常用汽车线束试验项目
线束试验大纲2010.08.06
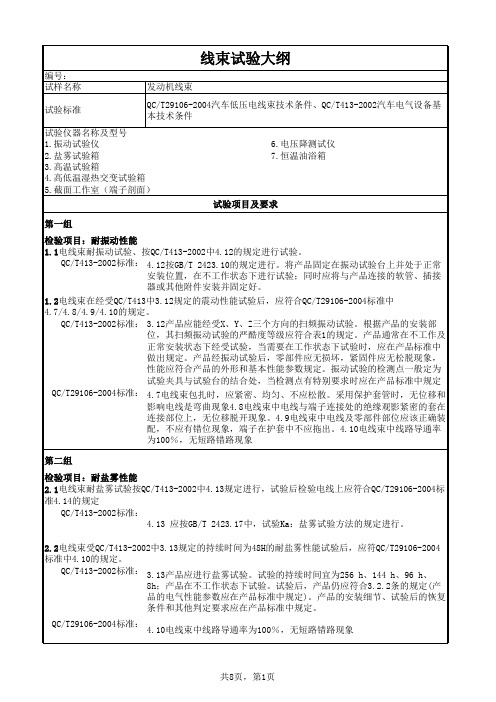
编号: 试样名称 试验标准 发动机线束 QC/T29106-2004汽车低压电线束技术条件、QC/T413-2002汽车电气设备基 本技术条件 6.电压降测试仪 7.恒温油浴箱
试验仪器名称及型号 1.振动试验仪 2.盐雾试验箱 3.高温试验箱 4.高低温湿热交变试验箱 5.截面工作室(端子剖面)
共8页,第1页
线束试验大纲
编号: 第三组 检验项目: 检验项目:节点间尺寸 3.1电线束尺寸用钢卷尺检测,应符合QC/T29106-2004中4.2的规定 3.1 QC/T29106-2004标准: 4.2电线束尺寸应符合下列要求:4.21干线和保护管长度不宜小于100mm, 并为10的倍数。4.2.2支线长度不宜小于30mm。4.2.3接点之间,接点和分 支点之间距离不宜小于20mm。4.2.4电线与端子连接处需装绝缘套管时,绝 缘套管长度不得小于20mm。4.2.5电线上基本尺寸极限偏差应符合表2规定.
共8页,第3页
线束试验大纲
编号: 第十组 检验项目: 检验项目:耐温度变化性能 10.1电线束耐温度变化实验,在不工作状态下进行。根据式样的安装位置将表5中下限工作温度值和 10.1 上限工作温度值作为试验温度,在每一种温度中的暴露时间为2H,温度转换时间不大于12min,循环 次数5次。 QC/T413-2002标准: 3.10.3耐温度变化性能产品应按GB/T 2423.22中试验Na的规定进行温度变 化试验。试验时的低温和高温值为选定的表5中的下限和上限工作温度值; 在每一种温度中的暴露时间取决于试验样品的热容量(即以试验样品达到 温度稳定为准),由产品标准规定,建议采用1h或2h;温度转换时间为20s ~30s;循环次数为5次;产品一般在不工作状态下经受试验。当产品标准 要求时,试验产品可处于运行状态 10.2电线束应分别按表5安装位置经QC/T413-2002标准3.10.3规定的耐温度变化性能试验后,应符合 10.2 QC/T29106-2004标准中4.7/4.8/4.10的规定 QC/T29106-2004标准: 4.7电线束包扎时,应紧密、均匀、不应松散。采用保护套管时,无位移和 影响电线是弯曲现象4.8电线束中电线与端子连接处的绝缘观影紧密的套在 连接部位上,无位移脱开现象。4.10电线束中线路导通率为100%,无短路 错路现象 第十一组 检验项目:耐温度、 检验项目:耐温度、湿度循环变化性能 11.1电线束耐温度、湿度循环变化实验,按QC/T413-2002中4.11在不工作状态下进行。 11.1 QC/T413-2002标准: 4.11参照GB/T 2423.34中,试验Z/AD:温度/湿度组合循环试验方法的有关 规定进行。 11.2电线束经QC/T413-2002标准中3.11规定的耐温度、耐湿度循环变化性能试验后,应符合 11.2 QC/T29106-2004标准4.7/4.8/4.10的规定 QC/T413-2002标准: 3.11产品应按GB/T 2423.34的规定在-10℃~65℃之间进行10个循环的温度 /湿度组合循环试验。每个循环为24h,其每个循环周期中的温度和湿度的 变化情况如图1所示。低温段不工作,高温段是否工作应在产品标准中做出 规定。试验结束后,产品仍应符合产品的电气性能参数的规定。对产品的 恢复条件和除去表面潮气的措施有要求时,应在产品标准中规定。 QC/T29106-2004标准: 4.7电线束包扎时,应紧密、均匀、不应松散。采用保护套管时,无位移和 影响电线是弯曲现象4.8电线束中电线与端子连接处的绝缘观影紧密的套在 连接部位上,无位移脱开现象。4.10电线束中线路导通率为100%,无短路 错路现象
汽车线束及连接器都有哪些检测项目

十二、电线束与连接器非金属材料分析
机械性能
成分分析
热学性能
塑料电学性能
燃烧性能
十三、电线束与连接器失效分析
失效分析是对已失效的产品进行的一种事后分析工作,通过使用各种测试分析技术和分析程序确认产品的失效现象,分辨其失效模式或机理,确定其最终原因,提出改进设计和制造工艺的建议,来消除失效并防止失效的再次发生,提高电子连接器可靠性,它是产品可靠性工程的一个重要组成部分。
辐射骚扰-TEM小室法
电磁干扰度(EMS)
电源线脉冲抗扰度
信号线脉冲抗扰度
RF能量直接注入
大电流注入
电源线音频耦合抗扰度
辐射抗扰度-天线照射法
辐射抗扰度-TEM小室法
辐射抗扰度-带状线法
辐射抗扰度-磁场环照射法
静电放电试验
十、清洁度测试
清洁度是指零件、总成和整机特定部位被杂质污染的程度。用规定的方法从规定的特征部位采集到的杂质微粒的质量、大小和数量来表示。“规定部位”是指危及产品可靠性的特征部位。“杂质”包括产品设计、制造、运输、使用和维修过程中,本身残留的、外界混入的和系统生成的全部杂质。
端子正压力
连接器的接合力、分离力
CPA、TPA的插入力和拔出力
锁止装置机械强度
固定结构机械强度
助力机构机械强度
端子、端子孔的防错结构
连接器的防错结构
密封件的保持力
板端插针保持力
牵引车电连接器插拔力
牵引车电连接器锁止装置检查
牵引车电连接器弹出力
牵引车电连接器锁止装置和电缆线固定强度
牵引车电连接器低温剪切强度
X射线荧光光谱分析XRF
显微傅利叶红外分析FTIR
俄歇电子成份分析AES
汽车电线束产品原材料入厂检验项目
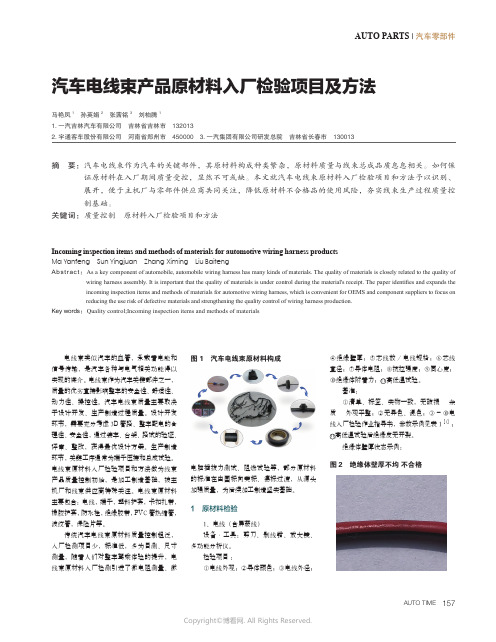
AUTO TIME157AUTO PARTS | 汽车零部件汽车电线束产品原材料入厂检验项目及方法马艳凤1 孙英娟2 张茜铭3 刘柏腾11.一汽吉林汽车有限公司 吉林省吉林市 132013 2.宇通客车股份有限公司 河南省郑州市 4500003.一汽集团有限公司研发总院 吉林省长春市 130013摘 要: 汽车电线束作为汽车的关键部件,其原材料构成种类繁杂,原材料质量与线束总成品质息息相关。
如何保证原材料在入厂期间质量受控,显然不可或缺。
本文就汽车电线束原材料入厂检验项目和方法予以识别、展开,便于主机厂与零部件供应商共同关注,降低原材料不合格品的使用风险,夯实线束生产过程质量控制基础。
关键词:质量控制 原材料入厂检验项目和方法电线束类似汽车的血管,承载着电能和信号传输,是汽车各种与电气相关功能得以实现的媒介。
电线束作为汽车关键部件之一,质量的优劣直接影响整车的安全性、舒适性、动力性、操控性。
汽车电线束质量主要取决于设计开发、生产制造过程质量。
设计开发环节,需要充分考虑3D 管路、整车配电的合理性、安全性,通过装车、台架、路试的验证、评审、整改,获得最优设计方案。
生产制造环节,关键工序通常为端子压接和总成试验。
电线束原材料入厂检验项目和方法做为线束产品质量控制初始,是加工制造基础,被主机厂和线束供应商特殊关注。
电线束原材料主要包含:电线,端子,塑料护套,卡扣扎带,橡胶护套,防水栓,绝缘胶带,PVC 管热缩管,波纹管,保险片等。
传统汽车电线束原材料质量控制粗泛,入厂检测项目少,标准低,多为目测、尺寸测量,随着人们对整车驾乘体验的提升,电线束原材料入厂检测引进了微电阻测量、微电脑插拔力测试、阻燃试验等,部分原材料的标准在由国标向美标、德标过渡,从源头加强质量,为后续加工制造坚实基础。
1 原材料检验1、电线(含屏蔽线)设备·工具:剪刀、剥线钳、放大镜、多功能分析仪。
检验项目:①电线外观;②导体颜色;③电线外径;④绝缘壁厚;⑤芯线数/电线规格;⑥芯线直径;⑦导体电阻;⑧抗拉强度;⑨同心度;⑩绝缘体附着力;11高低温试验。
汽车线束可靠性测试标准与仪器设备对照表
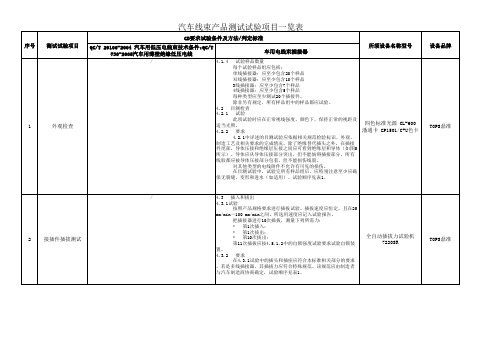
12印字耐久测试5.8.2.1准备三个试样,每个长600mm。
5.8.2.2 使用由两片纯毛毡组成的装置和装有50℃土3℃标准2号油(GB/T1690)的容器。
纯毛毡应至少含羊毛75%,密度为0.171 g/cm3—0.191 g/cm3,尺寸为50m*50mm*3mm。
5.8.2.3 试样浸入油中20h,使试样末端露在液面之上50mm。
从油中取出试样,在室温下干燥30min。
使用毛毡未用过的区域,将试样放置于两片毛毡之间。
在毛毡之间施加10N±1 N力,抽出试样。
试验后目视检查试样。
/自制TOPS鼎准13振动测试电线束耐振动试验,在不工作状态下,按QC/T 413-2002中4.12规定的试验方法进行,试验后检验电线束应符合4.13的规定。
/电磁振动试验系统T-300-3TOPS鼎准14结合温度振动/ 4.11 结合温度振动振动试验方法考虑了适合于电气插接的不同等级要求的振动程度。
建议汽车制造商和供应商按图13选择试验方法,按表5选择振动参数。
温湿度振动应力筛选系统ESS-300S-408DTOPS鼎准15热老化4.6 热性能4.6.1短期老化(240h) 电线应进行240h短期老化试验,试验温度见表进行卷绕试验应不开裂,再经受1min 1kV(均方根值)耐电压检查应不击穿。
4.18 老化性能4.18.1 试验把装配完全的试验样品放入实验室中,保存100h。
温度如表3。
注:试验时间也可在表3中的最高适用环境温度时增加到500h。
4.18.2 要求老化试验箱或烤箱(已有)TOPS鼎准16化学液体4.7 耐环境和化学品性能4.7.1 耐液体电线应进行耐汽油、柴油和机油试验。
经供需双方协商也可进行其他液体试验。
经试验液体浸渍后电线外径变化率应符合表9规定。
在室温下按表6进行卷绕试验应不开裂,再经受1min 1kV(均方根值)耐电压检查应不击穿。
4.23 化学试液4.23.1 试验对于有可能暴露于表8所列液体环境的插接器,建议汽车制造商和供方根据插接器的应用范围选择试液和试验。
QCT29106-2014汽车电线束的检测[整理版]
![QCT29106-2014汽车电线束的检测[整理版]](https://img.taocdn.com/s3/m/e967bccb69dc5022abea001d.png)
QC/T29106汽车电线束性能检测整理导读:汽车使用过程中所出现的相关故障问题,日益成为人们关注的焦点,其中,问题主要集中在汽车线束故障。
汽车线束主要由电线、接插件、包裹胶带和其他辅助性材料共同构成,其结构复杂、功能多样化,被成为整车的“汽车神经”,是控制汽车电信号的载体。
汽车线束是汽车电路的网络主体,没有线束也就不存在汽车电路。
线束是指由铜材冲制而成的接触件端子(连接器)与电线电缆压接后,外面再塑压绝缘体或外加金属壳体等,以线束捆扎形成连接电路的组件。
汽车线束检测是针对汽车线束进行环境测试、电性能测试、机械性能测试的检测项目。
汽车线束是汽车内部最关键的部件之一,其质量、安全性和可靠性对汽车质量具有举足轻重的影响。
如果线束失效,就会造成信号传递失效,功能设备失去作用;或接触电阻过大发热失火;或短路失火;或绝缘层失效漏电。
因而,为了保证汽车线束的品质、安全性和可靠性,汽车线束生产线上或用户使用前检测十分重要。
面对国内汽车线束检测系统功能单一、手段落后,国外汽车线束检测价格昂贵等问题,GRGT 建有专业汽车线束实验室,专注于汽车线束、连接器检测解决方案基础理论和前沿技术的研究、市场转化、技术运用,提供汽车线束环境测试、电性能测试和机械性能测试,满足汽车线束生产厂商对线束导通性和阻抗测试要求。
1整车线束应符合:QC/T29106-2014 汽车低压电线束技术条件。
1.1规定了检验线束尺寸的标准。
1.2规定了电线束中所用材料和零部件所符合的性能要求。
1.3规定了端子与线束的连接方法及连接后应符合的要求。
1.4 规定了端子与线束连接点应符合的要求。
1.5 密封塞在压接时不应损伤。
电线与密封塞之间、密封塞与护套之间不应有目视可见的间隙。
1.6电线束包扎时,应紧密、均匀,不应松散。
采用保护套管时,无位移和影响电线束弯曲现象。
1.7电线束中电线及零部件应正确装配,不应有错位现象,端子在护套中不应脱出。
1.8 电线束中线路导通率为100%,无短路、错路现象。
汽车电线束的检测
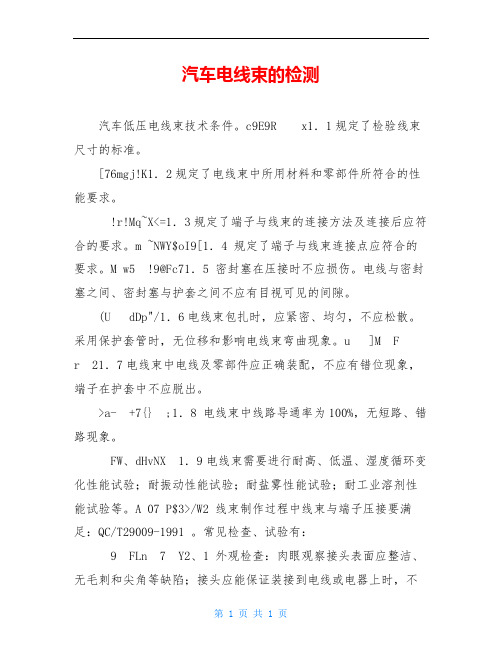
汽车电线束的检测汽车低压电线束技术条件。
c9E9R x1.1规定了检验线束尺寸的标准。
[76mgj!K1.2规定了电线束中所用材料和零部件所符合的性能要求。
!r!Mq~X<=1.3规定了端子与线束的连接方法及连接后应符合的要求。
m ~NWY$oI9[1.4 规定了端子与线束连接点应符合的要求。
M w5 !9@Fc71.5 密封塞在压接时不应损伤。
电线与密封塞之间、密封塞与护套之间不应有目视可见的间隙。
(U dDp"/1.6电线束包扎时,应紧密、均匀,不应松散。
采用保护套管时,无位移和影响电线束弯曲现象。
u ]M Fr 21.7电线束中电线及零部件应正确装配,不应有错位现象,端子在护套中不应脱出。
>a- +7{} ;1.8 电线束中线路导通率为100%,无短路、错路现象。
FW、dHvNX 1.9电线束需要进行耐高、低温、湿度循环变化性能试验;耐振动性能试验;耐盐雾性能试验;耐工业溶剂性能试验等。
A 07 P$3>/W2 线束制作过程中线束与端子压接要满足:QC/T29009-1991 。
常见检查、试验有:9 FLn 7 Y2、1 外观检查:肉眼观察接头表面应整洁、无毛刺和尖角等缺陷;接头应能保证装接到电线或电器上时,不出现断裂或裂纹。
r ; T / 2、2 耐潮试验:在相对湿度为90%~95%,温度为402℃的环境下进行。
试样在耐潮箱中历时100h后,取出并在自然环境下干燥24h后,检查其接触接头必须经受耐潮试验而不破坏其接触可靠性 KE &}*N f[2、3 接头在电线上的接合牢固性试验:在被测接头上用法码或测力计根据线束粗细加规定的静拉力,历时10s后观察之。
{n {} Y、2、4 电压降试验:电压降测定应在完成耐潮试验后进行。
q 5W P >3 汽车用蓄电池电线束接头应满足:QC T29013-91 汽车用蓄电池电线接头型式、尺寸和技术要求。
该标准主要规定了蓄电池电线束与电瓶正、负极接线柱连接的接头尺寸规格。
汽车线束检测方法_概述说明以及解释

汽车线束检测方法概述说明以及解释1. 引言1.1 概述随着汽车技术的不断发展与进步,汽车线束作为电气系统的重要组成部分,起到连接各个电器设备的作用。
而线束的品质和完好程度对汽车性能和安全至关重要。
因此,对汽车线束进行有效的检测方法研究具有重要意义。
本文将介绍汽车线束检测方法的概述及说明以及解释。
首先,我们将从概述、文章结构和目的三个方面来引入本文的主题。
1.2 文章结构本文总共分为五个部分:引言、汽车线束检测方法概述、常见的汽车线束检测方法说明、汽车线束检测方法解释与分析以及结论。
在引言部分,我们将介绍文章整体架构,并带领读者了解文章中各个部分所涵盖的内容。
1.3 目的本文旨在综合总结和探讨当前主流的汽车线束检测方法,包括视觉检测技术、高频无损检测技术和X射线检测技术等。
通过对这些方法进行概述、说明以及解释,我们希望读者可以更加全面地了解每种方法的原理、应用场景和优缺点。
同时,我们也将对当前存在的问题与挑战进行分析并提出未来研究方向和发展趋势的展望。
总而言之,本文旨在为汽车线束检测方法的研究者和从业人员提供一个清晰扼要的概述,并让读者对该领域有更加深入的理解和把握。
通过本文,我们希望能够促进汽车线束检测技术的进步与发展,为汽车行业的可靠性和安全性贡献一份力量。
2. 汽车线束检测方法概述:2.1 线束检测方法的定义汽车线束是指由多种电线组成的复杂系统,用于传输电力和信号以支持汽车的各种功能。
为了确保汽车线束的质量和可靠性,需要对其进行检测和测试。
汽车线束检测方法是指通过使用不同的技术手段来检测和评估汽车线束中存在的问题或缺陷的方法。
2.2 检测目标与需求汽车线束检测方法的主要目标是确保线束中没有任何故障或损坏,并且符合相关规范和标准。
这些故障或损坏可能会导致电气失效、性能下降、安全隐患以及其他问题。
因此,对于汽车制造商来说,实施有效的线束检测方法对于产品质量的控制至关重要。
对于汽车原材料供应商和零部件制造商来说,他们也需要确保提供给汽车制造商的线束符合预期质量标准。
汽车线束技术条件和试验方法-整合_图文(精)

ICSJ021-005汽车线束技术条件和试验方法Test Methods and Performance Requirements for Automotive Wire Harness (草案稿中国·合兴集团有限公司发布Q/HXQ/HX 104— 2006 目次前言 (III)1 范围 (1)2 规范性引用文件 (1)3 术语和定义 (1)4 一般要求 ............................................................................ 3 4.1 默认试验公差 . ...................................................................... 3 4.2 默认试验条件 . ...................................................................... 3 4.3 试验设备 . (2)4.4 测量精度要求 . (2)5 技术要求和试验方法 .................................................................. 2 5.1 总则 . .............................................................................. 2 5.1.1 尺寸特性 [1、 2、3]................................................................. 2 5.1.2 物料特性 ......................................................................... 3 5.1.3 环境温度范围(分级 ............................................................. 3 5.1.4 线束的工作电压范围 ............................................................... 3 5.1.5 接触件样品准备 ................................................................... 4 5.1.6 预处理—连接器和 /或接触件插拔循环 ................................................. 4 5.1.7 外观[3]........................................................................... 4 5.1.8 线路检测 [1](QC/T29106 ......................................................... 5 5.1.9 电连续性监测(瞬断监测 ......................................................... 5 5.2 接触件—机械性能试验 . .............................................................. 6 5.2.1 接触件—接触件插入力 /拔出力[1] .................................................... 6 5.2.2 接触件抗弯性[2]................................................................... 7 5.2.3 绝缘层压接部位的弯折试验[2](QC/T 29106 ......................................... 8 5.2.4 导线—接触件拉脱力[1](USCAR21 ................................................ 8 5.3 接触件—电性能试验 . ................................................................ 9 5.3.1 接触电阻(干电路电阻(总连接电阻[2]........................................... 9 5.3.2 电压降[2]........................................................................ 10 5.3.3 最大电流能力[2].................................................................. 11 5.3.4 1008h电流循环[2]................................................................. 13 5.4 线束—机械性能试验 . ............................................................... 14 5.4.1 接触件—连接器插入力 /拔出力[1] ................................................... 14 5.4.2 连接器—连接器插入力 /拔出力(无机械辅助的连接器 [1].............................. 16 5.4.3 连接器—连接器插入力 /拔出力(带机械辅助的连接器 [1].............................. 18 5.4.4 线束极性防错能力[1].............................................................. 18 5.4.5 连接器其它零件如 CPA 、 PLR 、locator clip的插入力 /拔出力 [1].......................... 19 5.4.6 振动 /机械冲击[2] ................................................................. 20 5.4.7 连接器—连接器装配时的喀哒声[2].................................................. 22 5.4.8 线束跌落试验[2] (22)IQ/HX 104— 20065.4.9 连接器塑件(塑件(塑件(塑件(护套孔的易受损伤性 [2]...................... 22 5.5 线束—电性能试验 . ................................................................. 23 5.5.1 绝缘电阻[2]...................................................................... 23 5.5.2 耐压 [2](ISO16750-2 ............................................................ 24 5.6 线束—环境试验 . ................................................................... 24 5.6.1 可焊性 [2](QC/T29106 .......................................................... 24 5.6.2 耐焊接热 [2](QC/T29106 ........................................................ 24 5.6.3 热冲击(温度循环[2]............................................................ 25 5.6.4 温度 /湿度循环[2] ................................................................. 25 5.6.5 高温试验[2]...................................................................... 27 5.6.6 低温试验 [2](QC/T29106 ........................................................ 28 5.6.7 耐工业溶剂[3].................................................................... 29 5.6.8 浸渍试验[2]...................................................................... 29 5.6.9 压力 /真空泄露[2] ................................................................. 30 5.6.10 盐雾 [2](QC/T29106 ........................................................... 32 5.7 特殊试验 . ......................................................................... 32 5.7.1 连接器安装结构的机械强度[2]...................................................... 32 5.8 严酷环境试验 . ..................................................................... 33 5.8.1 高压水喷射 ...................................................................... 33 5.8.2 严酷振动 ........................................................................ 34 5.9 试验顺序 . ......................................................................... 36 5.9.1 说明 ............................................................................ 36 5.10 推荐的试验项目 . ................................................................... 3 5.10.1 新工具设计、工具更改或材料更改后推荐进行的试验 . (3)5.10.2 新 /现有接触件或连接器设计后推荐进行的试验 (5)6 质量评定程序 ........................................................................7 6.1 鉴定检验 . .......................................................................... 7 6.1.1 抽样 ............................................................................. 7 6.1.2 程序 ............................................................................. 7 6.1.3 合格 ............................................................................. 7 6.1.4 样品处理 ......................................................................... 7 6.2 质量一致性检验 . .................................................................... 7 6.2.1 逐批检验 (7)6.2.2 周期检验 (9)7 标志、包装、运输和贮存 ............................................................. 12 7.1 标志 . ............................................................................. 12 7.2 包装 . ............................................................................. 12 7.2.1 检验:.......................................................................... 12 7.3 运输 . ............................................................................. 12 7.4 储存 . ............................................................................. 12附录 A (规范性附录加速老化试验 ................................................... 13附录 B (资料性附录恒定湿热[2]...................................................... 14附录 C (资料性附录温升[2].......................................................... 15附录 D (资料性附录表 D1 导线—接触件拉脱力 (16)IIQ/HX 104— 2006 前言本规范是修改采用 SAE/USCAR02 Performance Specification for Automotive Electrical Connector Systems 标准。
汽车线束技术条件和试验方法-试验清单
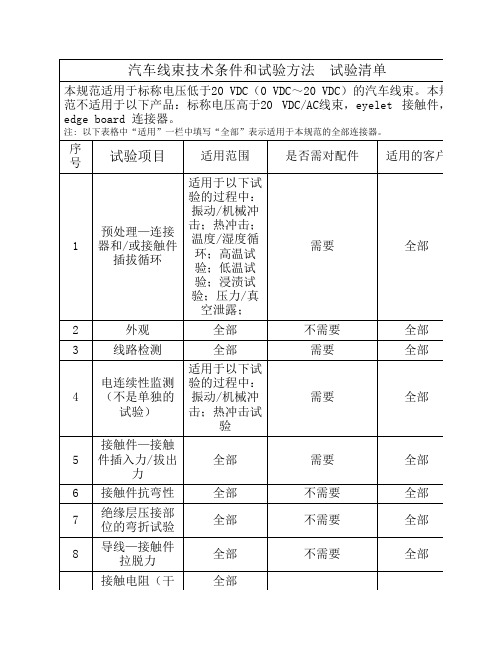
汽车线束技术条件和试验方法 试验清单本规范适用于标称电压低于20 VDC(0 VDC~20 VDC)的汽车线束。
本规范不适用于以下产品:标称电压高于20 VDC/AC线束,eyelet 接触件,edge board 连接器。
注: 以下表格中“适用”一栏中填写“全部”表示适用于本规范的全部连接器。
序号试验项目适用范围是否需对配件适用的客户1预处理—连接器和/或接触件插拔循环适用于以下试验的过程中:振动/机械冲击;热冲击;温度/湿度循环;高温试验;低温试验;浸渍试验;压力/真空泄露;需要全部2外观全部不需要全部3线路检测全部需要全部4电连续性监测(不是单独的试验)适用于以下试验的过程中:振动/机械冲击;热冲击试验需要全部5接触件—接触件插入力/拔出力全部需要全部6接触件抗弯性全部不需要全部7绝缘层压接部位的弯折试验全部不需要全部8导线—接触件拉脱力全部不需要全部接触电阻(干全部9电路电阻)需要全部10电压降全部需要全部11最大电流能力(最大电流能力试验只是为1008h电流循环试验提供电流极限值而已,而不作为接触件在实际应用中的最大电流值)全部需要一级市场客户121008h电流循环(用最大电流能力试验所测得的最大电流进行通电试验)全部需要一级市场客户13接触件—连接器插入力/拔出力全部不需要全部14连接器—连接器插入力/拔出力全部需要全部连接器极性防错能力全部需要全部15连接器其它零件的插入力/拔出力(适用时)根据情况根据情况根据情况16振动/机械冲击全部需要(电连续性监测和预处理—连接器全部和/或接触件插拔循环需要对配件)17连接器—连接器装配时的喀哒声全部需要全部18线束跌落试验全部不需要全部19连接器护套孔的易受损伤性适用于有接触件二级锁(TPA/PLR)的连接器不需要全部20绝缘电阻全部不需要全部21耐压全部不需要全部22可焊性适用于有焊接要求的产品不需要全部23耐焊接热适用于有焊接要求的产品不需要全部24热冲击全部需要(电连续性监测和预处理—连接器和/或接触件插拔循环需要对配件)全部25温度/湿度循环全部需要(预处理—连接器和/或接触件插拔循环需要对配件)全部26高温试验全部需要(预处理—连接器和/或接触件插拔循环需要对配件)一级市场客户:1008h;其他客户:8h27低温试验全部需要(预处理—连接器和/或接触件插拔循环需要对配件)全部28耐工业溶剂适用于密封型连接器不需要全部29浸渍试验适用于密封型连接器需要(预处理—连接器和/或接触件插拔循环需要对配件)全部30压力/真空泄露适用于密封型连接器需要(预处理—连接器和/或接触件插拔循环需要对配件)全部31盐雾全部不需要全部32连接器安装结构的机械强度全部(需要时)不需要全部33恒定湿热可选试验不需要全部34温升可选试验需要全部。
汽车线束检测标准

汽车线束检测标准
汽车线束检测标准主要包括以下内容:
1.导线的电气特性测试。
电阻、电容、电感等参数需要达到规定标准,以确保线束的传输性能符合要求。
2.外观检查。
包括线束外观的清洁度、损坏情况、缠绕程度、绝缘层的破损和划痕等方面。
3.功能测试。
对线束连接器的接触性能、接触阻抗等进行测试。
4.耐热性能检测。
对线束在高温环境下的耐受性进行测试。
5.抗振性能检测。
对线束在振动环境下的稳定性进行测试。
6.耐水性能检测。
对线束在潮湿环境下的稳定性进行测试,确保线束在潮湿环境下不会发生短路或带电现象。
7.防腐能力检测。
对线束的防腐性能进行测试,确保线束在恶劣环境下的长期性能稳定。
8.气密性检测。
对线束接头处的气密性进行测试,确保线束在高压环境下也不会
发生漏电。
总之,汽车线束检测标准的要求比较高,主要是为了保证汽车线束的安全、可靠、稳定性能符合要求。
汽车内部线束耐压试验标准_概述说明以及解释

汽车内部线束耐压试验标准概述说明以及解释1. 引言1.1 概述汽车内部线束耐压试验是对汽车内部电气线束在不同的耐压条件下进行测试,以确保其安全可靠地工作。
线束耐压试验是汽车行业中非常重要且必要的环节,它能够验证线束是否满足国家及行业标准的要求,以提高汽车的整体质量和可靠性。
1.2 文章结构此文将详细介绍汽车内部线束耐压试验的基本概念、重要性以及标准介绍。
接下来的章节将进一步探讨该测试方法,并对其中涉及到的关键要点进行解释和说明。
最后,文章将给出结论和建议,强调对于应用和遵守汽车内部线束耐压试验标准的必要性。
1.3 目的本文旨在为读者提供关于汽车内部线束耐压试验的全面认识。
通过阐述该测试方法的概念、重要性和相关标准,读者能够了解到该测试在保障汽车电气系统安全可靠运行方面所起到的作用。
同时,本文还将深入分析该测试方法中涉及到的关键因素和注意事项,帮助读者更好地理解并正确应用线束耐压试验标准。
2. 正文:2.1 汽车内部线束耐压试验基本概念解释汽车内部线束是指将电器设备连接起来的电线连接系统。
耐压试验是一项用于测试汽车内部线束在高压力、高温度和高湿度等极端条件下的稳定性和可靠性的测试工艺。
在汽车设计和制造过程中,对汽车内部线束进行耐压试验非常重要。
该测试能够确保线束在各种极端环境下仍然能够正常运行,避免因为电线松动、短路或损坏等问题导致的故障和事故。
2.2 汽车内部线束耐压试验的重要性说明汽车内部线束经受着各种外界环境的影响,比如高温、潮湿或者长时间运行后产生的振动等。
如果没有进行适当的耐压试验,这些因素可能会导致电子设备无法正常运作,甚至引发火灾等严重安全问题。
通过进行汽车内部线束耐压试验,可以验证其在不同工况下的稳定性,并评估其安全性和可靠性。
这些测试包括暴露于高温、低温、高湿度等极端环境下以及承受机械压力和振动等。
只有通过耐压试验,汽车制造商才能确保线束的质量,并提供可靠且安全的汽车产品。
2.3 汽车内部线束耐压试验标准介绍在汽车行业,有一系列的标准和规范用于指导和规范汽车内部线束耐压试验。
汽车线束及连接器都有哪些检测项目

十二、电线束与连接器非金属材料分析
机械性能
成分分析
热学性能
塑料电学性能
燃烧性能
十三、电线束与连接器失效分析
失效分析是对已失效的产品进行的一种事后分析工作,通过使用各种测试分析技术和分析程序确认产品的失效现象,分辨其失效模式或机理,确定其最终原因,提出改进设计和制造工艺的建议,来消除失效并防止失效的再次发生,提高电子连接器可靠性,它是产品可靠性工程的一个重要组成部分。
汽车线束及连接器都有哪些检测项目
汽车线束及连接器是汽车电路的网络主体,没有线束和连接器生也就不存在汽车电路。汽车线束和连接器生检测是针对线束和连接器进行环境测试、电性能测试、机械性能测试的检测项目。
汽车线束及汽车连接器是汽车内部最关键的部件之一,其质量、安全性和可靠性对汽车质量具有举足轻重的影响。如果线束或连接器失效,就会造成信号传递失效,功能设备失去作用;或接触电阻过大发热失火;或短路失火;或绝缘层失效漏电。因而,为了保证汽车线束和连接器的品质、安全性和可靠性,汽车线束和连接器生产线上或用户使用前检测十分重要。
牵引车电连接器静载荷
五、机械性能测试
微动腐蚀
插拔循环
连接器对插到位声响
自由跌落
滚筒跌落
金属箍保持力(高压连接器)
振动/机械冲击/三综合
连接器插拔寿命
压接切面检查
线缆剥离力
线缆低温卷绕
线缆冲击
线缆耐磨
线缆标志耐久性
端子与电线的压接强度
绝缘层压接弯折试验
六、环境应力试验
高温Biblioteka 低温恒定湿热湿热循环
冷热冲击
快速温变
参考标准:
ISO 16232道路车辆--流体回路零部件的清洁
汽车低压线束设计验证测试方法(一)
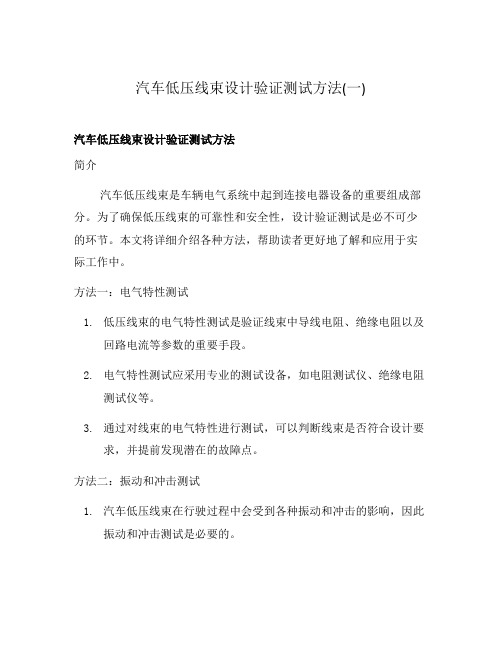
汽车低压线束设计验证测试方法(一)汽车低压线束设计验证测试方法简介汽车低压线束是车辆电气系统中起到连接电器设备的重要组成部分。
为了确保低压线束的可靠性和安全性,设计验证测试是必不可少的环节。
本文将详细介绍各种方法,帮助读者更好地了解和应用于实际工作中。
方法一:电气特性测试1.低压线束的电气特性测试是验证线束中导线电阻、绝缘电阻以及回路电流等参数的重要手段。
2.电气特性测试应采用专业的测试设备,如电阻测试仪、绝缘电阻测试仪等。
3.通过对线束的电气特性进行测试,可以判断线束是否符合设计要求,并提前发现潜在的故障点。
方法二:振动和冲击测试1.汽车低压线束在行驶过程中会受到各种振动和冲击的影响,因此振动和冲击测试是必要的。
2.可以采用振动测试台对线束进行振动测试,包括正弦振动、随机振动等。
3.冲击测试可以通过将线束固定在冲击测试台上,施加冲击力来模拟真实情况下的冲击情况。
方法三:环境适应性测试1.线束使用环境的适应性测试是指对线束在不同温度、湿度、盐雾等环境条件下的性能进行测试。
2.温度适应性测试可以模拟低温、高温条件下线束的工作性能。
3.湿度适应性测试可以模拟潮湿环境下线束的工作性能。
4.盐雾测试可以模拟海边等盐雾环境下线束的耐腐蚀性能。
方法四:绝缘性能测试1.绝缘性能测试是评估线束绝缘层和绝缘材料性能的重要手段。
2.可以通过绝缘电阻测试仪对线束的绝缘电阻进行测试。
3.较高的绝缘电阻值意味着线束的绝缘性能较好,能够有效防止电气短路等问题的发生。
方法五:机械强度测试1.汽车低压线束在安装和使用过程中需要承受一定的机械力,因此机械强度测试是必要的。
2.可以通过拉伸测试、抗扭测试等方法对线束的机械强度进行评估。
3.确保线束具有足够的机械强度,可以避免在使用过程中由于受力过大而导致线束损坏的问题。
结论通过电气特性测试、振动和冲击测试、环境适应性测试、绝缘性能测试以及机械强度测试等方法,可以全面评估汽车低压线束的设计和制造质量,确保线束的可靠性和安全性。
08-线束系统的试验体系
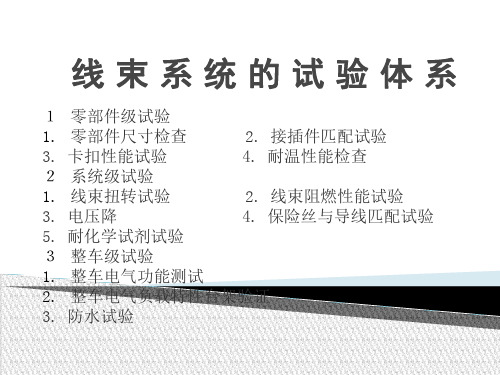
重点检查胶带、波纹管、橡胶件在不同的化学试剂下的性能变化
3 整车级试验
设计验证前移 -》 问题前移 -》 降低开发成本+提高设计质 量
Ø在样车生产前实现电气系统整车匹配试验 Ø实车试验中发生的故障再现和分析 Ø设计阶段利用快速原型实现整车匹配设计验证 Ø各种极限条件下的功能逻辑测试 Ø 特定工况下的功能逻辑测试(各种操作和行驶工况,各种与控制逻辑 相关的环境模拟,工况的组合等等)
n接触点电压降
4.
保险丝与导线匹配试验
Ø使用红外测量仪对整个回路进行温度监测 Ø调整负载,使回路电流与保险规格电流一致 Ø再调整负载,增加电路电流,超过保险规格的135%,记录保险熔断前 线束回路的温度值及保险熔断时间 保险丝熔断前,电线的温度应低于发烟温度,接插件处不应出现熔融痕迹
5.
耐化学试剂试验
单负载测试
全负载测试
Ø对每一个保险丝下的每一个负 载进行测试 Ø还要对每一个保险丝下的所有 负载进行测试
短路测试
潜藏电路测试 测试条件 Ø点火开关关闭 Ø所有车门关闭 Ø所有负防水试验 IPXX:第一标记数字表示电器防尘、防止外物侵入的等级,第二 标记数字表示电器防湿气、防水侵入的密闭程度。
Ø线束需不需要阻燃? Ø阻燃试验该怎么做?
3.
电压降
n整车电压降
需要测量的电压值: U1:蓄电池正极端电压 U2:用电器端电压(电流流进用电器端) U3:用电器端电压(电流流出用电器端) U4:用电器相应搭铁螺栓上的电压 1)U5:蓄电池负极端电压,作为基准电压0V。 2)(U1-U2)+(U3-U5)为回路压降; 3)U2-U3 即为电器实际工作电压
1 零部件级试验
1. 零部件尺寸检查 Ø零部件的尺寸一致性,是零部件能够保持其功能和性能的基础 Ø是零部件能否将进行后续各项试验的基础
汽车用线束波纹管的测试项目与测试方法

1外观目测,管子表面有光泽,不能有小孔、开裂和杂物,内壁光滑平整不允许有滑痕和凸起异物。
保持300—500mm距离,目测波纹管成吕。
并对波纹管的刚性、挠性及弹性作手感测试。
表面光滑无缩痕、流痕、熔迹痕、花斑痕等现象,开槽无错位、漏开及毛边现象。
用肉眼直接观察,内壁可以用光源照看。
塑料波纹管的外观应光滑,色泽均匀,内外壁不允许有隔体破裂、气泡、裂口、硬块及影响使用的划伤。
用肉眼直接观察,内壁可用光源照看。
料波纹管一般为黑色,色泽均匀,内外壁不允许有融体破裂、硬块、严重气泡等缺陷,为了达到较小的摩阻系数,本技术规范中的塑料波纹管为间隔圆形波纹的塑料管2耐寒性弯曲试验(低温柔软性)取5 段300mm 长的波纹管,存放在-40℃的低温箱中4h 后取出,沿4 倍波纹管内径的芯棒弯曲180°然后观察波纹管的外观变化要求波纹管表面不允许产生影响使用的裂纹、龟裂、脆裂等缺陷。
取长度为240mm开口波纹管三支,管中塞入一根直径为管子内径3/4粗细的导线,放入从室温开始的低温箱内,降温到-25±2℃,保持2h后取出,全部绕在金属管上(金属管直径为试样管外径的4倍)要求从箱内取出2min之内卷绕完毕,试样应无脆裂,波纹不变形。
将含75%填充物的波纹管200mm长,存放于-40℃低温中,存放4h,在常温下,将试样放在一个平板上且开口向下,从垂直100mm高处自由落下一个500g的物体,砸在试样上,要求不可以出现变形或裂纹以及影响使用的缺陷。
3热时效试验将5段长为500 mm的波纹管样品,存放于125℃热空气中,存放时间≥500h在常温下以2 倍于波纹管径的半径弯曲波纹管时,不允许出现断裂和裂纹以及影响使用缺陷。
取长度为240mm开口波纹管三支,管中塞入一根直径为管子内径3/4粗细的导线,升温到90±2℃(PE材料)或20±2℃(PP材料)保持2h后,取出检查试样波纹不变形。
根据不同温度等级(85、100、125、150、175、200)选择波纹管各一根,将外径为试样波纹管内径的4/5的电线束穿入380mm长的波纹管中,成为试样,将不同耐温等级的试样放入相应的温度环境中,存放时间为168h,试验后取出样件,在常温下放置30min,要求波纹管不可以发生脆变。
汽车电线束的检测与标准解析(QCT29106)

汽车电线束的检测与标准解析(QC/T29106)汽车线束是连接汽车电子电器部件并使之发挥功能的组件,是汽车电路的网络主体,主要由铜制插接件(插头、插座)和塑料护套、电线等组成,插接件与电线压接后安装在塑料护套内,电线以线束捆扎、胶带包裹构成。
电线束在整车中的作用是将电气系统的电源信号和数据信号进行传递和交换,实现电气系统的功能和要求。
汽车线束遍布汽车的各个角落,有在高温环境下工作的发动机线束、机舱线束,有在尘土飞扬、水、泥浸渍环境下工作的底盘线束,有跨接在门与车身之间长期反复伸缩的车门线束,有承载着大功率器件长期满负荷或过载工作的电力线束等,这些线束随着车辆在高温高湿的南方沿海、严寒的东北地区等恶劣的环境下工作,同时经受着电气热负荷、机油汽油的浸蚀、颠簸振动等条件的洗礼。
所以要保证汽车线束的品质,必须从设计、选材、制造工艺、试验及装配等各个环节加以重视。
1 试验标准解析现行的汽车线束标准主要是QC/T29106《汽车低压电线束技术条件》及各企业的企标,试验项目大概有:检验端子与导线或导线接点的压接品质、接点的防水性能、线束的耐高低温及湿热性能、耐盐雾性能及耐振动性能。
如果按照这些条款进行试验,我们会发现试验结果不尽如人意,如QC/T29106中第4.11、4.12条高低温及湿热试验,标准要求在不工作状态下贮存8h,再在常温下放置24h后,检验电线束的包扎是否松散、绝缘护套是否脱开、电线导通率是否为100%;再如第4.14条耐盐雾试验:电线束经48h中性盐雾试验后导通率应为100%,无短路、错路现象;还有振动试验,按QC/T413规定的耐振动性能来试验,但线束如何安放?标准中并未明确,而且振动后检验的内容主要也只是外观,无电性能方面的检验。
如上种种,经过多年的试验发现,这些试验项目不能完全验证线束及其辅材的材质、设计及工艺,不能完全达到试验验证的目的。
2 试验分类汽车线束试验按结构及材料分为接触件试验和线束试验;按试验类别分为机械性能试验、电性能试验、耐环境试验。
新能源汽车汽车线束环境可靠性试验有那些测试项目

汽车使用过程中所出现的相关故障问题,日益成为人们关注的焦点,其中,汽车线束故障是焦点问题之一。
汽车线束主要由电线、接插件、包裹胶带和其他辅助性材料共同构成,是控制汽车电信号的载体,其结构复杂、功能多样化,被称为整车的“汽车神经”。
汽车线束是汽车内部最关键的部件之一,其质量、安全性和可靠性对汽车质量具有举足轻重的影响。
如果线束失效,就会造成信号传递失效,功能设备失去作用;或接触电阻过大发热失火;或短路失火;或绝缘层失效漏电。
因而,为了保证汽车线束的品质、安全性和可靠性,汽车线束生产线上或用户使用前检测十分重要。
面对国内汽车线束检测系统功能单一、手段落后,国外汽车线束检测价格昂贵等问题。
关于汽车线束试验相关的,不得不说的一些个人看法。
就像汽车一样,线束本身虽然在车上是汽车的一个分件,但是其本身来看,又是一个总成件。
(线束总成内含分件大体包括:CABLE,CONNECTOR,TERMINAL,SPLICE,CLIP,GROMMET,PROTECTOR,TUBE,TAPE 等,稍远点的相关联零件还包括FUSE BOX,FUSE,RELAY等。
)对于总成件来说,个人觉得应该有选择性的做一些确认试验,总成和分件可以不同侧重点地合作完成所有需要考察的试验项目. 而不应该一股脑地来个大杂烩,该做的,无厘头的为了做试验而全部做了。
针对目前看到,听到的一些关于线束试验项目有关的言论,个人觉得不少是欠妥的。
以下是个人关于汽车线束试验项目的罗列.零部件试验:CABLE(一般电线)导体阻抗试验;耐电压(火花耐电压& 浸水耐电压);绝缘体抗拉强度和伸长率;绝缘电阻;耐油性;耐热性;低温性;难燃性;热收缩性;耐磨耗;CABLE(耐振动型电线)构造;导体阻抗;耐电压;耐油性;耐热性;低温性;难燃性;耐振动性;CABLE(耐热电线)追加高温耐久;SHIELD CABLE(屏蔽线)构造试验;耐电压;抗拉强度和伸长率;耐油性;耐热性;耐寒性;难燃性;屏蔽效果;静电容量;编织型扁平接地线外观;构造;导体阻抗; CONNECTOR(接插件) 外观;插座插入/拔出力; 插座卡扣强度;插座与端子保持力; 端子与电线保持力; 端子电压降;插座绝缘阻抗;插座漏电流;耐电压;温度上升;耐磨耗;瞬断;耐板摇性;耐寒性.。
汽车电线束试验标准与方法的研究

汽车电线束试验标准与方法的研究电线束是汽车电气系统中最为关键的零件之一,它由多根电线和连管、绝缘体等辅料组成,具有大量的功能和要求。
为了保证汽车电气系统的正常运行和长久使用,必须对电线束进行严格的试验和检测。
本文将重点研究汽车电线束试验标准与方法。
一、试验标准1、电线束完整性试验:在绝缘壳体完整的情况下,以静态或动态方式施加给定强度的热、振动或静电荷,通过视觉或电性测试等方法,检查电线束的完整性和连接性。
2、电线束电学性能试验:包括触摸电阻、绝缘电阻、导体间绝缘电阻、电容、电感、电压及电流测试等,以检测电线束的电学性能是否满足要求。
3、寿命试验:通过模拟车辆使用的实际情况,对电线束进行长时间的运行试验,以检测其寿命和使用可靠性。
4、环境适应性试验:通过模拟汽车日常使用场景下可能出现的各种恶劣环境条件,如高温、低温、潮湿、振动、盐雾等,检测电线束的适应性和耐久性。
二、试验方法1、眼视法:执行者进行目测,检查电线束外观是否完整,电线及管子连接是否紧固,是否有极性错误及锋锐刀锯口、刮痕等。
2、试验仪法:采用标准的电测试仪器,对电线束进行电性测试,如导通,绝缘电阻、电容、电感、电压及电流测试。
3、环境适应性试验仪法:将电线束置于模拟汽车使用情况下的恶劣环境条件中,以判断电线束是否能够适应不同的环境条件,如高温、低温、潮湿、振动、盐雾等。
4、振动试验仪法:通过模拟汽车行驶时车辆的振动情况,对电线束进行振动试验,以检测其抗振能力。
5、盐雾试验仪法:将电线束置于盐雾试验箱中,以模拟海边及雪地驾驶等恶劣环境,检测其防腐性。
三、总结汽车电线束的试验是保证汽车电气系统正常运行和使用可靠性的关键环节,对于确保汽车安全性和持续性十分重要。
目前,国内汽车电线束试验标准已经形成,并适用于不同电气系统和不同汽车类型的电线束。
同时,随着汽车技术的不断发展和更新换代,试验标准和方法也会不断完善和更新,以适应不同的技术需求和市场需求。
轿车整车线束试验标准

1电线束尺寸JT1-3703-09-68《轿车电线束总成技术条件》中4.2、4.3条。
1、线束的外形用通用量具检验。
2、将线束接点及分支处的胶带拆开,用目测和通用量具检查。
JT1-3703-09-68《轿车电线束总成技术条件》中3.2、3.3条,线束应符合QC/T 29106-2004中4.2.1~4.2.4的规定。
1、线束基本尺寸的极限偏差应符合表1的规定;QC/T 29106-2004《汽车低压电线束技术条件》中4.2.1、4.2.2、4.2.3、4.2.4条。
2、电线束尺寸应符合以下要求2.1 干线和保护套管长度宜不小于 100mm,并为 10的倍数,如:100mm、110mm、120mm等;2.2 支线长度宜不小于30mm;2.3 接点之间,接点与分支点之间距离宜不小于20mm;2.4 电线与端子连接处需装绝缘套管时,绝缘套管长度不得小于20mm。
钢卷尺(通用量具)2端子与电线连接JT1-3703-09-68《轿车电线束总成技术条件》中4.4、4.5条,绝缘层压接部位弯折试验,按照QC/T 29106-2004中5.4的规定进行。
1、线束的外观质量检查用目视法进行检查。
2、绝缘层压接部位弯折试验按图2所示进行。
以轴线为基准,弯折30°,再向相反的方向弯折60°,然后回到轴线这一过程为一个循环。
JT1-3703-09-68《轿车电线束总成技术条件》中3.5、3.8条,端子与电线连接采用压接方法,应符合QC/T 29106-2004中4.4.1、4.4.2、4.4.3、4.4.6.1、4.5.1、4.5.2、4.5.3条。
1、接点应符合以下要求:干区和湿区接点表面绝缘应良好,绝缘材料应靠紧在接点部位上,无位移、脱开现象;2、端子与导线连接采用压接方法,应符合以下要求:2.1 端子应分别压紧在导体和绝缘层上,导体不应压断,绝缘层不应压人导体压接部位,在图2所示的a区中可见电线导体,但不能妨碍插接;2.2 绝缘层压接部位经不少于3个循环的弯折试验后,在图2所示的b区中仍可见绝缘层;2.3 采用压接方法的端子与电线压接处的横断面应符合附录A的要求。
汽车电线束的检测与标准解析(QCT29106)

汽车电线束的检测与标准解析(QC/T29106)汽车线束是连接汽车电子电器部件并使之发挥功能的组件,是汽车电路的网络主体,主要由铜制插接件(插头、插座)和塑料护套、电线等组成,插接件与电线压接后安装在塑料护套内,电线以线束捆扎、胶带包裹构成。
电线束在整车中的作用是将电气系统的电源信号和数据信号进行传递和交换,实现电气系统的功能和要求。
汽车线束遍布汽车的各个角落,有在高温环境下工作的发动机线束、机舱线束,有在尘土飞扬、水、泥浸渍环境下工作的底盘线束,有跨接在门与车身之间长期反复伸缩的车门线束,有承载着大功率器件长期满负荷或过载工作的电力线束等,这些线束随着车辆在高温高湿的南方沿海、严寒的东北地区等恶劣的环境下工作,同时经受着电气热负荷、机油汽油的浸蚀、颠簸振动等条件的洗礼。
所以要保证汽车线束的品质,必须从设计、选材、制造工艺、试验及装配等各个环节加以重视。
1 试验标准解析现行的汽车线束标准主要是QC/T29106《汽车低压电线束技术条件》及各企业的企标,试验项目大概有:检验端子与导线或导线接点的压接品质、接点的防水性能、线束的耐高低温及湿热性能、耐盐雾性能及耐振动性能。
如果按照这些条款进行试验,我们会发现试验结果不尽如人意,如QC/T29106中第4.11、4.12条高低温及湿热试验,标准要求在不工作状态下贮存8h,再在常温下放置24h后,检验电线束的包扎是否松散、绝缘护套是否脱开、电线导通率是否为100%;再如第4.14条耐盐雾试验:电线束经48h中性盐雾试验后导通率应为100%,无短路、错路现象;还有振动试验,按QC/T413规定的耐振动性能来试验,但线束如何安放?标准中并未明确,而且振动后检验的内容主要也只是外观,无电性能方面的检验。
如上种种,经过多年的试验发现,这些试验项目不能完全验证线束及其辅材的材质、设计及工艺,不能完全达到试验验证的目的。
2 试验分类汽车线束试验按结构及材料分为接触件试验和线束试验;按试验类别分为机械性能试验、电性能试验、耐环境试验。
- 1、下载文档前请自行甄别文档内容的完整性,平台不提供额外的编辑、内容补充、找答案等附加服务。
- 2、"仅部分预览"的文档,不可在线预览部分如存在完整性等问题,可反馈申请退款(可完整预览的文档不适用该条件!)。
- 3、如文档侵犯您的权益,请联系客服反馈,我们会尽快为您处理(人工客服工作时间:9:00-18:30)。
绝缘胶带是以乙烯树脂为主体的混合拉 常温 开的粘 加热后 合力 拉 伸 常温 强度 加热后 延 伸 常温 率 加热后 耐寒性
耐燃烧性 耐电性 加热性
粘合剂不能移到下层背面 60gf/19mm 宽以上 60gf/19mm 宽以上
2Kgf/19mm 宽以上 2Kgf/19mm 宽以上 100%以上 80%以上 不能产生影响使用的变形、 割裂、龟裂等 30 秒内自动熄灭 耐 1000V 电压 1 分钟 不能产生影响使用的变 形、割裂、龟裂
样品放在火焰中 15 秒,移去火焰,样品在 15 秒内自 动熄灭。
按 JASO D 618-97 14.2 项
在 150℃下加热 15 分钟,热收缩量为 4%以下.
凝胶化在 50%以上 不能有剥落和褪色发生
在 70℃下加热 144 小时,电线外套最大收缩量为 4mm
规定的单位电阻值为 109Ω·mm 以上
项目要求
备注
重要
能耐 5000V 电压至少 0.15 秒;浸水时耐 1000V 电压 1 分钟 抗拉强度最小 15.7Mpa{1.6kgf/mm2};伸长率为 125% 以上 浸在 50℃的油中 20 小时并弯曲后,样品能承受 1000V 电压 1 分钟。 在 120℃下加热 168 小时并弯曲后,样品应能耐 1000V 电压 1 分钟 以自己的直径卷绕成试样,放在 200℃下加热 30 分钟, 导体应无裂纹及熔化的现象. 样品在-40℃下冷却 3 小时后折弯,应能耐 1000V 电压 1 分钟。
产品开发技术协议
共6页 第4页
序 号
项目
四 电气特性要求
24040 P2750 1. 耐电压性
2. 导体
3. 耐油性
4. 耐热性(1)
5. 耐热性(2)
6. 低温试验
7. 耐火试验
8. 耐磨耗试验 9. 热收缩 10 交联等级 11 标记强度 12 热收缩性(2) 13 绝缘性 五 绝缘胶带性能
重要度