优化设计报告
机械优化设计实验报告

一、实验目的本次实验旨在通过计算机编程,加深对机械优化设计方法的理解,掌握常用的优化算法,并能够利用计算机解决实际问题。
二、实验内容1. 黄金分割法(1)实验原理黄金分割法是一种常用的优化算法,适用于一元函数的极值求解。
其基本原理是:在给定初始区间内,通过迭代计算,逐步缩小搜索区间,直到满足收敛条件。
(2)实验步骤① 设计实验程序,实现黄金分割法的基本算法。
② 编写函数,用于计算一元函数的值。
③ 设置初始区间和收敛精度。
④ 迭代计算,更新搜索区间。
⑤ 判断是否满足收敛条件,若满足则输出结果,否则继续迭代。
(3)实验结果通过编程实现黄金分割法,求解函数f(x) = x^3 - 6x^2 + 9x + 1在区间[0, 10]内的极小值。
实验结果显示,该函数在区间[0, 10]内的极小值为1,且收敛精度达到0.001。
2. 牛顿法(1)实验原理牛顿法是一种求解非线性方程组的优化算法,其基本原理是:利用函数的导数信息,逐步逼近函数的极值点。
(2)实验步骤① 设计实验程序,实现牛顿法的基本算法。
② 编写函数,用于计算一元函数及其导数。
③ 设置初始值和收敛精度。
④ 迭代计算,更新函数的近似值。
⑤ 判断是否满足收敛条件,若满足则输出结果,否则继续迭代。
(3)实验结果通过编程实现牛顿法,求解函数f(x) = x^3 - 6x^2 + 9x + 1在区间[0, 10]内的极小值。
实验结果显示,该函数在区间[0, 10]内的极小值为1,且收敛精度达到0.001。
3. 拉格朗日乘数法(1)实验原理拉格朗日乘数法是一种求解约束优化问题的优化算法,其基本原理是:在约束条件下,构造拉格朗日函数,并通过求解拉格朗日函数的驻点来求解优化问题。
(2)实验步骤① 设计实验程序,实现拉格朗日乘数法的基本算法。
② 编写函数,用于计算目标函数、约束函数及其导数。
③ 设置初始值和收敛精度。
④ 迭代计算,更新拉格朗日乘数和约束变量的近似值。
西华大学优化设计实验报告

优化设计实验报告课程代码: 6003999 学生姓名:学号:所在学院:机械工程与自动化学院指导老师:陈宏实验地点:机械学院5A-304实验方板有限元分析一、实验目的1、了解、掌握优化设计有限元的分析过程2、熟练运用abaqus软件进行有限元的分析二、实验工具盒实验对象工具:微型计算机,abaqus6.12有限元分析软件实验对象:长、宽均为100mm,厚1毫米,平板几何中心处有一直径5mm通孔的方板。
运用abaqus软件对给定的实验对象进行有限元分析三、实验内容由于带孔方板是对称结构,我们取它的四分之一进行有限元分析,可以减少分析过程的复杂性。
将方板四分之一在abaqus中建模,分别对它属性、装配、分析步、载荷、网格进行参数设定,让后进行作业得出方板各个分析体受力过程位移和力大小的改变情况。
五、实验步骤1、打开abaqus软件建立模型如图1所示;图12、对模型的属性进行参数设置,包括材料的创建和截面的创建,如图2所示;图2 3、将模型进行装配,如图3所示;图3 4、进行分析步的设定,如图4所示;图45、对其载荷进行参数设置并且设置边界条件(载荷F=124MPa,边界条件设为与孔相邻的两边,如图5所示;图56、网格设置包括边上布种、指派网格控制属性、指派单元类型,如图6所示;图67、创建作业,提交作业经过分析得出方板在力和位移上的变化,如下图所示;方板受力变化云图方板受力前后比较方板位移前后变化比较六、实验总结及其注意事项1、实验过程中要做好软件中每一步的参数设置,如果出现问题仔细思考或者向指导老师反映,并反复操作完成实验。
2、实验步骤可以不按照上面的顺序进行,但是在网格布种的过程中,一定要将对象中的“装配”改成“部件”否则无法完成实验。
3、在该实验中划分的网格一定要尽量均匀,如果不均匀的话,分析出来的结果可能不会那么理想4、本实验也可以改用其他软件完成,例如vb编程、analysis等。
5、本实验中所加的力一定要是负的,即拉力。
建筑工程设计优化整改报告
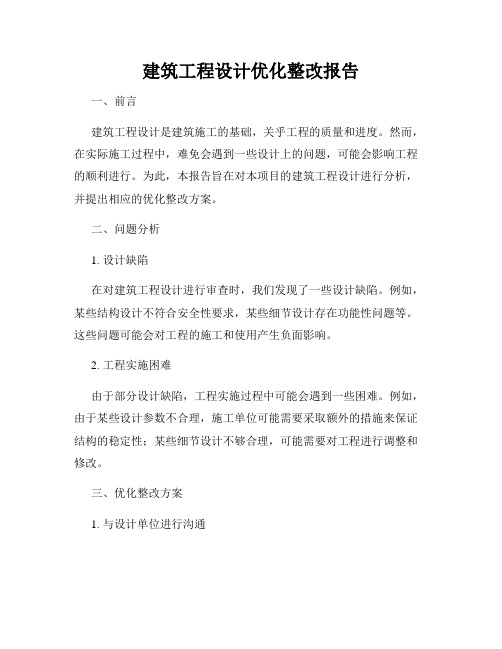
建筑工程设计优化整改报告一、前言建筑工程设计是建筑施工的基础,关乎工程的质量和进度。
然而,在实际施工过程中,难免会遇到一些设计上的问题,可能会影响工程的顺利进行。
为此,本报告旨在对本项目的建筑工程设计进行分析,并提出相应的优化整改方案。
二、问题分析1. 设计缺陷在对建筑工程设计进行审查时,我们发现了一些设计缺陷。
例如,某些结构设计不符合安全性要求,某些细节设计存在功能性问题等。
这些问题可能会对工程的施工和使用产生负面影响。
2. 工程实施困难由于部分设计缺陷,工程实施过程中可能会遇到一些困难。
例如,由于某些设计参数不合理,施工单位可能需要采取额外的措施来保证结构的稳定性;某些细节设计不够合理,可能需要对工程进行调整和修改。
三、优化整改方案1. 与设计单位进行沟通针对发现的设计缺陷,我们将与设计单位进行沟通,详细说明问题,并要求他们提出相应的整改方案。
同时,我们也将提供我们的建议和意见,以期达成共识,并确保问题得到解决。
2. 完善设计细节在与设计单位沟通的基础上,我们将对设计细节进行完善。
尤其是那些存在功能性问题的细节,我们将重新审视并提出改进方案,以确保工程的顺利进行。
3. 调整结构设计对于那些存在安全性问题的结构设计,我们将与设计单位一起进行详细的计算和分析,并根据实际情况提出相应的调整方案。
这些调整可能涉及到结构的加固、更换材料或者改变工艺等。
4. 检查实施过程在整改方案执行过程中,我们将加强对工程实施的监督和检查。
确保整改方案得到有效执行,并在实施过程中及时发现和解决问题,避免出现新的施工难题。
四、预期效果通过以上的优化整改方案,我们预期可以达到以下效果:1. 提高工程质量通过完善设计细节和调整结构设计,可以大幅提高工程的质量水平。
减少设计缺陷和施工困难,可以提高工程的稳定性和耐久性,确保工程在使用过程中能够正常运行。
2. 优化施工进度通过优化设计细节,减少设计问题对施工造成的影响,可以提高施工的效率。
优化设计的实验报告

优化设计的实验报告一、设计目的和背景现代工程设计中,优化设计是提高产品性能和降低成本的重要手段之一、优化设计的目标是通过合理的设计改进产品的形状、结构、材料和工艺等方面,使得产品在给定的约束条件下达到最优性能。
本实验旨在通过优化设计的方法,提高一个结构件的刚度。
二、实验内容实验采用有限元分析软件对原始结构件进行建模和分析,确定初始的结构刚度。
然后,在对初始结构进行可行性分析的基础上,采用一种优化算法,按照给定的约束条件进行优化设计,得到改进后的结构。
最后,再次使用有限元分析软件对改进后的结构进行分析,得到新的结构刚度。
三、实验步骤1.建立原始结构件的有限元模型。
首先,使用有限元分析软件将原始结构件的几何形状转换为一个虚拟三维模型。
然后,在模型上划分网格,并设置结构件材料的力学参数,以及边界条件等。
2.进行有限元分析。
对于原始结构件的有限元模型,进行静态或动态分析,得到相应的位移和应力场。
3.可行性分析。
根据分析结果,评估是否存在结构刚度不足问题,以及可能的改进方向。
4.优化设计。
根据可行性分析的结果,选择一种适当的优化算法进行设计优化。
将原始结构件的有限元模型作为初始解,通过迭代更新模型参数,直到满足约束条件。
5.进行新结构的有限元分析。
在得到优化后的结构模型后,使用有限元分析软件进行新结构的分析,得到新的位移和应力场。
6.结果分析和比较。
对比优化前后的分析结果,分析改进的效果,验证优化设计的可行性和有效性。
四、实验结果和分析根据实验中的步骤,首先对原始结构进行有限元分析,得到其初始的位移和应力场。
然后,根据初始分析结果进行可行性分析,发现结构刚度不足的问题。
在优化设计过程中,采用遗传算法对结构进行优化,设置约束条件为使结构刚度提高20%。
经过多次迭代后,得到优化后的结构。
最后,再次进行有限元分析,得到新的位移和应力场。
通过对比优化前后的分析结果,发现新结构在刚度方面有了显著的提高,并且在位移和应力方面也有所改善。
优化设计实验报告实验总结

优化设计实验报告实验总结1. 引言本次实验的目的是通过优化设计的方法,提高软件系统的性能和效率。
本文将对实验过程中所进行的优化设计以及效果进行总结和分析。
2. 实验内容2.1 实验背景本次实验使用了一个实验平台,该平台是一个高并发的网络爬虫系统。
系统的任务是从互联网上下载数据并进行处理。
由于任务的复杂性,系统在处理大量数据时会出现性能瓶颈。
2.2 实验方法为了提高系统的性能和效率,我们采取了以下优化设计方法:1. 并行化处理:将系统的任务分解为多个子任务,并使用多线程或分布式处理这些子任务,从而提高系统的并发能力和处理效率。
2. 缓存优化:针对系统中频繁读写的数据,使用缓存技术进行优化,减少对数据库和磁盘的访问,提高数据读写的速度。
3. 算法优化:针对系统中的关键算法进行优化,通过改进算法的实现方式、减少算法的时间和空间复杂度等方式,提高算法的执行效率。
4. 资源管理优化:通过合理管理系统的资源,如内存、网络等,避免资源的浪费和瓶颈,提高系统的整体性能。
2.3 实验过程我们首先对系统进行了性能测试,找出了系统存在的性能瓶颈。
然后,针对这些性能瓶颈,我们参考已有的优化设计方法,并结合我们的实际情况,进行了相应的优化设计。
最后,我们在实验平台上对优化后的系统进行了性能测试,评估了优化的效果。
3. 实验结果与分析经过优化设计后,系统的性能得到了明显提升。
在并行化处理方面,通过使用多线程和分布式处理,系统的并发能力得到了大幅提升,处理能力得到了有效利用。
在缓存优化方面,我们合理使用了缓存技术,减少了对数据库和磁盘的访问次数,提高了数据读写的速度。
在算法优化方面,我们通过改进算法的实现方式,使得算法的执行效率得到了明显提升。
在资源管理优化方面,我们对系统的资源进行了合理管理,避免了资源的浪费和瓶颈。
经过实验对比测试,我们发现,经过优化设计后的系统的性能较之前有了明显的提升。
系统的处理能力得到了有效利用,并发能力得到了大幅提升,整体的性能和效率明显提高。
优化设计实验报告

优化设计实验报告优化设计实验报告引言在当今科技高速发展的时代,优化设计成为了一项重要的研究领域。
通过优化设计,可以提高产品的性能和质量,降低生产成本,提高效率,满足不断增长的市场需求。
本实验报告旨在介绍优化设计的基本概念和方法,并通过一个具体案例来展示其在实际工程中的应用。
一、优化设计的基本概念优化设计是指通过系统地改进和调整设计参数,以达到最佳的设计目标的过程。
它是一种综合性的工程方法,涉及到多个学科领域,如数学、工程学、经济学等。
优化设计的基本概念包括目标函数、设计变量、约束条件等。
目标函数是指在优化设计中需要优化的设计指标,如最小化成本、最大化效率等。
设计变量是指可以调整的设计参数,如尺寸、材料、工艺等。
约束条件是指在设计过程中需要满足的限制条件,如材料强度、工艺要求等。
通过合理地选择目标函数、设计变量和约束条件,可以实现优化设计的目标。
二、优化设计的方法优化设计的方法有很多种,常见的有数学优化方法、试验设计方法和仿真优化方法等。
数学优化方法是利用数学模型和计算机算法来寻找最优解的方法,如线性规划、非线性规划等。
试验设计方法是通过设计一系列实验来寻找最优解的方法,如响应面法、Taguchi方法等。
仿真优化方法是通过建立数值模型,并通过计算机仿真来进行优化设计的方法,如有限元分析、计算流体力学等。
三、实际案例:汽车车身结构优化设计以汽车车身结构优化设计为例,介绍优化设计在实际工程中的应用。
汽车车身结构的优化设计旨在提高车身的刚度和强度,减少车身的重量和空气阻力,以提高汽车的性能和燃油经济性。
在汽车车身结构优化设计中,目标函数可以设定为最小化车身重量,设计变量可以包括材料的选择、截面的尺寸等,约束条件可以包括材料的强度、刚度要求等。
通过数学优化方法,可以建立数学模型,利用计算机算法来搜索最优解。
通过试验设计方法,可以设计一系列试验,通过响应面法来寻找最优解。
通过仿真优化方法,可以建立数值模型,通过有限元分析来进行优化设计。
优化设计进退法实验报告
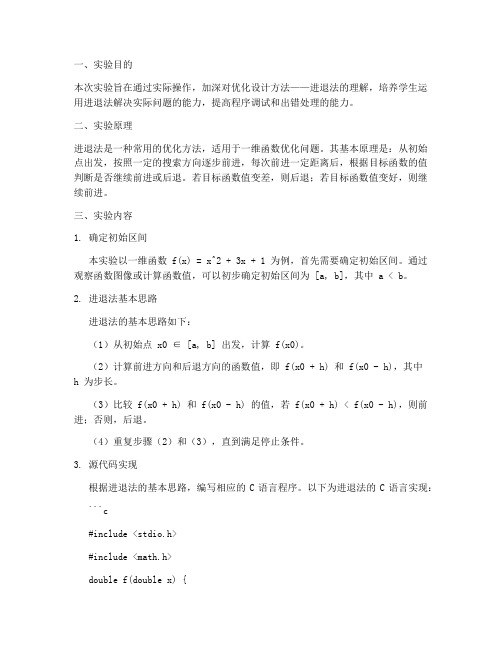
一、实验目的本次实验旨在通过实际操作,加深对优化设计方法——进退法的理解,培养学生运用进退法解决实际问题的能力,提高程序调试和出错处理的能力。
二、实验原理进退法是一种常用的优化方法,适用于一维函数优化问题。
其基本原理是:从初始点出发,按照一定的搜索方向逐步前进,每次前进一定距离后,根据目标函数的值判断是否继续前进或后退。
若目标函数值变差,则后退;若目标函数值变好,则继续前进。
三、实验内容1. 确定初始区间本实验以一维函数 f(x) = x^2 + 3x + 1 为例,首先需要确定初始区间。
通过观察函数图像或计算函数值,可以初步确定初始区间为 [a, b],其中 a < b。
2. 进退法基本思路进退法的基本思路如下:(1)从初始点x0 ∈ [a, b] 出发,计算 f(x0)。
(2)计算前进方向和后退方向的函数值,即 f(x0 + h) 和 f(x0 - h),其中h 为步长。
(3)比较 f(x0 + h) 和 f(x0 - h) 的值,若 f(x0 + h) < f(x0 - h),则前进;否则,后退。
(4)重复步骤(2)和(3),直到满足停止条件。
3. 源代码实现根据进退法的基本思路,编写相应的C语言程序。
以下为进退法的C语言实现:```c#include <stdio.h>#include <math.h>double f(double x) {return x x + 3 x + 1;}int main() {double a = -10, b = 10, x0 = 0, h = 0.1; double fa, fb, fx0, fx;while (b - a > 0.0001) {fx0 = f(x0);fa = f(x0 + h);fb = f(x0 - h);if (fa < fb) {a = x0;x0 += h;} else {b = x0;x0 -= h;}}printf("最优解为:%f\n", x0);printf("目标函数值:%f\n", f(x0));return 0;}```4. 执行结果分析运行上述程序,得到最优解为x ≈ -1.5,目标函数值约为 0.375。
工程设计优化整改报告
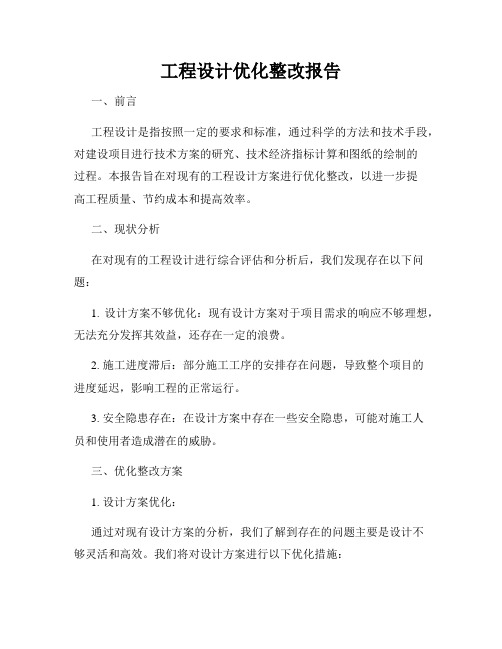
工程设计优化整改报告一、前言工程设计是指按照一定的要求和标准,通过科学的方法和技术手段,对建设项目进行技术方案的研究、技术经济指标计算和图纸的绘制的过程。
本报告旨在对现有的工程设计方案进行优化整改,以进一步提高工程质量、节约成本和提高效率。
二、现状分析在对现有的工程设计进行综合评估和分析后,我们发现存在以下问题:1. 设计方案不够优化:现有设计方案对于项目需求的响应不够理想,无法充分发挥其效益,还存在一定的浪费。
2. 施工进度滞后:部分施工工序的安排存在问题,导致整个项目的进度延迟,影响工程的正常运行。
3. 安全隐患存在:在设计方案中存在一些安全隐患,可能对施工人员和使用者造成潜在的威胁。
三、优化整改方案1. 设计方案优化:通过对现有设计方案的分析,我们了解到存在的问题主要是设计不够灵活和高效。
我们将对设计方案进行以下优化措施:(1)重新评估项目需求并持续调研,确保设计方案充分满足项目要求。
(2)加强与相关部门的合作,提高设计方案的综合性和可操作性。
(3)使用先进的技术和工具,提高设计效率和精度。
(4)优选材料和设备,提高工程性能和可持续性。
2. 进度优化:为解决施工进度滞后的问题,我们将采取以下措施:(1)优化施工计划,合理安排工程进度,确保各个节点的顺利进行。
(2)加强施工监管,提高施工人员的执行力和效率。
(3)协调各方资源,及时解决施工过程中的问题,避免进度延误。
3. 安全隐患的整改:为确保施工过程的安全性,我们将进行以下整改措施:(1)加强安全培训和教育,提高施工人员的安全意识和技能。
(2)加强现场监管,定期检查施工现场,及时发现和修复安全隐患。
(3)完善安全制度和常规操作程序,确保施工过程的标准化和规范化。
四、预期效果通过以上的优化整改方案,我们预期可以达到以下效果:1. 设计方案优化能够更好地满足项目需求,提高工程的效益和质量。
2. 进度优化能够减少工期延误,提高项目的交付效率。
3. 安全隐患的整改能够降低施工过程中的事故风险,确保施工人员和使用者的安全。
- 1、下载文档前请自行甄别文档内容的完整性,平台不提供额外的编辑、内容补充、找答案等附加服务。
- 2、"仅部分预览"的文档,不可在线预览部分如存在完整性等问题,可反馈申请退款(可完整预览的文档不适用该条件!)。
- 3、如文档侵犯您的权益,请联系客服反馈,我们会尽快为您处理(人工客服工作时间:9:00-18:30)。
(课程实践报告封面模版)合肥工业大学《机械优化设计》课程实践研究报告班级:机设六班学号:姓名:李继鑫授课老师:王卫荣日期: 2013年 5 月 7 日(一)一维搜索 min f(x)=]10,0[]2,0[]32)2[(*cos *π⎩⎨⎧+-x d x c 注:其中c 、d 为待定系数,用于确定选择的函数是哪一个。
C 语言程序段如下:#include <stdio.h>#include<math.h>#define p 3.14float fun(float x,float c,float d);void main(void){float a0,a1,a2,r,a,b;float y1=0.0000,y2=0.0000,u;float c,d;u=0.618;printf("input[a,b]and r:a= b= r= ");scanf("%f%f%f",&a,&b,&r);printf("choose only ONE function number c=1 0 or d=0 1\n"); scanf("%f%f",&c,&d);if(c==1) d=0;else c=0,d=1;a1=b-u*(b-a),y1=fun(a1,c,d);a2=a+u*(b-a),y2=fun(a2,c,d);do{if(y1>=y2){a=a1;a1=a2,y1=y2;a2=a+u*(b-a),y2=fun(a2,c,d);}else{b=a2;a2=a1,y2=y1;a1=b-u*(b-a),y1=fun(a1,c,d);}}while(fabs((b-a)/b)>r && fabs((y2-y1)/y2)>r); a0=0.5*(a+b);printf("The best result a0=%f\n",a0);}/******function editting********/float fun(float x,float c,float d){float Y;Y=c*cos(x)+d*((x-2)*(x-2)+3);return(Y);}●选择第二的函数(0,1)极小值a0=2.000970,理论值为2,正确。
●选择第一的函数(1,0)极小值a0=3.140134,理论值为 ,正确。
(二)单位矩阵C语言程序实现n阶单位矩阵如下:#include<stdio.h>void main(void){int n,i,j;int d=1,c=0;printf("Input the dimension of array n=\n");scanf("%d",&n);printf("the array of n*n is:\n");for(i=0;i<n-1;i++){for(j=0;j<n-1;j++){if(i==j) printf("%3d",d);else printf("%3d",c);}printf("\n");}}●实验数据验证如下,取n=5得到5阶单位矩阵:●取n=10得到10阶单位矩阵:(三)连杆机构问题优化设计修改程序实现过程如下:unit sumt_fgh;interfaceusesWindows, Messages, SysUtils, Classes, Graphics, Controls, Forms, Dialogs,Math; typearr3 = array[1..55]of real;typeTForm3 = class(TForm)private{ Private declarations }public{ Public declarations }end;varForm3: TForm3;Procedure ffx;Procedure ggx;Procedure hhx;implementationuses sumt_1, sumt_2;{$R *.DFM}// 应用惩罚函数法优化方法计算优化问题,用户应首先根据具体问题// 建立其优化的数学模型(①目标函数;②不等式约束函数;③等式约束函数。
);// min F[x]// s.t. GX[j]≤0 (j=1,2,...kg)// HX[j]=0 (j=1,2,...kh)// 再将目标函数、约束函数按DELPHI语言改写成表达式,// fx := ...;// gx[1] := ...;// gx[2] := ...;// .// .// gx[kg] := ...;// hx[1] := ...;// hx[2] := ...;// .// .// hx[kh] := ...;// 替换下面的procedure ffx段中的目标函数的计算表达式fx;// 替换下面的procedure ggx段中的目标函数的计算表达式gx[1]、gx[2]...gx[kg]// 替换下面的procedure hhx段中的目标函数的计算表达式hx[1]、hx[2]...hx[kh]}procedure ffx; //目标函数var y0,y1,z,t,b,a,y2 : double;var i :integer;beginwith form1.sumt do beginfx:=0;for i:= 1 to 30 dobeginy0:=arccos(((1+x[1])*(1+x[1])-x[2]*x[2]+25)/(10*(1+x[1])));y1:=y0+(i+1)*i*0.5;z:=arccos(((1+x[1])*(1+x[1])-x[2]*x[2]-25)/(10*x[2]));r:=sqrt(26-10*cos(y1));t:=z+2*(y1-y0)/3.0/3.14;b:=arccos((r*r+24)/(10*r));y2:=3.14-a-b;a:=arccos((r*r+x[2]*x[2]-x[1]*x[1])/(2*r*x[2]));fx:=fx+(y2-t)*(y2-t)*3.14/60.0;end;end;end;procedure ggx; //约束函数beginwith form1.sumt do begingx[1]:=x[1]*x[1]+x[2]*x[2]-1.414*x[1]*x[2]-16.0;gx[2]:=36.0-x[1]*x[1]-x[2]*x[2]-1.414*x[1]*x[2];gx[3]:=-x[1];gx[4]:=-x[2];gx[5]:=6-x[1]-x[2];gx[6]:=x[1]-x[2]-4;gx[7]:=x[2]-x[1]-4;end;end;procedure hhx; //约束函数beginwith form1.sumt do beginhx[1]:=x[1];end;end;End.●参数数输入窗口:●连杆问题存档资料:常用优化方法——惩罚函数法^^^^^^^^^^^^^^^^^^^^^^^^^^一、初始数据====================================================================== =========设计变量个数N = 2-----------------------------------------------------------------------------不等式约束个数KG = 7 等式约束个数KH = 0-----------------------------------------------------------------------------惩罚因子R = 4.41942089203984 惩罚因子降低系数 C = 0.2-----------------------------------------------------------------------------初始步长T0 = 0.01 收敛精度EPS = 0.0001-----------------------------------------------------------------------------无约束优化方法:-----------------------------------------------------------------------------设计变量初始点X0:X[1]=4X[2]=4-----------------------------------------------------------------------------设计变量下界BL:BL[1]=0BL[2]=0-----------------------------------------------------------------------------设计变量上界BU:BU[1]=10BU[2]=10-----------------------------------------------------------------------------初始点目标函数值F(X0)= 3355.25624403039-----------------------------------------------------------------------------初始点处的不等约束函数值G(X0):GX[1]= -6.624000E+00GX[2]= -1.862400E+01GX[3]= -4.000000E+00GX[4]= -4.000000E+00GX[5]= -2.000000E+00GX[6]= -4.000000E+00GX[7]= -4.000000E+00-------------------------------------------------------------------------------二、计算过程__数据====================================================================== =========IRC = 0 R = 4.419421E+00 PEN = 3362.83720242824-----------------------------------------------------------------------------IRC = 1 R = 8.114894E-01 PEN = 3332.21039499842-----------------------------------------------------------------------------三、优化结果__数据====================================================================== =========罚函数构造次数IRC = 2-----------------------------------------------------------------------------无约束优化方法调用次数ITE = 5 一维搜索方法调用次数ILI = 11-----------------------------------------------------------------------------惩罚函数值计算次数NPE = 76 目标函数值计算次数IFX = 0-----------------------------------------------------------------------------设计变量最优点X*:X[1]= 4.868133E+00X[2]= 1.650658E+00-----------------------------------------------------------------------------最优值F(X*)= 3308.87943922349-----------------------------------------------------------------------------最优点处的不等约束函数值G(X*):GX[1]= -9.389790E-01GX[2]= -1.785757E+00GX[3]= -4.868133E+00GX[4]= -1.650658E+00GX[5]= -5.187906E-01GX[6]= -7.825248E-01GX[7]= -7.217475E+00---------------------------------------------------------------------------------- STOP ---(四)自选工程问题例6-7 试求点集A (x 1,x 2,x 3)和点集B (x 4,x 5,x 6)之间的最短距离。