各 种 表 面 处 理 工 艺 防 腐 时 间
常用金属表面处理工艺及技术

金属表面处理工艺一、表面热处理1、表面淬火 n 表面淬火是指在不改变钢的化学成分及心部组织情况下,利用快速加热将表层奥氏体化后进行淬火以 强化零件表面的热处理方法。
感火焰加热 应加 热n 表面淬火目的: n ① 使表面具有高的硬度、耐磨性和疲劳极限; n ② 心部在保持一定的强度、硬度的条件下,具有足够的塑性和韧性。
即表硬里韧。
n 适用于承受弯曲、扭转、摩擦和冲击的零件。
轴 的 感 应 加加 热 表 面 淬淬 火n ①表面淬火用材料 n ⑴ 0.4-0.5%C的中碳钢。
n 含碳量过低,则表面硬度、耐磨性下降。
n 含碳量过高,心部韧性下降; n ⑵ 铸铁 提高其表面耐磨性。
机床导轨表面淬火齿轮n ②预备热处理 n ⑴工艺: n 对于结构钢为调质或正火。
n 前者性能高,用于要求高的重要件,后者用于要求不高的普 通件。
n ⑵目的: n 为表面淬火作组织准备; n 获得最终心部组织。
回火索氏体 索氏体n ③表面淬火后的回火 n 采用低温回火,温度不高于200℃。
n 回火目的为降低内应力,保留淬火高硬度、耐磨性。
n ④表面淬火+低温回火后的组织 n 表层组织为M回;心部组织为S回(调质)或F+S(正火)。
感应加热表面淬火 感应淬火机床n ⑤表面淬火常用加热方法 n ⑴ 感应加热: 利用交变电流在工件表面感应巨大涡流, 使工件表面迅速加热的方法。
感应加热 表面淬火示意图n 感应加热分为: n 高频感应加热频率为250-300KHz,淬 硬层深度0.5-2mm火传 感动 应轴 器连续 淬感应加热表面淬火齿轮的截面图n 中频感应加热 频 率 为 25008000Hz , 淬 硬 层 深度2-10mm。
中频感应加热表面淬火的机车凸轮轴各种感应器n 工频感应加热 n 频率为50Hz,淬硬层深度10-15 mm感应穿透加热各种感应器n ⑵ 火焰加热: 利用乙炔火焰直接加 热工件表面的方法。
成本低,但质 量不易控制。
铝件阳极氧化耐盐雾时间

铝件阳极氧化耐盐雾时间铝合金压铸件化学钝化表面处理在近年来得到了广泛关注,其耐盐雾性能达到1000h以上,性能成本效率优于现有的阳极氧化、喷粉、电镀、电泳等表面处理工艺。
这款化学钝化处理剂的出现,填补了铝合金压铸件在1000h以上耐盐雾腐蚀的高性能防腐涂层空白,为新能源汽车电机壳体、充电插头、压铸铝合金防腐和导电防屏蔽一体化提供了理想的涂层解决方案。
铝件阳极氧化是一种常见的表面处理方法,但其耐盐雾时间却不如化学钝化处理。
阳极氧化膜层厚度一般在2-3μm,颜色多为本色偏黄、浅蓝色、蓝灰色或五彩色。
其硬度约为2-3H,附着力为0级,可过百格测试。
然而,在盐雾腐蚀环境下,阳极氧化层的耐久性仅为数百小时,远低于化学钝化处理。
相比之下,化学钝化处理形成的膜层具有以下优势:1.膜层厚度:防腐导电一体化膜厚2-3μm,防腐绝缘膜厚5-8μm;2.膜层颜色:本色偏黄,浅蓝色,蓝灰色,五彩色;3.膜层硬度:2-3H;4.膜层附着力:0级,可过百格测试;5.膜层耐中性盐雾:铝合金型材和压铸件耐盐雾腐蚀1000h以上;6.膜层耐温:高温高湿盐雾交叉测试,长期持续120℃以内使用;7.膜层成膜效率:化学钝化约10分钟,烘干固化10分钟,周转约5分钟,约25分钟出成品;8.适合盲孔、微孔、管道内壁等各种复杂结构形状360°全涂覆,膜层致密。
综合以上优势,化学钝化处理在铝合金压铸件表面处理领域具有广泛的应用前景。
尤其是在新能源汽车等行业,对防腐、导电和防屏蔽性能有较高要求的零部件,化学钝化处理将为其提供优异的防护性能。
随着科技的不断进步,相信这种低成本、高性能的表面处理技术将会在更多领域得到广泛应用,推动我国铝合金表面处理技术的发展。
常见的表面处理工艺大汇总

常见的表面处理工艺大汇总常见的表面处理工艺有很多种,它们被广泛应用于各种行业和领域。
下面是一些常见的表面处理工艺,以及它们的文字描述:1.喷砂处理:喷砂处理是一种通过喷枪将砂粒喷向工件表面,以去除氧化膜、锈蚀和杂质等表面层的过程。
喷砂处理可以增加工件表面的粗糙度,提高涂层的附着力。
文字描述:喷砂处理是一种表面处理工艺,通过将砂粒喷向工件表面,以去除氧化膜、锈蚀和杂质等表面层。
喷砂处理可以增加工件表面的粗糙度,提高涂层的附着力。
2.磷化处理:磷化处理是一种通过化学反应在工件表面形成一层磷化膜的过程。
磷化膜可以提高工件的耐腐蚀性和耐磨性,并有助于涂层的附着。
文字描述:磷化处理是一种表面处理工艺,通过化学反应在工件表面形成一层磷化膜。
磷化膜可以提高工件的耐腐蚀性和耐磨性,并有助于涂层的附着。
3.镀锌处理:镀锌处理是一种在工件表面电镀一层锌的过程。
锌是一种活泼的金属元素,可以有效地防止工件腐蚀。
文字描述:镀锌处理是一种表面处理工艺,通过在工件表面电镀一层锌,以防止工件腐蚀。
镀锌处理广泛应用于各种行业和领域。
4.喷漆处理:喷漆处理是一种将涂料喷涂在工件表面的过程。
喷漆处理可以增加工件的美观度、保护工件不受腐蚀和磨损等。
文字描述:喷漆处理是一种表面处理工艺,通过将涂料喷涂在工件表面,以增加工件的美观度、保护工件不受腐蚀和磨损等。
喷漆处理广泛应用于各种行业和领域。
5.氧化处理:氧化处理是一种通过化学或电化学方法使金属表面生成氧化膜的过程。
氧化膜可以改变金属的颜色,增加表面的耐磨性和抗腐蚀性。
文字描述:氧化处理是一种表面处理工艺,通过化学或电化学方法使金属表面生成氧化膜。
氧化膜可以改变金属的颜色,增加表面的耐磨性和抗腐蚀性。
6.镀铬处理:镀铬处理是一种在工件表面电镀一层铬的过程。
铬是一种坚硬的金属元素,可以增加工件的硬度、抗腐蚀性和耐磨性。
文字描述:镀铬处理是一种表面处理工艺,通过在工件表面电镀一层铬,以增加工件的硬度、抗腐蚀性和耐磨性。
木工工艺中的表面处理与防腐防虫措施选择与实施
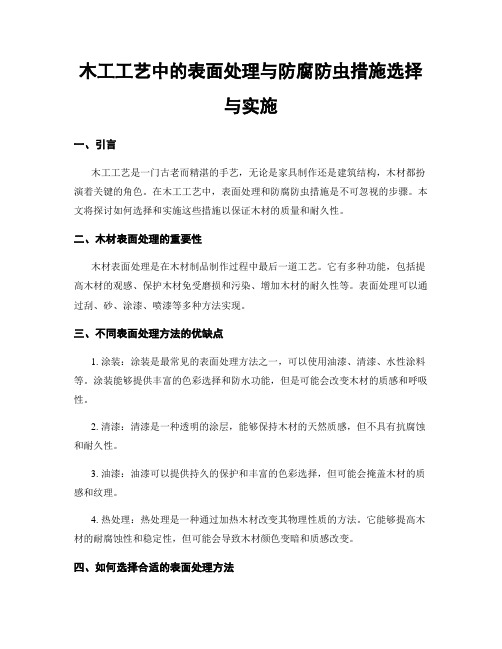
木工工艺中的表面处理与防腐防虫措施选择与实施一、引言木工工艺是一门古老而精湛的手艺,无论是家具制作还是建筑结构,木材都扮演着关键的角色。
在木工工艺中,表面处理和防腐防虫措施是不可忽视的步骤。
本文将探讨如何选择和实施这些措施以保证木材的质量和耐久性。
二、木材表面处理的重要性木材表面处理是在木材制品制作过程中最后一道工艺。
它有多种功能,包括提高木材的观感、保护木材免受磨损和污染、增加木材的耐久性等。
表面处理可以通过刮、砂、涂漆、喷漆等多种方法实现。
三、不同表面处理方法的优缺点1. 涂装:涂装是最常见的表面处理方法之一,可以使用油漆、清漆、水性涂料等。
涂装能够提供丰富的色彩选择和防水功能,但是可能会改变木材的质感和呼吸性。
2. 清漆:清漆是一种透明的涂层,能够保持木材的天然质感,但不具有抗腐蚀和耐久性。
3. 油漆:油漆可以提供持久的保护和丰富的色彩选择,但可能会掩盖木材的质感和纹理。
4. 热处理:热处理是一种通过加热木材改变其物理性质的方法。
它能够提高木材的耐腐蚀性和稳定性,但可能会导致木材颜色变暗和质感改变。
四、如何选择合适的表面处理方法1. 考虑木材用途和环境条件:不同的木材用途和环境条件对表面处理的要求不同。
例如,家具制品需要注重色彩和观感,而室外木材则需要更强的耐候性和抗腐蚀性。
2. 了解不同表面处理方法的特点:在选择表面处理方法之前,了解不同方法的优缺点、适用范围和使用成本是必要的。
可以通过咨询专家、参考书籍和互联网等渠道获得相关信息。
3. 考虑使用成本和施工难度:不同表面处理方法的使用成本和施工难度也是选择的重要考量因素。
一些方法可能需要特殊设备和专业技能来实施,而这可能增加额外的成本和复杂性。
五、木材防腐防虫措施的重要性木材容易受到真菌、细菌、虫害等生物侵蚀,因此采取防腐防虫措施是保护木材耐久性的关键。
防腐防虫措施可以分为物理防腐和化学防腐两类。
六、物理防腐措施的选择与实施1. 干燥处理:干燥是一种常见的物理防腐措施,通过降低木材含水率来防止真菌和细菌生长。
内外防腐工艺的专业知识

内外防腐工艺的专业知识
内外防腐工艺是指在工业设备、建筑物、管道等表面进行特殊的防腐处理,以提高其抗腐蚀性能和使用寿命。
以下是关于内外防腐工艺的一些专业知识:
1. 表面处理:在进行防腐处理之前,首先需要对被保护表面进行清洁和处理,以去除杂质、油脂、锈蚀物等,常用的表面处理方法有喷砂、喷丸、化学除锈等。
2. 防腐涂层:最常用的防腐工艺是涂层防腐,即在被保护表面涂覆一层具有防腐功能的涂料,常用的涂料有环氧树脂、聚氨酯、聚酯等,涂层的选择要根据被保护物体的材料、环境条件和使用要求等综合考虑。
3. 涂层施工:涂层施工需要根据具体情况选择不同的方法,如刷涂、喷涂、喷涂钢砂等,涂层要求均匀、密实、无气泡和缺陷。
4. 防腐材料:除了涂层,还可以使用其他防腐材料,如防腐膜、防腐胶带、防腐涂料等。
防腐膜可采用聚乙烯、聚氯乙烯等材料,防腐胶带多用于管道和焊缝等处,防腐涂料可用于小面积修补和维护。
5. 防腐监测:对已施工的防腐涂层进行定期检测和维护,以确保其防腐效果,常用的监测手段有观察外观、测量膜厚、电化学检测等。
6. 防腐标准:不同行业对于防腐工艺有不同的标准要求,如石油化工行业常用
的防腐标准有SY/T 0315、SY/T 4103等,建筑行业常用的防腐标准有GB/T 50545等。
以上是关于内外防腐工艺的一些专业知识,进行内外防腐工艺时需要根据具体情况选择适当的方法和材料,并遵循相关的标准和要求。
10.9级螺栓表面处理工艺
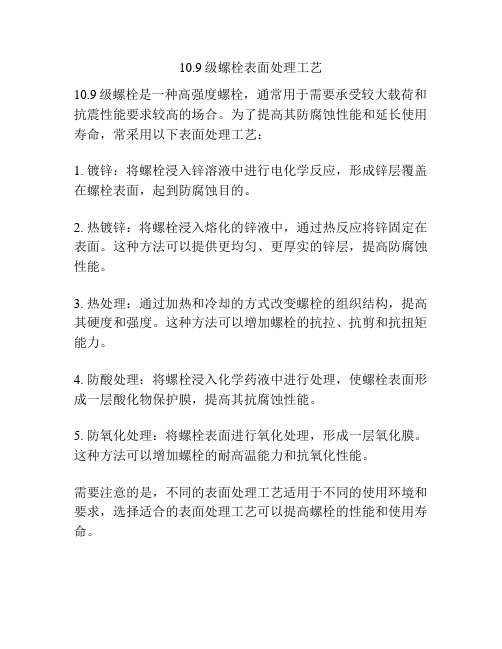
10.9级螺栓表面处理工艺
10.9级螺栓是一种高强度螺栓,通常用于需要承受较大载荷和抗震性能要求较高的场合。
为了提高其防腐蚀性能和延长使用寿命,常采用以下表面处理工艺:
1. 镀锌:将螺栓浸入锌溶液中进行电化学反应,形成锌层覆盖在螺栓表面,起到防腐蚀目的。
2. 热镀锌:将螺栓浸入熔化的锌液中,通过热反应将锌固定在表面。
这种方法可以提供更均匀、更厚实的锌层,提高防腐蚀性能。
3. 热处理:通过加热和冷却的方式改变螺栓的组织结构,提高其硬度和强度。
这种方法可以增加螺栓的抗拉、抗剪和抗扭矩能力。
4. 防酸处理:将螺栓浸入化学药液中进行处理,使螺栓表面形成一层酸化物保护膜,提高其抗腐蚀性能。
5. 防氧化处理:将螺栓表面进行氧化处理,形成一层氧化膜。
这种方法可以增加螺栓的耐高温能力和抗氧化性能。
需要注意的是,不同的表面处理工艺适用于不同的使用环境和要求,选择适合的表面处理工艺可以提高螺栓的性能和使用寿命。
金属的热喷锌(铝)防腐、有机涂料防腐、热浸镀锌防腐的工艺性能及经济效益比较
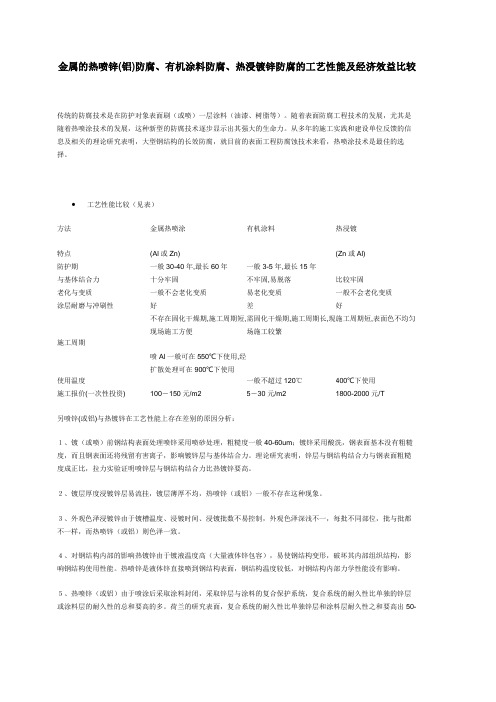
金属的热喷锌(铝)防腐、有机涂料防腐、热浸镀锌防腐的工艺性能及经济效益比较传统的防腐技术是在防护对象表面刷(或喷)一层涂料(油漆、树脂等)。
随着表面防腐工程技术的发展,尤其是随着热喷涂技术的发展,这种新型的防腐技术逐步显示出其强大的生命力。
从多年的施工实践和建设单位反馈的信息及相关的理论研究表明,大型钢结构的长效防腐,就目前的表面工程防腐蚀技术来看,热喷涂技术是最佳的选择。
•工艺性能比较(见表)方法特点金属热喷涂(Al或Zn)有机涂料热浸镀(Zn或Al)防护期一般30-40年,最长60年一般3-5年,最长15年与基体结合力十分牢固不牢固,易脱落比较牢固老化与变质一般不会老化变质易老化变质一般不会老化变质涂层耐磨与冲刷性好差好施工周期不存在固化干燥期,施工周期短,现场施工方便需固化干燥期,施工周期长,现场施工较繁施工周期短,表面色不均匀使用温度喷Al一般可在550℃下使用,经扩散处理可在900℃下使用一般不超过120℃400℃下使用施工报价(一次性投资) 100-150元/m2 5-30元/m2 1800-2000元/T另喷锌(或铝)与热镀锌在工艺性能上存在差别的原因分析:1、镀(或喷)前钢结构表面处理喷锌采用喷砂处理,粗糙度一般40-60um;镀锌采用酸洗,钢表面基本没有粗糙度,而且钢表面还将残留有害离子,影响镀锌层与基体结合力。
理论研究表明,锌层与钢结构结合力与钢表面粗糙度成正比,拉力实验证明喷锌层与钢结构结合力比热镀锌要高。
2、镀层厚度浸镀锌层易流挂,镀层薄厚不均,热喷锌(或铝)一般不存在这种现象。
3、外观色泽浸镀锌由于镀槽温度、浸镀时间、浸镀批数不易控制,外观色泽深浅不一,每批不同部位,批与批都不一样,而热喷锌(或铝)则色泽一致。
4、对钢结构内部的影响热镀锌由于镀液温度高(大量液体锌包容),易使钢结构变形,破坏其内部组织结构,影响钢结构使用性能。
热喷锌是液体锌直接喷到钢结构表面,钢结构温度较低,对钢结构内部力学性能没有影响。
螺丝的表面处理工艺
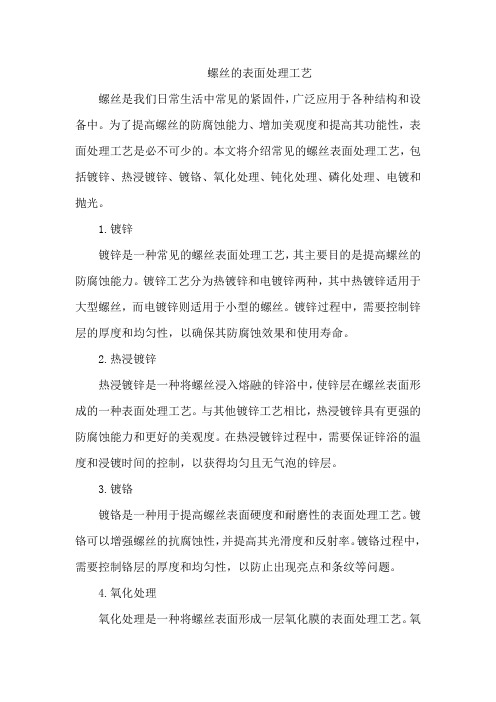
螺丝的表面处理工艺螺丝是我们日常生活中常见的紧固件,广泛应用于各种结构和设备中。
为了提高螺丝的防腐蚀能力、增加美观度和提高其功能性,表面处理工艺是必不可少的。
本文将介绍常见的螺丝表面处理工艺,包括镀锌、热浸镀锌、镀铬、氧化处理、钝化处理、磷化处理、电镀和抛光。
1.镀锌镀锌是一种常见的螺丝表面处理工艺,其主要目的是提高螺丝的防腐蚀能力。
镀锌工艺分为热镀锌和电镀锌两种,其中热镀锌适用于大型螺丝,而电镀锌则适用于小型的螺丝。
镀锌过程中,需要控制锌层的厚度和均匀性,以确保其防腐蚀效果和使用寿命。
2.热浸镀锌热浸镀锌是一种将螺丝浸入熔融的锌浴中,使锌层在螺丝表面形成的一种表面处理工艺。
与其他镀锌工艺相比,热浸镀锌具有更强的防腐蚀能力和更好的美观度。
在热浸镀锌过程中,需要保证锌浴的温度和浸镀时间的控制,以获得均匀且无气泡的锌层。
3.镀铬镀铬是一种用于提高螺丝表面硬度和耐磨性的表面处理工艺。
镀铬可以增强螺丝的抗腐蚀性,并提高其光滑度和反射率。
镀铬过程中,需要控制铬层的厚度和均匀性,以防止出现亮点和条纹等问题。
4.氧化处理氧化处理是一种将螺丝表面形成一层氧化膜的表面处理工艺。
氧化处理可以提高螺丝的耐腐蚀性和美观度,同时还可以增强其表面的摩擦力。
在氧化处理过程中,需要控制氧化膜的厚度和致密度,以确保其防腐蚀效果和使用寿命。
5.钝化处理钝化处理是一种在螺丝表面形成一层钝化膜的表面处理工艺。
钝化处理可以增强螺丝的耐腐蚀性和抗疲劳性,同时还可以避免螺丝出现生锈和腐蚀等问题。
在钝化处理过程中,需要控制钝化膜的厚度和致密度,以确保其防腐蚀效果和使用寿命。
6.磷化处理磷化处理是一种在螺丝表面形成一层磷化膜的表面处理工艺。
磷化处理可以提高螺丝的耐腐蚀性和美观度,同时还可以增强其表面的附着力和润滑性。
在磷化处理过程中,需要控制磷化膜的厚度和致密度,以确保其防腐蚀效果和使用寿命。
7.电镀电镀是一种利用电解原理在螺丝表面形成一层金属或合金镀层的表面处理工艺。
电子厂常用的五种表面处理工艺
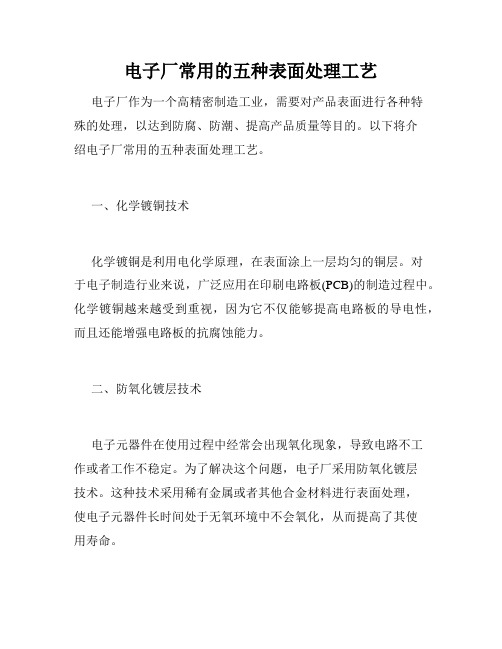
电子厂常用的五种表面处理工艺电子厂作为一个高精密制造工业,需要对产品表面进行各种特殊的处理,以达到防腐、防潮、提高产品质量等目的。
以下将介绍电子厂常用的五种表面处理工艺。
一、化学镀铜技术化学镀铜是利用电化学原理,在表面涂上一层均匀的铜层。
对于电子制造行业来说,广泛应用在印刷电路板(PCB)的制造过程中。
化学镀铜越来越受到重视,因为它不仅能够提高电路板的导电性,而且还能增强电路板的抗腐蚀能力。
二、防氧化镀层技术电子元器件在使用过程中经常会出现氧化现象,导致电路不工作或者工作不稳定。
为了解决这个问题,电子厂采用防氧化镀层技术。
这种技术采用稀有金属或者其他合金材料进行表面处理,使电子元器件长时间处于无氧环境中不会氧化,从而提高了其使用寿命。
三、阳极氧化技术阳极氧化是一种将金属表面转化为表面微孔或多孔氧化膜的技术。
它广泛应用于轻工、机械、电子等领域,用于增加表面硬度、耐磨性、防腐性等方面。
该技术可以增加优质金属表面的耐磨性和硬度。
四、电镀技术电镀是在金属表面上沉积一层金属膜以改变金属表面的物理、化学性质,进而达到提高抗腐蚀能力的目的。
电子产业中使用最多的是电镀锡、电镀钴、电镀银等电镀工艺。
例如,电子印刷板通常先经过镀铜,然后再进行镀金、镀锡、镀铅等表面处理工艺。
五、热处理技术对于电子产品来说,热处理技术往往在金属模具、模具工作表面处理以及金属钎焊等工艺中广泛应用。
热处理可以改变金属材料的结晶状态,使其在工作温度范围内具有良好的力学性能、疲劳性能、耐磨性和抗腐蚀性。
总的来说,电子厂常用的五种表面处理工艺是化学镀铜、防氧化镀层技术、阳极氧化技术、电镀技术和热处理技术。
这些工艺在电子产品的制造过程中起到了关键作用,提高了产品质量,增强了产品的耐用性。
防腐工艺特点
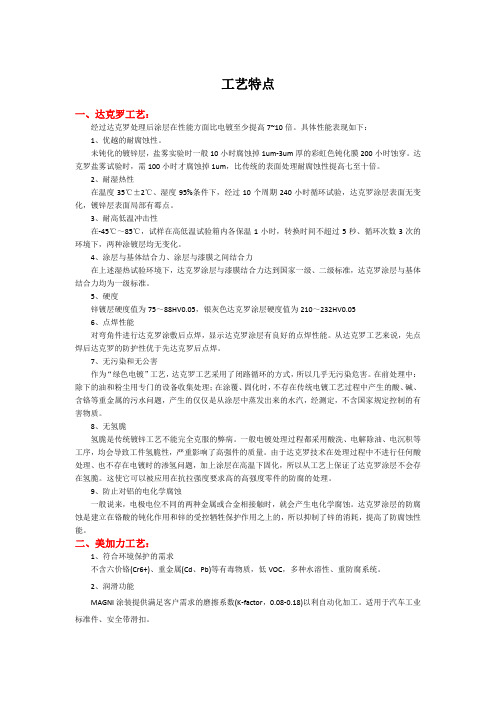
工艺特点一、达克罗工艺:经过达克罗处理后涂层在性能方面比电镀至少提高7~10倍。
具体性能表现如下:1、优越的耐腐蚀性。
未钝化的镀锌层,盐雾实验时一般10小时腐蚀掉1um-3um厚的彩虹色钝化膜200小时蚀穿。
达克罗盐雾试验时,需100小时才腐蚀掉1um,比传统的表面处理耐腐蚀性提高七至十倍。
2、耐湿热性在温度35℃±2℃、湿度95%条件下,经过10个周期240小时循环试验,达克罗涂层表面无变化,镀锌层表面局部有霉点。
3、耐高低温冲击性在-45℃~85℃,试样在高低温试验箱内各保温1小时,转换时间不超过5秒、循环次数3次的环境下,两种涂镀层均无变化。
4、涂层与基体结合力、涂层与漆膜之间结合力在上述湿热试验环境下,达克罗涂层与漆膜结合力达到国家一级、二级标准,达克罗涂层与基体结合力均为一级标准。
5、硬度锌镀层硬度值为75~88HV0.05,银灰色达克罗涂层硬度值为210~232HV0.056、点焊性能对弯角件进行达克罗涂敷后点焊,显示达克罗涂层有良好的点焊性能。
从达克罗工艺来说,先点焊后达克罗的防护性优于先达克罗后点焊。
7、无污染和无公害作为“绿色电镀”工艺,达克罗工艺采用了闭路循环的方式,所以几乎无污染危害。
在前处理中:除下的油和粉尘用专门的设备收集处理;在涂覆、固化时,不存在传统电镀工艺过程中产生的酸、碱、含铬等重金属的污水问题,产生的仅仅是从涂层中蒸发出来的水汽,经测定,不含国家规定控制的有害物质。
8、无氢脆氢脆是传统镀锌工艺不能完全克服的弊病。
一般电镀处理过程都采用酸洗、电解除油、电沉积等工序,均会导致工件氢脆性,严重影响了高强件的质量。
由于达克罗技术在处理过程中不进行任何酸处理、也不存在电镀时的渗氢问题,加上涂层在高温下固化,所以从工艺上保证了达克罗涂层不会存在氢脆。
这使它可以被应用在抗拉强度要求高的高强度零件的防腐的处理。
9、防止对铝的电化学腐蚀一般说来,电极电位不同的两种金属或合金相接触时,就会产生电化学腐蚀。
防腐喷漆的标准
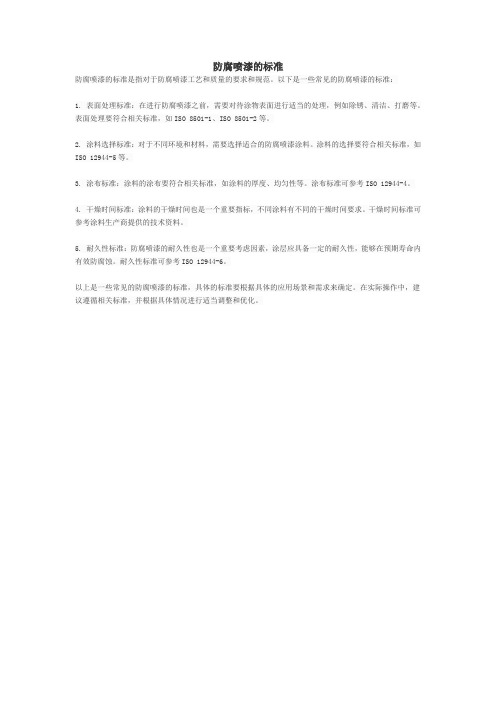
防腐喷漆的标准
防腐喷漆的标准是指对于防腐喷漆工艺和质量的要求和规范。
以下是一些常见的防腐喷漆的标准:
1. 表面处理标准:在进行防腐喷漆之前,需要对待涂物表面进行适当的处理,例如除锈、清洁、打磨等。
表面处理要符合相关标准,如ISO 8501-1、ISO 8501-2等。
2. 涂料选择标准:对于不同环境和材料,需要选择适合的防腐喷漆涂料。
涂料的选择要符合相关标准,如ISO 12944-5等。
3. 涂布标准:涂料的涂布要符合相关标准,如涂料的厚度、均匀性等。
涂布标准可参考ISO 12944-4。
4. 干燥时间标准:涂料的干燥时间也是一个重要指标,不同涂料有不同的干燥时间要求。
干燥时间标准可参考涂料生产商提供的技术资料。
5. 耐久性标准:防腐喷漆的耐久性也是一个重要考虑因素,涂层应具备一定的耐久性,能够在预期寿命内有效防腐蚀。
耐久性标准可参考ISO 12944-6。
以上是一些常见的防腐喷漆的标准,具体的标准要根据具体的应用场景和需求来确定。
在实际操作中,建议遵循相关标准,并根据具体情况进行适当调整和优化。
金属表面处理汇总
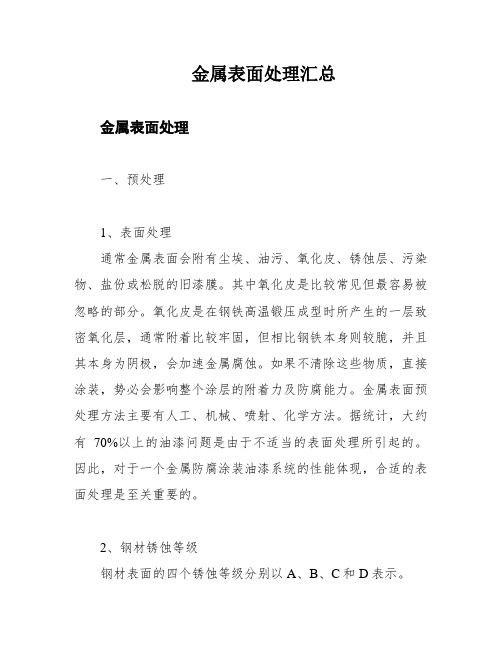
金属表面处理汇总金属表面处理一、预处理1、表面处理通常金属表面会附有尘埃、油污、氧化皮、锈蚀层、污染物、盐份或松脱的旧漆膜。
其中氧化皮是比较常见但最容易被忽略的部分。
氧化皮是在钢铁高温锻压成型时所产生的一层致密氧化层,通常附着比较牢固,但相比钢铁本身则较脆,并且其本身为阴极,会加速金属腐蚀。
如果不清除这些物质,直接涂装,势必会影响整个涂层的附着力及防腐能力。
金属表面预处理方法主要有人工、机械、喷射、化学方法。
据统计,大约有70%以上的油漆问题是由于不适当的表面处理所引起的。
因此,对于一个金属防腐涂装油漆系统的性能体现,合适的表面处理是至关重要的。
2、钢材锈蚀等级钢材表面的四个锈蚀等级分别以A、B、C和D表示。
A:全面地覆盖着氧化皮而几乎没有铁锈的钢材表面;B:已发生锈蚀,并且部分氧化皮已经剥落的钢材表面;C:氧化皮已因锈蚀而剥落,或者可以刮除,并且有少量点蚀的钢材表面;D:氧化皮已因锈蚀而全面剥离,并且已普遍发生点蚀的钢材表面。
3、清理等级也即清洁度国际标准代表性的有两种:一种是美国85年制订“SSPC-”,第二种是瑞典76年制订的“Sa-”,它分为四个等级分别为Sa1、Sa2、Sa2.5、Sa3,为国际惯常通用标准,详细介绍如下:Sa1级——相当于美国SSPC—SP7级。
采用一般简单的手工刷除、砂布打磨方法,这是四种清洁度中度最低的一级,对涂层的保护仅仅略好于未采用处理的工件。
Sa1级处理的技术标准:工件表面应不可见油污、油脂、残留氧化皮、锈斑、和残留油漆等污物。
Sa1级也叫做手工刷除清理级(或清扫级);Sa2级——相当于美国SSPC—SP6级。
采用喷砂清理办法,这是喷砂处置惩罚中最低的一级,即一般的要求,但对于涂层的保护要比手工刷除清理要提高很多。
Sa2级处置惩罚的技术标准:工件表面应不可见油腻、污垢、氧化皮、锈皮、油漆、氧化物、腐蚀物、和其它外来物质(疵点除外),但疵点限定为不超过每平方米表面的33%,可包孕稍微阴影;大批因疵点、锈蚀引起的稍微脱色;氧化皮及油漆疵点。
金属常见的表面处理工艺

金属常见的表面处理工艺一、喷砂处理喷砂是一种常见的金属表面处理工艺,它通过高速喷射砂粒对金属表面进行冲击,去除表面的氧化物、油污和污渍,使金属表面变得光滑、清洁。
喷砂处理能够增强金属表面的粗糙度,提高涂层的附着力,并且可以消除金属表面的应力,提高其抗腐蚀性能。
二、电镀处理电镀是一种通过电解将金属离子沉积在金属表面的工艺,常见的电镀方法包括镀铬、镀镍、镀锌等。
电镀处理可以提高金属的抗腐蚀性能、硬度和光泽度,还可以改变金属表面的颜色和外观。
电镀处理广泛应用于汽车、家具、电子产品等行业。
三、阳极氧化处理阳极氧化是一种将金属表面形成一层氧化膜的工艺,常见的应用是铝阳极氧化。
阳极氧化处理可以提高金属表面的抗腐蚀性能、硬度和耐磨性,并且可以改变金属表面的颜色和外观。
阳极氧化处理广泛应用于航空航天、建筑、电子等领域。
四、喷涂处理喷涂是一种将涂料喷射到金属表面的工艺,常见的喷涂方法包括喷漆、喷粉等。
喷涂处理可以改变金属表面的颜色、外观和质感,提高金属的防腐蚀性能和耐候性。
喷涂处理广泛应用于家具、建筑、汽车等行业。
五、抛光处理抛光是一种通过机械或化学方法将金属表面进行磨光的工艺,常见的抛光方法包括机械抛光、电解抛光等。
抛光处理可以使金属表面变得光滑、亮丽,提高其视觉效果和触感。
抛光处理广泛应用于钟表、首饰、厨具等领域。
六、喷涂处理喷涂是一种将涂料喷射到金属表面的工艺,常见的喷涂方法包括喷漆、喷粉等。
喷涂处理可以改变金属表面的颜色、外观和质感,提高金属的防腐蚀性能和耐候性。
喷涂处理广泛应用于家具、建筑、汽车等行业。
七、镜面抛光处理镜面抛光是一种通过机械或化学方法将金属表面进行精密磨光的工艺,使其表面光洁度高,反射率高。
镜面抛光处理常用于光学仪器、精密仪器、汽车零部件等领域,要求金属表面完全无瑕疵,提升产品的质感和品质。
总结:金属常见的表面处理工艺包括喷砂处理、电镀处理、阳极氧化处理、喷涂处理、抛光处理和镜面抛光处理等。
金属表面处理工艺,金属表面磷化处理工艺

金属表面处理工艺|金属表面磷化处理工艺金属表面处理工艺表面处理是在基体材料表面上人工形成一层与基体的机械、物理和化学性能不同的表层的工艺方法。
表面处理的目的是满足产品的耐蚀性、耐磨性、装饰或其他特种功能要求。
下面是金属表面处理工艺,一共21种。
微弧氧化微弧氧化又称微等离子体氧化,是通过电解液与相应电参数的组合,在铝、镁、钛及其合金表面依靠弧光放电产生的瞬时高温高压作用,生长出以基体金属氧化物为主的陶瓷膜层。
金属拉丝金属拉丝是通过研磨产品在工件表面形成线纹,起到装饰效果的一种表面处理手段。
烧蓝烧蓝是将整个胎体填满色釉后,再拿到炉温大约800℃的高炉中烘烧,色釉由砂粒状固体熔化为液体,待冷却后成为固着在胎体上的绚丽的色釉,此时色釉低于铜丝高度,所以得再填一次色釉,再经烧结,一般要连续四五次,直至将纹样内填到与掐丝纹相平。
1000G机械设计资料,限时下载喷涂喷丸即使用丸粒轰击工件表面并植入残余压应力,提升工件疲劳强度的冷加工工艺。
喷砂喷砂是利用高速砂流的冲击作用清理和粗化基体表面的过程,即采用压缩空气为动力,以形成高速喷射束将喷料(铜矿砂、石英砂、金刚砂、铁砂、海南砂)高速喷射到需要处理的工件表面,使工件表面的外表面的外表或形状发生变化。
蚀刻蚀刻是将材料使用化学反应或物理撞击作用而移除的技术。
通常所指蚀刻也称光化学蚀刻,指通过曝光制版、显影后,将要蚀刻区域的保护膜去除,在蚀刻时接触化学溶液,达到溶解腐蚀的作用,形成凹凸或者镂空成型的效果。
IMDIMD即In-Mold Decoration(模内装饰技术),亦称免涂装技术,是国际风行的表面装饰技术,表面硬化透明薄膜,中间印刷图案层,背面注塑层,油墨中间,可使产品耐摩擦,防止表面被刮花,并可长期保持颜色的鲜明不易退色。
OMDOMD模外装饰(Out Mold Decoration)简称,是视觉、触觉、功能整合展现,IMD 延伸之装饰技术,是一种結合印刷、纹理结构及金属化特性之3D表面装饰技术。
几种常见金属表面处理工艺

几种常见金属表面处理工艺文档编制序号:[KKIDT-LLE0828-LLETD298-POI08]金属表面处理种类简介电镀金属或其他不溶性材料做,待镀的工件做阴极,镀层金属的阳离子在待镀工件表面被还原形成镀层。
为排除其它阳离子的干扰,且使镀层均匀、牢固,需用含镀层金属阳离子的溶液做电镀液,以保持镀层金属阳离子的不变。
电镀的目的是在基材上镀上金属镀层,改变基材表面性质或尺寸。
电镀能增强金属的抗腐蚀性(镀层金属多采用耐腐蚀的金属)、增加、防止磨耗、提高导电性、润滑性、耐热性、和表面美观。
电泳电泳是电泳涂料在阴阳两极,施加于电压作用下,带电荷涂料离子移动到阴极,并与阴极表面所产生之碱性作用形成不溶解物,沉积于工件表面。
电泳表面处理工艺的特点:电泳漆膜具有涂层丰满、均匀、平整、光滑的优点,电泳漆膜的硬度、附着力、耐腐、冲击性能、渗透性能明显优于其它涂装工艺。
电泳工艺优于其他涂装工艺。
镀锌镀锌是指在、或者其它材料的镀一层锌以起美观、等作用的表面处理技术。
现在主要采用的方法是热镀锌。
电镀与电泳的区别电镀就是利用电解原理在某些金属表面上镀上一薄层其它金属或合金的过程。
电泳:溶液中带电粒子(离子)在电场中移动的现象。
溶液中带电粒子()在中移动的现象。
利用带电粒子在电场中移动速度不同而达到分离的技术称为电泳技术。
电泳又名——电着 (着),泳漆,电沉积。
发黑钢制件的表面发黑处理,也有被称之为发蓝的。
其原理是将钢铁制品表面迅速氧化,使之形成致密的氧化膜保护层,提高钢件的防锈能力。
发黑处理现在常用的方法有传统的碱性加温发黑和出现较晚的常温发黑两种。
但常温发黑工艺对于低碳钢的效果不太好。
A3钢用碱性发黑好一些。
在高温下(约550℃)氧化成的四氧化三铁呈天蓝色,故称发蓝处理。
在低温下(约3 50℃)形成的四氧化三铁呈暗黑色,故称发黑处理。
在兵器制造中,常用的是发蓝处理;在工业生产中,常用的是发黑处理。
采用碱性氧化法或酸性氧化法;使金属表面形成一层氧化膜,以防止金属表面被腐蚀,此处理过程称为“发蓝”。
几种常见金属表面处理工艺
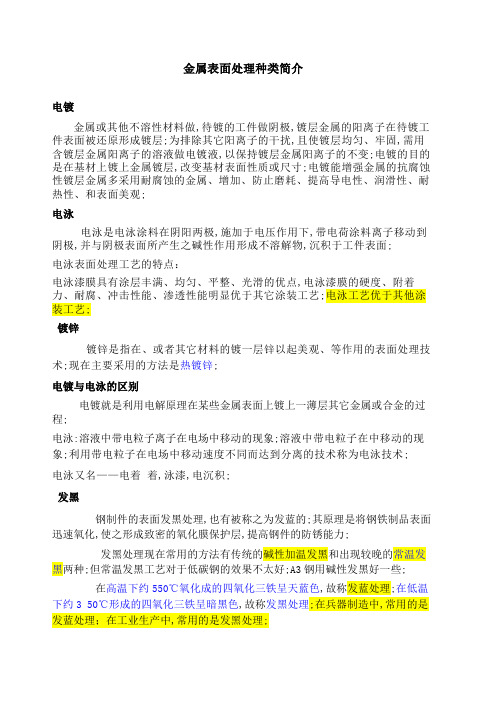
金属表面处理种类简介电镀金属或其他不溶性材料做,待镀的工件做阴极,镀层金属的阳离子在待镀工件表面被还原形成镀层;为排除其它阳离子的干扰,且使镀层均匀、牢固,需用含镀层金属阳离子的溶液做电镀液,以保持镀层金属阳离子的不变;电镀的目的是在基材上镀上金属镀层,改变基材表面性质或尺寸;电镀能增强金属的抗腐蚀性镀层金属多采用耐腐蚀的金属、增加、防止磨耗、提高导电性、润滑性、耐热性、和表面美观;电泳电泳是电泳涂料在阴阳两极,施加于电压作用下,带电荷涂料离子移动到阴极,并与阴极表面所产生之碱性作用形成不溶解物,沉积于工件表面;电泳表面处理工艺的特点:电泳漆膜具有涂层丰满、均匀、平整、光滑的优点,电泳漆膜的硬度、附着力、耐腐、冲击性能、渗透性能明显优于其它涂装工艺;电泳工艺优于其他涂装工艺;镀锌镀锌是指在、或者其它材料的镀一层锌以起美观、等作用的表面处理技术;现在主要采用的方法是热镀锌;电镀与电泳的区别电镀就是利用电解原理在某些金属表面上镀上一薄层其它金属或合金的过程;电泳:溶液中带电粒子离子在电场中移动的现象;溶液中带电粒子在中移动的现象;利用带电粒子在电场中移动速度不同而达到分离的技术称为电泳技术;电泳又名——电着着,泳漆,电沉积;发黑钢制件的表面发黑处理,也有被称之为发蓝的;其原理是将钢铁制品表面迅速氧化,使之形成致密的氧化膜保护层,提高钢件的防锈能力;发黑处理现在常用的方法有传统的碱性加温发黑和出现较晚的常温发黑两种;但常温发黑工艺对于低碳钢的效果不太好;A3钢用碱性发黑好一些;在高温下约550℃氧化成的四氧化三铁呈天蓝色,故称发蓝处理;在低温下约3 50℃形成的四氧化三铁呈暗黑色,故称发黑处理;在兵器制造中,常用的是发蓝处理;在工业生产中,常用的是发黑处理;采用碱性氧化法或酸性氧化法;使金属表面形成一层氧化膜,以防止金属表面被腐蚀,此处理过程称为“发蓝”;黑色金属表面经“发蓝”处理后所形成的氧化膜,其外层主要是四氧化三铁,内层为氧化亚铁; 发蓝发黑的操作流程:工件装夹→去油→清洗→酸洗→清洗→氧化→清洗→皂化→热水煮洗→检查;所谓皂化,是用肥皂水溶液在一定温度下浸泡工件;目的是形成一层硬脂酸铁薄膜,以提高工件的抗腐蚀能力;金属表面着色金属表面着色,顾名思义就是给金属表面“涂”上颜色,改变其单一的、冰冷的金属色泽,代之以五颜六色,满足不同行业的不同需求;给金属着色后一般都增加了防腐能力,有的还增加了抗磨能力;但表面彩色技术主要的应用还在装饰领域,即用来美化生活,美化社会;抛丸抛丸的原理是用电动机带动叶轮体旋转直接带动或用V型皮带传动,靠离心力的作用,将直径约在~的弹丸有铸钢丸、钢丝切丸、等不同类型抛向工件的表面,使工件的表面达到一定的粗糙度,使工件变得美观,或者改变工件的焊接拉应力为压应力,提高工件的使用寿命;通过提高工件表面的粗糙度,也提高了工件后续喷漆的漆膜附着力;其寓意即为抛丸处理可以为喷漆工艺的前道工序; 喷砂喷砂是采用为动力,以形成高速喷射束将喷料铜矿砂、、、铁砂、砂高速喷射到需要处理的工件,使工件表面的的外表或形状发生变化,由于对工件表面的冲击和切削作用,使工件的表面获得一定的清洁度和不同的,使工件表面的机械性能得到改善,因此提高了工件的抗疲劳性,增加了它和之间的附着力,延长了的耐久性,也有利于的流平和装饰;喷砂工艺与其它清理工艺如酸洗,工具清理相比有以下特点:一、喷砂处理是最彻底、最通用、最迅速、效率最高的清理方法;二、喷砂处理可以在不同粗糙度之间任意选择,而其它工艺是没办法实现这一点的;手工打磨可以打出毛面但速度太慢,化学溶剂清理则清理表面过于光滑不利于涂层粘接;喷丸的特点:1、清理的灵活性大;容易清理复杂工件的内外表面和管件的内壁;并且不受场地的限制,可以将其移至到特大型工件附近进行清理;2、设备结构简单,整机投资少,易损件少,维修费用低;3、消耗能量大,必须配备大功率的空压站4、清理表面易有潮气,容易生绣;5、清理效率低,操作人员多,劳动强度大;抛丸的特点:1、灵活性差;受场地的限制,清理工件有些盲目性,在工件内卫表面易产生清理不到的死角、2、不用压缩空气加速弹丸,不必设置大功率的空压站,3、清理表面不易有潮气,不容易生绣;4、设备结构比较复杂,易损件多,特别是叶片等零件,维修工时多,费用高;5、清理效率高,费用低,操作人员少,容易实现自动化控制,适用于大批量生产;喷丸喷丸shot peening ;用喷丸进行表面处理,打击力大,清理效果明显;但喷丸对薄板工件的处理,容易使工件变形,且钢丸打击到工件表面无论抛丸或喷丸使金属基材产生变形,由于Fe3O4和Fe2O3没有塑性,破碎后剥离,而油膜与基材一同变形,所以对带有油污的工件,抛丸、喷丸无法彻底清除油污;在现有的工件表面处理方法中,清理效果最佳的还数喷砂清理;喷砂适用于工件表面要求较高的清理;但是我国目前通用喷砂设备中多由铰龙、刮板、斗式提升机等原始笨重输砂机械组成;喷丸与抛丸的区别喷丸使用高压风或压缩空气作动力,而抛丸一般为高速旋转的飞轮将钢砂高速抛射出去;抛丸效率高,但会有死角,而喷丸比较灵活,但动力消耗大;两种工艺虽喷射动力和方式不同,但都是高速冲击工件为目的,其效果也基本相同,相比而言,喷丸比较精细,容易控制精度,但效率不及抛丸之高,适形状复杂的小型工件,抛丸比较经济实用,容易控制效率和成本,可以控制丸料的粒度来控制喷射效果,但会有死角,适合于形面单一的工件批量加工.两种工艺的选用主要取决工件的形状和加工效率.喷丸与喷砂的区别喷丸与喷砂都是使用高压风或压缩空气作动力,将其高速的吹出去冲击工件表面达到清理效果,但选择的介质不同,效果也不相同.喷砂处理后,工件表面污物被清除掉,工件表面被微量破坏,表面积大幅增加,从而增加了工件与涂/镀层的结合强度.经过喷砂处理的工件表面为金属本色,但是由于表面为毛糙面,光线被折射掉,故没有,为发暗表面.喷丸处理后,工件表面污物被清除掉,工件表面被微量而不被破坏,表面积有所增加.由于加工过程中,工件表面没有被破坏,加工时产生的多余能量就会引会工件基体的表面强化.经过喷丸处理的工件表面也为金属本色,但是由于表面为球状面,光线部分被折射掉,故工件加工为亚光效果.磷化磷化phosphorization是一种化学与形成磷酸盐化学的过程,所形成的磷酸盐转化膜称之为;磷化的目的主要是:给金属提供保护,在一定程度上防止金属被腐蚀;用于涂漆前打底,提高漆膜层的附着力与防腐蚀能力;在金属冷加工工艺中起减摩润滑使用;钝化其钝化的机理可用薄膜理论来解释,即认为钝化是由于金属与氧化性质作用,作用时在金属表面生成一种非常薄的、致密的、覆盖性能良好的、牢固地吸附在金属表面上的钝化膜;这层膜成独立相存在,通常是氧化金属的化合物;它起着把金属与腐蚀介质完全隔开的作用,防止金属与腐蚀介质接触,从而使金属基本停止溶解形成钝态达到防腐蚀的作用;钝化的优点1、与传统的物理封闭法相比,钝化处理后具有绝对不增加工件厚度和改变颜色的特点、提高了产品的精密度和附加值,使操作更方便;2、由于钝化的过程属于无反应状态进行,钝化剂可反复添加使用,因此寿命更长、成本更经济;3、钝化促使金属表面形成的氧分子结构钝化膜、膜层致密、性能稳定,并且在空气中同时具有自行修复作用,因此与传统的涂防锈油的方法相比,钝化形成的钝化膜更稳定、更具耐蚀性;金属或受一些因素影响,明显增强的现象,称为钝化;由某些钝化剂所引起的现象,称为;如浓HNO3、浓H2SO4、HClO3、K2Cr2O7、KMnO4等氧化剂都可使金属钝化;金属钝化后,其电极电势向正方向移动,使其失去了原有的特性,如钝化了的铁在铜盐中不能将铜置换出;此外,用方法也可使金属钝化,如将Fe置于H2SO4中作为阳极,用外加电流使,采用一定仪器使铁电位升高一定程度,就钝化了;由阳极引起的金属钝化现象,叫或电化学钝化;喷涂利用压力或静电力将油漆或粉末附着在工件表面,使工件有防腐和外观装饰作用.烤漆在基材上打上底漆、面漆,每上一遍漆,都送入无尘衡温烤房,烘烤; 浸渗是一种微孔细缝渗透密封工艺;将密封介质通常是低粘度液体通过自然渗透即微孔自吸、抽真空和加压等方法渗入微孔细缝中,将缝隙填充满,然后通过自然室温、冷却或加热等方法将缝隙里的密封介质固化,达到密封缝隙的作用;喷油将油漆喷在产品表面,自然风干的方式;抛光利用柔性抛光工具和磨料或其他抛光介质对表面进行的修饰加工;抛光不能提高工件的尺寸精度或几何形状精度,而是以得到表面或光泽为目的,有时也用以消除;通常以作为抛光工具;抛光轮一般用多层、或叠制而成,两侧用金属圆板夹紧,其轮缘涂敷由微粉和等均匀混合而成的;抛光时,高速旋转的抛光轮在20米/秒以上压向工件,使磨料对工件表面产生和微量,从而获得光亮的加工表面,表面一般可达~微米;当采用非油脂性的消光抛光剂时,可对光亮表面消光以改善外观;对产品表面要求稍低时,常采用的方法;粗抛时将大量磨料和产品放在罐状滚筒中,滚筒转动时,使产品与磨料等在筒内随机地滚动碰撞以达到去除表面凸锋而减小表面粗糙度的目的;超声波清洗是利用超声波在液体中的、加速度作用及直进流作用对液体和污物直接、间接的作用,使污物层被分散、乳化、剥离而达到清洗目的;紧固件的表面处理:紧固件表面处理的选择由于几乎所有商业紧固件都是由碳钢、合金钢制成,一些种类的紧固件希望能防止腐蚀,即使使用防腐蚀材料的紧固件,仍然需要表面处理来防止不同材料的腐蚀;此外,表面处理的镀层必须附着牢固,不能在安装和卸下的过程中脱落,对螺纹紧固件,镀层还需足够薄,使得镀后螺纹仍能旋合;一般镀层的温度限制比紧固件材料要低,因此还需考虑紧固件所处的工作温度要求;对于表面处理,人们一般关注的是美观和防腐,但紧固件的主要功能是紧固零部件,而表面处理对紧固件的紧固性能也有很大的影响,所以,选择表面处理时,也应考虑紧固性能的因素,即安装扭矩—预紧力的一致性;一名高水平的设计者,不仅应考虑设计,还因注意到装配的工艺性,甚至环保要求;下面根据上述因素简要介绍一些紧固件常用的镀层,以供设计人员和紧固件从业人员参考;电镀锌电镀锌是商业紧固件最常用的镀层;它比较便宜,外观也较好看,可以有黑色、军绿色;然而,它的防腐性能一般,其防腐性能是锌镀涂层中最低的;一般电镀锌中性盐雾试验在72小时之内,也有采用特殊封闭剂,使得中性盐雾试验达200小时以上,但价格贵,是一般镀锌的5~8倍;电镀锌加工过程易产生氢脆,所以级以上的螺栓一般不采用镀锌的处理.虽然镀后可以用烘箱去氢,但因钝化膜在60℃以上时将遭破坏,因此去氢必须在电镀后钝化前进行;如此可操作性差,加工成本高;在现实中,一般生产厂不会主动去氢,除非特定客户的强制要求;电镀锌的紧固件扭矩—预紧力一致性较差,且不稳定,一般不用于重要部位的连接;为了改善扭矩—预紧力一致性,也可采用镀后涂覆润滑物质的方法改善和提高扭矩—预紧力一致性;磷化磷化相对镀锌便宜,耐腐蚀性能比镀锌差磷化相对镀锌便宜,耐腐蚀性能比镀锌差;磷化后应涂油,其耐腐蚀性能的高低与所涂油的性能有很大的关系;例如,磷化后涂一般的防锈油,中性盐雾试验也只有10~20小时;涂高档的防锈油,则可达72~96小时;但其价格是一般磷化涂油的2~3倍;紧固件磷化常用的两种,锌系磷化和锰系磷化;锌系磷化润滑性能比锰系磷化好,锰系磷化抗腐蚀性,耐磨性镀锌较好;它的使用温度可达华氏225度到400度107~204℃;工业用紧固件很多用磷化涂油处理;因为它扭矩—预紧力一致性很好,装配时能保证达到设计所预期的紧固要求,所以在工业中使用较多;特别是一些重要零部件的连接;如,钢结构连接副,发动机的连杆螺栓、螺母,缸盖、主轴承、飞轮螺栓,车轮螺栓螺母等;高强度螺栓采用磷化,还可以避免氢脆问题,所以在工业领域级以上的螺栓一般采用磷化表面处理;氧化发黑发黑+涂油是工业紧固件很流行的镀层,因为它最便宜,并且在油耗尽之前看起来不错;由于发黑几乎无防锈能力,所以无油后它很快就会生锈;就是在有油状态下,其中性盐雾试验也只能达到3~5小时;发黑的紧固件扭矩—预紧力一致性也很差;如需提高,可以在装配时在内处螺纹上涂抹油脂后再旋合;电镀镉价格约是电镀锌的15~20倍镉镀层耐腐蚀性能很好,特别是在海洋性大气环境下的耐腐蚀性较其他表面处理好;电镀镉的加工过程中的废液处理费用大,成本高,其价格约是电镀锌的15~20倍;所以在一般行业不使用,只用于一些特定的环境;如,用于石油钻井平台和海航飞机用紧固件;电镀铬铬镀层在大气中很稳定,不易变色和失去光泽,硬度高耐磨性好;在紧固件上用铬镀层一般是作为装饰作用;在防腐性要求较高的工业领域很少使用,因为好的铬电镀紧固件与不锈钢同样昂贵,只是使用不锈钢强度不够时,才用镀铬紧固件代替;为了防止腐蚀,镀铬前应首先镀铜和镍;铬镀层可以承受华氏1200度650℃的高温;但也与电镀锌一样存在氢脆问题;镀银、镀镍银镀层既可以防腐蚀,又可以作为紧固件的固体润滑剂;由于成本原因,螺母使用镀银,螺栓不用,有时小螺栓也镀银;银在空气中失去光泽,但可以在华氏1600度下作用;所以,人们利用其耐高温和润滑的特性,用于在高温下工作的紧固件,以防止螺栓、螺母的氧化咬死;紧固件镀镍,主要用于既要防腐,又要导电性好的地方;如车辆电瓶的引出端子等;热浸锌热浸锌为锌加热到液体下热扩散涂层;其镀层厚度在15~10μm,并且不易控制,但搞腐蚀性好,多用于工程中;热浸锌加工过程中污染严重,有锌废料和锌蒸汽等;由于镀层厚,在紧固件中引发了内外螺纹难以旋合的问题;解决此问题有两种方法;一种是在镀后再攻内螺纹,虽然解决了螺纹旋合的问题;但也降低了防腐性能;一种是在螺母攻丝时,使螺纹大于标准纹约有~M5~M30,然后再热浸锌这样虽然也可解决旋合难题,但付出了强度降低的代价;目前,有一种防松螺纹——美国“施必牢”内螺纹可以解决此难题;因其内螺纹与外螺纹未紧固时容隙大,可以用于容得下厚的涂层,所以不影响旋合性,同时防腐性能和强度亦保持原样,不受影响;因热浸锌加工的温度原因,它不能用于级以上的紧固件;渗锌渗锌为锌粉固态冶金热扩散涂层;其均匀性好,螺纹、盲孔内都能获得均匀层;镀层厚度为10~110μm,并且误差可控制在10%;它与基体的结合强度和防腐性能在锌涂层中电镀锌、热浸锌、达克罗是最好的;其加工过程无污染,最环保;达克罗不存在氢脆问题,并且扭矩—预紧力一致性能很好;如不考虑六价铬的环保问题,它实际上最适用于高防腐要求的高强度紧固件;其他涂层上述镀层之外,还有许多金属或非金属涂层;这些涂层由各公司详细阐明;如美加力MAGNI、拉斯派特RUSPERT、耐美特NanoMate、美国TIODIZE公司的铝伏龙、钛伏龙;。
铝合金的表面处理及防腐

铝合金的表面处理及防腐铝合金是一种常见的金属材料,具有良好的机械性能和耐腐蚀性,然而,在特定环境下,铝合金的表面仍然需要进行处理和防腐,以延长其使用寿命并提高其美观度。
下面将介绍几种常见的铝合金表面处理和防腐方法。
1.阳极氧化:阳极氧化是一种常见的铝合金表面处理方法,通过在铝合金件上形成一层氧化膜,提高其耐磨、耐腐蚀、绝缘等性能。
阳极氧化的过程包括清洗、除油、酸洗、中和、阳极氧化和封孔等步骤。
阳极氧化可以根据不同的要求制备出不同颜色的氧化膜,如黑色、金色、银色等,同时还可以在氧化膜上进行印刷、染色和封孔等加工,提高其装饰性能和耐腐蚀性能。
2.电泳涂装:电泳涂装是一种在铝合金表面形成有机涂层的方法,通过在电解液中将漆液电泳到铝合金表面,使其形成均匀的涂层。
电泳涂装可以提高铝合金的外观质量和耐腐蚀性能,同时还可以实现不同颜色的涂层,提高铝合金的装饰性能。
电泳涂装的工艺比较复杂,需要严格的控制涂层的厚度、质量和均匀性。
3.喷涂和粉末涂料:喷涂和粉末涂料是一种简单常用的表面处理方法,通过在铝合金表面喷涂或粘附一层涂料或粉末,来改善其外观和耐腐蚀性能。
喷涂和粉末涂料可以选择不同颜色和质地的涂料,使铝合金件具有更好的装饰性能和耐候性。
但是,与电泳涂装相比,喷涂和粉末涂料的涂层质量和耐腐蚀性能较差。
4.氟碳喷涂:氟碳喷涂是一种常用的铝合金表面处理方法,通过在铝合金表面形成一层氟碳涂层,提高其耐候性、耐腐蚀性和外观质量。
氟碳喷涂是通过高温固化的方式,在铝合金表面形成一层均匀、致密的涂层,能够阻断氧、水和污染物的进入,使铝合金件具有更好的防腐性能。
氟碳喷涂具有耐高温、耐紫外线和耐化学腐蚀等特点,适用于室外环境和强酸碱环境。
综上所述,铝合金表面处理和防腐是保证其使用寿命和质量的重要措施。
不同的处理方法可根据实际需求选择,例如阳极氧化适用于提高耐磨和装饰性能,电泳涂装适用于提高耐腐蚀性能和外观质量。
在实际应用中,应根据材料的具体情况,结合使用环境和要求,选择适合的表面处理和防腐方法。
史上最全的金属表面处理工艺汇总
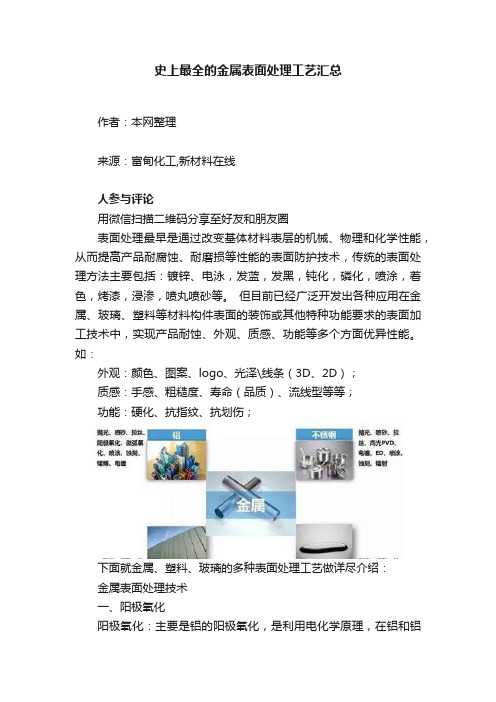
史上最全的金属表面处理工艺汇总作者:本网整理来源:富甸化工,新材料在线人参与评论用微信扫描二维码分享至好友和朋友圈表面处理最早是通过改变基体材料表层的机械、物理和化学性能,从而提高产品耐腐蚀、耐磨损等性能的表面防护技术,传统的表面处理方法主要包括:镀锌、电泳,发蓝,发黑,钝化,磷化,喷涂,着色,烤漆,浸渗,喷丸喷砂等。
但目前已经广泛开发出各种应用在金属、玻璃、塑料等材料构件表面的装饰或其他特种功能要求的表面加工技术中,实现产品耐蚀、外观、质感、功能等多个方面优异性能。
如:外观:颜色、图案、logo、光泽\线条(3D、2D);质感:手感、粗糙度、寿命(品质)、流线型等等;功能:硬化、抗指纹、抗划伤;下面就金属、塑料、玻璃的多种表面处理工艺做详尽介绍:金属表面处理技术一、阳极氧化阳极氧化:主要是铝的阳极氧化,是利用电化学原理,在铝和铝合金的表面生成一层Al2O3(氧化铝)膜。
这层氧化膜具有防护性、装饰性、绝缘性、耐磨性等特殊特性。
工艺流程:单色、渐变色:抛光/喷砂/拉丝→除油→阳极氧化→中和→染色→封孔→烘干双色:①抛光/喷砂/拉丝→除油→遮蔽→阳极氧化1→阳极氧化2 →封孔→烘干②抛光/喷砂/拉丝→除油→阳极氧化1 →镭雕→阳极氧化2 →封孔→烘干技术特点:1、提升强度,2、实现除白色外任何颜色。
3、实现无镍封孔,满足欧、美等国家对无镍的要求。
技术难点及改善关键点:阳极氧化的良率水平关系到最终产品的成本,提升氧化良率的重点在于适合的氧化剂用量、适合的温度及电流密度,这需要结构件厂商在生产过程中不断探索,寻求突破。
阳极氧化处理相关厂商1、比亚迪2、富士康3、大禹化工4、鸿荣恒铝制品……二、电泳 ( ED-Electrophoresis deposition )电泳:用于不锈钢、铝合金等,可使产品呈现各种颜色,并保持金属光泽,同时增强表面性能,具有较好的防腐性能。
工艺流程:前处理→电泳→烘干技术特点:优点:1、颜色丰富;2、无金属质感,可配合喷砂、抛光、拉丝等;3、液体环境中加工,可实现复杂结构的表面处理;4、工艺成熟、可量产。
- 1、下载文档前请自行甄别文档内容的完整性,平台不提供额外的编辑、内容补充、找答案等附加服务。
- 2、"仅部分预览"的文档,不可在线预览部分如存在完整性等问题,可反馈申请退款(可完整预览的文档不适用该条件!)。
- 3、如文档侵犯您的权益,请联系客服反馈,我们会尽快为您处理(人工客服工作时间:9:00-18:30)。
各 种 表 面 处 理 工 艺 防 腐 时 间 序号 加工类别 存放场地/环境
保护方
式
防腐时间 备注
1 热镀锌
室内
无 长时间 在无特殊环境基本无腐蚀 室外 无
长时间 在无特殊腐蚀环境,只暴露在普通大气环境下,防腐时间〉30年(理论值,未做具体实践) 2 酸洗
室内 内部酸
洗,外皮
涂漆
不固定(见备注) 内腔在3天后见轻微锈迹、一个星期见浮锈,一个月见局部腐蚀,三个月现深度腐蚀。
外皮由于喷涂不同的油漆,防腐时间不同,银粉无伤害条件下,样品半年出现泛黄,其余未发现锈蚀现象。
室外 内部酸
洗,外皮
涂漆 不固定(见备注) 内腔夏季无封堵的情况下,暴露在公司院内环境,1天后出现锈蚀,3天出现较多浮锈,一个星期局部出现腐蚀,半个月腐蚀较大,一个月出现深度腐蚀,冬季及干燥气候,2天出现腐蚀,一个星期出现浮锈,半个月见腐蚀,3个月出现深度腐蚀。
外皮因涂不同油漆出现腐蚀时间不同。
内腔夏季使用3M 贴的情况下,暴露在公司院内环境,36小时后可见出现锈
蚀,3天后出现较多浮锈,一个星期局部出现腐蚀,半个月腐蚀较大,一个月出
现深度腐蚀,冬季及干燥气候,2天出现腐蚀,一个星期出现浮锈,半个月见腐蚀,3个月出现深度腐蚀。
外皮因涂不同油漆出现腐蚀时间不同。
3 磷化室内
内腔磷
化,外皮
涂漆
不固定
(见备
注)
内腔在3个月后见轻微点蚀、半年出现可见点蚀,一年出现局部点蚀,18
个月出现局部面积性泛黄。
外皮由于喷涂不同的油漆,防腐时间不同。
室外
内腔磷
化,外皮
涂漆
不固定
(见备
注)
内腔夏季及严重潮湿天气无封堵的情况下,暴露在公司院内环境,7天后出
现点蚀,14天出现局部点蚀,一个月局部出现腐蚀,三个月腐蚀较大。
冬季及
干燥气候,45天后出现点蚀,90天出现局部点蚀,半年局部出现腐蚀。
外皮因
涂不同油漆出现腐蚀时间不同。
内腔夏季使用3M贴的情况下,15天后出现点蚀,30天出现局部点蚀,45
天局部出现腐蚀,三个月腐蚀较大。
冬季及干燥气候,60天后出现点蚀,半年
现局部点蚀。
外皮因涂不同油漆出现腐蚀时间不同。
4 串油室内
内腔酸
洗后串
油,外皮
不固定
(见备
注)
使用3M封堵,室内存放,内腔六个月未见锈蚀,有油迹,外皮因喷涂不同油漆防护时间不同。
涂漆
室外
内腔酸
洗后串
油,外皮
涂漆
不固定
(见备
注)
夏季使用3M封堵,20天后打开封堵,油迹微量,45天几乎无法发现油迹,60天出现明显锈蚀,冬季未验证。
外皮同样因不同的油漆,防护时间不同。
大连金州热镀锌有限公司
2010年8月13日。