脱硫运行中石膏含水量大的原因分析
浅析湿法脱硫石膏含水率高主要原因及控制措施

浅析湿法脱硫石膏含水率高主要原因及控制措施摘要:本文介绍了谏壁发电厂六期脱硫系统石膏含水率高的原因,并对其进行深入分析后列出了石膏含水率高的主要原因,针对存在问题采取了有效的措施,极大程度改善了石膏含水率过高的问题,并对进一步降低含水率提出了改进措施。
关键词:石膏含水率;原因;控制措施0引言国电谏壁发电厂六期#11、12机组脱硫装置已于2015年经过超低排放提效改造后投用,采用单塔双循环石灰石-石膏湿法脱硫工艺,设计脱硫效率不低于98.1%。
投产之后脱硫系统石膏实际含水率一直大于10%的设计要求,正常在15%左右,最高曾达到20%—25%,严重影响了石膏副产品的销售。
为解决此问题,对六期#11机组脱硫生产整个流程进行了分析,对相关参数进行控制和调整,目前石膏含水率基本稳定在10%左右。
1影响石膏含水率的主要原因1.1杂质含量过高,废水排放不正常脱硫浆液系统中的杂质主要有烟气中飞灰和石灰石杂质两个来源。
这些杂质会影响吸收塔内的反应,干扰石膏晶体的形成,使得脱硫石膏中飞灰含量急剧上升;另外,在脱水时杂质会夹在石膏表面和内部,因杂质脱水率很差,就会影响石膏的含水率。
石膏浆液中的这部分杂质可通过废水排出浆液系统,如果废水系统不能正常运行,杂质不断积累,达到一定的浓度就会影响石膏的含水率,而且是发生质变,对石膏含水率影响较大。
1.2脱硫运行中PH值控制不稳定,氧化反应不充分PH测量值是吸收塔反应控制的一个重要参数。
石灰石供浆量的多少应由锅炉负荷和FGD入口硫份的变化量来综合考虑决定,若PH值测量不准,则容易出现石灰石供浆量过多,CaCO3含量超标,从而影响石膏的脱水率。
由相关数据可知,随着吸收塔PH值得增加(均是一台氧化风机运行),CaCO3含量和石膏含水率明显增大,特别在PH值明显升高到5.8以上时,将会导致石灰石的溶解速率急剧下降,CaCO3含量和石膏含水率呈阶跃式上升。
由此说明浆液PH值对石膏结晶影响虽然是间接的,但却是重要的决定性因素之一。
脱硫系统运行中常见问题及处理

脱硫系统运行中常见问题及处理1 引言石灰石-石膏湿法烟气脱硫工艺是目前较为成熟的脱硫工艺,被广泛应用于火电厂烟气净化处理系统中,我公司三四期脱硫系统陆续投入运行,在调试及运行过程中出现了一些问题,也是其它电厂经常遇到的问题。
2 吸收塔溢流问题2.1 吸收塔溢流现象调试及运行中吸收塔会发生浆液溢流现象,而且此现象很普遍。
溢流现象不是连续的,而且有一定的规律性,表面现象来看,很不好解释。
例如我公司#5吸收塔溢流管线标高为11150mm,溢流排水管线位置13110mm,上面呼吸孔标高为14000mm。
系统停运时液位正常,运行中液位显示10000mm时溢流口开始间歇性溢流,并从呼吸孔排出泡沫。
对液位计、溢流口几何高度进行校验,没有发现问题。
当液位降低到8.5米左右,烟气会从塔体溢流口冒出,造成浆液从呼吸孔喷出。
2.2 原因分析DCS显示的液位是根据差压变送器测得的差压与吸收塔内浆液密度计算得来的值,而不是吸收塔内真实液位。
由于循环泵、氧化风机的运行,而且水中杂质(有机物,盐类等)、氧量较大,而引起浆液中含有大量气泡、或泡沫,从而造成吸收塔内浆液的不均匀性,由于浆液密度表计取样来自吸收塔底部,底部浆液密度大于氧化区上部浆液密度,造成仪表显示偏低。
我公司脱硫用水采自机组循环水排污水,水质较差,有机物较高可达30~40,CL-含量超过1100 mg/l。
此时吸收塔内液位超过了表计显示液位,此时塔内液位已经达到了溢流口的高度,再加上脉冲扰动、氧化空气鼓入、浆液的喷淋等因素的综合影响而引起的液位波动,并且浆液液面随时发生变化,导致吸收塔间歇性溢流。
2.3 处理方案2.3.1 确定合理液位调试期间确定合理的运行液位,根据现场运行条件,人为降低运行控制液位计显示液位,使塔内实际液位仅高于塔体溢流口高度,防止烟气泄露。
修正吸收塔浆液密度来提高液位计显示液位,控制液位在塔体溢流口至溢流排水口标高之间。
2.3.2 加入消泡剂尽管确定液位仅高于塔体溢流口高度,也难免吸收塔浆液泡沫从呼吸孔冒出。
脱硫运行中石膏含水量大的原因分析及解决办法

脱硫运行中石膏含水量大的原因分析及解决办法湿法石灰石-石膏烟气脱硫工艺中,石灰石浆液在吸收塔内对烟气进行逆流洗涤,生成半水亚硫酸钙并以小颗粒状转移到浆液中,利用空气将其强制氧化生成二水硫酸钙(CaSO4·2H2O)结晶。
用石膏排出泵将吸收塔内的浆液抽出,送往石膏旋流器,进行浓缩及颗粒分级,稀的溢流(细颗粒)返回吸收塔;浓缩的底流(较粗颗粒)送往真空皮带机进行石膏脱水。
脱水后的石膏含水率一般控制在10%(质量含量)以下,为达标。
若石膏水分过高,不仅影响脱硫系统和设备的正常运行,而且对石膏的储存、运输及后加工等都会造成一定的困难。
下面就脱硫石膏含水量大原因以及解决办法与各位交流一下。
造成脱硫石膏含水量大原因分析如下:1、吸收塔内浆液的密度偏小,启动石膏排出泵。
2、吸收塔液的pH测量值不达标。
3、氯离子含量超标。
4、脱硫塔入口含尘量偏高,导致吸收塔浆液“中毒”。
5、石灰石品质发生变化。
6.入炉煤含硫量突然发生变化,超设计值较多。
7、石膏旋流器发生异常。
8、真空皮带机异常9、氧化空气量不足。
1.1、吸收塔内浆液的密度直观地反映塔内反应物的浓度(固体含量)高低,密度值升高,浆液的固体含量增加。
工艺设计中在石膏排出泵出口管道上安装石膏浆液密度表,运行中根据该密度值的高低来自动控制石膏浆液的排放。
石膏浆液密度设定值根据反应产物—石膏形成和结晶情况来确定,一般要求是形成大颗粒易脱水的石膏晶体,运行过程中根据浆液性质的不同,设定值有所不同,一般控制在1180~1200之间,固体含量在10%左右。
假如,排出的石膏浆液固体含量偏低,即密度较小石膏浆液未达到饱和或过饱和度较低,形成的石膏晶体颗粒细小,石膏难以脱水。
1.2、吸收塔液的pH测量值是参与反应控制的一个重要参数,用于确定需要输送到烟气脱硫吸收塔的新鲜反应浆液的流量。
pH值升高,新的反应浆液供应量将减少,反之,pH值降低,新的反应浆液供应量将增加。
若pH计测量不准,则需要添加的石灰石量就不能准确控制,而过量的石灰石使石膏纯度降低,造成石膏脱水困难。
脱硫石膏含水量高的原因分析和控制措施
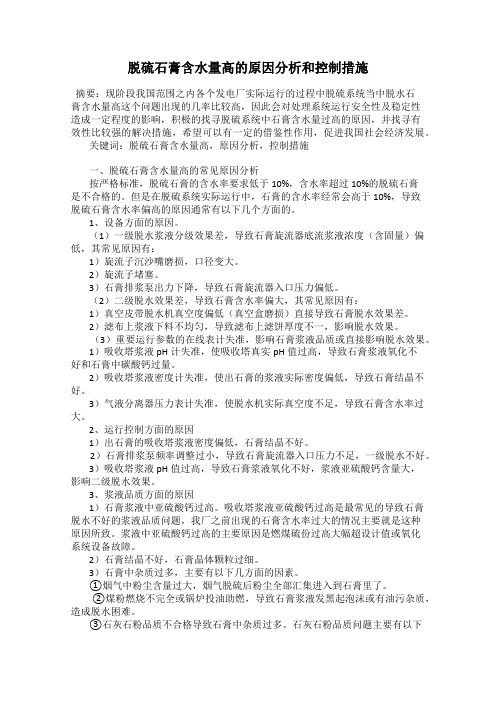
脱硫石膏含水量高的原因分析和控制措施摘要:现阶段我国范围之内各个发电厂实际运行的过程中脱硫系统当中脱水石膏含水量高这个问题出现的几率比较高,因此会对处理系统运行安全性及稳定性造成一定程度的影响,积极的找寻脱硫系统中石膏含水量过高的原因,并找寻有效性比较强的解决措施,希望可以有一定的借鉴性作用,促进我国社会经济发展。
关键词:脱硫石膏含水量高,原因分析,控制措施一、脱硫石膏含水量高的常见原因分析按严格标准,脱硫石膏的含水率要求低于10%,含水率超过10%的脱硫石膏是不合格的。
但是在脱硫系统实际运行中,石膏的含水率经常会高于10%,导致脱硫石膏含水率偏高的原因通常有以下几个方面的。
1、设备方面的原因。
(1)一级脱水浆液分级效果差,导致石膏旋流器底流浆液浓度(含固量)偏低,其常见原因有:1)旋流子沉沙嘴磨损,口径变大。
2)旋流子堵塞。
3)石膏排浆泵出力下降,导致石膏旋流器入口压力偏低。
(2)二级脱水效果差,导致石膏含水率偏大,其常见原因有:1)真空皮带脱水机真空度偏低(真空盒磨损)直接导致石膏脱水效果差。
2)滤布上浆液下料不均匀,导致滤布上滤饼厚度不一,影响脱水效果。
(3)重要运行参数的在线表计失准,影响石膏浆液品质或直接影响脱水效果。
1)吸收塔浆液pH计失准,使吸收塔真实pH值过高,导致石膏浆液氧化不好和石膏中碳酸钙过量。
2)吸收塔浆液密度计失准,使出石膏的浆液实际密度偏低,导致石膏结晶不好。
3)气液分离器压力表计失准,使脱水机实际真空度不足,导致石膏含水率过大。
2、运行控制方面的原因1)出石膏的吸收塔浆液密度偏低,石膏结晶不好。
2)石膏排浆泵频率调整过小,导致石膏旋流器入口压力不足,一级脱水不好。
3)吸收塔浆液pH值过高,导致石膏浆液氧化不好,浆液亚硫酸钙含量大,影响二级脱水效果。
3、浆液品质方面的原因1)石膏浆液中亚硫酸钙过高。
吸收塔浆液亚硫酸钙过高是最常见的导致石膏脱水不好的浆液品质问题,我厂之前出现的石膏含水率过大的情况主要就是这种原因所致。
影响脱硫石膏品质的常见原因修订稿
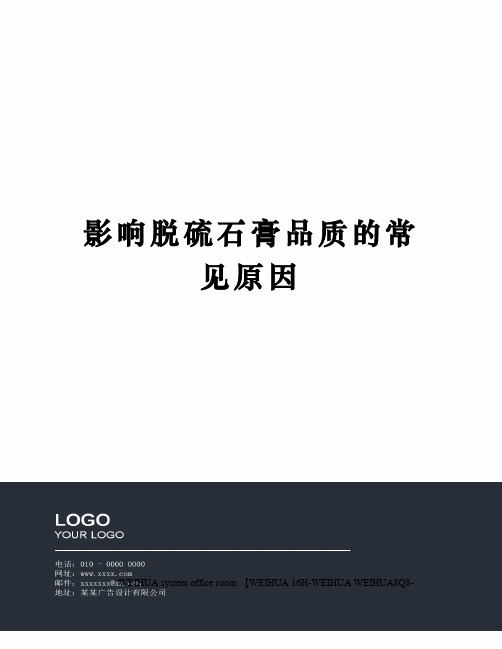
影响脱硫石膏品质的常见原因WEIHUA system office room 【WEIHUA 16H-WEIHUA WEIHUA8Q8-影响脱硫石膏品质的常见原因烟气中灰尘含高。
烟气中的灰尘在脱硫过程会因洗涤而进入浆液中,浆液中的杂质含量高时,不能随着脱水而全部排出,使成品石膏中的杂质含增加,影响石膏品质。
烟气中灰尘含量高的原因主要是煤质差及电除尘效果差所致,当入口烟气中灰尘含量超标时及时联系锅炉运行检查电除尘运行情况,适当关小增压风机静叶开度,减少进入脱硫的烟气量,待电除尘恢复正常后再恢复脱硫系统的正常运行。
也有可能是脱水后废水排放少,使吸收塔的杂质越积越多。
吸收塔浆液中亚硫酸钙含量高。
亚硫酸钙含量升高的主要原因是氧化不充分引起的,正常情况下由于烟气中含氧量低(4%~8%左右),锅炉燃烧后产生的烟气中的硫氧化物主要是二氧化硫,在脱硫过程中浆液吸收二氧化硫而生成亚硫酸钙,脱硫系统通过氧化风机向吸收塔补充空气,强制氧化亚硫酸钙生成硫酸钙,硫酸钙与2个水分子结合生成石膏分子,当石膏达到一定饱和程度后结晶析出,经脱水后产生成品石膏。
而由于种种原因不能使亚硫酸钙得到充分氧化时(原因包括氧化空气流量不够;氧化空气压力达不到要求;吸收塔搅拌器搅拌效果不佳等),浆液中亚硫酸钙的含量就会升高,最终使成品石膏品质下降,同时会造成脱水效果差、脱硫系统脱硫效率差、石灰石消耗量增加等一系列不良影响。
此时要检查氧化风机运行情况(压力、电流、流量等),氧化空气母管是否有漏气现象,必要时适当减少进烟量;也可以排出一部分吸收塔浆液,增加新鲜水,待吸收塔内浆液品质改善后再恢复正常运行。
吸收塔浆液中碳酸钙含量高。
碳酸钙作为脱硫的吸收剂,在脱硫系统运行过程中要不断的补充,为了保证脱硫效果,吸收塔内要保持一定的PH值,有时PH值保持较高,这样浆液中的碳酸钙含量就会较高;也有可能石灰石活性较差,石灰石浆液补充到吸收塔内后,在短时间内不能充分电离,也就不能和二氧化硫发生反应,最终会随脱水而进入石膏中。
脱硫石膏含水量高原因分析及应对

脱硫石膏含水量高原因分析及应对现阶段我国范围之内各个发电厂实际运行的过程中脱硫系统当中脱水石膏含水量高这个问题出现的几率比较高,因此会对处理系统运行安全性及稳定性造成一定程度的影响,积极的找寻脱硫系统中石膏含水量过高的原因,并找寻有效性比较强的解决措施,希望可以有一定的借鉴性作用,促进我国社会经济发展。
标签:脱硫石膏含水量高,原因分析,控制措施1 石灰石-石膏湿法脱硫工艺流程石灰石-石膏湿法是应用石灰石浆液作为吸收剂,其与高温烟气中的SO2接触后,二者发生化学反应形成一种副产物CaSO4·2H2O即石膏,从而实现对烟气脱硫的目的。
吸收塔内的石膏浆液,会通过石膏排出泵,输送到石膏浆液旋流器当中完成一级脱水。
此环节通常会脱去二分之一的水分。
一级脱水之后石膏饼会进入到真空皮带脱水机当中进行二级脱水。
在完成了一级、二级脱水后,最终产物的脱水量会达到90%以上。
二级脱水后的石膏送回到石膏仓内。
品质好的石膏可以对市场销售,为企业获取更多的经济效益。
2 石膏含水率高原因分析针对石膏脱水系统运行现状,先后联系电科院、航天环境及兄弟电厂人员作了详细的原因分析,通过逐个排查影响石膏含水率高的因素后,现分析情况如下。
2.1 烟气SO2浓度突变燃煤硫分或烟气SO2浓度是脱硫系统的重要设计参数。
在实际运行中,如果烟气SO2浓度高于设计值,超出吸收塔处理能力,则脱硫效率会显著下降,而且石膏品质也得不到保证。
SO2浓度升高会加大石灰石浆液给料量,导致石膏中碳酸盐含量超标。
由于烟气量或原烟气SO2浓度突变,造成吸收塔内反应加剧,CaCO3含量减少,PH值下降,此时为保证脱硫效率而增加石灰石供浆量以提高吸收塔浆液的PH值,但由于反应加剧吸收塔浆液中的CaSO3·1/2H2O含量大量增加,若此时不增加氧量使CaSO3·1/2H2O迅速反应成CaSO4·2H2O,则由于CaSO3·1/2H2O可溶解性强先溶于水中,而CaCO3溶解较慢,过饱和后形成固体沉积。
火电机组脱硫石膏问题研究与分析

火电机组脱硫石膏问题研究与分析摘要火电机组脱硫石膏普遍存在含水率高、不成型、脱水系统运行异常等问题,本文通过运行数据分析、样品化验,判断杂质堵塞脱水机滤布、硫分超设计值、氧化效果不佳是石膏含水率高且脱水困难的原因。
提出了保证石灰石品质、改善除尘效果、控制燃煤硫份,避免脱硫系统超负荷运行、保证浆池容积并延长石膏排出时间,合理控制吸收塔液位、改善氧化效果并等技术管理措施。
关键词脱硫;除尘;杂质;石膏;含水率;0 引言我国火电厂主要采用煤为燃料,燃煤产生的二氧化硫是我国火电行业排放的主要大气污染物。
目前国内大多数燃煤电厂采用石灰石-石膏法脱硫技术,该法具有反应速度快、设备简单、脱硫效率高等优点,但普遍存在腐蚀严重、运行维护费用高及易造成二次污染等问题,尤其在运行时间久,燃煤硫份较高的机组,易发生浆液石膏不成型,脱水困难等问题[1、2]。
1问题调查本案例为300MW火电机组,脱硫系统采用石灰石-石膏湿法脱硫工艺,设计工况下脱硫入口SO2浓度不超过4600mg/Nm3,脱硫出口SO2浓度≤35mg/Nm3(标态、干基、6%O2)。
现场查看石膏脱水装置运行情况发现两座吸收塔排出的石膏粘性大,真空皮带脱水机的滤布表面有黑色杂质,石膏松软且不能成型。
1.1 石膏旋流器石膏旋流器是脱水系统的重要设备,用于实现浆液的固液分离,将含固率提升至50%,排出剩余浆液返回吸收塔。
运行中需通过调整旋流器入口压力,保证固液分离效果,当旋流器的沉沙嘴破损或入口压力不足时,导致脱水困难[3、4]。
调查发现一级脱水系统中包含两台石膏旋流器,每台旋流器设有7个旋流子。
根据历史数据分析得知在5至6月,1、2号石膏旋流器入口压力平均值分别为166.87kPa、164.36kPa,能够满足脱硫运行规程的要求。
化验得到1、2号石膏旋流器底流浆液含固率分别为55.31%、52.34%,达到设计要求(40%~60%),石膏旋流器运行状况良好,可排除因沉沙嘴破损或入口压力不足对石膏脱水效果的影响[5]。
湿法脱硫石膏含水率高原因分析

湿法脱硫石膏含水率高原因分析1.脱硫废水中含水量高:湿法脱硫过程中,烟气中的二氧化硫与脱硫剂(如石灰石或石膏石)反应生成石膏,同时也产生大量的湿法脱硫废水。
废水中的石膏会带有一定的水分,并与废水一同沉积于石膏浆中。
2.脱硫废水处理不当:如果脱硫废水处理不当,例如处理设施设计不合理、运行不稳定等因素,废水中的悬浮物或泥浆含量较高,将会导致石膏中含水率的增加。
处理设施的不完善会影响废水的沉淀效果,使得石膏中的水分不能充分脱水。
3.细度不足:石膏生成后,如果其细度不足,即颗粒较大且粒度不均匀,那么其表面积相对较小,难以有效地释放水分。
这将导致石膏含水率的提高。
4.干燥条件不充分:湿法脱硫石膏需要经过干燥工艺,以获得可靠的石膏质量和减少含水率。
然而,如果干燥条件不充分,例如干燥器的处理能力不足或干燥温度不合适等原因,就会导致石膏的含水率较高。
5.操作不当或参数设置不当:湿法脱硫系统的操作过程中,操作人员需要根据具体情况设置适当的参数,例如脱硫剂的投加量、反应温度、流速等。
如果操作不当或者参数设置不当,就可能导致脱硫反应不完全或石膏过程中的含水率较高。
6.环境湿度:湿法脱硫石膏在运输、存储和使用过程中,如果处于高湿度环境中,就会导致石膏颗粒吸收湿气,增加含水率。
解决高含水率问题的方法包括:-改善脱硫废水处理工艺,提高脱硫废水中悬浮物和泥浆的去除效率,减少废水中的含水量;-监测并控制石膏颗粒的细度,提高其表面积,使其易于释放水分;-严格控制石膏干燥的条件,确保干燥器具备足够的处理能力,并按照适当的温度进行干燥;-做好湿法脱硫系统的操作管理,设置合适的参数,确保脱硫反应充分,并降低石膏含水率;-在运输、存储和使用过程中,控制环境湿度,减少石膏的吸湿量。
总之,湿法脱硫石膏含水率高的原因可能有多方面,需要综合考虑并解决不同环节中可能存在的问题,以降低石膏的含水率。
石灰石石膏脱硫工艺石膏脱水困难的原因分析以及解决方法

脱硫运行中石膏脱水困难的原因分析及解决办法1 原因分析脱硫运行中出现石膏含水量大,表现在脱机时石膏下料口不结块、不滑落,成稀泥状,甚至出现下部粘稠、上部成流水状。
这种脱水下的物质物理性质成粘性,分析原因一般有以下几种情况:1.1 入口含尘量偏高,导致吸收塔浆液“中毒”图片2:左侧为浆液含灰量大沉淀的取样照片,右侧为正常浆液取样沉淀后的照片原烟气中的飞灰进入吸收塔浆液中在一定程度上阻碍了SO2与脱硫剂的接触,降低了石灰石中Ca2+的溶解速率,同时飞灰中不断溶出的一些重金属如Hg、Mg、Cd、Zn等离子会抑制Ca2+与HSO3-的反应,“封闭”了吸收剂的活性。
一般要求吸收塔入口的烟尘含量不能超过200mg/m3,如果超过300 mg/m3以上就容易出现这种现象。
如果烟尘含量测量仪表不准,最直接的方法可以取样沉淀,如果沉淀的固体物质中上部的黑色灰状物质超过总量的1/3(正常的应在1/4以下),就说明入口的烟尘含量太大了(如图片2)。
现在由于电除尘器效率不是很好,吸收塔变成了吸尘器,吸收塔浆液发黑,起泡,脱水时在石膏表明有一层黑色物质(如图片3),在这种状况下再坚持运行可想而知。
吸收塔浆液极易“中毒”。
一旦发生“中毒”现象,就需要将浆液全部排出置换新鲜的浆液,造成很大的浪费,并影响脱硫系统的正常投入。
吸收塔浆液“中毒”后,需要半月时间纠正才能彻底改善,在此期间会浪费大量石灰石粉,排放大量浆液,提高了运行成本。
图片3:含灰量大时,皮带脱水时的状况1.2 石灰石品质发生变化石灰石粉的品质是影响脱硫运行的一个重要因素,其中碳酸钙含量及成品的细度是关键,杂质增多或含量下降都会使浆液品质恶化,细度越细反应效果就越好。
这就可能出现当碳酸钙含量及成品的细度发生较大变化时,其反应活性降低,极可能发生供浆过量,此时塔内浆液中含CaCO3量增大,由石灰石颗粒易粘结在一起,导致造成脱水困难现象的发生。
另外如果石灰石原料中夹带黏土、泥沙等杂质,这些杂质状态不稳定,也会在一定程度上造成脱水困难的现象发生。
关于石灰石-石膏湿法脱硫装置石膏脱水困难的分析及措施
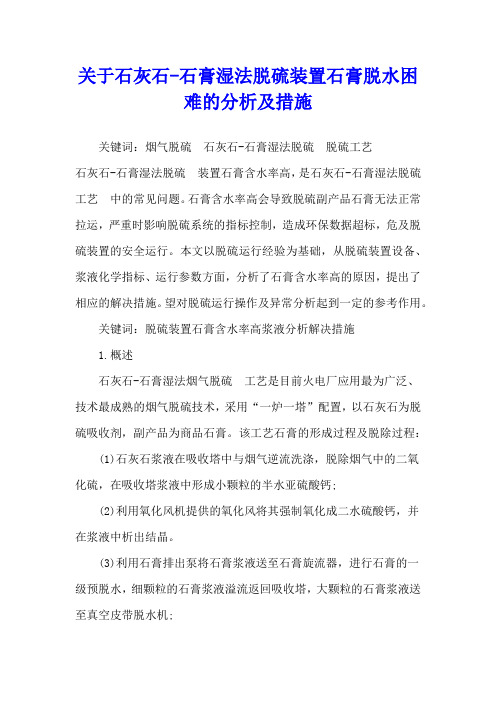
关于石灰石-石膏湿法脱硫装置石膏脱水困难的分析及措施关键词:烟气脱硫石灰石-石膏湿法脱硫脱硫工艺石灰石-石膏湿法脱硫装置石膏含水率高,是石灰石-石膏湿法脱硫工艺中的常见问题。
石膏含水率高会导致脱硫副产品石膏无法正常拉运,严重时影响脱硫系统的指标控制,造成环保数据超标,危及脱硫装置的安全运行。
本文以脱硫运行经验为基础,从脱硫装置设备、浆液化学指标、运行参数方面,分析了石膏含水率高的原因,提出了相应的解决措施。
望对脱硫运行操作及异常分析起到一定的参考作用。
关键词:脱硫装置石膏含水率高浆液分析解决措施1.概述石灰石-石膏湿法烟气脱硫工艺是目前火电厂应用最为广泛、技术最成熟的烟气脱硫技术,采用“一炉一塔”配置,以石灰石为脱硫吸收剂,副产品为商品石膏。
该工艺石膏的形成过程及脱除过程: (1)石灰石浆液在吸收塔中与烟气逆流洗涤,脱除烟气中的二氧化硫,在吸收塔浆液中形成小颗粒的半水亚硫酸钙;(2)利用氧化风机提供的氧化风将其强制氧化成二水硫酸钙,并在浆液中析出结晶。
(3)利用石膏排出泵将石膏浆液送至石膏旋流器,进行石膏的一级预脱水,细颗粒的石膏浆液溢流返回吸收塔,大颗粒的石膏浆液送至真空皮带脱水机;(4)浆液通过真空皮脱水机后,形成含水量小于10%的石膏,输送至石膏库外运。
在石灰石-石膏湿法烟气脱硫工艺中,石膏含水量高、石膏脱水困难是普遍存在的问题,石膏能否正常脱水,不但反应出吸收塔浆液品质活性,更是脱硫系统能否正常运行的关键。
在实际运行工作当中,多次遇到由于各种原因导致石膏脱水困难的情况,通过采取相应的调整措施,恢复了系统的正常运行。
2.石膏含水率高的表现(1)脱硫装置脱水系统无法形成含水率小于10%的商品石膏,只能形成含水率在15%-25%的稠糊状石膏,石膏库的石膏无法堆积、装车运输。
(2)吸收塔内浆液密度不断升高,脱硫效率明显下降,通过增加钙硫比、液气比后脱硫效果无明显提升,同等工况条件下供浆量大于正常运行值。
湿法脱硫石膏含水率高原因分析
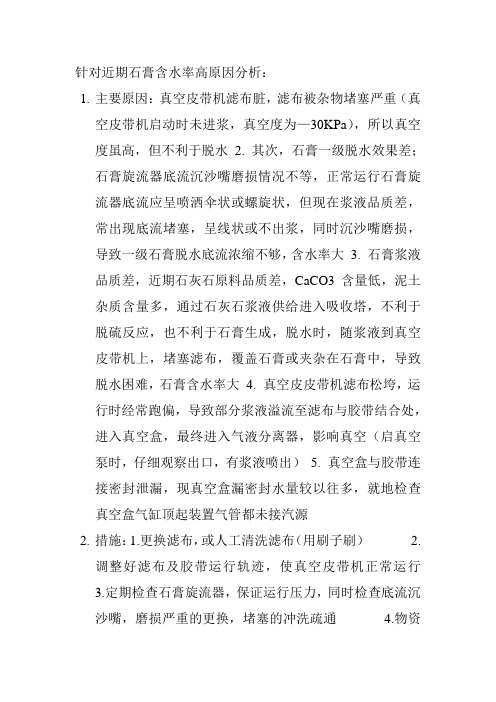
针对近期石膏含水率高原因分析:1.主要原因:真空皮带机滤布脏,滤布被杂物堵塞严重(真空皮带机启动时未进浆,真空度为—30KPa),所以真空度虽高,但不利于脱水 2. 其次,石膏一级脱水效果差;石膏旋流器底流沉沙嘴磨损情况不等,正常运行石膏旋流器底流应呈喷洒伞状或螺旋状,但现在浆液品质差,常出现底流堵塞,呈线状或不出浆,同时沉沙嘴磨损,导致一级石膏脱水底流浓缩不够,含水率大 3. 石膏浆液品质差,近期石灰石原料品质差,CaCO3含量低,泥土杂质含量多,通过石灰石浆液供给进入吸收塔,不利于脱硫反应,也不利于石膏生成,脱水时,随浆液到真空皮带机上,堵塞滤布,覆盖石膏或夹杂在石膏中,导致脱水困难,石膏含水率大 4. 真空皮皮带机滤布松垮,运行时经常跑偏,导致部分浆液溢流至滤布与胶带结合处,进入真空盒,最终进入气液分离器,影响真空(启真空泵时,仔细观察出口,有浆液喷出)5. 真空盒与胶带连接密封泄漏,现真空盒漏密封水量较以往多,就地检查真空盒气缸顶起装置气管都未接汽源2.措施:1.更换滤布,或人工清洗滤布(用刷子刷) 2.调整好滤布及胶带运行轨迹,使真空皮带机正常运行3.定期检查石膏旋流器,保证运行压力,同时检查底流沉沙嘴,磨损严重的更换,堵塞的冲洗疏通 4.物资采购合格的石灰石原料,保证石灰石浆液品质,运行验收、卸料时注意尽量避免杂物进入石灰石仓 5.对真空系统进行检查消漏 6.运行加强调整,控制石膏厚度**电厂2台300MW机组采用湿法脱硫技术,其中二期2台300MW机组同步建设烟气脱硫装置,于2010年10月投产,一期1号机组的烟气脱硫装置于2011年12月投产,2号机组脱硫装置正在改造施工也将相继投产。
投产之后3套脱硫系统石膏的实际含水率一直大于10%的设计要求,正常都在14%~15%,最高达到18%,影响了石膏的品质。
为此从脱硫整个流程进行了分析,对脱硫参数进行控制和调整,对相关设备进行了改进,现在石膏的含水率一直稳定在10%以内。
烟气脱硫系统石膏含水率高原因分析及对策

烟气脱硫系统石膏含水率高原因分析及对策燃煤火电厂普遍采用石灰石-石膏湿法烟气脱硫技术,而石膏含水率偏高是湿法脱硫装置经常性存在的问题。
以某电厂湿法脱硫石膏含水率严重超标现象为案例,通过对脱硫系统设备状况、入口烟气成分、浆液品质以及运行控制等影响石膏含水率的主要因素进行排查分析,其主要原因在于脱硫浆液亚硫酸根含量、pH值和密度值控制偏高,再加上浆液搅拌器发生故障无法投运造成一级塔浆液强制氧化效果偏差,综合导致了石膏脱水困难,其含水率偏高。
针对上述发现的问题采取有效的解决措施,最终使石膏含水率降低到合格范围内,并对今后的运行管理提出一些合理建议和优化措施。
石灰石—石膏湿法脱硫技术因其处理烟气量大、效率高、技术成熟、使用寿命长等优点被火电厂广泛采用。
采用石灰石-石膏湿法脱硫火电厂为了增加经济效益,脱硫石膏(主要成分CaSO4·2H2O与天然石膏相似,所以可替代天然石膏生产不同用途的石膏制品)都作为一种商品对外进行销售。
然而,在现运行的燃煤机组中脱硫系统普遍存在石膏含水率高、石膏品质差的状况。
若石膏含水率过高,造成石膏无法正常脱出,不但影响机组脱硫系统的安全稳定运行,还对石膏的销售有一定影响。
1石膏含水率超标情况概述某电厂3号机组为670MW燃煤机组,2019年7月对机组脱硫系统进行了超低排放改造,改造后脱硫系统为液柱塔+喷淋塔串联模式运行,设计参数:脱硫系统入口SO2质量浓度为9397mg/m3(标态、干基、6%O2)时,烟囱入口SO2质量浓度≤25.4mg/m3,满足超低排放限制值35mg/m3要求。
2020年3月22日,机组脱硫系统出现石膏脱水困难现象,石膏成稀泥状从石膏库淌出,严重影响了脱硫装置的稳定运行。
2石膏脱水困难的原因分析在石灰石-石膏湿法脱硫装置的实际运行过程中,影响石膏脱水效果的主要因素有:煤质、入口烟尘质量浓度、浆液pH值、浆液中亚硫酸钙质量浓度、石灰石品质、氧化风量、工艺水质等多个方面。
脱硫石膏含水率高的原因及控制措施

脱硫石膏含水率高旳原因及控制措施石灰石-石膏湿法烟气脱硫工艺中,用石灰石浆液作为吸取剂,石灰石、石膏混合浆液在吸取塔内对烟气进行逆流洗涤,烟气中旳 SO2与溶解旳石灰石中 Ca2+反应,在浆液中生成半水亚硫酸钙(CaSO3•·1/2H2O),再被氧化风机鼓入旳空气将其强制氧化生成二水硫酸钙(CaSO4·2H2O)结晶体。
石膏排出泵将吸取塔内旳浆液抽出,送往石膏旋流器进行分离,细颗粒旳溢流送往回收水箱,较粗颗粒旳底流送往真空皮带脱水机进行脱水,脱水后旳石膏含水率一般控制在 10%如下(称为达标)。
含水率过高,对石膏旳储存及加工都会导致一定旳困难,且直接影响石膏旳商业应用价值,为此,必须加以控制。
导致脱水效果差,石膏含水率高旳重要原因有如下几条:1.石膏旋流器沉砂嘴被磨损石膏旋流器最为石膏脱水旳一级脱水设备,在长时间旳使用过程中沉砂嘴被磨损,口径变大,致使底流流量变大,使得进入脱水机旳浆液含固量变小,液中小颗粒石膏晶体增多,使浆液中旳水不轻易从滤布孔隙分离出来;2.真空皮带机滤布堵塞真空皮带机是石膏二次脱水旳重要设备,脱水效果与浆液旳性质、滤布旳清洁程度有较大旳关系。
一是脱水设备运行不正常,如滤布冲洗不洁净或滤布使用周期过长都会使皮带机脱水效果变差,脱水不畅;二是石膏浆液自身性质旳变化,如浆液中旳杂质含量增长等引起滤布过滤通道旳堵塞。
若要到达一定旳固液分离效果,必须使真空升高,就我场旳现实状况来看,一号脱水机靠近操作侧旳吕布表面有一层黑乎乎旳油渍,致使滤布在喷嘴旳冲洗下不能彻底清洁表面旳污垢;3.废水排放量旳多少脱硫浆液系统中旳杂质重要是由烟气中飞灰和石灰石中杂质构成。
这些杂质一般不参与反应。
杂质量可间接从监测 Cl-浓度反应出来。
从四月份到目前旳石膏化验汇报中可以看出,我厂目前旳废水排放已能到达 FGD 正常运行原则,Cl-浓度已控制在正常范围之内。
因此就我厂目前现实状况而言,脱水效果差跟废水排放已经没有太大旳联络;4.氧化空气局限性石灰石浆液在吸取塔内对烟气进行逆流洗涤,生成半水亚硫酸钙并以小颗粒状转移到浆液中,运用空气将其强制氧化生成二水硫酸钙(CaSO4·2H2O)结晶进行脱水。
脱硫石膏脱水困难原因分析及解决方案

脱硫石膏脱水困难原因分析及解决方案控制吸收塔液位是影响石膏脱水的重要因素之一。
如果液位过高,会导致石膏颗粒沉积不均匀,形成分层现象,导致石膏脱水困难;如果液位过低,会使石膏颗粒浓度过高,导致石膏结晶不良,同样会影响石膏的脱水效果。
1.2.1.4粉尘含量和氧化风量粉尘含量和氧化风量也会影响石膏的脱水效果。
过高的粉尘含量会使石膏颗粒表面附着粉尘,影响石膏的结晶和脱水效果;而过高的氧化风量则会使石膏颗粒表面氧化,同样会影响石膏的脱水效果。
1.2.2脱水设备的运行状况脱水设备的运行状况也是影响石膏脱水的重要因素。
如果脱水设备的过滤布老化或者损坏,就会使石膏饼中的水分难以脱出;如果脱水设备的排水口堵塞或者不畅,也会影响石膏的脱水效果。
2解决方案2.1参数控制方案针对影响石膏脱水的因素,可以采取以下措施:控制吸收塔浆液的PH值和密度,保持合适的液位,控制粉尘含量和氧化风量。
具体来说,可以通过调整石灰石浆液的进料量和加入一定量的石膏晶种,控制浆液的PH值和密度;采用合适的液位控制方法,保持吸收塔内的浆液浓度均匀;加强粉尘和氧化风的管控,减少对石膏脱水的影响。
2.2脱水设备改进方案针对脱水设备的问题,可以采取以下措施:定期更换过滤布,保持设备的正常运转;加强设备的维护和保养,确保排水口畅通。
同时,可以考虑引进新型的脱水设备,提高石膏脱水的效率和质量。
总之,针对石膏脱水困难的问题,需要从吸收塔参数控制和脱水设备改进两个方面入手,综合采取措施,提高石膏的脱水效率和质量。
吸收塔中的石灰石CaCO3含量也会影响脱硫效果。
石灰石的含量越高,可以提供更多的Ca2+,有利于SO2与脱硫剂的反应,但同时也会增加石膏的产量和含量。
如果石灰石含量过低,则会影响SO2的吸收和氧化。
因此,需要控制石灰石的投加量,使其达到最佳的脱硫效果。
同时,石灰石的粒度也会影响脱硫效果,粒度过大会降低石灰石的反应速率,粒度过小则会影响石灰石的循环反应和石膏的脱水效果。
脱硫系统石膏含水率偏高的原因分析及控制措施
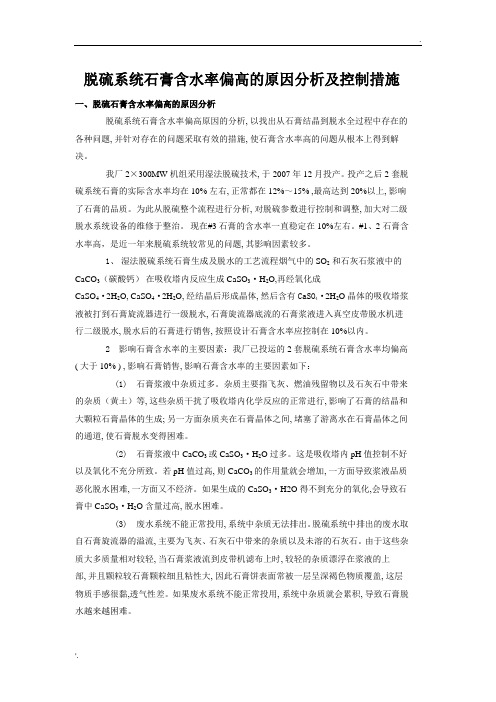
脱硫系统石膏含水率偏高的原因分析及控制措施一、脱硫石膏含水率偏高的原因分析脱硫系统石膏含水率偏高原因的分析, 以找出从石膏结晶到脱水全过程中存在的各种问题, 并针对存在的问题采取有效的措施, 使石膏含水率高的问题从根本上得到解决。
我厂2×300MW 机组采用湿法脱硫技术, 于2007 年12 月投产。
投产之后2套脱硫系统石膏的实际含水率均在10% 左右, 正常都在12%~15% ,最高达到20%以上, 影响了石膏的品质。
为此从脱硫整个流程进行分析, 对脱硫参数进行控制和调整, 加大对二级脱水系统设备的维修于整治。
现在#3石膏的含水率一直稳定在10%左右。
#1、2石膏含水率高,是近一年来脱硫系统较常见的问题, 其影响因素较多。
1、湿法脱硫系统石膏生成及脱水的工艺流程烟气中的SO2和石灰石浆液中的CaCO3(碳酸钙)在吸收塔内反应生成CaSO3·H2O,再经氧化成CaSO4·2H2O, CaSO4·2H2O, 经结晶后形成晶体, 然后含有CaSO4·2H2O 晶体的吸收塔浆液被打到石膏旋流器进行一级脱水, 石膏旋流器底流的石膏浆液进入真空皮带脱水机进行二级脱水, 脱水后的石膏进行销售, 按照设计石膏含水率应控制在10%以内。
2 影响石膏含水率的主要因素:我厂已投运的2套脱硫系统石膏含水率均偏高( 大于10% ) , 影响石膏销售, 影响石膏含水率的主要因素如下:(1) 石膏浆液中杂质过多。
杂质主要指飞灰、燃油残留物以及石灰石中带来的杂质(黄土)等, 这些杂质干扰了吸收塔内化学反应的正常进行, 影响了石膏的结晶和大颗粒石膏晶体的生成; 另一方面杂质夹在石膏晶体之间, 堵塞了游离水在石膏晶体之间的通道, 使石膏脱水变得困难。
(2) 石膏浆液中CaCO3 或CaSO3·H2O 过多。
这是吸收塔内pH 值控制不好以及氧化不充分所致。
若pH 值过高, 则CaCO3的作用量就会增加, 一方面导致浆液品质恶化脱水困难, 一方面又不经济。
脱硫石膏含水率高的原因分析及对策

脱硫石膏含水率高的原因分析及对策发布时间:2022-05-13T02:16:36.305Z 来源:《中国电业与能源》2022年2月3期作者:王浩吴香[导读] 石灰石-石膏湿法脱硫技术在电站锅炉系统应用较为普遍,但随着脱硫系统运行时间长,脱硫石膏产品质量出现含水率偏高的问题王浩吴香中韩(武汉)石油化工有限公司湖北省武汉市 430000摘要:石灰石-石膏湿法脱硫技术在电站锅炉系统应用较为普遍,但随着脱硫系统运行时间长,脱硫石膏产品质量出现含水率偏高的问题,本文针对脱硫石膏含水率高的现象,确定影响因素,运用变量分析方法,实施相关对策,取得了显著的效果,使脱硫石膏的含水率达标。
关键词:脱硫石膏;含水率;影响因素;对策1引言某装置脱硫系统采用石灰石——石膏湿法脱硫工艺,其副产品为石膏。
自2018年1月份起副产品石膏含水率持续偏高,石膏表面出现粘稠状物体,影响到设备的稳定运行,为了解决脱硫石膏含水率高的问题,保障脱硫设备长周期运行,本文通过研究石膏形成的机理,分析影响脱硫石膏含水率的各种因素,提出改善方法,实施了多种处理措施,取得了显著的成效。
2 脱硫石膏形成的机理脱硫石膏是烟气脱硫的主要副产品,烟气随后和泥浆完全相接触处,烟气被泥浆冷却并到达饱和,烟气中的SO2、SO3、HCl、HF等酸性组份被吸附,将脱硫反应产生的亚硫酸钙(CaSO31/2H2O)氧化为石膏(CaSO42H2O)。
吸收塔浆池中反应产生的石膏浆液,当吸收塔的石膏泥浆浓度达高设定值,便通过石膏的排出泵送至石膏旋流站,并进入石膏的脱水处理系统。
送到石膏旋流站后完成一级脱水过程。
将石膏旋流站的下溢浓缩液(悬浮物固定比重浓度约为40~50%)借助自重直接送入真空皮带脱水机完成二级脱水,经过调节真空脱水机上的石膏层厚薄以保证脱水特性,从真空皮带上流出的石膏含水率一般不超过百分之十,直接送到石膏库。
3 影响脱硫石膏含水率的因素2018年2月初,某装置石膏品质不合格,含水量偏大问题显著,不能正常拖运。
影响脱硫石膏品质的常见原因

影响脱硫石膏品质得常见原因烟气中灰尘含高。
烟气中得灰尘在脱硫过程会因洗涤而进入浆液中,浆液中得杂质含量高时,不能随着脱水而全部排出,使成品石膏中得杂质含增加,影响石膏品质。
烟气中灰尘含量高得原因主要就是煤质差及电除尘效果差所致,当入口烟气中灰尘含量超标时及时联系锅炉运行检查电除尘运行情况,适当关小增压风机静叶开度,减少进入脱硫得烟气量,待电除尘恢复正常后再恢复脱硫系统得正常运行。
也有可能就是脱水后废水排放少,使吸收塔得杂质越积越多。
吸收塔浆液中亚硫酸钙含量高。
亚硫酸钙含量升高得主要原因就是氧化不充分引起得,正常情况下由于烟气中含氧量低(4%~8%左右),锅炉燃烧后产生得烟气中得硫氧化物主要就是二氧化硫,在脱硫过程中浆液吸收二氧化硫而生成亚硫酸钙,脱硫系统通过氧化风机向吸收塔补充空气,强制氧化亚硫酸钙生成硫酸钙,硫酸钙与2个水分子结合生成石膏分子,当石膏达到一定饱与程度后结晶析出,经脱水后产生成品石膏。
而由于种种原因不能使亚硫酸钙得到充分氧化时(原因包括氧化空气流量不够;氧化空气压力达不到要求;吸收塔搅拌器搅拌效果不佳等),浆液中亚硫酸钙得含量就会升高,最终使成品石膏品质下降,同时会造成脱水效果差、脱硫系统脱硫效率差、石灰石消耗量增加等一系列不良影响。
此时要检查氧化风机运行情况(压力、电流、流量等),氧化空气母管就是否有漏气现象,必要时适当减少进烟量;也可以排出一部分吸收塔浆液,增加新鲜水,待吸收塔内浆液品质改善后再恢复正常运行。
吸收塔浆液中碳酸钙含量高、碳酸钙作为脱硫得吸收剂,在脱硫系统运行过程中要不断得补充,为了保证脱硫效果,吸收塔内要保持一定得PH值,有时PH值保持较高,这样浆液中得碳酸钙含量就会较高;也有可能石灰石活性较差,石灰石浆液补充到吸收塔内后,在短时间内不能充分电离,也就不能与二氧化硫发生反应,最终会随脱水而进入石膏中。
这两种情况也会影响石膏品质。
运行中要适当控制PH 值,兼顾脱率效果与石膏品质,同时要注意石灰石浆液得补充量,当补充大量石灰石而PH上升不明显时有可能就是石灰石活性差,必须要让石灰石有充分得时间在吸收塔内电离。
#2脱硫石膏含水量大的原因及解决办法

#2脱硫石膏含水量大的原因及解决办法摘要:针对火电厂湿法脱硫系统,结合实例,对可能造成石膏脱水困难的常见因素进行了分析。
结果表明,石膏脱水系统运行情况的优劣直接影响石膏脱水效果,且原烟气SO2浓度和飞灰含量,脱硫系统反应条件,吸收塔系统运行状况,废水处理系统设备的运行状况,石灰石浆液品质等均影响石膏脱水效果。
关键词:湿法烟气脱硫 SO2 吸收塔系统石膏脱水引言:湿法石灰石-石膏烟气脱硫工艺中,石灰石浆液在吸收塔内对烟气进行逆流洗涤,生成半水亚硫酸钙并以小颗粒状转移到浆液中,利用空气将其强制氧化生成二水硫酸钙(CaSO4•2H2O)结晶。
用石膏排出泵将吸收塔内的浆液抽出,送往石膏旋流器,进行浓缩及颗粒分级,稀的溢流(细颗粒)返回吸收塔;浓缩的底流(较粗颗粒)送往真空皮带机进行石膏脱水。
脱水后的石膏含水率控制在10%以下。
若石膏水分过高,不仅影响脱硫系统和设备的正常运行,而且对石膏的储存、运输及后加工等都会造成一定的困难。
2017年4月份我厂#2脱硫系统吸收塔密度缓慢升高,并伴有起泡现象,启动脱水系统后发现#1、2脱水机脱水效果均差,石膏含水量大、不成形。
(二)分析历史数据可得:1、#2吸收塔密度1090-1178Kg/m³,因此不存在密度低导致脱水差的情况。
检查并冲洗氧化空气管道未发现堵塞且氧化空气压力在45—55KPa间,氧化风机运行正常。
2、吸收塔液的pH测量值在4.9-5.6间,运行中不存在吸收塔浆液PH异常情况。
3、#2吸收塔入口烟气粉尘含量19-25mg/m³间,吸收塔入口粉尘在正常范围之内。
4、#2脱硫原烟气SO2浓度在300-500mg/m³间,未超过FGD系统的设计值849mg/m³,且未发生大幅度波动。
5、#2脱硫石膏旋流器压力在200-300KPa间,停运#2吸收塔石膏排出泵后检查旋流器旋流子无结垢、堵塞现象,检查无明显异常情况。
(二)分析化验单数据可得:1、石灰石品质未达到要求:四月份随机取样化验石灰石17车次,合格5车次;石灰石中碳酸钙含量偏低(要求大于91%),碳酸钙含量最低值72.06%,;氧化镁含量偏高(要求小于2%),氧化镁最大值9.92%。
- 1、下载文档前请自行甄别文档内容的完整性,平台不提供额外的编辑、内容补充、找答案等附加服务。
- 2、"仅部分预览"的文档,不可在线预览部分如存在完整性等问题,可反馈申请退款(可完整预览的文档不适用该条件!)。
- 3、如文档侵犯您的权益,请联系客服反馈,我们会尽快为您处理(人工客服工作时间:9:00-18:30)。
脱硫运行中石膏含水量大的原因分析及解决办法
湿法石灰石-石膏烟气脱硫工艺中,石灰石浆液在吸收塔内对烟气进行逆流洗涤,生成半水亚硫酸钙并以小颗粒状转移到浆液中,利用空气将其强制氧化生成二水硫酸钙(CaSO4·2H2O)结晶。
用石膏排出泵将吸收塔内的浆液抽出,送往石膏旋流器,进行浓缩及颗粒分级,稀的溢流(细颗粒)返回吸收塔;浓缩的底流(较粗颗粒)送往真空皮带机进行石膏脱水。
脱水后的石膏含水率一般控制在10%(质量含量)以下,为达标。
若石膏水分过高,不仅影响脱硫系统和设备的正常运行,而且对石膏的储存、运输及后加工等都会造成一定的困难。
下面就脱硫石膏含水量大原因以及解决办法与各位交流一下。
1、造成脱硫石膏含水量大原因分析如下。
1、吸收塔内浆液的密度偏小,启动石膏排出泵。
2、吸收塔液的pH测量值不达标。
3、氯离子含量超标。
4、脱硫塔入口含尘量偏高,导致吸收塔浆液“中毒”。
5、石灰石品质发生变化。
6.入炉煤含硫量突然发生变化,超设计值较多。
7、石膏旋流器发生异常。
8、真空皮带机异常
9、氧化空气量不足。
1.1、吸收塔内浆液的密度直观地反映塔内反应物的浓度(固体含量)高低,密度值升高,浆液的固体含量增加。
工艺设计中在石膏排出泵出口管道上安装石膏浆液密度表,运行中根据该密度值的高低来自动控制石膏浆液的排放。
石膏浆液密度设定值根据反应产物—石膏形成和结晶情况来确定,一般要求是形成大颗粒易脱水的石膏晶体,运行过程中根据浆液性质的不同,设定值有所不同,一般控制在1180~1200之间,固体含量在10%左右。
假如,排出的石膏浆液固体含量偏低,即密度较小石膏浆液未达到饱和或过饱和度较低,形成的石膏晶体颗粒细小,石膏难以脱水。
1.2、吸收塔液的pH测量值是参与反应控制的一个重要参数,用于确定需要输送到烟气脱硫吸收塔的新鲜反应浆液的流量。
pH值升高,新的反应浆液供应量将减少,反之,pH值降低,新的反应浆液供应量将增加。
若pH计测量不准,则需要添加的石灰石量就不能准确控制,而过量的石灰石使石膏纯度降低,造成石膏脱水困难。
1.3、原烟气进入吸收塔与石灰石浆液接触脱除SO2的同时,烟气中HCI、HF和飞灰以及石灰石中的杂质都会进入吸收塔浆液中,长期运行后吸收塔浆液的氯离子和飞灰中不断溶出的一些金属离子浓度会逐渐升高,不断增加的氯根和重金属离子浓度对吸收塔内SO2去除以及石膏晶体的形成产生不利的影响,并且过量氯离子将大量吸收Ca2+,增加石灰石的消耗。
因此,为保证塔内化学反应的正常进行,运行中从浆液中排出一定量废水是非常重要。
浆液中Cl-浓度及杂质含量升高改变了浆液的理化性质,影响了塔内化学反应的正常进行和
石膏的结晶体的长大,同时杂质夹杂在石膏结晶之间,堵塞了游离水在结晶之间的通道,使石膏脱水变得困难。
1.4、原烟气的飞灰进入吸收塔在一定程度上原烟气中的飞灰进入吸收塔浆液中在一定程度上阻碍了SO2与脱硫剂的接触,降低了石灰石中Ca2+的溶解速率,同时飞灰中不断溶出的一些重金属如Hg、Mg、Cd、Zn等离子会抑制Ca2+与HSO3-的反应,“封闭”了吸收剂的活性。
一般要求吸收塔入口的烟尘含量不能超过200mg/m3,如果超过300 mg/m3以上就容易出现这种现象。
由于除尘器效率不是很好,吸收塔变成了吸尘器,吸收塔浆液发黑,起泡,脱水时在石膏表明有一层黑色物质,在这种状况下再坚持运行可想而知。
吸收塔浆液极易“中毒”。
一旦发生“中毒”现象,就需要将浆液全部排出置换新鲜的浆液,造成很大的浪费,并影响脱硫系统的正常投入。
吸收塔浆液“中毒”后,需要近半月时间纠正才能彻底改善,在此期间会浪费大量石灰石粉,排放大量浆液,提高了运行成本。
1.5、石灰石品质发生变化。
石灰石粉的品质是影响脱硫运行的一个重要因素,其中碳酸钙含量及细度是关键,杂质增多或含量下降都会使浆液品质恶化,细度越细反应效果就越好。
这就可能出现当碳酸钙含量及成品的细度发生较大变化时,其反应活性降低,极可能发生供浆过量,此时塔内浆液中含CaCO3量增大,由石灰石颗粒易粘结在一起,导致造成脱水困难现象的发生。
另外如果石灰石原料中夹带黏土、泥沙等杂质,这些杂质
状态不稳定,也会在一定程度上造成脱水困难的现象发生。
一般要求入厂石灰石含量要求在90%以上。
1.6、入炉煤含硫量突然增大,导致吸收塔入口SO2浓度增大较大,而鼓入吸收塔的氧化空气量并未随之增加,特别当SO2浓度超过设计值,氧化风量也是无法改变,由于严重氧化不足,溶液中可溶性亚硫酸盐浓度增大将抑制CaCO3生成,可溶性亚硫酸盐结晶即CaSO3·1/2H2O晶体,该物质是层状或针状晶体,尤其是针状晶体,形成的石膏颗粒小,粘性大,容易吸附在真空皮带机上,增加脱水的难度。
1.7、石膏旋流器出口固体含量一般40-45%,发现内部堵塞及时处理,一般内部结垢以及沉沙嘴磨损超一般及时进行更换,注意监视控制入口压力值,否则旋流器分离效果较差,进入真空皮带机含水量加大,导致脱水困难,石膏相应含水量加大。
1.8、真空皮带机是石膏二次脱水的重要设备,脱水效果与浆液的性质、滤布的清洁程度有较大的关系。
汽液分离器的表计直观地反映了皮带机的真空,真空皮带机的真空与石膏含水率呈有规律的变化,皮带机真空升高,反映出滤水通过滤布时的压降增加,反应出石膏含水率增大。
其增加的原因,一是脱水设备运行不正常,如滤布冲洗不干净或滤布使用周期过长都会使皮带机脱水效果变差,脱水不畅;二是石膏浆液本身性质的变化,如浆液中小颗粒石膏晶体增多或浆液中的杂质含量增加等引起滤布过滤通道的堵塞,使浆液中的水不容易从滤布孔隙分离出来。
若要达到一定的固液分离效果,必须使真空升高。
2、解决办法
2.1、注意控制吸收塔内浆液密度,如密度计怀疑不准确,可以参照浆液循环泵正常时电流值,也可人工进行手动测量,注意必须保持密度达到规定时,方可启动石膏排出泵。
2.2、保持PH值在5.0—5.5之间,防止过高或过低。
过低可能造成脱硫效率的降低、腐蚀性加强,过高浆液中未反应的石灰石量增多,两种情况都不利于运行稳定。
2.3、加强废水排放,控制吸收塔内CL-含量在10000ppm以下不超标。
2.4、需要对加强对电除尘、布袋除尘器全面检查,分别查看各个高压柜的二次电流是否在合适的范围内。
在此提一点,如果发现高压柜全部在投,且电压正常,但效果还是较差时,就要对现在常用的顶部电磁振打进行检查,振打好坏,频率如何都是关键。
再一个是灰斗阳极振打,要保证定时振打,确保下灰顺畅;布袋除尘器注意差压变化。
2.5 严密监督石灰石质量。
对此制定严格的管理制定,确保车车化验,严格考核。
日常积极与供货厂家沟通,让厂家清楚脱硫生产过程,明白脱硫的重要性及严肃性,加强前期管理。
2.6 降低燃煤含硫量大的问题,积极协调燃料配煤。
通过厂内管理系统,及时指导其配煤工作,确保按脱硫运行中的烟气含硫量在设计值之内。
但长时间还是以降低采购合格含硫量的燃煤为根本。
2.7 加强对石膏旋流器的监控及维修
对于石膏旋流站的操作并不多,除了调整压力定期清理内部结垢以外并没有太多手段。
日常要加强检查底流口液体流出的状态,根据经验判断,当沉砂嘴喷出的为雾状时效果为最佳,接近直流时效果已经变差,此时可以考虑更换沉砂嘴。
也可以测量一下,旋流后达不到40-50%的脱水效果就要考虑更换旋流器了。
再者就是停运后增加冲洗时间,防止浆液在旋流子中沉淀结垢。
2.8 保持真空皮带机的最佳工作状态
皮带机的问题也就是关注滤布的状况,当被油污染后也会影响脱水效果,也就是锅炉投油时尽量退出脱硫运行。
另外保持稳定的滤布冲洗水压力,调整合理的皮带转速,发现真空异常时及时清理真空罐中的杂物等等。
2.9 提高浆液氧化程度
同样浆液高度,若发现氧化风机电流升高,估计氧化风管结垢已经结垢严重,在吸收塔检修的过程中要对氧化风管进行清垢处理。
另外、保持仪表准确程度是脱硫运行的关键,运行人员要加强对运行参数的监测分析,发现不正常时应查找原因,及时调整,防止多参数发生变化,给问题的处理造成困难。
现对我公司目前#6机组脱硫石膏含水量大,针对以上逐条进行排查发现如下问题:
1、#6炉PH值一直保持较低4.2-4.5,由于前一段时期,入炉煤参配出现问题导致进入脱硫塔硫浓度超标严重,氧化风量不足,导致内部生成大量亚硫酸钙,现仍无排出完毕。
2、#6炉氯离子浓度严重超标,现测量为17000ppmm,以前可能更高。
3、三台石膏旋流器存在内部堵塞以及沉砂嘴磨损问题,旋流器出口含水量偏大。
4、入厂石灰石含量偏低
5、#5炉除尘器效果较差,两个电场不能运行。
6、#6炉电除尘器阳极振打有问题。
7、现场脱硫密度计故障时间较长,不能为运行人员提供可靠德监视手段。
现紧急处理方法:1、#6炉加紧换浆液,提高PH值含量,降低氯离子浓度。
2、尽快清理石膏旋流器。
3、注意参配煤,保证入炉硫含量不超标。