冷轧铝板带材轧制油起泡
铝板带箔常见主要缺陷及控制浅析

铝板带箔常见主要缺陷及控制浅析摘要:随着社会发展,带动着我国各行业的高速发展。
由于铝及铝合金具有一系列的优异特性,近年来发展速度非常快,同时客户对产品质量的要求也越来越高,各大企业对铝加工产品缺陷的控制也越来越重视,本文重点阐述铝板带箔产品缺陷的分类及生产过程中常见的典型缺陷产生的原因及预防措施,方便企业进行产品缺陷特征分析和预防。
进而通过对缺陷的周期进行分析,可准确推断出此类缺陷产生的位置及原因,为有效改善铝板带箔产品质量提供了良好基础。
另外对目前各大铝加工企业存在的现状问题进行分析,并供同行参考资料。
关键词:铝板带箔;轧制;周期性缺陷;技术人才;引言中国的铝板带箔加工企业,多数只是掌握了一般产品生产线的工艺技术,对高精端产品和特殊生产线的工艺技术尚处于模仿阶段。
比如,中国已经建成了多条铝合金厚板生产线,其生产能力占世界总产能的一半以上,但因工艺技术不成熟,实际生产能力还不足三分之一;中国建成了一条2000mm级当今世界最大的连铸连轧生产线,年生产能力超过250kt,却因工艺技术没有完全掌握,开机率还不足五分之一,成品率普遍偏低,产品加工费用偏高;中国从二十世纪八十年代末期就开始研发并生产PS版铝板基,目前超过10家以上企业拥有专门生产PS版铝板基的生产线,而因产品质量缺陷的控制及技术工艺始终没有获得突破,产品至今还处于中低端水平[1]。
1、铝板带箔加工企业铝合金带材缺陷的分类1.1铝合金带材缺陷分类按照缺陷出现的原因分类如下:1.1.1轧制缺陷。
有厚差、板形不良、表面波、金属或非金属压入、压折(斜角)、水迹(腐蚀)、皱折、打折、开缝、松卷、串层(塔形)、针孔、亮点、不规则亮带、张力线、辊印或辊眼、油污或条印、亮印、裂边和翘边。
1.1.2包装和储运缺陷。
有磕碰伤、压陷和腐蚀不同的缺陷分类方法适台于不同的场合.例如,按生产工艺流程来分,对购买毛料的厂家很有参考意义;按缺陷性质分类,有助于用技术手段解决问题,按缺陷形态分类,便于成品检验。
铝合金压铸件电镀起泡的原因

铝合金压铸件电镀起泡的原因
1. 前处理不干净会不会是铝合金压铸件电镀起泡的原因呢?就好比你要画画,画布不干净,那画出来的能好吗?比如有油污啥的没处理干净,这就很容易导致起泡呀!
2. 电镀液的成分不对头,这可太关键了吧!这不就像做饭调料放错了,味道肯定不对呀!比如说某种成分比例失调,那铝合金压铸件电镀能不起泡吗?
3. 电流密度控制不好,也会惹祸呀!就好像开车速度忽快忽慢,能不出问题吗?电流太大或太小,都可能让电镀起泡哟!
4. 温度不合适咋行呢?你想想,大冷天穿短袖,大热天穿棉袄,能舒服吗?铝合金压铸件电镀时温度不合适,起泡就来了呀!
5. 搅拌不均匀也是个问题呀!就像搅拌混凝土没搅好,能坚固吗?电镀液搅拌不均匀,那起泡不就出现了嘛!
6. 铝合金材料本身有问题,这可麻烦了!好比盖房子用的砖头质量不好,房子能牢固吗?材料有缺陷,电镀起泡就不奇怪啦!
7. 操作不规范能不出事吗?哎呀,这就跟走路不看路一样危险!不按正确流程操作,铝合金压铸件电镀不起泡才怪呢!
8. 设备老化了可不行呀!就像一辆老破车,能好好工作吗?设备不行了,电镀起泡就容易发生啦!
9. 环境不达标也会有影响啊!好比在一个脏兮兮的环境里生活,能健康吗?环境不好,铝合金压铸件电镀也容易起泡呀!
10. 人为因素也不能忽视呀!人要是粗心大意,那可啥事都可能发生!一个不小心,就可能导致铝合金压铸件电镀起泡啦!
我的观点结论就是:铝合金压铸件电镀起泡的原因有很多,任何一个环节出问题都可能导致起泡,所以一定要仔细对待每个环节呀!。
铝合金压铸起泡改善方案

铝合金压铸起泡改善方案一、提高模具温度1. 提高模具表面温度适当地提高模具的温度,可以减少铝合金压铸起泡的现象。
通过提高模具的温度,可以使得铝合金材料更容易粘附在模具表面上,从而减少了气泡的形成。
2. 减少热应力铝合金压铸过程中产生的热应力也可能导致起泡。
因此,需要采取措施减少热应力。
比如,优化压铸工艺参数,控制压铸温度和压力等,以减少热应力的产生。
3. 降低料温波动铝合金材料的温度波动也可能导致起泡。
因此,需要控制铝合金材料的温度,减少波动。
可以采用恒温压铸的方法,即在铝合金材料中加入恒温剂,以控制温度波动。
二、优化压铸工艺1. 选择合适的压铸机器及材料选择合适的压铸机器和材料,可以减少铝合金压铸起泡的现象。
比如,选择符合工艺要求的压铸机器和材料,可以使得铝合金材料更容易粘附在模具表面上,从而减少了气泡的形成。
2. 优化压铸工艺参数优化压铸工艺参数,可以减少铝合金压铸起泡的现象。
比如,适当地调整压铸压力、压铸温度、压铸速度等参数,可以使得铝合金材料更容易粘附在模具表面上,从而减少了气泡的形成。
3. 调整压铸温度和压力等工艺参数在铝合金压铸过程中,合理地调整压铸温度和压力等工艺参数,可以减少起泡的现象。
比如,在保证铝合金材料充分凝固的前提下,适当地降低压铸温度和压力等参数,可以减少气泡的形成。
三、加强模具维护1. 定期检查模具磨损情况定期检查模具的磨损情况,可以及时发现模具表面粗糙或凹凸不平的问题。
这些问题会导致铝合金材料难以粘附在模具表面上,从而产生起泡现象。
因此,需要定期检查模具的磨损情况,并及时进行修复和保养。
2. 清洗模具定期清洗模具,可以保持模具表面的清洁度,从而减少铝合金压铸起泡的现象。
清洗模具时,需要使用合适的清洗剂和工具,彻底清除模具表面的污垢和杂质。
3. 涂抹润滑油脂在铝合金压铸过程中,涂抹适量的润滑油脂,可以减少铝合金材料与模具表面的摩擦,从而减少起泡现象的产生。
但是需要注意,涂抹的润滑油脂不能过多,否则可能影响铝合金材料的粘附性。
冷轧铝板带材轧制油起泡的原因及对策
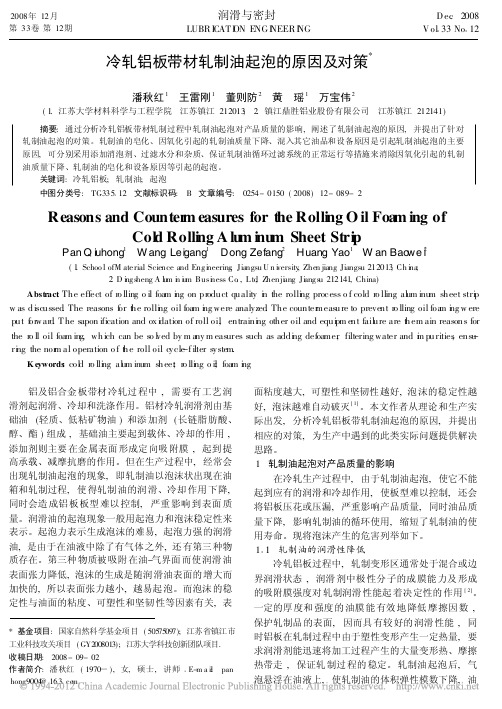
2008年12月第33卷第12期润滑与密封LUBR I CAT I ON ENG I NEER I NGD ec .2008V ol 133No 112*基金项目:国家自然科学基金项目(50575097);江苏省镇江市工业科技攻关项目(GY2008013);江苏大学科技创新团队项目.收稿日期:2008-09-02作者简介:潘秋红(1970)),女,硕士,讲师1E-m a i:l panhong9004@1631co m 1冷轧铝板带材轧制油起泡的原因及对策*潘秋红1 王雷刚1 董则防2 黄 瑶1 万宝伟2(1.江苏大学材料科学与工程学院 江苏镇江212013;2.镇江鼎胜铝业股份有限公司 江苏镇江212141)摘要:通过分析冷轧铝板带材轧制过程中轧制油起泡对产品质量的影响,阐述了轧制油起泡的原因,并提出了针对轧制油起泡的对策。
轧制油的皂化、因氧化引起的轧制油质量下降、混入其它油品和设备原因是引起轧制油起泡的主要原因,可分别采用添加消泡剂、过滤水分和杂质、保证轧制油循环过滤系统的正常运行等措施来消除因氧化引起的轧制油质量下降、轧制油的皂化和设备原因等引起的起泡。
关键词:冷轧铝板;轧制油;起泡中图分类号:TG335112 文献标识码:B 文章编号:0254-0150(2008)12-089-2Reasons and Counter m easures for t he Rolli ng O il Foa m ing ofCol d Rolli ng A lu m i nu m Sheet Stri pPan Q i u hong 1 W ang Lei g ang 1 Dong Zefang 2 Huang Yao 1 W an Bao we i2(1.School ofM aterial Science and Engi neering ,Jiangsu Un i versity ,Zhen jiang Jiangsu 212013,Ch i na ;2.D i ngs heng A l u m i n i u m Busi ness Co .,Ltd ,Zhenji ang Ji angs u 212141,China)Abstract :The effect of r o lling o il foa m i ng on pr oduct quality i n the rolli ng process o f cold r o lling al um inu m sheet stri pw as disc ussed .The reasons f or t he rolli ng oil foa m i ng were analyzed .The counter measure to preve nt r o lling oil foa m i ng w ereput f or war d .T he sapon ification and ox i dation of roll oi,l entraini ng other oil and equi pm e nt fail ure are t hem ain reasons for the r o ll oil foa m ing ,which can be so l ved by m a ny m easures such as addi ng defoa mer ,filtering water and m i purities ,ensu -ri ng the nor m al operation o f t he roll oil c ycle -f ilter syste m.K eywords :col d r o lli ng al um inum sheet ;r o lli ng o i;l foa m i ng铝及铝合金板带材冷轧过程中,需要有工艺润滑剂起润滑、冷却和洗涤作用。
铝板带冷轧机火灾事故原因分析
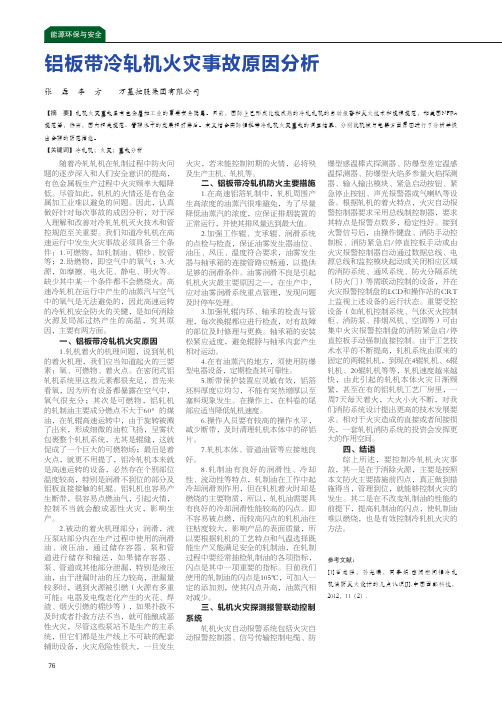
随着冷轧轧机在轧制过程中防火问题的逐步深入和人们安全意识的提高,有色金属板生产过程中火灾频率大幅降低。
尽管如此,轧机的火情还是有色金属加工业难以避免的问题。
因此,认真做好针对每次事故的成因分析,对于深入理解和改善对冷轧轧机灭火技术和管控规范至关重要。
我们知道冷轧机在高速运行中发生火灾事故必须具备三个条件:1.可燃物,如轧制油、棉纱、胶管等;2.助燃物,即空气中的氧气;3.火源,如摩擦、电火花、静电、明火等。
缺少其中某一个条件都不会燃烧火。
高速冷轧机在运行中产生的油蒸汽与空气中的氧气是无法避免的,因此高速运转的冷轧机安全防火的关键,是如何消除火源及局部过热产生的高温,究其原因,主要有两方面。
一、铝板带冷轧机火灾原因1.轧机着火的机理问题,说到轧机的着火机理,我们应当知道起火的三要素:氧、可燃物、着火点。
在密闭式铝轧机系统里这些元素都很充足,首先来看氧,因为所有设备都暴露在空气中,氧气很充分;其次是可燃物,铝轧机的轧制油主要成分燃点不大于60°的煤油,在轧辊高速运转中,由于旋转被溅了出来,形成细微的油粒飞扬,呈雾状包裹整个轧机系统,尤其是辊缝,这就促成了一个巨大的可燃物场;最后是着火点,就更不用提了,铝冷轧机本来就是高速运转的设备,必然存在个别部位温度较高,特别是润滑不到位的部分及铝板直接接触的轧辊。
铝轧机也容易产生断带,很容易点燃油气,引起火情,控制不当就会酿成恶性火灾,影响生产。
2.被动的着火机理部分:润滑,液压泵站部分内在生产过程中使用的润滑油、液压油,通过储存容器、泵和管道进行储存和输送,如果储存容器、泵、管道或其他部分泄漏,特别是液压油,由于泄漏时油的压力较高,泄漏量较多时,遇到火源被引燃(火源有多重可能:电器及电缆老化产生的火花、焊渣、烟火引燃的棉纱等),如果扑救不及时或者扑救方法不当,就可能酿成恶性火灾,尽管这些泵站不是生产的主系统,但它们都是生产线上不可缺的配套辅助设备,火灾危险性很大,一旦发生火灾,若未能控制初期的火情,必将殃及生产主机、轧机等。
轧制油管理
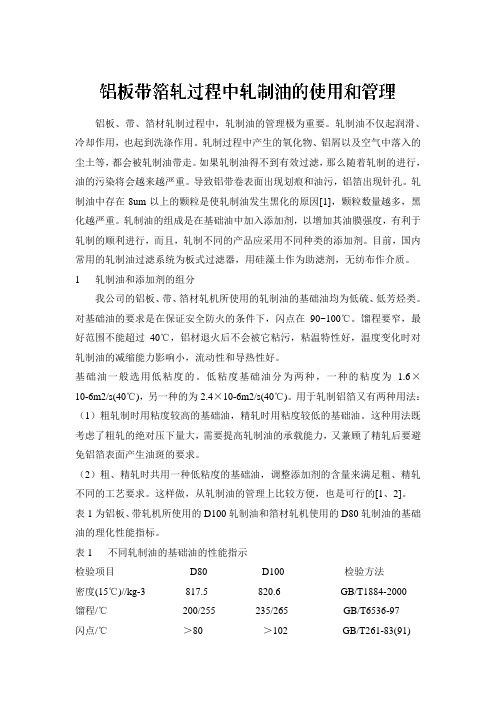
铝板、带、箔材轧制过程中,轧制油的管理极为重要。
轧制油不仅起润滑、冷却作用,也起到洗涤作用。
轧制过程中产生的氧化物、铝屑以及空气中落入的尘土等,都会被轧制油带走。
如果轧制油得不到有效过滤,那么随着轧制的进行,油的污染将会越来越严重。
导致铝带卷表面出现划痕和油污,铝箔出现针孔。
轧制油中存在8um以上的颗粒是使轧制油发生黑化的原因[1],颗粒数量越多,黑化越严重。
轧制油的组成是在基础油中加入添加剂,以增加其油膜强度,有利于轧制的顺利进行,而且,轧制不同的产品应采用不同种类的添加剂。
目前,国内常用的轧制油过滤系统为板式过滤器,用硅藻土作为助滤剂,无纺布作介质。
1 轧制油和添加剂的组分我公司的铝板、带、箔材轧机所使用的轧制油的基础油均为低硫、低芳烃类。
对基础油的要求是在保证安全防火的条件下,闪点在90~100℃。
馏程要窄,最好范围不能超过40℃,铝材退火后不会被它粘污,粘温特性好,温度变化时对轧制油的减缩能力影响小,流动性和导热性好。
基础油一般选用低粘度的。
低粘度基础油分为两种,一种的粘度为 1.6×10-6m2/s(40℃),另一种的为2.4×10-6m2/s(40℃)。
用于轧制铝箔又有两种用法:(1)粗轧制时用粘度较高的基础油,精轧时用粘度较低的基础油。
这种用法既考虑了粗轧的绝对压下量大,需要提高轧制油的承载能力,又兼顾了精轧后要避免铝箔表面产生油斑的要求。
(2)粗、精轧时共用一种低粘度的基础油,调整添加剂的含量来满足粗、精轧不同的工艺要求。
这样做,从轧制油的管理上比较方便,也是可行的[1、2]。
表1为铝板、带轧机所使用的D100轧制油和箔材轧机使用的D80轧制油的基础油的理化性能指标。
表1 不同轧制油的基础油的性能指示检验项目D80 D100 检验方法密度(15℃)//kg-3 817.5 820.6 GB/T1884-2000馏程/℃200/255 235/265 GB/T6536-97闪点/℃>80 >102 GB/T261-83(91)运动粘度(40℃)/mm2s-1 1.55~1.75 2.1~2.45 GB/T265-88硫/mg·kg-1 <0.5 <0.5 SH/T0253-92灰分/% <0.005 <0.005 GB/T508-85(91) 外观验员无色、无味、透明无色、无味、透明目测杂质和水无无为了获得轧制的各种功能,使轧制油具有薄而强的油膜和适当的磨擦因数,向轧制油中加入添加剂,最好采用精致的高醇、高脂肪醇或它们的脂类共氧化物作为添加剂,因为它们的稳定性好,与铝材不发生反应,不含产生铝材退火时油斑,在低温下退火能脱脂。
铝箔轧制过程产生的原因及控制方法

铝箔轧制常见缺陷的一般特征、原因及措施
铝箔作为一种极限加工,其生产工序多、加工技术难度大、厚度最薄的生产特点决定了其产生缺陷的几率要比其他压力加工高许多倍,其生产的可能性、稳定性除非设备有重大问题,否则绝大部分与缺陷有关,努力减少和消除轧制缺陷是实现安全、优质、高效、低耗生产的关键之一。
本资料主要以我厂在实际生产中遇到的一些问题为研究对象进行编制,旨在通过机台操作人员的学习来提升他们的基础知识和专业水平,更好地为顾客提供具有竞争力的产品。
* 表示该问题的原因尝不确定。
缺陷

3) 精整时板角划伤板面:
4) 包装时,异物划伤板面。
14、压过划痕
经轧辊压过的擦、划伤、粘铝等表面缺陷
15、黑条
板、带材表面沿轧制方向分布的黑色线条状缺陷
主要产生原因:
1) 工艺润滑不良:
2) 工艺润滑剂不干净:
3) 板、带表面有擦划伤:
2、 毛刺
板、带材经剪切,边缘存在有打大小不等的细短丝或尖而薄的金属刺。
主要产生原因:
1) 剪刃不锋利:
2) 剪刃润滑不良:
3) 剪刃间隙及重叠量调整不当。
3、 水痕
板、带材表面浅白色或浅黑色不规则的水线痕迹
主要产生原因:
1) 淬火后板材表面水份未处理干净,经压光机压光后留下的痕迹:
2) 润滑冷却不均,使板、带变形不均:
3) 道次压下量分配不合理:
4) 来料质量不好,同板差超标:
5) 卷取张力使用不均。
13、明暗条纹
组织不均匀,或有粗大晶粒存在而产生的与压延方向平行的明暗相间的光泽不同的条纹。
主要产生原因:
1) 铸锭表面质量差,热轧有没有铣面:
2) 板坯表面组织不均有粗大晶粒。
4) 板、带通过的导路不干净:
5) 铸轧带表面偏析或热轧用铸块铣面不彻底:
6) 金属中有夹杂:
7) 开坯轧制时,产生大量氧化铝粉,并压入金属,进一步轧制产生黑条。
16、油斑
残留在板、带上的油污,经退火后形成的淡黄色、棕色,黄褐色斑痕。
主要产生原因:
1) 轧制油的理化指标不适宜:
2) 冷轧吹扫不良,残留油过多,退火过程中,残留油不能完全挥发:
铝合金冷轧轧制油着火预防控制

学术论坛280 2015年18期铝合金冷轧轧制油着火预防控制段文彬河南豫联能源集团有限责任公司,河南巩义 451200摘要:铝合金冷轧断带易引起轧制油着火爆炸,是企业重点防控的风险因素,本文结合多年生产实践,对如何预防控制风险因素进行分析和阐述。
关键词:铝合金冷轧;轧制油着火;预防中图分类号:TG156.2 文献标识码:A 文章编号:1671-5780(2015)18-0280-01铝合金是工业中应用最广泛的一类有色金属结构材料,做为铝合金材料的重要生产形式,冷轧可生产厚度较薄、尺寸精确、表面质量高的板带材。
由于企业在进行铝合金冷轧过程中,常使用轧制油,主要作用是降温润滑,生产时如控制不好,易发生火灾或爆炸事故,是企业重点控制的危险源。
笔者结合冷轧生产实践,探讨如何避免发生轧制油火灾或爆炸事故,发生事故后如何紧急有效处理。
1 轧制油危险机理轧制润滑是集压力加工、机械和化学相关理论等于一体的综合技术,正确使用、管理轧制油是保证稳定、安全轧制和产品质量的重要手段。
冷轧过程中,轧件和辊面之间有前滑区、后滑区和黏着区,各区内摩擦力方向相同,存在复杂的相对运动,强烈的摩擦热效应可以使轧制变形区内温度高达100-200℃。
在此过程中,常常由于板带断带,极易发生静电积累和打火现象,从而增加了全油润滑轧机的火灾爆炸危险性。
2 轧机断带控制据多年生产实践和总结,轧机轧制铝合金板带过程中断带的主要原因有:铸轧来料豁边深或是冷轧开坯道次板形控制差,切边道次不足以剪切掉豁口;冷轧合金开坯错层严重;冷轧工艺道次安排不合理;辊型控制不好,延伸不均,或张力过大;热粗轧板坯质量不合格,热精轧卷坯质量缺陷;轧机振动,使板带产生波动,局部张力失控;液压或机械系统故障导致厚度波动过大;操作人员技能差,出现操作失误或不当,责任心不强;轧制中油压、张力、卷曲力、轧制力、轧制速度等参数控制,及供电稳定性发生波动、测速仪故障、测厚仪故障等都会导致断带。
浅议铝箔粗轧过程中产生黑色散油点的不良现象与对策

浅议铝箔粗轧过程中产生黑色散油点的不良现象与对策摘要:国民经济在发展,国民素质在提高,国民对生活质量更是有了质的飞跃,对日常生活中的各种制品也有了更高的要求。
因为铝箔具有材质轻、高阻隔性、遮光、抗紫外线、防潮、防腐蚀、保质期长、安全卫生等特性,具有更好的保鲜及保持水份不流失功能.同时,铝箔回收再利用率高,对节约资源、减少环境污染有积极意义.因此,近年来,铝易拉罐、铝箔餐盒、药用包装铝箔、铝箔食品保鲜膜、利乐包、利乐枕等铝箔制品越来越贴近人们的日常生活.关键词:铝箔;散油点;带油;脱粉;变质;清洁引言0.05~0.20 mm的铝箔在粗轧过程中,由于各种影响因素,在铝箔表面容易出现黑色散油点缺陷.铝箔表面黑色散油点的存在,严重影响铝箔涂层复合的粘结力,导致铝箔涂层产品和铝塑复合包装材料表面容易产生漏涂、脱胶等质量问题,影响罐装、袋装铝制品的阻隔、遮光、防潮和食用安全性能,因此,食用、药用包装铝箔表面不允许有任何黑色物质存在.可见研究铝箔粗轧过程中黑色散油点的成因与对策,对于提高食品、饮料和药品等食用包装铝箔的质量和使用具有重要的意义.一、概述散油点的产生在铝箔的生产中,铝箔的轧制分粗轧、中轧和精轧三个过程.0.05~0.20 mm单张铝箔轧制属于粗轧范围,且散油点一般分布在0.05~0.20 mm单张铝箔上表面.粗轧轧制特点为:铝箔咬入后,轧件两面的辊面仍处于部分或全部压靠状态,轧制过程中,整个轧制变形区内沿轧制方向油楔深浅变化不一,沿轧辊轴向油膜厚度分布不均匀,轧制油膜以外的油由辊颈处或轧机出口上、下方容易甩、溅、滴在轧制出口铝箔表面上,形成的散油点大小、多少、位置均不固定.二、浅议影响黑色散油点的不良因素2-1、来料板形不良来料板形严重不良的铸轧坯料或经中间退火后的卷取张力过大的卷材,带卷层间易发生黏连,在轧机开卷过程中会造成带材表面形成凹凸不平的黏铝坑点,凸起的黏铝点吸附于带材表面,在压延过程中很难与铝基体焊合.随着轧制带材的减薄,逐渐从轧制带材表面脱落而形成铝粉.2-2、工作辊两边挡油效果不好铝箔轧机上工作辊轴承箱两内侧一般都装有弧形挡油瓦,挡油瓦下方连有防溅丁腈橡胶油帘;或者是铝箔轧机出口导板两侧垂直装有带弧形刮油板的挡油盒,该刮油板的位置应跨过辊颈辊面10~20 mm为最佳.挡油瓦或挡油盒的刮油板与工作辊面应保持不大于5 mm的间隙,目的是避免剐蹭辊颈辊面发生摩擦起火.同时,为轧机出口边部辊缝吹扫气流的走向留有出口,防止边部出现气旋,导致辊径甩油回弹飞溅至轧制箔材边部,形成边部散油点.挡油瓦的材质一般用厚度为2 mm的不锈钢板或铝板制作,刮油板一般用聚氨酯板制作,挡油瓦或挡油盒除了靠轧机工作辊一侧留有缝隙外,其他方向与轧机出口机架各部位连接应密闭,防止铝箔轧机在高速运转中,轧制油膜以外的油由辊颈处甩、溅、滴落在轧制出口铝箔边部的上、下表面,形成边部散油点缺陷.2-3、铸轧组织致密度不够,压延轧制容易脱粉铸轧生产过程中,往往会采用增加铸轧板厚、提高铸轧速度等非正常生产手段提高产量,导致铸轧区液穴加深,铸轧区结晶前沿不一致,固液区上下两侧凝固壳减薄,铸轧板会出现从粗大中心线偏析到分散型偏析和表面偏析的变化,易形成铸轧板组织不致密.固液区的长短与合金的结晶区间有关,结晶区间大的合金,其区域稍长,纯铝较短,3003、3105等3系铝合金结晶区间大,易出现偏析且致密度较差[1],压延轧制时容易脱粉.生产实践表明,3003铝合金铸轧区设定在50~55 mm,前箱温度控制在695 ℃±2 ℃,铸轧速度在700~850 mm/min,可有效地预防铸轧板组织产生中心偏析.2-4、轧制油管理不严格箔轧过程中,轧制油氧化是生成油泥的一个不可忽视的因素,油泥的生成与轧制油的性能密切相关,轧制油的润滑性能差、承载能力低、酸值高以及抗氧化稳定性能低均可促使油泥的生成2-5、轧机清洁不到位铝箔轧制过程中,轧制油会发生黑化.黑化的轧制油滴黏附于轧机排烟罩内壁、轧机牌坊、轧辊轴承箱、轧机入出口机架各构件等表面,会发生沉积,形成油泥.当黏附的油泥颗粒吸附聚集长大到一定程度,油泥颗粒自重大于油泥颗粒与颗粒之间的吸附力时,大的油泥颗粒会被轧制油冲刷下来,滴落在轧制铝箔表面,形成黑油点.因此,要定期清洁轧机.三、分析控制黑色散油点的对策3-1、加强产品质量管理,提高质量责任意识引进岗位竞争激励长效机制,建立和完善企业薪酬体系,推行标准化作业与管理,克制因低级错误或执行力不强造成的批量性产品质量责任事故,是稳定产品质量的重要手段.3-2、合理加装和固定挡油位置,预防不良再发生合理地调整清辊器和支承辊的间隙和压力,在上支承辊的上方,上支承辊轴承座之间加装防油滴落盖板.轧机出口上下工作辊辊缝以外上下部位加装挡油板或挡油帘,在上支承辊与上工作辊的辊缝偏下20~25 mm位置增加中间接油板,铝箔轧机上工作辊两侧加装挡油瓦或挡油盒,在轧机出口测厚仪下方加装左高右低的导流板,合理地调整轧机排烟系统的抽力和轧制线位置,以及合理地调整中间吹扫、辊缝吹扫、板面吹扫角度与风压,可有效地预防轧制油膜以外的轧制油由辊颈处或轧机出口上、下方甩、溅、滴在铝箔表面上形成散油点.正常轧制生产中,控制散油点的最佳方法是以先消除中间带油,再消除两边带油为原则,精确地调整轧制线,确保轧机上下清辊器、中间吹扫风嘴、各挡油板、中间接油板基本位置维持不变.通过更换清辊器绒布、调节中间吹扫风压和中间接油板与上工作辊间隙,消除中间带油;再通过调节边部辊缝吹扫角度、风压及板面吹扫风压大小,消除边部带油.3-3、提高铝箔坯料内在冶金质量,减少轧制脱粉严格控制3003、3105等3系铝合金铸轧区大小、前箱温度和铸轧速度,可有效预防铸轧板组织产生中心偏析.适当地减小中间退火卷的卷取张力,可有效地预防中间退火后带卷层间黏连.对于纯铝料或中间退火料,在后续的轧制道次中,采用小轧制力高速生产,可有效地减少轧制脱粉.3-4、加强工艺管理,预防轧制油品老化变质根据来料合金状态,合理编排轧制道次和选择轧辊表面粗糙度,能减少轧制脱粉;在轧机前端加装压缩空气干燥器,能减少压缩空气中的水分带入轧制油中;规范各轧制道次工艺参数,严格控制工艺油温、油压,定期检测轧制油的各项理化性能指标,严格控制在规定范围之内,能降低轧制油品老化变质几率;合理地选用轧机油过滤介质,规范轧制油过滤用各种助滤剂的添加比例和轧制基础油的补油量及补油周期,对防止净油箱污油倒灌,确保轧制油清洁,有明显的效果.3-5、搞好文明生产,定期清洁轧机关好厂房大门,能保持厂房温度,减少空气湿度;每天定期搞好厂房生产环境卫生,能有效地降低厂房内粉尘的含量.每周定期清洁轧机,尤其是对轧机牌坊内侧上下前后左右密闭空间、轧机支承辊和工作辊轴承座上下表面、轧机出口机架各构件外表面,以及轧机出口排烟罩集油槽内表面的清理清洁,能有效地降低被轧制油膜以外的轧制油冲刷下来的油点灰分的含量.四、结束语总之,在新的市场背景下,铝箔的需求量逐渐增多,但是铝箔加工业一直都有着高成本、低产量的特点。
铝板带生产油斑的预防与控制

铝板带生产油斑的预防与控制【摘要】通过介绍铝板带材表面如何产生油斑质量缺陷,分析引起油斑的主要因素,进而针对主要因素提出相应的预防与控制措施。
【关键词】油斑;油品;厚度;吹扫;氮气退火退火工艺在板带材的生产中占有非常重要的地位,没有各种热处理工序,板带材的生产几乎不能进行。
退火油斑是热处理过程中极易产生的缺陷,油斑是铝板带在轧制过程中,铝带材表面携带的轧制油与退火炉内空气发生不完全氧化而在带材边部形成的黄色色差。
油斑因轧制油残留量混入的机械油和液压油的程度不同,呈现浅黄色、黄色、黄褐色等颜色,随程度加重,颜色加深。
1形成油斑的主要影响因素1.1油品指标通常良好的轧制油应该具备以下几个性能:粘度低,高闪点;低终馏点、窄馏分;易于挥发;润滑承压能力强;具有较好的溶解能力;且易于清洗;具有较强的稳定性,避免使用过程中氧化。
事实表明,一种具有较强润滑能力的轧制油,往往其碳链较长,退火易产生油斑。
同时生产过程中,随着轧制油回收循环使用过程中,铝粉的进入,轧制过程碳链的破坏氧化、机械设备等杂油的泄漏混入造成了轧制油指标的不稳定。
现实生产中,透光率与胶质含量是考量油品质量的重要指标,生产跟踪良好的轧制环境其透光率应该控制在90%以上,胶质含量应该控制在300mg/100ml以内。
1.2轧件厚度轧件在轧制过程中,轧件厚度越大,辊缝越大,轧制过程随着辊缝带出的油将越多,同时,轧制速度越快,轧制油随着轧件带出的油也越多。
1.3轧件板型铝板带材在轧制过程中,因为润滑、冷却等因素的影响,造成带材在轧制过程中延伸不均匀,最终导致带材表面的不平整,卷取完成,残留轧制油容易在凹处富集,退火后不完全氧化烧结。
同时如果边部过松,形成松边,边部富氧宽度将增加,退火时,该区域轧制油将燃烧形成油斑,通过控制边部板型质量,减小富氧区域将有效减少油斑宽度。
1.4轧件表面粗糙度因板带材在退火过程中,带材表面的残留轧制油随着温度的升高汽化,并沿着卷材层间间隙逸出。
铝加工冷轧轧制油基础介绍资料

脂肪酸、醇、酯的主要性能比较
特性
脂肪酸
脂肪醇
脂肪酸酯
O
O
结构
R – C – OH
油膜厚度
深
油膜强度
强
浸润性
劣
热稳定性
良
表面光亮性
优
不形成污痕能力 良
碳数 铝箔 C10 – C14
增加链长:降低摩擦系数,减少磨损,增加物理吸附。-C16, 阻力与减磨平衡。
网络,致密性:油膜强度,影响版面光洁度,针孔度。
综合:根据不同板系:考虑吸附,脱附情况,达到足够油膜强 度,致密性及应用范围选用适当链长及醇酯复合比例。
三、薄板厂目前轧制油情况
薄板厂目前使用的基础油为沧炼D115,使用的添加剂为特浦朗 克添加剂,包括A1-13、A1-3S、A3(酯)、A8E(醇)、抗氧 化剂、月桂酸等
基础油理化指标及作用
理化指标:粘度、闪点、倾点、馏程、初馏点、终馏点、酸 值、硫含量
理化指标的作用 轧制油的理化性能不仅是润滑剂本身品质高低的一个标志,同
时还是选择润滑的主要依据之一,另外,理化性能的好坏还直 接影响到使用性能以及加工后产品的质量,作为轧制油,理化 性能同样对轧制工艺、轧后板带材表面质量等产生较大影响。
铝板 C12 – C14
R – C – OH 深 弱 优 良 良
优
C10 – C14 C14 – C16
R–C–O–R' 厚 强 良 优 劣
良
C10 – C14 C12 – C16
- 添加剂碳链长度对油膜强度的影响 碳链越长,油膜强度越高; 碳链增加到一定程度时,对油膜强度影响趋缓。 - 醇、酯对摩擦系数、 轧制力的影响 醇的减摩效果优于酯; 酯的承载能力更强,可有效降低轧制压力 - 醇、酯添加剂复用效果 复用添加剂减摩降压效果优于单一添加剂; 醇酯复合有效增加了润滑效果。 - 醇、酯消耗量 醇的消耗量大于酯的消耗量; - 醇、酯对轧后光亮度的影响 醇对表面光亮度影响优于酯; 添加剂浓度达到一定程度后,表面光亮度反而下降。
冷轧铝板带材生产的板形控制
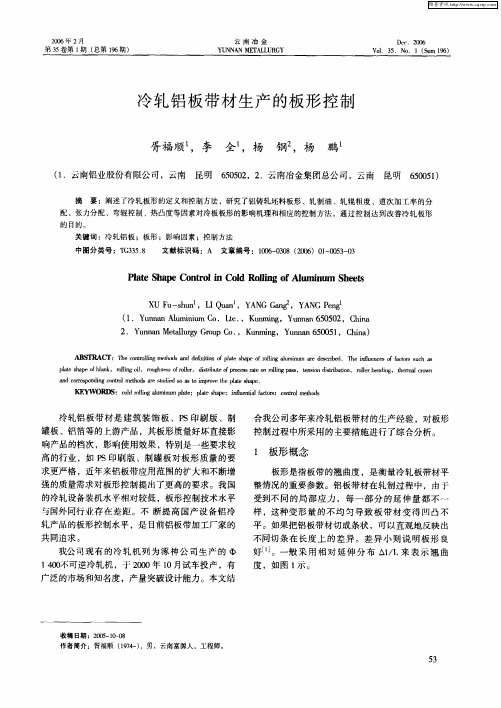
A S R ur h n oi  ̄ o n dfi no p f s p o rlga m nm a e r e .T eil ne o f ts u s B r A :T e otl g t d ad e t l h e f oi u i ds i d h f e s f a o c c rl u h s i i f 丑 a . l l u n m o e n cb n u c c r s h丑
( .Y n a l iim C .Le ,K n ig u nn6 00 ,C ia m u
2 unnMe l r ru o ,K n i ,Y n a 50 1 hn ) .Y na t l g GopC . u m n au y g u nn6 0 5 ,C ia
维普资讯
20 06年 2月
云 南 冶 金
YUNN AN MET^ IIR I . GY 7
D c 2x e . I】 6
第 3 卷第 1 ( 5 期 总第 1 期 ) 9 6
V 1 5 o 1 (u 9 ) o.3 .N . Sm 16
广泛的市场和知名度 ,产量突破设计能力。本文结
收 稿 日期 :2 0—0-8 05 1- 0
作者简介:胥福顺 (94 ) 1 _ ,男 ,云南富源人,工程师 。 7
冷轧铝板轧制油中基础油对轧制效果的影响
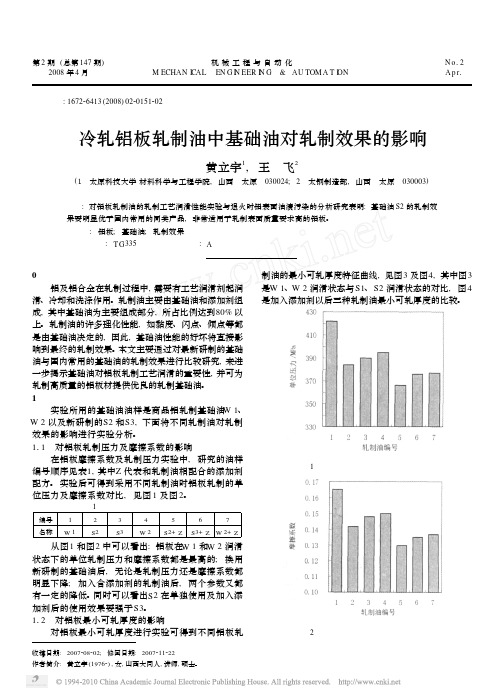
位压力及摩擦系数对比, 见图 1 及图 2。
表 1 实验中轧制油编号及名称
编号 1
2
3
45Leabharlann 67名称 W 1
S2
S3
W 2 S2+ Z S3+ Z W 2+ Z
从图1 和图2 中可以看出: 铝板在W 1 和W 2 润滑 状态下的单位轧制压力和摩擦系数都是最高的; 换用 新研制的基础油后, 无论是轧制压力还是摩擦系数都 明显下降; 加入含添加剂的轧制油后, 两个参数又都 有一定的降低。同时可以看出S2 在单独使用及加入添 加剂后的使用效果要强于 S 3。 112 对铝板最小可轧厚度的影响
油与国内常用的基础油的轧制效果进行比较研究, 来进 一步揭示基础油对铝板轧制工艺润滑的重要性, 并可为 轧制高质量的铝板材提供优良的轧制基础油。
1 实验过程 实验所用的基础油油样是商品铝轧制基础油W 1、
W 2 以及新研制的S2 和S3, 下面将不同轧制油对轧制 效果的影响进行实验分析。
111 对铝板轧制压力及摩擦系数的影响 在铝板摩擦系数及轧制压力实验中, 研究的油样
(1. 太原科技大学 材料科学与工程学院, 山西 太原 030024; 2. 太钢制造部, 山西 太原 030003)
摘要: 对铝板轧制油的轧制工艺润滑性能实验与退火时铝表面油渍污染的分析研究表明: 基础油 S2 的轧制效 果要明显优于国内常用的同类产品, 非常适用于轧制表面质量要求高的铝板。 关键词: 铝板; 基础油; 轧制效果 中图分类号: T G335 文献标识码: A
第 2 期 (总第 147 期) 2008 年 4 月
铝板带冷轧生产的板形控制技术及策略

铝板带冷轧生产的板形控制技术及策略发布时间:2022-05-23T02:35:58.915Z 来源:《中国科技信息》2022年第2月3期作者:韦成强[导读] 本文从当前常见的铝板带冷轧生产技术问题入手,对当前造成铝板带冷轧板形不良韦成强广西柳州银海铝业股份有限公司广西柳州 545001摘要:本文从当前常见的铝板带冷轧生产技术问题入手,对当前造成铝板带冷轧板形不良、不满足品控要求的因素进行了分析,分析了各类技术在生产实践当中的关键点,同时结合当前比较流行的CVC六辊轧机,探讨应该如何在该设备条件与技术环境下实现冷轧板形控制,从而在丰富相关理论成果的同时,也为同业提供一定的参考。
关键词:冷轧生产;铝板带;板形控制1.板形控制对铝板带冷轧生产的重要性与影响因素对于采用冷轧工艺生产的铝板带来说,板形是否符合生产预期,是决定板带产品质量与外观是否合格的重要判断标准[1]。
而对铝板带冷轧生产板形存在影响的重要因素主要有下列几种:第一,热轧的原料板形。
只有在原料板形标准的情况下,冷轧铝板带才能够最终保证板形标准。
第二,工作辊的凸度,包括工作辊的长度、硬度,同时需考虑坯料合金、宽度以及进行轧制过程中受热的凸度变化等。
第三,正负弯辊对工作辊辊型的改变,最终对辊间缝隙实现变化。
第四,道次加工率。
每一道的加工率是否恰当,是轧辊的弹性变形以及辊间缝隙是否恰当的关键。
第五,进行冷轧生产时的前后张力,在张力变化的过程中,轧制力也会出现改变,最终通过轧辊本身的弹性变形来实现对轧辊间缝隙的改变。
第六,冷轧用油的冷却。
无论是任何材质的轧辊,都会因为轧制出现热膨胀,这种温度导致的变形会使铝板带的宽度方向的厚度变化不均,只有在冷轧用油能够冷却轧辊的时候,板形才能维持稳定。
在20世纪90年代末到21世纪初,我国常见的宽幅铝板带冷轧机械通常是四辊设计,轧机宽度最多见的都不足2000mm,板形主要是通过轧辊角度倾斜、正负弯辊调整工作辊、分段冷却等方式完成控制[2]。
铝板幕墙起泡重难点分析及解决措施

铝板幕墙起泡重难点分析及解决措施
一、重难点分析
由于本工程大量地使用了铝板,所以铝板幕墙的质量直接影响着整个工程的质量,而众所周知铝板如果喷涂、施工不当,则容易起泡,所以如何解决铝板幕墙的起泡问题是本工程的重点。
二、解决措施
1、加工质量控制措施
我司必须要求铝板生产厂家严格按铝板喷涂工艺进行铝板表面处理。
根据铝板厂家喷涂加工经验,铝板气泡主要发生在铝板的边角处,由于边角处容易被油污污染,涂料不能充分均匀喷涂,因此在铝板喷涂之前,在铝板素材的边角处贴上胶纸,防止被油污污染,然后进行铝板喷涂,保证铝板在喷涂后没有气泡现象。
2、我司对每批到货的铝板进行检测,检测没有问题方可运往工地安装。
铝挤压带板表面气泡缺陷形成原因及解决方案探讨

铝挤压带板表面气泡缺陷形成原因及解决方案探讨作者:来临赵茂密李飞龙来源:《企业科技与发展》2016年第04期(广西南南铝加工有限公司,广西南宁 530031)【摘要】铝挤压带板是铝合金挤压材料中常见的产品类型,用途广泛,在建筑、交通领域的用量巨大,也是各铝合金加工厂常生产的产品。
铝挤压带板在生产过程中产品容易产生表面气泡缺陷,程度轻微时会影响产品外观,增加工人后续打磨气泡的工作量,严重时会造成产品报废,降低成材率或增加产品失效风险。
文章根据对带板挤压生产过程的观察分析及实验结果,总结在挤压过程中气泡形成的原因,为铝合金带板挤压生产气泡的问题提供了相应的控制措施。
【关键词】铝挤压;带板;表面气泡【中图分类号】TG379 【文献标识码】A 【文章编号】1674-0688(2016)04-0105-040 前言铝合金挤压带板是铝制品中常见的产品形式,用于建筑、航空、军工等民用和国防尖端领域。
它也是各个铝加工厂经常生产的产品类型,它的厚度和宽度也有多重规格。
挤压带板表面产生气泡,为带板常见缺陷,气泡缺陷严重影响了带板的内部结构、外观及产品性能,程度轻微时会影响产品外观,增加工人后续打磨气泡的工作量。
严重时,降低了成材率或增加了产品失效风险,造成废品,给生产带来极大的浪费和损失。
特别是2、5、7系硬铝合金带板的生产,如果处理不当,极易出现气泡现象。
因此,本文分析了带板挤压阶段产生气泡的原因,并针对原因制订了解决方案,可以减少此缺陷的发生概率,以及降低问题发生后的严重程度。
1 气泡的形态挤压带板表面气泡如图1所示,缺陷轻微时会形成连续或不连续的点状气泡存在于整支或部分挤压带板的表面,常表现为点状气泡呈直线排列,气泡的直径为1~10 mm。
挤压带板表面气泡如图2所示,缺陷严重时会产生较大的鼓包,如果将其表面一层切开会发现,表层金属与内部金属已经分层;或将表皮凿开,则会露出较深的孔洞或凹陷。
2 气泡形成的原因为了证明气泡的来源,本文以5083铝合金带材为研究对象进行分析和查找原因。
冷轧过程中轧制油对铝材表面质量的影响

收稿日期:2005-06-26 第一作者简介:袁 驰(1980-),男,辽宁丹东人,硕士。
冷轧过程中轧制油对铝材表面质量的影响袁 驰1,刘友良2,孙建林1,王志强2,孙艳伟1(11北京科技大学材料科学与工程学院,北京100083;21湖南冶金职业技术学院,湖南株洲412000)摘要:试验研究了铝材冷轧过程中,工艺润滑对铝材表面质量的影响。
通过对不同轧制油轧制时轧件的表面形貌和表面粗糙度的分析得出:使用轧制油可以有效的改善铝材的表面质量,尤其在基础油中加入添加剂后,轧制润滑效果得到更大的改善,但添加剂对铝板表面质量的影响具有双重性。
关键词:铝材;轧制油;表面形貌;表面粗糙度中图分类号:TG 335 文献标识码:A 文章编号:1007-7235(2005)11-0024-03I nfluence of R olling Oil on R olled Aluminum MaterialSurface Q uality in Cold R olling ProcessY UAN Chi 1,LI U Y ou 2liang 2,S UN Jian 2lin 1,WANG Zhi 2qiang 2,S UN Y an 2wei1(11School of Materials Science and E ngineering ,USTB B eijing ,B eijing 100083,China ;21H unan Metallurgy and V ocational T echnology College ,Zhuzhou 412000,China)Abstract :The experiment studied on in fluence of rolling oil on rolled aluminum ’s surface quality in cold rolling process 1Surface topography and surface roughness of the rolled aluminum plate is analyzed 1The experimental results showed that rolled aluminum ’s surface quality becomes better with the rolling oil 1Especially the rolling oil with the additives g ot the best lubrication action effect 1K ey w ords :aluminum ;rolling oil ;surface topography ;surface roughness 在铝材冷轧过程中,工艺润滑起着越来越重要的作用。
- 1、下载文档前请自行甄别文档内容的完整性,平台不提供额外的编辑、内容补充、找答案等附加服务。
- 2、"仅部分预览"的文档,不可在线预览部分如存在完整性等问题,可反馈申请退款(可完整预览的文档不适用该条件!)。
- 3、如文档侵犯您的权益,请联系客服反馈,我们会尽快为您处理(人工客服工作时间:9:00-18:30)。
【9】马前, 刘白成, 王兆昌. Fe2C合金高温保温过程中碳化 物表面的研究[ J ]. 钢铁, 1994, 29 (5) : 47. 【10】马前, 王兆昌. 白口铁热处理对共晶碳化物的溶解与粒 状化的影响[ J ]. 钢铁研究学报, 1990, 2 (1) : 63. 【11】王树奇, 姜启川, 崔向红. 稀土对莱氏体钢共晶碳化物 粒化的影响[ J ]. 中国稀土学报, 1998, 16 (3) : 242 -246.
一.轧制油起泡对产品质量的影响 轧制油起泡对产品质量的影响
在冷轧生产过程中, 由于轧制油起泡, 使它不能起到应有的润滑 冷轧铝板带材轧制油起泡的原 和冷却作用, 使板型难以控制, 还会将铝板压花或压漏, 严重影响产 品质量, 同时油品质量下降, 影响轧制油的循环使用, 缩短了轧制油 因及对策 的使用寿命。现将泡沫产生的危害列举如下。 1.轧制油的润滑性降低 轧制油起泡后, 气泡悬浮在油液上, 使轧制油的体积弹性模数下 降, 油的动力粘度增高, 导致油膜强度降低, 润滑性能下降; 泡沫内 制作人:尤凤霞 混入的空气使轧制油的散热性降低, 使大量的热量滞留, 冷却性能 下降, 变形的热效应使轧制区温度升高, 从而相应会抑制油膜厚度, 使摩擦因数增大, 润滑性能降低。
结束语
对轧制油起泡的原因从理论和实践上进行了系统分析, 并提 出了解决此问题的对策, 可防止铝板带材在冷轧过程中由于轧制 , 油起泡而引起产品质量的波动, 使冷轧生产能够顺利进行。
参考文献 【1】邹先瑞. 润滑油起泡原因、危害和处理[ J ]. 山西机械,2001 (增刊) : 164 - 166. 【2】孙建林. 轧制工艺润滑原理技术与应用[M ]. 北京: 冶金工业出版社, 2004. 【3】袁驰, 刘友良, 孙建林, 等. 冷轧过程中轧制油对铝材表面质量的影 响[ J ]. 轻合金加工技术, 2005, 33 ( 11 ) :24 - 26. 【4】熊绍钧. 液压设备设计和使用中如何预防气泡油问题[ J ]. 液压与气 动, 1999 (2) : 3 【5】吕振林, 周永欣, 时惠英. 破碎机械上易磨损件的材质选择[ J ]. 机械 工程材料, 1997 (5) : 44 - 46. , 【6】李茂林. 我国金属耐磨材料的发展和应用[ J ]. 铸造, 2002 (9) : 525 - 529. 【7】宋绪丁, 蒋志强, 符寒光. 高硼铸钢的制备与应用[ J ]. 铸造技术, 2006, 27 (8) : 805 - 808. 【8】符寒光, 胡开华. 高硼铸造铁基耐磨合金及其热处理方法: 中国, CN1624180 [ P ]. 2004: 12 - 14.
冷轧铝板带材轧制油起泡的原 冷轧铝板带材轧制油起泡的原因及对策 因及对策
制作人:尤凤霞
制作人:尤凤霞 制作人 尤凤霞
铝及铝合金板带材冷轧过程中, 需要有工艺润滑剂起润滑、 冷轧铝板带材轧制油起泡的原 冷却和洗涤作用。铝材冷轧润滑剂由基础油和添加剂组成, 基础 油主要起到载体、冷却的作用,添加剂则主要在金属表面形成定 因及对策 向吸附膜, 起到提高承载、减摩抗磨的作用。但在生产过程中, 经常会出现轧制油起泡的现象, 即轧制油以泡沫状出现在油箱和 轧制过程, 使得轧制油的润滑、冷却作用下降,同时会造成铝板板 型难以控制, 严重影响到表面质量。润滑油的起泡现象一般用起 泡力和泡沫稳定性来表示。起泡力表示生成泡沫的难易, 起泡力 制作人:尤凤霞 强的润滑油, 是由于在油液中除了有气体之外, 还有第三种物质 存在。而泡沫的稳定性与油面的粘度、可塑性和坚韧性等因素 有关, 表面粘度越大, 可塑性和坚韧性越好, 泡沫的稳定性越好, 泡 沫越难自动破灭 。
制作人:尤凤霞 制作人 尤凤霞
3.由设备原因引起的轧制油起泡对策 轧制油的循环过滤系统及其运行状况也是引起起泡的原因之 一。由过滤系统引起的起泡问题, 可通过定期更换滤纸(无纺布) , 按时加助滤剂解决。由其它设备原因引起的起泡, 应仔细排查, 对 设备进行检修改造, 即可解决起泡问题。尽量做好控制元件的检查 工作, 严格按要求调整控制气压, 尽量提高空气质量, 满足压力控制 系统和温度控制系统的要求 。
制作人:尤凤霞 制作人 尤凤霞
冷制油起泡的原因分析
冷轧铝板带材轧制油起泡的原 因及对策
1.轧制油的皂化 轧制油中的铝粉、铝屑含氧化铝较多, 随着轧制油中水分的增加(一 般不超过0.15 mg/kg) , 并与水溶液结合易形成皂乳溶液, 皂化的成分会降 低油的表面张力, 容易起泡且泡沫难以破灭, 积累留存; 同时水分进入到轧 制油中起到了表面活性剂的作用, 不仅对金属有腐蚀, 而且在轧制过程中 油温的升高使水分挥发, 生成了气泡, 加之油压大及油落差大产生冲击, 是 形成沫体的原因之一。 2.轧制油质量下降 轧制油中含大量的不饱和烷烃, 易氧化而导致酸值升高, 从而造成油 制作人:尤凤霞 品质量下降。同时刚加入的尚未溶解的添加剂由于分子间的范德华力的 作用而聚集在一起, 并吸附轧制油中游散的铝粉细粒, 形成一个大的分子 团和极性团,使油品的起泡倾向大大增加。
冷轧铝板带材轧制油起泡的原因及对策
制作人:尤凤霞 制作人 尤凤霞
冷轧铝板带材轧制油起泡的原因及对策
冷轧铝板带材轧制油起泡的原 因及对策
2.恶化轧后产品质量 冷轧润滑效果主要表现在轧制过程中的力能参数和轧后铝 板表面质量。力能参数上可以使轧制压力下降, 而工艺润滑对表 面质量是至关重要的。一方面, 铝板带板形对辊型变化敏感, 而 工艺润滑剂的冷却能力是控制辊型的有力手段, 提高润滑剂的冷 却能力可减少轧件变形不均匀, 控制板型; 同时工艺润滑可减少 轧辊磨损, 可提高轧制板带板的尺寸精度。另一方面, 工艺润滑 剂可清洗轧件表面, 改善制品表面质量, 降低轧后表面粗糙度, 减 少板面产生划伤、腐蚀等表面缺陷。 3.轧制油的寿命降低 制作人:尤凤霞 油品质量直接影响到轧制油的使用性能和加工后制品的质 量。轧制油中有了泡沫后, 与空气接触面积增大, 再加上油温高, 因此加剧了油品的氧化变质,影响润滑效果, 使轧制油在使用中油 膜强度降低, 从而缩短了轧制油的换油周期, 轧制油的使用寿命 降低, 增加了铝板带材的生产成本。
制作人:尤凤霞
制作人:尤凤霞 制作人 尤凤霞
三.轧制油起泡的对策 轧制油起泡的对策
冷轧铝板带材轧制油起泡的原因及对策
冷轧铝板带材轧制油起泡的原 因及对策
轧制油抗泡的方法较多, 归纳起来可分为以下3种: 物理抗泡法, 即对轧制油进行冷却; 机械抗泡法; 化学抗泡法, 即添加消泡剂 1.由皂化原因引起的起泡对策 对于由皂化原因引起的起泡, 可加强对购买油品的水分检查。经 油水分离器处理后还有一部分沉积水和溶解水可用机械的方法去除, 结合水经加热70~80 ℃转变为溶解水而去除。对于含有大量铝屑、 铝粉、灰尘及其它微小颗粒的轧制油, 采用过滤系统过滤时要符合过 滤精度的要求, 在一定时间间隔内要向滤层涂上一定剂量的助滤剂(硅 藻土和活性白土的混合物) , 定期吹扫更换过滤纸等。 2.由轧制油质量不佳引起的起泡对策 制作人:尤凤霞 轧制油使用一段时间后质量下降引起的起泡可采用消泡剂解决, 同时尽量防止轧制的氧化, 如控制好油温, 避免油在高温下运行, 对油 及时进行冷却。轧机的液压油尽量使用轧制油或者使用与轧制油相 同类型的矿物油, 以减少轧机漏油引起的轧制油质量下降, 此种方法 取决于轧机的装机水平。经常测定轧制油的浓度、粘度和酸值, 来了 解外来油的混入量, 判断其变质程度。
制作人:尤凤霞 制作人 尤凤霞
冷轧铝板带材轧制油起泡的原因及对策
冷轧铝板带材轧制油起泡的原 3.轧机漏油的影响 轧制油受到液压油、齿轮润滑油和油雾润滑油等油品的污染后, 轧制 因及对策 油起泡倾向增加。这是因为, 轧制油的溶解能力较低, 不能充分溶解各种极
性添加剂和混入的液压油、润滑油等高粘度油品, 长碳链的分子在范德华 力的作用下发生聚集, 形成大分子团的胶体,吸附在油- 气界面而使润滑油表 面张力降低, 在一定的条件下, 使轧制油起泡倾向增大。 4.设备原因引起的轧制油起泡 总结起泡原因如下: ( 1) 过滤净化效果差;( 2) 污油箱泡沫或脏物进入净 油箱; ( 3) 轧机集油盘导路被污物阻塞造成大量冲击泡沫; (4) 喷射装置中的 喷嘴阀门膜片破损, 导致压缩空气进入轧制油;( 5) 轧机板面吹扫用空气质 量不良; ( 6) 油箱进入水;( 7)系统泄漏; (8) 管路内有存气等等。