铝镍钴工艺流程[1]
01.铝镍钴磁铁简介02.铝镍钴磁铁生产工艺

01.铝镍钴磁铁简介铝镍钴永磁体:是由金属铝、镍、钴、铁和其它微量元素构成的一种合金。
铝镍钴永磁体有两种不同的生产工艺:铸造和烧结。
铸造工艺可以加工生产成不同的尺寸和形状;与铸造工艺相比,烧结产品局限于小的尺寸,其生产出来的毛坯尺寸公差比铸造产品毛坯要好,磁性能略低于铸造产品,但可加工性要好。
铝镍钴具有很强的抗锈蚀能力,表面不需要进行电镀处理。
铸造铝镍钴CAST ALNICO配料01Mixing熔炼02Melting浇铸03Modeling热处理04Heat Treatment性能检测05Testing机械加工06Cutting&Grinding检验07Inspection包装08Packing交货09Delivery售后服务10After-sale service烧结铝镍钴SINTERED ALNICO配料熔炼制粉压制烧结热处理010605020304MixingMeltingPowder ProductionPressingSinteringHeat Treatmen性能检测07Testing机械加工08Cutting&Grinding检验09Inspection包装10Packing交货1112Delivery售后服务After-sale Service02.铝镍钴磁铁生产工艺牌号 (Grade)美国标准(AmericanStandard)剩磁Br矫顽力Hcb最大磁能积(BH)max密度可逆温度系数可逆温度系数居里温度TC最高工作温度TW备注mT Gs KA/m Oe KJ/m³MGOe 6.9%/℃%/℃℃℃LN10ALNICO360060004050010 1.27.2-0.03-0.02810450LNGT18ALNICO85805800100125018 2.27.3-0.025+0.02860550 LNG40ALNICO5125012500486004057.3-0.02+0.02850525 LNG52ALNICO5DG1300130005670052 6.57.3-0.02+0.02850525 LNGT28ALNICO610001000057.672028 3.57.3-0.02+0.03850525 LNGT38ALNICO88008000110138038 4.757.3-0.025+0.02860550 LNGT60ALNICO995095001101380607.57.3-0.025+0.02860550各向同性LNG13ALNICO270070004860012.8 1.67.3-0.03+0.02810450 LNG37ALNICO51200120004860044 4.657.3-0.02+0.02850525 LNG44ALNICO51250125005265037 5.57.3-0.02+0.02850525 LNG60ALNICO5-713501350059740607.57.3-0.02+0.02850525LNGT36J ALNICO8HC7007000140175036 4.57.3-0.025+0.02860550 LNGT40ALNICO8820820011013804057.3-0.025+0.02860550 LNGT72ALNICO910501050011214007297.3-0.025+0.02860550各向异性03.铝镍钴磁铁性能明细。
烧结铝镍钴

烧结铝镍钴摘要:1.烧结铝镍钴的定义和特性2.烧结铝镍钴的生产工艺3.烧结铝镍钴的应用领域4.烧结铝镍钴的发展趋势和前景正文:烧结铝镍钴(Sintering Aluminum Nickel Cobalt)是一种具有高强度、高硬度、高耐磨性和高耐腐蚀性的金属材料。
它主要由铝、镍、钴三种金属元素组成,通过烧结工艺制成。
在许多工业领域中,烧结铝镍钴因其优异的性能而受到广泛关注和应用。
1.烧结铝镍钴的定义和特性烧结铝镍钴是一种粉末冶金材料,通过将铝、镍、钴金属粉末混合,并在高温条件下进行烧结而制成。
这种材料具有高密度、高强度、高硬度、高耐磨性和高耐腐蚀性等特点。
烧结铝镍钴的主要成分是铝、镍和钴,其中铝起到提高强度和硬度的作用,镍增加耐磨性,钴则提高耐腐蚀性。
2.烧结铝镍钴的生产工艺烧结铝镍钴的生产工艺主要包括原料准备、混合、成型、烧结和后处理等步骤。
首先,将铝、镍、钴金属粉末按照一定的比例混合,然后通过压制或注射成型等方式制成所需形状的坯件。
接着,将坯件放入高温炉中进行烧结,使其形成致密的结构。
最后,对烧结后的产品进行冷却、破碎、研磨等后处理,以满足实际应用需求。
3.烧结铝镍钴的应用领域烧结铝镍钴广泛应用于各种工业领域,如汽车、航空航天、化工、电子等。
在汽车工业中,烧结铝镍钴常用于制造发动机零件、传动部件等,以提高汽车的性能和寿命。
在航空航天领域,烧结铝镍钴被用于制造涡轮叶片、轴承等高温、高压部件。
此外,在化工、电子等产业中,烧结铝镍钴也发挥着重要作用。
4.烧结铝镍钴的发展趋势和前景随着科技的进步和工业的发展,对材料性能的要求越来越高。
烧结铝镍钴作为一种高性能金属材料,其市场需求不断增长。
未来,烧结铝镍钴的发展趋势主要表现在以下几个方面:(1)优化材料成分和工艺,进一步提高性能;(2)拓展应用领域,开发新型产品和终端应用;(3)研究环保、可持续的生产方法,降低能耗和环境污染。
镍钴矿的生产工艺与流程设计
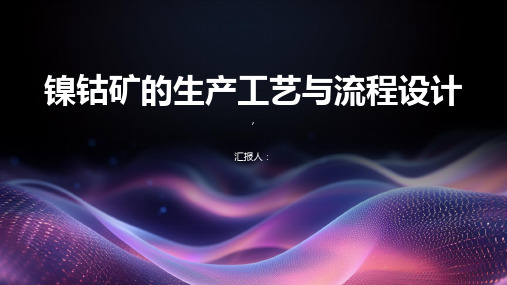
爆破法:适用于矿石坚硬、开采难度大的情况
钻探法:适用于勘探阶段,获取地质信息
选矿流程
矿石破碎:将矿石破碎至合适粒度,便于后续处理
添加标题
磨矿:将破碎后的矿石磨成细粉,提高后续选矿效率
添加标题
选别:根据矿石中镍钴矿与其他矿物的性质差异,采用合适的选矿方法进行选别
案例分析结果
案例背景:某镍钴矿生产企业的生产工艺与流程设计
生产工艺:包括矿石破碎、磨矿、选矿、冶炼等步骤
流程设计:根据矿石特性和生产需求,设计合理的生产流程
案例分析:通过对生产工艺和流程设计的分析,提出改进措施和建议,以提高生产效率和产品质量
案例经验总结
01
案例背景:某镍钴矿生产企业的生产工艺与流程设计
04
02
03
生产工艺:湿法冶金、火法冶金、氢还原等
流程设计:矿石破碎、磨矿、选矿、冶炼等
案例分析:生产效率、成本控制、环保措施等方面的分析
05
经验总结:优化生产工艺、提高生产效率、降低成本、加强环保等方面的经验总结
感谢观看
汇报人:
磨矿机:用于磨碎矿石,使有用矿物与脉石分离
破碎机:用于破碎矿石,提高选矿效率
选矿技术
浮选法:利用矿物表面的物理化学性质差异进行分离
磁选法:利用矿物磁性差异进行分离
重选法:利用矿物密度差异进行分离
化学选矿法:利用矿物化学性质差异进行分离
联合选矿法:结合多种选矿方法进行分离
选矿工艺优化:提高选矿效率,降低成本和环境影响
膜分离法:利用膜分离技术将镍钴矿中的金属离子分离出来
离子交换法:利用离子交换树脂将镍钴矿中的金属离子交换出来
铝镍钴磁铁工艺流程

铝镍钴磁铁工艺流程下载温馨提示:该文档是我店铺精心编制而成,希望大家下载以后,能够帮助大家解决实际的问题。
文档下载后可定制随意修改,请根据实际需要进行相应的调整和使用,谢谢!并且,本店铺为大家提供各种各样类型的实用资料,如教育随笔、日记赏析、句子摘抄、古诗大全、经典美文、话题作文、工作总结、词语解析、文案摘录、其他资料等等,如想了解不同资料格式和写法,敬请关注!Download tips: This document is carefully compiled by theeditor. I hope that after you download them,they can help yousolve practical problems. The document can be customized andmodified after downloading,please adjust and use it according toactual needs, thank you!In addition, our shop provides you with various types ofpractical materials,such as educational essays, diaryappreciation,sentence excerpts,ancient poems,classic articles,topic composition,work summary,word parsing,copy excerpts,other materials and so on,want to know different data formats andwriting methods,please pay attention!1. 配料:根据产品要求,将铝、镍、钴等原材料按一定比例进行配料。
烧结铝镍钴

烧结铝镍钴摘要:一、烧结铝镍钴的概述二、烧结铝镍钴的制备工艺三、烧结铝镍钴的性能与应用四、烧结铝镍钴的前景与发展趋势正文:一、烧结铝镍钴的概述烧结铝镍钴(Sintering AlNiCo)是一种高性能的硬质、高磁导率磁性材料。
它主要由铝(Al)、镍(Ni)、钴(Co)等元素组成,具有优良的磁性能、机械性能和化学稳定性。
在众多领域中,烧结铝镍钴都有着广泛的应用,如电机、磁性传感器、磁力矫治器等。
二、烧结铝镍钴的制备工艺1.配料:根据所需的铝镍钴成分,精确称取相应的铝、镍、钴等金属粉末。
2.混合:将称取的金属粉末进行充分混合,以确保成分均匀。
3.预烧:将混合好的粉末进行预烧,使其部分熔化并结合。
4.压制:将预烧后的粉末压制成所需的形状,如圆柱形、片状等。
5.烧结:将压制好的坯件放入高温炉中,进行烧结。
烧结过程中,铝镍钴粉末颗粒间的结合强度逐渐提高,形成致密的铝镍钴固体。
6.冷却:烧结完成后,将制品缓慢冷却至室温。
7.后处理:根据需要,对烧结铝镍钴制品进行切割、磨光等后处理。
三、烧结铝镍钴的性能与应用烧结铝镍钴具有以下优良性能:1.高磁导率:在磁场作用下,烧结铝镍钴具有较高的磁导率,能有效地传递和放大磁场信号。
2.高硬度:烧结铝镍钴具有较高的硬度,使其在磨损和腐蚀环境下具有较好的耐久性。
3.优良的磁稳定性:烧结铝镍钴在高温、高压等条件下,仍能保持稳定的磁性能。
4.良好的抗磁干扰性能:烧结铝镍钴对磁干扰具有较强的抵抗能力,使其在磁性传感器等应用中具有较高的准确性。
5.环保性能:铝镍钴材料不含铅、汞等有害物质,有利于环境保护。
烧结铝镍钴在以下领域中有广泛应用:1.电机:作为电机转子、定子等关键部件,具有高效、节能、高扭矩等特点。
2.磁性传感器:用于磁力测量、磁性识别、磁场检测等场合,具有高灵敏度、高精度、抗干扰能力强等优点。
3.磁力矫治器:用于口腔、骨科等磁力矫治领域,具有治疗效果好、损伤小等优势。
4.磁性密封件:用于磁性轴承、磁性密封等场合,具有优良的密封性能和抗磨损性能。
铸造铝镍钴工艺

铸造铝镍钴工艺铸造铝镍钴工艺是一种先进的金属加工技术,主要应用于制造高性能的航空发动机、火箭发动机、船舶螺旋桨等高强度、高温、耐腐蚀的零部件。
本文将从工艺流程、材料选择、设备要求等方面详细介绍铸造铝镍钴工艺。
一、工艺流程1.模具制作:根据零部件图纸设计出模具,然后进行加工和组装成完整的模具。
2.熔炼合金:将所需合金材料按比例放入电弧炉中熔化,然后进行除气处理,确保合金质量。
3.浇注成型:将熔化的合金倒入预先准备好的模具中,待其冷却凝固后取出零部件。
4.去毛刺处理:对于表面有毛刺或其他缺陷的零部件,需要进行去毛刺处理以提高表面质量。
5.热处理:对于需要提高材料强度和耐腐蚀性能的零部件,需要进行适当的热处理。
6.检验和包装:对于每个生产出来的零部件进行检验,合格后进行包装。
二、材料选择铝镍钴合金是一种高性能的金属材料,其具有高强度、高温、耐腐蚀等优良性能。
在铸造铝镍钴工艺中,常用的合金材料包括IN738LC、IN792、IN713C等。
IN738LC是一种镍基高温合金,具有优异的耐热性和耐腐蚀性能,主要应用于制造航空发动机和火箭发动机等高温零部件。
IN792是一种镍基超合金,具有优异的高温强度和抗氧化性能,主要应用于制造船舶螺旋桨等零部件。
IN713C是一种铝镍钴基合金,具有较好的耐热性和抗氧化性能,主要应用于制造汽车涡轮增压器等零部件。
三、设备要求铸造铝镍钴工艺需要使用先进的设备来保证生产质量和效率。
常用的设备包括电弧炉、真空熔炼炉、模具加工设备、去毛刺设备、热处理设备等。
电弧炉是将合金材料加热至熔化温度的主要设备,其可以通过控制电流、电压和时间等参数来实现合金材料的熔化和除气处理。
真空熔炼炉是一种特殊的电弧炉,其可以在真空环境下进行合金材料的熔化和除气处理,以保证合金材料质量。
模具加工设备包括数控机床、铣床、钻床等,用于制作零部件模具。
去毛刺设备可以对表面有毛刺或其他缺陷的零部件进行去毛刺处理,以提高表面质量。
锂镍钴的提取工艺流程

锂镍钴的提取工艺流程
锂、镍、钴的提取工艺流程各异,但通常涉及以下步骤:
1. 锂提取:主要来源于锂辉石、锂云母等矿物,采用硫酸法或石灰石烧结法预先处理,然后通过酸溶、沉淀、蒸发结晶等步骤提取硫酸锂,进一步通过电解法制备金属锂。
2. 镍提取:常见于硫化镍矿中,首先通过破碎、磨矿预处理,然后采用浮选法富集镍矿石,接着通过硫酸化焙烧、浸出、净化、电积等一系列湿法冶金工艺提取纯镍。
3. 钴提取:钴通常伴生于镍、铜矿石中,首先通过化学浸出(如硫酸浸出)提取钴离子,然后通过沉淀、萃取、电积等步骤分离纯化得到钴产品。
废旧电池回收中,可通过破碎、酸浸、萃取等工艺提取其中的钴。
典型的铝及铝合金化学镀镍的工艺
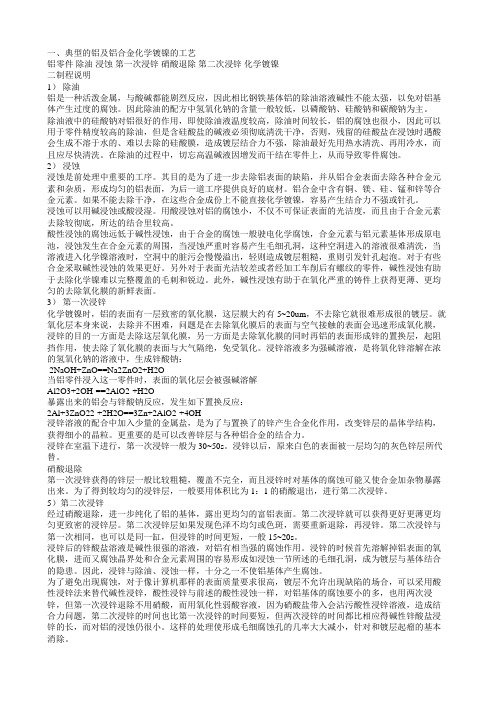
一、典型的铝及铝合金化学镀镍的工艺铝零件除油浸蚀第一次浸锌硝酸退除第二次浸锌化学镀镍二制程说明1)除油铝是一种活泼金属,与酸碱都能剧烈反应,因此相比钢铁基体铝的除油溶液碱性不能太强,以免对铝基体产生过度的腐蚀。
因此除油的配方中氢氧化钠的含量一般较低,以磷酸钠、硅酸钠和碳酸钠为主。
除油液中的硅酸钠对铝很好的作用,即使除油液温度较高,除油时间较长,铝的腐蚀也很小,因此可以用于零件精度较高的除油,但是含硅酸盐的碱液必须彻底清洗干净,否则,残留的硅酸盐在浸蚀时遇酸会生成不溶于水的、难以去除的硅酸膜,造成镀层结合力不强,除油最好先用热水清洗、再用冷水,而且应尽快清洗。
在除油的过程中,切忘高温碱液因增发而干结在零件上,从而导致零件腐蚀。
2)浸蚀浸蚀是前处理中重要的工序。
其目的是为了进一步去除铝表面的缺陷,并从铝合金表面去除各种合金元素和杂质,形成均匀的铝表面,为后一道工序提供良好的底材。
铝合金中含有铜、镁、硅、锰和锌等合金元素。
如果不能去除干净,在这些合金成份上不能直接化学镀镍,容易产生结合力不强或针孔。
浸蚀可以用碱浸蚀或酸浸湿。
用酸浸蚀对铝的腐蚀小,不仅不可保证表面的光洁度,而且由于合金元素去除较彻底,所达的结合里较高。
酸性浸蚀的腐蚀远低于碱性浸蚀,由于合金的腐蚀一般驶电化学腐蚀,合金元素与铝元素基体形成原电池,浸蚀发生在合金元素的周围,当浸蚀严重时容易产生毛细孔洞,这种空洞进入的溶液很难清洗,当溶液进入化学镍溶液时,空洞中的脏污会慢慢溢出,轻则造成镀层粗糙,重则引发针孔起泡。
对于有些合金采取碱性浸蚀的效果更好。
另外对于表面光洁较差或者经加工车削后有螺纹的零件,碱性浸蚀有助于去除化学镍难以完整覆盖的毛刺和锐边。
此外,碱性浸蚀有助于在氧化严重的铸件上获得更薄、更均匀的去除氧化膜的新鲜表面。
3)第一次浸锌化学镀镍时,铝的表面有一层致密的氧化膜,这层膜大约有5~20um,不去除它就很难形成很的镀层。
就氧化层本身来说,去除并不困难,问题是在去除氧化膜后的表面与空气接触的表面会迅速形成氧化膜,浸锌的目的一方面是去除这层氧化膜,另一方面是去除氧化膜的同时再铝的表面形成锌的置换层,起阻挡作用,使去除了氧化膜的表面与大气隔绝,免受氧化。
铝合金化学镍工艺流程图

铝合金化学镍工艺流程图英文回答:The chemical nickel process for aluminum alloy involves several steps to achieve the desired outcome. I will explain the process in detail below:1. Surface Preparation: Before the nickel plating can be done, it is important to prepare the surface of the aluminum alloy. This involves cleaning and degreasing the surface to remove any dirt, oil, or other contaminants. This can be done using a solvent or a cleaning solution.2. Electrocleaning: After the surface is cleaned, it needs to be electrocleaned to further remove any impurities and to activate the surface for plating. Electrocleaning is done by immersing the aluminum alloy in an electrolyte solution and applying an electric current. This process helps to remove any oxide layers and prepares the surface for the next step.3. Nickel Plating: Once the surface is properly prepared, the aluminum alloy can be plated with nickel. Nickel plating is done by immersing the alloy in a nickel plating bath and applying an electric current. The nickel ions in the bath are attracted to the aluminum alloy surface and form a layer of nickel on top. This process can be controlled to achieve the desired thickness of thenickel layer.4. Post-Treatment: After the nickel plating is completed, it is important to perform post-treatment steps to ensure the quality and durability of the plated surface. This can involve rinsing the plated part to remove any residual chemicals, drying the part, and applying a protective coating or sealant.5. Quality Control: Throughout the entire process, it is important to monitor and control various parameters to ensure the quality of the plated surface. This can include monitoring the plating bath composition, temperature, and current density. Regular testing and analysis can be doneto check the thickness and adhesion of the nickel layer.Overall, the chemical nickel process for aluminum alloy involves surface preparation, electrocleaning, nickel plating, post-treatment, and quality control steps. This process helps to improve the appearance, corrosion resistance, and wear resistance of the aluminum alloy.中文回答:铝合金化学镍工艺流程涉及多个步骤,以达到期望的效果。
铸造铝镍钴工艺

铸造铝镍钴工艺引言铝镍钴合金是一种具有广泛应用前景的高性能材料,具有优异的强度、耐腐蚀性和导电性能。
铸造是铝镍钴合金制备的重要工艺之一,通过铸造可以获得具有复杂形状和良好性能的铝镍钴合金制品。
本文将介绍铸造铝镍钴工艺的原理、流程以及相关的四大类常用铸造方法。
原理铸造是制备金属材料的一种重要工艺方法,通过将熔融金属注入到铸型中,经过冷却凝固形成所需形状的零件。
在铸造铝镍钴工艺中,使用铝镍钴合金作为原料,并且根据具体要求添加其他合金元素。
通过控制熔融金属的温度和冷却速度,可以获得具有良好性能的铸造件。
流程铸造铝镍钴的工艺流程主要包括以下几个步骤:1. 准备铸型首先根据所需零件的形状和尺寸,制作相应的铸造型腔。
铸造型腔可以采用砂型、金属型等不同材料和结构形式。
铸造型腔内需要考虑零件的缩孔和冷却问题。
2. 准备合金料将所需的铝镍钴合金材料按照配方比例准备好,同时添加适量的其他合金元素。
合金料需要经过严格的熔炼和纯化处理,以保证合金的质量和性能。
3. 熔炼合金将准备好的合金料放入熔炼炉中加热熔融。
熔融温度需要根据合金的成分和熔点进行控制。
在熔融过程中,可以通过搅拌、加热等操作来确保合金的均匀性和纯度。
4. 倒注将熔融的合金料倒入准备好的铸型中,填满整个型腔。
在倒注的同时需要控制好注液的速度和温度,以避免产生气孔、缩孔等缺陷。
5. 冷却凝固待合金料注入铸型后,开始进行冷却凝固。
冷却速度是影响凝固过程和铸造件性能的关键因素之一。
通过控制冷却速度可以获得不同结构和性能的铸造件。
6. 清理整理冷却凝固后的铸造件需要进行清理和整理。
去除可能存在的铸型残留物、表面氧化物等,以提高铸造件的表面质量和外观。
常用铸造方法在铸造铝镍钴工艺中,常用的铸造方法可以分为四类:砂型铸造、金属型铸造、压铸和失蜡铸造。
1. 砂型铸造砂型铸造是最常用的铸造方法之一,适用于各种形状和规模的铸件制造。
该方法以砂型为基础,通过填充、压实、模具分离等工艺步骤来制备铸造件。
铝镍钴工艺流程范文

铝镍钴工艺流程范文第一部分:引言,介绍铝镍钴工艺的背景和意义(150字)随着工业技术的不断发展,金属表面的防腐和美化处理变得越来越重要。
铝镍钴工艺的应用范围广泛,可以提供良好的耐蚀性、耐磨性和装饰性能,因此在航空、汽车、电子、机械等行业中得到了广泛应用。
本文旨在介绍一种铝镍钴工艺流程,以帮助读者了解铝镍钴工艺的制备方法和优势。
第二部分:铝镍钴工艺的原理和特点(300字)1.材料选择:铝镍钴工艺中,通常使用高纯度金属铝、镍和钴作为原材料,这些金属具有优异的化学稳定性,能够保证涂层的质量和稳定性。
2.工艺参数:铝镍钴工艺的制备过程中,工艺参数的选择对涂层质量具有重要影响。
例如,电流密度、温度、pH值和电解液中添加剂等参数需要进行合理调整,以获得均匀、致密且具有良好性能的涂层。
3.工艺流程:铝镍钴工艺的制备步骤主要包括清洗、预处理、电镀和后处理等环节。
合理的工艺流程可以保证涂层的附着力,并提高涂层的耐腐蚀性能。
第三部分:铝镍钴工艺流程的制备方法(500字)1.清洗:首先需要将金属基材进行清洗,以去除表面的污垢和氧化物。
可以使用酸洗、碱洗或电解清洗等方法进行清洗,保证基材表面的干净。
2.预处理:清洗后的基材需要进行预处理,以提高涂层的附着力。
常用的预处理方法包括活化处理、酸洗和钝化等,这些方法能够改善基材表面的粗糙度和化学活性,有利于涂层的形成和与基材的结合。
3.电镀:制备好的基材被放置在电解槽中,与阳极结合。
通过调整电流密度、温度和pH值等参数,可以控制镍、钴和铝的沉积速率和比例,得到所需的合金涂层。
制备过程中需要注意保持电解液的纯净度和稳定性,以确保涂层的均匀性和质量。
4.后处理:电镀后的基材需要进行后处理,以进一步提高涂层的性能。
后处理方式包括热处理、磨光和密封等,这些步骤能够增加涂层的硬度、耐磨性和耐腐蚀性。
第四部分:铝镍钴工艺流程的优势和应用(250字)1.耐腐蚀性能:铝镍钴涂层能够提供良好的耐腐蚀性能,对于在恶劣环境下使用的金属件具有较好的保护作用。
铝镍钴工艺流程[1]汇总
![铝镍钴工艺流程[1]汇总](https://img.taocdn.com/s3/m/561a91ef52d380eb63946d6b.png)
4.1.1铝镍钻永磁合金技术条件4.1.2合金成份4.1.3工艺流程图4.1.4造型工艺作业指导书4.1.5熔炼工艺作业指导书4.1.6磁场热处理工艺作业指导书4.1.7磨加工工艺作业指导书4.1.8检验工艺作业指导书4.1.1铸造铝镍钻永磁合金技术条件按国标GB4753— 84执行,一些特殊要求的产品(军品)则按合同及有关协议执行。
4.1.2合金成份A1Ni Co Ti Cu Ft315/315I. 6/5,1 2. 8/3. 20. 7/1.0氐5/7.2:13. 5/1i . 5Ni Co Cu Fe13.5/1 L5 |23.5/21, 5回4.1.3工艺流程图4.1.5熔炼工序作业指导书本工艺包括坩埚制作、配料、熔炼、浇注取向、清砂、退火等项目内容。
其基本任务是熔炼铸造得到化学成份合格、柱晶生长良好,无明显外在缺陷的磁钢铸坯。
1塔圳模芯2契型锤34、6、8磅榔头4台秤5天平6搅棒—打渣瓢8抱钳g地坑式水冷结晶器10保温即和;名称牌、;主餐化学成(*> 尺寸大小1L业纯铁DT2N99. I<p 12—(9 30X50—150 2电解怙进口或国产Co-0>99.9片状或10 X 50 X 100 3电解厲Ni-1沙.910X 50X 1004电解阳Cu—1 2 99・ 9510 X50 X505电解和Al—1>99.730 X40X 1006Ti—1M99.5甘状或小块状■I・;、Fe- Nb 1M:0小块状8分析纯FeS> 80小块状9Si—1Si >99粒块状10Si-Ca2Si+Ca> 如过0・3nn的细粉111S3 C $99.92n®以卜池状粉库4n-p用途1细温粕犬壮炉SX 10-131 A L KS I—12 If. 破約变控制端炉Mt尺寸400X200X160・功率10KW 盹宦淑曲1300T 1趙火2入温縮貰电炉SX 10-131 !lV KS T-12応樂可拧“胡腿拧購甜・炉悻尺寸I00X200X1M. 功^10KW 1300T13 1岡火炉SX—12—10 ・ 1MW・炉50C X 300X 200・製审.ttflt lOOtftt 配Kr—12—16 书可控桂il度控制1岡火!卑温电阳炉自SW助串3KW.炉腿尺寸W0X14QX115 IVDNK 702辂密温度控制器16执世即£血讯H制暮煤准雀备配200A/250V和100A/230V町拧科・战刑即为1盹中心场僅大尸3OQOGs 1提供等部处艸论场E遊風机IG——3砒.功率•间h】3伽阈訂19比较瘵检件处理产乩竹能10热处理1 11HJW的平搐制护腔丸细等皐送产品HOOtXl—1. 5 小时磴场热处理工序作业指导书一孚山磁钢顼热.髙温固溶*磁场拎却、靈场等温,多级时效(I 处理<获得优fl的永陪性能和几何形状满足婆求的磁性元件.i iffiJZt 5L H-EBW. U出炉4.161 LNGT磁钢的热处理工艺磁钢的热处理工艺包括铸件毛坯退火,初磨产品的热处理,其中产品热处理由中温预热,高温固溶,磁场冷却,低温预热,磁场等温,多级失效六个阶段,处理程序如下:0(1)铸坯退火,将铸坏装入26KW高温炉中,随炉开温至1100C,保温1 —2小时,炉冷。
烧结铝镍钴检测工艺操作规程
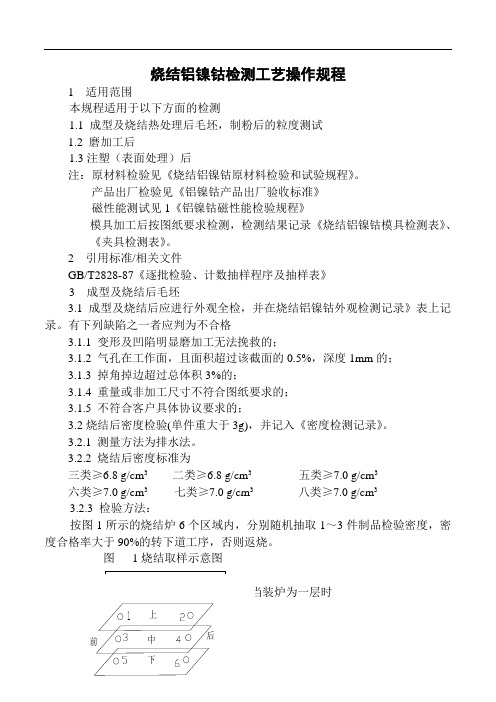
烧结铝镍钴检测工艺操作规程1 适用范围本规程适用于以下方面的检测1.1 成型及烧结热处理后毛坯,制粉后的粒度测试1.2 磨加工后1.3注塑(表面处理)后注:原材料检验见《烧结铝镍钴原材料检验和试验规程》。
产品出厂检验见《铝镍钴产品出厂验收标准》磁性能测试见1《铝镍钴磁性能检验规程》模具加工后按图纸要求检测,检测结果记录《烧结铝镍钴模具检测表》、《夹具检测表》。
2 引用标准/相关文件GB/T2828-87《逐批检验、计数抽样程序及抽样表》3 成型及烧结后毛坯3.1成型及烧结后应进行外观全检,并在烧结铝镍钴外观检测记录》表上记录。
有下列缺陷之一者应判为不合格3.1.1 变形及凹陷明显磨加工无法挽救的;3.1.2 气孔在工作面,且面积超过该截面的0.5%,深度1mm的;3.1.3 掉角掉边超过总体积3%的;3.1.4 重量或非加工尺寸不符合图纸要求的;3.1.5 不符合客户具体协议要求的;3.2烧结后密度检验(单件重大于3g),并记入《密度检测记录》。
3.2.1 测量方法为排水法。
3.2.2 烧结后密度标准为三类≥6.8 g/cm3 二类≥6.8 g/cm3五类≥7.0 g/cm3六类≥7.0 g/cm3 七类≥7.0 g/cm3 八类≥7.0 g/cm33.2.3 检验方法:按图1所示的烧结炉6个区域内,分别随机抽取1~3件制品检验密度,密度合格率大于90%的转下道工序,否则返烧。
图1烧结取样示意图当装炉为多层时3.2.4 制粉后的粒度测试对制粉工序球磨后的粉及混合粉进行粒度测试,过筛按20单位中抽1单位比例进行抽检。
全部过筛流转,否则转重磨或其它处理,并记入《粒度测试记录》。
3.3 磨加工后的外观检验3.3.1接收前的外观检验外观应无明显锈蚀,应清洗干净、无水、无污物,检验方法按GB/T2828-87正常检查一次抽样方案Ⅱ级,按AQL=2.5判定,锈蚀超过2%退回加工方处理;使用毛巾擦拭产品,使毛巾表面明显变黑的退回加工方处理。
- 1、下载文档前请自行甄别文档内容的完整性,平台不提供额外的编辑、内容补充、找答案等附加服务。
- 2、"仅部分预览"的文档,不可在线预览部分如存在完整性等问题,可反馈申请退款(可完整预览的文档不适用该条件!)。
- 3、如文档侵犯您的权益,请联系客服反馈,我们会尽快为您处理(人工客服工作时间:9:00-18:30)。
4.1.1 铝镍钴永磁合金技术条件4.1.2 合金成份4.1.3 工艺流程图4.1.4 造型工艺作业指导书4.1.5 熔炼工艺作业指导书4.1.6 磁场热处理工艺作业指导书4.1.7 磨加工工艺作业指导书4.1.8 检验工艺作业指导书4.1.1铸造铝镍钴永磁合金技术条件按国标GB4753—84执行,一些特殊要求的产品(军品)则按合同及有关协议执行。
4.1.2合金成份4.1.3工艺流程图4.1.5 熔炼工序作业指导书本工艺包括坩埚制作、配料、熔炼、浇注取向、清砂、退火等项目内容。
其基本任务是熔炼铸造得到化学成份合格、柱晶生长良好,无明显外在缺陷的磁钢铸坯。
(2) 坩埚制造工艺A.配比a)炉底、炉身用镁砂粉、粒各半,外加硼酸3%及适量的水。
b)炉口用镁砂细粉掺合用水稀释的水玻璃液。
B.镁砂的磁选与混合将称好的颗粒镁砂倒入盆中,选出白、黑异物,然后将镁砂撒在干净的胶板上用磁钢选出铁磁性物质,再将称量好的细粉倒入、混匀后再次用磁钢吸选,判断已无铁磁性物后,撒入硼酸混匀并加适量水,反复翻混多次,盖上湿麻袋备用。
C.坩埚打结工艺a)将感应圈人壁及底部置上玻璃丝布。
b)先打结坩埚底部,每次约加入1.5—2Kg的镁砂,用契形锤捣紧实,每加一层料前要用划钎划松打结层表面、以确保层间衔结。
c)放炉芯前,应仔细刮去松散的镁砂,用平锤将炉底捣平、捣实。
d)将园锥台形的炉芯放在平整的炉底中心位置并压紧。
用划钎沿炉芯周边,将炉底镁砂部份划松,加入1—2Kg镁砂用契形锤进行炉壁打结。
e)打结时务须用力均匀,确保四周紧实一致,为使层间衔接良好,在筑捣新的一层前务必将前层部份划松,再行加料筑打,这样层层捣实直至炉口。
f)将感应圈上沿炉口部份压平筑紧,并用弧形压圈紧贴炉芯上沿外壁将炉墙上端面压牢,取出炉芯,用镁砂水玻璃料敷好炉口。
D.坩埚烘烤a)将打结好的坩埚用管式电阴炉予烘12小时以上。
b)加入低碳钢(最好是冲子)于坩埚中,启动高频设备,半波烘烤4小时后,方可全波送电、熔化、洗炉1—2次,直至炉壁光滑完整并烧结良好即可熔炼磁钢。
(3)配料配料是按产品工艺卡规定的化学成份范围,根据原材料成份和单炉装入量进行计算称量的过程,磁钢熔炼分全新料和全返料两种,配料过程如下:A.金属原材料的外在质量要求,工业纯铁必须滚光使用,Ni、Co、Cu、Al必须干燥、洁净、无异物。
a) 按返料熔炼次数搭配,返回三次以上的回炉料将降级使用。
b) 返回料熔炼只补Al.Ti.S元素,按装入量0.5%Al,0.3%Ti和0.1%S配料称重,熔炼第一炉料呆适当多补加0.2%左右的Al。
c) 返回料称量前应彻底清除粘砂和异物。
D. Al、Ni、Co、Cu、Ti、Fe等金属料用10Kg台称量,Nb(或Fe— Nb)、Si、FeS、Si—Ca、C 等材料用0.5Kg药物天平称量,用天平称量的料装入试样袋中,熔炼时倾入不锈钢铲中加入。
E.料配好称重后,应按工艺卡要求进行复核,配料人和复核者均应签名备查。
(4)熔炼和定向结晶A.熔炼准备:a)将定向型模平放在底板砖上,盖上保温帽砖装入RTX—50—13炉内。
b)用钢片尺检查结晶器钢板,如果平整或微凹则可用,否则更换新板。
c)用砂轮砂去结晶器钢板表面锈层,扫净异物,然后用红砖烘烤除去潮气。
e)将定向结晶过程的操作器具摆放到位。
f)依照260型高频加热设备操作规程作好启动准备。
B.熔炼操作a)先将钴片Ni块,工业纯铁和电解铜等材料同时加入炉内大片料应顺炉壁摆放,电解镍板覆盖在最高层装料力求紧实,以迅速熔化。
b)启动高频加热设备,以最大功率进行熔化,熔化过程中,时时捅料,以防料悬空“架桥”。
c)料全熔后,将Si—Ca粉倒入不锈钢小铲,撒入液面进行预脱氧,捞去熔渣后,将碳粉均匀地撒在液面,让其充分地进行碳氧反应,反应时间隔30分秒。
d)待碳氧反应完毕后,将FeS放入加料不锈钢小铲中加入炉内,时时捞熔渣,并顺产欠加入Fe—Nb和结晶硅。
e)加入结晶硅后,液面出现羽毛花纹,待金属液面仅剩1/3羽毛状纹或全部消失时,立即加入钛铝金属,并用经950—10000C烘烤的搅拌棒对钢液进行充分地搅拌,为使成份均匀,上下搅拌次数不少于40次,搅拌后停电,静置2分钟加上1Kg返回料,提温,最后补加元素,搅拌出钢。
f)确认搅拌均匀后,停电、抬炉、浇注,渡注温度控制在16500C左右,在高压12-12.5Kv时,阳极电流3A左右, 栅极电流0.6A左右时,正常熔炼时间,应控制在0.8公斤/分以内。
C.浇注a)在搅拌钢液即将结束,冶炼工认为无其他异常时,下达出钢通知,浇注人员,迅速地用大抱钳将高温型模从13500C的高温炉中取出,判定型模底部平整无开裂现象后,立即放在定向结晶钢板上,放上压铁。
b)迅速抬起坩埚,大流快速浇注,与此同时将结晶器冷却水开至最大。
10Kg钢力求控制在5—6秒钟内浇完,夹型、施压、浇注、开水要求配合严密,动作敏捷。
整个过程应在1—2分钟。
c)浇注完后,取去压铁,从高温炉中夹出红砖,放在取向型模盖上,然后将整个浇注热型模用保温罩罩上静置不动,型在结晶器上,静置时间视产品大小而定,一般为20—30分钟。
d)浇注后用钢钎清理坩埚壁和炉底的熔渣,清净倒掉后立即装料,进入下一炉进行。
(5)清砂将经过定向结晶的磁钢铸件,从型模中清理出来的过程叫清砂,清砂按下列程序进行。
a) 用小钢钎起掉保温帽,把帽口上残余金属取下后,将完好的保温帽叠放好,下备用。
b)敲掉型模四周砂层,露出铸件后,用榔头敲击铸件保温层金属,使结晶取向的铸件沿保温层金属面自行掉落。
(3)逐根清理粘砂和残留的保温层金属。
(4)破坏一根铸件,检查断宏观状态,判断柱晶质量和化学成份。
(5)填写工艺卡,将合格的铸件送交中检工序。
(6) 退火为降低磁钢硬度,改善加工性能以利打毛刺和机床切磨加工,LNGT 磁钢,需要在恒定的温度下进行退火处理,使γ相大量析出。
退火制度如下图:温度0C出炉4.1.6.1 LNGT 磁钢的热处理工艺磁钢的热处理工艺包括铸件毛坯退火,初磨产品的热处理,其中产品热处理由中温预热,高温固溶,磁场冷却,低温预热,磁场等温,多级失效六个阶段,处理程序如下:(1) 铸坯退火,将铸坏装入26KW 高温炉中,随炉开温至11000C ,保温1—2小时,炉冷。
(2) 产品热处理a) 中温预热:将粗磨加工的产品整齐排列,装入不锈钢盒中在高温箱形炉中加热到850—9000C 保温30分钟以上。
b) 高温固溶:将预热透的产品用长把不锈钢铲送至12400C左右(校核温度)高温炉中,保温10—20分钟,为保证产品合金形成单一的固溶体和防止产品氧化,过烧变形除要特别注意掌握好温度和保温时间外,还应控制产品的装入数量和在炉中装入焦炭制造还原性气氛。
c) 磁场风淬或磁场空冷:将固溶好的产品从高温炉中用不锈钢勾迅速捞出放入磁场中风冷或空冷,根据重庆地区的天气情况,一般为夏天酷热季节吹急风冷却,其余时间可吹微风或在空气中自然冷却。
磁强度240KA/m(充磁机电50—60A)。
d) 低温予热:将固溶风淬后的产品退磁后装入不锈钢小盒中(一般装入量为20—40件),送入箱形电阻炉中予热,予热温度600—6500C保温时间不小于20—30分钟。
e) 磁场等温:将低温予热好的产品随同盛装的不锈钢盒一起迅速送入等温炉内,当702精密温度控制器偏差指示为-50C时施加磁场,将整流器输出电流调至50—60A,此时磁场强度为240KA/m左右,当温度达到8000C时开始计算等温时间,保温时间为15—20分钟左右。
当保温时间足够后,立即关掉磁场,取出产品缓冷。
并按5%的比例在比较表上检查等温后产品磁性能。
磁场控速处理:当产品尺寸较大,形状较复杂时可采用此工艺,将固溶透的产品迅速从炉中取出,置于极头上空冷并不断翻动产品,以保证产品四周冷却均匀,当产品冷至900—9500C,及时将产品夹入磁场,复盖保温纤维,使产品在磁场中缓慢冷却,18分钟后,打开保温纤维,产品应呈暗红色(约600—6500C),冷速一般控制在15—200C/分为好。
此工艺技术性强,优点在于产品不易开裂,操作不当容易造成永磁性能低下的缺点。
f) 多级时效回火:将磁场处理后的产品,装入12KW箱式回火炉中,炉膛底部用不锈钢板,板垫放栅型铁架,产品按组以一定间隙装好,以利热传导良好,均匀,每次装入量控制20—30Kg左右,炉门口用耐火纤维封档。
g) 回火制度:6500C×3h+6000C×10h+5500C×20h,回火结束后,炉冷至2000C以下左右出炉。
4.1.6.2 LNG磁钢热处理工艺LNG磁钢热处理主要采用磁场控速处理,操作与LNGT磁钢控速处理一样,具体工艺参数如下:预热:900—9500C固溶:1270—12900C磁场控速:20—250C/分回火:6200C×2h+6000C×4h+5500C×8h4.1.7 磨加工工序作业指导书本工序包括砂磨毛利,粗磨铸件坯外园,砂轮切割,粗磨产品端面,精磨外园和精磨端面等工作。
基本任务是对磁钢产品进行整型、切割、磨加工,提供外型尺寸合格的粗磨和精磨产品。
4.1.7.1 磨削工艺本工序包括:砂磨毛刺—无心磨床粗磨外园—多刀切割—立轴磨床磨平面—热处理—性能检测—无心磨床精磨外园—倒角—矩台平面磨床精磨-平面—倒角等工序。
(1)砂磨毛刺将退火后的磁铸件,用MC3040型或S3SL—400型砂轮机砂去表面凸出部份和砂渣等异物,砂园形磁钢铸坯时,一手握着磁钢放在砂轮托架上自由转动,另一只手用磁钢铸坯对砂磨铸件施力靠近砂轮,当一端砂磨好后,将铸件倒头,再重复上述过程直至满足要求。
砂轮型号:P400×40×30 TL46K5V35或P400×40×203 TL36K5V35。
(2)无心磨粗磨外园经打毛刺的铸坯送无心磨床粗磨外园或立柱磨床粗磨表面。
主要工艺:无心磨主要工艺参数:磨头材质磨头砂轮型号:PSA350×125×127WA36K5V35导轮材质及转速材质G2转速无级变速粗磨削工艺:进刀量:0.2—0.3mm/次冷却液:碳酸钠(NaCo3)0.5%亚硝酸钠(NaNo3)1—1.2%甘油 (C3H10O3)0.5—1% 或B83—2固体削液冷却液配制可根据实际使用效果进行调整,既要保证产品加工过程的冷却效果,又不能使产品造成腐蚀和锈蚀。
导轮转速:30—40转/分(3)立轴磨床粗磨平面将砂好的园坯或切割好的半成品磁钢送中检工序检查外观和尺寸后,送立轴磨床粗磨平面。
a) 立轴园台磨床主要技术参数园磁台直径和转速:直径:750mm 转速:20转/分磨头材质和转速:转速:1000转/分磨头材持和型号尺寸:N450×180×380WA或A36K5V35b) 磨削工艺将切割好的工件用矩形挡铁在园磁台上均衡地呈三角形摆好挡紧,启动电磁吸盘开关,吸牢磁钢产品,再用木榔头敲击其顶部及挡铁,确知全部工件均紧靠电磁园盘,并挡好吸牢后,才可启动磨头和转动电磁园磁。