产品平衡率及产能提升改善报告
改善的范文怎样写改善前改善后报告

改善的范文怎样写改善前改善后报告此类报告一般包含四个方面:(1)改善前的存在的问题、困境或缺陷(2)采取的改善的方案或措施(3)改善前后情况的对比:(4)改善后的成果参考的事例:生产流水线的改进一、改善前的问题点:1、流水线布局不合理,物流不畅通;2、平衡率偏低,效率低下;3、各工位所使用的工具无固定装置放置;4、部分工位会因物料配送不及时导致延误生产;5、5S推行不到位。
二、改善采取的措施:1、根据现生产机型安吉尔Y1160LKD-C制定工艺流程图,对工序重组,平衡各工位,并设定标准人力及产能;2、依据工艺流程图设计线体布局图,对各工位明确规定作业位置及摆放方式;3、工艺员对所用工具制作定位装置以便按位摆放;4、依据线体布局图推行5S;5、在实际生产中对工位内容再作调整,对作业方法进行修正以求完善。
三、改善前后对比:1、数据对比表2、成本对比表3、利润对比表四、改善后的成果:1、生产率:A.改善前23人作业,间接人员4人,时产45PCS,27人*7元/H ÷45PCS=4.2元;B.改善后24人作业,间接人员4人,时产55PCS, 28人*7元/H ÷55PCS=3.56元;C.节约成本:4.2-3.56=0.64元/台,平均日产量以600台计算,每月工作26天; 即:每天可节约成本:600台*0.64元/台=384元. 每月可节约成本:600台*26天*0.64元/台=9984元.每年可节约成本:600台*26天*12月*0.64元/台=119808元.D.生产率提高了:4.2元÷3.56元-1=17.98%。
2、5S推行:按制定的线体规划图进行按位摆放后,各工位均无乱放现象,5S 推行较为顺畅,生产现场有序进行。
3、IE思想推行:通过此次改善,让线长及全体员工都有深入参与,让他们有了成本意识,对工位及线体的改善方法有了初步了解,对于带动全体员工参与改善有着积极的影响。
生产效率提升与工艺优化工作总结汇报

生产效率提升与工艺优化工作总结汇报尊敬的领导和同事们:
我很荣幸能够在这里向大家总结汇报我们团队在生产效率提升与工艺优化方面所做的工作。
在过去的一年里,我们不断努力,不断探索,取得了一些令人振奋的成绩。
首先,我们团队在生产效率方面取得了显著的进展。
通过对生产流程的精细化管理和优化,我们成功地减少了生产周期,提高了生产效率。
我们还引进了先进的生产设备和技术,使生产过程更加智能化和自动化。
这些举措不仅提升了我们的生产能力,也大大降低了生产成本,为企业创造了更多的价值。
其次,我们团队在工艺优化方面也取得了一些成绩。
我们对生产工艺进行了全面的分析和调整,优化了生产流程,提高了产品质量。
我们还加强了与供应商和合作伙伴的沟通与合作,共同探讨工艺改进的方案,取得了一些创新性的成果。
在未来,我们将继续努力,不断挑战自我,进一步提升生产效率,优化工艺流程,为企业的发展贡献更多的力量。
我们相信,在
领导的指引下,在团队的合作下,我们一定能够取得更加辉煌的成绩!
谢谢大家!。
实施精益生产提高热轧的产品质量、产能利用率和稳定性
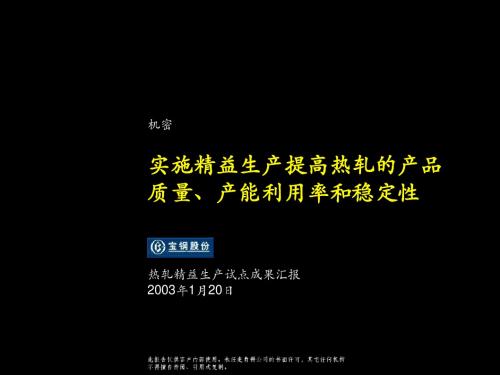
• 高层管理的决心和
参与
• 根据系统改善规划选
择项目
• 建立业绩管理系统 • 改善能力的培养
• 设置并培养改善专家 • 设置改善办公室
BS/030115/SH-PR(2000GB)
热轧的试点树立了良好的改善典范,为建立宝钢 持续改善方式打下了很好的基础
营运系统 解决问题的方法 • 在换辊、质量、维修 3个方面的试点都严 谨地用系统解决问题 的方法开展工作 解决问题的方法 改善工具和专业领域 知识
精益生产 六西格玛
“宝钢持续改善方式”
3
BS/030115/SH-PR(2000GB)
宝钢应将精益生产和六西格玛兼容并蓄,建立符 合宝钢特点的持续改善方式
营运系统 利用六西格玛 • 采用六西格 玛的DMAIC 标准化的, 严谨系统的 解决问题的 方法 解决问题的方法 改善工具和专业领域知识
• 在组织内部
密集型行业提高回报率 的关键手段
(不仅仅是突破性改进)?
2
BS/030115/SH-PR(2000GB)
精益生产和六西格玛都是企业实施营运改善的方 法,宝钢应兼容并蓄并加以创新以建立符合宝钢 特点的营运改善方法
全球领先的生产企业通过持之以恒地消 除生产系统和营运系统中的浪费和质量 波动,为股东创造了巨大的价值,并建 立起了长期的持续的竞争优势 精益生产和六西格玛的很多原则,工具 和方法可以为宝钢所用来提高公司业绩 和客户满意度 我们建议宝钢集精益生产和六西格玛之 精华,兼容并蓄,建立符合宝钢需要的 生产和营运方式以进行持续改善,应对 独特的战略和营运挑战
BS/030115/SH-PR(2000GB)
机密
实施精益生产提高热轧的产品 质量、产能利用率和稳定性
产能提升改善案
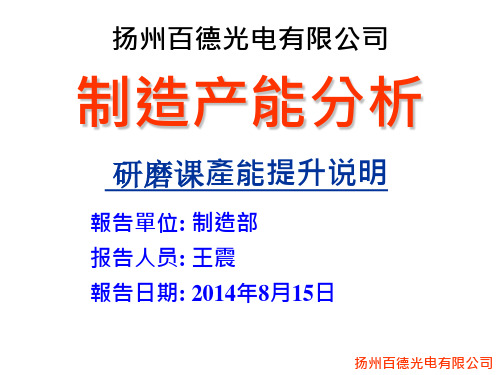
扬州百德光电有限公司
改善对策 原因分析
二.返工率高改善对策: A 与客户反馈来料异常问题,请协助改善前制程或沟通将 来料问题算为客户责任,降低反抛率;(业务协助) B 调配蚀刻前处理配方,使玻璃蚀刻后凹点/滚轮痕/刮伤 减轻,降低反抛率;(研发协助) C 请研磨机厂商指导如何将盘面修平;(采购/研发协助) D 将研磨液比重/吐液量调至范围内保证研磨的最基本条件; (制造部) E 讨论如何在研磨压力降低的情况下降低返工率; (研发协助)
扬州百德光电有限公司
产能低下原因分析
1、产能低下的原因分析
人
人员培训没有跟上
法
Sop培训 产量意识淡薄 绩效考核 质量意识培训
样品试验繁多
设备待机时无法人 工上料(玻璃) 来料异常 设备异常 实际单片研磨速度
为 什 么 产 能 低 下 ?
料
环
机
扬州百德光电有限公司
研磨课产能低原因分析 原因分析
一 机台稼动率低下: 1.1人员效率低下: 生产力低下,工作积极性不够,管理松散,团队合作欠缺,机器利用 率过低 A 员工计时工作热情不高涨-----反正时间到了就下班了,做多少都一样 B 公司计时工作成绩督导不够,有记录但无追踪-----员工一天做多少就 多少,无目标紧迫感 C 机台经常有停机现象-----待拿研磨玻璃/放玻璃至水槽车/刮水 D 公司管理制度不够严谨,员工随意离岗----没按照离岗制度落实执行, 且离岗无顶岗人员 E 线组长整体调配、相互协作的团队工作意识不足-----线体待料、堆料 无重视 F 各段产能没有硬性完成目标-----一天能做多少就做多少 G 无严格的奖惩机制-----产能的完成和自己没关系 H 多技能员工欠缺-----机动人员数量局限性 扬州百德光电有限公司
生产效率改善报告模板

测试CD-RW 烧K值 装上盖
固定上盖后部 固定上盖侧面
打高压 高清测试 打开设置 DVD+RW5.1CH DVD-9测试 VCD,MIC测试 外观检查 附件加工1 附件加工2 贴背板号板 加工彩盒
打刀卡 整机包装
卷刀卡 封箱,堆码
13.5 11.2 10.7
13.3 10.3
13.4 8.2
TPM
改善名称:烧KEY贴纸拿取改善
改善前
改善后
问题点说明:烧KEY贴纸放置太远,拿取时需 用M5的动作.
对策:将烧KEY贴纸挂在员工正前面,只需 M3动作.
效果:每台机节省时间M5-M3=0.258S/台. 6个月共计节省时间:0.258秒*2000台/天 *21.5天/月*6个月=1109分.节省费用:1109分 *0.4元/分=443元。
10.1 13.1 12.9 13.4 13.7 14.1
9.4 12.3
7.0 10.3 11.3 13.2 11.7 11.4 13.9 12.9 12.6 11.7 12.4
9.9 7.8
10.4 13.9
13.2 8.8
改善前:LOB=71.9%
改善后:LOB=82.5%
九、改善效果
NO. 项目 1 平均时产 2 人均产能
改善名称:改善面壳的放置位置
改善前
改善后
问题点说明:投入的面壳放置在作业员身后, 取面壳时需要转身180,浪费时间
对策:将面壳与垃圾箱的放置位置进行变 更,作业员取面壳转身90,减少转身的 时间浪费
效果:每台机节省时间=1.7S/台. 6个月共计节省时间:1.7S*2000台/天*21.5天/月*6个 月=7310分.节省费用:7310分 *0.4元/分=2924元。
生产效率提升总结汇报
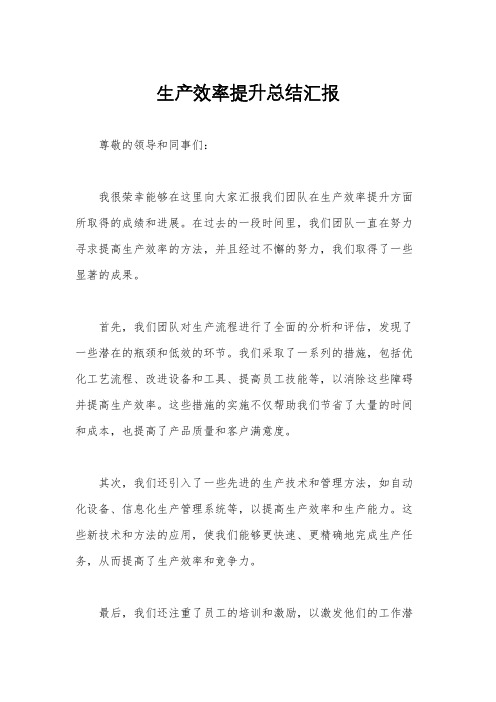
生产效率提升总结汇报
尊敬的领导和同事们:
我很荣幸能够在这里向大家汇报我们团队在生产效率提升方面所取得的成绩和进展。
在过去的一段时间里,我们团队一直在努力寻求提高生产效率的方法,并且经过不懈的努力,我们取得了一些显著的成果。
首先,我们团队对生产流程进行了全面的分析和评估,发现了一些潜在的瓶颈和低效的环节。
我们采取了一系列的措施,包括优化工艺流程、改进设备和工具、提高员工技能等,以消除这些障碍并提高生产效率。
这些措施的实施不仅帮助我们节省了大量的时间和成本,也提高了产品质量和客户满意度。
其次,我们还引入了一些先进的生产技术和管理方法,如自动化设备、信息化生产管理系统等,以提高生产效率和生产能力。
这些新技术和方法的应用,使我们能够更快速、更精确地完成生产任务,从而提高了生产效率和竞争力。
最后,我们还注重了员工的培训和激励,以激发他们的工作潜
力和创造力。
通过不断的培训和激励,我们的员工不仅增强了工作技能和专业素养,也更加积极主动地参与到生产工作中,为生产效率提升贡献了力量。
总的来说,通过团队的共同努力和不懈探索,我们成功地提高了生产效率,为企业的发展和竞争力提供了有力支持。
我们将继续努力,不断探索创新,为企业的发展和进步贡献更多的力量。
谢谢大家的支持和关注!
此致。
敬礼。
制程优化,生产效率提升改善案(应对产能爬坡)
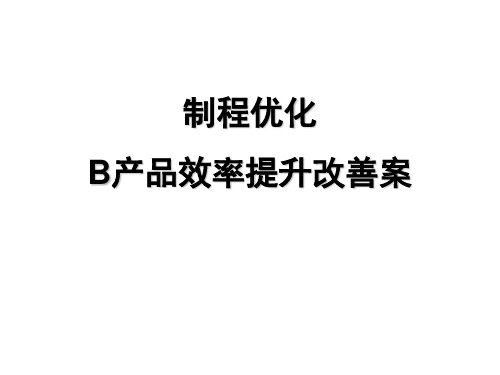
C2 1/2 1 1/2 0.630 0.190 3.136 C.I.=(λmax-3)/(3-1)=0.068<0.1
C3 3 2 1 1.817 0.547 3.136
B4
C1 C2 C3
Wi
Wi0
λmi
C1 1 1/4 1/7 0.329 0.082 3.004 λmax=1/3(λm1+λm2+λm3)=3.002
C1 0.081 0.540 0.263 0.082
Cj=ΣbiCji
0.156
C2 0.188 0.188 0.190 0.315 0.239
C3 0.731 0.163 0.547 0.603 0.593
方案三制程优化得分最高, 为最佳改善方向
二. 改善历程 (选择改善项目)
已改善过
量少影 响不大
无形效益
及时满足了出货 需求;
有形效益
使我建立了改善降理低念成, 本 ✓ 节省3人;
并已在E机种2上6应1万用R, MB/年✓. 产能提升30%;
产能从380台↗450台. ✓ 可降低成本261
万RMB/年.
工时: (280万台/年÷350台-280万台/年÷460台)
×1,273RMB/线.H =2, 435KRMB/年
1. 装HDD锁扣/贴贴纸工站 ( 8.8 〞)
1. 拆布套5〞/投基座2.2〞 2. 装遮片扣4.5〞 3. 装HDD扣5.5〞/贴贴纸3.3〞
无附加价值 能否取消布套?
二. 改善历程 (程序分析法﹑ECRS)
套布套
运输
拆布套
烤完漆
重取用复消E作套P业E/拆隔,无布开价套基值作座动业, 作.
运输
100% 81%
XXX产品效率提升改善方案
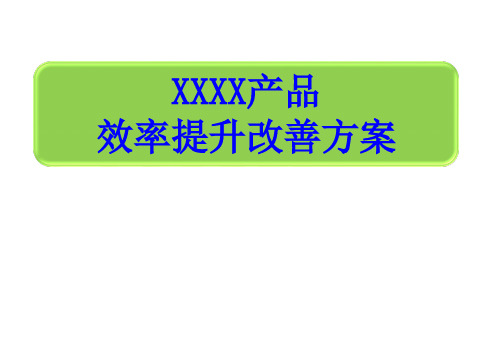
相关工位图片: 机器停板位置,PCB超过250mm,不能正常待板*3PCS,待板异常。
正常待板如图:
超过第二块 停板位置
三、改善方向
方案一:改善方向:制作合拼治具,在同一治具上同时装两快主板进行贴片
优化贴装工艺,提升产品效率: 1.治具钢网优化-----待讨论决议。
优化后:制作治具,同时贴片两块板
10-5号白班
1306 /
128
10-5夜班
1278 /
128
10-7号白班
/ 2710 280
效率提升 了1倍
效率提升 了1倍
经以上优化产能达到每天5K的,可以满足每天4K的出货计划。
优化后:制作治具,同时贴片两块板
2.贴片程序优化: 根据讨论后结果而定。
四、验证数据及追踪
合拼治具印刷效果:无存在偏移不良
印
印
刷
刷
BG
QF
A无
N
偏
无
移
偏具后实际生产效率看板
五、改善前后对比
XXX产品改善前后产能数据对比
项目
日期
独立治具贴片 交互合拼治具贴片 每小时实际产能
XXXX产品 效率提升改善方案
SMT工艺工程 2015年 5 月 28日
目录
一.提案团队成员 二.改善背景 三.改善方向及落实 四.数据验证及追踪 五.验证前后对比
一、提案团队成员
Team
Leader
工程
Name
Responsibility
1.计划目标订定 2.定期检讨,进度追踪 3. 任务分配 4.资料分析及汇整任务分配 钢网治具优化
优化前:A/B为阴阳板,不使用治具直接贴片
2.贴片程序优化: 根据讨论后结果而定。
家具厂精益改善推行报告

改善生产方式,提高产能,消除浪费
故为确保生产计划的顺利实施及精益化生产的顺利推行,我们准备先从生产计 划入手,通过下图的管理流程,合理安排生产,通过合并生产,提前排查等手 段防止半成品的挤压达到一线流的目的。
改善生产方式,消除浪费,提高产能
但由于物控方面一直无法及时排查,致我部门只能先从基础数据收集,改变员 工生产习惯,合理控制半成品等方面入手。下图是工人利用流水线流动方式进 行生产(目前网椅靠背线和座垫线大部分产品是流水线作业)
改善生产方式,消除浪费,提高产能
通过ECRS原则提高平衡率,提高产能:
符号 E C R S 名称 取消Eliminate 合并Combine 重排Rearrange 简化Simplify 说明 对于不合理、多余的动作或工序给予取消 对于无法取消又是合并后,再根据何人、何时、何处三个提问后进行重排 考虑能否采用最简单的方法或设备替代,以节省人力和时间
下图是关于网椅车间某些部件包装方式的改善,目前已经通知物控部去和供应 商沟通。
五、工装夹具的制定及工艺改善
下图是冲棉现场环境的改善,制作了一个冲棉收集装置,不仅大大改善了 现场环境,还更好的利用了循环利用。
改善前
改善后
五、工装夹具的制定及工艺改善
下图是根据工艺或者调整产能的一些改善定制的设备,目前已全部在使用中。
永艺家具股份有限公司
部门:办公椅IE部
组长:何文进 副组长:黄传胜
成员:占春辉、施龙、赵亚威 日期:2014-07-10
精益生产改善项目
一、制定推行进度以及各负责人
二、精益生产知识的培训以及宣传
三、车间厂房布局以及产线优化
四、改善生产方式,消除浪费,提高产能
五、工装夹具的制定及工艺改善
产能提升改善(QCC小组改善报告)

07/10月
月份
07/11月
测试时间
07/12月
经过导入新型测试治具,产能得到大幅度提升,测试品质进一步提高,改善效果明显,
可全面推广!
26
改善效果实际收益
产能 2000 1500 1000
PCS/H
50%
1000
1500
500
0 改善前产能(07-10) 改善后产能(07-12)
收益项目
实际收益
每一步工作输出
• 针对每一个关键因素 找出尽可能多的 改进方案
已使用的工具
• 头脑风暴 …
17
可选方案
18
采用五分制进行评分
选择方案
结论: 经过方案的筛选及对比三个备选方案的各项指标,从综合性的角度决定选择
第三套方案作为我们此次改善的切入目标!
19
执行解决方案
(1) 鉴别与 选择问题
(2) 理解问题 与探究根因
22
新旧测试方式对比
Comments:
使用改良后的新测试治具已经达成我们预设的每小时产能1300 台的目标,且能满足日后产能提升的需求.
23
新测试治具可靠性分析
可 控
24
评估与总结
(1) 鉴别与 选择问题
(2) 理解问题 与探究根因
(3) 制定解决
方案
(4) 选择方案
(5) 执行方案
(6) 评估与总结
每一步工作
实施选择 的解决方案
每一步工作输出
• 针对选择的方案进行逐步 实施和改进
已使用的工具
• 对比分析 • 图表分析 …
25
改善效果对比分析
改善 项目
改善XXX线初测站效率
提升HRXXXX生产效率-6Sigma改善报告
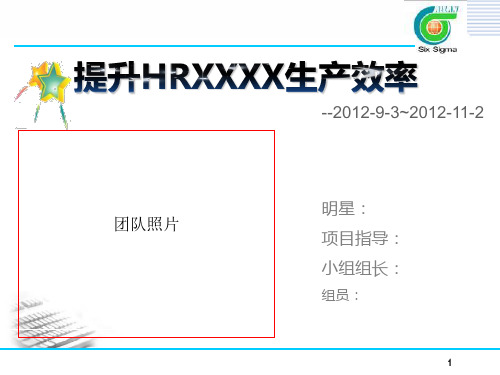
2
40
3
7
30
2
2
5
1 1 20 3
3
10
8
4
1 1.5 0 工序1
51.7 47 3
18
2 2 3 3 3 2 4 3 4 工序2
56.1 51 2 2 10
7 2 3
20
2 3 工序3
57.2
52 1 1 2
5
6
2 2
5
2 4 2 2 4 2 2 2
5
3 工序4
53.9
49 1 2 1 3 2 2
TT:节拍时间
51S
20.0
10.0
0.0
1
2
3
4
5
6
7
8
9
10 11 12 13 14 15
ST(s) 44.0 44.0 55.0 48.4 49.5 58.3 52.8 64.9 44.0 31.9 59.4 46.2 42.9 44.0 39.6
CT(s) 64.9 64.9 64.9 64.9 64.9 64.9 64.9 64.9 64.9 64.9 64.9 64.9 64.9 64.9 64.9
教导员工标准作业方法
改变电源线胶盆摆放方式 及运送方式
完成时间 2012-9-28 2012-9-28
2012-9-28 2012-9-28
负责人
22
确定 分析 关键流程 流程X
确定 主要X
快赢项目
改善前
工具放置位置改善
改善后
工序5剪钳放置位置挡住员工取料, 作业不方便,影响正常作业
更改剪钳放置位置,以方便取用物料 及工具为原则
团队照片
精益生产:公司生产效率提升改善项目报告

制作夹具,简化工艺 普通焊机改为储能式焊接机,减少后工序作业
人员 手动大螺丝改为自动打螺丝
月份
6月 6月 6月 6月 6月 6月 6月 6月
10
19系列天花灯固定器改善
螺丝加固定器改为半牙螺丝,取消固定器
6月
4.过程亮点展示
4.1、98,143系列压线扣工艺改善
1.压线扣单价0.03元 ,预计每年省1万元
54229.5
线外人员出勤
3298 457 488 1528 3595.5 9366.5
UPPH 151.98 35.15 39.78 76.96
2.70 345.67
数据分析 基准值 129.30 29.97 35.21 66.33
2.30
提升比率 17.54% 17.28% 12.98% 16.02% 17.56%
确认
2
953A 670 17 498 11 477 11 6 10.07%
3
9225N 650 19 535 13 483 13 6 8.52%
4
923N 650 19 535 13 479 13 6 7.63%
组装
5
9825 530 23 424 16 402 16 7 9.21%
6
983
530 23 424 16 419 16 7 11.02%
生物颗粒
优
高效,熔炼,安全 方便,灵活,节能 低碳,环保,恒温
4.过程亮点展示
4.7、异形插件机方案拟定
改善前视频
改善后方案视频
4.过程亮点展示
4.8、筒灯自动化生产线方案确认
筒灯自动化线视频
4.过程亮点展示
生产效率改进总结汇报
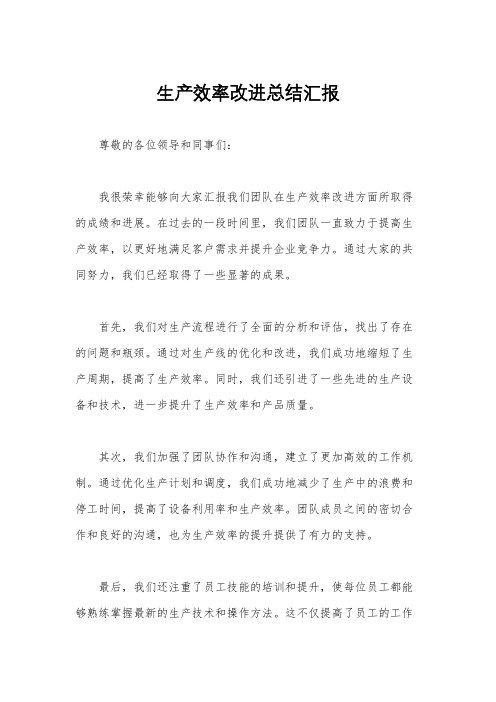
生产效率改进总结汇报
尊敬的各位领导和同事们:
我很荣幸能够向大家汇报我们团队在生产效率改进方面所取得的成绩和进展。
在过去的一段时间里,我们团队一直致力于提高生产效率,以更好地满足客户需求并提升企业竞争力。
通过大家的共同努力,我们已经取得了一些显著的成果。
首先,我们对生产流程进行了全面的分析和评估,找出了存在的问题和瓶颈。
通过对生产线的优化和改进,我们成功地缩短了生产周期,提高了生产效率。
同时,我们还引进了一些先进的生产设备和技术,进一步提升了生产效率和产品质量。
其次,我们加强了团队协作和沟通,建立了更加高效的工作机制。
通过优化生产计划和调度,我们成功地减少了生产中的浪费和停工时间,提高了设备利用率和生产效率。
团队成员之间的密切合作和良好的沟通,也为生产效率的提升提供了有力的支持。
最后,我们还注重了员工技能的培训和提升,使每位员工都能够熟练掌握最新的生产技术和操作方法。
这不仅提高了员工的工作
效率,也为企业的长期发展奠定了良好的基础。
总的来说,我们团队在生产效率改进方面取得了一些积极的成果,但也清楚地意识到还有很多工作需要继续努力。
我们将继续保
持团队的创新意识和进取精神,不断优化生产流程和改进工作方法,为企业的发展贡献更大的力量。
谢谢大家的支持和关注!
此致。
敬礼。
产品平衡率及产能提升改善报告

改进生产工艺
总结词
通过改进生产工艺,可以提高产品质量和生产效率,进而提升产品平衡率。
详细描述
对现有生产工艺进行全面分析,找出瓶颈环节和低效环节,针对性地进行改进。 可以采用新型工艺、引入新设备、优化生产线布局等方式,提高生产效率和产 品质量。
提升员工技能
总结词
通过培训和技能提升,提高员工的操 作水平和生产效率,有助于提升产品 平衡率。
增强企业抗风险能力
改进生产和产能管理可以降低企业对外部因素的依赖,提高抗风险 能力。
感谢您的观看
THANKS
时间安排与进度跟踪
时间安排
制定详细的实施计划时间表,包括各阶段的 时间节点和主要任务。
风险评估与应对措施
识别潜在风险和障碍,制定应对策略和预案。
进度跟踪
建立进度监控机制,定期检查实施进度,确 保按计划推进。
调整与优化
根据实施过程中遇到的问题和变化,及时调 整计划和资源配置。
06
预期效果与收益
提高产品平衡率的效果
实施多班次作业
总结词
通过实施多班次作业,提高设备利用 率和产能。
详细描述
根据产品特性和市场需求,合理安排 多班次作业,提高设备利用率和产能, 满足客户需求。
提高生产效率的其它方法
总结词
采用科学的管理方法和生产技术,提高生产效率。
详细描述
推行精益生产、六西格玛等科学管理方法,优化生产计划和调度,加强员工培训和技能提升,提高生产效率。
实施策略与措施
• 设立激励机制,鼓励员工积 极参与改进活动。
• 加强班组长管理能力培训, 提升生产现场管理水平。
策略三:数据分析与持续改进
实施策略与措施
• 收集生产相关数据,分析产品平衡 率和产能瓶颈。
【改善报告】宇龙产品包装线UPPH提升报告

点胶机、电脑异常较多 作业台面灯管灯光度不够
订单切换,切线损失较大 物料供应不及时
物料
人员流动性较大,新近作 业员动作不熟练
人为原因,返工不断
人
无
单 需 求 ?
法 满 足 客 户
订
三、生产效率提升改善对策
问题点
1.线平衡率低 2.动作、等待浪费
改善
改善对策
改善瓶颈工站,通过ECRS四大原则对 产线进行优化,使产能提升
组装工位工时图
16.00
标准工时 11.53S
14.00
12.00
10.00
8.00
6.ห้องสมุดไป่ตู้0
4.00
2.00
0.00 1 2 3 4 5 6 7 8 9 10 11 12 13 14 15 16 17 18 19 20 21 22 23 24
系列2 标准工时
二、原因分析---鱼骨图分析法
法
設備
线平衡率低 线平衡率低 作业动作、等待浪费
三、生产效率提升改善对策
目标UPH=420
线平衡率88%
四、改善状况追踪
连续2天平均产出 UPH达420
UPH提升验证线体包装L6在6/24~6/25每天平均产出UPH达到目标420; 最高UPH可达到520。
五、绩效评估
Item 总人力 UPH UPPH
改善前 31 220 8.05
改善后 40 420 10.5
2.因5860E面壳表面为高光面,作业时极易划伤,导致产线作业速 度下降,且外观不良较高
3. 由于客户订单要求较严,且出货时间较紧,产能无法满足 出货需求,需紧急对包装线进行产能提升。
一、现状分析
1、 当前5860E面壳预加工线配置人力28人/线,目标UPH为400, 可实际UPH仅达250(员工熟练度/壳体划伤不良较多影响),经过工 时量测以及UPH评估、线平衡率计算对现状进行详细的分析和评估。
【改善报告】8020组装线UPH提升
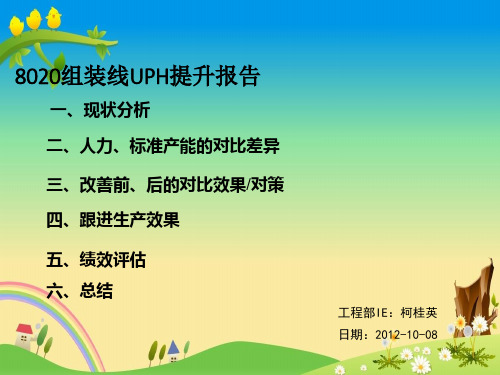
六、总结
侧按键弹性不良依仍存在,不良率占3%~5%左右,不良品跟线维修技术员可按 键1人负责维修,不影响标准产能
从生产日报表收集的数据来看,功能预检还有个别人员的测试速度还有待提升, 达不到要求(要求至少每人每小时达到55PCS),否则标准产能受影响,所以测试必
须无提件提升.
通过生产报表的数据收集显示,每小时产出520PCS不是问题,完全可以达到标 准要求.
二、人力、标准产能的对比差异
名称
当前人力
改善后人力
投入人力 39(包含FQC 10人)
40(包含FQC 11人)
UPH UPPH
425 10.9
520 13.0
人力差异 标准产/效果
L5线
四、跟进生产效果
五、绩效评估
1)人均产能提升19.3% 2)每小时总产能提升22.4% 3)生产效率提升19.3%约当精简人力=39-425/12.7=6.31人/线 4)月Costdown=单线精简人力*线体数*月工资=6.31*3*2000=37860RMB/月
另外,此款产品有很多工序可以提前预加工,这样标准产能还会有更大的提升 空间.
8020组装线UPH提升报告
一、现状分析 二、人力、标准产能的对比差异 三、改善前、后的对比效果/对策 四、跟进生产效果 五、绩效评估 六、总结
工程部IE:柯桂英 日期:2012-10-08
一、现状分析
由于现加工的产品利较低,而目前所投入的人力、设备的支出较高,客 户订单需求大,通过这断时间的磨合期,为满足客户的需求现对组装线的 标准产能进行改善。
产能分析报告范文(两篇)2024
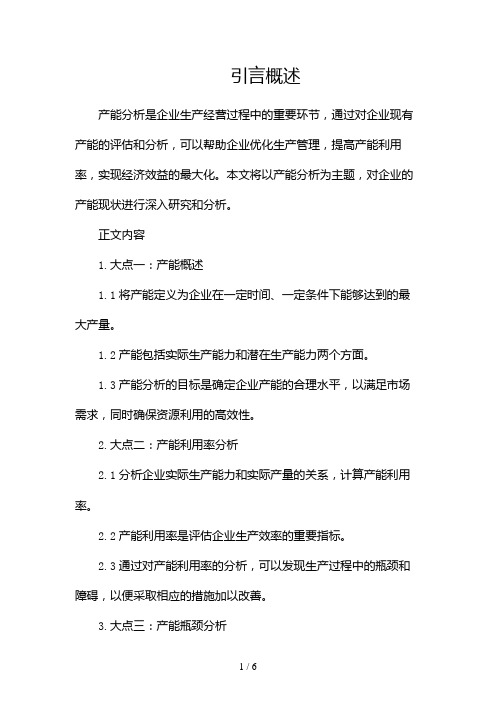
引言概述产能分析是企业生产经营过程中的重要环节,通过对企业现有产能的评估和分析,可以帮助企业优化生产管理,提高产能利用率,实现经济效益的最大化。
本文将以产能分析为主题,对企业的产能现状进行深入研究和分析。
正文内容1.大点一:产能概述1.1将产能定义为企业在一定时间、一定条件下能够达到的最大产量。
1.2产能包括实际生产能力和潜在生产能力两个方面。
1.3产能分析的目标是确定企业产能的合理水平,以满足市场需求,同时确保资源利用的高效性。
2.大点二:产能利用率分析2.1分析企业实际生产能力和实际产量的关系,计算产能利用率。
2.2产能利用率是评估企业生产效率的重要指标。
2.3通过对产能利用率的分析,可以发现生产过程中的瓶颈和障碍,以便采取相应的措施加以改善。
3.大点三:产能瓶颈分析3.1分析企业生产过程中的瓶颈环节,确定产能的瓶颈因素。
3.2产能瓶颈可能来自人力、设备、原材料等方面。
3.3通过产能瓶颈分析,可以找到优化产能的关键点,并提出解决方案以提高产能。
4.大点四:产能扩容方案4.1当企业的产能无法满足市场需求时,需要通过扩大产能来增加产量。
4.2产能扩容方案需要综合考虑市场需求、投资成本、技术条件等因素。
4.3可以通过增加设备、拓展生产线、优化生产流程等方式实现产能的扩容。
5.大点五:产能优化措施5.1产能优化是提高产能利用率和产能水平的重要手段。
5.2通过优化生产计划、提升设备效率、改善管理等方面,可以实现产能的优化。
5.3同时,还可以通过技术创新、流程改进等手段提高企业的核心竞争力和产能水平。
总结产能分析是企业管理中不可或缺的环节,通过对产能的评估和分析,可以为企业提供合理的产能水平和扩容方案。
通过优化产能利用率和实施产能优化措施,可以提升企业的生产效率和竞争力,实现经济效益的最大化。
在现代经济竞争激烈的环境下,不断优化产能是企业持续发展的关键因素。
因此,企业应高度重视产能管理,并不断提升自身的产能水平。
生产效率提升成果总结汇报
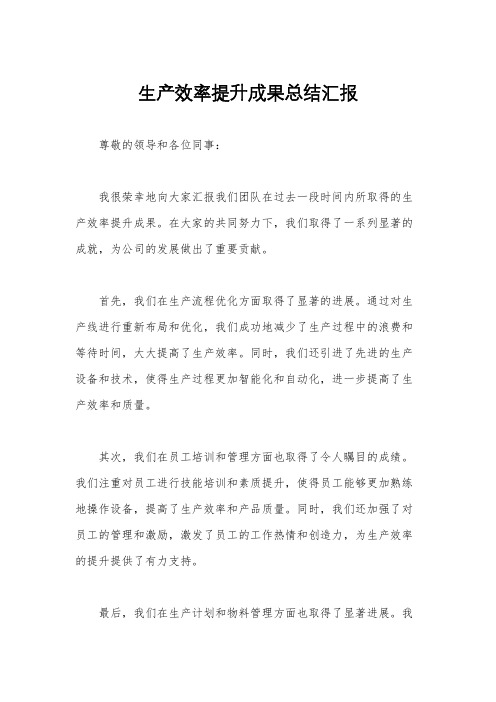
生产效率提升成果总结汇报尊敬的领导和各位同事:
我很荣幸地向大家汇报我们团队在过去一段时间内所取得的生产效率提升成果。
在大家的共同努力下,我们取得了一系列显著的成就,为公司的发展做出了重要贡献。
首先,我们在生产流程优化方面取得了显著的进展。
通过对生产线进行重新布局和优化,我们成功地减少了生产过程中的浪费和等待时间,大大提高了生产效率。
同时,我们还引进了先进的生产设备和技术,使得生产过程更加智能化和自动化,进一步提高了生产效率和质量。
其次,我们在员工培训和管理方面也取得了令人瞩目的成绩。
我们注重对员工进行技能培训和素质提升,使得员工能够更加熟练地操作设备,提高了生产效率和产品质量。
同时,我们还加强了对员工的管理和激励,激发了员工的工作热情和创造力,为生产效率的提升提供了有力支持。
最后,我们在生产计划和物料管理方面也取得了显著进展。
我
们优化了生产计划,合理安排生产任务,避免了生产过程中的闲置和拥堵,提高了生产效率。
同时,我们还改进了物料管理系统,减少了物料的浪费和损耗,为生产提供了充足的原材料保障。
总的来说,我们团队在生产效率提升方面取得了显著的成果,为公司的发展做出了重要贡献。
但是,我们也清楚地意识到,生产效率的提升是一个持续不断的过程,我们将继续努力,不断改进和创新,为公司的发展贡献更多的力量。
谢谢大家的支持和合作!
此致。
敬礼。
生产效率提升总结汇报
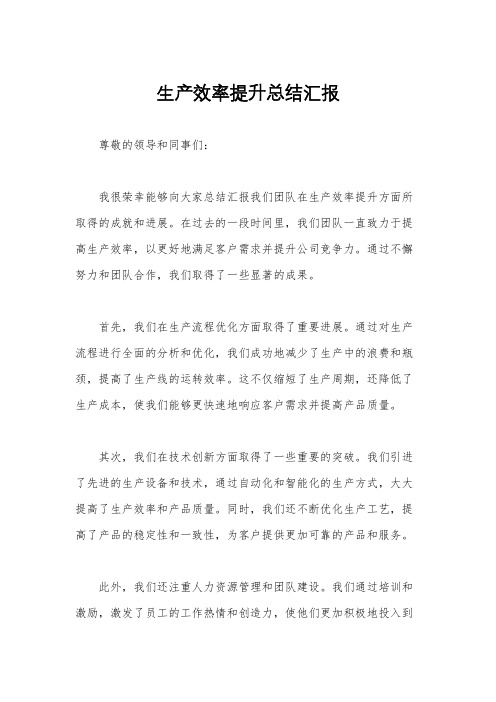
生产效率提升总结汇报
尊敬的领导和同事们:
我很荣幸能够向大家总结汇报我们团队在生产效率提升方面所取得的成就和进展。
在过去的一段时间里,我们团队一直致力于提高生产效率,以更好地满足客户需求并提升公司竞争力。
通过不懈努力和团队合作,我们取得了一些显著的成果。
首先,我们在生产流程优化方面取得了重要进展。
通过对生产流程进行全面的分析和优化,我们成功地减少了生产中的浪费和瓶颈,提高了生产线的运转效率。
这不仅缩短了生产周期,还降低了生产成本,使我们能够更快速地响应客户需求并提高产品质量。
其次,我们在技术创新方面取得了一些重要的突破。
我们引进了先进的生产设备和技术,通过自动化和智能化的生产方式,大大提高了生产效率和产品质量。
同时,我们还不断优化生产工艺,提高了产品的稳定性和一致性,为客户提供更加可靠的产品和服务。
此外,我们还注重人力资源管理和团队建设。
我们通过培训和激励,激发了员工的工作热情和创造力,使他们更加积极地投入到
生产工作中。
团队合作和沟通也得到了大大加强,使我们能够更加高效地协同工作,共同推动生产效率的提升。
总的来说,我们团队在生产效率提升方面取得了一些令人鼓舞的成绩,但我们也清楚地意识到还有许多工作需要继续努力。
我们将继续保持团队合作精神,不断探索和创新,以更加高效地满足客户需求并为公司发展做出更大的贡献。
谢谢大家的关注和支持!
此致。
敬礼。
- 1、下载文档前请自行甄别文档内容的完整性,平台不提供额外的编辑、内容补充、找答案等附加服务。
- 2、"仅部分预览"的文档,不可在线预览部分如存在完整性等问题,可反馈申请退款(可完整预览的文档不适用该条件!)。
- 3、如文档侵犯您的权益,请联系客服反馈,我们会尽快为您处理(人工客服工作时间:9:00-18:30)。
波蜂焊设备因影响品 质链速无法加快
载具为单板过炉,造成单片过炉时间长
分產 析能 影 響
TV
組 包
物料
过炉方向
三.改善方法:(一)
改善方向一:增加设备以满足出货量
解決方法
增加一条插件线,一台波蜂焊,一条补焊 线。以满足出货量.
三.改善方法:(二)
改善方向二:改变过炉基板数量
解決方法
改变过炉基板数量为两板过炉.
三.改善歷程:
方案確定 採用評價矩陣對方案進行選擇
序 號 1 2 對策 預期 實現 實施 產品 綜合 排序 效果 難度 成本 品質 評分
增加设 备
1板→2 板
14 24 3分
1 2
1分
9分
採取方案二: 1板→2板
四.績效評估--投資收益
方案一變更費用:
需增加过炉载具20套,费用为20*800RMB=16000RMB 以一月22天月產能2000K計算投資回收期︰
xxxxx有限公司
xx產品平衡率及产能提升改善报告
报告: 工程部IE课 报告 人: 报告日期: 2008年10月30日
报告内容
问题描述 原因分析 改善过程 绩效分析 效果确认
一.問題描述:
1.现每条线的人力配置为11人,产能为 350PCS/H 2.每天的产量为7000PCS(20H/天) 3.为满足12000PCS(20H/天)的出货量需 增加线体一条(波蜂焊设备因影响品质链速 无法加快)
成本分析
方 案 項 目
產能(Pcs/H) 設備成本(RMBH) 產能(KPcs/M) 設備成本(RMB/M) 現狀 方案一 方案二
350 8000 606 4,000
650 16,000 698 8,000
350 250,000 639 250,000
方案一成本: 16,OOO
方案二成本: 250,000
过炉方向
三.改善方法:(二)
改善方向二:降低平均傳輸時間(增加連板數量)
項目 連板數量 方案
優
點
缺
點
方案一
增加设备
2.提升產能;
1.更改方案时间长 2.增加战地空间; 3.投入成本較大.
方案二
1板→2板
1.提升設備利用率; 2.提升產能;
1.先前载具将报废; 2.只能做为单一机种;
三.改善歷程:
觀測統計各工站工作時間直方圖如下: 瓶颈时间为21.22S,平衡率为78%
插件段工时分析
波蜂焊时 间为瓶颈
5W1H法提问分析:
1.WHAT:增加波蜂焊线体一条 2.WHY:提升产能满足出货量 3.WHO:制造部门 4.WHERE:车间 5.WHEN:一直 1.HOW:增加设备
五因素魚骨圖分析
設備
四.績效評估—COST.DOWN
总产出工时下降3.22SEC/PCS 人力C.D/天/月:(人工费用按7.5RMB/H)
=(3.22*1200*10*22/3600*7.5)
=1077RMB/月
同時可節省1條線場地:80m
2
180,580/0.16=1128.6kpcs
T=1128.6/2000*26=21(天)
五.效果确认
改善后各工站工作時間直方圖如下: 瓶颈时间为10.0 5.0 0.0 HI-1 HI-2 HI-3 HI-4 HI-5 HI-6 HI-7 HI-8 HI-9 HI-10 HI-11