离子注入技术工艺-中文
离子注入工艺流程
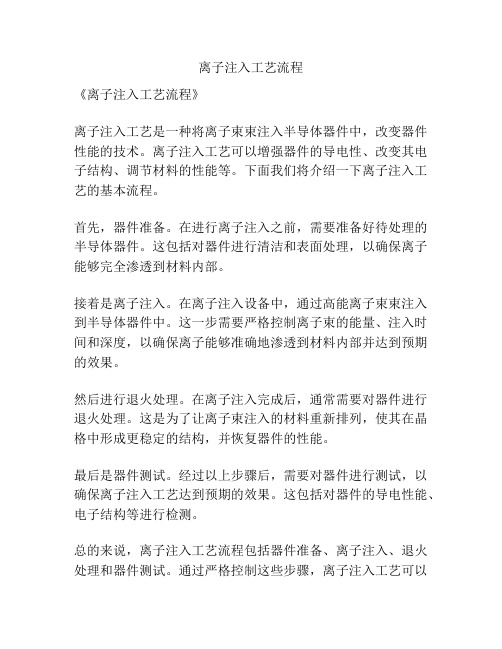
离子注入工艺流程
《离子注入工艺流程》
离子注入工艺是一种将离子束束注入半导体器件中,改变器件性能的技术。
离子注入工艺可以增强器件的导电性、改变其电子结构、调节材料的性能等。
下面我们将介绍一下离子注入工艺的基本流程。
首先,器件准备。
在进行离子注入之前,需要准备好待处理的半导体器件。
这包括对器件进行清洁和表面处理,以确保离子能够完全渗透到材料内部。
接着是离子注入。
在离子注入设备中,通过高能离子束束注入到半导体器件中。
这一步需要严格控制离子束的能量、注入时间和深度,以确保离子能够准确地渗透到材料内部并达到预期的效果。
然后进行退火处理。
在离子注入完成后,通常需要对器件进行退火处理。
这是为了让离子束注入的材料重新排列,使其在晶格中形成更稳定的结构,并恢复器件的性能。
最后是器件测试。
经过以上步骤后,需要对器件进行测试,以确保离子注入工艺达到预期的效果。
这包括对器件的导电性能、电子结构等进行检测。
总的来说,离子注入工艺流程包括器件准备、离子注入、退火处理和器件测试。
通过严格控制这些步骤,离子注入工艺可以
有效地改善半导体器件的性能,为半导体工业的发展提供重要支持。
半导体制造技术导论离子注入工艺

• 阈值电压控制:通过离子注入工艺调节PMOS和NMOS
区
的阈值电压
• NMOS器件:N型半导体作为沟道,P型半导体作为源漏
• 掺杂区形成:通过离子注入工艺形成PMOS和NMOS的
区
源漏区
离子注入工艺在光电二极管中的应用
光电二极管的结构特点
• P-N结:由P型半导体和N型半导体组成的结
• 光敏区:位于P-N结附近的区域,对光敏感
• 掺杂浓度均匀性:如何实现更均匀的掺杂,提高器件性能
• 注入损伤:离子注入过程中如何减少对半导体材料的损伤
• 工艺集成:如何将离子注入工艺与其他工艺集成,提高生产效率
解决方案
• 优化离子注入设备和工艺:提高掺杂浓度的均匀性和降低注入损伤
• 采用新型离子注入技术:如扫描离子注入、等离子体浸入离子注入等,提高工艺效
• 多离子注入技术的发展:实现多种元素的共注入,提高器件的性能和可靠性
离子注入工艺的发展方向
• 精确控制掺杂:实现更精确的浓度控制和更均匀的掺杂
• 降低能耗优化离子注入设备和工艺,降低能耗
• 环保减排:减少离子注入过程中的污染排放,提高环保水平
离子注入工艺面临的挑战及解决方案
离子注入工艺面临的挑战
果
• 加强工艺集成:与光刻、刻蚀等工艺进行集成,提高生产效率
离子注入工艺在未来半导体制造中的应用前景
离子注入工艺在集成电路制造中的应用
• 提高晶体管、二极管等器件的性能,提高集成电路的整体性能
• 实现新型器件的制作,如鳍式场效应晶体管(FinFET)等
离子注入工艺在光电二极管制造中的应用
• 提高光电二极管的光电转换效率,提高光电传感器的性能
• 大电流器件:需要承受大电流的器件
【doc】离子注入工艺简介
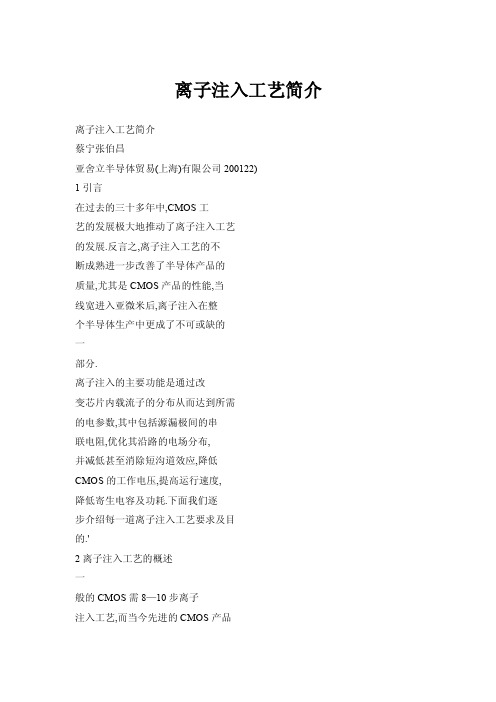
离子注入工艺简介离子注入工艺简介蔡宁张伯昌亚舍立半导体贸易(上海)有限公司200122)1引言在过去的三十多年中,CMOS工艺的发展极大地推动了离子注入工艺的发展.反言之,离子注入工艺的不断成熟进一步改善了半导体产品的质量,尤其是CMOS产品的性能,当线宽进入亚微米后,离子注入在整个半导体生产中更成了不可或缺的一部分.离子注入的主要功能是通过改变芯片内载流子的分布从而达到所需的电参数,其中包括源漏极间的串联电阻,优化其沿路的电场分布,并减低甚至消除短沟道效应,降低CMOS的工作电压,提高运行速度,降低寄生电容及功耗.下面我们逐步介绍每一道离子注入工艺要求及目的.'2离子注入工艺的概述一般的CMOS需8—10步离子注入工艺,而当今先进的CMOS产品更需20多步离子注入.根据在场效应管的位置,离子注入工艺可分为三大块:1)沟道区及井区(Channe1 andWel1)掺杂;2)多晶硅(Poly)注入:3)源漏区(SourceDrain)注入.2.1沟道及井区掺杂沟道区及井区的掺杂主要有阈值电压调节(V+Adjust)注入,反穿通(Anti-punchthrough)注入,埋层(BuriedLayer)注入,井问绝缘注入(Channe1Stop),井区反型(RetrogradeWel1)注入及吸收(Gettering)注入.这部分注入工艺的能量比较宽,但剂量属中低范围,所以此部分注入工艺基本上使用中束流及高能注入机.2.1.1阈值电压调节注入工艺(V.Adjust)阈值电压调节注入工艺是半导体工业中使用最早的离子注入技术工艺.由于在CMOS中N型井与P型井共存,它们的功能电压会有不同,V+ 注入是将所需的元素掺杂在门下方的沟道区内,改变电荷而得到所需的工作电压,使这两种井区共用一个闸门电压.高性能产品的N井区里传统的硼掺杂逐渐被铟(indium)注入所代替,其目的是使载子浓度分布更陡,以提高开关速度并降低功耗.2.1.2反击通注入工艺(Ant1一Dunchthr0ugh)该注入工艺的功能是防止源漏两极在沟道下面导通,因PN结深与载流子浓度成反比,如果沟道下部载流子浓度很低,在细线宽情况下源漏之间的PN结就会靠很近而容易被击通,增加此区域的载流子浓度就是为了降低耗尽层的厚度,使源漏不会在沟道下面导通,所以此注入要比阈值电压调节注入要更深一些.2.1.3井间绝缘注入工艺(Channel Stop)井间绝缘的注入是将杂质掺在用于隔开井区的绝缘栏的下方,此目的是为了提高井间寄生场效应管的阈值电压,使在正常的工作情形下此寄生三极管不会被导通而起到绝缘的效果.2.1.4埋层注入工艺(BuriedLayer)该工艺是要降低井区底部的电阻,以防芯片在运行中出现死循环(Latch—up)现象.井区内二个寄生的三极管(NPN&PNP)在一定的条件下可变成一个PNPN可控硅而形成自锁,埋层注入可降低PNP--极管的输出电阻,抬高死循环引发电流而彻底消除死循环现象.2.1.5吸取注入工艺(Gettering)它是在CM0S离子注入中能量最高的工艺,其目的是利用所注入的元素的化学特性和注后所形成的缺陷的物理特性来吸收井区里的其它杂质(如:重金属等)及晶格缺陷,以提高井区内,尤其是沟道区内的材料质量来提升产品性能.离子注入晶体后与原子核碰撞的可能性是和离子本身的能量成反比,所以在高能注入的条件下,有些轻元素如硼及磷,因注入而产生的缺陷分布与注入元素的分布极为接近,利用这—特性离子注入就可在所需的地方将晶格破坏,此外利用硼与磷的化学特性也可将重金属元素吸收.2.1.6反型井区注入工艺(RetrogradeWel1)在早期此工艺由炉管扩散或注入后驱动扩散而完成,但其不能在井区内形成优化的载流子分布,高性能的芯片要求硅片表面的载流子浓度低,而在硅片深度的某些部位要浓,这样既能提高芯片的运行速度,又能达到以上所述的反穿通,抑制死循环及吸取污染杂质的效果.由于在扩散时载流子的浓度是从硅片表面逐步向硅片内部降低的连续分布,这样的分布势必影响到硅片表面载流子的移动集虞电?蠢用2o年9居●■率而降低芯片的运营速度,为提高芯片的功能离子注入就成了必不可少的手段,新一代的CMOS技术已全部使用离子注入方式,当今的CMOS技术更采用双井反型工艺(Twin Retrogradewel1),它综合了以上所讨论的阈值电压调节注入,反穿通注入,井问绝缘注入,及埋层注入,构成一个完整的反型井层注入工艺链. 亚舍立科技(Axcelis)公司的高能注入机的设计,可提供连续注入(ChainImplant)技术,即将这些注入工艺步骤在一次装片中连续注入,这样既可提高产量,降低成本,还可提高产品性能,降低在硅片上的尘粒总数量.2.2多晶硅注入此注入工艺是为了降低多晶硅的电阻,是CMOS注入工艺中注入剂量最大的工艺.有的制成在长多晶硅的同时已掺入所需的元素,假如长多晶硅时没有掺杂,则要做多晶硅注入,再进行退火,注入后的元素在退火时在多晶硅中的扩散率与单晶硅相比会高出二个数量级,因此掺杂后的多晶硅的阻值与非掺杂的多晶硅相比会有大幅度的下降.此工艺因剂量很大,能量较低,在生产中一般都采用大束流离子注入机. 2.3源漏区注入工艺源漏区注入主要包括大角度晕环(Halo)注入,延伸(Extension)注入,源漏(Source—drain)及非晶体化(Pre-amorphouse)注入,此部分工艺技术要求越来越高,并与注入后的退火工艺有着密切的联系. 该部分的注入工艺其能量相对较低, 但剂量属中高范围,一般采用中束流及大束流注入机.2.3.1大角度注入工艺(Halo)Halo是大角度(>20度)四方向的中剂量离子注入工艺,它的主要功能是防止源漏相通,降低延伸区的结深及缩短沟道长度,有利于提高芯片的性能,一般在延伸注入工艺之后注入.为了使载流子分布更陡,以更有效的防止短沟道效应,最新的掺杂技术是用锑来替代砷,用铟来替代硼.2.3.2延伸注工艺(Extension)它先前也称作低剂量掺杂(LDD),它是在CMOS中注入能量最低的工艺,其作用是优化源漏问的电场分布,降低最高电场,在高阻与电阻区之间起一个衔接作用.其剂量随着沟道缩短而增加.线宽的变窄要求延伸区的结深越来越浅,晕环注入可对此有帮助.但还不够,尤其对n+井区,唯一可用的注入元素是质量很轻的硼,或稍高的BF,并在退火时由于存在过渡性扩散(TED),硼在退火时的扩散率很高,这就更要求注入的能量要非常低,所以如何在延伸区形成浅结是近年来注入工业界的最大课题.2.3.3源漏注入工艺(source-drain)源漏注入的剂量很大,是降低场效应管串型电阻的重要一环.与延伸注入工艺一样,现在源漏注入最大挑战是如何形成具有一定导电率的浅结,这是一个离子注入与快速退火的工艺优化问题,但最基本的要求是低能量注入.因其要求的剂量很大,这对离子注入机的生产率是一大考验,如何设计出在低能时能产生高电流是每个离子注入厂家的努力方向.2.3.4非晶体化注入工艺((pre-amorphouse)在源漏区还有一种注入工艺被有些厂家所采用,它就是非晶体化注入工艺,其注入元素主要有锗(Ge)和硅(Si),其中锗的使用比较广泛一些,因为其原子重量大,容易达到非晶体化效果,并能降低源漏区的接触电阻.非晶体化的目的主要是防止下—步注入的沟道效应,并可降低在退火时其掺杂元素激活的激活能.其不利之处在于难于消除在晶体与非晶体界面层的缺陷因而增加源漏区的漏电.3总结离子注入工艺的优化就是选择所需的掺杂元素和注入的能量,剂量及角度的过程,当今的离子注入工艺无论是从能量还是剂量涵盖很广,所以对设备的要求可大致分为高能,大束流及中束流.设备的合理选择及搭配就是要既能满足工艺要求,又能达到高效低成本的目的.亚舍立科技(Axcelis)公司是当今全球唯—提供整合注入相关工艺配套的半导体设备商,产品种类包括光刻胶定型机,去胶机,快速退火炉及全套离子注入系统,包括具有低能量功能的大束流注入机,中束流注入机及高能注入机,并可为用户提供整套设备和工艺服务.-■集成电路应用2oo2年9月。
微电子工艺 离子注入

称作投影射程。
内有多少条鱼浓度(个数域单位体积内有多少条鱼,…….离子源通过吸极电源把离子从离子源引出可变狭缝v⊕一个质量数为M的正离子,以速度v垂直于磁力线的方向进入磁场,受洛伦茨力的作用,在磁场中作匀速圆周运动的半径为R。
子离开分析仪电磁场的磁极平行平板电极⊕当离子束垂直进入均匀的正交电磁场时,将同时受到电场力和洛伦茨力的作用,这两个力的方向正好相反,只有在某个质量为M的离子在分析器中所受的电场力和洛伦茨力的数值相等时,不发生偏转而到达靶室,大于或小于M的离子则被偏转加速器加速离子,获得所需能量;高真空(<10-6Torr 静电加速器:调节离子能量静电透镜:离子束聚焦静电偏转系统:滤除中性粒子X方向扫描板Y方向扫描板扫描范围中性束偏转板+-的浓度比其它地方高。
终端台:控制离子束扫描和计量离子束扫描:扫描方式:静电扫描、机械扫描和混合扫描。
常用静电扫描和混合扫描。
静电光栅扫描适于中低束流机,机械扫描适于强束流机。
两种注入机扫描系统<110>向和偏转10°方向的晶体结构视图<111><100><110>40 kevP +31注入到硅中的浓度分布0.20.40.60.8 1.0µm43210 注入深度对准<110> 偏<110> 2°偏<110> 8°子在靶中行进的重要效应之一。
窗口边缘处浓度为同等深度窗口中心部位浓度的1/2离子越轻,阈值剂量越高;温度越高,阈值剂量越高。
扩散率提高,聚集成团,几种等时退火条件下,硅中注入硼离子的激活百分比。
离子注入技术(Implant)

离子注入技术摘要离子注入技术是当今半导体行业对半导体进行掺杂的最主要方法。
本文从对该技术的基本原理、基本仪器结构以及一些具体工艺等角度做了较为详细的介绍,同时介绍了该技术的一些新的应用领域。
关键字离子注入技术半导体掺杂1绪论离子注入技术提出于上世纪五十年代,刚提出时是应用在原子物理和核物理究领域。
后来,随着工艺的成熟,在1970年左右,这种技术被引进半导体制造行业。
离子注入技术有很多传统工艺所不具备的优点,比如:是加工温度低,易做浅结,大面积注入杂质仍能保证均匀,掺杂种类广泛,并且易于自动化。
离子注入技术的应用,大大地推动了半导体器件和集成电路工业的发展,从而使集成电路的生产进入了大规模及超大规模时代(ULSI)。
由此看来,这种技术的重要性不言而喻。
因此,了解这种技术进行在半导体制造行业以及其他新兴领域的应用是十分必要的。
2 基本原理和基本结构2.1 基本原理离子注入是对半导体进行掺杂的一种方法。
它是将杂质电离成离子并聚焦成离子束,在电场中加速而获得极高的动能后,注入到硅中而实现掺杂。
离子具体的注入过程是:入射离子与半导体(靶)的原子核和电子不断发生碰撞,其方向改变,能量减少,经过一段曲折路径的运动后,因动能耗尽而停止在某处。
在这一过程中,涉及到“离子射程”、“”等几个问题,下面来具体分析。
2.1.1离子射程图2.1.1(a ) 离子射程模型图图2.1.1(a )是离子射入硅中路线的模型图。
其中,把离子从入射点到静止点所通过的总路程称为射程;射程的平均值,记为R ,简称平均射程 ;射程在入射方向上的投影长度,记为p x ,简称投影射程;投影射程的平均值,记为p R ,简称平均投影射程。
入射离子能量损失是由于离子受到核阻挡与电子阻挡。
定义在位移x 处这两种能量损失率分别为n S 和e S :nn xdE S d =(1)ee e dE S k E dx==(2)则在dx 内总的能量损失为:()n e n e dE dE dE S S dx =+=+(3)P0000P 0nd d d d d R E E E ER x E x S S ===+⎰⎰⎰(4)n S 的计算比较复杂,而yxpx py pz d Ed E且无法得到解析形式的结果。
集成电路工艺第四章:离子注入
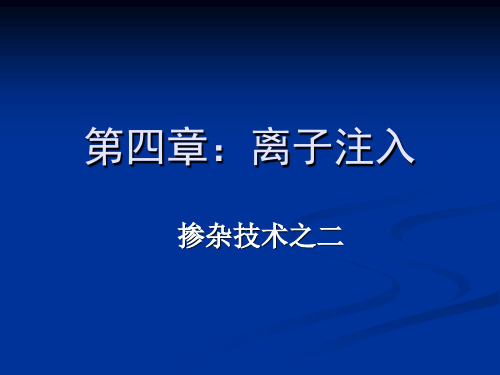
其中N为入射离子总数, 为第i 其中N为入射离子总数,RPi为第i个离子的投影射 程
离子投影射程的平均标准偏差△ 离子投影射程的平均标准偏差△RP为
其中N 其中N为入射离子总数 Rp 为平均投影射程 Rpi为第 Rpi为第i个离子的投影射程 为第i
离子注入浓度分布
LSS理论描述了注入离子在无定形靶中的浓度分布 LSS理论描述了注入离子在无定形靶中的浓度分布 为高斯分布其方程为
其中φ为注入剂量 其中 为注入剂量 χ为离样品表面的深度 为离样品表面的深度 Rp为平均投影射程 为平均投影射程 △Rp为投影射程的平均标准偏差 为投影射程的平均标准偏差
离子注入的浓度分布曲线
离子注入浓度分布的最大浓度Nmax 离子注入浓度分布的最大浓度Nmax
从上式可知,注入离子的剂量φ越大, 从上式可知,注入离子的剂量φ越大,浓度峰值越高 从浓度分布图看出, 从浓度分布图看出,最大浓度位置在样品内的平均投 影射程处
4.2 离子注入工艺原理
离子注入参数
注入剂量φ 注入剂量 注入剂量φ是样品表面单位面积注入的离子总数 是样品表面单位面积注入的离子总数。 注入剂量 是样品表面单位面积注入的离子总数。单 位:离子每平方厘米
其中I为束流,单位是库仑每秒( 其中 为束流,单位是库仑每秒(安 培) t为注入时间,单位是秒 为注入时间, 为注入时间 q为电子电荷,等于 ×10-19库仑 为电子电荷, 为电子电荷 等于1.6× n为每个离子的电荷数 为每个离子的电荷数 A为注入面积,单位为 2 —束斑 为注入面积, 为注入面积 单位为cm
2267 475 866 198 673 126
4587 763 1654 353 1129 207
6736 955 2474 499 1553 286
离子注入
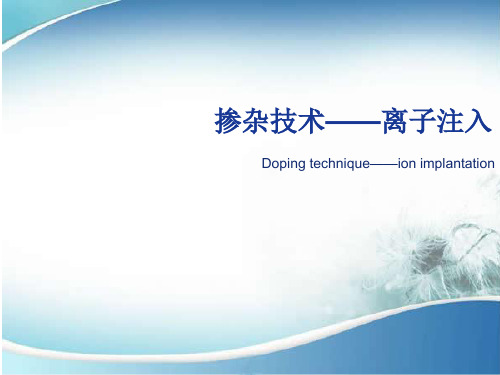
43
热退火过程中的扩散效应 热退火过程中的扩散效应
高斯分布的杂质在热退火过程中会使其分布展宽,偏 离注入时的分布,尤其是尾部,出现了较长的按指数 衰减的拖尾
44
快速热退火( RTA) 快速热退火( RTA) 传统热退火的缺点
不能完全消除缺陷,产生二次缺陷
28
解决办法
怎么解决???
29
阴影效应
离子束
掺杂区域
阴影区域
30
阴影效应消除
退火和扩散后
31
注入损伤过程 注入后发生了什么………
晶格损伤和无定型层
靶原子在碰撞过程中,获得能量,离开晶格位置,进 入间隙,形成间隙-空位缺陷对;
脱离晶格位置的靶原子与其它靶原子碰撞,也可使得 被碰靶原子脱离晶格位置。 缺陷的存在使得半导体中载流子的迁移率下降,少子 寿命缩短,影响器件性能。
非晶层的退火机理是与固相外延再生长过程相联系 在再生长过程中,Ⅴ族原子实际上与硅原子难以区分,它们在再 结晶的过程当中,作为替位原子被结合在晶格位置上。所以在相 对很低的温度下,杂质可被完全激活。
41
热退火过程中的扩散效应
热退火的温度与热扩散的温度相比,要低得多。
但是,对于注入区的杂质,即使在比较低的温度下
退火温度可以分为三个区域
• 500℃以下,电激活比例又随温度上升而增加 • 500~600℃范围内,出现逆退火特性
– 晶格损伤解离而释放出大量的间隙Si原子,这些间隙Si原 子与替位B原子接近时,可以相互换位,使得B原子进入晶 格间隙,激活率下降。
• 600℃以上,电激活比例又随温度上升而增加
39
核碰撞和电子碰撞
离子注入法介绍
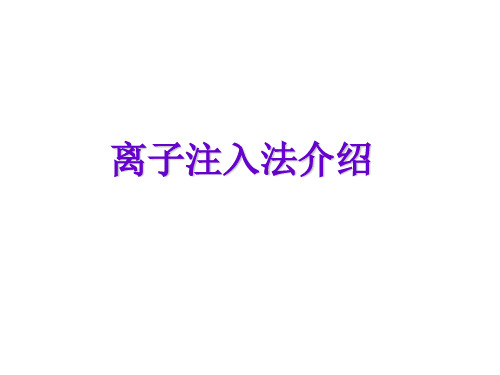
平行于主晶轴时 1、沟道效应:在单晶靶中,当离子速度方向平行于主晶轴时, 沟道效应: 单晶靶中 当离子速度方向平行于主晶轴 有部分离子可能会行进很长距离 造成较深的杂质分布。 有部分离子可能会行进很长距离,造成较深的杂质分布。 很长距离,
当离子速度方向与晶轴方向夹角远大于临界角 远大于临界角时 ■ 当离子速度方向与晶轴方向夹角远大于临界角时, 沟道效应很小。 沟道效应很小。
当剂量固定时,束流越大,扫描时间越短, 当剂量固定时,束流越大,扫描时间越短,机器产能越高 扫描时间太短,会影响注入的均匀性(一般最短扫描时间l0s) 扫描时间太短,会影响注入的均匀性(一般最短扫描时间l0s)
(6)杂质剂量与杂质浓度的关系 杂质剂量与杂质浓度 剂量与杂质浓度的关系
三、射程与入射离子的分布
■
决定引出离子的能量(速度) 决定引出离子的能量(速度)
(2)质量分析器: 质量分析器:
■
选择注入所需的杂质成分(B+) 选择注入所需的杂质成分(B+)
分析磁铁:磁场方向垂直于离子束的速度方向 方向垂直于离子束的速度方向 分析磁铁:磁场方向垂直于离子束的
离子运动路径: 离子运动路径:
离子运动速率: 离子运动速率: 质量m+δ 的离子产生的位移量 质量m+δm的离子产生的位移量
气态源: 或固体源) 气态源: (或固体源) BF3 AsH3 PH3 SiH4 H2
■
放电室:低气压、 放电室:低气压、分解离化气体 BF3 → B,B+,BF2+,F+, B+, F+, …… 引出狭缝:负电位,吸引出离子 引出狭缝:负电位,
离子束流量(最大mA量级) 离子束流量(最大mA量级 量级) 吸极电压Vext:约15~30KV, 吸极电压V 15~30KV,
离子注入工艺 (课程设计)
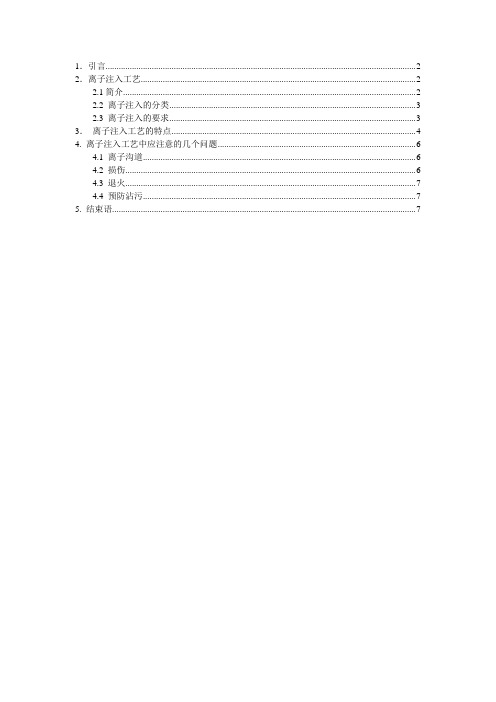
1.引言 (2)2.离子注入工艺 (2)2.1简介 (2)2.2 离子注入的分类 (3)2.3 离子注入的要求 (3)3.离子注入工艺的特点 (4)4. 离子注入工艺中应注意的几个问题 (6)4.1 离子沟道 (6)4.2 损伤 (6)4.3 退火 (7)4.4 预防沾污 (7)5. 结束语 (7)1.引言离子注入是现代集成电路制造中的一种非常重要的技术,其利用离子注入机实现半导体的掺杂,即将特定的杂质原子(Dopant)以离子加速的方式注入硅半导体晶体内改变其导电特性并最终形成晶体管结构。
随着半导体集成电路的高速发展,对工艺提出了更高的要求,特别是对关键工艺的影响更大。
本文对半导体集成电路工艺中的离子注入工艺的主要特点、工艺中存在的几个问题及在化合物半导体集成电路工艺中的应用等方面进行了重点阐述。
2.离子注入工艺2.1简介现代的半导体制造工艺中制造一个完整的半导体器件一般要用到许多步(15~25步)的离子注入。
离子注入的最主要工艺参数是杂质种类,注入能量和掺杂剂量。
杂质种类是指选择何种原子注入硅基体,一般杂质种类可以分为N型和P型两类,N型主要包括磷,砷,锑等,而P型则主要包括硼,铟等。
注入能量决定了杂质原子注入硅晶体的深度,高能量注入得深,而低能量注入得浅。
掺杂剂量是指杂质原子注入的浓度,其决定了掺杂层导电的强弱。
通常半导体器件的设计者需要根据具体的目标器件特性为每一步离子注入优化以上这些工艺参数。
图1给出了130nm器件上离子注入后和回火后的B、BF2的深度和浓度变化。
2.2 离子注入的分类离子注入设备根据具体的应用分为三类:中束流,大束流和高能量。
这三种离子注入设备在半导体工艺中各有其特殊的应用。
中束流(MC)离子注入设备用于那些掺杂剂量适中或较低但精度控制要求非常重要的掺杂工艺,其在半导体器件制造中的具体应用例如栅阀值调整(Threshold Adjust),Halo 注入等;大束流(HC)离子注入设备用于掺杂剂量很高且精度控制不重要的场合,例如源极,漏极的形成和多晶硅栅极的掺杂。
半导体离子注入原理及工艺

半导体离子注入原理及工艺1. 引言1.1 概述本文将深入探讨半导体离子注入原理及工艺。
离子注入作为一种重要的半导体加工技术,广泛应用于集成电路制造和材料改性领域。
通过向半导体材料中注入特定类型和能量的离子,可以实现掺杂调节、PN结修复、特殊结构制造等目标。
1.2 文章结构本文共分为五个部分进行论述。
首先,在引言部分,我们将介绍整篇文章的概述、结构以及目的。
接下来,在第二部分,我们将详细讲解半导体离子注入原理,包括对半导体材料的概述、离子注入原理的介绍以及离子注入设备和工艺流程。
第三部分将阐述影响离子注入工艺控制的因素,包括能量控制因素、剂量控制因素和温度控制因素。
在第四部分,我们将重点探讨离子注入在半导体加工中的应用与优势,包括PN结形成与修复、掺杂调节与电性能优化以及特殊结构和器件应用方面的内容。
最后,在结论与展望部分,我们将对全文进行总结,并对未来的研究方向和发展趋势进行展望。
1.3 目的本文旨在全面介绍半导体离子注入原理及工艺,让读者了解离子注入技术在半导体加工中的重要性和应用价值。
通过对离子注入原理、工艺控制因素以及应用优势的深入分析,希望读者能够全面了解并掌握该领域的基础知识,为进一步研究和实践提供参考和指导。
同时,本文也将为行业相关人士提供有益的信息和思路,促进半导体制造技术的发展与创新。
2. 半导体离子注入原理2.1 半导体材料概述半导体是一种具有介于导电体和绝缘体之间的电阻特性的材料。
常见的半导体材料包括硅、锗和砷化镓等。
这些材料中,原子结构具有特殊的能带结构,使得它们在一定条件下可以表现出较好的电导性能。
2.2 离子注入原理介绍离子注入是一种将高能量离子引入半导体材料中的技术。
其原理基于离子与半导体材料之间发生相互作用,从而改变材料内部的物理和化学性质。
在离子注入过程中,离子源产生高能量的正或负离子束,并通过加速装置使得这些离子获得足够高的动能。
这些高能量离子穿过空气以及其他保护层,在最终进入半导体材料前经过滤波等处理。
§4离子注入工艺

2019/11/17
9
当具有高能量的离子注入到固体靶面以 后,这些高能粒子将与固体靶面的原子与电 子进行多次碰撞,这些碰撞将逐步削弱粒子 的能量,最后由于能量消失而停止运动,新 城形成一定的杂质分布。
同时,注入离子和晶格原子相互作用, 那些吸收了离子能量的电子,可能激发或从 原子之内游离,形成二次电子。
2019/11/17
11
在一般情况下,杂质浓度最大值在距离 表面0.1um处,其分布有一点像高斯分布, 是由于杂质被电场加速注入到硅片内后,受 到硅原子的阻挡,使其动能完全消失,停留 在原位。但由于杂质离子具有的能量是不均 匀的,也就是使杂质离子的能量有大有小, 这样就形成了按一定的曲线分布,能量大和 能量小的都是少数,而能量近似相等的居多 数。当然注入后,能量最大的注入深,能量 小的注入浅。
2019/11/17
40
2.硼的退火特性
1 区单调上升:点缺陷、
陷井缺陷消除、自由 载流子增加
2 区出现反退火特性: 代位硼减少,淀积在 位错上
3 区单调上升
剂量越大,所需退火 温度越高。
2019/11/17
41
3.磷的退火特性
杂质浓度达1015以上时出 现无定形硅退火温度达到
600℃~800℃
7
基个概念:
(1)靶:被掺杂的材料。 (2)一束离子轰击靶时,其中一部分
离子在靶面就被反射,不能进入靶内, 称这部分离子为散射离子,进入靶内的 离子成为注入离子。 (3)非晶靶成为无定形靶,本章所涉 及道德靶材料,都是按无定形来考虑。
2019/11/17
8
三、离子注入原理
“离子” 是一种经离化的原子和分子,也称
“等离子体”,它带有一定量的电荷。“等离子 发生器”已广泛应用到CVD、金属镀膜、干法刻 蚀、光刻胶的去除等工艺中,而在离子注入的设 备中,它被用来制造工艺所要注入的离子。因为 离子带电荷,可以用加速场进行加速,并且借助 于磁场来改变离子的运动方向。当经加速后的离 子碰撞一个固体靶面之后,离子与靶面的原子将 经历各种不同的交互作用,如果离子“够重”, 则大多数离子将进入固体里面去。反之,许多离 子将被靶面发射。
离子注入技术(Implant)
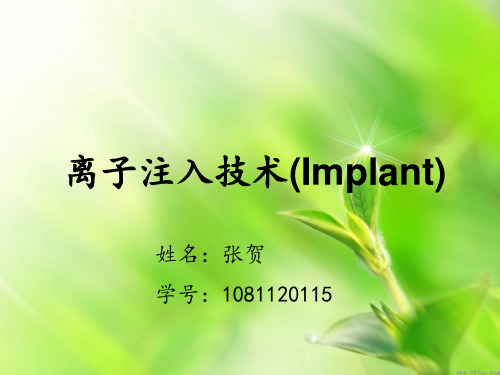
GSD/200E2离子注入机技术指标 3.160KeV注入机的最大束流
离子注入机设备与发展
离子注入机设备与发展
目前最大的几家IMP设备厂商是VARIAN(瓦 里安 ), AXCELIS, AIBT(汉辰科技 ), 而全球最大的设备厂商AMAT(应用材料)基 本退出了IMPLANTER的领域,高能离子注入 机以AXCELIS为主,主要为批量注入,而 Varian则占领了Single的市场 。 22nm以下的离子注入机
基本结构:离子注入系统(传统) 基本结构:离子注入系统(传统)
离子源: 离子源:用于离化杂质的容器。常用的杂质 源气体有 BF3、 AsH3 和 PH3 等。 质量分析器: 质量分析器:不同离子具有不同的电荷质量 比,因而在分析器磁场中偏转的角度不同,由 此可分离出所需的杂质离子,且离子束很纯。 加速器: 加速器:为高压静电场,用来对离子束加速。 该加速能量是决定离子注入深度的一个重要参 量(离子能量为100keV量级)。 中性束偏移器: 中性束偏移器:利用偏移电极和偏移角度分 离中性原子。
1、离子注入将在靶中产生大量晶格缺陷; 离子注入将在靶中产生大量晶格缺陷; 2、离子注入难以获得很深的结(一般在 离子注入难以获得很深的结(
1um以 内,例如对于100keV离子的平均射程的典型值约为0.1um );
离子注入的生产效率比扩散工艺低; 3、离子注入的生产效率比扩散工艺低; 离子注入系统复杂昂贵。 4、离子注入系统复杂昂贵。
离子注入技术(Implant) 离子注入技术
姓名:张贺 学号:1081120115
1 综述 2 基本原理和基本结构 3 技术指标 4 应用及结论
1
综述 • 最早应用于原子物理和核物理研究 • 提出于1950’s • 1970’s中期引入半导体制造领域
离子注入

原理
等离子体基离子注入PBⅡ装置示意图离子注入技术又是近30年来在国际上蓬勃发展和广泛应用的一种材料表 面改性技术。其基本原理是:用能量为100keV量级的离子束入射到材料中去,离子束与材料中的原子或分子将发 生一系列物理的和化学的相互作用,入射离子逐渐损失能量,最后停留在材料中,并引起材料表面成分、结构和 性能发生变化,从而优化材料表面性能,或获得某些新的优异性能。 此项技术由于其独特而突出的优点,已经 在半导体材料掺杂,金属、陶瓷、高分子聚合物等的表面改性上获得了极为广泛的应用,取得了巨大的经济效益 和社会效益。
集成电路前道制程中有许多光刻层之后的工艺是离子注入(ion implantation),这些光刻层被称为离子注 入光刻层(implant layers)。离子注入完成后,晶圆表面的光刻胶必须被清除掉,清除离子注入后的光刻胶是 光刻工艺中的一个难点。
优势
高能离子注入的优势 多样性:原则上任何元素都可以作为注入离子;形成的结构可不受热力学参数(扩散、溶解度等)限制; 不改变:不改变工件的原有尺寸和粗糙度等;适合于各类精密零件生产的最后一道工序; 牢固性:注入离子直接和材料表面原子或分子结合,形成改性层,改性层和基底材料没有清晰的界面,结合 牢靠,不存在脱落的现象; 不受限:注入过程在材料温度低于零下、高到几百上千度都可以进行;可对那些普通方法不能处理的材料进 行表面强化,如塑料、回火温度低的钢材等;
(2)热挤压和注塑模具,可使能耗降低20%左右,延长使用寿命10倍左右;
(3)精密运动耦合部件,如抽气泵定子和转子,陀螺仪的凸轮和卡板,活塞、轴承、齿轮、涡轮涡杆等,可 大幅度地降低摩擦系数,提高耐磨性和耐蚀性,延长使用寿命最多可以达到100倍以上;
(4)挤压合成纤维和光导纤维的精密喷嘴,可以大大提高其抗磨蚀性和使用寿命;
半导体工艺--离子注入

注入离子将能量转移给晶格原子 – 产生自由原子(间隙原子-空位缺陷对)
自由原子与其它晶格原子碰撞 – 使更多的晶格原子成为自由原子 – 直到所有自由原子均停止下来,损伤才停止
一个高能离子可以引起数千个晶格原子位移
9、退火:
退火:将完成离子注入的硅片在一定的温度下,经 过适当的热处理,则硅片上的损伤就可能得到消除, 少数载流子寿命以及迁移率也会不同程度的得到恢复, 杂质也得到一定比例的电激活。
2、离子束的性质:
离子束是一种带电原子或带电分子的束状流, 能被电场或磁场偏转,能在高压下加速而获得很高 的动能。
离子束的用途: 掺杂、曝光、刻蚀、镀膜、退火、净化、改性、 打孔、切割等。不同的用途需要不同的离子能量 E :
E < 10 KeV ,刻蚀、镀膜 E = 10 ~ 50 KeV,曝光 E > 50 KeV,注入掺杂
7、离子与衬底原子的相互作用:
注入离子与衬底原子的相互作用,决定了注入离 子的分布、衬底的损伤。
注入离子与靶原子的相互作用,主要有离子与电 子的相互作用,称为电子阻止。和离子与核的相互作 用,称为核阻止。核阻止主要表现为库仑散射。
在同样能量下,靶原子质量越大,核阻止越大,靶原 子质量越小电子阻止越大。
10、离子注入的 优缺点:
优点:
1、可控性好,离子注入能精确控制掺杂的浓度分布 和掺杂深度,因而适于制作极低的浓度和很浅的结深;
2、注入温度低,一般不超过 400℃,退火温度也在 650℃ 左右,避免了高温过程带来的不利影响,如结 的推移、热缺陷、硅片的变形等;
3、工艺灵活,可以穿透表面薄膜注入到下面的衬底 中,也可以采用多种材料作掩蔽膜,如 SiO2 、金属 膜或光刻胶等;
4、离子注入系统:
离子注入工艺,靶材料

离子注入工艺,靶材料
离子注入工艺是一种将离子束加速并注入到固体材料中的技术,用于改变材料的物理、化学和电学性质。
在离子注入工艺中,靶材料是被注入离子的固体材料。
靶材料可以是各种类型的半导体、金属、陶瓷或其他材料。
选择靶材料的类型取决于具体的应用和所需的改性效果。
对于半导体行业,常用的靶材料包括硅、锗、砷化镓等。
离子注入可以用于改变半导体的导电性、掺杂浓度、阈值电压等性质,以实现器件性能的调控。
在金属材料领域,离子注入可以用于改善材料的硬度、耐磨性、耐腐蚀性等性质。
靶材料可以是钢、铝、钛等金属。
在陶瓷材料方面,离子注入可以用于改变陶瓷的光学、电学和机械性能。
靶材料可以是氧化铝、氮化硅等陶瓷材料。
除了上述材料,还有许多其他类型的靶材料可以用于离子注入工艺,具体选择取决于应用需求和目标性质的改变。
需要注意的是,离子注入工艺是一种高精度的技术,需要在专业的实验环境中进行,以确保注入离子的准确性和均匀性。
半导体工艺-离子注入(精)
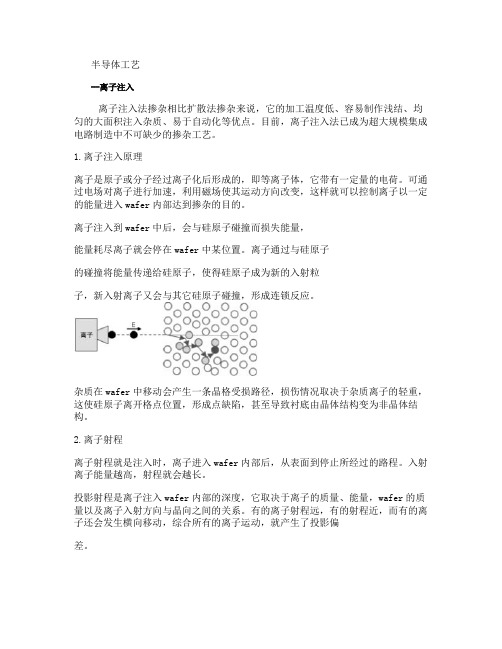
半导体工艺--离子注入离子注入法掺杂相比扩散法掺杂来说,它的加工温度低、容易制作浅结、均匀的大面积注入杂质、易于自动化等优点。
目前,离子注入法已成为超大规模集成电路制造中不可缺少的掺杂工艺。
1.离子注入原理离子是原子或分子经过离子化后形成的,即等离子体,它带有一定量的电荷。
可通过电场对离子进行加速,利用磁场使其运动方向改变,这样就可以控制离子以一定的能量进入wafer内部达到掺杂的目的。
离子注入到wafer中后,会与硅原子碰撞而损失能量,能量耗尽离子就会停在wafer中某位置。
离子通过与硅原子的碰撞将能量传递给硅原子,使得硅原子成为新的入射粒子,新入射离子又会与其它硅原子碰撞,形成连锁反应。
杂质在wafer中移动会产生一条晶格受损路径,损伤情况取决于杂质离子的轻重,这使硅原子离开格点位置,形成点缺陷,甚至导致衬底由晶体结构变为非晶体结构。
2.离子射程离子射程就是注入时,离子进入wafer内部后,从表面到停止所经过的路程。
入射离子能量越高,射程就会越长。
投影射程是离子注入wafer内部的深度,它取决于离子的质量、能量,wafer的质量以及离子入射方向与晶向之间的关系。
有的离子射程远,有的射程近,而有的离子还会发生横向移动,综合所有的离子运动,就产生了投影偏差。
3.离子注入剂量注入剂量是单位面积wafer表面注入的离子数,可通过下面的公式计算得出,式中,Q是剂量;I是束流,单位是安培;t是注入时间,单位是秒;e是电子电荷,1.6×10-19C;n是电荷数量;A是注入面积,单位是。
4.离子注入设备离子注入机体积庞大,结构非常复杂。
根据它所能提供的离子束流大小和能量可分为高电流和中电流离子注入机以及高能量、中能量和低能量离子注入机。
离子注入机的主要部件有:离子源、质量分析器、加速器、聚焦器、扫描系统以及工艺室等。
(1)离子源离子源的任务是提供所需的杂质离子。
在合适的气压下,使含有杂质的气体受到电子碰撞而电离,最常用的杂质源有和等,(2)离子束吸取电极吸取电极将离子源产生的离子收集起来形成离子束。
离子注入工艺
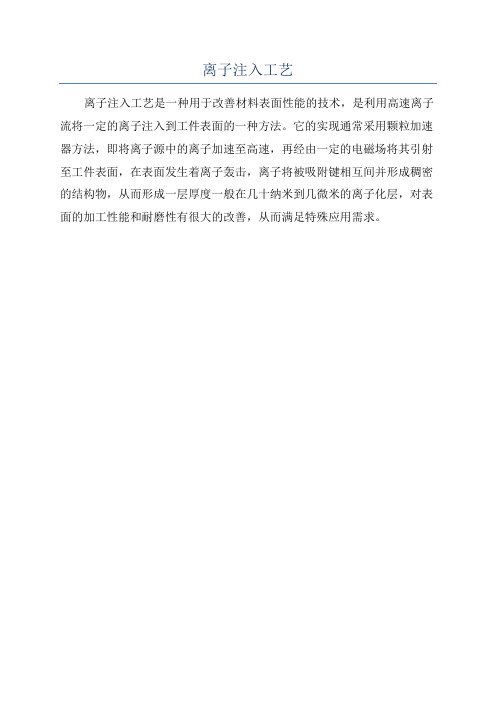
离子注入工艺
离子注入工艺是一种用于改善材料表面性能的技术,是利用高速离子流将一定的离子注入到工件表面的一种方法。
它的实现通常采用颗粒加速器方法,即将离子源中的离子加速至高速,再经由一定的电磁场将其引射至工件表面,在表面发生着离子轰击,离子将被吸附键相互间并形成稠密的结构物,从而形成一层厚度一般在几十纳米到几微米的离子化层,对表面的加工性能和耐磨性有很大的改善,从而满足特殊应用需求。
离子注入技术
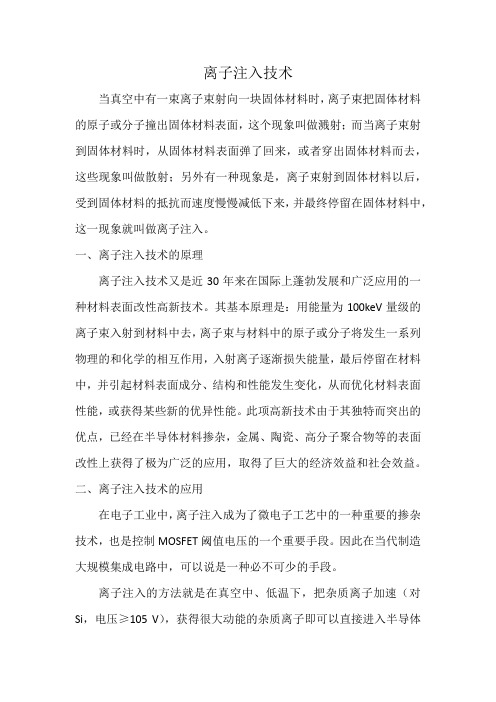
离子注入技术当真空中有一束离子束射向一块固体材料时,离子束把固体材料的原子或分子撞出固体材料表面,这个现象叫做溅射;而当离子束射到固体材料时,从固体材料表面弹了回来,或者穿出固体材料而去,这些现象叫做散射;另外有一种现象是,离子束射到固体材料以后,受到固体材料的抵抗而速度慢慢减低下来,并最终停留在固体材料中,这一现象就叫做离子注入。
一、离子注入技术的原理离子注入技术又是近30年来在国际上蓬勃发展和广泛应用的一种材料表面改性高新技术。
其基本原理是:用能量为100keV量级的离子束入射到材料中去,离子束与材料中的原子或分子将发生一系列物理的和化学的相互作用,入射离子逐渐损失能量,最后停留在材料中,并引起材料表面成分、结构和性能发生变化,从而优化材料表面性能,或获得某些新的优异性能。
此项高新技术由于其独特而突出的优点,已经在半导体材料掺杂,金属、陶瓷、高分子聚合物等的表面改性上获得了极为广泛的应用,取得了巨大的经济效益和社会效益。
二、离子注入技术的应用在电子工业中,离子注入成为了微电子工艺中的一种重要的掺杂技术,也是控制MOSFET阈值电压的一个重要手段。
因此在当代制造大规模集成电路中,可以说是一种必不可少的手段。
离子注入的方法就是在真空中、低温下,把杂质离子加速(对Si,电压≥105 V),获得很大动能的杂质离子即可以直接进入半导体中;同时也会在半导体中产生一些晶格缺陷,因此在离子注入后需用低温进行退火或激光退火来消除这些缺陷。
离子注入的杂质浓度分布一般呈现为高斯分布,并且浓度最高处不是在表面,而是在表面以内的一定深度处。
离子注入能精确控制杂质的总剂量、深度分布和面均匀性,而且是低温工艺(可防止原来杂质的再扩散等),同时可实现自对准技术(以减小电容效应)。
三、离子注入技术的优点作为一种材料表面工程技术,离子注入技术具有以下一些其它常规表面处理技术难以达到的独特优点:(1)它是一种纯净的无公害的表面处理技术;(2)无需热激活,无需在高温环境下进行,因而不会改变工件的外形尺寸和表面光洁度;(3)离子注入层由离子束与基体表面发生一系列物理和化学相互作用而形成的一个新表面层,它与基体之间不存在剥落问题;(4)离子注入后无需再进行机械加工和热处理。
- 1、下载文档前请自行甄别文档内容的完整性,平台不提供额外的编辑、内容补充、找答案等附加服务。
- 2、"仅部分预览"的文档,不可在线预览部分如存在完整性等问题,可反馈申请退款(可完整预览的文档不适用该条件!)。
- 3、如文档侵犯您的权益,请联系客服反馈,我们会尽快为您处理(人工客服工作时间:9:00-18:30)。
离子注入技术工艺
中国科学院半导体研究所离子注入组
我们的离子注入机是中国电子科技集团公司第四十八研究所研制的LC–4 型离子注入机,中国科学院半导体研究所后对该注入机的真空系统、离子源、靶室等设施进行了升级改造,使该注入机在研究方面的性能和功能更加强大。
经过二十多年的运行,我们已为全国一百多家科研院所、大学和企业提供了离子注入技术工艺制作,来我们这里做离子注入工艺的不仅有中科院、北大、清华等众多内地著名单位而且还包括台湾和香港的多所大学;在国际上,美国、德国等西方国家的研究部门也多次来我们这里做离子注入,而我们对国外的收费一直是按照基本上与国际接轨的标准。
从国内外的回头客情况看,他们对我们离子注入的质量水平感到满意,特别是,德国Paderborn大学的Wolf Sohler 教授2009年专门来我们这里参观,他说:“我们多次来你们这里做注入,经我们德方的实验测试,你们注入的质量很好”。
这说明德国人来我们这里花费得到的技术工艺是物有所值的,也说明我们的离子注入技术经受住了国际方面的检验从而达到国际水平。
有关这台离子注入机的技术指标,其能量在15keV–600keV范围内连续可调,束流强度0.02μA–100μA。
注入离子的种类可做铅以下所有离子,现做过的离子包括Al+、As+、Ar+、Ag+、Au+、B+、BF
2
+、Br+、Be+、Bi+ 、Ba+ 、C+、Cr+、Ga+、
Cu+、Ge+、Ca+、Co+、Ce+、Dy+、Eu+、Er+ 、Fe+、Gd+、H+、H
2
+、He+、I+、In+、La+、
Li+、Mg+、Mo+、Mn+、N+、N
2+、Ni+、Nb+、Nd+、Ne+、O+、O
2
+、P+、Pr+、Pt+、Pd+、
S+、Si+、Se+、Sb+、Sm+、SiF
2
+、Te+、Ti+、Tb+、Ta+、Tm+、V+、W+、Xe+、Y+、Yb+、Zr+、Zn+、Zr+等超过60种离子。
我们可以实现重叠注入、垂直注入、大偏角或双偏角注入以及冷靶(液氮温度)或热靶(500 ℃以下)注入等,注入样品的形状可以是任意尺寸,最小可以是几个平方毫米,最大可达4英寸直径的圆片。
应用该机已在多种半导体器件、表面物理、半导体材料、金属材料、超导材料、生物材料、医学结构材料、地质矿藏材料、粮食种子改性、微生物品种改良等方面开展了研究,其中在很多方面已取得显著效果。
电子邮件:jml@(联系注入需通过发电子邮件网上预约,联系人:李建明)
地址:中国科学院半导体研究所,北京市海淀区清华东路甲35号4号实验楼102室
邮编:100083;电话/传真:(010)82304443。