焦炉烟道气脱硝系统氨气化工艺的比较
工艺方法——焦炉烟气脱硫脱硝工艺

工艺方法——焦炉烟气脱硫脱硝工艺工艺简介由备煤车间来的洗精煤,由运煤通廊运入煤塔,由煤塔漏嘴经装煤车按序装入炭化室,在950-1050度的温度下高温干馏成焦炭。
焦炉加热用回炉煤气由外管送至焦炉各燃烧室,在燃烧室内与经过蓄热室预热的空气混合燃烧,燃烧后的废气经跨越孔、立火道、斜道,在蓄热室与格子砖换热后经分烟道、总烟道,最后从烟囱排出。
焦炉因其生产工艺的特殊性,烟囱排放的热烟气中含二氧化硫、氮氧化物、粉尘,氮氧化物含量较高,烟气需进行脱硫脱硝除尘处理后方可满足排放要求。
烟气中NOx主要是在煤气高温燃烧条件下产生的,焦炉煤气含50%以上的氢气,燃烧速度快,火焰温度高达1700-1900度,煤气中氮气与氧气在1300度左右会发生激烈的氧化反应,生成NOx。
1、脱硫技术烟气中的SO2是弱酸性物质,与适当的碱性物质反应可脱除烟气中SO2。
按照吸收剂的形态,目前脱硫工艺一般可分为干法(半干法)和湿法。
干法脱硫:主要是采用粉末状脱硫剂和催化脱硫剂,干法脱硫的优势是不产生废水;半干法脱硫:主要是采用碳酸钠或石灰溶液作为脱硫剂,优势是不产生废水,但会产生大量固废脱硫渣,不太容易处理;湿法脱硫:主要采用是氨法脱硫,氨法脱硫的主要问题是产生氨逃逸,且容易产生烟气溶胶和烟气拖尾现象。
干法(半干法)脱硫工艺特点:在干法和半干法烟道气脱硫系统中,固体碱性吸收剂被喷入烟道气流中,或通过让烟气穿过碱性吸收剂床的方式使其与烟道气相接触。
无论哪种情况,烟气中的SO2都是与固体碱性物质反应,生成相应的亚硫酸盐和硫酸盐。
为了使这种反应能够进行,固体碱性物质必须是十分疏松或相当细碎。
在半干法烟道气脱硫系统中,水被加入到烟道气中,以在碱性物质颗粒物表面形成一层液膜,SO2溶入液膜,加速了与固体碱性物质的反应。
干法脱硫技术的脱硫吸收和产物处理均在干状态下进行,该法具有无污水废酸排出、设备腐蚀程度较轻,烟气在净化过程中无明显降温、净化后烟温高、利于烟囱排气扩散等优点,但存在脱硫效率低、脱硫剂利用率低、反应速度较慢、设备庞大、反应后烟气含尘量大需要增加除尘装置等问题。
焦炉烟气脱硫脱硝工艺简介
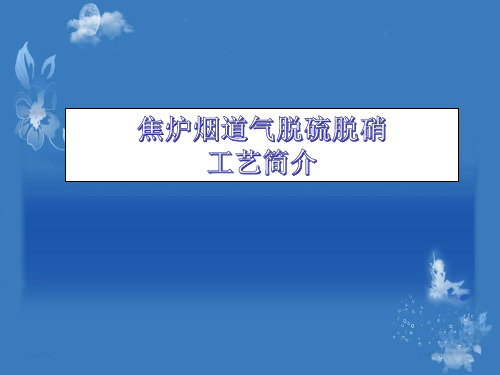
工艺简介
• 热解单元:燃气热风炉将单元内的SCR催 化剂加热至360℃~400℃,对单元内的 SCR催化剂进行热解再生,去除催化剂表 面粘结的硫酸氢铵。 • 催化单元:催化氨气选择性与氮氧化物反 应,达到脱硝效果。
除尘脱硝一体化装置(宝钢湛江钢铁)
催化反应段
混合段
烟气入口管道 烟气分配口
除尘段Βιβλιοθήκη SCR脱硝工艺简介4、工艺目标
• 净化焦炉烟道气(主要指NOx、SO2和颗粒物等污染物),
满足环保要求;回收烟气余热,节能减耗。 • 执行标准---《中华人民共和国环境保护法》(最新版) 、《炼焦化学工业污染物排放标准》(GB16171-2012) 。 • 最终净化效果:烟气排放指标达到NOx<150 mg/Nm3、SO2 <30 mg/Nm3、颗粒物<15 mg/Nm3,并要求装置预留处理 空间,确保烟气指标能达到NOx<50 mg/Nm3、SO2<30
平衡罐
雾化器电机
顶罐
脱硫灰
半干法脱硫工艺特点
1、SDA脱硫技术优点
(1)脱除SO2效率同样可达90%以上; (2)SO3几乎全部去除,不需防腐; (3)系统非常简单,可用率和可靠性高; (4)不产生污水,且可以用低质量的水,如河水、海水及其它工艺废水 (5)占地面积小,投资费用低;
2.SDA脱硫技术缺点:
mg/Nm3、颗粒物<10 mg/Nm3。
二、工艺分解
1、半干法脱硫(SDA喷雾干燥脱硫技术,
含脱硫溶液制备系统); 2、SCR低温烟气脱硝(含布袋除尘); 3、余热锅炉; 4、相关公辅系统;
三、工艺介质及作用
1、压缩空气:
(1)脉冲吹扫 (2)气动阀门
2、氮气:
(1)热风炉系统保压、置换 (2)氨气系统置换 3、蒸汽: (1)加热水箱加热用 (2)溶液管道吹扫、溶液罐保温 4、工艺水: (1)冷却水 (2)反冲洗 (3)配制溶液
焦炉烟道气脱硫脱硝工艺的选择
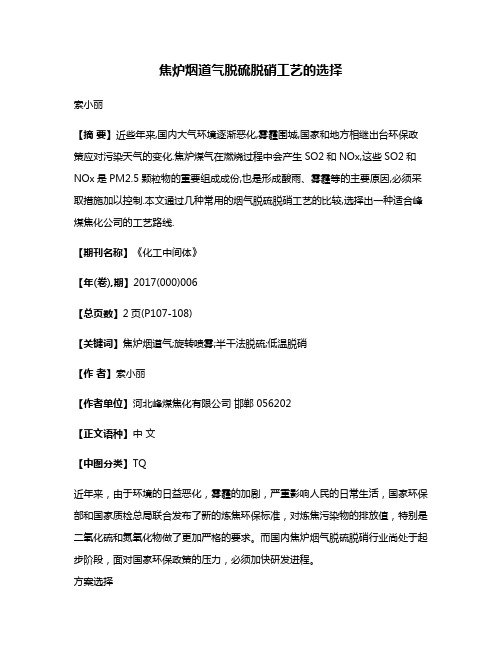
焦炉烟道气脱硫脱硝工艺的选择索小丽【摘要】近些年来,国内大气环境逐渐恶化,雾霾围城,国家和地方相继出台环保政策应对污染天气的变化.焦炉煤气在燃烧过程中会产生SO2和NOx,这些SO2和NOx是PM2.5颗粒物的重要组成成份,也是形成酸雨、雾霾等的主要原因,必须采取措施加以控制.本文通过几种常用的烟气脱硫脱硝工艺的比较,选择出一种适合峰煤焦化公司的工艺路线.【期刊名称】《化工中间体》【年(卷),期】2017(000)006【总页数】2页(P107-108)【关键词】焦炉烟道气;旋转喷雾;半干法脱硫;低温脱硝【作者】索小丽【作者单位】河北峰煤焦化有限公司邯郸 056202【正文语种】中文【中图分类】TQ近年来,由于环境的日益恶化,雾霾的加剧,严重影响人民的日常生活,国家环保部和国家质检总局联合发布了新的炼焦环保标准,对炼焦污染物的排放值,特别是二氧化硫和氮氧化物做了更加严格的要求。
而国内焦炉烟气脱硫脱硝行业尚处于起步阶段,面对国家环保政策的压力,必须加快研发进程。
方案选择峰煤焦化公司现有焦炉6座,其中2座4.3m捣固焦炉,4座6.98m顶装焦炉,焦炭年产能250万吨。
烟道气指标经检测,均未达到国家标准要求,必须进行治理。
目前国内主流的焦炉烟道气脱硫脱硝工艺主要为三种,即:工艺1:SDA半干法脱硫+除尘SCR脱硝一体化工艺+烟气回原烟囱工艺2:SCR脱硝+ SDA半干法脱硫+布袋除尘工艺+烟气回原烟囱工艺3:SCR脱硝+气气换热器+氨法脱硫+气气换热器+烟气回原烟囱(1)SDA半干法脱硫+除尘SCR脱硝一体化工艺+烟气回原烟囱。
①工艺流程及原理。
焦炉烟气被引风机抽取,首先进入旋转喷雾半干法(SDA法)脱硫塔,烟气从脱硫塔上部烟气分配器进入塔体,烟气中的SO2与塔顶旋转雾化器喷出的雾化状态的Na2CO3溶液充分混合反应,生成Na2SO3、Na2SO4,随烟气一起进入布袋除尘器。
烟气中的颗粒物被除尘滤袋过滤,经压缩空气反吹后由输灰系统收集,其中未反应的Na2CO3可循环使用,脱硫除尘后的烟气进入脱硝反应器。
传统烟气脱硝技术的相互比较
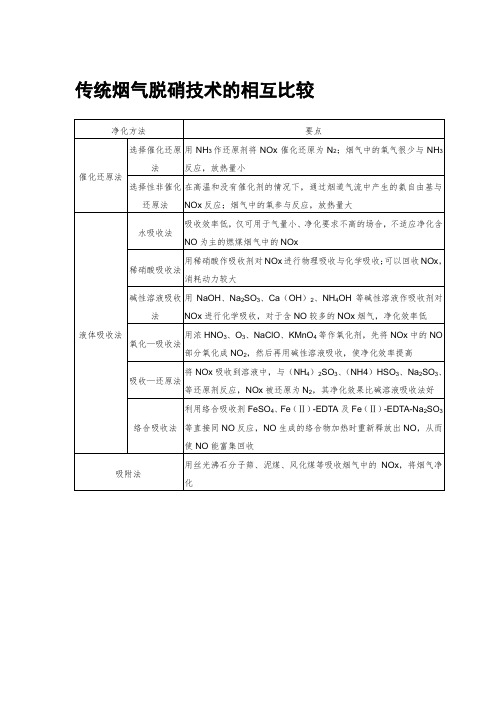
将NOx吸收到溶液中,与(NH4)2SO3、(NH4)HSO3、Na络合吸收法
利用络合吸收剂FeSO4、Fe(Ⅱ)-EDTA及Fe(Ⅱ)-EDTA-Na2SO3等直接同NO反应,NO生成的络合物加热时重新释放出NO,从而使NO能富集回收
传统烟气脱硝技术的相互比较
净化方法
要点
催化还原法
选择催化还原法
用NH3作还原剂将NOx催化还原为N2;烟气中的氧气很少与NH3反应,放热量小
选择性非催化还原法
在高温和没有催化剂的情况下,通过烟道气流中产生的氨自由基与NOx反应;烟气中的氧参与反应,放热量大
液体吸收法
水吸收法
吸收效率低,仅可用于气量小、净化要求不高的场合,不适应净化含NO为主的燃煤烟气中的NOx
稀硝酸吸收法
用稀硝酸作吸收剂对NOx进行物理吸收与化学吸收;可以回收NOx,消耗动力较大
碱性溶液吸收法
用NaOH、Na2SO3、Ca(OH)2、NH4OH等碱性溶液作吸收剂对NOx进行化学吸收,对于含NO较多的NOx烟气,净化效率低
氧化—吸收法
用浓HNO3、O3、NaClO、KMnO4等作氧化剂,先将NOx中的NO部分氧化成NO2,然后再用碱性溶液吸收,使净化效率提高
吸附法
用丝光沸石分子筛、泥煤、风化煤等吸收烟气中的NOx,将烟气净化
焦化厂焦炉烟气脱硫脱硝工艺技术分析

焦化厂焦炉烟气脱硫脱硝工艺技术分析摘要:将安全风险、环保评估和经济性分析纳入火电厂烟气脱硝性能测试评价中有着重要的工程意义。
在工程现场测试过程中,不能将脱硝性能测试的安全、环保和经济性要求简单化、形式化的糅合。
在机组超低排放改造工程脱硝设备性能试验技术规范和国家及电力行业相关脱硝性能试验技术规范要求下,对具体的性能指标进行测试考核,不仅需要考核烟气进出口参数、脱硝效率、系统阻力、氨逃逸等核心参数,还需要结合工程现场将环保效益、经济效益和安全效益系统性的呈现出来。
这无疑对工程测试人员提出较高的要求,不仅需要具有扎实的基础理论知识和实验测试技能,动手能力强,综合素质好;还需掌握科学的思维方法,具备较强的获取知识能力和探索精神、创新能力和优秀的科学品质。
关键词:焦化厂焦炉;烟气脱硫脱硝;工艺技术分析引言氮氧化物(NOx)是主要空气污染物之一,会造成酸雨、光化学烟雾等环境污染,成为工业烟气重点治理对象。
NH3选择性催化还原技术(NH3-SCR)是目前最有效的脱硝技术之一,其脱硝原理是以氨气、尿素等作为还原剂,利用钒、锰、铁等金属氧化物的催化作用,在200~450℃时,将NOx转化成无污染的N2和H2O,其反应式为:4NH3+4NO+O2→4N2+6H2O、4NH3+2NO2+O2→3N2+6H2O。
火力发电厂是氮氧化物最主要的排放源之一,相关环保标准要求到2020年国内火电厂全部实施超低排放,NOx排放浓度小于50mg/m3。
基于上述背景,火电行业积极推进烟气脱硝治理,在2017年,国内火力发电厂SCR脱硝工艺应用比例达到94.1%。
随着环保治理力度不断加强,钢铁工业烟气脱硝也面临着巨大的减排压力,其中铁矿烧结工序由于NOx排放量占整个钢铁生产流程的70%而受到重点关注。
1.氧化法烧结机烟气脱硝工艺流程(氧化法),利用臭氧、二氧化氯、双氧水等强氧化化学药剂氧化原烟气中的NO,待原烟气中的NO被氧化成NO2等高价态物质后,再进入脱硫塔用碱性吸收剂(如CaO等)进行吸收。
烟气脱硝技术方案的对比
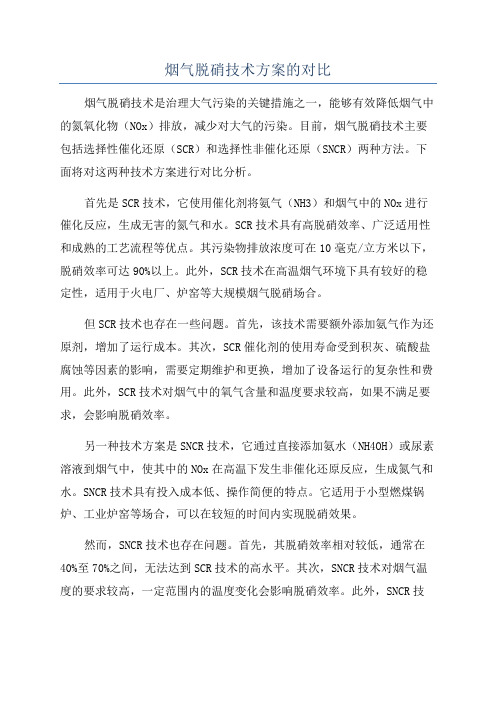
烟气脱硝技术方案的对比烟气脱硝技术是治理大气污染的关键措施之一,能够有效降低烟气中的氮氧化物(NOx)排放,减少对大气的污染。
目前,烟气脱硝技术主要包括选择性催化还原(SCR)和选择性非催化还原(SNCR)两种方法。
下面将对这两种技术方案进行对比分析。
首先是SCR技术,它使用催化剂将氨气(NH3)和烟气中的NOx进行催化反应,生成无害的氮气和水。
SCR技术具有高脱硝效率、广泛适用性和成熟的工艺流程等优点。
其污染物排放浓度可在10毫克/立方米以下,脱硝效率可达90%以上。
此外,SCR技术在高温烟气环境下具有较好的稳定性,适用于火电厂、炉窑等大规模烟气脱硝场合。
但SCR技术也存在一些问题。
首先,该技术需要额外添加氨气作为还原剂,增加了运行成本。
其次,SCR催化剂的使用寿命受到积灰、硫酸盐腐蚀等因素的影响,需要定期维护和更换,增加了设备运行的复杂性和费用。
此外,SCR技术对烟气中的氧气含量和温度要求较高,如果不满足要求,会影响脱硝效率。
另一种技术方案是SNCR技术,它通过直接添加氨水(NH4OH)或尿素溶液到烟气中,使其中的NOx在高温下发生非催化还原反应,生成氮气和水。
SNCR技术具有投入成本低、操作简便的特点。
它适用于小型燃煤锅炉、工业炉窑等场合,可以在较短的时间内实现脱硝效果。
然而,SNCR技术也存在问题。
首先,其脱硝效率相对较低,通常在40%至70%之间,无法达到SCR技术的高水平。
其次,SNCR技术对烟气温度的要求较高,一定范围内的温度变化会影响脱硝效率。
此外,SNCR技术对氨水或尿素的溶液浓度、喷射位置和喷射方式等参数也有一定要求,需要认真调节和管理。
综上所述,SCR技术和SNCR技术各有特点,适用于不同的烟气脱硝场合。
对于大型火电厂、炉窑等高温烟气场合,SCR技术具有脱硝效率高、稳定性好的优点,但运行成本较高,需要额外添加氨气和定期维护催化剂。
而对于小型燃煤锅炉、工业炉窑等低温烟气场合,SNCR技术具有投入成本低、操作简便的优点,但脱硝效率相对较低。
火电厂脱硝系统氨气制备方案比较
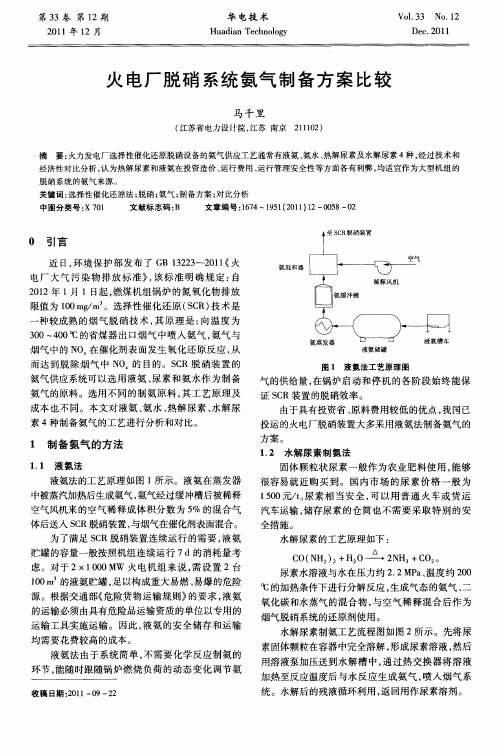
水 解尿 素 的工艺原 理如 下 :
^
C N 2 2 2 _ 2 H3 C 2 O( H ) +H O_ N + 0 。 =
尿素水 溶液 与水 在压 力约 22MP 、 . a温度 约 20 0 ℃ 的加热条 件下 进行 分解 反应 , 生成 气态 的氨 气 、 二
源。根据交通部《 危险货物运输规则》 的要求 , 液氨
一
种较成熟的烟气脱硝技术 , 其原理是 : 向温度为
} 夜氨储 罐
30 4 0C 0 — 0 的省煤器 出口烟气 中喷人氨气 , o 氨气 与
烟气 中的 N 在催 化剂 表 面发 生 氧化 还 原 反应 , O 从
而达到脱除烟气 中 N 的 目的。S R脱硝装 置的 O C 氨气供应系统可以选用液氨 、 尿素和氨水作为制备 氨气的原料。选用不 同的制氨原料 , 其工艺原理及
的运输必须由具有危险品运输资质的单位以专用的 运输工具实施运输。因此 , 液氨的安全储存和运输 均需要花费较高的成本。
氧化碳和水蒸气的混合物, 与空气稀释混合后作 为 烟气脱硝系统的还原剂使用。
水解 尿素 制氨工 艺 流程 图如 图 2所示 。先将 尿
液氨法 由于系统简单 , 不需要化学反应制氨的
经济性对 比分析 , 为热解尿素和液氨在投资造价 、 认 运行 费用 、 运行管理安全性等方面各有利弊 , 均适 宜作 为大型机 组 的 脱硝系统的氨气来源 。 关键词 : 选择性催化还原法 ; 脱硝 ; 氨气 ; 制备方案 ; 比分析 对
中图分类号 : 0 X71 文献标志码 : B 文章编号 :64—15 (0 1 1 0 5 O 17 9 12 1 ) 2— 0 8一 2
全措 施 。
液氨法的工艺原理如 图 1 所示。液氨在蒸发器 中被蒸汽加热后生成氨气 , 氨气经过缓冲槽后被稀释 空气风机来 的空气稀释成体积分数为 5 的混合气 % 体后送入 S R脱硝装置, C 与烟气在催化剂表面混合 。
焦炉烟气脱硫脱硝常见工艺流程对比
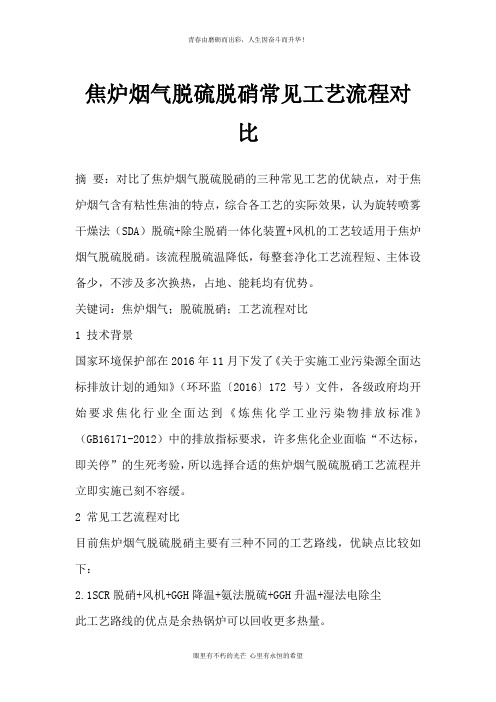
焦炉烟气脱硫脱硝常见工艺流程对比摘要:对比了焦炉烟气脱硫脱硝的三种常见工艺的优缺点,对于焦炉烟气含有粘性焦油的特点,综合各工艺的实际效果,认为旋转喷雾干燥法(SDA)脱硫+除尘脱硝一体化装置+风机的工艺较适用于焦炉烟气脱硫脱硝。
该流程脱硫温降低,每整套净化工艺流程短、主体设备少,不涉及多次换热,占地、能耗均有优势。
关键词:焦炉烟气;脱硫脱硝;工艺流程对比1 技术背景国家环境保护部在2016年11月下发了《关于实施工业污染源全面达标排放计划的通知》(环环监〔2016〕172号)文件,各级政府均开始要求焦化行业全面达到《炼焦化学工业污染物排放标准》(GB16171-2012)中的排放指标要求,许多焦化企业面临“不达标,即关停”的生死考验,所以选择合适的焦炉烟气脱硫脱硝工艺流程并立即实施已刻不容缓。
2 常见工艺流程对比目前焦炉烟气脱硫脱硝主要有三种不同的工艺路线,优缺点比较如下:2.1SCR脱硝+风机+GGH降温+氨法脱硫+GGH升温+湿法电除尘此工艺路线的优点是余热锅炉可以回收更多热量。
此工艺路线的缺点是脱硝催化剂处于不利位置。
焦炉烟气中的SO2会被催化剂氧化成相对较多的SO3,SO3与氨反应生成硫酸氢铵,气态硫酸氢铵随着烟气温度降低,凝结成液态(270℃以下),长期运行会粘附、堵塞催化剂,降低脱硝催化剂的脱硝效率。
焦炉烟气中含有~30mg/Nm3颗粒物,直接排放不达标,必须设置湿法电除尘器,此项的设备费用和能耗极大。
2.2 活性炭吸附脱硫+氨气脱硝+活性炭再生装置此工艺路线的优点是可以同时进行脱硫脱硝;生产过程中无需工艺水,不仅避免了废水处理难题,而且烟气温降小,可以省去烟气冷却和再热等环节。
此工艺路线的缺点是目前技术不成熟,仍有许多关键问题尚未解决。
首先是吸附容量低:出口SO2很难达到30mg/Nm3以下的标准,且吸附速率慢。
其次,活性炭工艺再生频繁,炭原料损失高,运营成本不尽如人意。
最后,本工艺设备并不可靠,塔器内壁易被氨盐腐蚀,且塔内温度分布不均匀,容易形成热点甚至引起着火。
焦炉烟道气脱硫脱硝工艺探讨

焦炉烟道气脱硫脱硝工艺探讨作者:苗社华来源:《中国化工贸易·中旬刊》2018年第10期摘要:焦炉烟气是焦炉生产中由煤气燃烧而产生的废气,其中含有大量的二氧化硫、粉尘和氮氧化物等物质,它们是形成酸雨和雾霾的主要污染物之一,如果焦炉烟气未加处理,肆意排放的话,则会对大气环境造成极大的污染破坏。
随着近年来大气污染问题的日益严峻,国家加大了对企业污染排放的限制和治理,在此形势下,各种烟气脱离脱硝技术逐渐开始研究并应用于焦化企业的烟气净化处理中,本文对当前几种常见的焦炉烟气脱硫脱硝工艺进行了探讨。
关键词:焦炉烟道气;大气污染;脱硫脱硝;工艺探讨1 焦炉烟道气脱硫脱硝技术1.1 烟道气脱硫技术目前,已投入工业化应用的脱硫工艺主要分为湿法脱硫、干法脱硫和半干法脱硫三种,它们所采用的工艺原理和流程各不相同,各有优缺点。
1.1.1 湿法脱硫湿法脱硫是采用脱硫吸收剂和喷淋的方法,将烟气中二氧化硫在吸收塔内吸收,然后对不同的吸收液进行后处理。
该方法的技术优点是投资小、能耗低,但在脱硫处理时吸收剂总量比较多,产生的吸收废液较多,废水处理难度较大。
湿法脱硫中最为常见的是石灰石-石膏法和氨法脱硫,技术也较为成熟,脱硫处理中会发生一系列复杂的酸碱反应,石灰石-石膏法脱硫的反应方程式如下:中和反应:CaCO3+2SO2+H2O=Ca(HSO3)2+CO2氧化反应:Ca(HSO3)2+CaCO3+O2+3H2O=2CaSO4·H2O+ CO2氨法脱硫是利用氨水与二氧化硫反应生产氨盐,以达到吸收烟气中二氧化硫的目的。
其反应方程式为:(NH4)2SO3+SO2+H2O→2HN4HSO3氨基吸收剂的碱性相对钙基吸收剂要更强,吸收效率也更高,因而也更适用于焦炉烟道气的脱硫处理,脱硫副产物硫酸铵经过结晶干燥后还可做为氨肥原料得到回收利用。
1.1.2 干法脱硫是利用粉状或是颗粒状吸收剂或催化剂来拖去烟气中的二氧化硫。
其常用的吸收剂主要有碳酸钙、活性炭等。
焦化厂焦炉烟气脱硫脱硝工艺技术分析
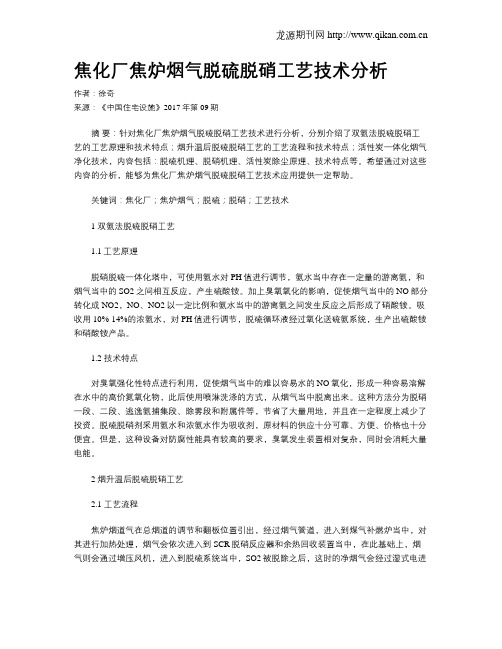
焦化厂焦炉烟气脱硫脱硝工艺技术分析作者:徐奇来源:《中国住宅设施》2017年第09期摘要:针对焦化厂焦炉烟气脱硫脱硝工艺技术进行分析,分别介绍了双氨法脱硫脱硝工艺的工艺原理和技术特点;烟升温后脱硫脱硝工艺的工艺流程和技术特点;活性炭一体化烟气净化技术,内容包括:脱硫机理、脱硝机理、活性炭除尘原理、技术特点等。
希望通过对这些内容的分析,能够为焦化厂焦炉烟气脱硫脱硝工艺技术应用提供一定帮助。
关键词:焦化厂;焦炉烟气;脱硫;脱硝;工艺技术1 双氨法脱硫脱硝工艺1.1工艺原理脱硝脱硫一体化塔中,可使用氨水对PH值进行调节,氨水当中存在一定量的游离氨,和烟气当中的SO2之间相互反应,产生硫酸铵。
加上臭氧氧化的影响,促使烟气当中的NO部分转化成NO2,NO、NO2以一定比例和氨水当中的游离氨之间发生反应之后形成了硝酸铵。
吸收用10%-14%的浓氨水,对PH值进行调节,脱硫循环液经过氧化送硫氨系统,生产出硫酸铵和硝酸铵产品。
1.2 技术特点对臭氧强化性特点进行利用,促使烟气当中的难以容易水的NO氧化,形成一种容易溶解在水中的高价氮氧化物,此后使用喷淋洗涤的方式,从烟气当中脱离出来。
这种方法分为脱硝一段、二段、逃逸氨捕集段、除雾段和附属件等,节省了大量用地,并且在一定程度上减少了投资。
脱硫脱硝剂采用氨水和浓氨水作为吸收剂,原材料的供应十分可靠、方便、价格也十分便宜。
但是,这种设备对防腐性能具有较高的要求,臭氧发生装置相对复杂,同时会消耗大量电能。
2 烟升温后脱硫脱硝工艺2.1 工艺流程焦炉烟道气在总烟道的调节和翻板位置引出,经过烟气管道,进入到煤气补燃炉当中,对其进行加热处理,烟气会依次进入到SCR脱硝反应器和余热回收装置当中,在此基础上,烟气则会通过增压风机,进入到脱硫系统当中,SO2被脱除之后,这时的净烟气会经过湿式电进行除尘,此后经过塔顶的烟囱向外排放出去。
脱硫所生成的副产品被送到焦化回收车间中,然后生产硫酸铵成品。
SCR脱硝四种制氨方法的工艺技术经济比较分析

SCR脱硝四种制氨方法的工艺技术经济比较分析作者:陈曦来源:《中国科技纵横》2013年第07期【摘要】目前SCR脱硝还原剂氨气有四种较常用的生成方式,分别为:液氨气化、尿素炉外热解、尿素炉内热解和尿素水解,简要介绍这4种工艺的反应原理、工艺特点,并对其进行了技术经济比较分析。
分析结果表明4种工艺方案各有优劣,火力发电厂应根据自己自身条件选择最适合自己的制氨工艺。
【关键词】火力发电厂烟气脱硝液氨气化尿素炉外热解尿素炉内热解尿素水解技术经济比较目前在电厂脱硝领域商业化应用的脱硝工艺为达到出口NOx浓度低于100mg/Nm3可采用SCR脱硝,SCR工艺是一种以NH3作为还原剂将烟道中的NOx分解成无害的N2和H2O的干法脱硝方法。
反应的基本原理是:4NO+4NH3+O2 4N2+6H2O6NO2+8NH3 7N2+12H2ONO+NO2+2NH3 2N2+3H2O其中SCR脱硝的还原剂可采用不同还原剂制备方法:液氨气化,尿素热解和尿素水解。
总的来说即分为四种技术:(1)采用液氨作为还原剂的SCR脱硝,(2)采用尿素热解制氨作为还原剂的SCR脱硝,(3)采用尿素水解制氨作为还原剂的SCR脱硝,(4)SNCR/SCR 耦合脱硝。
1 氨气制备工艺技术介绍1.1 采用液氨气化工艺液氨由槽车运送到液氨贮槽,液氨贮槽输出的液氨在氨气蒸发器内采用蒸汽或电加热作为热源将其气化化为氨气,并将氨气加热至一定温度后,送到氨气缓冲槽备用。
缓冲槽的氨气经调压阀减压后,送入各机组的脱硝系统。
液氨气化制氨工艺特点如下:(1)初投资费用较少;(2)运行费用较低;(3)操作简单,响应速度快;(4)自动化程度高。
1.2 采用尿素炉外热解制氨工艺尿素颗粒与去离子水配制成指定浓度(40~60%)溶液后输送至尿素溶液储罐储存,配制好的尿素溶液通过高流量循环模块(HFD)输送到计量分配模块(MDM),该计量模块能根据系统氨需量自动控制尿素溶液进入流量,并利用压缩空气将尿素溶液雾化并通过喷头喷入热解室(DC)内,与经由稀释风机、换热器和电加热器输送过来的高温空气混合热解,生成NH3、H2O和CO2,分解产物与稀释空气混合均匀并喷入脱硝系统。
各种烟气脱硝工艺的比较
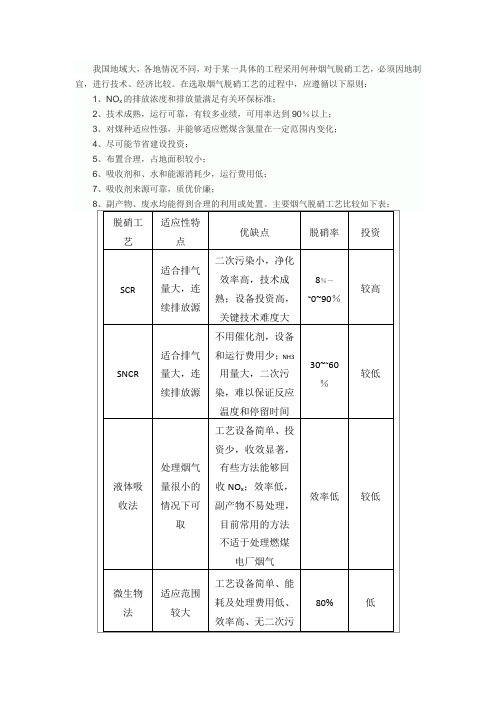
较高
SNCR
适合排气量大,连续排放源
不用催化剂,设备和运行费用少;NH3用量大,二次污染,难以保证反应温度和停留时间
30~~60%
较低
液体吸收法
处理烟气量很小的情况下可取
工艺设备简单、投资少,收效显著,有些方法能够回收NOx;效率低,副产物不易处理,目前常用的方法不适于处理燃煤电厂烟气
我国地域大,各地情况不同,对于某一具体的工程采用何种烟气脱硝工艺,必须因地制宜,进行技术、经济比较。在选取烟气脱硝工艺的过程中,应遵循以下原则:
1、NOx的排放浓度和排放量满足有关环保标准;
2、技术成熟,运行可靠,有较多业绩,可用率达到90%以上;
3、对煤种适应性强,并能够适应燃煤含氮量在一定范围内变化;
效率低
较低
微生物法
适应范围较大
工艺设备简单、能耗及处理费用低、效率高、无二次污染;微生物环境条件难以控制,仍处于研究阶段
80%
低
活性炭吸附法
排气量不大
同时脱硫脱硝,回收NOx和SO2,运行费用低;吸收剂用量多,设备庞大,一次脱硫脱硝效率低,再生频繁
80%~90%
高
电子束法
适应范围较大
同时脱硫脱硝,无二次污染;运行费用高,关键设备技术含量高,不易掌握
4、尽可能节省建设投资;
5、布置合理,占地面积较小;
6、吸收剂和、水和能源消耗少,运行费用低;
7、吸收剂来源可靠,质优价廉;
8、副产物、废水均能得到合理的利用或处置。主要烟气脱硝工艺比较如下表:
脱硝工艺
适应性特点
优缺点
脱硝率
投资
SCR
适合排气量大,连续排放源
二次污染小,净化效率高,技术成熟;设备投资高,关键技术难度大
焦炉烟气脱硫脱硝技术的选择与应用武学风张洋
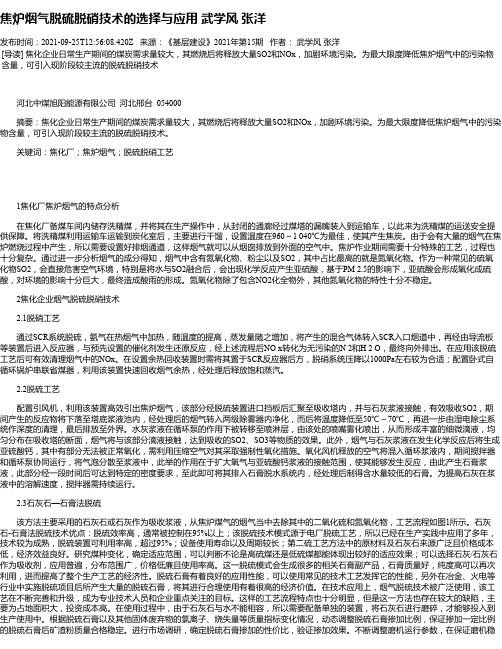
焦炉烟气脱硫脱硝技术的选择与应用武学风张洋发布时间:2021-09-25T12:56:08.420Z 来源:《基层建设》2021年第15期作者:武学风张洋[导读] 焦化企业日常生产期间的煤炭需求量较大,其燃烧后将释放大量SO2和NOx,加剧环境污染。
为最大限度降低焦炉烟气中的污染物含量,可引入现阶段较主流的脱硫脱硝技术河北中煤旭阳能源有限公司河北邢台 054000摘要:焦化企业日常生产期间的煤炭需求量较大,其燃烧后将释放大量SO2和NOx,加剧环境污染。
为最大限度降低焦炉烟气中的污染物含量,可引入现阶段较主流的脱硫脱硝技术。
关键词:焦化厂;焦炉烟气;脱硫脱硝工艺1焦化厂焦炉烟气的特点分析在焦化厂备煤车间内储存洗精煤,并将其在生产操作中,从封闭的通廊经过煤塔的漏嘴装入到运输车,以此来为洗精煤的运送安全提供保障。
将洗精煤利用运输车运输到炭化室后,主要进行干馏,设置温度在960~1 040℃为最佳,使其产生焦炭。
由于会有大量的烟气在焦炉燃烧过程中产生,所以需要设置好排烟通道,这样烟气就可以从烟囱排放到外面的空气中。
焦炉作业期间需要十分特殊的工艺,过程也十分复杂。
通过进一步分析烟气的成分得知,烟气中含有氮氧化物、粉尘以及SO2,其中占比最高的就是氮氧化物。
作为一种常见的硫氧化物SO2,会直接危害空气环境,特别是将水与SO2融合后,会出现化学反应产生亚硫酸,基于PM 2.5的影响下,亚硫酸会形成氧化成硫酸,对环境的影响十分巨大,最终造成酸雨的形成。
氮氧化物除了包含NO2化全物外,其他氮氧化物的特性十分不稳定。
2焦化企业烟气脱硫脱硝技术2.1脱硝工艺通过SCR系统脱硫,氨气在热烟气中加热,随温度的提高,蒸发量随之增加,将产生的混合气体转入SCR入口烟道中,再经由导流板等装置后进入反应器,与预先设置的催化剂发生还原反应,经上述流程后NO x转化为无污染的N 2和H 2 O,最终向外排出。
在应用该脱硫工艺后可有效清理烟气中的NOx。
焦炉烟气脱硫脱硝技术汇总详解

焦炉烟气脱硫脱硝技术汇总,这个必须看2015-07-31汇总目录碳酸钠半干法脱硫+低温脱硝一体化工艺加热焦炉烟气+高温催化还原脱硝工艺SICS法催化氧化(有机催化法)脱硫脱硝工艺活性炭/焦脱硫脱硝工艺碳酸钠半干法脱硫+低温脱硝一体化工艺1.脱硫脱硝原理采用半干法脱硫工艺,使用Na2CO3溶液为脱硫剂,其化学反应式为:Na2CO3+SO2→Na2SO3+CO2(1)2Na2SO3+O2→2Na2SO4(2)脱硝采用NH3-SCR法,即在催化剂作用下,还原剂NH3选择性地与烟气中NOx反应,生成无污染的N2和H2O随烟气排放,其化学反应式如下:4NO+4NH3+O2→4N2+6H2O (3)2.工艺流程焦炉烟气被引风机引入工艺系统,先脱硫除SO2,后除尘脱硝,再脱除颗粒物和NOx,最后经引风机增压回送至焦炉烟囱根部(见图1)。
图1 碳酸钠半干法脱硫+低温脱硝一体化工艺流程示意该工艺主要由以下系统组成:脱硫系统由脱硫塔及脱硫溶液制备系统组成。
Na2CO3溶液通过定量给料装置和溶液泵送到脱硫塔内雾化器中,形成雾化液滴,与SO2发生反应进行脱硫,脱硫效率可达90%。
脱硫剂喷入装置与系统进出口SO2浓度联锁,随焦炉烟气量及SO2浓度的变化自动调整脱硫剂喷入量。
核心设备为烟气除尘、脱硝及其热解析一体化装置,包括由下至上集成在一个塔体内的除尘净化段、解析喷氨混合段和脱硝反应段。
氨系统负责为烟气脱硝提供还原剂,可使用液氨或氨水蒸发为氨气使用。
热解析系统负责为脱硝装置内的催化剂提供380-400℃高温解析气体,分解黏附在催化剂表面的硫酸氢铵,净化催化剂表面。
3.工艺特点①半干法脱硫设置在脱硝前,将烟气中的SO2含量脱除至30mg/Nm3以下,以保证后续的高效脱硝。
②烟气脱硫、除尘、脱硝、催化剂热解析再生一体化,节省投资、运行费用低、占地面积少。
③脱硝前先除尘,以减少粉尘对催化剂的磨损、延长催化剂使用寿命。
④通过除尘滤袋过滤层和混合均流结构体的均压作用,使烟气速度场、温度场分布更加均匀,可提高脱硝效率。
【硫老师】几种焦炉烟气脱硫脱硝技术详解

【硫老师】几种焦炉烟气脱硫脱硝技术详解关键词:低温脱硝焦炉烟气有机催化一、碳酸钠半干法脱硫+低温脱硝一体化工艺;二、加热焦炉烟气 +高温催化还原脱硝工艺;三、SICS法催化氧化(有机催化法)脱硫脱硝工艺;四、活性炭/焦脱硫脱硝工艺;碳酸钠半干法脱硫+低温脱硝一体化工艺1.脱硫脱硝原理采用半干法脱硫工艺,使用Na2CO3溶液为脱硫剂,其化学反应式为:Na2CO3+SO2→Na2SO3+CO2(1)2Na2SO3+O2→2Na2SO4(2)脱硝采用NH3-SCR法,即在催化剂作用下,还原剂NH3选择性地与烟气中NOx反应,生成无污染的N2和H2O随烟气排放,其化学反应式如下:4NO+4NH3+O2→4N2+6H2O (3)2.工艺流程焦炉烟气被引风机引入工艺系统,先脱硫除SO2,后除尘脱硝,再脱除颗粒物和NOx,最后经引风机增压回送至焦炉烟囱根部(见图1)。
图1 SICS法催化氧化(有机催化法)脱硫脱硝工艺流程示意该工艺主要由以下系统组成:脱硫系统由脱硫塔及脱硫溶液制备系统组成。
Na2CO3溶液通过定量给料装置和溶液泵送到脱硫塔内雾化器中,形成雾化液滴,与SO2发生反应进行脱硫,脱硫效率可达90%。
脱硫剂喷入装置与系统进出口SO2浓度联锁,随焦炉烟气量及SO2浓度的变化自动调整脱硫剂喷入量。
核心设备为烟气除尘、脱硝及其热解析一体化装置,包括由下至上集成在一个塔体内的除尘净化段、解析喷氨混合段和脱硝反应段。
氨系统负责为烟气脱硝提供还原剂,可使用液氨或氨水蒸发为氨气使用。
热解析系统负责为脱硝装置内的催化剂提供380-400℃高温解析气体,分解黏附在催化剂表面的硫酸氢铵,净化催化剂表面。
3.工艺特点①半干法脱硫设置在脱硝前,将烟气中的SO2含量脱除至30mg/Nm3以下,以保证后续的高效脱硝。
②烟气脱硫、除尘、脱硝、催化剂热解析再生一体化,节省投资、运行费用低、占地面积少。
③脱硝前先除尘,以减少粉尘对催化剂的磨损、延长催化剂使用寿命。
焦化厂焦炉烟气脱硫脱硝工艺技术分析
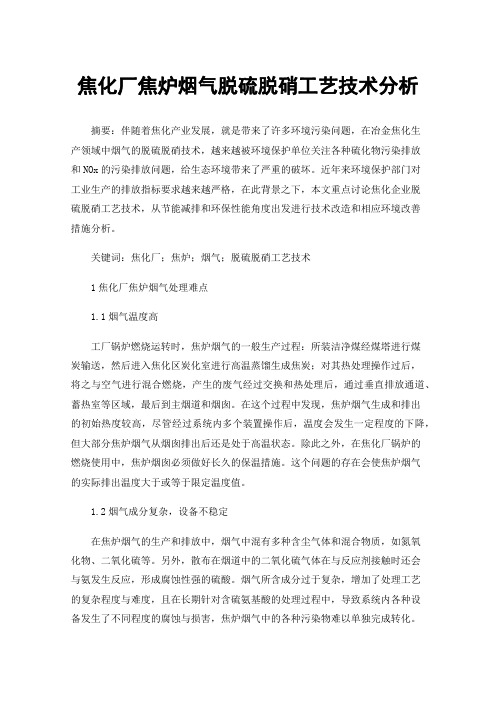
焦化厂焦炉烟气脱硫脱硝工艺技术分析摘要:伴随着焦化产业发展,就是带来了许多环境污染问题,在冶金焦化生产领域中烟气的脱硫脱硝技术,越来越被环境保护单位关注各种硫化物污染排放和NOx的污染排放问题,给生态环境带来了严重的破坏。
近年来环境保护部门对工业生产的排放指标要求越来越严格,在此背景之下,本文重点讨论焦化企业脱硫脱硝工艺技术,从节能减排和环保性能角度出发进行技术改造和相应环境改善措施分析。
关键词:焦化厂;焦炉;烟气;脱硫脱硝工艺技术1焦化厂焦炉烟气处理难点1.1烟气温度高工厂锅炉燃烧运转时,焦炉烟气的一般生产过程:所装洁净煤经煤塔进行煤炭输送,然后进入焦化区炭化室进行高温蒸馏生成焦炭;对其热处理操作过后,将之与空气进行混合燃烧,产生的废气经过交换和热处理后,通过垂直排放通道、蓄热室等区域,最后到主烟道和烟囱。
在这个过程中发现,焦炉烟气生成和排出的初始热度较高,尽管经过系统内多个装置操作后,温度会发生一定程度的下降,但大部分焦炉烟气从烟囱排出后还是处于高温状态。
除此之外,在焦化厂锅炉的燃烧使用中,焦炉烟囱必须做好长久的保温措施。
这个问题的存在会使焦炉烟气的实际排出温度大于或等于限定温度值。
1.2烟气成分复杂,设备不稳定在焦炉烟气的生产和排放中,烟气中混有多种含尘气体和混合物质,如氮氧化物、二氧化硫等。
另外,散布在烟道中的二氧化硫气体在与反应剂接触时还会与氨发生反应,形成腐蚀性强的硫酸。
烟气所含成分过于复杂,增加了处理工艺的复杂程度与难度,且在长期针对含硫氨基酸的处理过程中,导致系统内各种设备发生了不同程度的腐蚀与损害,焦炉烟气中的各种污染物难以单独完成转化。
2焦化厂主要焦炉烟气脱硫技术2.1干法脱硫技术干法脱硫工艺技术原理:碳酸钙固体在高温下喷入炉中进行锻造和燃烧,反应生成氧化钙,后与焦炉烟气中的二氧化硫发生化学反应转化为硫酸钙。
或根据焦化厂的具体情况,通过活性炭吸附或电子束辐照的方式,将烟气中的二氧化硫转化成硫酸或硫酸铵,该工艺也称为干法脱硫技术。
脱硫脱硝工艺对比
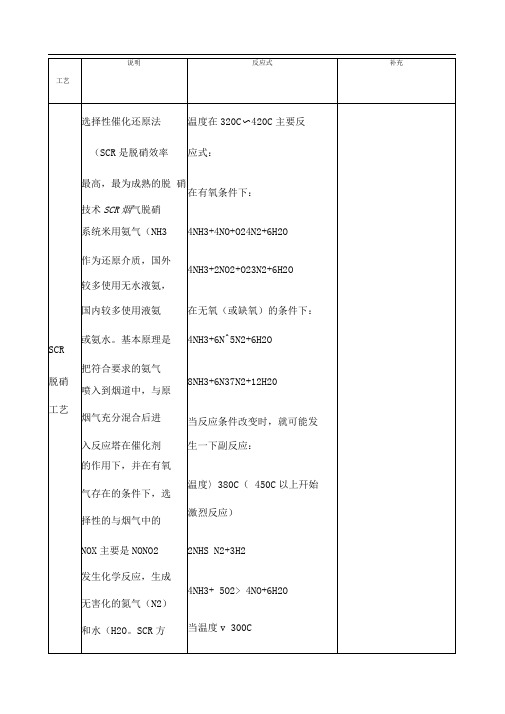
-石膏湿法烟气脱硫工-艺(单减法)
SO升H23 H2SO4
中和:CaCO3 + H2S8CaSO3
+CO2+H2O
CaCO3 + H2SO^CaSO4 +CO2+H2O
氧化:CaSO群1/202—CaSO4
结晶:
CaS04+H2OCaS04 H20[
锅炉应用最广泛的
吸收剂中的水分蒸发干燥,脱硫反应后的废渣以干态排出。
?从锅炉出来的含有粉尘和S02的烟气,从脱硫塔的底部经过文丘里管上升,进入塔内。
生石灰在消化器内加水消化后,在消石灰仓储存。
将一定量的消石灰粉和水在文丘里喉口上端加入,在脱硫塔内与烟气混合流动,并与烟气中的SO2反应,生成亚硫酸钙和硫酸钙。
携带反应产物和煤灰的烟气冷却到稍高于露点以上的温度,进入后面的布袋除尘器。
反应1/202^ CaS04+ H2O 剂的利用率;在相同的
脱硫效率下;
缺点:
1、主要缺点是对锅炉
负荷变化的适应性差;
2、脱硫和除尘相互影
响,脱硫系统之后必须
再加除尘设备,运行控
制要求较高。
3、运行存在塔壁积灰、
雾化器堵塞磨损等严重
问题。
主要应用范围
★火力发电厂烟气脱
硫;★中小型工业锅炉
(工况稳定型)烟气脱
硫;。
- 1、下载文档前请自行甄别文档内容的完整性,平台不提供额外的编辑、内容补充、找答案等附加服务。
- 2、"仅部分预览"的文档,不可在线预览部分如存在完整性等问题,可反馈申请退款(可完整预览的文档不适用该条件!)。
- 3、如文档侵犯您的权益,请联系客服反馈,我们会尽快为您处理(人工客服工作时间:9:00-18:30)。
2018年7月第49卷第4期
燃料与化工
Fuel&Chemical Processes
焦炉烟道气脱硝系统氨气化工艺的比较
于清野薛建勋杜立广赵丹萍田孝东
(中冶焦耐工程技术有限公司,大连116085)
摘要:介绍了液氨气化、氨水精馏、浓氨水气化3种工艺流程,并分别从工艺特点、项目投资、介质消耗和操作费用进行比较分析,为脱硝系统氨气化工艺的选择提供参考。
关键词:烟道气;脱硝;液氨气化;氨水精馏;浓氨水气化
中图分类号:X784文献标识码:A文章编号:1001-3709(2018)04-0059-03
Comparison of ammonia vaporization processes of
coke oven flue gas denitration system
Yu Qingye Xue Jianxun Du Liguang Zhao Danping Tian Xiaodong
(ACRE Coking&Refractory Engineering Consulting Corporation,MCC,Dalian116085,China) Abstract:Three ammonia vaporization processes,liquid ammonia vaporization,ammonia liquor distillation and concentrated ammonia liquor vaporization,are introduced and compared with respect to process features,project investment,media consumption and operating cost.It provides a reference for selection of ammonia vaporization process.
Key words:Flue gas;Denitration;Vaporization of liquid ammonia;Distillation of ammonia liquor;
Vaporization of concentrated ammonia liquor
收稿日期:2018-03-16
作者简介:于清野(1985-),男,工程师
基金项目:
燃料与化工
Fuel &Chemical Processes
Jul.2018Vol.49No.4
馏塔内,氨水被从塔底进来的1.6MPa 中压蒸汽加热、蒸馏,从塔顶逸出氨气(浓度为99.8%),经精馏塔冷凝器冷凝成液氨,液氨经回流罐后由回流泵送往精馏塔。
产品氨气由精馏塔冷凝器前氨气管道采出,减压至0.2~0.3MPa 后经缓冲罐送往焦炉烟道气脱硝系统。
精馏塔顶压力控制在1.45MPa、操作温度约40℃,精馏塔底压力控制在1.5MPa、操作温度约200℃。
蒸氨塔送来的氨气中所含S 2-、CN -等酸根离
子在氨水给料槽中与蒸氨装置碱液贮槽送来的碱液中和为钠盐,随精馏废水排至蒸氨装置。
加入碱液也用于分解固定铵,不增加消耗。
蒸氨塔送来的氨气中所含油类等杂质由精馏塔上部设置的油侧线采出,送至脱硫脱氨前煤气管道。
图2 氨水精馏工艺
1.3 浓氨水气化工艺
浓氨水气化工艺见图3。
储罐车运送的20%合格浓氨水通过卸车泵送入氨水槽储存,再由氨水泵送入氨气化器中,通过蒸汽加热气化为0.2~0.3MPa、约130℃的氨气,然后经管道输送至焦炉烟道气脱硝系统。
氨水气化工艺设置氨气化器,20%氨水蒸发所需要的热量由蒸汽提供。
氨气化器顶部设有压力调节,通过进入氨气化器的蒸汽流量调节氨气化器的气相压力,当压力过高时停止加热。
2 氨气化工艺比较
2.1 工艺特点的比较
液氨气化工艺操作简单,主要以低压蒸汽为热源,利用氨气化器对外购液氨进行气化,操作温度低,须在1.6MPa 压力下对液氨进行储存和使用,对
运输和设备制造的要求较高。
液氨品质应符合
GB 536—88《液体无水氨》技术指标的要求,保证供
应脱硝系统的氨气品质稳定。
液氨气化工艺的设计应满足国家对乙类危险品罐区的有关规定。
同时,液氨属于国家重点监管的危险化学品,存在一定的安全隐患,需要进行重大危险源辨识。
结合厂区周边情况,液氨气化工艺可能会提升重大危险源危险程度,增加自动化控制系统的投资。
图3 浓氨水气化工艺
氨水精馏工艺主要是利用焦炉煤气净化装置蒸氨塔送来的氨气,以中压蒸汽为热源,精馏制取纯氨气,供脱硝系统使用。
原料自给,无需外购液氨或氨水,不仅节约原料成本,而且避免了液氨装卸、储存带来的潜在危险。
氨水精馏工艺对煤气净化工艺流程的依赖较强,只有剩余氨水蒸氨的工艺才能配套使用氨水精馏工艺,蒸氨塔送来的氨气质量需稳定,否则直接影响送往脱硝系统的氨气质量。
氨水精馏工艺较为复杂,操作难度大且产生废水,同时减少了
煤气净化系统中的氨源,对于利用煤气自身碱源脱硫的工艺(如HPF 工艺)会造成一定影响。
浓氨水气化工艺是在常压下对20%合格浓氨水进行卸车和储存,利用低压蒸汽加热的氨气化器制取20%氨气。
工艺和操作简单,供应脱硝系统的氨气品质稳定,不属于重大危险源,安全系数高。
但因为氨水中含水较多,因此氨气化器负荷较大,同时浓氨水具有一定的腐蚀性,对设备材质要求较高。
2.2 项目投资、介质消耗和操作费用的比较以处理焦炉烟道气120000m 3/h、纯氨消耗量
65kg /h 的脱硫脱硝装置作为比较基准,项目投资费用比较见表1,介质消耗量比较见表2,操作费用比较见表3。
表1 项目投资费用比较
万元
项目液氨气化工艺
氨水精馏工艺浓氨水气化工艺
投资费用∗
155
300
119
注:“∗”表示投资费用包括工艺、土建、安装及配套设施如电气、仪
表等投资。
6
2018年7月第49卷第4期
燃料与化工
Fuel &Chemical Processes
表2 介质消耗量比较
项目循环水/(m 3·h -1)
操作电量/kW 低压蒸汽/(t ·h -1)中压蒸汽/(t ·h -1)外购液氨/(kg ·h -1)
外购氨水/(kg ·h -1)产生废水∗/(t ·h -1)
液氨气化工艺3
5.50.05—65—— 氨水精馏工艺255.5—0.2——0.2 浓氨水气化工艺
—
1.5
0.35
—
—
325
—
注:“∗”表示连同整个煤气净化系统增加的废水量。
表3 操作费用比较
万元/a
项目液氨气化工艺
氨水精馏工艺
浓氨水气化工艺
单价
循环水费用1.2110.07—0.46元/t 耗电费用
2.602.600.710.54元/kWh 低压蒸汽费用
3.85—26.9888元/t 中压蒸汽费用—19.27—110元/t 外购液氨费用125.27——2200元/t 外购氨水费用——113.88400元/t 废水处理费用
—4.38—25元/t
运行费用总计∗
132.93
36.32
141.57
注:“∗”表示运行费用中不含运输成本和工业水费用。
3 结论
液氨气化工艺的优势在于操作简单,一次性投资较少,系统运行较稳定。
但液氨属于国家重点监管的危险化学品,给生产带来一定的安全隐患,需要进行重大危险源辨识,对防火间距、消防系统均有严格的要求,且后期运行成本较高。
氨水精馏工艺最大的优势是无需外购液氨或氨水,可以实现原料的自给,后期运行成本低,长期的经济性明显优于其他2种工艺。
但流程较为复杂,操作困难,一次性投资较大,且依赖于煤气净化所选择工艺,适用范围窄。
浓氨水气化工艺流程简单,操作容易,一次性投资少,供应脱硝系统的氨气品质稳定,且氨水危险性
明显低于液氨,安全可靠。
但后期运行成本略高于液氨气化工艺,明显高于氨水精馏工艺。
综上所述,在煤气净化系统配备剩余氨水蒸氨工艺,且靠外来碱源脱硫或利用煤气自身碱源脱硫,煤气中氨硫比较大的焦化厂,氨水精馏工艺具有较大的优势,应优先选择。
其他情况,根据原料取得的难易、原料价格、运输条件以及重大危险源配置等因素,选择液氨气化工艺或浓氨水气化工艺。
参考文献
[1]李鹏元,李宝东,杨懿,等.焦炉烟道气脱硫脱硝及余热回收利
用一体化技术[J].冶金能源,2016,35(1):48-51.
张晓林 编辑
一种带有新型进气方式和气流分布结构的袋式除尘器
本发明涉及一种带有新型进气方式和气流分布结构的袋式除尘器,包括尘气入口、重力分离区、灰斗、滤袋区、外壁板、清灰组件、净气出口、花板,其特征在于,在尘气入口侧安装有迷宫式导流分离板组,迷宫式导流分离板组位于除尘器外壁板的内侧,除尘器滤袋区的外侧。
迷宫式导流分离板组由两组错位对扣相互咬合布置的型板组成,可为C 型、或V 型、或[型、或〔型。
本发明的有益效果是:使含尘气流进入除尘器后形成突扩状态,经过迷宫式导流板组再次分离,在滤袋区形成由下向上的气体运动趋势,利于清除滤袋灰尘,适用于各种气体净化,尤其适用于高浓度、大颗粒、磨琢性强的粉尘过滤,能够比常规除尘器提高除尘滤袋使用寿命1/2以上。
[专利申请号ZL 200910219866.0 专利发明人:王充霍延中吴绍军等]
1
6。