零缺陷抽样方案
C=0抽样方案
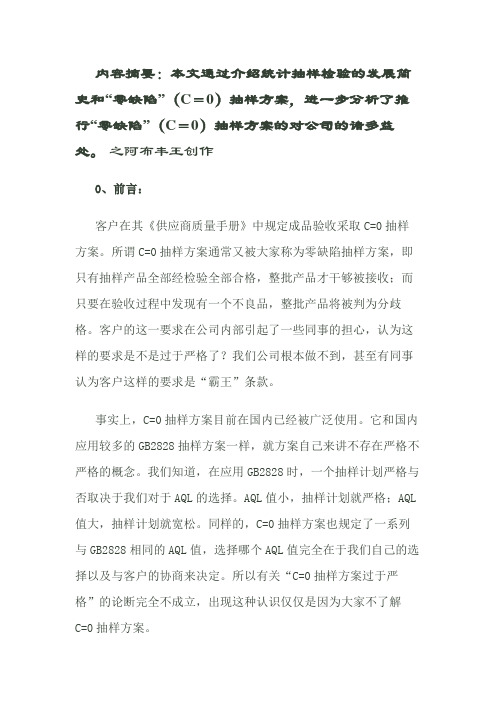
内容摘要:本文通过介绍统计抽样检验的发展简史和“零缺陷”(C=0)抽样方案,进一步分析了推行“零缺陷”(C=0)抽样方案的对公司的诸多益处。
之阿布丰王创作0、前言:客户在其《供应商质量手册》中规定成品验收采取C=0抽样方案。
所谓C=0抽样方案通常又被大家称为零缺陷抽样方案,即只有抽样产品全部经检验全部合格,整批产品才干够被接收;而只要在验收过程中发现有一个不良品,整批产品将被判为分歧格。
客户的这一要求在公司内部引起了一些同事的担心,认为这样的要求是不是过于严格了?我们公司根本做不到,甚至有同事认为客户这样的要求是“霸王”条款。
事实上,C=0抽样方案目前在国内已经被广泛使用。
它和国内应用较多的GB2828抽样方案一样,就方案自己来讲不存在严格不严格的概念。
我们知道,在应用GB2828时,一个抽样计划严格与否取决于我们对于AQL的选择。
AQL值小,抽样计划就严格;AQL 值大,抽样计划就宽松。
同样的,C=0抽样方案也规定了一系列与GB2828相同的AQL值,选择哪个AQL值完全在于我们自己的选择以及与客户的协商来决定。
所以有关“C=0抽样方案过于严格”的论断完全不成立,出现这种认识仅仅是因为大家不了解C=0抽样方案。
需要说明的是,该客户的《供应商质量手册》是根据ISO/TS16949(即GB/T18305)建立的,而ISO/TS16949在7.1.2 条款中明确要求接收水平必须是零缺陷。
(ISO/TS16949 7.1.2接收准则:组织应规定接收准则,要求时,由顾客批准。
对于计数型数据抽样,接收水平应是零缺陷。
)所以,客户的要求是根据的,不存在任何“霸王”要求。
1、抽样检验简介抽样检验又称为统计抽检检验,是指从交验的一批产品中,随机抽取若干单位产品组成样本进行检验,通过对样本的检验结果对整批产品做出质量判定的过程。
我们知道,检验是不发生价值的工作,因此如何更经济、快捷的进行检验就直接关系到生产的成本和效率。
零缺陷(c=0)抽样方案

零缺陷(C=0)正常一次抽样方案
接收质量限(AQL)0.0100.0150.025
0.040
0.065
0.10
0.15
0.25
0.40
0.65
1.0
1.5
2.5
4.0
6.5
10
批量(N)
样本大小(n)
2~8
*
*
*
*
*
*
*
*
*
*
*
*
5
3
2
2
9~15
*
*
*
*
*
*
*
*
*
*
13
8
5
556 435 303 244
123 96 74 56
156 119 90 64
189 143 102 64
40 29 15 9
40 29 15 9
40 29 15 9
* Indicates entire lot must be inspected
NOTE: The Acceptance Number in all cases is ZERO.
23 18 13 9
29 22 15 9
35 29 15 9
35,001 to 150,000
150,001 to 500,.00
500,001 and over
1250 800 500 490
1250 800 750 715
1250 1200 1112 715
476 294 218 170
476 345 270 200
2不合格的可接收数为0即ac0零缺陷抽样方案目前还不是国际或国家标准但由于零缺陷的观念已在全球盛行欧美很多企业都采用零缺陷抽样方案
零缺陷(C=0)抽样方案

零缺陷概念的产生:被誉为“全球质量管理大师”、“零缺陷之父”和“伟大的管理思想家”的菲利浦·克劳士比(Philip B. Crosby)在20世纪60年代初提出“零缺陷”思想,并在美国推行零缺陷运动。
后来,零缺陷的思想传至日本,在日本制造业中得到了全面推广,使日本制造业的产品质量得到迅速提高,并且领先于世界水平,继而进一步扩大到工商业所有领域。
零缺陷理论核心是:“第一次就把事情做对”。
所谓"零缺陷"抽样方案,简单的说,就是不管你的批量和样本大小如何,其抽样检验的接收数Ac=0,即"0收1退"。
举例:某客户在其《供应商质量手册》中规定成品验收采用 C=0 抽样方案。
所谓 C=0 抽样方案通常又被大家称为零缺陷抽样方案,即只有抽样产品全部经检验全部合格,整批产品才能够被接收;而只要在验收过程中发现有一个不良品,整批产品将被判为不合格。
客户的这一要求在公司内部引起了一些同事的担心,认为这样的要求是不是过于严格了?公司根本做不到,甚至有同事认为客户这样的要求是“霸王”条款。
事实上,C=0 抽样方案目前在国内已经被广泛使用。
它和我们中国应用较多的GB/T2828.1-2012抽样方案一样,就方案本身来讲不存在严格不严格的概念。
在应用GB/T2828.1-2012时,一个抽样计划严格与否取决于我们对于 AQL 的选择。
AQL 值小,抽样计划就严格;AQL 值大,抽样计划就宽松。
同样的,C=0 抽样方案也规定了一系列与GB/T2828.1-2012 相同的 AQL值,选择哪个AQL 值完全在于我们自己的选择以及与客户的协商来决定。
所以有关“C=0 抽样方案过于严格”的论断完全不成立,出现这种认识仅仅是因为大家不了解C=0 抽样方案。
需要说明的是,该客户的《供应商质量手册》是根据IATF16949:2016 建立的,而IATF16949 :2016标准条款8.6.6中明确要求接收水平必须是零缺陷。
零缺陷抽样方案

2
简介及说明
组织
IQC
STEP1 STEP2 STEP3
OQC
IPQC
3
各项检验的趋势(IQC)
供货商 OQC
组织 IQC
IQC目前的趋势倾向由供货商负责,进来时免 检方式,但前提是你能相信供货商的制造能力 以及供货商OQC的情形,这样可以避免供货商 和组织的重复检验以及人员的投资
4
各项检验的趋势(IPQC)
e 2.71828
期望值:E( X )
變異數:Var( X )
表示式:X ~ P.D()
18
泊松分布例题
设有一检验批,其批量为100,000个,其不良率已知为 3%,试问从其中随机抽取100个样品检验,其中含有0 个以及1个不良品的概率分别为多少?
N 100,000, n 100,則n / N 0.001 0.1
8
P5
(8
8! 5)!
8! 3!
6720
因为有8篇文可用但却仅能容纳5篇,第一篇时有8种选择,第二 篇时有7种选择,第三篇有6种选择,第四篇有5种选择,第五篇 有4种选择,共有8*7*6*5*4=6720种不同的可能安排,但 8*7*6*5*4恰为8!/3!。一般上,从n件可用事物中取出r件,即共 有n!/(n-r)!种不同的可能安排数,这即排列法则。
28
分层随机抽样
++++++++ ++++++++ *********** *********** ######## ######## $$$$$$$$$$$ $$$$$$$$$$$
+++ *** ### $$$
C=0抽样方案

内容摘要:本文通过介绍统计抽样检验的发展简史和“零缺陷”(C=0)抽样方案,进一步分析了推行“零缺陷”(C=0)抽样方案的对公司的诸多益处。
0、前言:客户在其《供应商质量手册》中规定成品验收采用C=0抽样方案。
所谓C=0抽样方案通常又被大家称为零缺陷抽样方案,即只有抽样产品全部经检验全部合格,整批产品才能够被接收;而只要在验收过程中发现有一个不良品,整批产品将被判为不合格。
客户的这一要求在公司内部引起了一些同事的担心,认为这样的要求是不是过于严格了?我们公司根本做不到,甚至有同事认为客户这样的要求是“霸王”条款。
事实上,C=0抽样方案目前在国内已经被广泛使用。
它和国内应用较多的GB2828抽样方案一样,就方案本身来讲不存在严格不严格的概念。
我们知道,在应用GB2828时,一个抽样计划严格与否取决于我们对于AQL的选择。
AQL值小,抽样计划就严格;AQL值大,抽样计划就宽松。
同样的,C=0抽样方案也规定了一系列与GB2828相同的AQL值,选择哪个AQL值完全在于我们自己的选择以及与客户的协商来决定。
所以有关“C=0抽样方案过于严格”的论断完全不成立,出现这种认识仅仅是因为大家不了解C=0抽样方案。
需要说明的是,该客户的《供应商质量手册》是根据ISO/TS16949(即GB/T18305)建立的,而ISO/TS16949在7.1.2条款中明确要求接收水平必须是零缺陷。
(ISO/TS16949 7.1.2接收准则:组织应规定接收准则,要求时,由顾客批准。
对于计数型数据抽样,接收水平应是零缺陷。
)所以,客户的要求是根据的,不存在任何“霸王”要求。
1、抽样检验简介抽样检验又称为统计抽检检验,是指从交验的一批产品中,随机抽取若干单位产品组成样本进行检验,通过对样本的检验结果对整批产品做出质量判定的过程。
我们知道,检验是不产生价值的工作,因此如何更经济、快捷的进行检验就直接关系到生产的成本和效率。
统计抽样检验理论是美国贝尔实验室的道奇和罗米格于1929年创立的,它和1924年休哈特提出的统计过程控制(控制图)一起被视为质量管理从质量检验阶段进入统计质量控制阶段的两个标志性成果。
浅析“零缺陷抽样检验方案”_如风的小世界
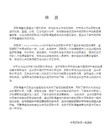
3) 按零缺陷抽样检验方案(C=0),并结合GB/T2828.1的相关要求。
第一个质量特性(A类),n=125,(Ac,Re=0,1)
2) 按我们公司现有C=0抽样方案,并结合GB/T2828.1的相关要求。
第一个质量特性(A类),n=80,(Ac,Re=0,1)
第二个质量特性(C类),n=80,(Ac,Re=0,1)。
上面的第一中抽样方案对于一般的企业可能是适用的,但对于通过了ISO/TS16949的汽车零部件制造性企业肯定是不允许的。同样我们公司也不能采用。我们仔细分析下上面的第二种情形,是粗略的理解了零缺陷抽样检验方案中有关AQL所带来的作用。我们试想对于一个C类的项目如果不考虑AQL值也简单抽取那么大的样本而按零缺陷接收的,无疑将增加生产方(供应商)的风险,浪费我们使用方的资源。过多的抽取样本。
产品有2个质量特性项目需要检测,一个是A类的,一个是C类的。按照我们以往的做法,有下面两种情况:
1) 按GB/T2828.1的正常检验一次抽样方案II级检验水平的抽样方案为
第一个质量特性(A类),n=125,(Ac,Re=0,1)
第二个质量特性(C类),n=80,(Ac,Re=10,11)。
接收准则必须由组织定义,要求时,必须由顾客批准。对于计数型数据抽样,接收水平必须是零缺陷”。
标准条文明确规定的,也就是我们要恪守的。其实我们也一直在实用C=O的抽样检验方案。但对其认识上可能存在一定的误区。导致其真正的效率发挥的不够充分。所以希望通过本文,能起抛砖引玉作用,为公司后续检验和试验活动更加顺畅的开展起到积极作用。
C=0-抽样方案介绍

C=0-抽样方案介绍1965年,零缺陷抽样检验方案(c=0)首次发表在国际刊物上,虽然零缺陷抽样检验方案目前还是不是国际和国家标准。
但由于“零缺陷”的品质理念已经深入人心,在加上ISO/TS16949:2002中有明确的条文要求。
所以欧美很多的企业,特别是汽车供应链相关企业普遍采用的都是零缺陷抽样检验方案。
零缺陷抽样检验方案简单的说,就是不管你的批量和样本大小如何,其抽样检验的接收数Ac=0,即“0收1退”。
在抽样检验过程中,一旦发现一个缺陷或不合格,就要实施100%的全检或退货处置。
零缺陷抽样检验方案的优点就是不存在加严、放宽与正常检验之间的转移规定。
在ISO/TS16949:2002里面的7.1.2条款里面有明确规定“7.1.2接收准则必须由组织定义,要求时,必须由顾客批准。
对于计数型数据抽样,接收水平必须是零缺陷”。
标准条文明确规定的,也就是我们要恪守的。
其实我们也一直在实用C=O的抽样检验方案。
但对其认识上可能存在一定的误区。
导致其真正的效率发挥的不够充分。
所以希望通过本文,能起抛砖引玉作用,为公司后续检验和试验活动更加顺畅的开展起到积极作用。
首先,零缺陷抽样检验方案的准则就是我们通常说的C=0,0收1退。
但其要和GB/T2828.1-2003按接收质量限(AQL)检索逐批检验抽样计划结合使用,要使用GB/T2828.1来确定其“零缺陷抽样检验方案”的样本大小。
按我们以前的经验,采用GB/T2828.1的时候,首先是确定批量大小、确定检验水平、那么它的样本大小就确定,再定义我们的接收质量限(AQL)就可以得出我们的接收准则,而现在采用零缺陷抽样检验方案的接收准则是已知的,意味着AQL值在零缺陷抽样检验方案中就失去了作用。
这就是我们认识上的一个明显误区。
试想,如果采用零缺陷抽样检验方案与AQL值无关的话,那么假设采用GB/T2828.1里面的正常检验一次抽样方案II级检验水平的话,意味着样本量是统一的。
零缺陷抽样方案
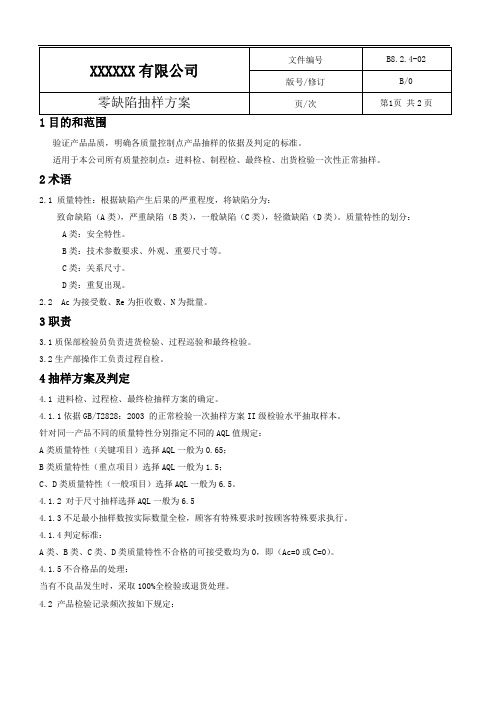
验证产品品质,明确各质量控制点产品抽样的依据及判定的标准。
适用于本公司所有质量控制点:进料检、制程检、最终检、出货检验一次性正常抽样。
2术语2.1 质量特性:根据缺陷产生后果的严重程度,将缺陷分为:致命缺陷(A类),严重缺陷(B类),一般缺陷(C类),轻微缺陷(D类)。
质量特性的划分:A类:安全特性。
B类:技术参数要求、外观、重要尺寸等。
C类:关系尺寸。
D类:重复出现。
2.2 Ac为接受数、Re为拒收数、N为批量。
3职责3.1质保部检验员负责进货检验、过程巡验和最终检验。
3.2生产部操作工负责过程自检。
4抽样方案及判定4.1 进料检、过程检、最终检抽样方案的确定。
4.1.1依据GB/T2828:2003 的正常检验一次抽样方案II级检验水平抽取样本。
针对同一产品不同的质量特性分别指定不同的AQL值规定:A类质量特性(关键项目)选择AQL一般为0.65;B类质量特性(重点项目)选择AQL一般为1.5;C、D类质量特性(一般项目)选择AQL一般为6.5。
4.1.2 对于尺寸抽样选择AQL一般为6.54.1.3不足最小抽样数按实际数量全检,顾客有特殊要求时按顾客特殊要求执行。
4.1.4判定标准:A类、B类、C类、D类质量特性不合格的可接受数均为0,即(Ac=0或C=0)。
4.1.5不合格品的处理:当有不良品发生时,采取100%全检验或退货处理。
4.2 产品检验记录频次按如下规定:控制程序》处理。
4.3质量记录抽样结果记录5个数据:最大值 1个、最小值1个、中间值 3个5相关文件5.1 A8.3-01 不合格品控制程序6相关质量记录6.1 JL8.2.4-02 产品检验记录表6.2 JL8.2.4-07 进货检验记录6.3 JL8.2.4-13 终检检验记录表7本程序更改记录。
零缺陷抽样方案

P0
=
30 0!
e -3
=
0 .04979
d =1
P1
=
31 1!
e -3
=
0 .14937
一般应用上的检验,使 用卜氏分布求近似值时, 除了与二项分布相同 n/N要小于0.1外,样本 数n要大于16以上,以 及不良率要小于10%, 方可求得正确结果.
计数分布汇总:
N<10n 不归还法
计数值分配
N 10n
品数为0、1个的概率分別为多少
d=0
P0
30 970 ( )( ) = 01010000=
()
03!30!0!1•1 00 0 9!!0 0 8 7!7 0!0=8970!1 0 !0 9070!0 !0 =0.04036
100
10!0 90!0
d =1
30 970
( )(
)
30 !
970 !
P1 =
组合法则
从n个可用事物中取出r件组合数为如下式子:(式 中n=可用事物总数,r=取出事物数.利用上述组合法则, 须有n个事物,且由n个中取出r个做组合,另应考虑相同 事物重新安排是相同的.)
C
r n
=
(n
n! - r)!r!
组合例题
纽约发行彩券,设头奖一名,由1至54中选出6
种不同组合数,恰好与头奖号码完全一样则贏得头
例如一批产品有1000件,分四层放置,每层有 250件,现准备选择样本20件,可从每层的250件 中随机抽取5件,合计为20件样本.
区域抽样
区域抽样时,要求每个区域內部的差异大些,区域之间 的差异要小些,这样的效果才会比较好.
例如有一批螺丝共100盒,每盒中有100个螺丝,准备抽 取500个样本,可从100盒中随机抽取5盒,检查5盒中的 全部螺丝.
零缺陷抽样方案QS/TS

QS9000、ISO/TS16949的要求-零缺陷(A C=0或c=0)抽样检验方案3。
1 企业引进零缺陷抽样方案的必要性在全面介绍零缺陷抽样检验方案前,请先看一看QS9000之4.10.1.1条款(计数特性的接收准则)的要求。
4.10.1.1 计数特性的接收准则计数数据接收抽样计划的接收准则必须是零缺陷。
所有其他情况(如:目视标灌)的接收准则必须由供方形成文件并由顾客批准。
从这一条款不难看出,QS9000标准要求所有计数抽样方案都为零缺陷,也即抽样验收的合格判定数为零,即“0收1不收”。
这一条款对企业来说,是一很大挑战。
在满足这一条款时,很多企业缺乏科学的抽样表,往往使用GB2828(或MIL-SrD-105E)正常检查一次抽样方案中的样本大小(n)作为零缺陷抽样检验方案的样本大小(n)。
这一作法无论从理论上抑或从实践上都是很不经济的(表3-2显示GB2828之样本数量大大地超过了零缺陷抽样方案对样本数量的要求),为此企业有必要引进零缺陷的抽样方案。
3.2 零缺陷(c=0)抽样方案之发展历史1965年,c=0抽样方案首次发表于国际刊物,1969年首次出书,1981年再版,1983年发行第三版。
零缺陷(c=0)抽样方案目前还不是国际或国家标准,但由于“零缺陷”的品质观念已通行全球,因此欧美很多企业都广泛采用零缺陷(c=0)抽样方案。
从使用者报告中犟示,当抽样方案由MIL-STD-105E改变为c=0的抽样方案时,可节省8%-30%的成本。
从理论上来说,批量及AQL值愈大,节省成本愈多。
3.3 c=0抽样方案的特点任何批量检验的产品,c=0抽样方案均可应用,特别适合孤立批的检验(如从临时供应商处采购)。
c=0抽样方案无加严、放宽转移的规定。
3.4 c=0抽样方案的—些概念(1) 暂扣批(withhold the lot)暂扣批是一个特别的概念,它并不意味着“拒收”,在“零缺陷抽样方案中”,只有抽检样本中“不合格”(nonconformity)为零时才接收(即A c=0)。
零缺陷抽样方案
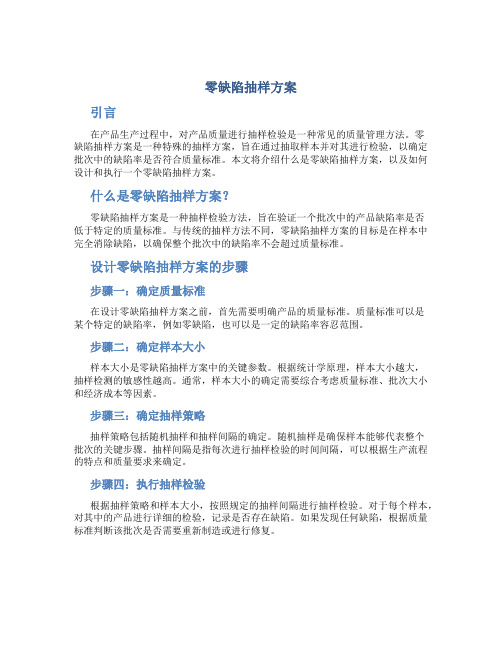
零缺陷抽样方案引言在产品生产过程中,对产品质量进行抽样检验是一种常见的质量管理方法。
零缺陷抽样方案是一种特殊的抽样方案,旨在通过抽取样本并对其进行检验,以确定批次中的缺陷率是否符合质量标准。
本文将介绍什么是零缺陷抽样方案,以及如何设计和执行一个零缺陷抽样方案。
什么是零缺陷抽样方案?零缺陷抽样方案是一种抽样检验方法,旨在验证一个批次中的产品缺陷率是否低于特定的质量标准。
与传统的抽样方法不同,零缺陷抽样方案的目标是在样本中完全消除缺陷,以确保整个批次中的缺陷率不会超过质量标准。
设计零缺陷抽样方案的步骤步骤一:确定质量标准在设计零缺陷抽样方案之前,首先需要明确产品的质量标准。
质量标准可以是某个特定的缺陷率,例如零缺陷,也可以是一定的缺陷率容忍范围。
步骤二:确定样本大小样本大小是零缺陷抽样方案中的关键参数。
根据统计学原理,样本大小越大,抽样检测的敏感性越高。
通常,样本大小的确定需要综合考虑质量标准、批次大小和经济成本等因素。
步骤三:确定抽样策略抽样策略包括随机抽样和抽样间隔的确定。
随机抽样是确保样本能够代表整个批次的关键步骤。
抽样间隔是指每次进行抽样检验的时间间隔,可以根据生产流程的特点和质量要求来确定。
步骤四:执行抽样检验根据抽样策略和样本大小,按照规定的抽样间隔进行抽样检验。
对于每个样本,对其中的产品进行详细的检验,记录是否存在缺陷。
如果发现任何缺陷,根据质量标准判断该批次是否需要重新制造或进行修复。
步骤五:分析结果和调整方案根据抽样检验的结果,可以计算出批次的缺陷率。
如果缺陷率低于质量标准,说明产品符合质量要求,可以继续生产。
如果缺陷率超过了质量标准,需要对生产过程进行分析,找出产生缺陷的原因,并相应地调整质量控制方案。
实施零缺陷抽样方案的优势及注意事项优势1.零缺陷抽样方案可以及时发现和纠正生产过程中的缺陷,确保产品质量符合质量标准。
2.通过不断的抽样检验和分析结果,可以不断改进生产过程,并最终实现零缺陷的目标。
C=0-抽样方案介绍

C=0-抽样方案介绍
C=0-抽样方案介绍
C=0-抽样方案介绍
1965年,零缺陷抽样检验方案(c=0)首次发表在国际刊物上,虽然零缺陷抽样检验方案目前还是不是国际和国家标准。
但由于“零缺陷”的品质理念已经深入人心,在加上ISO/TS16949:2002中有明确的条文要求。
所以欧美很多的企业,特别是汽车供应链相关企业普遍采用的都是零缺陷抽样检验方案。
零缺陷抽样检验方案简单的说,就是不管你的批量和样本大小如何,其抽样检验的接收数Ac=0,即“0收1退”。
在抽样检验过程中,一旦发现一个缺陷或不合格,就要实施100%的全检或退货处置。
零缺陷抽样检验方案的优点就是不存在加严、放宽与正常检验之间的转移规定。
在ISO/TS16949:2002里面的7.1.2条款里面有明确规定“7.1.2接收准则必须由组织定义,要求时,必须由顾客批准。
对于计数型数据抽样,接收水平必须是零缺陷”。
标准条文明确规定的,也就是我们要恪守的。
其实我们也一直在实用C=O的抽样检验方案。
但对其认识上可能存在一定的误区。
导致其真正的效率发挥的不够充分。
所以希望通过本文,能起抛砖引玉作用,为公司后续检验和试验活动更加顺畅的开展起到积极作用。
C=0抽样方案
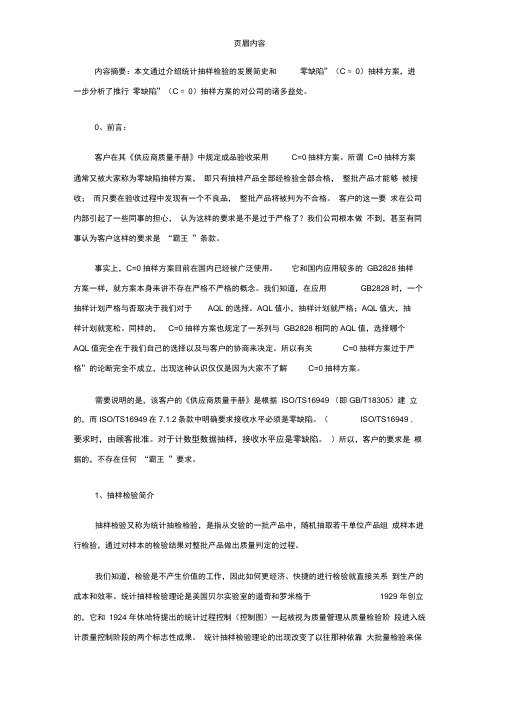
内容摘要:本文通过介绍统计抽样检验的发展简史和零缺陷”(C = 0)抽样方案,进一步分析了推行零缺陷”(C = 0)抽样方案的对公司的诸多益处。
0、前言:客户在其《供应商质量手册》中规定成品验收采用C=0抽样方案。
所谓C=0抽样方案通常又被大家称为零缺陷抽样方案,即只有抽样产品全部经检验全部合格,整批产品才能够被接收;而只要在验收过程中发现有一个不良品,整批产品将被判为不合格。
客户的这一要求在公司内部引起了一些同事的担心,认为这样的要求是不是过于严格了?我们公司根本做不到,甚至有同事认为客户这样的要求是“霸王”条款。
事实上,C=0抽样方案目前在国内已经被广泛使用。
它和国内应用较多的GB2828抽样方案一样,就方案本身来讲不存在严格不严格的概念。
我们知道,在应用GB2828时,一个抽样计划严格与否取决于我们对于AQL的选择。
AQL值小,抽样计划就严格;AQL值大,抽样计划就宽松。
同样的,C=0抽样方案也规定了一系列与GB2828相同的AQL值,选择哪个AQL值完全在于我们自己的选择以及与客户的协商来决定。
所以有关C=0抽样方案过于严格”的论断完全不成立,出现这种认识仅仅是因为大家不了解C=0抽样方案。
需要说明的是,该客户的《供应商质量手册》是根据ISO/TS16949 (即GB/T18305)建立的,而ISO/TS16949在7.1.2条款中明确要求接收水平必须是零缺陷。
(ISO/TS16949 , 要求时,由顾客批准。
对于计数型数据抽样,接收水平应是零缺陷。
)所以,客户的要求是根据的,不存在任何“霸王”要求。
1、抽样检验简介抽样检验又称为统计抽检检验,是指从交验的一批产品中,随机抽取若干单位产品组成样本进行检验,通过对样本的检验结果对整批产品做出质量判定的过程。
我们知道,检验是不产生价值的工作,因此如何更经济、快捷的进行检验就直接关系到生产的成本和效率。
统计抽样检验理论是美国贝尔实验室的道奇和罗米格于1929 年创立的,它和1924 年休哈特提出的统计过程控制(控制图)一起被视为质量管理从质量检验阶段进入统计质量控制阶段的两个标志性成果。
- 1、下载文档前请自行甄别文档内容的完整性,平台不提供额外的编辑、内容补充、找答案等附加服务。
- 2、"仅部分预览"的文档,不可在线预览部分如存在完整性等问题,可反馈申请退款(可完整预览的文档不适用该条件!)。
- 3、如文档侵犯您的权益,请联系客服反馈,我们会尽快为您处理(人工客服工作时间:9:00-18:30)。
8.1当问题出现时,我们需要持续改进:在这个过程中,生产主管必须要求员工执行;(1)确认上道工序产品的加工质量;(2)确认本工序加工的技术﹑工艺要求和加工质量;(3)确认交付到下道工序的完成品质量.
8.2在生产环节中体现在两个方面:一是控制,二是操作.所谓的控制主要是指管理﹑计划﹑经营﹑设计等内部的各个环节.所谓的操作是指一种产品在制造过程中的各个工序或流程.其结果表现就是产品符合顾客的要求,也就是产品没有缺陷了.
5.刮花面积≤6mm×2mm,
4.3解决缺陷方案:
4.3.1.当出现缺陷时,要及时向车间主管反映,核心是预防,重点是分析,分析有两层意思:一是找原因,二是控制及改善.
4.3.2.凡是属于A﹑B类就是零缺陷,在终检时发现一个,整批货就要作返工处理,对于返工产品100﹪检验,返工后还须重检,合格后方可放行.
9.0相关文件
《产品检验程序》
编制
彭小珍
审核
批准
5
51-90
5
91-150
8
151-280
13
281-500
13
501-1200
20
1201-3200
32
3201-10000
32
10001-35000
50
35001-150000
80
150001-500000
80
500001以上
125
编制
彭小珍
审核
批准
江门市富成金属制品有限公司
文件编号
WI803
版本编号
江门市富成金属制品有限公司
文件编号
WI803
版本编号
BO
文件标题:
宜家成品抽样方案
页码
第1页共2页
生效日
2012.9.4
1.0目的
对最终检验取样计划的目的,确保交给客户合格的产品,符合客户的要求。
2.0适用范围
适用于宜家公司所有包装出货的成品。
3.0内容
①零缺陷(C=0)抽样方案。
4.0缺陷及其分类:
4.3.3.在生产过程中,全检QC要认真检查好质量,如巡检发现有一个属于A﹑B类的产品一定要把当天所做的作返工处理,返工后巡检员要重检,确保合格才能入仓.
5.0取样计划
抽样标准MIL-STD-105E特殊抽样S-4
批量(N)
样本大小
A、B类
(Ac,Re)
2-8
2
(0,1)
9-50
BO
文件标题:
宜家成品抽样方案
页码
第2页共2页
生效日
2012.9.4
5.1在最终检验中宜家A、B类只接受零缺陷.C类可接受7﹪不良数.
6.0每批货品检验合格后,要根据批量,产品名称,数量,合同号等标识好,同时对检查的结果要详细记录在《成品验货报表》上并交给品质主管保存.
7.0凡返工或返修的产品,终检员必须进行重检,并对重检结果再记录在报表上.
4.1缺陷:产品的某一“不合格”特征项,即产品不满足预期的使用或不满足规范的要求即构成缺陷。
4.2质量特性:根据缺陷产生后果的严重程度,将缺陷分为:致命缺陷(A类),严重缺陷(B类),一般缺陷(C类),可潜在改善项.
A类:伤及人身体健康(利角或利边)
B类:技术参数要求、外形、外观、安装尺寸等。
C类:1.文字局部印虚,2.文字笔划短缺,3.同批同色色差超过标准样盒,4.不明显污渍