PCB可生产性设计规范
PCBA可制造设计规范
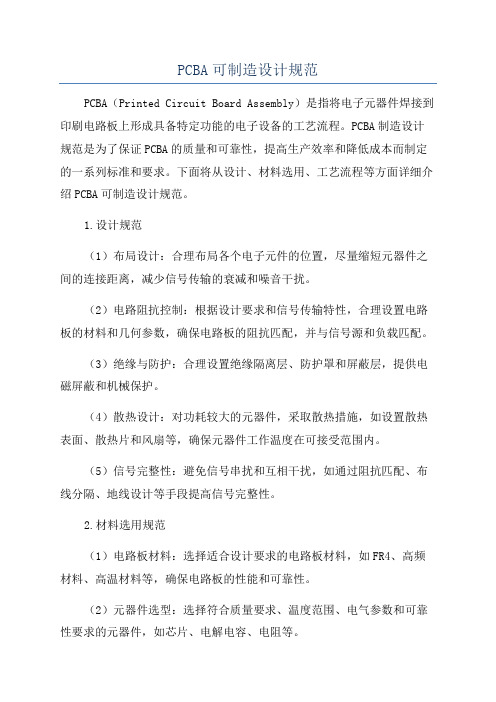
PCBA可制造设计规范PCBA(Printed Circuit Board Assembly)是指将电子元器件焊接到印刷电路板上形成具备特定功能的电子设备的工艺流程。
PCBA制造设计规范是为了保证PCBA的质量和可靠性,提高生产效率和降低成本而制定的一系列标准和要求。
下面将从设计、材料选用、工艺流程等方面详细介绍PCBA可制造设计规范。
1.设计规范(1)布局设计:合理布局各个电子元件的位置,尽量缩短元器件之间的连接距离,减少信号传输的衰减和噪音干扰。
(2)电路阻抗控制:根据设计要求和信号传输特性,合理设置电路板的材料和几何参数,确保电路板的阻抗匹配,并与信号源和负载匹配。
(3)绝缘与防护:合理设置绝缘隔离层、防护罩和屏蔽层,提供电磁屏蔽和机械保护。
(4)散热设计:对功耗较大的元器件,采取散热措施,如设置散热表面、散热片和风扇等,确保元器件工作温度在可接受范围内。
(5)信号完整性:避免信号串扰和互相干扰,如通过阻抗匹配、布线分隔、地线设计等手段提高信号完整性。
2.材料选用规范(1)电路板材料:选择适合设计要求的电路板材料,如FR4、高频材料、高温材料等,确保电路板的性能和可靠性。
(2)元器件选型:选择符合质量要求、温度范围、电气参数和可靠性要求的元器件,如芯片、电解电容、电阻等。
(3)焊接材料:选用适合工艺流程的焊接材料,如无铅焊料、焊膏等,确保焊接质量和可靠性。
3.工艺流程规范(1)印刷:确保PCB板材表面光洁、均匀,印刷厚度均匀一致,避免短路和偏厚现象。
(2)贴片:确保元器件与PCB板材精准对位,减少误差和偏离,避免虚焊、漏焊和偏焊。
(3)回流焊接:控制焊接温度和时间,确保焊点可靠性和焊接质量,避免过热和虚焊。
(4)清洗:清除焊接过程中产生的残留物,如焊膏、金属颗粒等,保证PCBA表面的干净和可靠性。
(5)测试与检验:进行全面的功能测试和质量检验,确保PCBA的功能和质量达到设计要求。
4.环境标准(1)温度和湿度:控制生产环境的温度和湿度,以确保PCBA的稳定性和可靠性。
PCB可制造性设计工艺规范

PCB可制造性设计工艺规范PCB(Printed Circuit Board,印刷电路板)是电子产品中非常常见的一部分。
它是由一种基层材料(通常是玻璃纤维增强复合材料)和通过印刷或压合技术固定在基层上的导电层构成的。
PCB可制造性设计工艺规范是一系列准则和要求,用于确保PCB的设计在生产制造过程中能够达到高质量和可重复性。
首先,对于PCB可制造性设计工艺规范来说,一个重要的方面是布局和布线。
布局指的是元件在PCB上的位置和排列方式,而布线则是指通过导线将元件连接在一起。
在布局方面,应该根据电路的需求和元件的特性进行合理的布局,避免不必要的干扰和噪音。
在布线方面,应该注意导线的长度、走线的宽度和间距,以及阻抗匹配和传输速率等因素。
其次,PCB可制造性设计工艺规范还包括了对于孔的规定。
在PCB制造过程中,通常需要在板上打孔以安装元件。
对于孔的规定,包括孔的类型(如贴片孔、通孔等)、孔的直径和位置等。
这些规定需要考虑到元件的尺寸和安装的要求,以及后续的焊接和连接等操作。
此外,在PCB可制造性设计工艺规范中还包括了对于焊盘和焊接的要求。
焊盘是指用于连接元件和导线的金属圆盘。
对于焊盘的规定,包括焊盘的形状、尺寸和间距等。
而对于焊接的要求,包括焊接的方法、焊点的形状和强度等。
这些规定需要考虑到焊接工艺的可行性和可靠性,以及后续的维修和升级等操作。
最后,PCB可制造性设计工艺规范还应该包括对于阻焊和丝印的要求。
阻焊是一种覆盖在PCB表面的绝缘材料,用于保护导线和焊盘不受外界环境的影响。
对于阻焊的规定,包括阻焊的类型、颜色和厚度等。
丝印则是一种印刷在PCB表面的文字和标记,用于标识元件和线路的位置和功能。
对于丝印的规定,包括丝印的颜色、位置和字体等。
总的来说,PCB可制造性设计工艺规范是为了确保PCB在生产制造过程中能够达到高质量和可重复性而制定的一系列准则和要求。
这些准则和要求涵盖了PCB布局和布线、孔的规定、焊盘和焊接的要求,以及阻焊和丝印等方面。
PCB设计的可制造性原则

PCB设计的可制造性原那么1. 引言在电子产品制造过程中,PCB〔Printed Circuit Board,印制电路板〕的设计是非常关键的一步。
一个好的PCB设计不仅可以提高产品的性能和可靠性,还可以降低制造本钱和生产周期。
为了确保PCB设计的可制造性,设计人员需要遵循一些根本原那么和最正确实践。
本文将介绍一些常用的PCB设计的可制造性原那么。
2. 原那么一:保持布局简单和紧凑在进行PCB设计时,保持布局简单和紧凑是非常重要的原那么。
简单的布局可以降低PCB的复杂性,减少错误的可能性。
紧凑的布局可以缩短信号传输路径,减少电磁干扰,提高信号完整性。
3. 原那么二:考虑耦合和信号完整性PCB上的不同电路和组件之间存在着耦合作用。
在设计PCB时,需要考虑不同信号之间的干扰和交叉耦合。
通过合理的布局和地线规划,可以减少电磁干扰的影响,并提高信号的完整性。
4. 原那么三:合理设置电源和地线电源和地线的布局在PCB设计中扮演着重要的角色。
良好的电源和地线布局可以确保良好的电源分配和地线回流,减少电源噪声和干扰。
在设计中,应尽量将电源和地线别离,并使用适宜的地引脚和电源引脚进行连接。
5. 原那么四:防止过于密集的布线在PCB设计中,过于密集的布线可能导致信号干扰和短路等问题。
因此,应尽量防止过于密集的布线,合理规划和安排信号线和电源线的路径。
同时,应留出足够的空白区域,方便焊接和维修工作。
6. 原那么五:合理选择元件和材料在PCB设计中,选择适宜的元件和材料也是非常重要的。
适宜的元件和材料可以提供更好的性能和可靠性。
应选择具有良好可焊性和耐高温的元件,并防止使用过时或质量不佳的元件和材料。
7. 原那么六:考虑制造和组装过程在PCB设计中,要考虑制造和组装过程。
例如,要确保元件的放置和布线不会影响到焊接和组装的顺利进行。
同时,要尽量减少PCB板的层数和复杂性,以降低制造和组装的本钱。
8. 原那么七:进行设计验证和测试PCB设计完成后,应进行设计验证和测试。
PCB可制造性设计规范

PCB可制造性设计规范PCB (Printed Circuit Board)的制造性设计规范是指在设计和布局PCB电路板时所需考虑的一系列规范和标准,以确保电路板的制造过程顺利进行并获得可靠性和性能。
一、尺寸规范1.PCB电路板的尺寸要符合制造商的要求,包括最小尺寸、最大尺寸和板上零部件之间的间距。
2.确保电路板的边缘清晰、平整,并防止零部件或钳具与电路板边缘重叠。
二、层规范1.根据设计要求确定所需的层次和层的数量,确保原理图和布局文件的一致性。
2.定义PCB的地平面层、电源层、信号层和垫层、焊盘层等的位置和规格。
三、元件布局规范1. 合理布局元件,以最小化路径长度和EMI (Electromagnetic Interference),提高电路的可靠性和性能。
2.避免元件之间的相互干扰和干涉,确保元件之间有足够的间距,以便于焊接工序和维修。
四、接线规范1.线路走向应简洁、直接,避免交叉和环形走线。
2.确保信号和电源线路之间的隔离,并使用正确的引脚布局和接线技术。
五、电路可靠性规范1.选择适当的层次和厚度,以确保足够强度和刚度。
2.确保电路板表面和感应部件光滑,以防止划伤和损坏。
六、焊接规范1.在设计中使用标准的焊盘尺寸和间距,以方便后续的手工或自动焊接。
2.制定适当的焊盘和焊缺陷防范措施,以最小化焊接问题的发生。
七、标准规范1. 遵循IPC (Institute for Interconnecting and Packaging Electronic Circuits)标准,以确保PCB的制造符合国际标准。
2.正确标注和命名电路板上的元件和信号,以方便生产和测试。
八、生产文件和图纸规范1.提供准确和详细的生产文件和图纸,包括层叠图、金属化孔、引线表和拼图图等。
2.确保文件和图纸的易读性和可修改性。
九、封装规范1.选择适当的封装类型和尺寸,以满足电路板的要求。
2.避免使用不常见或过于复杂的封装,以确保可靠的元件焊接和连接。
可制造性需求规范AQ2A-05-R002

< 0.8mm
< 0.8mm
缩短贴片周期、减少短 路,提高直通率
BGA旁边加MARK 标识点
φ1.0mm,圆或方形
依照IPC-7351设 计
依照IPC-7351设计
缩短贴片周期、减少短 路,提高直通率 缩短贴片周期、减少短 路,提高直通率
依照IPC-7351设 计
缩短贴片周期、减少短 路,提高直通率
1.2mm
器件的重量
表贴器件最大重量≤
35g,元件重量与顶部可
吸附面积比小于0.600g/ ㎡.A=器件重量/引脚与 焊盘接触面积,片式器 件A≤0.075g/㎡,翼形引 脚器件A≤0.300g/㎡,J
器件重量符合要求, 利于自动贴片机的生 产,且保证焊接质量, 器件不易脱落。
形引脚器件A≤0.200g/
38
电容及信号接口接 地PAD
39
插件管脚过孔
40
功放IC
41
管脚PAD间距
42
单板可 制造性
43
单板可 制造性
Φ30-50mi
Φ30-50mi
≧ 0.1mm
≧ 0.1mm
缩短装配周期、减少装 配出错率。
缩短装配周期、减少装 配出错率。
按原理图标识重 要的测试点
缩短装配周期、减少装 配出错率。
≧ 5mm
≧ 5mm
≧ 2.0mm 清晰、不得印在 焊盘上 ≧ 5mm
缩短装配周期、减少装 配出错率。 缩短装配周期、减少装 配出错率。 缩短装配周期、减少装 配出错率。 缩短装配周期、减少装 配出错率。 缩短装配周期、减少装 配出错率。
≧ 5mm
缩短装配周期、减少装 配出错率。
椭圆形
椭圆形、泪滴型
PCB设计规范范文

PCB设计规范范文PCB(Printed Circuit Board)是电子产品中不可或缺的关键组件之一、它承载着电子元件并提供电气连接,为电子设备的正常运行提供支持。
为了确保PCB的正常工作和受到适当的维护,有一套规范和指南来指导PCB的设计和生产。
以下是一些常见的PCB设计规范:1.尺寸规范:PCB的尺寸应根据实际应用需求进行设计,并应考虑到电子产品的外部尺寸要求。
尺寸的准确性对于PCB和组装工艺的成功都至关重要。
2.电气规格:PCB设计应符合应用需求的电气规范。
其中包括电压、电流、频率等参数的限制。
电气规格的合理设计可以确保电路的稳定性、可靠性和性能。
3.材料选用:PCB的材料选择应考虑到产品应用场景和要求,包括高温环境、潮湿环境、抗震性能等。
常见的PCB材料有FR-4、铝基板、陶瓷基板等。
4.敏感电路隔离:PCB设计中敏感电路应与其他电路隔离,以避免相互之间的干扰。
敏感电路包括模拟电路和高频电路。
5.地线规划:良好的地线规划可以降低电路中的噪声和干扰。
地线应尽可能宽,避免共线回流路径,减小回流电流的磁场。
6.线宽距规范:PCB中导线的线宽和间隔距离应根据电流和电压要求设计。
较大的电流需要较宽的线宽,较大的电压需要较大的间距。
7.最小孔径:PCB设计中应注意最小孔径的限制,以确保钻孔的准确性和稳定性。
通常情况下,最小孔径应大于钻头直径的两倍。
8.贴片元件安装规范:PCB设计中应合理安排贴片元件并留出足够的安装空间。
贴片元件的布置应符合组装工艺的要求,并确保元件之间的电气连接。
9.GPIO引脚排列:PCB设计中应按照IC的GPIO引脚功能进行排列。
相同功能的引脚应相邻,以方便信号的连接和布线。
10.PCB标记和标识:PCB设计中应包含元件的标记和标识。
标记包括元件的名称和编号,以方便组装和维护。
11.焊盘设计:PCB设计中应合理设计焊盘,确保良好的焊接质量。
焊盘的尺寸和形状应适应元件的尺寸和引脚间距。
PCB设计规范
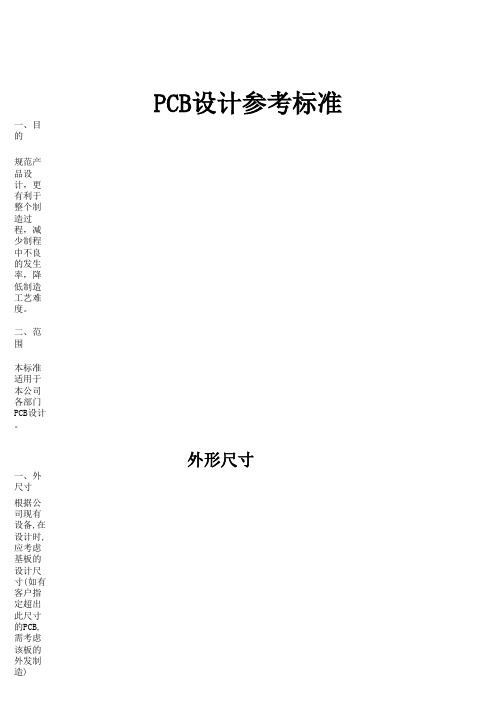
一、目的规范产品设计,更有利于整个制造过程,减少制程中不良的发生率,降低制造工艺难度。
二、范围本标准适用于本公司各部门PCB设计。
一、外尺寸根据公司现有设备,在设计时,应考虑基板的设计尺寸(如有客户指定超出此尺寸的PCB,需考虑该板的外发制造)根据公司设备情况.模板时应避免将PCB窄边作为制造用板边.或在窄边布置工艺板边.注:②.自动插件部品脚距离制造板边<5 mm(图中②)③.手动插件、自动插件部品表面任意部分距离制造板边尺寸<2.00mm;(图中③)⑤.<1.00mm空电路线距离制造板边尺寸<3.00mm(图中⑤)⑥.定位孔中心距离制造板边>7.00mm或定位孔边缘距离制造板边距离>8.50(图中⑥)④.手动插件的背面焊盘距离制造板边<1.00mm;(图中④)PCB设计参考标准1、公司当前设备可制造最大PCB外尺寸为330.00*250.00mm;但最小整板不得低于64.00mm.2、当有以下情况之一,需要增加工艺板边:①.SMD贴装部品焊盘距离制造板边尺寸<5.00mm;(图中①)外形尺寸无工艺板边布板时需要特别注意禁止布置SMD元件区域,不得安放任何SMD元件.释义:工艺板边——工艺边其实就是为了辅助生产插件走板、焊接过波峰在PCB板两边或者四边增加的部分,主要为了辅助生产,不属于PCB板的一部分,生产完成需去除。
制造板边——是指在完全没有工艺板边的情况下PCB四周的边缘部分,常常被视作板边在制造过程中使用。
二、定位标示释义:定位孔——用于制造过程中安装夹具或机械定位的通孔。
定位开孔与安装孔可通用.螺丝孔——产品组装时用于固定或安装产品的通孔。
因受力较大。
在设计时需要做加强其机械应力.1.定位孔的设计根据制造工艺来定,公司现行使用定位孔的工艺段分别为:自动插件印刷ICT FCT高压测试公司现行AI采用弹簧爪片对PCB进行定位作业,故对PCB定位孔有一定的技术要求.①.爪片的可定位尺寸在3.00-6.00mm.最佳生产状态为3.00mm(中心距离板边5.00mm)②.定位孔大小定∅4.00mm,允许误差为+0.05③.所有定位孔或螺丝孔周围5*5mm范围内,禁止布置SMD元件.以避免基板加工或螺丝紧定时产生外力导致部品损坏.(定位孔设计在工艺板边时,则无需考虑此问题)2、MARK点的设置.焊盘外径D一般不小于(d+1.5)mm,其中d为孔径,对于一些密度比较大的元件的焊盘最小直径可取(d+1.2)①MARK点为1*1mm露铜圆形,可以选用镀锡,在周围再围绕∮3.00mm圆环,以增强与隔绝外围线路。
PCB设计规范

PCB设计规范1. 目的规范产品的电路和工艺设计,确定设计时的各项参数,使得PCB的设计满足可生产性、易测试性、EMC(电磁兼容性)、EMI(电磁干扰)、DFM(面向制造的技术)等技术规范要求,在产品设计过程中构建产品的工艺、技术、质量、成本等优势。
2. 使用范围本规范使用于所有电子产品的PCB工艺设计,运用于但不限于PCB的设计、PCB投板工艺审查、单板工艺审查等活动。
3. 规范内容3.1 PCB物理参数要求3.1.1 PCB板材根据PCB的使用条件以及机械、电性能要求确定基材材质,例如:FR-4、CEM-1、铝基板、陶瓷基板、纸芯板等;根据PCB的结构确定覆铜箔层数,例如:单面、双面或多层板;根据PCB的尺寸和元器件重量确定基材厚度,一般在0.3mm~6mm,常用PCB的厚度是1.6mm,特大型板可用2mm。
基材参数Tg(玻璃化转变温度)、CTE(热膨胀系数)、耐热性、平整度、电气性等符合要求。
3.1.2 PCB表面处理确定PCB铜箔的表面处理镀层,例如镀锡、镀镍、镀金或OSP等,并在文件中表明。
3.2 热设计要求3.2.1 高热器件应考虑放于出风口或利于对流的位置。
3.2.2 较高的元件应考虑放于出风口,且不阻挡风路。
3.2.3 散热器的放置应考虑利于对流。
3.2.4 温度敏感器械件应考虑远离热源。
对于自身温升高于 30℃的热源,一般要求:a.在风冷条件下,电解电容等温度敏感器件离热源距离要求大于或等于 2.5mm;b.自然冷条件下,电解电容等温度敏感器件离热源距离要求大于或等于 4.0mm。
若因为空间的原因不能达到要求距离,则应通过温度测试保证温度敏感器件的温升在降额范围内。
3.2.5 大面积铜箔要求用隔热带与焊盘相连。
为了保证透锡良好,在大面积铜箔上的元件的焊盘要求用隔热带与焊盘相连,即焊盘与铜箔间以“十”字或“米”字形连接;对于需过5A以上大电流的焊盘不能采用隔热焊盘,如图1所示:3.2.6 过回流焊的0805以及0805以下片式元件两端焊盘的散热对称性。
PCB可生产性设计规范
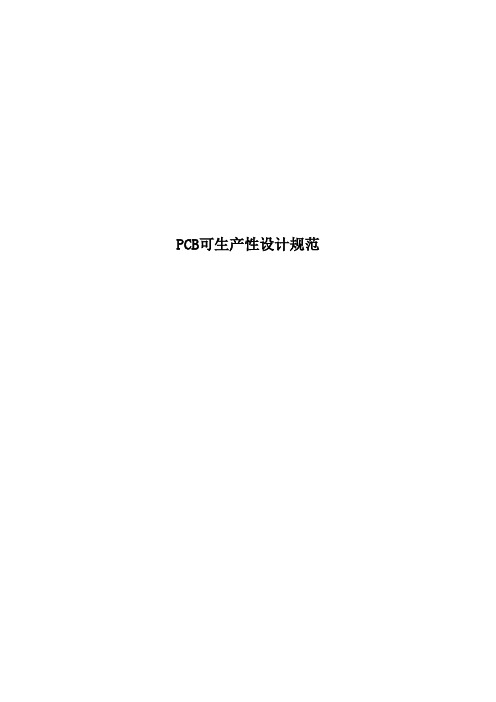
PCB可生产性设计规范PCB可生产性设计规范1 目的为规范PCB的设计工艺,保证PCB的设计质量和提高设计效率,提高PCB设计的可生产性、可测试性、可维护性。
本规范适用于公司设计的所有印制板(简称PCB)2 名词定义Pcb layout:pcb布局Solder mask:防焊膜面、防焊漆、防焊绿漆Fiducial Mark:光学定位点或基准点Via hole:导通孔SMD:表面贴装器件THC/THD:通孔插装器件Mil:长度单位,1mil=0.0254mm3 PCB总体设计要求3.1 PCB外形PCB外形(含工艺边)为矩形,单板或拼板的工艺边的四角须按半径R=2mm圆形倒角。
应尽可能使板形长与宽之比为3:2或4:3,以便夹具夹持印制板。
PCB传送方向3.2 印制板的可加工尺寸范围适用于全自动生产线的PCB尺寸为最小长×宽:50mm×50mm、最大长×宽:320mm×250mm,设计单板或拼板时,SMT阶段允许使用最大拼板尺寸为320mm×250mm,SMT完成后,可拆成不大于220mm×220mm的单板或拼板。
(PCB单板尺寸较小时,建议拼板尺寸不大于210mm×210mm)3.3 传送方向的选择:为减少焊接时PCB的变形,对不作拼板的PCB,一般将其长边方向作为传送方向;对于拼板也应将拼板的长边方向作为传送方向。
但是对于短边与长边之比大于50~80%的PCB,可以用短边传送。
3.4 传送边单面贴片PCB的传送边的两边应分别留出≥5mm(200m il)的宽度,传送边正反两面在离板边5mm的范围内不能有任何元器件或焊点。
双面贴片PCB,第一面的传送边的两边分别留出≥5mm的宽度,传送边在5mm内的范围内不能有任何元器件或焊点,第二面的传送边要求同第一面贴片PCB。
PCB外形示意图表1 SMT贴片PCB尺寸要求●单面贴装单面贴装示意图●单面混装单面混装示意图●双面贴装双面贴装示意图●双面混装常规波峰焊双面混装示意图3.4.1 如果PCB单元板尺寸在传送边器件禁布区尺寸上不能满足上述5mm宽度要求时,必须在相应的板边增加≥5mm宽的工艺边。
某公司PCB设计规范样本

某公司PCB设计规范样本1. 引言PCB(Printed Circuit Board,印刷电路板)是现代电子设备中常见的一种重要组成部分,它承载着电子元器件,并提供了电子元器件之间的电气连接。
为了保证PCB的质量和可靠性,某公司制定了一套严格的PCB设计规范样本,本文将介绍该规范样本的具体内容和要求。
2. PCB设计规范2.1 PCB尺寸和层数根据不同的应用需求,PCB的尺寸和层数会有所不同。
在某公司的设计规范样本中,PCB的尺寸通常不超过20cm×20cm,并且层数不超过4层。
若需要超出这个范围,需要额外申请和审批。
2.2 PCB布局和布线2.2.1 元器件布局•元器件应按照电路图要求合理布局,尽量缩短信号传输路径,降低信号干扰。
•元器件之间应保留足够的间距,以便于安装和维修。
•高功率元器件和高频元器件应与敏感元器件保持一定的间距,防止互相干扰。
2.2.2 信号和电源平面•PCB上应划分信号和电源平面,以降低信号串扰和提供稳定的电源供应。
•信号和电源平面之间应保持一定的距离,以减少互相干扰。
2.2.3 信号走线•信号走线应尽量保持短、直、对称。
•临近平面的信号线应与平面保持一定距离,以减少互电容和互感。
•若有高速信号或高频信号,应采取差分走线或者层间引线走线方式,以减少信号衰减和串扰。
2.3 焊盘和焊接2.3.1 焊盘设计•焊盘的大小应根据元器件引脚的尺寸和数量合理确定,避免太小或太大。
•焊盘的形状应选择圆形或方形,避免使用带尖角的形状。
2.3.2 焊盘与元器件引脚的间距•焊盘与元器件引脚之间应保留一定的间距,避免短路或接触不良。
2.3.3 焊接工艺•焊接工艺应符合IPC标准,并采用无铅焊接方式。
•焊接时应遵循良好的工艺控制,如控制温度、焊接时间和焊接扩展量等。
2.4 丝印和字体2.4.1 PCB丝印•PCB上的丝印应清晰、易读,方便组装和维修。
•丝印的颜色应与PCB背景颜色形成明显对比,以提高可视性。
最全PCB设计规范

最全PCB设计规范PCB设计规范是指对PCB板设计与布线进行规范化的要求和标准。
合理的PCB设计规范可以提高电路的可靠性、可制造性和可维护性,减少设计错误和生产问题。
以下是一个最全的PCB设计规范指南:一、尺寸和层数规范1.预留适当的板边用于固定和装配。
2.保持板厚适当,符合设备尺寸和散热要求。
3.层数应根据电路需求合理选择,减少层数可以降低生产成本。
二、元器件布局规范1.分配适当的空间给每个元器件,避免过于拥挤。
2.避免敏感元器件(如高频元器件)靠近高噪声源(如高压变压器)。
3.分组布局,将相关功能的元器件放在一起,便于调试和维护。
三、信号线布线规范1.信号线走线应尽量保持短而直的原则,减小传输延迟和信号损耗。
2.高频信号线避免与高电流线路交叉,以减少互相干扰。
3.分层布线,将高频信号和低频信号分开,避免互相干扰。
四、电源和地线布线规范1.电源线和地线应尽量宽而短,以降低阻抗。
2.使用大面积的地平面,减少地回流电流的路径。
3.电源线和地线应尽量平行走线,减少电感和电容。
五、阻抗控制规范1.布线时应根据需求控制差分对阻抗和单端信号阻抗。
2.保持差分对信号的平衡,避免阻抗不匹配。
3.使用合适的线宽和间距设计走线,以满足阻抗要求。
六、焊盘和插孔规范1.确保焊盘和插孔的尺寸、形状和位置符合零部件要求,并适合选用的焊接工艺。
2.避免焊盘和插孔之间过于拥挤,以便于手动和自动插件。
七、丝印规范1.丝印应清晰可见,包括元器件标识、引脚标识、极性标识等。
2.不要在元器件安装位置上涂抹丝印墨水,以免影响焊接质量。
八、通孔布局规范1.确保通孔位于焊盘的中心,避免焊盘过大或过小,影响焊接质量。
2.根据电路需求选择合适的通孔类型(如PTH、NPTH等)。
九、防静电规范1.PCB板表面清洁,避免灰尘和静电积累。
2.使用合适的静电防护手套和接地装置进行操作。
十、符号和标识规范1.适当添加电路图符号和标识,便于后续调试和维护工作。
印制电路板可制造性设计规范共11页word资料

1范围1.1主题内容本标准规定了电子产品中印制电路板设计时应遵循的基本要求。
1.2适用范围本标准适用于以环氧玻璃布层压板为基板的表面组装印制板设计,采用其它材料为基板的设计也可参照使用。
2引用标准GB 2036-94 印制电路术语GB 3375-82 焊接名词术语SJ/T 10668-1995 表面组装技术术语SJ/T 10669-1995 表面组装元器件可焊性试验Q/DG 72-2019 PCB设计规范3定义3.1术语本标准采用GB 3375、GB2036、SJ/T 10668定义的术语。
3.2缩写词a. SMC/SMD(Surface mounted components/ Surface mounted devices):表面组装元器件;b. SMT(Surface mounted technology):表面组装技术;c. SOP(Small outline package):小外形封装,两侧具有翼形或J形短引线的一种表面组装元器件封装形式;d. SOT(Small outline transistor):小外形晶体管;e. PLCC(Plastic leaded chip carrier):塑封有引线芯片载体,四边具有J形短引线,典型引线间距为1.27mm,采用塑料封装的芯片载体,外形有正方和矩形两种形式f.;QFP(Quad flat package):四边扁平封装,四边具有翼形短引线,引线间距为1.00mm,0.80mm,0.65mm,0.50mm,0.30mm等;g. DIP (Dual in-line package):双列直插式封装h.;BQFP (QFP with buffer):带缓冲垫封装的Q FP;i. PCB (Printed circuit board):印制板。
J.BGA(Ball Grid Array):球形栅格列阵4一般要求4.1印制电路板的尺寸厚度4.1.1印制板最小尺寸L×W为80mm×70mm,最大尺寸L×W为457mm×407mm4.1.2印制板厚度一般为0.8~2.0mm。
PCB设计参考规范
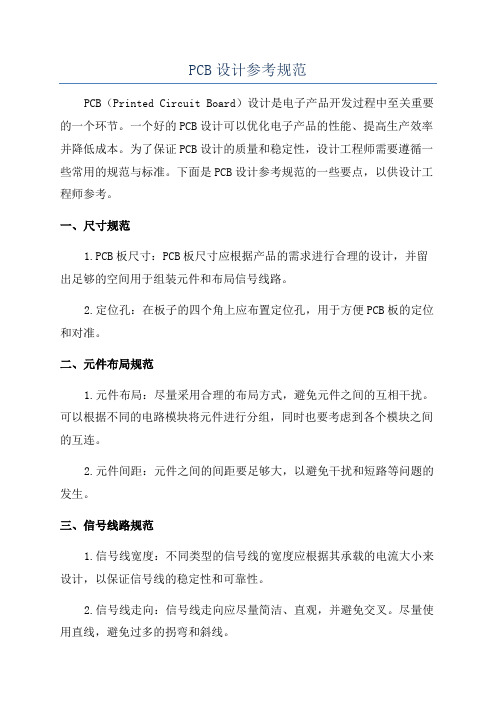
PCB设计参考规范PCB(Printed Circuit Board)设计是电子产品开发过程中至关重要的一个环节。
一个好的PCB设计可以优化电子产品的性能、提高生产效率并降低成本。
为了保证PCB设计的质量和稳定性,设计工程师需要遵循一些常用的规范与标准。
下面是PCB设计参考规范的一些要点,以供设计工程师参考。
一、尺寸规范1.PCB板尺寸:PCB板尺寸应根据产品的需求进行合理的设计,并留出足够的空间用于组装元件和布局信号线路。
2.定位孔:在板子的四个角上应布置定位孔,用于方便PCB板的定位和对准。
二、元件布局规范1.元件布局:尽量采用合理的布局方式,避免元件之间的互相干扰。
可以根据不同的电路模块将元件进行分组,同时也要考虑到各个模块之间的互连。
2.元件间距:元件之间的间距要足够大,以避免干扰和短路等问题的发生。
三、信号线路规范1.信号线宽度:不同类型的信号线的宽度应根据其承载的电流大小来设计,以保证信号线的稳定性和可靠性。
2.信号线走向:信号线走向应尽量简洁、直观,并避免交叉。
尽量使用直线,避免过多的拐弯和斜线。
3.分层布局:合理使用PCB板的多层结构,将功率线和地线分层布局,避免互相干扰。
四、阻抗控制规范1.差分信号的阻抗控制:对于差分信号,其阻抗应尽量保持一致,以避免信号失真和互相干扰。
2.时钟信号的阻抗控制:对于高速时钟信号,应采用特殊的布线方式和阻抗控制,以避免信号抖动和失真。
五、电源和地线规范1.电源线和地线:电源线和地线应采用足够宽的线路来设计,以保证稳定的电源供应和良好的接地。
2.空域分离:电源线和地线应尽量分离,以避免互相干扰。
六、丝印规范1.丝印位置:丝印应放置在元件的旁边或正上方,方便用户查看和识别。
2.字体和标识:使用合适的字体和标识,确保丝印清晰可读。
七、焊盘规范1.焊盘尺寸:焊盘尺寸应根据元件的尺寸来设计,使得焊接过程更加方便和稳定。
2.焊盘间距:焊盘之间的间距应足够大,以便焊接过程中的热量扩散,避免焊接不良。
PCB设计规范(最新版本)

印刷电路板〔PCB〕设计标准一:适用范围:本标准适用于我司CAD设计的所有印刷电路板〔简称:PCB〕二:目的:1. 本标准规定我司PCB设计流程和设计原那么,为PCB设计者提供必须准那么2. 提高PCB设计质量和效率,提高PCB的可生产性,可测性,可维护性。
三:设计任务受理:1. 电子工程师接到上级分配的新产品开发工程时,首先填写?新产品PCB设计进度表?。
然后根据新产品要求完成电路原理图设计,并通过电子组及软件组审核。
2 . 对于设计电路中不常用元件,先通过查公司ERP,如果没有库存,那么需要在第一时间写申购单申请所需元器件,保证新产品开发进度。
3. 要求构造组负责人员提供正确的PCB构造图及3D效果图,在导入构造图过程中须与构造工程师沟通,了解各筋位线分层情况及定位孔位置等等信息。
4. 对于常规产品的设计,那么可根据原有的资料进展LAYOUT,须注意样品单上产品的交期。
四:设计过程:1 创立网络表:1. PCB设计人员根据具体的CAD设计软件创立符合要求的网络表。
2. 确定元器件封装〔PCB FOOTPRINT〕,对于新元件需根据元器件资料制作相应封装。
3. 引入网络表创立PCB板设计文件。
2 元器件布局1. 根据构造图设计板框尺寸,按构造要求定位元器件,并按要求给予尺寸标注。
比方:PCB板厚,PCB的外形尺寸等等。
2. 根据构造图和生产实际要求设计制止布线区。
3. 根据产品要求合理选取板材,定义板层。
4. 布局的根本原那么:a). 按照<先大后小,先难后易,先整体,后局部>的布局原那么,重要的单元电路,核心元器件应优先布局。
b). 布局应参考电原理图,根据信号流向规律按排主要元器件。
c). 布局应尽可能满足:连线尽可能短,高电压,大电流信号线与低电压,小电流信号线完全分开。
d). 板面元器件均匀分布,重心平衡,版面美观的标准优化布局。
5. 布局过程中的元件放置:a). 同类型插装元器件在X或Y方向上应朝一个方向放置,便于生产和检验。
pcb设计的可制造性

可测试性设计
考虑PCB测试的需求,合理规划测试 点和测试结构。
可维护性设计
考虑PCB使用和维护的需求,合理规 划结构和接口。
03
pcb设计的可制造性分析
制造可行性分析
板材选择
根据产品的规格和要求,对不同 的PCB板材进行选择,以满足制 造过程中的刚度、尺寸和可靠性
要求。
制造能力评估
对PCB制造过程中可能遇到的技术 难题和生产能力进行评估,以确保 产品能够顺利生产。
案例四:微小间距连接器的可制造性设计
总结词
微小间距连接器的可制造性设计需要考虑到 连接器的机械性能、电气性能和可靠性等因 素。
详细描述
微小间距连接器的可制造性设计需要考虑到 连接器的机械性能、电气性能和可靠性等因 素。为了实现微小间距和小型化,设计者需 要采用高精度和高可靠性的制造工艺,如激 光焊接、超声波焊接和引线键合等。同时, 还需要进行仿真和测试,以确保连接器的性 能和可靠性。
PCB的组成
导电路径(线路)、导电图形(焊盘、元件引脚 )、绝缘基材(FR4、CEM-1等)。
3
PCB的分类
单面板、双面板、多层板。
pcb设计流程
设计规划
根据需求进行总体设计和规划 ,包括布局、布线等。
制作PCB
将原理图转化为PCB图,并进 行布局和布线。
需求分析
明确设计需求,包括功能、性 能、成本等。
风险评估
对制造过程中可能出现的质量风险 、交货风险等进行评估,并提出相 应的应对措施。
制造流程分析
流程规划
根据产品需求和制造能力,制定 合理的PCB制造流程,包括材料 采购、前处理、制作、后处理等
环节。
流程优化
通过对制造流程进行优化,提高 生产效率和产品质量,降低生产
ipc pcb设计标准

ipc pcb设计标准一、概述IPC-PBCB设计标准是工业电子委员会(IPC)为印刷电路板(PCB)设计制定的标准规范。
该标准旨在提供一套适用于各种电子设备制造商的通用设计原则和指导,以确保PCB设计的可靠性和可制造性。
二、设计原则1. 功能性原则:PCB设计应符合设备的功能需求,确保电路正常工作。
2. 可靠性原则:应采取适当的防护措施,防止电气干扰和机械应力对电路的影响,确保电路的稳定性和使用寿命。
3. 可维护性原则:设计应考虑维修和调试的方便性,便于故障诊断和修复。
4. 可制造性原则:PCB制造应易于实现,减少不必要的加工步骤和材料浪费,降低生产成本。
三、设计要求1. 布局要求:a. 按照功能模块进行布局,确保电路间的信号传输顺畅。
b. 避免布线之间的电磁干扰,减少电路间的串扰。
c. 遵循电源线和地线的规则,确保电气隔离。
2. 尺寸要求:a. 使用的导线宽度和间距应符合IPC标准,确保电路的电气性能。
b. PCB尺寸应符合设备制造商的要求,以适应设备的尺寸和结构。
3. 元器件选择:a. 应选择具有可靠性能和低成本的元器件,以降低生产成本。
b. 应考虑元器件的可制造性和可维护性,选择易于采购和更换的型号。
4. 焊接要求:a. 应采用适当的焊接方法,如波峰焊或回流焊,以确保焊接质量。
b. 应考虑焊接后的热应力对PCB的影响,采取适当的散热措施。
四、设计流程1. 需求分析:明确设备的功能和性能要求,确定PCB的功能和结构。
2. 布局设计:根据功能模块进行布局规划,确定元器件的位置。
3. 布线设计:根据信号传输要求进行布线设计,确保电路间的信号传输顺畅。
4. 验证与测试:对设计进行验证和测试,确保电路的正确性和稳定性。
5. 可制造性优化:根据可制造性原则,对设计进行优化,减少制造难度。
6. 出图与生产:将设计结果输出为生产所需的文件,交付给制造部门进行生产。
五、注意事项1. 应遵循IPC-PBCB设计标准的所有规定,确保设计的合规性。
公司PCB设计规范

公司PCB设计规范PCB设计规范是现代电路设计的重要组成部分,它对保证电路的品质、生产效率和设计成本等方面具有重要的作用。
为了确保公司生产的PCB设计符合规范要求,我们需要建立一套完整的PCB设计规范。
一、规范的内容PCB设计规范应包括以下内容:1.设计固定参数:包括PCB厚度、金属化孔壁厚度、印刷电路板(PCB)尺寸、焊盘间距、引脚排列等。
这些参数对于设计电路的尺寸和布局非常重要,需要在设计前定义清楚。
2.热量和尺寸限制:PCB设计需要考虑热量传递和排放,尤其是在高压和高频电路中,需要特别注意。
因此,在规范中需要约定热量和尺寸的限制条件,以确保设计符合实际需求。
3.层级规定:在PCB设计中,常常会涉及到不同电路层的设计和布局,这时需要约定不同电路层的名称和编号,并定义所在电路板的顺序、颜色、布线等等。
4.标称值和偏差规定:在PCB设计中,各元件的标称值和偏差会对设计造成很大影响,因此需要定义各元件的标称值和偏差范围。
5.重点部分的细节规定:对于设计中一些比较特殊的部分,如高压射频、高速信号传输等,需要定义设计的参数和限制。
这些细节规定有助于确保重点部分的设计符合实际要求。
二、规范的实施为了确保规范的有效实施,公司需要建立相应的管理体系。
具体措施如下:1.明确责任:规范的实施需要有明确的责任人。
由部门主管或生产管理人员负责制定规范,并确定实施的计划和步骤。
2.培训和普及:为了让所有参与设计的人员能够理解和遵守规范,公司需要开展相应的培训和普及工作。
可以通过内部培训、讲座、技术交流等方式进行普及,让人员了解和掌握规范的要求。
3.监督检查:在实施过程中需要对设计文档进行监督检查,确保设计符合规范。
监督检查的方式可以通过审核、抽查等,查出不符合规范要求的设计文档,及时进行改正。
4.完善修改:规范随着技术和工艺的变化而不断完善,一旦有新的要求和调整,需要及时进行修改和更新,确保规范与实际情况相符。
三、规范带来的好处1.提高生产效率:规范可以固定设计参数和部分设计细节,减少重复设计、修改和排版,同时通过提高设计的质量,减少产生错误、漏洞和灾难的概率,从而提高生产效率。
PCB工艺流程和可制造性设计

前言:可制造性设计DFM(Design ForManufacture)是保证质量的最有效的方法。
DFM就是从产品开发设计时起,就考虑到可制造性和可测试性,使设计和制造之间紧密联系,实现从设计到制造一次成功的目的。
DFM具有缩短开发周期、降低成本、提高产品质量等优点,是企业产品取得成功的途径。
HP公司DFM统计调查表明:产品总成本60%取决于产品的最初设计,75%的制造成本取决于设计说明和设计规范,70-80%的生产缺陷是由于设计原因造成的。
一、PCB简介及工艺流程二、可制造性设计2.1.多层板叠层设计可靠性通常PP介质厚度的设计不要低于80um,介质太薄耐压性相应减弱,可能会出现电击穿的现象。
不同材料的PCB产品,其介质层耐电压能力情况如下表:序号介质层材料类型耐电压能力/(V/mil)1环氧树脂材料5002陶瓷材料7003BT材料10004PI材料1000对称性多层板叠层设计不论从叠层材料厚度(板材、PP、铜箔)还是布线设计(信号层、电源层、地层)、钻孔设计均需保证对称性,以避免PCB翘曲钻带设计对称:盲孔设计时,避免不对称结构设计线路图形分布的对称:处于对称结构位置的线路层,图形面积不能差距太大,如6层板,1层和6层,2层和5层分别处于对称结构的位置,同张芯板两面图形面积不能差距太大,否则很容易导致板弯曲超标,影响贴片(如遇到如下图所示的情况,可在图2空旷区域铺上铜,减少图形面积的差异)。
其他(多层板叠层厚度设计)普通多层板叠层厚度应该比成品厚度小0.1mm(如下图示),因层压后还需要电镀、印刷绿油等,会增加板厚。
2.2.钻孔设计最小钻咀及孔径公差(孔直径小于6.3mm的孔)机械钻孔的最小钻咀:0.15mmPTH孔公差:插件孔:常规+/-4mil(非常规可做到+/-3mil )压接孔:+/-2milNPTH孔公差:+/-2mil孔径纵横比纵横比(如下图示):纵横比过大,在沉铜工序或电镀工序药水在孔内交换困难,会产生薄铜或局部缺铜,影响产品可靠性。
PCB设计规范大全

PCB设计规范大全PCB设计规范大全1,目的规范印制电路板(以下简称PCB)设计流程和设计原则,提高PCB设计质量和设计效率,保证PCB 的可制造性、可测试、可维护性。
2,范围所有PCB 均适用。
3,名词定义3.1原理图:电路原理图,用原理图设计工具绘制的、表达硬件电路中各种器件之间的连接关系的图。
3.2网络表:由原理图设计工具自动生成的、表达元器件电气连接关系的文本文件,一般包含元器件封装、网络列表和属性定义等组成部分。
3.3布局:PCB 设计过程中,按照设计要求,把元器件放置到板上的过程。
3.4模拟:在器件的IBIS MODEL 或SPICE MODEL 支持下,利用EDA 设计工具对PCB 的布局、布线效果进行模拟分析,从而在单板的物理实现之前发现设计中存在的EMC 问题、时序问题和信号完整性问题,并找出适当的解决方案。
3.5 SDRAM :SDRAM 是Synchronous Dynamic Random Access Memory(同步动态随机内存)的简称,同步是指时钟频率与CPU 前端总线的系统时钟频率相同,并且内部的命令的发送数据和数据的传输都以它为准;动态是指存储数组需要不断刷新来保证数据不丢失;随机是指数据不是线性一次存储,而是自由指定地址进行数据的读写。
3.6 DDR :DDR SDRAM 全称为Double Data Rate SDRAM ,DDR SDRAM 在原有的SDRAM 基础上改进而来。
DDR SDRAM 可在一个时钟周期内传送两次数据。
3.7 RDRAM :RDRAM 是Rambus 公司开发的具有系统带宽的新型DRAM ,它能在很高的频率范围内通过一个简单的总线传输数据。
RDRAM 更像是系统级的设计,它包括下面三个关键部分:3.7.1 基于DRAM 的Rambus(RDRAM );3.7.2 Rambus ASIC cells (专用集成电路单元);3.7.3 内部互连的电路,称为Rambus Channel(Rambus 通道);3.8 容性耦合:即电场耦合,引发耦合电流,干扰源上的电压变化在被干扰对象上引起感应电流而导致电磁干扰。
手机PCB设计可制作性规范(DFM)

手机及模块PCB设计可制作性工艺规范(DFM)术语1. PCB(Printed Circuit Board) :指印制板电路2. SMT(Surface Mounting Technology):表面贴装技术,指用自动贴装设备将表面组装元件/器件贴装到PCB 表面规定位置的一种电子装联技术。
3.DFM(Design for manufacturability ):可制造性设计。
4. 回流焊(Reflow Soldering):是指事先把焊膏涂敷在PCB焊盘上,通过回流焊炉加热焊接的焊接方式。
5. 基准Mark (FIDUCIAL MARK) :SMT设备为了辨认、补正基板或部品的坐标而使用的焊盘。
统计调查表明: 产品总成本60%取决于产品的最初设计;75%的制造成本取决于设计说明和设计规范;70-80%的生产缺陷是由于设计原因造成的。
意义和目的DFM就是从产品开发设计时起,就考虑到可制造性和可测试性,使设计和制造之间紧密联系,实现从设计到制造一次成功的目的。
DFM具有缩短开发周期、降低成本、提高产品质量等优点,是企业产品取得成功的途径。
原则DFM基本规范中涵盖下文提到的“PCB设计的工艺要求”、“PCB 焊盘设计的工艺要求”、“屏蔽盖设计”三部分内容为R&D Layout 时必须遵守的事项,否则SMT或割板时无法生产。
DFM建议或推荐的规范为制造单位为提升产品良率,建议 R&D在设计阶段加入PCB Layout。
零件选用建议规范: Connector零件应用逐渐广泛, 又是 SMT生产时是偏移及置件不良的主因,故制造希望R&D及采购在购买异形零件时能顾虑制造的需求, 提高自动贴片的比例。
主要内容一、不良设计在SMT制造中产生的危害二、目前SMT印制电路板设计中的常见问题及解决措施三、PCB设计的工艺要求四、PCB焊盘设计的工艺要求五、屏蔽盖设计一. 不良设计在SMT生产制造中的危害1. 造成大量焊接缺陷。
- 1、下载文档前请自行甄别文档内容的完整性,平台不提供额外的编辑、内容补充、找答案等附加服务。
- 2、"仅部分预览"的文档,不可在线预览部分如存在完整性等问题,可反馈申请退款(可完整预览的文档不适用该条件!)。
- 3、如文档侵犯您的权益,请联系客服反馈,我们会尽快为您处理(人工客服工作时间:9:00-18:30)。
1.概况1.1本规范的内容是确保所设计之PCB符合相关标准及实际生产,以降低生产之困惑,使制程生产顺畅.1.2主要生产设备有:锡膏印刷机、贴片机、回流焊炉、AOI自动检验机、波峰焊.2.PCB外形、尺寸及其他要求:2.1 PCB外形应为长方形或正方形,如PCB外形不规则,可通过拼板方式或在PCB的长方向加宽度不小于8mm的工艺边。
PCB的长宽比以避免超过2.5为宜。
2.2 SMT生产线可正常加工的PCB外形尺寸最小为50mm×50mm(长×宽)。
最大尺寸因受现有设备的如下表限制.因此PCB(拼板)外形尺寸(长×宽)正常不宜超过450mm×380mm。
如果由于设计确实需要超过此尺寸,制板时请通知工艺人员协商确定生产方案。
各设备可加工的最大PCB尺寸及设备夹持长度见下表:(单位:mm)2.3拼板及工艺边:2.3.1 何种情况下PCB需要采用拼板:当PCB外形尺寸有如下的特征之一时需考虑采用拼板:(1)SMT板长<120mm或直插件板长<80mm;(2)SMT板宽<50mm或直插件板宽<80mm;(3)基标点的最大距离<100mm;(4)板上元件较少(少于180个元件)拼板后板的长宽不会超出350mm×245mm时。
采用拼板将便于定位贴装及提高生产效率。
2.3.2 拼板的方法:为了减少拼板的总面积节约PCB的成本,板与板之间一般不留间距(采用板边缘线重叠零间距);拼板时一般是以板的长边互拼,或长短边同时互拼的方式进行,但应避免拼板后板的长宽比超过2.5为宜。
拼板一般采用V-CUT方法进行。
工艺边同样采用此方法与板连接。
对于焊接面只有阻容器件或较简单的SOP封装IC时,双面均是表贴件的PCB可采用正反拼(阴阳拼板)的双面SMT工艺,但对于双面均有精密元器件或有较大体积元器件的板,则不宜采用正反拼(阴阳拼板)工艺。
拼板在订制PCB及网板时一定要注明统一的拼板方式及各单板的精确相对位置尺寸,如板与板之间的间距为零时是以板的边缘线重叠或是以板的边缘线紧靠来确定相对位置的,一般在没有特别说明的的情况下是以板边缘线重叠作为默认值的。
2.3.3 何种情况下PCB需要增加工艺边:当PCB有如下的特征之一时应增加工艺边:[1]PCB的外形不规则难以定位;[2]在定位用的边上元件(包括焊盘和元件体)距离板边缘太小(SMT板的元件面<5mm或焊接面<8mm,直插件<8mm),造成流板时轨道刮碰到元件;[3]板上布有引线间距≤0.65mm的IC或≤0603(英制)规格的片状元器件但没有PCB所要求的标准定位孔。
2.3.4 增加工艺边的方法:工艺边增加是为了PCB 在生产时能得到准确的定位,一般是加在(拼)板的较长边上,由于它的增加直接影响了PCB 的成本,因而在保证满足使用功能时尽可能减小工艺边的尺寸以节约成本,而要满足准确定位的要求一般是要求能够在工艺边上得到标准的定位孔,从下面的图中可以看到,得到标准定位孔的工艺边应不小于8mm 的宽度,长度一般是与(拼)板的边长一致。
(下图是异形双面表贴板的同面双拼外加工艺边示意图)2.3.5带工艺边的拼板中V-CUT 连接特别说明:带有工艺边的拼板,如果工艺边已将各板连接固定好,那拼板之间如果是零间距时可采用V-CUT 切断连接(如上图),省去后续的割板工序,但如果厂家做不到切断,可留一点连接而不完全切断,用手瓣断时不致造成弯曲变形,但切不可将连接用的工艺边也切断!另外,对于单板尺寸的长宽比大于2的板,由于切断后单板的稳定性明显变差,所以此时不宜将板间的连接切断!为防止印制板在生产过程中变形(如贴片/回流/插件/波峰时),垂直于生产流向的工艺边上尽量避免开V-CUT 槽或邮票孔。
如下图:PCB 外形要求:PCB 板基板边缘不能有缺口且不能断开,确保流水线各设备轨道加卸载的顺利进行。
而且,若有大缺口,则在生产过程、焊接过程、周转过程都容易变形,影响焊接可靠性(含出厂后)。
生产流向好的设计 图一不好的设计 图二2.3.6 异形板的工艺边的邮票孔要求:有些异形板由于本身的形状会影响定位的准确及稳定性,因此在不影响印制板成本的情况下应将板的缺口补齐成方形,补缺口一般是采用邮票孔结合长孔的连接方式,邮票孔连接的方式应该考虑掰板后的毛刺是凹陷在板边缘内(通过将邮票孔位放在板边缘线内侧),以减少掰板后修边的动作。
如果生产中不会影响板的定位及稳定性,就不要补齐缺口。
如果无法确定可由工艺人员决定方案。
附:邮票孔的使用规则:孔完全内嵌PCB板,即孔圆内切板边(除非有特别要求板的边缘必须非常平齐);每处邮票桥接的连接宽度一般5mm-10mm(据PCB板的受力情况及板尺寸而定),即孔内径0.6mm-0.7mm,孔中心距1.0mm,桥接外延左右处各加两个引孔(以除去连接处两边毛刺,如下图红色孔),桥接共5-10个孔(含2个引孔);若定位孔在工艺边上,则定位孔所在工艺边要求较大的邮票连接强度;邮票桥一般要求远离PCB的折角边处;邮票桥不能在元件体下(如外露接口器件);桥接处两边并不是都要打孔,若所桥接的是无电路作用的工艺边,则工艺边上的桥接处不需要邮票孔。
示例:2.4 PCB 安装定位孔尺寸要求: 2.4.1 表贴定位孔尺寸要求:至少要二个定位孔(在定位边方向,一般为长边),两个定位孔位置尺寸要求如下图。
直径要求统一为3.3mm (包括在工艺边上的定位孔也统一为3.3mm)。
定位孔不能金属化。
在定位孔外围1mm 范围内不允许有SMT 元件,5mm 范围内不能有基标点。
另注:板上螺丝孔直径也请统一为3.3mm 。
(有时需要螺丝孔兼作定位孔)。
定位孔和螺丝孔请统一制作成器件封装形式。
2.4.2 表贴锡膏印刷定位孔尺寸要求:在板四个角,分布四个孔。
直径要求Φ3.3mm 。
(四个孔直径要保持相同)。
这四个孔的位置不作精确要求。
其中底边两个孔也可用定位孔代替(定位孔兼作此孔),直径要一致。
(定位孔不能金属化)2.4.3 过炉支撑孔要求(防止板变形):若板的长度超过250mm ,则在板长方向的大约中央线上 约等长地分布两个孔(非金属化),直径要求Φ3mm 。
但孔位置不必非常精确要求。
但属于同系列的PCB 板产品,此两个孔位置在此系列PCB 上要保持相同。
Φ3.30mm流板方向流板方向5±0.055±0.05Φ3.30mm ±0.05表贴定位孔要求:1、 直径3.3mm2、 两边距5mm3、 周禁1mm 无SMD 元件 4、 周禁5mm 无MARK 点2.5 基标(Fiducial Mark )尺寸要求:基标分为PCB 基标和细间距IC 基标。
基标的中心为Φ1.0mm 的镀锡平面,全反光性好,外围Φ3.0mm 内无反光(无铜箔、绿油或白油);PCB 的基标至少要有两点,最好在板的四个角上均有基标点,但注意不要作在对称的位置上(防止生产反向流板)。
板上应有两个基标点的距离大于100mm ,达不到要求的应做成拼板;如果是双面均有表贴元件,则两面均应布基标。
细间距IC 基标可分布在IC 的任意两对角上,但最好设计为IC 位置的中心一点为好。
所有板面上基标点的中心点距离板边缘均应大于5mm ,距离定位孔也要大于5mm 。
注意:基标点统一制作成器件封装形式,即要有自身封装对应的位号(Ref 名),以便于准确定位坐标。
3.SMC/SMD 封装代号的一般识别:3.1 片状阻容元器件外形代号及其尺寸(长×宽):3.2 MELF 、MLL 、SOD 元件为类似圆柱形的器件,如二级管。
3.3 SOT 元件为类似三级管的元件 3.4 SOP 为两侧有引脚朝外的IC 3.5 SOJ 为两侧有引脚朝内的IC 3.6 PLCC 为四面有引脚朝内的IC 3.7 QFP 为四面有引脚朝外的IC 3.8 BGA 是以球栅阵列为引线的IC焊盘在PCB 上的排布设计原则:PCB 排版时需考虑板卡的可生产操作性,为了尽早发现可能存在的布板问题,避免造成投产后的再次改板,因此在订制PCB 板前需由板卡工艺人员确认一下。
3.9相临元件焊盘的间距极限如下图:但对于插件较多的双面表贴板,因波峰焊接表贴件受到许多方面的限制,因此双面表贴件通常均采用回流焊接,焊接面的表贴件在波峰焊接前采用夹具或阻焊带屏蔽掉,故焊接面的表贴件与插焊孔边缘之间的间距须在3mm 以上(对于1206及以上的表贴元件与插焊孔边缘之间的间距须在5mm 以上),若焊接面的表贴元件高度超过5mm,则一般以表贴件的高度尺寸为上述的最小间距要求。
焊接面的表贴件最好集中排布,特别是不要分散排布在插件孔之间。
SMD尽量能够移到Top元件面。
反面元件不多的产品尽量改为单面表贴板,以减少生产流程。
3.10特殊yy类高端产品的阻容元件,因性能要求所限,表贴阻容间的间距若实在无法达3.11SMD焊盘与通孔最小空隙距6mil即SMT焊盘边缘距过孔(塞绿油)的最小距离为6m il,最佳0.5mm以上,焊盘与通孔之间须有阻焊膜覆盖。
焊盘表面严禁有通孔,以避免焊料流失造成虚焊。
通孔与焊盘的连接线的宽度小于0.25mm并且小于焊盘宽度或直径的1/2。
3.12距PCB长边或定位边(即不带露出板边缘插座的边及对边)5mm内不应有焊盘和基标,双面表贴板的焊接面则应有8mm的范围无焊盘。
3.13元件排布及焊盘设计应考虑方位及对称性,方向一致性为最佳,体积大的元件应尽可能排在PCB中间,特别是波峰焊接面Bootom面更应该考虑元件排布的方位,以免在波峰焊时产生阴影效应造成难以克服的焊接缺陷,同时应避免排布间距小于1mm的IC,Bottom面表矩形元件焊盘严禁设计为尺寸大小不等的不对称的焊盘图形。
焊盘之间、焊盘与通孔以及焊盘与大面积接地(或屏蔽)铜铂之间的连线,其长度尽量大于0.5mm,其宽度须小于0.25mm并且应小于其中较小的焊盘宽度或直径的1/2。
细间距IC引线焊盘之间如没有涂覆绿油,其焊盘之间严禁直接用短接线相连,须用引出线在外连接并覆盖绿油。
无外引脚的元件的焊盘之间不允许有通孔,以保证焊接质量。
各导通孔在没有特别要求的情况下均应涂覆绿油。
3.14查选焊盘设计尺寸时,应与自己所选用的元件封装外形、焊端、引脚等与焊接相关的尺寸相匹配、尺寸单位(公英制),同一面的IC本体之下不能布其他元器件,焊接片状元件的焊盘绝不允许兼作测试点,为避免损坏器件必须另外设计专用的测试焊盘。
4无外引线元器件焊盘尺寸设计原则:4.1 常用矩形阻容元件焊盘尺寸(此类元件易出现偏移、虚焊和一端立起)如下表:由于小元件的焊盘尺寸对焊接质量的影响较大,不同的焊接方式(SMT回流焊接和波峰焊接)要求不同,在布板时一定要注意区分清楚!通常情况下焊接面的表贴件如果较多且相对集中,一般采用双面回流焊接方式,只有焊接面的表贴件与插焊点距离较小且混排在一块时才考虑采用波峰焊接方式。