第08章-离子注入工艺
离子注入工艺流程
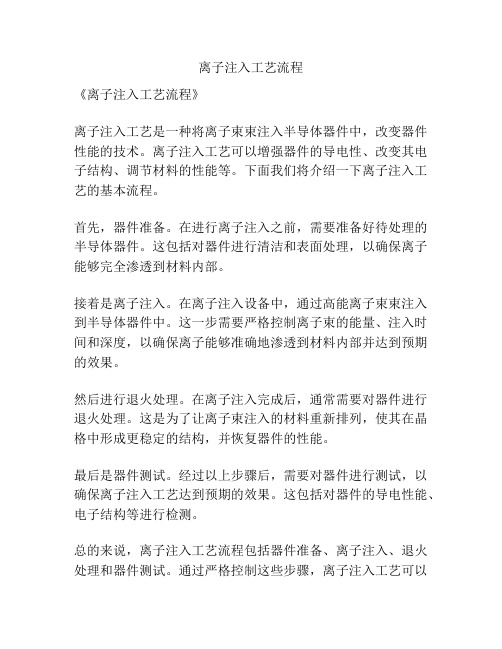
离子注入工艺流程
《离子注入工艺流程》
离子注入工艺是一种将离子束束注入半导体器件中,改变器件性能的技术。
离子注入工艺可以增强器件的导电性、改变其电子结构、调节材料的性能等。
下面我们将介绍一下离子注入工艺的基本流程。
首先,器件准备。
在进行离子注入之前,需要准备好待处理的半导体器件。
这包括对器件进行清洁和表面处理,以确保离子能够完全渗透到材料内部。
接着是离子注入。
在离子注入设备中,通过高能离子束束注入到半导体器件中。
这一步需要严格控制离子束的能量、注入时间和深度,以确保离子能够准确地渗透到材料内部并达到预期的效果。
然后进行退火处理。
在离子注入完成后,通常需要对器件进行退火处理。
这是为了让离子束注入的材料重新排列,使其在晶格中形成更稳定的结构,并恢复器件的性能。
最后是器件测试。
经过以上步骤后,需要对器件进行测试,以确保离子注入工艺达到预期的效果。
这包括对器件的导电性能、电子结构等进行检测。
总的来说,离子注入工艺流程包括器件准备、离子注入、退火处理和器件测试。
通过严格控制这些步骤,离子注入工艺可以
有效地改善半导体器件的性能,为半导体工业的发展提供重要支持。
【doc】离子注入工艺简介
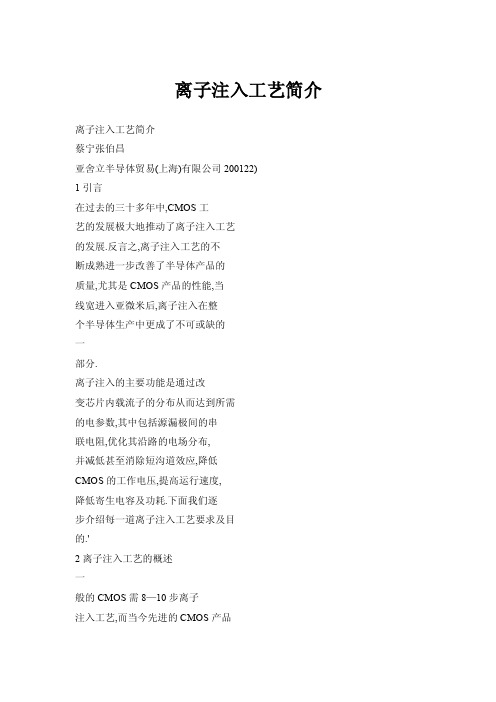
离子注入工艺简介离子注入工艺简介蔡宁张伯昌亚舍立半导体贸易(上海)有限公司200122)1引言在过去的三十多年中,CMOS工艺的发展极大地推动了离子注入工艺的发展.反言之,离子注入工艺的不断成熟进一步改善了半导体产品的质量,尤其是CMOS产品的性能,当线宽进入亚微米后,离子注入在整个半导体生产中更成了不可或缺的一部分.离子注入的主要功能是通过改变芯片内载流子的分布从而达到所需的电参数,其中包括源漏极间的串联电阻,优化其沿路的电场分布,并减低甚至消除短沟道效应,降低CMOS的工作电压,提高运行速度,降低寄生电容及功耗.下面我们逐步介绍每一道离子注入工艺要求及目的.'2离子注入工艺的概述一般的CMOS需8—10步离子注入工艺,而当今先进的CMOS产品更需20多步离子注入.根据在场效应管的位置,离子注入工艺可分为三大块:1)沟道区及井区(Channe1 andWel1)掺杂;2)多晶硅(Poly)注入:3)源漏区(SourceDrain)注入.2.1沟道及井区掺杂沟道区及井区的掺杂主要有阈值电压调节(V+Adjust)注入,反穿通(Anti-punchthrough)注入,埋层(BuriedLayer)注入,井问绝缘注入(Channe1Stop),井区反型(RetrogradeWel1)注入及吸收(Gettering)注入.这部分注入工艺的能量比较宽,但剂量属中低范围,所以此部分注入工艺基本上使用中束流及高能注入机.2.1.1阈值电压调节注入工艺(V.Adjust)阈值电压调节注入工艺是半导体工业中使用最早的离子注入技术工艺.由于在CMOS中N型井与P型井共存,它们的功能电压会有不同,V+ 注入是将所需的元素掺杂在门下方的沟道区内,改变电荷而得到所需的工作电压,使这两种井区共用一个闸门电压.高性能产品的N井区里传统的硼掺杂逐渐被铟(indium)注入所代替,其目的是使载子浓度分布更陡,以提高开关速度并降低功耗.2.1.2反击通注入工艺(Ant1一Dunchthr0ugh)该注入工艺的功能是防止源漏两极在沟道下面导通,因PN结深与载流子浓度成反比,如果沟道下部载流子浓度很低,在细线宽情况下源漏之间的PN结就会靠很近而容易被击通,增加此区域的载流子浓度就是为了降低耗尽层的厚度,使源漏不会在沟道下面导通,所以此注入要比阈值电压调节注入要更深一些.2.1.3井间绝缘注入工艺(Channel Stop)井间绝缘的注入是将杂质掺在用于隔开井区的绝缘栏的下方,此目的是为了提高井间寄生场效应管的阈值电压,使在正常的工作情形下此寄生三极管不会被导通而起到绝缘的效果.2.1.4埋层注入工艺(BuriedLayer)该工艺是要降低井区底部的电阻,以防芯片在运行中出现死循环(Latch—up)现象.井区内二个寄生的三极管(NPN&PNP)在一定的条件下可变成一个PNPN可控硅而形成自锁,埋层注入可降低PNP--极管的输出电阻,抬高死循环引发电流而彻底消除死循环现象.2.1.5吸取注入工艺(Gettering)它是在CM0S离子注入中能量最高的工艺,其目的是利用所注入的元素的化学特性和注后所形成的缺陷的物理特性来吸收井区里的其它杂质(如:重金属等)及晶格缺陷,以提高井区内,尤其是沟道区内的材料质量来提升产品性能.离子注入晶体后与原子核碰撞的可能性是和离子本身的能量成反比,所以在高能注入的条件下,有些轻元素如硼及磷,因注入而产生的缺陷分布与注入元素的分布极为接近,利用这—特性离子注入就可在所需的地方将晶格破坏,此外利用硼与磷的化学特性也可将重金属元素吸收.2.1.6反型井区注入工艺(RetrogradeWel1)在早期此工艺由炉管扩散或注入后驱动扩散而完成,但其不能在井区内形成优化的载流子分布,高性能的芯片要求硅片表面的载流子浓度低,而在硅片深度的某些部位要浓,这样既能提高芯片的运行速度,又能达到以上所述的反穿通,抑制死循环及吸取污染杂质的效果.由于在扩散时载流子的浓度是从硅片表面逐步向硅片内部降低的连续分布,这样的分布势必影响到硅片表面载流子的移动集虞电?蠢用2o年9居●■率而降低芯片的运营速度,为提高芯片的功能离子注入就成了必不可少的手段,新一代的CMOS技术已全部使用离子注入方式,当今的CMOS技术更采用双井反型工艺(Twin Retrogradewel1),它综合了以上所讨论的阈值电压调节注入,反穿通注入,井问绝缘注入,及埋层注入,构成一个完整的反型井层注入工艺链. 亚舍立科技(Axcelis)公司的高能注入机的设计,可提供连续注入(ChainImplant)技术,即将这些注入工艺步骤在一次装片中连续注入,这样既可提高产量,降低成本,还可提高产品性能,降低在硅片上的尘粒总数量.2.2多晶硅注入此注入工艺是为了降低多晶硅的电阻,是CMOS注入工艺中注入剂量最大的工艺.有的制成在长多晶硅的同时已掺入所需的元素,假如长多晶硅时没有掺杂,则要做多晶硅注入,再进行退火,注入后的元素在退火时在多晶硅中的扩散率与单晶硅相比会高出二个数量级,因此掺杂后的多晶硅的阻值与非掺杂的多晶硅相比会有大幅度的下降.此工艺因剂量很大,能量较低,在生产中一般都采用大束流离子注入机. 2.3源漏区注入工艺源漏区注入主要包括大角度晕环(Halo)注入,延伸(Extension)注入,源漏(Source—drain)及非晶体化(Pre-amorphouse)注入,此部分工艺技术要求越来越高,并与注入后的退火工艺有着密切的联系. 该部分的注入工艺其能量相对较低, 但剂量属中高范围,一般采用中束流及大束流注入机.2.3.1大角度注入工艺(Halo)Halo是大角度(>20度)四方向的中剂量离子注入工艺,它的主要功能是防止源漏相通,降低延伸区的结深及缩短沟道长度,有利于提高芯片的性能,一般在延伸注入工艺之后注入.为了使载流子分布更陡,以更有效的防止短沟道效应,最新的掺杂技术是用锑来替代砷,用铟来替代硼.2.3.2延伸注工艺(Extension)它先前也称作低剂量掺杂(LDD),它是在CMOS中注入能量最低的工艺,其作用是优化源漏问的电场分布,降低最高电场,在高阻与电阻区之间起一个衔接作用.其剂量随着沟道缩短而增加.线宽的变窄要求延伸区的结深越来越浅,晕环注入可对此有帮助.但还不够,尤其对n+井区,唯一可用的注入元素是质量很轻的硼,或稍高的BF,并在退火时由于存在过渡性扩散(TED),硼在退火时的扩散率很高,这就更要求注入的能量要非常低,所以如何在延伸区形成浅结是近年来注入工业界的最大课题.2.3.3源漏注入工艺(source-drain)源漏注入的剂量很大,是降低场效应管串型电阻的重要一环.与延伸注入工艺一样,现在源漏注入最大挑战是如何形成具有一定导电率的浅结,这是一个离子注入与快速退火的工艺优化问题,但最基本的要求是低能量注入.因其要求的剂量很大,这对离子注入机的生产率是一大考验,如何设计出在低能时能产生高电流是每个离子注入厂家的努力方向.2.3.4非晶体化注入工艺((pre-amorphouse)在源漏区还有一种注入工艺被有些厂家所采用,它就是非晶体化注入工艺,其注入元素主要有锗(Ge)和硅(Si),其中锗的使用比较广泛一些,因为其原子重量大,容易达到非晶体化效果,并能降低源漏区的接触电阻.非晶体化的目的主要是防止下—步注入的沟道效应,并可降低在退火时其掺杂元素激活的激活能.其不利之处在于难于消除在晶体与非晶体界面层的缺陷因而增加源漏区的漏电.3总结离子注入工艺的优化就是选择所需的掺杂元素和注入的能量,剂量及角度的过程,当今的离子注入工艺无论是从能量还是剂量涵盖很广,所以对设备的要求可大致分为高能,大束流及中束流.设备的合理选择及搭配就是要既能满足工艺要求,又能达到高效低成本的目的.亚舍立科技(Axcelis)公司是当今全球唯—提供整合注入相关工艺配套的半导体设备商,产品种类包括光刻胶定型机,去胶机,快速退火炉及全套离子注入系统,包括具有低能量功能的大束流注入机,中束流注入机及高能注入机,并可为用户提供整套设备和工艺服务.-■集成电路应用2oo2年9月。
半导体制造技术导论chapter8离子注入工艺

PPT文档演模板
半导体制造技术导论chapter8离子注 入工艺
热退火
•晶格原子
PPT文档演模板
•掺杂物原子
半导体制造技术导论chapter8离子注 入工艺
热退火
•晶格原子
PPT文档演模板
•掺杂物原子
半导体制造技术导论chapter8离子注 入工艺
• 离子束并非完美的平行,许多离子在穿入 基片之后立刻会和晶格原子发生许多的原 子核碰撞。一部分的离子可以沿着通道深 入基片,而很多其他离子则被阻滞成常态 的高斯分佈.
PPT文档演模板
半导体制造技术导论chapter8离子注 入工艺
损害制程
• 注入的离子转移能量给晶格原子
– 原子从晶格的束缚能释放出来
半导体制造技术导论chapter8离子注 入工艺
离子注入:气体系统
• 特殊的气体递送系统控制有害的气体 • 更换气体钢瓶需要特殊的训练 • 氩气用来吹除净化和离子束校正
PPT文档演模板
半导体制造技术导论chapter8离子注 入工艺
ቤተ መጻሕፍቲ ባይዱ 离子注入:电机系统
• 高压系统
– 决定控制接面深度的离子能量
快速加热步骤和高温炉退火
•多晶 硅 •硅
•RTP退火
•匣
极 •二
氧化
硅匣
极 •源极 / 漏极
•硅
•多晶 硅
•高温炉退 火
PPT文档演模板
半导体制造技术导论chapter8离子注 入工艺
问与答
• 为什么高温炉的温度无法像RTP系统一样 急速上升及冷却?
• 高温炉有非常高的热容量,需要非常高的 加热功率以快速升高温度。由于温度会过 高(overshoot)或是过低(undershoot),所以很 难做到快速升温而没有大的温度震盪.
离子注入技术(Implant)

能源等领域。
新能源
离子注入技术在太阳能电池、燃 料电池等新能源领域中也有广泛 应用,通过优化材料表面的性能, 提高新能源器件的效率和稳定性。
离子注入技术的发展历程
起源
离子注入技术最早起源于20世纪 50年代的美国贝尔实验室,最初 是为了解决半导体材料的掺杂问 题而发明的。
注入机的结构
注入机通常由离子束控制 装置、注入室、注入了材 料夹具等组成,以实现精 确控制和高效注入。
检测与控制系统
检测与控制系统的作用
检测与控制系统用于实时监测离子注入的过程和结果,同时对设备进行精确控制,确保 工艺参数的一致性和稳定性。
检测与控制系统的组成
检测与控制系统通常包括传感器、信号处理电路、控制电路和显示面板等组成,以实现 实时监测和控制。
离子注入技术(Implant)
• 离子注入技术概述 • 离子注入技术的基本原理 • 离子注入技术的主要设备 • 离子注入技术在半导体制造中的应
用 • 离子注入技术的挑战与未来发展
01
离子注入技术概述
定义与特点
定义
离子注入技术是一种将离子化的物质注入到固体材料表面的工艺,通过改变材 料表面的成分和结构,实现材料改性或制造出新材料的表面工程技术。
真空系统的组成
真空系统通常包括真空 室、机械泵、扩散泵、 分子泵等组成,以实现 高真空的获得和维持。
注入机
01
02
03
注入机的作用
注入机是离子注入技术的 关键设备之一,它能够将 离子束按照预设的参数注 入到材料表面。
注入方式
注入机通常采用定点注入、 扫描注入和均匀注入等方 式,以满足不同材料和工 艺的需求。
离子注入工艺 (课程设计)
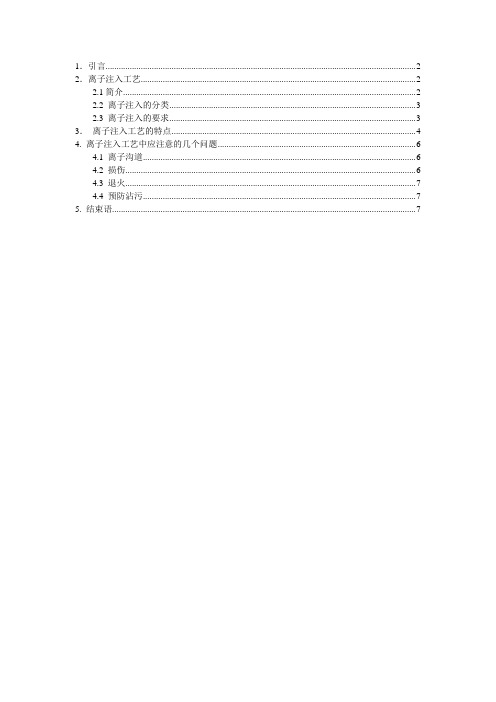
1.引言 (2)2.离子注入工艺 (2)2.1简介 (2)2.2 离子注入的分类 (3)2.3 离子注入的要求 (3)3.离子注入工艺的特点 (4)4. 离子注入工艺中应注意的几个问题 (6)4.1 离子沟道 (6)4.2 损伤 (6)4.3 退火 (7)4.4 预防沾污 (7)5. 结束语 (7)1.引言离子注入是现代集成电路制造中的一种非常重要的技术,其利用离子注入机实现半导体的掺杂,即将特定的杂质原子(Dopant)以离子加速的方式注入硅半导体晶体内改变其导电特性并最终形成晶体管结构。
随着半导体集成电路的高速发展,对工艺提出了更高的要求,特别是对关键工艺的影响更大。
本文对半导体集成电路工艺中的离子注入工艺的主要特点、工艺中存在的几个问题及在化合物半导体集成电路工艺中的应用等方面进行了重点阐述。
2.离子注入工艺2.1简介现代的半导体制造工艺中制造一个完整的半导体器件一般要用到许多步(15~25步)的离子注入。
离子注入的最主要工艺参数是杂质种类,注入能量和掺杂剂量。
杂质种类是指选择何种原子注入硅基体,一般杂质种类可以分为N型和P型两类,N型主要包括磷,砷,锑等,而P型则主要包括硼,铟等。
注入能量决定了杂质原子注入硅晶体的深度,高能量注入得深,而低能量注入得浅。
掺杂剂量是指杂质原子注入的浓度,其决定了掺杂层导电的强弱。
通常半导体器件的设计者需要根据具体的目标器件特性为每一步离子注入优化以上这些工艺参数。
图1给出了130nm器件上离子注入后和回火后的B、BF2的深度和浓度变化。
2.2 离子注入的分类离子注入设备根据具体的应用分为三类:中束流,大束流和高能量。
这三种离子注入设备在半导体工艺中各有其特殊的应用。
中束流(MC)离子注入设备用于那些掺杂剂量适中或较低但精度控制要求非常重要的掺杂工艺,其在半导体器件制造中的具体应用例如栅阀值调整(Threshold Adjust),Halo 注入等;大束流(HC)离子注入设备用于掺杂剂量很高且精度控制不重要的场合,例如源极,漏极的形成和多晶硅栅极的掺杂。
离子注入工艺PPT课件
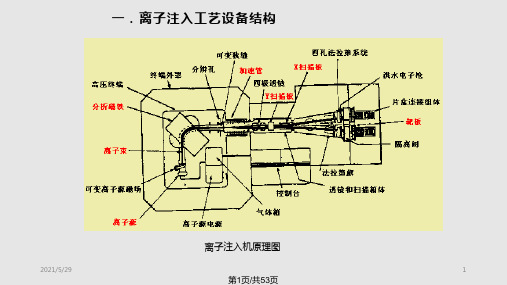
2021/5/29
8
第8页/共53页
•
•
当具有高能量的离子注入到固体靶面以后,这些高能粒子将与固体靶面的原子
与电子进行多次碰撞,这些碰撞将逐步削弱粒子的能量,最后由于能量消失而停止
运动,新城形成一定的杂质分布。
•
同时,注入离子和晶格原子相互作用,那些吸收了离子能量的电子,可能激
发或从原子之内游离,形成二次电子。
As, N), 能量(keV)
2.单位面积注入电荷:Qss =I t /A, I:注 入束流,t: 时间,A:扫描面积(园片尺 寸)
3.单位面积注入离子数(剂量)N:s
Ns = Qss/q =(I t) /(q A) 2 R
4.最大离子浓度:第22N页/M共5A3X页=
22
*注入离子分布
• •
N(x)=Nmax
2、可能沿某些方向由原子列包围成直通道--沟道,离子进入沟道时,沿沟道前进阻力小,射程要大
得多。
2021/5/29
27
第27页/共53页
3、 沟道效应的存在,将使得对注入离子在深度上难以控制,尤其对大规模集成电路制造更带来麻烦。 如MOS器件的结深通常只有0.4um左右,有了这种沟道效应万一注入距离超过了预期的深度,就使元器件 失效。因此,在离子注入时,要考虑到这种沟道效应,也就是说要抑止这种现象的产生。
2021/5/29
5
第5页/共53页
• (8)离子往往是通过硅表面上的薄膜注入到硅中,因此硅表面上的薄膜 起到了保护膜作用
• (9)化合物半导体是两种或多种元素按 一定组分构成的,这种材料经 高温处理时,组分可能发生变化。采用离子注入技术,基本不存在上述问 题,因此容易实现对化合物半导体的掺杂
半导体工艺-离子注入

半导体工艺--离子注入离子注入法掺杂相比扩散法掺杂来说,它的加工温度低、容易制作浅结、均匀的大面积注入杂质、易于自动化等优点。
目前,离子注入法已成为超大规模集成电路制造中不可缺少的掺杂工艺。
1.离子注入原理离子是原子或分子经过离子化后形成的,即等离子体,它带有一定量的电荷。
可通过电场对离子进行加速,利用磁场使其运动方向改变,这样就可以控制离子以一定的能量进入wafer内部达到掺杂的目的。
离子注入到wafer中后,会与硅原子碰撞而损失能量,能量耗尽离子就会停在wafer中某位置。
离子通过与硅原子的碰撞将能量传递给硅原子,使得硅原子成为新的入射粒子,新入射离子又会与其它硅原子碰撞,形成连锁反应。
杂质在wafer中移动会产生一条晶格受损路径,损伤情况取决于杂质离子的轻重,这使硅原子离开格点位置,形成点缺陷,甚至导致衬底由晶体结构变为非晶体结构。
2.离子射程离子射程就是注入时,离子进入wafer内部后,从表面到停止所经过的路程。
入射离子能量越高,射程就会越长。
投影射程是离子注入wafer内部的深度,它取决于离子的质量、能量,wafer的质量以及离子入射方向与晶向之间的关系。
有的离子射程远,有的射程近,而有的离子还会发生横向移动,综合所有的离子运动,就产生了投影偏差。
3.离子注入剂量注入剂量是单位面积wafer表面注入的离子数,可通过下面的公式计算得出 ,式中,Q 是剂量;I 是束流, 单位是安培;t 是注入时间,单位是秒;e 是电子电荷,1.6×10-19C ;n 是电荷数量;A 是注入面积,单位是 。
4.离子注入设备离子注入机体积庞大,结构非常复杂。
根据它所能提供的离子束流大小和能量可分为高电流和中电流离子注入机以 及高能量、中能量和低能量离子注入机。
离子注入机的主要部件有:离子源、质量分析器、加速器、聚焦器、扫描系统以及工艺室等。
(1)离子源离子源的任务是提供所需的杂质离子。
在合适的气压下,使含有杂质的气体受到电子碰撞而电离,最常用的杂质源有 和 等,(2)离子束吸取电极吸取电极将离子源产生的离子收集起来形成离子束。
离子注入工艺原理ppt课件

7
硅中离子注入能量(KeV)与射程(Å)的对 应关系
入射能量
杂质
B
RP
RP
P
RP
RP
As
RP
RP
20
714 276 255 90 151 34
40
1413 443 488 161 263 59
60
80
100 120 140 160
180
2074 2695 3275 3802 4284 4745 5177
溶解度的限制
4
离子注入的ห้องสมุดไป่ตู้论描述
在离子注入过程中被掺杂的材料一般称为靶,离子轰击靶时, 其中一部分离子在靶的表面被折射出,不能进入靶内,这部 分离子叫做散射离子,进入的部分离子叫做注入离子,为了 精确控制注入的深度,避免沟道效应,往往使靶片的晶轴方 向与入射离子束的方向由一定的角度。
核碰撞 注入离子与靶内原子核之间的相互碰撞 电子碰撞 注入离子与靶内自由电子以及束缚电子之间的碰
(2) 注入剂量增大,靶的晶格损伤越严重。
移位原子 移位阈能 能量淀积过程
12
由于轻离子和重离子引起的晶格损伤
轻离子冲击
重离子冲击
13
(三)、离子注入参数 1、剂量
Q It qnA
Q : 剂量,原子数 / cm2 ;I : 束流,库仑 / 秒 n:每个离子的电荷数;A:注入面积
2、射程:离子穿越硅片的总距离
缺点:缺陷不能完全消除,而且容易产生二次缺陷,杂质 电激活率不高,容易增加表面污染,高温容易导致杂质再分 布,破坏了离子注入的优点。
19
快速退火
优点:通过降低退火温度,缩短退火时间 脉冲激光退火
集成电路工艺基础——离子注入课件

2
通过离子注入技术,可以在光学材料中制造出各 种光电子器件,如激光器、光放大器、光调制器 等。
3
离子注入技术还可以用于制造光子晶体、光子集 成电路等新型光电子器件,提高光电子器件的性 能和集成度。
离子注入在传感器中的应用
传感器是实现智能化、自动化 的重要器件,离子注入技术在 传感器制造中也有着重要的应 用。
通过离子注入技术,可以在传 感器材料中制造出各种敏感元 件,如压力传感器、温度传感 器、气体传感器等。
离子注入技术还可以用于制造 生物传感器、化学传感器等新 型传感器,提高传感器的灵敏 度和稳定性。
CHAPTER
04
离子注入的未来发展
新型离子注入设备的研究
研发更高效、精确的 离子注入设备是未来 的重要研究方向。
与硅材料相比,化合物半导体材 料的离子注入工艺较为复杂,需
要更高的技术和设备条件。
离子注入化合物半导体材料在光 电子器件、高速电子器件和微波 器件等领域具有广泛的应用前景
。
离子注入金属材料
金属材料在集成电路制造中主要用于 互连线、电极和引脚的制造,离子注 入金属材料可以改变其表面特性和导 电性能。
离子注入硅材料的方法具有较高的精度和可重复性,可以实现对硅材料的微细加工 。
离子注入硅材料还可以提高硅材料的机械性能和化学稳定性,使其更适应于集成电 路制造中的各种工艺条件。
离子注入化合物半导体材料
化合物半导体材料是集成电路制 造中的另一种重要材料,离子注 入化合物半导体材料可以改变其
电子结构和光电性能。
开发具有自主知识产 权的离子注入设备, 打破国外技术垄断。
利用新材料和新技术 提高设备的稳定性和 可靠性,降低生产成 本。
离子注入与其他微纳加工技术的结合
离子注入最详细的课件演示文稿

质量分析器:不同的离子具有不同的质量与电荷,因而在质量分析
器磁场中偏转的角度不同,由此可分离出所需的杂质离子,且离子束很 纯。
加速器:为高压静电场,用来对离子束加速。该加速能量是决定离 子注入深度的一个重要参量。
中性束偏移器:利用偏移电极和偏移角度分离中性原子。 聚焦系统:将离子聚集成直径为数毫米的离子束。 偏转扫描系统:使离子束沿 x、y 方向扫描。 工作室(靶室):放置样品的地方,其位置可调。
qo
q m
Vf2 2d 2 B2Va
对于荷质比为 qo 的所需离子,可通过调节偏转电压 Vf 或偏转 磁场 B,使之满足下式,就可使这种离子不被偏转而通过光阑。
1
Vf dB(2qoVa )2 ,
或 B
Vf
1
d (2qoVa )2
通常是调节 Vf 而不是调节B。
第二十四页,共130页。
下面计算当荷质比为 qo 的离子不被偏转时,具有荷质比为qs = q/ms 的其它离子被偏转的程度。该种离子在 y 方向受到的加速度为
引
若改变 E2 的极性 ,则可排斥离
子而拉出电子,使这种源改变成电
子束源。
第十八页,共130页。
共晶合金 LMIS
通常用来对各种半导体进行离子注入掺杂的元素因为熔点高或蒸汽
压高而无法制成单体 LMIS 。
根据冶金学原理,由两种或多种金属组成的合金,其熔点会大大 低于组成这种合金的单体金属的熔点,从而可大大降低合金中金属处 于液态时的蒸汽压。
光阑2
1
Fm
qvB
qB
2qVa m
2
为向心力,使离子作圆周运动,其
1
1
半径为
r
mv qB
半导体工艺--离子注入

注入离子将能量转移给晶格原子 – 产生自由原子(间隙原子-空位缺陷对)
自由原子与其它晶格原子碰撞 – 使更多的晶格原子成为自由原子 – 直到所有自由原子均停止下来,损伤才停止
一个高能离子可以引起数千个晶格原子位移
9、退火:
退火:将完成离子注入的硅片在一定的温度下,经 过适当的热处理,则硅片上的损伤就可能得到消除, 少数载流子寿命以及迁移率也会不同程度的得到恢复, 杂质也得到一定比例的电激活。
2、离子束的性质:
离子束是一种带电原子或带电分子的束状流, 能被电场或磁场偏转,能在高压下加速而获得很高 的动能。
离子束的用途: 掺杂、曝光、刻蚀、镀膜、退火、净化、改性、 打孔、切割等。不同的用途需要不同的离子能量 E :
E < 10 KeV ,刻蚀、镀膜 E = 10 ~ 50 KeV,曝光 E > 50 KeV,注入掺杂
7、离子与衬底原子的相互作用:
注入离子与衬底原子的相互作用,决定了注入离 子的分布、衬底的损伤。
注入离子与靶原子的相互作用,主要有离子与电 子的相互作用,称为电子阻止。和离子与核的相互作 用,称为核阻止。核阻止主要表现为库仑散射。
在同样能量下,靶原子质量越大,核阻止越大,靶原 子质量越小电子阻止越大。
10、离子注入的 优缺点:
优点:
1、可控性好,离子注入能精确控制掺杂的浓度分布 和掺杂深度,因而适于制作极低的浓度和很浅的结深;
2、注入温度低,一般不超过 400℃,退火温度也在 650℃ 左右,避免了高温过程带来的不利影响,如结 的推移、热缺陷、硅片的变形等;
3、工艺灵活,可以穿透表面薄膜注入到下面的衬底 中,也可以采用多种材料作掩蔽膜,如 SiO2 、金属 膜或光刻胶等;
4、离子注入系统:
集成电路工艺之离子注入

▪ 缺陷的存在使得半导体中载流子的迁移率下降,少子寿命缩短, 影响器件性能。
❖ 杂质未激活
▪ 在注入的离子中,只有少量的离子处在电激活的晶格位置。
现在您浏览到是三十一页,共五十三页。
注入损伤
❖ 级联碰撞?
❖ 简单晶格损伤
▪ 孤立的点缺陷或缺陷群(注入离子每次传递给硅原子的能 量约等于移位阈能)
现在您浏览到是二十八页,共五十三页。
怎么解决???
现在您浏览到是二十九页,共五十三页。
浅结的形成
❖ 为了抑制MOS晶体管的穿通电流和减小器件的短沟效 应,要求减小CMOS的源/漏结的结深
❖ 形成硼的浅结较困难,目前采用的方法:
▪ 硼质量较轻,投影射程深,故采用BF2分子注入法
F的电活性、B的扩散系数高 B被偏转进入主晶轴的几率大
现在您浏览到是九页,共五十三页。
离子注入的优缺点
❖ 缺点:
▪ 产生的晶格损伤不易消除
▪ 很难进行很深或很浅的结的注入
▪ 高剂量注入时产率低
▪ 设备价格昂贵(约200万美金)
现在您浏览到是十页,共五十三页。
4.1 核碰撞和电子碰撞
❖ 高能离子进入靶后,不断与 靶中原子核和电子发生碰撞, 在碰撞时,注入离子的运动 方向发生偏转并损失能量, 因此具有一定初始能量的离 子注射进靶中后,将走过一 个非常曲折的道路,最后在 靶中某一点停止下来
注入离子在无定形靶中的分布
❖ 对于无定形靶(SiO2、Si3N4、光刻胶等),注入离子的纵向分 布可用高斯函数表示:
其中:
n(x)N exp1([xRp)2]
max
2 R
半导体制造技术--离子注入工艺
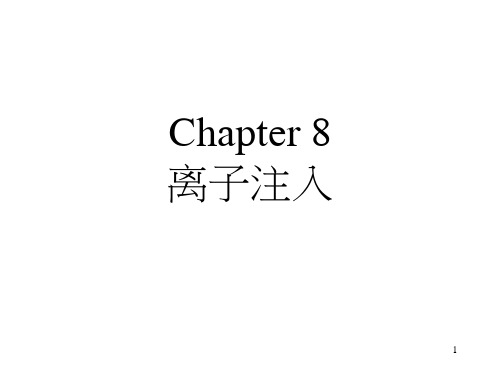
沉积掺杂氧化层
沉积掺杂氧化层 二氧化硅 硅基片
9
氧化
二氧化硅 硅基片
10
驱入
二氧化硅 硅基片
掺杂接面
11
剥除和清洗
二氧化硅 硅基片
掺杂接面
12
掺杂半导体:离子注入
• 用在原子和核的研究 • 1950年代观念便已被提出 • 在1970年代中期才被引进到半导体制造.
13
掺杂半导体:离子注入
制 • …...
21
阻滞机制
• 离子贯穿进入基片 • 和晶格原子发生碰撞 • 逐渐失去能量,最后停在基片里面 • 有两种阻滞机制
22
两种阻滞机制
• 原子核阻滞
– 与晶格原子的原子核碰撞 – 引起明显的散射 – 造成晶体结构的混乱和损害.
• 电子阻滞
– 和晶格原子的电子产生碰撞 – 入射离子路径几乎是不变的 – 能量的转换非常的小 – 晶格结构的损害可以忽略
P型硅
P+ n+
16
离子注入和扩散的比较
掺杂区域
二氧化硅
硅 扩散
光阻
硅
接面深度
离子注入
17
离子注入和扩散的比较
扩散
离子布植
高温, 硬光罩
低温, 光阻光罩
等向性掺杂物浓度
非等向性掺杂物轮廓
不能单独控制离子浓度和 能单独控制离子浓度和接
接面深度
面深度
批量制程
批量和单晶圆制程
18
离子注入控制
• 离子束电流和注入时间控制掺杂物的浓 度
I
II
III
原子核阻 滞
电子阻滞
阻滞功率
离子的速度
26
离子轨迹和投影射程
[理学]2011第八章离子注入
![[理学]2011第八章离子注入](https://img.taocdn.com/s3/m/21a061266137ee06eef9188a.png)
注入机分类
中低电流
大电流 高能
描述和应用
• 高纯离子束,电流小于 10mA。 • 束流能量一般< 180 keV。 • 多数情况下硅片固定,扫描粒子束。 • 穿通注入专用。 • 产生的粒子束电流 > 10 mA 大剂量注入最大能到
25 mA。 • 粒子束能量通常 <120 keV。 • 大多数情况下粒子束固定,硅片扫描。 • 超浅源漏区注入的超低能束流 (<4keV down to 200
掺杂浓度
离子注入机有中低电流、大电流之分
中低电流:0.1mA~10mA 注入剂量1011-1013ions/cm2
大电流:10~25mA 注入剂量大于1014ions/cm2
2.射程
射程:离子穿入硅片的总距离;
射程与能量
离子的射程与注入离子的能量有关,注入 离子的能量越高,意味着杂质原子能穿入 硅片越深,射程越大,投影射程越大。
a) 低掺杂浓度 (n–, p–) 和浅结深 (xj)
b) 高掺杂浓度 (n+, p+) 和深结深 (xj)
思考: 如何控制掺杂浓度和结深?
8.1.2离子注入参数:剂量和射程
离子源
等离子体 吸出组件
分析磁体 粒子束
加速管
工艺腔 扫描盘
离子注入机示意图
1. 剂 量
定义:单位面积硅片表面注入的离子数Q ,单位是原子每
加速系统的排列方式
1.先分析后加速 2.先加速后分析 3.前后加速,中间分析 4.前后分析,中间加速
§8.2 离子注入系统
离子源
等离子体 吸出组件
分析磁体 粒子束
加速管
工艺腔 扫描盘
高能注入机的线形加速器
- 1、下载文档前请自行甄别文档内容的完整性,平台不提供额外的编辑、内容补充、找答案等附加服务。
- 2、"仅部分预览"的文档,不可在线预览部分如存在完整性等问题,可反馈申请退款(可完整预览的文档不适用该条件!)。
- 3、如文档侵犯您的权益,请联系客服反馈,我们会尽快为您处理(人工客服工作时间:9:00-18:30)。
75As
2
2
51014
NMOS源/漏
31P
4
3.51015
56
阱区离子注入工艺
阱区离子注入工艺
57
调整阈值电压的离子注入工艺
调整阈值电压的离子注入工艺
58Biblioteka 多晶硅硼离子注入工艺多晶硅硼离子注入工艺
59
SDE离子注入工艺
源极/漏极延伸(SDE)离子注入工艺的形成过程
60
源极/漏极离子注入工艺
– 使用硬光刻版在指定区域注入掺杂而不需要光刻工艺,节省制造成本
63
粒子引起的电子—空穴对
粒子引起的电子—空穴对
64
SOI衬底上的MOSFET
SOI衬底上的MOSFET示意图
65
图形介质工艺流程
图形介质工艺流程示意图:(a) 刻蚀;(b) 离子注入
66
TaBN吸收模式EUV光刻版
具有阴影效应的吸收模式EUV光刻版
栅极和源极/漏极对准工艺
(a) 正常对准;(b) 对准失误
7
源极/漏极自对准工艺
源极/漏极自对准工艺
8
离子注入技术的优点
离子注入与扩散工艺比较
扩散
离子注入
高温,硬遮蔽层
低温,光刻胶作为遮蔽层
等向性掺杂轮廓
非等向性掺杂轮廓
不能独立控制掺杂浓度和结深
可以独立控制掺杂浓度和结深
批量工艺
批量及单晶圆工艺
折射率
N/A
反射率
N/A
熔点
938.3 ℃
沸点
2820 ℃
热传导系数
60 W/(m·K)
热膨胀系数
610-6 K-1
主要应用
Ge和SiGe以及半导体衬底,非晶硅注入用Ge离子源
主要来源
Ge, GeH4
16
离子注入技术简介
阻滞机制
不同的阻滞机制示意图
:原子核阻滞力;:电子阻滞力
18
阻滞机理和离子速率的关系
名称
砷
原子符号
As
原子序数
33
原子量
74.9216
固态密度
5.727 g/cm3
摩尔体积
12.95 cm3
音速
N/A
电阻系数
33 μΩ·cm
折射率
1.001,552
反射率
N/A
熔点
817 ℃ (27.5 atm)
沸点
614 ℃ (升华)
热传导系数
50 W/(m·K)
线性热膨胀系数
N/A
主要应用
扩散、离子注入、外延生长和多晶硅沉积N型掺杂物
射束电流控制及后段加速装置
43
离子束轨迹弯曲
离子束轨迹弯曲示意图
44
电荷中性化系统
• 晶圆电荷效应
– 离子注入将正电荷带入晶圆表面
– 带正电荷的晶圆表面排斥正离子
– 引起射线放大和不均匀离子注入
– 导致整个晶圆掺杂物分布不均匀
• 电荷中性化系统
– 等离子体注入系统
– 电子枪
– 电子淋浴器
晶圆电荷效应形成的
24
具有通道效应的掺杂物分布
具有通道效应的掺杂物分布
25
通道效应最小化方法
• 晶圆倾斜
– 在倾斜的晶圆上进行离子注入,角度通常为7°
– 可能会因光刻胶而产生阴影效应,可以通过晶圆转动和注入后退火过程
的小量掺杂物扩散解决
– 如果倾斜角度太小,掺杂物浓度可能会因为通道效应形成双峰分布
• 屏蔽氧化层
– 穿过一层非晶态二氧化硅薄膜进行注入
– 精确控制离子束的能量、电流和离子种类,控制机械部分和节流阀
• 射线系统
– 离子源、萃取电极、质谱仪、后段加速系统、等离子体注入系统、终端
分析仪
35
射线系统
离子注入机的射线系统
36
射线系统
• 离子源
– 热灯丝离子源、射频离子源、微波离子源
• 萃取系统
– 负偏压萃取电极将离子从离子源内的等离子体中抽出并加速到~50keV
源极/漏极离子注入工艺
61
离子注入在DRAM的应用
离子注入在DRAM单元阵列和连接方面的应用
SAC:自对准接触;SNC:存储节点接触;BLC:位线接触
62
离子注入技术的其他应用
• 绝缘体上硅(SOI)衬底制造
– 注氧隔离:高能量、高电流氧离子注入和高温退火
– 键合技术:高电流氢离子注入和晶圆键合
– 由离子的能量决定
• 离子浓度
– 由离子电流和注入的时间决定
54
离子注入在元器件中的应用
离子注入工艺
阱区注入
中度阱区注入
说明
高能量、低电流注入,形成阱区
大倾角注入,抑制结击穿效应
阈值电压调整注入
低能量、低电流注入,决定MOS晶体管的阈值电压
多晶硅栅重掺杂注入
重掺杂降低电阻系数,P/N型管栅极分别掺杂P/N型
28
损伤与热退火
• 晶格损伤
– 高能量离子与晶格原子的碰撞,可以使数千晶格原子的位置偏离
– 损伤效应与剂量、能量和离子质量有关,并随剂量和能量的增大而增加
– 若注入剂量过高,离子射程内的晶体结构会完全被破坏成非晶态
• 热退火
– 晶格损伤必须在热退火过程中修复成单晶结构并激活掺杂物原子
– 温度较低时,扩散过程快于退火过程
– 温度较高时,退火过程快于扩散过程
– 高温炉退火需要较长的时间,掺杂物原子的扩散十分严重
– 快速加热退火(RTA)能使掺杂物的扩散减小到符合缩小元器件的条件
29
单一离子造成的损伤
单一离子造成的损伤
30
离子注入后退火的晶格变化
离子注入后退火形成的晶格变化
31
高温炉和RTP退火中的扩散
高温炉和RTP退火工艺中的掺杂物扩散
• 元素污染
– 由掺杂物和其他元素的共同离子注入造成
– 相同的荷质比:94Mo++污染11BF2+,28N2+、CO+污染28Si+
– 接近的荷质比:75As+污染74Ge+、76Ge+,11BF+污染31P+
– 射线管和晶圆夹具材料的溅射:铝(Al)、碳(C)
• 工艺整合
69
晶圆带电
天线式电容器
70
粒子污染物
粒子污染在离子注入中的效应
71
离子注入工艺评估
• 离子注入工艺重要因素
– 掺杂物种类、结深、掺杂物浓度
• 二次离子质谱仪 (SIMS)
– 使用重离子束轰击样品表面并收集不同时间溅射的二次离子质谱
– 可测量掺杂种类、掺杂浓度和掺杂浓度的深度剖面
48
旋转轮式晶圆处理系统
旋转轮式晶圆处理系统示意图
49
旋转盘式晶圆处理系统
旋转盘式晶圆处理系统示意图
50
单晶圆离子注入系统
单晶圆离子注入系统示意图
(a) 扫描离子束;(b) 扩展离子束
51
射线阻挡器
射线阻挡器示意图
52
离子注入工艺过程
离子注入过程
• 掺杂物形态
– 由离子的种类决定
• 晶体管结深
阻滞机理和离子速率的关系
19
离子射程
离子的轨迹和投影射程
20
投影离子的分布区域
投影离子的分布区域
21
硅衬底中离子的投影射程
硅中掺杂离子的投影射程
22
掺杂离子所需阻挡层厚度
200 keV掺杂离子所需的阻挡层厚度
23
通道效应
通道效应
离子以合适的注入角度进入通道,只需有很少的能量就可以行进很长的距离
32
离子注入技术硬件设备
离子注入机
离子注入机示意图
34
离子注入机的组成
• 气体系统
– 降低危险气体渗漏风险,离子注入机内的气柜专门存储化学药品
• 电机系统
– 离子加速高压直流电源、离子源供电系统、质谱仪磁铁电源
• 真空系统
– 射线必须在高真空状态下减少带电离子和中性气体分子发生碰撞的概率
• 控制系统
610-6 K-1
主要应用
扩散、离子注入、外延生长和多晶硅沉积P型掺杂物
硅玻璃(BPSG)化学气相沉积掺杂物
主要来源
B, B2H6, BF3
15
锗元素参数列表
名称
锗
原子符号
Ge
原子序数
32
原子量
72.64
固态密度
5.323 g/cm3
摩尔体积
13.63 cm3
音速
5400 m/s
电阻系数
~50,000 μΩ·cm
9
离子注入和扩散掺杂过程
离子注入和扩散掺杂过程的比较
10
离子注入技术的应用
应用
离子
掺杂
N型:P, As, Sb;P型:B
预非晶化
Si, Ge
埋氧层
O
多晶硅阻挡层
N
11
磷元素参数列表
名称
磷
原子符号
P
原子序数
15
原子量
30.973,762
固态密度
1.823 g/cm3
摩尔体积
17.02 cm3
音速
– 注入离子与硅、氧原子碰撞散射,进入硅晶体的角度分布在较广的范围
• 预非晶态注入
– 高电流的硅或锗离子注入破坏单晶结构,在晶圆表面附近产生非晶态层
– 可以完全消除通道效应
– 增加了额外的离子注入步骤,需要热退火恢复其引起的晶体损伤
26
阴影效应和扩散处理
阴影效应和扩散处理