责3.1技术部负责从样品试制、试产到试产小结全过程的组织和跟进。
3.2制造部负责安排新产品上线试制试产,负责新产品工艺性审查和生产组织评价。
3.3品质部负责新产品测试评价和供方物料质量评价。
3.4营业部负责评价新产品是否满足顾客要求,采购组织是否有保障。
4.0程序4.1定义4.1.1试制新产品开发在完成了技术设计,编制了必要的技术文件(如总明细表、图纸等)以后主要为验证设计而进行的样品生产活动;或技术部门对产品进行了重大设计更改,主要为验证设计更改是否达到预期目标而进行的样品生产活动。
4.1.2试产新产品投入批量生产前,主要为验证生产工艺(包括工艺方案、工艺流程、操作方法、特殊工艺检测手段和控制方式、生产组织、物料供应等)能否适应大批量稳定生产合格品要求而进行的生产活动;或技术部对产品进行了重大设计更改、对产品进行改进采用新材料、新工艺、新部件后,为验证能否适应大批量稳定生产合格品需求而进行的样品生产活动。
4.1.3投产鉴定即技术部将新产品向制造部移交前的设计最终确认,审查产品结构、性能、工艺性、安全性、可靠性、成本等是否满足设计任务书或顾客要求;审查各种技术文件、工装设备、工程数据、生产组织、物料质量控制等能否满足批量生产的要求,确定新产品是否能向制造部移交,确定是否进入批量生产。
4.2新产品试制。
4.2.1试制申请。
4.2.1.1技术部根据相关要求和项目开发进度编制“试制试产申请表”,经技术部经理审核、制造部会签后发制造部。
4.2.1.2试制申请在考虑物料采购周期的前提下要明确注明计划上线试制时间、样品规格、试制数量和专用物料到位时间等。
4.2.1.3 如由于某种特殊原因要中途更改试制的规格或数量,技术部需重新下发“试制试产申请表”,而上线试制时间则按期顺延。
新产品试制流程管理办法
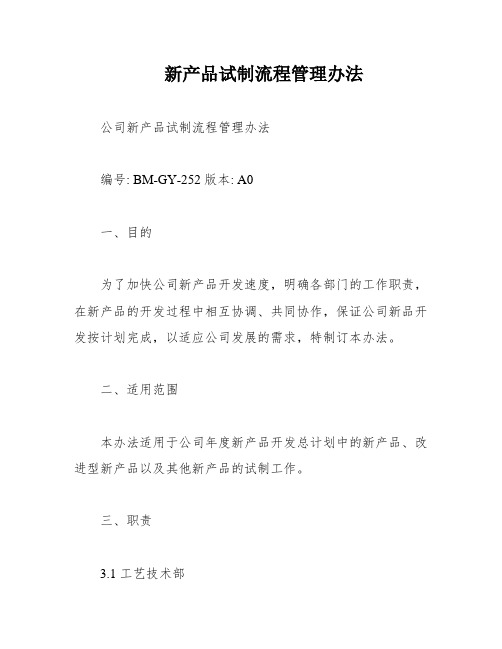
新产品试制流程管理办法公司新产品试制流程管理办法编号: BM-GY-252 版本: A0一、目的为了加快公司新产品开发速度,明确各部门的工作职责,在新产品的开发过程中相互协调、共同协作,保证公司新品开发按计划完成,以适应公司发展的需求,特制订本办法。
二、适用范围本办法适用于公司年度新产品开发总计划中的新产品、改进型新产品以及其他新产品的试制工作。
三、职责3.1 工艺技术部3.1.1 技术部是公司新产品设计、开发、试制等工作的责任部门,负责统筹、监督和管理新产品的设计和开发、试制工作。
对设计的正确性、设计控制的有效性以及工艺的执行情况进行监督、考核。
3.1.2 工艺技术部在试制图纸下发后负责新产品试制的工艺方案、作业指导书、工装设计、试制计划等工艺文件及生产技术准备工作。
3.1.3 工艺技术部跟踪试制过程中关键零部件的自制加工、关键外协件的加工及整机的装配,并针对试制过程中出现的问题进行汇总,然后与设计人员进行沟通,避免再次试制时类似问题的出现。
3.1.4 工艺技术部负责样机的测试,并记录整理试验数据存档。
3.2 生产部3.2.1 生产部根据试制图纸合理安排相关零部件的采购,保证新产品外购物料按时回厂并对外购物料的质量负责。
3.2.2 生产部根据样机试制计划编制样机生产计划、工装模具制造计划,合理安排相关人员,保证样机在规定时间内完成。
3.2.3 生产部按计划在规定时间内将样机装配完成。
3.3 质检部3.3.1 负责新产品外购件、自制件及外协件的检验工作,对于试验和检验中存在的问题应及时与技术部沟通解决。
3.3.2 零部件在检验合格装配前,质检部需安排人员对所有零部件再次检查确认。
3.4 库房库房负责对所有合格入库的试制零部件、外购件等进行保管,并按照物料明细进行物料发放,确保整机装配的顺利进行。
四、工作要求及考核1.在新产品试制过程中,工艺部要作好相关的技术服务工作,及时处理试制中的技术问题,对于重大技术质量问题,要分析出产生的原因,并写出处理报告。
新产品开发管理办法
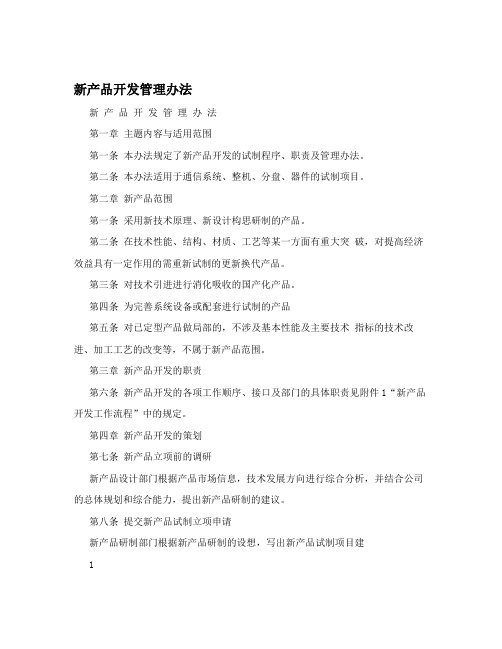
新产品开发管理办法新产品开发管理办法第一章主题内容与适用范围第一条本办法规定了新产品开发的试制程序、职责及管理办法。
第二条本办法适用于通信系统、整机、分盘、器件的试制项目。
第二章新产品范围第一条采用新技术原理、新设计构思研制的产品。
第二条在技术性能、结构、材质、工艺等某一方面有重大突破,对提高经济效益具有一定作用的需重新试制的更新换代产品。
第三条对技术引进进行消化吸收的国产化产品。
第四条为完善系统设备或配套进行试制的产品第五条对已定型产品做局部的,不涉及基本性能及主要技术指标的技术改进、加工工艺的改变等,不属于新产品范围。
第三章新产品开发的职责第六条新产品开发的各项工作顺序、接口及部门的具体职责见附件1“新产品开发工作流程”中的规定。
第四章新产品开发的策划第七条新产品立项前的调研新产品设计部门根据产品市场信息,技术发展方向进行综合分析,并结合公司的总体规划和综合能力,提出新产品研制的建议。
第八条提交新产品试制立项申请新产品研制部门根据新产品研制的设想,写出新产品试制项目建1议书。
建议书的首页格式见附表1,建议书的续页为A4打印纸,建议书内容主要应包括:1. 新产品的技术发展前景及可行性分析;2. 产品的市场前景;3. 初步的技术方案;4. 产品的经济效益分析;5. 项目经费的估算;6. 资源(人力、设备、环境)的基本要求;7. 完成的时间。
建议书交试制部门的主管领导。
经试制部门汇总后交上级主管部门。
第九条新产品试制项目建议书的评审根据项目建议书的内容,上级主管部门召集由专业人员组成的评审组对试制建议书进行评审。
评审的内容主要为:建议的理论依据是否充分、项目试制的可实行程度、是否符合公司近期或中长期规划、项目立项申请可否继续进行的建议。
评审结束后出具书面的评审报告交公司的总工程师,总工将报告连同项目建议书报厂务会。
评审报告格式见附表2,报告内容行文A4打印纸。
第十条新产品试制项目建议书的批准经公司办公例会研究后批准的项目建议书,由试制管理部门拟制,总工程师批准下达新产品试制任务通知书到新产品开发的建议部门(新产品试制任务通知书的格式可以采用行文方式)。
新产品开发管理制度

新产品开发管理制度一、总则为促进公司产品技术水平的提高,满足客户需求,实现公司以市场为中心的经营方针,特制定本制度。
本规定规范了公司的新产品开发分类、新产品开发立项、新产品开发试制的工作。
本规定适用于本公司新产品开发工作涉及的所有部门、员工。
二、公司的新产品开发分类:1、是自主产品开发,主要由公司根据市场调研、自主进行的开发2、是根据客户(包括集团各子分公司)需求进行的产品开发。
三、新产品开发立项:1、自主产品开发立项技术研发部搜集并分析本行业国内外新产品信息和市场需求信息,结合公司生产经营现状,拟订新产品自主开发方案。
新产品开发方案由提案人提交技术研发部,由技术研发部初审后上报公司。
2、根据客户需求进行的产品开发立项生产相关部门分析客户的新产品需求,并将客户需求及时传达给技术研发部。
技术研发部进一步分析客户需求,同时和客户沟通,明确客户真实需求。
技术研发部根据客户要求以及产品复杂程度设计方案,并与客户沟通确认。
技术研发部产品根据客户要求设计新产品图纸、模具、工艺,并与客户沟通确认。
同时初步测算开发成本,并将相关测算信息交经营部门计算产品价格。
经营部和客户就新产品报价与客户进一步沟通,并最终得到客户的确认。
客户确认后,由经营部添写研发项目立项表。
3、公司分管副总对新产品开发方案进行审核,同时参考相关部门对新产品开发立项的意见。
审核后报总经理批准。
总经理批准后,技术研发部根据新产品开发方案编制新产品试制文件。
四、新产品的开发试制工作程序:1、技术研发部根据新产品试制任务书进行产品图纸设计。
2、进行工艺流程的编制。
3、制定材料配件采购计划:本着经济可靠,保证产品质量要求的原则,充分利用现有的材料和配件。
4、安排样件试制任务,样件的修改确认,产品最终定型。
5、产品试制结束后,技术研发部将新产品开发的相关技术资料分类归档,并编制详细技术图纸和工艺文件,并存档。
新产品试制与鉴定管理规定
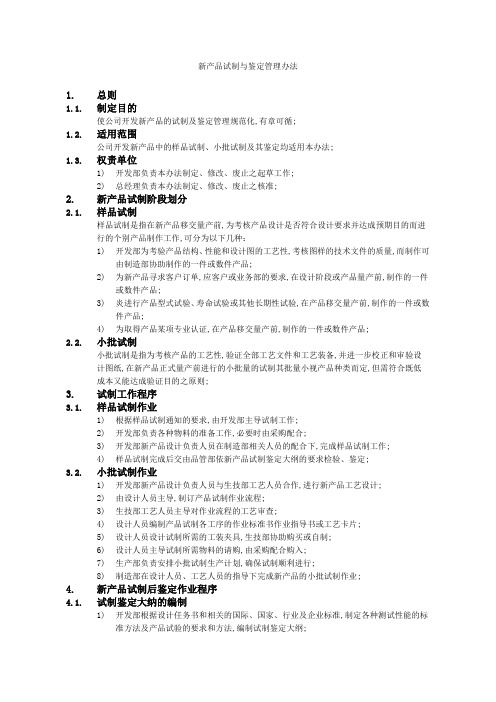
新产品试制与鉴定管理办法1.总则1.1.制定目的使公司开发新产品的试制及鉴定管理规范化,有章可循;1.2.适用范围公司开发新产品中的样品试制、小批试制及其鉴定均适用本办法;1.3.权责单位1)开发部负责本办法制定、修改、废止之起草工作;2)总经理负责本办法制定、修改、废止之核准;2.新产品试制阶段划分2.1.样品试制样品试制是指在新产品移交量产前,为考核产品设计是否符合设计要求并达成预期目的而进行的个别产品制作工作,可分为以下几种:1)开发部为考验产品结构、性能和设计图的工艺性,考核图样的技术文件的质量,而制作可由制造部协助制作的一件或数件产品;2)为新产品寻求客户订单,应客户或业务部的要求,在设计阶段或产品量产前,制作的一件或数件产品;3)炎进行产品型式试验、寿命试验或其他长期性试验,在产品移交量产前,制作的一件或数件产品;4)为取得产品某项专业认证,在产品移交量产前,制作的一件或数件产品;2.2.小批试制小批试制是指为考核产品的工艺性,验证全部工艺文件和工艺装备,并进一步校正和审验设计图纸,在新产品正式量产前进行的小批量的试制其批量小视产品种类而定,但需符合既低成本又能达成验证目的之原则;3.试制工作程序3.1.样品试制作业1)根据样品试制通知的要求,由开发部主导试制工作;2)开发部负责各种物料的准备工作,必要时由采购配合;3)开发部新产品设计负责人员在制造部相关人员的配合下,完成样品试制工作;4)样品试制完成后交由品管部依新产品试制鉴定大纲的要求检验、鉴定;3.2.小批试制作业1)开发部新产品设计负责人员与生技部工艺人员合作,进行新产品工艺设计;2)由设计人员主导,制订产品试制作业流程;3)生技部工艺人员主导对作业流程的工艺审查;4)设计人员编制产品试制各工序的作业标准书作业指导书或工艺卡片;5)设计人员设计试制所需的工装夹具,生技部协助购买或自制;6)设计人员主导试制所需物料的请购,由采购配合购入;7)生产部负责安排小批试制生产计划,确保试制顺利进行;8)制造部在设计人员、工艺人员的指导下完成新产品的小批试制作业;4.新产品试制后鉴定作业程序4.1.试制鉴定大纳的编制1)开发部根据设计任务书和相关的国际、国家、行业及企业标准,制定各种测试性能的标准方法及产品试验的要求和方法,编制试制鉴定大纲;2)试制鉴定大纲应提出工艺、工装、设备、检测手段等与生产要求、品质保证及成本、安全、环保等相适应的要求;3)品管部对试制鉴定大纲进行审核,并依品质管理相关规范进行必要的修改、补充;4)试制鉴定大纲经技术副总经理或总工程师核准后生效;4.2.样品鉴定作业由开发部、品管部对样品进行鉴定;1)开发部自行审核设计图样的合理性、工艺性;2)品管部依检验规范鉴定样品之合格性;3)品管部审查新产品设计结构之合理性;4)开发部、品管部明确样品应改进的事项,并评价是否可投入小批试制;5)技术副总经理或总工程师对鉴定最后结论作核示;4.3.小批试制鉴定作业1)开发部审核设计图样的合理、工艺性;2)生技部审核产品生产工艺、工装夹具、各种技术资料的完备与可靠程度;3)采购部审核物料供应、外购外协件定点定型情况;4)制造部审核产品生产工艺之合理性、可靠性;5)品管部审核产品之合理性,测试设备之合理性、可靠性;6)各部门提出产品制造应改进的事项确定产品是否可投入批量生产;7)技术副总经理或总工程师对鉴定最后结论作核示;4.4.设计整改作业试制鉴定过程发现的设计问题点,由开发部负责作整改工作;新产品试制鉴定表。
新产品开发试制管理规定
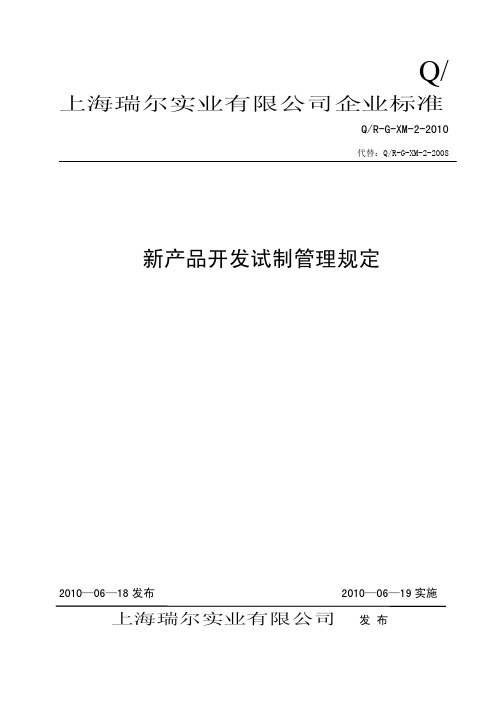
Q/ 上海瑞尔实业有限公司企业标准Q/R-G-XM-2-2010代替:Q/R-G-XM-2-2008 新产品开发试制管理规定2010—06—18发布 2010—06—19实施上海瑞尔实业有限公司发布Q/R-G-XM-2-2010前 言本标准系参照Q/R-G-XM-2-2008《新产品试制管理规定》和Q/R-G-GC-8-2010《产品质量先期策划程序》等标准进行编制,并代替Q/R-G-XM-2-2008《新产品试制管理规定》。
本标准由上海瑞尔实业有限公司提出。
本标准由上海瑞尔实业有限公司标准化科归口。
本标准起草单位:上海瑞尔实业有限公司项目部。
本标准主要起草人:王前明、李玲章。
本标准于2010年2月第一次修订。
ⅠQ/R-G-XM-2-2010新产品开发试制管理规定1 范围本标准规定了上海瑞尔实业有限公司(以下简称本公司)新产品开发试制过程中的职责与权限、管理内容、奖惩、成本控制、考核规定等。
本标准适用于本公司新产品开发项目。
2 规范性引用文件下列文件对于本文件的应用是必不可少的,凡是注日期的引用文件,仅注日期的版本适用于本文件。
凡是不注日期的引用文件,其最新版本(包括所有的修改单)适用于本文件。
Q/R-G-CG-12 仓库管理程序Q/R-G-GC-8 产品质量先期策划(APQP)程序Q/R-G-GC-12新产品技术开发事故处理办法Q/R-G-MJ-2工装、模具、夹具、检具管理程序Q/R-G-RS-15奖惩制度Q/R-G-XM-5 项目管理程序Q/R-G-ZB-25 新产品送样流程管理规定3 职责3.1各部门相关岗位职责按照图1、图2和图3。
3.2按照Q/R-G-XM-5《项目管理程序》中规定的职责。
3.3按照Q/R-G-GC-8《产品质量先期策划(APQP)程序》中规定的职责。
3.4 在2TP前有订单交货要求时由项目组负责组织实施。
4 流程4.1 S4-1试制流程见图1。
4.2 S4-2 初期小批量试制流程见图2。
新产品试产管理规范

实用文档1.0目的:1.1 验证当前阶段的产品整机及其零配件的各项性能能否达到设计意图要求;1.2 尽可能地将新产品尚还存在的问题在批量生产前充分暴露出来,为后续问题点改善创造更加适宜的条件,为促成新产品顺利量产提前做好各项充分准备工作;1.3明确新产品试产所涉及到各环节的工作任务和职责,确保试产工作顺畅开展。
2.0适用范围:2.1 适用于公司产品的各个新项目在投入量产前的每一次试生产。
包括全新产品的试产、关键零配件在功能或装配配合上有较大变动的老产品的例行试产。
试产的对象可以是产品的功能、试装配配合或加工工艺等。
2.2 客户提出的其它的需要进行试产的情况;3.0定义3.1样品试制:开发阶段中首次样板的试制,在于验证新品设计的完善性。
(一般由研发部内部样板组完成)3.2小批量试产:开发阶段中样板试制成功后的小批量试产,尽可能地模拟批量生产状态,验证工艺、产品整机等能力。
(小批量试产装配必须在生产车间完成。
)3.0主要职责3.1研发部:负责新产品的开发、相关技术资料制定和发布受控、样品鉴定和评审会组织、设计问题的改进、主导推进试产的进行;同时处理试产中的异常状况,主导产前会议和试产后总结报告会议召开。
a项目工程师:负责新产品工程技术图纸的制作、零部件及整机确认样的确认、零部件测试评估记录、组织召开试产前培训会以及完成试产所需的其它准备工作;解决试产过程中的异常问题,主导试产后的总结评审会议和改善工作;b.工艺工程师负责:新产品作业指导书制作,标准工时的制订,并在试产时与生产部门安排工艺流程;试产过程中问题的总结;负责试产过程中工装夹具的策划及制作、与品质部沟通策划并制作产品零部件检具量具。
协助解决试产过程中的异常问题,配合项目工程师负责人完成试产报告和后续改善。
c.实验室:完成试产前以及试产后的相关样品测试;d.样板组:协助项目工程师完成试产前样板的组装;实用文档3.2品质部:负责新产品试产全过程的质量跟踪监控。
产品研发与试制管理制度
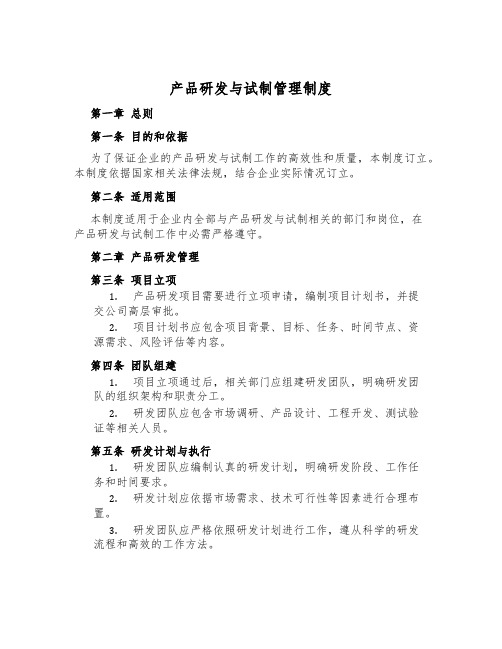
产品研发与试制管理制度第一章总则第一条目的和依据为了保证企业的产品研发与试制工作的高效性和质量,本制度订立。
本制度依据国家相关法律法规,结合企业实际情况订立。
第二条适用范围本制度适用于企业内全部与产品研发与试制相关的部门和岗位,在产品研发与试制工作中必需严格遵守。
第二章产品研发管理第三条项目立项1.产品研发项目需要进行立项申请,编制项目计划书,并提交公司高层审批。
2.项目计划书应包含项目背景、目标、任务、时间节点、资源需求、风险评估等内容。
第四条团队组建1.项目立项通过后,相关部门应组建研发团队,明确研发团队的组织架构和职责分工。
2.研发团队应包含市场调研、产品设计、工程开发、测试验证等相关人员。
第五条研发计划与执行1.研发团队应编制认真的研发计划,明确研发阶段、工作任务和时间要求。
2.研发计划应依据市场需求、技术可行性等因素进行合理布置。
3.研发团队应严格依照研发计划进行工作,遵从科学的研发流程和高效的工作方法。
第六条技术保障1.研发过程中需要有技术保障的支持。
技术保障团队负责解决研发过程中的技术难题和技术支持。
2.技术保障团队应定期与研发团队进行沟通和协作,确保技术支持的及时性和有效性。
第七条产品测试与验证1.研发团队在完成产品设计后,需要进行相应的测试与验证工作,确保产品的质量和性能实现预期要求。
2.测试与验证工作应遵从相应的流程和标准,对产品功能、安全性、稳定性、可靠性等进行全面检测。
第三章试制管理第八条试制前准备1.试制前需要明确试制的目标、任务和时间节点。
试制计划应与产品研发计划紧密衔接。
2.公司相关部门应对试制所需的资源进行调配,确保试制工作的顺利进行。
第九条试制过程掌控1.试制过程中,应设立试制团队,明确各成员的职责和任务。
2.试制团队应依照试制计划进行工作,并对试制过程进行严格掌控和管理。
第十条试制结果评估1.试制完成后,试制团队需要对试制结果进行评估和分析,确保试制目标的实现。
- 1、下载文档前请自行甄别文档内容的完整性,平台不提供额外的编辑、内容补充、找答案等附加服务。
- 2、"仅部分预览"的文档,不可在线预览部分如存在完整性等问题,可反馈申请退款(可完整预览的文档不适用该条件!)。
- 3、如文档侵犯您的权益,请联系客服反馈,我们会尽快为您处理(人工客服工作时间:9:00-18:30)。
Q/ 上海瑞尔实业有限公司企业标准
Q/R-G-XM-2-2010
代替:Q/R-G-XM-2-2008 新产品开发试制管理规定
2010—06—18发布 2010—06—19实施上海瑞尔实业有限公司发布
Q/R-G-XM-2-2010
前 言
本标准系参照Q/R-G-XM-2-2008《新产品试制管理规定》和Q/R-G-GC-8-2010《产品质量先期策划程序》等标准进行编制,并代替Q/R-G-XM-2-2008《新产品试制管理规定》。
本标准由上海瑞尔实业有限公司提出。
本标准由上海瑞尔实业有限公司标准化科归口。
本标准起草单位:上海瑞尔实业有限公司项目部。
本标准主要起草人:王前明、李玲章。
本标准于2010年2月第一次修订。
Ⅰ
Q/R-G-XM-2-2010
新产品开发试制管理规定
1 范围
本标准规定了上海瑞尔实业有限公司(以下简称本公司)新产品开发试制过程中的职责与权限、管理内容、奖惩、成本控制、考核规定等。
本标准适用于本公司新产品开发项目。
2 规范性引用文件
下列文件对于本文件的应用是必不可少的,凡是注日期的引用文件,仅注日期的版本适用于本文件。
凡是不注日期的引用文件,其最新版本(包括所有的修改单)适用于本文件。
Q/R-G-CG-12 仓库管理程序
Q/R-G-GC-8 产品质量先期策划(APQP)程序
Q/R-G-GC-12新产品技术开发事故处理办法
Q/R-G-MJ-2工装、模具、夹具、检具管理程序
Q/R-G-RS-15奖惩制度
Q/R-G-XM-5 项目管理程序
Q/R-G-ZB-25 新产品送样流程管理规定
3 职责
3.1各部门相关岗位职责按照图1、图2和图3。
3.2按照Q/R-G-XM-5《项目管理程序》中规定的职责。
3.3按照Q/R-G-GC-8《产品质量先期策划(APQP)程序》中规定的职责。
3.4 在2TP前有订单交货要求时由项目组负责组织实施。
4 流程
4.1 S4-1试制流程见图1。
4.2 S4-2 初期小批量试制流程见图2。
4.3产品送样流程见图3。
5 内容要求
5.1当量试阶段评审通过时,应进行批产移交申请,经相关部门会签,总工程师批准(包括带条件通过)后,该项目进入批产状态。
对于待条件通过的条件事项应指定责任人先期解决。
5.2整体开发阶段的费用、成本管理和项目考核办法根据Q/R-G-XM-5《项目管理程序》中关于新产品开发项目的成本、费用管理规定和项目考核规定执行。
5.3 在S1(产品设计开发阶段)
5.3.1通过评审的数据应分开保存,且文件名称应注明年月日。
1
Q/R-G-XM-2-2010
5.3.2 工程图纸应会签受控下发,会签的顺序应为CAD工程师、CAD主管、产品工程师、部门主管、部门标准化员、部门经理。
5.4 在S4-1(试制阶段)
5.4.1 物料准备阶段
5.4.1.1技术部门提出物料、外协购物件需求,并控制生产进度和跟踪交货情况。
5.4.1.2用料与批产产品相同的原材料,各技术部门每月20日前根据各试制项目编制下月试制物料需求计划,经部门经理审核后分发到物料计划员,物料计划员据此编制物料需求计划。
5.4.1.3对于新材料,产品工程师负责根据实际需求提交物料需求报告单给采购部,由采购部跟踪外协外购件的到货情况。
5.4.1.4新产品开发原材料采购后按Q/R-G-CG-12《仓库管理程序》中的有关规定办理入库手续。
5.4.2 物料领料阶段
5.4.2.1技术部门填写领料单时应注明所用的项目编号、名称等信息,并经台帐管理人员在台账上登记签名后,主管方可审查签字。
领料量必须在其物料需求计划量内,超过需求计划时,项目负责人应做出说明,并进行后续的工作安排。
5.4.2.2 车间物料员依据领料单配合领料。
5.4.2.3 仓管员依据符合5.4.2.1项要求的领料单进行发料。
5.4.3 试制要求
5.4.3.1模具制作完成后应进行验证试模,由模具中心主导,参照《工装、模具、夹具、检具管理程序》进行。
要求验证试模次数控制在3次以内,当模具问题全部得以解决时方可转交生产单位进行产品试制,否则仍由模具中心负责进行验证试模,发生的成本计入模具中心,直至模具问题全部得以解决。
5.4.3.2试制(试模)申请单应经部门二级主管或以上领导审核、批准,并应经过项目经理会签。
5.4.3.3对跨厂区的新产品开发项目,试制申请单由各厂区技术部门项目负责人(产品工程师)编制。
5.4.3.4大于两次的试制,在提交“试制(试模)申请单”时应附上前2次试制完成后的《试制报告单》。
5.4.3.5试制应安排在白班,生产车间应规划开发试制件放置区域并做好试制产品的状态标识。
5.4.3.6产品工程师应主导试制全过程,开发质量工程师、模具工程师等其他相关被指定人员应参与试制全过程,记录相关问题,并提出解决方案。
5.4.3.7 试制总结应详细记录试制中出现的问题及解决措施。
5.4.3.8工时定额及物料的核定应有制造部参与,试制工时包括上模、卸模、准备工时、调试工时、生产工时。
试制生产工时无法准确核定时可参照批产同类产品的生产工时,一般为批产产品的1.5-2倍,并由项目负责人和生产部门项目小组成员核定,并记入试制人员的业绩考核及新产品开发成本。
5.4.3.9试制剩余物料的处理:在项目开发结束进入批产后,技术部门应配合仓库对剩余物料进行处理,可以批产使用的物料,办理账务转移手续。
对于不能使用的物料,办理出库手续,仓库按“废料”报废程序处理,在出库单上由技术部门确认签字,并注明项目编号、名称,交项目经理计入开发费用。
5.4.3.10试制数量的规定见表1。
5.4.3.11试制产品(包含样品库内外的样品)及废品的管理:试制完毕后产品工程师应处理所产生的产品及余料,废品处理应该经产品工程师及开发质量工程师签字确认后由车间试制人员作报废处理,相关费用计入开发成本。
2
Q/R-G-XM-2-2010 5.4.4 试制工时的规定
5.4.4.1 试制申请时应预测该次试制所需的各工序工时,项目经理在会签申请单时应与预算进行核对,对超出部门应进行讨论确定。
5.4.4.2 试制完毕后产品工程师应向项目经理提交该次试制发生的实际工时,对超出部门也应进行讨论确定。
表1 试制类别、次数
5.5 S4-2(量试阶段)
5.5.1 PPAP和2TP工作流程按照Q/R-G-GC-8《产品质量先期策划程序》中的流程。
5.5.2初期小批量试制及2TP的进行由技术部门负责,运作模式参照批产模式进行,制造部负责物料、外协购物件的需求提出,并跟踪到货,控制生产进度和交货情况。
5.5.3在量试过程中发现异常情况时,生产部门应配合产品工程师记录量试的生产记录、数据、异常情况,并配合解决,产品工程师主导对策问题,须召集相关人员讨论。
5.5.4客户有订单下发,量试阶段的产品可依正常的生产管理程序进行出货,初期小批量试制可以在无订单的情况下进行,但较大数量的量试(如2TP或其他状况)则应在接到客户订单的前提下进行。
5.5.5量试产品(包含样品库内外的样品)及废品的管理:量试完毕后产品工程师应处理所产生的产品及余料:对于无订单的产品、余料参照5.4.3.9进行,对于有订单的量试产品、余料参照批产件进行处理。
5.6 移交
3
Q/R-G-XM-2-2010
在试制开始后的各阶段技术部门须将相应的软件、硬件向对应的使用单位进行移交,前提为被移交的软件、硬件已通过试用合格。
在批产申请(2TP)通过后一周内技术部应进行最终的硬件与软件的移交确认、软件的初始版本必须改为最终版本并受控发行。
5.7 外部送样的规定
5.7.1样品检验、评审的依据、内容按客户标准及技术规范、质量要求进行。
5.7.2 样品包装应满足运输过程中的防护要求,样品及外包装应标示品名、规格、数量、送样单位、收样单位、人员等信息,样品标示中应标明样品用途、限定状况等内容。
5.7.3送样流程按照Q/R-G-ZB-25《新产品送样流程管理规定》,客户有特殊要求时按客户特殊要求执行。
6 奖惩
6.1新产品开发试制过程中发生以下情况时,领用人除全额赔偿公司损失外还将扣除当月绩效10分:
a)擅自修改领料单信息;
c)挪用公物,公作私用;
c)冒用他人签名者。
6.2 关于流程执行中的奖惩按照表2。
表2 流程执行奖惩对照表
6.3 新产品技术开发事故按照Q/R-G-GC-12《新产品技术开发事故处理办法》执行。
7 记录
记录按照Q/R-G-GC-8《产品质量先期策划》和Q/R-G-XM-5《项目管理程序》中的记录表单。
4
Q/R-G-XM-2-2010
5
Q/R-G-XM-2-2010
图2 S4-2阶段工作流程图6
Q/R-G-XM-2-2010
图3 产品送样流程
7
Q/R-G-XM-2-2010
图3(续) 产品送样流程8。