数控车床的对刀与刀具补偿(附图)
项目二数控车床对刀操作课件
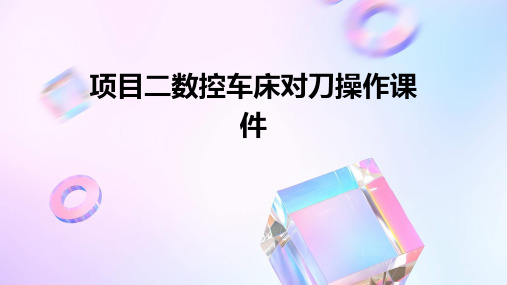
目录
• 对刀操作的基本概念 • 对刀操作的步骤 • 对刀操作的注意事项 • 对刀操作的应用实例 • 对刀操作常见问题及解决方案
01
对刀操作的基本概念
对刀操作的定义
对刀操作是指在数控车床上,通过调整刀具相对于工件的位 置,使刀具的刀位点对准工件坐标系的某一参考点,以确保 加工过程中刀具与工件正确对齐的过程。
2. 使用减震装置或工具夹具等辅助工具 ,减小振动传递;
详细描述:切削振动的原因有多种,如 工件材料硬度过高等。为了解决这一问 题,可以采取以下措施
1. 调整主轴转速和切削深度等参数,以 改变切削力的变化规律,减少振动;
加工精度问题及解决方案
总结词:加工精度问题是对刀操作中的核心问题之一, 它直接影响到工件的质量和性能。 1. 选用高精度刀具和夹具,提高对刀精度;
总结词
异形零件的形状各异,对刀操作需要根据零件的具体形状进行调整。
详细描述
在异形零件的对刀操作中,需要仔细观察工件的形状,并根据需要进行调整。对于某些具有特殊形状的零件,可 能需要采用特殊的对刀方法,以确保加工精度和表面质量。同时,还需要特别注意安全问题,以避免因操作不当 而造成意外事故。
05
对刀操作常见问题及解决 方案
刀具安装
将刀具正确安装在刀架上 ,确保刀具夹紧牢固,不 会松动。
刀具调整
调整刀具的角度、高度和 偏移量,以适应加工需求 。
刀具补偿参数设置
刀具长度补偿
根据刀具的实际长度,设 置刀具长度补偿参数,确 保加工过程中的切深与编 程深度一致。
刀具半径补偿
根据刀具的实际半径,设 置刀具半径补偿参数,确 保加工出的工件轮廓与编 程轮廓一致。
数控车床刀具补偿指令编程及刀偏值设定
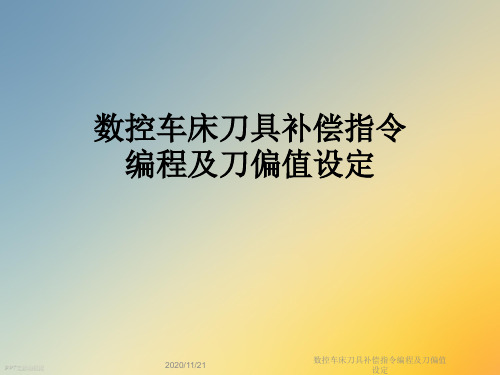
2.刀具位置补偿基准 设定与补偿方式(6)
PPT文档演模板
数控车床刀具补偿指令编程及刀偏值 设定
PPT文档演模板
3.刀具位置补偿类型
•刀具位置补偿可分为 刀具几何形状补偿(G) 和 刀 具 磨 损 补 偿 (W) 两种,需分别加以设 定。刀具几何形状补 偿实际上包括刀具形 状几何偏移补偿和刀 具安装位置几何偏移 补偿,而刀具磨损偏 移补偿用于补偿刀尖 磨损,如图所示。
PPT文档演模板
数控车床刀具补偿指令编程及刀偏值 设定
6.刀具几何偏移动作 (4)
PPT文档演模板
数控车床刀具补偿指令编程及刀偏值 设定
PPT文档演模板
三、刀尖圆弧半径补偿
数控车床刀具补偿指令编程及刀偏值 设定
1.理想刀具和实际刀具(1)
•理想刀具是具有理想刀尖A的刀具。但实际 使用的刀具,在切削加工中,为了提高刀尖 强度,降低加工表面粗糙度,通常在车刀刀 尖处制有一圆弧过渡刃;一般的不重磨刀片 刀尖处均呈圆弧过渡,且有一定的半径值; 即使是专门刃磨的“尖刀”,其实际状态还 是有一定的圆弧倒角,不可能绝对是尖角。 因此,实际上真正的刀尖是不存在的,这里 所说的刀尖只是一“假想刀尖”。
位置时,刀尖位置B相对标刀刀尖位置A就会
出现偏置,原来建立的坐标系就不再适用,
因此应对非标刀具相对于标准刀具之间的偏
置值Δx、Δz进行补偿,使刀尖位置B移至位
置A。标准刀具偏置值为机床回到机床零点时,
工件坐标系零点相对于工作位上标准刀具刀
尖位置的有向距离。
PPT文档演模板
数控车床刀具补偿指令编程及刀偏值 设定
数控车床刀具补偿指令 编程及刀偏值设定
PPT文档演模板
2020/11/21
华中世纪星数控车床对刀及刀补值的设置方法
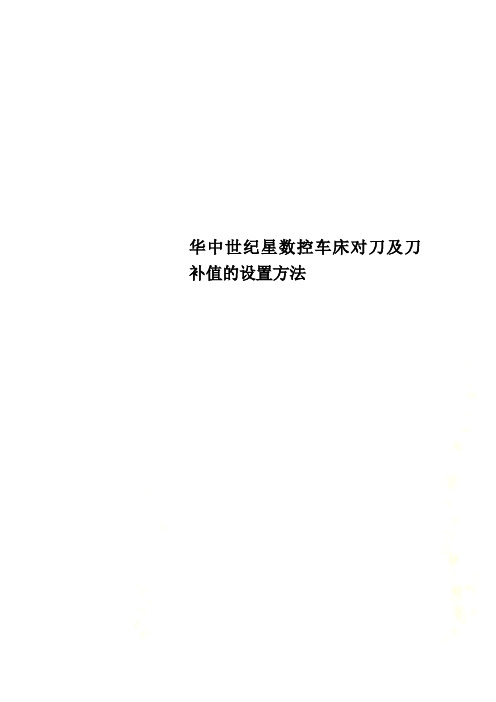
华中世纪星数控车床对刀及刀补值的设置方法华中世纪星数控车床对刀及刀补值的设置方法1. 刀具补偿值设置(F4)在主操作界面下,按F4键进入刀具补偿功能子菜单。
命令行与菜单条的显示如图1-9所示。
图1-9 刀具补偿功能主菜单刀具补偿分为刀具的几何补偿和刀具的半径补偿。
T代码指定刀具的几何补偿(偏置补偿与磨损补偿之和),其后的4位数字分别表示选择的刀具号(前两位数字)和刀具偏置补偿号(后两位数字)。
补偿号可以和刀具号相同,也可以不同,即一把刀具可以对应多个补偿号(值)。
刀具补偿号为00表示补偿量为0,即取消补偿功能。
G40、G41、G42指定刀具的半径补偿。
(1)刀偏数据设置(F4→F1)刀具的几何补偿包括刀具的偏置补偿和刀具的磨损补偿,刀具的偏置补偿有绝对刀具偏置补偿和相对刀具偏置补偿两种形式。
我们推荐采用绝对刀具偏置补偿。
在主操作界面下,按F4→F1进入刀具偏置编辑画面如图1-10所示。
图1-10 刀具偏置编辑车床编程轨迹实际上是刀尖的运动轨迹,但实际中不同的刀具的几何尺寸、安装位置各不相同,其刀尖点相对于刀架中心的位置也就不同。
因此需要将各刀具刀尖点的位置值进行测量设定,以便系统在加工时对刀具偏置值进行补偿。
我们采用试切法来设置绝对刀具偏置补偿值。
图1-11 绝对刀偏法刀具偏置补偿值如图1-11所示,刀具偏置值即机床回到机床零点时,刀架工作位上各刀刀尖位置相对工件零点的有向距离。
当执行刀具偏置补偿时,各刀以此值设定各自的工件坐标系。
机床到达机床零点时,机床坐标值显示均为零,整个刀架上的点可考虑为一理想点,故当各刀对刀时,机床零点可视为在各刀刀位点上。
我们通过输入试切直径、长度值,自动计算工件零点相对与各刀刀位点的距离。
其步骤如下:①用光标键将蓝色亮条移动到要设置刀具偏置值的行。
②用刀具试切工件的外径,然后沿Z轴方向退刀,在此过程中不要移动X轴。
③测量试切后的工件外径,如为ф25.26 ,然后将此值输入到刀偏表中“#××01”一行中“试切直径”一栏中并确认,设置好X偏置。
数控车床操作之数控车对刀与刀补PPT课件(35页)

• 刀位点:
• 刀位点是表示刀具特征的点,一般是刀具上的 一点。
刀尖点 • 尖形车刀的刀位点为假想
,园
形车刀的刀位点为园相对工件运动的起点,即加工 程序开始时刀具刀尖点的起始位置,经常也 把它作为加工程序的终点。
(3)对刀点:
• 对刀点是用来确定刀具与工件的相对位置 关系的点.是确定工件坐标系与机床坐标系 关系的点。
• 式中:X、 Z:快速点定位的终点绝对坐标值。
• U、W :快速定位终点相对于起点(上一点)的
位移量相对坐标值
2、直线插补指令:
• 控制刀具在坐标轴间以插补联动方式按指定进 给速度做任意斜率的直线运动.
• 指令格式: G01 X Z F_ ;
•
G01 U W F_ ;
• 式中:X、 Z:直线插补的终点坐标值。
后续课程安排:
• 仿真机房:数控车床对刀仿真操作
•
1.后现代社会以大众文化的兴起为特 征,而 大众文 化要求 文化的 大众消 费性质 ,图像 以强有 力的视 觉冲击 力成为 实现大 众消费 的主要 途径。
•
2.传统意义上的书籍,没有图像的填 充就被 边缘化 ,纯文 学也只 有借助 图像才 能走向 市场中 心、大 众视野 ,充斥 市场的 总是图 文并茂 的大众 读物, 这就形 成了当 下对文 学的消 费由读 字到读 图的转 变。
•
3.当然,文学毕竟是图像无法取代的 ,人类 文明的 传播方 式从图 像过渡 到文学 ,就是 因为文 字的抽 象描述 、概括 能力是 超越图 像的。 文字通 过语言 唤起人 脑中的 想象, 其魅力 在于建 构一个 内视形 象,这 种内视 审美是 文学独 有的, 语言艺 术独有 的。
•
4.文学独特的“味外之旨”、“韵外 之致” ,其丰 富性和 多重意 义,依 靠图像 是永远 无法接 近的。 图像的 直观性 正好切 断了这 种对文 字魅力 的省思 和想象 。
数控机床怎么对刀【图解】
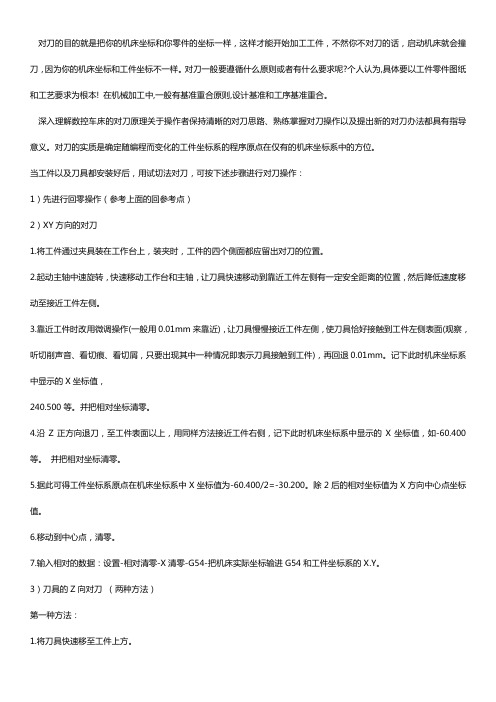
对刀的目的就是把你的机床坐标和你零件的坐标一样,这样才能开始加工工件,不然你不对刀的话,启动机床就会撞刀,因为你的机床坐标和工件坐标不一样。
对刀一般要遵循什么原则或者有什么要求呢?个人认为,具体要以工件零件图纸和工艺要求为根本! 在机械加工中,一般有基准重合原则,设计基准和工序基准重合。
深入理解数控车床的对刀原理关于操作者保持清晰的对刀思路、熟练掌握对刀操作以及提出新的对刀办法都具有指导意义。
对刀的实质是确定随编程而变化的工件坐标系的程序原点在仅有的机床坐标系中的方位。
当工件以及刀具都安装好后,用试切法对刀,可按下述步骤进行对刀操作:1)先进行回零操作(参考上面的回参考点)2)XY方向的对刀1.将工件通过夹具装在工作台上,装夹时,工件的四个侧面都应留出对刀的位置。
2.起动主轴中速旋转,快速移动工作台和主轴,让刀具快速移动到靠近工件左侧有一定安全距离的位置,然后降低速度移动至接近工件左侧。
3.靠近工件时改用微调操作(一般用0.01mm来靠近),让刀具慢慢接近工件左侧,使刀具恰好接触到工件左侧表面(观察,听切削声音、看切痕、看切屑,只要出现其中一种情况即表示刀具接触到工件),再回退0.01mm。
记下此时机床坐标系中显示的X坐标值,240.500等。
并把相对坐标清零。
4.沿Z正方向退刀,至工件表面以上,用同样方法接近工件右侧,记下此时机床坐标系中显示的X坐标值,如-60.400等。
并把相对坐标清零。
5.据此可得工件坐标系原点在机床坐标系中X坐标值为-60.400/2=-30.200。
除2后的相对坐标值为X方向中心点坐标值。
6.移动到中心点,清零。
7.输入相对的数据:设置-相对清零-X清零-G54-把机床实际坐标输进G54和工件坐标系的X.Y。
3)刀具的Z向对刀(两种方法)第一种方法:1.将刀具快速移至工件上方。
2.起动主轴中速旋转,移动工作台和主轴,让刀具移动到靠近工件上表面有一定安全距离的位置,然后降低速度移动让刀具端面接近工件上表面.3.靠近工件时改用微调操作(一般用0.01mm来靠近),让刀具端面慢慢接近工件表面,使刀具端面恰好碰到工件上表面,再将Z轴再抬高0.01mm,记下此时机床坐标系中的Z值,如-140.400等,则机床坐标系中的Z坐标值为-140.400。
刀具补偿功能

图3-50假想刀尖位置序号
第十节 刀具补偿功能 图3-51 数控车床假想刀尖位置
第十节 刀具补偿功能 例题 如图所示,运用刀具半径补偿指令编程。
如图在对刀时,确定一把刀为标准刀具,并以其刀尖 位置A为依据通过对刀,输入刀偏值建立坐标系。
这样,当其它各刀转到加工位置时, 刀尖位置B相对标刀刀尖位置A就 会出现偏置,原来建立的坐标系 就不再适用。因此应对非标刀具 相对于标准刀具之间的偏置值 △x、△z 进行补偿。使刀尖位置B移至位置A。标刀偏置值为 机床回到机床零点时,工件坐标系零点相对于工作位上标刀刀 尖位置的有向距离。
③ G41、G42、G40指令应在G00、G01程序段中加入。 ④ 在补偿状态下,没有移动的程序段(M指令、主轴功能 等),不能在连续2个以上的程序段中指定,否则会造成过 切或欠切。 ⑤ 在补偿启动段或补偿状态下,不得指定移动距离为0的 G00、G01等指令。
第十节 刀具补偿功能 ⑥ 在G40刀尖圆弧半径补偿取消段,也必须同时有X、Z两个 轴方向的位移。
第十节 刀具补偿功能
(2) 绝对补偿形式 即机床回到机床零点时,
工件坐标系零点,相对于刀 架工作位上各刀刀尖位置的 有向距离。当执行刀偏补偿 时,各刀以此值设定各自的 加工坐标系。见右图所示。
第十节 刀具补偿功能 1.在数控车床的实际加工中,我们对刀时采用什么样的 补偿形式,对刀具偏置进行补偿的呢? 2.如何对刀,输入偏置值? 回顾对刀过程,观看视频录像
第十节 刀具补偿功能
三、刀尖圆弧半径补偿G40、G41、G42 在编程时,通常将车刀刀尖作为一点考虑(即假想刀 尖位置),但实际上刀尖部分是带有圆角的(如图3-47 所示) 。编程时所指定的刀具轨迹就是假想刀尖的轨迹。
华中数控对刀过程(配图版)

华中数控对刀过程(配图版)1、开机。
(总电源总闸,机床后侧电闸)2、机械回零。
(开机必须回零,否则运行程序时会报警)方法:预先用手轮将刀具停放在工件的中心正上方略高位置,按[回参考点]→按[+Z]→按[+X]→按[+Y]→机床一般会先快递再慢速接近回零位置→耐心等待[+Z][+X][+Y]零点灯全部亮起则完成回零工作。
3、对刀:2)同样方法对Y轴:碰后侧Y清零,碰前侧读数,移至除2处,再将Y清零。
3)对Z轴:第一步:[增量]灯亮用手轮将铣刀下移贴住工件上表面。
第二步:Z相对坐标清零确定。
4)G54抄数:按[坐标系设定F1]→[G54坐标系F1]→进入自动坐标系G54画面。
在坐标值中输入机床坐标系中的XYZ数值后enter回车。
5)G54确定。
按两次[返回F10]进入主菜单画面。
按[MDI F3]进入“MDI运行画面”。
按[单段]按钮灯亮,在“MDI运行”中输入“G54”按循环启动按钮。
则对刀完成。
此时可按[返回F10]进入主菜单画面,再[显示切换F10],观察机床现在的机床坐标全部变成0。
如下图所示:6)对刀校验。
第一步,用手轮摇开铣刀(随意远离位置)。
第二步,在主菜单画面。
按[MDI F3]进入“MDI运行画面”。
按[单段]按钮灯亮,在“MDI运行”中输入“G1X0Y0F500”按循环启动按钮。
按[循环启动]。
这时刀具就会自动定位至工件中心正上方。
再输入Z6,按[循环启动],停下主轴,用φ6通过一下。
看Z位置是否相符。
华中数控超程解除的方法:华中数控的Z轴行程开关很低,所以Z轴较易超程。
华中数控,机床超程后,会出现“急停”字样。
解决方法是:按[超程解除]键,等“急停”字样变成“复位”后,按住的[超程解除]键同时,转换成手动状态,再同时按住[起程解除]键和方向键(如-Z),直到超程解除。
超程后不需重新对刀,刀具的坐标位置是正确的。
关机,再开机也不需要重新对刀。
我校的华中数控存在的问题:1、面铣程序不可以走圆角,否则程序校验时出错一般显示为“XX行圆弧数据错”。
数控机床补偿功能

三、铣刀刀具半径补偿
数控铣床在切削中,由于刀具总有一定的半径,刀具中 心的运动轨迹与加工零件的实际轮廓并不重合。如图所示, 在加工内轮廓时,刀具中心偏离零件内轮廓表面一个刀具半 径值。在加工外轮廓时,刀具中心又偏离零件外轮廓表面一 个刀具半径值。此现象习惯上称为刀具半径补偿。根据ISO 标准,当刀具中心轨迹在编程轨迹前进方向的右侧时,称为 右刀补,用G42表示。反之,称为左刀补,用G41表示。取 消刀尖半径补偿使用G40指令。使用时,编程人员只是在零 件程序中指明补偿要求即可。铣刀刀具半径补偿执行过程分 为刀补建立、刀补进行和刀补撤消三步,刀补仅在指定的两 维坐标平面进行。铣刀半径补偿应注意事项同车刀刀具补偿 要求。
五、数控误差补偿
数控机床在加工时,指令的输入、译码、计 算以及控制电机的运动都是由数控系统统一 控制完成的,从而避免了人为误差。但是, 由于整个加工过程都是自动进行的,人工几 乎不能干预,操作者无法对误差加以补偿, 这就需要数控系统提供各种补偿功能,以便 在加工过程中自动地补偿一些有规律的误差, 提高零件的精度。根据数控机床上加工误差 的主要来源其主要的解决方法如下。
刀具刀尖半径补偿的过程分为三步:刀补 的建立,刀具中心从与编程轨迹重合过渡到 与编程轨迹偏离一个偏置量的过程;刀补进 行,执行有G41、G42指令的程序段后,刀具 中心始终与编程轨迹相距一个偏置量;刀补 的取消,刀具离开工件,刀具中心轨迹要过 渡到与编程重合的过程。如图为刀补的建立 与取消过程。
8.刀尖圆弧半径补偿还与车刀形状、刀尖位 置有关。车刀形状、刀尖位置各种各样,他 们决定加工时刀尖圆弧在工件的什么位置, 所以刀尖圆弧半径包括刀尖圆弧半径、车刀 形状和刀尖位置。车刀形状和刀尖位置共有9 种,如图 所示。车刀形状和刀尖位置分别用 参数L1~L9表示,并通过手工操作在参数设 置方式下输入到系统中。
数控车床对刀方法
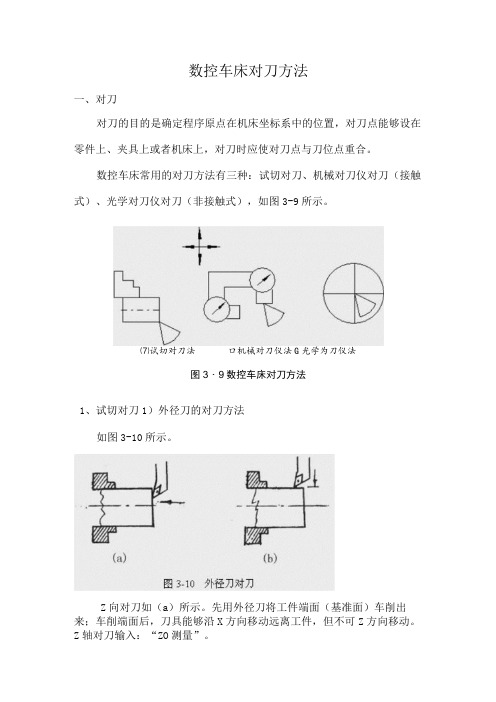
数控车床对刀方法一、对刀对刀的目的是确定程序原点在机床坐标系中的位置,对刀点能够设在零件上、夹具上或者机床上,对刀时应使对刀点与刀位点重合。
数控车床常用的对刀方法有三种:试切对刀、机械对刀仪对刀(接触式)、光学对刀仪对刀(非接触式),如图3-9所示。
⑺试切对刀法口机械对刀仪法G光学为刀仪法图3・9数控车床对刀方法1、试切对刀1)外径刀的对刀方法如图3-10所示。
Z向对刀如(a)所示。
先用外径刀将工件端面(基准面)车削出来;车削端面后,刀具能够沿X方向移动远离工件,但不可Z方向移动。
Z轴对刀输入:“ZO测量”。
X向对刀如(b)所示。
车削任一外径后,使刀具Z向移动远离工件,待主轴停止转动后,测量刚刚车削出来的外径尺寸。
比如,测量值为φ50.78mm,则X轴对刀输入:“X50.78测量2)内孔刀的对刀方法类似外径刀的对刀方法。
Z向对刀内孔车刀轻微接触到己加工好的基准面(端面)后,就不可再作Z向移动。
Z轴对刀输入:“ZO测量X向对刀任意车削一内孔直径后,Z向移动刀具远离工件,停止主轴转动,然后测量已车削好的内径尺寸。
比如,测量值为φ45.56mm,则X轴对刀输入:“X45.56测量”。
3)钻头、中心钻的对刀方法如图3-11所示。
图3J1钻头、中心钻对刀Z向对刀如(a)所示。
钻头(或者中心钻)轻微接触到基准面后,就不可再作Z向移动。
Z轴对刀输入:“ZO测量二X向对刀如(b)所示。
主轴不必转动,以手动方式将钻头沿X轴移动到钻孔中心,即看屏幕显示的机械坐标到“X0.0”为止。
X轴对刀输入:“XO测量二2、机械对刀仪对刀将刀具的刀尖与对刀仪的百分表测头接触,得到两个方向的刀偏量。
有的机床具有刀具探测功能,即通过机床上的对刀仪测头测量刀偏量。
3、光学对刀仪对刀将刀具刀尖对准刀镜的十字线中心,以十字线中心为基准,得到各把刀的刀偏量。
二、刀具补偿值的输入与修改根据刀具的实际参数与位置,将刀尖圆弧半径补偿值与刀具几何磨损补偿值输入到与程序对应的存储位置。
数控车床对刀与偏置、补偿应用 标注版

1.2 数控车床对刀与偏置、补偿应用1.2.1 数控车床坐标系及机床各点a机床零点与参考点不在同一点 b机床零点与参考点在同一点图8-2-1 机床坐标系中的各点1.数控车床原点及机床的坐标系数控车床一般这样规定坐标系:平行主轴线的运动方向取名Z轴方向,横滑座上导轨方向名为X轴方向,且规定刀架离开工件方向为正向。
如图8-2-1a,若数车生产厂把机床坐标零点设在主轴线与卡盘定位面之交点M,则建立了以M为原点的数控车床坐标系。
如图8-2-1b,数车生产厂把机床坐标零点M设在X、Z正向的极限行程点。
2.机床参考点对于增量式测量系统的数控机床,机床厂家设置另一固定的点——机床参考点,机床参考点通常设在X、Z正向的极限行程点,用于标定进给测量系统的测量起点。
机床参考点相对机床零点具有准确坐标值,出厂前由机床厂家精密测量并固化存储在数控装置的内存里。
一些机床将机床参考点和机床原点不设为同一点。
如图8-2-1a,机床参考点在机床坐标系中坐标值为(X600,Z1010)。
一些机床将机床参考点和机床原点设为同一点。
如图8-2-1b,机床参考点在机床坐标系中坐标值为(X0,Z0)。
3.刀架参考点机床坐标系无法直接提供追踪测量刀具相对工件坐标位置的功能,是因为数车生产厂无法预先确定具体工件和刀具的位置。
数车生产厂选择刀架上一定点——刀架参考点,作为机床坐标系直接追踪测量的目标。
刀架参考点用来代表刀架在机床的位置,如图8-2-1中的刀架中心。
4.回参考点操作增量式测量的数控机床开机后,首先要执行回参考点操作,让刀架参考点与机床参考点重合,确立进给测量系统的测量起点及坐标值,然后,机床具有在坐标系上对测量目标的位置测量功能。
若机床将机床参考点和机床原点设为同一点,则起始坐标值为零坐标值,返回参考点操作又称为回零操作。
值得注意的是参考点操作不能让CNC直接测量到刀具刀位点相对工件位置,数控车床坐标系追踪测量的目标是刀架参考点的坐标位置。
试论数控车床对刀(ppt 16页)
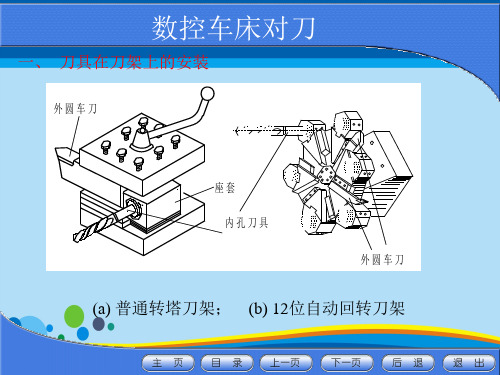
自动对刀又叫刀具检测功能,它是利用数控系统自动、精确地 测量出刀具在两个坐标方向上的长度,并自动修正刀具补偿值,然 后直接开始加工零件。自动对刀是通过刀尖检测系统实现的,如图 所示刀尖随刀架向已经设定了位置的接触式传感器缓缓行进并与之 接触,直到内部电路接通后发出电信号,数控系统立即记下该瞬时 的坐标值,接着将此值与设定值比较,并自动修正刀具补偿值。
928TC数控系统 对刀步骤:
第一步:在手动方式下移动刀具在工件上切出一个小台阶。测量所切出的 台阶的直径,按 I 键,屏幕显示 刀偏 X ,输入测量出的直径值,按 Enter 键
第二步在手动方式下移动刀具在工作上切出一个端面。在Z轴不移动的情况下沿 X方向将刀具移动到安全位置,停止主轴旋转。按 K 键,屏幕显示 刀偏 Z ,输入0 。。。。。。。。。。。。。。
数设定界面,将光标移到与刀位号相对应的位置,输入Xα,按菜单软键[测 量],对应的刀具偏移量自动输入 ;
第二步:试切工件端面,把端面在工件坐标系中Z的坐标值,保持Z轴方向不动, 刀具退出。进入形状补偿参数设定界面,将光标移到相应的位置,输入Z0,按 [测量]软键对应的刀具偏移量自动输入 ;
第三步:按照第一、二步对刀方法,对其余2把刀具进行对刀及设置
2. 对刀仪自动对刀
现在很多车床上都装备了对刀仪,使用对刀仪对刀可免 去测量时产生的误差,大大提高对刀精度。由于使用对刀 仪可以自动计算各把刀的刀长与刀宽的差值,并将其存入 系统中,在加工另外的零件的时候就只需要对标准刀,这 样就大大节约了时间。需要注意的是使用对刀仪对刀一般 都设有标准刀具,在对刀的时候先对标准刀。
不知道自己缺点的人,一辈子都不会想要改善。成功的花,人们只惊慕她现时的明艳!然而当初她的芽儿,浸透了奋斗的泪泉,洒遍了牺牲的血雨。成功的条件在于勇气和 信乃是由健全的思想和健康的体魄而来。成功了自己笑一辈子,不成功被人笑一辈子。成功只有一个理由,失败却有一千种理由。从胜利学得少,从失败学得多。你生而有 前进,形如蝼蚁。你一天的爱心可能带来别人一生的感谢。逆风的方向,更适合飞翔。只有承担起旅途风雨,才能最终守得住彩虹满天只有创造,才是真正的享受,只有拚 活。知识玩转财富。志不立,天下无可成之事。竹笋虽然柔嫩,但它不怕重压,敢于奋斗、敢于冒尖。阻止你前行的,不是人生道路上的一百块石头,而是你鞋子里的那一 爱,不必呼天抢地,只是相顾无言。最值得欣赏的风景,是自己奋斗的足迹。爱的力量大到可以使人忘记一切,却又小到连一粒嫉妒的沙石也不能容纳。生活不可能像你想 不会像你想的那么糟。时间告诉你什么叫衰老,回忆告诉你什么叫幼稚。不要总在过去的回忆里缠绵,昨天的太阳,晒不干今天的衣裳。实现梦想往往是一个艰苦的坚持的 到位,立竿见影。那些成就卓越的人,几乎都在追求梦想的过程中表现出一种顽强的毅力。世界上唯一不变的字就是“变”字。事实胜于雄辩,百闻不如一见。思路决定出 细节决定成败,性格决定命运虽然你的思维相对于宇宙智慧来说只不过是汪洋中的一滴水,但这滴水却凝聚着海洋的全部财富;是质量上的一而非数量上的一;你的思维拥 所有过不去的都会过去,要对时间有耐心。人总会遇到挫折,总会有低潮,会有不被人理解的时候。如果你希望成功,以恒心为良友,以经验为参谋,以小心为兄弟,以希 个人不知道他要驶向哪个码头,那么任何风都不会是顺风。沙漠里的脚印很快就消逝了。一支支奋进歌却在跋涉者的心中长久激荡。上天完全是为了坚强你的意志,才在道 碍。拥有资源不能成功,善用资源才能成功。小成功靠自己,大成功靠团队。炫耀什么,缺少什么;掩饰什么,自卑什么。所谓正常人,只是自我防御比较好的人。真正的 防而又不受害。学习必须如蜜蜂一样,采过许多花,这才能酿出蜜来态度决定高度。外在压力增加时,就应增强内在的动力。我不是富二代,不能拼爹,但为了成功,我可 站在万人中央成为别人的光。人一辈子不长不短,走着走着,就进了坟墓,你是要轰轰烈烈地风光下葬,还是一把骨灰撒向河流山川。严于自律:不能成为自己本身之主人 他周围任何事物的主人。自律是完全拥有自己的内心并将其导向他所希望的目标的惟一正确的途径。生活对于智者永远是一首昂扬的歌,它的主旋律永远是奋斗。眼泪的存 伤不是一场幻觉。要不断提高自身的能力,才能益己及他。有能力办实事才不会毕竟空谈何益。故事的结束总是满载而归,就是金榜题名。一个人失败的最大原因,是对自 的信心,甚至以为自己必将失败无疑。一个人炫耀什么,说明内心缺少什么。一个人只有在全力以赴的时候才能发挥最大的潜能。我们的能力是有限的,有很多东西飘然于 之外。过去再优美,我们不能住进去;现在再艰险,我们也要走过去!即使行动导致错误,却也带来了学习与成长;不行动则是停滞与萎缩。你的所有不甘和怨气来源于你 你可以平凡,但不能平庸。懦弱的人只会裹足不前,莽撞的人只能引为烧身,只有真正勇敢的人才能所向披靡。平凡的脚步也可以走完伟大的行程。平静的湖面锻炼不出精 生活打造不出生活的强者。人的生命似洪水在奔流,不遇着岛屿、暗礁,难以激起美丽的浪花人生不怕重来,就怕没有将来。人生的成败往往就在于一念之差。人生就像一 为你在看别人耍猴的时候,却不知自己也是猴子中的一员!人生如天气,可预料,但往往出乎意料。人生最大的改变就是去做自己害怕的事情。如果不想被打倒,只有增加 你向神求助,说明你相信神的能力;如果神没有帮助你,说明神相信你的能力。善待自己,不被别人左右,也不去左右别人,自信优雅。活是欺骗不了的,一个人要生活得 象这杯浓酒,不经三番五次的提炼呵,就不会这样一来可口!生命不止需要长度,更需要宽度。时间就像一张网,你撒在哪里,你的收获就在哪里。世上最累人的事,莫过于 你感到痛苦时,就去学习点什么吧,学习可以使我们减缓痛苦。当世界都在说放弃的时候,轻轻的告诉自己:再试一次。过错是暂时的遗憾,而错过则是永远的遗憾!很多 结果,但是不努力却什么改变也没有。后悔是一种耗费精神的情绪后悔是比损失更大的损失,比错误更大的错误所以不要后悔。环境不会改变,解决之道在于改变自己。积 成功者的最基本要素。激情,这是鼓满船帆的风。风有时会把船帆吹断;但没有风,帆船就不能航行。
数控车床对刀的原理及方法之欧阳音创编

一、数控车床对刀的原理:对刀是数控加工中的主要操作和重要技能。
在一定条件下,对刀的精度可以决定零件的加工精度,同时,对刀效率还直接影响数控加工效率。
仅仅知道对刀方法是不够的,还要知道数控系统的各种对刀设置方式,以及这些方式在加工程序中的调用方法,同时要知道各种对刀方式的优缺点、使用条件等。
一般来说,数控加工零件的编程和加工是分开进行的。
数控编程员根据零件的设计图纸,选定一个方便编程的工件坐标系,工件坐标系一般与零件的工艺基准或设计基准重合,在工件坐标系下进行零件加工程序的编制。
对刀时,应使指刀位点与对刀点重合,所谓刀位点是指刀具的定位基准点,对于车刀来说,其刀位点是刀尖。
对刀的目的是确定对刀点,在机床坐标系中的绝对坐标值,测量刀具的刀位偏差值。
对刀点找正的准确度直接影响加工精度。
在实际加工工件时,使用一把刀具一般不能满足工件的加工要求,通常要使用多把刀具进行加工。
在使用多把车刀加工时,在换刀位置不变的情况下,换刀后刀尖点的几何位置将出现差异,这就要求不同的刀具在不同的起始位置开始加工时,都能保证程序正常运行。
为了解决这个问题,机床数控系统配备了刀具几何位置补偿的功能,利用刀具几何位置补偿功能,只要事先把每把刀相对于某一预先选定的基准刀的位置偏差测量出来,输入到数控系统的刀具参数补正栏指定组号里,在加工程序中利用T 指令,即可在刀具轨迹中自动补偿刀具位置偏差。
刀具位置偏差的测量同样也需通过对刀操作来实现。
生产厂家在制造数控车床,必须建立位置测量、控制、显示的统一基准点,该基准点就是机床坐标系原点,也就是机床机械回零后所处的位置。
数控机床所配置的伺服电机有绝对编码器和相对编码器两种,绝对编码器的开机不用回零,系统断电后记忆机床位置,机床零点由参数设定。
相对编码器的开机必须回零,机床零点由机床位置传感器确定。
编程员按工件坐标系中的坐标数据编制的刀具运行轨迹程序,必须在机床坐标系中加工,由于机床原点与工件原点存在X向偏移距离和Z向偏移距离,使得实际的刀尖位置与程序指令的位置有同样的偏移距离,因此,须将该距离测量出来并设置进数控系统,使系统据此调整刀具的运动轨迹,才能加工出符合零件图纸的工件。
- 1、下载文档前请自行甄别文档内容的完整性,平台不提供额外的编辑、内容补充、找答案等附加服务。
- 2、"仅部分预览"的文档,不可在线预览部分如存在完整性等问题,可反馈申请退款(可完整预览的文档不适用该条件!)。
- 3、如文档侵犯您的权益,请联系客服反馈,我们会尽快为您处理(人工客服工作时间:9:00-18:30)。
数控车床的对刀与刀具补偿(附图)
一、对刀
对刀的目的是确定程序原点在机床坐标系中的位置,对刀点可以设在零件上、夹具上或机床上,对刀时应使对刀点与刀位点重合。
数控车床常用的对刀方法有三种:试切对刀、机械对刀仪对刀(接触式)、光学对刀仪对刀(非接触式),如图3-9 所示。
1、试切对刀
1 )外径刀的对刀方法
如图3-10 所示。
Z 向对刀如(a) 所示。
先用外径刀将工件端面( 基准面) 车削出来;车削端面后,刀具可以沿X 方向移动远离工件,但不可Z 方向移动。
Z 轴对刀输入:“Z0 测量”。
X 向对刀如(b) 所示。
车削任一外径后,使刀具Z 向移动远离工件,待主轴停止转动后,测量刚刚车削出来的外径尺寸。
例如,测量值为Φ50.78mm, 则X 轴对刀输入:“X50.78 测量”。
2 )内孔刀的对刀方法
类似外径刀的对刀方法。
Z 向对刀内孔车刀轻微接触到己加工好的基准面(端面)后,就不可再作Z 向移动。
Z 轴对刀输入:“Z0 测量”。
X 向对刀任意车削一内孔直径后,Z 向移动刀具远离工件,停止主轴转动,然后测量已车削好的内径尺寸。
例如,测量值为Φ45.56mm, 则X 轴对刀输入:“X45.56 测量”。
3 )钻头、中心钻的对刀方法
如图3-11 所示。
Z 向对刀如(a )所示。
钻头( 或中心钻) 轻微接触到基准面后,就不可再作Z 向移动。
Z 轴对刀输入:“Z0 测量”。
X 向对刀如(b )所示。
主轴不必转动,以手动方式将钻头沿X 轴移动到钻孔中心,即看屏幕显示的机械坐标到“X0.0 ”为止。
X 轴对刀输入:“X0 测量”。
2、机械对刀仪对刀
将刀具的刀尖与对刀仪的百分表测头接触,得到两个方向的刀偏量。
有的机床具有刀具探测功能,即通过机床上的对刀仪测头测量刀偏量。
3、光学对刀仪对刀
将刀具刀尖对准刀镜的十字线中心,以十字线中心为基准,得到各把刀的刀偏量。
二、刀具补偿值的输入和修改
根据刀具的实际参数和位置,将刀尖圆弧半径补偿值和刀具几何磨损补偿值输入到与程序对应的存储位置。
如试切加工后发现工件尺寸不符合要求时,可根据零件实测尺寸进行刀偏量的修改。
例如测得工件外圆尺寸偏大0.5mm ,可在刀偏量修改状态下,将该刀具的X 方向刀偏量改小0.25mm。