生产车间分层审核标准表
分层审核用表模板

问题描述
改善计划
责任部门人签字 预计完成日期 实际完成日期
检查工位周围是否整洁有序,设备、工装模具、工作台及周边
5 地面进行了清洁,对废弃物进行了分类管理,并使用了正确的 工位器具。
6
检查工位周围是否有滞留的不明状态零件(无标识,无标 签,)
7
检查零件标签是否与实物一致,无错漏且标识填写完整
零件的周转、存储是否符合规定,不可超装、叠压、不良品分
8 类放置,料箱标识卡填写需完整且具有唯一性,不可有多余标 识卡,外箱不能有废旧标签;
设备运转是否有异常或故障情况,急停开关,双手开 14 关,光栅是否安全有效,各水流量、气流量压力值是否
在正常范围。 作业结束后设备、工装、物料是否放置在正确的位置 15
点焊工作站作业员是否正确有效的做自检画线检查,产品涂胶
16
是否清理干净
17 抽检确认设备使用参数是否符合标准,点焊焊点数量是否正确
18 检查凸焊数量核对表有无如实记录填写
9
首件是否及时送检并得到认可,并在首件检验合格后才进行批 量生产
10 检查记录表填写是否符合标准,巡检记录是否完整
11
检查操作者是否对正确的当前设备进行了点检(包括工装模具 、检具、设备、叉车、行车等)
12
检查设备(包括但不限于机床、运输设备、消防器材等)无明 显安全隐患。
13
检查操作者能够且能够简单口述设备点检的检查内容,及判定 标准。
序号 1
要素
周 班次
员工穿着符合要求(手套、工作衣、工作鞋等穿戴齐全)
2
作业指导书是否正确存放于现场,员工是否按照作业指导书要 求规范操作
3
员工是否充分理解与掌握了设备操作、设备点检、工艺参数点 检内容;并在生产开始前进行了点检与记录。
车间分层审核检查表3
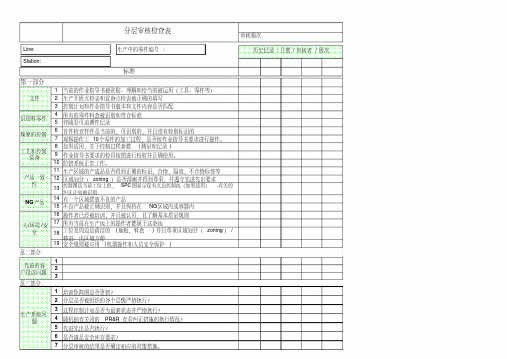
1当前的作业指导书被张贴、理解和恰当的被运用(工具、零件等)2生产开班点检表和设备点检表被正确的填写3控制计划和作业指导书版本和文件内容是否匹配4所有的零件料盒被识别和符合标准5伴随着可追溯性记录6首件检查样件是当前的,可识别的,并且带有特别标识的7观察操作工10个零件的加工过程,是否按作业指导书要求进行操作。
8如果适用,关于控制过程参数 (测量和记录)9作业指导书要求的检具按期进行校验并正确使用。
10防错系统正常工作。
11生产区域的产成品是否得到正确的标识,合格,隔离,不合格标签等12区域划分(zoning )是否清晰并得到尊重,并遵守先进先出要求13控制图是当前工位上的,SPC 图显示没有点出控制线(如果适用),有关的纠正计划被识别14有一个区域摆放不良的产品15不良产品被正确识别,并且保持在NG 区域内或容器内16操作者已经被培训,并且被认可,且了解基本质量规则17所有当前在生产线上的操作者都属于这条线18工位及周边是清洁的 (地板,料盒…) 并且尊重区域划分(zoning ) /移进、出区域方便19安全规则被应用 (机器操作和人员安全保护)1231培训矩阵图是否更新?2分层是否被组织的各个层级严格执行?3过程控制计划是否为最新状态并严格执行?4随机抽查关闭的PR&R ,查看纠正措施的执行情况?5先进先出是否执行?6是否满足安全库存要求?7分层审核的结果是否确定相应的对策措施。
人/环境/安全先前的客户投诉问题生产系统问题分层审核检查表第二部分:第三部分:文件识别料零件频繁的控制工艺和控制装备产品一致性NG 产品审核频次:历史记录: 日期 / 审核者 / 班次标准第一部分Line:生产中的零件编号:Station:。
LPA 分层审核检查表(生产)
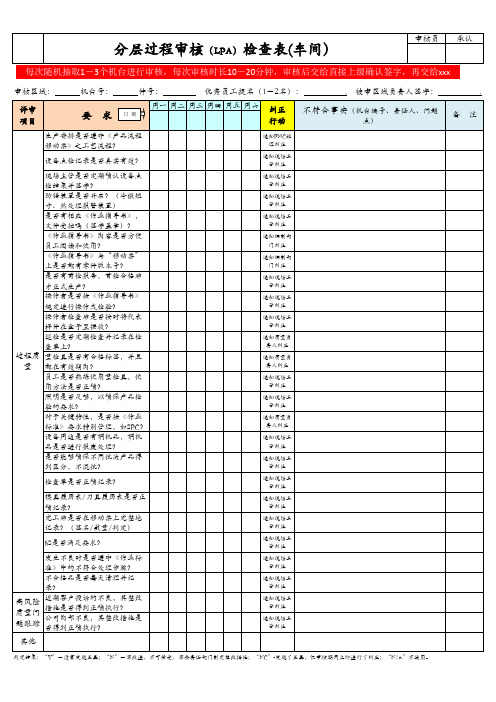
评审 项目
要 求 日 期
周一 周二 周三 周四 周五 周六 纠题 备 注
点)
生产安排是否遵守《产品流程 移动票》之工艺流程?
设备点检记录是否真实有效?
现场主管是否定期确认设备点 检结果并签字? 防错装置是否开启?(冷镦短 寸、热处理报警装置) 是否有相应《作业指导书》, 文件受控吗(签字盖章)? 《作业指导书》内容是否方便 员工阅读和使用? 《作业指导书》与“移动票” 上是否都有零件版本号? 是否有首检报告,首检合格后 才正式生产? 操作者是否按《作业指导书》 规定进行操作或检验? 操作者检查后是否按时将代表 样件在盒子里摆放? 巡检是否定期检查并记录在检 查单上? 过程质 量检具是否有合格标签,并且 量 都在有效期内? 员工是否熟练使用量检具,使 用方法是否正确? 照明是否足够,以确保产品检 验的要求? 对于关键特性,是否按《作业 标准》要求特别管理,如SPC? 设备周边是否有调机品,调机 品是否进行报废处理? 是否能够确保不同批次产品得 到区分,不混批?
评审项目要求通知现场主管纠正通知pmc经理纠正通知编制部门纠正通知质量负责人纠正发生不良时是否遵守作业标准中的不符合处理步骤
分层过程审核(LPA)检查表(车间)
审核员 承认
每次随机抽取1-3个机台进行审核,每次审核时长10-20分钟,审核后交给直接上级确认签字,再交给xxx
审核区域: 机台号: 件号: 优秀员工提名(1-2名): . 被审区域负责人签字: .
题跟踪 否得到正确执行?
通知PMC经 理纠正
通知现场主 管纠正
通知现场主 管纠正
通知现场主 管纠正
通知现场主 管纠正
通知编制部 门纠正
通知编制部 门纠正
通知现场主 管纠正
分层审核检查表
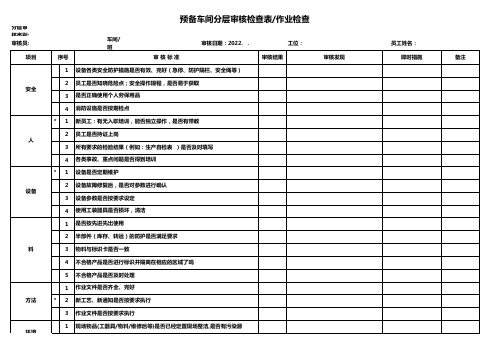
2 半部件(库存、转运)的防护是否满足要求
3 物料与标识卡是否一致
4 不合格产品是否进行标识并隔离在相应的区域了吗
5 不合格产品是否及时处理
1 作业文件是否齐全、完好
* 2 新工艺、新通知是否按要求执行
3 作业文件是否按要求执行
1 现场物品(工器具/物料/维修后等)是否已经定置现场整洁,是否有污染源
分层审 核类别: 审核员:
项目 安全
人
设备
料
方法 环境
预备车间分层审核检查表/作业检查
序号
车间/ 班
审核标准
审核日期:2022. .
1 设备各类安全防护措施是否有效、完好(急停、防护隔栏、安全绳等)
2 员工是否知晓危险点;安全操作规程,是否易于获取
3 是否正确使用个人劳保用品
4 消防设施是否按期检点
工位: 审核结果
审核发现
员工姓名: 即时措施
备注
环境
2 锭子房内外部温度差是否符合标准要求
1 使用的计量器具是否齐全、完好、有标识、在有效期内
检测
2 员工是否会准确使用计量器具 3 皮带秤、小料称是否定期校验
4 在线测量设备、防误是否正常使用
变更
* 1 4M1E变更是否按要求执行
顾客要 求
内部 外部
* 1 新员工:有无入职培训,能否独立操作,是否有带教
2 员工是否持证上岗
3 所有要求的检验结果(例如:生产自检表 )是否及时填写
4 各类事故、重点问题是否得到培训
* 1 设备是否定期维护
2 设备故障修复后,是否对参数进行确认
3 设备参数是否按要求设定
4 使用工装器具是否损坏,清洁
1 是否按先进先出使用
分层审核检查表(科长)
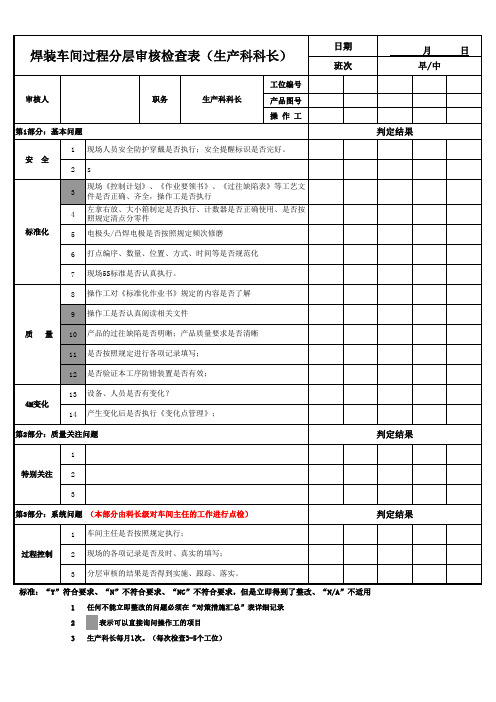
焊装车间过程分层审核检查表(生产科科长)
班次
月
日
早/中
审核人 第1部分:基本问题
职务
生产科科长
工位编号 产品图号 操作工
安全
1 现场人员安全防护穿戴是否执行;安全提醒标识是否完好。 2s
标准化
3
现场《控制计划》、《作业要领书》、《过往缺陷表》等工艺文 件是否正确、齐全,操作工是否执行
4
左拿右放、大小箱制定是否执行、计数器是否正确使用、是否按 照规定清点分零件
4M变化
13 设备、人员是否有变化? 14பைடு நூலகம்产生变化后是否执行《变化点管理》;
第2部分:质量关注问题
判定结果
1
特别关注 2
3
第3部分:系统问题 (本部分由科长级对车间主任的工作进行点检)
判定结果
1 车间主任是否按照规定执行;
过程控制 2 现场的各项记录是否及时、真实的填写;
3 分层审核的结果是否得到实施、跟踪、落实。
5 电极头/凸焊电极是否按照规定频次修磨
判定结果
6 打点编序、数量、位置、方式、时间等是否规范化
7 现场5S标准是否认真执行。
8 操作工对《标准化作业书》规定的内容是否了解
9 操作工是否认真阅读相关文件
质 量 10 产品的过往缺陷是否明晰;产品质量要求是否清晰
11 是否按照规定进行各项记录填写;
12 是否验证本工序防错装置是否有效;
标准:“Y”符合要求、“N”不符合要求、“NC”不符合要求,但是立即得到了整改、“N/A”不适用
1 任何不能立即整改的问题必须在“对策措施汇总”表详细记录
2
表示可以直接询问操作工的项目
3 生产科长每月1次。(每次检查3-5个工位)
分层审核表(新版)

部长第1第2第3第4周3周3周3周31生产工位(包括返工)是否有作业标准书,作业标准书是否与实际生产的产品符合;2生产作业员是否按作业指导书的步骤进行操作;3作业后的质量确认方法、项目、内容、基准是否明确;5制程中实物的品质是否在按规定要求进行检查,是否将检测的数据如实的记录;6首未件和制程检验记录表是否按要求填写;7良品和不良品是否有明确的状态标识;8良品和不良品的周转容器是否放置在规定的区域;9工作区域地面是否整洁、物品摆放是否整齐;10生产线员工是否按规定进行穿着(工作服、工作帽、工作鞋等);11生产线出现不良品,组长是否及时作不良现状分析及处理;12设备和过程参数是否按时点检,是否符合受控设定的参数要求;13生产线是否有潜伏安全隐患,是否有物品占用通道和消防通道;14特殊岗位人员是否按规定配戴安全防护用品;15危险区域是否有标识、安全防护和警示;16工装治具是否有明确的标识以及放置在规定的位置内;17原辅材料是否按规定的位置放置;18现场地面是否杂乱无章;19各设备是否有漏油现象;20工序间是否有堆积现象及品质重大事故;21分层审核的问题是否准时整改完成;22顾客反馈的问题点是否在现场公布并及时更新;23过程审核的问题点是否按节点整改完成和有效;24管理看板中的内容是否定期更换;25各组月、周工作计划是否在定期开展;26现场检具、量具是否在有效期内使用;27主管是否定期与员工交流沟通;现场是否有小型会议场所;28主管是否对生产员工定期进行品质培训,特别是当发生顾客抱怨后;29当发生品质抱怨后生产现场的作业标准书等指导性文件是否及时更新;30顾客的反馈的问题点整改是否根据时间节点整改完成;31车间月度的工作计划是否按节点完成;32车间管理人员是否了解,车间的管理目标以及部门的经营指标;33公司成本降低改善项目担当者是否有续的在开展;实施结果众恒装配车间---审核项目验证结果并关闭验证人日期主管改善项目生产现场普遍问题项目NO 对策月度质量关注点说明: 1、审核后每个检查项可以有三个结果:“Y”代表没有发现差异;“N”代表发现了差异;“NC”代表发现了差异,审核期间纠正了。
分层审核表部门审核(挤出车间)可编辑全文

□NC □N □Y □N/A
审核员签名: 纠正措施
责任人
完成时间
1、灰色框里的内容是需要对操作员提问的 2、当对某项进行审核时,如果问题立即改正,则填入“NC”,否则填入“N”,并且在反面备注对策措施。 3、评级:Y合格 N发现偏差 N/A 不适用
临时 增加 审核 项目
问题序号
问题描述
审核员签名:
分层审核记录
检查结果(第一次) □NC □N □Y □N/A □NC □N □Y □N/A □NC □N □Y □N/A □NC □N □Y □N/A □NC □N □Y □N/A □NC □N □Y □N/A □NC □N □Y □N/A □NC □N □Y □N/A □NC □N □Y □N/A □NC □N □Y □N/A □NC □N □Y □N/A □NC □N □Y □N/A □NC □N □Y □N/A □NC □N □Y □N/A □NC □N □Y □N/A □NC □N □Y □N/A □NC □N □Y □N/A □NC □N □Y □N/A □NC □N □Y □N/A □NC □N □Y □N/A □NC □N □Y □N/A □NC □N □Y □N/A
17 待定及不良品料有无按照要求使用红色料筐盛放?
18 摆放管坯操作工手指甲是否过长;
19 针对异常点有无张贴质量警示卡?
减少 20 产品是否有明确的零件编号?卡物是否一致? 制造 时间 21 管坯料箱盛放数量有要求么?执行了么?物料是否按照先进先出的原则执行?
持续 改进
22
是否规定并执行了首末件检验?有执行么?(查看实物和记录)
11 标准化作业中是否有正确的工具和量具能够使用?
分层审核检查表样表

车间: 钢化预处理 生产线名称: 项目 序号 人员 资格 培训 1 2 3 4 标准 化 5 6 7 8 不合 格品 控制 9 10 11 12 13 14 质量 控制 点 15 16 17 18 19 20 1 内部 问题 关注 2 吸盘真空度在运行过程中漏气导致产品不合格; 班次: 日期: 检查人: 审核: 结果 内 容 第一部分:各生产线日常管理项目 员工是否有资格胜任其岗位,培训员工是否有相应的培训教师指导和监督其工作。(人 员上岗资格、培训情况) 新项目、新的作业指导书及更新的文件是否对员工进行培训,是否有培训记录? 各项记录是否填写,且真实、完整、规范?(车间首检、点检、不合格品记录、SPC) 是否进行了首件、末件检验并保留现场? 生产过程是否遵循了控制计划的各项要求?工艺参数设定是否符合规定? 产品的质量要求是否明确、是否能够获得且易于遵守?(缺陷样片和标准样片、质量要求) 现场标识是否规范?(物料、产品) 防错装置是否经过防错验证检查,且处于良好的工作状态? 不合格品是否被正确标识并放置在不合格区域或者红色料架上? 出现不合格品,是否及时记录并采取措施? 返工返修品是否有正确标识并存放在指定区域?返修后是否经检验、标识流入下道工序? 第二部分:本生产线重点关注项目和质量控制点 吸盘真空度是否达到参数设置要求。 磨轮质量是否达到要求,磨边质量是否符合要求;是否有斜边、烧焦、亮斑存在; 是否对孔径尺寸、钻孔质量进行确认。 针对边部磨边质量、亮斑等是否进行了整车检验; 切割样片的编号(包括本厂编号、零件号)与跟踪单要求是否一致; 尺寸检验是否符合要求; 。。。。。。
REV01(0804)
1 顾客投诉产品磨边不良; 外部 投诉 2
备注
班组长每班审核一次,车间主任每天抽查一个班次进行审核,厂长每周抽查一个班次进 行审核,各班组审核报表及时放置在各车间的相应栏目内;原工艺监督只需跟踪快速反 应中的问题关闭实施情况。
LPA生产车间分层审核检查表
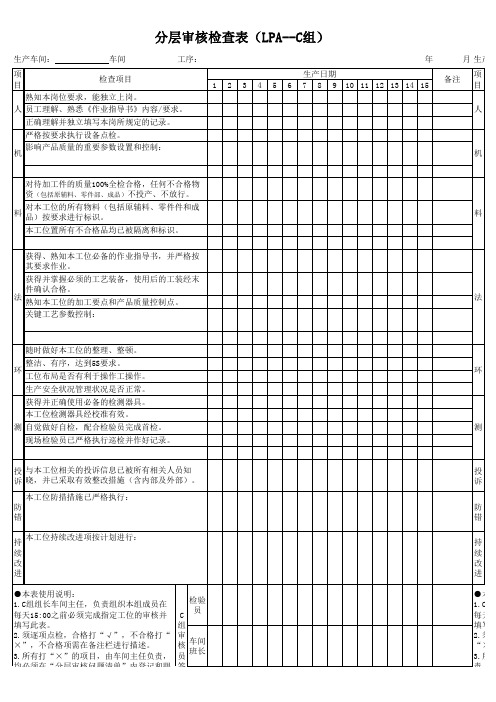
审 核 员
车间 班长
责,均必须在“分层审核问题清单”内登 签
记和跟踪。
字
4.本表由车间主任负责回收,并提交总经
办归档保存。
“×”,不合格项需在备注栏进行描述。 3.所有打“×”的项目,由车间主任负 责,均必须在“分层审核问题清单”内登 记和跟踪。 4.本表由车间主任负责回收,并提交总经 办归档保存。
审 核 员
车间 班长
均必须在“分层审核问题清单”内登记和跟 签
踪。
字
4.本表由车间主任负责回收,并提交总经办
归档保存。
环
测
投 诉
防 错
持 续 改 进
●本表 1.C组组 每天15 填写此 2.须逐 “×” 3.所有 责,均 记和跟 4.本表 办归档
×”,不合格项需在备注栏进行描述。
核
3.所有打“×”的项目,由车间主任负责, 员
备注
项 目
人
机
对待加工件的质量100%全检合格,任何不合格物 资(包括原辅料、零件部、成品)不投产、不放行。
对本工位的所有物料(包括原辅料、零件件和成
料 品)按要求进行标识。
料
本工位置所有不合格品均已被隔离和标识。
获得、熟知本工位必备的作业指导书,并严格按 其要求作业。
获得并掌握必须的工艺装备,使用后的工装经末
投 与本工位相关的投诉信息已被所有相关人员知 诉 晓,并已采取有效整改措施(含内部及外部)。
本工位防措措施已严格执行: 防 错
持 本工位持续改进项按计划进行: 续 改 进
●本表使用说明: 1.C组组长车间主任,负责组织本组成员在 每天15:00之前必须完成指定工位的审核并
检验 C员
填写此表。
组
分层审核检查表-机加工

2
设备工装
2.1 观察设备标识/生产状态标识/生产产品标识是否齐全,没有缺少;
2.2 机台是否有异常停机履历表,并按照要求进行填写及更新;
2.3 检查设备点检表是否按照要求填写,并随机抽取点检项目要求操作员口述点检操作,是否清晰了解;
问题简述
2.4 产品加工结束,要求暂停加工,检查机加工工装是否存在松动以及损坏;
审核结果 Y N C NG
1.2 观察员工作业手法,是否存在违规操作,导致的可能人身侵害;
1.3 设备上下料区域是否有明确的区域划分,并保持整体清爽;
1.4 对应工位是否具有5S检查标准,并能按照5S标准进行区域清洁和物品摆放整齐;
1.5 员工是否正确的穿戴了劳保用品,防噪耳塞以做安全防护;
1.6
待(已)生产物料放置于正确的容器或区域,加以标识产品名称/数量/批次,并保持整齐及无其他风险 (如跌落);
3.6 过程质量是否进行了过程巡检,巡检的结果是符合的,或者不符合被跟踪处理;
4
其他事项
4.1
工序是否建立物料检查标准,检查待生产物料,是否存在上工序明显缺陷流出,如未去隔皮,同时询问员工 是否会做检查;
4.2 观察员工作业,是否存在未经批准的返工返修动作,如对产品进行打磨;
4.3 观察员工作业,气枪清洁动作时长是否足以完全清洁加工底座铝屑;
2.5 产品加工结束,要求暂停加工,检查设备刀具寿命控制与工艺要求一致,且未超出管控寿命;
2.6 其他设备参数与工艺要求保持一致且未超出管控要求,如切削液浓度/主轴转速/进给倍率等;
2.7 工位是否具有设备维护作业指导书及维护作业记录,相关记录填写完整;
3
过程监控
生产工位是否具有相对应的标准作业指导书/质量作业标准,且文件是受控下发的,随机抽取要求项目询 3.1 问操作员是否理解;
分层审核检查表(一)
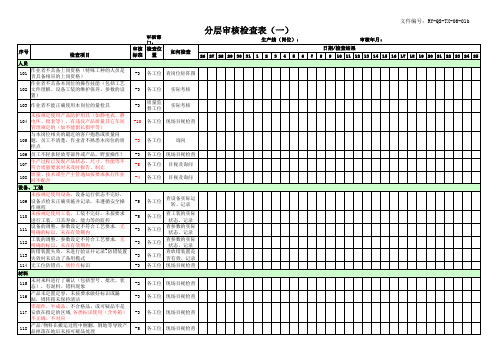
132
样件未进行管理,无台账,标识不清晰,超 过有效期
133
标样件不能在作业现场得到正确使用(包括 目视图片),未进行样件验证
134
出现不良时未填写制程异常情况报告且在10 分钟内通知巡检
135
半成品、成品未经检验流入下工序,检验记 录不认真、未记或不标识
136
生产过程中错装、漏装,下工序发现上工序 不良品
126
返工/返修未按作业指导书进行,返工/返修 后的产品或零件无合适的标识和确认
127
生产首件提交后检验不合格,成品抽检不合 格
128
首件提交不合格再次调整工艺参数后提交仍 不合格,首检未通过开始批量生产
129
未按要求执行了首末件检验,未做好相关记 录
130 首末件品未按规定标识、放置
131
未按工艺要求的频率、抽样数进行检验并记 录
-5
各工位
查工装的实际 状态、记录
111
设备的调整、参数设定不符合工艺要求,无 明确的标识,未在有效期内
-3
各工位
查参数的实际 状态、记录
112
工装的调整、参数设定不符合工艺要求,无 明确的标识,未在有效期内
-3
各工位
查参数的实际 状态、记录
113
防错装置失效,未进行验证并记录?防错装置 失效时未启动了备用模式
-5 各工位 目视及询问
108
质量、技术或生产主管通知按要求执行作业 时不配合
-4 各工位 目视及询问
设备、工装
未按规定使用设备,设备运行状态不完好, 109 设备点检未正确实施并记录,未遵循安全操
作规程
-5
各工位
查设备实际运 转、记录
110
分层审核检查表 生产
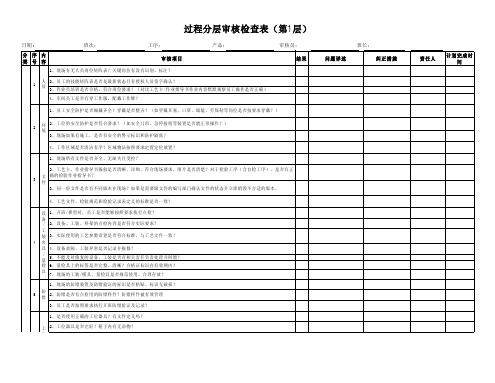
一 、 工 位 问 题
7
材 3 、 自 制 件 是否有标识( 流转 卡)? 填 写 是否正确? 料 4 、 来料包 装是否无 破损 、符合要求? 5 、 线边库存被 有 效管理了吗 ?标识是否 清晰 , 产 品 是否有防护 6 、 多余 物 料 是否按 照 要求 登 记并执行 退库 处 理 ? 记录 是否 完 整? 1 、正 在使用 的 测量 装置( 量具 、 检 具 )是否是 检验 指导书 或 控 制计划中 指 定 的 测量 装置? 2 、是否正确 执行 了首 、 末 件及 过程 检验 ? 不 符合 项 是否按 照 反应计划 正确 处 理 ? 3 、 首 件 是否保 留 在 现场?且按 照 要求 进 行 标识? 4 、对 于需 要 进 行 外 观 检 查 的 产 品 ,有无 明 确的 目视化 的 可接收 标 准 ? 5 、员工是否能 依据外 观标 准 作 出了 正确的 判断 ?正确识别 OK 与 NOK 件 过 程 6 、现场 张贴 不 合格 品处 置 流程吗 ? 控 制 7 、 不 合格 品记录 是否 完 整 清晰 ? 8 、 检验 后 不 合格 品 是否 及时 被 隔离 以 防 止混 用 ? 9 、 看板信息 是否 及时 更 新且有 效 ? 10 、 当 班 生产过程 是否有 变 化 点 ? 变更信息 是否有 效 传递 ?(人员、 材料 、工装、工艺、 测量 等 变 化 ) 11 、 零 件 是否 粘贴 正确标识? 12 、 生产 节拍 是否 平衡 ? 1 、现场是否有 受控 的 换 模 指导书?
过程分层审核检查表(第 1 层)
日期 : 分 序 内 类 号 容 班 次: 工序: 审核项目
1 、现场有无人员岗位矩阵表?关键岗位有没有识别、标注? 1 人 2 、员工的技能矩阵表是否是最新状态且有授权人员签字确认? 员 3 、作业员培训是否合格,符合岗位要求?(对比工艺卡 / 作业指导书作业内容默默观察员工操作是否正确) 4 、车间员工是否有穿工作服,配戴工作牌? 1 、员工安全防护是否佩戴齐全?穿戴是否整齐?(如穿戴耳塞、口罩、眼镜、劳保鞋等岗位是否按要求穿戴?) 环 2 、工位的安全防护是否符合要求?(如安全门帘、急停按钮等装置是否能正 常 操作?) 境 3 、现场如 果 有 施 工,是否有安全的 警示 标识 和 防护 隔离 ? 4 、工作 区域 是否 清洁 有 序 ? 区域物品 按 照 要求 定 置 定 位 放 置? 1 、现场 所 有 文件 是否齐全、无 缺失 且 受控 ? 2 、工艺卡、作业指导书 描叙 是否 清晰 、 详细 、符合现场要求, 图片 是否 清楚 ?对 于检验 工 序 ( 含自检 工 序 ),是否有正 文 确的 检验 作业指导书? 件 3 、 同一份文件 是否有 不同版本在 现场?如 果 是 需 要 跟文件 的 编写部 门确认 文件 的状态 并立即销毁不 合 适 的 版本。 4 、工艺 文件 、 检验规范和检验记录 表 定义 的标 准 是否 一致 ? 设 备 / 工 装 夹 具 / 量 检 具 1 、 开班 / 换型时 ,员工是否能 够 按 照 要求 执行点检 ? 2 、 设备 、工装、 样架 的 点检 内容是否符合 实际 要求? 3 、 实际使用 的工艺 参数设 置是否符合标 准 , 与 工艺 文件一致 ? 4 、 设备故障 、工装 异常 是否 记录并报修 ? 5 、 不 能 及时修复 的 设备 、工装是否有 相 关 责任负责处 理 并 回馈 ? 6 、 量 检 具上 的标签是否 完 整、 清晰 ?合格 证 标识 在 有 效期 内? 7 、现场的工装 / 模具 、 量 检 具 是否 规范使用 ,合 理存 放 ? 1 、现场的防 错 装置 及 防 错 验 证 的标识是否 粘贴 、标识无 破损 ? 5 防 2 、防 错 是否有 点检用 的防 错 样件 ?防 错 样件 被 有 效管理 错 3 、员工是否按 照 要求 执行开班 防 错 验 证 及记录 ? 1 、是否 使用 正确的工位 器具 ?有 文件定义 吗 ? 工 2 、工位 器具 是否 完好 ? 箱子 内有无 杂 物 ? 位
生产车间分层审核标准表

善
2.不合格品处理单和8D报告是否及时外理或回复?
3
现场职业健康 1.操作工人是否按要求穿戴安全防护用品?如工作服、手套、护目镜、口罩、防护鞋等? 安全管理 2.设备安全防护装置是否有效,如安全光栅、安全门等?
1.操作人员是否明白作业流程和作业指导书要求?
2.是否按流程和作业指导书规定操作?是否按文件规定执行点检并按要求记录?
10.生产数量和效率是否达到要求,如果未达到,是否有改善措施?
1.设备/模具是否按规定进行点检,是否按要求填写相关记录,异常是否及时处理?
2.机器/模具状态牌与实际状况是否一致?
3.模具及冲子刀口是否按规定周期维护保养,并填写保养记录?
6
设备/模具的管 理,日常维护
4.模具维修是否有详细记录? 5.模具备件清单与实物是否一致,备件数量是否大于安全库存? 6.《模具履历表》是否及时填写?
1.机台参数是否和CP、工艺规程规定一致(吨位、闭合高度、冲床速度、步距等)?
11
参数
2.热处理槽液成分,浓度,温度,PH值是否与文件规定一致?
3.点检时参数超出文件规定,是否及时处理?
1.ERP系统录入是否正确? 12 ERP系统录入 2.ERP系统录入信息是否齐全?
3.批次量设置是否与工艺规程一致?
1.是否按检验指导书进行QC首检/末检/巡检,作业员自检,并填写检验记录?
2.是否在现场放置标准合格样件,在有效期内,并有QE签字确认?
3.如检验结果异常时,是否及时处理?
13
检验
4.极限样品是否有效?
5.不良履历是否及时更新?
6.SPC是否有效控制,对超出控制线的是否及时调整,并记录?
பைடு நூலகம்
分层过程审核标准及审核记录表
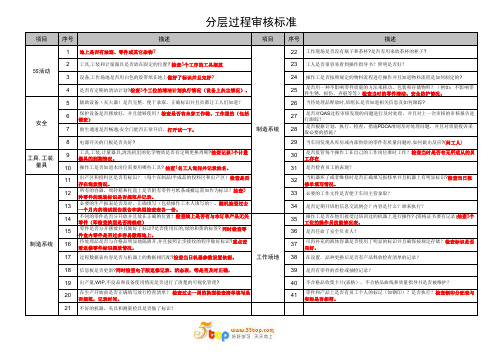
1 地上是否有油迹、零件或其它杂物?22 工作现场是否没有瓶子和茶杯?是否有用来放茶杯的柜子?2工具,工装和计量器具是否放在固定的位置? 检查3个工序的工具摆放23 工人是否很容易看到操作指导书?照明是否好?3 设备,工作场地是否用白色的胶带纸在地上做好了标识并且完好?24 操作工是否按照规定的物料流程进行操作并且知道物料流程是如何制定的?4 是否有定期的清洁计划?检查3个工位的清洁计划执行情况(设备上灰尘情况)。
25 是否用一种不影响零件质量的方法来移动,包装和存储物料?(例如:不影响零件生锈,损伤,弄脏等等)检查当时的零件清洁、安全防护情况。
5 辅助设备(灭火器)是否完整,便于拿取,正确标识并且员都让工人们知道?26 当待处理品释放时,班组长是否知道相关信息及如何跟踪?6保护设备是否摆放好,并且能够使用?检查是否有未穿工作鞋、工作服的(包括领班)27是否对QAS 过程审核发现的问题进行及时处理,并且对上一次审核的审核报告进行跟踪?7 救生通道是否畅通,安全门能否正常开启。
打开试一下。
28 是否根据计划,执行,检查,措施PDCA 准则及时处理问题,并且对质量投诉采取必要的措施?8电源开关的门板是否关好?29 当车间发现从库房或内部供给的零件有质量问题时,如何做出反应?(问工人)9 工具,工装,计量器具,清洗机里的化学物质是否有定期更换周期?抽查记录3个计量器具的到期情况。
30 是否监管每个操作工在自己的工作岗位准时工作?检查当时是否有无所适从的员工存在10 操作工是否知道本岗位需要用哪些工具? 抽查1名工人询问并记录姓名。
31 是否检查员工的表现?11 出产区和投料区是否有标识?(每个在制品/半成品的投料区和出产区)检查是否存在混放情况。
32 当机器坏了或者维修时是否正确填写报修单并且机器上有明显标识?检查当日报修单填写情况。
12 所有的容器,周转箱和托盘上是否附有零件号纸条或搬运需知作为标识?抽查3种零件的现场标识是否规范并记录。
分层审核表 (第一层)

分 层 审 核 检 查 表(适用于第二层、第三层)
审核部门:
主管经理:
车间责任人:
审核人: PI - 全员参与, STD - 标准化, BIQ - 质量控制, SLT - 现场物流, CI - 持续改进
日期:
编制:
第4页共4页
12 过程检验和确认是否严格执行并有效记录 不合格品是否放置在醒目的隔离容器内(零件清晰标
13 识,隔离容器为红色)?
现场的零件周转箱,转运装置上所有的标识是否和零件 14
对应,是否正确的零件放置在正确的容器内?
编制:
第1页共4页
责任人 完成时间 效果验证
STD标 PI
准化
CI 持续 SLT现场物流
7 新? 现场问题板上是否有足够的证据证据快速反应问题解
8 决会议按计划进行,并且所有发现的问题都有跟踪解 决?
SLT现 场物流
9 原材料和产品是否遵循先进先出管理?
10 设备布局调整后是否能提高效率,形成流动制造? 11 车间的区域划分是否能够清晰的反映各区域的位置?
工件清洗设备、清洗液是否在原有基础上有改进并得 12
改进
分 层 审 核 检 查 表(适用于第二层、第三层)
审核部门:
主管经理:
车间责任人:
审核人: 检查最少/最多周转量的符合性,零件是否遵循先进先
15 出原则?
日期:
是否每次设备启动和班次轮转的确认验证都被明确定 16
义并有效实施?
第二部分 工序质量关注(重点关注顾客反映以及内部审核过程中 发现的质量关注点)
审核部门:
主管经理:
STD标 准化
审核人: 3 工作现场5S是否符合标准要求?
分 层 审 核 检 查 表(适用于第二层、第三层)
分层审核表格

7
1.7
员工的生产动作是紧凑,流畅?(主管及以 上填)
8
1.8 员工是否知道目前的质量问题?
9
2.1 对防错装置验证是否有效
10
2.2 班组无人时,各电器电源是否关闭
11
生产安全管理状况是否正常(主管及以上 2.3 填)
12
设备工装控制
量具是否在校准期内?并且量具能正常 2.4 使用?
13
对于工装/设备维修后是否经检验员确 2.5 认?调机器是否受控?
YN
NC N/A 不符合内容描述
Y
N NC N/A 不符合内容描述
1
1.1 操作员工具备岗位操作资质(老员工)
2
1.2 在岗操作员工经培训后上岗(新员工)
3
1.3 操作员工穿戴,着装是否符合要求
4
1.4 员工是否遵守劳动纪律
5
人员控制
1.5ቤተ መጻሕፍቲ ባይዱ
是否按要求佩戴安全防护用具(如手 套,指套等)
6
1.6 员工是否正确理解作业指导书的要求
3.5 是否使用了FIFO系统?
21
3.6 是否使用了正确的流转用具?
22
4.1 工位上是否放置当前操作的作业指导书
工位上是否有作废的作业指导书,或本工
23
4.2 位同一加工产品,有不同版本的2份作业
指导书
24
作业指导书是否员工可直接可目视,直接 4.3 可取得
25
作业方法/过程
4.4
工序是否有背离工艺(即与作业标准不 符,另外的加工工艺要求)
N/A计数值= 0
总数= 0
43
6.1
工位上(包括地面)物料摆放是否整齐,标 识清楚,放在规定的区域范围内
过程分层审核-制造过程(一级)

生产车间(生产线):
审 审核员:班组长/技术员/车间主任 核
类别
序 号
检查项目
检查范围
如何检查
审核结果
周周周周周周 一二三四五六
作业者是否具备本岗位的操作技能(包括工艺文件 1 理解、设备工装的维护保养、参数的设置等)?特 抽查
殊工种的人员是否具备相应的上岗资格
6
本工位是否有与工位生产产品不相关或状态不明的 物料?
100%检查 100%检查
现场目视检查 现场目视检查
7
塑胶粒子是否按标准烘烤,烘烤的温度和时间是否 有记录确认?
100%检查
现场目视检查
8
本工位使用的模具/工装、设备是否与作业文件要求 一致?
100%检查
现场目视检查
设备运行状态是否完好,设备点检是否正确实施并
100%检查 现场目视检查
环境
20
现场环境是否符合6S要求?工位附近是否有与工作 无关的零件、工装等其它物品?
/安
全
21
工位照明是否正常,并满足强度要求,以便于操作 工进行外观目视自检?
100%检查 100%检查
现场目视检查 现场目视检查
注: 审核
执行审核员:
车间负责人:
审核问题记录
现场已整改问题
第 2 页,共 2 页
查上岗证、培训记 录、员工技能矩阵 图等;实际考核
审核问题记录
人员 2 操作员工是否知道如何使用紧急停机按钮?戴劳保防护用品( 眼镜、手套 、工作鞋、防护服、耳塞、防护面罩等)?
100%检查
现场目视检查
4 材料在生产区域是否定置摆放?
100%检查 现场目视检查
公司车间班组分层审核检查表
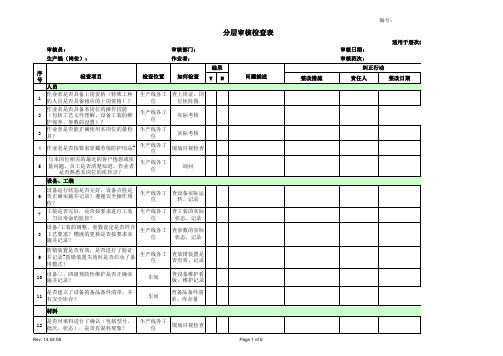
编号:
分层审核检查表
适用于层次3——公司层审核员:审核部门:审核日期:
生产线(岗位):作业者:审核班次:
30现场工位器具是否清洁、完好?生产线各工
位
现场目视检查
31现场工位是否按要求进行了污染物预
防,现场无污染物?
各车间记录
32是否配备了工艺文件规定的量检具,
并易于作业者得到?
生产线各工
位
现场目视检查
33量检具是否在鉴定有效期内,量检具
是否完好? 量检具的编号是否清晰。
生产线各工
位
现场目视检查
34对于特殊工位的检测装置是否进行了
校验:对扭矩按工艺值进行校验?阻
尼力值标样件校验?探伤、示漏工序
缺陷件校验?
特殊工位验证记录
35车间是否按要求实施了分层审核?各车间现场目视检查
36班组长和质管员是否按要求对首检记
录,参数记录,设备点检进行确认?
生产线各工
位
现场目视检查
37班组长和质管员是否对班组目视板进
行了更新?
各车间目视
板
现场目视检查
38实物质量是否工艺要求?生产现场是
否有生锈的产品和零件?
生产线各工
位
实物质量抽查测量
其他
1.未检查的项目记作“NR”,审核项数 项;其中不符合项数 项;分层审核 % 。
次3——公司层。
- 1、下载文档前请自行甄别文档内容的完整性,平台不提供额外的编辑、内容补充、找答案等附加服务。
- 2、"仅部分预览"的文档,不可在线预览部分如存在完整性等问题,可反馈申请退款(可完整预览的文档不适用该条件!)。
- 3、如文档侵犯您的权益,请联系客服反馈,我们会尽快为您处理(人工客服工作时间:9:00-18:30)。
第 1 页,共 2 页
1.是否按文件要求填写记录? 2.记录填写是否及时、清晰、完整、真实?(不允许未经实际操作或点检,造假/窜改记录) 10 记录和表单 3.记录是否按要求有相关人员的确认签字? 4.修改记录是否使用划改法,并签名和标注日期,不使用修正液? 5.记录使用的模板是否与DCC受控的最新版本一致?
8.卷盘、工件盒摆放是否超过标准高度10层或0.8M?
9.热处理/清洗/包装等关注化学品有效期、隔离及标识等。
10.生产数量和效率是否达到要求,如果未达到,是否有改善措施?
1.设备/模具是否按规定进行点检,是否按要求填写相关记录,异常是否及时处理?
2.机器/模具状态牌与实际状况是否一致?
3.模具及冲子刀口是否按规定周期维护保养,并填写保养记录?
、机器/模具/产品质量状况等。
1.早晨交接班是否打扫卫生? 2.现场是否整洁有序,设备、机台面、修模台、柜子、桌椅、窗台、暖气、地面是否整洁?地 面是否无废料及工件? 3. 电灯、气、水、门、窗等是否关闭? 15 现场6S管理 4.现场物品(如文件、卷盘、废料、水管等)放置是否都有标识,是否按区域摆放? 5.工具是否配套齐全,并按照要求分类放置?消耗品等是否放在指定位置(如手套、抹布、 酒精等)? 6.快速响应看板、生产看板、质量看板等现场看板是否及时更新、维护? 7.每周一早晨是否检查大扫除结果?
1.是否按检验指导书进行QC首检/末检/巡检,作业员自检,并填写检验记录?
2.是否在现场放置标准合格样件,在有效期内,并有QE签字确认?
3.如检验结果异常时,是否及时处理?
13
检验
4.极限样品是否有效?
5.不良履历是否及时更新?
6.SPC是否有效控制,对超出控制线的是否及时调整,并记录?
1.员工是否清楚交接班适宜? 14 交接班管理 2.交接班事宜是否被有效追踪和落实,是否有结果记录和反馈?如材料损耗、生产量、批次
1.机台参数是否和CP、工艺规程规定一致(吨位、闭合高度、冲床速度、步距等)?
11
参数
2.热处理槽液成分,浓度,温度,PH值是否与文件规定一致?
3.点检时参数超出文件规定,是否及时处理?
1.ERP系统录入是否正确? 12 ERP系统录入 2.ERP系统录入信息是否齐全?
3.批次量设置是否与工艺规程一致?
6
设备/模具的管 理,日常维护
4.模具维修是否有详细记录? 5.模具备件清单与实物是否一致,备件数量是否大于安全库存? 6.《模具履历表》是否及时填写?
7.模具存放是否符合定址定位的要求?
8、误送保护针和定位导位针是否安装到并正确使用?ຫໍສະໝຸດ 9.热处理是否按照日常维护计划审核。
7
测量设备仪器 和夹治具
1.是否对测量设备仪器和治具进行日常点检? 2.检测设备是否有效,校验标签是否在有效期内? 3.夹治具是否适用,并正常使用?
第 2 页,共 2 页
生产车间分层审核标准表 Workshop Layered Process Audit
审核项目
审核内容及标准
1 分层审核发现 1.以往分层审核发现是否关闭,纠正措施是否被有效执行?
2
客诉和制程改 1.客诉和制程改善所采取的措施是否被有效执行?
善
2.不合格品处理单和8D报告是否及时外理或回复?
3
现场职业健康 1.操作工人是否按要求穿戴安全防护用品?如工作服、手套、护目镜、口罩、防护鞋等? 安全管理 2.设备安全防护装置是否有效,如安全光栅、安全门等?
8
防错装置和防 错验证样品
1.PPT(自动检测)是否正常使用? 2.是否确认防错装置的有效性并填写验证确认记录? 3.校验标签是否在有效期内,有QE确认?
1.确认现场工艺规程、作业指导书、图纸、检验文件(如检验指导书、不良履历、外观辅助 图)是否齐全且为最新版本,并张贴在现场? 2.旧版文件是否及时从现场移走,并保证其无法恢复使用? 9 现场文件 3.使用的文件/图面是否保持清楚易读,无破损,容易识別? 4.文件名称是否与产品一致? 5.文件是否有受控章,有审批(相关人员签字或盖章,不允许打印签名)? 6.临时文件是否有审批,并在有效期内?
16
工作纪律
是否有聊私人电话、玩弄手机、擅离岗位、睡觉、聚众聊天、吃零食、上网做与工作无关的 事?
备注:1.如有新品生产,优先考虑LPA; 2.如检查结果为No,责任人需立即采取纠正行动; 3.如不能立即改善,责任人必须提交改善计划和预计完成时间; 4.如检查项与检查机台无关填写NA; 5.审核员将审核结果等记录到《QA080 分层审核问题追踪表》内,并追踪审核发现的改善; 6.对于上层级的审核发现,由下一层级或第三方来进行追踪验证后关闭。
1.操作人员是否明白作业流程和作业指导书要求?
2.是否按流程和作业指导书规定操作?是否按文件规定执行点检并按要求记录?
4
人员操作
3.异常情况是否上报到班组长? 4.是否熟练、正确的操作设备?
5.是否清楚产品的特殊特性、重点管控要求?
6.是否进行作业准备&清场记录?
1.原材料,半成品,成品是否有正确标签和质量状态标识,物料是否放置在规定区域内?
2.不合格品是否放置在隔离区域,并标识清楚与台帐一致?
3.每次换料是否将原材料标识单贴在(或写在)相应的表单上面并按要求填写换料记录?
5
原材料,半成 品,成品的控
制
4.标签(包括临时标签)是否能及时标识,并填写完整? 5.现场使用的物料是否与工艺规程规定一致? 6.产品是否有防护,避免污染、受损? 7.合格产品是否及时入库,满足温湿度管控要求?