第9章 吹塑模具设计-10.
多口瓶吹塑模具设计方案
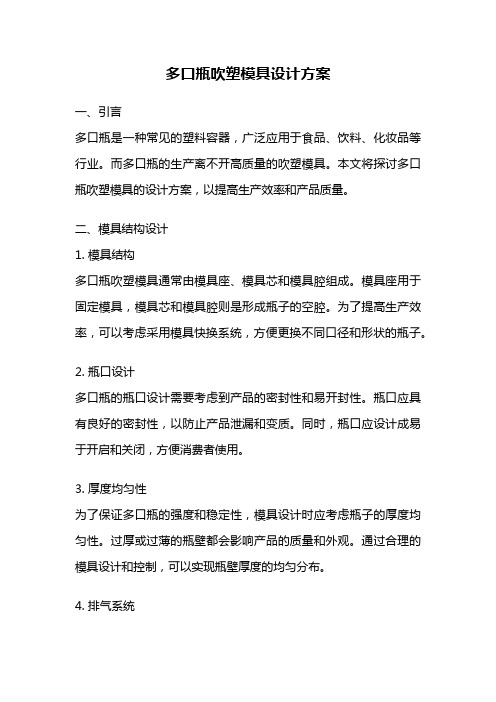
多口瓶吹塑模具设计方案一、引言多口瓶是一种常见的塑料容器,广泛应用于食品、饮料、化妆品等行业。
而多口瓶的生产离不开高质量的吹塑模具。
本文将探讨多口瓶吹塑模具的设计方案,以提高生产效率和产品质量。
二、模具结构设计1. 模具结构多口瓶吹塑模具通常由模具座、模具芯和模具腔组成。
模具座用于固定模具,模具芯和模具腔则是形成瓶子的空腔。
为了提高生产效率,可以考虑采用模具快换系统,方便更换不同口径和形状的瓶子。
2. 瓶口设计多口瓶的瓶口设计需要考虑到产品的密封性和易开封性。
瓶口应具有良好的密封性,以防止产品泄漏和变质。
同时,瓶口应设计成易于开启和关闭,方便消费者使用。
3. 厚度均匀性为了保证多口瓶的强度和稳定性,模具设计时应考虑瓶子的厚度均匀性。
过厚或过薄的瓶壁都会影响产品的质量和外观。
通过合理的模具设计和控制,可以实现瓶壁厚度的均匀分布。
4. 排气系统多口瓶在吹塑过程中,需要通过排气系统排出模具腔内的空气,以避免瓶子出现气泡和瑕疵。
因此,模具设计时应合理设置排气系统,确保充分排出空气,从而得到高质量的产品。
三、材料选择1. 塑料材料多口瓶通常采用聚乙烯(PE)、聚丙烯(PP)等塑料材料制成。
不同的塑料材料具有不同的特性和适用范围,因此在模具设计时需要根据产品的具体要求选择合适的材料。
2. 模具材料多口瓶吹塑模具通常采用优质的耐磨合金钢制成,以保证模具的耐用性和精度。
模具材料的选择应考虑到模具的使用寿命、生产效率和成本等因素,以达到性价比最优化。
四、模具生产工艺1. 模具加工多口瓶吹塑模具的加工需要采用精密的数控机床和先进的加工工艺,以确保模具的精度和质量。
模具加工过程中需要严格控制尺寸和表面光洁度,以满足产品的要求。
2. 热流道系统为了提高多口瓶的生产效率和减少废品率,可以考虑采用热流道系统。
热流道系统可以使塑料材料在模具腔内均匀流动,减少冷料的产生,从而提高产品的质量和产量。
3. 模具调试模具生产完成后,需要进行模具调试。
塑料挤出模具设计
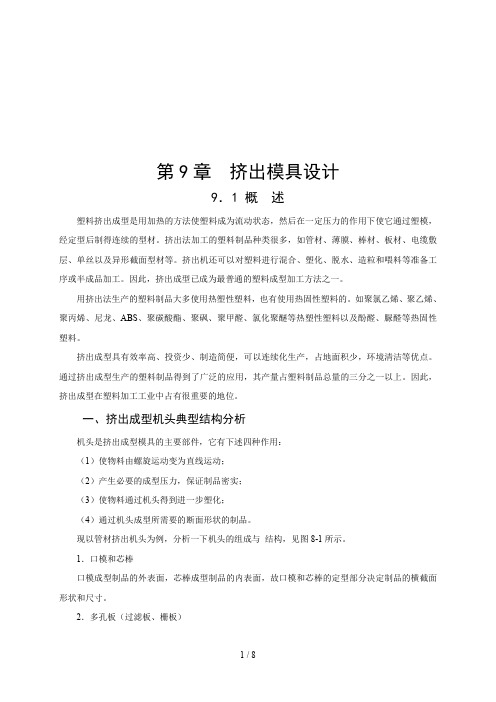
第9章挤出模具设计9.1 概述塑料挤出成型是用加热的方法使塑料成为流动状态,然后在一定压力的作用下使它通过塑模,经定型后制得连续的型材。
挤出法加工的塑料制品种类很多,如管材、薄膜、棒材、板材、电缆敷层、单丝以及异形截面型材等。
挤出机还可以对塑料进行混合、塑化、脱水、造粒和喂料等准备工序或半成品加工。
因此,挤出成型已成为最普通的塑料成型加工方法之一。
用挤出法生产的塑料制品大多使用热塑性塑料,也有使用热固性塑料的。
如聚氯乙烯、聚乙烯、聚丙烯、尼龙、ABS、聚碳酸酯、聚砜、聚甲醛、氯化聚醚等热塑性塑料以及酚醛、脲醛等热固性塑料。
挤出成型具有效率高、投资少、制造简便,可以连续化生产,占地面积少,环境清洁等优点。
通过挤出成型生产的塑料制品得到了广泛的应用,其产量占塑料制品总量的三分之一以上。
因此,挤出成型在塑料加工工业中占有很重要的地位。
一、挤出成型机头典型结构分析机头是挤出成型模具的主要部件,它有下述四种作用:(1)使物料由螺旋运动变为直线运动;(2)产生必要的成型压力,保证制品密实;(3)使物料通过机头得到进一步塑化;(4)通过机头成型所需要的断面形状的制品。
现以管材挤出机头为例,分析一下机头的组成与结构,见图8-1所示。
1.口模和芯棒口模成型制品的外表面,芯棒成型制品的内表面,故口模和芯棒的定型部分决定制品的横截面形状和尺寸。
2.多孔板(过滤板、栅板)如图8-2所示,多孔板的作用是将物料由螺旋运动变为直线运动,同时还能阻止未塑化的塑料和机械杂质进入机头。
此外,多孔板还能形成一定的机头压力,使制品更加密实。
3.分流器和分流器支架分流器又叫鱼雷头。
塑料通过分流器变成薄环状,便于进一步加热和塑化。
大型挤出机的分流器内部还装有加热装置。
分流器支架主要用来支撑分流器和芯棒,同时也使料流分束以加强搅拌作用。
小型机头的分流器支架可与分流器设计成整体。
4.调节螺钉用来调节口模与芯棒之间的间隙,保证制品壁厚均匀。
5.机头体用来组装机头各零件及挤出机连接。
高分子材料成型加工中的吹塑模具设计与制造

高分子材料成型加工中的吹塑模具设计与制造在高分子材料的成型加工过程中,吹塑模具是至关重要的环节。
吹塑模具的设计与制造直接影响到成型制品的质量和生产效率。
本文将就高分子材料成型加工中吹塑模具的设计与制造进行探讨。
一、吹塑模具的设计吹塑模具的设计包括模具结构设计和模具零部件的设计两个方面。
模具结构设计是指确定模具整体结构的尺寸和形状,包括模具的内腔结构和外部支撑结构等。
模具零部件的设计则是指各个零部件的尺寸和形状设计,包括吹气头、挤出口等。
在吹塑模具的设计过程中,需要考虑各种因素的影响,如材料的选择、制品的形状和尺寸、生产效率等。
合理的模具设计可以降低生产成本,提高生产效率,提高产品质量。
二、吹塑模具的制造吹塑模具的制造是指根据设计图纸制作出实际可用的模具。
吹塑模具的制造一般包括以下步骤:选材、粗加工、精密加工、组装和调试。
选材是指选择合适的模具材料,通常吹塑模具的制造材料选择优质的合金钢或不锈钢。
粗加工是指直接利用加工中心、数控车床等设备对模具进行初步加工,制作出初步的模具形状。
精密加工是指进一步对模具进行精细加工,保证模具的尺寸精度和表面光洁度。
组装和调试是指将各个零部件组装在一起,并进行试模调试,确保模具的正常使用。
三、吹塑模具的维护与保养吹塑模具在使用过程中需要进行定期的维护与保养,以延长模具的使用寿命,保持模具的精度和表面质量。
维护与保养工作包括清洁、润滑、检查、磨削等。
清洁是指定期清洗模具内腔和外表面,避免杂质的积聚和腐蚀。
润滑是指在适当部位添加润滑剂,减少摩擦,延长模具使用寿命。
检查是指定期进行模具的尺寸检查、表面质量检查等,及时发现问题并采取措施。
磨削是指定期对模具进行表面磨削,消除磨损,恢复表面精度和光洁度。
四、吹塑模具的发展趋势随着科技的发展和工业的进步,吹塑模具的设计与制造技术不断地创新和进步。
未来吹塑模具的发展趋势主要有以下几个方面:1. 自动化:吹塑模具将更多地向自动化和数字化方向发展,提高生产效率和质量稳定性。
吹塑成型模具
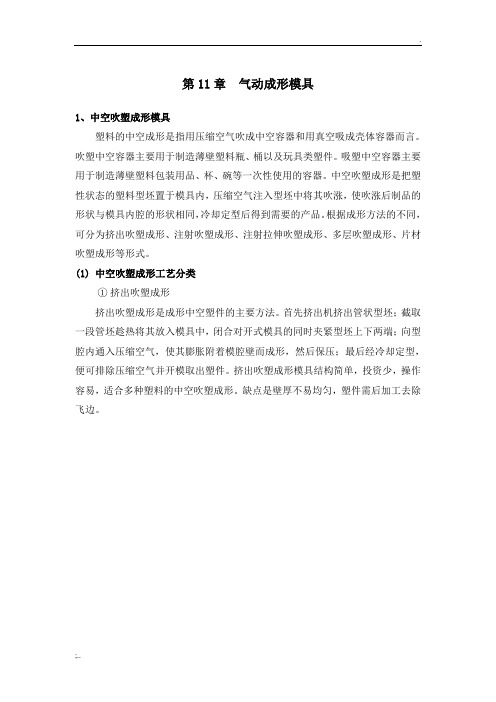
第11章气动成形模具1、中空吹塑成形模具塑料的中空成形是指用压缩空气吹成中空容器和用真空吸成壳体容器而言。
吹塑中空容器主要用于制造薄壁塑料瓶、桶以及玩具类塑件。
吸塑中空容器主要用于制造薄壁塑料包装用品、杯、碗等一次性使用的容器。
中空吹塑成形是把塑性状态的塑料型坯置于模具内,压缩空气注入型坯中将其吹涨,使吹涨后制品的形状与模具内腔的形状相同,冷却定型后得到需要的产品。
根据成形方法的不同,可分为挤出吹塑成形、注射吹塑成形、注射拉伸吹塑成形、多层吹塑成形、片材吹塑成形等形式。
(1) 中空吹塑成形工艺分类①挤出吹塑成形挤出吹塑成形是成形中空塑件的主要方法。
首先挤出机挤出管状型坯;截取一段管坯趁热将其放入模具中,闭合对开式模具的同时夹紧型坯上下两端;向型腔内通入压缩空气,使其膨胀附着模腔壁而成形,然后保压;最后经冷却定型,便可排除压缩空气并开模取出塑件。
挤出吹塑成形模具结构简单,投资少,操作容易,适合多种塑料的中空吹塑成形。
缺点是壁厚不易均匀,塑件需后加工去除飞边。
图11-1挤出吹塑成型1-挤出机头;2-吹塑模;3-管状型坯;4-压缩空气管;5-塑件②注射吹塑成形注射吹塑成形是用注射机在注射模中制成型坯,然后把热型坯移入中空吹塑模具中进行中空吹塑。
首先注射机在注射模中注入熔融塑料制成型坯;型芯与型坯一起移入吹塑模内,型芯为空心并且壁上带有孔;从芯棒的管道内通入压缩空气,使型坯吹涨并贴于模具的型腔壁上;保压、冷却定型后放出压缩空气,并且开模取出塑件。
经过注射吹塑成形的塑件壁厚均匀,无飞边,不需后加工,由干注射型坯有底,因此底部没有拼和缝,强度高,生产效率高,但是设备与模具的价格昂贵,多用于小型塑件的大批量生产。
图11-2注射吹塑成型1-注塑机喷嘴;2-注塑型坯;3-空心凸模;4-加热器;5-吹塑模;6-塑件③注射拉伸吹塑成形图11-3 注射拉伸吹塑成型1-注塑机喷嘴;2-注塑模;3-拉伸芯棒(吹管);4-吹塑膜具;5-塑件注射拉伸吹塑成形与注射吹塑成形比较,增加了延伸这一工序。
2024-中空吹塑模具设计
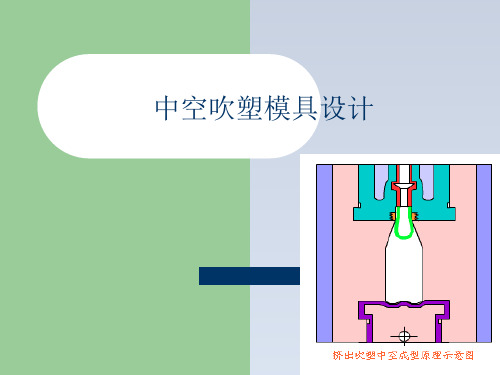
中空吹塑模具设计
2、余料槽 余料槽应跟据夹持后的余料宽度、厚度确定。
中空吹塑模具设计
3、排气孔〔排气槽〕 排气孔:φ0.5~φ1; 排气槽:〈 0.05mm。
4、冷却 均匀冷却。
中空吹塑模具设计
5、吹管
W t BR
W:口模厚度; t : 塑件壁厚; BR :吹胀比;
:修正系数,常取1 ~ 1.5。
中空吹塑模具设计
2、延伸比:
塑件的长度与型坯之比,SR。 为保证制品的强度、壁厚,一般SR× BR = 4 ~ 6。
中空吹塑模具设计
3、制品的斜度:
一般原那么,最 小斜度:1°/边; 推荐斜度:2 °/ 边。
中空吹塑模具设计
横向、纵向收缩率的相较:
纵向 横向
聚乙烯 2.1±0.1 1.9±0.2
聚氯乙烯 0.36±0.04 0.13±0.05
中空吹塑模具设计
三、模具设计〔以挤出吹塑为例〕 1、夹坯口
1、夹坯口
1、夹坯口
hmin=0.38 通常:0.51~2.5mm; 大型容器:2~3mm。 〔美〕Norman C.Lee ?吹塑成型技术 ?
中空吹塑模具设计
中空吹塑模具设计
1、教学目的与要求 学习掌握中空吹塑模具的结构与设计要求。
中空吹塑模具设计
一、分类 1、挤出吹塑
1、挤出吹塑
1、挤出吹塑
中空吹塑模具设计
2、注射吹塑
中空吹塑模具设计
3、延伸吹塑设计
二、中空制品的塑件设计
1、吹胀比: 塑件的最大直径与型坯直径之比,BR。 BR = 2:1 ~ 4:1 如是挤出吹塑可由吹胀比确定挤出口模的尺寸:
中空吹塑模具设计
4、圆角:
吹塑模具的设计
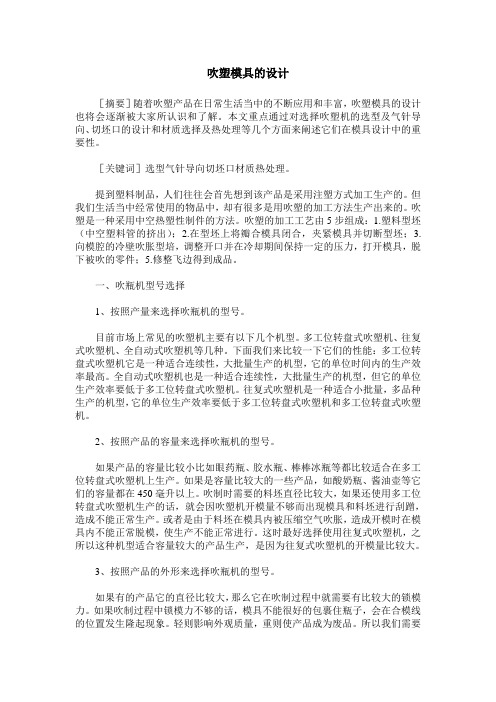
吹塑模具的设计[摘要]随着吹塑产品在日常生活当中的不断应用和丰富,吹塑模具的设计也将会逐渐被大家所认识和了解。
本文重点通过对选择吹塑机的选型及气针导向、切坯口的设计和材质选择及热处理等几个方面来阐述它们在模具设计中的重要性。
[关键词]选型气针导向切坯口材质热处理。
提到塑料制品,人们往往会首先想到该产品是采用注塑方式加工生产的。
但我们生活当中经常使用的物品中,却有很多是用吹塑的加工方法生产出来的。
吹塑是一种采用中空热塑性制件的方法。
吹塑的加工工艺由5步组成:1.塑料型坯(中空塑料管的挤出);2.在型坯上将瓣合模具闭合,夹紧模具并切断型坯;3.向模腔的冷壁吹胀型培,调整开口并在冷却期间保持一定的压力,打开模具,脱下被吹的零件;5.修整飞边得到成品。
一、吹瓶机型号选择1、按照产量来选择吹瓶机的型号。
目前市场上常见的吹塑机主要有以下几个机型。
多工位转盘式吹塑机、往复式吹塑机、全自动式吹塑机等几种。
下面我们来比较一下它们的性能:多工位转盘式吹塑机它是一种适合连续性,大批量生产的机型,它的单位时间内的生产效率最高。
全自动式吹塑机也是一种适合连续性,大批量生产的机型,但它的单位生产效率要低于多工位转盘式吹塑机。
往复式吹塑机是一种适合小批量,多品种生产的机型,它的单位生产效率要低于多工位转盘式吹塑机和多工位转盘式吹塑机。
2、按照产品的容量来选择吹瓶机的型号。
如果产品的容量比较小比如眼药瓶、胶水瓶、棒棒冰瓶等都比较适合在多工位转盘式吹塑机上生产。
如果是容量比较大的一些产品,如酸奶瓶、酱油壶等它们的容量都在450毫升以上。
吹制时需要的料坯直径比较大,如果还使用多工位转盘式吹塑机生产的话,就会因吹塑机开模量不够而出现模具和料坯进行刮蹭,造成不能正常生产。
或者是由于料坯在模具内被压缩空气吹胀,造成开模时在模具内不能正常脱模,使生产不能正常进行。
这时最好选择使用往复式吹塑机,之所以这种机型适合容量较大的产品生产,是因为往复式吹塑机的开模量比较大。
吹塑模具设计与加工
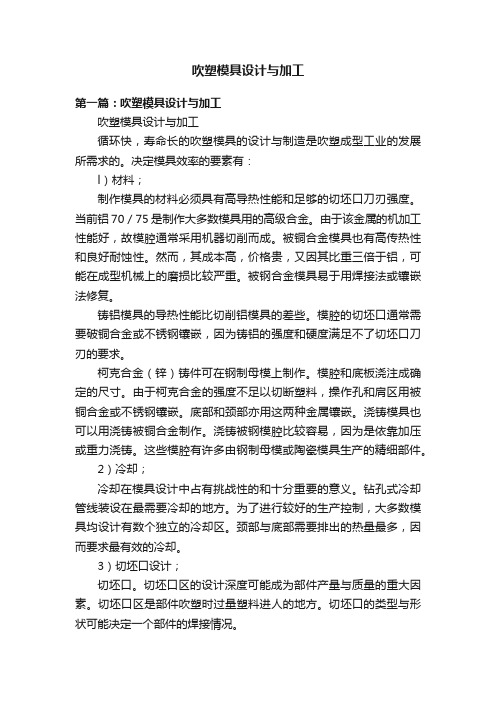
吹塑模具设计与加工第一篇:吹塑模具设计与加工吹塑模具设计与加工循环快,寿命长的吹塑模具的设计与制造是吹塑成型工业的发展所需求的。
决定模具效率的要素有:l)材料;制作模具的材料必须具有高导热性能和足够的切坯口刀刃强度。
当前铝70/75是制作大多数模具用的高级合金。
由于该金属的机加工性能好,故模腔通常采用机器切削而成。
被铜合金模具也有高传热性和良好耐蚀性。
然而,其成本高,价格贵,又因其比重三倍于铝,可能在成型机械上的磨损比较严重。
被钢合金模具易于用焊接法或镶嵌法修复。
铸铝模具的导热性能比切削铝模具的差些。
模腔的切坯口通常需要破铜合金或不锈钢镶嵌,因为铸铝的强度和硬度满足不了切坯口刀刃的要求。
柯克合金(锌)铸件可在钢制母模上制作。
模腔和底板浇注成确定的尺寸。
由于柯克合金的强度不足以切断塑料,操作孔和肩区用被铜合金或不锈钢镶嵌。
底部和颈部亦用这两种金属镶嵌。
浇铸模具也可以用浇铸被铜合金制作。
浇铸被钢模腔比较容易,因为是依靠加压或重力浇铸。
这些模腔有许多由钢制母模或陶瓷模具生产的精细部件。
2)冷却;冷却在模具设计中占有挑战性的和十分重要的意义。
钻孔式冷却管线装设在最需要冷却的地方。
为了进行较好的生产控制,大多数模具均设计有数个独立的冷却区。
颈部与底部需要排出的热量最多,因而要求最有效的冷却。
3)切坯口设计;切坯口。
切坯口区的设计深度可能成为部件产量与质量的重大因素。
切坯口区是部件吹塑时过量塑料进人的地方。
切坯口的类型与形状可能决定一个部件的焊接情况。
对于较硬的树脂而言,需要采用钢或被铜合金作切坯口材料。
有时候切坯口区要用气吹,以加速塑料冷却,去除多余的材料,防止部件畸变。
4)排气。
排气。
在部件吹塑成型时,为了使气体迅速逸出,必须使模具排气。
最常见而经济的排气方法是表面排气。
对模腔进行深度喷砂或纹理处理也有助于排气。
要排气的另一个重要原因(对那些塑料必须吹入到紧密窄小区间的部件而言)是为显示出细部。
第二篇:模具设计与加工复习题模具设计与加工复习题一、名词解释1、冷冲压;2、冲裁工序;3、变形工序;4、复合工序;5、塑性;6、塑性变形;7、黑色金属;8、有色金属;9、冲裁模;10、冲裁搭边;11、复合模;12、级进模;13、最小弯曲半径;14、冲压生产三要素;15、冲裁件的工艺性;16、挡料;17、导料;18、极性效应;19、正极性加工;20、负极性加工。
吹塑模具设计要点(新)概要
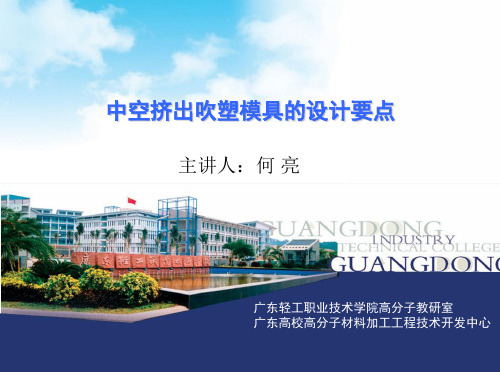
主讲人 广东高校高分子材料加工工程技术开发中心
四.中空挤出吹塑模具工艺设计要点
1. 模具型腔
• 型腔表面 许多吹塑制件的外表面都有一定的质量要求,因此, 要针对不同的要求对型腔表面采用不同的加工方式。 喷砂处理、镀铬抛光、电化学腐蚀等(吹塑PE的模具, 型腔表面应有些粗糙,易于排气,可做喷砂处理;工 程塑料的吹塑,型腔一般不能喷砂。) • 型腔尺寸 主要由制品的外形尺寸与塑料的收缩率确定。
然升温的方向流动。模面较大的冷却水通道内,可安装折流板来 引导水的流向,还可促进湍流的作用,避免冷却水流动过程中出 现死角。
6.模具冷却
吹塑模的模温一般控制在20℃~50℃左右。如果模温差 异太大会使制品的表面质量受影响,表面光泽的差异也随之 加大。 冷却方法可以参考注射模的循环水冷方式之外,还可以 选用喷淋冷却的方法:在模体背面铣出冷却水室,再用铜管 做成循环水路状,并在铜管上钻很多直径为0.1~0.3mm的 小孔,孔对着模体背面,水由孔中按照一定的方向喷出。此 方式适合于大型模具。
4.余料槽
• 在上下刃口附近开设 余料槽是为了容纳余 料。其大小应根据型 坯夹持后余料的宽度 和厚度来决定,以模 具能闭合严密为准。
5.排气问题
• 型坯吹胀时,必需把模腔表面和型坯表面之间 的空气排除,这些区域的空气不仅妨碍模具和 型坯的充分接触而降低冷却效率,而且妨碍型 坯从型腔上获得清晰的花纹或字码。 • 吹塑模具采用的排气方法很多: 模具表面喷砂处理、排气孔或沟槽(开设在型 腔易存气的部位,也可开设在分型面上)、嵌 棒排气、抽真空排气(常用在工程塑料)。
(a)凹形表面容器(b)三个分型面设置
3. 夹坯刃口
• 其作用是切除余料,同时 在吹胀以前还起着在模内 夹持和封闭型坯的作用。 • 夹坯刃口的角度和宽度对 吹塑件的质量影响很大(尤 其是上刃口)。 • 一般底部夹坯刃口宽度为 1~2mm,刃口角度为 15°~30°。
PROE模具设计吹塑模具设计
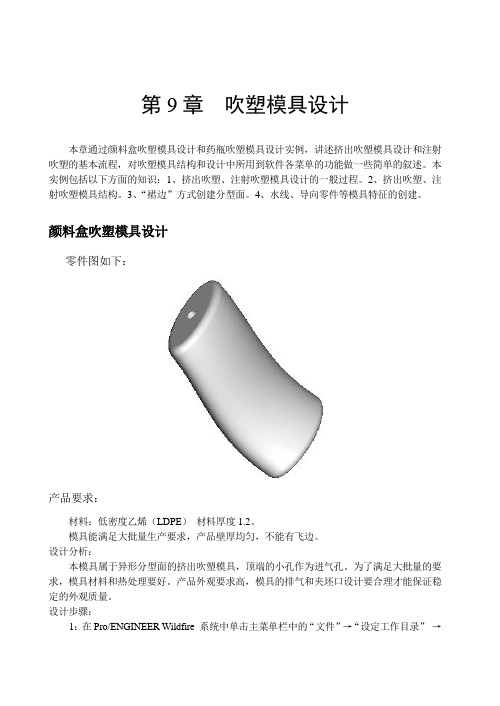
第9章吹塑模具设计本章通过颜料盒吹塑模具设计和药瓶吹塑模具设计实例,讲述挤出吹塑模具设计和注射吹塑的基本流程,对吹塑模具结构和设计中所用到软件各菜单的功能做一些简单的叙述。
本实例包括以下方面的知识:1、挤出吹塑、注射吹塑模具设计的一般过程。
2、挤出吹塑、注射吹塑模具结构。
3、“裙边”方式创建分型面。
4、水线、导向零件等模具特征的创建。
颜料盒吹塑模具设计零件图如下:产品要求:材料:低密度乙烯(LDPE)材料厚度1.2。
模具能满足大批量生产要求,产品壁厚均匀,不能有飞边。
设计分析:本模具属于异形分型面的挤出吹塑模具,顶端的小孔作为进气孔。
为了满足大批量的要求,模具材料和热处理要好。
产品外观要求高,模具的排气和夹坯口设计要合理才能保证稳定的外观质量。
设计步骤:1:在Pro/ENGINEER Wildfire 系统中单击主菜单栏中的“文件”→“设定工作目录”→选取ylh.prt文件所在的目录→确定。
2:单击“文件”→“新建”→“制造”,如图7-1所示。
在“子类型”中选择“模具型腔”,接受默认的文件名称“Mfg0001”,取消“使用缺省模块”,并单击此对话框中的“确定”按钮。
出现的图7-2所示对话框,在该对话框中选择“mmns_mfg_mold”→“确定”。
图7-1 模具型腔组件名称图7-2 组件模板选择2:单击右边级连菜单“模具型腔”→“装配”→“参照模型”,出现如图7-3所示的窗口,选择文件名为“ylh.prt”的零件,单击“打开”按钮。
出现如图7-4所示的“元件放置”对话框,在约束类型中选择“坐标系”,系统提示选择坐标系,分别按照图7-5选择参考模型坐标系“prt_csys_def”、组件模型坐标系“mold_def_csys”, 单击此对话框中的“确定”按钮。
图7-3 参照模型选择图7-4 参照模型放置图7-5 约束坐标系选择3:出现如图7-6所示的“创建参照模型”对话框,接受默认的参照模型名称,单击“确定”按钮。
苏打水瓶中空吹塑模具设计(含全套CAD图纸)
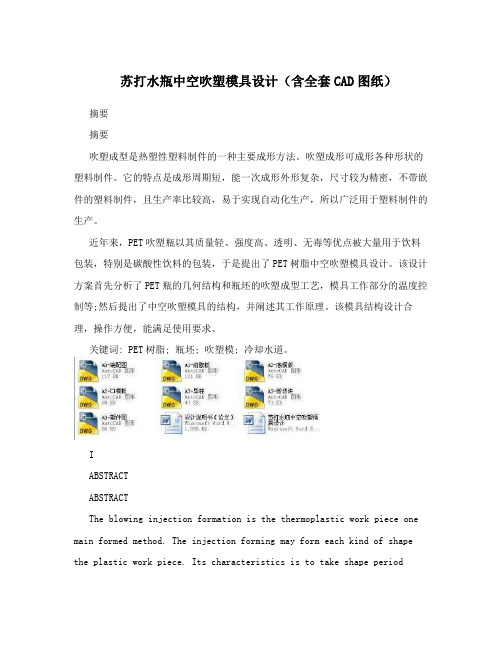
苏打水瓶中空吹塑模具设计(含全套CAD图纸)摘要摘要吹塑成型是热塑性塑料制件的一种主要成形方法。
吹塑成形可成形各种形状的塑料制件。
它的特点是成形周期短,能一次成形外形复杂,尺寸较为精密,不带嵌件的塑料制件,且生产率比较高,易于实现自动化生产,所以广泛用于塑料制件的生产。
近年来,PET吹塑瓶以其质量轻、强度高、透明、无毒等优点被大量用于饮料包装,特别是碳酸性饮料的包装,于是提出了PET树脂中空吹塑模具设计。
该设计方案首先分析了PET瓶的几何结构和瓶坯的吹塑成型工艺,模具工作部分的温度控制等;然后提出了中空吹塑模具的结构,并阐述其工作原理。
该模具结构设计合理,操作方便,能满足使用要求。
关键词: PET树脂; 瓶坯; 吹塑模; 冷却水道。
IABSTRACTABSTRACTThe blowing injection formation is the thermoplastic work piece one main formed method. The injection forming may form each kind of shape the plastic work piece. Its characteristics is to take shape periodshort, can take shape the shape complications once, size nicety, take the plastics system piece of have the piece, and the rate of production is high, being easy to carry out the automation production, so used for the production of the plastics system piece extensively.In recent years, with its quality mould high trength, ransparent, non-toxic advantages ,PET bottles were used to the beverage packaging, especially the carbonate drink . Then PET resin for blow molding mould design. The design scheme is firstly analyzed the geometrical structure of PET bottle of bottle preform and blow molding process. Mould work of temperature control parts etc. Then it puts forward for blow molding mould structure.,and its working principle. The mould structure reasonable design, convenient operation, can satisfy the requirements of operation .Keywords: PET resin; bottle reform; blowing mold; cooling channels.II目录目录摘要 ..................................................................... ........................................................................ . (I)ABSTRACT ........................................................... ........................................................................ .. II第一章简介 ..................................................................... ...................................................... 1 1.1 概述 ..................................................................... .......................................................... 1 1.2 吹塑制品的应用 ..................................................................... ........................................ 2 1.3 选题的依据和意义 ..................................................................... .................................. 4 1.4 本课题目前发展状况 ..................................................................... ................................ 4 1.5 本课题在国外的发展现状 ..................................................................... ........................ 5 1.6 塑料注塑模具的地位和未来的发展趋势 .....................................................................6第二章吹塑制件设计 ..................................................................... .................................... 9 2.1 吹塑件的功能和性能要求 ..................................................................... .................... 9 2.2 材料及其性能 ..................................................................... ...................................... 10 2.3 吹塑制件的几何结构设计 ..................................................................... (12)2.3.1容积 ..................................................................... .. (12)2.3.2.外形 ..................................................................... . (12)2.3.3.垂直载荷强度 ..................................................................... (13)2.3.4.刚度 ..................................................................... . (14)2.3.5.壁厚 ..................................................................... . (14)2.3.6.底部(支撑面) .................................................................... (14)2.3.7.边缘及转角(圆角) .................................................................... . (15)2.3.8.口部 ..................................................................... . (15)2.3.9.螺纹 ..................................................................... . (16)2.3.10.脱模斜度 ..................................................................... (17)第三章吹塑成型工艺 ..................................................................... .................................. 18 3.1 中空吹塑成型方式 ..................................................................... .............................. 18 3.2 吹塑成型的工艺及技术参数 ..................................................................... .. (20)3.2.1塑料挤出工艺 ..................................................................... . (21)3.2.2 吹胀定型工艺 ..................................................................... (22)3.2.3成型技术参数 ..................................................................... . (24)3.2.4 成型设备选用 ..................................................................... .. (26)第四章模具结构设计 ..................................................................... .................................. 28 4.1 吹塑模具结构选择 ..................................................................... (28)4.1.1 吹塑模具的工作方式 ..................................................................... .. (28)4.1.2 吹塑模具的组装方式 ..................................................................... .. (29)4.1.3 吹塑模具的吹气方式 ..................................................................... .. (30)4.1.4 吹塑模具的启闭方式 ..................................................................... .............. 30 4.2 分模面的选择 ..................................................................... ...................................... 31 4.3 成型零件设计 ..................................................................... .. (31)目录4.3.1 成型零件应具备的性能 ..................................................................... . (31)4.3.2 成型零件结构设计 ..................................................................... (32)4.4 吹塑模具的排气系统设计 ..................................................................... (36)4.4.1模腔排气 ..................................................................... (36)4.4.2螺纹处排气 ..................................................................... .. (39)4.5 吹塑模具冷却系统设计 ..................................................................... . (40)4.5.1 模具材料的选择 ..................................................................... . (40)4.5.2 冷却系统设计计算 ..................................................................... (40)4.5.3冷却水的位置布置 ..................................................................... .. (45)4.6 导向机构设计 ..................................................................... .. (46)4.6.1 导柱 ..................................................................... (46)4.6.2 导套 ..................................................................... (47)4.6.3 导柱位置的布置 ..................................................................... ...................... 47 第五章模具尺寸与技术参数校核 ..................................................................... (48)5.1模具结构尺寸 ..................................................................... . (48)5.2锁模力的校核 ..................................................................... . (48)5.3 模板开距的校核 ..................................................................... ...................................... 49 结束语 ..................................................................... .. (50)致谢 ..................................................................... .........................................................................56 参考文献 ..................................................................... (46)河南理工大学本科毕业论文第一章简介1.1 概述人们生活中使用的各种容器,随着科学技术的进展,制造容器的材料在不断演变和发展,如石头、泥土、木材、竹、藤、草、纸张、棉布、皮革、陶瓷、玻璃、水泥、铁、钢、有色金属、橡胶和合成塑脂等,而塑料容器时19世纪中叶才出现的新材料、新产品。
《塑料成型工艺与模具设计》(上册)电子教案完全版

《塑料成型工艺与模具设计》(上册)电子教案完全版第一章:塑料成型工艺概述1.1 塑料成型的基本概念塑料的定义与特性塑料成型的定义与分类1.2 塑料成型工艺流程塑料原料的准备塑料的加热与塑化塑料的冷却与固化塑料的脱模与后处理1.3 塑料成型工艺参数温度压力速度时间第二章:塑料模具概述2.1 模具的分类与结构模具的分类模具的基本结构2.2 模具的设计原则模具设计的要求与步骤模具设计中的关键参数2.3 模具的材料与制造模具材料的选用原则模具的制造工艺第三章:塑料注射成型工艺与模具设计3.1 注射成型工艺概述注射成型原理与特点注射成型工艺参数3.2 注射模具的结构设计模具的型腔与型芯设计模具的冷却系统设计模具的加热系统设计3.3 注射模具的导向与定位模具的导向设计模具的定位设计第四章:塑料挤出成型工艺与模具设计4.1 挤出成型工艺概述挤出成型的原理与特点挤出成型工艺参数4.2 挤出模具的结构设计模具的口模设计模具的定径套设计模具的切割装置设计模具的导向设计模具的调整方法第五章:塑料吹塑成型工艺与模具设计5.1 吹塑成型工艺概述吹塑成型的原理与特点吹塑成型工艺参数5.2 吹塑模具的结构设计模具的型腔设计模具的吹气系统设计模具的后处理设计5.3 吹塑模具的导向与定位模具的导向设计模具的定位设计第六章:塑料压缩成型工艺与模具设计6.1 压缩成型工艺概述压缩成型的原理与特点压缩成型工艺参数6.2 压缩模具的结构设计模具的型腔设计模具的压柱设计模具的冷却系统设计模具的导向设计模具的定位设计第七章:塑料压注成型工艺与模具设计7.1 压注成型工艺概述压注成型的原理与特点压注成型工艺参数7.2 压注模具的结构设计模具的型腔设计模具的压注系统设计模具的冷却系统设计7.3 压注模具的导向与定位模具的导向设计模具的定位设计第八章:塑料传递成型工艺与模具设计8.1 传递成型工艺概述传递成型的原理与特点传递成型工艺参数8.2 传递模具的结构设计模具的型腔设计模具的传递系统设计模具的冷却系统设计模具的导向设计模具的定位设计第九章:塑料成型工艺与模具设计的计算与模拟9.1 模具设计计算塑料收缩率的计算模具尺寸的计算模具强度的计算9.2 模具设计模拟模具流动分析模具冷却分析模具翘曲分析9.3 模具设计软件介绍模具设计软件的功能与特点模具设计软件的应用实例第十章:塑料成型工艺与模具设计的实践与应用10.1 塑料成型工艺实践成型工艺的操作步骤与注意事项成型过程中的常见问题与解决方法10.2 模具设计应用实例典型模具设计案例分析模具设计在实际生产中的应用10.3 塑料成型工艺与模具设计的未来发展塑料成型技术的发展趋势模具设计技术的创新与突破重点和难点解析重点环节1:塑料成型的基本概念与特性补充和说明:塑料成型的基本概念和特性是理解后续成型工艺与模具设计的基础。
吹塑模具的设计与制造毕业设计说明书

集美大学毕业设计(论文)题目:吹塑模具的设计与制造院系:工程技术学院专业:数控技术年级:姓名:学号:指导教师:2011年5月吹塑模具的设计与制造摘要,一种进展迅速的加工方式。
树脂经挤出或取得的管状塑料型坯,趁热(或加热到软化状态),置于对开模中,闭模后当即在型坯内通入紧缩空气,使塑料型坯吹胀而紧贴在模具内壁上,经冷却脱模,即取得各类中空制品。
关键词:管状塑料型坯冷却脱模内表面处置目录前言吹塑的概述---------------------------------------------------------------------------5 第一章塑件的工艺分析-----------------------------------------------------------7 第二章塑件的吹塑方式-----------------------------------------------------------8第三章塑件的设计-----------------------------------------------------------------9-----------------------------------------------------------10第四章塑料模具设计-------------------------------------------------------------11 模具的冷却系统-------------------------------------------------------11-------------------------------------------------------13模具的颈部结构-------------------------------------------------------13-----------------------------------------------14------------------------------------------------------------------14------------------------------------------------------------------15------------------------------------------------------------15------------------------------------------------------------------16前言模具课程设计是在完成冷冲模具设计、塑料模具设计、CAD软件等相关专业课程学习以后,一个重要的综合性的环节。
吹塑模具设计要点概要

吹塑模具设计要点概要1.产品设计要点:在进行吹塑模具设计之前,首先需要对要生产的产品进行深入的分析和了解。
包括产品的形状、尺寸、容量、材质等要求。
这些数据将直接影响到模具的设计和制造。
2.模具结构设计要点:吹塑模具通常由芯棒、冷却系统、分模系统和出料系统等部分组成。
在进行模具结构设计时,需要考虑产品的形状和尺寸,并选择合适的结构形式。
如常用的两片式模具、多片式模具、套筒模具等。
3.材料选用要点:吹塑模具通常采用优质合金钢或特殊材料制造,以保证模具的耐磨性、强度和使用寿命。
在选择材料时,需要考虑模具的工作环境和要求,选择合适的材料,同时还需要考虑材料的可加工性和成本。
4.出料系统设计要点:吹塑模具的出料系统用于将熔融的塑料注入模具中,同时将成型品取出。
在出料系统设计时,需要考虑塑料的流动性、冷却性和断面均匀性等因素,以保证产品的质量和生产的效率。
5.冷却系统设计要点:吹塑模具在生产过程中需要进行冷却,以便塑料快速凝固并保持形状。
在冷却系统设计时,需要考虑到产品的不同部位的冷却速度不同,需合理安排冷却系统的布局和设计冷却水路。
6.模具加工要点:吹塑模具的制造需要经过多道工序,包括车床加工、铣床加工、电火花加工、线切割加工等。
在进行模具加工时,需要保证加工工艺和精度,尤其是对于塑件的尺寸和表面光洁度要求较高的模具。
吹塑模具设计的要点总结如上,不同类型的吹塑模具在设计和制造时会有一些特定的要求和注意事项,根据实际情况进行具体的分析和设计。
模具设计师需要熟悉吹塑工艺的原理和要求,结合实际的生产情况,进行综合考虑和优化设计,以提高模具的质量和生产效率。
吹塑铝合金模具设计与制造

吹塑铝合金模具设计与制造以吹塑铝合金模具设计与制造为题,本文将从模具设计和制造的角度介绍吹塑铝合金模具的相关知识。
一、吹塑铝合金模具的概述吹塑铝合金模具是一种用于吹塑成型的模具,它采用铝合金材料制造而成。
吹塑成型是一种常见的塑料加工方法,通过将熔化的塑料注入到模具中,经过冷却和固化后得到所需的塑料制品。
铝合金模具由于其优良的导热性能和较低的成本,成为吹塑模具制造中的重要选择。
二、吹塑铝合金模具的设计1. 模具结构设计吹塑铝合金模具的结构设计应考虑到产品的形状、尺寸和生产要求。
模具结构通常包括模具座、模具芯、模具腔等部分,其中模具芯和模具腔是形成产品形状的关键部分。
设计时需要考虑产品的收缩率、壁厚、表面光洁度等因素,确保最终产品的质量。
2. 模具材料选择吹塑铝合金模具的材料选择主要考虑到其导热性能和机械性能。
铝合金具有良好的导热性能,能够快速散热,提高模具的生产效率。
同时,铝合金还具有较高的强度和硬度,能够满足模具在生产过程中的工作要求。
3. 模具制造工艺吹塑铝合金模具的制造工艺主要包括模具结构加工、表面处理和装配等环节。
模具结构加工包括数控加工、线切割、铣削等,通过这些工艺将模具的结构加工成所需的形状。
表面处理则是为了提高模具的耐磨性和防腐性,常见的表面处理方法包括阳极氧化、喷砂、电镀等。
最后,将各个部件装配到一起,确保模具的完整性和可靠性。
三、吹塑铝合金模具的制造1. 设计验证在制造吹塑铝合金模具之前,需要进行设计验证,确保模具的设计符合产品要求。
通过计算和模拟分析,验证模具的结构和尺寸是否满足产品的要求,避免因设计错误导致的生产问题。
2. 材料准备吹塑铝合金模具的制造需要准备相应的铝合金材料。
选择合适的铝合金材料,根据模具的尺寸和形状进行切割和加工,确保材料符合设计要求。
3. 模具制造模具制造包括模具结构加工、表面处理和装配等环节。
根据设计要求,通过数控加工、线切割、铣削等工艺将模具的结构加工成所需形状。
- 1、下载文档前请自行甄别文档内容的完整性,平台不提供额外的编辑、内容补充、找答案等附加服务。
- 2、"仅部分预览"的文档,不可在线预览部分如存在完整性等问题,可反馈申请退款(可完整预览的文档不适用该条件!)。
- 3、如文档侵犯您的权益,请联系客服反馈,我们会尽快为您处理(人工客服工作时间:9:00-18:30)。
第9章 吹塑模具设计
(2)将注塑的型坯,其螺纹部分 随模具螺纹成型块一起随转盘带动 移到加热位置,用电阻再将型坯内 外加热,如图9-4所示。
第9章 吹塑模具设计
(3)将加热后有底型坯,移至拉伸吹塑位置,拉 伸长2倍,如图9-5a所示,吹塑成型如图9-5b所示。 (4)将拉伸吹塑后的制件移到下一位置,螺纹成 型块半合部打开,取出制品,如图9-6所示。
9.1.1 吹塑成型方法 吹塑成型方法主要有以下几种形式。 1.挤出吹塑成型 其成型过程如图9-1所示。
第9章 吹塑模具设计
2.注塑吹塑成型 这种方法是用注塑机在注塑模具中制成吹塑型坯, 然后把热型坯移入吹塑模具中进行吹塑成型,如图 9-2所示。
第9章 吹塑模具设计
3.注塑拉伸吹塑成型 这种方法与注塑吹塑相比,只是增加了将有底 的型坯加以拉伸这一工序,成型过程如下: (1)把熔融塑料注入模具,急剧 冷却,成型出透明的有底型坯,如 图9-3所示。
第9章 吹塑模具设计
1.吹胀比(BR)
吹胀比表明了塑料制品径向最大尺寸与挤出机头口模尺寸之 间的关系。当吹胀比确定后,便可根据塑料制品的最大径向尺 寸及制品壁厚确定机头口模尺寸。机头口模与芯模间隙可用下 式确定: δ=tBRα 式中δ—口模与心模的单边间隙; t—制品壁厚; BR—吹胀比; α—修正系数,一般取1~1.5,它与加工塑料粘度有关, 粘度大,取小值。 型坯截面形状一般要求与制品外形轮廓形状大小一致,如 吹塑圆形截面瓶子,型坯截面应为圆形,若吹塑方形截面塑料 桶,则型坯为方形截面,或用壁厚不均匀的圆截面型坯,以获 得壁厚均匀的方形截面桶。
第9章 吹塑模具设计
2.成型空气压力
一般在0.2~0.69Mpa范围内,主要根据塑料熔融粘度的高 低来确定其大小。 粘度低的,如尼龙、聚乙烯,易于流动吹胀,则成型空气 压力可小些; 粘度高的,如聚碳酸脂、聚甲醛,流动及吹胀性差,那就 需要较高的压力。 成型空气压力大小还与制品的大小、型坯壁厚有关,一般 薄壁和大容积制品宜用较高压力,而厚壁和小容积制品则用较 低压力。最合适的压力在0.1~0.9Mpa的压力范围内,以每递 增0.1Mpa的办法,分别吹塑成型一系列中空制件,用肉眼分辨 其外形、轮廓、螺纹、花纹、文字等清晰程度而进行确定。
第9章 吹塑模具设计
这种成型设备实际 上是一台多工位注塑机 模具,设有四个工位, 每个工位相隔90°,图 9-7所示是注塑有底型 坯第一工位和拉伸吹塑 第三工位。
第9章 吹塑模具设计
件制品的主 要方法。下面以挤出吹塑为例介绍其工艺特点。 1.加工温度和螺杆转速 原则是在既能挤出光滑而均匀的塑料型坯, 又不会使挤压转动系统超负荷的前提下,尽可能采 用较低的加工温度和较快的螺杆转速。
第9章 吹塑模具设计
表9-1为几种有代表性的塑料中空制件的吹塑成型工艺条件。
醋酸纤维CA 工艺条件 电筒 料筒温度 后(℃) 中(℃) 前( ℃) 机头温度 (℃) 模口温度 (℃) 螺杆形式 型坯挤出时间(s) 充气时间 (s) 冷却时间 (s) 总周期 (s) 充气压力(10×Pa) 充气方法 吹胀比 产品质量 (g) 螺杆转速 r/min 挤压机 110~115 130~135 150~155 160~162 160 渐变压缩 22 12 3 45 0.3~0.34 顶吹 1.5:1 50~55 16.5 φ45mm 立式挤出机 硬聚氯乙 烯HPVC 500ml瓶 145~150 150~155 165~168 165~170 180 渐变压缩 30 15 3 55 0.4 顶吹 2:1 75~80 16.5 φ45mm 立式挤出 机 聚乙烯PE 浮球 140~150 155~160 160 160 渐变压缩 15 15 5 40 0.3~0.4 顶吹 2.5:1 80 22 φ89mm 卧式挤出 机 尼龙1010 100ml瓶 140~170 215~225 210~215 210~215 180~190 突变压缩 20 10 5 40 0.2~0.3 顶吹 2:1 7 12 φ30mm 卧式挤出机 聚碳酸酯 PC 圆筒 220~240 240~260 240~260 190~210 190~200 渐变压缩 60 20~30 10~15 120 0.69 顶吹 1.6:1 300 11.5 φ50mm 立式挤出 机
主讲教师: 丁 立 刚
第9章 吹塑模具设计
9.1 概述 9.1.1 吹塑成型方法 9.1.2 工艺特点 9.1.3 吹塑制品结构工艺特点 9.2 吹塑模具的类型及典型结构 9.2.1 吹塑模具的类型 9.2.2 模具典型结构 9.3 吹塑模具设计要点 思考题及习题
第9章 吹塑模具设计
9.1 概述
第9章 吹塑模具设计
9.1.3 吹塑制品结构工艺特点
常见的中空成型制品几何型状有圆形、长方形、 正方形、椭圆形、球形、异形等。进行中空制品的 结构设计时要综合考虑塑料制品的使用性能、外观、 成型工艺性与成本等因素。也就是说要确定好塑件 的吹胀比、延伸比、螺纹、塑件上的圆角、支承面 及脱模斜度等。下面分别叙述对它们的具体要求。
第9章 吹塑模具设计
4.模温和冷却时间
材料的熔融温度较高者,允许有较高的模具温度,反之, 则应尽可能降低模具温度。模具温度过低,塑料冷却就过早, 则形变困难,制品的轮廓和花纹等均会变得不清楚;若模具 温度过高,则冷却时间延长,生产周期增加;如果冷却程度 不够,则容易引起制品脱模变形,收缩率大和表面无光。 为防止聚合物因产生弹性回复作用引起制品形变,中空吹 塑成型制品的冷却时间一般较长,可占成型周期的1/3 ~ 2/3。 对厚度为1~2mm的制品,一般只需几秒到十几秒的冷却时 间已足够。
第9章 吹塑模具设计
3.吹胀比 制品尺寸和型坯尺寸之比,亦即型坯吹胀的倍 数,称为吹胀比。 型坯尺寸和质量一定时,制品尺寸愈大,型坯 吹胀比愈大。 虽然增大吹胀比可以节约材料,但制品壁厚变 薄,成型困难,制品的强度和刚度降低;吹胀比过 小,塑料消耗增加,制品有效容积减少;壁厚,冷 却时间延长,成本增高。一般吹胀比为2~4倍,用 1:2较适宜,此时壁厚较均匀。
吹塑成型是将处于熔融状态的塑料型 坯置于模具型腔中,借助压缩空气将其 吹胀,使之紧贴于型腔壁上,经冷却定 型得到中空塑料制品的成形方法。 吹塑成型可以获得各种形状与大小的 中空薄壁塑料制品,在工业中尤其是在 日用工业中应用十分广泛。几乎所有的 热塑性塑料都可以用于吹塑成型,尤其 是PE。
第9章 吹塑模具设计