大型催化裂化装置再生器旋风分离器更换施工技术
催化裂化装置甲醇制烯烃反应器旋风分离器安装方法
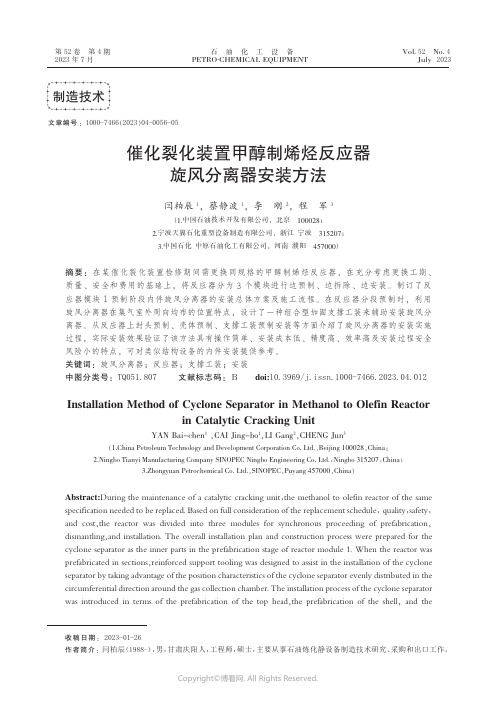
# 旋风分离器安装方案实施
术确定集气室的安装位置及一级旋风分离器的开 孔位置!完成集气室的安装及开孔' 焊接前将集 气室与上封头进行十字加固!防止焊接引起上封 头端口水平度超标' 采用气体保护焊进行对称焊 接!先焊接外口!再焊接里口' 所有工序完成后再 将封头进行翻转' 壳体预制
因壳体直径大!因此在组焊筒节纵焊缝时!应 保证单节筒节纵焊缝错边量和端口水平度' 各筒 节环焊缝组对时应控制对口间隙均匀一致! 保证 组对后的端口水平度' 大段筒节上下端口采用 :;*$")// 钢 管 十 字 加 固 ! 纵 焊 缝 * 环 焊 缝 的 错 边 量 * 棱 角 度 以 及 椭 圆 度 应 当 符 合 %&'()*$"-* < *$"-2 ) !"** # 压 力 容 器 $ %,&的 要 求 '
用带间隙全尺寸内样板检查上封头内表面形 状偏差!最大形状偏差外凸不得大于 *-!$45+5 为内径,!内凹不得大于 "-6!$45' 检查时样板垂 直于待测表面!避开焊缝进行测量'上封头各尺寸 应 符 合 %&'(7!$*+,)!"*" 的 规 定 %6&' 集气室安装
上封头预制完成检测合格后安装集气室' 安 装集气室时!先将上封头翻转!端口朝上+集气室 为分片预制整体安装,! 调整上封头端口水平度! 使 其 保 持 在 #)// 以 内 ' 然 后 利 用 89: 辅 助 放 样 技
催化裂化装置两器旋风分离器更换技术探讨

梁
卓
彭振亚
周旭东
构 景武
中国石油天然气第一建设公司 河南洛阳
4 7 1 0 1 2
摘
要
随着我 国炼油建设总体技术水平的发展 , 催化裂化装置两器 内旋风分离器 的更换施工技术有了长足发展。如何利 用施工企业现有机械设 备、 根据现场催化装置特点和施工条件 , 经济合理选择施 工方案成 了施工企业 日益关注的 问题。本 文通过对旋风分离器 内部组焊 、 侧壁开孔 、 顶部开 孔、 整体更换施工技术进行 比较分析 , 对 几种施工方法进
头 1 0 沉 降段 1 1提 升 管 l 2 汽提 段 1 3待 生立 管 l 4 二 段 密 相床 1 5再 生立 管 1 6再生塞阀
同样采用临时拉杆 固定后焊接 。焊接后对旋风分离器整体进行
复查。待所有安装料腿 、 拉杆及翼阀安 装完毕 , 检查合格后对所
有加固件进行拆除。
大成 为催 化裂化装置检修的重点 。合理 的选择施工方案是保证 施工企业 目标控 制、 进度控制 、 费 用控 制重要的技术 手段 。
1旋风 分 离器 更换 的原 因
在两器 内长期 高温的作用下 ( 再生器 6 5 0 ~6 8 0  ̄ C,反应器 4 8 0 ~5 0 0  ̄ C) , 会 发生 金属 蠕变、 焊缝 开裂 、 局部变形及 衬里脱 落
图 2同轴式提升管催化裂化
首先对旋 风分离本体安装就位后 ,采用临时拉杆与两器器壁进
行 相 焊 加 固 。焊 接 完 毕 经 复 查 合 格 , 然 后对 灰 斗 部分 进 行 组 对 ,
注: l空气分布管 2待 生塞 阀 3一段密相床 4 5旋风分 离器 6外部烟气集合 管 7旋风分 离系统 8快速分离设 施 9耐磨弯
2007一再旋风系统更换施工方案.

工程编号:发放编号:炼油厂一催化装置塔-2002再生器恢复生产施工方案编制:审核:审定:安全:会签:北京燕华公司炼油厂检修项目部2007年11月一、工程概述炼油厂一催化装置于1969年6月建成投产,按加工大庆常压蜡油原料设计,实际生产条件为大庆混合蜡油掺炼60﹪大庆减压蜡油,年开工时数为6000小时。
对旋风系统改造完成后开车至2000年。
2000年由于各种原因一催化停车,应生产厂要求一催化恢复生产。
本次施工内容包括修复平台、塔本体除锈防腐、内部修复、喷火嘴修复或更换。
1995年改造完成后停滞时间过长部分操作参数调整受到了再生器负荷及取热能力、催化剂活性的维持、反应器操作参数等限制,此次根据原料的性质,对装置进行完善改造。
再生器旋风系统改造包括更换再生器内8组旋风分离器,其中每组由1台一级旋风分离器(φ1400/1094×10039×10)和1台二级旋风分离器(φ1400/998×8911×10)组成,共计16台;旋风分离器的料腿、拉杆(利旧)、防倒锥、翼阀等。
现场打衬里、恢复衬里由正邦公司负责,焊接保温钉、龟甲网由我公司负责。
本次施工主要难点在于,需更换的16台旋风分离器全部位于再生器内部,拆除、安装作业空间狭小,特别是取出第一台旋风分离器和放入最后一台旋风分离器施工难度相当大。
由于大部分工作都集中在再生器内部,深度交叉作业不可避免,不安全因素较多,加大了施工风险。
再生器顶部有油气集气管、烟道、平台等,无法将其顶部封头打开,只能在其壁板上开天窗。
改造设备均有衬里,这就增加了设备重量和施工工序。
因为无法进入设备内部进行实际测量,这就增加了许多不可预见的困难,大大的加大了技术准备和施工准备工作的难度。
二、编制依据及施工验收规范1. SEI设计图纸B230-238/Ⅳ-EQ12.《钢制压力容器》GB150-983.《中、低压化工设备施工及验收规范》HGJ208-834.《现场设备、工业管道焊接工程施工及验收规范》GB50236-985.《催化裂化装置反应再生系统设备施工及验收规范》SH3504-20006.《工程建设交工技术文件规定》SH3503-20017.《石油化工施工安全技术措施》SH3505-1999三、施工准备1. 施工前由施工技术人员向施工班组作业人员进行技术交底。
旋风分离器更换的施工方法及措施
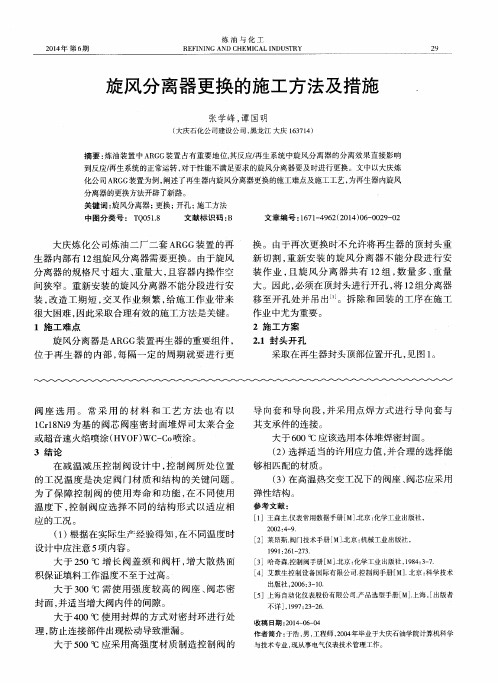
设 计 中应 注意 5 项 内容 。
大于2 5 0 o C增 长 阀 盖 颈 和 阀杆 , 增 大 散 热 面
[ 3 ]哈奇森. 控制阀手册 [ M] . 北京 : 化学工业 出版社 , 1 9 8 4 : 3 - 7 . [ 4 ]艾默生控制设备国际有限公 司. 控制阀手册[ M] . 北京 : 科学技术
[ 5 ]上海 自 动化仪表股份有限公司. 产品选型手册 E M] . 上海 , [ 出版者
不详] , 1 9 9 7 : 2 3 — 2 6 .
收稿 E t 期: 2 0 1 4 — 0 6 — 0 4
作者简介 : 于浩, 男, 工程师 , 2 0 0 4 年毕业于大庆石油学院计算机科学 与技术专业, 现从事 电气仪表技术管理工作。
作业 中尤 为重 要 。
2 施工 方案 2 . 1 封头 开孔
旋风 分离 器是 A R G G装置再 生 器 的重要 组件 , 位 于再 生 器 的 内部 , 每 隔 一 定 的 周期 就 要 进行 更
采 取在再 生 器封 头顶 部位 置开孔 , 见图 1 。
阀 座 选 用 。 常 采 用 的 材 料 和 工 艺 方 法 也 有 以
炼 油 与 化 工
2 0 1 4年 第 6 期
REFI NI NG AND CHEM I CAL I NDUS TRY
2 9
旋 风 分 离器更 换 的施 工方 法及 措 施
张 学峰 , 谭 国明
( 大 庆 石 化 公 司 建设 公 司 , 黑龙 江 大庆 1 6 3 7 1 4 )
摘要 : 炼油装置 中A R G G 装置 占有重要地位, 其反应/ 再生系统中旋风分离器的分离效果直接影响 到反应, 再生系统的正常运转 , 对于性能不满足要求的旋风分离器要及时进行更换。文中以大庆炼 化公司A R G G装置为例, 阐述了再生器 内旋风分离器更换 的施工难点及施工工艺, 为再生器内旋风 分离器的更换方法开辟了新路。 关键词 : 旋风分离器 ; 更换; 开孔 ; 施工方法 中图分类号 : T Q 0 5 1 . 8 文献标识码 : B 文章 编号 : 1 6 7 1 — 4 9 6 2 ( 2 O l 4 ) 0 6 一 O 0 2 9 — 0 2
催化裂化装置再生器旋分系统更换
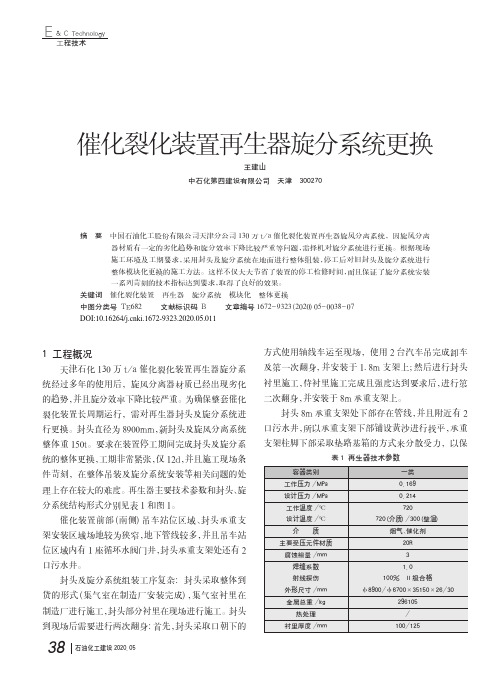
石油化工建设2020.051工程概况天津石化130万t /a 催化裂化装置再生器旋分系统经过多年的使用后,旋风分离器材质已经出现劣化的趋势,并且旋分效率下降比较严重。
为确保整套催化裂化装置长周期运行,需对再生器封头及旋分系统进行更换。
封头直径为8900mm ,新封头及旋风分离系统整体重150t 。
要求在装置停工期间完成封头及旋分系统的整体更换,工期非常紧张,仅12d ,并且施工现场条件苛刻,在整体吊装及旋分系统安装等相关问题的处理上存在较大的难度。
再生器主要技术参数和封头、旋分系统结构形式分别见表1和图1。
催化装置前部(南侧)吊车站位区域、封头承重支架安装区域场地较为狭窄,地下管线较多,并且吊车站位区域内有1座循环水阀门井,封头承重支架处还有2口污水井。
封头及旋分系统组装工序复杂:封头采取整体到货的形式(集气室在制造厂安装完成),集气室衬里在制造厂进行施工,封头部分衬里在现场进行施工。
封头到现场后需要进行两次翻身:首先,封头采取口朝下的方式使用轴线车运至现场,使用2台汽车吊完成卸车及第一次翻身,并安装于1.8m 支架上;然后进行封头衬里施工,待衬里施工完成且强度达到要求后,进行第二次翻身,并安装于8m 承重支架上。
封头8m 承重支架处下部存在管线,并且附近有2口污水井,所以承重支架下部铺设黄沙进行找平,承重支架柱脚下部采取垫路基箱的方式来分散受力,以保催化裂化装置再生器旋分系统更换王建山中石化第四建设有限公司天津300270摘要中国石油化工股份有限公司天津分公司130万t /a 催化裂化装置再生器旋风分离系统,因旋风分离器材质有一定的劣化趋势和旋分效率下降比较严重等问题,需择机对旋分系统进行更换。
根据现场施工环境及工期要求,采用封头及旋分系统在地面进行整体组装,停工后对旧封头及旋分系统进行整体模块化更换的施工方法。
这样不仅大大节省了装置的停工检修时间,而且保证了旋分系统安装一系列苛刻的技术指标达到要求,取得了良好的效果。
再生器内部旋风分离器更换吊装施工方法
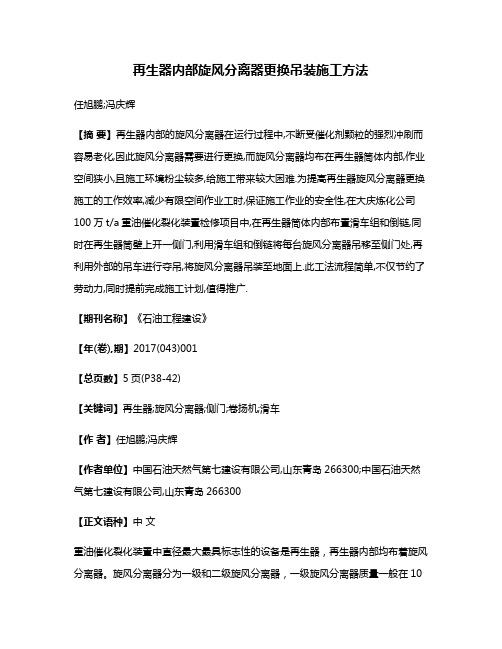
再生器内部旋风分离器更换吊装施工方法任旭鹏;冯庆辉【摘要】再生器内部的旋风分离器在运行过程中,不断受催化剂颗粒的强烈冲刷而容易老化,因此旋风分离器需要进行更换,而旋风分离器均布在再生器筒体内部,作业空间狭小,且施工环境粉尘较多,给施工带来较大困难.为提高再生器旋风分离器更换施工的工作效率,减少有限空间作业工时,保证施工作业的安全性,在大庆炼化公司100万t/a重油催化裂化装置检修项目中,在再生器筒体内部布置滑车组和倒链,同时在再生器筒壁上开一侧门,利用滑车组和倒链将每台旋风分离器吊移至侧门处,再利用外部的吊车进行夺吊,将旋风分离器吊装至地面上.此工法流程简单,不仅节约了劳动力,同时提前完成施工计划,值得推广.【期刊名称】《石油工程建设》【年(卷),期】2017(043)001【总页数】5页(P38-42)【关键词】再生器;旋风分离器;侧门;卷扬机;滑车【作者】任旭鹏;冯庆辉【作者单位】中国石油天然气第七建设有限公司,山东青岛266300;中国石油天然气第七建设有限公司,山东青岛266300【正文语种】中文重油催化裂化装置中直径最大最具标志性的设备是再生器,再生器内部均布着旋风分离器。
旋风分离器分为一级和二级旋风分离器,一级旋风分离器质量一般在10t左右,长度10 m,直径最大处约1.5 m;二级旋风分离器质量一般在8 t左右,长度和最大直径比一级略小。
近年来再生器旋风分离器的更换施工较为频繁,由于旋风分离器位于再生器内部,四周是封闭状态,施工人员需在狭小的有限空间内作业,且施工环境粉尘较多,因此给施工带来较大困难。
传统的拆除方法主要分为两种,一种是拆除再生器封头,再将旋风分离器用吊车直接提升出来;第二种是旋风分离器分段或整体从装卸孔拆卸出来。
但如果遇到同轴式两器(再生器和沉降器在同一条轴线上),沉降器位于再生器上方,则不可能先将沉降器全部拆除后再拆除再生器的旋风分离器,这样做工程量相当巨大,方案不可行;而对于第二种方法,装卸孔一般仅比旋风分离器直径稍大,旋风分离器长度较长,不易向外移出,因而施工进度缓慢。
同轴式催化裂化装置旋风系统及汽提段更换

同轴式催化裂化装置旋风系统及汽提段更换发布时间:2023-03-07T07:34:39.618Z 来源:《中国科技信息》2022年19期第10月作者:孙海强张正[导读] 主要设备的同轴重催化装置是由于设备老化、轴瓦磨损、支架堵塞等原因造成的,结合施工条件和工期孙海强张正(大庆炼化公司炼油生产一部催化作业区黑龙江省大庆市163000)摘要:主要设备的同轴重催化装置是由于设备老化、轴瓦磨损、支架堵塞等原因造成的,结合施工条件和工期,采取了一种以四个单级旋风式旋流机为一体的保护拆解方式,在同轴催化裂化装置的生产过程中,由于干气流量的增加,吸收系统难以运行。
关键词:同轴式催化装置;再生器;旋风系统;汽提段引言比较运行数据,分析机组结构,确定了造成这一问题的原因是由于沉淀塔汽提段的磨损和穿孔。
增加蒸汽段容积、降低两台设备之间的扩散压力、将提升管中的干气预提升至蒸汽预提升等一系列措施有效解决了吸附系统运行中的问题,有效防止了磨损和再生系统之间的交叉安全事故。
同时,将干气流量从9吨/小时降至约5吨/小时,将氮含量从20%降至10%以下,将烟机-发电量从0.5兆瓦降至0.000兆瓦,为同类催化裂化装置的同类问题分析与治理提供参考。
一、工程概况某炼油厂140000 t/a重油催化装置从1997年投产后,经历了几次技术改造,使其运行状况有了很大的改变,其中存在衬里磨损、腿部延迟、排气段人体锯齿形护罩磨损等问题。
为了确保双催化装置在未来四年内的安全生产,本次停机维护包括:将再生器的第一和第二循环更换为12组,共24组,完全更换除尘器和等待提升管的蒸汽取样部分,并更换提升管出口的两组粗涡流。
更换催化剂分配器和主通风管。
最大提升高度和物体重量:屋顶沉降器,4个单节旋转,再装4个单段,总的起重质量114.8 t (含塔顶平台和部分管线),吊装高度68.70米,由于施工时间紧迫,施工场地狭小,需要45天才能完成两个内部部件的拆卸和更换。
催化装置反应器内件更换施工技术

3 . 材料验收
3 . 1材 料检验 :
本工程采用的所有材料均应具有 出厂质量证 明书 ,
1 . 施 工程序
施 工准备一设备 、材料验收一衬里拆除一拆除加
并符合设计要求和 国家现行有关 标准的规定 。 3 . 2设备及 附件 的检 验
固一 内件拆除一 内件安装一衬里修补一交工验收。
梁 志 强
( 陕西化建工程有限责任公 司 陕西杨 凌 7 1 2 1 0 0 )
摘
要:以延安炼油厂2 0 0 7  ̄ 吨/ 年重油催化裂化装 置反应器 内件更换 为例 ,详细阐述 了反应 器内件 更换 的施工方法, 介 绍了此类工程施工的经验 ,它对类似 装置反应 器的内件更换施工具有一定的参考价值 。
c 、锥体表面用 3 0 0 a r m钢板尺沿母线检查 ,其局部 凸凹值不得大 于 l mm;锥体下端插入灰斗 内的长度允许
偏差为 + 5 —0 m m。
5 . 3料腿加 固 :在 封闭罩上焊接立式 支架对料腿进
行加 固。 5 . 4 封头 吊耳焊接 :在 旧吊耳顺 时针方 向6 0 0 m m 处重 新焊接4 个3 0 吨板式 吊耳 ( 均布 )。
现过再次解体安装 以及机体变形等情况 ,这就为对接质
催化裂化装置反应器和再生器的技术改造
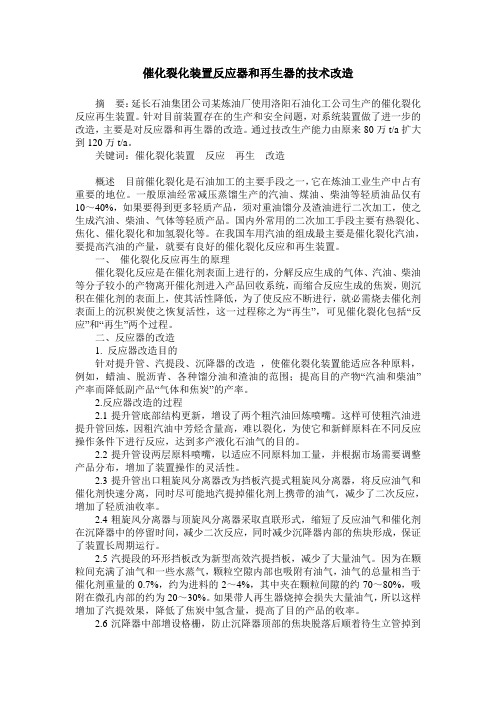
催化裂化装置反应器和再生器的技术改造摘要:延长石油集团公司某炼油厂使用洛阳石油化工公司生产的催化裂化反应再生装置。
针对目前装置存在的生产和安全问题,对系统装置做了进一步的改造,主要是对反应器和再生器的改造。
通过技改生产能力由原来80万t/a扩大到120万t/a。
关键词:催化裂化装置反应再生改造概述目前催化裂化是石油加工的主要手段之一,它在炼油工业生产中占有重要的地位。
一般原油经常减压蒸馏生产的汽油、煤油、柴油等轻质油品仅有10~40%,如果要得到更多轻质产品,须对重油馏分及渣油进行二次加工,使之生成汽油、柴油、气体等轻质产品。
国内外常用的二次加工手段主要有热裂化、焦化、催化裂化和加氢裂化等。
在我国车用汽油的组成最主要是催化裂化汽油,要提高汽油的产量,就要有良好的催化裂化反应和再生装置。
一、催化裂化反应再生的原理催化裂化反应是在催化剂表面上进行的,分解反应生成的气体、汽油、柴油等分子较小的产物离开催化剂进入产品回收系统,而缩合反应生成的焦炭,则沉积在催化剂的表面上,使其活性降低,为了使反应不断进行,就必需烧去催化剂表面上的沉积炭使之恢复活性,这一过程称之为“再生”,可见催化裂化包括“反应”和“再生”两个过程。
二、反应器的改造1. 反应器改造目的针对提升管、汽提段、沉降器的改造,使催化裂化装置能适应各种原料,例如,蜡油、脱沥青、各种馏分油和渣油的范围;提高目的产物“汽油和柴油”产率而降低副产品“气体和焦炭”的产率。
2.反应器改造的过程2.1提升管底部结构更新,增设了两个粗汽油回炼喷嘴。
这样可使粗汽油进提升管回炼,因粗汽油中芳烃含量高,难以裂化,为使它和新鲜原料在不同反应操作条件下进行反应,达到多产液化石油气的目的。
2.2提升管设两层原料喷嘴,以适应不同原料加工量,并根据市场需要调整产品分布,增加了装置操作的灵活性。
2.3提升管出口粗旋风分离器改为挡板汽提式粗旋风分离器,将反应油气和催化剂快速分离,同时尽可能地汽提掉催化剂上携带的油气,减少了二次反应,增加了轻质油收率。
350万t催化裂化装置再生器现场建造技术
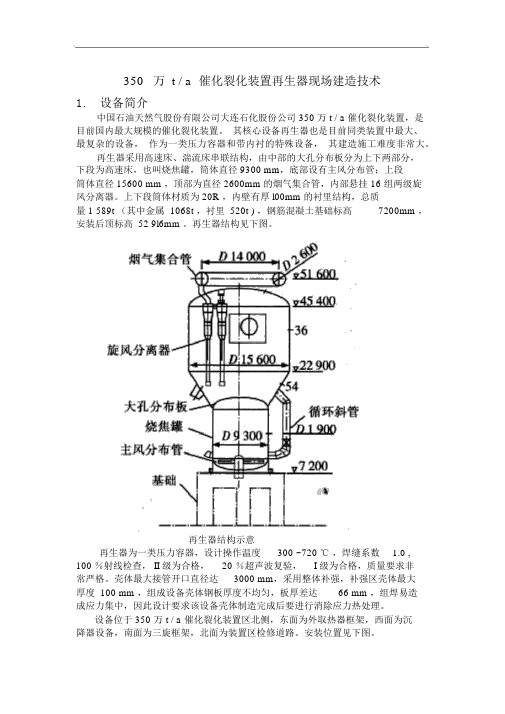
350万 t / a 催化裂化装置再生器现场建造技术1.设备简介中国石油天然气股份有限公司大连石化股份公司 350 万 t / a 催化裂化装置,是目前国内最大规模的催化裂化装置。
其核心设备再生器也是目前同类装置中最大、最复杂的设备,作为一类压力容器和带内衬的特殊设备,其建造施工难度非常大。
再生器采用高速床、湍流床串联结构,由中部的大孔分布板分为上下两部分,下段为高速床,也叫烧焦罐,筒体直径 9300 mm,底部设有主风分布管;上段筒体直径 15600 mm ,顶部为直径 2600mm 的烟气集合管,内部悬挂 16 组两级旋风分离器。
上下段筒体材质为 20R ,内壁有厚 l00mm 的衬里结构,总质量 1 589t (其中金属 1068t ,衬里 520t ) ,钢筋混凝土基础标高7200mm ,安装后顶标高 52 9l6mm 。
再生器结构见下图。
再生器结构示意再生器为一类压力容器,设计操作温度300 ~720 ℃,焊缝系数 1.0 ,100 %射线检查, II 级为合格,20 %超声波复验,I 级为合格,质量要求非常严格。
壳体最大接管开口直径达3000 mm,采用整体补强,补强区壳体最大厚度 100 mm ,组成设备壳体钢板厚度不均匀,板厚差达66 mm ,组焊易造成应力集中,因此设计要求该设备壳体制造完成后要进行消除应力热处理。
设备位于 350 万 t / a 催化裂化装置区北侧,东面为外取热器框架,西面为沉降器设备,南面为三旋框架,北面为装置区检修道路。
安装位置见下图。
再生器采用分段、分片到货方式:烧焦罐底封头和裙座为1段整体到货;烧焦罐 D9300 mm 筒体分 5 段到货;烧焦罐顶大孔分布板分2段到货;大锥段、上部 D 15600 mm 筒体、顶封头均为分片到货;顶部烟气集合管分8 段到货;主风分布管整体到货;旋风分离器整体到货;其他构件分别按图纸上的件号供货。
2.施工流程施工流程见下图:施工流程壳体到货后分 3 大段预制成型:下段即烧焦罐部分包括裙座、下封头及D9D 300 mm 筒体段,重约190t ;中段包括再生器D15 600 / D9300 mm 锥段、15600 mm 筒体段及大孔分布板,重约405t ; 上段包括再生器顶封头重约180t。
再生器内部旋风分离器更换吊装施工方法
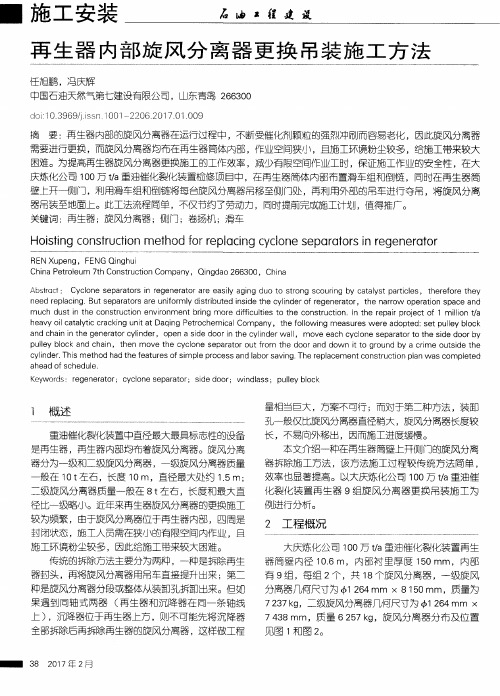
摘
要 :再 生器 内部的旋 风分离器在运 行过 程中 ,不断 受催化剂颗 粒的强烈) q D f  ̄ U 而容 易老化 ,因此旋风分 离器
需要进行更换 ,而旋风 分离器均布在再 生器筒体 内部 ,作业 空间狭小 ,且施 工环境 粉尘较多 ,给施工带来较大 困难 。为提高再生器旋风 分离器更换施 工的工作效率 ,减少有 限空间作业工 时 ,保证施 工作业的安全性 ,在大 庆炼化公司 1 O 0万 t / a重油催 化裂化装置检 修项目中 ,在再 生器筒体 内部 布置滑车 组和倒链 ,同时在再生器 筒 壁上开一侧 门 ,利 用滑车组和倒链将每 台旋风 分离器 吊移至I  ̄ I U i ' ] 处 ,再利用外部 的吊车进 行夺吊 ,将旋风 分离 器吊装至地面上。此工法流程简 单 ,不 仅节约 了劳动力 ,同时提前完成施工计划 ,值得 推广。
mu c h d u s t i n t h e c o n s t r u c t i o n e n v i r o n me n t b r i n g mo r e d i f f i c u l t i e s t o t h e c o n s t r u c t i o n . t n t h e r e p a i r p r o j e c t o f 1 mi l I i o n t / a
a n d c h a i n i n t h e g e n e r a t or c y l i n d e r ,o p e n a s i d e d o or i n t h e c y l i n d e r wa l l ,mo v e e a c h c y c l o n e s e p a r a t o r t o t h e s i d e d o o r b y
催化裂化装置反再系统施工技术方法

催化裂化装置反再系统施工技术方法摘要:反再系统(反应器和再生器)是催化裂化装置的核心设备,是影响催化裂化装置安全和经济效益的关键因素,两器的施工工艺复杂,壳体厚度相差较大,焊接工作量和施工难度比较大,焊接变形较难控制、吊装难度大、内件安装精度要求高.本文我们主要以青海大美项目60万吨/年DMTO装置反再系统为例来探讨“两器”的组对安装工艺流程。
关键词:反应器、再生器、壳体组装、焊接、压力试验。
一、施工概述1、施工方法反应器、再生器采用“立式组装法”施工。
分段组对时按排版图的顺序和位置,采用立装法,由下至上依次组装各筒节,形成分段筒体。
分段安装时采用正装法将各分段筒体按顺序进行吊装。
封头、椎体需在组装平台上单独进行组装。
顶部封头预制成型组焊合格后,需翻转进行衬里施工。
顶部封头吊装前需将旋风、料腿等内部构件临时放置在筒体内。
2、反应器、再生器主要设备参数设备名称反应器(R1101)再生器(R1102)容器类别III类(A2级)II类(D2级)设计压力 MPa 0.25 0.25工作压力 MPa 0.2―0.3 0.2―0.3设计温度℃介质550,壳体350 介质720,壳体350工作温度℃450―550 600―720介质甲醇,油气,催化剂烟气,催化剂容器规格ϕ15600/ϕ11800×45090×36ϕ7000/ϕ5500×25300×22/24金属净重(不含衬里)600t 160t热处理局部热处理不做热处理液压试验 MPa3、反应器、再生器主要吊装分段参数筒节预制组对时可采用75t汽车吊两台,280t履带吊一台,400t履带吊一台进行现场分片分段组装。
其中反应器分四段、再生器分二段进行吊装,反应器、再生器分段吊装时第一段均采用400t履带吊吊装,其余各段吊装以及封头翻转均采用600t履带吊主吊,采用400t履带吊溜尾配合。
二、主要施工程序筒体、封头成品半成品及旋风分离器等内件检验验收→封头、椎体等组装成型→筒节、裙座组装成型→分段组装焊接→焊缝无损检测→接管安装→各段部分内件安装→劳动保护安装→基础验收→分段吊装(除封头外)→段之间环焊缝热处理、无损检测→上封头衬里→上封头翻转、吊装→旋风系统及内件安装→拆除临时加固件→交工验收。
大型催裂化反应器封头及旋风系统整体双机抬吊施工工法(2)

大型催裂化反应器封头及旋风系统整体双机抬吊施工工法大型催裂化反应器封头及旋风系统整体双机抬吊施工工法一、前言大型催裂化反应器封头及旋风系统整体双机抬吊施工工法是用于大型催化裂化装置封头和旋风系统的安装方法。
本文将详细介绍该工法的特点、适应范围、工艺原理、施工工艺、劳动组织、机具设备、质量控制、安全措施、经济技术分析以及工程实例。
二、工法特点该工法特点如下:1. 双机抬吊:采用两台起重机同时协同作业,提高施工效率。
2. 整体吊装:封头和旋风系统一起进行吊装,减少吊装次数,减少施工周期。
3.安全可靠:采取多种安全措施,确保施工过程中的安全。
三、适应范围该工法适用于大型催化裂化装置封头和旋风系统的安装,适用于需求较高的化工、石油等行业。
四、工艺原理该工法通过双机抬吊的方式,将催化裂化装置封头和旋风系统整体吊装到指定位置。
其原理为首先通过计算和预测确定起重机的位置和高度,然后进行协同作业,确保吊装过程中的平衡和稳定。
在施工过程中,需要采取一系列技术措施,如加固梁、牵引索等,以确保吊装的安全和顺利进行。
五、施工工艺施工工艺包括以下几个阶段:1. 设计和准备阶段:根据实际情况进行工艺设计和准备工作,包括选定起重机的型号和数量、确定起重机的位置和高度等。
2. 预制阶段:根据设计要求进行封头和旋风系统的预制工作,包括制作封头和旋风系统的零部件、进行检验和质量控制等。
3. 吊装阶段:根据预先确定的吊装计划进行吊装作业,采用双机抬吊的方式,确保封头和旋风系统整体吊装到指定位置。
4. 安装和调试阶段:进行封头和旋风系统的安装和调试工作,包括连接管道、调整位置等。
5. 完工阶段:进行工程验收和完工报告,确保施工过程完成。
六、劳动组织施工过程中,需要合理安排劳动力和团队,包括起重机操作人员、工程师和工人等。
同时,还需要进行周密的协调和沟通,确保各个环节的顺利进行。
七、机具设备该工法需要使用起重机、加固梁、牵引索等机具设备。
催化裂化装置第三级旋风分离器的技术改造
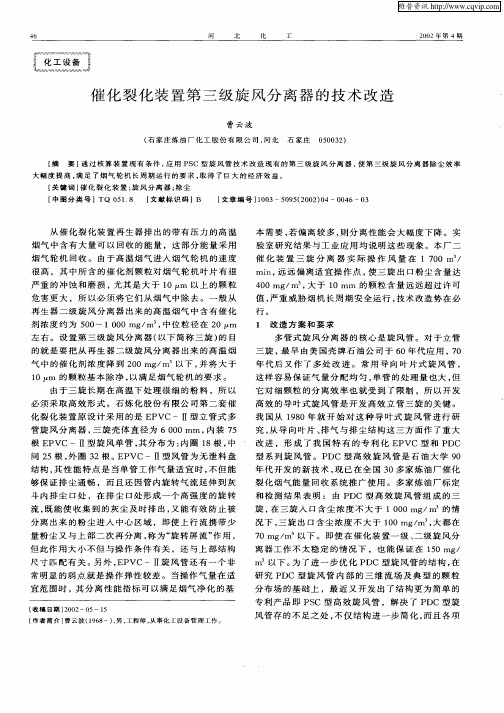
旋 , 三 旋 入 口含 尘 浓 度 不 大 于 10 0mg m3 情 在 0 / 的 况 下 , 旋 出 口含 尘 浓 度 不 大 于 1 0mg m 大 都 在 三 0 / , 7 / 0mg m 以下 。即 使 在 催 化 装 置 一级 、 级 旋 风 分 二 离 器 工 作 不 太 稳 定 的情 况 下 ,也 能 保 证 在 1 0mg 5 /
必 须 采 取 高 效 形 式 。 石炼 化 股 份 有 限公 司第 二 套 催
化 裂 化 装 置 原 设 计 采 用 的是 E VC一 Ⅱ型 立 管 式 多 P
高 效 的 导 叶 式 旋 风 管 是 开 发 高效 立 管三 旋 的关 键 。
我 国从 1 8 9 0年 就 开 始 对 这 种 导 叶式 旋 风 管 进 行 研 究 , 导 向 叶片 、 气 与 排 尘结 构 这 三 方 面作 了重 大 从 排 改 进 ,形 成 了我 国特 有 的专 利 化 E PVC 型 和 P DC 型 系 列 旋 风 管 。P DC 型 高 效 旋 风 管 是 石 油 大 学 9 0
【 摘
要 】 过 核算装 置 现有条 件 , 用 P C型 旋风 管技 术改造 现有 的第三 级旋风 分 离器 , 第 三级旋 风分 离器 除尘效率 通 应 S 使
大 幅 度 提 高 , 足 了烟 气 轮 机 长 周 期 运 行 的 要 求 , 得 了 巨 大 的 经 济 效 益 。 满 取
【 键 词 】 化 裂 化 装 置 ; 风 分 离 器 ; 尘 关 催 旋 除 【 图分 类号 】 中 TQ 5 . 0 18 【 献 标 识 码 】B 文 【 章 编 号 】0 3 0 5 2 0 ) 4 0 6 3 文 1 0 —5 9 ( 0 2 0 —0 4 —0
催化裂化装置沉降器旋风分离器翼阀更换
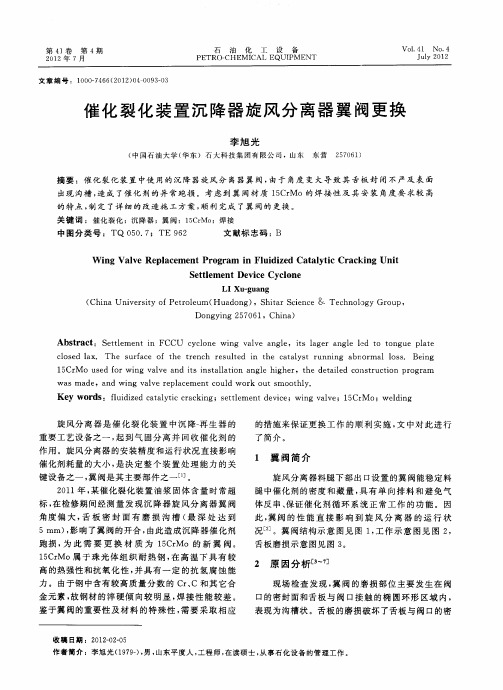
2 原 因分 析 ~] 。’
现场 检查 发 现 , 阀 的磨 损部 位 主 要发 生 在 阀 翼 口的密封 面和舌 板 与 阀 口接 触 的椭 圆环 形 区域 内 ,
金元素 , 故钢 材 的淬 硬倾 向较 明显 , 接 性 能较 差 。 焊
鉴于翼 阀的重要性 及 材 料 的 特殊 性 , 要 采 取相 应 需
Ab ta t S tlm e ti CCU y l n n av n l , i a e n l e o t n u lt s r c : ete n n F c co e wig v l e a g e t lg r a g e ld t o g e p ae s
况_ 。翼 阀结构示 意 图 见 图 1 工 作示 意 图见 图 2 2 ] , , 舌板磨 损示 意 图见 图 3 。
键设备 之一 , 阀是其 主要部 件之 一_ 。 翼 】 ] 21 0 1年 , 催化 裂化装 置 油浆 固体 含量 时 常超 某 标 , 检修期 间经 测 量发 现 沉 降 器旋 风 分 离 器翼 阀 在
K e r s fu d z d c t l t r c i g;s t l me td vc ;wi g v l e CI o y wo d : l i ie a a y i c a k n c e te n e ie n a v ;1 ;we d n 5 M l ig
出现沟槽 , 成 了催 化剂 的异 常跑损 。考虑 到 翼 阀材 质 1 C Mo的焊 接 性及 其 安 装 角度要 求较 高 造 5r
的 特 点 , 定 了详 细 的 改 造 施 工 方 案 , 利 完 成 了翼 阀 的 更 换 。 制 顺 关 键 词 :催化裂化 ; 降器 ;翼 阀;1CMo 沉 5 r ;焊接 中 图 分 类 号 :T 0 0 7 Q 5 . ;TE 9 2 6 文献标 志码 : B
浅述催化裂化装置三级旋风分离器衬里的施工
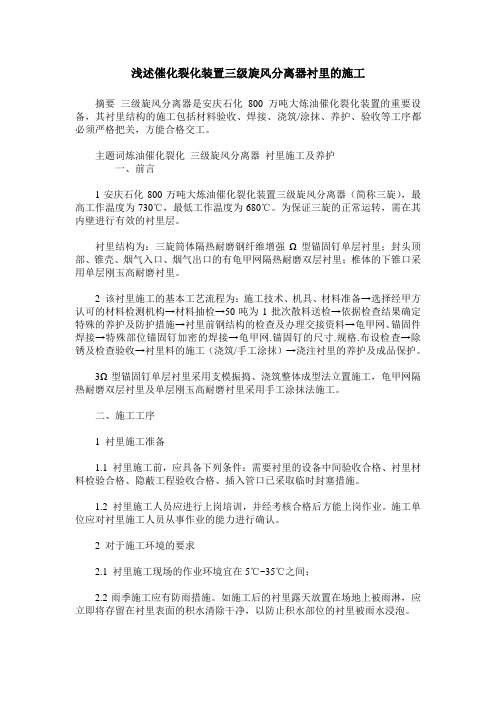
浅述催化裂化装置三级旋风分离器衬里的施工摘要三级旋风分离器是安庆石化800万吨大炼油催化裂化装置的重要设备,其衬里结构的施工包括材料验收、焊接、浇筑/涂抹、养护、验收等工序都必须严格把关,方能合格交工。
主题词炼油催化裂化三级旋风分离器衬里施工及养护一、前言1安庆石化800万吨大炼油催化裂化装置三级旋风分离器(简称三旋),最高工作温度为730℃,最低工作温度为680℃。
为保证三旋的正常运转,需在其内壁进行有效的衬里层。
衬里结构为:三旋筒体隔热耐磨钢纤维增强Ω型锚固钉单层衬里;封头顶部、锥壳、烟气入口、烟气出口的有龟甲网隔热耐磨双层衬里;椎体的下锥口采用单层刚玉高耐磨衬里。
2 该衬里施工的基本工艺流程为:施工技术、机具、材料准备→选择经甲方认可的材料检测机构→材料抽检→50吨为1批次散料送检→依据检查结果确定特殊的养护及防护措施→衬里前钢结构的检查及办理交接资料→龟甲网、锚固件焊接→特殊部位锚固钉加密的焊接→龟甲网.锚固钉的尺寸.规格.布设检查→除锈及检查验收→衬里料的施工(浇筑/手工涂抹)→浇注衬里的养护及成品保护。
3Ω型锚固钉单层衬里采用支模振捣、浇筑整体成型法立置施工,龟甲网隔热耐磨双层衬里及单层刚玉高耐磨衬里采用手工涂抹法施工。
二、施工工序1 衬里施工准备1.1 衬里施工前,应具备下列条件:需要衬里的设备中间验收合格、衬里材料检验合格、隐蔽工程验收合格、插入管口已采取临时封塞措施。
1.2 衬里施工人员应进行上岗培训,并经考核合格后方能上岗作业。
施工单位应对衬里施工人员从事作业的能力进行确认。
2 对于施工环境的要求2.1 衬里施工现场的作业环境宜在5℃~35℃之间;2.2雨季施工应有防雨措施。
如施工后的衬里露天放置在场地上被雨淋,应立即将存留在衬里表面的积水清除干净,以防止积水部位的衬里被雨水浸泡。
3 衬里结构焊接3.1从事衬里结构焊接的焊工,应由考试合格的焊工担任,参加施焊的焊工须有相应施焊项目的合格证,并经业主考核持证上岗。
催化热裂解装置三级旋风分离器施工技术

位母 线并做出标记 , 按开 孑 L 方位 图组焊接 管。
3 . 3过渡段组焊
过渡段在 钢平台上采用整体 成形法组对 。在过渡段 中心立
E& C T e c h n o l o g yl 工程技术
施工技术
梁志强
陕西化建 工程有 限责任公司
陕西杨 凌 7 1 2 1 0 0
摘
要
三级旋风分离器 ( 简称 : 三旋) 为催化热裂解装置的核心设备之一 , 由于设备直径较大、 受公路运 输条件 的限制 , 一 般在施工现场进行制作 、 安装。 本文 以榆林能化 1 5 0 万t / a 催化热裂解装置三旋 (  ̄9 5 0 0 × 7 0 0 0 G = 2 4 0 t ) 为例 , 探 讨 了大型催化热裂解装置三级旋风分离器 的施工技术及施工过程 中应注意 的问题 ,介绍 了此类工程的施工经验 ,
口对 焊 。
第 五段 ( 上封 头段) : 首先进行球 形封 头的组装及接管 的安
2 施工 组装 流程
施工准备一铺 设组装平台一材料 、 半成品检查验 收一封头、
装, 对上封 头翻转后进行衬里 ; 衬里完成 后 , 将 封头翻转 与筒节
组装成 为一个整体。最后 用 4 0 0 t 履带 吊车整体就位安装 , 与上
车整体 吊装就位 。 第二段( 下锥形封头段) : 在预制平 台上 分片组装成锥体 , 安
装接管 , 检验合格 后用 吊车整体 吊装就位 , 与裙座筒体段下 口对
处点焊定位板 , 每个瓣片的定位 板不少于二块 口 图1 ) 。
以定位板和组装胎具为基准 ,用工卡具使瓣 片紧靠定位板
大型催化裂解反应器旋风系统及安装

关键词:催化裂解;反应器;翼阀DCC装置反应器技改作为榆能化2021年重点技改项目,反应器内件更换在装置停车期间,性质属于检修施工,难度大、工期紧,任务重。
本次技改内容包括反应器大封头分片组装更换、旋风分离系统更换、内提升管更换、汽提段挡板更换及底封头、催化剂出口更换、拆装量共计2600t;总工期50天,旋风组对质量与翼阀安装角度一次合格至关重要,是实现施工进度目标的关键因素之一。
1工程概况150万吨/年催化裂解(DCC)制乙烯装置再生器、反应器(以下简称两器)作为整个装置核心设备,反应器(900-T-4101)内一级旋风和二级旋风各12组。
DCC装置反应器旋风分离器入口变形严重,二级料腿堵塞,内件破损严重导致大量催化剂流失,两器催化剂藏量降低,催化剂单耗偏高,且催化剂进入油浆系统使油浆固含量持续走高,已达26g/L,造成油浆系统油浆泵、管道、阀门经常堵塞,导致装置多次被迫停车。
为解决此问题,项目团队对反应器(900-T-4101)进行系统改造,现已平稳运行三个月,且油浆固含量保持在4.4g/L,为装置长周期运行打下坚实的基础。
该工程的安装要点、难点主要体现在以下三个方面:反应器旋风单体部件规格大,一级旋风φ1536mm×9196mm,11.32t,二级旋风φ1468mm×8418mm,9.33t,垂直度难控制;本次施工属旧设备改造,不确定因素多;翼阀安装角度要求较高。
2反应器旋风系统及翼阀安装关键技术反应器旋风系统及翼阀安装之前的施工准备工作如下:(1)项目施工前,项目部多次派人到SEI总部、营口生产厂家对接,组织参与施工的相关人员对反应器旋风及翼阀安装技术要求、施工难点、翼阀角度如何控制等做了大量咨询,找出以往焊接变形难控制原因,应用数显电子角度仪,根据测量值确定焊接变形方向,调整施焊顺序,从而控制焊接变形,最后形成作业指导书,对所有参与施工的项目管理及施工管理人员进行了安全技术交底。
- 1、下载文档前请自行甄别文档内容的完整性,平台不提供额外的编辑、内容补充、找答案等附加服务。
- 2、"仅部分预览"的文档,不可在线预览部分如存在完整性等问题,可反馈申请退款(可完整预览的文档不适用该条件!)。
- 3、如文档侵犯您的权益,请联系客服反馈,我们会尽快为您处理(人工客服工作时间:9:00-18:30)。
大型催化裂化装置再生器旋风分离器更换施工技术周旭东;梁卓;彭振亚【摘要】在炼油装置中催化裂化装置占有重要地位,其反应/再生系统中旋风分离器的分离效果直接影响到反应/再生系统的正常运转,对于性能不满足要求的旋风分离器要及时进行更换.文章以中国石油大连石化公司350万t/a催化裂化装置检修为例,介绍了大直径再生器旋风分离器的更换作业,详细阐述了旋风分离器高精度安装的施工难点及施工工艺.施工实践验证了再生器顶部大直径开孔、旋风分离器成组更换施工方法的可行性,有效地缩短了施工工期.【期刊名称】《石油工程建设》【年(卷),期】2014(040)001【总页数】5页(P34-37,41)【关键词】催化裂化装置;大直径再生器;旋风分离器;更换;高精度安装;施工工艺【作者】周旭东;梁卓;彭振亚【作者单位】中国石油天然气第一建设公司,河南洛阳471000;中国石油天然气第一建设公司,河南洛阳471000;中国石油天然气第一建设公司,河南洛阳471000【正文语种】中文在炼油装置中催化裂化装置占有重要地位,其反应/再生系统中旋风分离器的分离效果不但直接影响到反应/再生系统的正常运转和催化剂的跑损,而且对分馏塔底油浆固体含量亦有很大影响。
因此保证旋风分离器的分离效果对企业节能减排、环境保护具有重要意义,对于性能不满足要求的旋风分离器要定期进行更换。
中国石油大连石化分公司 350 万 t / a 催化裂化装置,是我国迄今为止最早、最大的高低并列式催化裂化装置,其核心设备之一再生器的规格为D15600/9 300 × 43 550×36/34(单位为 mm),焊接后采用内燃法进行整体热处理。
这是 2003 年该催化裂化装置建成后运行至今的首次大修。
更换旋风分离器因其施工周期长、难度大,成为催化裂化装置检修工作的重点。
常规的再生器旋风分离器更换多采用侧壁开孔、单体更换的施工工艺。
本次旋风分离器更换作业对实际情况进行了充分分析,首次采用了旋风分离器工厂化深度预制,壳体顶部开孔,脚手架分段循环拆搭的施工方法,确保了整个工程的如期完工。
本次旋风分离器更换施工的主要内容有:封头开孔、16 组旋风分离器(分一、二级旋风分离器,共计 32 个)更换、料腿利旧恢复、拉杆更换、16 个翼阀更换、衬里拆除与恢复。
主要更换构件的参数见表1。
2.1 成组旋风分离器的检查大连石化公司与旋风分离器生产厂相距200 km左右,路况较好,车程只需 4 h,方便大型设备运输。
生产厂设施齐全,所有旋风分离器(以下简称分离器)均在厂内预组装,经过检查后将一、二级分离器组对焊接成型,由业主、监理、质检以及施工方到厂内验收,保证出厂的一、二级分离器的同心度以及其他几何尺寸满足安装精度要求。
运输前在分离器的筒体直段和灰斗部分分别做“十”字加固,并制作运输胎具,以保证运输过程中不发生变形。
制订每日到货计划,到货后直接进行安装,减少二次倒运造成的分离器变形,而且不占用现场施工用地。
2.2 脚手架的搭设分离器的更换作业要求有足够作业空间,并且保证作业安全。
首先要做好脚手架搭设工作。
传统的施工方法是以再生器过渡段内侧壁作为脚手架支撑点,搭设满堂红脚手架。
然而在本次分离器更换施工项目中,再生器过渡段内径为 9.3 m、高度为 25 m,若采用再生器过渡段侧壁作为支撑点,因脚手架跨距大、自重过大,无法搭设满堂红脚手架;若在大孔分布板上增加支撑点,在再生器中心位置搭设“井”字型支撑框架,施工量大,将影响整个施工的工期。
本次施工项目中采用下述方法搭设脚手架,既考虑到方便单体作业施工,又考虑到有利于整体施工工序的合理安排。
(1)分离器的更换,在分离器顶部采用分段循环拆搭法搭设脚手架。
在分离器更换前,先在其顶部搭设满圈脚手架,进行再生器顶部开孔;根据分离器的拆装循环拆搭其顶部脚手架;所有分离器更换后,最终通过其顶部满圈脚手架回装开孔板,进行衬里修补后拆除脚手架。
此方法在保证分离器更换施工的同时减少了大量的脚手架作业。
(2)分离器料腿切割分离与拉杆更换。
料腿及拉紧装置整体采用 16 组 10 t 倒链固定在再生器壁上,借助拉杆与料腿形成的环形整体结构,搭设环形悬空作业平台,待料腿与分离器切割分离后整体悬空于再生器内,保证上部和下部施工的作业空间,分离器更换后,料腿与拉杆局部交替安装(见图1)。
2.3 再生器顶封头的大直径开孔采用 ANSYS 软件对再生器顶封头的大直径开孔进行有限元分析,结果表明在大直径开孔区,高轴向压应力的分布范围较大,对稳定性和安全性有较大的影响。
因此采取在开孔区域加环向和径向加强筋的办法进行局部加强,可显著改善该区域的应力分布状况(见图2)。
再生器顶封头开孔直径为 8 m,在距孔边缘 100 mm处,焊接一个用 [ 20 槽钢形成的圆环,进行环向加固;再在此圆环两侧每间隔 1 m交错焊接径向加固立筋。
这样做提高了开孔刚度,还可减少以后修复开孔时的焊接变形。
2.4 再生器内 16 组分离器更换每组分离器由一级、二级分离器各一个组焊而成。
对16 组分离器的更换曾考虑了三种施工方案:方案一:再生器内部设卷扬机,所有分离器单体分解成灰斗和分离器两部分,从装卸孔进出进行更换施工。
优点:无需大型吊车配合,压力容器壳体不破坏。
缺点:分离器单体在再生器内部倒运繁琐、工期长,脚手架拆搭量大;分离器单体在再生器内部组对、焊接量大。
方案二:再生器侧壁开孔,供分离器单体更换施工用,单体更换后再在再生器内部进行两级分离器组对焊接。
优点:在再生器内部施工倒运距离适中、分离器成对焊接,焊接量适中。
缺点:内部施工倒运繁琐、工期长,脚手架施工拆搭量大。
方案三:再生器封头壳体大直径开孔,加大分离器到货预制深度,使分离器成对更换。
优点:垂直吊装使分离器在再生器内部倒运距离短,分离器成对安装焊接量小。
缺点:大直径开孔风险大,分离器成对组对精度要求高。
针对分离器更换施工量大、工期紧的特点,决定采用方案三。
相比较而言该方案最经济、最节省时间,也是最有效的施工方案;而对其存在的风险也必须采取有效措施加以防范。
3.1 施工前衬里清除在施工前为保证施工质量和满足施工需要,需将再生器内部封头及筒体内的部分衬里拆除,待内部施工结束后对衬里进行恢复。
衬里清除量见表2。
3.2 “天窗”的开孔及吊装对再生器原有焊缝进行测量,再生器封头的开孔与恢复必须满足 GB 150-2011 规定;同时应满足吊装要求,最终确定再生器开孔的直径。
本次施工确定再生器顶封头开孔直径为 8 m,切割下来的封头板称为“天窗”(见图3),其内部切割焊道处衬里清除完成后,在顶部焊接 4 个 10 t 级吊耳以及一个翻转吊耳。
“天窗”质量为 24 t,采用 400 t 履带吊和 150 t履带吊配合把它翻转后放到地面上,将衬里接口处做成燕尾槽型。
再生器内构件更换完毕后,再将“天窗”进行恢复焊接,根据焊接工艺要求进行焊前预热、焊后热处理。
3.3 旋风分离器更换依托再生器内的分离器搭设环形施工作业平台,悬挑至距离再生器中心轴4 m 处。
将 16 组分离器立筋开设 8个吊耳孔(编号:1 ~ 8,见图4),封头顶对应垂直设置4 个吊耳,悬挂 4 个 10 t 倒链(编号:③、④、⑦、⑧)锁死。
同时在分离器与料腿结合部依托拉紧装置搭设环形作业平台。
分离器料腿及拉紧装置用 16 个10 t 倒链锁死后,对料腿和拉紧装置进行气刨分离,分离后将料腿及拉紧装置整体下降 800 mm,悬空于再生器中部。
准备工作完毕后,将第一组分离器的一级分离器与吊座分离;二级分离器与集气室分离,用倒链将第一组分离器降 500 mm。
400 t 吊车小钩勾住二级分离器外侧吊耳孔(编号:1、2)起吊,吊装平稳后将倒链(对应编号:③、④)松开夺吊至一级分离器外侧吊耳孔(编号:5、6);平稳吊装后将一级分离器内侧倒链(对应编号:⑦、⑧)缓缓松开;此时二级分离器已夺吊出洞口,400 t 吊车大钩将一、二级分离连接风箱锁住(见图5),平稳吊装后将 400 t 吊车小钩吊耳孔(编号:1、2)松开,小钩收起;再次平稳吊装后将倒链(对应编号:③、④)松开。
400 t吊车大钩垂直吊装分离器风箱,旋转扒杆至开孔中心,将成组分离器通过封头开孔吊装至地面。
按照上述步骤依次拆除 4 组旧分离器后,留出足够的安装空间,安装第一组新分离器。
通过上述拆除分离器步骤的逆操作,将新分离器倒运至安装位置,立即在其上搭设施工作业平台,调整分离器安装角度和高度,达到安装标高后,将平台连接成整体。
调整一级分离器的吊杆高度的同时对二级分离器与升气管进行组对,分别测量一、二级分离器至再生器中心(挂有线坠)间的距离,当达到图纸要求尺寸后再次对分离器的垂直度进行校验,确认合格后即采用 [14 槽钢制作支架,与调整好的分离器构成三角形支撑,将分离器固定于再生器器壁上。
将再生器的一级分离器调整吊杆与吊座固定,拧紧吊杆下端M 110×4 螺母,吊杆上端螺母拧紧后再松回半扣,用第二个螺母锁紧。
待一、二级分离器都固定好后再进行二级分离器的焊接作业,采取双人对称焊。
首先对焊缝进行多段固定焊,然后再采用交错断续焊(每段焊缝不小于 50 mm,焊缝间距不大于 50mm),最后才可进行封闭打底焊接。
待第一组分离器固定好后,按照上述施工方法循环拆、搭作业平台,拆一组旧分离器后安装一组新分离器,交替更换新旧分离器,直至完成 4 组新分离器的安装。
3.4 料腿和拉杆的安装本再生器的分离器料腿均为不规则形状,无法按传统的方法进行安装施工。
经观察发现所有分离器料腿下端形成的一个圆周,与分离器所形成的圆周及再生器壳体圆周理论上为同心。
所以,料腿安装时应调整好料腿的垂直度,以料腿上垂直段截面中心为轴心对料腿进行旋转,并同时测量料腿下端至再生器中心的距离,当达到图纸要求的距离值后立即把料腿限位固定至再生器器壁上并进行焊接。
当所有料腿均按上述方法安装并安装完所有拉杆后,才可拆除分离器料腿的临时加固。
料腿和拉杆安装中的注意事项:(1)安装料腿的每层拉杆时,拉杆中心轴应在同一水平面上,注意调整好拉杆的水平度,偏差不得大于2 mm/m。
(2)拉杆应与相应的连接板焊牢,焊接时不得强力组装,保证设计规定的位置及相互间距离。
(3)料腿下段安装时,必须检查底口标高,以保证防倒锥和翼阀的顺利安装。
3.5 旋风分离器翼阀的安装分离器安装前应由制造厂家做翼阀冷态试验,提供安装角度。
翼阀现场安装时允许角度偏差为0°~+ 0.5°,用旋转角度尺测量。
翼阀与分离器的安装焊接必须采用防变形措施,即焊前沿圆周设置 4 块加固板,采用小电流焊接工艺,且每焊完一层要详细测量变形情况,通过改变焊接顺序来纠正或防止变形,确保翼阀角度。