浅谈沉镍金工艺
沉镍金制作流程(精)

沉镍金制作流程一、简介:通过化学反应在铜表面沉积较薄一层镍金、金层具有稳定的化学和电器特性,镀层具有优良的可焊性,耐蚀性等特点。
二、流程及作用:(1沉金前处理:①微蚀:除去烘烤绿油造成的铜面过度氧化物。
② 1200#磨刷幼磨:除去铜面杂物,清洁板面。
(2沉镍金流程:上板→除油→Ⅱ级水洗→微蚀→→Ⅱ级水洗→酸洗→Ⅱ级水洗→预浸→活化→Ⅱ级水洗→后浸酸→Ⅰ级水洗→沉镍→Ⅱ级水洗→沉金→金回收→水洗→热水洗→下板①除油:除去铜表面之轻度油脂及氧化物,使表面活化及清洁。
②微蚀:除去铜面氧化物及污染物,适度粗化铜面,增加镀层密着性、结合力。
③预浸:保护活化药液。
④活化:使用离子钯溶液使表面铜活化,可以只在铜面上沉积而基材的Pd化合物极易清洗,提供化学沉镍的启镀剂。
⑤化学镀镍:利用电子转移使溶液中的Ni2+还原在待镀铜面上而沉积出镍金属:但同时会有P析出,Ni层实际为Ni/P合金,Ni层厚度一般为100-200u〃。
⑥通过置换反应在新鲜镍面置换一层薄金,作为防止基体金属氧化和作为自身活化型镀金的底层,镍基体上覆盖一层金后金沉积就停止,所以厚度有一定了限制,Au层厚度一般为1-3 u〃。
(3沉金后处理:①草酸洗:除去金面氧化异物,,对金层疏孔处的镍底层作酸封孔处理,增加其耐蚀性。
②抗氧化清洗:防止镀层氧化,使焊锡维持更长的寿命。
三、流程控制注意事项:(1控制微蚀速率在0.6-0.8um,速率太低,镀层发亮,太高出现色差即金色不良。
(2活化缸Cu2+浓度≤200PPM需更换,且后期易出现渗金。
(3Ni缸温度不可太高,药水高温对绿油攻击较大,易出现甩S/M问题,槽液使用4.0MTD后需换槽。
(4金缸需控制Ni2+含量≤800PPM,Ni2+太高易出现金色不良及不上金问题。
四、常见问题介绍及处理方法:(1漏镀:①活化浓度温度过低,浴老化或活化后水洗过久。
②镍缸浓度、温度、PH值太低,或有不以纯物混入,成份失调。
③绿油冲板不净,有残渣附着铜面,需煲板返印。
沉镍钯金工艺(一)

沉镍钯金工艺(一)沉镍钯金工艺1. 简介•沉镍钯金工艺是一种常用于表面镀层的工艺技术。
•它通过在金属表面沉积一层镍和钯的合金薄膜来实现防腐、提高硬度和耐磨性的效果。
2. 工艺流程1.表面预处理–清洗:将待处理的金属表面进行清洗,去除污垢、氧化物等。
–酸洗:使用酸性溶液消除金属表面的氧化层,提高后续工艺的效果。
2.沉镍钯金–沉镍:将金属表面浸入含有镍盐的溶液中,施加电流使镍离子在金属表面还原沉积。
–镍层均匀性:控制电流密度、搅拌溶液等因素,确保沉积的镍层均匀。
3.沉钯–沉钯:将经过镍层处理的金属再次浸入含有钯盐的溶液中,进行类似的电化学反应,沉积钯层。
–钯层厚度:通过控制电流密度、溶液浓度,调整钯层的厚度。
4.表面处理–精整:去除不平整的部分,提高镀层的外观。
–抛光:使得镀层表面更加光滑,增强镀层的光泽度。
3. 应用领域•汽车工业:沉镍钯金工艺常用于汽车发动机零部件的表面处理,提高其耐腐蚀性和耐磨性。
•电子工业:沉镍钯金可用于电子器件的接点材料,提高其连接稳定性和导电性。
•机械工业:沉镍钯金工艺可应用于机械零件的表面涂层,提高其硬度和耐磨性。
4. 优势和局限性•优势:1.镀层均匀,能够提供出色的防腐和耐磨性能。
2.镀层与基材结合牢固,不易剥落。
3.工艺成熟,操作相对简单。
•局限性:1.沉镍钯金工艺对金属表面的准备要求较高。
2.镀层厚度有限,不适用于需要特别厚度的场景。
5. 结论•沉镍钯金工艺是一种可靠且成熟的表面处理技术,在许多领域得到广泛应用。
•通过控制工艺流程和参数,可以获得优良的防腐和耐磨性能的镀层。
•然而,工艺的局限性也需要考虑,根据具体需求选择适合的表面处理技术。
化学沉镍金工艺控制概述-刘兴武

化学沉镍金工艺控制概述生益电子:刘兴武摘要:本文简单介绍了化学沉镍金工艺的优缺点、原理、流程参数控制;并总结了常见问题的原因、改善措施以及检测方法等。
一、前言随着电子工业的飞速发展,IC组装对印制板(PCB)的要求也越来越高,无铅化表面处理(Lead-free Surface Finishes)已成主流。
化学沉镍金(Electroless Nickel Immersion Gold简称ENIG)、沉银(Immersion Silver简称ImAg)、沉锡(Immersion Tin 简称ImSn)、有机助焊保护膜(Organic Solderability Presevatives简称OSP)是替代传统锡铅涂覆的有效工艺方法,又因化学沉镍金的众多优点,其更受客户的青睐,已成为锡铅涂覆替代工艺的核心。
化学沉镍金又叫无电镍浸金或化镍浸金,它是通过钯的催化作用,在酸性条件下使裸铜面上沉积一层镍,然后通过置换反应再沉积上一层薄金的表面涂覆工艺,其金层提供良好的电气连接性,镍层作为阻挡层以阻止铜的扩散,从而避免在焊接和返工操作过程中焊料对铜层的污染。
二、化学沉镍金的优缺点1、优点(1)、高可靠性,适用复杂的电路设计。
(2)、高可焊性,适用多种及多重焊接(熔焊/Solder Fusing、波峰焊/Wave Solder、回流焊/Re-flow Solder、线焊/Wire Bonding)。
(3)、高平整、共面性,适用各种精密元器件的复杂组装。
(4)、良好的外观,不褪色,耐腐蚀、储存寿命长。
(5)、电气接触导通性、散热性好、具EMI(电磁干扰)屏蔽作用。
2、缺点(1)、焊点不良(工艺控制不当时发生)(2)、工艺复杂、操作温度较高(3)、成本高、价格昂贵三、主要化学反应原理1、活化Cu + Pd2++ 2NH4Cl Cu(NH3)2Cl2+ Pd+ 2H+2、化学沉镍催化剂[H2PO2]-+ H2O [H2PO3]-+ 2H(催化剂)Ni2++ 2H(催化剂)Ni ↓+ 2H+[H2PO2]-+ H(催化剂)H2O+ OH-+ P3Ni + P Ni3P (会产生金属间化合物)2H(催化剂)H2 ↑(会产生气泡)3、化学浸金Ni + 2[Au(CN)2]-Ni2+ + 2Au + 4CN-四、所需之设备物料1、目前,安美特、麦德美、优美科、罗门哈斯、上村药水在市场上较为流行,本公司所用安美特的Aurotech系列药水。
沉镍金工艺

沉镍金工艺我呀,今天想跟你唠唠一个超酷的工艺,那就是沉镍金工艺。
你知道电路板不?就那小小的、看起来错综复杂的板子,可别小看它,现代的好多高科技设备都离不开它呢。
这沉镍金工艺啊,就像是给电路板穿上了一层超厉害的防护服,而且还是那种带金闪闪特效的。
我有个朋友叫小李,他就在一家电子厂工作。
有一次我去他厂里参观,那场面可把我震撼到了。
他指着那些正在进行沉镍金工艺处理的电路板说:“你看,这就是咱们电子设备的心脏框架,要是没这工艺,好多设备都得歇菜。
”我当时就特别好奇,这看起来普普通通的工艺,咋就这么重要呢?沉镍金工艺,简单来说,就是在电路板的铜表面先沉积一层镍,然后再在镍的上面沉积一层金。
这就好比是盖房子,先打一个镍的地基,然后再在上面盖一个金的小别墅。
这镍层啊,它可是很有本事的,它就像一个忠诚的卫士,防止铜被氧化。
你想啊,如果铜被氧化了,那就像铁生锈一样,电路板的性能肯定会大打折扣。
而金呢,金就更厉害了,它导电性超级好,就像电子们的高速公路,让电子在电路板上跑得飞快。
我在厂里看到那些工人们小心翼翼地操作着设备,心里就想,这可真是个精细活啊。
每一个步骤都像是在雕刻一件艺术品。
小李跟我说:“这沉镍金可不像你想象的那么简单,里面的门道多着呢。
”他告诉我,在沉积镍之前,得先把电路板表面处理得干干净净,就像要给一个孩子洗澡一样,得洗得彻彻底底,不能有一点脏东西。
要是有一点杂质,那就像是在平整的马路上突然出现了一块大石头,电子在传输的时候就会被挡住,这设备就可能出故障了。
这时候我就忍不住问他:“那怎么才能保证这个过程不出差错呢?”小李笑着说:“这就得靠严格的工艺控制啦。
就像你做饭,盐放多放少都不行,这个工艺也是,化学药剂的浓度啊、温度啊、处理时间啊,都得精确控制。
”我听了之后,心里对那些工人真是充满了敬佩。
他们就像是一群魔法师,通过沉镍金工艺,把一块块普通的电路板变成了高科技的核心部件。
你可能会想,为啥非得是镍和金呢?这就像是组建一个超级战队,每个成员都有自己独特的能力。
PCB沉金工艺介绍
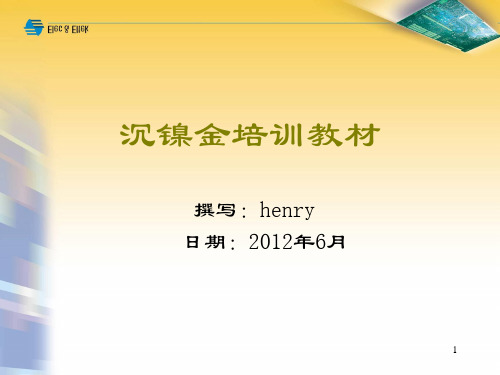
化学镍药水的分类:
按操作温度分可将镀液分成高温镀液(85950C)、中温镀液(65-750C)、低温 镀液(500C)以下
按其使用的还原剂又可大致分为次磷酸盐 型、硼氢化物型、肼型、胺基硼烷型4种。
26
按pH值分又可将其分为酸性镀液和碱性镀 液; 最常用的是次磷酸盐为还原剂的酸性高温 化学镀镍液,常称为普通化学镀镍液。
1.5 ±0.5min
搅拌:摆动及药液循环搅拌或空气打气
槽材质:PVC或PP
加热器:石英或铁弗龙加热器
15
铜浓度控制:
由于Cu2+对微蚀速率影响较大,通 常须将Cu2+的浓度控制在5-25g/l, 以保证微蚀速率处于0.5-1.5μm之间。 生产过程中,换缸时往往保留1/5-1/3 缸母液(旧液),以保持一定的Cu2+浓 度。
通常情况,不采用调节药水浓度或 升高温度来弥补因时间不足而引起的镍 厚不足,一定要根据客户镍层要求来设 置适当的镀镍时间。否则,可能引起活 性不稳定,会造成许多不良后果。
44
C、浓度: 不同供应商之不同系列药水,
其浓度控制范围各不相同。由于化 学镀镍的本身特点,其动态平衡的 控制难度远远大于化学镀铜,其控 制范围很窄则可说明这一点。因此, 尽可能使用自动补料器来控制药水 浓度,手动补料是很难保证每一个 制板的良品率。
• B、随着NaH2PO2和NiSO4浓度的增加, 沉积速度逐渐提高,而后趋于稳定或稍 有降低。但此时溶液的稳定性下降;
40
•C、化学镀镍层的厚度一般控制4~5μm, 最少要大于2.5μm厚的镍磷层才能起到 有效的阻挡层作用,防止铜的迁移,以免渗 出金面,氧化后导致导电性不良;
•D、镀覆PCB的装载量(裸铜面)应适 中,以0.1~0.5dm2/L为宜。负载太大会导 致镍缸活性逐渐升高,甚至导致反应失 控,造成严重后果;负载太低会导致镍 缸活性逐渐降低,造成漏镀等问题。
化学镍金工艺原理
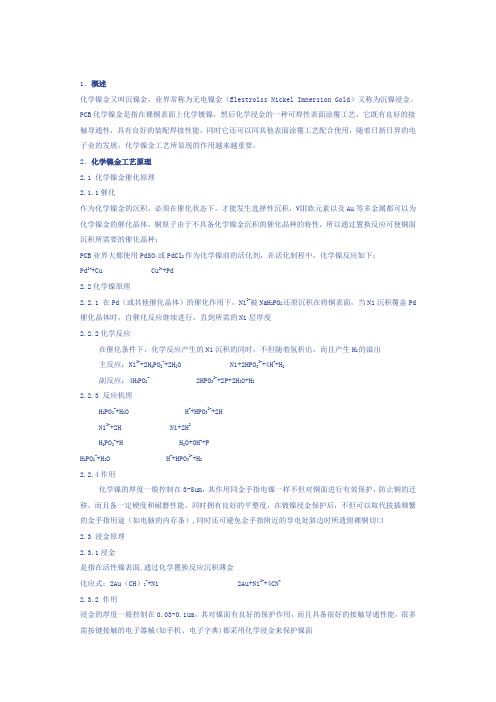
1.概述化学镍金又叫沉镍金,业界常称为无电镍金(Elestrolss Nickel Imnersion Gold)又称为沉镍浸金。
PCB化学镍金是指在裸铜表面上化学镀镍,然后化学浸金的一种可焊性表面涂覆工艺,它既有良好的接触导通性,具有良好的装配焊接性能,同时它还可以同其他表面涂覆工艺配合使用,随着日新日异的电子业的发展,化学镍金工艺所显现的作用越来越重要。
2.化学镍金工艺原理2.1 化学镍金催化原理2.1.1催化作为化学镍金的沉积,必须在催化状态下,才能发生选择性沉积,VⅢ族元素以及Au等多金属都可以为化学镍金的催化晶体,铜原子由于不具备化学镍金沉积的催化晶种的特性,所以通过置换反应可使铜面沉积所需要的催化晶种;PCB业界大都使用PdSO4或PdCl2作为化学镍前的活化剂,在活化制程中,化学镍反应如下:Pd2++Cu Cu2++Pd2.2化学镍原理2.2.1 在Pd(或其他催化晶体)的催化作用下,Ni2+被NaH2PO2还原沉积在将铜表面,当Ni沉积覆盖Pd 催化晶体时,自催化反应继续进行,直到所需的Ni层厚度2.2.2化学反应在催化条件下,化学反应产生的Ni沉积的同时,不但随着氢析出,而且产生H2的溢出主反应:Ni2++2H2PO2-+2H2O Ni+2HPO32-+4H++H2副反应:4H2PO2- 2HPO32-+2P+2H2O+H22.2.3 反应机理H2PO2-+H2O H++HPO32-+2HNi2++2H Ni+2H2H2PO2-+H H2O+OH-+PH2PO2-+H2O H++HPO32-+H22.2.4作用化学镍的厚度一般控制在3-5um,其作用同金手指电镍一样不但对铜面进行有效保护,防止铜的迁移,而且备一定硬度和耐磨性能,同时拥有良好的平整度,在镀镍浸金保护后,不但可以取代拔插频繁的金手指用途(如电脑的内存条),同时还可避免金手指附近的导电处斜边时所遗留裸铜切口2.3 浸金原理2.3.1浸金是指在活性镍表面,通过化学置换反应沉积薄金化应式:2Au(CH)2-+Ni 2Au+Ni2++4CN-2.3.2 作用浸金的厚度一般控制在0.03-0.1um,其对镍面有良好的保护作用,而且具备很好的接触导通性能,很多需按键接触的电子器械(如手机、电子字典)都采用化学浸金来保护镍面3.化学Ni/Au的工艺流程3.1 工艺流程简介作为化学镍金流程,只要具备6个工作站就可满足生产要求3-7分钟1-2分钟0.5-4.5分钟2-6分钟除油微蚀活化预浸沉Au沉Ni20-30分钟7-11分钟3.2 工艺控制3.2.1除油缸一般情况下,PCB沉镍金采用酸性除油剂处理制板,其作用在于除掉铜面的轻度油脂及氧化物,达到清洁及增加湿润效果的目的,它应当具备不伤SOiderMask(绿油)以及低泡型易水洗的特点。
沉镍金工艺
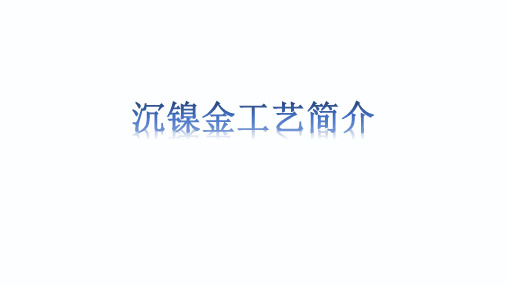
沉镍金工艺-原理
反应机理:
Pd2+
Cu Pd
Cu Pd
Cu2+
活化Ni-P沉积源自Au+Ni = 4g/L Au Ni = 5g/L
Cu
Cu
Cu Ni-P
Cu Ni-P
pH = 4.4
Ni-P成长 化学镍
Ni2+
Au 沉积
化镍金层
pH = 4.8
沉镍金后图片
沉镍金工艺-常见品质不良
7.可焊性差
1、金面污染 2、水洗水(含后处理)水质差; 3、镍槽或金槽老化,使镀层有机杂质含量高; 4、镍厚不足或镍层发生原电池反应遭到腐蚀(黑垫)。
除 油:去除表面油渍,指纹,轻度氧化,清洁铜面。 微 蚀:粗化铜表面,增强镍铜层结合力。 酸 洗:调整铜面,改善SPS对半塞孔板的影响。 预 浸:清除铜面氧化,防止活化槽受污染。 活 化:在铜面上置换上一层钯,作化学镍反应催化剂。 后 浸:去除绿油面上多余钯,改善绿油面上金或渗镀等。 化学镍:自催化氧化还原反应,在铜层与金层间沉积上镍层,防止金层
思考
以下几种概念分别是什么?
沉金 化金 电金 镀金
金手指
硬金 软金
闪金
概念
沉金
沉金采用的是化学沉积的方法,通过化学氧化还原反应的方法生成一层镀金层
电金
采用电镀的方式,将金盐溶于化学药水中,将电路板浸于电镀缸中并通电流,在铜面上生产镍金镀层。 在电镀过程中,由于金无法与铜皮直接起反应,所以会先镀上一层镍,然后再把金镀在镍上面,所以也称为电镀镍金。
沉镍金工艺
一、概述 二、流程 三、原理 四、常见品质不良
沉镍金工艺-概述
沉镍钯金工艺
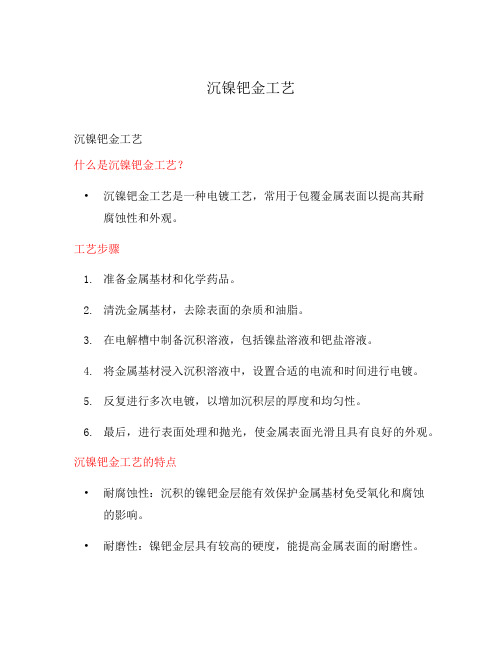
沉镍钯金工艺沉镍钯金工艺什么是沉镍钯金工艺?•沉镍钯金工艺是一种电镀工艺,常用于包覆金属表面以提高其耐腐蚀性和外观。
工艺步骤1.准备金属基材和化学药品。
2.清洗金属基材,去除表面的杂质和油脂。
3.在电解槽中制备沉积溶液,包括镍盐溶液和钯盐溶液。
4.将金属基材浸入沉积溶液中,设置合适的电流和时间进行电镀。
5.反复进行多次电镀,以增加沉积层的厚度和均匀性。
6.最后,进行表面处理和抛光,使金属表面光滑且具有良好的外观。
沉镍钯金工艺的特点•耐腐蚀性:沉积的镍钯金层能有效保护金属基材免受氧化和腐蚀的影响。
•耐磨性:镍钯金层具有较高的硬度,能提高金属表面的耐磨性。
•外观美观:经过表面处理和抛光后,沉镍钯金层具有金属光泽和良好的外观。
应用领域•高端饰品:沉镍钯金工艺常用于镀饰品,提供耐腐蚀性和精美的外观。
•电子行业:电子器件常使用沉镍钯金工艺,以保护导电元件免受腐蚀。
•汽车制造:部分汽车零部件经过沉镍钯金工艺处理,提高其耐用性和外观质量。
结论沉镍钯金工艺是一种常用的电镀工艺,能为金属表面提供耐腐蚀性和外观美观。
其特点包括耐腐蚀性、耐磨性和外观美观。
在饰品、电子行业和汽车制造等领域有广泛的应用。
工艺优势沉镍钯金工艺具有以下优势:1.耐腐蚀性强:通过沉积镍钯金层,金属基材的表面能够形成一层保护膜,有效防止氧化和腐蚀的影响,延长金属的使用寿命。
2.耐磨性高:沉积的镍钯金层具有较高的硬度和抗磨损能力,能够提高金属表面的耐磨性,减少因摩擦而引起的损坏。
3.良好的外观效果:经过表面处理和抛光后,沉镍钯金层具有金属光泽和良好的外观质量,提升产品的品质和档次。
4.成本效益高:与其他表面处理方法相比,沉镍钯金工艺的成本相对较低,但能够达到相似的耐腐蚀性和外观效果,使其成为许多行业的首选工艺。
注意事项在进行沉镍钯金工艺时,需要注意以下事项:1.安全操作:工艺中使用的化学药品具有一定的危险性,需要穿戴个人防护装备,确保操作者的安全。
表面处理之化学沉镍金

化学沉镍金部分本公司EC-303系列为弱酸性镍/磷合金化学镍镀液,具有如下特性:、镀层磷含量稳定,镀层组成Ni93±1% P 7±1% 。
、适用于PCB/FPC沉镍金,FPC沉镍金时仅镍缸参数有所不同。
、操作温度范围宽,对绿油攻击极小。
、槽液稳定,管理简易方便,镍槽可使用自动加药装置。
、化学镍沉积速率稳定:PCB一般为10~13um/hr,FPC一般为8~11 um/hr。
、生产中前后制程对化学沉镍金的影响生产中前后制程对化学沉镍金的影响、板材:特殊板材吸附钯能力特强,在水洗不足或镍缸活性较强时,易出现渗镀现象。
如一些无卤素单面板材,孔及背面易上镍金。
一般采用过毒钯液处理或适当降低镍缸活性做板,即可避免。
、钻孔:钻孔进、退刀速率控制不良,钻咀刀锋前缘有损坏,导致钻孔后孔壁太粗糙,则化镍金时N-PTH孔易上镍金。
、图形制作/图形电镀:在线路制作工序,因板面显影不良易导致图形电镀时板面粗糙、发白。
此类缺陷是电镀铜后夹在铜层下面,经表面处理无法去除,而在化镍金时镍层无法掩盖此缺陷,最终的结果直接导致报废。
图形电铜面本身颗粒、针孔、发白、子弹孔等问题在化镍金时亦会呈现类似问题。
、蚀刻/退锡:蚀刻不净问题,在化镍金时可能会长胖或架桥,或N-PTH孔上镍金;有NPTH孔的化镍金板在蚀刻后、退锡前需做毒钯处理,否则NPTH孔容易上Ni/Au;剥锡不净问题,在化镍金时可能会出现白点或露铜甚至甩镍金现象。
丝印阻焊油:渗油(干绿油)、显影不净(感光绿油)等常见问题,在化镍金时极易出现发白、漏镀或甩镍金;油墨烘烤不够,曝光能量过低或者油墨厚度低于15um,在化镍金后极易出现掉油,油墨起泡。
曝光菲林上有垃圾时,化镍金后防焊油墨会点状上镍金。
若显影液残留板面未处理干净则化镍金时容易出现白点与阴阳色问题。
、化镍金前处理的刷磨:.最好使用800#以上或1000#、1200#磨辘细磨,磨辘太粗磨痕太深,化镍金时,金面可能会粗糙或发白,同时也会伤及阻焊油与保护膜,刷磨太轻太浅,则达不到应有的效果。
沉镍金技术详解

沉镍金生产操作技术一、流程及操作条件1、酸性清洁剂用于去除铜面轻度油脂及氧化物,使铜面清洁及增加润湿性操作条件:清洁剂80~120ml/L温度40-60℃时间3~7min过滤5~10umPP滤芯边疆过滤搅拌摆动及循环搅拌配制方法:A、加入纯水到槽体的2/3。
B、加入清洁剂C、充分搅拌至完全混合D、加纯水调整液位。
铜溶解速率:每小时约0.4微英寸。
补充及更新:每生产一平米补充清洁剂10ML/L每一升槽液处理4-6平米或铜含量达250PPM须更新。
2、微蚀用于使铜面微粗糙化,增加铜与化学镍层的密着性。
操作条件:SPS 80~120G/L硫酸15-35ML/L铜含量3-20G/L温度室温时间1~3MIN搅拌摆动、循环及打气搅拌配制方法:A、加入纯水至槽体的2/3B、加入硫酸及过硫酸钠C、充分搅拌到完全溶解D、加纯水调整液位补充及更新:每生产一平米须补充SPS15-25G铜含量达20G/L时须更新。
注意:温度越高咬蚀铜的速率就越快。
槽液的铜含量越高,咬蚀的速率就越慢。
3、酸洗用于去除微蚀后铜面氧化物,增加与化学镍层的密着性。
操作条件:硫酸(98%)40-70ML/L温度室温时间1-3MIN搅拌摆动及循环搅拌配制方法:A、加入纯水至槽体的2/3B、加入硫酸C、充分搅拌到完全混合D、加纯水调整至液位补充及更新:每一平米补充硫酸2-5ML每1L槽液处理4-6平米或铜含量达2000PPM时须换槽4、活化在铜面上析出一层钯,做为化学镍启始反应的触媒。
操作条件:活化剂80-120ML/L温度25-35℃处理时间1-4MIN过滤1~2UMPP滤芯过滤搅拌摆动及循环搅拌配制方法:A、加入纯水至槽体2/3B、加入活化剂并充分搅拌C、加纯水调整液位活化槽硝槽程序:A、加入30-40%的硝酸B、启动循环泵循环2小时以上或直到槽壁灰黑色沉积物完全去除为止(如有需要可加热至40-50度)C、排出硝酸液,并加水循环10-20分钟后,排放,至少更换两次以上。
PCB沉金工艺介绍解析
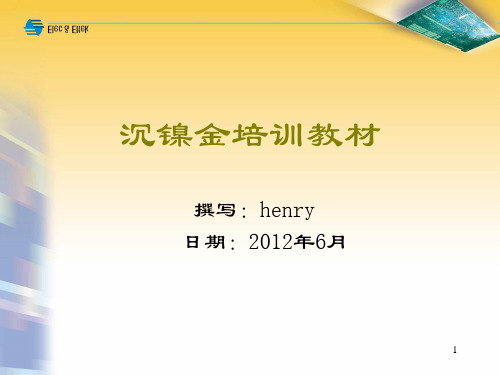
4、预浸
作用:
维持活化缸的酸度及使铜面在新鲜状 态(无氧化物)的情况下,进入活化缸。
操作条件:
温度: 时间: 搅拌: 槽材质: 室温 1±0.5min 摆动及药液循环搅拌 PVC或PP
18
作用: 在电化序中,铜位于镍的后面,所以必须 将铜面活化,才能进行化学镀镍。PCB行 业大多是采用先在铜面上生成一层置换钯 层的方式使其活化。 反应式:Pd2++Cu Pd+Cu2+ PCB沉镍金工序之活化剂一般为硫酸型和 盐酸型两种,现较多使用硫酸型钯活化液。 行业中也有使用Ru(Ruthenium)做催化 晶核,效果也较为理想。
42
操作条件
A、温度 不同系列的沉镍药水其控制范围不 同。一般情况下,镍缸的操作范围是 86±50C,有的药水则控制在81±50C。 具体操作温度应根据试板结果来定, 不同型号的制板,有可能操作温度不同。 一个制板的良品操作范围一般情况下只 有±20C,个别制板也有可能小于±10C.
41
•E、镀液应连续过滤,以除去溶液中的 固体杂质。镀液加热时,必须要有空气 搅拌或连续循环系统,使被加热的镀液 迅速扩散开。当槽内壁镀有镍层时,应 及时用硝酸(1:3)褪除,适当时可考虑加 热,但不可超过50OC, 以免污染空气。 •F、镀液寿命一般控制在4MTO(即Ni离 子添补量累积达到4倍开缸量),超过此 限主要问题是镍厚不足。
29
C、缓冲剂、络合剂 缓冲剂主要用处是维持镀液的pH值防止化学镀镍 时由于大量析氢所引起的pH值下降 络合剂作用主要是与镍离子进行络合降低游离镍 离子的浓度,提高镀液的稳定性。
一般均使用NaH2PO2,其控制浓度一般为2040g/l。在镀液中,主反应将Ni2+还原成为 金属Ni,副反应为其本身的歧化反应生成 单质P,主反应及副反应过程中均伴随H2逸 出。
沉镍金制作流程

沉镍金制作流程一、简介:通过化学反应在铜表面沉积较薄一层镍金、金层具有稳定的化学和电器特性,镀层具有优良的可焊性,耐蚀性等特点。
二、流程及作用:(1)沉金前处理:①微蚀:除去烘烤绿油造成的铜面过度氧化物。
② 1200#磨刷幼磨:除去铜面杂物,清洁板面。
(2)沉镍金流程:上板→除油→Ⅱ级水洗→微蚀→→Ⅱ级水洗→酸洗→Ⅱ级水洗→预浸→活化→Ⅱ级水洗→后浸酸→Ⅰ级水洗→沉镍→Ⅱ级水洗→沉金→金回收→水洗→热水洗→下板①除油:除去铜表面之轻度油脂及氧化物,使表面活化及清洁。
②微蚀:除去铜面氧化物及污染物,适度粗化铜面,增加镀层密着性、结合力。
③预浸:保护活化药液。
④活化:使用离子钯溶液使表面铜活化,可以只在铜面上沉积而基材的Pd化合物极易清洗,提供化学沉镍的启镀剂。
⑤化学镀镍:利用电子转移使溶液中的Ni2+还原在待镀铜面上而沉积出镍金属:但同时会有P析出,Ni层实际为Ni/P合金,Ni层厚度一般为100-200u〃。
⑥通过置换反应在新鲜镍面置换一层薄金,作为防止基体金属氧化和作为自身活化型镀金的底层,镍基体上覆盖一层金后金沉积就停止,所以厚度有一定了限制,Au层厚度一般为1-3 u〃。
(3)沉金后处理:①草酸洗:除去金面氧化异物,,对金层疏孔处的镍底层作酸封孔处理,增加其耐蚀性。
②抗氧化清洗:防止镀层氧化,使焊锡维持更长的寿命。
三、流程控制注意事项:(1)控制微蚀速率在0.6-0.8um,速率太低,镀层发亮,太高出现色差即金色不良。
(2)活化缸Cu2+浓度≤200PPM需更换,且后期易出现渗金。
(3)Ni缸温度不可太高,药水高温对绿油攻击较大,易出现甩S/M问题,槽液使用4.0MTD后需换槽。
(4)金缸需控制Ni2+含量≤800PPM,Ni2+太高易出现金色不良及不上金问题。
四、常见问题介绍及处理方法:(1)漏镀:①活化浓度温度过低,浴老化或活化后水洗过久。
②镍缸浓度、温度、PH值太低,或有不以纯物混入,成份失调。
化学沉镍工艺

化学沉镍工艺
化学沉镍工艺是一种利用化学方法在金属表面沉积镍层的工艺。
它是将金属表面通过一系列的化学反应处理,使得金属表面上形成一层均匀的、致密的、具有良好附着力的镍层。
这种工艺可以有效地提高金属件的耐腐蚀性、硬度和耐磨性,并且可以使金属件具有更好的外观和更长的使用寿命。
化学沉镍工艺的基本步骤包括表面处理、预处理、镀镍、后处理等几个环节。
在表面处理环节中,需要对金属表面进行清洗、去油、除锈等处理,以保证金属表面的洁净度。
在预处理环节中,需要进行活化处理、酸洗处理等,以提高金属表面的光洁度和附着力。
在镀镍环节中,需要将金属件浸泡在镍盐溶液中,并通过电解反应将镍离子还原成为金属镍,并沉积在金属表面上。
在后处理环节中,需要对沉积在金属表面上的镍层进行处理,以提高其硬度和耐腐蚀性。
化学沉镍工艺具有成本低、工艺简单、镀层均匀、硬度高、附着力强等优点。
它广泛应用于航空、航天、汽车、电子、机械等领域中,可以为这些领域提供高质量的金属表面处理服务。
同时,化学沉镍工艺也存在一些缺点,比如对环境有一定的污染、工艺条件要求较高等。
沉镍金制作流程范文

沉镍金制作流程范文沉镍金是一种具有高精度、高硬度、高抗磨损性和耐蚀性的金属材料,广泛应用于电子器件、机械工具和汽车零部件等领域。
沉镍金的制作流程主要包括镀液制备、金属基材准备、沉镍金层的成型和后处理等环节。
以下是一个关于沉镍金制作流程的详细介绍。
一、镀液制备1.选择合适的化学品:镀液通常由羧酸镍、硫酸镍、草酸钠、硼酸和一些添加剂组成。
这些化学品具有良好的镀液稳定性和金属沉镍层的特性。
2.准备盛装器皿:选择一种能耐受镀液的器皿,如玻璃或聚丙烯材料制成的容器。
将容器清洗干净,并确保无存留的杂质。
3.称量化学品:根据制定的镀液配方,按照比例称取所需化学品,并严格控制各组分的配比。
4.配制镀液:将称取的化学品逐一加入容器中,按照特定的操作流程进行搅拌和配制,使其充分溶解和混合,形成均匀的镀液。
二、金属基材准备1.选择合适的基材:沉镍金可用于镀液重金属基材,如钢、铜、铝等。
选用基材需要根据实际使用环境和需求来确定。
2.基材的表面处理:首先,将基材进行清洗,去除表面的油污和杂质。
然后,通过酸洗、电解去氧等工艺,处理基材表面,以提高沉镍金层与基材的结合力和附着力。
三、沉镍金层的成型1.工艺参数设定:根据具体的工艺要求和所制备镀液的特点,设置适当的工艺参数,如温度、pH值、电流密度等。
2.浸泡基材:将经过处理的金属基材浸泡入镀液中,然后在规定的时间内进行电解反应。
镀液中的阳极引入电流,从而在基材上形成沉镍金层。
3.调整电流和工艺参数:根据实际观察和测量,适时调整电流密度和工艺参数,以确保沉镍金层的成型质量。
同时,根据需要,可以进行多次电镀,以增加金属层的厚度。
四、后处理1.水洗:将沉镍金层的基材进行水洗,以去除残留的镀液和杂质。
2.烘干:将水洗后的基材进行烘干处理,以去除水分。
3.烧结:为提高沉镍金层的致密性和硬度,将烘干的基材进行烧结处理,以达到金属层充分结合的目的。
4.研磨和抛光:对烧结后的沉镍金层进行研磨和抛光,以提高表面光洁度和平整度。
无电沉镍工艺流程

无电沉镍工艺流程
无电沉镍是一种常用的金属表面处理方法,主要用于给金属制品镀上一层具有良好耐蚀性和装饰性的镍层。
下面将介绍一下无电沉镍的工艺流程。
首先,准备金属工件。
将需要进行无电沉镍的金属工件进行表面清洁,去除表面的油污、尘土和氧化物等。
清洁方法可以采用化学清洗或机械清洗的方式。
其次,进行除油处理。
将已经清洁好的金属工件进行除油处理,以保证镍层的附着力和光泽度。
除油处理可以通过浸泡法或喷洒法进行,常用的除油剂有有机溶剂和碱性溶剂。
接着,进行活化处理。
活化处理的目的是去除金属表面的氧化物,以提高镍层的附着力。
活化处理可采用酸性活化液进行,常用的活化液有硫酸、盐酸和磷酸等。
然后,进行无电沉镍。
将已经完成活化处理的金属工件,放入含有镍离子的溶液中进行无电沉镍。
镍离子溶液中的镍离子将在金属工件表面还原成金属镍,并与金属工件表面的活化层发生反应,形成一层均匀致密的镍层。
镍离子溶液的配方根据需求的镍层厚度和镍层性能来确定。
最后,进行后处理。
无电沉镍完成后,需要进行后处理以提高镀层的亮度和光泽度。
后处理可采用酸洗或热处理的方式进行。
酸洗可去除镀层表面的杂质和氧化物,热处理可提高镀层的致密度和光泽度。
总结一下无电沉镍的工艺流程:金属工件清洁→除油处理→活化处理→无电沉镍→后处理。
这个流程简单明了,能够保证无电沉镍工艺的顺利进行,镀层的质量稳定可靠。
无电沉镍不仅可以提高金属工件的耐蚀性能,还可以美化金属表面,延长使用寿命。
因此,无电沉镍工艺在金属制品的制造和加工中得到了广泛应用。
化学镍金工艺探讨
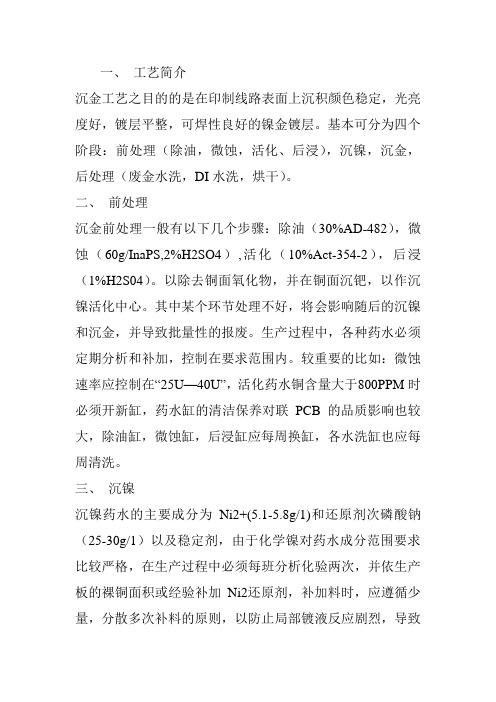
一、工艺简介沉金工艺之目的的是在印制线路表面上沉积颜色稳定,光亮度好,镀层平整,可焊性良好的镍金镀层。
基本可分为四个阶段:前处理(除油,微蚀,活化、后浸),沉镍,沉金,后处理(废金水洗,DI水洗,烘干)。
二、前处理沉金前处理一般有以下几个步骤:除油(30%AD-482),微蚀(60g/InaPS,2%H2SO4),活化(10%Act-354-2),后浸(1%H2S04)。
以除去铜面氧化物,并在铜面沉钯,以作沉镍活化中心。
其中某个环节处理不好,将会影响随后的沉镍和沉金,并导致批量性的报废。
生产过程中,各种药水必须定期分析和补加,控制在要求范围内。
较重要的比如:微蚀速率应控制在“25U—40U”,活化药水铜含量大于800PPM时必须开新缸,药水缸的清洁保养对联PCB的品质影响也较大,除油缸,微蚀缸,后浸缸应每周换缸,各水洗缸也应每周清洗。
三、沉镍沉镍药水的主要成分为Ni2+(5.1-5.8g/1)和还原剂次磷酸钠(25-30g/1)以及稳定剂,由于化学镍对药水成分范围要求比较严格,在生产过程中必须每班分析化验两次,并依生产板的裸铜面积或经验补加Ni2还原剂,补加料时,应遵循少量,分散多次补料的原则,以防止局部镀液反应剧烈,导致镀液加速老化,PH值,镀液温度对镍厚影响比较大,镍药水温度抄袭控制在85℃-90℃。
PH在5.3-5.7,镍缸不生产时,应将镍缸温度降低至70℃左右,以减缓镀液老化,化学镍镀液对杂质比较敏感,很多化学成分对化学镍有害,可分为以下几类:抑制剂:包括Pb.Sn..Hg.Ti.Bi(低熔点的重金属),有机杂质包括S2,硝酸及阴离子润湿剂。
所有这些物质都会降低活性,导致化学镀速度降低并漏镀,严惩时,会导致化学镀镍工艺完全停止。
有机杂质:包括:除以上所提到的有机的稳定剂以外,还有塑料剂以及来自于设备和焊锡的杂质。
尽管可通过连续镀清除一部分杂质,但不能完全清除。
不稳定剂:包括Pd和少量的铜,这两种成分造在化学镍不稳定,使镀层粗糙,而且过多地镀在槽壁及加热器上。
关于沉镍金工艺在镍层产生裂痕问题的机理
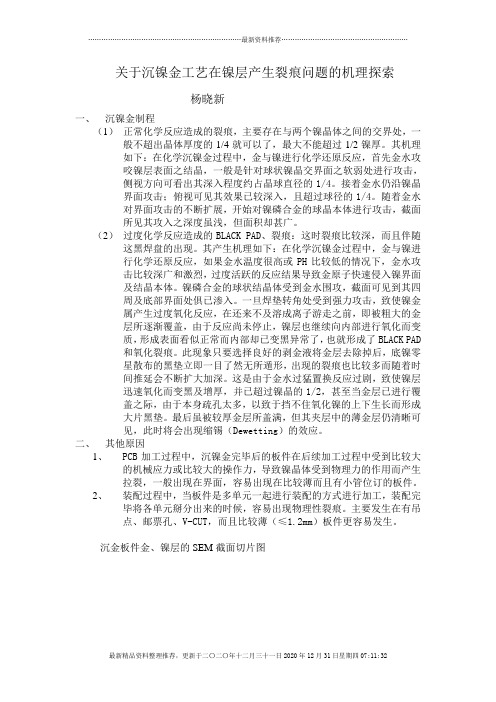
关于沉镍金工艺在镍层产生裂痕问题的机理探索杨晓新一、沉镍金制程(1)正常化学反应造成的裂痕,主要存在与两个镍晶体之间的交界处,一般不超出晶体厚度的1/4就可以了,最大不能超过1/2镍厚。
其机理如下:在化学沉镍金过程中,金与镍进行化学还原反应,首先金水攻咬镍层表面之结晶,一般是针对球状镍晶交界面之软弱处进行攻击,侧视方向可看出其深入程度约占晶球直径的1/4。
接着金水仍沿镍晶界面攻击;俯视可见其效果已较深入,且超过球径的1/4。
随着金水对界面攻击的不断扩展,开始对镍磷合金的球晶本体进行攻击,截面所见其攻入之深度虽浅,但面积却甚广。
(2)过度化学反应造成的BLACK PAD、裂痕:这时裂痕比较深,而且伴随这黑焊盘的出现。
其产生机理如下:在化学沉镍金过程中,金与镍进行化学还原反应,如果金水温度很高或PH比较低的情况下,金水攻击比较深广和激烈,过度活跃的反应结果导致金原子快速侵入镍界面及结晶本体。
镍磷合金的球状结晶体受到金水围攻,截面可见到其四周及底部界面处俱已渗入。
一旦焊垫转角处受到强力攻击,致使镍金属产生过度氧化反应,在还来不及溶成离子游走之前,即被粗大的金层所逐渐覆盖,由于反应尚未停止,镍层也继续向内部进行氧化而变质,形成表面看似正常而内部却已变黑异常了,也就形成了BLACK PAD和氧化裂痕。
此现象只要选择良好的剥金液将金层去除掉后,底镍零星散布的黑垫立即一目了然无所遁形,出现的裂痕也比较多而随着时间推延会不断扩大加深。
这是由于金水过猛置换反应过剧,致使镍层迅速氧化而变黑及增厚,并已超过镍晶的1/2,甚至当金层已进行覆盖之际,由于本身疏孔太多,以致于挡不住氧化镍的上下生长而形成大片黑垫。
最后虽被较厚金层所盖满,但其夹层中的薄金层仍清晰可见,此时将会出现缩锡(Dewetting)的效应。
二、其他原因1、PCB加工过程中,沉镍金完毕后的板件在后续加工过程中受到比较大的机械应力或比较大的操作力,导致镍晶体受到物理力的作用而产生拉裂,一般出现在界面,容易出现在比较薄而且有小管位订的板件。
- 1、下载文档前请自行甄别文档内容的完整性,平台不提供额外的编辑、内容补充、找答案等附加服务。
- 2、"仅部分预览"的文档,不可在线预览部分如存在完整性等问题,可反馈申请退款(可完整预览的文档不适用该条件!)。
- 3、如文档侵犯您的权益,请联系客服反馈,我们会尽快为您处理(人工客服工作时间:9:00-18:30)。
一,引言自1997年以来,化学镍金工艺在国内得到迅速推广,这得益于化学镍金工艺本身所带来种种优点。
由于化学镍金板镍金层的分散性好、有良好的焊接及多次焊接性能、良好的打线(Bonding,TS Bond或U Bond)性能、能兼容各种助焊剂,同时又是一种极好的铜面保护层。
因此,与热风整平、有机保焊膜(OSP)等PCB表面处理工艺相比,化学镍金镀层可满足更多种组装要求,具有可焊接、可接触导通、可打线、可散热等功能,同时其板面平整、SMD焊盘平坦,适合于细密线路、细小焊盘的锡膏熔焊,能较好地用于COB及BGA的制作。
化学镍金板可用于并能满足到移动电话、寻呼机、计算机、笔记型电脑、IC 卡、电子字典等诸多电子工业。
而随着这些行业持久、迅猛的发展,化学镍金工艺亦将得到更多的应用与发展机会。
化学镍金工艺,准确的说法应为化镍浸金工艺(Electro-less Nickel and Immersion Gold Pro-cess,即ENIG),但现在在业界有多种叫法,除”化学镍金”、”化镍浸金”外,尚有”无电镍金”、”沉镍金”。
国内PCB行业多用”沉镍金”一词来谈论这一工艺,因而在本文中,我们也将用”沉镍金”来表述化镍浸金。
二,沉镍金原理概述沉镍金工艺的原理,实际上反而从”化镍浸金”一词中能够较容易地被我们所理解。
即其中镍层的生成是自催化型的氧化-还原反应,在镀层的形成过程中,无需外加电流,只靠高温(880C左右)槽液中还原剂的作用,即可在已活化的铜表面反应析出镍镀层,而金镀层的生成,则是典型的置换反应。
当PCB板进入金槽时,由于镍的活性较金大,因而发生置换反应,镍镀层表面逐渐被金所覆盖。
以下简单介绍一个沉镍金的反应过程:1,沉镍的化学反应:关于沉镍的反应机理,曾有多篇文章提及。
其过程基本上用一个反应式即可表达:在上述各反应式中,可看到一个自催化氧化-还原反应的典型模式。
而在上述各反应中,需要注意的是反应⑤⑥,从中我们可看到有单体磷的生成,在沉镍过程中,此单体磷亦会一并沉于镍层中,因而,事实上的沉镍层,是磷镍构成。
正常情况下,磷的含量应在8%-12%之间,磷含量的多少对PCB板的焊接性能极具影响。
由此,还会引出另外一个关于测量的问题,在目前的大多数PCB厂家及其客户处,金、镍层厚度的测定,普遍采用X-ray镀层测厚仪,但当购买仪器时,仪器制造商所提供的镍标准片均为纯镍片(除非特别指定),用这样的标准片校核之后,再来测沉镍金板,则所测得的镍厚与实际镍厚有一明显偏差,一般的,实际厚度应为X-ray机测得厚度的1.15至1.20倍,我们曾多次通过金相切片的方式证实此点。
2,沉金的化学反应此置换反应的机理较简单,用下式即可表述:从这个反应式亦可大致想见沉镍后的板在金缸中的反应情形:在镍层表面逐渐被金所覆盖的过程中(包括疏孔),上述反应会越来越慢直至终此。
因而沉金层能够做到的厚度是有限的,大致在0.15μm左右。
三,沉镍金实际生产应用为顺应市场的变化需求,我公司于97年引入了沉镍金线,其基本流程如下:上板→除油→二级水洗→微蚀→二级水洗→预浸→活化→二级DI水洗→沉镍→镍回收→二级DI水洗→沉金→金回收→DI水洗→热DI水洗→烘干→下板。
基于上述流程,再结合我们实际生产经验,我们认为:合理的流程、设备设计、对预防和减少某些工艺问题非常重要,而相关工序工艺、生产用水等方面的控制亦至关紧要。
1,缸体排布在新设计沉镍金线或将旧生产线改造成沉镍金线时,如何根据生产流程优化缸位排布显得极其重要。
如果设计得当,可避免许多难以预料的工艺问题。
因此,绝对应当事先多花功夫去研究哪一种缸体排布或怎样的一个行车程序是最合理的、所带来的生产问题可能减到最小。
例如:沉镍金板可焊性不良的问题,除了板面污染外,镍面钝化是很主要的一个成因,要防止镍面钝化,就必须考虑到沉镍、沉金之间的控制,包括行车时间长短、滴水时间长短(这些是板在空气中的停留时间);水洗(尤其是DI水洗)及空气搅拌的大小。
因此,镍缸与金缸之间的距离不能相距太远。
此外,活化缸不宜太靠近镍缸,否则,药水的交叉污染(行车移动时的飞巴滴液、镍缸的热蒸气滴液等)会使缸寿命变短及严重影响生产板品质。
2,镍缸设计镍缸是整条生产线的心脏部分,镍缸设计的好坏,直接影响到生产能否正常进行,这是因为镍缸在整个流程中是最难控制的。
现在,常用的用于制作镍缸缸体的材料有两种:一种是PP;另一种是316不锈钢。
对于PP缸,一般需在缸内壁套上表面光滑的PNN,且在缸壁内镶不锈钢板,以增加强度。
这种缸,生产初期一般较为理想,但生产至约2个MTO(Metal Turn Over)或由于产量不足而经常出现升温、降温的情况时,会有较多的镍渣产生,当镍渣的数量达到某一程度后,会超过镍缸所能承受的负荷,镍渣在镍缸中产生自催化剧烈反应,造成反应失控(俗称反缸),导致生产不能正常进行。
此时,解决的方法是:停止生产,把药水过滤到另外一个槽内,除掉镍渣,方可继续生产。
因此,在用PP缸时,一般每2个MTO需倒一次缸,这不仅影响产能,也容易浪费药液。
而使用316不锈钢材料制作的镍缸,通过外加电压,抑制渣的形成,从而保证正常稳定的生产。
其具体做法是:在镍缸缸壁上接一根或几根导线使整个缸体作为阳极,而在镍缸药水中放置一定数量的316不锈钢棒作为阴极,然后再加上一稳压电源,电压大小应保持在0.8-1.2V之间(镍缸事先需用50%体积比的HNO3浸泡,把316不锈钢缸缸壁钝化,形成一较大电阻)。
当镍渣沉积到一定程度,缸壁的电阻会慢慢变小,在0.8-1.2V的恒定电压下,电流会逐渐增大,根据实际生产经验,当在0.9V的恒定电压下,电流至1.8-2.0A时,缸内反应就会变得剧烈,有”反缸”的危险,此时,需把药水温度迅速降至700C以下,把药水过滤到另一个缸,一般地,如无特殊情况,一个镍缸可生产到5个MTO,电流才升至1.8-2.0A.因此,与PP缸相比较,不锈钢缸可节省保养镍缸的时间,延长药水的使用寿命,降低生产成本。
此外,还有一种镍缸的设计较特别,它在镍缸的底部安上转动凸轮,使得镍缸可上下振动,这对赶走附在板面或孔中的氢气泡是一种好方法,尤其在制作1.0mm以上厚度、含小孔(ψ0.35mm)的大拼板时,对改善孔内漏镀很有帮助。
镍缸尚有一不为人关注的问题,就是加热器的漏电现象,因镍缸需高温生产,故缸中(或其子缸中)会有多根加热器。
因此,须特别注意加热器是否漏电,一旦发生漏电现象(尤其是间歇性漏电),则生产出来的板五花八门。
往往花费许多精力也查不出个所以然,我们知道有数间工厂都发生过此类问题,所以每次生产前、生产中最好检查一下这种情况。
在镍缸的设计过程中,最好药水供应商也能参与过来,因目前沉镍金药水基本分为两大体系:即盐酸体系和硫酸体系。
这二种体系对镍缸的要求是不同的(如盐酸体系需打气、硫酸体系则不需)。
因此,各工厂可根据自己的运行系统和经验,意向性地确认好选用的药水体系后,再与药水供应商、设备供应商一起讨论镍缸的设计为好。
镍缸的循环过滤泵的选择也是一件令人头痛的事,我们经过多次改进,最终选择直立式耐高温、耐强碱、强碱泵。
3,挂具设计挂具在设计中容易被忽视,但在生产中又显得十分重要,其一般有两种设计方案,一种为狗骨架设计,另一种为挂篮设计。
两种挂具各有优势。
生产中可根据生产板的特点而择优选择。
狗骨架挂板时,上部通过板子板边上预留的两个孔把板子串在不锈钢条上,每块板之间用PP条隔开,下面用绳子串起来,并用胶把板子分隔开来,狗骨架的设计优点在于:滴水干净,缸与缸的交叉污染小,挂具保养简单及占用空间小。
但上板操作较为复杂。
而挂篮的设计则有利于操作,它表面包一层Teflon,且通过梳齿把板子分隔开并定位。
由于挂篮四周有固定铜条,在缸内摇摆效果佳,有利于赶走小孔内的气泡,且对于大拼板时的薄板(0.5mm以下)生产有利,不易出现叠板现象,但挂篮保养复杂,缸与缸之间交叉污染较大,需用较大水流量清洗,一般来讲,对于大拼板板子的生产,采用挂篮设计较为有利。
4,DI水的使用沉镍金生产过程中,”清洗生产”的要领十分重要,因沉镍金制程相当敏感、抗污染程度低,因此,生产中所使用的各种化学试剂如硫酸、过硫酸钠等都应是CP级以上的。
DI水的使用更是必不可少,所有的药水槽必须用DI水开缸、补充液位。
同时,清洗药水槽时最后也应该用DI水循环清洗二次。
在镍缸、金缸前后均应至少各有一道DI水洗。
并且对DI 水的品质亦须经常监测,尤其要注意其中的CI一含量。
此外,在沉镍金之后的工序中,对沉镍金板也须格外保护,一定要使用DI水来洗板。
同时注意在清洗或烘干过铜板、喷锡板后,再用同一部机器进行沉镍金板生产时,务必将机器清洗干净。
否则,残存的Cu2+、Sn会对沉镍金板产生严重影响。
四,沉镍金生产中的一些问题和解决方法由于沉镍金制程敏感,沉镍金板有多种用途,且表观要求极严。
因此,沉镍金板生产中所遇到的问题五花八门,绝对可以写成一本书。
因为一种现象可能有几种原因,做十几个试验才能确定真正成因是经常的事。
所幸在生益电子有限公司,经过最初两、三个月的摸索,制程即已完全受控。
近几年的大批量生产过程一直稳定在一个极高的水准上,广受客户好评。
沉镍金板生产过程中常见的一些问题及解决方法可用下表1表示:在生产中,须特别注意前工序(W/F)与沉镍金工序的工艺配合。
目前,仍有部分厂家认为,沉镍金板所用的W/F应特别选定,要求其耐化学冲击能力强。
但事实上,经我们研究,目前常用的一些W/F品牌如Tamura DSR-2200 C-7BSX、Tamura DSR-2200K-31D、Taiyo PSR 4000 Z-26、LeaRonal OPSR-5600GM等,都可以找到一个合适的参数来生产沉镍金板,即使经历最严格的测试也毫无问题。
W/F工序尤须注意显影及阻焊油墨塞孔这两点,前者对沉镍金板表观大有影响,而后者更直接牵涉到漏镀现象(见参考文献[1])。
这里顺便提一下字符的制作,一般都认为,字符应在沉镍金前制作完毕,以防金面受到污染(台湾的白蓉生先生也持这一观点,见参考文献[2],但根据我们的经验,字符应该在沉镍金后制作,因为字符油墨可能会受到沉镍金药水的攻击而改变结构,就我们所用的白字油墨而言,即会发生这种现象,我们曾用谱图证明这一点。
这种现象所表现出来的情况是:字符在生产厂家没有问题,表观亦无异常,但在客户处经回流焊或波峰焊后,则字符(尤其是字符块)会变成粉红色,从而遭致客户投拆和退货。
一沉镍金常见问题及解决方法。