Moldflow注塑报告
注塑模流分析报告格式范例

此方案满足成型
备注
/ / Z方向收缩量
图示变形比例 不包括缩水变形量
1 -4.5~9.3mm
翘曲
结论及建议
评估项目 进胶方案
成型
外观 翘曲 最终结论
分析结果
成型采用.5点针阀热嘴转斜顶进胶 充填顺畅,无明显滞流 压力,98.12MPa 锁模力,105t
熔接线:表面熔接线见P16 气穴:注意筋位、扣位、boss柱及分型面排气
产品表面熔接线上图颜色线所示,均由孔位导致,无法避免。
达到顶出温度的时间
达到顶出温度的时间说明 大部分区域14s左右达到顶出温度。
体积收缩率
体积收缩分布说明
充填末端收缩较大,注意加强保压。
缩痕估算
体积收缩分布说明
0.07mm,有缩痕风险;
翘曲
测量产品变形的基准 (三个基准点构成)
变形说明
图示变形比例 总变形量
产品3D图片
数据版本号(数据路径)
零件编号 模具编号 零件名称 CAD模型版本 Moldflow版本 Moldflow工程师
日期
/
/ / 亮饰条 UG9.0 Moldflow 2016
2022.02.01
分析信息说明
产品/注塑机信息
功能纹
说明产品外观面及要求
结构要求
说明产品安装位置
变形要求
说明产品匹配面的位置
流动前沿温差 材料推荐成型温度范围 流前温度判断说明
19℃
产品外观面温差 13℃
230℃ ~ 270℃
产品流动前沿温度分布均匀,且不超过熔融温度±20℃。
注射压力
喷嘴压力最大时刻 保压时间 压力曲线说明
moldflow分析报告
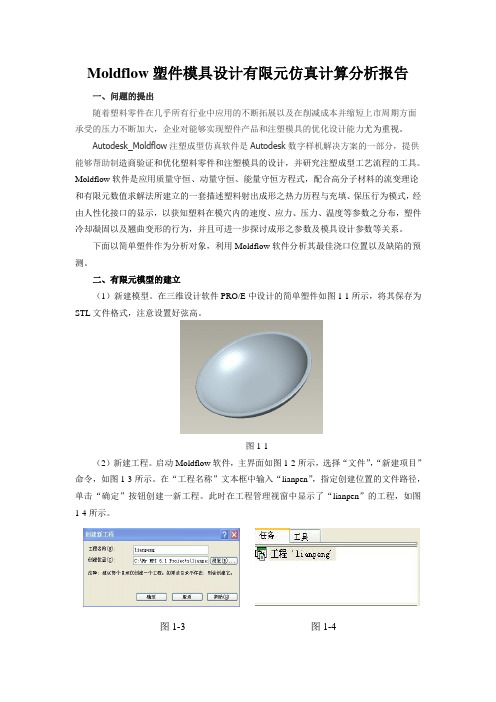
Moldflow塑件模具设计有限元仿真计算分析报告一、问题的提出随着塑料零件在几乎所有行业中应用的不断拓展以及在削减成本并缩短上市周期方面承受的压力不断加大,企业对能够实现塑件产品和注塑模具的优化设计能力尤为重视。
Autodesk_Moldflow注塑成型仿真软件是Autodesk数字样机解决方案的一部分,提供能够帮助制造商验证和优化塑料零件和注塑模具的设计,并研究注塑成型工艺流程的工具。
Moldflow软件是应用质量守恒、动量守恒、能量守恒方程式,配合高分子材料的流变理论和有限元数值求解法所建立的一套描述塑料射出成形之热力历程与充填、保压行为模式,经由人性化接口的显示,以获知塑料在模穴内的速度、应力、压力、温度等参数之分布,塑件冷却凝固以及翘曲变形的行为,并且可进一步探讨成形之参数及模具设计参数等关系。
下面以简单塑件作为分析对象,利用Moldflow软件分析其最佳浇口位置以及缺陷的预测。
二、有限元模型的建立(1)新建模型。
在三维设计软件PRO/E中设计的简单塑件如图1-1所示,将其保存为STL文件格式,注意设置好弦高。
图1-1(2)新建工程。
启动Moldflow软件,主界面如图1-2所示,选择“文件”,“新建项目”命令,如图1-3所示。
在“工程名称”文本框中输入“lianpen”,指定创建位置的文件路径,单击“确定”按钮创建一新工程。
此时在工程管理视窗中显示了“lianpen”的工程,如图1-4所示。
图1-3 图1-4图1-2(3)导入模型。
选择“文件”,“输入”命令,或者单击工具栏上的“输入模型”图标,进入模型导入对话框。
选择STL文件进行导入。
选择文件“lianpen.stl”。
单击“打开”按钮,系统弹出如图1-5所示的“导入”对话框,此时要求用户预先旋转网格划分类型(Fusion)即表面模型,尺寸单位默认为毫米。
图1-5单击“确定”按钮,脸盆模型被导入,如图1-6所示,工程管理视图出现“lp1_study”工程,如图1-7所示,方案任务视窗中列出了默认的分析任务和初始位置,如图1-8所示。
基于Moldflow的塑料件注塑工艺分析
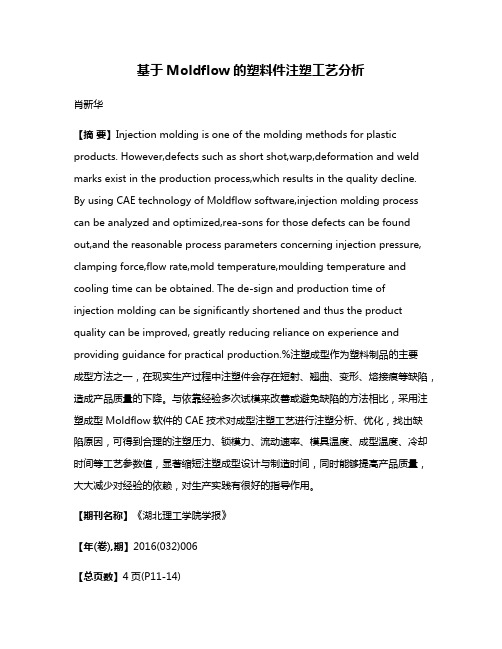
基于Moldflow的塑料件注塑工艺分析肖新华【摘要】Injection molding is one of the molding methods for plastic products. However,defects such as short shot,warp,deformation and weld marks exist in the production process,which results in the quality decline. By using CAE technology of Moldflow software,injection molding process can be analyzed and optimized,rea-sons for those defects can be found out,and the reasonable process parameters concerning injection pressure, clamping force,flow rate,mold temperature,moulding temperature and cooling time can be obtained. The de-sign and production time of injection molding can be significantly shortened and thus the product quality can be improved, greatly reducing reliance on experience and providing guidance for practical production.%注塑成型作为塑料制品的主要成型方法之一,在现实生产过程中注塑件会存在短射、翘曲、变形、熔接痕等缺陷,造成产品质量的下降。
注塑成型CAE报告(mlodflow分析报告)

材料成型CAE论文(Moldflow注塑工艺分析)在Moldflow Plastic Insight 6.0环境中,运用MPI的各项菜单及其基本操作,来实现对所选制件在注塑成型过程中的填充、流动、冷却以及翘曲分析,以此来确定制件的最佳成型工艺方案,为工程实际生产提供合理的工艺设置依据,减少因工艺引起的制件缺陷,有助于降低实际生产成本,提高生产效率。
一、导入零件导入文件guolingling.stp。
选择【Fusion】方式。
二、划分网格【网格】—【生成网格】—【立即划分】三、网格诊断【网格】—【网格诊断】,诊断结果如下:图1、网格诊断对诊断结果进行检查,发现连通区域为1,交叉边为0,最大纵横比为7.218616<8,均符合要求,网格划分合理。
四、选择分析类型1、浇口位置1)双击任务栏下的【充填】—【浇口位置】;2)选择材料:双击任务栏下的【材料……】—【搜索】—输入“ABS”—搜索—在结果中任选一种材料,点击【选择】即可;3)双击任务栏下的【立即分析】。
在分析结果中勾选:Best gate location,查看最佳浇口位置,如下图:图2、最佳浇口由最佳浇口位置分析结果可以知道,浇口设在零件上表面的中间部位,零件的注塑工艺效果好。
可采用直接浇口。
2、流动分析1)设置注射位置:设置之前,先将方案备份。
【文件】—【另存方案为】。
双击任务栏下的【设置注射位置】—鼠标变成一个十字光标和一漏斗形状,然后在上一步分析中的最佳浇口位置处单击,即可完成注射点的设置;2)选择分析类型:双击任务栏下【浇口位置】—【流动】;3)设置浇注系统:【建模】—【浇注系统向导】,设定直浇道、横浇道、内浇道的尺寸,各浇道尺寸均采取的默认值。
根据制件的形状特征以及最佳浇口位置,采用直接浇口。
4)双击任务栏下的【立即分析】。
查看分析结果中的“pressure at V/P swithover”项,发现出现了浇不足的现象,经分析是由于注射压力过小所引起的,只需增大注射压力即可。
(完整版)MOLDFLOW分析报告2024

引言概述:MOLDFLOW分析是一种重要的工具,广泛应用于塑料制品设计和生产过程中。
它可以提供关于模具充填、冷却和固化的详细信息,帮助设计师优化模具设计,提高产品质量和生产效率。
本文将通过分析报告的方式,详细介绍MOLDFLOW分析的应用和意义。
正文内容:一、模具充填分析1.熔体流动模拟:对熔体在模具中的流动进行模拟,可以分析熔体的充填情况、充填时间和充填压力等参数,以及可能出现的缺陷,如短充、气泡等。
2.塑料充填模拟:通过模拟塑料在模具中的充填过程,可以评估模具的设计是否合理,以及可能存在的充填不良、厚薄不均等问题。
3.充填时间分析:根据模具充填模拟的结果,可以计算出塑料充填的时间,从而优化生产周期和工艺参数。
二、冷却系统分析1.冷却效果模拟:通过模拟冷却系统的布局和工艺参数,在模具充填结束后,对模具进行冷却效果的分析。
可以评估冷却系统的设计是否合理,以及可能存在的冷却不均、温度过高等问题。
2.温度分布模拟:根据冷却系统分析结果,可以计算出模具内部的温度分布,帮助优化冷却系统的设计和工艺参数。
3.冷却时间分析:根据冷却系统模拟的结果,可以计算出模具冷却的时间,从而优化生产周期和工艺参数。
三、固化模拟分析1.熔体固化分析:通过模拟塑料在模具中的固化过程,可以评估模具冷却效果和固化时间,避免可能出现的缺陷,如收缩、变形等。
2.温度变化分析:根据固化模拟分析结果,可以计算出模具内部的温度变化曲线,帮助优化冷却系统和固化参数的设计。
3.固化时间分析:根据固化模拟分析的结果,可以计算出模具固化的时间,从而优化生产周期和工艺参数。
四、缺陷分析1.模具缺陷预测:通过模拟模具充填、冷却和固化的过程,可以预测可能出现的缺陷,如短充、气泡、收缩等,并给出相应的解决方案。
2.缺陷修复优化:根据缺陷分析结果,可以优化模具设计和工艺参数,减少缺陷的发生,并提高产品质量和生产效率。
五、效果验证与总结1.效果验证:通过对MOLDFLOW分析结果与实际生产产品进行对比,验证分析的准确性和可靠性,并修正和改进分析模型。
注塑模流分析报告

华东交通大学螺丝刀盒moldflow实训说明书Administrator2015/11/30课程:材料成型计算机仿真学校:华东交通大学学院:机电工程学院专业:材料成型及控制工程班级:2012模具2班姓名:覃钊学号:20120310040指导老师:匡唐清1、三维造型利用UG8.0设计出模型如下图1.1、1.2表示图1.1 实物图图1.2三维图模型参数长宽高为143*85*19.5,主壁厚为1.5mm。
二维图如图1.3图1.3二维图壁厚均匀,但在盖钩和挂孔处厚度和壁厚相差较大,体积收缩率在这两个地方应该会出现一些问题。
主分型面在上表面,侧面有卡勾及圆孔,需要做侧抽芯。
材料选用普通PP材料。
模型建好之后导出为IGES格式。
2、模型修复与简化打开CAD Doctor后导入IGES模型,检查并修复,直到所有错误都为0,修复完成之后将模型导出,格式为udm格式。
3、moldflow模流分析3.1网格划分(1)新建工程,输入工程名称,导入模型,在导入窗口选择双层面。
(2)网格划分,网格变长取壁厚的3倍,为4.5mm,合并容差默认为0.1,启用弦高控制0.1mm,立即划分网格,划分之后打开网格统计,看到网格的基本情况,不存在自由边和多个连通区域的问题后进行下一步。
一般来说初始划分的网格纵横比都比较大,所以要进行修复。
纵横比诊断结果如图3.1.1:最大纵横比达到了45.57。
图3.1.1初次纵横比诊断3.2网格诊断与修复点击【网格】——【网格修复向导】,前进到选择目标纵横比,输入6,点击修复。
之后在进行手动修复,通过合并节点移动节点等方式进行,直到得到满意的结果。
如下图3.2.1:图3.2.1修改后的纵横比诊断修复后的纵横比为13.68,只出现少数,可以接受。
修复后的网格统计如下图3.2.2:图3.2.2网格统计由统计结果知,匹配率都达到了91%以上,合理。
3.3确定浇口位置重复上述方案并冲命名为【浇口位置确定】,设置分析序列为【浇口位置】,选择材料为默认的PP材料(由于产品上信息为PP,且没有太高使用要求故选用默认的PP材料),该材料的推荐工艺如下图3.3.1:最大剪切速率为100000(1/s),最大剪应力为0.25MPa。
代做dfm分析和moldflow报告

代做dfm分析和moldflow报告DFM(Design for Manufacturability,中文为可制造性设计)分析和Moldflow(模流分析)报告是在产品设计和制造过程中的两个重要环节。
DFM分析旨在优化产品设计,使其更易于生产和制造,并提前发现潜在的问题和缺陷。
而Moldflow报告则是用来预测注塑成型过程中可能发生的问题,从而指导制造商进行相应的调整和改进。
在进行产品设计之初,进行DFM分析可以帮助设计师发现并解决潜在的生产制造问题。
这种分析通常是由专业的团队完成,他们会评估设计方案的可制造性,包括材料的选择、零件加工、工艺流程等等。
DFM分析旨在提高产品的质量、降低制造成本并缩短生产周期。
通过对设计文件的仔细审查,DFM分析可以发现设计中可能存在的问题,如零件结构过于复杂、尺寸容差过大或过小、加工难度大等等。
通过提前识别这些问题,设计团队可以及时进行调整和改进,从而避免后期生产过程中的问题和延误。
一旦产品设计完成,并确定采用注塑成型工艺进行生产制造,Moldflow分析就变得尤为重要。
Moldflow是一种计算机模拟技术,在注塑成型过程中提供准确的预测和模拟,从而更好地指导制造商进行生产。
通过模拟注塑成型过程中的温度、压力、填充速度等参数,Moldflow可以帮助制造商预测可能出现的问题,如气泡、翘曲、收缩等等。
这些问题在生产过程中可能会引发零件变形、裂纹、尺寸偏差等质量问题。
通过提前进行Moldflow分析,制造商可以针对性地调整注塑工艺参数,例如模具温度、注射速度、注射压力等,以优化产品的质量和一致性。
需要强调的是,在进行DFM和Moldflow分析时,设计师和制造商需要紧密合作。
设计师应根据制造商的意见和建议进行相应调整,并充分考虑产品的可制造性。
制造商则应准确提供产品的材料和工艺参数以及所需的注塑设备信息。
通过有效的沟通和协作,DFM和Moldflow的分析结果可以为产品的质量、成本和生产周期提供有力支持。
Moldflow分析报告结果解释大全

一流动分析部分1 Fill time result填充时间填充时间显示了模腔填充时每隔一定间隔的料流前锋位置。
每个等高线描绘了模型各部分同一时刻的填充。
在填充开始时,显示为暗蓝色,最后填充的地方为红色。
如果制品短射,未填充部分没有颜色。
使用:制品的良好填充,其流型是平衡的。
一个平衡的填充结果:所有流程在同一时间结束,料流前锋在同一时间到达模型末端。
这个意味着每个流程应该以暗蓝色等高线结束。
等高线是均匀间隔,等高线的间隔指示了聚合物的流动速度。
宽的等高线指示快速的流动,而窄的等高线指示了缓慢的填充。
查看项目:确认填充行为的显示状况。
短射—在填充时间结果上,短射将显示为半透明的,查看流动路径的末端是否有半透明区域。
关于3D模型, 可以使用未填充的模穴(短射)结果来检查是否在制品的内部存在未充填的部分。
滞流—如果填充时间结果显示一些区域上的云图有很近的间隔,将产生滞流。
如果一个薄区域在制品完全填充之前冻结滞流会导致短射。
过保压—如果填充时间结果显示某个流程的流程之前完成,将显示过保压。
过保压会导致高的制品重量、翘曲和不均匀的密度分布。
????熔接线和气穴—在填充时间结果上重叠熔接线结果可以确定其存在,熔接线会导致结构和视觉上的缺陷。
气穴—在填充时间结果上重叠气穴结果可以确认其存在,气穴会导致结构和视觉上的缺陷。
跑道效应—跑道效应会导致气穴和熔接线,查看气穴和熔接线的位置及数量。
2 Pressure at velocity/pressure switchover resultV/P切换时刻的压力该结果从流动分析产生,显示了通过模型内的流程在从速度到压力控制切换点的压力分布。
使用:在填充开始前,模腔内各处的压力为零(或者为大气压,绝对压力)。
熔料前沿到达的位置压力才会增加,当熔料前沿向前移动填充后面的区域时压力继续增加,此取决于该位置与熔料前沿的长度。
各个位置的压力不同促使聚合物熔料的填充流动,压力梯度是压力差除以两个位置间的距离。
MOLDFLOW完整分析报告
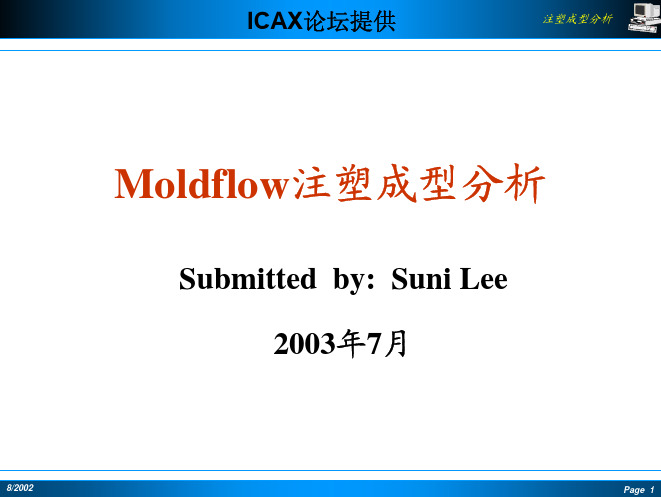
8/2002
Page 7
ICAX论坛提供 成型工艺条件:
填充时间:2.5秒 冷却时间:20秒 模具温度:80度 熔料温度:295度 冷却水温度:25度 冷却液控制方法:雷络数控制(雷络系数=10,000) 保压曲线: 时间(秒) 2 3 保压压力 填充压力的70% 填充压力的60%
注塑成型分析
8/2002
RHEOLOGY: The material's rheological behavior was tested by Moldflow by an injection molding rheometer. Data was last updated on 29-JUN-01. This method exposes the sample to shear, temperature, and pressure history similar to those in injection molding. Studies performed by Moldflow Plastics Labs have shown the use of injection molding rheology data contribute to improved comparisons between experimental mold pressure traces and simulation results of molding pressure during the filling stage. This data is per Moldflow Plastics Labs current recommended best method for process simulation CAE. The method used applies well to most materials and applications.
moldflow报告

华东交通大学Moldflow实训报告11级材料成型及控制工程(模具)-1潘俊宇20110310040122目录一、前言 (3)二、工艺设计与分析 (3)2.1源文件 (3)2.2网格划分 (4)2.3浇口位置的确定 (8)2.4成型窗口分析 (9)2.5充填分析 (13)2.6流道系统的构建与优化 (17)2.7冷却分析及优化 (19)2.8保压分析及优化 (24)2.9翘曲分析及优化 (29)三、总结 (30)一、前言本次Moldflow实训目的在于掌握、熟悉Moldflow2012软件,同时训练注塑模具的设计过程中相关的工艺参数的设定。
要求掌握一定的高分子(塑料)知识和成型原理,同时必须掌握注塑模具的设计和原理。
此次,我的“手机后盖的注塑成型”就是根据上述要求完成的。
这次使用的实物原件是一个普通的手机后盖,使用Pro.e三维软件造型,在Moldflow2012中经历了网格划分及调整、成型窗口分析、浇口流道及冷却水路的创建、充填分析、冷却分析、保压分析、翘曲分析等等程序,在多次修改成型工艺方案后最终确定了能获得较好成型质量的相关工艺参数。
二、工艺设计与分析本次手机后盖的注塑分析是借助注塑模Moldflow软件对传统注塑生产注射工艺过程的模拟,为制品设计、材料选择、模具设计,注射工艺的制定及注射过程的控制提供科学依据。
注塑模CAE技术借助于有限元法、有限差分法和边界元法等数值计算方法,分析型腔中塑料的流动、保压和冷却过程,计算制品和模具的应力分布,预测制品的翘曲变形,并由此分析工艺条件、材料参数及模具结构对制品质量的影响,达到优化制品和模具结构、优选成型工艺参数的目的。
2.1源文件本次使用的是一个手机后盖,应用Pro.e软件经拉伸、倒角、打孔、去除、抽壳等等方法仿制实物而成。
图2.1-1 三维实体零件图2.2网格划分Moldflow网格模型是Moldflow分析的基础,良好的网格质量是获取准确分析结果的前提。
基于MOLDFLOW的塑料件注射成型方案分析

熔接痕的影响[J]. 轻工机械,2007,25( 1) : 24 - 27. [4]郑建,胡治流,何娟. moldf low 在注塑模在设计中的
应用[J ]. 装备制造技术,2006,( 4) : 44 - 54.
74
江西化工
2011 年第 4 期
基于 MOLDFLOW 的塑料件注射成型方案分析
郑志刚 余筱勤 钟 勤
( 江西陶瓷工艺美术职业技术学院材料工程系,江西 景德镇 333000)
摘 要:借助计算机辅助工程( CAE) 软件 moldflow 的模流分析功能,对鼠标外壳件塑 件进行了填充、流动前沿温度、压力、熔接痕及表层取向、螺杆行程等模拟分析。确定了最 优设计方案,并且结合模拟结果,介绍了注塑模 CAE 技术对塑件模具优化设计的重要作 用: CAE 技术可以有效地简化设计过程,提高设计效率,降低模具的报废率。
两点进胶,在产品的中部会产生一条细长的熔接痕,但 熔接时溶体温度较高,熔接质量较好,不会影响产品强 度,但熔接痕迹还是会有,由图 7 结合模拟表层取向结 果显示不影响产品外观[3]。
图 7 表层取向
图 8 流动前沿温度
( 4) 流动前沿温度 图 8 为流动前沿温度模拟结果。从图中可以看 出,此模型的模温分布比较均匀,说明熔体在流动过程 中温度下降 缓 慢,利 于 填 充,且 该 产 品 温 度 降 幅 较 小, 这意味着该塑件的表面质量将会得到保证。由图 8 分
关键词:moldflow 模流分析 注塑模 CAE 优化设计
1 前言 Moldflow 技术无论在提高生产率、保证产品质量,
注塑件moldflow模拟报告

最大锁模力为:5600.18t,最大注射压力为:140.00Mpa,最佳浇口位置附近的节点编号为N6888.
最佳浇口位置:
最佳浇口位置
深蓝色部分即为最佳浇口位置。
Fill过程分析结果:
由上图看到,熔体几乎同时到达制品的边缘,说明浇口位置设置合理。
熔体流动前沿温度分布图
可以看出,温度分布基本均匀,温差值为3.3℃,小于允许值20℃,符合注射成
型的要求。
浇口处压力曲线如图所示,不存在压力不稳定现象。
气穴的位置大多数位于制品表面,可通过分型面排掉。
熔接痕位置
孔洞部分附近是必然会产生熔接痕的
Flow分析结果:
缩凹结果
由图可以看到最大缩凹为5.081%,这是由于该处厚度比较大,通过修改厚度,可以减少缩
凹。
锁模力随时间变化曲线
第一主方向残余应力
理论上,残余应力的正值表示处于拉伸状态,负值表示压缩状态,数值越大对产品越不利。
Cool分析结果:
制件冷却时间
从上图可看出,冷却液的出口温度和入口温度差为0.34,说明冷却液的冷却能力没有问题。
冷却管道温度分布
该结果显示了冷却管道温度分布。
这个温度不能高于冷却介质温度的5°C。
由上图可知符
合要求。
制件表面温度。
MOLDFLOW模流分析报告
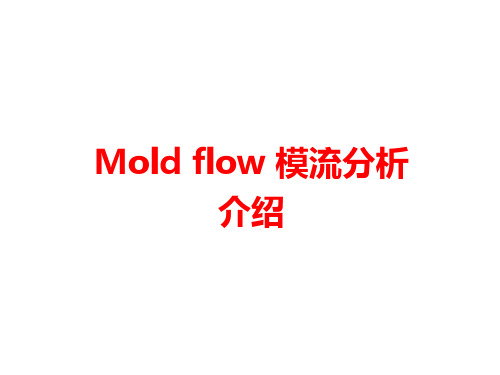
STEP 10-选择分析类型
填充
快速填充
流动 冷却 成型窗口 最佳浇口位置 流道平衡 冷却+流动+翘曲 流动+收缩 冷却+流动+收缩
常用分析类型
分析熔融塑胶在注塑段的填充行为 快速模拟熔融塑胶在注塑段的填充行为,分析的输出结果较正常 填充少 分析熔融塑胶在注塑段的填充行为和保压效果 分析保压结束后,运水管道的冷切效果 提供最佳成型参数和合理的成型工艺参数 产品上最佳进浇位置和产品上不同区域作为进浇口的合理性程度 从填充平衡的角度优化流道的尺寸 完整的模拟分析产品的成型过程和翘曲 分析熔融塑胶在型腔内的流动以及产品的收缩情况 分析熔融塑胶的流动和冷却管道的冷却效果得出产品收缩值
Mold flow 模流分析 介绍
珠海优特电力科技股份有限公司
引子
我们遇到了哪些问题?
2
引子
短射
3
引子
飞边
4
引子
银条纹
5
引子
流痕
6
引子
应力痕
7
引子
冲击纹
8
引子
缩水
9
引子
熔接痕
10
引子
发脆
11
引子
翘曲
12
引子
预避知 如何改变传统的依靠经验的
“试错”的设计模式?
13
目录
1 MOLDFLOW简介 23 MOLDFLOW分析流程介绍 43 产品缺陷判定及优化对策
MOLDFLOW简介
优化制品形 状和结构
优化模具结构
优化注塑工艺 参数
18
MOLDFLOW简介 功能1
最佳浇口位置分析
根据塑件的形状结构,分析出最佳的胶口位置。
moldflow 注塑成型分析 模流分析报告

1. 熔体密度 2.实体密度 3.顶出温度 4.推荐模具温度 5.推荐熔料温度 6.材料失效温度
0.88 g/cu.cm 1.06 g/cu.cm
119 deg.C 45 deg.C 225 deg.C 290 deg.C
7. 熔料温度下限 8. 熔料温度上限 9. 模具温度上限 10.模具温度下限 11.最大剪切速率 12.最大剪切应力
Page 8
体积收缩
体积收缩结果用来判断产 品各处的体积收缩情况,收 缩不均匀会造成翘曲变形, 收缩较大则造成缩痕。 由图可见产品内部收缩较小, 且比较均匀。出现缩痕风险 小。
Page 9
困气位置
1
Air traps可提供模具的困气位 置。air traps产生在填充末端包 括高rib和boss柱位置、结合线、 流动包封位置。故而在这些位置 一般需要开设排入槽或排气入子。 另外在熔体温降较大处也应增加 排气,提高流动性。
pagepage1919尾部分子剪切作用较高故而分子取向度高并且分子结晶度高取向诱导结晶在取向方向上收缩较大故而收缩应力导致产品尾部收拉力而张开变形
Moldflow注塑成型分析
For
滨海
Reporter : 孟栋梁 sduan@
2010-07-16
分析描述
▪ 产品描述 此是汽车用产品,使用热浇道系统注射成型。
200.0 deg.C 250.0 deg.C 30.0 deg.C 60.0 deg.C 100000.0 1/s
0.25 Mpa
PVT Plow材料数据库
Page 3
工艺条件
注塑机设定:
最大锁模力:
未限定
最大注塑压力:
未限定
最大注射速度:
结合线
Moldflow模流分析经典报告(简体版)
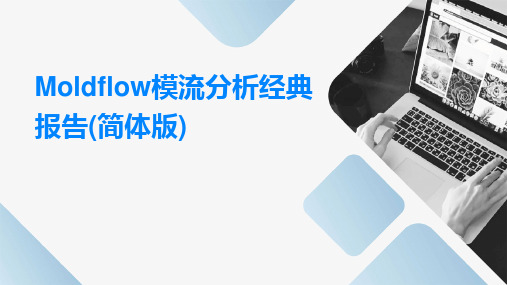
设置注射压力、注射速度、注射温度等边界条件。
塑化边界条件
设置塑化温度、塑化速度等边界条件。
模拟求解与结果分析
模拟求解
根据设置的边界条件进行模拟求解。
结果分析
对模拟结果进行分析,如压力分布、温度分布、流动行为等。
结果优化
根据分析结果对模型进行优化,提高成型质量和效率。
Moldflow模流分析
Moldflow模流分析是一种计算机模 拟技术,用于预测塑料模具填充、流 动、冷却和翘曲等行为,从而优化模 具设计和产品成型过程。
通过模拟分析,Moldflow可以帮助工 程师预测和解决模具制造和塑料产品 成型过程中可能出现的问题,减少试 模次数和缩短产品上市时间。
Moldflow模流分析的重要性
2. 翘曲变形分析不准确
翘曲变形是塑料成型过程中的常见问题,分析不准确可能导致模具优化措施失效。
3. 解决方案
加强Moldflow模流分析理论学习,深入理解流动前沿、翘曲变形等关键指标的含义和影 响。结合实际案例进行分析和总结,提高模拟结果解读能力。积极参与行业交流和技术培 训,不断更新知识和技能。
Moldflow模流分析的应用领域
汽车行业
01
Moldflow在汽车行业中广泛应用于汽车零部件的模具设计和产
品成型过程优化,如保险杠、仪表盘和座椅等。
电子产品
02
Moldflow模流分析可用于手机、电视、电脑等电子产品的模具
设计和产品成型过程优化。
包装行业
03
Moldflow可以帮助包装企业优化包装盒、瓶盖等产品的模具设
案例三:热流道系统模拟
总结词
热流道系统是塑料加工中常用的技术,通过加热模具流道来控制塑料熔体的温度和流动。 Moldflow模流分析可以用于热流道系统的模拟和优化。
Moldflow注塑模具成型过程分析实例_完整经典
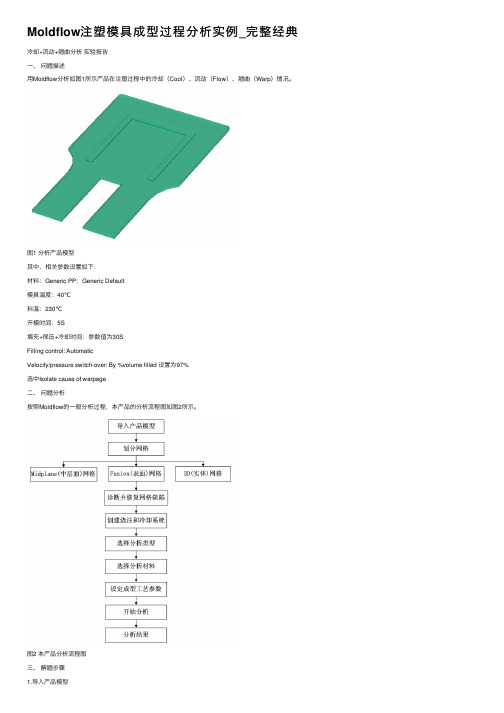
Moldflow注塑模具成型过程分析实例_完整经典冷却+流动+翘曲分析实验报告⼀、问题描述⽤Moldflow分析如图1所⽰产品在注塑过程中的冷却(Cool)、流动(Flow)、翘曲(Warp)情况。
图1 分析产品模型其中,相关参数设置如下:材料:Generic PP:Generic Default模具温度:40℃料温:230℃开模时间:5S填充+保压+冷却时间:参数值为30SFilling control: AutomaticVelocity/pressure switch-over: By %volume filled 设置为97%选中Isolate cause of warpage⼆、问题分析按照Moldflow的⼀般分析过程,本产品的分析流程图如图2所⽰。
图2 本产品分析流程图三、解题步骤1.导⼊产品模型点击File→Import,选取待分析的产品模型,点击“打开”。
在弹出的“模型导⼊选项设置”对话框中,⽹格类型选“Fusion”,模型单位设置为“Millimeters”。
单击“OK”完成设置。
此时弹出“项⽬创建”对话框,在“Project”⼀栏设置项⽬名称,本实验取名为“CFW”。
在“Create in”⼀栏选取项⽬保存地址。
单击“OK”完成项⽬创建。
此时,窗⼝中会显⽰出导⼊的模型。
以防分析中修改变动,习惯先对模型进⾏复制。
对着左上⾓“Project”栏内的模型名称,在右击菜单中选择“Duplicate”,完成模型复制。
其后操作都在复制的模型中进⾏。
⼀般在做流动分析时,要求产品锁模⼒⽅向(⼀般也为产品分型⾯的垂直⽅向)与Z轴的正⽅向⼀直。
此时的模型位姿不对(如图3所⽰),需要⽤旋转命令对模型进⾏旋转操作。
执⾏Modeling→Move\Cope→Rotate,在左侧选项栏中,点击“Select”⼀栏的选框,其意思为选取旋转对象,框选产品模型。
“Axis”⼀栏选取X轴。
“Angle”填写90。
(完整版)MOLDFLOW分析报告

Moldflow Analysis Report 塑料材料簡介
PPE+PS+40%GF Xyron X1764 Asahi Kasei Corporation
1. Melt Density 1.2827 g/cu.cm 2. Solid Density 1.3645 g/cu.cm 3. Ejection Temperature 110.000000 deg.C 4. Recommended Mold Temperature 75 deg.C 5. Recommended Melt Temperature 275 deg.C 6. Absolute Max. Melt Temperature 340 deg.C
Moldflow Analysis Report
Moldflow模流分析報告
B039பைடு நூலகம்901
Page 1
Moldflow Analysis Report 内容提要
1. 分析说明一 2. 塑料材料简介 3. 产品模型简介 4. 分析模型简介 5. 原始方案浇注系统设计 6. 原始方案冷却系统设计 7. 原始方案基本成型条件 8. 原始方案分析结果 9. 结论与建议 1 10.分析说明二 11.改善方案1浇注系统设计 12.改善方案1冷却系统设计 13.改善方案1基本成型条件 14.改善方案1分析结果 15.结论与建议 2 16.分析说明三 14.改善方案2浇注系统设计 15.改善方案2冷却系统设计 16.改善方案2基本成型条件 17.改善方案2分析结果 18.结论与建议 3
Page 2
Moldflow Analysis Report 分析说明一
➢如下图的产品,为复印机上的零件,对尺寸精度要求较高。采用PPE+PS+40%GF的塑 料以热流道成型,产品结构与进浇位置均已确定,客户希望通过调整冷却水路或冷却条件 将整个周期时间缩短,因此藉以Moldflow模流分析验证是否可行。 ➢因Moldflow材料数据库内暂无客户使用的GE PPE+PS+40%GF塑料,故在分析中使用 物性较为相似的Asahi Kasei Corporation的PPE+PS+40%GF塑料来代替,在数值上会与 实际试模有差异,但趋势是一致的。此报告中以几种方案进行分析比较,其中Original n 为客户原始设计方案,Revised n为我们基于Moldflow上的改善方案。
模流分析报告

V/P切换时,注塑压力在产品上的压力梯度分布比较均匀。
Result : Injection Pressure
在填充阶段,最大的注塑压力为76.0Mpa.
Result : Volumetric Shrinkage Distribution
产品整体的收缩比较均匀,红色位置的收缩比较大。
Result : Displacements, hardware final shift (x5)
Moldflow Analysis Report
Runner System
浇口改为1端侧浇口
Result : Fill Pattern
Result : Temperature Distribution (Melt Front)
熔体前锋的温度分布比较均匀。
Result : Pressure at V/P switchover
五金件在Y方向的变形较大, 红色位置会移动0.86mm 0.86mm
五金件在Z轴上有较小的变 形,红色位置会移动0.05mm 0.05mm
五金嵌件在填充过程中,会产生较大的变形,约为0.87mm.
Result : Von Mises Stress, core
五金嵌件在填充过程中受力不均匀。
Conclusions From the above analysis: 将产品的浇口位置改为此处,对五金件的变形没有改善,变形量比原方案还要 大。
- 1、下载文档前请自行甄别文档内容的完整性,平台不提供额外的编辑、内容补充、找答案等附加服务。
- 2、"仅部分预览"的文档,不可在线预览部分如存在完整性等问题,可反馈申请退款(可完整预览的文档不适用该条件!)。
- 3、如文档侵犯您的权益,请联系客服反馈,我们会尽快为您处理(人工客服工作时间:9:00-18:30)。
材料成型CAE论文(Moldflow注塑工艺分析)姓名:学号:班级:基于MPI的塑料模具成形仿真实验指导书一、实验目的1.了解注塑模模拟仿真软件MPI-Moldflow Plastic Insight的功能;2.熟悉Moldflow Plastic Insight各个菜单和工具栏;3.运用实例初步掌握Moldflow Plastic Insight的成形分析流程;4.独立完成范例文件的塑性成形分析。
二、实验内容1.介绍Moldflow Plastic Insight软件的菜单、工具栏、显示控制、图层控制及文件接口等;2.介绍Moldflow Plastic Insight软件分析流程;3.学生在教师指导下完成示例模型的成形分析,并提交成形分析报告。
三、实验设备1.每个学生一台PC机,CPU:P5D2.8G,硬盘120G,内存,10242MB,显示器17LCD2. Moldflow Plastic Insight6.0中文版软件3.InternetExplorer软件四、实验原理1.注塑成形的基础知识所谓注塑成形(Injeetion Molding)是指将已熔化的材料喷射注入到模具内,经由冷却与固化后,得到成品的方法。
实验将运用Moldflow Plastic Insight软件来学习如何通过计算机仿真技术模拟塑件成形的过程,并估计成形缺陷、优化成形工艺参数,使学生掌握先进的注塑模设计手段和方法。
2.Moldflow软件介绍Moldflow 的产品适用于优化制件和模具设计的整个过程,并提供了一套整体解决方案。
Moldflow软硬件技术为制件设计、模具设计、注塑生产等整个过程提供了非常有价值的信息和建议,而且这些信息可以方便地实现共享。
下面介绍Moldflow的产品。
Moldflow Plastics Insight简称为MPI它是Moldflow动态系列的升级产品,是一个更为深入的制件和模具设计分析的软件集成体,它提供了强大的分析功能、可视化功能和项目管理工具。
这些工具使使用者可以进行深入的分析和优化。
MPI使用者可以对制件的几何形状、材料的选择、模具设计及加工参数设置进行优化,从而获得高品质的产品。
1)MPI具有集成的用户界面使用者可以方便地输入CAD模型、选择查找材料、建立模型并进行一系列的分析,同时先进的后处理技术能给使用者观察分析结果带来方便,还可以生成集成基于Insight的分析报告,方便实现。
2)提供了最为优秀的CAE模型获取集成方案MPI可以直接读取任何CAE集成方案,实现了最广泛的几何模型集成。
无论设计的几何模型是什么形式(包括线框模型、表面造型、薄壁实体以及难以用中型面来表达的厚壁实体),MPI都能提供已于使用的、稳定的、集成的环境来处理。
线框表面造型MPI可以直接读取任何CAD表面模型并进行分析。
在用户采用线框和表面造型文件时,MPI可以自动生成Midplane网格并准确计算单元厚度和进行精确的分析,因此节省了用户大量的CAE建模时间。
薄壁实体MPI的Fusion 模块基于Moldflow的独家专利的Dual Domain分析技术,使用户可以直接进行薄壁实体模型分析,这将原来需要几小时甚至几天的建模工作缩短为几分钟,并且无需进行中型面网格的生成和修改。
Fusion模块可以直接从塑件顾问(MPA)中读取模型,用来进一步的分析。
厚壁实体Moldflow的MPI/Flow3D和MPI/Cool3D等模块通过使用经过验证的、基于四面体的有限元体积网格解决方案技术,可以通过对厚壁产品和厚度变化较大的产品进行真实的三维模拟分析。
3)拥有广泛、深入的模拟分析工具MPI能够模拟最广泛的热塑性塑料和热固性塑料注射成型中的制造工艺。
具体地说就是MPI可以模拟热塑性塑料注射成型过程中的充填、保压以及冷却阶段,还能预测处制品成型后的缺陷,如制品翘曲变形等。
甚至能够分析纤维填充材料的流动情况,预测纤维的取向并在预测产品翘曲时加以考虑。
MPI还可以模拟其他各种热塑性塑料成型工艺,如砌体辅助注射成型、共注和注压成型以及反应成型过程,包括热固性注射成型、反应注射成型和半导体芯片封装。
●MPI/SynergyMPI/Synergy是一个前置和后置处理器,支持MPI系列产品的所有分析模式,分析组建提供塑料行业范围最广的成型模拟工具,MPI/Synergy环境支持传统的中性层模型、基于Moldflow专利(Dual Domain技术)的Fusion模型和3D实体模型。
●MPI/MidplaneMPI/Midplane不仅大大缩短了对塑件产品进行造型的时间,而且可以自动产生网格化的实体中型面,使用户可以致力与深入的工艺分析。
●MPI/FusionMPI/Fusion是处理CAD模型最方便的方法,在保证流动、保压、优化、冷却和翘曲等分析基础上,能够减少处理模型的时间。
在用户MPI使用组件进行热固性塑料模具分析时,也可以使用MPI/Fusion。
使用MPI/Fusion可以改进纸片和模具设计,确定材料和工艺条件,从而在质量、成本和时间上取得最佳组合。
●MPI/3DMPI/3D技术解决的是一类以前用传统的有限元方法无法解决的问题。
即在厚的部件中,熔融的塑料向各个方向上流动的这类问题。
通过使用基于实体四面体的有限单元网格,即使在由非常大的厚薄变化的情况下,MPI/3D技术也能在非常厚的实体上执行正真的、三维模拟。
●MPI/flow流动分析模块MPI/flow 可以模拟注射时的充模和保压阶段,预测热塑性材料的流动件,以便有效地得到高质量的产品。
运用MPI/flow,可以急性制品和模具设计,选择合适的材料和工艺条件,以取得质量、成本和时间的最佳平衡点。
●MPI/Cool冷却分析模块MPI/Cool通过分析冷却系统对流动过程的影响,达到优化冷却管路的布局和工作条件,Cool与flow模块相结合,可以产生十分万马的注塑过程分析结果。
这样可以改善冷却管路的设计,从而产生均匀的冷却,缩短成型周期,减少产品成型后的内应力。
●MPI/Wap翘曲分析模块MPI/Wap可使用户了解在注射成型过程中制品收缩和翘曲的原因,并且能预测变形发生的区域。
分析结果可使用户在模具制造之前,就可优化设计,选择适当的材料和工艺条件,使用MPI/Wap,即使是严格要求尺寸的稳定性,良好的表面质量及与其他部件精确配合的制品都能高质量、快速、低成本地制造出来。
3.注塑制品易出现的缺陷、原因和解决方法通过合理地运用Moldflow系列软件,可以预先估计出好的注塑制品及其模具中可能存在的缺陷,同时结合实际经验,就可以在开模之前分析缺陷出现的原因,并最终解决这些问题,从而减少修模、试模的次数,提高一次成功率。
注塑成型中产品出现缺陷有各种各样的原因,从材料、模具、工艺参数到成型设备都对制品的质量有着直接或间接的影星,这是一个综合因素的影响,出现产品缺陷一般有以下一些因素:●模具设计不合理●成型工艺参数选择不当●材料(聚合物)性质本身造成的产品缺陷●注塑成型设备(注塑机)选择不当(1)欠注欠注(Short Shot)也可以称为填充不足或短射,是指聚合物不能完全充满模具型腔的各个角落的现象。
1)产生欠注的原因●流动受限,由于浇注系统设计的不合理导致熔体流动受到限制,流道过早凝结●出现滞流或者制品流程过长,过于复杂●排气不充分,未能及时排出的气体会产生阻止流体前沿前进的压力,从而导致欠注发生●模具温度或者熔体温度过低,降低了熔体的流动性,导致填充不完全●成型材料不足,注塑机注塑量不足或者螺杆前端缺料等,都会造成压力损失和成型材料体积不足,形成欠注。
2)欠注的解决方案针对可能导致欠注发生的因素,应当从以下几个方面避免欠注产生。
●避免滞流现象的发生●尽量消除气穴,将气穴放置在容易排气的位置或者利用顶杆(cjcction pin)排放气体●增加模具温度和熔体温度●增加螺杆速率,螺杆速率的增加会产生更多的剪切热,降低熔体粘性,增加流动性●改进制件设计,使用平衡流道,并尽量减小制件厚度的差异,减小制件流程的复杂程度●更换成型材料,选用具有较小粘性的材料,材料粘性小,易于填充,而且完成填充所要求的注塑压力也会降低●增大注塑压力最大值(2)气穴气穴是指由于熔体前沿汇聚而在塑件内部或者模腔表层形成的气泡。
气穴的出现可能导致欠注的发生,造成填充不完全和保压不充分,形成最终制件的表面瑕疵,甚至可能由于气体压缩产生热量出现焦痕(burn mark).1)气穴成因●跑道效益●滞流●流长不平衡,即使制件厚度均匀,各个方向的流长夜不一定相同,导致气穴产生●排气不充分,在制件最后填充区域缺少排气口或者排气口不足是引起气穴形成最常见的原因2)解决方案●平衡流长●避免滞流和跑道效应的出现,对浇注系统作修改,从而使制件最后填充位置位于容易排气的区域●充分排气,将气穴放置在容易排气的位置或者利用顶杆排气(3)熔接痕和焊接线当两个或多个流动前沿融合时,会形成接痕和熔接线。
两者的区别在于融合流动前沿夹角的大小。
两个箭头为流动前沿方向,若图4-1中标注的角大于135°,则形成熔接痕。
图 4-1熔接线位置上的分子趋向变化强烈,因此该位置的机械强度明显减弱。
熔接线的强度大,视觉上缺陷也不如熔接线明显。
熔接痕和熔接线的出现的部位还可能出现凹陷、色差等质量缺陷。
1)熔接线和熔接痕成因由于制件的几何形状,填充过程中出现两个或者以上流动前沿时,很容易形成熔接痕或者熔接线。
2)解决方案●增加模具温度和熔体温度,使两个相遇的熔体前沿融合得更好●增加螺杆速率●改进浇注系统的设计,在保持熔体流动速率的前提下减小流道尺寸,以产生摩擦热。
●如果不能消除熔接线和熔接痕,那么应使其位于制件上较不敏感的区域,以防止影响制件的机械性能和表现质量,通过改变浇口位置或者改变制件壁厚可以改变熔接线和熔接痕的位置。
(4)滞流滞流式指某个流动路径上的流动变缓甚至停止。
1)滞流成因如果流动路径上出现壁厚差异,熔体会选择阻力较小的壁厚区域首先填充,这会造成薄壁区域填充缓慢或者停止填充,一旦熔体流动缓慢,冷却速度就会加快,粘度增大,从而使流动更加缓慢,形成循环,滞流通常出现在筋、制件上与其他区域存在较大厚度差异的薄壁区域等。
滞流会产生制件表面变化,导致保压效果低劣、高应力和分子趋向不均匀,降低制件质量。
如果质量的熔体前沿完全冷却,那么成型缺陷旧由滞流变为欠注2)解决方案●浇口位置远离可能发生滞流的区域●尽量使容易发生滞流的区域成为最后填充的区域●增加容易发生滞流区域的壁厚,从而减小其对熔体流动的阻力●选用粘度较小的成型材料●增加注塑速率以减少滞流时间●增大熔体温度,使熔体更容易进入滞流区域(5)飞边飞边时指在分型面或者顶杆部位从模具模腔溢出的一层材料。