机械制造课程设计报告拨叉
机械制造技术基础课程设计拨叉

《机械制造技术课程设计》说明书设计题目:5-拨叉学生:学号:专业:班级:指导教师:目录一、设计题目-5-拨叉1.1 零件的功用1.2 零件工艺分析二、确定毛坯2.1 确定毛坯制造方法2.2 确定总余量2.3 绘制毛坯图三、制定零件工艺规程3.1 选择表面加工方法3.2 选择定位基准3.3 拟定零件加工工艺路线3.4填写工艺过程卡片3.5 机械加工工序设计四、夹具设计(以13工序夹具为例进行说明)4.1 功能分析与夹具总体结构设计4.2 夹具设计计算4.3 夹具制造与操作说明五、总结六、参考文献一、设计题目-5-拨叉三维图:1.1 零件的功用如图所示的零件,它是车床上的拨叉。
它是车床机构中变速机构的一部分,主要作用是在换挡过程中起作用,换挡之后使主轴在使用者的意图下达到需要的转速。
具体换档过程是通过拨叉拨动滑套与旋转齿轮的啮合实现换挡,从而使车床主轴获得不同的转速。
滑套上有凸块,凸块与旋转齿轮的凹块固连在一起,让齿轮带动滑套,滑套带动输出轴。
控制滑套与不同的齿轮啮合与分离,使输出轴获得不同转速。
1.2 零件工艺分析确定零件的材料为HT200,灰铸铁具有生产工艺简单,铸造性好的特点,但灰铸铁的塑性比较差,脆性高,因此不适合磨削。
以下是拨叉需要加工的表面以及加工表面之间的位置要求。
⑴铸拨叉⑵前端面和后端面⑶左端面和左端面U型台以及右端面⑷上端面和95×24面⑸2×φ5锥型销孔和2×M8螺孔⑹内花键孔⑺M10螺孔⑻M22螺孔⑼42×16槽二、确定毛坯2.1 确定毛坯制造方法零件材料为HT200。
由于拨叉在换挡过程中经常会受到冲击性载荷,采用这种材料零件的强度也能得到保证。
又由于零件成批生产,而且零件的轮廓尺寸不大。
所以选用砂型铸造,采用机械翻砂造型,铸造精度1级,能保证铸件的尺寸要求,从而提高生产率和保证了加工精度。
零件材料HT200,硬度200HBS。
生产类型为成批生产,采用砂型铸造,机械翻砂造型,1级精度。
机械设计工艺学课程设计拨叉
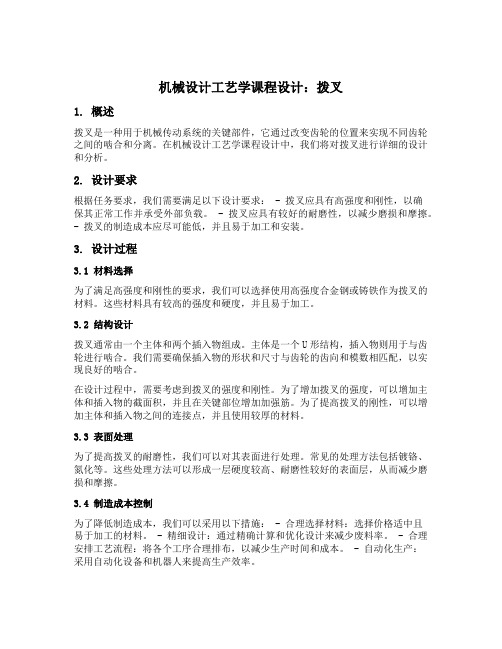
机械设计工艺学课程设计:拨叉1. 概述拨叉是一种用于机械传动系统的关键部件,它通过改变齿轮的位置来实现不同齿轮之间的啮合和分离。
在机械设计工艺学课程设计中,我们将对拨叉进行详细的设计和分析。
2. 设计要求根据任务要求,我们需要满足以下设计要求: - 拨叉应具有高强度和刚性,以确保其正常工作并承受外部负载。
- 拨叉应具有较好的耐磨性,以减少磨损和摩擦。
- 拨叉的制造成本应尽可能低,并且易于加工和安装。
3. 设计过程3.1 材料选择为了满足高强度和刚性的要求,我们可以选择使用高强度合金钢或铸铁作为拨叉的材料。
这些材料具有较高的强度和硬度,并且易于加工。
3.2 结构设计拨叉通常由一个主体和两个插入物组成。
主体是一个U形结构,插入物则用于与齿轮进行啮合。
我们需要确保插入物的形状和尺寸与齿轮的齿向和模数相匹配,以实现良好的啮合。
在设计过程中,需要考虑到拨叉的强度和刚性。
为了增加拨叉的强度,可以增加主体和插入物的截面积,并且在关键部位增加加强筋。
为了提高拨叉的刚性,可以增加主体和插入物之间的连接点,并且使用较厚的材料。
3.3 表面处理为了提高拨叉的耐磨性,我们可以对其表面进行处理。
常见的处理方法包括镀铬、氮化等。
这些处理方法可以形成一层硬度较高、耐磨性较好的表面层,从而减少磨损和摩擦。
3.4 制造成本控制为了降低制造成本,我们可以采用以下措施: - 合理选择材料:选择价格适中且易于加工的材料。
- 精细设计:通过精确计算和优化设计来减少废料率。
- 合理安排工艺流程:将各个工序合理排布,以减少生产时间和成本。
- 自动化生产:采用自动化设备和机器人来提高生产效率。
4. 结论通过本次机械设计工艺学课程设计,我们对拨叉进行了全面的设计和分析。
我们根据设计要求选择了合适的材料,并进行了结构设计、表面处理和制造成本控制。
这些措施可以确保拨叉具有高强度、刚性和耐磨性,并且能够在机械传动系统中正常工作。
拨叉的设计是机械传动系统中不可忽视的一环,它直接影响到整个系统的性能和可靠性。
拨叉完整课程设计
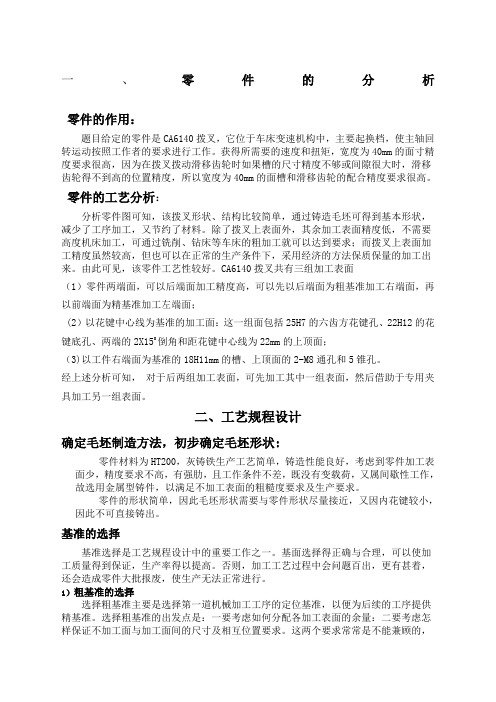
一、零件的分析零件的作用:题目给定的零件是CA6140拨叉,它位于车床变速机构中,主要起换档,使主轴回转运动按照工作者的要求进行工作。
获得所需要的速度和扭矩,宽度为40mm的面寸精度要求很高,因为在拨叉拨动滑移齿轮时如果槽的尺寸精度不够或间隙很大时,滑移齿轮得不到高的位置精度,所以宽度为40mm的面槽和滑移齿轮的配合精度要求很高。
零件的工艺分析:分析零件图可知,该拨叉形状、结构比较简单,通过铸造毛坯可得到基本形状,减少了工序加工,又节约了材料。
除了拨叉上表面外,其余加工表面精度低,不需要高度机床加工,可通过铣削、钻床等车床的粗加工就可以达到要求;而拨叉上表面加工精度虽然较高,但也可以在正常的生产条件下,采用经济的方法保质保量的加工出来。
由此可见,该零件工艺性较好。
CA6140拨叉共有三组加工表面(1)零件两端面,可以后端面加工精度高,可以先以后端面为粗基准加工右端面,再以前端面为精基准加工左端面;(2)以花键中心线为基准的加工面:这一组面包括25H7的六齿方花键孔、22H12的花键底孔、两端的2X150倒角和距花键中心线为22mm的上顶面;(3)以工件右端面为基准的18H11mm的槽、上顶面的2-M8通孔和5锥孔。
经上述分析可知,对于后两组加工表面,可先加工其中一组表面,然后借助于专用夹具加工另一组表面。
二、工艺规程设计确定毛坯制造方法,初步确定毛坯形状:零件材料为HT200,灰铸铁生产工艺简单,铸造性能良好,考虑到零件加工表面少,精度要求不高,有强肋,且工作条件不差,既没有变载荷,又属间歇性工作,故选用金属型铸件,以满足不加工表面的粗糙度要求及生产要求。
零件的形状简单,因此毛坯形状需要与零件形状尽量接近,又因内花键较小,因此不可直接铸出。
基准的选择基准选择是工艺规程设计中的重要工作之一。
基面选择得正确与合理,可以使加工质量得到保证,生产率得以提高。
否则,加工工艺过程中会问题百出,更有甚着,还会造成零件大批报废,使生产无法正常进行。
机械设计课程设计拨叉摘要

机械设计课程设计拨叉摘要一、课程目标知识目标:1. 让学生掌握拨叉的基本结构、工作原理及其在机械设计中的应用。
2. 使学生了解并能够运用拨叉的相关设计参数,如长度、宽度、角度等,进行简单的拨叉设计。
3. 帮助学生理解拨叉材料选择、强度计算、运动稳定性分析等设计要点。
技能目标:1. 培养学生运用CAD软件绘制拨叉零件图的能力。
2. 培养学生根据实际需求,进行拨叉结构设计和修改的能力。
3. 提高学生运用理论知识解决实际工程问题的能力。
情感态度价值观目标:1. 培养学生对机械设计学科的兴趣,激发学生的创新意识和探索精神。
2. 培养学生严谨、细致的工作态度,提高团队合作能力和沟通能力。
3. 增强学生的环保意识,引导学生关注并积极参与绿色机械设计。
本课程旨在结合学生的年级特点和知识水平,通过理论教学与实践操作相结合的方式,使学生掌握拨叉设计的基本知识和技能。
课程注重培养学生的实际操作能力、创新思维和团队协作能力,为今后的学习和工作打下坚实基础。
二、教学内容1. 理论知识:(1)拨叉的基本概念、分类及用途。
(2)拨叉的结构参数、设计原则及材料选择。
(3)拨叉的强度计算、运动稳定性分析及优化方法。
2. 实践操作:(1)运用CAD软件绘制拨叉零件图。
(2)根据设计要求,进行拨叉结构设计和修改。
(3)拨叉设计实例分析与讨论。
3. 教学大纲:第1课时:拨叉基本概念、分类及用途学习。
第2课时:拨叉结构参数、设计原则及材料选择学习。
第3课时:拨叉强度计算、运动稳定性分析及优化方法学习。
第4课时:CAD软件绘制拨叉零件图实践操作。
第5课时:拨叉结构设计与修改实践操作。
第6课时:拨叉设计实例分析与讨论。
教学内容根据课程目标,紧密结合教材章节,注重理论与实践相结合,使学生在掌握拨叉设计基本知识的同时,提高实际操作能力。
在教学过程中,教师可根据学生的实际情况调整进度,确保教学内容的科学性和系统性。
三、教学方法1. 讲授法:用于介绍拨叉的基本概念、分类、用途以及设计原则等理论知识。
机械制造专业课程设计--CA6140拨叉
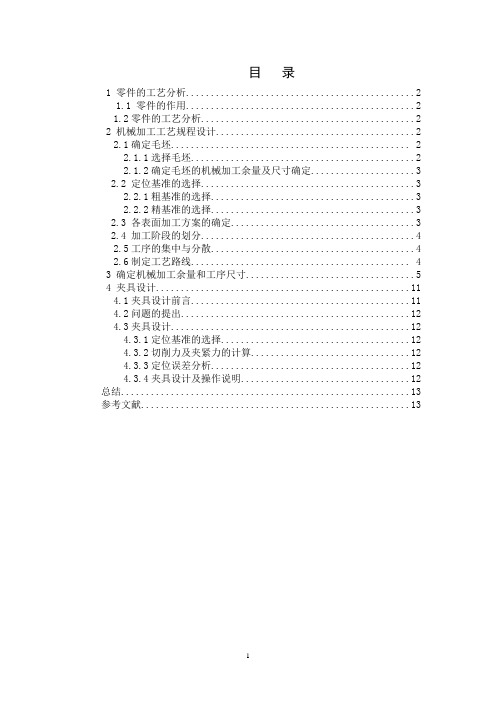
目录1 零件的工艺分析 (2)1.1 零件的作用 (2)1.2零件的工艺分析 (2)2 机械加工工艺规程设计 (2)2.1确定毛坯 (2)2.1.1选择毛坯 (2)2.1.2确定毛坯的机械加工余量及尺寸确定 (3)2.2 定位基准的选择 (3)2.2.1粗基准的选择 (3)2.2.2精基准的选择 (3)2.3 各表面加工方案的确定 (3)2.4 加工阶段的划分 (4)2.5工序的集中与分散 (4)2.6制定工艺路线 (4)3 确定机械加工余量和工序尺寸 (5)4 夹具设计 (11)4.1夹具设计前言 (11)4.2问题的提出 (12)4.3夹具设计 (12)4.3.1定位基准的选择 (12)4.3.2切削力及夹紧力的计算 (12)4.3.3定位误差分析 (12)4.3.4夹具设计及操作说明 (12)总结 (13)参考文献 (13)1 零件的工艺分析1.1零件的作用题目给定的零件是CA6140拨叉,它位于车床变速机构中,主要起换档,使主轴回转运动按照工作者的要求进行工作。
宽度为18+0.0120mm的槽尺寸精度要求很高,因为在拨叉拔动使滑移齿轮时如果槽的尺寸精度不高或间隙很大时,滑移齿轮得不到很高的位置精度。
所以,宽度为18+0.0120mm的槽和滑移齿轮的配合精度要求很高。
1.2零件的工艺分析该拨叉的技术要求如表1所示。
2机械加工工艺规程设计2.1确定毛坯2.1.1 选择毛坯确定毛坯种类:零件材料为HT200。
考虑零件在机床运行过程中所受冲击不大,零件结构又比较简单,生产类型为大批生产,故选择铸件毛坯。
查《机械制造工艺及设备设计指导手册》表15-5选用铸件尺寸公差等级CT9级。
采用铸造,拨叉属于轻型机械产品类型,产量1000件,因而在此选择机械砂型铸造。
2.1.2 确定毛坯的机械加工余量及尺寸确定1)右端面的加工余量:右端面有3±0.8mm的加工余量,足够把铸铁的硬质表面层切除。
2)矩形花键底孔。
机械制造装备设计课程设计--CA6140车床的拨叉(含CAD图纸)

机械制造装备设计课程设计--CA6140车床的拨叉(含CAD 图纸)目录1. 零件的工艺性分析 (3)1.1拨叉的用途 (3)1.2 确定各加工表面 (4)1.3拨叉的技术要求 (4)1.4毛坯的选择 (4)2 加工工艺规程设计 (4)2.1选择毛坯 (4)2.2确定毛坯尺寸公差和机械加工余量 (5)2.2.1 公差等级 (5)2.2.2 零件表面粗糙度 (5)2.2.3 机械加工余量 (5)2.3 绘制铸件毛坯简图 (5)3拟定拨叉工艺路线 (5)3.1定位基准的选择 (5)3.2表面加工方法的选择 (6)3.3 工序顺序的安排 (6)3.4工序的集中与发散 (6)3.5制定工艺路线 (7)4 机械加工余量、工序尺寸及毛坯尺寸的确定 81、后端面加工余量 (8)2、花键底孔加工余量 (8)3、18H11底槽的加工余量 (8)4、上端面的加工余量 (9)5 确定切削用量及基本工时 (9)6夹具的设计 (16)6.1问题的提出 (16)6.2夹具设计 (16)6.2.1定位基准的选择 (16)6.2.2.夹紧机构 (17)6.2.3对刀装置 (18)6.2.4夹具与机床连接元件 (18)6.2.5使用说明 (18)6.2.6. 结构特点 (18)7总结 (18)8参考文献 (19)1. 零件的工艺性分析1.1拨叉的用途题目所给的零件是CA6140车床的拨叉。
它位于车床变速机构中,主要起换档,使主轴回转运动按照工作者的要求工作,获得所需的速度和扭矩的作用。
1.2 确定各加工表面CA6140拔叉(型号:831003)共有3组加工表面:⑴、零件两端面,由于后端面要求的加工精度高,可以先以后端面为粗基准加工前端面,再以前端面为精基准加工后端面;⑵、以花键中心线为基准的加工面:Ø25H7的六齿方花键孔、Ø22H12的花键底孔、两端的2X150倒角和距花键中心线为22mm的上顶面;⑶、以工件后端面为基准的加工面:18H11mm的槽、上顶面的2-M8通孔和Ø5锥孔。
机械制造拔叉课程设计

目录第1章零件分析 (1)1.1 零件作用分析 (1)1.2 零件工艺分析 (1)第2章确定毛坯、画毛坯—零件合图 (3)2.1 确定毛坯种类 (3)2.2 确定毛坯尺寸公差和加工余量 (3)2.3 确定铸件基本尺寸 (3)2.4 毛坯—零件合图如下图所示 (4)第3章工艺规程设计 (5)3.1 定位基准的选择 (5)3.2 制定工艺路线 (5)3.3 选择加工设备及刀、夹、量具 (5)3.4 加工工序设计 (7)3.5 确定切削用量 (7)3.6 时间定额计算 (15)3.7 填写机械加工工艺过程卡和机械加工工序卡 (19)第4章铣mm03.08槽的工序专用夹具设计 (20)4.1 工件自由度分析及定位方案的确定 (20)4.2 夹紧力的计算 (20)4.3 定位误差的计算及定位精度分析 (21)4.4 操作说明 (21)参考文献 (22)第1章 零件分析1.1 零件作用分析题目给定的零件是CA6140拨叉,它位于车床变速机构中,主要起换档,使主轴回转运动按照工作者的要求进行工作。
宽度为mm 0.012018+的槽尺 寸精度要求很高,因为在拨叉拔动使滑移齿轮时如果槽的尺寸精度不高或间隙很大时,滑移齿轮得不到很高的位置精度。
所以,宽度为mm 0.012018+的槽和滑移齿轮的配合精度要求很高。
1.2 零件工艺分析零件得视图正确、完整,尺寸、公差及技术要求齐全,如下图所示。
1—1零件图此零件需要加工的表面有:(1)右端面粗糙度要求为3.2。
(2)两端的2*15°倒角粗糙度要求为6.3。
(3)上端面粗糙度要求为3.2。
(4)尺寸8的槽粗糙度要求为1.6,上偏差+0.03、下偏差0。
(5)尺寸18的槽粗糙度要求为3.2,上偏差+0.012、下偏差0。
(6)Ø25的六齿方花键孔粗糙度要求为1.6,上偏差+0.023、下偏差0。
(7)Ø22的花键底孔粗糙度要求为6.3,上偏差+0.28、下偏差0。
拨叉工艺规程及专用夹具设计课程设计报告

拨叉工艺规程及专用夹具设计课程设计报告课程设计报告(理工类)题目拨叉工艺规程及专用夹具设计课程名称机械制造技术基础院部名称龙蟠专业车辆工程班级M10车辆工程学生姓名包徐平学号1021106013指导教师智淑亚金陵科技学院教务处制目录第二节拨叉的工艺分析及生产类型的确定 3一、拨叉的用途 3二、拨叉的用途 3三、审查拨叉的工艺性 5四、确定拨叉的生产类型 6 第二节确定毛坯、绘制毛坯简图 6一、选择毛坯 6二、绘制拨叉锻造毛坯简图 6三、确定毛坯的尺寸公差和机械加工余量 6 第三节拟定拨叉工艺路线 8一、定位基准的选择 9二、各表面加工方案的确定 9三、加工阶段的划分10四、工序的集中与分散10五、确定工艺路线10六、机床设备及工艺装备的选用11七确定工艺路线 11第四节确定加工余量和工序尺寸12 一工序1和工序2——加工拨叉头两端面至设计尺寸12二、工序5和工序8——加工拨叉脚两端面至设计尺寸 15第五节确定切削用量及时间额定 17一、确定切削用量 17二、时间定额的计算 20工序卡片23课程设计示例及相关内容讲解图2-1、图2-2分别为某拖拉机用拨叉零件的零件图和三维图样。
已知:零件材料为35钢,重量为4.5kg,年产量Q=3000台/年,m=1件/台。
试为该拨叉零件编制工艺规程。
第一节零件的工艺分析及生产类型的确定一、零件的作用该拨叉应用在某拖拉机变速箱的换档机构中。
拨叉头以孔套在变速叉轴上,并用销钉经孔与变速叉轴联结,拨叉脚则夹在双联变换齿轮的槽中。
当需要变速时,操纵变速杆,变速操纵机构就通过拨叉头部的操纵槽带动拨叉与变速叉轴一起在变速箱中滑动,拨叉脚拨动双联变换齿轮在花键轴上滑动以改换档位,从而改变拖拉机的行驶速度。
该拨叉在改换档位时要承受弯曲应力和冲击载荷的作用,因此该零件应具有足够的强度、刚度和韧性,以适应拨叉的工作条件。
该零件的主要工作表面为拨叉脚两端面、叉轴孔Ф30+0.021 0mm(H7)和锁销孔Ф8+0.015 0mm(H7),在设计工艺规程时应重点予以保证。
拨叉锻造课程设计
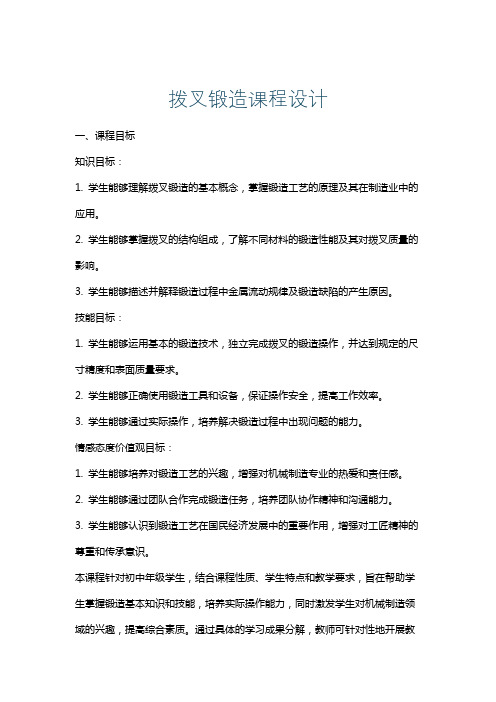
拨叉锻造课程设计一、课程目标知识目标:1. 学生能够理解拨叉锻造的基本概念,掌握锻造工艺的原理及其在制造业中的应用。
2. 学生能够掌握拨叉的结构组成,了解不同材料的锻造性能及其对拨叉质量的影响。
3. 学生能够描述并解释锻造过程中金属流动规律及锻造缺陷的产生原因。
技能目标:1. 学生能够运用基本的锻造技术,独立完成拨叉的锻造操作,并达到规定的尺寸精度和表面质量要求。
2. 学生能够正确使用锻造工具和设备,保证操作安全,提高工作效率。
3. 学生能够通过实际操作,培养解决锻造过程中出现问题的能力。
情感态度价值观目标:1. 学生能够培养对锻造工艺的兴趣,增强对机械制造专业的热爱和责任感。
2. 学生能够通过团队合作完成锻造任务,培养团队协作精神和沟通能力。
3. 学生能够认识到锻造工艺在国民经济发展中的重要作用,增强对工匠精神的尊重和传承意识。
本课程针对初中年级学生,结合课程性质、学生特点和教学要求,旨在帮助学生掌握锻造基本知识和技能,培养实际操作能力,同时激发学生对机械制造领域的兴趣,提高综合素质。
通过具体的学习成果分解,教师可针对性地开展教学设计和评估,确保课程目标的实现。
二、教学内容1. 锻造基本知识:介绍锻造的定义、分类及应用,使学生了解锻造工艺的广泛用途,对应教材第一章。
- 锻造原理与工艺流程- 锻造与其他加工方法的区别与联系2. 拨叉结构与材料:分析拨叉的组成结构、材料选择及其锻造性能,为学生锻造拨叉奠定基础,对应教材第二章。
- 拨叉的结构特点及设计要求- 常用锻造材料及其性能3. 锻造设备与工具:讲解锻造设备、工具的类型及使用方法,提高学生实际操作能力,对应教材第三章。
- 锻造设备的功能与操作要点- 锻造工具的选择与维护4. 锻造操作技巧:通过实际操作,让学生掌握锻造过程中的技巧,提高拨叉锻造质量,对应教材第四章。
- 锻造过程中的金属流动规律- 锻造缺陷的产生原因及防止方法5. 安全与质量控制:强调锻造过程中的安全注意事项,培养学生安全意识,同时关注锻造质量,对应教材第五章。
机械制造基础课程设计拨叉

机械制造基础课程设计拨叉设计一个拨叉的机械制造基础课程设计。
设计目标:1. 学习并理解拨叉的原理和工作原理;2. 熟悉拨叉的设计、制造流程和相关工艺;3. 培养学生的机械制造基础知识和工程实践能力。
设计内容:1. 拨叉原理和工作原理的讲解:- 介绍拨叉的作用、分类和应用领域;- 解析拨叉的工作原理和关键参数。
2. 拨叉的设计:- 了解拨叉的设计要求和流程;- 学习使用相关设计软件进行拨叉的结构设计; - 进行拨叉的零件设计和装配设计。
3. 拨叉的工艺与制造:- 学习拨叉的加工工艺和制造流程;- 了解拨叉的加工设备和工具;- 进行拨叉的工艺规程和制造工艺分析。
4. 拨叉的装配与调试:- 学习拨叉的装配方法和要点;- 进行拨叉的装配实践;- 进行拨叉的调试和性能测试。
5.拨叉的质量控制和检验:- 学习拨叉的质量控制标准和方法;- 进行拨叉的非破坏性检测和性能测试;- 学习拨叉的质量问题分析和解决方法。
6. 设计报告和展示:- 学生按照设计要求完成拨叉设计报告;- 学生进行拨叉设计成果展示。
7. 实践项目:- 学生自主设计并制造一个简单的拨叉模型; - 进行模型的装配和调试;- 进行模型的性能测试。
评估方式:- 学生参与课堂讨论和互动的积极程度;- 设计报告的全面性和准确性;- 拨叉模型的装配质量和性能测试结果。
授课方式:- 理论讲解;- 设计软件操作演示;- 实验室操作实践;- 实践项目实施。
教材参考:- 《机械制造基础》;- 《机械设计手册》;- 相关拨叉设计、制造及质量控制标准等。
机械制造基础课程设计拨叉
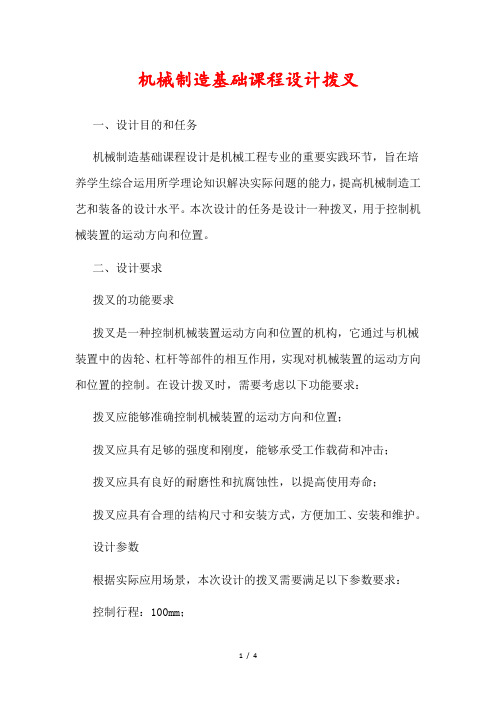
机械制造基础课程设计拨叉一、设计目的和任务机械制造基础课程设计是机械工程专业的重要实践环节,旨在培养学生综合运用所学理论知识解决实际问题的能力,提高机械制造工艺和装备的设计水平。
本次设计的任务是设计一种拨叉,用于控制机械装置的运动方向和位置。
二、设计要求拨叉的功能要求拨叉是一种控制机械装置运动方向和位置的机构,它通过与机械装置中的齿轮、杠杆等部件的相互作用,实现对机械装置的运动方向和位置的控制。
在设计拨叉时,需要考虑以下功能要求:拨叉应能够准确控制机械装置的运动方向和位置;拨叉应具有足够的强度和刚度,能够承受工作载荷和冲击;拨叉应具有良好的耐磨性和抗腐蚀性,以提高使用寿命;拨叉应具有合理的结构尺寸和安装方式,方便加工、安装和维护。
设计参数根据实际应用场景,本次设计的拨叉需要满足以下参数要求:控制行程:100mm;控制力:500N;拨叉材料:45钢;表面处理:镀硬铬。
三、设计步骤和方法确定设计方案在设计拨叉时,需要考虑其功能要求和结构特点。
根据设计任务书的要求,我们可以确定以下设计方案:采用摇臂式拨叉,通过与齿轮的啮合实现控制机械装置的运动方向和位置;采用45钢作为拨叉材料,通过镀硬铬处理提高表面耐磨性和抗腐蚀性;拨叉的结构尺寸和安装方式应根据实际应用场景进行设计。
绘制草图根据设计方案,我们可以绘制出拨叉的草图。
在绘制草图时,需要注意以下几点:确定拨叉的结构尺寸和安装方式;绘制出拨叉的各个部件,包括摇臂、轴、齿轮等;确定各个部件之间的连接方式和配合关系;确定表面处理方法。
进行尺寸计算和校核根据草图,我们需要对拨叉的各个部件进行尺寸计算和校核。
在计算尺寸时,需要注意以下几点:根据控制行程和控制力计算齿轮的尺寸和模数;根据控制力和摇臂长度计算摇臂轴的尺寸和强度;根据控制行程和摇臂长度计算摇臂的尺寸和刚度;对摇臂轴和摇臂进行静力学校核,确保其能够承受工作载荷和冲击。
绘制零件图和装配图在完成尺寸计算和校核后,我们需要绘制出拨叉的各个零件图和装配图。
机械制造技术基础课程设计(拨叉)

摘要
拔叉的加工质量直接影响机器的性能和使用寿命。本次设计旨在提高 CA6140 车床 拔叉的加工效率,由此我们首先对拔叉的结构特征和工艺进行仔细的分析,然后确定一 套合理的加工方案,加工方案要求简单,操作方便,并能保证零件的加工质量。制定加 工工艺的顺序如下: 1 分析零件。 2 选择毛坯。 3 设计工艺规程,包括制定工艺路线,选择基准面等。 4 工序设计:包括选择机床,确定加工余量,工序尺寸和毛坯尺寸,确定切削用量及设 计基本工时等。 5 编制工艺文件。 由于能力所限,设计尚有许多的不足之处,恳请老师指正。
4
根据以上资料及路线, 分别确定各加工表面的机械加工余量、 工序尺寸及毛坯如下: 1、Ф20mm 孔和Ф50mm 孔轴线方向长度方向的加工余量及公差(Ф20mm、Ф50mm 端面) 查《工艺手册》表 2.2-4 取Ф20mm、Ф50mm 端面长度余量为 3mm(均为单侧加工)。 铣削加工余量为:粗铣:Z=2mm(单侧)毛坯尺寸及公差为:Ф20mm 端面: 36 1.8 mm 精铣:Z=1mm(单侧) 2、Ф50mm 孔的加工余量及公差 查《工艺手册》表 2.2-3 和表 2.2.3-10,取Ф50mm 已铸成长度余量为 2.5mm(双侧 加工余量),即已铸成孔Ф45mm,根据其内表面尺寸精度要求为 IT12,所以确定工序尺 寸及余量为:
机械制造技术基础
课程设计说明书
设计题目 设计“CA6140 车床拨叉”零件的 机械加工工艺规程(年产量为 5000 件)
设计者: 指导教师: 日期: 2015 年 1 月
广西科技大学
机械制造技术基础课程设计任务书
题目:设计“CA6140 车床拨叉”零件的机械加工工艺 规程(年产量为 5000 件) 内容:1.毛坯图 2.课程设计说明书 3.机械加工工艺过程综合卡片 4.机械加工工序卡片
机械设计课程设计之拨叉的设计
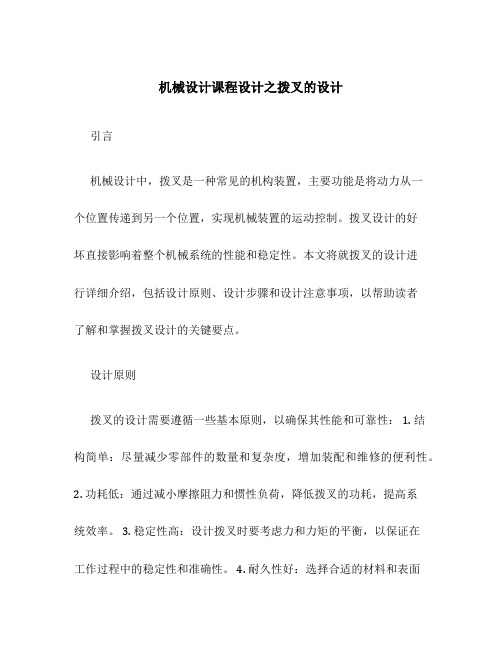
机械设计课程设计之拨叉的设计引言机械设计中,拨叉是一种常见的机构装置,主要功能是将动力从一个位置传递到另一个位置,实现机械装置的运动控制。
拨叉设计的好坏直接影响着整个机械系统的性能和稳定性。
本文将就拨叉的设计进行详细介绍,包括设计原则、设计步骤和设计注意事项,以帮助读者了解和掌握拨叉设计的关键要点。
设计原则拨叉的设计需要遵循一些基本原则,以确保其性能和可靠性: 1. 结构简单:尽量减少零部件的数量和复杂度,增加装配和维修的便利性。
2. 功耗低:通过减小摩擦阻力和惯性负荷,降低拨叉的功耗,提高系统效率。
3. 稳定性高:设计拨叉时要考虑力和力矩的平衡,以保证在工作过程中的稳定性和准确性。
4. 耐久性好:选择合适的材料和表面处理技术,增强拨叉的抗磨损和耐腐蚀性能,延长使用寿命。
5. 易于制造:考虑工艺性和成本因素,选择合适的加工方法和工艺流程,以便实现高效率的制造和组装。
设计步骤步骤一:确定拨叉的用途和功能要求在进行拨叉设计前,首先需要明确拨叉的用途和所需实现的功能。
例如,拨叉可用于切换机械系统的工作状态,抓取或释放物体等。
这有助于准确定义拨叉的运动和控制要求。
步骤二:选择合适的拨叉类型拨叉的设计和选择取决于其应用场景和功能要求。
根据具体情况,可选择常用的拨叉类型,如平面摆式、滑动摆式或平行摆式等。
同时,还需考虑拨叉的材料选择,以满足强度、刚度和耐磨性等要求。
步骤三:确定拨叉的工作参数根据拨叉的用途和功能要求,确定拨叉的工作参数,如工作行程、速度、力矩等。
这些参数的选择应基于机械系统的运动要求和负载情况,以保证拨叉工作的稳定性和可靠性。
步骤四:进行拨叉的结构设计和分析拨叉的结构设计需要综合考虑刚度、精度、负载和工作环境等因素。
通过使用CAD软件进行三维建模,可以实现对拨叉结构的设计和分析。
在结构设计过程中,需要进行受力分析、刚度分析和动力学分析等,以确保拨叉结构设计的合理性。
步骤五:选择拨叉的传动方式和控制系统拨叉的传动方式和控制系统的选择取决于具体应用场景和功能要求。
机械制造基础课程设计说明书(拨叉)

Ff=371×2.251.3×10.7×0.691=735.7N
(2)夹紧力的计算
在本工步中为防止工件转动所需的最小夹紧力为Fj=KMsin45o/(f1Rsin45o+f2R)=3×46.3×sin45o/(0.25×30×sin45o+0.7×30)=3.07N
2.以φ60mm孔为中心的加工表面
这一组加工表面包括:φ60H7mm的孔,以及φ60H7mm的两个端面。主要是φ60H7mm的孔。
3.铣16H11mm的槽
这一组加工表面包括:此槽的端面,16H11mm的槽的底面,
16H11mm的槽两侧面。
4.以M22×1.5螺纹孔为中心的加工表面。
这一组加工表面包括:M22×1.5的螺纹孔,长32mm的端面。
主要加工表面为M22×1.5螺纹孔。
这两组加工表面之间有着一定的位置要求,主要是:
(1)φ60孔端面与φ25H7孔的垂直度公差为0.1mm.。
(2)16H11mm的槽与φ25H7孔的垂直度公差为0.08mm。
由上面分析可知,加工时应先加工一组表面,再以这组加工后表面为基准加工另外一组。
由上面分析可知,可以粗加工拨叉底面,然后以此作为粗基准采用专用夹具进行加工,并且保证位置精度要求。再根据各加工方法的经济精度及机床所能达到的位置精度,并且此拨叉零件没有复杂的加工曲面,所以根据上述技术要求采用常规的加工工艺均可保证。
2.精基准的选择。
主要应该考虑基准重合的问题。当设计基准与工序基准不重合时,应该进行尺寸换算,这在以后还要专门计算,此处不再重复。
1.2.3制定工艺路线
制定工艺路线的出发点,应当是使零件的几何形状、尺寸精度及位置精度等技术要求能得到合理的保证,在生产纲领已确定的情况下,可以考虑采用通用机床配以专用夹具,并尽量使工序集中来提高生产率。除此之外,还应当考虑经济效果,以便使生产成本尽量下降。
机械制造工艺学课程设计-CA6140车床拨叉设计说明书

=46.9(m/min) (4)确定机床主轴转速 ns=1000vc/dw=229.8(r/min)
1.2零件的工艺分析
CA6140拨叉共有两组加工表面: 2.2.1以花键孔的中心线为基准的加工面
这一组面包括Ø25+0.0230mm的六齿矩形花键孔Ø22+0.280花键底 孔两端的2X150倒角和距中心线为27mm的平面。 2.2.2以工件右端面为基准的8+0.030 mm的槽和18+0.0120mm的槽 经上述分析可知, 对于两组加工表面,可先加工其中一组表 面,然后借助于专用夹具加工另一组表面。
4.1 工序一:车削A面、钻扩孔、倒角
1.加工条件 工件材料:灰口铸铁HT200,σb=145MPa,铸造。 加工要求:粗、半精铣、A面并保证18mm的工序尺寸,Ra=3.2µm。 机床: 砖塔式六角卧式车床C3163—1. 刀具: 刀片材料,r =12. ao=6-8 b= -10 rE=0.5 Kr=90 n=15 2.计算切削用量
按C3163-1 车床说明书 f=0.53mm/r (3)计算切削速度 切削速度的计算公式为(寿命选T=60min,刀具材 料为YG6)
V=Cv/(Tm·ap xv·f yv) ·kv 其中:根据《机械加工工艺师手册》表27—12加工外形:外圆纵车 (kr>00)、刀具材料YG6、进给量f > 0.40可得:Cv=158 xv=0.15 yv=0.4 M=0.2修正系数Kv:
半精车 (1) 已知粗加工余量为1mm (2) 进给量f 根据《机械制造技术基础》表5—116表面粗糙度
拨叉课程设计(1)
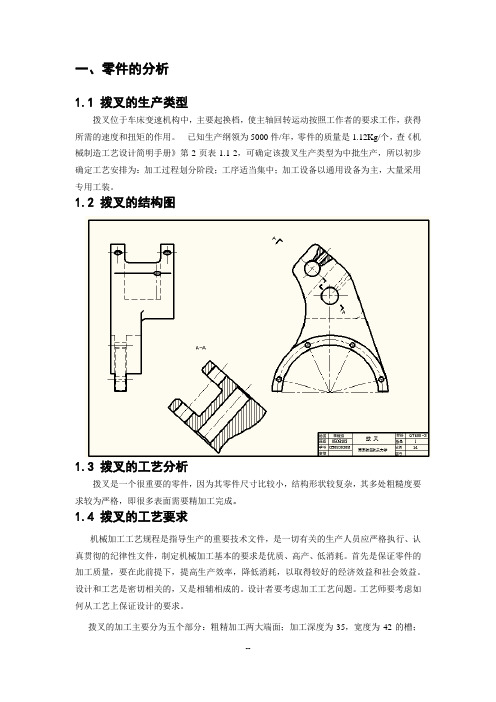
一、零件的分析1.1 拨叉的生产类型拨叉位于车床变速机构中,主要起换档,使主轴回转运动按照工作者的要求工作,获得所需的速度和扭矩的作用。
已知生产纲领为5000件/年,零件的质量是1.12Kg/个,查《机械制造工艺设计简明手册》第2页表1.1-2,可确定该拨叉生产类型为中批生产,所以初步确定工艺安排为:加工过程划分阶段;工序适当集中;加工设备以通用设备为主,大量采用专用工装。
1.2 拨叉的结构图1.3 拨叉的工艺分析拨叉是一个很重要的零件,因为其零件尺寸比较小,结构形状较复杂,其多处粗糙度要求较为严格,即很多表面需要精加工完成。
1.4 拨叉的工艺要求机械加工工艺规程是指导生产的重要技术文件,是一切有关的生产人员应严格执行、认真贯彻的纪律性文件,制定机械加工基本的要求是优质、高产、低消耗。
首先是保证零件的加工质量,要在此前提下,提高生产效率,降低消耗,以取得较好的经济效益和社会效益。
设计和工艺是密切相关的,又是相辅相成的。
设计者要考虑加工工艺问题。
工艺师要考虑如何从工艺上保证设计的要求。
拨叉的加工主要分为五个部分:粗精加工两大端面;加工深度为35,宽度为42的槽;钻、铰2-M8通孔,并攻丝;Φ156圆端面(粗糙度要求较高)以及Φ113和Φ156的圆的粗精加工;四个Φ6的小孔的粗精加工等:工艺要求如下: (1)首先总体遵循先粗后精,先面后孔的原则;(2)端面的粗精加工均在卧式铣床上完成,且是互为基准进行加工,使得粗糙度达到Ra6.3的要求;(3)2-M8的螺纹因其粗糙度要求较高,所以遵循典型孔的加工路线:钻、扩、铰,最后攻丝完成螺纹加工;(4)四个Φ6的小孔的粗精加工钻、扩、铰即可完成;(5)深度与宽度方向均有尺寸要求与粗糙度要求的槽的加工采用卧式铣床上的盘形铣刀实现;(6)Φ156和Φ113的孔以及Φ156的外圆采取的是卧式镗床上粗镗加精镗实现。
二、工艺规程设计2.1毛坯的选择拨叉材料为QT600-3,考虑零件在机床运行过程中所受冲击不大,零件结构又比较简单,生产类型为中批生产,故毛坯选择金属型铸造。
机械制造技术基础课程设计说明书正文(机床拨叉)

一、零件加工工艺规程的设计1、分析零件图该零件为车床拨叉,年产量为10000件,为大批量生产。
由图知,未注明粗糙度的表面不加工。
小头孔内表面与大头孔两个端面的表面粗糙度要求均为Ra5,可知要进行精加工。
未注明公差的尺寸默认为IT14~IT18,并且确定各个尺寸的公差度等级,综合表面粗糙度和形位误差要求决定各个加工面要选取何种加工方式如下:小头孔上下端面:粗铣大头孔上下端面:粗糙度较高,粗铣后精铣小头孔:粗糙度要求高,扩、铰大头孔:扩其余不加工。
但是该零件大头孔为半圆孔,其加工工艺性不如整圆孔的加工工艺性好,因此确定毛坯形状为两个车床拨叉相对的形状,使大头孔为一个整圆,一次性加工出两个零件。
2、确定毛坯的材料和形状由零件图上标题栏中注明,该零件材料为ZG45。
分析零件的工艺性,确定毛坯精度为一级精度,查表获得总余量,确定毛坯形状如下图所示:3、拟定加工的工艺路线根据《机械制造技术基础》课程所学的内容,在制定机械加工工艺规程时要解决的问题有:(1)定位基准的选择原则:选精基准时要遵循基准重合原则、基准统一原则、互为基准原则和自为基准原则,来保证经济合理地达到零件的加工精度要求;选择粗基准时,考虑的重点是如何保证加工面有足够的余量,使不加工表面与加工表面间的尺寸、位置符合图样要求,因此选择原则是保证相互位置,余量均匀分配,尽量使用一次和便于工件装夹。
(2)加工方法的选择:根据被加工材料的性质、零件的生产类型、工件的形状及每个加工面的技术要求等条件,参阅相关机械加工手册来确定加工方法和分几次加工。
(3)加工工序安排的基本原则:先加工定位基准面在加工其他表面来提高定位精度;先加工主要表面再加工次要表面;先安排粗加工再安排精加工和光整加工;先加工表面再加工孔。
方案一:工序一:以小头孔下端面C、D定位,粗铣A、B。
工序二:以小头孔上端面A、B定位,粗铣C、D。
工序三:以小头孔下端面C、D和大头孔内圆轴线定位,扩两个小头孔。
拨叉机械制造课程设计

拨叉机械制造课程设计一、课程目标知识目标:1. 让学生掌握拨叉机械的基本结构及其工作原理,理解其在机械制造中的应用。
2. 使学生了解并掌握拨叉机械制造过程中的关键工艺参数及其影响。
3. 帮助学生掌握拨叉机械的材料选择、加工方法和质量控制要点。
技能目标:1. 培养学生运用CAD软件进行拨叉机械零件设计的实际操作能力。
2. 培养学生运用CAM软件进行拨叉机械零件加工编程的能力。
3. 提高学生实际操作机床进行拨叉机械制造的综合技能。
情感态度价值观目标:1. 培养学生对机械制造专业的兴趣,激发他们学习的积极性和主动性。
2. 培养学生的团队协作精神,提高沟通与交流能力,增强集体荣誉感。
3. 引导学生树立正确的质量观,培养严谨细致、追求卓越的工作态度。
本课程针对高年级学生,具有较强的实践性和应用性。
结合课程性质、学生特点和教学要求,将目标分解为具体的学习成果,以便后续的教学设计和评估。
通过本课程的学习,使学生不仅掌握拨叉机械制造的相关理论知识,而且能够运用所学知识解决实际问题,为将来的职业生涯奠定基础。
二、教学内容1. 拨叉机械概述:介绍拨叉机械的定义、分类、应用领域及发展现状,使学生对其有一个全面的认识。
教材章节:《机械设计基础》第三章第二节2. 拨叉机械结构及工作原理:分析拨叉机械的主要组成部分,讲解其工作原理,为后续设计制造打下基础。
教材章节:《机械设计基础》第三章第三节3. 拨叉机械制造工艺:详细讲解拨叉机械制造的关键工艺参数,包括材料选择、加工方法、热处理等。
教材章节:《机械制造工艺学》第四章4. CAD/CAM软件在拨叉机械制造中的应用:使学生掌握CAD/CAM软件进行拨叉机械零件设计和加工编程的方法。
教材章节:《CAD/CAM技术与应用》第二章5. 拨叉机械制造质量控制:分析影响拨叉机械制造质量的因素,讲解质量控制要点及措施。
教材章节:《质量管理与控制》第三章6. 实践教学:组织学生进行拨叉机械制造的实际操作,包括机床操作、工艺参数调整、质量控制等。
- 1、下载文档前请自行甄别文档内容的完整性,平台不提供额外的编辑、内容补充、找答案等附加服务。
- 2、"仅部分预览"的文档,不可在线预览部分如存在完整性等问题,可反馈申请退款(可完整预览的文档不适用该条件!)。
- 3、如文档侵犯您的权益,请联系客服反馈,我们会尽快为您处理(人工客服工作时间:9:00-18:30)。
一、零件分析(一)拨叉的作用拨叉是车床变速箱换挡机构中的一个主要零件(位置如图1所示),主要起换挡作用。
通过拨叉的拨动使车床滑移齿轮与不同的齿轮啮合从而达到要求的主轴转速。
如果拨叉槽口的配合尺寸精度不高时,滑移齿轮就达不到要求的定位精度,这样滑移齿轮就不能很好的与其他齿轮进行正确有效的啮合,从而影响整个传动系统的工作。
所以拨叉宽度为30mm 的上端面和宽度为18H11槽的侧面以及花键的精度要求较高。
图1 卧式车床主轴展开图(二)拨叉的工艺分析该拨叉尺寸比较小,结构形状较复杂,属于典型的叉杆类零件。
为实现换挡、变速的功能,其叉轴孔与叉轴有配合要求,因此加工精度要求较高。
叉脚两端面在工作过程中受轻微冲击载荷,为保证拨叉换挡时叉脚受力均匀,要求底槽侧面与花键孔中心轴有垂直度公差要求为0.08mm。
拨叉的顶面要与换挡手柄等零件相配合,因此为使工作时拨叉承受水平方向上的力要求上端面与叉轴孔轴线有平行度要求为0.10mm。
故该零件的主要加工表面为叉轴孔、叉脚底槽侧面和拨叉上端面,由于这些主要加工表面的精度相对较低,因此采用较经济的方法保质保量的加工即可。
二、工艺规程设计(一)确定毛坯的制造形式根据零件材料HT200确定毛坯为铸件,零件生产类型为中批生产。
故从提高生产效率,保证经济性的角度讲,应该采用铸造成型中的金属模铸造的方法制造毛坯。
又因为零件形状相对简单,故毛坯形状需与零件的形状尽量接近,孔很小,可不铸出。
(二)基准的选择基准的选择是工艺规程设计中的重要工作之一。
基准选择的正确与合理,可以使加工质量得到保证,生产率得到提高。
否则,加工工艺过程中会出现很多问题,使生产无常进行。
通常先选精基准后选粗基准。
1.精基准的选择精基准的选择有利于保证加工精度,并使工件装夹方便。
在选择时,主要应该考虑基准重合、基准统一等问题。
当设计基准与工序基准不重合时,应该进行尺寸换算。
在本零件中花键孔的中心线为叉脚部分沟槽和顶面的设计基准,故以花键孔的中心线为精基准,实现了设计基准与工艺基准相重合,保证了被加工表面的垂直度和平行度要求。
同时由于零件在轴向上的刚度较大,因此选用零件的左端面作为精基准,夹紧力作用在右端面上,可避免在机械加工工程中发生变形,加紧稳定可靠。
2.粗基准的选择对于零件而言,尽可能选择不加工表面为粗基准。
而对有若干个不加工表面的工件,则应以与加工表面要求相对位置精度较高的不加工表面作粗基准。
所以选择右端面,40×80的顶面和75×80的右侧面及外圆中心线为粗基准,可以为后续工序准备好精基准。
(三)制订工艺路线1. 表面加工方法确定根据零件图上各加工表面的尺寸精度和表面粗糙度,查相关表格,确定零件各表面的加工方法,如表1所示。
表1 各表面加工方案2. 工艺路线拟定尊循“先粗后精”原则,先安排粗加工后安排精加工。
尊循“先基准后其他”原则,首先加工精基准—左侧面和花键轴孔;尊循“先主后次”原则,先加工主要表面—左侧面和花键轴孔,后加工次要表面—顶面和操纵槽侧面及底面;由此安排工艺路线如表2。
表2 机械加工工艺路线(四)机械加工余量、工序尺寸及毛坯尺寸的确定零件的材料为HT200,净重量约为0.93千克,生产类型为中批量生产,可以采用金属模铸造的方法进行毛坯的制造。
根据上述原始资料及加工工艺,分别确定各个加工表面的机械加工余量、工序尺寸及毛坯尺寸如下:1.面的加工余量及工序尺寸考虑到零件的很多表面没有粗糙度要求,不需要加工。
从铸造出来即可符合使用要求,因此,只需确定后端面的尺寸即可。
选取铸件的尺寸公差等级为CT8,查表得出其公差值为1.6mm。
又根据零件的铸造方法(金属模铸造)、公差等级(CT1~CT16)和零件的材料(灰口铸铁),查表确定零件的加工余量等级,即MA 值。
经查,确定加工余量等级为F 级。
最后根据CT 、MA 和工件基本尺寸查表确定机械加工余量,该拨叉的基本尺寸≤100mm ,公差等级为CT8,加工余量等级为F ,故查表所得的机械加工余量为2.0mm 。
机械加工余量分为单侧和双侧,单侧加工余量与加工要求的关系如图所示。
毛坯的最大极限尺寸lmax=零件基本尺寸+MA+CT/2=mm 8.8226.1280=++;毛坯的最小极限尺寸lmin=零件的基本尺寸+MA-CT/2=mm 2.8126.1280=-+。
即毛坯尺寸为82±0.8mm 。
2. 花键底孔的加工余量及工序尺寸根据《机械制造技术基础课程设计》表2.53得出:在实体材料上加工孔,一次性钻孔,孔的公差等级可以达到H13~12级,符合Φ22H12的要求,但为提高其表面精度需进行扩孔。
再根据《金属机械加工工艺设计手册》表4-22查出拉键槽加工余量为f=0.4mm ,即预制孔加工到Φ21.2mm ,一次性拉削到设计要求Φ25H7。
查表2.56可知扩孔的加工余量为 1.5~2.0mm ,由于本工序的待加工表面的金属厚度较小,故取扩孔的加工余量为0.6mm 。
3.底槽18H11的加工余量及工序尺寸该槽铸造时没有铸出,参照《机械加工工艺师手册》表21-5,得粗铣其槽边机加工余量(双边余量)Z=3.0mm ,半精加工的余量(双边余量)Z=1mm 。
由于该工序加工时选用的刀具为Φ16的立式铣刀,粗加工时要铣去大部分的余量,因此取半精加工的双边余量为Z=2.0mm 。
又由刀具选择可得其极限偏差为:粗铣为+0.210mm ,半精铣为+0.13mm 。
粗铣两边工序尺寸为:mm 0.160.218=-; 粗铣后毛坯最大尺寸为:mm 21.1621.016=+;粗铣后毛坯最小尺寸为: 16+0=16mm ;即粗加后的工件尺寸为16+0.21 0mm 。
半精铣两边工序尺寸为: 18+0.31 0mm 能够满足加工要求。
4.螺纹的加工查《机械制造工艺设计简明手册》表2.3-20,得M8螺纹攻螺纹前所用麻花钻的直径为6.7mm 。
现将各工序加工余量及工序尺寸整理成表,如表3所示。
表3 各工序加工余量与工序尺寸(五)确定切削用量及基本工时工序Ⅰ:粗铣、精铣后端面 工件材料:HT200,b δ=220MPa ,硬度HBS=157~236;加工要求:表面粗糙度Ra=3.2um ; 机床:X51立式铣床刀具:刀具材料 高速钢端面铣刀2. 背吃刀量的确定因为粗加工余量较小故一次切削就可切除所有余量,因此取粗加工的背吃刀量等于粗加工余量,即ap 11=z=1.5mm 。
精铣时ap 12=0.5mm 。
3.进给量查《实用机械加工工艺手册》表11-90,根据机床功率及工艺系统刚度,查得粗铣每齿进给量粗f =0.15~0.3mm/z, 精铣每齿进计量精f =0.05~0.12mm/z ;取粗加工的每齿进给量z f =0.2mm/z ,精加工的每齿进给量z f =0.05m/z 。
4.切削速度及进给速度的确定查表确定粗加工的铣削速度为min /43m V =粗,精加工的铣削速度为min /71m V =精。
min /17.17180431000v 1000r D n =⨯⨯==ππ粗 r/min64.28280711000=⨯⨯=π精n查表 3.6,粗铣和精铣时的转速分别为160r/min 和300r/min 。
修正后的切削速度为:min /20.401000801601000n m D V =⨯⨯==ππ粗 m/min36.751000803001000n =⨯⨯==ππD V 精则进给速度为:min /320160102.0mm zn f V z f =⨯⨯==粗 min /1503001005.0mm zn f V z f =⨯⨯==精工序Ⅱ:钻花键轴孔、扩孔 1.钻孔(1)钻孔时选用直径为Φ20mm 的高速钢麻花钻,机床则选用Z525立式钻床。
(2)钻削速度及进给速度的确定由《机械加工工艺师手册》表28-15,根据高速钢麻花钻的直径do =20mm ,铸铁的硬度约为200HBS ,查得进给量f=0.43~0.53mm/r 。
由于Yd =80/20=4查得修正系数95.0=tf k ,则f =0.41~0.50mm/r 。
由《切削用量简明手册》表2.8可查得钻头强度允许的进给量为f =1.75mm/r 。
因此进给量在允许围,取f =0.45mm/r 。
则对应的钻削速度为v=17m/min 。
因此主轴转速为min /7.270201710001000r D v n =⨯⨯==ππ 查表3.18得钻床主轴转速为272r/min ,因此其实际的钻削速度为:min/08.171000202721000m D n V =⨯⨯=⨯⨯=ππ进给速度为:min /4.12227245.0mm n f v =⨯=⨯=2.扩孔时(1)扩孔时考虑钻孔所达到的直径及拉花键时的加工余量,选择直径为Φ20.7mm 扩孔钻,扩孔后的孔径Φ21.2mm ,符合花键的加工余量刀具材料为高速钢。
(2)切削速度及进给速度的确定由《机械加工工艺师手册》表28-30高速钢及硬质合金扩孔钻的进给量,得进给量f=0.7~0.8mm/min,取f=0.7mm/r ,由于修正系数K=0.95,所以进给量f=0.7x0.95=0.67mm/min 。
再查表28-32,确定切削速度为v=25m/min 。
则主轴转速为:min/62.3847.202510001000r D v n =⨯⨯=⨯⨯=ππ 查表3.18确定主轴实际转速为392r/min ,故其实际的切削速度为:min/48.2510007.203921000m D n V =⨯⨯=⨯⨯=ππ进给速度为:min /4.2743927.0mm n f v =⨯=⨯=3.检验机床功率根据所选的切削用量、切削速度及寄给速度进行功率估算,经计算加工所需功率为1.20kw 小于所选用的机床主电机功率2.8kw 。
故所选切削用量可用。
工序Ⅲ 拉花键机床:卧式拉床L6120。
刀具:查参考文献《实用机械加工工艺手册》表10-266,选择拉刀类型为矩形花键拉刀第三型号,该刀具特点:拉削长度大于30mm ,同时加工齿数不小于5。
材料:W18Cr4V 做拉刀材料,柄部采用40Cr 材料。
拉削过程中,刀具进给方向和拉削方向一致,拉刀各齿齿升量详见拉刀设计,拉削的进给量即为单面的齿升量。
查参考文献《实用机械加工工艺手册》表2.4-118和2.4-119,确定拉削速度v=0.116~0.08mm/s ,取v=0.10mm/s 。
拉削工件长度:mm l 80=; 拉刀长度:mm l 9951=;拉刀切出长度mm l 10~52=,取mm l 102=。
工序Ⅳ 粗铣、精铣顶面本工序刀具采用高速钢立铣刀,机床为X51立式铣床。