反应再生器安全技术
SH 3504-2000催化裂化装置反应再生系统设备施工及验收规范

2 壳体直径允许偏差为 mm,同一断面上最大直径与最小直径之差不得大于设计 0
直径的 0.5%。筒体直段的长度允许偏差为±3mm; 3 锥体表面用 300mm 钢板尺沿母线检查,其局部凸凹值不得大于 lmm。锥体下端插
入灰斗内的长度允许偏差+50 mm; 4 螺旋顶板表面应平整,螺旋线应圆滑过渡; 5 焊缝按设计要求检验完毕,内部焊缝加强高度均应打磨平滑,其局部凸凹值不
UDC
中 华 人 民 共 和 国 行业 标 准
P
SH 3504-2000
催化裂化装置反应再生系统设备
施工及验收规范
Specification for construction and acceptance of Reactor-regenerator system equipment of catalytic crakdng unit
4
b 一、二级旋风分离器接口处断面中心线应与筒体直段轴线平行,其平行度偏差不 应大子 2mm。
9 旋风分离器总长允许偏差为 ± 8 mm,同一装置中同一级任意两个旋风分离器总长 之差不得超过 6mm;
10 已衬里后供货的旋风分离器尚应检查衬里的质量,衬里质量应符合《隔热耐磨 混凝土衬里技术规范》SH3531 的有关要求。 3.2.2 翼阀制造质量应符合设计图样要求,若设计无要求,则应符合下列规定:
主编单位: 中国石化集团第四建设公司 主编部门: 中 国 石 油 化 工 集 团 公 司 批准部门: 国 家 石 油 和 化 学 工 业 局
2000—10—26 发布
2001—03—01 实施
国家石油和化学工业局 发 布
关于批准《石油化工厂区绿化设计规范》
等 27 项石油化工行业标准的通知
什么是化工本质安全?本质安全详解
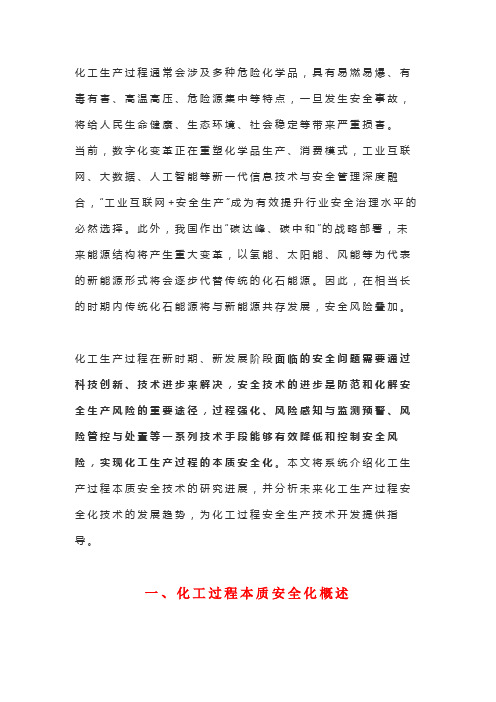
化工生产过程通常会涉及多种危险化学品,具有易燃易爆、有毒有害、高温高压、危险源集中等特点,一旦发生安全事故,将给人民生命健康、生态环境、社会稳定等带来严重损害。
当前,数字化变革正在重塑化学品生产、消费模式,工业互联网、大数据、人工智能等新一代信息技术与安全管理深度融合,“工业互联网+安全生产”成为有效提升行业安全治理水平的必然选择。
此外,我国作出“碳达峰、碳中和”的战略部署,未来能源结构将产生重大变革,以氢能、太阳能、风能等为代表的新能源形式将会逐步代替传统的化石能源。
因此,在相当长的时期内传统化石能源将与新能源共存发展,安全风险叠加。
化工生产过程在新时期、新发展阶段面临的安全问题需要通过科技创新、技术进步来解决,安全技术的进步是防范和化解安全生产风险的重要途径,过程强化、风险感知与监测预警、风险管控与处置等一系列技术手段能够有效降低和控制安全风险,实现化工生产过程的本质安全化。
本文将系统介绍化工生产过程本质安全技术的研究进展,并分析未来化工生产过程安全化技术的发展趋势,为化工过程安全生产技术开发提供指导。
一、化工过程本质安全化概述本质安全(i n h e r en t sa f e t y)概念最早由英国的T re vo r K l e tz 于1976年提出,其理念是从工艺源头上永久地消除风险,而不是单独靠控制系统、报警系统、联锁系统的使用来减小事故发生概率和减轻事故后果的严重性。
本质安全是绝对安全的理想状态,生产运行上很难达到,实际中需要通过本质安全化(i n h e r e n t l y s af e r)的一系列技术措施降低过程风险,使化工过程本质上更安全。
化工过程全生命周期的本质安全如图1所示,最小化、替代、缓和、简化这4个本质安全化策略适用于研发、设计、建设、操作、变更和维护等化工过程的整个生命周期。
工艺过程的本质安全化与被动型、主动型和程序型安全防护措施一起构成了化工过程的保护层,其中本质安全化工艺技术在所有保护层中处于最核心的部分,对安全风险控制起到决定性作用。
反应器、再生器检修施工方案
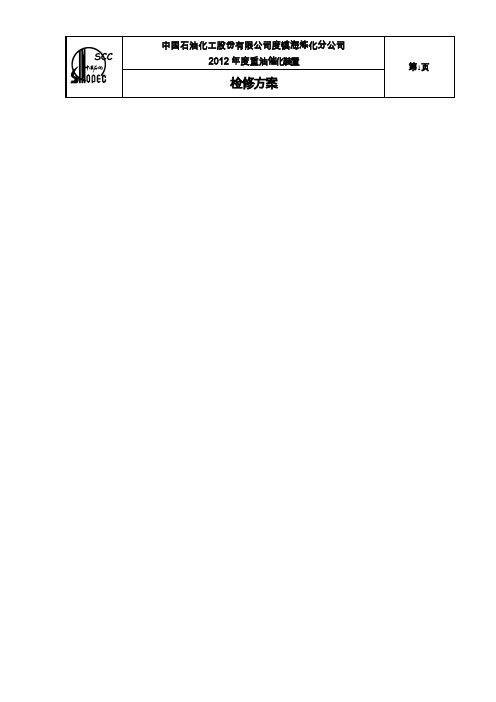
检修方案检修方案1.0工程概况1.1工程简介中国石化镇海炼化分公司炼油四部催化车间反应区的沉降器(T-201)、第二再生器(T-203)、外取热器(T-204)及其附属的项目检修是镇海炼化2012年度催化车间检修的关键项目。
本方案将重点阐述检修过程中的生产组织、施工程序、计划安排、质量控制、现场管理、安全措施以及施工机具和手段用料等内容。
1.2 工程特点本次检修施工时间紧,安装、吊装难度大,沉降器器、再生器、外取热器同时检修,由于施工作业空间狭小,给安装、吊装制造了极大的难度,施工时,大型吊车交叉作业多,各工种、工序、空间交叉施工较多,施工难度非常大。
为确保施工工期,前期预制工作要求在装置停气前进入施工现场并提前预制完毕。
1.3具体检修内容(根据镇海炼化炼油四部提供的资料)1.3.1沉降器(T-201)检修具体工作量1.3.2第二再生器(T-203)检修具体工作量序号名称材质规格(毫米)重量(吨)标高(米)备注序号名称材质规格(毫米)重量(吨)标高(米)备注1 开、封人孔和装卸孔2 ∮1100大油气线盲板装2次,拆1次3 ∮1100大油气线盲板法兰加碟璜.4 反再系统各人孔软梯安放固定5 DN1200提升管封头拆开6 提升管沉降器人孔、装卸孔档圈修理7 沉降器翼阀检查、更换8 汽提档板通气孔疏通9 提升管原料油进料喷嘴更换10 油桨进料喷嘴检查11 提升管中心环管,喷嘴加工更换12 DN1200提升管封头及法兰恢复13 底封头法兰拆开4对。
14 底部短节拆装(DN150)检修方案1 开、封人孔2 炉前瓦斯过滤短节拆装1只,DN803 F202火盆1只拆开,DN700,PN2.04 火盆连接软管拆除,DN80,DN40,DN15各1只5 配合火盆调试,油枪疏通,阀门拆装6 二再主风分布板检查,修补7 烧焦罐筒体钢板部分更换。
8 脱气罐锥体,再生立管部分更换。
9 大孔分布检查,耐磨喷嘴更换。
10 二再旋分检查3只,翼阀更换2只。
UOP连续重整第三代再生技术的应用
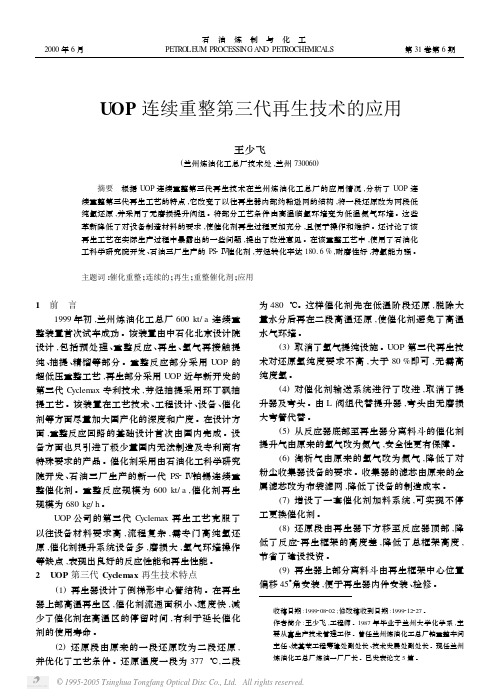
UOP连续重整第三代再生技术的应用王少飞(兰州炼油化工总厂技术处,兰州730060) 摘要 根据UOP连续重整第三代再生技术在兰州炼油化工总厂的应用情况,分析了UOP连续重整第三代再生工艺的特点,它改变了以往再生器内部约翰逊网的结构,将一段还原改为两段低纯氢还原,并采用了无磨损提升阀组。
将部分工艺条件由高温临氢环境变为低温氮气环境。
这些革新降低了对设备制造材料的要求,使催化剂再生过程更加充分,且便于操作和维护。
还讨论了该再生工艺在实际生产过程中暴露出的一些问题,提出了改进意见。
在该重整工艺中,使用了石油化工科学研究院开发、石油三厂生产的PS2Ⅳ催化剂,芳烃转化率达180.6%,耐磨性好,持氯能力强。
主题词:催化重整;连续的;再生;重整催化剂;应用1 前 言1999年初,兰州炼油化工总厂600kt/a连续重整装置首次试车成功。
该装置由中石化北京设计院设计,包括预处理、重整反应、再生、氢气再接触提纯、抽提、精馏等部分。
重整反应部分采用UOP的超低压重整工艺,再生部分采用UOP近年新开发的第三代Cyclemax专利技术,芳烃抽提采用环丁砜抽提工艺。
该装置在工艺技术、工程设计、设备、催化剂等方面尽量加大国产化的深度和广度。
在设计方面,重整反应回路的基础设计首次由国内完成。
设备方面也只引进了极少量国内无法制造及专利商有特殊要求的产品。
催化剂采用由石油化工科学研究院开发、石油三厂生产的新一代PS2Ⅳ铂锡连续重整催化剂。
重整反应规模为600kt/a,催化剂再生规模为680kg/h。
UOP公司的第三代Cyclemax再生工艺克服了以往设备材料要求高,流程复杂,需专门高纯氢还原,催化剂提升系统设备多,磨损大,氢气环境操作等缺点,表现出良好的反应性能和再生性能。
2 U OP第三代Cyclem ax再生技术特点(1)再生器设计了倒梯形中心管结构。
在再生器上部高温再生区,催化剂流通面积小、速度快,减少了催化剂在高温区的停留时间,有利于延长催化剂的使用寿命。
大型催化裂化装置再生器旋风分离器更换施工技术

大型催化裂化装置再生器旋风分离器更换施工技术周旭东;梁卓;彭振亚【摘要】在炼油装置中催化裂化装置占有重要地位,其反应/再生系统中旋风分离器的分离效果直接影响到反应/再生系统的正常运转,对于性能不满足要求的旋风分离器要及时进行更换.文章以中国石油大连石化公司350万t/a催化裂化装置检修为例,介绍了大直径再生器旋风分离器的更换作业,详细阐述了旋风分离器高精度安装的施工难点及施工工艺.施工实践验证了再生器顶部大直径开孔、旋风分离器成组更换施工方法的可行性,有效地缩短了施工工期.【期刊名称】《石油工程建设》【年(卷),期】2014(040)001【总页数】5页(P34-37,41)【关键词】催化裂化装置;大直径再生器;旋风分离器;更换;高精度安装;施工工艺【作者】周旭东;梁卓;彭振亚【作者单位】中国石油天然气第一建设公司,河南洛阳471000;中国石油天然气第一建设公司,河南洛阳471000;中国石油天然气第一建设公司,河南洛阳471000【正文语种】中文在炼油装置中催化裂化装置占有重要地位,其反应/再生系统中旋风分离器的分离效果不但直接影响到反应/再生系统的正常运转和催化剂的跑损,而且对分馏塔底油浆固体含量亦有很大影响。
因此保证旋风分离器的分离效果对企业节能减排、环境保护具有重要意义,对于性能不满足要求的旋风分离器要定期进行更换。
中国石油大连石化分公司 350 万 t / a 催化裂化装置,是我国迄今为止最早、最大的高低并列式催化裂化装置,其核心设备之一再生器的规格为D15600/9 300 × 43 550×36/34(单位为 mm),焊接后采用内燃法进行整体热处理。
这是 2003 年该催化裂化装置建成后运行至今的首次大修。
更换旋风分离器因其施工周期长、难度大,成为催化裂化装置检修工作的重点。
常规的再生器旋风分离器更换多采用侧壁开孔、单体更换的施工工艺。
本次旋风分离器更换作业对实际情况进行了充分分析,首次采用了旋风分离器工厂化深度预制,壳体顶部开孔,脚手架分段循环拆搭的施工方法,确保了整个工程的如期完工。
化工企业工艺管理制度
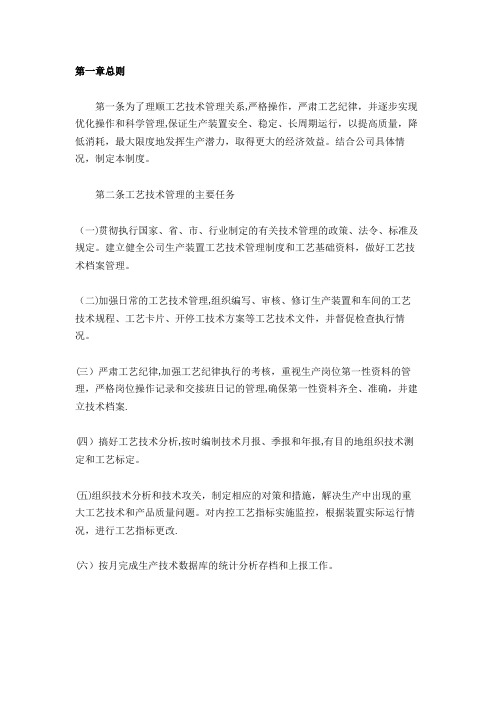
第一章总则第一条为了理顺工艺技术管理关系,严格操作,严肃工艺纪律,并逐步实现优化操作和科学管理,保证生产装置安全、稳定、长周期运行,以提高质量,降低消耗,最大限度地发挥生产潜力,取得更大的经济效益。
结合公司具体情况,制定本制度。
第二条工艺技术管理的主要任务(一)贯彻执行国家、省、市、行业制定的有关技术管理的政策、法令、标准及规定。
建立健全公司生产装置工艺技术管理制度和工艺基础资料,做好工艺技术档案管理。
(二)加强日常的工艺技术管理,组织编写、审核、修订生产装置和车间的工艺技术规程、工艺卡片、开停工技术方案等工艺技术文件,并督促检查执行情况。
(三)严肃工艺纪律,加强工艺纪律执行的考核,重视生产岗位第一性资料的管理,严格岗位操作记录和交接班日记的管理,确保第一性资料齐全、准确,并建立技术档案.(四)搞好工艺技术分析,按时编制技术月报、季报和年报,有目的地组织技术测定和工艺标定。
(五)组织技术分析和技术攻关,制定相应的对策和措施,解决生产中出现的重大工艺技术和产品质量问题。
对内控工艺指标实施监控,根据装置实际运行情况,进行工艺指标更改.(六)按月完成生产技术数据库的统计分析存档和上报工作。
(七)开展合理化建议活动和“三剂”(催化剂、添加剂、助剂等)的日常管理工作,制定生产装置化工“三剂”消耗定额,审查化工“三剂”年度和月度消耗计划,组织新型“三剂”应用技术方案审查、实施和效果验收工作。
(八)参加技措项目的方案讨论,参加设计审查,组织并参加技术考核和标定总结。
(九)收集和对比国内外技术发展的情报资料,开展公司内外的技术交流工作,结合公司实际,推广应用先进的工艺技术和新型“三剂"。
(十)认真学习和研究国内外先进的工艺技术管理经验,逐步应用现代化管理手段和方法,充分发挥信息资源共享的作用,提高工艺技术管理水平。
第三条工艺技术管理体制(一)工艺技术管理实行统一领导,分级管理.即公司、车间二级管理。
以公司一级为主,基点放在车间。
典型化工单元操作过程的安全技术—加热操作的安全技术
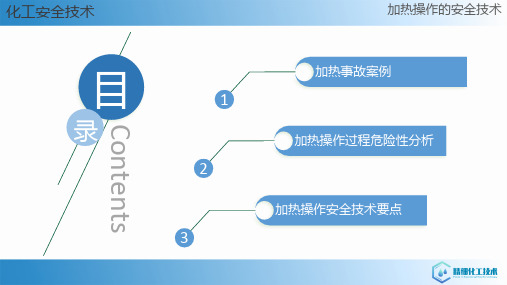
化工安全技术
加热操作安全技术
事故原因:在再生器系统清洗、置换不彻底的情况下,用蒸汽对再生器下部的加 热器进行试漏(等于用加热器加热),使残留和附着在器壁等部件上的铜氨液(或沉积 物)解析或分解,析出的一氧化碳、氨气等可燃气与再生器内空气形成混合物达到爆 炸极限范围,遇再生器内试漏作业产生的机械火花(不排除内衣摩擦静电火花)引起 爆炸。
15:40,用空气试漏,合成车间主任熊某等二人戴面具再次从再生器人孔进入检 查。17:20,在未对再生器内采样分析的情况下,车间主任李某决定用0.12MPa蒸 汽第三次试漏,并四人一起进入,李某用哨声对外联系关停蒸汽,工艺主任王某在 人孔处进行监护。17:40再生器内混合气发生爆炸。除一人负重伤从器内爬出外, 其余三人均死在器内,人孔处王某被爆炸气浪冲击到氨洗塔平台死亡。生产副厂长 赵某、安全员蔡某和机械员魏某均被烧伤。
化工安全技术
加热操作安全技术
二、加热操作过程危险性分析
➢生产中常用的加热方式:直接火加热(包括烟道气加热)、蒸汽或热水加热、有机载体 (或无机载体)加热以及电加热等。
热水: 100℃以下 水蒸气:100-140℃ 加热炉或热载体: 140℃以上 电加热: 250℃以上 ➢提供热源的设备主要为:蒸汽锅炉、导热油炉、热风炉等,均属于特种设备。
化工安全技术
加热操作的安全技术
目
录
Contents
1 2 3
加热事故案例 加热操作过程危险性分析 加热操作安全技术要点
化工安全技术
加热操作安全技术
一、加热事故案例
1995年1月,陕西省某化肥厂铜洗工段回流塔在检修过程中发生再生器爆炸事故, 造成4人死亡,多人受伤。
该化肥厂铜氨液再生由回流塔、再生器和还原器组成。1月13日早7时,再生系统 清洗置换后打开再生器人孔和顶部排气孔。14:00采样分析,14:30用蒸汽对再生器下 部的加热器试漏,技术员徐某和陶某戴面具进入再生器检查。因温度高,所以用消防 车向再生器充水降温。
催化裂化装置操作安全技术(2篇)

催化裂化装置操作安全技术催化裂化是蜡油和渣油在高温和催化剂作用下,在提升管式反应器中进行快速反应,把较大分子的烃类裂化为较小分子烃类,再经分馏、吸收等工序生产汽油、柴油、液态烃干汽等产品的炼油生产装置。
催化裂化反应类型主要有裂化反应、异构化反应、氢转移反应和芳构化反应四种。
反应再生和分馏是催化裂化装置的核心。
装置除具有易燃、易爆、易中毒特点外,油浆易结焦堵塞设备管线,也是比较突出的安全问题。
(一)反应再生单元安全特性在反应再生过程中,原料油与再生后的高温催化剂在反应器提升管的下部进入并呈沸腾流化状态(催化剂为固体)接触反应,反应后的催化剂和油气经上部的反应沉降器进行气固分离,反应油气去分馏。
催化剂由斜管回到烧焦罐烧焦。
在烧焦罐中,反应后催化剂自待生斜管进入烧焦罐底部,在压缩空气推动下呈沸腾流化状态进行烧焦,并由主风带入上部再生器进一步烧焦。
再生后的高温催化剂由再生斜管进入提升管式反应器底部流化反应。
在这个反应再生过程中,同时存在着易燃物(反应油气)、助燃物(压缩空气)和烧焦明火三个要素。
所以在实际操作中必须严格控制汽提段流量和二段流量。
另外,如果沉降器顶压过高,不仅会迫使系统停车,甚至可能会使催化剂倒流引发重大事故。
(二)反应再生过程操作异常现象(1)提升管温度大幅度波动,会烧坏设备。
引起温度大幅度波动的原因主要有:流量波动大或原料带水;烧焦罐温度大幅度波动;原料预热温度大幅度波动;两器差压波动;催化剂量波动;再生滑阀控制失灵。
对温度波动要查明原因,有针对性地采取措施。
如对原料进行脱水,稳定进料量和原料预热温度,稳定烧焦温度,调节两器差压。
如仪表失灵改用手动等。
(2)沉降器压力大幅波动。
如果沉降器出现压力大幅度波动,首先要准确判断异常原因,采取对应的处理措施。
如果是原料带水,要立即进行脱水。
进料量波动大时要稳定进料量。
其它原因如汽提蒸汽量及压力波动大,催化剂循环波动量大,以及分馏塔釜液位过高等,都要及时采取对应的调节控制措施。
反应再生器安全技术(三篇)

反应再生器安全技术反应再生器是一种用于化工、石油、制药等工业生产中的重要设备,其作用是通过高温、高压的条件下,使废物或副产品得到再生和利用。
由于其操作环境的特殊性,反应再生器的安全技术至关重要。
本文将从设计、材料、设备保护、操作控制和紧急处置等方面,详细介绍反应再生器的安全技术。
首先,在设计方面,反应再生器的结构和尺寸应该满足所需的反应能力和操作要求。
设计应考虑废物或副产物的物性、热传导特性以及温度、压力和反应物种类等因素,以确保设备的强度和稳定性。
此外,设计中还应考虑到可能发生的事故和紧急情况,如泄漏、爆炸和火灾等,采取相应的安全措施,如增设安全阀和爆炸隔离器等。
其次,在材料选择方面,反应再生器的材料应具有良好的耐高温、耐腐蚀性能。
常用的材料包括不锈钢、钛合金和镍基合金等。
此外,材料的厚度和焊缝的质量也是直接影响设备安全性的重要因素,应进行充分的材料检测和焊接检验,确保设备的完整性和密封性。
再次,在设备保护方面,反应再生器应配备安全阀、爆破片、爆炸隔离器等安全装置,以及液位、压力、温度和流量等监测仪表。
安全阀和爆破片可以在设备压力超过安全值时释放压力,防止设备破裂和爆炸。
爆炸隔离器则可以隔离反应再生器和其他设备,防止火灾和爆炸的扩散。
监测仪表可以实时监测设备的工作状态,及时发现异常情况并采取相应的措施。
此外,操作控制也是反应再生器安全的重要环节。
操作人员应具备相关的专业知识和技能,熟悉设备的操作规程和安全操作规范。
在操作过程中,需要遵循严格的工艺和操作要求,确保设备的运行稳定和产品质量合格。
同时,应制定紧急故障处理和事故应急预案,并进行定期的演练,提高操作人员的应急能力和处置能力。
最后,在紧急处置方面,反应再生器发生事故时,应及时采取相应的紧急处置措施,以最大程度地减少事故的损失和危害。
紧急处置包括防止火灾蔓延、停止反应和清理危险物质等。
同时,应立即启动事故应急预案,组织人员进行救援和灭火,确保人员安全和设备完整。
常用化工设备标准规范

常用化工设备标准第一部分:1 《压力容器安全技术监察规程》2 《压力管道安全管理与监察规定》3 钢制压力容器(GB150-1998)4 钢制管壳式换热器(GB151-1999)5 钢制化工容器设计基础规定(HG20580-1998)6 钢制化工容器材料选用规定(HG20581-1998)7 钢制化工容器强度计算规定(HG20582-1998)8 钢制化工容器结构设计规定(HG20583-1998)9 钢制化工容器制造技术要求(HG20584-1998)10 钢制低温压力容器技术规定(HG20585-1998)11 塔器设计技术规定(HG20652-1998)12 钢制压力容器焊接工艺评定(JB4708-2000)13 钢制压力容器焊接规程(JBT4709-2000)14 钢制塔式容器(JB/T4710-2005)15压力容器涂敷与运输包装(JB4711-2003)16 压力容器无损检测(JB4730-2005)17 钢制卧式容器(JB/T4731-2005)18 钢制焊接常压容器(JBT4735-1997)第二部分1 机械搅拌设备(HG/T20569-94)2 塔盘制造安装技术条件(JB/T1025-2001)3 钢制管法兰及垫片选用规定(HG20593-98)4 不锈钢-硫酸铜腐蚀试验方法()第三部分1 化工管道设计规范(HG20695-1986)2 化工装置管道布置设计规定(HG/T20549-1998)3 化工设备、管道外防腐设计规定(HG/T20679-1990)4 管架标准图(HG/T21629-1999)5 石油化工企业设备和管道隔热设计规范(SH3010-2000)6 化工装置设备布置设计规定(HG20546-92)7 石油化工管道布置设计通则(SH3012-2000)8 石油化工企业蒸汽伴管及夹套管设计规范(SHJ40-91)9 石油化工企业管架设计规范(SH3055-93)10 管道常用数据表(TC42A1-93)HG 20580-1998 钢制化工容器设计HG 20581-1998 钢制化工容器材料选用规定HG 20582-1998 钢制化工容器强度计算规定HG 20583-1998 钢制化工容器结构设计规定HG 20584-1998 钢制化工容器制造技术要求HG 20585-1998 钢制低温压力容器技术规定HG 20592-1997 钢制管法兰型式,参数( 欧洲体系)HG 20593-1997 板式平焊钢制管法兰( 欧洲体系)HG 20594-1997 带颈平焊钢制管法兰( 欧洲体系)HG 20595-1997 带颈对焊钢制管法兰( 欧洲体系)HG 20596-1997 整体钢制管法兰( 欧洲体系)HG 20597-1997 承插焊钢制管法兰( 欧洲体系)HG 20598-1997 螺纹钢制管法兰( 欧洲体系)HG 20599-1997 对焊环松套钢制管法兰( 欧洲体系)HG 20600-1997 平焊环松套钢制管法兰( 欧洲体系)HG 20601-1997 钢制管法兰盖( 欧洲体系)HG 20602-1997 不锈钢衬里法兰盖HG 20603-1997 钢制管法兰技术条件( 欧洲体系)HG 20604-1997 钢制管法兰压力- 温度等级HG 20605-1997 钢制管法兰焊接接头和坡口尺寸( 欧洲体系)HG 20607-1997 钢制管法兰用聚四氟乙烯包HG 20608-1997 钢制管法兰用柔性石墨复合垫片( 欧洲体系) HG 20609-1997 钢制管法兰用金属包覆垫片( 欧洲体系)HG 20610-1997 钢制管法兰用缠绕式垫片( 欧洲体系)HG 20611-1997 钢制管法兰用齿形组合垫( 欧洲体系)HG 20612-1997 钢制管法兰用金属环垫( 欧洲体系)HG 20613-1997 钢制管法兰用紧固件HG 20614-1997 钢制管法兰,垫片,紧固件选配规定( 欧洲体系)HG 20615-1997 钢制管法兰型式,参数( 美洲体系)HG 20616-1997 带颈平焊钢制管法兰HG 20617-1997 带颈对焊钢制管法兰( 美洲体系)HG 20618-1997 整体钢制管法兰( 美洲体系)HG 20619-1997 承插焊钢制管法兰( 美洲体系)HG 20620-1997 螺纹钢制管法兰( 美洲体系)HG 20621-1997 对焊环松套钢制管法兰( 美洲体系)HG 20622-1997 钢制管法兰盖( 美洲体系)HG 20623-1997 大直径钢制管法兰( 美洲体系)HG 20624-1997 钢制管法兰技术条件( 美洲体系)HG 20625-1997 钢制管法兰压力- 温度等级( 美洲体系)HG 20626-1997 钢制管法兰焊接接头和坡口尺寸( 美洲体系)HG 20627-1997 钢制管法兰用非金属平垫片( 美洲体系)HG 20628-1997 钢制管法兰用聚四氟乙烯包覆垫片( 美洲体系)HG 20629-1997 钢制管法兰用柔性石墨复合垫片( 美洲体系)HG 20630-1997 钢制管法兰用金属包覆垫片( 美洲体系)HG 20631-1997 钢制管法兰用缠绕式垫片( 美洲体系)HG 20632-1997 钢制管法兰用齿形组合垫( 美洲体系)HG 20633-1997 钢制管法兰用金属环垫( 美洲体系)HG 20634-1997 钢制管法兰用紧固件( 美洲体系)HG 20635-1997 钢制管法兰,垫片,紧固件选配规定( 美洲体系)HG/T 20549-1998 化工装置管道布置设计规定HG/T 20552-1994 化工企业化学水处理设计计算规定(新增加)HG/T 20560-1997 化工机械化运输工艺设计施工图内容和深度规定(新增加)HG/T 20561-1994 化工工厂总图运输工图设计文件编制深度规定HG/T 20562-1994 化工企业自备铁路机车和车辆数量计算规定(新增加)HG/T 20563-1994 化工企业货运汽车数量计算规定(新增加)HG/T 20564-1994 化工企业运输、装卸人员数量计算规定(新增加)HG/T 20565-1994 化工企业厂内铁路装卸线、装卸货位、存车线计算规定(新增加)HG/T 20567-1994 热油炉技术条件(新增加)HG/T 20568-1994 化工固体物料堆场及仓库设计规定HG/T 20569-1994 机械搅拌设备HG/T 20572-1995 化工企业给排水设计施工图内容深度统一规定(暂缺)HG/T 20573-1995 分散型控制系统工程设计规定HG/T 20574-1995 化工企业总图运输设计工程测量技术规定(新增加)HG/T 20575-1995 化学工业炉阻力计算规定HG/T 20576-1998 粉粒体静壁面摩擦系数的测定(新增加)HG/T 20589-1996 化学工业炉受压元件强度计算规定(新增加)HG/T 20636-1998 自控专业设计管理规定HG/T 20637-1998 自控专业工程设计文件的编制规定HG/T 20638-1998 自控专业工程设计文件深度的规定HG/T 20639-1998 自控专业工程设计用典型图表及标准目录HG/T 20641-1998 石灰窑砌筑技术条件HG/T 20642-1998 化学工业炉耐火纤维炉衬设计技术规定HG/T 20643-1998 化工设备基础设计规定HG/T 20645-1998 化工装置管道机械设计规定HG/T 20647-1998 总体模型设计规定HG/T 20648-1998 设备布置模型设计规定HG/T 20649-1998 化工企业总图运输设计规范HG/T 20650-1998 化工企业汽车运输设计运营费计算规定(暂缺)HG/T 20651-1998 化工企业铁路运输设计运营费计算规定(暂缺)HG/T 20653-1998 化工企业化学水处理设计技术规定HG/T 20656-1998 化工采暖通风与空气调节详细设计内容和深度的规定HG/T 2081-2001 阳离子艳蓝2RL 500% (暂缺)HG/T 2098-2001 釜用机械密封系列及主要参数(暂缺)HG/T 2154-1991 工业硫氰酸铵(暂缺)HG/T 21549-1995 钢制低压湿式气柜系列(暂缺)HG/T 21551-1995 柱塞式放料阀(暂缺)HG/T 2155-1991 工业过硫酸钾(暂缺)HG/T 2156-1991 工业循环冷却水中阴离子表面活性剂的测定-亚甲蓝分光光度法(暂缺)HG/T 21562-1994 衬聚四氟乙烯钢管和管件HG/T 2157-1991 工业循环冷却水中铵的测定电位法HG/T 21574-1994 设备吊耳HG/T 21575-1994 带灯视镜HG/T 21576-1994 双切换旋塞阀(暂缺)HG/T 21577-1994 快速特种管接头HG/T 21579-1995 聚丙烯/玻璃钢(PP/FRP)复合管及管件(新增加)HG/T 2158-1991 工业循环冷水中铵的测定蒸溜和滴定法HG/T 21583-1995 快开不锈钢活动盖(暂缺)HG/T 21584-1995 磁性液位计HG/T 可拆型槽盘气液分布器(暂缺)HG/T 21586-1998 抽屉式丝网除沫器(暂缺)SH 3001-1992 石油化工设备抗震鉴定标准SH/T 3002-2000石油库节能设计导则SH/T 3003-2000石油化工合理利用能源设计导则SH 3004-1999 石油化工采暖通风与空气调节设计规范SH 3005-1999 石油化工自动化仪表选型设计规范SH 3006-1999 石油化工控制室和自动分析器室设计规范SH 3007-1999 石油化工储运系统罐区设计规范SH3008-2000 石油化工厂区绿化设计规范SH 3009-2001 石油化工企业燃料气系统和可燃性气体排放系统设计规范SH 3010-2000 石油化工设备和管道隔热技术规范SH 3011-2000 石油化工工艺装置布置设计通则SH 3012-2000 石油化工管道布置设计通则SH/T 3013-2000 石油化工厂区竖向布置设计规范SH/T 3014-2002石油化工企业储运系统泵房设计规范SH 3015-2003 石油化工企业给水排水系统设计规范(附条文说明) SH 3016-1990 石油化工企业循环水场设计规范SH 3017-1999 石油化工生产建筑设计规范SH/T 3018-2003石油化工安全仪表系统设计规范(附条文说明) SH/T 3019-2003 石油化工仪表管道线路设计规范SH 3020-2001 石油化工仪表供气设计规范SH 3021-2001石油化工仪表及管道隔离和吹洗设计规范SH 3022-99 石油化工设备和管道涂料防腐蚀技术规范SH/T 3023-2005 石油化工厂内道路设计规范SH 3024-1995 石油化工企业环境保护设计规范SH 3025-1990 合成纤维厂环境保护设计规范SH 3026-1990 常压立式储罐抗震鉴定标准SH/T 3027-2003 石油化工企业照度设计标准SH 3028-1990 石油化工企业生产装置电信设计规范SH 3029-1991 石油化工企业排气筒和火炬塔架设计规范SH 3030-1997 石油化工塔型设备基础设计规范SH 3031-1997 石油化工逆流式机械通风冷却塔结构设计规范SH/T 3032-2002 石油化工企业总体布置设计规范SH 3033-1991 石油化工企业汽车运输设施设计规范SH 3034-1999 石油化工给水排水管道设计规范SH 3035-1991 石油化工企业工艺装置管径选择导则SH/T 3036-2003 一般炼油装置用火焰加热炉SH/T 3037-2002 炼油厂加热炉炉管壁厚计算SH 3038-2000 石油化工企业生产装置电力设计技术规范SH/T 3039-2003 石油化工非埋地管道抗震设计通则(附条文说明) SH/T 3040-2002 石油化工管道伴管和夹套管设计规范SH/T 3041-2002 石油化工管道柔性设计规范SH 3042-1991 合成纤维厂采暖通风与空气调节设计规范SH 3043-2003 石油化工企业设备管道表面色和标志规定SH 3044-1992 石油化工精密仪器抗震鉴定标准SH/T 3044-2004 石油化工精密仪器抗震鉴定标准SH/T 3045-2003 石油化工管式炉热效率设计计算SH 3046-1992 石油化工立式圆筒形钢制焊接储罐设计规范SH 3047-1993 石油化工企业职业安全卫生设计规范SH 3048-1999 石油化工钢制设备抗震设计规范SH 3049-1993 石油化工企业建筑抗震设防等级分类标准SH 3050-1994 石油化工企业设备地震破坏等级划分标准SH/T 3051-2004 石油化工配管工程术语SH/T 3052-1993 石油化工配管工程设计图例SH/T 3052-2004 石油化工配管工程设计图例SH/T 3053-2002 石油化工企业厂区总平面布置设计规范SH 3054-1993 石油化工企业厂区管线综合设计规范SH 3055-1993 石油化工企业管架设计规范SH 3056-1994 石油化工企业排气筒(管)采样口设计规范SH 3057-1994 石油化工企业落地式离心泵基础设计规范SH 3058-1994 石油化工企业冷换设备和容器基础设计规范SH 3059-2001 石油化工管道设计器材选用通则SH 3060-1994 石油化工企业工厂电力系统设计规范SH 3061-1994 石油化工企业管式炉基础设计规范SH 3062-1994 石油化工企业球罐基础设计规范SH 3063-1999 石油化工企业可燃气体和有毒气体检测报警设计规范SH 3064-94 石油化工钢制通用阀门选用、检验及验收SH/T 3064-2003 石油化工钢制通用阀门选用、检验及验收SH 3065-1994 石油化工管式炉急弯弯管技术标准SH 3065-2005 石油化工管式炉急弯弯管技术标准SH 3066-95 石油化工企业反应器、再生器框架设计规范SH 3067-1995 石油化工企业钢筋混凝土冷换框架设计规范SH 3068-1995 石油化工企业钢储罐地基与基础设计规范SH 3069-1995 石油化工企业构筑物抗震设防分类标准SH/T 3070-2005 石油化工管式炉钢结构设计规范SH 3071-1995 石油化工企业电气设备抗震鉴定标准SH 3072-1995 石油化工企业电气图图形和文字符号SH 3073-1995 石油化工企业管道支吊架设计规范SH/T 3073-2004 石油化工企业管道支吊架设计规范SH 3074-1995 石油化工钢制压力容器SH 3075-1995 石油化工钢制压力容器材料选用标准SH 3076-1996 石油化工企业建筑物结构设计规范SH 3077-1996 石油化工企业钢结构冷换框架设计规范SH 3078-1996 立式圆筒形钢制和铝制料仓设计规范SH 3079-1997 石油化工企业焦炭塔框架设计规范SH 3080-1997 石油化工企业横流式机械通风冷却塔结构设计规范SH 3081-1997 石油化工仪表接地设计规范SH/T 3081-2003 石油化工仪表接地设计规范SH/T 3082-2003石油化工仪表供电设计规范SH/T 3083-1997 石油化工钢储罐地基处理技术规范SH 3084-97 石油化工总图运输设计图例SH 3085-1997 石油化工管式炉碳钢和铬钼钢炉管焊接技术条件SH 3086-1998 石油化工管式炉钢结构工程及部件安装技术条件SH 3087-1997 石油化工管式炉耐热钢铸件技术标准SH 3088-1998 石油化工塔盘设计规范SH 3089-1998 石油化工给水排水管道设计图例SH 3090-1998 石油化工铁路设计规范SH 3091-1998 石油化工压缩机基础设计规范SH/T 3092-1999 石油化工分散控制系统设计规范SH 3093-1999 石油化工企业卫生防护距离SH 3094-1999 石油化工排雨水明沟设计规范SH 3095-2000 石油化工污水处理设计规范SH/T 3096-2001 加工高硫原油重点装置主要设备设计选材导则SH 3097-2000 石油化工静电接地设计规范SH 3098-2000 石油化工塔器设计规范SH 3099-2000 石油化工给水排水水质标准SH3100-2000 石油化工工程测量规范SH/T 3101-2000炼油厂流程图图例SH/T 3102-2000石油化工采暖通风与空气调节设计图例SH/T 3103-2000T炼油厂中心化验室设计技术规定SH/T 3104-2000 石油化工仪表安装设计规范SH/T 3105-2000 炼油厂自动化仪表管线平面布置图图例及文字代号SH/T 3106-2000 炼油厂氮气系统设计技术规定SH/T 3107-2000 石油化工液体物料铁路装卸车设施设计规范SH/T 3108-2000 炼油厂全厂性工艺及热力管道设计规范SH/T 3109-2001 炼油厂添加剂设施设计规范SH 3110-2001 石油化工设计能量消耗计算方法SH 3111 没有查到此标准SH/T 3112-2000 石油化工管式炉炉胀接工程技术条件SH/T 3113-2000 石油化工管式炉燃烧器工程技术条件SH/T 3114-2000 石油化工管式炉耐热铸铁件工程技术条件SH/T 3115-2000 石油化工管式炉轻质浇注料衬里工程技术条件SH/T 3116-2000 炼油厂用电负荷设计计算方法SH/T 3117-2000 炼油厂设计热力工质消耗量计算方法SH/T 3118-2000 石油化工蒸汽喷射式抽空器设计规范SH/T 3119-2000 石油化工钢制套管换热器设计规范SH/T 3120-2000石油化工喷射式混合器设计规范SH/T 3121-2000 炼油装置工艺设计规范SH/T 3122-2000 炼油装置工艺管道流程设计规范SH/T 3123-2001 石油化工钢储罐地基充水预压监测规程SH/T 3124-2001 石油化工给水排水工艺流程设计图例SH 3125-2001 石油化工防火堤设计规范SH 3126-2001石油化工仪表及管道伴热和隔热设计规范SH/T 3127-2001 石油化工管式炉铬钼钢焊接回弯头技术标准SH/T 3128-2002 一般炼油装置火焰加热炉陶瓷纤维衬里SH/T 3129-2002 加工高硫原油重点装置主要管道设计选材导则SH/T 3130-2002 石油化工建筑抗震鉴定标准SH/T 3131-2002 石油化工电气设备抗震设计规范SH/T 3132-2002 石油化工钢筋混凝土水池结构设计规范SH/T 3133-2002石油化工企业现状图图式SH/T 3134-2002 采用橇装式加油装置的汽车加油站技术规范SH/T 3135-2003 石油化工工程地震破坏鉴定标准SH 3136-2003 液化烃球形储罐安全设计规范(附条文说明)SH 3137-2003石油化工钢结构防火保护技术规范SH/T 3138-2003 球形储罐整体补强凸缘HG -G30阻燃增强聚对苯二甲酸丁二醇酯(PBT)工程塑料HG 2010-1991橡胶球胆HG 2011-1991橡胶热水袋HG 2012-1991磨机橡胶衬里技术条件HG 2014-1991钢丝绳牵引难燃输送带HG 2014-2005 钢丝绳牵引阻燃输送带HG 2018-1991轻便胶鞋HG 20201-2000工程建设安装工程起重施工规范HG 20202-2000脱脂工程施工及验收规范HG 20202-2000脱脂工程施工及验收规范HG 20203-2000化工机器安装工程施工及验收通用规范HG 2022-1991工业循环冷却水中游离氯和总氯的测定 N,N--二乙基苯二胺滴定法HG 20225-95化工金属管道工程施工及验收规范HG 20225-95化学金属管道工程施工及验收规范HG 2023-1991工业循环冷却水中游离氯和总氯的测定 N,N--二乙基--1,4--苯二胺分光光度法HG 2023-1991工业循环冷却水中游离氯和总氯的测定分光光度法HG 20234-93; 化工建设项目进口设备、材料检验大纲HG 20235-93化工建设项目施工组识设计标准HG 20236-93《化工设备安装工程质量检验评定标准》HG 20236-93化工设备安装质量标准HG 20237-1994化学工业工程建设交工技术文件规定HG 20238-2003化工建设概算定额HG 20238-2003化工建设概算定额HG 2035-1991黄磷包装桶技术条件HG 2036-1991搪玻璃容器参数HG 2037-1991卧式胶浆搅拌机HG 2038-1991立式胶浆搅拌机HG 2039-1991平带鼓式硫化机HG 2040-1991手动液体燃料鹤管通用技术条件HG 2041-1991橡胶厚度计技术条件HG 20504-92化工废渣填埋场设计规定HG 20518-92化工机械化运输设计原则规定HG 设备地脚螺栓表HG 管道布置图HG 管段表及管道特性表HG 特殊管架图HG 管架表HG 特殊管件图HG 特殊阀门和管道附件表HG 管道常用缩写词HG 管道的标注HG 20519[1].22-1992隔热材料表HG 20519[1].23-1992防腐材料表HG 20519-92垫片代号HG 20519-92化工工艺设计施工图内容和深度统一规定HG 20520-1992玻璃钢PVC复合管道设计规定HG 20522-92 化工企业冷却塔设计规定HG 20523-1992 化工企业水处理加氯设施设计统一规定HG 20523-1992化工企业水处理加氯设施设计统一规定HG 20536-1993 聚四氟乙烯衬里设备HG 20537《奥氏体不锈钢焊接钢管选用规定》等系列标准HG 20538-1992_衬塑(PP、PE、PVC)钢管和管件HG 20539-1992 增强聚丙烯(FRPP)管和管件HG 修订大纲HG 20546-1992 化工装置设备布置设计内容和深度规定HG 20546一92化工装置设备布置设计规定HG 20551-93化工厂电力设计常用计算规定HG 20553-93化工配管用无缝及焊接钢管尺寸选用系列HG 20556-1993 化工厂控制室建筑设计规定HG 20557 工艺系统设计管理规定(全套)HG 20558-1993工艺系统设计文件内容的规定(全套)HG 管道仪表流程图隔热、保温、防火和隔声代号HG 管道仪表流程图设备位号HG 20559-93 管道仪表流程图物设计规定HG 20568-94化工固体物料堆场及仓库设计规定HG 20570[1].1-1995工艺系统工程设计技术规定设备和管道系统设计压力和设计温度的确定HG 20570[1].2-1995工艺系统工程设计技术规定安全阀的设置和选用HG 20570[1].3-1995工艺系统工程设计技术规定爆破片的设置和选用H.20570[1].6-95《管径选择》.H.20570[1].7-95《管道压力降计算》.HG 20581-1998 钢制化工容器材料选用规定HG 20581-1998钢制化工容器设计基础规定HG 20583-1998HG 20583-1998钢制化工容器结构设计规定HG 20592—_0635-97 法兰标准HG 20592~20635-97钢制管法兰、垫片、紧固件者[信息]HG 20592-0635-97 法兰标准HG 20593板式平焊钢制管法兰HG 20594带颈平焊钢制管法兰HG 20595带颈对焊钢制管法兰HG 20596整体钢制管法兰HG 20598螺纹钢制管法兰HG 20599对焊环松套钢制管法兰HG 20602不锈钢衬里法兰盖HG 20604钢制管法兰压力—温度等级HG 20605钢制管法兰焊接接头和坡口尺寸HG 20606-1997 钢制管法兰用非金属平垫片(欧洲体系)HG 20606钢管管法兰用非金属平垫片HG 20615-97钢制管法兰型式, 参数(美洲体系)HG 20634-1997钢制管法兰用紧固件(美洲体系)HG 20640-1997 塑料设备HG 20652-98塔器设计技术规定HG 20652塔器设计技术规定HG 20660-2000 压力容器中化学介质毒性危害和爆炸危险程度分类HG 20660-2000压力容器中化学介质毒性危害和爆炸危险程度分类HG 20663-1999化工粉粒产品计量、包装及码垛系统设计规定HG 20679-1990 化工设备、管道外防腐设计规定HG 20679-1990化工设备管道外防腐设计规定HG 20690-2000 化工企业循环冷却水处理设计技术规定HG 20698-2000化工采暖通风与空气调节设计规定HG 2074-1991保险粉(连二亚硫酸钠)HG 2086-1991S101型硫酸生产用钒催化剂HG 2087-1991 S101--2H型硫酸生产用钒催化剂HG 2088-1991 S107,S108型硫酸生产用钒催化剂HG 2090-1991B113型--氧化碳中温变换催化剂HG 2094-91 橡胶配合剂简称HG 2100-1991液环式氯气泵用机械密封HG 2101-1991单级悬臂双作用液环式氯气泵试验及参数测量方法HG 2101-1991单级悬臂双作用液环式氯气泵试验及参数测量方法HG 2102-1991外滤面转鼓真空滤碱机HG 2103-1991衬胶铁道罐车技术条件HG 2116-1991常规型国际橡胶硬度计高硬度HG 2117-1991常规型国际橡胶硬度计中硬度HG 2118-1991常规型国际橡胶硬度计低硬度HG 21501-1993 衬胶钢管和管件HG 21503-92 钢制固定式薄管板列管式换热器HG 21505-1992组合式视镜HG 21506-1992补强圈HG 21506-92 补强圈HG 21514-HG 21535-2005钢制人孔和手孔,共22个标准HG 21515-95 常压人孔HG 21537 化工填料箱标准HG 21542-92_单轨、悬挂吊车梁通用图HG 21542-92单轨、悬挂吊车梁通用图HG 21544-92预埋件通用图HG 21574-94(T)_设备吊耳PDFHG 21581-95自控安装图册HK01HG 21581-95自控安装图册HK02HG ~2 -95视镜式玻璃板液面计HG 21595-1999HG 21596-1999HG 21605-95 钢与玻璃烧结视境HG 21606-95钢与玻璃烧结液位计HG 21607-96异形筒体和封头HG 21607-96异形筒体和封头HG 2161-1991三环唑可湿性粉剂HG 21618-98 丝网除沫器HG 2162-199150%草甘膦可溶性粉剂HG 2167-1991聚三氟氯乙烯树脂HG 2168-1991绿麦隆原药HG 2169-1991绿麦隆可湿性粉剂HG 2176-1991力车轮胎模具HG 2178-1991家用煤气表橡胶膜片HG 2179-1991橡胶涂覆织物绝缘带HG 2180-1991磷酸贮罐衬里用自然硫化橡胶板HG 2183-1991耐稀酸碱橡胶软管HG 2195-2001航空轮胎使用与保养HG 2199-1991水胺硫磷乳油HG 2200-1991甲基异柳磷乳油HG 2201-1991扑草净原药HG 2202-1991扑草净可湿性粉剂HG 2203-19912甲4氯钠水剂HG 2204-1991莠去净水悬浮剂HG 2206-1991甲霜灵原药HG 2207-1991甲霜灵粉剂HG 2208-1991甲霜灵可湿性粉剂HG 2209-1991哒嗪硫磷原药HG 2210-1991哒嗪硫磷乳油HG 2211-1991乙酰甲胺磷原药HG 2212-1991乙酰甲胺磷乳油HG 2227-1991水处理剂硫酸铝HG 2228--91水处理剂多元磷酸醇脂HG 2229--91水处理剂马来酸酐丙烯酸共聚物HG 2230--91水处理剂十二烷基二甲基苄基氯化铵HG 2264-1992 釜用机械密封类型、主要尺寸及标志HG 23011-1999厂区动火作业安全规程HG 23012–1999厂区设备内作业安全规程HG 23018–1999厂区设备检修作业安全规程HG 2322-92工业金属钠HG 2326-2005 工业硫酸锌HG 2432-2001 搪玻璃设备技术条件HG 2432-2001 搪玻璃设备技术条件HG 2432-2001中的若干问题HG 25039-91 皮带运输机维护检修规程HG 2565-94工业硫酸铝钾HG 2566-94工业氢氧化钡HG 2599-94 液氨汽车罐车技术条件HG 2616-2005 食品添加剂复合疏松剂HG 3092-1988燃气输送管及配件用橡胶密封圈胶料HG 3093-1988石油基油类输送管道及连接件用橡胶密封制品胶料HG 3158-2005 液化气体罐车用紧急切断阀HG 3247-2000工业高氯酸钾HG 3581-1999工业叠氮化钠HG 3607-2000 工业氢氧化镁HG 3746-2004 水处理剂铝酸钙HG 3788-2005 工业氯化亚砜HG -T 蓝胶指示剂、变色硅胶和无钴变色硅胶HG T 3174-2002 尿素高压设备制造检验方法HG -T2078-1991氰基硝基苯胺HG/T 2015-91橡胶海绵地毯衬垫HG/T 2020532-1993化工粉体工程设计安全卫生规定HG/T 202056运输工艺HG/T 2021566-1995搅拌传动装置单支点机架HG/T 搅拌传动装置带短接联轴器HG/T 2021618-1998丝网除沫器HG/T 2021634-1988锻钢承插焊管件HG/T 2021635-1987无缝对焊管件HG/T 2036-2005 搪玻璃容器参数HG/T 2044-2003机械密封用喷涂氧化铬密封环技术条件HG/T 2049-2005 搪玻璃设备高颈法兰HG/T 20508-2000 控制室设计规定HG/T 20508-2000 控制室设计规定HG/T 20509-2000 仪表供电设计规定HG/T 20512-2000HG/T 20513-2000 仪表系统接地设计规定HG/T 管道等级号及管道材料等级表HG/T 20521-1992化工蒸汽系统设计规定HG/T 2053-2005 搪玻璃设备人孔法兰HG/T 20535-1993化工固体物料装卸系统设计规定HG/T 20546-92化工装置设备布置设计规定HG/T 20553-1993化工配管用无缝及焊接钢管尺寸选用系列HG/T 20561-1994化工工厂总图运输施工图设计文件编制深度规定HG/T 20565 化工企业厂内铁路装卸线、装卸货位、存车线计算规定HG/T 20566-1994 化工回转窑设计规定HG/T 20566-1994 化工回转窑设计规定HG/T 20568-1994 化工固体物料堆场及仓库设计规定HG/T 20568-1994化工固体物料堆场及仓库设计规定HG/T 工艺系统专业噪声控制设计HG/T 工艺系统专业噪声控制设计HG/T 隔热、保温类型的选用HG/T 隔热、保温类型的选用HG/T 火炬系统设置HG/T 火炬系统设备HG/T 公用物料站的设置HG/T 公用物料站的设置HG/T 人身防护应急系统的设置HG/T 人身防护应急系统的设置HG/T 管路限流孔板的设置HG/T 管路限流孔板的设置HG/T 气封的设置HG/T 气封的设置HG/T 液封的设置HG/T 液封的设置HG/T 阀门的设置HG/T 阀门的设置HG/T 设备和管道系统设计压力和设计温度的确定HG/T 设备和管道系统设计压力和设计温度的确定HG/T 阻火器的设置HG/T 阻火器的设置HG/T 静态混合器的设置HG/T 静态混合器的设置HG/T 蒸汽疏水阀的设置HG/T 蒸汽疏水阀的设置HG/T 管道过滤器的设置HG/T 管道过滤器的设置HG/T 盲板的设置HG/T 检流器的设置HG/T 检流器的设置HG/T 安全阀的设置和选用HG/T 安全阀的设置和选用HG/T 爆破片的设置和选用HG/T 爆破片的设置和选用HG/T 泵和压缩机压差分析HG/T 泵和压缩机压差分析HG/T 泵的系统特性计算和设备相对安装高度的确定HG/T 泵的系统特性计算和设备相对安装高度的确定HG/T 管径选择HG/T 管径选择HG/T 管道压力降计算HG/T 管道压力降计算HG/T 气-液分离器设计HG/T 气-液分离器设计HG/T 设备进、出管口压力损失计算HG/T 设备进、出管口压力损失计算HG/T 20570[1].14-95 人身防护应急系统的设置HG/T 20570[1].21-95 蒸汽疏水阀的设置HG/T 20575-95化学工业炉阻力计算规定HG/T 工艺装置模型设计规定HG/T 工艺装置管道模型质量验收标准HG/T 模型设计成品包装运输技术规定HG/T 20586-1996化工企业照明设计技术规定HG/T 20636~20639-1998化工装置自控工程设计规定(上、下,国际通用设计体制和方法)HG/T 20637-1998自控专业工程设计HG/T 20638~20639-1998化工装置自控设计规定HG/T 20642-1998化学工业炉耐火纤维炉衬设计技术规定HG/T 化工装置管道材料设计内容和深度规定HG/T 化工装置管道材料设计工程规定HG/T 化工装置管道材料控制专业技术管理规定HG/T 化工装置管道材料控制专业提出的设计条件HG/T 化工装置管道材料设计技术规定HG/T 20646-1998化工装置管道材料设计规定(国际通用设计体制和方法)HG/T 20650-1998 化工企业汽车运输设计运营费计算规定HG/T 20651-1998化工企业铁路运输设计运营费计算规定哪位有钢板和钢带的尺寸、外形、重量及尺寸允许偏差和HG/T 20662-1999化工粉体物料机械输送设计技术条件HG/T 20667-2005 化工建设项目环境保护设计规定HG/T 20667-2005化工建设项目环境保护设计规定HG/T 20668-2000 化工设备设计文件编制规定HG/T 20670-2000 化工、石油化工管架、管墩设计规定HG/T 20672-2005尿素造粒塔设计规定HG/T 20674-2005化工建(构)筑物荷载设计规定HG/T 20681-1990 锅炉房、汽机房土建荷载设计条件技术规定HG/T 20681-2005锅炉房、汽机房土建荷载设计条件技术规定HG/T 20682-1990 化学工业炉燃料燃烧设计计算规定HG/T 20682-2005化学工业炉燃料燃烧设计计算规定HG/T 20683-1990 化学工业炉耐火、隔热材料选用规定HG/T 20683-1990;化学工业炉耐火、隔热材料设计选用规定HG/T 20684-1990 化学工业炉金属材料设计选用规定HG/T 20685-2005 工业炉名词术语HG/T 20690-2000化工企业循环冷却水处理设计技术规定(附条文说明)HG/T 20696-99 玻璃钢化工设备设计规定HG/T 20698-2000 化工采暖通风与空气调节设计规定(附条文说明)HG/T ~9-2000《容器、换热器专业职责范围与设计各阶段的任务》等系列标准HG/T 容器、换热器专业职责范围与设计各阶段的任务。
甲苯甲醇烷基化技术的分析与优化

甲苯甲醇烷基化技术的分析与优化王宏乐,韦鹏,刘燕 (蒲城清洁能源化工有限责任公司, 陕西 渭南 715500)摘要:文章对甲苯甲醇烷基化制备对二甲苯技术进行了分析和讨论,分析了甲苯转化率对产品收率、运行能耗及投资的影响,分析了甲醇转化率对污水排放系统的影响。
经过分析得出,甲苯甲醇烷基化技术制备对二甲苯,产品的选择性很高,非常适于生产对二甲苯。
甲苯甲醇烷基化反应产物中剧毒物质苯的含量非常少,在环境保护方面优于其他芳烃生产工艺。
关键词:甲苯;甲醇;烷基化;分析中图分类号:TQ02文献标志码:A文章编号:1008-4800(2021)15-0092-02DOI:10.19900/ki.ISSN1008-4800.2021.15.046The Analysis and Optimization about Alkylation Technology of Toluene with MethanolWANG Hong-le, WEI Peng, LIU Yan (Pucheng Clean Energy Chemical Co., Ltd., Weinan 715500, China)Abstract: The process using alkylation of toluene and methanol to produce paraxylene is analyzed. The influence of toluene’s conversionon product yields, unit energy consumption and investment are also analyzed. Otherwise, the conversion of methanol also influences the downstream waste water processing system. Alkylation technology of toluene with methano is especially suitable for paraxylene production due to the high selectivity of paraxylene in the product yields. In the product, the amount of toxic benzene is approaching to zero, so it is more environment-friendly than other technologies. Keywords: toluene; methanol; alkylation; analysis0引言由于我国芳烃资源较少,工业上采用甲苯、C9芳烃的烷基转移和甲苯歧化技术生产苯和二甲苯。
催化裂化装置反再系统施工技术方法

催化裂化装置反再系统施工技术方法摘要:反再系统(反应器和再生器)是催化裂化装置的核心设备,是影响催化裂化装置安全和经济效益的关键因素,两器的施工工艺复杂,壳体厚度相差较大,焊接工作量和施工难度比较大,焊接变形较难控制、吊装难度大、内件安装精度要求高.本文我们主要以青海大美项目60万吨/年DMTO装置反再系统为例来探讨“两器”的组对安装工艺流程。
关键词:反应器、再生器、壳体组装、焊接、压力试验。
一、施工概述1、施工方法反应器、再生器采用“立式组装法”施工。
分段组对时按排版图的顺序和位置,采用立装法,由下至上依次组装各筒节,形成分段筒体。
分段安装时采用正装法将各分段筒体按顺序进行吊装。
封头、椎体需在组装平台上单独进行组装。
顶部封头预制成型组焊合格后,需翻转进行衬里施工。
顶部封头吊装前需将旋风、料腿等内部构件临时放置在筒体内。
2、反应器、再生器主要设备参数设备名称反应器(R1101)再生器(R1102)容器类别III类(A2级)II类(D2级)设计压力 MPa 0.25 0.25工作压力 MPa 0.2―0.3 0.2―0.3设计温度℃介质550,壳体350 介质720,壳体350工作温度℃450―550 600―720介质甲醇,油气,催化剂烟气,催化剂容器规格ϕ15600/ϕ11800×45090×36ϕ7000/ϕ5500×25300×22/24金属净重(不含衬里)600t 160t热处理局部热处理不做热处理液压试验 MPa3、反应器、再生器主要吊装分段参数筒节预制组对时可采用75t汽车吊两台,280t履带吊一台,400t履带吊一台进行现场分片分段组装。
其中反应器分四段、再生器分二段进行吊装,反应器、再生器分段吊装时第一段均采用400t履带吊吊装,其余各段吊装以及封头翻转均采用600t履带吊主吊,采用400t履带吊溜尾配合。
二、主要施工程序筒体、封头成品半成品及旋风分离器等内件检验验收→封头、椎体等组装成型→筒节、裙座组装成型→分段组装焊接→焊缝无损检测→接管安装→各段部分内件安装→劳动保护安装→基础验收→分段吊装(除封头外)→段之间环焊缝热处理、无损检测→上封头衬里→上封头翻转、吊装→旋风系统及内件安装→拆除临时加固件→交工验收。
典型反应过程的安全技术(三篇)
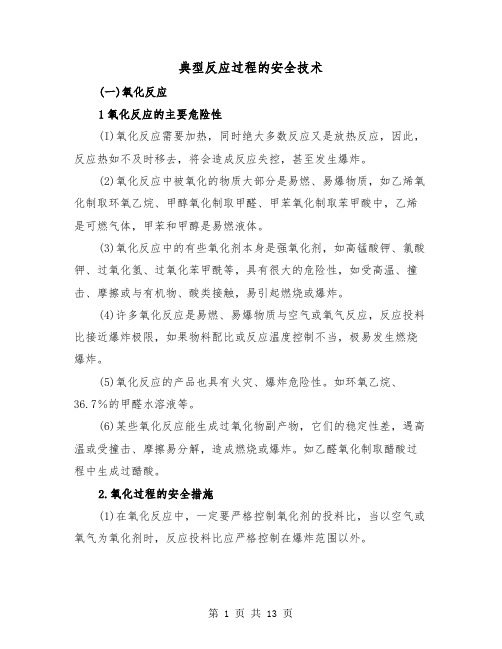
典型反应过程的安全技术(一)氧化反应1氧化反应的主要危险性(I)氧化反应需要加热,同时绝大多数反应又是放热反应,因此,反应热如不及时移去,将会造成反应失控,甚至发生爆炸。
(2)氧化反应中被氧化的物质大部分是易燃、易爆物质,如乙烯氧化制取环氧乙烷、甲醇氧化制取甲醛、甲苯氧化制取苯甲酸中,乙烯是可燃气体,甲苯和甲醇是易燃液体。
(3)氧化反应中的有些氧化剂本身是强氧化剂,如高锰酸钾、氯酸钾、过氧化氢、过氧化苯甲酰等,具有很大的危险性,如受高温、撞击、摩擦或与有机物、酸类接触,易引起燃烧或爆炸。
(4)许多氧化反应是易燃、易爆物质与空气或氧气反应,反应投料比接近爆炸极限,如果物料配比或反应温度控制不当,极易发生燃烧爆炸。
(5)氧化反应的产品也具有火灾、爆炸危险性。
如环氧乙烷、36.7%的甲醛水溶液等。
(6)某些氧化反应能生成过氧化物副产物,它们的稳定性差,遇高温或受撞击、摩擦易分解,造成燃烧或爆炸。
如乙醛氧化制取醋酸过程中生成过醋酸。
2.氧化过程的安全措施(1)在氧化反应中,一定要严格控制氧化剂的投料比,当以空气或氧气为氧化剂时,反应投料比应严格控制在爆炸范围以外。
(2)氧化剂的加料速度不宜过快,防止多加、错加。
反应过程应有良好的搅拌和冷却装置,严格控制反应温度、流量,防止超温、超压。
(3)防止因设备、物料含有杂质为氧化剂提供催化剂,例如有些氧化剂遇金属杂质会引起分解。
空气进入反应器前一定要净化,除掉灰尘、水分、油污以及可使催化剂活性降低或中毒的杂质,减少着火和爆炸的危险。
(4)反应器和管道上应安装阻火器,以阻止火焰蔓延,防止回火。
接触器应有泄压装置,并尽可能采用自动控制、报警联锁装置。
(二)还原反应1.还原反应的主要危险性(1)许多还原反应都是在氢气存在条件下,并在高温、高压下进行,如果因操作失误或设备缺陷发生氢气泄漏,极易发生爆炸。
(2)还原反应中使用的催化剂,如雷内镍、钯碳等,在空气中吸湿后有自燃危险,在没有点火源存在的条件下,也能使氢气和空气的混合物引燃。
s-zorb技术的优缺点(个人整理珍藏版)

S-Zorb的技术优缺点中国石化S-Zorb装置已经开始运行,由于是一个全新的技术,还在不断完善中。
由于汽油质量升级需要,可能还有更多的装置要上此装置。
可能很快进入基础设计阶段,以下是我收集到此技术的优缺点。
优点1、适应于长周期运行。
2、适应原料硫含量的变化。
3、能够保证产品收率。
4、全运转周期反应及产品性质稳定。
5、氢气用量低。
6、汽油吸附脱硫(S-Zorb)技术是专为汽油脱硫开发的新技术。
该技术具有脱硫率高(产品汽油硫含量可低于10ppm)、耗氢少、能耗低、辛烷值损失少、液收高、操作费用低的特点。
S-Zorb技术的开发与应用有益于清洁城市的建设和发展。
7、高适应性。
根据康菲公司的介绍,S-Zorb并不像其他一些工艺路线那样不得不以减少油品总产量作为脱硫的代价。
康菲公司在其网站上还指出,S-Zorb技术适用于几乎所有进料,即,无论是重组分、轻组分、还是混合油气,经可以未经预处理或分馏直接送进S-Zorb装置脱硫。
而该装置在生产过程中并不产生大量的轻组分,从而有助于缓解出口油汽的过高压力。
与此同时,S-Zorb对各种现有的全厂总流程有很强的适应性。
其中,S-Zorb的再生单元对吸附剂的连续再生能力使S-Zorb装置具有很强的连续生产能力。
作为针对催化石脑油设计的非固定床的长效工艺流程,S-Zorb装置可以与催化装置采用同样的检修周期,这样,可以最大限度缩短检修期、最大限度增加油品产量。
8、低造价及低运行费用。
根据康菲公司的宣传资料,在综合考虑运行周期、辛烷值、保证总产量及各种操作参数的基础上,S Zorb技术具有相对较低的操作费用。
康菲公司还介绍说,S Zorb装置的主要工艺设备(流化床反应器及再生器)并没有显著增加投资,原因是,这些设备均采用普通碳钢材料、较低操作压力和较高的空速,这些因素均使得这些设备的成本大幅度降低。
9、可得到较高的液体收率。
单质Ni的加氢活性更高,苯加氢就是用的金属Ni作为加氢催化剂。
危险化学品裂化过程安全技术要点
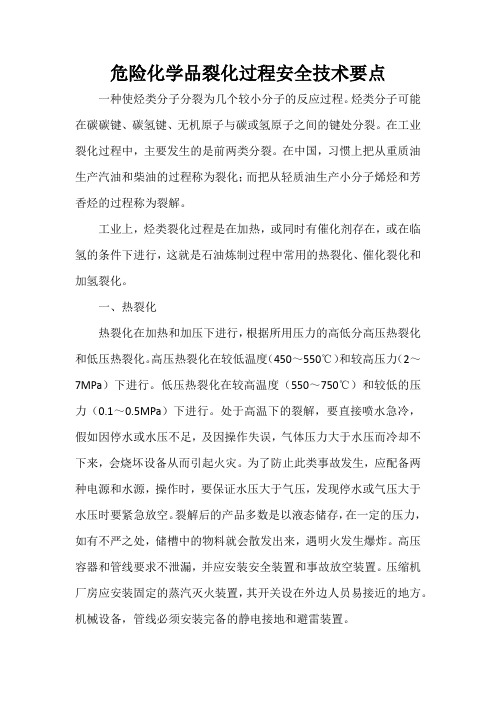
危险化学品裂化过程安全技术要点一种使烃类分子分裂为几个较小分子的反应过程。
烃类分子可能在碳碳键、碳氢键、无机原子与碳或氢原子之间的键处分裂。
在工业裂化过程中,主要发生的是前两类分裂。
在中国,习惯上把从重质油生产汽油和柴油的过程称为裂化;而把从轻质油生产小分子烯烃和芳香烃的过程称为裂解。
工业上,烃类裂化过程是在加热,或同时有催化剂存在,或在临氢的条件下进行,这就是石油炼制过程中常用的热裂化、催化裂化和加氢裂化。
一、热裂化热裂化在加热和加压下进行,根据所用压力的高低分高压热裂化和低压热裂化。
高压热裂化在较低温度(450~550℃)和较高压力(2~7MPa)下进行。
低压热裂化在较高温度(550~750℃)和较低的压力(0.1~0.5MPa)下进行。
处于高温下的裂解,要直接喷水急冷,假如因停水或水压不足,及因操作失误,气体压力大于水压而冷却不下来,会烧坏设备从而引起火灾。
为了防止此类事故发生,应配备两种电源和水源,操作时,要保证水压大于气压,发现停水或气压大于水压时要紧急放空。
裂解后的产品多数是以液态储存,在一定的压力,如有不严之处,储槽中的物料就会散发出来,遇明火发生爆炸。
高压容器和管线要求不泄漏,并应安装安全装置和事故放空装置。
压缩机厂房应安装固定的蒸汽灭火装置,其开关设在外边人员易接近的地方。
机械设备,管线必须安装完备的静电接地和避雷装置。
分离主要是在气相下进行的。
所分离的气体均有火灾爆炸危险,假如设备系统不严密或操作失误,造成可燃气体泄漏,与空气混合形成爆炸性气体混合物,遇火源就会燃烧或爆炸。
分离都是在一定压力下进行的。
原料经压缩机压缩有较高的压力,若设备材质不良,误操作造成负压或超压,或者因压缩机冷却不好,设备因腐蚀、裂缝而泄漏物料,就会发生设备爆炸或油料着火。
分离大都在低温下进行,操作温度有的低至-30~100℃。
在这样的低温条件下,假如原料气或设备系统含水,就会发生冻结堵塞,以至爆炸起火。
化工生产工艺过程与岗位操作安全技术
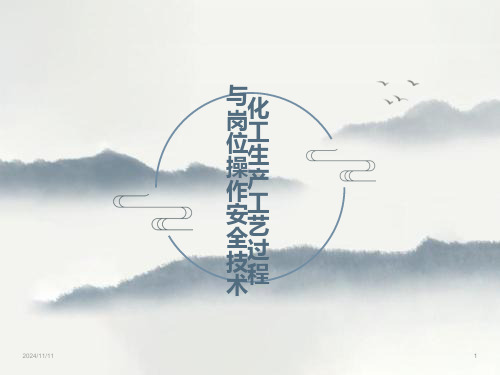
*
11.磺化
*
磺化是在有机化合物分子中引入磺(酸)基(一SO3H)的反应。
常用的磺化剂有发烟硫酸、亚硫酸钠、亚硫酸钾、三氧化硫等。
固体还原剂保险粉、硼氢化钾、氢化铝锂等都是遇湿易燃危险品。 保险粉遇水发热,在潮湿空气中能分解析出硫,硫蒸气受热具有自燃的危险,且保险粉本身受热到190℃也有分解爆炸。 硼氢化钾(钠)在潮湿空气中能自燃,遇水或酸即分解放出大量氢气,同时产生高热。 氢化锂铝是遇湿危险的还原剂。
保险粉用于溶解使用时,要严格控制温度,可以在开动搅拌的情况下,将保险粉分批加入水中,待溶解后再与有机物接触反应;
如用硝基苯与发烟硫酸生产间氨基苯磺酸钠,卤代烷与亚硫酸钠在高温加压条件下生成磺酸盐等均属磺化反应。
*
二、化工单元操作安全技术
*
01
加热 2.冷却
02
加压操作 4.负压操作
03
冷冻 6.物料输送
04
熔融 8.干燥
05
蒸发与蒸馏过程
加氢裂化。由于加氢裂化使用大量氢气,而且反应温度和压力都较高,在高压下钢与氢气接触,钢材内的碳分子易被氢气所夺取,使碳钢硬度增大而降低强度,产生氢脆,如设备或管道检查或更换不及时,就会在高压(10~15MPa)下发生设备爆炸。
8.氯化
*
氯化反应中最常用的氯化剂是液态或气态的氯。氯气本身毒性较大,氧化性极强,储存压力较高,一旦泄漏是很危险的。所以贮罐中的液氯在进入氯化器使用之前,必须先进入蒸发器使其气化。
*
连续重整装置中反再系统钢结构框架和设备的施工

1概述上海石化新建100t/a 连续重整装置中,反应再生系统(以下简称反再系统)施工是整个工程的关键线路,包括钢结构框架、设备、工艺管道等。
该区域的施工重点在于要通过优化钢结构框架安装、吊装工艺,合理安排结构与设备、管道的安装交叉、衔接,达到缩短施工工期、减少安全隐患、提高经济效益的目的。
反再框架主体钢结构工作量包括:钢结构总吨位约1800t 。
框架总体尺寸:长×宽×高为33.8m ×7.5m ×81.89m 。
图1反再框架平面布置图其中轴线1高度64m ,轴线2~5高度81.89m ,轴线6高度24m ,安装标高为0.2m 。
3~4轴线之间为楼梯间。
表1反再框架主立柱规格型式每种规格H 型钢之间为变截面结构。
框架共20层平台,框架梁、平台梁采用H 型钢、工字钢、槽钢,平台上铺设钢格板。
钢结构主体连接形式为:立柱间连接为焊接,梁、斜撑构件翼缘板采用等强坡口焊接,腹板采用高强螺栓连接。
设备:共计45台、套;表2重点安装的设备2总体施工方案的确定框架施工首先是确保安全,同时要满足质量、进度的总体要求。
因此在确定方案时主要考虑以下几点:加大框架在地面预制深度,减少高空作业量;框架的分段要满足吊车的吊装能力,并且每段的安装要与设备、管道相互配合;根据现有场地,做好平面布置和规划,满足吊车站位及变换工况、框架预制和运输、设备进场等的要求,并减少对周边区域的影响。
根据现场实际情况、吊车的使用、设备到货计划,确定以下施工方案:对主体钢结构采用分段预制,即在地面组框、组片的连续重整装置中反再系统钢结构框架和设备的施工■黄峰北京燕华建筑安装工程有限责任公司上海分公司上海201512摘要连续重整装置中反应再生系统的主体钢结构框架高度在80m 以上,总体工作量大,通过分段预制、吊装,优化结构与设备安装的衔接,能有效缩短施工工期、减少安全隐患,提高经济效益,总结其施工方法,可为类似装置施工提供借鉴。
反应再生器安全技术范本(2篇)
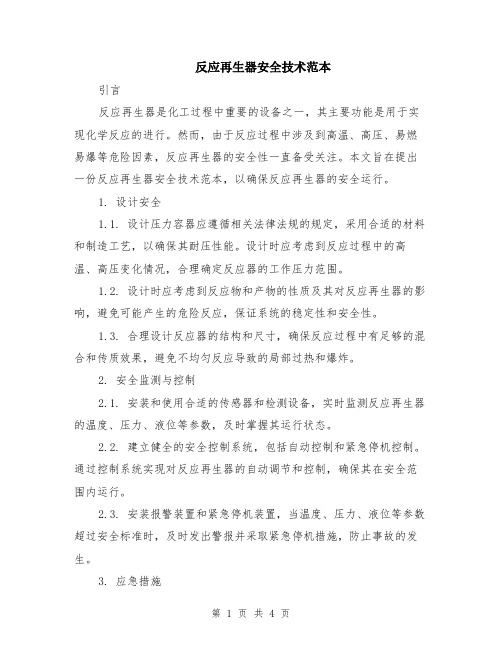
反应再生器安全技术范本引言反应再生器是化工过程中重要的设备之一,其主要功能是用于实现化学反应的进行。
然而,由于反应过程中涉及到高温、高压、易燃易爆等危险因素,反应再生器的安全性一直备受关注。
本文旨在提出一份反应再生器安全技术范本,以确保反应再生器的安全运行。
1. 设计安全1.1. 设计压力容器应遵循相关法律法规的规定,采用合适的材料和制造工艺,以确保其耐压性能。
设计时应考虑到反应过程中的高温、高压变化情况,合理确定反应器的工作压力范围。
1.2. 设计时应考虑到反应物和产物的性质及其对反应再生器的影响,避免可能产生的危险反应,保证系统的稳定性和安全性。
1.3. 合理设计反应器的结构和尺寸,确保反应过程中有足够的混合和传质效果,避免不均匀反应导致的局部过热和爆炸。
2. 安全监测与控制2.1. 安装和使用合适的传感器和检测设备,实时监测反应再生器的温度、压力、液位等参数,及时掌握其运行状态。
2.2. 建立健全的安全控制系统,包括自动控制和紧急停机控制。
通过控制系统实现对反应再生器的自动调节和控制,确保其在安全范围内运行。
2.3. 安装报警装置和紧急停机装置,当温度、压力、液位等参数超过安全标准时,及时发出警报并采取紧急停机措施,防止事故的发生。
3. 应急措施3.1. 制定反应再生器事故应急预案,明确责任和任务,确保在事故发生时能够及时、有效地处理问题,保护人员生命安全和设备财产。
3.2. 配备必要的安全设备和救援装备,如防护服、呼吸器、安全带等,提供必要的培训和演练,以应对紧急情况。
3.3. 建立与应急救援机构的联系,及时获取专业救援支持,提高处理事故的能力和效率。
4. 维护与管理4.1. 定期进行设备的检修和维护,及时处理设备的故障和隐患,保持设备的良好状态。
4.2. 建立完善的操作管理制度,指导操作人员安全正确地操作设备,规范设备的使用流程。
4.3. 建立反应再生器的安全档案,记录设备的维修、维护、检测等情况,方便跟踪和管理设备的安全性能。
反应再生器安全技术

反应再生器安全技术反应再生器是一种非常重要的化工装置,它主要用于各种化学反应的进行。
然而,由于反应再生器存在着一定的安全风险,因此在工作过程中需要加强对其安全性的保障。
以下是关于反应再生器安全技术的一些介绍和措施,希望对大家有所帮助。
一、反应再生器安全技术介绍1.防爆设计反应再生器的设计应该遵循“防爆”原则,因为化学反应会产生各种气体,其中很多都是易燃的。
针对这种情况,设计人员需要采取一系列有效的预防措施,如将反应器置于独立区域内,并用围栏隔离,安装完备的防爆措施,必要时还可以采用气体检测器等设备,确保反应器的运行安全。
2.防毒设计反应再生器中产生的气体有些还可能对人体带来伤害,因此设计人员还需要考虑反应器的防毒设计。
具体而言,可采用质量闭门、气密实验室、自动闭合阀门等防毒措施,确保操作人员的安全。
3.防火设计反应再生器的操作过程中还需要注意防火工作。
因此,设计人员需要在反应器中增加防火措施,如加装防火墙、安装灭火器等。
此外,在操作过程中还需要禁止吸烟、打火机等火源进入反应器周围区域。
4.自动控制系统设计反应再生器是一种具有高危险性的化工装置,为了更好地控制反应过程,减少人为因素所带来的安全隐患,设计人员需要在反应器中增加自动控制系统,以确保反应器的安全、高效运行。
二、反应再生器安全技术措施1.加强操作人员的安全教育和培训对于使用反应再生器的操作人员来说,他们是反应器运行的直接责任人。
因此,在提高反应器安全性方面,加强操作人员的安全教育和培训显得尤为重要。
操作人员需要了解反应再生器的基本构造、工作原理及其特点,清楚掌握各种应急处理措施,提高反应器的安全性。
2.定期进行安全检查和维护反应再生器是一种高精度的化工装置,为了确保其长期稳定运行,操作人员需要定期进行安全检查和维护。
具体而言,需要对反应器的各个部位进行仔细检查,及时更换损坏的零部件,做好防腐蚀、绝缘和排放等工作,确保反应器设备的长期、稳定运行。
反应再生器安全技术

反应再生器安全技术反应再生器是化工工业中常用的一种设备,用于进行化学反应的过程。
在操作过程中,由于反应条件的特殊性以及反应物和产物的性质,反应再生器的安全性成为至关重要的一环。
为了保证反应再生器的安全性,需要采取一系列的安全技术措施。
首先,反应再生器的选择是安全的首要考虑因素之一。
选择适合反应条件和产物特性的反应再生器,并确保其材料的耐腐蚀性和抗压性能。
此外,还需要根据反应物和产物的性质,选择适当的搅拌方式和搅拌强度,避免发生过大的物理反应。
其次,反应再生器的安全控制系统也是非常重要的。
安全控制系统包括温度、压力和流量等参数的监测和控制。
通过安全控制系统的实时监测,可以及时发现并处理可能的危险情况。
例如,当温度超过设定值或压力超过安全范围时,自动控制系统可以及时切断反应再生器的加热或加压装置,避免连锁反应的发生。
此外,反应再生器的保护装置也是必不可少的。
保护装置可以分为被动保护和主动保护两种。
被动保护装置主要包括爆炸隔离板、过压阀和过温阀等,可以及时隔离和释放过高的压力和温度。
而主动保护装置则通过设定特定的报警值,在危险情况发生时自动触发报警和紧急关闭设备,保护操作人员的生命和财产安全。
此外,完善的操作规程和紧急预案也是保证反应再生器安全的重要措施。
操作人员需要充分了解反应再生器的工艺特点和操作规程,严格按照操作流程进行操作。
同时,应建立完善的紧急预案,包括事故的处理流程和应急设备的准备,以应对可能发生的危险情况。
最后,反应再生器的定期检修和维护也是确保其安全性的重要环节。
定期检修和维护可以消除潜在的安全隐患,包括阀门和密封件的更换、设备的清洗和排污等。
同时,还需要建立设备的详细维护记录,对设备的状况进行跟踪和分析,确保设备的正常运行和性能的稳定。
综上所述,反应再生器安全技术包括反应再生器的选择、安全控制系统、保护装置、操作规程和紧急预案,以及定期检修和维护。
通过采取这些安全技术措施,可以有效地保证反应再生器的安全性,防止危险事故的发生,保护人员的生命和财产安全。
- 1、下载文档前请自行甄别文档内容的完整性,平台不提供额外的编辑、内容补充、找答案等附加服务。
- 2、"仅部分预览"的文档,不可在线预览部分如存在完整性等问题,可反馈申请退款(可完整预览的文档不适用该条件!)。
- 3、如文档侵犯您的权益,请联系客服反馈,我们会尽快为您处理(人工客服工作时间:9:00-18:30)。
反应再生器安全技术
设备名称故障故障原因及后果预防措施反应器(沉降器)提升管温度
过高( 1)进料量减少( 2)再生剂循环量过大,易造成分馏系统大幅
度波动,只产气体,下部液体少,冲塔等事故(1)提高进料量( 2)检查再生器滑阀是否出现问题提升管温度过低(1)原料油带水严重(2)再生器循环量减少或中断,造成沉降压力上升,气体段藏量急降,待
生催化剂带油,再生器超温,严重时烟囱带黄烟( 1
④ 减少待生催化剂,去再生器的量⑤温度太低 (重催低于 485℃)启动原料自动保护联锁装置切断
进料( 2
阀无问题要考虑是否是再生管被堵塞,尤其是滑阀无问题,催化剂中
断,应停工处理压力波动大( 1)原料带水( 2)反应温度波动( 3)分
馏塔液面高( 4)分馏冷回流启动大或冷空出现问题( 5)气压机故障停车,易造成反应 --再生器压力波动大,沉降器油气压力波动大,再生器超温,烧坏设备。
沉降器旋风分离器工作不稳定造成油浆中固体含
量增加,若处理不好,造成油浆系统堵塞不畅等(1)原料带水见上(2)降低分馏塔底页面多甩油浆,提高分馏塔下部温度少产油浆(3)检查好塔顶空冷冷却温度等( 4)必要时启动原料自动保护联锁装置
再生器超温( 1)待生催化剂带油( 2)重油催化、原料轻重不均( 3)再生取热系统故障造成再生器以及烟气后部系统内构件损坏,损坏烟
道,催化剂跑损等(1)检查汽提蒸汽除油气效果(2)调整好重油催
化的重油与蜡油的比例( 3)分析再生取热系统故障原因后要加大取热量以降低再生温度,自动联锁启用,保护装置安全反应 ----再生系统衬
里脱落,尤其是斜管、提升管衬里脱落(1)施工质量不好(2)两器开工升温不按升温曲线,升温波动大(3)两器超温频繁,反应—再生出现热点(壁温在500℃以上)强度降低,增加磨损,产生催化剂泄露,处理不当,停工斜管、提升管衬里脱落,造成再生滑阀堵塞,斜管堵
塞,催化剂循环量减少或中止,装置大幅度降量或停工( 1)严把施工质量关,选用好的绝缘耐磨衬里( 2)两器尤其在装置第一次开工,严格按升温要求烘干衬里( 3)严格操作,做到原料、操作条件平衡,保证水、电、气、风平衡,防止两器频繁超温( 4)加强两器日常检查,使用红外温度计和夜间闭烟检查,及早发现过热点,及早维护超压或
压力过低(1)沉降室压力大,造成再生压力波动(自动位量)(2)再生主风控制波动(3)再生压力控制或烟机突然故障停车(4)再生器取热管爆管再生器超压易引起主风机、增压机飞动,从而引起无主风,引起催化剂倒入,主风机恶性事故或再生压力太高,再生剂压空,空
气要进入沉降室的重大恶性事故(催化剂倒流)(1)再生压力控制手动,控制好再生压力( 2)再生器主风进量改手动,控制入再生器风量稳定( 3)三机组时烟机停车则主风机要减少一半(二台主风机并联操作),反应—再生降压操作,若烟机与主风机分体,只发电,则控制好烟气放空( 4)取热器坏,停用取热器,同时要调解好原料,降低生焦油量以保证热平衡( 5)造成倒流迹象启动主风、原料自动保护联锁装
置沉降室结焦( 1)沉降室提升管出口的快速分离器型式落后(2)沉降室中油气停留时间长(3)大气管线保温不好,结焦焦块堵塞,能分
离造成催化剂进分馏系统,加速油浆系统磨损和堵塞,进入待生斜管
或在待生催化剂出口结焦、造成待生催化剂进不了再生器而停工(1)选用新型提升管出口的快速分离器,减少油气在沉降室中停留时间(2)大油气线改用冷壁管,降低油气管的温差,减少结焦(3)采用新型汽提段,采用滤油设施,防止焦块进入待生斜管(4)采用高效喷嘴,提高原料雾化粒度。