水泥激发剂应用常见技术问题探讨
混凝土中添加碱激发剂的效果研究及应用的

混凝土中添加碱激发剂的效果研究及应用的观点和理解在混凝土工程中,添加碱激发剂是一种常见的做法,旨在改善混凝土的性能和使用寿命。
通过深入研究和应用碱激发剂,可以实现一系列显著的效果和优势。
本文将对混凝土中添加碱激发剂的效果研究及应用进行探讨,帮助读者更全面地了解这一领域的知识。
1. 碱激发剂的基本概念和原理1.1 什么是碱激发剂碱激发剂是指一类能够提高混凝土碱活性和化学反应性的化学物质。
1.2 碱激发剂的原理碱激发剂通过在混凝土中引入碱离子,促使混凝土中的硅酸盐矿物与水发生化学反应,生成二次水化产物。
这些产物能够填充混凝土内部微观孔隙,提高混凝土的致密性和耐久性。
2. 碱激发剂对混凝土性能的影响2.1 硬化性能2.1.1 提高混凝土的早期强度发展碱激发剂能够促进混凝土中的水化反应,加速硬化过程,提高混凝土的早期强度发展速度。
2.1.2 改善混凝土的抗压强度和抗裂性能添加碱激发剂可以增强混凝土的力学性能,提高混凝土的抗压强度和抗裂性能。
2.2 耐久性能2.2.1 提高混凝土的耐久性碱激发剂能够填充混凝土内部微观孔隙,提高混凝土的致密性,减少渗透介质的渗透和侵蚀,从而提高混凝土的耐久性。
2.2.2 抑制混凝土的碳化和氯离子渗透添加碱激发剂能够减缓碳化和氯离子渗透的速度,减少混凝土的腐蚀和氧化现象,延长混凝土的使用寿命。
3. 碱激发剂的应用领域3.1 桥梁工程桥梁通常处于恶劣的环境条件下,需要具有较高的耐久性。
添加碱激发剂可以改善混凝土的耐久性,提高桥梁的使用寿命。
3.2 高层建筑高层建筑的混凝土结构承受着巨大的荷载和变形,添加碱激发剂可以提高混凝土的强度和抗裂性能,增强建筑结构的稳定性和安全性。
3.3 水利工程水利工程中的混凝土结构需要具有较高的抗渗性和耐久性。
添加碱激发剂可以减少水泥浆体的渗水现象,保证工程的安全和稳定。
总结回顾:通过添加碱激发剂,可以改善混凝土的性能和使用寿命,提高混凝土的强度、耐久性和抗裂性能。
分析水泥工艺外加剂技术及应用
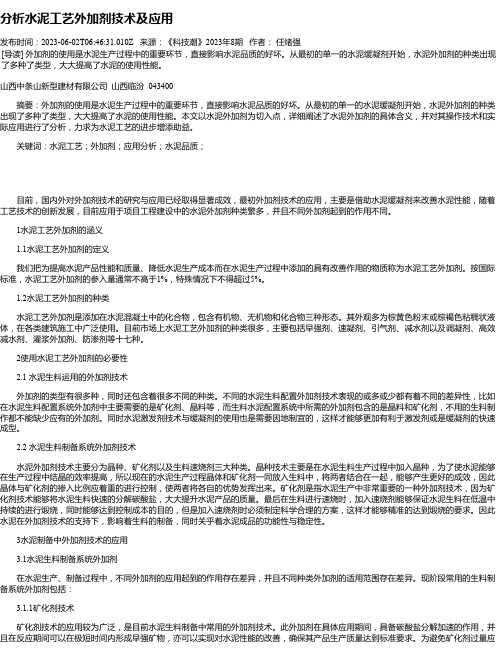
分析水泥工艺外加剂技术及应用发布时间:2023-06-02T06:46:31.010Z 来源:《科技潮》2023年8期作者:任绪强[导读] 外加剂的使用是水泥生产过程中的重要环节,直接影响水泥品质的好坏。
从最初的单一的水泥缓凝剂开始,水泥外加剂的种类出现了多种了类型,大大提高了水泥的使用性能。
山西中条山新型建材有限公司山西临汾 043400摘要:外加剂的使用是水泥生产过程中的重要环节,直接影响水泥品质的好坏。
从最初的单一的水泥缓凝剂开始,水泥外加剂的种类出现了多种了类型,大大提高了水泥的使用性能。
本文以水泥外加剂为切入点,详细阐述了水泥外加剂的具体含义,并对其操作技术和实际应用进行了分析,力求为水泥工艺的进步增添助益。
关键词:水泥工艺;外加剂;应用分析;水泥品质;目前,国内外对外加剂技术的研究与应用已经取得显著成效,最初外加剂技术的应用,主要是借助水泥缓凝剂来改善水泥性能,随着工艺技术的创新发展,目前应用于项目工程建设中的水泥外加剂种类繁多,并且不同外加剂起到的作用不同。
1水泥工艺外加剂的涵义1.1水泥工艺外加剂的定义我们把为提高水泥产品性能和质量、降低水泥生产成本而在水泥生产过程中添加的具有改善作用的物质称为水泥工艺外加剂。
按国际标准,水泥工艺外加剂的参入量通常不高于1%,特殊情况下不得超过5%。
1.2水泥工艺外加剂的种类水泥工艺外加剂是添加在水泥混凝土中的化合物,包含有机物、无机物和化合物三种形态。
其外观多为棕黄色粉末或棕褐色粘稠状液体,在各类建筑施工中广泛使用。
目前市场上水泥工艺外加剂的种类很多,主要包括早强剂、速凝剂、引气剂、减水剂以及调凝剂、高效减水剂、灌浆外加剂、防渗剂等十七种。
2使用水泥工艺外加剂的必要性2.1 水泥生料运用的外加剂技术外加剂的类型有很多种,同时还包含着很多不同的种类。
不同的水泥生料配置外加剂技术表现的或多或少都有着不同的差异性,比如在水泥生料配置系统外加剂中主要需要的是矿化剂、晶料等,而生料水泥配置系统中所需的外加剂包含的是晶料和矿化剂,不用的生料制作都不能缺少应有的外加剂。
大掺量混合材复合水泥活性激发技术研究

激发 方案 初凝 ̄l/ i h mn ]
3% 0
由于各类混合材的活性 普遍 较低 , 合水泥 的早 复 期强度往往随混合材掺 量 的增加 而显著 降低 , 从而 不 利 于各类工业废渣 的高效 利用 。 目前 , 用于激发 复 合水泥 中混合 材 活性 的主 要技 术途 径分 为 机械力 活 化和化学激发两大类 , 而化学激发 活性 的方法具有 操 作简单 , 入 成本低 等 优 点 。 因此 , 中研 究几 种 投 文 不 同种类化 学激 发剂 对 大掺 量混 合材 复合 水泥 强度 发展 的影响规律 , 具有重要 的实 际意义 。
采用吉林 辽 源金 刚水 泥集 团生产 的硅 酸盐 水 泥 熟料 , 山钢铁集 团公 司生 产 的粒状高 炉矿 渣 , 庆 鞍 大 油 田自备电厂产干排粉煤 灰 , 山东 枣庄生产 的天然 石 膏 。所采用的 4种化 学激 发剂均 为化学纯 试剂 : 碱 纯 ( 、 明粉 ( S 、 耵) 元 N ) 烧碱 ( J 、 s ) 明矾石( ) MF 。
【 中图分类号】 T 12 Q 7 【 文献标识码 】 B 【 文章编 号】 10 — 84 21 )2 0 1 一 2 0 1 66 (0 11 — 00 O
传统硅酸盐水 泥存 在早期 水化放 热量 大、 容易开
2 结果与分析
裂和耐久性 差等缺 点 , 时带来 巨大 的资源 、 同 能源
量的影 响最小 为 0 4 , F对用 水量 的增 加值 最多 .% 而 根 据实际 生 产 经验 和前 期 研 究 结 果 , 虑生 产 考 4 . 、2 5两个强度 等 级 的复合 水 泥 , 2 5 3. 分别 确定 矿物 掺合料总量为 3 %和 4 %的两配方复合水 泥 : 0 4 ①水泥 熟料 : 粉煤灰 : 矿渣 : 膏 = 4 2 :0 6 ②水 泥熟料 : 石 6 :0 1 : ;
水泥工艺外加剂技术及应用研究
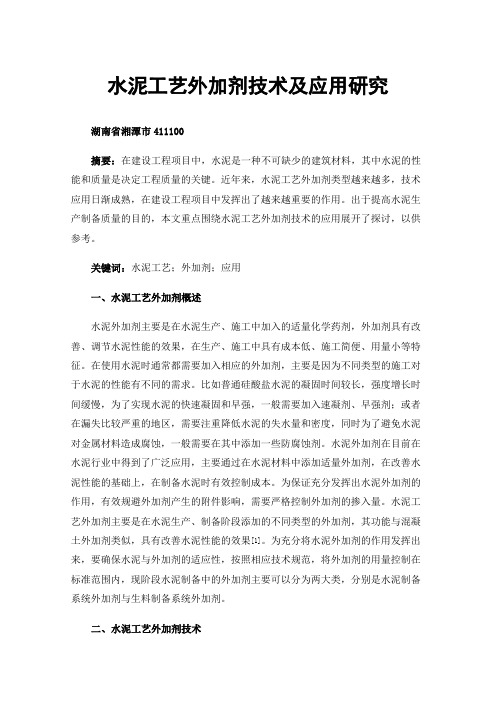
水泥工艺外加剂技术及应用研究湖南省湘潭市411100摘要:在建设工程项目中,水泥是一种不可缺少的建筑材料,其中水泥的性能和质量是决定工程质量的关键。
近年来,水泥工艺外加剂类型越来越多,技术应用日渐成熟,在建设工程项目中发挥出了越来越重要的作用。
出于提高水泥生产制备质量的目的,本文重点围绕水泥工艺外加剂技术的应用展开了探讨,以供参考。
关键词:水泥工艺;外加剂;应用一、水泥工艺外加剂概述水泥外加剂主要是在水泥生产、施工中加入的适量化学药剂,外加剂具有改善、调节水泥性能的效果,在生产、施工中具有成本低、施工简便、用量小等特征。
在使用水泥时通常都需要加入相应的外加剂,主要是因为不同类型的施工对于水泥的性能有不同的需求。
比如普通硅酸盐水泥的凝固时间较长,强度增长时间缓慢,为了实现水泥的快速凝固和早强,一般需要加入速凝剂、早强剂;或者在漏失比较严重的地区,需要注重降低水泥的失水量和密度,同时为了避免水泥对金属材料造成腐蚀,一般需要在其中添加一些防腐蚀剂。
水泥外加剂在目前在水泥行业中得到了广泛应用,主要通过在水泥材料中添加适量外加剂,在改善水泥性能的基础上,在制备水泥时有效控制成本。
为保证充分发挥出水泥外加剂的作用,有效规避外加剂产生的附件影响,需要严格控制外加剂的掺入量。
水泥工艺外加剂主要是在水泥生产、制备阶段添加的不同类型的外加剂,其功能与混凝土外加剂类似,具有改善水泥性能的效果[1]。
为充分将水泥外加剂的作用发挥出来,要确保水泥与外加剂的适应性,按照相应技术规范,将外加剂的用量控制在标准范围内,现阶段水泥制备中的外加剂主要可以分为两大类,分别是水泥制备系统外加剂与生料制备系统外加剂。
二、水泥工艺外加剂技术(一)水泥生料制备系统外加剂1、矿化剂技术该技术在水泥制备过程中有着比较广泛的应用,其具有碳酸盐分解加速的效果,在反应过程中能在非常短的时间内形成早强矿物,达到改善水泥性能的目标,保证水泥产品的生产达到相应的质量标准。
浅谈碱激发水泥、混凝土的力学性能
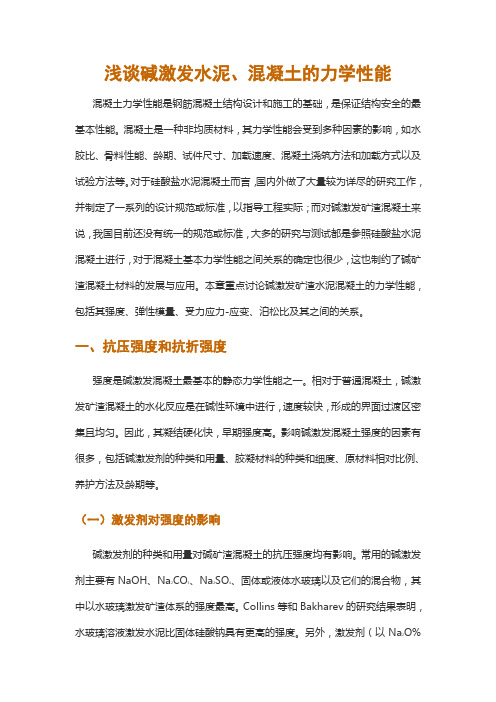
浅谈碱激发水泥、混凝土的力学性能混凝土力学性能是钢筋混凝土结构设计和施工的基础,是保证结构安全的最基本性能。
混凝土是一种非均质材料,其力学性能会受到多种因素的影响,如水胶比、骨料性能、龄期、试件尺寸、加载速度、混凝土浇筑方法和加载方式以及试验方法等。
对于硅酸盐水泥混凝土而言,国内外做了大量较为详尽的研究工作,并制定了一系列的设计规范或标准,以指导工程实际;而对碱激发矿渣混凝土来说,我国目前还没有统一的规范或标准,大多的研究与测试都是参照硅酸盐水泥混凝土进行,对于混凝土基本力学性能之间关系的确定也很少,这也制约了碱矿渣混凝土材料的发展与应用。
本章重点讨论碱激发矿渣水泥混凝土的力学性能,包括其强度、弹性模量、受力应力-应变、泊松比及其之间的关系。
一、抗压强度和抗折强度强度是碱激发混凝土最基本的静态力学性能之一。
相对于普通混凝土,碱激发矿渣混凝土的水化反应是在碱性环境中进行,速度较快,形成的界面过渡区密集且均匀。
因此,其凝结硬化快,早期强度高。
影响碱激发混凝土强度的因素有很多,包括碱激发剂的种类和用量、胶凝材料的种类和细度、原材料相对比例、养护方法及龄期等。
(一)激发剂对强度的影响碱激发剂的种类和用量对碱矿渣混凝土的抗压强度均有影响。
常用的碱激发剂主要有NaOH、Na2CO3、Na2SO4、固体或液体水玻璃以及它们的混合物,其中以水玻璃激发矿渣体系的强度最高。
Collins等和Bakharev的研究结果表明,水玻璃溶液激发水泥比固体硅酸钠具有更高的强度。
另外,激发剂(以Na2O%计)的掺量对碱矿渣水泥砂浆、混凝土强度也有重要的影响,当采用水玻璃(M s=1.0)为激发剂时,激发剂的掺量存在一个最佳值,结果如表1所示。
碱含量在4%到12%时,随着碱含量的增加,砂浆的抗折强度和抗压强度先增大后减少,最佳的碱含量为8%。
表1 激发剂掺量对碱矿渣水泥砂浆强度的影响然而,由于原材料的来源不同,制备工艺、养护制度以及水玻璃的模数等不同,都会影响到最佳碱含量。
复合激发剂对高掺量粉煤灰水泥的影响研究

灰的水泥硬化浆体的早期强度,而且提高了后期的强度;正交实验优化的30%和50%粉煤灰复合硅酸盐水泥复合激发剂的添加量分别
为:1%隔$0<, l%CaS04, l%Na2SiO3^l%Na2SO4, 4%CaS0” 1.5%Na2SiO3.复合激发剂中各组分发挥了各自的激发作用,复合水泥性能满足国
家标准.
2
1
2
1. 0 30.5 5.11 57.1 8.42
3
1
4
1.5 29. 3 4.92 54. 3 8. 11
4
2
1
1. 0 29.6 4.93 53.2 8. 02
5
2
2
0.5 24. 3 4. 36 45. 3 7. 14
6
2
4
1.5 27.2 4.62 48.4 7.21
7
3
1
1.5 28. 3 4.73 51.6 7.86
Key words: fly ash; composite cement^ compound activation
粉煤灰作为混合材料应用于水泥生产不仅可以防止粉 煤灰对环境和生态的影响,而且降低水泥生产成本,改善水 泥的施工和使用性能,具有水化热低,干缩小等特点,因此 被广泛应用“化在我国的水泥标准中,以粉煤灰为主要混 合材料的水泥有通用水泥和特性水泥。随着工业发展,粉煤 灰的排放量逐年增加,其品质指标(用于水泥混合材料)也 越来越好,但由于其结构特性,造成粉煤灰水泥早期强度偏 低,影响了粉煤灰掺加量。为了提高粉煤灰水泥的早期强 度,必须激发粉煤灰的活性,而活性激发的关键是使Si-o键 和A1-0键断裂。采用化学激发剂激发粉煤灰的活性,国内外 已有较多研究炉叫由于激发剂单掺对粉煤灰活性的激发效 果并不理想,所以,化学激发剂的复合使用已成为粉煤灰活 性激发的趋势。本文主要研究化学激发剂对高掺量粉煤灰水 泥浆体性能的影响。
碱矿渣水泥激发剂的试验与应用

表4
试 样 品 种
墙体材料试验结果 1)
弯曲强度检验 导热系数 干缩系数 / ( mm/ m) 合格 合格 合格 0 18 0 20 0 16 0 92 0 98 0 88 成本 / ( 元 / m2 ) 32 30 26
产品可移动时间 / h 阻燃性能 面密度 / ( kg/ m2 ) 24 48 24 600 mm 合格 合格 合格 48 0 50 5 47 0
场前景。 参考文献:
[ 1] S. Minders. Materials Selection Proportion And Quality Control [ J] . High Performance Contest And Application, 1994, ( 7) : 18. [ 2] 重庆建筑工程学院 , 南京工学院 . 混凝土学 [ M ] . 北京 : 中 国建筑工业出版社 , 1983. [ 4] 冯乃谦 . 高强 混凝土 技术 [ M ] . 北京 : 中国 建材工 业出 版 社 , 1992. 作者简介 : 韩美 玲 ( 1965- ) , 女 , 山 西文 水 人 , 讲师 、 工 程师 , 1986 年 7 月毕业于上海建材学院胶凝材料制品专 业 , 现从 事 无机非金属材料的教学工作 。 收稿日 期 : 2000- 12- 19 ( 编辑 于振朝 )
1) 表中三组混凝土试样配比均为水泥 砂 石子 = 1 1 93 3 52。
试验表明, F 型碱矿渣水泥制成的混凝土, 坍落 度、 流动度大于普通水泥混凝土, 早强、 后期强度高 于普通水泥混凝土 , 冻融损失也只有普通水泥混凝 土的 1/ 2, 说明 其具有 更好的 耐久性 , 而 且成本 比 P O 425水泥低 20 % 左右。 5. 2 碱矿渣水泥在墙体材料中的应用试验 在易于推广碱矿渣水泥的非承重结构墙体材料 制品方面, 我们用 F ( 液态 ) 型碱激发剂制作的碱矿 渣水泥与目前常用的 P O 425 水泥、 快硬硫铝酸盐 425 水泥作为胶凝材 料, 分别进行了产品性 能和成 20
激发剂对钢渣水泥的活化及作用机理
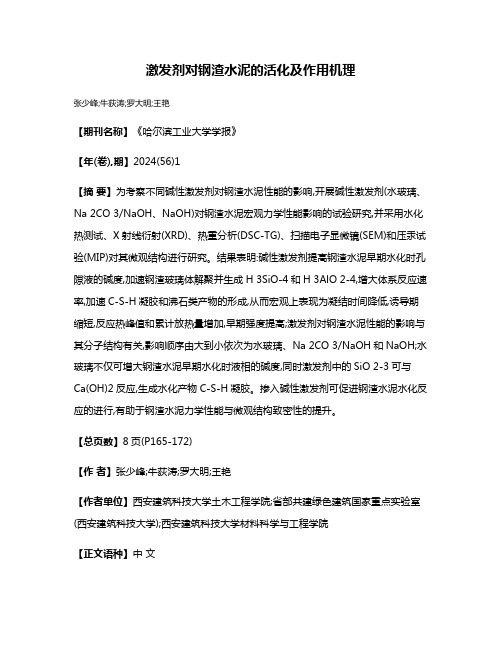
激发剂对钢渣水泥的活化及作用机理张少峰;牛荻涛;罗大明;王艳【期刊名称】《哈尔滨工业大学学报》【年(卷),期】2024(56)1【摘要】为考察不同碱性激发剂对钢渣水泥性能的影响,开展碱性激发剂(水玻璃、Na 2CO 3/NaOH、NaOH)对钢渣水泥宏观力学性能影响的试验研究,并采用水化热测试、X射线衍射(XRD)、热重分析(DSC-TG)、扫描电子显微镜(SEM)和压汞试验(MIP)对其微观结构进行研究。
结果表明:碱性激发剂提高钢渣水泥早期水化时孔隙液的碱度,加速钢渣玻璃体解聚并生成H 3SiO-4和H 3AlO 2-4,增大体系反应速率,加速C-S-H凝胶和沸石类产物的形成,从而宏观上表现为凝结时间降低,诱导期缩短,反应热峰值和累计放热量增加,早期强度提高;激发剂对钢渣水泥性能的影响与其分子结构有关,影响顺序由大到小依次为水玻璃、Na 2CO 3/NaOH和NaOH;水玻璃不仅可增大钢渣水泥早期水化时液相的碱度,同时激发剂中的SiO 2-3可与Ca(OH)2反应,生成水化产物C-S-H凝胶。
掺入碱性激发剂可促进钢渣水泥水化反应的进行,有助于钢渣水泥力学性能与微观结构致密性的提升。
【总页数】8页(P165-172)【作者】张少峰;牛荻涛;罗大明;王艳【作者单位】西安建筑科技大学土木工程学院;省部共建绿色建筑国家重点实验室(西安建筑科技大学);西安建筑科技大学材料科学与工程学院【正文语种】中文【中图分类】TU375【相关文献】1.酸性激发剂激发钢渣替代部分水泥熟料的机理研究2.水玻璃对钢渣水泥激发机理的研究3.矿渣–煤渣复合水泥激发剂及其作用机理(英文)4.激发剂对粉煤灰-钛石膏-电石渣体系的活化及作用机理5.碱激发下砒砂岩钢渣粉水泥复合土强度及微观机理因版权原因,仅展示原文概要,查看原文内容请购买。
混凝土中添加碱激发剂的效果研究及应用
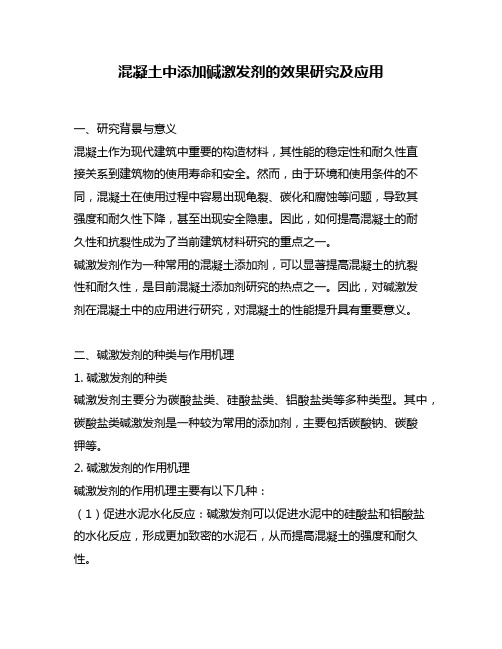
混凝土中添加碱激发剂的效果研究及应用一、研究背景与意义混凝土作为现代建筑中重要的构造材料,其性能的稳定性和耐久性直接关系到建筑物的使用寿命和安全。
然而,由于环境和使用条件的不同,混凝土在使用过程中容易出现龟裂、碳化和腐蚀等问题,导致其强度和耐久性下降,甚至出现安全隐患。
因此,如何提高混凝土的耐久性和抗裂性成为了当前建筑材料研究的重点之一。
碱激发剂作为一种常用的混凝土添加剂,可以显著提高混凝土的抗裂性和耐久性,是目前混凝土添加剂研究的热点之一。
因此,对碱激发剂在混凝土中的应用进行研究,对混凝土的性能提升具有重要意义。
二、碱激发剂的种类与作用机理1. 碱激发剂的种类碱激发剂主要分为碳酸盐类、硅酸盐类、铝酸盐类等多种类型。
其中,碳酸盐类碱激发剂是一种较为常用的添加剂,主要包括碳酸钠、碳酸钾等。
2. 碱激发剂的作用机理碱激发剂的作用机理主要有以下几种:(1)促进水泥水化反应:碱激发剂可以促进水泥中的硅酸盐和铝酸盐的水化反应,形成更加致密的水泥石,从而提高混凝土的强度和耐久性。
(2)改善混凝土的微观结构:碱激发剂可以改变混凝土中的离子平衡,使得混凝土中的孔隙率减小,微观结构更加致密,从而提高混凝土的耐久性。
(3)抑制混凝土的碳化:碱激发剂可以中和混凝土中的酸性物质,抑制混凝土的碳化反应,从而延长混凝土的使用寿命。
(4)提高混凝土的抗裂性:碱激发剂可以增加混凝土中的胶凝材料的粘着力,使得混凝土的抗拉强度和抗裂性得到提高。
三、混凝土中添加碱激发剂的效果研究1. 碱激发剂对混凝土强度的影响研究表明,适量添加碳酸盐类碱激发剂可以显著提高混凝土的强度。
当碳酸盐类碱激发剂的掺量为2%时,混凝土的抗压强度提高了10%以上。
2. 碱激发剂对混凝土耐久性的影响研究表明,适量添加碳酸盐类碱激发剂可以显著提高混凝土的耐久性。
当碳酸盐类碱激发剂的掺量为2%时,混凝土的耐久性可以提高20%以上。
3. 碱激发剂对混凝土抗裂性的影响研究表明,适量添加碳酸盐类碱激发剂可以显著提高混凝土的抗裂性。
碱激发水泥对混凝土性能的影响研究

碱激发水泥对混凝土性能的影响研究一、引言混凝土是建筑工程中重要的结构材料之一。
它的性能对建筑物的安全性和使用寿命有着直接的影响。
近年来,随着人们对建筑物质量和安全性的要求越来越高,对混凝土的性能要求也越来越严格。
因此,研究混凝土的性能及其影响因素具有重要的意义。
其中,碱激发水泥对混凝土性能的影响是一个热门的研究领域。
二、碱激发水泥的概念碱激发水泥是一种新型水泥,在混凝土制作中具有一定的优势。
它是一种以硅酸钠为主要成分的水泥,与传统水泥相比,其强度和抗裂性能更优秀,能够提高混凝土的耐久性和抗渗性能。
三、碱激发水泥对混凝土性能的影响1. 硬化时间碱激发水泥的硬化时间比传统水泥短,可以缩短混凝土的养护期,提高工程效率。
2. 抗裂性能碱激发水泥中硅酸钠的存在可以提高混凝土的抗裂性能。
研究表明,使用碱激发水泥制作的混凝土比传统水泥制作的混凝土更能够承受外部应力,抗裂性能更好。
3. 抗渗性能碱激发水泥中硅酸钠的存在可以使混凝土的孔隙率减少,提高混凝土的密实性和抗渗性能。
此外,碱激发水泥还可以提高混凝土的碳化抗性。
4. 抗压强度研究表明,使用碱激发水泥制作的混凝土的抗压强度相对较高。
这是因为碱激发水泥的晶体结构更加稳定,且其硬化产物的结晶度更高。
5. 相变过程碱激发水泥的晶体结构和硬化产物的相变过程具有一定的特殊性质。
因此,研究碱激发水泥对混凝土性能的影响,也需要考虑其中的相变过程。
四、影响碱激发水泥对混凝土性能的因素1. 碱激发水泥的配比碱激发水泥的配比对混凝土性能的影响非常重要。
在制作混凝土时,需要根据混凝土的实际情况进行配比,以达到最佳的性能表现。
2. 水灰比水灰比是指混凝土中水和水泥的质量比,对混凝土性能的影响也非常显著。
在使用碱激发水泥制作混凝土时,需要根据实际情况选择合适的水灰比。
3. 养护条件混凝土的养护条件对其性能也有着重要的影响。
在使用碱激发水泥制作混凝土时,需要注意养护条件的选择和控制,以达到最佳的性能表现。
混凝土中添加碱激发剂的效果研究及应用

混凝土中添加碱激发剂的效果研究及应用一、引言混凝土作为建筑材料的主要组成部分,其性能的稳定性和耐久性对于建筑物的安全性和寿命有着至关重要的作用。
然而,由于混凝土的主要成分水泥在制造过程中使用较多的热能、排放较多的CO2,同时也会因为硬化过程中的收缩而导致开裂问题。
因此,如何提高混凝土的性能,减少混凝土的开裂和延长混凝土的使用寿命,成为了混凝土研究领域的热门话题之一。
二、碱激发剂的作用原理碱激发剂是一种能够提高混凝土性能的添加剂,其主要作用是通过激发混凝土中的碱性物质,促进混凝土中的反应和结晶过程,增强混凝土的强度和耐久性。
具体来说,碱激发剂能够改变混凝土中的化学反应过程,使得混凝土中的氢氧化钙和氢氧化铝等成分与水发生反应,形成强度更高的水化产物,从而提高混凝土的强度和耐久性。
三、碱激发剂的种类及添加方法1.碳酸钠碱激发剂碳酸钠是一种常见的碱激发剂,其添加量一般为水泥质量的1%-3%。
碳酸钠碱激发剂的添加方法一般是将碳酸钠溶解在水中,然后将其与混凝土拌合均匀即可。
2.硅酸钠碱激发剂硅酸钠也是一种常用的碱激发剂,其添加量一般为水泥质量的1%-3%。
硅酸钠碱激发剂的添加方法与碳酸钠类似,需要将其溶解在水中,然后与混凝土拌合均匀。
3.氢氧化钠碱激发剂氢氧化钠是一种强碱性物质,其添加量一般较少,一般为水泥质量的0.1%-0.3%。
氢氧化钠碱激发剂的添加方法需要注意,一般需要先将氢氧化钠溶解在一定量的水中,然后将其与混凝土拌合均匀。
添加氢氧化钠碱激发剂时需要注意安全,避免皮肤接触和吸入。
四、混凝土中添加碱激发剂的效果研究1.强度性能研究表明,混凝土中添加碱激发剂能够显著提高混凝土的强度性能。
以硅酸钠为例,添加硅酸钠的混凝土28天龄期的抗压强度可提高20%-40%左右。
同时,碳酸钠和氢氧化钠的添加效果也相当不错。
2.耐久性能混凝土的耐久性是衡量其质量的一项重要指标,研究表明,混凝土中添加碱激发剂能够显著提高混凝土的耐久性能。
碱激发水泥对混凝土性能的影响研究
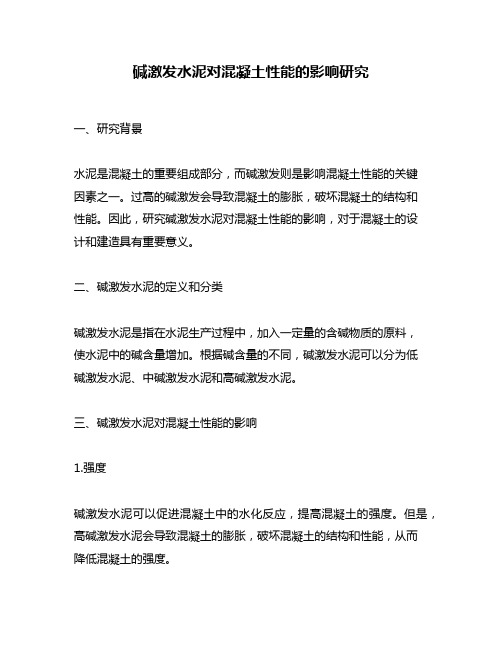
碱激发水泥对混凝土性能的影响研究一、研究背景水泥是混凝土的重要组成部分,而碱激发则是影响混凝土性能的关键因素之一。
过高的碱激发会导致混凝土的膨胀,破坏混凝土的结构和性能。
因此,研究碱激发水泥对混凝土性能的影响,对于混凝土的设计和建造具有重要意义。
二、碱激发水泥的定义和分类碱激发水泥是指在水泥生产过程中,加入一定量的含碱物质的原料,使水泥中的碱含量增加。
根据碱含量的不同,碱激发水泥可以分为低碱激发水泥、中碱激发水泥和高碱激发水泥。
三、碱激发水泥对混凝土性能的影响1.强度碱激发水泥可以促进混凝土中的水化反应,提高混凝土的强度。
但是,高碱激发水泥会导致混凝土的膨胀,破坏混凝土的结构和性能,从而降低混凝土的强度。
2.耐久性碱激发水泥中的碱离子会与混凝土中的氯离子结合,形成氯化物,进而导致混凝土的腐蚀和损坏。
因此,高碱激发水泥会降低混凝土的耐久性。
3.收缩性高碱激发水泥会导致混凝土的膨胀,使混凝土产生收缩应力,从而引起混凝土的开裂和变形。
4.渗透性碱激发水泥中的碱离子会降低混凝土的孔隙度,从而降低混凝土的渗透性。
但是,高碱激发水泥会导致混凝土的膨胀和开裂,增加混凝土的渗透性。
四、减少碱激发水泥对混凝土性能的影响的方法1.选择低碱激发水泥选择低碱激发水泥可以降低混凝土的膨胀和开裂,从而减少碱激发水泥对混凝土性能的影响。
2.添加掺合料添加掺合料可以降低混凝土中的碱含量,从而减少碱激发水泥对混凝土性能的影响。
3.控制混凝土中的水化反应控制混凝土中的水化反应可以降低混凝土中的温度和水分蒸发,从而减少碱激发水泥对混凝土性能的影响。
4.控制混凝土的湿度控制混凝土的湿度可以降低混凝土中的碱含量,从而减少碱激发水泥对混凝土性能的影响。
五、结论碱激发水泥对混凝土性能有着重要的影响,高碱激发水泥会导致混凝土的膨胀和开裂,降低混凝土的强度和耐久性。
为了减少碱激发水泥对混凝土性能的影响,可以选择低碱激发水泥、添加掺合料、控制混凝土中的水化反应和控制混凝土的湿度。
水泥激发剂应用常见技术问题探讨
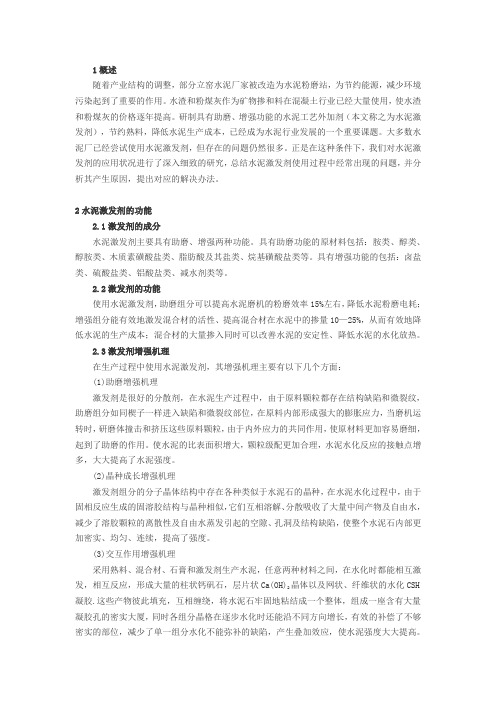
1概述随着产业结构的调整,部分立窑水泥厂家被改造为水泥粉磨站,为节约能源,减少环境污染起到了重要的作用。
水渣和粉煤灰作为矿物掺和料在混凝土行业已经大量使用,使水渣和粉煤灰的价格逐年提高。
研制具有助磨、增强功能的水泥工艺外加剂(本文称之为水泥激发剂),节约熟料,降低水泥生产成本,已经成为水泥行业发展的一个重要课题。
大多数水泥厂已经尝试使用水泥激发剂,但存在的问题仍然很多。
正是在这种条件下,我们对水泥激发剂的应用状况进行了深入细致的研究,总结水泥激发剂使用过程中经常出现的问题,并分析其产生原因,提出对应的解决办法。
2水泥激发剂的功能2.1激发剂的成分水泥激发剂主要具有助磨、增强两种功能。
具有助磨功能的原材料包括:胺类、醇类、醇胺类、木质素磺酸盐类、脂肪酸及其盐类、烷基磺酸盐类等。
具有增强功能的包括:卤盐类、硫酸盐类、铝酸盐类、减水剂类等。
2.2激发剂的功能使用水泥激发剂,助磨组分可以提高水泥磨机的粉磨效率15%左右,降低水泥粉磨电耗;增强组分能有效地激发混合材的活性、提高混合材在水泥中的掺量10—25%,从而有效地降低水泥的生产成本;混合材的大量掺入同时可以改善水泥的安定性、降低水泥的水化放热。
2.3激发剂增强机理在生产过程中使用水泥激发剂,其增强机理主要有以下几个方面:(1)助磨增强机理激发剂是很好的分散剂,在水泥生产过程中,由于原料颗粒都存在结构缺陷和微裂纹,助磨组分如同楔子一样进入缺陷和微裂纹部位,在原料内部形成强大的膨胀应力,当磨机运转时,研磨体撞击和挤压这些原料颗粒,由于内外应力的共同作用,使原材料更加容易磨细,起到了助磨的作用。
使水泥的比表面积增大,颗粒级配更加合理,水泥水化反应的接触点增多,大大提高了水泥强度。
(2)晶种成长增强机理激发剂组分的分子晶体结构中存在各种类似于水泥石的晶种,在水泥水化过程中,由于固相反应生成的固溶胶结构与晶种相似,它们互相溶解、分散吸收了大量中间产物及自由水,减少了溶胶颗粒的离散性及自由水蒸发引起的空隙、孔洞及结构缺陷,使整个水泥石内部更加密实、均匀、连续,提高了强度。
Na_2CO_3激发剂对高掺量矿渣水泥性能的影响[1]
![Na_2CO_3激发剂对高掺量矿渣水泥性能的影响[1]](https://img.taocdn.com/s3/m/4ab3bc59804d2b160b4ec0a4.png)
第21卷 第3期 2006年9月西 南 科 技 大 学 学 报Journal o f Sout hwest U niversity of Sc i ence and T echno logyV o.l 21N o .3 Sept .2006收稿日期:2006-05-20基金项目:四川省科学基金项目(01GY051-36)。
作者简介:刘 涛(1979-),男,硕士研究生,专业方向为新型建筑材料。
E -m ai:l ltz hy@l 126.co m 。
N a 2CO 3激发剂对高掺量矿渣水泥性能的影响刘 涛1谭克锋2(1.西南科技大学材料科学与工程学院 四川绵阳 621010;2.西南科技大学土木工程与建筑学院 四川绵阳 621010)摘要:探讨了化学激发剂N a 2CO 3对高掺量矿渣水泥的力学及耐久性能的影响。
研究结果证明:在矿渣掺量达70%的情况下,以1.5%N a 2CO 3作为激发剂可显著改善高掺量矿渣水泥的力学性能,28d 的抗折强度提高了25%,且该高掺量矿渣水泥的耐久性能如安定性、水化热、抗硫酸盐腐蚀均优于纯硅酸盐水泥。
关键词:矿渣水泥 N a 2CO 3 强度 耐久性中图分类号:TQ172.1 文献标识码:A 文章编号:1671-8755(2006)03-0019-04Properties of Che m icall y A cti vated H igh R ange Sl ag Ce m entL I U T ao 1,TAN K e -feng2(1.School of M aterial Science and Eng ineering,South w est University o f Science and Technology,M ianyang 621010,S ichuan,Ch ina;2.School of C ivil Eng ineering and Architecture ,M ianyang 621010,S ichuan,Ch i n a)Abstract :The m echanical properties and durability of che m ica ll y activated h i g h range slag ce m en tw ere stud ied .The che m ical acti v ator is N a 2CO 3w it h i n co r po ration rate fro m 0.5%to 2.0%.The content o f slag is 70%.The test results show that the i n corporati o n ofN a 2CO 3i n to h i g h range slag ce m en t can si g -n ifi c antly i m prove its m echan ica l pr operties ,and the opti m um con tent of N a 2CO 3is 1.5%.Co m pared w it h pure Po rtland ce m en,t the durability of the h i g h range slag ce m ent such as soundness ,heat o f hydra -ti o n and resistance to su lfate attack have been si g nificantly i m proved .K ey w ords :slag ce m en;t reactiv ity acti v ator ;strength ;durability矿渣作为水泥混合材已有数十年历史,因矿渣水泥具有耐化学腐蚀能力强、水化热低的优点,尤其适用于海洋工程、水下工程和大坝工程等。
混凝土外加剂研究和应用现状及存在的几个问题

混凝土外加剂研究和应用现状及存在的几个问题混凝土外加剂是一种可提高混凝土性能的化学品,通常能改变混凝土的物理和化学性质,如延迟凝结、提高强度、改善工作性等,其应用广泛,可用于各种混凝土结构中。
当前,市场上常见的混凝土外加剂主要有水泥减水剂、减缩剂、引气剂、增强剂、缓凝剂、防水剂等。
水泥减水剂是混凝土外加剂中使用频率最高的一种,其主要功能是减少混凝土中的水用量,提高混凝土的坚实性和强度。
减缩剂主要用于减少混凝土收缩量,控制混凝土内部应力,同时提高混凝土的耐久性。
引气剂可增加混凝土内的小气泡数量,改善混凝土的抗冻和抗渗性能。
增强剂主要改善混凝土的力学性能,使其具有更高的抗压强度和抗拉强度。
缓凝剂可延缓混凝土的凝结过程,方便混凝土的施工和制作。
防水剂能使混凝土表面形成一层防水保护层,延长混凝土的使用寿命。
目前,混凝土外加剂的应用已经相当广泛,被应用于大多数混凝土结构中,如公路、桥梁、洞渠、楼房、水利、地下工程等。
然而,在混凝土外加剂的研究和应用中也存在一些问题。
首先是产品质量参差不齐,市场上很多小型厂家生产的混凝土外加剂质量无法得到保证,往往存在使用效果不明显、出现质量问题等情况。
其次是不良的应用实践,有些施工方不注重施工效果,没有按照适当的配比和使用方法使用外加剂,导致混凝土强度不达标。
此外,外加剂与混凝土本质上存在化学反应,而在实际应用中有些厂家没有对混凝土本身的化学性质进行充分了解,这也是潜在的问题。
面对这些问题,需要加强对混凝土外加剂的质量监管,让市场上产品质量得到保证,同时,应加强对施工方的培训和管理,提高工程施工质量。
另外,研究人员需要加强对混凝土本身特性的了解,深入研究外加剂与混凝土反应机理,为混凝土外加剂的研发和应用提供更加科学的理论依据。
混凝土外加剂研究和应用现状及存在的几个问题
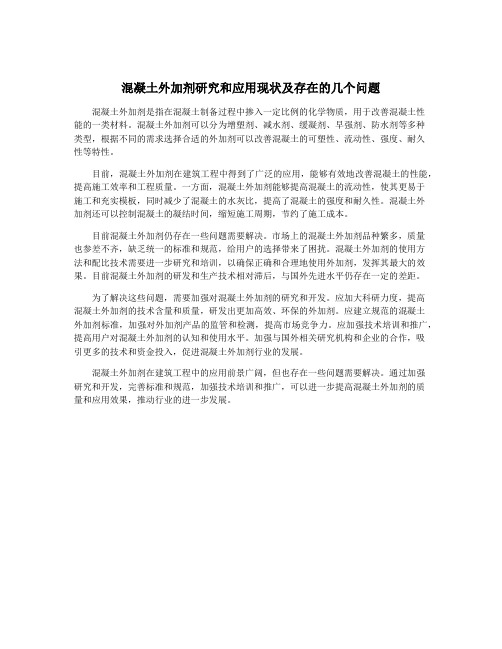
混凝土外加剂研究和应用现状及存在的几个问题混凝土外加剂是指在混凝土制备过程中掺入一定比例的化学物质,用于改善混凝土性能的一类材料。
混凝土外加剂可以分为增塑剂、减水剂、缓凝剂、早强剂、防水剂等多种类型,根据不同的需求选择合适的外加剂可以改善混凝土的可塑性、流动性、强度、耐久性等特性。
目前,混凝土外加剂在建筑工程中得到了广泛的应用,能够有效地改善混凝土的性能,提高施工效率和工程质量。
一方面,混凝土外加剂能够提高混凝土的流动性,使其更易于施工和充实模板,同时减少了混凝土的水灰比,提高了混凝土的强度和耐久性。
混凝土外加剂还可以控制混凝土的凝结时间,缩短施工周期,节约了施工成本。
目前混凝土外加剂仍存在一些问题需要解决。
市场上的混凝土外加剂品种繁多,质量也参差不齐,缺乏统一的标准和规范,给用户的选择带来了困扰。
混凝土外加剂的使用方法和配比技术需要进一步研究和培训,以确保正确和合理地使用外加剂,发挥其最大的效果。
目前混凝土外加剂的研发和生产技术相对滞后,与国外先进水平仍存在一定的差距。
为了解决这些问题,需要加强对混凝土外加剂的研究和开发。
应加大科研力度,提高混凝土外加剂的技术含量和质量,研发出更加高效、环保的外加剂。
应建立规范的混凝土外加剂标准,加强对外加剂产品的监管和检测,提高市场竞争力。
应加强技术培训和推广,提高用户对混凝土外加剂的认知和使用水平。
加强与国外相关研究机构和企业的合作,吸引更多的技术和资金投入,促进混凝土外加剂行业的发展。
混凝土外加剂在建筑工程中的应用前景广阔,但也存在一些问题需要解决。
通过加强研究和开发,完善标准和规范,加强技术培训和推广,可以进一步提高混凝土外加剂的质量和应用效果,推动行业的进一步发展。
混凝土中碱激发剂的作用机理及其应用

混凝土中碱激发剂的作用机理及其应用一、引言混凝土作为一种常用的建筑材料,其强度和耐久性是其优点之一。
然而,在特定环境下,混凝土可能会出现碱硅反应(ASR),导致混凝土结构的破坏。
为了解决这一问题,研究人员提出了使用碱激发剂的方法来减轻ASR的影响。
本文将介绍混凝土中碱激发剂的作用机理及其应用。
二、碱硅反应的机理碱硅反应(ASR)是混凝土中一种常见的化学反应,它是水泥中含有的碱性化合物与混凝土中的反应性硅酸盐矿物质产生的一种反应。
该反应会产生氢氧化钠(NaOH),这会通过混凝土中的孔隙向外扩散,与大气中的二氧化碳反应,形成碳酸钠(Na2CO3)。
这种反应会导致混凝土中的体积膨胀,从而引起开裂,最终导致混凝土结构的破坏。
三、碱激发剂的作用机理为了减轻ASR的影响,研究人员提出了使用碱激发剂的方法。
碱激发剂是一种添加剂,可用于减少混凝土中的ASR反应。
其主要作用机理(1)促进反应。
碱激发剂可以促进水泥中的碱性化合物与反应性硅酸盐矿物质之间的反应,从而消耗水泥中的碱性化合物,减少ASR反应的发生。
(2)保护反应。
碱激发剂可以形成一层保护膜,覆盖在反应性硅酸盐矿物质表面,从而防止水泥中的碱性化合物与反应性硅酸盐矿物质之间的反应,减少ASR反应的发生。
四、碱激发剂的应用碱激发剂是混凝土中常用的添加剂之一,其应用主要有以下几个方面:(1)混凝土结构中的防护。
碱激发剂可以降低混凝土中的ASR反应,并增强混凝土结构的耐久性。
(2)混凝土中的节能环保。
碱激发剂可以减少混凝土中的水泥用量,从而减少混凝土对环境的影响。
(3)混凝土中的强度和性能改善。
碱激发剂可以提高混凝土的强度和性能,从而提高混凝土的使用寿命。
在混凝土结构中,ASR反应是一种常见的问题。
为了解决这一问题,研究人员提出了使用碱激发剂的方法。
碱激发剂可以减少ASR反应的发生,从而降低混凝土结构的破坏风险,并提高混凝土的使用寿命。
此外,碱激发剂还可以减少混凝土对环境的影响,从而实现节能环保的目的。
化学激发剂对铜渣及铜渣水泥激发作用的研究
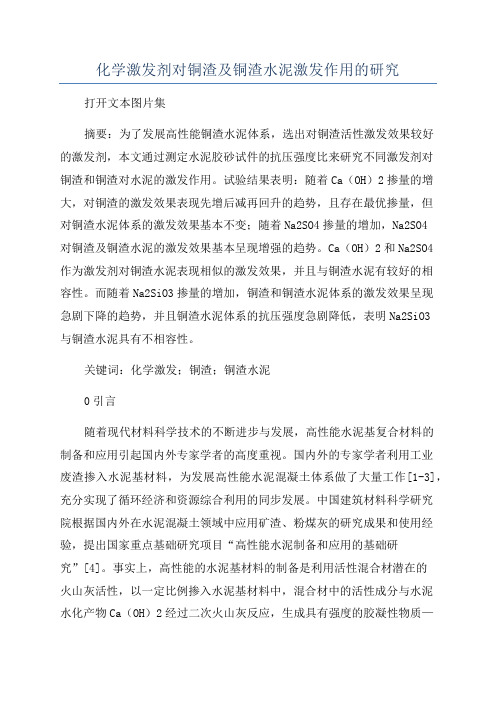
化学激发剂对铜渣及铜渣水泥激发作用的研究打开文本图片集摘要:为了发展高性能铜渣水泥体系,选出对铜渣活性激发效果较好的激发剂,本文通过测定水泥胶砂试件的抗压强度比来研究不同激发剂对铜渣和铜渣对水泥的激发作用。
试验结果表明:随着Ca(OH)2掺量的增大,对铜渣的激发效果表现先增后减再回升的趋势,且存在最优掺量,但对铜渣水泥体系的激发效果基本不变;随着Na2SO4掺量的增加,Na2SO4对铜渣及铜渣水泥的激发效果基本呈现增强的趋势。
Ca(OH)2和Na2SO4作为激发剂对铜渣水泥表现相似的激发效果,并且与铜渣水泥有较好的相容性。
而随着Na2SiO3掺量的增加,铜渣和铜渣水泥体系的激发效果呈现急剧下降的趋势,并且铜渣水泥体系的抗压强度急剧降低,表明Na2SiO3与铜渣水泥具有不相容性。
关键词:化学激发;铜渣;铜渣水泥0引言随着现代材料科学技术的不断进步与发展,高性能水泥基复合材料的制备和应用引起国内外专家学者的高度重视。
国内外的专家学者利用工业废渣掺入水泥基材料,为发展高性能水泥混凝土体系做了大量工作[1-3],充分实现了循环经济和资源综合利用的同步发展。
中国建筑材料科学研究院根据国内外在水泥混凝土领域中应用矿渣、粉煤灰的研究成果和使用经验,提出国家重点基础研究项目“高性能水泥制备和应用的基础研究”[4]。
事实上,高性能的水泥基材料的制备是利用活性混合材潜在的火山灰活性,以一定比例掺入水泥基材料中,混合材中的活性成分与水泥水化产物Ca(OH)2经过二次火山灰反应,生成具有强度的胶凝性物质—水化硅酸钙(C-S-H凝胶)来改善水泥基材料的力学性能,对提高水泥基材料的耐久性具有重要意义。
水泥工业通过将水泥熟料与活性混合材二者以一定比例混合,改变水泥熟料中的矿物组成,从而生产出强度和耐久性二者兼优的高性能水泥体系。
因此,高性能水泥体系能否获得,一定程度上取决于混合材所表现的活性高低。
其中,化学激发剂对活性混合材潜在活性的提升有极其关键的作用[5-6]。
水泥激发剂原料及配方

水泥激发剂原料及配方下载温馨提示:该文档是我店铺精心编制而成,希望大家下载以后,能够帮助大家解决实际的问题。
文档下载后可定制随意修改,请根据实际需要进行相应的调整和使用,谢谢!并且,本店铺为大家提供各种各样类型的实用资料,如教育随笔、日记赏析、句子摘抄、古诗大全、经典美文、话题作文、工作总结、词语解析、文案摘录、其他资料等等,如想了解不同资料格式和写法,敬请关注!Download tips: This document is carefully compiled by the editor. I hope that after you download them, they can help yousolve practical problems. The document can be customized and modified after downloading, please adjust and use it according to actual needs, thank you!In addition, our shop provides you with various types of practical materials, such as educational essays, diary appreciation, sentence excerpts, ancient poems, classic articles, topic composition, work summary, word parsing, copy excerpts,other materials and so on, want to know different data formats and writing methods, please pay attention!水泥激发剂是一种能够提高水泥活性和促进水泥硬化的添加剂。
- 1、下载文档前请自行甄别文档内容的完整性,平台不提供额外的编辑、内容补充、找答案等附加服务。
- 2、"仅部分预览"的文档,不可在线预览部分如存在完整性等问题,可反馈申请退款(可完整预览的文档不适用该条件!)。
- 3、如文档侵犯您的权益,请联系客服反馈,我们会尽快为您处理(人工客服工作时间:9:00-18:30)。
1概述随着产业结构的调整,部分立窑水泥厂家被改造为水泥粉磨站,为节约能源,减少环境污染起到了重要的作用。
水渣和粉煤灰作为矿物掺和料在混凝土行业已经大量使用,使水渣和粉煤灰的价格逐年提高。
研制具有助磨、增强功能的水泥工艺外加剂(本文称之为水泥激发剂),节约熟料,降低水泥生产成本,已经成为水泥行业发展的一个重要课题。
大多数水泥厂已经尝试使用水泥激发剂,但存在的问题仍然很多。
正是在这种条件下,我们对水泥激发剂的应用状况进行了深入细致的研究,总结水泥激发剂使用过程中经常出现的问题,并分析其产生原因,提出对应的解决办法。
2水泥激发剂的功能2.1激发剂的成分水泥激发剂主要具有助磨、增强两种功能。
具有助磨功能的原材料包括:胺类、醇类、醇胺类、木质素磺酸盐类、脂肪酸及其盐类、烷基磺酸盐类等。
具有增强功能的包括:卤盐类、硫酸盐类、铝酸盐类、减水剂类等。
2.2激发剂的功能使用水泥激发剂,助磨组分可以提高水泥磨机的粉磨效率15%左右,降低水泥粉磨电耗;增强组分能有效地激发混合材的活性、提高混合材在水泥中的掺量10—25%,从而有效地降低水泥的生产成本;混合材的大量掺入同时可以改善水泥的安定性、降低水泥的水化放热。
2.3激发剂增强机理在生产过程中使用水泥激发剂,其增强机理主要有以下几个方面:(1)助磨增强机理激发剂是很好的分散剂,在水泥生产过程中,由于原料颗粒都存在结构缺陷和微裂纹,助磨组分如同楔子一样进入缺陷和微裂纹部位,在原料内部形成强大的膨胀应力,当磨机运转时,研磨体撞击和挤压这些原料颗粒,由于内外应力的共同作用,使原材料更加容易磨细,起到了助磨的作用。
使水泥的比表面积增大,颗粒级配更加合理,水泥水化反应的接触点增多,大大提高了水泥强度。
(2)晶种成长增强机理激发剂组分的分子晶体结构中存在各种类似于水泥石的晶种,在水泥水化过程中,由于固相反应生成的固溶胶结构与晶种相似,它们互相溶解、分散吸收了大量中间产物及自由水,减少了溶胶颗粒的离散性及自由水蒸发引起的空隙、孔洞及结构缺陷,使整个水泥石内部更加密实、均匀、连续,提高了强度。
(3)交互作用增强机理采用熟料、混合材、石膏和激发剂生产水泥,任意两种材料之间,在水化时都能相互激发,相互反应,形成大量的柱状钙矾石,层片状Ca(OH)2晶体以及网状、纤维状的水化CSH 凝胶.这些产物彼此填充,互相缠绕,将水泥石牢固地粘结成一个整体,组成一座含有大量凝胶孔的密实大厦,同时各组分晶格在逐步水化时还能沿不同方向增长,有效的补偿了不够密实的部位,减少了单一组分水化不能弥补的缺陷,产生叠加效应,使水泥强度大大提高。
(4)减水增强机理有的水泥激发剂含有减水剂成分,经过粉磨制得的水泥,在进行胶砂试验时,由于减水和分散作用,使水泥浆体拌和得更加均匀,超细粉微集料填充效应跟加充分,相同水胶比条件下制得的试件更加密实,强度提高。
3水泥激发剂使用过程常见问题在实际应用过程中,大多数激发剂都没有达到试验室测试时的效果。
液体助磨剂小磨试验对比效果特别明显;在工业化中试生产时,采用微型计量泵计量,可以提高产量15%左右,28天强度增加2MPa左右。
实际生产一段时间后,水泥厂普遍反映产量没有提高,生产时停用了助磨剂,导致液体助磨剂大量堆放于库房内。
此时又更换其它厂家的产品进行生产,结果均大同小异。
这种现象在我国南方的水泥厂经常发生,而北方的水泥厂出现这种情况大多在春夏之交。
粉体的助磨剂小磨对比试验效果较好。
工业化大磨中试生产时,可以提高产量15%,节约熟料5%,28天强度增加3MPa。
实际生产一段时间后,水泥厂普遍反映水泥质量波动大,水泥质量时好时坏,严重影响水泥的正常使用,迫不得已在生产时停用了助磨剂。
更换不同厂家的产品仍然出现这种问题,这种现象在全国各地普遍存在。
复合激发剂小磨试验效果很好。
在工业化试生产时,试验不顺利的情况,激发剂加入后磨机房及其周围的环境粉尘迷漫,采用浮选工艺时水泥比表面积没有变化,选粉机经常出现堵塞;采用开路工艺时水泥比表面积增大,两小时后由于斗式提升机故障停止了试验;试验顺利的情况,可以提高产量15%,混合材掺量增加10—25%,28天强度增加5—7MPa。
但是水泥正常生产过程也会出现质量事故,由于没有弄明白造成质量事故的原因,在生产时停止了激发剂的使用,这种现象在国内的水泥厂都普遍存在。
4常见问题产生原因及解决办法4.1问题产生的原因4.1.1 助磨组分挥发针对液体助磨剂、粉体助磨剂、复合激发剂在工业化生产时出现的问题,我们进行了详细调察和深入研究,发现在小磨试验时由于熟料、矿渣、石膏和粉煤灰等在掺加激发剂后形成一个封闭的空间,助磨组分均匀地分散到原料颗粒表面,像木块端头放了一个楔子,在钢球钢锻的作用下,快速扩散,改变了颗粒表面的结构性质,降低了原料颗粒的强度和硬度,同时加速了新裂纹的产生以及物料自身裂缝的扩展,使水泥原材料更容易粉磨,且成品颗粒级配更加合理。
提高了水泥的台时产量,扩大了水泥颗粒的比表面积,水泥强度增加。
在工业化试生产时,熟料、矿渣、石膏、粉煤灰和助磨剂处于常温状态。
中试生产时加入助磨剂,由于配备了小型计量泵,计量准确,助磨剂能够充分发挥作用,助磨和增强效果明显。
生产一段时间后,虽然助磨剂产品质量稳定,计量和配料也显示为正常,常温熟料已经用完,经常出现高温的熟料刚从篦式冷却机出来,就被直接送到磨机进行粉磨。
易挥发的助磨组分由于接触高温的熟料而快速蒸发,这些蒸汽在选粉机的抽力作用下,没有被原材料吸附到固体颗粒表面而直接进入大气中,没有起到助磨作用,水泥的产量没有增加。
因此在水泥生产时停用了助磨剂,导致助磨剂大量堆放于库房内,这是目前水泥助磨剂使用过程中最常见问题产生的真正原因。
无论液体、粉体还是复合激发剂,只要含有挥发性的助磨组分,在大批量的工业化生产过程中均存在这一问题。
南方地区水泥原材料的温度普遍偏高,特别是水泥熟料温度降不下来,进行工业化大磨试验后短时间内就出现这种情况;北方地区由于四季温度变化大,秋冬季节进行工业化大磨试验时由于熟料和其他原材料温度较低,助磨组分的挥发不明显,到了春夏之交气温升高时,由于熟料温度没有降低就开始使用,助磨组分的挥发非常快,最终出现上述问题。
虽然外加剂厂生产的激发剂质量确实没有发生变化,由于助磨组分的挥发,水泥厂使用激发剂后没有达到提高产量的目的。
4.1.2 掺量过低(1)液体助磨剂使用液体助磨剂生产水泥时质量不稳定,主要原因是掺量太低导致计量误差偏大引起的。
在水泥厂生产时按班次将助磨剂定量储存于原料罐里,采用计量泵根据时间确定配料量。
液体助磨剂粘度受温度的影响较大,当环境温度较高时粘度较低,流动阻力变小,流速变快,在相同的时间范围内,由于流速快引起掺量偏高,后期生产的水泥由于助磨剂用完而没有掺加助磨剂,导致生产的水泥质量不稳定。
当环境温度较低时,液体助磨剂的粘度增大,流动阻力变大,流速变慢,在相同的时间范围内,由于流速变慢导致助磨剂的掺量偏低,助磨效果不明显。
特别是计量泵出料口周围始终处于粉尘环境中,由于助磨剂流速较慢,粉尘在出口部位逐渐粘结聚集,最后堵塞了出料口,阻断了助磨剂的配料,水泥生产中没有助磨剂,由于操作工人的疏忽好长时间都没有发现,水泥出现质量事故。
这是液体水泥助磨剂在水泥生产过程中表现质量不稳定的一个重要原因。
例如:液体助磨剂掺量0.05%,对20t/h的磨机,每小时只需10kg,粉体助磨剂配料控制量166g/min,而计量秤的控制误差为0.5kg/min,当计量秤处于正误差时,超过正常掺量3倍以上,当计量秤处于负误差时,助磨剂几乎没有掺加,水泥质量波动特别明显。
综上所述,粘度大以及计量误差大是是液体助磨剂使用过程中出现的通病,在水泥企业普遍存在,严重影响水泥质量的稳定。
(2)粉体助磨剂粉体助磨剂使用效果良好和出现问题的原因可以分为两种情况。
一种为含有低沸点挥发成分,其使用效果及问题同液体助磨剂相同;另一种为含有非挥发性助磨组分,在工业化生产时,有专用计量秤,在工业化试生产中助磨和增强效果相当理想。
实际生产一段时间后,虽然助磨剂产品质量稳定,计量和配料系统显示正常,但水泥助磨剂的助磨效果和增强效果均出现很大的波动。
经现场调研、大量研究和分析可知,当粉体助磨剂掺量较小时,由于含有醇胺等有机组分的粉体助磨剂比较潮湿,含松香和减水剂等组分的粉体助磨剂颗粒比较粗,经常出现粉体料粘罐和起拱蓬料的现象,虽然计量秤显示平均配料比例正常,但粉体助磨剂的实际配料比例极其不稳定,导致水泥质量剧烈波动;另一方面计量误差偏大是引起助磨和增强效果波动的另一个重要原因。
例如:对20t/h的磨机,木钙推荐掺量为0.1%,每小时需要20kg,配料控制速度由333g/min,而计量秤的误差为0.5kg/min,当计量秤处于正误差时,粉体助磨剂对应掺量为正常控制量的2.5倍,当计量秤处于负误差时,助磨剂对应掺量为0,计量几乎没有发挥作用。
综上所述,粉料潮湿以及计量误差偏大是粉体助磨剂使用过程中常见的问题,在水泥企业普遍存在,是粉体助磨剂应用过程中的一个巨大障碍。
4.1.3工业化生产设备不配套无论液体、粉体还是复合激发剂,对于小磨试验效果较好的产品,在不同厂家进行工业化大磨试验时,都出现过掺加外加剂后磨机房环境粉尘迷漫、选粉机中途堵塞、皮带断裂以及斗式提升机突然停转等问题。
从表面现象看,掺加激发剂后生产既没有提高产量又没有提高产品的比表面积,设备故障是工业化中试停止的原因。
经过认真研究,我们认为中试设备的不匹配是造成这一问题出现的关键。
工业化中试生产开始时,由于激发剂的加入,原材料得到了充分的粉磨,水泥比表面积增大,形成大量的悬浮物漂流到空气中,使磨机房及周围的环境粉尘飞扬;采用选粉工艺时,达到一定颗粒级配的水泥粉料均被选出,由于选粉机的抽力是固定的,选出的水泥比表面积没有增大或者增加很少,但由于助磨效果明显,选粉机选出的水泥产量快速增加,超过选粉机设计能力,导致选粉机被堵塞;在此期间,斗式提升机的提升能力也没有调整,导致电机过载停机或皮带超负荷断裂,迫使工业化中试停止。
在工业化中试的过程中,生产设备能力的欠缺是使用激发剂生产水泥过程出现故障的重要原因。
4.2解决办法4.2.1助磨组分挥发问题的解决助磨组分在高温下容易挥发问题的解决,建议在液体助磨剂、粉体助磨剂以及复合激发剂的配制过程中多选用沸点较高的助磨剂成分、避免选择易挥发组分。
在选材方面充分利用原材料的高沸点性能,实现较高温度的水泥熟料与助磨剂混合后能相互吸附,不产生挥发的现象,在水泥生产中充分发挥助磨剂的作用。
4.2.2掺量过低问题的解决(1)液体助磨剂关于液体助磨剂粘结堵塞计量泵出料口导致水泥生产质量剧烈波动问题的解决,建议采用粘度受温度影响较小的低粘度助磨组分配制液体助磨剂;如果选用粘度较大的材料,建议采用较大量的溶剂将液体助磨剂稀释,有效降低液体助磨剂的粘度。