组装不良的改善对策报告案例
组装部改善报告
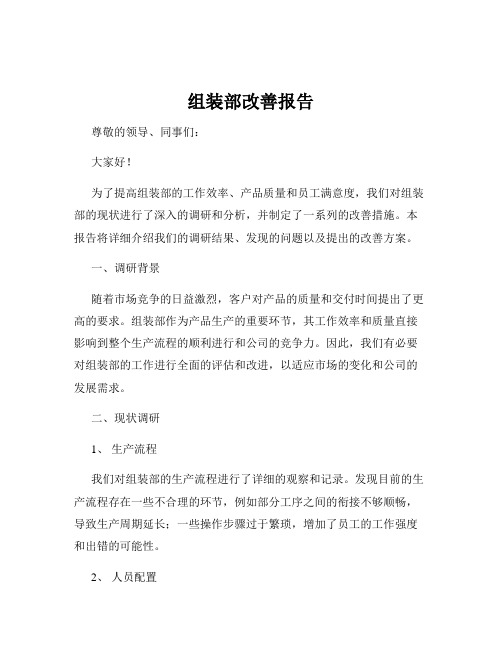
组装部改善报告尊敬的领导、同事们:大家好!为了提高组装部的工作效率、产品质量和员工满意度,我们对组装部的现状进行了深入的调研和分析,并制定了一系列的改善措施。
本报告将详细介绍我们的调研结果、发现的问题以及提出的改善方案。
一、调研背景随着市场竞争的日益激烈,客户对产品的质量和交付时间提出了更高的要求。
组装部作为产品生产的重要环节,其工作效率和质量直接影响到整个生产流程的顺利进行和公司的竞争力。
因此,我们有必要对组装部的工作进行全面的评估和改进,以适应市场的变化和公司的发展需求。
二、现状调研1、生产流程我们对组装部的生产流程进行了详细的观察和记录。
发现目前的生产流程存在一些不合理的环节,例如部分工序之间的衔接不够顺畅,导致生产周期延长;一些操作步骤过于繁琐,增加了员工的工作强度和出错的可能性。
2、人员配置通过对组装部人员的调查和分析,发现存在人员配置不合理的情况。
部分岗位人员过剩,而一些关键岗位人员不足,导致工作分配不均衡,影响了整体工作效率。
3、设备状况对组装部所使用的设备进行检查,发现部分设备老化、故障率较高,影响了生产的正常进行。
同时,一些设备的性能无法满足生产的需求,需要进行升级或更换。
4、物料管理在物料管理方面,存在物料供应不及时、物料质量不稳定等问题。
物料的存放和领取流程不够规范,导致物料浪费和寻找物料的时间过长。
5、质量控制对组装部的产品质量进行抽查,发现存在一定比例的不合格产品。
质量控制体系不够完善,员工的质量意识有待提高,部分工序缺乏有效的质量检验环节。
三、问题分析1、流程优化不足生产流程没有经过系统的优化和改进,导致工序之间的协调性差,工作效率低下。
2、人力资源管理不善人员配置没有根据工作任务和员工技能进行合理安排,缺乏有效的绩效考核和激励机制,导致员工工作积极性不高。
3、设备维护与更新不及时对设备的维护和保养工作不够重视,没有制定合理的设备更新计划,导致设备性能下降,影响生产效率和产品质量。
不良品改善报告范文(3篇)

不良品改善报告范文第1篇P:计划(一)制定改善计划20xx年1月P公司派训的L工程师结训回到企业后,立即深入现场进行问题调研,再结合参训前收集的现场管理问题点,然后召集改善工作筹组会议决定IE改善工作小组由工艺部工程师、生产副总、车间主管、品检工程师等8位成员共同组成,并由工艺部L 工程师担任IE改善工作小组组长,制定出每位小组成员的工作职责及IE改善小组的工作计划。
IE改善小组将IE改善工作主题聚焦于车间制程的改善及标准化。
(二)设定改善目标两周后,改善小组就改善主题对P公司的生产流程及产品的现况展开讨论,发现车间生产效率仅有61%,改善小组随即运用SMART原则来进行改善目标设定,并将改善目标设定为:1、从简化生产流程设计上入手,运用作业程序(流程)分析手法来降低产品加工成本,在现有成本基础上降低15%。
2、通过生产线工站重新部置及人员编成,运用IE手法使生产线平衡,并提高装配效率,在现有的基础提升55%。
3、改善时间为五个月(20xx年1月20xx年5月)。
改善目标确定下来,改善小组立即将主题及目标进行分解成小项目,由改善小组成员分别负责各个小项目,进行团队合作。
并定每两周召开一次改善小组会议,共同探讨实现目标的方法。
D:执行(一)执行改善对策20xx年1月下旬改善小组召开二次改善小组会议,共同探讨改善对策。
决议改善初期先设计几组新规格的模具投入生产流程中进行改善对策的尝试。
于20xx年2月上旬模具完成制作及验模后,随即将此模具投入生产流程开始进行小批量试产。
而在其试产过程中,肯定会有各式各样的问题存在,到时改善小组成员需到现场进行跟踪讨论发现的问题及解决问题的方法。
C:检查(一)改善对策执行结果验证20xx年2月中旬改善小组召开第三次改善小组会议,共同对改善对策的初期执行结果进行验证。
发现生产效率提高了,人力需求降低了2/3,表示此改善对策是可行的。
但以仅运用此改善对策的情况来看,要达成改善计划所设定的目标,仍然有许多的问题要解决。
装配车间改善报告
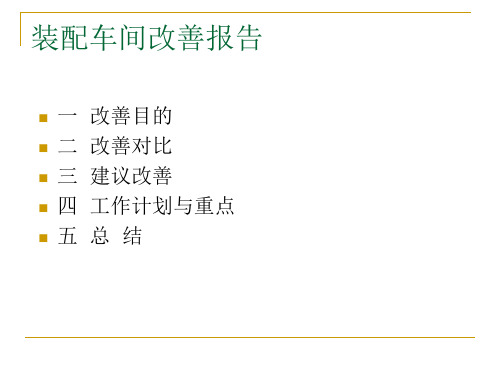
4.建议桌子类用刀模(3层纸板)来包装脚管和中架,这也取决于一 定的订单量,如此增加的刀模费用大概在500元左右,可是能减少的 人工成本,产效的提高,气泡袋的材料成本远远大于刀模的费用。
5.第4点的建议同时要将现有的普通袋改为收缩袋,如此能美化外观, 更能确保品质,更重要的是能节约人工成本,方便操作。
我们必须具备一定的危机意识,饮水思源!我们 改善无止境!
以上! 谢 谢!
取放塑料 配件口
建议(二)用冲床冲面料的剪口
该模具使用可调节试刀口
建议(四)产品工艺改善
1.产品的部分横管,支管等,只要是不影响 其结构和功能测试的,建议将管件的壁厚 和直径改小。
2.产品的辅助功能管件或配件,设计过于复 杂,同样能达到的客人的要求,但现实的 生产工艺却能改善很多!比如沙滩躺椅背 部
其次针对治具,工具的改善,让半机械或自动化来代 替人工作业,从而减少员工的劳动强度来提升产能。
再次对于现场的作业流程来改善,秉持以《删除,简 化,合并,重组》的管理核心。
摆放管件载具
物料摆放载具
异形管件载具
扩孔治具
该刀具可以调节扩孔 尺寸,刀片可以拆卸,
可以更换刀片
可调式拉布治具
可调节宽度 和长度
装配车间改善报告
一 改善目的 二 改善对比 三 建议改善 四 工作计划与重点 五 总 结
改善目的
改善是无止境的,改善是企业的生存之本,只有不停 的去改善,才能挖掘潜力,降低成本,减少浪费,增 加附加价值。
现场改善不能犹豫,大则一项工程小则一个配件或动 作。
首先从现场的载具改善入手,让员工作业时取给方便, 减少搬运时间,增加工作效率。
推荐 QCC案例--改善装配螺钉不良(联想) 精品

1
15
绿叶圈——原因分析(饼图)
10.25-11.7日固定螺钉不良故障分布:
按故障类别分
故障类别比例图 操作不良, 6%
按不良部件分
其他部件 不良, 14% 不良部件比例图
配合不良, 30%
来料不良, 64%
机箱不良, 86%
重点从机箱的来料和配合 两方面展开分析!
数据来源:惠阳厂品管处。(批量问题:不良率》3%)
1
14
绿叶圈——目标制订
1500 1200 900 600 300 0 改善前(10.25-11.7) 改善后(12.1-12.15)
1262DPPM
共降 低61%!
500DPPM
数据来源:惠阳厂维修数据库。
主目标:固定螺钉不良由装配第一位降到第三位;
配 合 不 良 员 工 操 作 不 良 治 工 具 不 良
针对前8大 机械牙螺钉不好用 主要因子制 生产将不同厂家的螺钉 混用,导致螺钉和螺孔 机箱结构设计原因导致 订改善对策! 机箱与部件配合尺寸公
差偏上下线 改锥倾斜固定螺钉 5 IQC抽检 4 140 4 288 4 252 4 252 8 作业指导书 部件未装到位就打螺钉 7 培训操作方法 员工固定螺钉不熟练 改锥扭力不当 7 培训员工技能 7
填写人 序 号 课题名称 吴红玲 对应职责 质量 效率 质量、效率 影响程度 30% 填写日期 迫切性 30% 数据齐备 20% 2004/11/12 成功可能 20% 总计
课 题 选 择
1 2 3
改善装配固定螺钉 不良
开天M产能提升 提升机箱易制造性
10
8 8
10
9 8
9
8 8
零件错装8d报告案例

零件错装8d报告案例在包装时由于经常装错和漏装零配件,给成包带来很大的隐患和麻烦,包装生产受环境制约以及不规范性的包装作业操作,错放,漏放配件仍是当前、后续长期需要控制的重点项目。
仍需从包装流程控制、QA成品检验处加严管控才是。
我想解决的是在较常见的车间环境下如何实现包装步骤的简化法:一、首件法:每批次的产品生产组装完成后,拉倒另外的地方,集中隔离进行单独包装作业。
在每一个批量包装前,先包装一件样板,由专门负责的QA检验人员对其进行全方位的测试,并作出测试报告,也叫首件报告。
后面的包装作业以此为参照。
保证了产品出厂后在商业,质量,数量,配件,备件等多方面要求的完整性,符合客户的订单要求,减少投诉和退货。
二、称重法:对于较重的产品,容易称重的产品,因其对重量敏感,采用称重法控制。
建议测试成品箱的样板重量,然后再设定一个公差值,每生产一箱成品就过一次称重,这样就可以预防减少装错,漏装的现象。
三、数控法:1、十件法,(看具体的产量,或者是每个箱子里的数量,所有的附件都是一样的数量,配套,如果最后少了,或者不配套,就能及时处理这一小批包装产品。
2、利用软件控制,把附件能够贴标签的,然后扫描。
3、制作零配件清单,放了后做点检,关键是每个工序必须留下证据,员工才有责任心,增加员工的责任感,然后有目标地对员工进行教育培训。
4、设计数控自动控制装置用来计数,每通过一次,装置就自动计数一次。
5、专门定人取东西入包装袋如果每个包装袋成在的数量有出入即不相等,就得找原因。
6、小集合包装,小零件的打包工作,比如螺钉,垫片等小的零件,不超过3种集合在一起,做成一小包。
7、最终包装工作的标准可视化,三个部分组成,每部分为约3个零件的组合。
工作的这样分下来,每个操作工简化为只针对3个元件分配,消除了复杂程度,也能提高效率。
防止漏放配件应该从多个方面去管控。
8、发料及领料数量的管控,仓库发料时应一个个的点数及称重比较核对,当然对于大批量的物料可以分批发放(比如:500或1000为一个单位进行)。
产品打错螺丝改善报告

产品打错螺丝改善报告1. 引言本报告旨在总结并改善我们产品生产过程中遇到的问题:打错螺丝。
在产品组装过程中,打错螺丝是一种常见的错误,给我们的生产效率和产品质量带来了不良影响。
通过对该问题的详细分析和改进措施的提出,我们将寻求一种可行的解决方案,以减少打错螺丝的发生率,并提高产品组装的效率。
2. 问题描述在产品组装过程中,由于螺丝种类过多且相似度较高,工人们很容易将不同种类的螺丝混淆,导致错误装配。
这些错误在以下方面给我们带来了困扰:2.1 生产效率低下由于螺丝打错后,需要进行重新组装,这无疑增加了我们的生产时间和成本。
工人们需要花费额外的时间来找出错误并进行修复,从而降低了整体生产效率。
2.2 质量问题错误装配的螺丝可能导致产品组装不牢固,甚至在使用过程中出现故障。
这会给我们的品牌声誉带来负面影响,并增加售后服务的成本。
2.3 工人劳动强度大由于需要花费额外的精力和时间来修复错误,工人们的劳动强度增加。
长期以往可能会导致员工疲劳,甚至影响到他们的工作积极性和工作效率。
3. 分析原因为了改善产品组装过程中打错螺丝的问题,我们需要先分析并找出造成该问题的原因。
3.1 缺乏螺丝识别标识当前我们使用的螺丝种类繁多,但缺乏清晰的识别标识,使得工人们很难迅速辨别螺丝的类型和用途。
3.2 工人操作失误在快速工作节奏下,工人们可能会因疏忽或粗心导致螺丝错装。
3.3 带来高压力由于螺丝错误装配的后果,工人们面临着额外的工作压力和责任,尤其是在需要交付大量产品的情况下。
这可能会引发工人的工作焦虑和工作不稳定。
4. 行动计划为了解决产品组装过程中打错螺丝的问题,我们提出以下行动计划:4.1 引入螺丝识别标识为了方便工人快速辨别螺丝的类型和用途,我们计划在每个螺丝上引入清晰的识别标识,例如颜色编码或字母编号。
这样一来,工人们只需要轻松识别颜色或字母即可将螺丝正确装配。
4.2 强化培训和质量检查我们将加强对工人的培训,确保他们具备正确的工作流程和操作技巧。
8d报告案例范文

8D报告案例:汽车制造业中的质量问题解决1. 案例背景汽车制造业是一个竞争激烈的行业,汽车制造商需要不断提高产品质量以满足市场需求。
然而,由于生产过程中的各种原因,质量问题时常出现。
这就需要制造商采取措施解决问题,以降低不良率,提高产品质量。
本案例以某汽车制造商的一个具体质量问题为背景,展示了如何使用8D报告方法解决质量问题。
2. 案例过程2.1 问题发现在该汽车制造商的生产线上,某一型号的汽车在组装过程中出现了一定比例的漏油问题。
漏油问题不仅影响了汽车的外观和品质,还可能导致机械故障,给消费者带来不便和安全隐患。
因此,该问题被认为是一个严重的质量问题,需要尽快解决。
2.2 问题分析制造商成立了一个专门的团队来分析漏油问题。
团队首先进行了现场调查,观察了漏油现象发生的具体情况,并收集了相关数据和样本。
通过对数据和样本的分析,团队发现漏油问题主要发生在某一特定的组装工序中。
进一步的分析表明,问题可能是由于该工序使用的密封胶出现了质量问题,导致密封不完全,从而引起漏油。
2.3 制定解决方案基于问题分析的结果,团队制定了以下解决方案:1.更换密封胶供应商:通过与多家供应商的沟通和评估,选择一家质量可靠的密封胶供应商,以确保密封胶的质量稳定。
2.优化工艺参数:对组装工序的工艺参数进行优化,确保密封胶的使用量和施工方式合理,从而提高密封效果。
3.强化质量控制:加强对组装工序的质量控制,建立更严格的检查和测试流程,确保每辆汽车的密封质量符合标准。
2.4 实施解决方案制造商在生产线上实施了以上的解决方案。
他们与新的密封胶供应商建立了合作关系,并对工艺参数进行了调整。
此外,他们还培训了员工,提高了他们对质量控制的意识和能力。
2.5 结果评估在实施解决方案后,制造商对漏油问题进行了跟踪和评估。
经过一段时间的观察和测试,他们发现漏油问题得到了显著改善。
对于经过改进的生产线,漏油问题的发生率大大降低,质量得到了有效控制。
不良专案改善

CY通过团队专案检讨进一步做持续改善,以达到满足CPT客户品质要求 。
Suzhou Chon Yang Electronics Co.Ltd
2. 建立团队
Authority name
林佑泉
Department
专员
responsibility
主导整个专案推动,制定改善的目标和方向, 资源的提供。
100.00% 90.00% 80.00% 70.00% 60.00% 50.00% 40.00% 30.00% 20.00% 10.00% 0.00%
不良項目
M/L错位 M/L折偏 M/L油污 漏黄胶 漏PIN
不良率
65.61% 19.76% 13.44% 1.19% 0.00%
225
65.61% 85.38% 98.81% 100.00% 100.00%
1.后续架模员针对模具打油 后,要先进行模具上下数次 作业,使多余渗出的油渍及 时擦拭,以防作业过程造成 油渍在产品上。 2.另外规定针对机台2H一次 5S清洁。 3.产线外观检查人员先检查 产品外部在检查产品内部, 对于影响产品外观问题的产 品挑出,再经擦拭后流下一 工站。
MFG 李红秀
7/13
Suzhou Chon Yang Electronics Co.Ltd
4.4 漏工序(漏黄胶/漏铆PIN)
Issue 不良图片: 原因分析 1.铆PIN时因速度 过快,PIN脚未铆 紧导致出现PIN胶 脱落现象。 2.产品贴胶区域过 多,贴胶人员易漏 贴胶。 3.产品多工序作业 时,前工序与后工 序之间区分不明确。 4.作业方式不当, 已制品与未制品未 区分开。自检/全 检时未能及时发现 漏工序。 改善对策 1.在铆合治具上加磁,以便将PIN 吸
组装工序改善措施
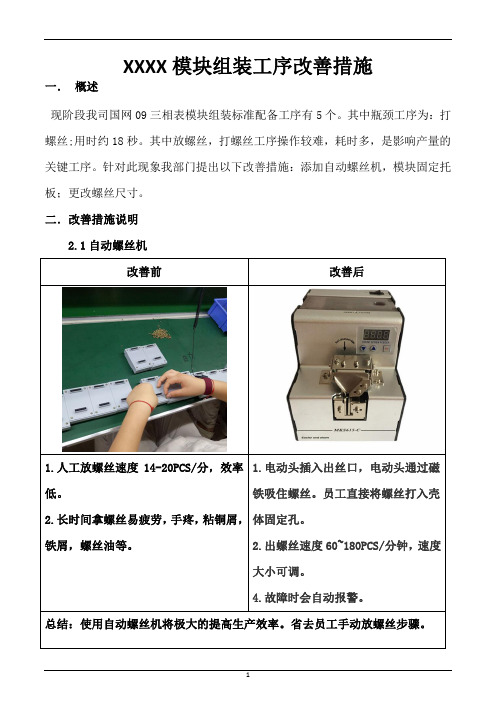
XXXX模块组装工序改善措施
一.概述
现阶段我司国网09三相表模块组装标准配备工序有5个。
其中瓶颈工序为:打螺丝;用时约18秒。
其中放螺丝,打螺丝工序操作较难,耗时多,是影响产量的关键工序。
针对此现象我部门提出以下改善措施:添加自动螺丝机,模块固定托板;更改螺丝尺寸。
二.改善措施说明
2.1自动螺丝机
2.2壳体固定托板
模块运送时,拿取过程中螺丝易掉出来。
打螺丝时需要用手握住模块,长时间操作易疲劳。
打螺丝时如果电动力度稍大,人手没有握住模块极有可能将模块下壳打飞,甚至伤到里面电路板。
如果螺丝放入不正,螺丝很容易打滑,无法取出。
1.模块固定托板,可牢固的固定住壳体。
不必用
现模块组装采用2.6*8mm 的自攻螺丝固定,螺综合我司其他产品组装经验,使用3*8mm 螺丝
三、改善方案比较
3.1产线人员安排
3.2产能比较
3.3改善总结
◆产能提升:50只/小时
◆人员节省:1人
◆产量提升比率:10%
◆生产环境:改善了原有操作的弊端,减去放螺丝的工序。
添加模块固定托板,使人们在打螺丝时不必再用手用力握住模块,减少了操作难度。
四.后续改善目标
将单一的模块托板量化,安装固定到自动化产线上,生产过程中人将模块放在托板上之后,所有的操作都在托板上完成,直到包装工序将模块取下。
此方法适用于我公司目前所有的打螺丝模块。
XXXXX部 xxx。
开关产品不良纠正预防措施改善报告

Eight-Discipline CAPAR WorksheetCAR NO:FY-QA-CAR20201200101. 产品信息:PN No.Product name Quantity Ship date Order number91.813161-0012x2机械式光开关 2 2020.12.23 /2. 产品退回状况:使用吸塑盒包装,包装无破损。
3. 产品外观检查:退回产品2pcs中有1pcs壳体底部有胶,产品S/N号为:20S1122-62574. 产品光性能检测:产品光特性测试正常5. 产品退回不良分析原因:SN:20S1122-6257/6317产品经测量PIN脚长度发现,其PIN脚长度较短,如下图所示:不良品图片:经测量PIN脚长度只有2mm左右,无法满足客户要求(客户要求>/=2.5mm)PIN脚太短不良发生原因:1、继电器底部点胶装入壳体后放到热盘上时,由于作业员是将壳体倒放的,有可能在固化过程中,继电器受重力的影响,会往下沉,导致PIN脚伸出长度变短,无法满足客户要求。
2、作业员在进行组装时,继电器底部点胶装入壳体后没有装到位,壳体与继电器之间胶层太厚,导致继电器PIN脚伸出壳体长度较短,造成无法满足客户要求。
壳体底部有胶不良发生原因:1、作业员在进行钢管外封帽封装作业时,不小心将胶水点到壳体底部,没有及时清洁,导致残留胶水一直遗留在壳体底部。
Discipline 5 改善对策日期:2020-12.24PIN脚太短改善对策:1、继电器底部点胶装入壳体后增加按压这一动作,确保继电器底部不会因为胶水的影响导致继电器与壳体之间存在未完全贴紧的现象,从而使PIN脚露出长度无法满足客户要求。
2、变更继电器与壳体在热盘固化的方式,如下图所示:变更前变更后壳体底部有胶改善对策:1、作业员在进行胶水封装作业时,应注意避免胶水流入产品光纤、PIN脚、壳体表面等部位,如发现有胶水残留时,应及时将胶水清洁干净。
组装车间改善提案案例

组装车间改善提案案例一、背景介绍。
我们公司的组装车间是整个生产线中非常重要的一环,直接关系到产品的质量和生产效率。
然而,在实际操作中,我们发现了一些存在的问题,例如生产线停机时间过长、零部件配送效率低下、工人操作繁琐等,这些问题直接影响了整个车间的生产效率和产品质量。
二、问题分析。
1.生产线停机时间过长。
在实际生产过程中,我们发现生产线停机时间过长是一个普遍存在的问题。
这不仅会影响产品的生产进度,还会增加生产成本。
2.零部件配送效率低下。
零部件的配送效率低下也是一个需要解决的问题。
由于配送不及时,导致生产线上的工人等待零部件,从而影响了整个生产线的运转效率。
3.工人操作繁琐。
工人在操作过程中需要频繁的更换工具和零部件,这不仅增加了工人的劳动强度,还影响了整个生产线的效率。
三、改善提案。
1.引入自动化设备。
为了解决生产线停机时间过长的问题,我们可以引入一些自动化设备,例如自动上料机、自动拧紧机等,从而减少人工操作时间,提高生产效率。
2.优化零部件配送流程。
我们可以对零部件的配送流程进行优化,引入智能化的仓储管理系统和物流配送系统,从而提高零部件的配送效率,减少等待时间。
3.改善工作台设计。
对工作台进行重新设计,将常用的工具和零部件设置在工作台附近,减少工人的操作繁琐程度,提高工作效率。
四、实施计划。
1.引入自动化设备的实施计划。
首先,我们需要对生产线进行全面的调研分析,确定哪些环节适合引入自动化设备。
然后,选择合适的自动化设备供应商,进行设备的采购和安装。
最后,对工人进行培训,确保他们能够熟练操作新的设备。
2.优化零部件配送流程的实施计划。
我们需要与供应商合作,建立智能化的仓储管理系统和物流配送系统。
同时,对配送流程进行优化,确保零部件能够及时到达生产线上。
最后,对工人进行培训,确保他们能够顺利适应新的配送流程。
3.改善工作台设计的实施计划。
我们需要对工作台进行重新设计,确保工作台上的工具和零部件能够方便工人的操作。
不良原因分析及改善报告

原因分析
第一工序铣加工两平面时 员工装夹不到位,导致厚 度超差 (如下图示)
问题不良原因分析及改善报告
暂定改善对策
暂定改善对 策实施日期
责任部门/人员
恒久改善对策
恒久改善对 策实施日期
责任部门/人员
1.检讨优化现在生产加工工艺,重新制 订新工艺.如下图所示
厚度尺寸6.35 ±0.46超差至 5.61பைடு நூலகம்
制作:
2003标准 水准Ⅱ
GB/T2828.1-2003标准 水 货检查正常单次抽样方案》,记录
AQL(1.0%)抽样检测,记录 准Ⅱ AQL(1.0%) 抽样检 5个样品的数据
没按抽样数记录
测,记录5个样品的数据
2009.11.19
承认:
确认:
新工艺真空吸塑装夹
我司抽样方案详见附页《来料/出货检 查正常单次抽样方案》,记录5个样品 2009.11.19 数据
装夹到位图片
装夹不到位有 部分凸出
换用合格量具对仓库 存品及客户换回成品 进行全检
厚度专用检具图示
2009.11.19
现工艺平口钳装夹
2009.12.01
装夹不到位图片
厚度专用检具全检图片
检查报告上 面只记录了5 个样品的数 据
我司出货抽样方案外观全 外观全检,厚度尺寸专用厚
检,尺寸按照GB/T2828.1- 度检具全检,其它尺寸按照 我司抽样方案详见附页《来料/出
组装精益改善报告

组装精益生产改善阶段性总结七月,又是一个骄阳似火的七月!七月的大地,有一种希望在罗美播种!七月的天空,有一种思潮在组装涌动!七月一号,******会议室,由集团**牵头在罗美正式宣告“组装精益改善小组”的成立,经过两个多小时的讨论,会议上提出了实现组装效率提升20%的总方针目标。
俗语云”山雨欲来风满楼“,让我们先回顾一下组装在精益改善之前的样子吧;1.现场物料堆积,半成品占据了车间的“半壁江山“2.计划安排混乱,车间计划和项目计划始终难以吻合3.产品合格率低下,受上几道工序影响严重“穷则变,变则通,通则久”——《易经.系辞下》针对组装目前存在的问题,精益生产执行小组先从中选取一个最具代表性的生产的项目(798项目)进行研究。
首先,我们运用“鱼骨图”主要从人、机、料、法、环五个方面对798项目进行问题分析:1.人通过建立员工技能水平表,我们可以直观反映员工技能水平,发现了部分员工技能经验不足的问题2.机通过精益生产小组成员一个周的观察,发现员工在操作过程中有些工装模具并不适用以及需要新曾一些工装模具3 . 料通过统计每日的完成计划情况,发现组装目前的缺料问题。
通过观察组装798员工的操作以及车间物料布局我们发现物料拿取的不方便。
4.法运用动作打分表,精益生产小组成员分别对员工的操作动作进行打分,然后根据动作打分表的分值找出员工操作中的动作浪费。
对于鱼骨图反映出来的问题,我们进行了如下解决:1.人对于部分员工技能不足,精益生产小组组织工艺工程师对新员工进行了培训并向全体员工讲解了精益生产的知识。
2.机对于员工在操作中反映的工装模具存在的缺陷,我们组织技术部工程师进行了改变。
对于员工频繁需要翻动产品,我们又制作了翻转工装供员工使用3.料对于组装欠料问题,我们组织了生产部、采购部、物流部进行开会讨论,最后决定建立安全库存,若以后再出现缺料则有采购部负责提请采购。
4.法在本次改善中,生产方式方法的改变是我们组装精益改善的最大变化。
组装问题点及改善对策

溢膠
產品沾膠
掉key
浮高
劃傷 壓傷
改善對策
重新調整出膠量 檢視氣壓是否足夠7kg,及通知廠商維修,或增加換uv膠 需於設計端時解決 注意清潔 注意清潔 注意清潔 調整自動點膠機出膠量 更換燈管 延長輸送帶運行速度 調整電火花功率及輸送帶速度 加強作業手法訓練 減少脫模劑次數,貼合表面以酒精擦拭 減少脫模劑次數,貼合表面以酒精擦拭 加強作業手法訓練 使用治具檢驗橡膠尺寸 調整出膠至適當 通知工程改善產品設計 使用電木治具或橡膠治具 訓練作業手法 清潔治具 通知廠商修改
組裝常見問題點分析及改善對策
不良項目 原因分析
膠量過大 點膠機氣壓不穩定 針管管徑太大 氣壓太大 膠質太稀 rubber表面太小 手指沾到膠 指套沾到膠 治具沾到膠 膠量不足或無點到膠 uv燈管能量不足 照射時間不足 電火花不完全達因值不夠 貼合手法錯誤 橡膠汙染 pc汙染 組裝手法不正確 橡膠尺寸異常 膠量過大 配合干涉 治具材質過硬 作業中擦傷 治具內有顆粒 治具加工不良
富士康工作失误改善报告
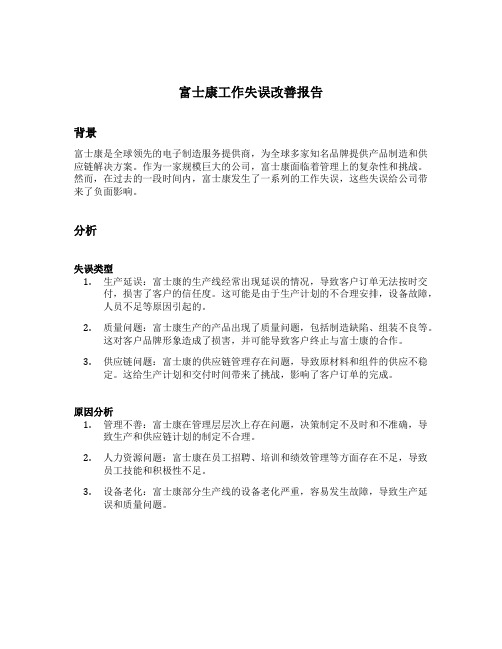
富士康工作失误改善报告背景富士康是全球领先的电子制造服务提供商,为全球多家知名品牌提供产品制造和供应链解决方案。
作为一家规模巨大的公司,富士康面临着管理上的复杂性和挑战。
然而,在过去的一段时间内,富士康发生了一系列的工作失误,这些失误给公司带来了负面影响。
分析失误类型1.生产延误:富士康的生产线经常出现延误的情况,导致客户订单无法按时交付,损害了客户的信任度。
这可能是由于生产计划的不合理安排,设备故障,人员不足等原因引起的。
2.质量问题:富士康生产的产品出现了质量问题,包括制造缺陷、组装不良等。
这对客户品牌形象造成了损害,并可能导致客户终止与富士康的合作。
3.供应链问题:富士康的供应链管理存在问题,导致原材料和组件的供应不稳定。
这给生产计划和交付时间带来了挑战,影响了客户订单的完成。
原因分析1.管理不善:富士康在管理层层次上存在问题,决策制定不及时和不准确,导致生产和供应链计划的制定不合理。
2.人力资源问题:富士康在员工招聘、培训和绩效管理等方面存在不足,导致员工技能和积极性不足。
3.设备老化:富士康部分生产线的设备老化严重,容易发生故障,导致生产延误和质量问题。
结果客户影响1.失去订单:由于富士康的工作失误,客户可能失去信任并取消订单,这将导致销售额的下降。
2.品牌形象受损:富士康生产的质量有问题的产品可能影响客户的品牌形象,这可能导致客户遭受损失并选择其他供应商。
3.客户投诉:富士康的工作失误会增加客户的投诉,这需要公司投入额外资源来解决问题。
公司内部影响1.生产效率下降:由于工作失误导致的生产延误和质量问题,生产效率将下降,可能需要额外的资源和时间来弥补损失。
2.成本增加:在处理工作失误和客户投诉的过程中,公司可能需要投入更多的资源来解决问题,这将增加成本。
3.员工士气低下:工作失误可能导致员工士气低下,影响员工的工作热情和积极性。
建议管理改进1.改进决策制定:加强对管理层的培训,提高其决策制定的能力和准确性,以避免不合理的生产和供应链计划。
组装螺丝盒专案改善报告
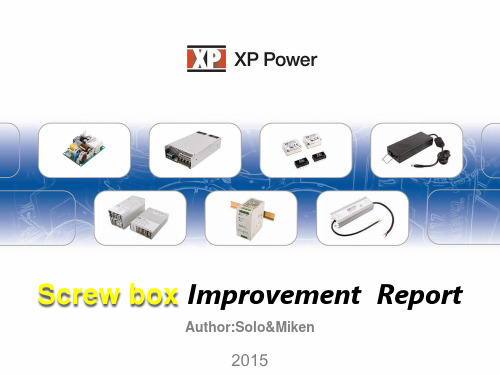
7. Cost saving
XP Power
1
2
Saving: 1737.93RMB/Yearly
Rework time
40790 RMB/Yearly
Saving: 39052.8RMB/Yearly
UPH
XP Power
XP Power
根据PK每月统计漏锁螺丝不良记录表,每天平均1pcs螺丝漏锁,返工工时5分钟*1人*30天 *12月=180H*9.6=1737.93RMB/Yearly 2. 节省人工UPH工时费用:根据七月份ASSY生产机台总数量
使用手放到电动起子头锁附时间(2PCS) 1. 14.10S 2. 14.17S 3. 14.85S 4. 14.00S 5. 14.01S 平均时间为:14.26S
XP Power
为了改善以上问题,提升UPH,提升产品品质,我们需替换 原来物料盒 在考虑替换物料盒时需考虑以下几点:
1> 可以管控螺丝数量 2> 方便锁附螺丝; 3>区分混料螺丝; 4> 调整螺丝盒大小尺寸。
4. Introduction New Screw boxXP Power
新的螺丝盘:
5. Introduction of Screw box
之前使用的物料盒 ¥6.5/pcs 现在使用的螺丝盘 ¥2.0/pcs
XP Power
6. Screw box Comparison
NO. Description Before
XP Power
After
1
螺丝盒外形变更
2
数量管控
无法确定数量
定制固定数量
6. Flow Card Comparison
XP Power
- 1、下载文档前请自行甄别文档内容的完整性,平台不提供额外的编辑、内容补充、找答案等附加服务。
- 2、"仅部分预览"的文档,不可在线预览部分如存在完整性等问题,可反馈申请退款(可完整预览的文档不适用该条件!)。
- 3、如文档侵犯您的权益,请联系客服反馈,我们会尽快为您处理(人工客服工作时间:9:00-18:30)。
D1 Issue Informations and FA Team 基本信息與改善團隊
D2 Problem Description 問題描述
D3 Containment Actions (Immediately) 圍堵措施
Supplier 供應商 长增
Supplier Car No. # 供應商客訴編號 Login Date 客訴日期 2015.12.18 Supplier Reply Date 供應商回覆日期 2015.12.21
Product Name 產品名稱
14-50500-041
CPT Car No. # 群電編號
Happened Place 發現地點
□ IQC
□ Production Line
□ OOBA □ Customer □ ORT □ Other
Team members 改善團隊
Team Leader : 品保:袁树年
工程:寇润林 、李寿炎 製造:张建华 業務:杜军 其他:生管/赵菊芳
Describe the problem 不良問題描述
高效客戶端反應我司料號為14-50500-041组装尺寸0.65偏小,导致组装不良
When 日期 Where 地點 Who 人員 What 事情
How much 不良率 Date Code 生產週期 2015.12.18 高效客戶端
14-50500-041组装不良
不良圖片1、2、3……
D4 FA Analysis ( OK/NG sample contrast) 失效分析
D5 Root Cause 根本原因
分析流程: 展開流程圖找出異常站別→針對異常站別用魚骨圖(人/機/料/法/環)找出可能原因→查檢表排除找出不良原因→5Why找出真因→模擬再現
發生原因結論:
1.工程修模品放入半成品中
2.半成品成型成品包装时作业员全检漏失
流出原因結論:
1.接料员工作疏忽
2.作业员目视全检眼睛疲痨
5 why4M1E排除分析
D6 Corrective and Prevent actions 改善與預防對策
改善與預防對策:
改善前:
1.工程人员未将修模品清理干净
2.接料员疏忽将修模品放入半成品中
3.半成品成型成品包装时作业员全检漏失
4.作业员目视全检眼睛疲痨
改善后:
1.后续工程人员修模后必须把工作台上修模品清理干净,以防混入。
工程课长不定期巡查;负责人:寇润林完成时间12/21
2. 现场PQC人员对工作台面物料进行全检。
负责人:向海浓完成时间12/21
3.由生产组长每天早上上班前对操作员、全检员进行工作宣导;负责人:王辉志完成时间12/21
4.生产组长每两小时调换全检作业员,以免眼睛疲痨;负责人:王辉志完成时间12/21
5.工程人员.将组装尺寸0.65制作成SIP后续作重点管控;负责人:李寿炎完成时间12/23
D7 Verification 對策有效性驗證
對策有效性驗證:
將此異常納入重點管控
D8 Tracking 效果追蹤
核准(改善方):杜军審核(改善方):寇润林作成(改善方):袁树年------以上資料填寫由供應商負責人填寫,最終核準必須由供應商品管經理級以上(含)人員簽核------。