回转窑内衬图内衬方案图
回转窑危险废物焚烧炉耐火内衬设计及优化建议技术前沿

回转窑危险废物焚烧炉耐火内衬设计及优化建议技术前沿危险废物(以下简称危废)种类繁多、成分复杂、区域差异化严重,处理不当会带来一系列民生和社会问题。
实践证明,高温焚烧是危废安全处置和减容化的有效途径,其中回转窑焚烧工艺是危废处理中最有效的处置工艺之一,具有处理危废种类多、处理量大等优点。
我国自20世纪90年代,逐步开始使用回转窑焚烧系统处理危废。
近年来,因耐火材料损毁导致的停窑事故多有发生,严重影响了危废焚烧生产线的稳定运转率,对回转窑危废焚烧炉耐火内衬设计优化以及高效运行等提出了迫切需求。
1、我国危险废物无害化处置现状我国的危废处置从1990年开始起步,到1996年初步形成相关管理体系,直至2008年才形成《国家危废名录》, 2013年,两高司法解释,“非法排放、倾倒、处理3吨以上危废将入刑”,被视为我国危废处理行业启动的关键点。
2016年上半年,《土壤污染防治行动计划》、《国家危险废物名录(2016年版)》等危废处理相关专项规划的相继颁布实施,2017年,《“十三五”全国危险废物规范化管理督查考核工作方案》颁布,2018年,生态环境部开展“清废行动2018”计划、工信部开展长江经济带工业绿色发展行动,2019年11月12日,生态环境部办公厅发布《危险废物焚烧污染控制标准(二次征求意见稿)》, 2020年3月10日,国家标准《固体废物玻璃化处理产物技术要求(征求意见稿)》公开征求意见等,均让危废处理行业发展提速,进一步催化危废处理行业发展机遇。
随着工业的发展,生产过程排放的危废日益增多。
2016年, 214个大、中城市工业危废产生量达3344.6万吨,其中,工业危废综合利用量占利用处置总量的45.3%,处置、贮存分别占比43.8%和10.9%,有效地利用和处置是处理工业危废的主要途径。
2018年, 200个大、中城市工业危废产生量达4643.0万吨,预计2020年因为疫情原因,危废将增至近1亿吨。
回转窑设计方案手册

回转窑的设计一、窑型和长径比1.窑型所谓窑型是指筒体各段直径的变化。
按筒体形状有以下几种窑型:(1)直筒型:制造安装方便,物料在窑内移动速度较均匀一致,操作控制较易掌握,同时窑体砌造及维护较方便;(2)热端扩大型:加大单位时间内燃烧的燃料量及传热量,在原窑直径偏小的情况下,扩大热端将相应提高产量,适用于烧成温度高的物料;(3)冷端扩大型:便于安装热交换器,增大干燥受热面,加速料浆水分蒸发,降低热耗及细尘飞损,适用于处理蒸发量大、烘干困难的物料;(4)两端扩大型(哑铃型):中间的填充系数提高,使物料流动的机会减少,还可以节约部分钢材;还有单独扩大烧成带或分解带的“大肚窑”,这种窑型易挂窑皮,在干燥带及烧成带能力足够时,可以显著提高产量。
但这种窑型操作不便。
总之,不论扩大哪一带,必须保持预烧能力和烧结能力趋于平衡。
只有在生产窑上,经过生产实践和充分调查研究(包括必要的热工测定和计算),发现某一带确为热工上的薄弱环节,在这种特定条件下将该带扩大,才会得出较明显的效果。
目前国内外发展趋势仍以直筒型窑为主,而且尺寸向大型方面发展。
其他有色金属工业用回转窑(还原、挥发、硫化精矿焙烧、氯化焙烧、离析、烧结转化等)多采用较短的直筒窑。
2.长径比要得长径比有两种表示方法:一是筒体长度L与筒体公称直径D之比;另一是筒体长度L与窑的平均有效直径D均之比。
L/D便于计算,L/D均反映要的热工特点更加确切,为了区别起见,称L/D均为有效长径比。
窑的长径比是根据窑的用途、喂料方式及加热方法来确定的。
根据我国生产实践的不完全统计,各类窑的长径比示于表1中。
长径比太大,窑尾废气温度低,蒸发预热能力降低,对干燥不利;长径比太小,则窑尾温度高,热效率低。
同类窑的长径比与窑的规格有关,小窑取下限,大窑取上限。
表1各类窑的长径比窑的名称公称长径比有效长径比氧化铝熟料窑(喷入法)20~2522~27氧化铝焙烧窑20~2321.5~24碳素煅烧窑13.5~1917~24干法和半干法水泥窑11~15——湿法水泥窑30~42——单筒冷却机8~12——铅锌挥发窑14~1716.7~18.3铜离析窑——15~16氯化焙烧窑——12~17.7二、回转窑的生产率回转窑生产是一个综合热工过程,其生产率受多方面因素影响。
回转窑的结构与工作原理 (2)ppt课件
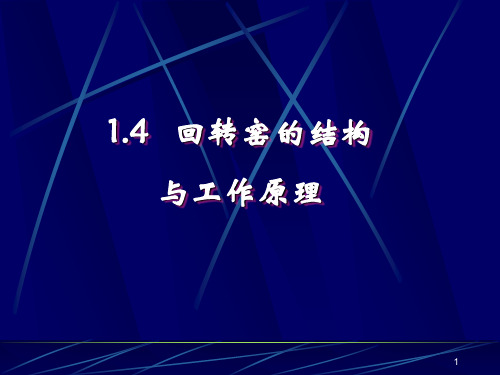
思考:
烧成温度偏低时,适当 A、增大外风 B、减少煤风 √ C、增大内风 D、减少内风
46
排风大,火焰变() 料少,火焰() 煅烧温度高,火焰() 煤粉粗、湿、灰分大、挥发分低、固定 碳多,火焰() 煤多一次风少,一、二次风温度低,火 焰()
47
四通道回转窑燃烧器
直流风速:140m/s~250m/s;压力:≥0.014MPa 旋流风速:110m/s~250m/s;压力:≥0.014MPa 煤流风速:20m/s~35m/s 可调 中心风速:60m/s 占一次风总量的0.03%~0.05%
窑体每班上下移动
筒体
1~3次,每次移动
幅度约50mm
上下移动可通过:
托轮的倾斜
液压挡轮完成。
止动挡轮
11
4、液压挡轮
1、液压挡轮是围绕纵向轴运动的滚轮安装在 窑尾轮带靠近窑头侧的平面上。
2、作用:及时指出窑体在托轮上的运转位置 是不否合理,并限制或控制窑体轴向窜动。
12
5 传动装置
目的:保证窑的旋转和调节窑的转数
16
薄片式密封
密封要求具有足够大的摩 擦表面,密封性好,同时 对窑的弯曲偏摆等具有很 大的适应性。此外零件加 工、更换和找正都较方便
1mm厚
17
7 辅助设备
烧成带的轴流风机:利于窑皮的形成,保护筒体
18
传感器
筒体温度传感器; 用来测定窑传动力矩的电流表或功率表; 窑纵向高位或地位的传感器,用于控制液压挡轮。
35
煤粉燃烧过程的控制
控制内容有:火焰的温度、长度、着火位置及形状
(1)什么是火焰?
火焰是燃烧中的气体混合物,当悬浮物中含有固体颗粒时, 形成明亮火焰。
第三章_原料煅烧窑-回转窑
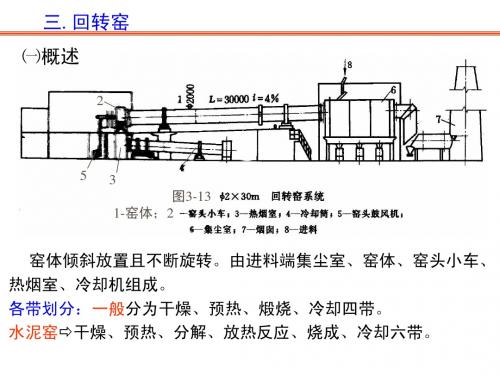
回转窑
冷却筒
热交换
窑尾
出料
冷空气
(靠窑尾排烟机在窑头处产生的负压吸进来)
特点:
优点:结构简单,坚固;热效率高,电耗低。 缺点:冷却效果差,扬尘大。
多筒冷却机:
由围绕窑的卸料端的6~14个冷却筒构成。属于逆
流工作方式。冷却空都是靠窑尾排烟机在窑头处产生
的负压吸进来。
篦式冷却机:
㈢回转窑的工作原理
1.物料的运动 理想状况不考虑物料颗粒在窑壁上和料层内的滑动, 以及物料颗粒大小对物料运动的影响。图3-20。 实际状况物料间由于粉料的存在或加料量太少,粉料 或中间一层物料不能与其它物料均匀混合,往往夹在中 间滑动。
煅烧带
预热带
窑尾(冷端) 集尘室
冷却机 出料
二次空气
除尘器 烟 囱
排出
㈡ 回转窑的结构
1.窑体 ⑴窑体形式: 直筒形—窑体直径相同,结构简单,便于制作和维修; 热端扩大型—扩大燃烧区域(煅烧带)的直径,加大煅烧带的
容积,提高窑的发热能力,同时加大火焰气体辐射层的厚度, 改善了窑内高温区域的传热。 冷端扩大型—扩大干燥带和预热带,提高窑的预热能力,降低 窑尾风速和废气温度。主要用于湿法长窑。 哑铃型—冷端扩大是为了放置热交换装置而不致过多地提高气 体的流速,热端扩大是为了提高窑的发热能力,中间收缩可节 省钢材。
③液压挡轮 。
结构 图3-16。挡轮布置于滚圈的下侧,通过
空心轴支撑在两根平行的支承轴(由上底座、下
底座固定在基础上)上。空心轴可在活塞—活塞 杆的推动下,沿支承轴轴向滑移。
图3-16
工作原理设有这种挡轮的窑,托轮与滚圈可以平行安装,窑筒 体在下滑力的作用下向下滑动,到达一定位置后触动限位开关而 启动液压油泵,靠液压油的压力推动活塞—活塞杆,从而推动挡
水泥回转窑结构图及水泥回转窑流程宏科

水泥回转窑结构图及水泥回转窑原理讲解水泥回转窑结构图水泥回转窑模型图解1 水泥回转窑生产工艺简介整个工艺流程主要有生料粉末预均化,五级旋风预热,预分解,窑内煅烧,蓖冷机冷却及熟料粉碎等工序组成。
2 水泥回转窑原理讲解:水泥回转窑生产自动化对DCS系统的要求对于年产30万吨水泥生产线,按工艺及实现生产过程控制对DCS系统有如下要求:(1)根据厂方的具体技术要求,目前DCS主要监控生产线的四大部分:窑头、窑中、窑尾和煤粉制备。
共设置560个I/O点,其中模拟量输入72点,模拟量输出25点,数字量输入267点,数字量输出139点,热电偶及热电阻分别为22点和35点。
窑头、窑中(点) 窑尾(点) 煤粉制备(点)AI 21 11 40AO 7 6 12DI 112 48 107DO 64 20 55RTD 5 16 14T/C 3 4 15(2)根据该水泥厂实际情况和生产工艺,整个回转窑系统共设置12个控制回路,其它各设备则采用直接控制和顺序控制方式。
12个控制回路中,压力控制回路6个,流量控制回路3个,料位控制回路1个,温度控制回路2个。
(3)为减轻人工操作强度,提高自动化程度和系统可靠性,由DCS系统实现联锁保护功能。
同时为了操作方便和直观,在工作站界面中,将工艺流程及各种运行设备工况按比例设计操作界面,并随时对各部位进行动态显示。
测量值如温度、压力、流量、料位等数据实现动态显示,阀位开度以百分比表示,料位用彩色棒图动态模拟。
不同物料管道用不同颜色来区别,其物料流向用箭头表示。
(4)为了对生产进行有效监控,以便优化工艺条件如故障查找,对32个重要参数用历史趋势曲线进行汇总。
如回转窑各段的窑温,五级旋风及窑尾分解炉等处的温度、压力等,以及各控制回路的测量值等,以上就是关于水泥回转窑原理讲解和水泥回转窑结构图的讲解。
回转窑技术参数及工作原理图.ppt

由于填充率低、传热条件差,窑的热效率仅 30~40%
2.2 回转窑的结构参数
第 5
长径比: 窑的长度与直径的比值称长径比,其表示方法
有两种。即有效长度L与筒体内径D之比L/D;二为L与
章
窑体砌砖后的平均有效直径 之比,L/ D称为有效长径
比。
回 转
窑型:按其筒体形状可分为四种, ①直筒型:中型窑较
3 回转窑的运转参数及生产能力
3.1 运转参数
第 窑内物料的填充系数(填充率): 是窑内物料层
5 章
截面与整个截面面积之比或窑内装填物料占有
体积与整个容积之比用符号 φ表示
回 转 窑
??
AM
2
π 4
D
或
??
4G M
2
60 π D v M ρ M
式中AM—窑内物料所占弓形面积,m2 ; GM—单位时间内窑内物料流通量,t ·h-1 ; VM—窑内物料轴向移动速度,m ·min-1 ; ρM—窑内物料体积密度,t ·m-3。
到支承装置上,是回转窑最重的部件。
回
? 支承装置 :承受回转部分的全部重量,它是由一对托轮轴承组和一个大底
座组成。
转 窑
? 传动装置 :回转窑的回转是通过传动装置实现的。
? 窑头罩和窑尾罩 :窑头罩是热端与下道工序中间体;窑尾罩是冷端与物料
预处理设备及烟气处理设备的中间体。
? 燃烧器 : 燃烧器一般是从筒体热端插入;有喷煤管、油喷嘴、煤气喷嘴等。
第
表2-2-2 斜度与填充系数的关系
5
章
回
转 斜度i (%) 5.0 4.5 4.0 3.5 3.0 2.5
窑
填充系数 φ(%) 8.0 9.0 10.0 11.0 12.0 13.0
水泥行业回转窑的详细结构及工作原理
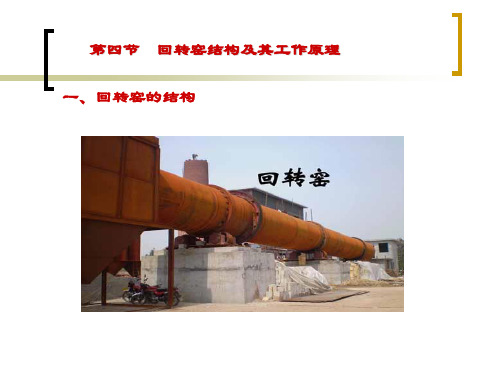
在对回转窑内物料运动的规律进行分析和模拟试验后,得出 很多计算回转窑内物料运动的速度的公式其中最为常用的一般公 式为:
vm
Di n Di n L , (m / s ) , (m / min) 60 m 60 1.77 1.77
式中:
vm
m
—物料在窑内运动的速度,m/s; L—窑的长度,m; —物料在窑内停留的时间:
影响窑内火焰长度的因素:有很多。主要有:燃烧速度和窑 内气体的流速。 燃烧速度:
粉煤的细度、煤粉与空气混合情况、一、二次风的温度
等因素有关。
煤粉粉愈细,或在喷煤管内加装风翅,以加还煤与空气
的混合,或提高一、二次空气的温度,均能提高燃烧速度, 而使火焰短。
风煤的混合速度和均匀程度也是影响燃烧速度的关键。
第四节
回转窑结构及其工作原理
一、回转窑的结构
海螺水泥厂
回转窑齿圈
托
轮
挡
轮
窑筒体轴向位移
窑筒体
轮带 挡轮
图2-72
轮带与挡轮
轮
带
回转窑轮带的润滑
Байду номын сангаас
轮 带 节
迷宫式密封装置是利用空气多次通过曲折通道增 大流动阻力而防止漏风的。
固定迷宫环
活动迷宫环 窑筒体
图2-73
迷宫式密封装置示意图
燃料燃烧的火焰温度要达到1600~1800℃;(保持高温) 火焰要有适当的长度;(保持物料高温时间) 处于适当的位置。(适合 C3 S 的形成的反应)
2、回转窑对入窑煤粉和助燃空气的要求
(1)对入窑煤粉的质量要求
低热值:
g QDW 20600 kJ / kg
挥发份:
灰分: 水分:
回转窑结构及工作原理
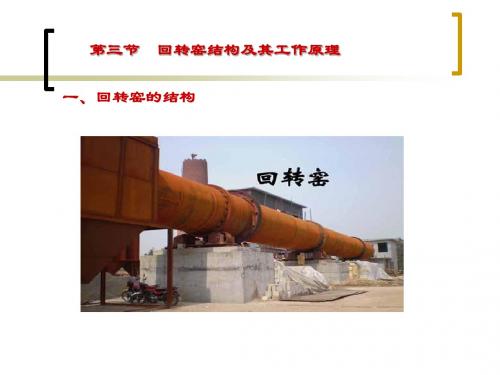
(2)火焰温度分布(火焰形状)
窑内火焰温度分布,通常是两头低、中间高。热端较低温度 区就是窑内的冷却带。
煤粉从喷管喷出后,须经过干燥预热至700~800℃才着 火燃烧,回转窑中所看到的黑火头就是煤粉从喷出后至着火 燃烧前气流所移动的距离。黑火头长则使回转窑的传热面积 减小,对产量、质量不利,黑火头过短则冷却带短,熟料离 窑的温度提高,增加冷却机的负荷。
窑尾风速增大,回转窑的飞灰量增多,一般,窑 内的飞灰量与窑尾风速的2.5~4次方成正比。
(三)回转窑内燃料的燃烧
在回转窑的烧成带,物料进行的主要物理化学反应是 C 2 S 吸收 f CaO 生成 C 3 S ,这是微吸热反应。为了使生成 C 3 S 的反应完全,必须使物料在1400~1450℃的高温下停留 一定的时间。
(一)回转窑内物料的运动 1、物料在窑内的运动过程
生料从窑的冷端喂入,在向热端运动的过程中煅烧成熟料。
物料在窑内的运动情况直接影响到物料层温度的均匀性; 物料的运动动速度影响到物料在窑内的停留时间(即
物料的受热时间)和物料在窑内的填充系数(即物料的受 热面积);因此也影响到物料和热气体之间的传热。
水泥回转窑窑尾密封装置
窑 尾 密 封
窑尾密封及冷风套
接触式密封装置
弹簧
摩擦板 筒体
密封装置
二、回转窑的工作原理
物料回转窑内煅烧的过程是生料从窑的冷端喂入,由 于窑有一定的倾斜度,且不断回转,因此使生料连续向热 端移动。燃料自热端喷入,在空气助燃下燃烧放热并产生 高温烟气,热气在风机的驱动下,自热端向次端流动,而 物料和烟气在逆向运动的过程中进行热量交换,使生料烧 成熟料。因此,研究回转窑的工作原理,主要是研究物料 在窑内的运动,窑内气体的流动,燃料燃烧和物料与气体 间传热的现象和规律。
回转窑的结构与工作原理PPT幻灯片
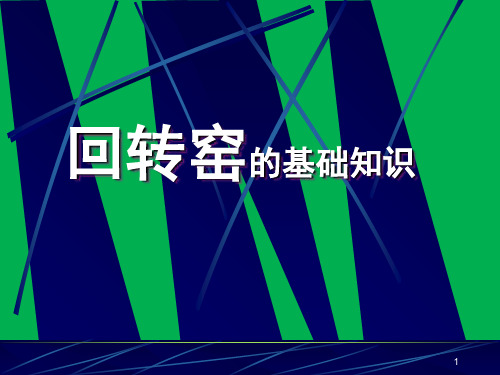
每次移动幅度约50
mm以内上下移动
可通过:
托轮的倾斜
液压挡轮完成止。动挡轮
21
托轮其直径一般为轮带的1/4,宽比轮带宽 50~100mm,为什么?
考虑冷窑和热窑时 轮带的位置不同, 同时移动轮带使托 轮整个表面受到均 匀的磨损,否则会 留下沟纹,无法正 常工作。
4/23/2020
22
5、液压挡轮
4/23/2020
29
6 密封装置
组成端面密封的两个摩擦环之一是固定在径向 密封环上的固定摩擦环,另一个是与连接在窑 筒体上的回料勺连接在一起的活动摩擦环,它 是随窑一起转动的。通过均匀设置在径向密封 环圆周上的若干个气缸的活塞杆产生的作用力, 推动径向密封环使两个摩擦环始终保持接触状 态。为了减轻两摩擦环接触面间的磨损,由电 动干油泵将润滑脂送进摩擦环来进行润滑,密 封可靠。
4/23/2020
34
6 密封装置
情况下仍能保持良好机械 性能,从而保证密封效果及 使用寿命。彻底解决回转部 件与固定部件间的漏风、漏 灰问题,提高窑头三次风温 保证正常的热工环境。
4/23/2020
35
7 辅助设备
烧成带的轴流风机:利于窑皮的形成,保护筒体
4/23/2020
36
传感器
筒体温度传感器; 用来测定窑传动力矩的电流表或功率表; 窑纵向高位或地位的传感器,用于控制液压挡轮。
液压挡轮装置主要由挡轮、挡轮轴、轴承体、 导向轴、滚动轴承、挡轮行程开关装置等组 成。挡轮设置在靠大齿圈邻近轮带的下侧。 通过液压挡轮迫使轮带和窑筒体一起按一定 的速度和行程沿窑中心线方向在托轮上往复 移动,使轮带和托轮在全宽上能均匀磨损, 以延长使用寿命。 液压挡轮的示意图:
多段炉与回转炉全面对比分析(1)
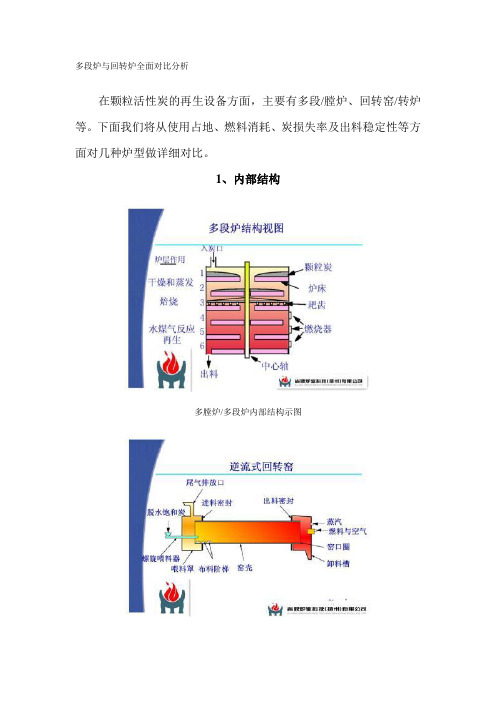
多段炉与回转炉全面对比分析在颗粒活性炭的再生设备方面,主要有多段/膛炉、回转窑/转炉等。
下面我们将从使用占地、燃料消耗、炭损失率及出料稳定性等方面对几种炉型做详细对比。
1、内部结构多膛炉/多段炉内部结构示图气固相物料逆向接触式/逆流式回转窑/转炉结构示图气固相物料同向接触式/顺流(并流、平行)式回转窑/转炉结构示图2、设备的运行和使用情况2.1占地回转窑对于工厂用地,建筑用地及附属结构所需用地要大于多段炉。
2.2燃料消耗多段炉内衬砖后面的隔热材料的使用能够减少热量的损失,而类似的隔热材料是不能够用于回转窑上的,另外回转窑表面积大,热量损失大。
炉型能量消耗(KJ/KG炭)多段炉5815至10467回转窑8141至186082.3炭损失率回转窑因其内部环境的不稳定性容易造成损失率高于多段炉,并且各个批次的物料情况也波动较大。
2.4 多段炉热再生活性炭之优势(1)可对再生工艺参数进行严格控制,尤其在炉膛气氛——蒸汽比率和燃气用量——的控制方面更是如此;(2)可降低由气化反应引起的炭损耗率,该项损失率一般在3%到5%范围内,比其它类型的再生炉炭损失率(一般在5%到10%范围内)要低得多;(3)可降低因机械磨耗导致的炭损失率;(4)单位产品的能耗较低,通常在1380 到2500kcal/kg再生炭范围内;(5)固相活性炭与气相活化剂的相接触几率高(反应速率快),故炉子的最小设计容量比率可允许降低到35%的水平,装置系统更加紧凑;(6)结构简单、坚固,使用寿命长,保养维修容易;(7)运转操作简单,最适合自动化,易于管理;(8)装置系统占地面积小;(9)对负荷波动安定性好。
(10)值守工人少(1到2人)(11)热值利用高。
定点供热高效利用热能,可满足氧化性、还原性及中性气氛需要。
(12)多段炉炉床采用异形耐火砖铺设,相互锁紧,稳定性高,不脱落。
回转窑因空腔内无支撑耐火砖或耐火金属之结构,在高温且重力作用下易出现坍塌、断裂的情况,且修复处易出现反复脱落情况。
回转窑的结构1-24

• (3)N-KSV分解炉 • 如图1-9,这是川崎公司开发的喷腾与旋流相结合的炉型,其特点: • ⊙ 直接与窑尾烟室相接,下部锥形,窑气作喷腾流动上升入炉;中部柱体, 三次风以切向旋转流入,中间设一道缩口、形成二次喷腾效应,最上面还设 有缩口以促进混合。 • ② 分解炉也可分为四个作业区如图1-9。 • 喷腾床——主要燃料喷咀布置在这一区域,燃料在窑气中开始燃烧,形成的 NOx少。 • 旋涡室——由于三次风切向送入,和C3来的部分热生料,在此得到充分分散 与混合,燃烧与分解反应得以强化,而且不致形成明火焰。为了调节的需要, 在此设有辅助喷咀,可适当增加煤粉用量,调节控制炉温在860~ 870C上下。 • 缩口区——由于加速作用,形成了一种补充的次喷腾效应,其目的为进一步 促进混合与反应。 • 混合室——使气固分散与均布得到强化,以完成燃烧反应和满足分解率的要 求。 • 为了进一步降低能耗,川崎公司又开发了KS-5分解炉系统。即采用5级旋风 筒与上述 • KSV炉相组合,其中C2、C3两级选用了卧式旋风筒,其余各级旋风筒入 口形状也有改进,从而使全系统热损失与动力消耗均有所下降。
• (6)M-MFC分解炉
• 系日本三菱公司所开发,初期主要用密相流化床作为分解炉,后来为了进一 步节能,改进了炉型的相对尺寸并改变三次风入炉的流型。新型的带部分 旋流风的分解炉系统如图2-63。其主要特点是: • ① 分解炉底部设有一截面不大的多孔板,用3~5kPa高压风机鼓入流化风 (占总风量8~10%), 建立生料与燃料的密相流化床区; 煤粉喷咀设在流化床 上部,C4来的生料自流化床侧面加入,混合非常均匀,燃烧、换热、分解反 应开始进行,物料在床内停留时间达2min之久。 • ② 三次风在分解炉下锥底部分,送入到流化料层上部,切向进入,形成一定 的旋转流,携带流化生料形成了涡流床区。充足的空气,使反应激烈进行。 • ③ 气料流在经过下锥部分变速形成了涡旋混合作用,促进了气固传热与反 应。 • ④ 细长的柱体部分,使高温气流与粉料进一步均化形成了稀相悬浮态流 动,完成要求的反应程度。自顶部排出,与出窑高温气体在上升烟道内 汇集,进一步完成燃烧与分解反应,再入C5气固分离后,分解率达90%的 热生料入窑。 • 值得强调的是在N-MFC系统中,为了充分利用窑尾烟气中的高温热量和过 剩的氧气,对分解妒本身的反应完成度有所控制。即强调了全系统的优化 组合,达到减少废气量,降低热耗和NOx排放量的实效。为此MFC分解炉实 际的炉温控制较低,过剩空气系数也较小。
回转窑结构及其工作原理
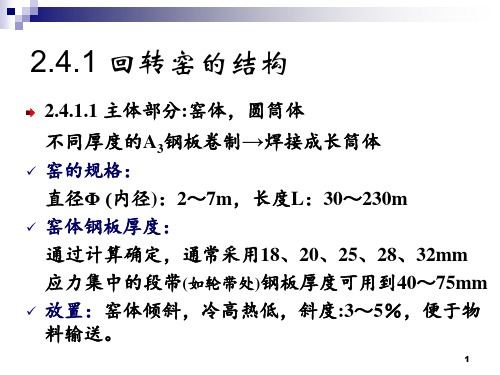
2.4.1.3 传动系统
大齿轮:安装在筒体中部或略近窑尾,转速 约1~4r/min 机械传动、液压传动: 机械传动:需要减速比很大的减速机,将主 电机的高速旋转传给小齿轮,再与筒体上大 齿轮啮合而带动窑回转 功率:主电机W>250KW,采用双传动系统
10
11
12
2.4.1.3 传动系统
无级变速装置:回转窑运行时需要改变转 速 辅助传动设备:避免临时断电停窑或事故 停窑,筒体热重力变形造成的弯曲 断电时能维持窑每小时1-4r的慢转
1
2
2.4.1.2 支撑装置
轮带、托轮、挡轮 轮带 托轮:窑筒体借助轮带支撑在成对的托轮上,托
轮固定在混凝土基础的架子上 2~9对
限制径向位移
挡轮:限制并检验窑体在加热、运转时的纵向移 动,在传动设备附近的轮带两侧安装一对挡轮 承受窑回转时全部重力,限制窑体径向轴向位移, 使筒体安全平稳回转
29
料层厚度与运动速度
窑内物料填充率高,被带起的高度高,回 转一周时间内,物料被带起的次数少,即 翻动次数少,受热的均匀性差;
近代煅挠技术都是在密切注视筒体表面温 度不过高的情况下,采取快转薄层煅烧的 方法
18
2.4.2.1 回转窑内物料的运动
物料在窑内的运动方式 料层温度均匀性 物料运动速度(窑内停留时间) 物料受热时间、反应时间
19
2.4.2 回转窑的工作原理
物料在窑内填充系数
窑内堆积物料所占体积
相应窑的总容积 100 %
气固换热的有效接触表面积 窑内气体流动的速度、阻力损失
度并改变窑的转速可
控制物料在窑内的停
留时间
25
②
①
③