如何系统控制汽车涂装中的色差问题
车身油漆色差的分析及控制方法

车身油漆色差的分析及控制方法现代工业的蓬勃发展,人们对车辆外观的性能指标要求越来越高,车辆油漆色差是越来越受到重视的细节问题,而且复杂难以控制。
本文主要分析了影响车辆油漆色差的因素以及车辆油漆色差的控制方法。
一、前言现代车体越来越重视细节的搭配与装饰,例如车体与窗框、车门、端墙的颜色无偏差,以及编好组的列车每节车厢之间的颜色无偏差,这就对如何有效控制油漆色差提出了更高的要求。
现在色差的测量一般都采用仪器测量与目测相结合的方法,即根据标准比色板,通过仪器测量和目测相结合,使车辆与彩色小部件的色差在允许的误差范围之内。
这就需要究其根本,不断地改进技术和方法,控制车辆油漆色差。
二、车辆油漆色差的影响因素1.不同油漆批次的色差影响:不同批次的油漆由于在调配及原料采购过程中存在差异,所以就导致油漆本身就存在色差,但只要在所允许的色差范围之内,就能通过现场施工参数的调整来做出改变。
但是油漆原漆的色差误差范围要比现场施工范围要小,这是因为现场施工条件要远比油漆实验室的条件差,为了降低现场施工的难度,必须对原漆的色差做出严格控制。
2.油漆遮盖能力的影响:研究表明只有当材料的涂抹厚度大于15μm时,才能达到遮盖的效果。
一般车辆底色漆膜的厚度只能达到(12~15)μm,并不能完全遮盖底材,这是造成车辆漆膜发花、色差差的主要原因。
经研究表明,只有当漆膜的厚度达到遮盖厚度时,色差才能稳定,不再有大的波动。
这种缺陷主要表现在返修和补修时,由于一些颜色较浅的遮盖能力较差,再次重涂时容易超出色差误差范围。
3.现场施工参数的影响:现场施工参数的调整对油漆色差有直接影响。
主要是影响到L值的变化。
出漆量增大时,L减小,雾化空气、成型空气和喷涂速度增大时,L值增大。
4.手工补漆的影响:车辆涂漆的流水线上一般都设有手工补漆区,来弥补涂漆流程中的一些油漆缺陷和划碰伤,手工喷涂技术的高低和喷涂工艺的先进与否在很大程度上的影响了车辆油漆色差的质量。
汽车油漆色差产生的原因与控制方法
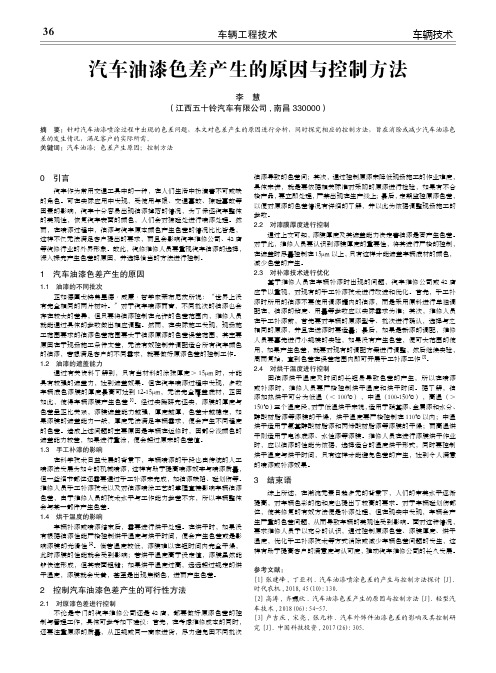
车辆工程技术36车辆技术0 引言 汽车作为常用交通工具中的一种,在人们生活中扮演着不可或缺的角色。
可在实际应用中发现,受使用年限、交通事故、擦碰事故等因素的影响,汽车十分容易出现油漆掉落的情况,为了保证汽车整体的美观性,恢复汽车表面的颜色,人们会对擦碰处进行喷漆处理。
然而,在喷漆过程中,油漆与汽车原本颜色产生色差的情况比比皆是,这样不仅无法满足客户提出的要求,而且会影响汽车维修公司、4S店等汽修行业的外界形象。
故此,汽修维修人员要重视汽车油漆的选择,深入探究产生色差的原因,并选择恰当的方法进行控制。
1 汽车油漆色差产生的原因1.1 油漆的不同批次 正如德国戈特弗里德·威廉·哲学家莱布尼茨所说:“世界上没有完全相同的两片树叶。
”对于汽车喷漆而言,不同批次的油漆也会存在较大的差异,但只要将油漆控制在允许的色差范围内,维修人员就能通过具体的参数做出相应调整。
然而,在实际施工发现,现场施工范围要求的油漆色差范围要大于油漆原漆的色差误差范围,其主要原因在于现场施工条件太差,无法有效控制并调配适合所有汽车颜色的油漆,若想满足客户的不同需求,就要做好原漆色差的控制工作。
1.2 油漆的遮盖能力 通过有关资料了解到,只有当材料的涂抹厚度>15μm时,才能具有较强的遮盖力,达到遮盖效果。
但在汽车喷漆过程中发现,多数车辆底色漆膜的厚度最高可达到12-15μm,无法完全覆盖底材,正因如此,使得车辆漆膜产生色差[1]。
经过实践研究证实,漆膜的厚度与色差呈正比关系,漆膜遮盖能力越强,厚度越厚,色差才越稳定,如果漆膜的遮盖能力一般,厚度无法满足车辆需求,便会产生不同程度的色差。
造成上述问题的主要原因是车辆在返修时,因部分浅颜色的遮盖能力较差,如果进行重涂,便会超过原来的色差值。
1.3 手工补漆的影响 在科学技术日益发展的背景下,车辆喷漆的手段也由传统的人工喷漆法发展为如今的机械喷漆,这样有助于提高喷漆效率与喷漆质量,但一些细节部位还需要通过手工补漆来完成,如油漆缺陷、碰划伤等。
汽车涂装的缺陷和改进措施
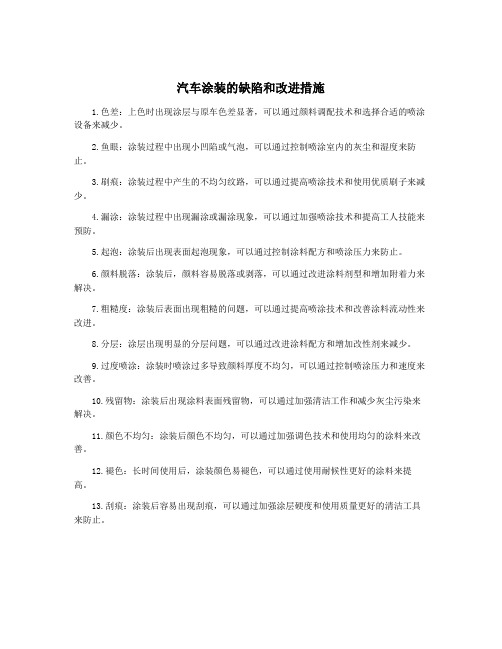
汽车涂装的缺陷和改进措施
1.色差:上色时出现涂层与原车色差显著,可以通过颜料调配技术和选择合适的喷涂设备来减少。
2.鱼眼:涂装过程中出现小凹陷或气泡,可以通过控制喷涂室内的灰尘和湿度来防止。
3.刷痕:涂装过程中产生的不均匀纹路,可以通过提高喷涂技术和使用优质刷子来减少。
4.漏涂:涂装过程中出现漏涂或漏涂现象,可以通过加强喷涂技术和提高工人技能来预防。
5.起泡:涂装后出现表面起泡现象,可以通过控制涂料配方和喷涂压力来防止。
6.颜料脱落:涂装后,颜料容易脱落或剥落,可以通过改进涂料剂型和增加附着力来解决。
7.粗糙度:涂装后表面出现粗糙的问题,可以通过提高喷涂技术和改善涂料流动性来改进。
8.分层:涂层出现明显的分层问题,可以通过改进涂料配方和增加改性剂来减少。
9.过度喷涂:涂装时喷涂过多导致颜料厚度不均匀,可以通过控制喷涂压力和速度来改善。
10.残留物:涂装后出现涂料表面残留物,可以通过加强清洁工作和减少灰尘污染来解决。
11.颜色不均匀:涂装后颜色不均匀,可以通过加强调色技术和使用均匀的涂料来改善。
12.褪色:长时间使用后,涂装颜色易褪色,可以通过使用耐候性更好的涂料来提高。
13.刮痕:涂装后容易出现刮痕,可以通过加强涂层硬度和使用质量更好的清洁工具来防止。
浅谈汽车喷漆过程中色差产生的原因及预防方法
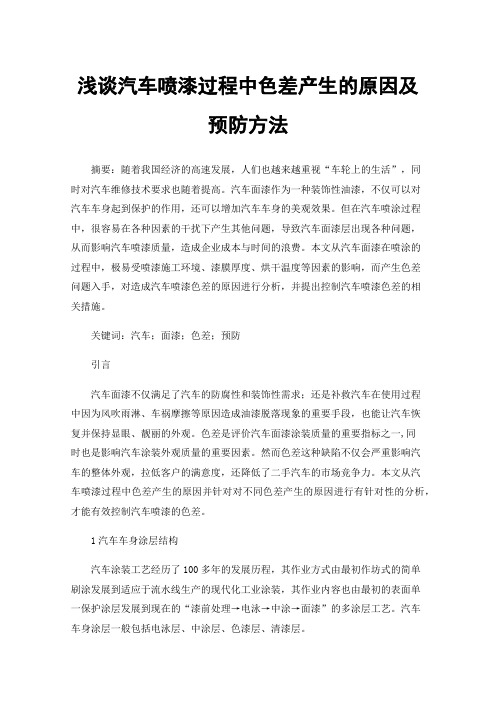
浅谈汽车喷漆过程中色差产生的原因及预防方法摘要:随着我国经济的高速发展,人们也越来越重视“车轮上的生活”,同时对汽车维修技术要求也随着提高。
汽车面漆作为一种装饰性油漆,不仅可以对汽车车身起到保护的作用,还可以增加汽车车身的美观效果。
但在汽车喷涂过程中,很容易在各种因素的干扰下产生其他问题,导致汽车面漆层出现各种问题,从而影响汽车喷漆质量,造成企业成本与时间的浪费。
本文从汽车面漆在喷涂的过程中,极易受喷漆施工环境、漆膜厚度、烘干温度等因素的影响,而产生色差问题入手,对造成汽车喷漆色差的原因进行分析,并提出控制汽车喷漆色差的相关措施。
关键词:汽车;面漆;色差;预防引言汽车面漆不仅满足了汽车的防腐性和装饰性需求;还是补救汽车在使用过程中因为风吹雨淋、车祸摩擦等原因造成油漆脱落现象的重要手段,也能让汽车恢复并保持显眼、靓丽的外观。
色差是评价汽车面漆涂装质量的重要指标之一,同时也是影响汽车涂装外观质量的重要因素。
然而色差这种缺陷不仅会严重影响汽车的整体外观,拉低客户的满意度,还降低了二手汽车的市场竞争力。
本文从汽车喷漆过程中色差产生的原因并针对对不同色差产生的原因进行有针对性的分析,才能有效控制汽车喷漆的色差。
1汽车车身涂层结构汽车涂装工艺经历了100多年的发展历程,其作业方式由最初作坊式的简单刷涂发展到适应于流水线生产的现代化工业涂装,其作业内容也由最初的表面单一保护涂层发展到现在的“漆前处理→电泳→中涂→面漆”的多涂层工艺。
汽车车身涂层一般包括电泳层、中涂层、色漆层、清漆层。
电泳层:使汽车涂层获得耐久性和耐腐蚀性中涂层:具有与电泳底漆和面漆涂膜的良好附着结合力、耐崩裂性、耐气候性、提高面漆遮盖性和高级外观功能性。
色漆层:具有色彩,金属效果装饰性,且与中涂和清漆两者具有良好的附着力,具有一定的自身保护性。
清漆层:是一层透明保护层。
处于最外层,和色漆层结合具有防紫外线功能,防透水性能,耐气候性、保色性、耐酸雨性、抗划伤性能等功能。
喷漆工艺中常见的质量问题及分析处理方法
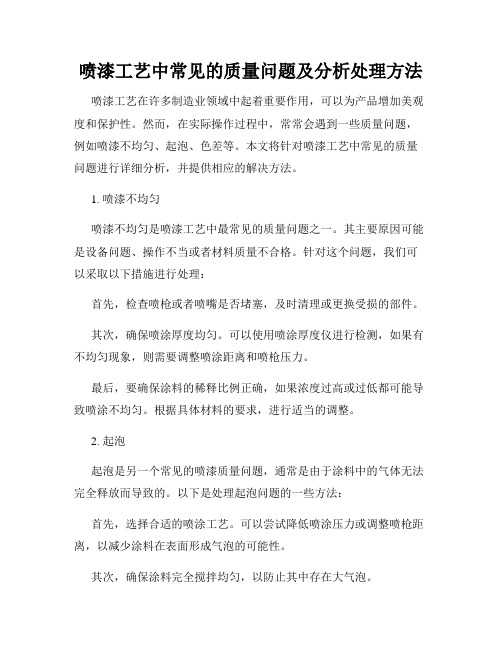
喷漆工艺中常见的质量问题及分析处理方法喷漆工艺在许多制造业领域中起着重要作用,可以为产品增加美观度和保护性。
然而,在实际操作过程中,常常会遇到一些质量问题,例如喷漆不均匀、起泡、色差等。
本文将针对喷漆工艺中常见的质量问题进行详细分析,并提供相应的解决方法。
1. 喷漆不均匀喷漆不均匀是喷漆工艺中最常见的质量问题之一。
其主要原因可能是设备问题、操作不当或者材料质量不合格。
针对这个问题,我们可以采取以下措施进行处理:首先,检查喷枪或者喷嘴是否堵塞,及时清理或更换受损的部件。
其次,确保喷涂厚度均匀。
可以使用喷涂厚度仪进行检测,如果有不均匀现象,则需要调整喷涂距离和喷枪压力。
最后,要确保涂料的稀释比例正确,如果浓度过高或过低都可能导致喷涂不均匀。
根据具体材料的要求,进行适当的调整。
2. 起泡起泡是另一个常见的喷漆质量问题,通常是由于涂料中的气体无法完全释放而导致的。
以下是处理起泡问题的一些方法:首先,选择合适的喷涂工艺。
可以尝试降低喷涂压力或调整喷枪距离,以减少涂料在表面形成气泡的可能性。
其次,确保涂料完全搅拌均匀,以防止其中存在大气泡。
另外,要保证基材的表面干燥、清洁和光滑,以便涂料能够更好地附着并排出潜在的气泡。
3. 色差色差是指涂装表面出现的不一致的颜色。
这可能是由于涂料本身的质量问题、施工环境的差异或操作人员的不当处理导致的。
下面是解决色差问题的几种方法:首先,确保使用的涂料来源可靠,并符合预期颜色的要求。
其次,要控制好施工环境的温度和湿度。
过高或过低的温度都会影响涂料的干燥速度和颜色表现。
另外,操作人员应该严格按照涂料生产厂家提供的使用说明进行操作,以确保正确的涂装过程。
4. 涂料流挂涂料流挂是指喷涂后在表面上形成垂直流痕或滴状流动的现象。
这可能是由于喷涂过度或者涂料粘度过高导致的。
下面是处理涂料流挂问题的一些建议:首先,调整喷涂时间和压力,确保每一次喷涂的涂料量适中。
其次,可以尝试使用低粘度的涂料,以减少涂料在表面上流动的可能性。
汽车涂装工艺中的喷漆过程质量控制
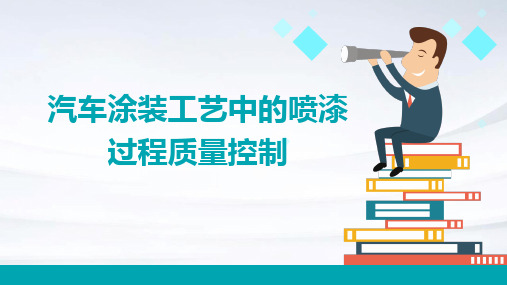
涂层外观质量的检查
01
02
03
04
颜色
检查涂层的颜色是否与标准色 相符,有无色差、发花等现象
。
光泽度
检查涂层的光泽度是否符合要 求,有无失光、眩光等现象。
表面平整度
检查涂层表面是否平整光滑, 有无桔皮、起皱等现象。
附着力
检查涂层的附着力是否良好, 是否能够牢固地附着在基材表
面。
03 喷漆后的质量检测与控制
02
常用的涂层硬度检测方 法有铅笔硬度法和邵氏 硬度法。
03
铅笔硬度法是通过在涂 层表面划痕,观察所需 施加的力来评定涂层的 硬度。
04
邵氏硬度法则是通过测 量涂层表面的反弹力来 确定其硬度值。
涂层附着力的检测
01
02
03
04
涂层附着力是指涂层与基材之 间的粘结力,是评价涂装质量
的重要指标之一。
常用的涂层附着力检测方法有 划格法、拉开法等。
汽车涂装工艺中的喷漆 过程质量控制
目录
Contents
• 喷漆前的准备 • 喷漆过程中的质量控制 • 喷漆后的质量检测与控制 • 喷漆过程中的常见问题及解决方案 • 案例分析
01 喷漆前的准备
表面处理
01
02
03
表面清洁
清除表面污渍、油渍、锈 迹和其他杂质,确保表面 干净无异物。
表面干燥
确保待喷漆表面完全干燥 ,无水分残留,以免影响 漆膜质量。
稳定等。
解决方案
03
定期清洁和检查喷枪,确保涂料混合均匀,调整压缩空气压力
。
涂层出现流淌
总结词
涂层在干燥前出现流动或不均匀分布的现象。
详细描述
可能是由于涂料粘度不合适、喷涂距离过近或喷 涂层数过多等。
喷漆作业中色差出现的原因与解决方法

喷漆作业中色差出现的原因与解决方法喷漆作业是一项常见的涂装工艺,广泛应用于汽车、家具等行业。
然而,在喷漆作业过程中,色差问题常常会引起不少不满。
本文将探讨喷漆作业中色差出现的原因以及解决方法,旨在帮助读者更好地理解和处理这一难题。
1. 原因分析1.1 颜料质量不均匀颜料是喷漆作业中决定颜色的关键因素。
如果颜料质量不均匀,其中某部分颜料含量过高或过低,就会导致色差问题。
这可能是由于原料不准确配比、生产工艺不规范等因素引起的。
1.2 喷涂厚度不均匀喷涂厚度不均匀也是导致色差的常见原因。
喷涂时,如果涂层的厚度在不同区域存在差异,会导致颜色呈现出不一致的情况。
这可能是由于喷涂设备不匀速或者操作人员技术水平不高引起的。
1.3 喷漆环境影响喷漆作业的环境也会对涂层的色差产生一定影响。
例如,温度、湿度等环境因素的变化都有可能导致颜色不稳定,从而产生色差。
此外,喷漆过程中存在的灰尘、污染物等也会对涂层的颜色产生影响。
2. 解决方法2.1 选择优质颜料为了避免颜料质量不均匀导致的色差问题,选用优质颜料是至关重要的。
优质颜料配比准确且稳定,能够保证涂层的色彩一致性。
在选择颜料供应商时,应该注重其信誉度和产品质量。
2.2 控制喷涂厚度为了解决喷涂厚度不均匀带来的色差问题,需要加强对喷涂厚度的控制。
可以使用合适的喷涂设备,确保喷漆速度和厚度均匀。
此外,还可以加强对操作人员的培训,增强其专业技能和操作经验。
2.3 优化喷漆环境为了减少喷漆环境对色差的影响,可以采取一些措施进行优化。
控制喷漆作业的温度和湿度,确保环境条件的稳定。
此外,在喷漆区域设置过滤装置,有效过滤灰尘和污染物,减少其对涂层颜色的影响。
3. 结论喷漆作业中色差问题是一个常见但又十分困扰的难题。
在解决这一问题时,我们需要充分认识色差产生的原因。
只有明确了原因,才能针对性地采取解决方法。
因此,选择优质颜料、控制喷涂厚度、优化喷漆环境等方法都是可以采取的措施。
希望本文的内容能够给读者带来帮助,使他们在喷漆作业中更好地解决色差问题。
汽车车身油漆色差匹配与目视色差控制
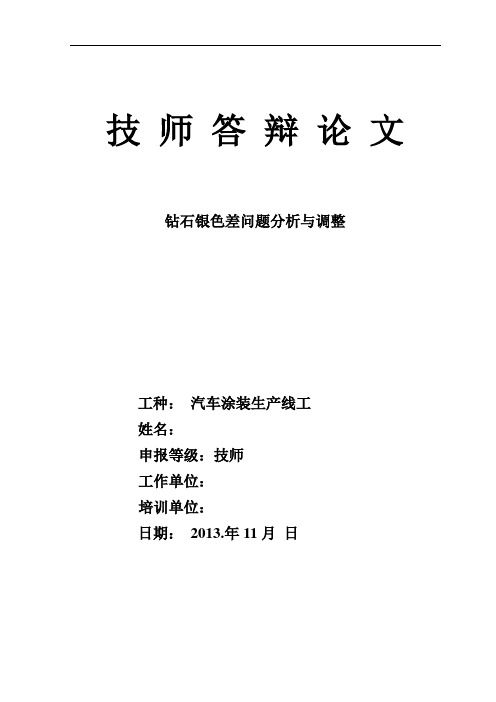
技师答辩论文钻石银色差问题分析与调整工种:汽车涂装生产线工姓名:申报等级:技师工作单位:培训单位:日期:2013.年11月日车身油漆色差匹配目视色差控制内容摘要及关键词内容摘要:通过对颜色、目视和色差仪的基本介绍,了解色差测量的原理;在介绍车身油漆颜色匹配控制方法的同时,重点阐述在XX车制造系统中,当漆后车身颜色(出现色差)匹配过程中,色差仪测量数据不能满足调整需要时,XX目视色差控制方法对钻石银色相调整的作用。
关键词:颜色、色差仪,漆后车身、颜色匹配、Willing booth、目视色差评判。
前言随着汽车市场的发展,乘用车进入家庭的不断普及,用户对于所购买车辆要求也在不断提高。
以前,顾客挑选汽车主要是看性能,只要性能好,其他都是次要的。
而随着汽车性能的提高以及品质的增加,外观日渐成为顾客挑选汽车的首选要素;而车身颜色的匹配问题逐渐突显出来!现在车身各部位大量使用不同厂家生产的外协件时,底材和工艺不同,对涂装厂油漆颜色的控制提出了更高的要求。
所以根据多年的色差考核经验,在本文中以钻石银色差匹配为例,通过介绍油漆色差仪器检测数据问题和XX独特的目视检查色差控制方法。
对色差问题进行分析,查找原因,调整油漆色相,改进钻石银色差匹配问题。
一、颜色基本原理颜色是一种通过观察者的眼睛所捕获的光线刺激(波长、强度等等),并在头脑中形成的解释。
色彩的3种特质:1、色相(Hue):是区分不同彩色的视觉属性,它取决于光源的光谱组成以及物体表面对各种波长可见光的反射比例,是表示物体的颜色质的方面的特性,色相就是物体呈现各种颜色的特性。
2、明度(Lighting):是人眼对物体明亮程度的感觉,明度不仅取决定物体照明程度,而且取决于物体表面的反射系数。
如果我们看到的光线来源于光源,那么明度决定了光源的强度。
如果我们看到的是来源于物体表面反射的光线,那么明度决定于照明的光源的强度和物体表面的反射系数。
3、彩度(Chroma)通俗意义上来讲,就是颜色的鲜艳程度。
汽车涂装中的涂装色差与配色技术
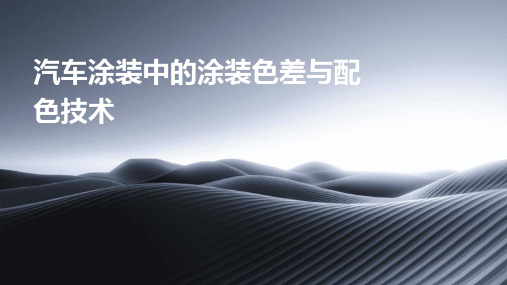
未来发展趋势预测
智能化技术应用
随着人工智能、大数据等技术的不断发展,未来汽车涂装将实现更高程度的自动化和智 能化,提高生产效率和涂装质量。
环保法规要求提高
随着全球环保意识的增强和环保法规的日益严格,汽车涂装行业将面临更高的环保要求 和挑战,需要采取更环保的涂料和涂装工艺。
为满足市场多元化需求,提升车型竞争力,某汽车厂商决定对旗下某款车型进行全新颜色设计。
设计过程
设计团队首先进行了市场调研,分析了目标消费者的喜好和流行趋势,然后结合车型特点和品牌定位,制定了多种颜 色方案。经过多次评审和修改,最终选定了符合市场需求和品牌形象的车身颜色。
设计成果
新颜色方案的应用显著提升了该车型的视觉效果和辨识度,赢得了消费者的广泛好评,同时也为品牌注 入了新的活力。
建立色差管理体系
建立完善的色差管理体系,包括色差标准制定、色差检测、色差分 析和处理等环节,以确保涂装质量的稳定性和一致性。
强化质量意识教育
加强员工的质量意识教育,使员工充分认识到色差对产品质量和客户 满意度的影响,提高员工对色差控制的重视程度。
05
配色技术应用实践
某车型车身颜色设计案例分享
设计背景
01
案例一
某汽车制造厂涂装车间出现色差问题,通过目视法和色差计法进行检测
,发现ΔE值超过了企业标准。经过调整涂料配方和工艺参数,最终使
色差控制在标准范围内。
02
案例二
某汽车零部件供应商向主机厂提供的涂装件存在明显色差,经过光谱分
析发现涂料中某种颜料含量不足。供应商对涂料进行调整后,重新提供
的涂装件颜色与主机厂要求一致。
喷涂色差原因分析及喷涂不良现象原因分析对策技术资料
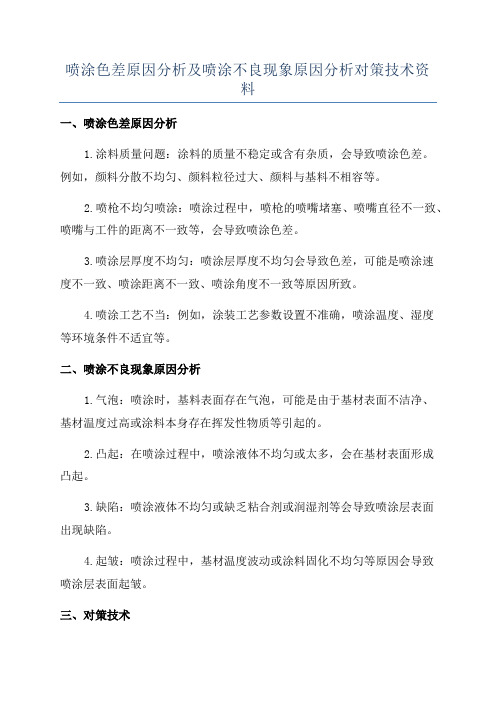
喷涂色差原因分析及喷涂不良现象原因分析对策技术资料一、喷涂色差原因分析1.涂料质量问题:涂料的质量不稳定或含有杂质,会导致喷涂色差。
例如,颜料分散不均匀、颜料粒径过大、颜料与基料不相容等。
2.喷枪不均匀喷涂:喷涂过程中,喷枪的喷嘴堵塞、喷嘴直径不一致、喷嘴与工件的距离不一致等,会导致喷涂色差。
3.喷涂层厚度不均匀:喷涂层厚度不均匀会导致色差,可能是喷涂速度不一致、喷涂距离不一致、喷涂角度不一致等原因所致。
4.喷涂工艺不当:例如,涂装工艺参数设置不准确,喷涂温度、湿度等环境条件不适宜等。
二、喷涂不良现象原因分析1.气泡:喷涂时,基料表面存在气泡,可能是由于基材表面不洁净、基材温度过高或涂料本身存在挥发性物质等引起的。
2.凸起:在喷涂过程中,喷涂液体不均匀或太多,会在基材表面形成凸起。
3.缺陷:喷涂液体不均匀或缺乏粘合剂或润湿剂等会导致喷涂层表面出现缺陷。
4.起皱:喷涂过程中,基材温度波动或涂料固化不均匀等原因会导致喷涂层表面起皱。
三、对策技术1.选择质量稳定的涂料:在进行喷涂工艺前,要选择质量稳定的涂料,确保涂料中颜料分散均匀、颜料粒径适宜、颜料与基料相容等。
2.喷枪维护保养:定期清洁喷枪的喷嘴,保证喷枪的喷嘴直径一致,并确保喷嘴与工件的距离一致。
3.控制喷涂层厚度:根据工艺要求,控制喷涂层的厚度均匀,确保喷涂速度、距离和角度一致。
4.合理设置喷涂工艺参数:根据不同的工件和涂料,合理设置喷涂工艺参数,包括喷涂温度、湿度等环境条件。
5.处理基材表面:确保基材表面清洁,有利于涂料附着和固化。
6.控制喷涂液体量:调整喷涂量,确保涂料均匀喷涂,避免出现凸起、缺陷和起皱等问题。
7.控制喷涂层固化:确保喷涂层的固化均匀,避免喷涂层表面出现起皱等现象。
总结:喷涂色差及喷涂不良现象的原因很多,可能是涂料质量问题、喷枪不均匀喷涂、喷涂层厚度不均匀、喷涂工艺不当等。
解决这些问题需要选择质量稳定的涂料、维护保养喷枪、控制喷涂层厚度、合理设置喷涂工艺参数、处理基材表面、控制喷涂液体量以及控制喷涂层固化等对策技术。
汽车涂装修补色差控制
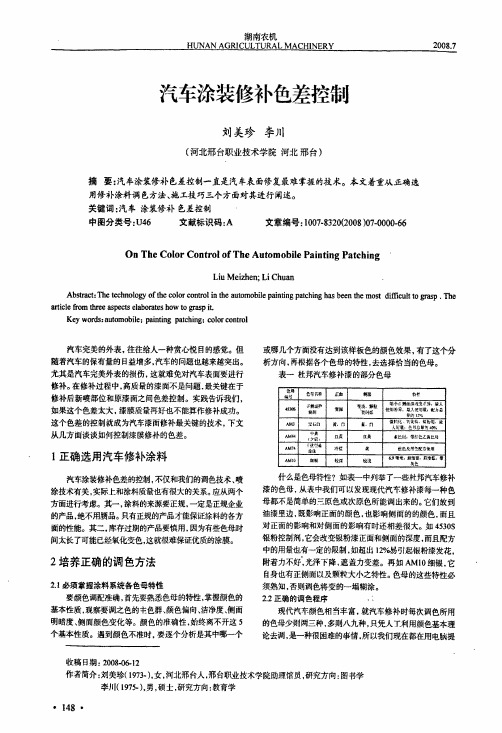
2.1蹇矮 掌握 涂料 系统 冬色 母特 性 要颜 色躅配 躐确, 蓄先要 熟悉色 母豹耪 缝,掌 糕颏龟 的
基本性质,观察 簧谰之色的丰色群、颜色偏向、 洁净魔、侧面 明暗度、侧而颜色变化等。颜色的凇确性,始终离不开这5 个基本性质。遇魏凝色不准时,舞逐个分析是其中哪一个
或戮咫个方嚣爱骞达到浚祥叛色稳颜毽效槊,有了这个势 析宵 向,再根据 各个色 璐的特性, 去选择 恰嬲的色母 。
图1
步骤 二:表嚣准 备
日常工作中,我们所使用的颜色标准板( 如油箱盖,车
身部位泼蟊往镰有诲多污染物,可笺会影响颜色的毙对效
果。 因此, 配色前 ,应该 用细 蜡进行 清洁处 理,以 免造成 将
来车 身土的颜 色差异 。
步骤三 :色卡的 比对
麴祭第一步孛无法我劐缀厂色号,鄂么簿泼蒯掰漆漆
公司 提供 的各种 色卡, 从色 相、明 度、 彩度三 个方面 进行 比
袋一杜邦汽车修补漆的部分色母
鬯母 瓣蜷
硝辫
AMJ ^ M“ AM74 ^醚播
苞罐嚣转
手嚣蓬挣 旗熬
宝 石由 中请
( ,锝, { ’抗岱曲 缘庸
燕整
正蠡 蹙鞋 赭. n £L点 持监 觳罐
褥垂 亳T囔t 髯轻
‘墼魏 嚣 蓝. n 红煎
特种
端枣《 舞激撵意 耋孽葶, 鼙^ 霞瓣箨霉。竣五 理| §薤t 鬈由霉
荦柏i ! % {堑札纯.锻化镜,镪耘增.衄
^Ⅲ 髓{敬 雌船瞬 相40 %
索媳州- {苷打心上受也坶
鳇 较琏
鲢戡盥撒皂&方娃堆
6.9罐米,轻辩毪}。毒盎瓿,帮 袭盎
补么是色母特性?如裘一孛嬲举了一些牲邦汽车修料 漆的色垛,从表中我们诃以发现现代汽车修补漆每一种色 母都不是简单的三原色戏次原色所能调出米的。它们放列 油漆里逑, 既影响正蕊的颜பைடு நூலகம், 也影嚷侧瓤的的颜色 ,{}l ;E 对匿黉鲍影璃:穰对裁露的影晌毒薅还鞠差缀大。如4530S 镊粉 控制 潮,宅 会改变 银粉 漆正蘑 稻绷 褥酌深 度,丽 且配 方 中的 用黻也 有一定的 限制, 如超出 12%易 引勰银粉 漆发花 。 附着力不好,光泽下降。遮懿力变差。再如AMl 0细银,它 是身也露正侧恧以及颡糙大小之特性。色母的这些特性必 蔟熬 麓,孬照调 色将变 的~塌糊涂 。 2.2嚣 鞴麴调色 程序
车身油漆色差的影响因素及控制方法

车身油漆色差的影响因素及控制方法摘要:从色漆材料、喷涂工艺、喷涂设备及供漆系统状态等方面探讨了色差的影响因素,提出了相应的控制方法。
1 前言车身油漆色差是每个涂装生产部门都会遇到的一个非常复杂且难以控制的问题,随着保险杠、门把手、后视镜及加油小门等彩色塑料件的大量采用,要求车身与塑料件的颜色无偏差,这就对车身油漆色差的控制提出了更高的要求。
目前轿车厂流行的方法是采用仪器测量与目测相结合的方式来控制色差,一般提供一块标准颜色样板,要求车身及塑料配件的颜色与该标准样板相比无论是目测,还是仪器测量都应接近。
车身油漆色差的影响因素众多,它与色漆材料、喷涂工艺、喷涂设备、供漆系统状态等因素密切相关。
本文就车身油漆色差的控制谈一点看法。
2.色差的概念及测量2.1 色差为了定量地表示颜色,目前通常采用CIE 表色系统,它采用分光光度法对颜色进行分析,精度高。
Lab 色空间是目前最流行的用于测量物体颜色的色空间(如图1所示)。
在该色空间中,L *为明度,+L *为白色方向,-L *为黑色方向。
a *,b *为色度坐标,其中+a *为红色方向,-a *为绿色方向,+b *为黄色方向,-b *为蓝色方向,中心为无色。
L *、a *、b *可由三刺激值X 、Y 、Z 计算而得。
图1 L *a *b *色空间LCH 色空间与Lab 色空间的色度图相同,但该色空间为柱面坐标而不是直角坐标。
L *表示明度,与Lab 色空间的L *值相同,H 表示色相,C 表示饱和度。
CIELAB 色空间中的两个色度值(L *样品,a *样品,b *样品)和(L *标准,a *标准,b *标准)之间的色差△E ab *由下式决定:△E ab * = [(△L *)2+(△a *)2+(△b *)2]1/2绿 -a*其中:△L*= L*样品- L*标准(明度差异),△a*= a*样品- a*标准(红/绿差异),△b*= b*样品- b*标准(黄/蓝差异)如△L*为正值,说明样品颜色偏浅;△L*为负值,样品偏深。
车身喷漆工艺步骤详解实现色差调整与涂装效果控制

车身喷漆工艺步骤详解实现色差调整与涂装效果控制车身喷漆是车辆制造过程中非常重要的一环,它不仅可以保护车身表面,还能提升车辆的外观质量。
然而,由于车辆生产过程中的各种原因,车身喷漆中常常会出现色差问题,这对于整车的外观造成了很大的影响。
因此,如何实现色差调整与涂装效果的控制变得尤为重要。
本文将详细介绍车身喷漆工艺步骤,并探讨实现色差调整与涂装效果控制的方法。
一、准备工作在进行车身喷漆之前,我们需要做一些准备工作。
首先,要对车身表面进行清洁和打磨,确保涂料能够附着在车身表面。
其次,要对车身进行检查,发现任何瑕疵或损坏,都需要进行修复。
最后,要对喷漆设备进行检查和保养,确保其正常工作。
二、底漆喷涂底漆是车身喷漆的第一步,它起到了防锈和增强涂料附着力的作用。
底漆的选择很重要,要保证它与涂料相容,并且能够与车身表面形成均匀的底膜。
在喷涂底漆之前,需要进行调色和调配,确保与整车车漆的颜色相匹配。
同时,底漆喷涂过程中要注意喷涂厚度的控制,以免影响整体涂装效果。
三、修平喷漆在车身喷漆过程中,由于多种原因可能会出现凹陷或磨损的情况。
为了修复这些问题,需要进行修平喷漆。
修平喷漆是一项精细的工作,需要技术熟练的操作者和高质量的喷涂设备。
在进行修平喷漆之前,需要对车身表面进行打磨和清洁,修复损坏或凹陷的部位,使其与周围的车身表面平整一致。
然后,使用合适的喷漆工具进行均匀喷涂,并确保修平部位与周围的车身表面无明显色差。
四、涂装阶段涂装是车身喷漆的核心步骤,决定了最终涂装效果的好坏。
在涂装过程中,需要控制喷漆的厚度、涂料的流动性和喷漆的速度等因素,以保证涂料能够均匀地覆盖在车身表面,并且形成光滑的漆膜。
同时,还需要注意喷漆的角度和喷漆的顺序,以避免出现重叠或合并的问题。
在涂装过程中,也要注意湿润时间和干燥时间的控制,确保每一层涂料能够充分干燥和固化。
五、色差调整尽管我们在整个车身喷漆过程中都会尽可能地控制涂料的质量和涂装工艺,但仍然难以完全避免色差的出现。
汽车油漆色差产生的原因以及控制措施分析

汽车油漆色差产生的原因以及控制措施分析油漆喷涂色差是目前我国汽车喷涂行业里十分棘手的一个现象,有着十分重要的研究价值。
但是目前,我国关于汽车油漆喷涂色差出现以及相关控制策略的研究还相对较少,针对这样的实际情况,需要制定切实可行的方式对其进行不断总结与完善。
例如可以通过制定事先标准化的作业流程、强化施工材料选择、提升员工自身喷涂技能、基于技术层面进行分析等角度对其进行完善。
1 颜色属性自然界的颜色千千万万,但所有的颜色都有着三个共同的特点,就是具备一定的色彩相貌、浓淡程度和明亮程度。
一般来说,我们把颜色的这三个特点可以共称为颜色的三个特性或属性,分别为色调、明度与彩度,不管是什么颜色都可以利用这三个特性进行评定,可以对其进行定性、定量的描述。
此外颜色的这三个特性也可以利用现代仪器进行测定,也可以利用目测的方式对其进行评定。
1.1 色调色调又可称作是色别或者是色相,是色彩最为显著的特征,也是不同色彩之间最容易区别的特征之一。
色调一般表示为带有一定波长的单色光,能够准确表示颜色类别,也可以利用其对颜色类别名称进行分类,比如红、橙、黄、绿、青、蓝、紫,其所对应的都是某一具体的色调,紫红、红、红黄都是属于红色中的不同色调,其颜色之间的差别也可称之为色调差别。
1.2 明度明度又可稱为深浅度、亮度或者是黑白度,其代表的是物体反射光线的颜色属性,也是人们视觉上所能够看到的颜色明暗程度差别,同一种色调可以有不同的明度,不同的色调也可以存在不同的明度。
比如对于太阳光谱来说,紫色的明度最低,处于中等明度的颜色为红色、绿色,所有颜色中黄色的明度最高,这也是为什么我们感觉黄色是最亮的一种颜色的原因。
1.3 彩度彩度又可称作是饱和度或是纯度,指的是具有反射光线或是透射光线接近光谱色的一种程度,比如彩度一般可以分成0-20档,如果小于0.5,就可以称作为无彩度;如果彩度接近20,则可以称作是饱和度。
一般彩度是人体的心理纯度感觉,对于可见光谱来说,单色光是最纯的颜色,也可称作为极限纯度。
汽车外饰件油漆色差影响因素及控制措施
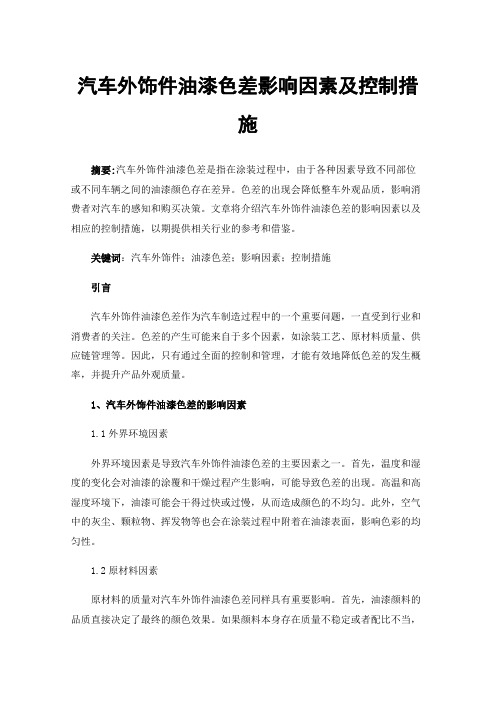
汽车外饰件油漆色差影响因素及控制措施摘要:汽车外饰件油漆色差是指在涂装过程中,由于各种因素导致不同部位或不同车辆之间的油漆颜色存在差异。
色差的出现会降低整车外观品质,影响消费者对汽车的感知和购买决策。
文章将介绍汽车外饰件油漆色差的影响因素以及相应的控制措施,以期提供相关行业的参考和借鉴。
关键词:汽车外饰件;油漆色差;影响因素;控制措施引言汽车外饰件油漆色差作为汽车制造过程中的一个重要问题,一直受到行业和消费者的关注。
色差的产生可能来自于多个因素,如涂装工艺、原材料质量、供应链管理等。
因此,只有通过全面的控制和管理,才能有效地降低色差的发生概率,并提升产品外观质量。
1、汽车外饰件油漆色差的影响因素1.1外界环境因素外界环境因素是导致汽车外饰件油漆色差的主要因素之一。
首先,温度和湿度的变化会对油漆的涂覆和干燥过程产生影响,可能导致色差的出现。
高温和高湿度环境下,油漆可能会干得过快或过慢,从而造成颜色的不均匀。
此外,空气中的灰尘、颗粒物、挥发物等也会在涂装过程中附着在油漆表面,影响色彩的均匀性。
1.2原材料因素原材料的质量对汽车外饰件油漆色差同样具有重要影响。
首先,油漆颜料的品质直接决定了最终的颜色效果。
如果颜料本身存在质量不稳定或者配比不当,就可能导致色差的出现。
其次,清漆和底漆的选择也会影响最终的色差情况,不同的涂料层之间的结合性能和透明度也会对颜色效果产生影响。
1.3涂装工艺因素涂装工艺是汽车外饰件油漆色差产生的重要因素之一。
首先,涂料的施工方式和涂布厚度对颜色的均匀性和稳定性有着重要影响。
如果涂层厚度不均匀、过厚或过薄,都可能导致色差的出现。
其次,涂布速度和涂布压力也会对涂料的均匀性产生影响。
较高的涂布速度和较大的涂布压力可能会导致油漆流动性不佳,进而影响颜色的一致性。
2.现有的油漆色差质量管理方法与技术手段2.1光谱仪及其应用光谱仪是一种能够测量物体反射、透射光谱的仪器。
在汽车外饰件油漆色差管理中,光谱仪常被用于精确测量颜色值,并与标准样品进行比对。
汽车修补漆调色色差管控对策
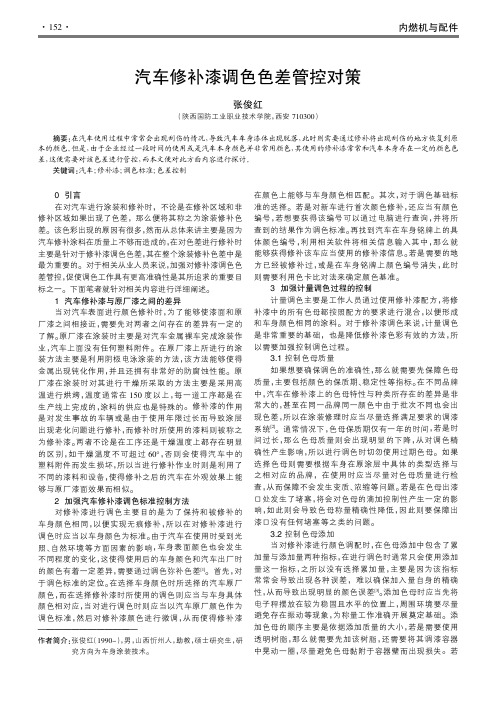
内燃机与配件0引言在对汽车进行涂装和修补时,不论是在修补区域和非修补区域如果出现了色差,那么便将其称之为涂装修补色差。
该色彩出现的原因有很多,然而从总体来讲主要是因为汽车修补涂料在质量上不够而造成的,在对色差进行修补时主要是针对于修补漆调色色差,其在整个涂装修补色差中是最为重要的。
对于相关从业人员来说,加强对修补漆调色色差管控,促使调色工作具有更高准确性是其所追求的重要目标之一。
下面笔者就针对相关内容进行详细阐述。
1汽车修补漆与原厂漆之间的差异当对汽车表面进行颜色修补时,为了能够使漆面和原厂漆之间相接近,需要先对两者之间存在的差异有一定的了解。
原厂漆在涂装时主要是对汽车金属裸车完成涂装作业,汽车上面没有任何塑料附件。
在原厂漆上所进行的涂装方法主要是利用阴极电泳涂装的方法,该方法能够使得金属出现钝化作用,并且还拥有非常好的防腐蚀性能。
原厂漆在涂装时对其进行干燥所采取的方法主要是采用高温进行烘烤,温度通常在150度以上,每一道工序都是在生产线上完成的,涂料的供应也是特殊的。
修补漆的作用是对发生事故的车辆或是由于使用年限过长而导致涂层出现老化问题进行修补,而修补时所使用的漆料则被称之为修补漆。
两者不论是在工序还是干燥温度上都存在明显的区别,如干燥温度不可超过60°,否则会使得汽车中的塑料附件而发生损坏,所以当进行修补作业时则是利用了不同的漆料和设备,使得修补之后的汽车在外观效果上能够与原厂漆面效果而相似。
2加强汽车修补漆调色标准控制方法对修补漆进行调色主要目的是为了保持和被修补的车身颜色相同,以便实现无痕修补,所以在对修补漆进行调色时应当以车身颜色为标准。
由于汽车在使用时受到光照、自然环境等方面因素的影响,车身表面颜色也会发生不同程度的变化,这使得使用后的车身颜色和汽车出厂时的颜色有着一定差异,需要通过调色弥补色差[1]。
首先,对于调色标准的定位。
在选择车身颜色时所选择的汽车原厂颜色,而在选择修补漆时所使用的调色则应当与车身具体颜色相对应,当对进行调色时则应当以汽车原厂颜色作为调色标准,然后对修补漆颜色进行微调,从而使得修补漆在颜色上能够与车身颜色相匹配。
汽车涂装常见的质量缺陷及其对策
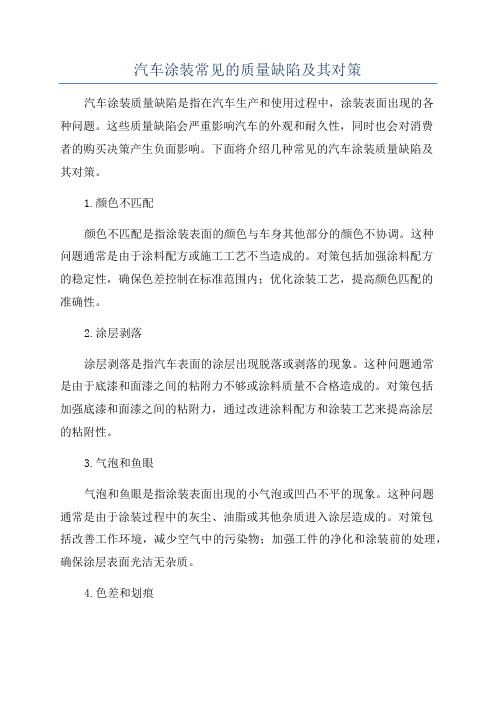
汽车涂装常见的质量缺陷及其对策汽车涂装质量缺陷是指在汽车生产和使用过程中,涂装表面出现的各种问题。
这些质量缺陷会严重影响汽车的外观和耐久性,同时也会对消费者的购买决策产生负面影响。
下面将介绍几种常见的汽车涂装质量缺陷及其对策。
1.颜色不匹配颜色不匹配是指涂装表面的颜色与车身其他部分的颜色不协调。
这种问题通常是由于涂料配方或施工工艺不当造成的。
对策包括加强涂料配方的稳定性,确保色差控制在标准范围内;优化涂装工艺,提高颜色匹配的准确性。
2.涂层剥落涂层剥落是指汽车表面的涂层出现脱落或剥落的现象。
这种问题通常是由于底漆和面漆之间的粘附力不够或涂料质量不合格造成的。
对策包括加强底漆和面漆之间的粘附力,通过改进涂料配方和涂装工艺来提高涂层的粘附性。
3.气泡和鱼眼气泡和鱼眼是指涂装表面出现的小气泡或凹凸不平的现象。
这种问题通常是由于涂装过程中的灰尘、油脂或其他杂质进入涂层造成的。
对策包括改善工作环境,减少空气中的污染物;加强工件的净化和涂装前的处理,确保涂层表面光洁无杂质。
4.色差和划痕色差和划痕是指涂装表面出现的颜色不均匀或划痕的现象。
这种问题通常是由于施工工艺不当、涂装设备不良或外界磨损等因素造成的。
对策包括改进施工工艺,提高涂装设备的精度和可靠性;加强保养和维护,减少外界磨损对涂装表面的影响。
5.线条和凹陷线条和凹陷是指涂装表面出现的直线或凹陷的痕迹。
这种问题通常是由于涂装设备不良或施工工艺不当造成的。
对策包括改进涂装设备,提高喷涂均匀性和覆盖率;加强施工工艺的培训和监督,确保涂装表面的平整和一致。
为了确保汽车涂装的质量,汽车制造商应加强质量控制和检测,确保涂装过程的每一个环节都符合标准要求。
同时,消费者在购买汽车时也应注意检查涂装表面是否存在质量缺陷,并在发现问题时及时向售后服务部门投诉和维权。
只有通过制造商和消费者的共同努力,才能提高汽车涂装的质量,提升汽车品牌形象,满足消费者对于汽车外观和品质的要求。
汽车车身涂装面漆色差的分析与对策

汽车车身涂装面漆色差的分析与对策作者:韩红军来源:《科学与财富》2015年第36期【摘要】面漆色差是汽车车身在涂装过程中难以控制的问题,也是汽车涂装环节中最易出现的问题。
在当代,人们对产品的质量要求不仅仅体现在内在品质上,在外在的质量以及美观上也有着较高的要求。
这也意味着汽车车身的涂装工作需严格掌握色彩的运用,结合车身造型的不同采用不同的面漆效果,从而提高产品的外在质量。
但是,由于汽车车身在涂装过程中常常因工艺的不同而出现面漆色差,使得汽车无法保持色彩的整体性,最终影响了汽车的整体美观,对汽车的外在品质造成了一定的影响。
对此,本文针对汽车车身涂装面漆的色差问题展开分析,并根据问题提出相应的解决对策。
【关键词】汽车车身;涂装面漆;色差的分析0.引言涂装面漆是打造汽车外在造型的重要环节之一,也是美化汽车的重要步骤。
对于汽车整体来说,为汽车涂装色彩能够赋予汽车不同的光泽与色彩,甚至能够使汽车打造出立体的质感形象,对汽车外在质量有着直接的影响。
在当前,汽车在使用不同的色彩来美化外观时,其也会出现不同的色差差距,这不仅是由于涂装面漆的施工所导致,其与面漆涂料的选择也有着较大关联,因此,如何避免汽车车身在涂装面漆后出现色差问题已成为当前人们关注的问题。
1.汽车车身涂装面漆色差的问题分析1.1测值数据表呈现的问题为了使汽车车身涂装面漆色差能够完整呈现出来,本文采用色差仪测试了面漆车身在烘干后的整体颜色值,并将颜色值与标准色板进行对比,详细对比信息请见表一[1]。
从表一中可以发现,符合汽车车身涂装面漆色差范围的只有雷迅灰以及银灰,而其它涂装面漆如开罗金、摩卡棕、新月银、珍珠白等都与标准的色差板存有十分明显的色差,均超过了汽车车身涂装面漆的要求,由此可看出,我国当前的汽车车身涂装面漆条件难以保障车身色差与标准色板达到一致,色差范围难以控制[2]。
1.2汽车车身涂装面漆过程中存在的问题1.2.1汽车车身涂装面漆的工艺问题首先对汽车车身喷涂白色色漆一遍,再对该车身涂抹一遍珍珠粉,遮盖原本颜色色彩,其它颜色色漆喷涂二遍,最终发现喷涂过程中难以使得色漆膜厚,使得车身的多个部位出现了色差现象[3]。
汽车涂装工艺中的涂装质量问题分析与改进
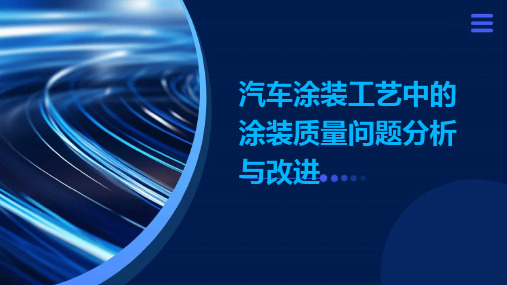
05
CATALOGUE
结论与展望
当前涂装质量改进的成果与不足
成果
随着涂装工艺技术的不断改进,汽车涂装质量得到了显 著提升,提高了汽车外观的持久性和耐腐蚀性。
不足
尽管取得了一定的成果,但仍存在一些涂装质量问题, 如色差、流挂、颗粒等,需要进一步改进和优化。
未来涂装工艺的发展趋势与展望
趋势
未来涂装工艺将朝着更加环保、高效、智能 的方向发展,新材料、新工艺、新技术的应 用将不断涌现。
涂装工艺的改进
总结词
涂装工艺的改进可以提高涂层质量和生产效率,降低不良率。
详细描述
优化涂装工艺流程,确保各道工序的稳定性和可靠性。采用先进的涂装设备和自动化技术,提高涂层 厚度、均匀性和光泽度的控制精度。同时,加强工艺参数的监控和调整,确保涂装质量的稳定性和一 致性。
环境因素的应对措施
总结词
环境因素对涂装质量产生影响,采取有效的应对措施可以提高涂层质量和使用寿命。
汽车涂装工艺中的 涂装质量问题分析 与改进
目录
• 涂装质量概述 • 涂装质量问题分析 • 涂装质量改进方法 • 涂装质量改进案例 • 结论与展望
01
CATALOGUE
涂装质量概述
涂装质量的重要性
01
02
03
提升汽车外观
涂装质量直接影响汽车外 观的持久性和美观度,高 质量的涂装能够使汽车外 观更加亮丽、持久。
涂料选择的优化
总结词
选择合适的涂料对涂装质量至关重要,优化涂料配方可以提高耐候性、防腐性和外观效 果。
详细描述
针对汽车不同部位和涂层要求,选用适合的涂料类型和品牌。关注涂料的耐候性、防腐 性、色泽和光泽度等性能指标,确保涂料的质量和稳定性。同时,考虑环保因素,优先
- 1、下载文档前请自行甄别文档内容的完整性,平台不提供额外的编辑、内容补充、找答案等附加服务。
- 2、"仅部分预览"的文档,不可在线预览部分如存在完整性等问题,可反馈申请退款(可完整预览的文档不适用该条件!)。
- 3、如文档侵犯您的权益,请联系客服反馈,我们会尽快为您处理(人工客服工作时间:9:00-18:30)。
车身油漆色差控制摘要:从油漆漆材料、喷涂工艺、喷涂设备等方面探讨了色差的影响因素,提出了相应的控制方法。
关键词:色差;喷涂;施工工艺;影响因素;控制1.前言随着我国加入WTO,汽车工业的竞争趋于白热化,世界各大汽车巨头纷纷涌入国内建合资企业,丰田、日产、本田、马自达等日本汽车企业基本上在中国都形成了自己的战略部署,北汽与韩国现代联姻,华晨与宝马合资,通用、大众、福特、戴克、罗孚、菲亚特等国际知名汽车企业纷纷入主中国市场,吉利、奇瑞、哈飞、长城汽车等高举民族品牌大旗者也不甘示弱,国内汽车行业进入战国时代。
竞争是全方位的,价格、质量、营销、品牌等,要想在竞争中生存下来,就必须在各方向都尽可能做到让用户满意。
车身油漆颜色就像是汽车的外衣,在顾客选购车辆时给予第一感观的认知,很可能左右消费者有没有兴趣对车子进行更详细的了解。
随着人们生活水平的提高,人们消费更趋理性,要求也更加苛刻和专业。
原来大家可能只对颜色有个大致的要求,比如能找到自己喜欢的色系就行了,可现在这种最初层次的性能已远不能满足消费者的需求,消费者对油漆的光泽度、鲜映性、甚至色差都有自己的要求。
如何做出色差令顾客满意的油漆车身,这是每一个汽车油漆工程师都应考虑的问题。
然而车身色差控制是一个极为复杂的工作,可能影响最终漆膜色差的因素众多,如何有效地控制各种影响因素,提高车身油漆色差的质量,是每个汽车涂装工作者面临的一个挑战。
随着保险杠、门把手、后视镜及加油小门等彩色塑料件的大量采用,要求车身与塑料件的颜色无偏差,这就对车身油漆色差的控制提出了更高的要求。
目前轿车厂流行的方法是采用仪器测量与目测相结合的方式来控制色差,一般提供一块标准颜色样板,要求车身及塑料配件的颜色与该标准样板相比无论是目测,还是仪器测量都应接近。
车身油漆色差的影响因素众多,它与油漆漆材料、喷涂工艺、喷涂设备、供漆系统等因素密切相关。
本文就车身油漆色差的控制谈一点看法。
2.色差的概念颜色可以用色相H(Hue),饱和度C(Chroma), 或表示红绿的a值,表示黄蓝的b值以及明度L(Lightness)来定义。
L﹡a﹡b﹡色空间是目前最实用和普及的用于测量物体颜色的空间模型,它是CIE (国际照明委员会,法文:Corporación Interamericana de Entretenimiento ,英文名称:International Commission on Illumination )定义的色空间(如图1所示),本文中所提及的Lab 均为CIE 模型标准。
在该空间中L 为明度,L 为正值表示颜色偏白,L 为负值表示颜色偏黑;a ,b 为色度坐标,其中a 为正值表示颜色偏红,a 为负值表示颜色偏绿;b 值为正值表示颜色偏黄,b 值为负值表示颜色偏蓝图1LCH 色空间与Lab 色空间的色度图相同, 但该色空间为极坐标而不是直角坐标,L 表示明度,与Lab 色空间的L 值相同,H 表示色相,C 表示该颜色的饱和度,如图2图2 两个色度值(L 样品,a 样品,b 样品)和(L 标准,a 标准,b标准)之间的色差△E ab 由下式决定:ΔE ab =[(ΔL)2+(Δa)2+(Δb)2]1/2其中:ΔL=L 样品-L 标准,Δa=a 样品-a 标准,Δb=b 样品-b 标准如ΔL 为正值,说明样品颜色偏浅;ΔL 为负值,说明样品颜色偏深。
如Δa 为正值,说明样品颜色偏红;Δa 为负值,说明样品颜色偏绿。
+ b*yellowL = 100white*- b*blue+ a *r ed- a *g r e e nL = 0black*如Δb为正值,说明样品颜色偏黄;Δb为负值,说明样品颜色偏蓝。
在这个体系中,任一点的容差大小是一样的,由于人眼对各种颜色的的敏感程度并不完全相同,这有时并不能反映真实的视觉效果。
为把人眼对颜色的感受特点考虑进去,德国大众在大量实验和实践的基础上,采用了一套ΔE CMC值的椭圆公式,ΔE CMC=[(ΔL/S L)2+(Δa/S a)2+(Δb/S b)2]1/2 ①或者ΔE CMC=[(ΔL/ S L)2+(ΔC/S c)2+(ΔH/S H)2]1/2 ②其中S L ,S a ,S b表示ΔL,Δa,Δb的修正系数,S L ,S C ,S H表示ΔL,ΔC,ΔH 的修正系数。
这套公式下标是CMC,是在CMC(l:c)色差公式的基础上演变而来的,但和CMC(l:c)色差公式并不完全相同,CMC(l:c)色差公式是McDonald 采用了视觉判断方式(用八个专业人士)的实验来決定色配对是否可被接受,后来据此结果再演译成JPC79 公式,並被命名为CMC(l:c) ( Colour Measurement Committee of the Society of Dyers and Colourists)。
主要是针对lightness 和chroma 做了权重的估算:由于考虑了人眼对颜色的感受,人眼对不同的颜色有不同的敏感程度,而在此评价体系中不同的颜色有不同的容差系数,因此该评价方式更为精确,如下图目前全世界车身油漆色差的修正系数无统一的标准,各厂根据自身的经验进行控制,我们根据德国大众的经验,不同的颜色根据其L、a、b、C、H可计算出对ΔL,Δa,Δb或是ΔL,ΔC,ΔH给出不同的容差系数,具体计算公式在这里不做讨论。
对于特定颜色的油漆,究竟是用公式①还是②,取决于该颜色的彩度C和明度L,当C < 10或(C < 18且L>27)时,我们认为该颜色不是鲜艳颜色,适用公式①,而其它情况,我们认为该颜色为鲜艳颜色,适用公式②。
最终对色差的综合评价,我们目前是从五个角度对ΔE CMC 进行综合评价,单个角度ΔE CMC 小于2.0且五角度ΔE CMC 平均1.7即颜色合格,否则为不合格。
3.色差的测量色差的测量一般采用分光测色法,目前上海大众和相关供应商均采用X-RITE 生产的MA86II 色差仪,可采用D 65(标准日光,色温为6500K )等多种光源单方向(450)照明,可从5个角度(15°、25°、45°、75°及110° )同时测量金属漆或珠光漆的颜色。
4.车身油漆色差影响因素4.1油漆材料油漆色漆可分为两大类:单色漆和闪光漆,闪光漆包括金属闪光漆和珍珠闪光漆。
单色漆是通过颜料粒子将入射光进行反射的,由于散射光是主体,无随角异色效应。
闪光漆的组成主要有三部分,除了传统单色漆所具有的透明树脂溶液和着色颜料外还添入了闪光铝粉或珠光粉。
其中闪光铝粉和珠光粉就是我们通常所说的效果颜料。
就它们的光谱特性来讲,普通颜料对照射到它的光基本都是漫反射;铝粉除了两端为漫反射外,基本都是镜面反射;而珠光粉为半透明材料,除了和铝粉一样两端漫反射、平面镜面反射外,还有透射。
三种组份的光谱特性可用图简单表示:对于金属闪光漆,铝粉在漆膜内不同层次排列,反射出去的光线其亮度也不一。
而光线射入漆膜内颜料粒子成有色光,再经不同层次铝粉反射出漆膜时,就会产生色光和金属光的变化,即闪光效应。
当入射光或视角由垂直逐渐转向与漆膜平行,反射光变弱,颜色变深(铝粉平行于漆膜理想排列情况下)。
所以金属闪光漆随着视角的改变,可观察到不同程度的金属色感及闪烁感。
铝粉颜料对于珠光漆,入射光经反射、折射、透射及部分吸收时,平行的各种反射光之间的互相干涉而出现珍珠般色彩,如下图按照上海大众对的色差控制要求,单色漆由于其光谱特性各项的均一性,所以只对其45度角的色差数据进行控制,而对于闪光漆,则需要对15º、25º、45º、75º、110º五个角度的色差数据进行控制。
测色角度如下图:其中,15º25° 为近镜面反射角,其镜面反射色主要受金属片或珠光粉颜料的定向排列影响。
45º为直视角,是目视样板的最佳角度,受铝粉珠光粉排列与着色颜料的双重影响。
75º 和110º 为侧视角,受着色颜料影响最大。
对单色漆色差影响最明显的是油漆的膜厚。
单色漆由透明的树脂和着色颜TiO 2 Fe 2O 3º料组成,相对有铝粉的的金属漆来讲,遮盖力相对较差,红或黑等深颜色由于颜料的透光率较低,遮盖力尚可,而对于颜色较浅的白色和黄色等颜色,通常正常的施工条件下的色漆膜厚并不能达到黑白格意义上的完全遮盖,这时使用何种颜色的中涂以及漆膜的厚度控制对色差的影响显得至关重要。
为了减少中涂对最终色差的影响,通常的做法是采用较浅颜色的中涂,比如白色或浅灰中涂,尽管如此,较低的膜厚仍会让光线射到中涂后反射回色漆层,经过中涂的吸收后,吸收光谱必然产生变化,所以单色漆如黄颜色,其颜色数据往往是由色漆层和部分中涂层的吸收光谱叠加出来的,其色漆膜厚的微小变化可能会产生较大的色差,这对施工是一个很大的挑战。
清漆色漆中涂电泳钢板而闪光漆除了树脂和着色颜料外,还有铝粉(珠光粉)等效果颜料,其色差不但受膜厚的影响,还受效果颜料定向排列的影响。
通常闪光漆的遮盖力都较好,更多对闪光漆色差的影响来自效果颜料的的含量及其定向排列。
闪光漆喷涂后溶剂挥发漆膜收缩,一次喷涂湿膜簿的,漆膜收缩后,铝粉(珠光粉)平行于漆膜排列的倾向性大。
湿膜厚的,溶剂挥发漆膜收缩后,其膜厚空间扩大,铝粉(珠光粉)随机排列趋向加大,则平行于漆膜定向排列趋向减少,如下图所示。
在油漆配方一定的情况下,不同的施工参数可以得到不同的铝粉(珠光粉)排列,产生不同的颜色效果。
4.2施工参数:表格1和表格2分别为同一油漆(小麦黄) 在两种施工条件下得到的色差数据:表格 12表格化空气压力,从而使得到的漆膜小角度明度dL*明显下降,45和75度明度略有增加,而110度主要受ESTA喷涂影响,因为ESTA参数没变,所以110度变化不明显.而大角度明度变化不大,色相方面也发生了类似的变化,即小角度黄相db*明显上升,而大角度变化不明显。
这是因为雾化空气压力的降低,使喷涂时雾化变粗,漆膜相对较湿,从而小麦黄的铝粉随机排列趋向加大,则平行于漆膜定向排列趋向减少,镜面反射也就减少,所以小角度明度下降,而黄相恰恰相反,因为它由着色颜料的漫反射影响,由于铝粉纵向排列增多,对颜色的散色光的阻挡变弱了,黄相颜色的光线更多的反射出来。
因此,雾化空气压力降低,铝粉定向排列的趋向减少,从而使小角度明度下降,黄相增加。
同样,其他施工参数也会对铝粉的定向排列产生影响,从而影响油漆的色差。
下表给出了各参数对闪光漆小4.3喷涂设备:相同的色漆材料,在不同的喷涂设备上喷出的色差也有所不同。
以人工喷涂来控制色差是不切实际的,由于人工喷涂受人为因素的影响较大,无法始终保持稳定的喷涂参数,ESTA高速旋杯自动静电喷涂由于其喷涂效率高,油漆利用率高成膜分布好,颜色均匀,质量稳定等显著特点在汽车涂装中被广泛应用,目前上海大众各生产线基本都采用ESTA+Spraymate喷涂的工艺。