制程不良改善报告
QCC制程改善方案
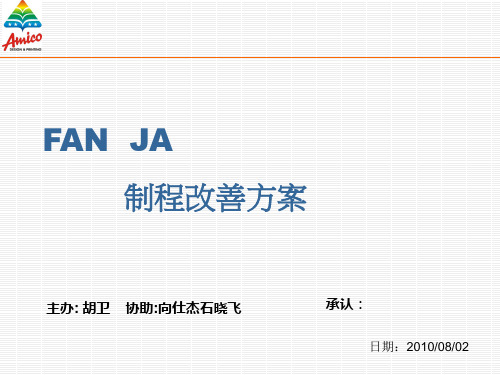
19/28
应对措施
NO. 对策内容 1 1.轮转保养时对拉纸压轮重点清洁,防 止压轮脏污转移至材料表面,轮转机台标 识重点清洁区域,提醒作业员!见附图八: 责任人 执行时间
轮转/宋财富
2010/08/01
2.修改作业方式,量产中针对有满版底 色印刷的产品多开一座UV灯(即3色印 轮转/宋财富 刷时,打开4座UV灯),所有颜色印刷 完成后经多次UV灯烘烤,确保烘干效果. 此对策执行由产线品管首件及巡检中核 查。
4.
不良信息的传递
A.由品保部整理每天检验的不良样品,提交给相关生产单位,由领班召集作业人员了解分析。 B.生产领班根据不良样品分析得出的结论进行不良追踪确认,确保改善效果及对策执行情况。
责任人:向仕杰 胡卫 完成日期:10/07/30
22/28
后期改善方案
5. 改善成果的维持
A.丝印部将YUPO材料掉油墨的改善课题持续维持,保持品质稳定。
3
商标 2% 1.8% 1.9% 1.6% 2.0% 1.6% 1.8% 1.3% 1.1% 1.0% 1.07% 0.5% 1.1% 0.3% 1.3%
25/28
达成状况一
丝印制程目标与达成
10.00% 8.00% 6.00% 4.00% 2.00% 0.00% 5月 6月 7月 8月 9月 10月 11月 12月
B.根据材料特性将对策水平展开到其它部品上,确保不良不再发生。 责任人:胡卫 完成日期:10/07/30
6.
异物不良的改善
A.丝印部品在印刷前由助手用除尘滚轴在材料表面上来回滚压一次,将表面的灰尘去除,防止异物不良发生. B.轮转机印刷部品,在材料送纸处增加除尘胶带,印前将材料表面的异物粉尘粘掉,减少异物不良的发生.
PCBA红胶工艺贴片掉件改善(6Sigma改善报告)
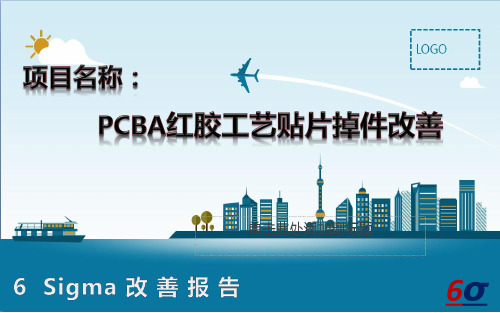
通过以上实际导入跟进改善效果, 掉件率降为平均0.29,有明显效果.
6
C2 控制计划
DMA I C
序号
1 2
改善对象
what
红胶铜网 波峰焊参数
相对应文件
how
胶网开孔规范
波峰焊标准作业指导书
责任单位
who
自动化SMT IT工程
责任人
who
詹三 李斯
实施位置 控制时间
where
自动化SMT
波峰焊
when
5. 红胶固化温度和时间控制测量数据:
I2 实验执行
DMA I C
6
二. 实验执行:
6. 贴片固化后图片:
I2 实验执行
DMA I C
富士
新懿
6
二. 实验执行:
7. 进行常温和高温推力,记录数据和计算平均值:
I2 实验执行
DMA I C
6
三. 实验分析:
1. 实验表和数据:
Y1为高温推力数据, Y2为常温推力数据.
固化后相关图片:
DMA I C
6
A3.0805掉件改善和新懿红胶改善跟进
2.过波峰焊炉试验: 试ቤተ መጻሕፍቲ ባይዱ结果:
DMA I C
结果说明: 1. 第一遍过板后确认掉件无, 确认焊接状况, 没有因溢胶或侧边胶导致的焊接不良问题. 2. 0805电容在过第6次时开始出现掉件 3. 玻璃二极管在过第4次时开始出现掉件 4. PCB板在过第7次后板面出现较多变形,轻微起泡, 决定停止过炉实验证, 改做最后浸入锡中, 并上下抖动板实验. 5. 做完浸锡后,板严重起泡,分层,变形.
由于从平均推力上不能明确判定 增加胶点内距后的推力效果要好, 因此 下一步使用假设检定工具来进行判定.
不良品改善报告范文(3篇)

不良品改善报告范文第1篇P:计划(一)制定改善计划20xx年1月P公司派训的L工程师结训回到企业后,立即深入现场进行问题调研,再结合参训前收集的现场管理问题点,然后召集改善工作筹组会议决定IE改善工作小组由工艺部工程师、生产副总、车间主管、品检工程师等8位成员共同组成,并由工艺部L 工程师担任IE改善工作小组组长,制定出每位小组成员的工作职责及IE改善小组的工作计划。
IE改善小组将IE改善工作主题聚焦于车间制程的改善及标准化。
(二)设定改善目标两周后,改善小组就改善主题对P公司的生产流程及产品的现况展开讨论,发现车间生产效率仅有61%,改善小组随即运用SMART原则来进行改善目标设定,并将改善目标设定为:1、从简化生产流程设计上入手,运用作业程序(流程)分析手法来降低产品加工成本,在现有成本基础上降低15%。
2、通过生产线工站重新部置及人员编成,运用IE手法使生产线平衡,并提高装配效率,在现有的基础提升55%。
3、改善时间为五个月(20xx年1月20xx年5月)。
改善目标确定下来,改善小组立即将主题及目标进行分解成小项目,由改善小组成员分别负责各个小项目,进行团队合作。
并定每两周召开一次改善小组会议,共同探讨实现目标的方法。
D:执行(一)执行改善对策20xx年1月下旬改善小组召开二次改善小组会议,共同探讨改善对策。
决议改善初期先设计几组新规格的模具投入生产流程中进行改善对策的尝试。
于20xx年2月上旬模具完成制作及验模后,随即将此模具投入生产流程开始进行小批量试产。
而在其试产过程中,肯定会有各式各样的问题存在,到时改善小组成员需到现场进行跟踪讨论发现的问题及解决问题的方法。
C:检查(一)改善对策执行结果验证20xx年2月中旬改善小组召开第三次改善小组会议,共同对改善对策的初期执行结果进行验证。
发现生产效率提高了,人力需求降低了2/3,表示此改善对策是可行的。
但以仅运用此改善对策的情况来看,要达成改善计划所设定的目标,仍然有许多的问题要解决。
生产工艺改进总结汇报

生产工艺改进总结汇报
尊敬的领导、各位同事:
我很高兴在这里向大家汇报我们部门最近进行的生产工艺改进
工作。
经过一段时间的努力,我很自豪地告诉大家,我们取得了一
些显著的成果。
首先,我们对现有的生产工艺进行了全面的分析和评估。
我们
发现了一些存在的问题,例如生产效率低、产品质量不稳定等。
为
了解决这些问题,我们制定了一系列的改进方案,并进行了实施。
其次,我们引进了一些先进的生产设备和技术。
这些设备和技
术大大提高了我们的生产效率,同时也提高了产品的质量和稳定性。
我们还对员工进行了相关的培训,使他们能够熟练运用这些新的设
备和技术。
另外,我们还优化了生产流程,简化了生产工艺。
通过精益生
产的理念,我们大大减少了生产过程中的浪费,提高了生产效率和
产品质量。
最后,我们对生产过程进行了全面的监控和管理。
通过引入一
些先进的生产管理系统,我们能够实时监控生产过程中的各项指标,并及时发现和解决问题,确保生产的顺利进行。
通过这些改进措施的实施,我们的生产效率得到了显著提高,
产品质量和稳定性也得到了有效保障。
我相信这些改进不仅将为公
司带来更多的利润,也将为我们的客户带来更好的产品和服务。
在未来的工作中,我们将继续努力,不断改进和提高我们的生
产工艺,为公司的发展贡献更多的力量。
谢谢大家!。
经典QCC改善报告

4 15000
3853 25.7%
5 15000
2782 18.5%
6 19000
2774 14.6%
7 12800
3660 28.6%
日期
8
9
14000 17400
2225 2490
15.9% 14.3%
11 25900
2334 9.0%
12 21900
3366 15.4%
13 平均不良率
23000
计划在三个月内(9.15-12.15)完成 !
消除三大不良:插板不过,绝缘体残屑,六片变形变曲!7
The first issue
插板不过和六片变形弯曲关系phase1-1
主体来料六片变形
主体来料六片弯曲
装配后保持变形或变曲, 出现
六片弯曲变形/插板不过
8
插板不过和六片变形弯曲鱼骨分析 phase1-1
人力资源
小计:704元+960元=1664元
3 QC筛选员外观检验 基本工资:32元/天×22天=704元;
QC 3人筛选全检
工时节约
加班费:8元/小时×120小时/月=960元 效率提高1/3倍
小计:704元+960元=1664元
5 每年成本节约
(180元+1664元×2)=42,096元
22
QCC第一阶段改善总结phase1
1.SQE/李广 2.IQC/何洪锋 3.SQE(李广)/ IQC(何洪锋)
对不同批次来料主体生产上线时,QC和生产线班长/组 长要关注刚生产时的产品,如有异常及时找生技解决,将 模具调到最佳位置
QC/黄祥成 装配/何春泽 生技/李跃
1.Φ5.13/ Φ 3.51复合检具,保证QC人员在检验上一致性. 1.PIE/王雄飞
焊接不良改善报告【25页】
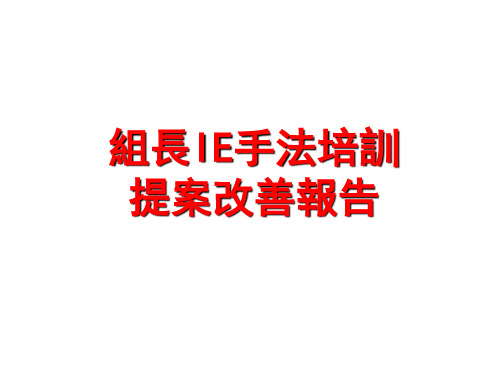
三:改善歷程
A.實驗參數因子,水平的選取
實驗因子 預熱溫度 預熱時間 恆溫溫度 恆溫時間
因子代號 A B C D
水準一 160 ℃
1s 500℃
8s
水準二 180 ℃
2s 550℃ 10s
三:改善歷程
B.根據A項中所列因子,水平畫出L8 ( 24 ) 直交表.
A
B
C
D
1
1
1
1
1
2
1
1
2
2
3
1
2
1
112
36
20
12
Percent
57.9
26.2
8.4
4.7
2.8
Cum %
57.9
84.1
92.5
97.2
100.0
三:改善歷程
1.為驗證Hot bar機台的焊接品質,故運用DOE法評 估Hot bar機台的焊接可行性:
WIFI Antenna
Hot bar焊接治具
BT Antenna
焊接天線位置圖
PAD是獨立 一塊,散熱慢, 溫度高,焊接 品質好
整個PAD全 板均接地,散 熱快,溫度低, 易冷焊
PAD是獨立一塊, 散熱慢,溫度高,焊 接品質好
整個PAD全板均 接地,散熱快,溫 度低,易冷焊
三:改善歷程
b.為保證焊接品質.達到兩PAD溫度相同(避免散熱慢
的一邊溫度過高而燙傷PAD),運用實驗驗證法將熱熔 頭偏移,減少一邊結合面積,如下,使PAD焊接溫度一致. 從而達到焊接要求.
五:標准化及推廣應用
效益評估
1. 無形效益 此改善案有效提高客戶滿意度,維
護了公司形象,增進了與客戶間關係,贏得 了客戶認同,極大的鼓舞了團隊士氣,增強 了市場競爭力,達到了降低生產成本,提高 生產效率的目的!
制程改善报告

1350 1140
540 517 850 1100 280 1500 2250 1150 1200
630 64.7
2.67 3.16
6.67 6.96 4.24 3.27 12.86 2.40 1.60 3.13 3.00
5.71 55.66
自動印字打點
自動装PS 手工裝PS
装PIN 壓PIN 組合 灌胶 切中 入长管 測試
↑20%
59.47 Pcs/人/H
改善後實績
標准 工時
72.64 Sec
60.54 Sec
注:
一般型是一個量大,耗用人力最多的產品系列,惟達+立達每年 生產量35000K,目前使用人力200人,按訂單需求,需人力234人。
3
改善前產能工時
工序
3P
產能 PCS/人/H
工時 SEC
工序
印字 打点
装PS 插PIN 壓PIN 組合 灌胶 切中 切整 测试 打D/C
7
改善方案與進度追蹤
NO 工序
缺陷
改善方案
改為雙手插PIN:
1
插PIN
左手大部份時間持住底座, 1、制作治具盤2套
為無價值動作
2、試作雙手作業
3、治具盤復制
印字
2
打點 分三道工序
打DC
三工序合並,做半自動機: 1、DS一台 2、DP一台
3
灌膠 耗人多
做DP型自動灌膠機一台: 1、與廠商評估 2、採購及制作
12.86 7.83 83.57
4
改善方向
方向:制程改善有別於全員改善,將針對量大、人多的品名,進一 步提升改善的層次,加大改善的深度,對以下方面作重點改善:
制程改善报告ppt模板

制程改善报告ppt模板篇一:考察报告PPT模板下载酒店考察报告考察时间:20XX年5月19日至5月23日考察地点:花水湾名人度假酒店、青城(豪生)国际酒店、成都城市名人酒店考察人:考察目的:通过实地考察,加深对酒店的了解,了解酒店的现状和酒店的宣传推广方式,亲自体会酒店环境感受酒店氛围,了解酒店服务流水线,从酒店人的角度来换位思考、发现不足,通过借鉴学习,建立一套符合本酒店的市场营销推广方案,确定酒店的目标市场,并且设计、组合、创造适当的酒店产品,以满足其目标市场的需求,最终实现酒店的盈利。
引言:本次考察的对象为成都地区的五星级酒店,以温泉度假为主题的酒店两家,以商务会员为主的酒店一家。
一般说来,主题酒店也称为“特色酒店”,是以某一特定的主题来体现酒店的建筑风格和装饰艺术,以及特定的文化氛围,让顾客获得富有个性的文化感受。
主题酒店是市场竞争的产物,也是酒店竞争进入高层次文化竞争的表现。
本次考察报告主要以调查酒店的文化定位、服务项目、综合管理、营销推广策略为主。
考察内容:酒店的服务项目、硬件设施、软件服务、团队管理、营销推广策略等。
一、花水湾名人度假酒店1、地理位置与交通驾车体验:我们驾驶商务车,平均车速约80码,从成都到酒店全程大约1小时。
在大邑下高速后,我们在路口看到有到花水湾方向的指示牌,很快找到了路去花水湾方向的路,路况较好,一路畅通无阻。
沿途看到很多宣传的广告牌,关于还未到达酒店的时候,已经对酒店周边的旅游资源极其丰富。
2、客源市场的定位概况:客源以四川省内地区的为主,以旅游休闲观光为目的的游客占50%以上。
心得体会:其地理位置距离成都主城区有一定距离,反应出长途度假客源缺少,商务度假客源还有待开发的特点。
以温泉为主题的酒店,使其酒店客人主要集中在冬季,其次是夏季。
3、装修、设施、环境概况:主楼外观整体视觉效果不错,层次感、时代感较强。
内部装修属奢华气派风格;地面、墙体均采用高档大理石板材;酒店大厅空高高,就餐区错落有致的特色三层设计。
DIP IMPROVE REPORT -制程改善总结报告 SMT工序
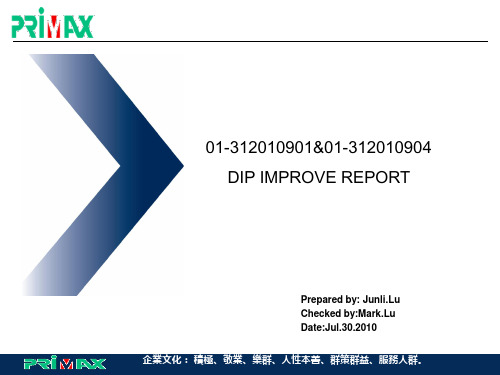
48.85
145.26 82.98 150.98 100.26 51.29 191.51 83.69 25.19
48.95
144.98 81.01 150.47 101.29 52.19 191.48 84.25 24.49
49.00
145.49 82.14 151.36 100.25 51.89 191.49 83.02 24.56
Before Change
After Change Improve
73.08%
80.69% 7.61%
33
32 1
25.79
24.88 3.53%
企業文化: 積極、敬業、樂群、人性本善、群策群益、服務人群。
2
一: 改善前数据收集
Station F1 F2 F3 F4 F5 F6 F7 F8 F9 F10 F11 F12 F13 Action 分边&集装PCBA板&插件 插件2 炉前目检 拆治具&剪脚&插J-ENG1 焊接J-ENG1 修补 元件面目检 锡面目检 ICT测试&贴SN标签&点黄胶 焊接电池 电池电压测试 补焊&目检 电池测试&点热熔胶
1
42.06 46.08 10.23 27.34 50.95 30.14 30.14 32.02 34.52 39.73 55.89 59.16 116.49
Measurement Time 2 3 4 41.54 47.52 13.76 27.75 60.69 27.26 27.38 29.26 33.12 35.11 53.45 61.16 115.69 41.20 44.52 12.70 29.25 58.63 39.26 30.88 32.76 34.02 32.60 62.71 59.26 116.53 40.69 42.88 15.56 27.79 49.79 30.90 30.02 31.90 32.56 31.89 62.92 61.34 115.01
10月制程不良分析总结报告
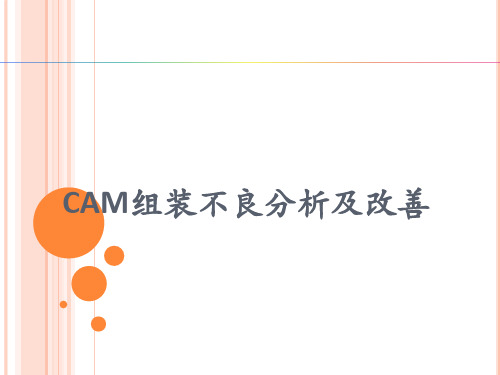
法
使用激光分板、超声波清洗 COB
公司高层
11月10日
棉签擦拭次数,废弃棉签误用 棉签蘸取酒精量多 振动后才能测试,终检前跌落工 序 百级工作台封装—测试洁净度 环
梁江(技术) 梁江(技术) 刘新昌(CAM) 马宏伟(品质)
10月30日 10月30 11月3日 11月1日 透明赃物 IPQC巡查 外校 避免硬板打磨 粉尘
CAM组装不良分析及改善
一.制程不良报表 二.TOP3不良原因分析 三.改善措施及验证计划
一.制程不良前三项
1.脏污 2.功能不良 3.模糊
从10月报表统计出前三大不良项目为:
二.TOP3不良原因分析
1.脏污原因分析:
人
漏检 自身作业水平 人员作业没有休息 棉签蘸取酒精太多
脏 污
测
没有调焦最清晰
说明:OQC退检数据下降,说明产线发现问题的能力提高,流出问题减少
使用的棉签是正牌,
棉签公司网站为 http://www.sa-nyo.co.jp/
脏污棉签防止误用装置 (丢进去后无法从顶部取出)
试验1 使用1280*1024显示屏检测前、后,OQC检出不良数据对比 使用前 10月27日 10月28日 10月29日 10月30日 11月3日 OQC检出不良批数 4 1 5 9 11 使用后 11月6日 11月7日 11月8日 11月9日 11月10日 OQC检出不良批数 6 2 6 3 2
11月5日
11月3日 11月3日
委外做镀层分析
川田 符合使用规定要求
功能不良改善措施
改善对象
措施要点
上料前目视检查FPC洁净度
责任人员
张光水(SMT)
实施时间
11月1日
不良改善报告

severity level 问题严重度
■Severe严重
Part Name 品名
Part No 产品料号
□ critical 主要 □Minor次要
Specific description of defect product 产品具体不良内容
Date日期 : Inspection/Shipment Date 检验/出货日期
Lot Q'ty批量
DISCIPLINE 2 Use team approach: ( 改善团队 )
DISCIPLINE 3 Implement Containment Plan:( 临时对策 )
1. Scope对策实施范围
Q''Ty/数量
Methods/处理方式
Date日期: Results/处理结果
Date日期:
DISCIPLINE 8 Congratulate your team:( 结案确认)
Date日期:
Approved by核定:
Checked by 审核:
Prepared by制表:
东莞市**精密五金有限公司
******不良改善报告
Non-Conformity 不符合来源
□IQC进料/半成品检验 □ IPQC程巡检 □FQC 成品检验■客户投诉
□other其它( )
□OQC出货检验
第一部分:Discipline 1:Describe The Problem 问题描述 :
Responsible Dept 责任单位
Countermeasures for outflow of defective products(流出原因对策):
SMT制程不良原因及改善报告
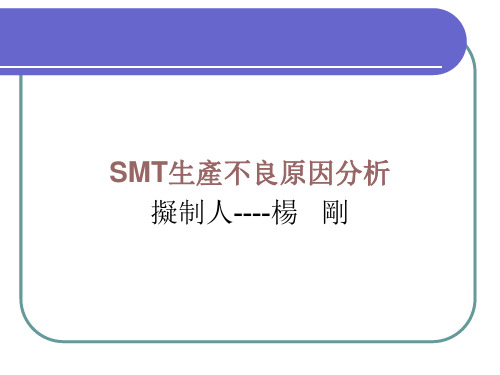
新旧锡膏混用
手放零件方法不当 载板系统不良 元件数据 轨道速度过快 设定不当 吸嘴 规格 吸嘴 弯曲 置件 不稳 坐标 偏移
方法
机器
人
人为跳掉 mark 作业
材料
零件有一边焊盘 吃锡不良 零件过大过重 未及时收板,PCB在回焊 炉中碰撞 人为手抹锡膏 备料时料带过紧 零件厚度不均 零件氧化 异形零件 手推撞板 人为手拨 缺锡 PAD间距与组 件长度不符 零件与PAD不符 手摆料 缺乏质量意识 PAD宽度与组件 宽度不符 零件脚歪 焊盘上有异物 零件脚弯 PAD 离轨道边小 于3mm. PAD氧化
(3) WHERE——何處?在哪裡做?從 哪裡入手? (4) WHEN——何時?什麼時間完成? 什麼時機最適宜? (5) WHO——誰?由誰來承擔?誰來 完成?誰負責?
(6) HOW ——怎麼做?如何提高效率? 如何實施?方法怎樣? (7) HOW MUCH——多少?做到什麼 程度?數量如何?品質水準如何?費用產 出如何?
环境
人
材料
露铜 无尘布毛絮堵 塞钢网开口 氧化 沾锡性
焊盘 有杂物 距板边不足3mm 沾油漆 不平整
缺乏质量意识 人为设定E-pass模式 手放散料遗漏/错误 收板不及时炉内撞板 人为设定跳过
PCB
设计 有异物 变形 黏 性 低
印刷后PCB板停留时间过长 手推撞板 手抹锡膏 通风不畅 生产模式被改动 (pass,idle) 未上锡 不正确操机 温度高锡膏变硬 未认真检查 真空不畅 程序缺件 擦钢网方法不正确 元件高度设定太薄 作业标准书不完善 流程错误 新旧锡膏混用 清线时关 闭料站 更改贴片顺序 紧急停止 锡膏印刷缺锡 电磁阀不良 钢网材质 传感器失灵 机器故障 轨道不洁 Z轴不平 机器振动 开口堵塞 MTS振动太大 轨道卡板 气压 Mark点设置 钢网设计不良 钢网未开口 运转速度 开口不正确 贴片 速度 过快 吸嘴 尺寸 不符 吸 嘴 弯 曲 坐 标 误 差 吸 嘴 磨 损 吸嘴 堵塞 跳掉次序数据 收板 零 件 氧 化 外形 尺寸 变形 厚度 不规 损 大小 抛件 差异 则 件 料带过紧 或过松 沾 锡 料带粘性 物质多 性 包裝不良
车间制程工艺优化改善报告

1
14003EC黑色 2016年10月23日 A13 前加工(镭雕) 1
650
1
900
提升率 38.5%
产能提升 (pcs/h)
成本下降(元)
250
0.014
2
13038黑色
2016年10月23日 A13 前加工(镭雕) 1
650
1
1000
53.8%
350
3 PS10F美规(白色) 2016年10月22日 A13 前加工(镭雕) 1
改善后产能: 成本下降:
按USB机种计算每小时产能:1500PCS/H 1人 产能提升不明显,可提高品质要求;投入后不良率由2.6%降低到0.5%。
14
10.PCBA后焊夹具(PS65B)
改善前
改善后
无治具后焊散热片组合件,作业困难
4拼后焊散热片治具,有效提高效前产能:650PCS/H 2人
日
日
/
进行中
样品已确认,待商 务洽谈导入
○
散热片
加工散热片改为设备自动 加工
266PCS/ 550PCS/
H
H
13万
0.04元 /PCS
1年 11月8日
/
/
评估报告已提报, / 暂停 李总通知暂停后续
扩产再上马
☆
超声机传输 带
便于超声完成后流拉
750PCS/ 850PCS/
H
H
2K
0.0024 元
/PCS
16
12.散热片加工自动化方案
改善前
改善后
3人加工散热片组合件
改善前产能:
1人操作机器加工散热片组合件
800PCS/H
3人
改善后产能: 成本下降:
制程异常分析(典型案例)报告
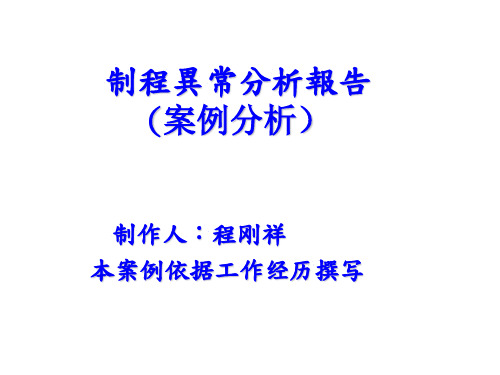
制作人:程刚祥 本案例依据工作经历撰写
一、不良现象描述
a.日期: 2019/12/25
工位: 孔规
b.機型:XXXXX-0X USB 3.1 TYPE-3 沉板母座
c.不良現象及不良率:
USB 3.1 TYPE-3 沉板母座上在做孔规测量,放入孔规不顺畅(不平贴,严
重者可能导致SMT装板不良) 。
剪除毛刺或剪短
孔规检测
五、长期对策
a.图面,作业指导书标准化: 1、修订SIP,补充内容:料带预断点检验毛刺环节并加以组装实配5PCS; 2、来料通过CCD和二次元量测把握冲压件上毛刺的缺陷等级,不得大于 0.01mm。 b.JIG/TOOL工治具修复合理化: 1、通知冲压工序,对该模具进行确认并修复; c.防呆(POKA YOKE)措施(颜色形状方向,声音左右,夹治具布局设变): 1、首件重点检验此异常,重点抽查并以实配检测是否平贴,是否顺畅。
不良圖片說明
12月12日、量化数据求出: 1、抽查料带库存品发现: 其中12月21日2500*7(外强);3500*4; 3500*6外发、 共
计420.9KPCS,经检查铁壳预断面宽度为:0.147-0.125mm,切断后有毛刺(高度超出 0.02mm)现象;
b.现场,现物,现状调查: 1、抽查来料7托盘/ 420.9KPCS ;成品2280PCS各5PCS; c. 调查制程,物料,设备5M1E因子: 1、可能因子:法/机/料。(人/机/物/环/法)
三、验证可能因子(分析)
a. 预计验证时间表: 1、12月26日现场检讨并确认SOP(作业指导); 2、12月26日已抽查来料库存/成品; b. 验证可能因子: 装配不到位;胶芯来料不良,铁壳来料异常; c.验证报告分析提出说明: 1、USB 3.1 TYPE-3 沉板母座上的铁壳预断位点应力异常,手工掰 断有毛刺,高出胶芯界面0.02mm;
个人工作改善报告书范文3篇

个人工作改善报告书范文3篇事务改善是指间接部门的改善活动,目的主要是消除各类管理损耗、减少间接人员、改进管理系统、提高办事或事务效率,更好地为生产活动服务。
本文是学习啦小编为大家整理的工作改善报告范文,仅供参考。
工作改善报告范文篇一我于12月1日正式成为东方CJ顾客中心商谈7组组员,成为正式员工已有3个月左右的日子,在最近的1个多月里,我的情况不敬如人意,已经犯下了多次商谈错误,并且被领导谈话教育。
在此,辜负了领导及同事对于我的信任,深表歉意。
在这段时间里,我进行了深刻的反思,归根结底主要问题出在以下2点:1.对工作态度的散漫由于在起初的2个月里没有犯下致命错误,并且成为正式员工已有一段时间,造成了自满的情绪,忽略了自己的不足点,所以在工作中,缺少主动性,对我组老员工提出的建议也是听过算数,没有认真思考并加以改善。
随着工作态度的下降,业务看的少了,对工作的关心程度,参与度也少了,在商谈中抱着侥幸的心理去应对。
导致了QA成绩下降,犯下商谈员错误等一系列问题。
2.对工作失去热情在工作了一段时间后,渐渐发觉每天的工作就是重复接听电话,也没有空余的时间来调节自己,与同事之间缺乏沟通交流。
每天上班变的枯燥乏味起来,对商谈产生了抗拒的心理。
改进目标通过总结以上两点问题,改变自己对工作态度上的散漫,提高自己对工作的职业操守。
争取在以后的工作中提高自己的QA成绩,重新得到领导和同事的信任。
改善措施针对以上两点问题,首先严格要求自己,有空余时间就看KMS和共享等,以加强我司业务流程及应对方法,提高自己的工作效率和商谈技巧,有不懂的地方多寻求领导或老员工的帮助,同时对出现的问题及自己的薄弱环节加以思考并改进。
在商谈过程中做到思想集中,对客户情切,耐心等基本QA要求,用心应对。
提高自己的商谈水平。
其次,对工作多一点参与和关心,多与我组的优秀员工进行交流取经,以此来提高自己的工作经验。
领着这份薪水就应该对得起它,提高自己的职业素养和个人修养,认真完成每一份工作,吸取各位每一份建议。
制程品质异常报告(精)
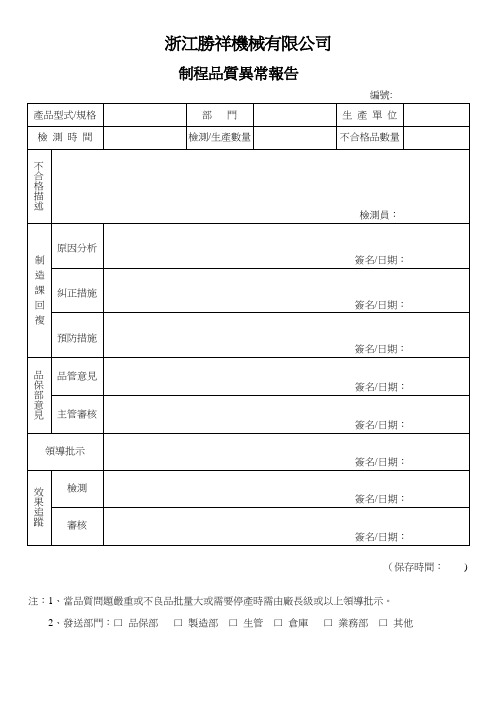
浙江勝祥機械有限公司制程品質異常報告編號:(保存時間:) 注:1、當品質問題嚴重或不良品批量大或需要停產時需由廠長級或以上領導批示。
2、發送部門:口品保部口製造部口生管口倉庫口業務部口其他________品质管理制度公司为了保证产品的品质制定,品质管理制度的推行,能提前发现异常、迅速处理改善,借以确保及提高产品品质符合管理及市场需要。
目录展开编辑本段1、总则第一条:目的为保证本公司品质管理制度的推行,并能提前发现异常、迅速处理改善,借以确保及提高产品品质符合管理及市场需要,特制定本细则。
第二条:范围本细则包括:(一)组织机能与工作职责;(二)各项品质标准及检验规范;(三)仪器管理;(四)品质检验的执行;(五)品质异常反应及处理;(六)客诉处理;(七)样品确认;(八)品质检查与改善。
第三条:组织机能与工作职责本公司品质管理组织机能与工作职责。
各项品质标准及检验规范的设订第四条:品质标准及检验规范的范围规范包括:(一)原物料品质标准及检验规范;(二)在制品品质标准及检验规范;(三)成品品质标准及检验规范的设订;第五条:品质标准及检验规范的设订(一)各项品质标准总经理室生产管理组会同品质管理部、制造部、营业部、研发部及有关人员依据"操作规范",并参考①国家标准②同业水准③国外水准④客户需求⑤本身制造能力⑥ 原物料供应商水准,分原物料、在制品、成品填制"品质标准及检验规范设(修)订表"一式二份,呈总经理批准后品质管理部一份,并交有关单位凭此执行。
(二)品质检验规范总经理室生产管理组召集品质管理部、制造部、营业部、研发部及有关人员分原物料、在制品、成品将①检查项目②料号(规格)③品质标准④检验频率(取样规定)⑤检验方法及使用仪器设备⑥允收规定等填注于"品质标准及检验规范设(修)订表"内,交有关部门主管核签且经总经理核准后分发有关部门凭此执行。
第六条:品质标准及检验规范的修订(一)各项品质标准、检验规范若因①机械设备更新②技术改进③制程改善④市场需要⑤加工条件变更等因素变化,可以予以修订。
SMT制程不良原因及改善对策

调整印刷机平台的水平度平行度;
6
基板表面异物造成周边元件锡膏印刷 过厚;
基板使用前进行除尘作业;
7
一次面基板背面残留锡膏过炉形成锡 珠,二次面锡膏印刷时垫起钢网形成 多锡;
避免一次面基板粘附锡膏,避免洗 板作业;
8 修理员回锡过多;
指导修理员按标准作业。
11
立起
产生原因
1 铜铂两边大小不一产生拉力不均; 2 预热升温速率太快; 3 机器贴装偏移; 4 锡膏印刷厚度不均; 5 回流焊内温度分布不均; 6 锡膏印刷偏移; 7 机器轨道夹板不紧导致贴装偏移; 8 机器头部晃动贴装偏移; 9 焊盘两端的散热程度不一致融化速度差异; 10 炉温设置不当; 11 铜铂间距过大; 12 MARK点误照造成元件打偏; 13 料架不良,元件吸着不稳打偏; 14 原材料不良; 15 钢网开孔不良;
发形成干锡膏,混入印刷产生钢网堵孔。
改善对策
10
多锡
产生原因
改善对策
1 钢网开孔过大或厚度过厚;
按标准制作钢网;
2 锡膏印刷厚度过厚;
调整印刷参数(压力、脱模等) ;
3 钢网底部粘锡;
清洗钢网;
4 IC元件底部接地焊盘锡膏溢出形成多 接地焊盘开孔适当减小,贴装高度适
锡;
当调高;
5
印刷平台不平行或高于基板导致印刷 多锡;
19 原材料设计不良;
反馈IQC联络供应商;
20 料架中心偏移;
校正料架中心;
21 机器吹气过大将锡膏吹跑;
将贴片吹气调整为0.2mm/cm² ;
22 元件氧化;
更换OK之材料;
23 PCB贴装后长时间没过炉,导致活性剂挥发; 及时将PCB-A过炉,生产过程中避免堆积;
尺寸不良8d报告改善的案例

尺寸不良8d报告改善的案例8d报告模板在质量管理活动中,我们常用到各种各样的质量工具,而大多数情况下,都是多种质量工具的混合使用.不管使用工具的多或者少,每种工具所发挥的成效都是特定的.有些工具长用记录,有些长于分析,有些长于决策,有些长于思考,而问题的解决都是多种工具配合使用所得,而这种配合的模式就形成了解决问题的套路.在某些大企业中,为了管理的方便,格式的统一,往往会固化成特定的标准化的模板.今天我们一起学习的这个工具就是一种套路,它就是福特汽车公司惯用的g8d报告.8d又称团队导向问题解决方法、8d问题求解法.是福特公司处理问题的一种方法,它提供了一套符合逻辑的解决问题的方法,同时对于统计制程管控与实际的品质提升架起了一座桥梁.目前已广泛应用于汽车制造行业,取得了显著的经济效益和社会效益.8d主要用于汽车及类似加工行业的问题解决方法.原始是由ford公司,全球化品质管制及改善的特殊必备方法,之后已成为qs9000/iso ts16949、福特公司的特殊要求.凡是做ford的零件,需采用8d作为品质改善的工具.后来名气大了,其它车厂也移植了福特的做法、使之成为汽车行业的标准做法.目前国际汽车行业(特别是汽车零部件产家)广泛采用来解决产品质量问题最好的、有效的方法.8d方法是一种归纳与推测的问题解决方法.归纳法以基于观测数据为起点,建立与数据一致的推测.推测法以一种推测为起点,并通过收集数据并分析来确定数据是否同理论一致,从而企图证明一个推测是否能适用于某个特定的条件.在8d程序的初始阶段期,主要是归纳法.收集以及分析数据,从而描述问题.确定可选择性的根本原因推测,并且与问题描述比较,从而确定最佳的推测.然后,通过收集数据,采用演绎法来确定这个最佳推测是实际的根本原因.解决问题时,团队经常在归纳法与演绎法之间转换.这通常是完成工程任务的最有效的方法.8d方法有以下几方面的明显作用:通过建立小组训练内部合作的技巧;提供一种通用的流程有效确定并解决问题;防止相同或类似问题的再发生;增加管理层对问题本身及解决方法的理解;鼓励直接开放的问题解决方法;提高顾客满意度,增强其对供方的产品和过程的信心.8d方法适用于以下两方面的情形;1.用于解决各类可能遇到的简单或复杂的问题;8d方法就是要建立一个体系,让整个团队共享信息,努力达成目标.8d本身不提供成功解决问题的方法或途径,但它是解决问题的一个很有用的工具;2.亦适用于过程能力指数低于其应有值时有关问题的解决;面对顾客投诉及重大不良时,提供解决问题的方法.我们常见的质量问题主要有两种类型:变异引起的问题和从未满足要求的问题.8d这套方法特别适合于解决由某个变化导致的问题,或者说是特殊原因引起的问题;6-sigma这套方法特别适合于解决从未满足要求的问题,或者说是普通原因引起的问题.8d方法和6-sigma都是用于解决质量问题的有效工具,两者在解决问题中相辅相成.8d是解决问题的8条基本准则或称8个工作步骤,但在实际应用中却有9个步骤:d0:准备8d过程d1:组建团队d2:描述问题d3:制定临时处置措施(ica)d4:确定并验证根本起因和遗漏点d5:选择并验证针对根本原因和遗漏点的永久性纠正措施(pca) d6:执行并确认pcad7:预防问题重现d8:表彰小组和个人的贡献针对每一步,我们详细介绍其使用过程:d0:准备8d过程实施本阶段的原因:g8d过程是一个可能涉及大量人力、时间和资源的过程,如果使用不适当将会浪费很多时间、人力和相关的一些资源.d0帮助我们把焦点放在问题上,以便有效地使用资源.本阶段实施过程:了解症状并量化症状,决定是否需要era,选择并验证era,执行并确认era,查看是否适用g8d标准.紧急反应措施(era)是保护顾客及相关的各方不受症状的影响的任何措施,它在g8d把问题和症状区分开来确认g8d是否有必要启动时应用.症状是可测量的事件或效果(它们必须是顾客体验到的),它表示一个或多个问题存在.如果没有症状,你就无法得知有问题存在.当症状能被测量或量化时,它才被考虑在内.通常有许多工具可以用来测量并量化故障:paynter图,柏拉图,运行(趋势)图,风险图等.g8d的适用标准:1.症状被定义;2.确定了顾客;3.存在性能差距;4.原因未知;5.管理层致力于从根本起因的层面去解决问题,并采取预防措施防止问题再次发生;6.症状很复杂,不可能单凭一个人的能力完成.如果六个标准都满足,并且没有其他的g8d团队为同样的或类似的问题工作,那么就应该开始g8d过程.d1:组建团队原因:组建团队是g8d过程中的重要部分.团队的功能需要花时间去增强,但是非常重要的是,一个人很少能拥有解决复杂故障所有必要的资源、信息、和技能.另一方面,合适的人一起工作能包括所有必要的特性,这建立在每个有关人员的技能的基础之上.建立一个团队是g8d过程的真正开始;团队成员的指导方针:1.团队成员的人数控制在4到10个之间;2.选择具有所需技能、知识、资源、权力等,这样的人作为团队成员来解决现有的问题;3.各类成员之间合理搭配;4.按需要调整团队成员.g8d的过程依赖于所有团队成员的努力来达到团队的目标.为了达到团队目标,每个成员扮演一个角色.团队设置负责人,团队领导,成员及其它角色.实现团队角色的指导方针:1.角色不是特指某个人,而是指要行使的职责;2.成员通常要在会议持续期间或是更长的时间内充当某个固定的角色;3.会议中角色的互换会导致混乱;4.一些角色是可以共同承担的,比如记录员等;5.监督人是g8d生产过程中的一个角色,然而,监督人不是团队的成员.6.调解工作在整个讨论过程中是必不可少的,通常这个角色由某个领导承担.团队运作程序的三个要素:1.确定团队运作的基本规则;2.分配任务、维护和过程观察;3.使用有效沟通交流的技巧.d2:描述问题目的:将问题清楚并且客观的描述会使问题最终得到有效的解决.帮助团队将焦点放在实际的问题上,避免直接对问题下结论或者作没有根据的设想.对问题的描述要基于观测的内容而非结论.要描述好一个问题,我们需要:1.对问题进行陈述;问题陈述应该是简单,简洁明了的陈述,它确定了发生问题的对象及其这个问题的缺陷.一个问题陈述能让团队关注,也能让范围缩小到寻找问题的根本原因上,通常当作问题描述的开端.2.对问题进行描述;问题描述是指根据问题是什么和不是什么,但可能是某种状况来确定问题的范围.一个详细的问题描述包括四方面的信息,什么时候、什么地方、发生什么及其问题的严重程度如何.问题陈述告诉了你最基本的事实,但是详细的问题描述给了你找到根本原因的细节.d3:制定临时处置措施(ica)目的:为团队找到问题产生的根源争取时间;保护顾客不受问题影响;ica是针对故障而非根本起因,在知道根本起因之前保护顾客.如果根本起因被查明,或者era(应急处理措施)足够可靠来继续保护顾客,可以不需要ica.ica与era的差异:era以最小的支撑数据执行.ica为调查提供更多的机会.任何你执行的ica必须保护顾客使其免受故障而不导致新故障的出现.同样,单一ica可能不够.你可能需要执行多个ica以充分保护顾客.执行ica的步骤;1.选择ica;确定选择标准,分析执行ica的好处,分析ica的风险性,在好处和风险性的最好平衡点选择ica.2.验证ica;实施前证明能保护顾客不受问题影响,能提供前后的对比,证明ica不会产生新的问题.常见的验证方法有:实验,演示,类似措施对比等.3.执行ica;按照pdca的循环进行,并制定行动计划.4.确认ica.确认是在成功的验证后,确认ica执行没有产生新的问题,确认形式:售前验证和售后顾客的验证.d4:确定并验证根本起因和遗漏点目的:找出根本起因是任何故障解决成就的重要部分.当确定了根本起因,可以在最根本的程度上解决一个故障.任何不是从根本起因入手的故障解决方案都仅仅是一个权宜之计,当识别出根本起因,就可以完全的消除了整个故障并使它决不再发生.原因的几种分类:可能原因:任何原因,常在一个因果图表里识别,它描述一个结果可能怎样发生.最可能的原因:根据可用的数据得到的一个理论,它可能最能解释详细的问题描述。
- 1、下载文档前请自行甄别文档内容的完整性,平台不提供额外的编辑、内容补充、找答案等附加服务。
- 2、"仅部分预览"的文档,不可在线预览部分如存在完整性等问题,可反馈申请退款(可完整预览的文档不适用该条件!)。
- 3、如文档侵犯您的权益,请联系客服反馈,我们会尽快为您处理(人工客服工作时间:9:00-18:30)。
冠金属科
技有限公
DongGuan Metalking Technology CO.,Ltd
生产制程不良改善报告
發文單位: 品质部 責任單位 工程/品质/生产
不良主題: 1866/1862材料蚀刻前发现有整批表面紫色异常不良;
發文日期
2016/5/6
不良現象:
材料蚀刻 前发现有
立即對策: 1.停止生
产2.,准待备作补
料生产;
要因分
析:
1.材料表
面2.的磨杂板质清
洗干ห้องสมุดไป่ตู้,
日期
7月6日
責任人: 完成時間: 工程確認:
永久對策實施:
責任 人:图转/彭主管
1.采购知会供应商检讨分析原材料问题,从原材料着手改善;
2.培训磨板接板员,针对磨板后表面要求作相关资料文件夹,形成磨板标准;
3.磨板生产涂布前测试两张是否有紫色情况,没问题再投产大货,以免造成整批不良; 4.磨板后 表面异常
责任人 责任人 责任人 责任人 监督人
對策追蹤 確認:
追蹤人:
備注: 核准:
審核:
作成: 2016/7/6
責任擔擋
彭兴艳
肖主管 熊经理 聂剑华
聂剑华 2016/7/6