棒线厂三切分轧制调整操作培训
棒材三切分轧制要点

棒材三切分轧制为顺利完成Φ12*3、Φ14*3三切分螺纹钢轧制调试工作,特提出工艺要求如下:1、原料工严把原料质量关,杜绝有肉眼可见缺陷的钢坯入炉。
2、看火工按工艺规程要求,严格控制钢坯出炉温度,既要防止钢坯高温氧化甚至脱碳现象,影响钢材性能,又要防止低温钢轧制损坏设备甚至造成轧制事故。
3、导卫的调整与安装3.1 导卫在上线前必须对油路、水路、轴承等进行检查,确保油路、水路畅通,零部件完好,并对导卫加油。
3.2导卫上线前的调整应坚持以下原则:①、粗轧滚动导卫的开口度比标准料型大2—4mm 为宜;中轧滚动导卫的开口度比标准料型大1—2mm为宜;精轧滚动导卫的开口度比标准料型大0.1—0.5mm为宜。
②、15、16架双排轮前面两个辊的开口度必须与后边两个辊的开口度一致。
调整时可先调前面两个辊的开口度与后边两个辊的开口度一致,然后再调内支撑臂后端的调整螺丝左右两个螺丝可同时、同步改变前后两组辊的开口度。
④、切分导卫切分轮间隙应调整适当,控制在0.3—0.5mm,以用手转动其中一个轮子时,另一个轮子也能转动,且无明显阻力为宜。
⑤、要特别注意切分刀片中心线必须与切分轮两切分刃在同一直线上,并与铲嘴内孔中心线吻合。
⑥、铲嘴在设计时已经考虑到来料与轧槽形状,在现场安装时铲嘴离轧槽的距离控制在1—2mm。
⑦、分料盒离切分轮越近越好。
⑧、扭转导卫的扭转角控制在30。
—35。
范围内。
3.3导卫在安装时尤其是15、16架进口导卫,必须保证导卫中心线与孔型中心线相吻合,以保证切分开的料型尺寸上的一致性。
4、轧辊在安装时必须保证轧辊装配的正确性以及轧机安装前轧辊轴承的加油工作;保证轧辊安装时上下轧槽的对正、磨槽以及轧辊两端辊缝的一致性,要求精轧机两边辊缝差小于0.1mm。
5、必须保证各机架孔型中心线对正轧制线,以防止轧槽偏磨,保证料型的正确性。
6、料型控制6.1轧制过程中的料型控制严格执行《工艺技术规程》要求。
6.2第一次轧制前,中轧、13、14、15架必须各试轧2—3根小样,并测试各架次料型尺寸,要特别注意考虑小样与正常轧制时轧件尺寸及变形条件的差别。
轧钢工段培训教材

轧钢工段培训教材轧钢生产实践培训教材第一章轧制过程中易出事故的原因及处理一、带钢(带坯)的翘头1.产生原因:①钢坯的上下表面温度差:上表面温度大于下表面温度时会引起带钢的扣头,反之会引起带钢的翘头;②轧制线的标高:轧制线标高过高会引起带钢的扣头,反之会使带钢翘头;③摩擦因素的影响:当带钢表面除鳞不净或轧辊粗糙时,带钢会弯向带有铁皮或辊面粗糙的一面,从而引起带钢的翘头或扣头;④辊系配辊的辊压大小的影响:采用上辊压时会使带钢扣头;采用下辊压会使带钢产生翘头;⑤轧制速度的影响:下辊的辊面线速度大于上辊的速度时会导致带钢的翘头,反之会引起扣头;⑥轧制负荷分配不合理。
2.预防措施:①合理安排加热制度,保证钢坯的加热温度,上下表面的温差及芯部与外表面的温差≤30℃;轧制过程保持合理的轧制节奏,同时保证辊系的均匀冷却;②按照轧线标高与轧机垫板的工艺要求及时更换垫板;③保证粗除鳞、精除鳞的除鳞效果。
粗除鳞水压力≥16MPa,精除鳞水压力≥18MPa;④在轧制线标高满足要求的条件下采用上辊压。
3.处理方法:①减慢轧制节奏;②调整钢坯上、下表面加热温度的差值;③检查轧辊的冷却系统是否有堵塞现象;④重新调整各机架、各道次的负荷电流;⑤翘头严重时,要及时进行更换轧辊(调整辊压、轧制标高及适当降低出口上卫板的高度。
)二、料偏废钢1.产生的原因:①板坯的厚度不均,有侧弯等,或粗轧带坯来料不平直,进入精轧机组后导致带坯两侧的延伸不一致;②换辊后压靠、调平的精度不高,致使两侧辊缝存在较大的偏差;③压下手没有对带钢的料形变化及时地做出正确的调整;④导卫的开口度中心线不对中或开口度过大,致使带钢跑偏;⑤轧机的辊缝跑位,操作工对此确认不到位而没有及时调整导致料偏废钢;⑥辊身掉肉,压入带钢产生料偏;⑦轧辊车削精度不够,如轧辊的锥度、不圆度或三点差等超出工艺指标导致的料偏;⑧轧线上存留杂物,如扳手、调平用的盘圆等影响带钢穿带过程造成料偏。
Ф14棒材生产中三切分轧制技术研究

题 。 但 孔 型 设 计 时 ,还 需 考 虑 预 切 分 与切 分 孔 型 的 配 合 问 题 ,如 配 合 不 当 ,会 造 成 轧 制 过程 中 的调 整 难 度 及 导 卫粘 铁 的现 象 。 ( 3 )立箱孔 立箱孔型延伸系数 很小 ,基本无 宽展 , 起到轧件微调平整 的作用 ,其与前 后孔的配 合很重要 。 根据经验, 其侧壁斜度为 7 。左右,
以达到限制宽展 的 目的 ,立箱孔型 的槽底 宽
应 比来 料 高 小 1 - 2 m m ,如 果 过 大 ,边 孔 会 出
一
现过大的强制性压下 ,导致 出现 中间料型比 两边料型突 出的现象 即 中间料型 的面积比两 边料型大 ,进而导致后续道次料型不好调整 方案一中 1 2 # 料型设计 高度为 2 4 . 6 m m, 而1 3 撑 孔型槽底宽为 2 0 mm,与料型相 比槽底 过窄,咬入 困难 ,且 l 3 孔型限制 了边孔的宽 展, 由 图 8可 以看 出 , 边 孔 最 宽处 为 2 2 . 2 5 mm, 而中间孔不考虑 宽展 已达到 了2 2 . 6 mm,毫无 疑 问会造 成 1 3 料型 中间突出的现象, 而两边 的料 型 明 显 比 中 间 的料 型 偏 大 。 方案二 中 1 2 # 边孔 比 1 3 捍 孔 对 应 位 置 稍 低, 这样 l 3 # 孔 不会 过 多 限制 1 2 # 边孔 的 宽展 , 从而避免造成轧件 向中间孔的流动过 多。 综 合 以 上分 析 , 最 终选 择 了方 案 二 : l 群 - 8 料型与 中1 6两 切分基本相同 , 可减少换孔量 , 1 8 群 、1 9 # 沿用中1 4两 切 分 孔 型 。
切不开,过 小会形成对切分轮的夹持力过 大, 加大切分轮 的负荷 ,一般 在 6 0 。一 6 5 。 :楔子 尖部圆角为 1 ~1 . 5 mm 为好 , 过尖会 加快轧辊 磨损,甚至 掉肉;连接带厚度应 与辊缝接近 , 1 - 2 mm 最好 ;延伸系数在 1 . O 8 ~1 . 1 5 ,并留有 定量的宽展余地 。 工艺布局确 定后 ,初步确 定了两套孔 型 系统,具体情 况如下 : f 1 )预 切 分 孔 第 一 道 预 切分 孔 ( 1 2 撑 ) : 1 2 #  ̄ L 是第一道预切 ,主要作用是可减 小 l 4 牟 孔的变形量,降低 1 4 #  ̄ L 的轧制负荷,减 轻 1 4 #  ̄ L 的变形不均匀性 ,提高轧制稳定性; 同时经过 1 2 # 轧制后的料 型带有 凹槽 , 在进入 1 4 #  ̄ L 时对中性比较好 ,成 品尺寸较均匀。其 延伸系数一般为 1 - 3 ~1 . 4 。 两方案 9 一 1 1 撑 料型 ( 9 撑 都 是 由 4 7 . 8 r m n的 基 圆 放 大辊 缝 ) 。 方案 二设定的料型 比较合理 ,压 下分 配 比较平均 ,l l 的压下量 为 1 2 am左右 ,在轧 r 制过程 中 1 1 # 电流大于 2 O %。 第二道预切分孔 ( 1 4 #) ; 1 4 # ? L 型 的切 分楔进 一步对 初步 压 出凹 陷形状的轧件完成压下 定位 ,并精确 分配 轧 件 的断面面积 。其 变形系数较小 ,延伸系数 般为 1 . 1 . 1 . 2 两种方案中 1 4 #  ̄ L 的 延伸 系数 分别 为 1 . 4 0 7 、1 . 1 9 o ,由此可见方案 一的轧制负荷较 大 ,冲击力大。 方案一中连接带的高度为 4 . 9 am,仅为 r 孔 型 高度 的 0 . 2 5倍 , 且 其 圆 角 半径 为 3 mm, 边孔 与中间孔的连接 比较陡,易导致 1 6 ≠ } 边孔 靠里侧料 型扁平 即边孔型里侧未充满。
切分轧制技术培训

切分轧制技术一、切分轧制技术发展概况切分轧制技术早在19世纪60年代就由美国和英国首先提出,并成功应用于旧钢轨的利旧方面,开创了切分轧制的先例,但此后切分轧制技术发展较为缓慢。
具有现代意义的切分轧制技术始于20世纪40年代,美国的西拉库兹厂成功利用切分轧制生产出了小型材。
在20世纪70年代,加拿大首先应用了两线切分技术生产棒材产品,自此,切分技术得到了快速发展,80年代,日本的新日铁、德国的巴登公司等利用导卫箱内切分轮切分法来实现棒材的多线切分投入大生产。
在切分方法的实践中,人们先后尝试过圆盘剪切分法、火焰切分法、辊切法和切分轮切分法等多种切分方法。
目前,无论是双线切分还是多线切分,广泛采用的都是带切分轮的专用导卫切分法,即利用带有切分孔型系统的轧槽,首先将轧件加工成由薄而窄的连接带相连的几个并联轧件,然后再利用安装在该架次轧机出口的带切分轮的专用切分导卫将切分带撕开,从而获得几个面积相同的相互独立的轧件,最后经后续道次轧制成成品。
二、切分轧制1定义切分轧制是指在轧制过程中利用轧辊孔型、导卫装置中的切分轮或其他切分装置将轧件沿纵向切成两线或多线的轧制技术.2切分方法简介(1)切分轮法:先用特殊的孔型将轧件或轧成准备切分的形状,再在轧机的出口处安装不传动的切分轮,利用其侧向分力将轧件切开。
这种方法连轧机上普遍采用,是目前切分轧制主要方法。
(2)辊切法:利用轧辊孔型的特殊设计,在变形过程中将轧件分开,但轧辊强度和韧性要求高,轧辊孔型设计合理准确。
(3)圆盘剪切分法:利用剪切原理,用圆盘剪将轧件切开。
剪刃由一定重合量,切分后有扭转,剪切设备较重,不用时移开,操作不方便较少用.(4)火焰切分法:先将轧件准备成切分的形状,再用火焰纵向切开,消耗能源和损失金属,较少使用。
3切分轧制的优点(1)切分轧制可以极大的提升中、小规格棒材的产量;(2)在不增加轧机数量的前提下,生产小规格和生产大规格产品能够采用相同断面的钢坯,可以减少原料的种类;(3)用同样的坯料生产同规格的产品,由于总变形率仅为单线轧制的1/2~1/4,因而可减少轧制道次.(4)在增加产量的同时,终轧速度并未随之提高,有的规格采用切分轧制后,终轧速度还有所降低;(5)无论是在现有连轧机上还是在新建连轧机上采用切分轧制技术,由于生产工艺仅局部变动,而且主要工艺设备并无特殊要求,因此具有投入少、产出高、见效快的特点.(6)在条件相同时,采用切分轧制可降低钢坯温度加热炉40℃左右,燃料消耗减少20%,电耗可降低15%,轧辊消耗降低15%,生产总费用降低10% ~15%。
棒线材生产工艺培训

生产工艺-加热
加热:线材生产属于热轧一种形式,轧制 之前的钢坯原料需要先经过加热到一定温 度。
加热目的:提高塑性,降低变形抗力,改 善内部组织,消除铸锭缺陷。
加热要求:严格执行加热制度,钢坯整体 温度均匀,无过热、过烧等现象。
生产工艺-开轧温度
开轧温度:咬入第一架轧机时的轧件温度。 我们经常把开轧温度和加热温度混为一谈,这是
精轧机组前后设置有轧件控冷装置,精轧机组后设有剪切、 精整、收集等装置。
主要设备
两条高线主要设备的选择,根据钢坯断面、产品规 格及其尺寸精度的要求,全线均采用无扭轧制。共 分4个机组,由粗轧6架、中轧6架、预精轧6架、精 轧10架、共28个机架组成。
A、B线轧机配置相同,B线和A线的不同在于B线考 虑了预留减定径机组,A线不设减定径机组也不考 虑预留。粗轧机组由4架Φ610/520mm和2架 Φ480/420mm轧机组成;中轧机组由4架 Φ480/420mm和2架Φ380/320mm轧机组成;预精轧 机组前4架由Φ380/320mm轧机组成。以上轧机均为 短应力线轧机,平立交替布置。
高速无扭精轧
高速无扭精轧工艺是现代线材生产的核心 技术之一,它是针对以往各种线材轧机存 在诸多问题,综合解决产品多品种规格、 高断面尺寸精度、大盘卷和高生产率的有 效手段。唯精轧高速度才能有高生产率。 才能解决大盘重线材轧制过程的温降问题。 精轧的高速度要求轧制过程中轧件无扭转, 否则事故频发,轧制根本无法进行。因此, 高速无扭精轧是高速线材轧机的一个基本 特点。
棒材主要设备及工艺特点
全轧线共有18架轧机,分为粗轧、中轧、精轧机组。
轧机平-立交替布置的轧机组成,其中:1-10架为闭口轧机, 11-18架为短应力线轧机,第14、16、18架为平/立可转换轧 机,各架轧机均由直流电机单独传动,在中轧机组及精轧机 组前各设一台启停式飞剪对轧件进行切头、切尾及事故碎断。 整个轧线采用全连续、全无扭轧制,粗、中轧机组采用微张 力轧制,精轧机组之间和精轧机组各架轧机之间均设置立活 套,实行无张力控制轧制。根据产品规格的不同,粗轧机组 轧出的Ф72mm圆轧件在中轧和精轧机组轧制6~12道次, Ф12~40mm带肋钢筋(其中:Ф12~22mm带肋钢筋用切分 法生产) 、Ф18-22树脂锚杆用热轧钢筋。成品最大轧制速 度为18m/s。
棒线厂三切分轧制调整操作培训
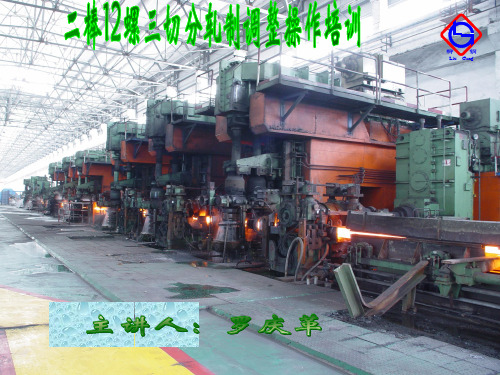
柳
Liu
钢
Gang
• 本次修改的孔型系统的特点: • 1、由一道预切分(K4)改为二道预切分(K4、 K6),目的是减少K4孔的压下量,从而减少K4的 磨损,稳定预切分孔的料形。 • 2、K3孔切分楔由原来比辊环高改为比辊环低,目 的是减少K3崩孔。 • 详见孔型图
轧制料形调整要点
• 1、辊缝设 定要比标准辊缝小0.3mm。 • 2、轧制过程料形调整要根据轧件实 际尺寸与料形标准比较来调整。
•
•
• •
1、由生产技术科制定每个导卫预装标 准尺寸: 1)滑动导卫内腔尺寸及制定允许磨损 最大值。 2)每个滚动导卫辊轮开口度预装标准 及允许偏差。 本项工作在6月10日前完成
2、准备车间要严格按生产技术下发的预装标 准进行预装,管区工程师和生产车间加强 检查验收,凡预装不合格的,责任由准备 车间承担(生产车间调整过的由生产车间 承担)
• • • •
11、两侧线合格,中间线小或大; 12、三线全部合格。 二、料形调整顺序: 1、先保证中间料形符合要求,注意导卫的调 整对中间线的料形不影响,只能通过调整K1、 K2、K3来保证,其它机架料形对中间线料形 影响很小。 • 2、调整中间线料形时,同时兼顾
柳
Liu
钢
Gang
• • • • • • • • •
柳
Liu
钢
Gang
树立信心,排出困难,实现12螺三切分达产攻关 • 1、12螺三切分达产目标:日产2400吨,成材 率大于102.20%。 • 2、攻关的主要措施: • 2.1、料形控制标准化 • 2.2、导卫预装和调整的准确性 • 2.3、采用耐磨性高的轧辊 • 2.4、轧制通道适应性改造 • 2.5、调整工的熟练调整
棒材三切分轧制工艺实践
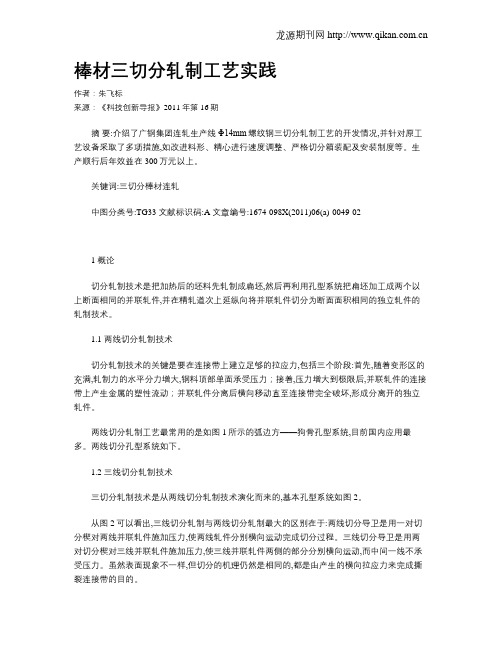
棒材三切分轧制工艺实践作者:朱飞标来源:《科技创新导报》2011年第16期摘要:介绍了广钢集团连轧生产线Φ14mm螺纹钢三切分轧制工艺的开发情况,并针对原工艺设备采取了多项措施,如改进料形、精心进行速度调整、严格切分箱装配及安装制度等。
生产顺行后年效益在300万元以上。
关键词:三切分棒材连轧中图分类号:TG33 文献标识码:A 文章编号:1674-098X(2011)06(a)-0049-021 概论切分轧制技术是把加热后的坯料先轧制成扁坯,然后再利用孔型系统把扁坯加工成两个以上断面相同的并联轧件,并在精轧道次上延纵向将并联轧件切分为断面面积相同的独立轧件的轧制技术。
1.1 两线切分轧制技术切分轧制技术的关键是要在连接带上建立足够的拉应力,包括三个阶段:首先,随着变形区的充满,轧制力的水平分力增大,钢料顶部单面承受压力;接着,压力增大到极限后,并联轧件的连接带上产生金属的塑性流动;并联轧件分离后横向移动直至连接带完全破坏,形成分离开的独立轧件。
两线切分轧制工艺最常用的是如图1所示的弧边方——狗骨孔型系统,目前国内应用最多。
两线切分孔型系统如下。
1.2 三线切分轧制技术三切分轧制技术是从两线切分轧制技术演化而来的,基本孔型系统如图2。
从图2可以看出,三线切分轧制与两线切分轧制最大的区别在于:两线切分导卫是用一对切分楔对两线并联轧件施加压力,使两线轧件分别横向运动完成切分过程。
三线切分导卫是用两对切分楔对三线并联轧件施加压力,使三线并联轧件两侧的部分分别横向运动,而中间一线不承受压力。
虽然表面现象不一样,但切分的机理仍然是相同的,都是由产生的横向拉应力来完成撕裂连接带的目的。
棒材的三线切分轧制技术自问世以来,替代了两线切分轧制技术应用于Φ10mm、Φ12mm 及Φ14mm的小规格产品,迅速地发展成为主流轧制技术,个别生产厂还应用于Φ16mm的螺纹钢产品。
2 工艺条件介绍广钢连轧线是引进20世纪80年代先进水平的达涅利公司棒材生产线,轧制品种为Φ10mm~Φ40mm圆钢及带肋钢筋。
Φ14棒材生产中三切分轧制技术研究

Φ14棒材生产中三切分轧制技术研究摘要:本文叙述了棒材生产中φ14螺纹钢三切分的工艺选择、调试时出现的问题、改进方案及效果。
关键词:螺纹钢三切分工艺方案1、前言切分轧制是在轧机上利用特殊的轧辊孔型和导卫或者其他切分装置,将原来的一根坯料纵向切成两根以上的轧件,进而轧制多根成品或中间坯的轧制工艺。
采用切分轧制技术可缩短轧制节奏,提高机时产量,显著提高生产效率,降低能耗和成本。
目前切分轧制技术已发展到五切分轧制,且两线切分轧制技术和三线切分轧制技术作为成熟技术已经普遍应用在小规格螺纹钢的生产中。
本文所述棒材厂从2005年开始逐步应用切分轧制技术,现已成功开发了φ14、φ16、φ18螺纹钢二切分、φ12螺纹钢三切分轧制技术。
2010年,为了实现147万吨的年产量目标,棒材厂决定充分发挥切分技术的产能优势,在ф12螺纹钢三切分的基础上实施ф14螺纹钢的三切分轧制。
2、设备配置情况车间的工艺布置为粗轧7架平轧闭口轧机、中轧为平立交替的6架两辊闭口轧机、精轧为平立交替6架预应力轧机。
、3、工艺方案的选择3.1 工艺布局的确定在φ12螺纹三切工艺和φ14螺纹两切分工艺的经验基础上,对一道预切与两道预切的方案进行了比较:如采用一道预切,则预切分孔(k4)的压下和延伸比较大,轧制负荷大、轧制不稳定,且其切分楔处的压下系数远大于槽底的压下系数,造成切分楔处磨损严重;来料进预切分孔时的对中性差,进而导致预切料型进切分孔时不均匀,这样3支成品之间的尺寸不均匀,负差也不易控制。
采用两道预切,可减小k4孔(第二道预切)的变形量,降低k4孔的轧制负荷,减轻其变形不均匀性,提高轧制稳定性;同时带有凹陷部位的来料进k4孔时,容易对中,对轧辊切分楔的冲击较小,成品尺寸较均匀;由于k4变形系数小,故改变k4的压下量对轧件的断面面积影响较小,降低了成品尺寸随k4料型变化而变化的敏感性,提高了轧制的稳定性及料型调整的方便性和精确性。
3.2 孔型设计切分工艺的孔型设计中预切分和切分孔的设计尤为重要,其次是立箱孔型,这几道次的孔型设计,关系到切分轧制是否能成功。
棒材3线切分轧制技术的应用与改进

2 3线切分轧制技术的应用及改进
2.1 切分轧制技术的优点
(1)提高生产率
采用切分轧制不仅可减少轧制道次,减少轧制时间,而且,对棒材轧机,同样架次可采用较大规格的坯料生产较小规格的产品,产量不受影响。如单线生产Φ12、Φ14mm带肋钢筋,由于受总变形量的限制,通常采用小于140mm×140mm的坯料,这不仅增加坯料的规格种类,给炼钢、连铸及轧钢的生产组织带来影响,而且机时产量低。根据棒材轧机140t/h的设计能力,Φ12、Φ14mm带肋钢筋,采用3线切分轧制最合理,机时产量比2线切分提高1倍以上。
③由于3线切分上冷床不顺利,因此改进了拨钢器的设计,使之既能适应1线切分生产,又能满足3线切分生产。
④为精确定位,提高车削精度,设计了连体样板以检验轧槽。在车床上安装了数显表,以精确定位,保证车槽精度,提高配辊的精确度。
⑤由于切分轮设计不合理,第1次生产Φ14mm带肋钢筋时,中线产生大量折叠废品,因而改进了切分轮设计。并针对切分轮不耐磨现象,与生产厂家共同进行多次试验,最后选择了一种新的热作模具钢。
精整区采用裙板辊道上冷床,步进式冷床132.5m×11.5m。出口辊道将钢材送入定尺剪定尺后,由链床送到打包收集区,包装入库。
2.2 产品状况
产品规格共有39个,圆钢规格为Φ14~Φ50mm,带肋钢筋规格为Φ12~Φ40mm。Φ12、Φ14mm带肋钢筋用3线切分技术,Φ16、Φ18mm带肋钢筋用2线切分技术,可根据用户要求生产6~12m任意长度的定尺尺寸范围内的各规格带肋钢筋。
/% 成材率
/% 烧损
/kg.t-1 油耗
/kg.t-1 机时产量
/t.h-1 成本
/元.t-1
12 97.42 95.03 32.00 98.00 61.75 2323.05
Φ18mm热轧带肋钢筋三切分轧制工艺及其控制要点
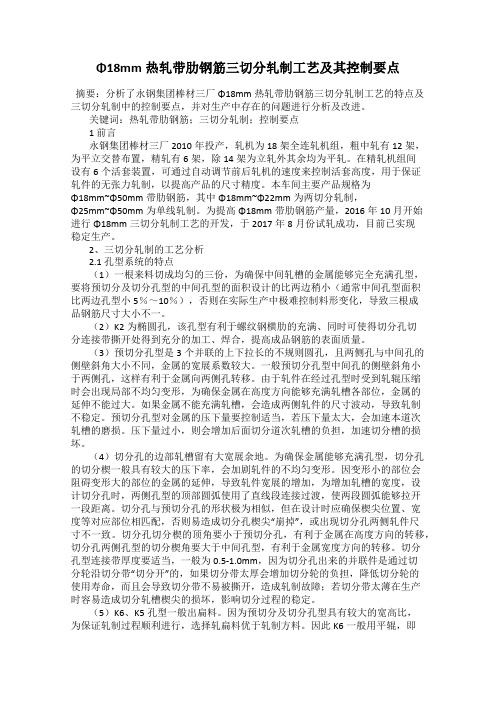
Φ18mm热轧带肋钢筋三切分轧制工艺及其控制要点摘要:分析了永钢集团棒材三厂Φ18mm热轧带肋钢筋三切分轧制工艺的特点及三切分轧制中的控制要点,并对生产中存在的问题进行分析及改进。
关键词:热轧带肋钢筋;三切分轧制;控制要点1 前言永钢集团棒材三厂2010年投产,轧机为18架全连轧机组,粗中轧有12架,为平立交替布置,精轧有6架,除14架为立轧外其余均为平轧。
在精轧机组间设有6个活套装置,可通过自动调节前后轧机的速度来控制活套高度,用于保证轧件的无张力轧制,以提高产品的尺寸精度。
本车间主要产品规格为Φ18mm~Φ50mm带肋钢筋,其中Φ18mm~Φ22mm为两切分轧制,Φ25mm~Φ50mm为单线轧制。
为提高Φ18mm带肋钢筋产量,2016年10月开始进行Φ18mm三切分轧制工艺的开发,于2017年8月份试轧成功,目前已实现稳定生产。
2、三切分轧制的工艺分析2.1 孔型系统的特点(1)一根来料切成均匀的三份,为确保中间轧槽的金属能够完全充满孔型,要将预切分及切分孔型的中间孔型的面积设计的比两边稍小(通常中间孔型面积比两边孔型小5%~10%),否则在实际生产中极难控制料形变化,导致三根成品钢筋尺寸大小不一。
(2)K2为椭圆孔,该孔型有利于螺纹钢横肋的充满、同时可使得切分孔切分连接带撕开处得到充分的加工、焊合,提高成品钢筋的表面质量。
(3)预切分孔型是3个并联的上下拉长的不规则圆孔,且两侧孔与中间孔的侧壁斜角大小不同,金属的宽展系数较大。
一般预切分孔型中间孔的侧壁斜角小于两侧孔,这样有利于金属向两侧孔转移。
由于轧件在经过孔型时受到轧辊压缩时会出现局部不均匀变形,为确保金属在高度方向能够充满轧槽各部位,金属的延伸不能过大。
如果金属不能充满轧槽,会造成两侧轧件的尺寸波动,导致轧制不稳定。
预切分孔型对金属的压下量要控制适当,若压下量太大,会加速本道次轧槽的磨损。
压下量过小,则会增加后面切分道次轧槽的负担,加速切分槽的损坏。
轧机操作人员技能培训教材
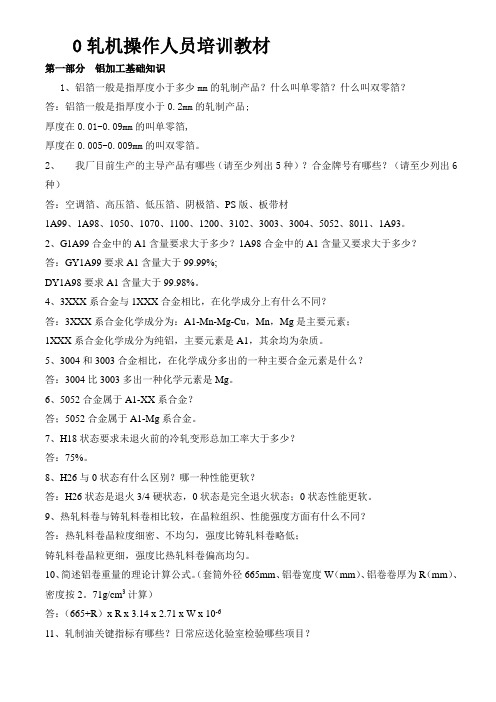
0轧机操作人员培训教材第一部分铝加工基础知识1、铝箔一般是指厚度小于多少mm的轧制产品?什么叫单零箔?什么叫双零箔?答:铝箔一般是指厚度小于0.2mm的轧制产品;厚度在0.01-0.09mm的叫单零箔,厚度在0.005-0.009mm的叫双零箔。
2、我厂目前生产的主导产品有哪些(请至少列出5种)?合金牌号有哪些?(请至少列出6种)答:空调箔、高压箔、低压箔、阴极箔、PS版、板带材1A99、1A98、1050、1070、1100、1200、3102、3003、3004、5052、8011、1A93。
2、G1A99合金中的A1含量要求大于多少?1A98合金中的A1含量又要求大于多少?答:GY1A99要求A1含量大于99.99%;DY1A98要求A1含量大于99.98%。
4、3XXX系合金与1XXX合金相比,在化学成分上有什么不同?答:3XXX系合金化学成分为:A1-Mn-Mg-Cu,Mn,Mg是主要元素;1XXX系合金化学成分为纯铝,主要元素是A1,其余均为杂质。
5、3004和3003合金相比,在化学成分多出的一种主要合金元素是什么?答:3004比3003多出一种化学元素是Mg。
6、5052合金属于A1-XX系合金?答;5052合金属于A1-Mg系合金。
7、H18状态要求未退火前的冷轧变形总加工率大于多少?答:75%。
8、H26与0状态有什么区别?哪一种性能更软?答:H26状态是退火3/4硬状态,0状态是完全退火状态;0状态性能更软。
9、热轧料卷与铸轧料卷相比较,在晶粒组织、性能强度方面有什么不同?答:热轧料卷晶粒度细密、不均匀,强度比铸轧料卷略低;铸轧料卷晶粒更细,强度比热轧料卷偏高均匀。
10、简述铝卷重量的理论计算公式。
(套筒外径665mm、铝卷宽度W(mm)、铝卷卷厚为R(mm)、密度按2。
71g/cm3计算)答:(665+R)x R x 3.14 x 2.71 x W x 10-611、轧制油关键指标有哪些?日常应送化验室检验哪些项目?答:轧制油的关键指标有:粘度、酸值、羟值。
棒材三切分轧制工艺实践和控制要点

棒材三切分轧制工艺实践和控制要点本文结合生产实际,分析并比较了三切分轧制工艺的特点及三切分轧制中的控制要点,针对生产实践中遇到的问题提出了适当改进建议。
标签:棒材;三切分轧制;工艺实践;控制要点1 Φ16mm规格棒材三切分轧制工艺实践(1)孔型轧机设计。
外径为十六规格三分切轧制应用六道粗轧加之四道中轧加之六道精轧合计为十六道次。
整体轧机中第一架和第九架应该是无孔型轧制、第十架为圆孔型,中轧来料是不规则的圆形。
参照二切分轧制技术的生产实践,三切分应该应用切分轮法。
外径十六规格三分切轧制要运用”狗骨型孔型系统”,也就是精轧运用六机架:十三号机架用平型辊、十四号机架用立箱、孔型,十五号机架用三狗骨头型,十六号机架是切分孔型,十七号机架是平椭,经过十八架机架轧制出螺纹钢筋成品。
(2)孔型轧机原理。
1)十四号机架设计。
理论上十四号机架立箱、孔型为十五号机架夯实了矩形的标准尺寸,否则将影响十五号机架预期切孔的三孔充满度,十四号机架料型天地宽度尺寸主要参照十五号机架边线的充满度和十四号机架料型天地的平整度。
高度尺寸主要参考十五号机架的下压量和中线充满度。
在辊径确定、其余参照不更改的条件下,轧件宽展决定压下率的大小。
当压下率和轧件的宽高之比小于零点四,轧件与轧辊触面产生变形,轧件产生双鼓型侧面。
轧件变形程度的压下率在百分之十以下,轧件表面产生变形,当压下率在百分之二十以上,中心部分由于渗透产生变形。
当压下率在百分之三十以上,接触面积部分小于中心部分变形。
2)十五号机架设计。
十五号机架预切孔型的作用是:切分楔完成对扁钢轧件的压下定位,并精准确定分配轧件的断面积,从而减轻切分孔型的负担,切实加强切分的均匀性和稳定性。
十四号机架出口轧件料型是不规则的矩形,合理设计十五号机架三线孔型,确保这个孔型轧制之后的轧件每截面积相等或者控制在相差数最小。
保证靠两边轧件不产生耳子,反之,在但影响下道工序的咬入,还能够使下道轧机在作业是产生折叠,甚至堆钢(俗称“挤王八”)。
轧钢调整培训教材
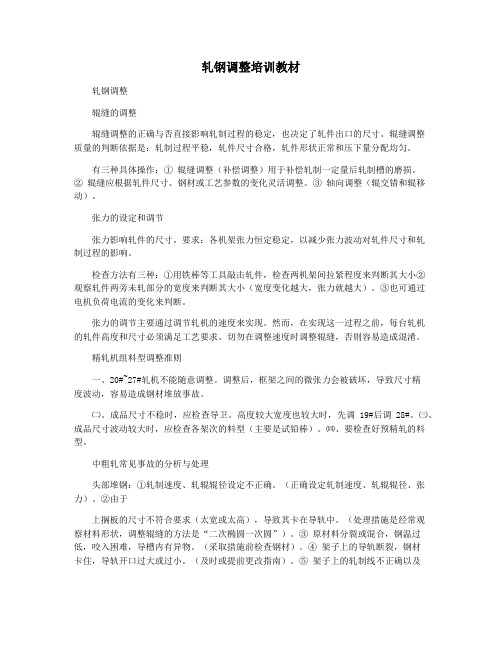
轧钢调整培训教材轧钢调整辊缝的调整辊缝调整的正确与否直接影响轧制过程的稳定,也决定了轧件出口的尺寸。
辊缝调整质量的判断依据是:轧制过程平稳,轧件尺寸合格,轧件形状正常和压下量分配均匀。
有三种具体操作:① 辊缝调整(补偿调整)用于补偿轧制一定量后轧制槽的磨损。
② 辊缝应根据轧件尺寸、钢材或工艺参数的变化灵活调整。
③ 轴向调整(辊交错和辊移动)。
张力的设定和调节张力影响轧件的尺寸。
要求:各机架张力恒定稳定,以减少张力波动对轧件尺寸和轧制过程的影响。
检查方法有三种:①用铁棒等工具敲击轧件,检查两机架间拉紧程度来判断其大小②观察轧件两旁未轧部分的宽度来判断其大小(宽度变化越大,张力就越大)。
③也可通过电机负荷电流的变化来判断。
张力的调节主要通过调节轧机的速度来实现。
然而,在实现这一过程之前,每台轧机的轧件高度和尺寸必须满足工艺要求。
切勿在调整速度时调整辊缝,否则容易造成混淆。
精轧机组料型调整准则一、20#~27#轧机不能随意调整。
调整后,框架之间的微张力会被破坏,导致尺寸精度波动,容易造成钢材堆放事故。
㈡、成品尺寸不稳时,应检查导卫。
高度较大宽度也较大时,先调19#后调28#。
㈢、成品尺寸波动较大时,应检查各架次的料型(主要是试铅棒)。
㈣、要检查好预精轧的料型。
中粗轧常见事故的分析与处理头部堆钢:①轧制速度、轧辊辊径设定不正确。
(正确设定轧制速度、轧辊辊径、张力)。
②由于上搁板的尺寸不符合要求(太宽或太高),导致其卡在导轨中。
(处理措施是经常观察材料形状,调整辊缝的方法是“二次椭圆一次圆”)。
③ 原材料分裂或混合,钢温过低,咬入困难,导槽内有异物。
(采取措施前检查钢材)。
④ 架子上的导轨断裂,钢材卡住,导轨开口过大或过小。
(及时或提前更改指南)。
⑤ 架子上的轧制线不正确以及导轨和防护装置安装偏差导致的弯头。
(处理措施为经常观察导向,经常观察材料类型,经常测量尺寸)。
中间堆钢:①料型不好造成张力不合,拉断轧件。
- 1、下载文档前请自行甄别文档内容的完整性,平台不提供额外的编辑、内容补充、找答案等附加服务。
- 2、"仅部分预览"的文档,不可在线预览部分如存在完整性等问题,可反馈申请退款(可完整预览的文档不适用该条件!)。
- 3、如文档侵犯您的权益,请联系客服反馈,我们会尽快为您处理(人工客服工作时间:9:00-18:30)。
关于检查、考核和奖励
• 1、关于检查和考核已在提高工艺执行率文件 上制定了相关规定。 • 2、生产技术科增加参数中间值控制最优奖励 制度,通过检查记录,每月评出最佳工艺控制 车间(在无超标前提下,平均控制值最靠近中 间标准值的车间),每条生产线每个工序评一 个(先评加热温度、料形、上冷床温度(吐丝 温度),轧辊和导卫预装命中率达95%以上的 给奖励
柳
Liu
钢
Gang
导卫设计标准化是指导卫设计的各种尺寸要 符合料形标准化的要求,并根据现场使用情况设 计有一定的配合尺寸,保证不堵钢、不倒钢、不 粘钢。
柳
Liu
钢
Gang
•
1、轧机辊缝预装标准化,粗轧预装辊 缝在标准辊缝±0.2mm,两端辊缝差控制在 0.2mm之内。中轧预装辊缝在标准辊缝 ±0.15mm,两端辊缝差控制在0.15mm之内。 精轧预装辊缝在标准辊缝±0.1mm,两端辊 缝差控制在0.1mm之内。 • 2、其它预装标准由准备车间制定
三切分料形调整要点
• • • • • • • • • • • 一、上冷床料形会有以下几种情况: 1、三条轧件同时偏小,严重的全部没有纵肋; 2、三条轧件同时偏大,造成纵肋超大; 3、中间线大,两侧线同时小; 4、中间线大,两侧线一大一小 5、中间线小,两侧同时大; 6、中间线小,两侧线一大一小; 7、中间线合格,两侧线同时小; 8、中间线合格,两侧线同时大; 9、中间线合格,两侧一大一小,同时超标; 10、中间线合格,两铡线有一条合格,一条小或大
• • • •
11、两侧线合格,中间线小或大; 12、三线全部合格。 二、料形调整顺序: 1、先保证中间料形符合要求,注意导卫的调 整对中间线的料形不影响,只能通过调整K1、 K2、K3来保证,其它机架料形对中间线料形 影响很小。 • 2、调整中间线料形时,同时兼顾
柳
Hale Waihona Puke Liu钢Gang• • • • • • • • •
柳
Liu
钢
Gang
• 本次修改的孔型系统的特点: • 1、由一道预切分(K4)改为二道预切分(K4、 K6),目的是减少K4孔的压下量,从而减少K4的 磨损,稳定预切分孔的料形。 • 2、K3孔切分楔由原来比辊环高改为比辊环低,目 的是减少K3崩孔。 • 详见孔型图
轧制料形调整要点
• 1、辊缝预调整:轧机弹跳一般在 0.2—0.4mm之间,所以预调辊缝设 定要比标准辊缝小0.3mm。 • 2、轧制过程料形调整要根据轧件实 际尺寸与料形标准比较来调整。
柳
Liu
钢
Gang
树立信心,排出困难,实现12螺三切分达产攻关 • 1、12螺三切分达产目标:日产2400吨,成材 率大于102.20%。 • 2、攻关的主要措施: • 2.1、料形控制标准化 • 2.2、导卫预装和调整的准确性 • 2.3、采用耐磨性高的轧辊 • 2.4、轧制通道适应性改造 • 2.5、调整工的熟练调整
1、孔型设计标准化 2、导卫设计标准化 3、轧机和导卫预装标准化 4、在线料形及速度控制标准化 5、在线温度控制标准化 6、在线张力控制标准化 7、辅助设备控制参数标准化。 8、严格执行按炉送钢制度 9、检验标准规范统一性
一、孔型设计标准化
• 孔型设计是型钢生产工艺的最基本、最 重要的基础,它是导卫设计、料形设计 的依据,关系到是否能轧出合格产品及 料形、张力的稳定问题,好的孔型设计 应保证在上道料形符合要求时本道次料 形充满度在92—98%之间。料形越小充 满度应越高。
柳
Liu
钢
Gang
1、按各条生产线的工艺操作规程、料形控制表、 速度参数汇编进行控制。 2、要求生产技术科对各规格各机架的实际速度 (延伸率)进行跟踪,制定各机架实际速度基准 及允许波动标准,对活套起套高度、起落套时间 制定标准值及允许偏差。要求从现在开始每生产 完一个规格就完成该规格的参数标准。 3、各轧机班的调整要以中值为目标,越靠近中值, 说明控制得越稳定。
• 1、加热温度;要求强度高而韧性可以稍 差的微合金钢,如螺纹钢,加热温度可 以高于1200度,对以韧性为主要指标的 钢材,如拉丝材,则必须控制在1150度 以下。 • 2、开轧温度越低,钢材强度越高,伸长 率会稍有下降
柳
Liu
钢
Gang
•
•
• •
1、由生产技术科制定每个导卫预装标 准尺寸: 1)滑动导卫内腔尺寸及制定允许磨损 最大值。 2)每个滚动导卫辊轮开口度预装标准 及允许偏差。 本项工作在6月10日前完成
2、准备车间要严格按生产技术下发的预装标 准进行预装,管区工程师和生产车间加强 检查验收,凡预装不合格的,责任由准备 车间承担(生产车间调整过的由生产车间 承担)
1、张力调整越好,成品通条尺寸均匀性就越 好。 2、粗中轧张力在不堆钢情况下越小越好。 3、活套投入越多,消除张力就越好。 4、生产技术科要制定各规格最低投入活套数 量,低于本数量不得生产,否则会极大影响 成材率指标。
• 1、各飞剪在轧制不同钢种、不同规格时 各项参数的基准值及允许偏差。 • 2、风冷线(冷床)各项参数的基准值及 允许偏差。 • 3、冷剪机剪切支数及允许超剪支数规定 • 4、打包道次及位置标准
1、化学成分是影响产品性能的第一大要素, 所以必须按规定严格坯料的专坯专用。 2、按炉送钢制度是冶炼、轧钢两个工序质量 控制的最基本、最重要制度,必须严格遵 守。 3、当坯料不能满足专坯专用时,由生产技术 科重新制定温度工艺,在确保性能前提下 才允许生产。
1、检验站要研究产品的相关标准和用户的作 用要求,制定出详细的入库标准。 2、对标准未明确的产品缺陷要有实物或照片 作对照。 3、检验作为我厂产品质量的最后一道关口, 要严格统一执法,避免出现大量的质量异 议和质量事故。
• 1、影响产品性能的三大因素是:化学成分、 加热和轧制温度、冶炼和轧制缺陷。 • 2、在线温度控制要严格按工艺操作规程(常 规产品)、品种钢操作规程、核电钢操作规程 和新产品新工艺的试轧操作要点进行控制。 • 3、所有参数控制不能满足于不超标就成,而 应以中间值为调整目标,越靠近中间值越好。 若参数已很靠近中间值,还出现性能不合问题, 就及时调整工艺参数标准。