焦炉烟道气脱硫脱硝技术研究
试析焦炉烟气脱硫脱硝净化技术与工艺

试析焦炉烟气脱硫脱硝净化技术与工艺焦化厂在炼焦过程中会产生大量烟气,其主要污染指标是NOx、SO2等,会严重污染城市的环境空气质量,本文在对烟气主要污染指标进行分析的基础上,简述干法脱硫工艺、湿法脱硫工艺、SCR法脱销工艺,并对焦化脱硫脱硝工艺进行优化,从而提高处理效率。
标签:焦炉烟气;脱硫脱硝技术;优化措施焦炉在实际生产过程中,会产生严重的环境污染问题。
现阶段,我国在治理焦炉烟气过程中,常用脱硫脱硝工艺进行处理,根据相关环保标准规定,将NOx 的整合到总量控制因子中,且NOx排放浓度小于500mg/Nm3,SO2排放浓度小于50mg/Nm3时,可以直接排入大气环境,如果排放浓度不符合排放标准要求时,需要经过处理之后再排入大气。
一、焦炉烟道气的特点二、焦炉烟气脱硫脱硝工艺1、干法脱硫工艺烟气与碱性吸收剂接触,烟气内的SO2与碱性吸收剂在接触过程中发生化学反应,生产新的化学物质硫酸盐、亚硫酸盐,从而降低烟气中的SO2的含量。
为了加快该反应的反应速度,可以增大碱性物质的接触面,如碱性物质为细碎状态、疏松状态,并且在半干法脱硫工艺过程中,可以在烟道气内加入适量水,使碱性物质表面会形成液膜,有利于SO2融入碱性物质。
与此同时,干法脱硫工艺中的各个工序都需要在干燥的操作环境下进行,这种工艺不会对运行设备产生腐蚀作用,并且也不会有污染废水排出,同时,有利于烟气的排放和扩散,但是,这种工艺的脱硫剂利用率较低,以及脱硫效率较低。
2、湿法脱硫工艺将石灰石、碳酸钠等物质作为洗涤剂,能够在反应塔中对烟气进行洗涤操作,从而去除烟气中的SO2。
如图1所示。
湿法脱硫工艺在脱硫处理中的应用较早,这种工艺技术已趋于成熟化,并且始终处于创新和优化过程中,其脱硫效率已經超过95%,同时能够回收反应中产生的所有副产品。
与此同时,石灰石-石膏湿法烟气脱硫工艺的吸收剂成本较低、脱硫效率较高、吸收剂利用率较高,主要用于处理高浓度的SO2烟气。
焦炉烟气SDA 脱硫+SCR脱硝技术装备研发生产方案(一)

焦炉烟气SDA 脱硫+SCR脱硝技术装备研发生产方案一、实施背景随着中国工业的快速发展,焦炉烟气中的硫氧化物(SOx)和氮氧化物(NOx)含量持续升高,对环境和人类健康造成了严重的影响。
为此,国家对环保技术的需求愈发迫切,从而推动了SDA脱硫+SCR脱硝技术装备的研发和生产。
二、工作原理1.SDA脱硫:通过碱性吸收剂,如氢氧化钙、氧化钙等,与烟气中的SOx反应,生成硫酸钙,从而实现脱硫。
2.SCR脱硝:利用还原剂(如氨气、尿素等),在催化剂的作用下,与烟气中的NOx反应,生成无害的氮气和水蒸气。
三、实施计划步骤1.技术研发:开展基础研究,设计实验模型,研发高效的碱性吸收剂和催化剂。
2.实验验证:在实验室条件下,对所研发的技术进行验证,确保其有效性。
3.中试生产:在小规模生产线上进行试验,进一步验证技术的可行性。
4.规模生产:根据中试结果,调整生产线,实现规模化生产。
5.安装调试:对已生产的设备进行现场安装调试,确保设备正常运行。
6.验收测试:对设备进行性能测试,确保其满足设计要求。
7.推广应用:将设备推广至各大焦化企业,进行现场应用。
四、适用范围本方案适用于焦炉烟气的治理,可广泛应用于各类焦化企业。
五、创新要点1.高效吸收剂:研发出一种新型碱性吸收剂,具有高吸收效率和低成本的特点。
2.高活性催化剂:所研发的催化剂能够在较低的温度下实现NOx的高效转化。
3.双重脱硫脱硝技术:将SDA脱硫与SCR脱硝相结合,实现了烟气中SOx和NOx的同时去除。
4.模块化设计:设备采用模块化设计,便于运输和安装。
5.自动化控制:引入先进的自动化控制系统,提高了设备的稳定性和效率。
6.资源回收:将生成的硫酸钙回收利用,实现了资源的有效利用。
六、预期效果1.降低SOx和NOx排放量,满足国家环保标准。
2.提高企业环保形象和社会责任感。
3.通过技术转让和设备销售,为企业带来可观的收益。
4.为同类企业的环保治理提供示范和借鉴。
焦炉烟气脱硫脱硝工艺研究

高 ,需要 开发具有 自主知识产权 的技术 ,尽快提 高国产
化率 ,降低 成本 。而 当烟气 中的颗粒物含量过高 时 ,会
对活性炭 的吸附 l生能产 生重要影 响。
烟气
尘对催化 剂的磨损 ,延长催化剂 寿命 ,还可 省略SCR脱
气排放 浓度而言 ,难 以达到这一排放标 准 ,尽快探 寻适
如 图 l所 示 ,焦 炉烟 气经 加热 后进 人SCR脱 硝反 应
合焦化 行业脱硫脱硝除尘工艺 显得尤为重要 。
器 ,加入脱硝还原 剂 ,发生还原反 应 ,脱 除氮 氧化物 ,
2 焦炉烟气特 点
然后进 入余 热锅炉 回收热量 ,再经 氨法脱硫脱 除二氧化 硫 ,通 人氧化空气将 亚硫酸铵氧化 为硫酸铵 ,最 后经湿
料煤以及焦炉串漏等都会影 响烟气组成 p】。焦炉烟气中SO, 仍有较好 的脱硝效果 。采用氨法脱硫 可充分利 用焦化厂
中 国环保 产 业 201 8年 第3期
流程如 图3所示 ,焦炉烟气 先进人 预热锅炉 回收热量 ,
再冷却 降温 ,然后进入活性炭 吸附装置 。吸附塔 分为两
级 ,第一级 先脱硫 ,烟气 中二氧化硫被 吸附到活性 炭表
度 ≤50mg/Nm ,颗 粒物 浓度 ≤30mg/Nm ,对 于特别 地 尘+SCR脱硝和活性炭法 脱硫脱硝技术 等。
区 ,排放 的氮 氧化 物 浓度 ≤ 150mg/Nm。,二 氧化 硫 浓 3.ห้องสมุดไป่ตู้ 加热+SCR脱硝+余热锅 炉+氨法脱硫
度  ̄<30mg/Nm。,颗粒物浓度 ≤15mg/Nm。。就 当前焦 炉烟 3.1.1 工 艺流 程
焦炉烟气同时脱硫脱硝技术路线探讨
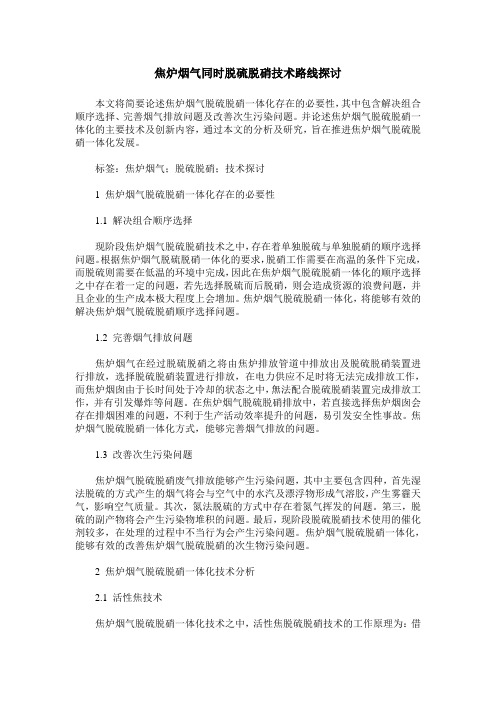
焦炉烟气同时脱硫脱硝技术路线探讨本文将简要论述焦炉烟气脱硫脱硝一体化存在的必要性,其中包含解决组合顺序选择、完善烟气排放问题及改善次生污染问题。
并论述焦炉烟气脱硫脱硝一体化的主要技术及创新内容,通过本文的分析及研究,旨在推进焦炉烟气脱硫脱硝一体化发展。
标签:焦炉烟气;脱硫脱硝;技术探讨1 焦炉烟气脱硫脱硝一体化存在的必要性1.1 解决组合顺序选择现阶段焦炉烟气脱硫脱硝技术之中,存在着单独脱硫与单独脱硝的顺序选择问题。
根据焦炉烟气脱硫脱硝一体化的要求,脱硝工作需要在高温的条件下完成,而脱硫则需要在低温的环境中完成,因此在焦炉烟气脱硫脱硝一体化的顺序选择之中存在着一定的问题,若先选择脱硫而后脱硝,则会造成资源的浪费问题,并且企业的生产成本极大程度上会增加。
焦炉烟气脱硫脱硝一体化,将能够有效的解决焦炉烟气脱硫脱硝顺序选择问题。
1.2 完善烟气排放问题焦炉烟气在经过脱硫脱硝之将由焦炉排放管道中排放出及脱硫脱硝装置进行排放,选择脱硫脱硝装置进行排放,在电力供应不足时将无法完成排放工作,而焦炉烟囱由于长时间处于冷却的状态之中,無法配合脱硫脱硝装置完成排放工作,并有引发爆炸等问题。
在焦炉烟气脱硫脱硝排放中,若直接选择焦炉烟囱会存在排烟困难的问题,不利于生产活动效率提升的问题,易引发安全性事故。
焦炉烟气脱硫脱硝一体化方式,能够完善烟气排放的问题。
1.3 改善次生污染问题焦炉烟气脱硫脱硝废气排放能够产生污染问题,其中主要包含四种,首先湿法脱硫的方式产生的烟气将会与空气中的水汽及漂浮物形成气溶胶,产生雾霾天气,影响空气质量。
其次,氮法脱硫的方式中存在着氮气挥发的问题。
第三,脱硫的副产物将会产生污染物堆积的问题。
最后,现阶段脱硫脱硝技术使用的催化剂较多,在处理的过程中不当行为会产生污染问题。
焦炉烟气脱硫脱硝一体化,能够有效的改善焦炉烟气脱硫脱硝的次生物污染问题。
2 焦炉烟气脱硫脱硝一体化技术分析2.1 活性焦技术焦炉烟气脱硫脱硝一体化技术之中,活性焦脱硫脱硝技术的工作原理为:借助活性焦的吸附作用及催化作用,祛除烟气之中的SO2及NO2,是一种有效的回收硫资源的干法烟气处理技术。
焦炉烟气SDA 脱硫+SCR脱硝技术装备研发生产方案(二)
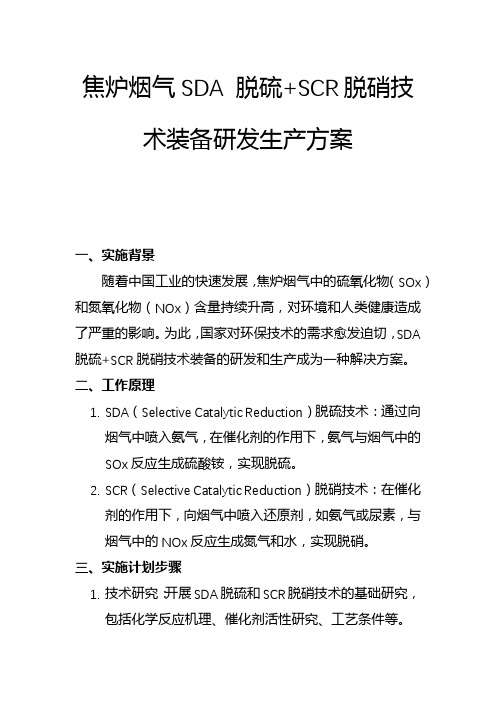
焦炉烟气SDA 脱硫+SCR脱硝技术装备研发生产方案一、实施背景随着中国工业的快速发展,焦炉烟气中的硫氧化物(SOx)和氮氧化物(NOx)含量持续升高,对环境和人类健康造成了严重的影响。
为此,国家对环保技术的需求愈发迫切,SDA 脱硫+SCR脱硝技术装备的研发和生产成为一种解决方案。
二、工作原理1.SDA(Selective Catalytic Reduction)脱硫技术:通过向烟气中喷入氨气,在催化剂的作用下,氨气与烟气中的SOx反应生成硫酸铵,实现脱硫。
2.SCR(Selective Catalytic Reduction)脱硝技术:在催化剂的作用下,向烟气中喷入还原剂,如氨气或尿素,与烟气中的NOx反应生成氮气和水,实现脱硝。
三、实施计划步骤1.技术研究:开展SDA脱硫和SCR脱硝技术的基础研究,包括化学反应机理、催化剂活性研究、工艺条件等。
2.装备设计:根据研究结果,设计适合焦炉烟气处理的SDA脱硫+SCR脱硝装备。
3.装备制造:依据设计图纸和工艺要求,制造SDA脱硫+SCR脱硝技术装备。
4.现场安装:在焦炉现场安装SDA脱硫+SCR脱硝装置,并进行调试。
5.运行调试:启动设备,进行实际运行调试,优化运行参数。
6.验收评估:对SDA脱硫+SCR脱硝装置进行性能验收,确保装置正常运行并达到预期的减排效果。
四、适用范围此技术装备适用于焦炉、电厂、化工厂等产生高硫氧化物和氮氧化物废气的场所。
五、创新要点1.结合了SDA脱硫和SCR脱硝两种技术,实现了单一设备同时处理SOx和NOx。
2.采用了新型高效催化剂,提高了反应效率和设备运行稳定性。
3.装备设计紧凑,占地面积小,降低了建设成本。
4.装备自动化程度高,减少了人工操作和维护工作量。
六、预期效果1.减排效果:预计可实现SOx减排80%以上,NOx减排90%以上。
2.空气质量改善:减少污染物排放,改善当地空气质量。
3.环保合规:满足国家对污染物排放的限制要求,提高企业的环保合规性。
焦炉烟道气脱硫脱硝技术路线探讨
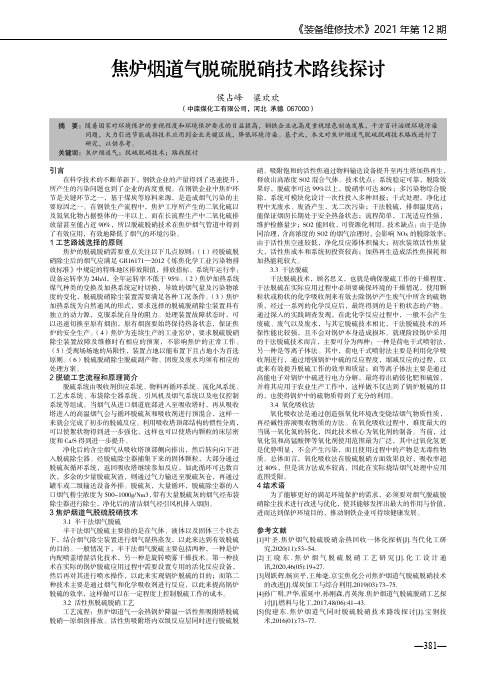
《装备维修技术》2021年第12期—381—焦炉烟道气脱硫脱硝技术路线探讨侯占峰梁欢欢(中滦煤化工有限公司,河北承德067000)摘要:随着国家对环境保护的重视程度和环境保护要求的日益提高,钢铁企业也高度重视绿色制造发展,千方百计治理环境污染问题,大力引进节能减排技术应用到企业关键区域,降低环境污染。
基于此,本文对焦炉烟道气脱硫脱硝技术路线进行了研究,以供参考。
关键词:焦炉烟道气;脱硫脱硝技术;路线探讨引言在科学技术的不断革新下,钢铁企业的产量得到了迅速提升,所产生的污染问题也到了企业的高度重视。
在钢铁企业中焦炉环节是关键环节之一,基于煤炭等原料来源,是造成烟气污染的主要原因之一。
在钢铁生产流程中,焦炉工序所产生的二氧化硫以及氮氧化物占据整体的一半以上,而在长流程生产中二氧化硫排放量甚至能占近90%,所以脱硫脱硝技术在焦炉烟气管道中得到了有效应用,有效地降低了烟气的环境污染。
1工艺路线选择的原则焦炉的脱硫脱硝需要重点关注以下几点原则:(1)经脱硫脱硝除尘后的烟气应满足GB16171—2012《炼焦化学工业污染物排放标准》中规定的特殊地区排放限值,排放指标。
系统年运行率:设备运转率为24h/d,全年运转率不低于95%。
(2)焦炉加热系统煤气种类的变换及加热系统定时切换,导致的烟气量及污染物浓度的变化,脱硫脱硝除尘装置需要满足各种工况条件。
(3)焦炉加热系统为自然通风的形式,要求选择的脱硫脱硝除尘装置具有独立的动力源,克服系统自身的阻力。
处理装置故障状态时,可以迅速切换至原有烟囱,原有烟囱要始终保持热备状态,保证焦炉的安全生产。
(4)焦炉为连续生产的工业窑炉,要求脱硫脱硝除尘装置故障及维修时有相应的预案,不影响焦炉的正常工作。
(5)受现场场地的局限性,装置占地以能布置下且占地小为首选原则。
(6)脱硫脱硝除尘脱硫副产物、固废及废水均须有相应的处理方案。
2脱硫工艺流程和原理简介脱硫系统由吸收剂供应系统、物料再循环系统、流化风系统、工艺水系统、布袋除尘器系统、引风机及烟气系统以及电仪控制系统等组成。
焦化厂焦炉烟气脱硫脱硝工艺技术分析
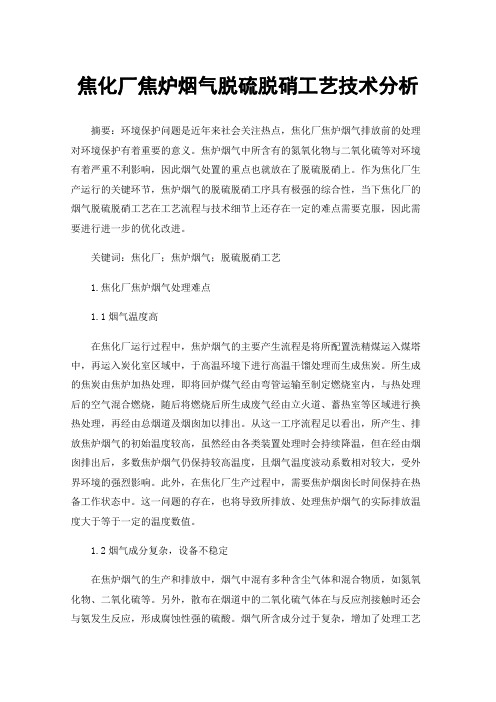
焦化厂焦炉烟气脱硫脱硝工艺技术分析摘要:环境保护问题是近年来社会关注热点,焦化厂焦炉烟气排放前的处理对环境保护有着重要的意义。
焦炉烟气中所含有的氮氧化物与二氧化硫等对环境有着严重不利影响,因此烟气处置的重点也就放在了脱硫脱硝上。
作为焦化厂生产运行的关键环节,焦炉烟气的脱硫脱硝工序具有极强的综合性,当下焦化厂的烟气脱硫脱硝工艺在工艺流程与技术细节上还存在一定的难点需要克服,因此需要进行进一步的优化改进。
关键词:焦化厂;焦炉烟气;脱硫脱硝工艺1.焦化厂焦炉烟气处理难点1.1烟气温度高在焦化厂运行过程中,焦炉烟气的主要产生流程是将所配置洗精煤运入煤塔中,再运入炭化室区域中,于高温环境下进行高温干馏处理而生成焦炭。
所生成的焦炭由焦炉加热处理,即将回炉煤气经由弯管运输至制定燃烧室内,与热处理后的空气混合燃烧,随后将燃烧后所生成废气经由立火道、蓄热室等区域进行换热处理,再经由总烟道及烟囱加以排出。
从这一工序流程足以看出,所产生、排放焦炉烟气的初始温度较高,虽然经由各类装置处理时会持续降温,但在经由烟囱排出后,多数焦炉烟气仍保持较高温度,且烟气温度波动系数相对较大,受外界环境的强烈影响。
此外,在焦化厂生产过程中,需要焦炉烟囱长时间保持在热备工作状态中。
这一问题的存在,也将导致所排放、处理焦炉烟气的实际排放温度大于等于一定的温度数值。
1.2烟气成分复杂,设备不稳定在焦炉烟气的生产和排放中,烟气中混有多种含尘气体和混合物质,如氮氧化物、二氧化硫等。
另外,散布在烟道中的二氧化硫气体在与反应剂接触时还会与氨发生反应,形成腐蚀性强的硫酸。
烟气所含成分过于复杂,增加了处理工艺的复杂程度与难度,且在长期针对含硫氨基酸的处理过程中,导致系统内各种设备发生了不同程度的腐蚀与损害,焦炉烟气中的各种污染物难以单独完成转化。
2.焦化企业烟气中脱硫脱硝的要求及原则相对于传统的燃煤锅炉和烧结机,焦炉的烟气排放排放量较小,但成分极其复杂,其中伴随着大量的和等污染物,这就要求在进行环境保护相关工艺设计时,要充分考虑到生产情况的各种变化,保证烟气排放达标,在焦炉烟气环保工作过程中,脱硫脱硝工作是重点。
冶金焦炉烟气脱硫脱硝工艺技术分析

冶金焦炉烟气脱硫脱硝工艺技术分析摘要:现阶段,由北京工业大学中科院、兰州物理研究所、中科院大连化物所等单位开发的低温催化剂,在焦炉企业实行的工业测试中,已经得到了证实,催化剂的性能能够满足脱硝的要求。
下面文章提出了一种SCR脱硫塔+除尘器+加热炉+SCR脱销的焦炉烟气治理工艺,脱硫脱硝设备纵向并列布置,以减小占地面积。
该工艺可以实现较高的脱硫脱硝效率,适应焦炉加煤出焦转换是烟气温度、成分波动大的问题,实现长期有效运行。
关键词:冶金;焦炉;烟气脱硫脱硝;工艺技术1 烟气脱硫工艺1.1 干法脱硫固体碱吸收剂在干燥和半干燥烟道气脱硫系统中主要是通过烟气穿透烟道气和吸收剂的方法来接触烟道气,其中的SO2无论是在何种环境下,都会发生一定反应进而生成亚硫酸盐与硫酸盐。
想要使反应速度加快,要保证固体碱松散或细小。
烟气脱硫系统中的烟气在半干法烟道中加入水,会有一种液膜形成在碱性物质颗粒的表面,然后加入SO2,能提高固体碱物质的反应速度,这种方法不会明显的腐蚀设备,也不存在排放污水情况,且气体排放中温度并未明显降低,让烟囱更易扩散与通风。
1.2 湿法脱硫在科学技术的不断成熟下,脱硫效率已明显高于95%。
其能回收利用副产品,运行成本较低,煤种适应性强,且产能较大。
同时由于石灰石湿法脱硫工艺所具有的吸收剂成本较低,所以,已在湿法脱硫领域中得到了广泛应用。
该工艺能对高浓度SO2处理要求进行充分满足,所具有的吸收剂利用率与脱硫率较高。
其缺点是脱硫废水具有腐蚀性,建设成本高,而最重要的一个问题就是需要持续对脱硫剂进行采买,而且难以处理副产品的亚硫酸钙。
通常而言,焦化厂会使用氨脱硫技术,其能有效将管道中的氧气去除,同时也能够对焦化厂回收车间处理系统进行充分利用,让两者相结合反应生成硫酸铵。
氨法脱硫一般使用液体吸收剂洗涤烟气除氧,该装置操作简单,具有很高的脱硫效率。
2 SCR脱硫塔+除尘器+加热炉+SCR脱销的焦炉烟气治理工艺2.1 工艺路线工艺流程如图1,所含主要设备包括:脱硫塔、除尘器、氨气、SCR脱硝反应塔、刮板机、循环风机。
焦炉烟道气脱硫脱硝技术研究
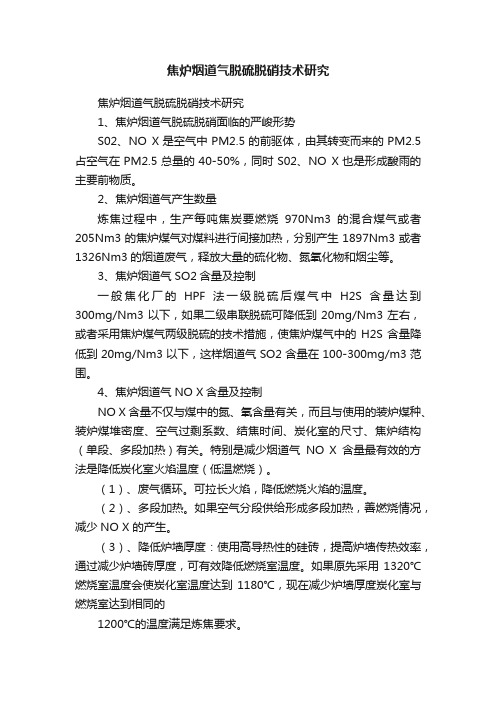
焦炉烟道气脱硫脱硝技术研究焦炉烟道气脱硫脱硝技术研究1、焦炉烟道气脱硫脱硝面临的严峻形势S02、NO X是空气中PM2.5的前驱体,由其转变而来的PM2.5占空气在PM2.5总量的40-50%,同时S02、NO X也是形成酸雨的主要前物质。
2、焦炉烟道气产生数量炼焦过程中,生产每吨焦炭要燃烧970Nm3的混合煤气或者205Nm3的焦炉煤气对煤料进行间接加热,分别产生1897Nm3或者1326Nm3的烟道废气,释放大量的硫化物、氮氧化物和烟尘等。
3、焦炉烟道气SO2含量及控制一般焦化厂的HPF法一级脱硫后煤气中H2S含量达到300mg/Nm3以下,如果二级串联脱硫可降低到20mg/Nm3左右,或者采用焦炉煤气两级脱硫的技术措施,使焦炉煤气中的H2S含量降低到20mg/Nm3以下,这样烟道气SO2含量在100-300mg/m3范围。
4、焦炉烟道气NO X含量及控制NO X含量不仅与煤中的氮、氧含量有关,而且与使用的装炉煤种、装炉煤堆密度、空气过剩系数、结焦时间、炭化室的尺寸、焦炉结构(单段、多段加热)有关。
特别是减少烟道气NO X含量最有效的方法是降低炭化室火焰温度(低温燃烧)。
(1)、废气循环。
可拉长火焰,降低燃烧火焰的温度。
(2)、多段加热。
如果空气分段供给形成多段加热,善燃烧情况,减少NO X 的产生。
(3)、降低炉墙厚度:使用高导热性的硅砖,提高炉墙传热效率,通过减少炉墙砖厚度,可有效降低燃烧室温度。
如果原先采用1320℃燃烧室温度会使炭化室温度达到1180℃,现在减少炉墙厚度炭化室与燃烧室达到相同的1200℃的温度满足炼焦要求。
(4)、调整加热燃气结构:尽量采用CO或者氮含量低的煤气作为加热燃料。
减少氮氧化物的生成。
(5)、降低炼焦温度:在保证焦炭成熟的条件下,调整焦炉加热制度,降低空气过剩系数,降低燃烧温度。
5、焦炉烟道气污染物排放限值标准为此国家于2012年颁布的GB16171-2012《炼焦化学工业污染物排放标准》规定2015年1月1日起现有企业执行限值标准,即焦炉烟道气排放限值执行:S02≤50mg/m3,NO X≤500mg/m3。
焦化厂焦炉烟气脱硫脱硝工艺技术分析
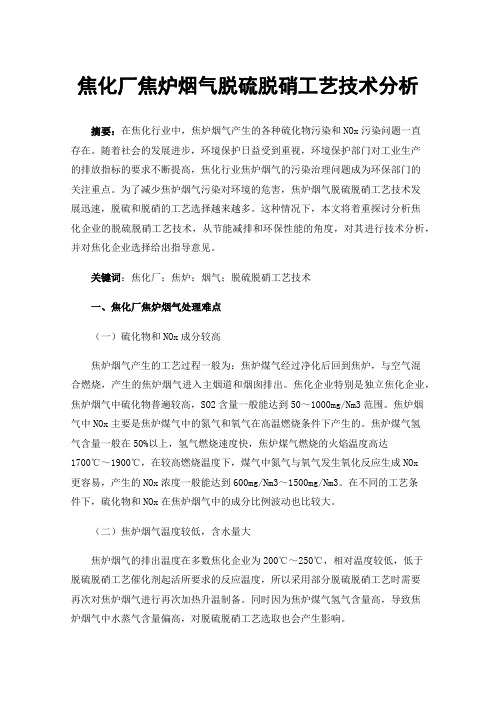
焦化厂焦炉烟气脱硫脱硝工艺技术分析摘要:在焦化行业中,焦炉烟气产生的各种硫化物污染和NOx污染问题一直存在。
随着社会的发展进步,环境保护日益受到重视,环境保护部门对工业生产的排放指标的要求不断提高,焦化行业焦炉烟气的污染治理问题成为环保部门的关注重点。
为了减少焦炉烟气污染对环境的危害,焦炉烟气脱硫脱硝工艺技术发展迅速,脱硫和脱硝的工艺选择越来越多。
这种情况下,本文将着重探讨分析焦化企业的脱硫脱硝工艺技术,从节能减排和环保性能的角度,对其进行技术分析,并对焦化企业选择给出指导意见。
关键词:焦化厂;焦炉;烟气;脱硫脱硝工艺技术一、焦化厂焦炉烟气处理难点(一)硫化物和NOx成分较高焦炉烟气产生的工艺过程一般为:焦炉煤气经过净化后回到焦炉,与空气混合燃烧,产生的焦炉烟气进入主烟道和烟囱排出。
焦化企业特别是独立焦化企业,焦炉烟气中硫化物普遍较高,SO2含量一般能达到50~1000mg/Nm3范围。
焦炉烟气中NOx主要是焦炉煤气中的氮气和氧气在高温燃烧条件下产生的。
焦炉煤气氢气含量一般在50%以上,氢气燃烧速度快,焦炉煤气燃烧的火焰温度高达1700℃~1900℃,在较高燃烧温度下,煤气中氮气与氧气发生氧化反应生成NOx更容易,产生的NOx浓度一般能达到600mg/Nm3~1500mg/Nm3。
在不同的工艺条件下,硫化物和NOx在焦炉烟气中的成分比例波动也比较大。
(二)焦炉烟气温度较低,含水量大焦炉烟气的排出温度在多数焦化企业为200℃~250℃,相对温度较低,低于脱硫脱硝工艺催化剂起活所要求的反应温度,所以采用部分脱硫脱硝工艺时需要再次对焦炉烟气进行再次加热升温制备。
同时因为焦炉煤气氢气含量高,导致焦炉烟气中水蒸气含量偏高,对脱硫脱硝工艺选取也会产生影响。
(三)焦炉烟气杂质较多烟气中的组分复杂,焦油等物质在较低的烟气温度下进入脱硫脱硝系统,容易凝结在脱硫脱硝系统设备中,污染催化剂,堵塞系统气路,造成系统阻力增加,反应效率下降。
焦炉烟气SDS脱硫脱硝技术探讨

张超,叶昊,严大群:焦炉烟气SDS脱硫脱硝技术探讨焦炉烟气SDS脱硫脱硝技术探讨张超,叶昊,严大群(江苏科行环保股份有限公司,江苏盐城224051)摘要:SDS脱硫除尘技术在140益以上低硫烟气工况下具有较好的脱硫效率,可实现SO2的超低排放;中低温SCR催化剂具备在160~400益间低硫工况下NO X超低排放条件。
以上两种技术的组合实现了焦炉烟道气脱硫脱硝除尘超低排放改造的目标。
对野SDS脱硫除尘+中低温SCR脱硝冶技术的探讨,可为后续项目提供参照,更可扩展到其他行业相似工况。
关键词:焦炉烟气;干法脱硫;催化剂热解析;脱硝Abstract:SDS desulfurization and dust technology has good desulfurization efficiency under the condition of low sulfur flue gas at the temperature above140益and can achieve ultra-low emission of SO2.Under the condition of low sulfur flue gas at the temperature between160益and400益,the SCR catalyst at medium-low temperature can achieve ultra-low emission of NOx.The combination of the above two technologies can achieve the goal of ultra-low emission transformation of coke oven flue gas'desulfurization,denitrification and dust removal.The discussion on the"SDS desulfurization and dust removal combined with medium-low temperature SCR denitrification"technology provides a reference for subsequent projects and can also be extended and applied to similar working conditions in other industries.Key words:coke oven flue gas;dry desulfurization;catalyst thermal analysis;denitration[中图分类号]X701.3[文献标识码]B[文章编号]1004-5538(2021)02-0009-030引言近年来国家环保要求趋严,焦炉烟气排嗷需达到《炼焦化学工业污染物排放标准》(GB16171—2012)中的特别排放限值要求,即NOx臆150mg/Nm3、S02臆30mg/Nm3、粉尘臆15mg/Nm3o目前,焦炉烟道气常用环保治理工艺为“中低温SCR脱硝+余热回收+氨法脱硫+(消白)+烟囱直排”,该工艺存在脱硫塔腐蚀、脱硝效率衰减、余热锅炉阻力异常等问题,影响焦炉正常生产。
焦化厂脱硫脱硝技术探讨

焦化厂脱硫脱硝技术探讨摘要:为及早贯彻落实焦化厂焦炉烟气“近零排放”处理目标,实现人与自然的和谐共处,提高生态环境防治力度与污染源控制力度。
各焦化厂必须分析总结当前应用的各项焦炉烟气脱硫脱硝工艺技术,采取各项技术优化措施,不断改进工艺流程,为烟气脱硫脱硝工作的有序开展提供前提基础与技术支持。
关键词:焦化厂;脱硫脱硝技术1焦炉烟气概述焦炉的生产方式较为特殊,焦炉所排出的烟雾中含有各种混合物和气体,其中含量较多的就是氮化物和氧化物,因此这些气体需要经过脱硫脱硝处理后才能排出室外。
焦炉烟气内部含有的二氧化碳会在高温燃烧后形成,焦炉内部由于氢气体积较大致使燃烧速度较快,在燃烧过程中氧气与氮气会在高温作用下产生氧化反应形成二氧化氮。
结合实际情况来进行分析,焦炉内部烟气有以下几种特点。
首先,烟气温度始终保持在250℃左右。
其次,焦炉烟气成分构造非常复杂,在焦炉排出烟气中二氧化硫的成分最高,浓度保持在300mg/Nm3,焦炉烟气中的二氧化硫会与氨元素产生硫氨酸,加速管道腐蚀。
最后,焦炉烟气温度较高,因此需要焦炉管道处于受热准备中。
焦炉烟气在脱硫脱硝之后需要将烟气温度保持在100℃左右,在焦炉烟气脱硝过程中需要对脱硝系统进行调试,保证系统在正常状况下进行脱硝。
另外,相关人员还需重视烟气脱硫脱硝过程中的安全因素,使焦炉能够稳定生产,为工作人员提供安全可靠的工作环境。
2焦化厂主要焦炉烟气脱硫工艺技术2.1干法脱硫工艺技术(1)干法脱硫工艺技术原理。
将碳酸钙喷入炉膛内高温煅烧,随后将其分解为氧化钙,氧化钙再与所处理焦炉烟气中所分布的二氧化硫发生化学反应,持续生成硫酸钙;或是结合实际情况采用活性炭吸附抑或电子束照射等方法,将烟气中所分布二氧化硫转化为硫酸或是硫酸氨,这一处理工艺也被称作干法脱硫工艺技术。
(2)干法脱硫工艺主要特点。
可将这一工艺细分为半干法及干法烟气脱硫工艺。
不论采用哪项工艺,所处理焦炉烟气在与固体碱性吸收剂接触过程中,烟气所含有二氧化硫都将会与固体碱性吸收剂产生物质反应,进而持续转化生成硫酸盐。
柳钢焦炉烟气脱硫脱硝技术应用探究
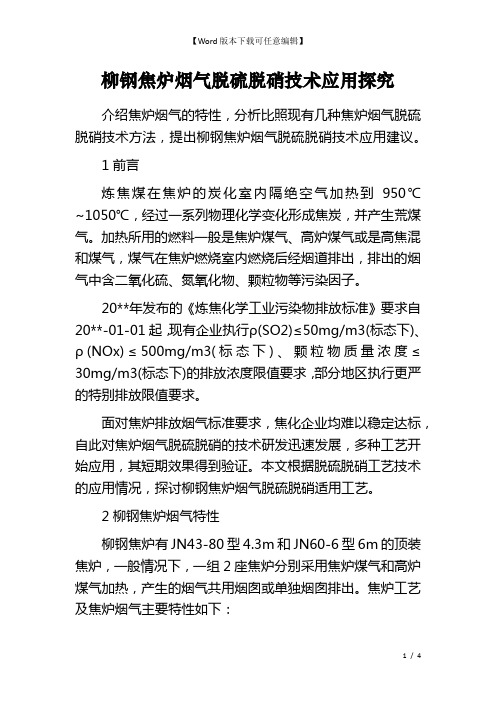
柳钢焦炉烟气脱硫脱硝技术应用探究介绍焦炉烟气的特性,分析比照现有几种焦炉烟气脱硫脱硝技术方法,提出柳钢焦炉烟气脱硫脱硝技术应用建议。
1前言炼焦煤在焦炉的炭化室内隔绝空气加热到950℃~1050℃,经过一系列物理化学变化形成焦炭,并产生荒煤气。
加热所用的燃料一般是焦炉煤气、高炉煤气或是高焦混和煤气,煤气在焦炉燃烧室内燃烧后经烟道排出,排出的烟气中含二氧化硫、氮氧化物、颗粒物等污染因子。
20**年发布的《炼焦化学工业污染物排放标准》要求自20**-01-01起,现有企业执行ρ(SO2)≤50mg/m3(标态下)、ρ(NOx)≤500mg/m3(标态下)、颗粒物质量浓度≤30mg/m3(标态下)的排放浓度限值要求,部分地区执行更严的特别排放限值要求。
面对焦炉排放烟气标准要求,焦化企业均难以稳定达标,自此对焦炉烟气脱硫脱硝的技术研发迅速发展,多种工艺开始应用,其短期效果得到验证。
本文根据脱硫脱硝工艺技术的应用情况,探讨柳钢焦炉烟气脱硫脱硝适用工艺。
2柳钢焦炉烟气特性柳钢焦炉有JN43-80型4.3m和JN60-6型6m的顶装焦炉,一般情况下,一组2座焦炉分别采用焦炉煤气和高炉煤气加热,产生的烟气共用烟囱或单独烟囱排出。
焦炉工艺及焦炉烟气主要特性如下:(1)烟气温度较低,并且因焦炉炉型不同、热工效率不同、加热煤气种类不同,烟气温度有较大差异。
焦炉烟气温度一般为180℃~250℃,相较于当前成熟的SCR脱硝工艺所需烟气温度来讲,该温度偏低。
(2)焦炉烟气中SO2质量浓度一般为30~500mg/m3(标态下),相较于其它烟气如烧结、燃煤发电等烟气,其SO2浓度比较低。
SO2浓度主要与所用煤气中硫含量以及焦炉串漏、炼焦煤中硫含量等有关。
(3)焦炉烟气中NOx浓度一般为350~1000mg/m3(标态下),浓度比较高。
NOx浓度主要与焦炉构造、加热制度、加热煤气种类有关。
(4)焦炉烟气中的SO2、NOx浓度随生产呈周期性变化且浓度含量的波峰和波谷差值较大。
【硫老师】几种焦炉烟气脱硫脱硝技术详解

【硫老师】几种焦炉烟气脱硫脱硝技术详解关键词:低温脱硝焦炉烟气有机催化一、碳酸钠半干法脱硫+低温脱硝一体化工艺;二、加热焦炉烟气 +高温催化还原脱硝工艺;三、SICS法催化氧化(有机催化法)脱硫脱硝工艺;四、活性炭/焦脱硫脱硝工艺;碳酸钠半干法脱硫+低温脱硝一体化工艺1.脱硫脱硝原理采用半干法脱硫工艺,使用Na2CO3溶液为脱硫剂,其化学反应式为:Na2CO3+SO2→Na2SO3+CO2(1)2Na2SO3+O2→2Na2SO4(2)脱硝采用NH3-SCR法,即在催化剂作用下,还原剂NH3选择性地与烟气中NOx反应,生成无污染的N2和H2O随烟气排放,其化学反应式如下:4NO+4NH3+O2→4N2+6H2O (3)2.工艺流程焦炉烟气被引风机引入工艺系统,先脱硫除SO2,后除尘脱硝,再脱除颗粒物和NOx,最后经引风机增压回送至焦炉烟囱根部(见图1)。
图1 SICS法催化氧化(有机催化法)脱硫脱硝工艺流程示意该工艺主要由以下系统组成:脱硫系统由脱硫塔及脱硫溶液制备系统组成。
Na2CO3溶液通过定量给料装置和溶液泵送到脱硫塔内雾化器中,形成雾化液滴,与SO2发生反应进行脱硫,脱硫效率可达90%。
脱硫剂喷入装置与系统进出口SO2浓度联锁,随焦炉烟气量及SO2浓度的变化自动调整脱硫剂喷入量。
核心设备为烟气除尘、脱硝及其热解析一体化装置,包括由下至上集成在一个塔体内的除尘净化段、解析喷氨混合段和脱硝反应段。
氨系统负责为烟气脱硝提供还原剂,可使用液氨或氨水蒸发为氨气使用。
热解析系统负责为脱硝装置内的催化剂提供380-400℃高温解析气体,分解黏附在催化剂表面的硫酸氢铵,净化催化剂表面。
3.工艺特点①半干法脱硫设置在脱硝前,将烟气中的SO2含量脱除至30mg/Nm3以下,以保证后续的高效脱硝。
②烟气脱硫、除尘、脱硝、催化剂热解析再生一体化,节省投资、运行费用低、占地面积少。
③脱硝前先除尘,以减少粉尘对催化剂的磨损、延长催化剂使用寿命。
焦炉烟道废气脱硫脱硝治理技术

in o当代化工研究丄U D Modmi Chemical R嘶aFch环境工程2021・09焦炉烟道废气脱硫脱硝治理技术*胡明亮(山西焦煤集团五麟煤焦开发有限责任公司山西032200)摘要:本文主要分析了焦炉烟道废气中常见的脱硫、脱硝技术,重点介绍了脱硫脱硝联合治理技术,它不仅能够有效降低焦炉烟道废气中SO?和叫浓度,而且还可以达到生态环保的要求。
通过对焦炉烟道废气脱硫脱硝技术进行研究,以期为焦炉的安全生产提供可靠的保障,创造出最大化的经济与社会效益。
关键词:焦炉烟道废气;脱硫;脱硝中图分类号:TQ520文献标识码:ADesulfurization and Denitration Treatment Technology of Coke Oven Flue GasHu Mingliang(Wulin Coal Coke Development Co.?Ltd.,Shanxi Coking Coal Group,Shanxi,032200) Abstracts This paper mainly analyzes the common desulfurization and denitration technologies in coke oven flue gas,and emphatically introduces the combined treatment technology of d esulfurization and denitration,which can not only effectively reduce the concentration of S O2and NO x in coke oven f lue gas,but also meet the requirements of e cological environment p rotection.Through the research of f lue gas desulfurization and denitration technology of coke oven,it can provide reliable guarantee for safe production of coke oven and create maximum economic and social benefits.Key words:flue gas of c oke oven;desulfurization ;denitration在《炼焦化学工业污染物排放标准》(GB16171-2012)中明确规定了焦炉烟道废气中污染物排放浓度,其要求:S02^50mg/m3,N0x^500mg/m3,当然一些特殊地区执行特别排放限值,即S02^30mg/m3,N0x^150mg/m3o虽然现有电厂具有比较成熟的脱硫脱硝技术,然而因为焦炉烟道废气具有特殊性,无法将电厂常用的脱硫脱硝技术引入到焦炉烟道废气治理中。
焦化厂焦炉烟气脱硫脱硝工艺技术分析
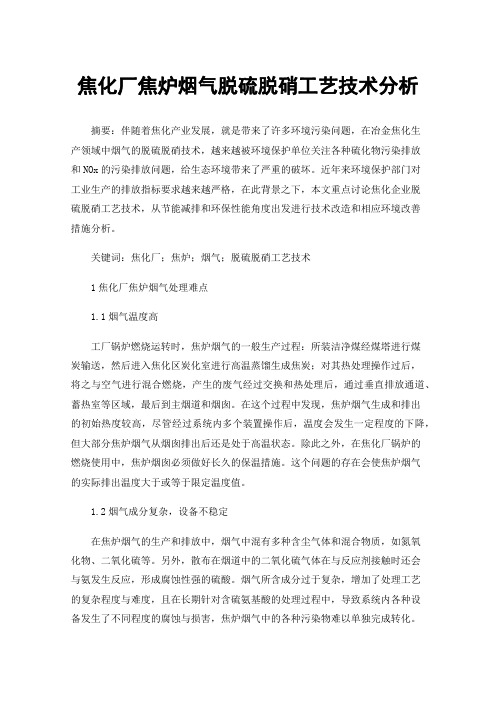
焦化厂焦炉烟气脱硫脱硝工艺技术分析摘要:伴随着焦化产业发展,就是带来了许多环境污染问题,在冶金焦化生产领域中烟气的脱硫脱硝技术,越来越被环境保护单位关注各种硫化物污染排放和NOx的污染排放问题,给生态环境带来了严重的破坏。
近年来环境保护部门对工业生产的排放指标要求越来越严格,在此背景之下,本文重点讨论焦化企业脱硫脱硝工艺技术,从节能减排和环保性能角度出发进行技术改造和相应环境改善措施分析。
关键词:焦化厂;焦炉;烟气;脱硫脱硝工艺技术1焦化厂焦炉烟气处理难点1.1烟气温度高工厂锅炉燃烧运转时,焦炉烟气的一般生产过程:所装洁净煤经煤塔进行煤炭输送,然后进入焦化区炭化室进行高温蒸馏生成焦炭;对其热处理操作过后,将之与空气进行混合燃烧,产生的废气经过交换和热处理后,通过垂直排放通道、蓄热室等区域,最后到主烟道和烟囱。
在这个过程中发现,焦炉烟气生成和排出的初始热度较高,尽管经过系统内多个装置操作后,温度会发生一定程度的下降,但大部分焦炉烟气从烟囱排出后还是处于高温状态。
除此之外,在焦化厂锅炉的燃烧使用中,焦炉烟囱必须做好长久的保温措施。
这个问题的存在会使焦炉烟气的实际排出温度大于或等于限定温度值。
1.2烟气成分复杂,设备不稳定在焦炉烟气的生产和排放中,烟气中混有多种含尘气体和混合物质,如氮氧化物、二氧化硫等。
另外,散布在烟道中的二氧化硫气体在与反应剂接触时还会与氨发生反应,形成腐蚀性强的硫酸。
烟气所含成分过于复杂,增加了处理工艺的复杂程度与难度,且在长期针对含硫氨基酸的处理过程中,导致系统内各种设备发生了不同程度的腐蚀与损害,焦炉烟气中的各种污染物难以单独完成转化。
2焦化厂主要焦炉烟气脱硫技术2.1干法脱硫技术干法脱硫工艺技术原理:碳酸钙固体在高温下喷入炉中进行锻造和燃烧,反应生成氧化钙,后与焦炉烟气中的二氧化硫发生化学反应转化为硫酸钙。
或根据焦化厂的具体情况,通过活性炭吸附或电子束辐照的方式,将烟气中的二氧化硫转化成硫酸或硫酸铵,该工艺也称为干法脱硫技术。
- 1、下载文档前请自行甄别文档内容的完整性,平台不提供额外的编辑、内容补充、找答案等附加服务。
- 2、"仅部分预览"的文档,不可在线预览部分如存在完整性等问题,可反馈申请退款(可完整预览的文档不适用该条件!)。
- 3、如文档侵犯您的权益,请联系客服反馈,我们会尽快为您处理(人工客服工作时间:9:00-18:30)。
焦炉烟道气脱硫脱硝技术研究
1、焦炉烟道气脱硫脱硝面临的严峻形势
S02、NO X是空气中PM2.5的前驱体,由其转变而来的PM2.5占空气在PM2.5总量的40-50%,同时S02、NO X也是形成酸雨的主要前物质。
2、焦炉烟道气产生数量
炼焦过程中,生产每吨焦炭要燃烧970Nm3的混合煤气或者
205Nm3的焦炉煤气对煤料进行间接加热,分别产生1897Nm3或者1326Nm3的烟道废气,释放大量的硫化物、氮氧化物和烟尘等。
3、焦炉烟道气SO2含量及控制
一般焦化厂的HPF法一级脱硫后煤气中H2S含量达到300mg/Nm3以下,如果二级串联脱硫可降低到20mg/Nm3左右,或者采用焦炉煤气两级脱硫的技术措施,使焦炉煤气中的H2S含量降低到20mg/Nm3以下,这样烟道气SO2含量在100-300mg/m3范围。
4、焦炉烟道气NO X含量及控制
NO X含量不仅及煤中的氮、氧含量有关,而且及使用的装炉煤种、装炉煤堆密度、空气过剩系数、结焦时间、炭化室的尺寸、焦炉结构(单段、多段加热)有关。
特别是减少烟道气NO X含量最有效的方法是降低炭化室火焰温度(低温燃烧)。
(1)、废气循环。
可拉长火焰,降低燃烧火焰的温度。
(2)、多段加热。
如果空气分段供给形成多段加热,善燃烧情况,减少NO X的产生。
(3)、降低炉墙厚度:使用高导热性的硅砖,提高炉墙传热效率,通过
减少炉墙砖厚度,可有效降低燃烧室温度。
如果原先采用1320℃燃烧室温度会使炭化室温度达到1180℃,现在减少炉墙厚度炭化室及燃烧室达到相同的1200℃的温度满足炼焦要求。
(4)、调整加热燃气结构:尽量采用CO或者氮含量低的煤气作为加热燃料。
减少氮氧化物的生成。
(5)、降低炼焦温度:在保证焦炭成熟的条件下,调整焦炉加热制度,降低空气过剩系数,降低燃烧温度。
5、焦炉烟道气污染物排放限值标准
为此国家于2012年颁布的GB16171-2012《炼焦化学工业污染物排放标准》规定2015年1月1日起现有企业执行限值标准,即焦炉烟道气排放限值执行:S02≤50mg/m3,NO X≤500mg/m3。
依据国家环境保护部2013年第14号文件”关于执行大气污染物特别批复限值的公告”:按照国务院批复实施的《重点区域大气污染物防治“十三五”规划》的相关要求,重点地区:京津冀、长三角、珠三角、三区十群19个省(区、市)47个地级及以上城市,十三五期间焦炉烟道气排放限值执行:S02≤30mg/m3,NO X≤150mg/m3。
重点控制区范围
6、焦炉烟道气的特点分析
目前在国内外焦化领域,针对焦炉烟道气脱硫脱硝技术尚处于研究阶段。
但是NH3-SCR脱硝技术已广泛应用于电厂、玻璃、水泥等烟气脱硝,其全国80%电厂烟气采用NH3-SCR脱硝技术,及电厂烟气相比,焦炉烟道气具有以下特点:
(1)、焦炉烟道气温度相对较低
一般在烟道气温度在250℃左右,如果采用高炉煤气加热温度更低在200℃左右。
如果在烟道气温度250℃情况下,采用电厂烟道气的NH3-SCR脱硝技术,则脱硝效率很低,无法满足烟道气排放标准要求。
(2)、烟道气杂质较多
烟道气含有的CO、焦油、SO2等物质,可导致催化剂中毒或者效率降低,特别是SO2含量影响:在SCR催化剂作用下,焦炉烟气SO2会转化为SO3,氨及SO3反应产生硫酸铵,粘附在催化剂表面,影响催化剂使用效率。
(3)、焦炉烟囱必须保持一定的吸力状态
经过脱硫脱硝工艺,加热焦炉烟囱以后再排入大气,使焦炉烟囱始终处于热备用状态。
经过脱硫脱硝后烟道气温度必须高于烟气露点温度,即烟道气温度低不于130℃,以保持烟囱吸力,维持焦炉正常生产。
7、焦化行业烟道气脱硫方法
一般烟道气脱硫可分为:湿法脱硫、干法脱硫、半干法脱硫三大类。
(1)、石灰石-石膏法
将石灰石制成水浆液,在吸收塔内进行,及烟道气接触生产硫酸钙。
副产品是CaSO4。
此脱硫效率达到95%以上,技术成熟,运行费用高,占地面积大,易堵塞现象。
(2)、双碱法
采用Na2CO3溶液吸收烟道气中的SO2,吸收后有CaO再生,最终产品是石膏,产品不纯。
严重影响石膏质量,一般作为废品处理掉。
形成二次污染。
这是双碱法最大的缺点。
主要优点是:对设备管道无腐蚀、堵塞问题,吸收速度快,效率高90%,工艺成熟。
(3)、氨法
采用氨水作为吸收剂,转化为硫酸铵化肥的湿法烟道气脱硫工艺。
此工艺不产生废水、废液、废渣二次污染,可利用焦化厂的氨水,生产硫铵可及饱和器的硫铵系统共同处理。
(4)、活性焦法
活性焦具有活性炭的特点,吸附SO2,然后通过加热再生,释放高浓度的SO2,可生产单质硫、硫酸等化工产品。
(5)、半干式旋转喷雾法
将CaO制浆作为吸收剂,经过高速旋转雾化喷入烟道气中及SO2发生反应,此工艺中冶焦耐和安徽同兴环保在湛江钢铁公司开始建设。
(6)、半干式Ca(OH)2法
将CaO制浆作为吸收剂,比石膏法简单,投资小,脱硫效率低
70-80%。
产生二次污染。
(7)、氨-镁联合法
利用氨水和氧化镁联合吸收,脱出SO2。
一级采用氧化镁吸收,产生硫酸镁溶液,烟气再经过脱炭塔(取5-30%烟道气进行脱碳)后,CO2及氨水吸收后转会为碳酸氢铵。
此工艺上海交通大学支持,在山西海姿开始建设。
8、我国焦炉烟道气脱硫脱硝一体化工艺技术
(1)、低温脱硫脱硝一体化工艺。
由中冶焦耐设计供货(EP)的宝钢湛江钢铁焦化项目焦炉烟气净化设施正式投产,标志着世界首套焦炉烟气低温脱硫脱硝工业化示范装置正式诞生。
先进行烟气脱硫,后除尘,然后低温SCR脱硝,实现污染物达标排放,该项目采用碳酸钠半干法脱硫+低温脱硝一体化工艺:采用碳酸钠作为半干法脱硫工艺,脱硝采用NH3-SCR工艺。
投资费用:35-40元/吨焦,操作费用:12.6元/吨焦。
2x65孔7m焦炉烟道气-51.7万m3/h。
烟道气采用中冶焦耐开发总承包的(EPC项目):碳酸钠烟道气脱硫+颗粒物回收+烟道气小幅提升+低温度选择性催化还原法(SCR)脱硝工艺。
设计值烟道气温度180℃,入口SO2含量100mg/Nm3,NOx含量500mg/Nm3,出口SO2含量≤30mg/Nm3,NOx含量≤150mg/Nm3,颗粒物含量≤
15mg/Nm3。
脱硫采用半干法脱硫工艺,使用Na2CO3溶液为脱硫剂,其化学反应为: Na2CO3 SO2→Na2SO3 CO2(1)
2Na2SO3 O2→2Na2SO4(2)
脱硝采用NH3-SCR法,即在催化剂作用下,还原剂NH3选择性地及烟气中NOx反应,生成无污染的N2和H2O随烟气排放,其化学反应式如下:
4NO +4NH3+ O2→4N2+6H2O (3)
(2)、加热焦炉煤气+高温催化还原脱硝工艺(高温脱硝)烟道气通过换热器或者加热方式将焦炉烟道气生温到320℃,采用高温催化剂还原脱硝,主要设备有:GGH换热器、烟道气家热炉、余热锅炉、SCR反应器、氨站等组成。
(3)、SICS法催化氧化脱硫脱硝工艺
SO2吸收机理:吸收剂为氨水,烟道气脱硫吸收反应生产硫酸铵化肥;
NOx吸收机理:加入强氧化剂(臭氧),生产NH4NO3化肥。
Hg吸收机理:煤燃烧后形成的产物,Hg吸收是把KHgI3、和K2HgI4两种沟通物质吸收到催化剂有机物中,如果催化剂吸收饱和,通过化学洗涤方式使催化剂再生。
(4)、活性碳脱硫脱硝工艺
采用新型吸附材料,吸附SO2、NO x。
工艺流程是:焦炉烟道气---余热锅炉--活性炭反应器--引风机--烟囱排放。
活性炭再生采用加热400℃解析出SO2,脱硝原理同低温脱硝。
(5)、活性焦干法脱硫脱硝工艺
原理及活性炭脱硫脱硝原理相同。
几种焦炉烟道气脱硫脱硝工艺技术比较
项目低温SCR
(脱硫脱
硝)高温SCR
(只脱硝)
SICS
(脱硫脱
硝)
活性炭
(脱硫脱
硝)
活性焦
(脱硫脱
硝)
催化剂低温催化
剂高温催化
剂
进口催化
剂
活性炭活性焦
吸收剂脱硫剂:碳
酸钠
还原剂:
NH3还原剂
-NH3
氧化剂-臭
氧
吸附剂-活
性炭
还原剂:
NH3
吸附剂-活
性焦
还原剂:
NH3
副产品碳酸钠硫铵、硝铵SO2SO2
结论:
焦炉烟道气脱硫脱硝是一个新课题,目前国内外没有一家焦化企业有稳定运行的实践经验和业绩,当前研究的公司很多,提出的方法也很多,只有在全面分析工艺原理、实践结果、操作要求、流程设备的基础上,才能找出切实可行、经济适用的处理方法。
11 / 11。