塑料模具设计第十一周 第一讲(第四章)
塑料模具基础课程讲义(doc21)

塑料模具基础课程讲义第一章塑料一﹑塑料的分子结构:塑料主要成份是树脂﹐树脂有天然树脂和合成树脂两种。
二﹑塑料的成份:1.树脂:主要作用是将塑料的其它成份加以粘合,并决定塑料的类型(热塑性或热固性)和主要性能,如机械﹑物理﹑电﹑化学性能等。
树脂在塑料中的比例一般为40~65%。
2.填充剂:又称填料,正确地选择填充剂,可以改善塑料的性能和扩大它的使用范围。
3.增塑剂:有些树脂的可塑性很小,柔软性也很差,为了降低树脂的熔融粘度和熔融温度,改善其成型加工性能,改进塑料的柔韧性,弹性以及其它各种必要的性能,通常加入能入树脂相容的不易挥发的高沸点的有机化合物。
这类物质称增塑剂。
增塑常是一种高沸点液纳或熔点固体的酯类化合物。
4.着色剂:又称色料,主要是起美观和装饰作用,包括涂料两部分。
5.稳定剂:凡能阴缓塑料变质的物质称稳定剂,分光稳定剂﹑热稳定剂﹑抗氧剂。
6.润滑剂:改善塑料熔体的流动性,减少或避免对设备或模具的磨擦和粘附,以及改进塑件的表面光洁度。
三﹑塑料的工艺特性:塑料在常温下是玻璃态,若加热则变成高弹态,进而变成粘流态,从而具有优良的可塑性,可以用许多高生产率的成型方法来制造产品,这样就能节省原料﹑节省工时,简化工艺过程,且对人工技朮要求低,易组织大批量生产。
1. 收缩率或称缩水率。
设计前一定先问供货商的缩水率,模具设计时采用计算收缩率=常温模具尺寸-常温塑件尺寸2.比容和压缩率。
3.流动性。
是塑料成形中一个很重要的因素,流动性好的易长毛边,设计时配合的间隙,气槽的深度等要根据不同材料的流动性设计尺寸。
4.吸湿性。
热能性及挥发物含量。
吸水的塑料有的在塑料成型后直接放于水中让它吸饱水后再进行使用,有的塑料吸湿性特别大,比例有1﹕100。
5.结晶性。
6.应力开裂及熔体液裂。
7.定型速度。
四﹑塑料种类:1.热塑性塑料:这类塑料的合成树都是线型或支链型高聚物,因而受热变软﹐甚至成为可流动的稳定粘稠液体,在此状态时具有可塑性,可塑制成一定形状的塑件,冷却后保持既得的形状,如再加热又可变软成另一种形状,如此可以进行反复多次。
塑料模具设计第八周-第一讲(第四章)
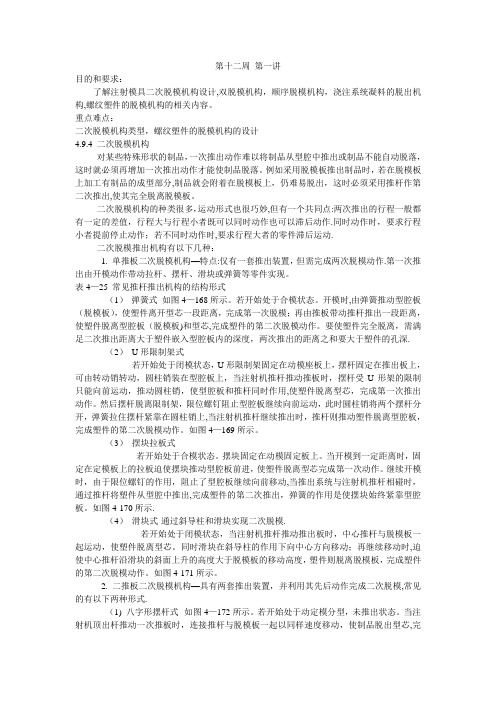
第十二周第一讲目的和要求:了解注射模具二次脱模机构设计,双脱模机构,顺序脱模机构,浇注系统凝料的脱出机构,螺纹塑件的脱模机构的相关内容。
重点难点:二次脱模机构类型,螺纹塑件的脱模机构的设计4.9.4 二次脱模机构对某些特殊形状的制品,一次推出动作难以将制品从型腔中推出或制品不能自动脱落,这时就必须再增加一次推出动作才能使制品脱落。
例如采用脱模板推出制品时,若在脱模板上加工有制品的成型部分,制品就会附着在脱模板上,仍难易脱出,这时必须采用推杆作第二次推出,使其完全脱离脱模板。
二次脱模机构的种类很多,运动形式也很巧妙,但有一个共同点:两次推出的行程一般都有一定的差值,行程大与行程小者既可以同时动作也可以滞后动作.同时动作时,要求行程小者提前停止动作;若不同时动作时,要求行程大者的零件滞后运动.二次脱模推出机构有以下几种:1. 单推板二次脱模机构—特点:仅有一套推出装置,但需完成两次脱模动作.第一次推出由开模动作带动拉杆、摆杆、滑块或弹簧等零件实现。
表4—25 常见推杆推出机构的结构形式(1)弹簧式如图4—168所示。
若开始处于合模状态。
开模时,由弹簧推动型腔板(脱模板),使塑件离开型芯一段距离,完成第一次脱模;再由推板带动推杆推出一段距离,使塑件脱离型腔板(脱模板)和型芯,完成塑件的第二次脱模动作。
要使塑件完全脱离,需满足二次推出距离大于塑件嵌入型腔板内的深度,两次推出的距离之和要大于塑件的孔深.(2)U形限制架式若开始处于闭模状态,U形限制架固定在动模座板上,摆杆固定在推出板上,可由转动销转动,圆柱销装在型腔板上,当注射机推杆推动推板时,摆杆受U形架的限制只能向前运动,推动圆柱销,使型腔板和推杆同时作用,使塑件脱离型芯,完成第一次推出动作。
然后摆杆脱离限制架,限位螺钉阻止型腔板继续向前运动,此时圆柱销将两个摆杆分开,弹簧拉住摆杆紧靠在圆柱销上,当注射机推杆继续推出时,推杆则推动塑件脱离型腔板,完成塑件的第二次脱模动作。
塑胶品质培训

送检批中抽取样本80检验
样品中不良数量
3个或3个下列时 4个或4个以上时
鉴定该批允收 鉴定该批允收
8
第二章 品质检验措施
• 二、AQL抽样检验(MIL-STD-105E) • MIL-STD-105E主要由一系列抽检表构成,
分别为: • 正常检验单次抽样计划表(1.50) • 严格检验单次抽样计划表(0.65) • 减量检验单次抽样计划表(2.50) • 决定品质原则:对不合格品与合格品拟定
• 对产品需要进行破坏性试验,产品批量太大,无法进行全数检验; • 在送检产品中允许有一定程度旳不良品存在; • 送检产品需要较长旳检验时间和较高旳检验费用。
7
第二章 品质检验措施
• 一、术语阐明 • 抽样:在送检批中抽取一定数量样本旳过程; • 批 : 一样产品集中在一起作为抽验对象; • 批量:批中所含单位数量,其大小用N表达; • 样本数:从批中抽取旳部分单位数量,其大小用n表达; • 不合格鉴定个数:样品中允许旳最大不良品数,如该批产品被检出旳
12
第四章:塑胶基本知识
• 第二节 热塑性塑料 • 一、收缩性:影响塑料成型收缩旳主要原因有如下几种方面 • 塑料品种:热塑性材料较热固塑性材料旳收缩大,因其成形时引起旳
体积变化,造成内应力强,分子取向性强等原因造成。 • 塑件特征:成型时,塑料与型腔表面接触外层立即冷却,形成低密度
旳固态外壳,因为塑料导热性差,使塑胶件内层缓慢冷却而形成收缩 较大旳高密度固态层,所以塑胶件壁愈厚收缩越大。 • 浇口形式与尺寸 • 成型条件:模具温度、注塑压力、保压时间、注塑时间等成型时间对 塑胶件旳收缩都有一定旳影响。 • 应力开裂与熔融开裂:有塑料相应力敏感,成型时易产生内应力且质 脆易裂,塑胶件在外力作用下或在溶剂作用下发生开裂现象,可改水 口流道、降低注塑速度、提升料温改善。 • 二、流动性,常用塑料旳流动性分三类: • 流动性好:尼龙、PE、PS、PP、CA; • 流动性中档:ABS、AS、PMMA(有机玻璃)、POM(赛钢); • 流动性差:PC、PBT、EVA;
塑料成型模具设计热成型
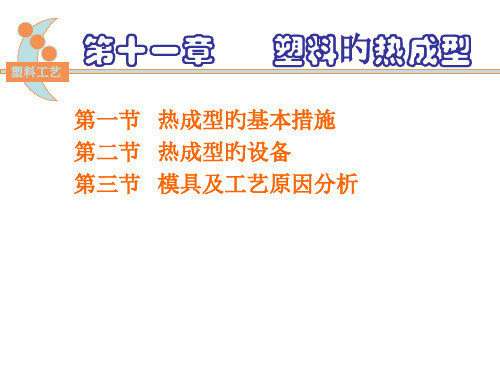
7.其他成型 板材旳弯曲,法兰旳弯制,管材旳弯制等,另外,有板材
卷成筒,容器旳口部或底部旳卷边和管材旳扩口等,都属于热 成型旳范围。
第二节 热成型旳设备
塑料工艺
热成型旳基本工序: 片材夹持、加热、成型、冷却、脱模
一.模具
1.工作压力不高时,可采用强度底旳材料制造模具。材料旳选择 要根据成型旳数量和质量要求而定,如木制模具合承受500次成型, 石膏模具可承受50次,型砂模具和树脂砂模可承受500次以上。 2.模具上旳通风孔制作也是在浇注型砂前插上表面涂有隔离剂旳 钢丝,浇注14小时后抽出钢丝。 3.外形简朴旳制品用阴模成型。因制品收缩,易取出,若构造复 杂,要施加顶出力;对用阳模成型小型拉伸制品时,阳模旳高度尤 为主要。阳模侧圆半径不应不大于板厚旳3-5倍。
品。
2) 应用范围广;日常生活中器皿,食品和药物包装, 汽车部件等。
3) 设备投资少;热成型压力不高,对设备要求不高。 4) 模具制造以便;∵压力低,除金属外,木材,塑料, 石膏等∴热成型在近十年才有较大旳发展。
塑料工艺
3.成型基本过程 1) 先将裁诚一定尺寸和固定形样旳片材夹在框架上; 2) 加热到热高弹态; 3) 成型 凭借施加压力使其贴近模具旳形面,从而得
定压强)→片材包住(模具反压力)封死→打开底模具部抽气孔抽 气→回吸而贴合→成型→冷却脱模→修整→制品 3)推气真空成型 如图 13-11
塑料工艺
塑料工艺
5.模压成型 单阳模法、 单阴模法、 对模成型
多和模压成型 使用也全部热塑性塑料
6.双片成型 这是成型中空制品旳一种措施 如图13-13 两块已加热到足够温度塑料片材,放在半合模具模框上夹
塑料模具设计课件第四章

2
4.1 热固性塑料注射模具
1.浇注系统 浇注系统的类型、形状与热塑性注射模具 相同,但设计时应该注意采用由热固性塑料注 射工艺特点而获得的经验数据。 (1)主浇道 为了使主浇道脱模顺利,主浇道内壁粗糙 度应有旧国标▽8以上的表面光洁度,斜角α 取1°30′~3°主浇道与分浇道连接处做成圆 角为R5~10。如图4-2所示。
优秀课件,精彩无限!
12
4.1
热固性塑料注射模具
4.模具成型零件的设计 热固塑料注射成型时料流易进入细小缝隙 (0.01~0.02毫米),因此尽量避免组合式, 而采用整体式另件结构。 考虑到溢料问题,可以使动、定模在分型 面处的贴合面减小,使两半模贴得更紧些。
优秀课件,精彩无限!
13
4.2
高速成型与自动成型模具
优秀课件,精彩无限! 15
4.2
高速成型与自动成型模具
2.自动成型用模具 为了提高生产效率,节省劳动力, 最近几年来无人操作的自动化生产得到 了发展。我们知道塑料制件生产的工序 大致为:填充、冷却固化、开模、取出 塑料制件、闭模。要使这些工序自动地 进行下去,需要成型设备、模具、工艺 条件等共同保证。
F内=KG
式中 F内—内浇口截面积(毫米2); G—塑件重量(克); K—系数0.25(毫米2/克)。
优秀课件,精彩无限! 5
4.1
热固性塑料注射模具
(4)排气槽 排气槽的作用是排气,保证塑料料流顺利 填充型腔,减少熔接痕,提高塑料制件质量。 在热固性塑料注射成型过程中,除型腔内 原来存留的气体外,还有化学反应所产生的挥 发物,都需要迅速排出模外。而热固性塑料料 流的流动性很好,在注射时极易将型腔中的所 有缝隙堵死,所以利用配合间隙排气往往不能 满足要求,需要开设专门的排气槽。如图4-4 所示。
塑料模具培训计划

塑料模具培训计划一、培训目的本培训旨在帮助学员掌握塑料模具设计、制造和使用的基本技能,提高其在塑料模具行业的实际操作水平,提升工作技能和综合能力,满足市场对高素质技术人才的需求。
二、培训对象及要求1. 培训对象:本培训适合对塑料模具感兴趣、从事塑料模具相关工作的企业员工、技工、技术人员等。
2. 培训要求:学员须具有中专及以上学历,有一定的机械制造基础、模具制造基础等相关技能,有较强的动手能力和学习能力。
三、培训内容本培训内容分为理论教学和实际操作两部分,主要包括以下内容:1. 塑料模具设计基础知识- 塑料模具设计原理- 模具零部件设计- 模具结构设计2. 塑料模具制造技术- 模具制造工艺流程- 模具材料选型及加工- 数控加工技术- 模具装配调试3. 塑料模具应用技术- 塑料注塑工艺- 模具维护与保养- 模具故障分析与处理- 模具改进与优化4. 安全生产知识- 塑料模具生产安全规范- 紧急救护知识- 安全事故预防知识四、培训方法1. 理论课程采用面授结合在线教学的方式,讲解塑料模具的设计、制造和应用理论知识,并结合实例进行详细讲解,以便学员更好地理解和掌握知识。
2. 实操课程采用实际模具加工、组装、调试等实操训练,学员亲自动手操作,掌握实际操作技能,并通过实际案例进行模拟操作,帮助学员熟练掌握技术和操作规程。
五、培训要求1. 学员要懂得自律,课堂上要认真听讲,不得闲聊打扰他人,上课期间要关注老师的讲解内容,积极参与课堂互动。
2. 学员要尊重师资,学员要尊重师资,不得对老师进行人身攻击的言辞。
学员要尊重老师的知识产权, 未经老师的允许,不得将培训中的教学资源转发、发布到其他媒体上。
3. 学员要爱惜培训设备和场地,禁止随意破坏教学设备或者教学场地。
4. 学员要服从培训中心的管理规定,不得在教学区域抽烟、大声喧哗、乱扔垃圾等行为。
六、培训计划1. 第一周:塑料模具设计基础知识第一天:塑料模具设计原理介绍第二天:模具零部件设计第三天:模具结构设计2. 第二周:塑料模具制造技术第四天:模具制造工艺流程第五天:模具材料选型及加工第六天:数控加工技术3. 第三周:塑料模具应用技术第七天:塑料注塑工艺第八天:模具维护与保养第九天:模具故障分析与处理4. 第四周:安全生产及总结第十天:塑料模具生产安全规范第十一天:紧急救护知识第十二天:培训总结及考核七、培训考核1. 学员必须完成培训期间的理论学习和实际操作任务。
塑料制品及其成型模具设计第 4 章PPT课件
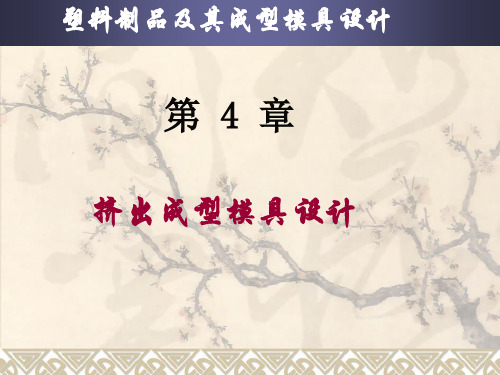
1.1 挤出成型原理
挤出成型是利用电热环的热能与挤出螺杆旋转对塑料产生挤压、剪切和摩擦 产生的热能,使塑料熔融成粘流态,被螺杆挤压、推送到挤出机头的口模和定 型装置,成型并经过冷却固化定型后,成为连续成型型材制品的工艺过程。
(玻璃态----粘流态----高弹态----玻璃态)
筒,机头,口模)
传动系统
温控系统
(加热,冷却)
传动系统:电机经变速箱变速,使螺杆按要求均匀转动
温控系统(加热和冷却系统): 加热使进入料筒和螺杆的塑料熔融塑化,便于挤出成型 冷却使定型制品冷却、固化定型
挤出系统:由螺杆、料筒、机头和口模组成,是挤出机关键部分。 其作用是塑化物料,定量、定压、定温挤出熔体
1)挤出机 挤出系统:由螺杆、料筒、机头和口模组成,是挤出机关键部分。 传动系统:驱动螺杆 温控系统(加热和冷却系统)
2)辅助机 由定型装置、冷却装置、牵引装置、卷取装置、切割组成
3)控制系统 作用:控制主、辅机电动机、以满足所需转速和功率;控 制主辅 机温度、压力、流量,保证制品质量;
第四章 挤出成型模具设计
第四章 挤出成型模具设计
1、挤出成型原理、设备、工艺
1.2 挤出成型设备
1 —螺杆; 2 —料筒; 3—加热器; 4—料斗支座; 5—料斗 6—止推轴承; 7—传动系统; 8—螺杆冷却系统;9 —机身
第四章 挤出成型模具设计
1、挤出成型原理、设备、工艺
1.2 挤出成型设备
辅助机
卧式单螺杆挤出机
挤出成型设备组成
第四章 挤出成型模具设计
1、挤出成型原理、设备、工艺
1.3 挤出成型工艺
挤塑模与定型装置的作用原理
第四章 挤出成型模具设计
塑料模具_抽芯机构
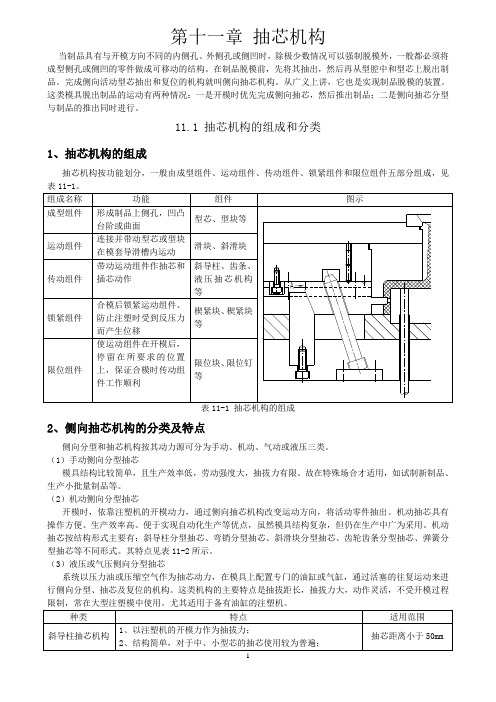
第十一章抽芯机构当制品具有与开模方向不同的内侧孔、外侧孔或侧凹时,除极少数情况可以强制脱模外,一般都必须将成型侧孔或侧凹的零件做成可移动的结构。
在制品脱模前,先将其抽出,然后再从型腔中和型芯上脱出制品。
完成侧向活动型芯抽出和复位的机构就叫侧向抽芯机构。
从广义上讲,它也是实现制品脱模的装置。
这类模具脱出制品的运动有两种情况:一是开模时优先完成侧向抽芯,然后推出制品;二是侧向抽芯分型与制品的推出同时进行。
11.1 抽芯机构的组成和分类1、抽芯机构的组成抽芯机构按功能划分,一般由成型组件、运动组件、传动组件、锁紧组件和限位组件五部分组成,见表11-1 抽芯机构的组成2、侧向抽芯机构的分类及特点侧向分型和抽芯机构按其动力源可分为手动、机动、气动或液压三类。
(1)手动侧向分型抽芯模具结构比较简单,且生产效率低,劳动强度大,抽拔力有限。
故在特殊场合才适用,如试制新制品、生产小批量制品等。
(2)机动侧向分型抽芯开模时,依靠注塑机的开模动力,通过侧向抽芯机构改变运动方向,将活动零件抽出。
机动抽芯具有操作方便、生产效率高、便于实现自动化生产等优点,虽然模具结构复杂,但仍在生产中广为采用。
机动抽芯按结构形式主要有:斜导柱分型抽芯、弯销分型抽芯、斜滑块分型抽芯、齿轮齿条分型抽芯、弹簧分型抽芯等不同形式。
其特点见表11-2所示。
(3)液压或气压侧向分型抽芯系统以压力油或压缩空气作为抽芯动力,在模具上配置专门的油缸或气缸,通过活塞的往复运动来进行侧向分型、抽芯及复位的机构。
这类机构的主要特点是抽拔距长,抽拔力大,动作灵活,不受开模过程11.2 抽芯机构的设计要点1、模具抽芯自锁自锁:自由度F≥1,由于摩擦力的存在以及驱动力方向问题,有时无论驱动力如何增大也无法使滑块运动的现象称为抽芯的自锁。
在注塑成型中,对于机动抽芯机构,当抽芯角度处于自锁的摩擦角之内,即使增大驱动力,都不能使之运动,因此,模具设计时必须考虑避免在抽芯方向上发生自锁。
第十一章 热成型
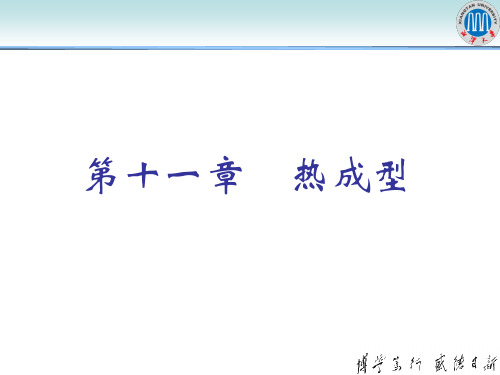
图11-8 挤出-真空成型
6、其它热成型
弯曲
卷筒 卷边和翻边 扩口 成波
热收缩管
异型管件的成型
(1)板材的弯曲 大 批 量 生 产 几 何 尺 寸 严格的制品常采用阴模 阳模弯曲成型方法。 阳 模 预 热 后 加 热 型 坯 , 逐渐下压弯曲型坯。 类似于模压成型
1-型坯 2-阳模 3-模板
2、成型机种类及结构 (1)单片供料热成型机
(2)片卷供料热成型机
(3)连接在生产线中的专用热成型机
(1)单片供料热成型机
适于不易成卷的厚片及板材的热成型,特别是大 型制件的生产。
1)单工位热成型机
片材进入成型机之后,在同一位置先后进行加热、 成型、冷却,取件等操作,所以,所设置的加热装置、 模具台、柱塞、冷却装置等,均以片材夹持框为中心。 2) 多工位热成型机
1、滑动成型(slip-forming)
型坯可在成型过程中滑动
适合于厚壁,大深度制品
2、弹性隔膜成型(a)
隔膜成型是一种复合材料成型方法,即将预浸的 复合材料层压后放置于模具上,通过一种特制隔膜的 辅助作用经过抽真空和加热等方法,将层压件压向模 具,形成所需形状。
弹性隔膜成型(b)弹性隔膜液压成型
工位热成型机,主要是双工位和三工位,以三工 位热成型机为例:第一工位是取件和片材夹持,第二 工位加热,第三工位成型,周而复始
单工位热成型机
双工位热成型机
旋转式三工位热成型机
旋转式四工位热成型机
(2)片卷供料热成型机
(9)冷成型
用热塑性塑料板材在玻璃态和结晶状态拉伸成型容 器类制品,在工业上称冷成型。该办法是借助于金属加 工中板材冷冲压法发展起来的新方法,其主要特点是型 坯在低于玻璃化温度(非结晶型塑料)或低于熔融温度 (结晶型塑料)下成型。型坯在室温下或加热到 20~40℃,低于玻璃化温度或熔融温度,将其周边固定 在夹紧装置上,用阳模施以成型压力,进行成型。减少 或完全取消了型坯的加热工序,也没有冷却阶段。用冷 成型法制得的产品厚度精度和壁厚均匀性都优于热成型 法。
塑料模具设计课件第4章

中受热受压,成为熔融状态而充满型腔,固化成型后开模,
接着又开始下一个压缩成型循环。
上一页 下一页 返回
第一节 压缩模结构及分类 Nhomakorabea
压缩模与注射模一样,也有几大部分组成: (一)型腔 型腔是直接成型塑件的部位,加料时与加料腔一道起装料的 作用,图4-1中的模具型腔由上凸模3、下凸模9、型芯8 和 凹模4等构成。 (二)加料腔 由于塑料原料与塑件相比具有较大的比容,塑件成型前单靠 型腔往往无法容纳全部原料,因此在型腔之上设有一段加料 腔。在图4-1中加料腔为凹模4的上半部,为凹模断面尺寸 扩大的部分。 (三)导向机构 图4-1中由布置在模具上周边的四根导柱6和导套10组成。 导向机构用来保证上、下模合模的对中性。为了保证推出机 构上下运动平稳,该模具在下模座板15上设有二根推板导柱, 在推板上还设有推板导套。
上一页 下一页 返回
第一节 压缩模结构及分类
(二)根据模具加料室的形式分类 1.溢式压缩模 溢式压缩模如图4-4所示,这种模具无加料腔,模腔总高度 h基本上就是塑件高度,由于凸模与凹模无配合部分,完全 靠导柱定位,故压缩成型时,塑件的径向壁厚尺寸精度不高, 而高度尺寸尚可,过剩的物料极易从分型面处溢出。环形面 积是挤压面,其宽度B比较窄,以减薄塑件的飞边。合模刚 开始的压缩阶段,挤压面仅产生有限的阻力,合模到终点时, 挤压面才完全密合。因此,塑件密度往往较低,强度等力学 性能也不高,特别是模具闭合太快,会造成溢料量的增加, 既造成原料的浪费,又降低了塑件的密度。溢式模具结构简 单,造价低廉、耐用(凸凹模间无摩擦),塑件易取出,通 常可用压缩空气吹出塑件。对加料量的精度要求不高,加料 量一般稍大于塑件重量的5% ~ 9%,常用预压型坯进行压 缩成型,适用于压缩成型厚度不大、尺寸小和形状简单的塑 件。
塑胶件设计指导
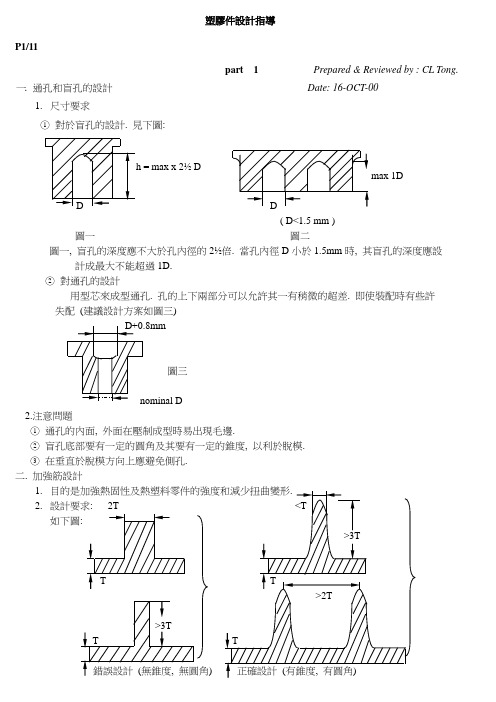
塑膠件設計指導P1/11part 1 Prepared & Reviewed by : CL Tong.一. 通孔和盲孔的設計 Date: 16-OCT-001. 尺寸要求○1 對於盲孔的設計. 見下圖:max 1D( D<1.5 mm ) 圖一圖二圖一, 盲孔的深度應不大於孔內徑的2½倍. 當孔內徑D 小於1.5mm 時, 其盲孔的深度應設計成最大不能超過1D.○2 對通孔的設計用型芯來成型通孔. 孔的上下兩部分可以允許其一有稍微的超差. 即使裝配時有些許 失配 (建議設計方案如圖三)圖三2.注意問題○1 通孔的內面, 外面在壓制成型時易出現毛邊. ○2 盲孔底部要有一定的圓角及其要有一定的錐度, 以利於脫模. ○3 在垂直於脫模方向上應避免側孔. 二. 加強筋設計1.2. 設計要求: 2T 如下圖)圖四P2/11 圖四中, 加強筋根部的厚度應不大於所要加強部分壁厚T, 筋高度應大於3T, 而筋與筋之間的距離(筋中心線與筋中心線之間) 應大於2T.3.注意問題○1多根加強筋設計其效果優於單根加強筋(即使你增大其厚度或高度)○2筋的根部要有一定的圓角, 要有一定的錐度, 以利於脫模.○3加強筋的方向應跟模壓, 成型, 熔料流動方向相一致.三.击台1.目的: 增強孔的穩固及強度或裝配附件之用.2.設計要求圖五圖六击台高度最大不超過击台根部尺寸D的二倍, 击台根部外徑與內徑之差的一半應為0.8T如圖五. 击台跟平面相裝配時, 击台須設計在成型件的四周. 且其高度如圖六所示應為0.4mm. 如果A外平面的平面度要求較高. 還需要打磨.3.注意問題○1击台根部要有一定的圓角和其要有一定的錐度, 以利於脫模.○2當击台高度過高時, 可在击台外部加加強筋, 不僅可以增大击台強度. 而且還有利於促進熔爐塑料的流動.四.錐度設計1.含義: 由於成型時零件內外表面收縮率不一致, 在設計時, 根據塑料對型蕊的粘附力要大於對型腔的粘附力, 設置內表面錐度大於外表面錐度.2.注意問題○1成型件設計要有一定錐度是有利於脫模.○2同樣有利於減少成型過程中瑕疵的形成.五.螺紋的設計(熱固性塑料)塑料螺紋包括螺紋孔和螺牙.1.如下圖○1螺牙要圓, 不宜尖.○2螺紋長度要短.2.如下圖P3/11, 螺紋的中心線位於分型面上.3.螺牙角選擇為32º4.採取成型後再加工螺紋方式去獲取塑料螺紋.5.當螺紋孔要多次裝配時, 建議使用內嵌件.六.嵌件1.要求:○1在塑膠件成型之後. 立即把嵌件壓制到膠件上. 讓包圍著嵌件的部分收縮而來緊嵌件.○2外部嵌件會因為合成物料的收縮而松軟, 內部嵌件會因它的收縮而破裂. 所以在設計嵌件時應考慮配套零件的壁厚,嵌件包圍部分壁厚設計參考表6.1-3.(略)2.注意問題○1用模具壓制嵌件時, 易出現嵌件由於圍壁出現收縮而松動又或者壁易出現斷裂現象.七.平面度由於在成型時易混入氣泡等使熱固性塑料出現收縮現象. 要獲得良好的平面度十分不易的. 通常要求表面留有0.3%的余量.八.零件圖:最終零件圖要指出, 哪一個地方不可以出現分型線. 不可以出現澆口痕, 哪一個地方需要印上模號和模具標記. 哪一個表面出現缺點不能接受等等. 使用SPI/SPE的配套完模工具作為指導.這樣做的目的是易於發現問題和解決問題.九.尺寸因素熱固性塑料成型件尺寸精度可以達到要求公差. 但是, 其精度難以跟加工金屬零件相提並論.造成這樣的原因是:1.塑膠料的收縮率(在成型中).2.成型後塑膠料的收縮率.3.時間, 溫度, 壓力(成型條件)4.模具類型.5.射出及預成型尺寸.6.熔料的流量變異.7.塑膠料種類.十.公差尺寸公差表參考表6.1.4(略)P4/11PART 2一. 注射成型過程○1粒狀塑膠料加入到料斗在180℃高溫下隔熔成液體狀. (熔化的溫度同塑膠料的種類和成型條件有關) 進入鋼模, 被水冷卻成固體狀(水在模外) 取零件.○2整個過程周期為45秒. 壓力為70,000Kpa, 大部分時間用於冷卻.二. 注射成型件的典型特徵及發展趨勢.注射成型適用於大批量複雜零件的生產. 雖然其仍然有極多局限性, 但由於一個注射成型產品可以代替裝配出來的產品, 所以, 其經濟性很好, 另外, 由於顏色, 形狀可以一次性成型做到, 免去二次加工.○1主要特徵:I. 廣泛應用於薄壁零件, 但也可以成型大塊及不同壁厚的零件.II. 強度低, 適用於外殼, 連接桿等受力較小的場合.○2發展超勢熱塑性材料強度會變得越來越大, 機械特性越來越好, 一些類似尼龍, 複合碳酸鹽等,其強度可以同鐵, 鋁, 甚至鋼相比美.PART 3 P5/11一. 收縮率的影響1.啤模時會產生許多不規則或拗曲的形狀, 常見的有夾水紋, 縮水等, 它們常發生在零件較厚的部位.(如圖七)圖七2.另一種經常產生的缺限就是“U”型楔面收縮(如圖八). 第三種情況就是在左右平面收縮變形. (如圖九) 方向易產生平面出現固收縮而引起的曲線.圖八圖九二. 經濟的生產數量注射模適用於量生產的, 一般不會用此方式, 除非有上萬或者更多零件要生產. 之所以有此限製是因為每種零件都需做一個自己獨有的模.只有大量生產開模的經費才能在批量生產中收回, 即便是很小的零件都要花幾千元的開模費. 那些較大較複雜的零件就更會花上萬乃甚至十萬元的經費.三. 合適的原料多種合適的熱熔膠可用於注射模生產. 常用的有聚乙烯﹑PVC﹑尼龍﹑ABS﹑等.注射模在熱塑模市場有很重要的地位, 因此工程人員必須設法使之更利於生產. 物理特性及價格常是選擇這些材料時比加工性能更為重要的因素.通常, 高性能的工程塑料往往比日常使用的塑料像PE料, PP料, PS料等之類更難開模, 特別是PVC雖具有價廉和高性能的優點, 但卻比一般塑膠更難注塑, 最主要的缺點是它的熔點到凝固溫度範圍太窄.表6-2-2列出了一些常用的注塑材料及其特性, 價格和使用範圍. (略)四. 設計指南1.水口及頂針位:設計者須考慮它們的方位, 因為它們會對表面成型產生影響. 如果注件有內外側的話, 水口常開在下側. 水口一般的方位見圖6-2-6(略) 圓形或圓柱型注件的中央水口或者近於中央水口(較大面積的注件)在注塑時是最理想的安全模塑頂料方式.2.注件厚度:表6-2-3 列出了注件厚度的正常值及下限(略), 表明了塑料在注塑完工以前它在模件中冷卻和固化的趨勢, 塑料流動愈緩慢, 則注件厚度要求愈窄, 當然注件的厚度要盡可能的一致. 即便是不得已要改動厚度, 最好變動要舒緩, 不突變.(如圖十)圖十P6/11錯誤設計 正確設計錯誤設計 稍好設計 最好設計3. 孔的設計● 注塑件開孔雖可行卻是開模最複雜的一個因素. 孔周圍易產生飛邊以及 “夾紋” 或是 “夾水weld line圖十一●兩孔間距或是孔到邊的距離至少要有一個孔徑. (如圖十二)錯誤設計 正確設計 圖十二●為避免外應力的影響,單孔必須開在距注件邊緣三個或以上孔徑的地方.(如圖十三)P7/11正確設計錯誤設計圖十三●通孔較盲孔好, 因為做孔所用到的頂針可以在兩頭加以固定, 這樣做出的孔位置尺寸很標準而且可以避免彎曲或折斷.●在注件底部開孔較在邊上開孔好, 因為後者須要可折卸頂針.●盲孔深度須小於兩孔徑之和, 若孔徑為1.5mm或更小, 那麼其深度最小應有一個孔徑. (如圖十四)大孔小孔圖十四●利用击台可以增加盲孔深度, 這須用到較硬的頂針(型蕊). (如圖十五)錯誤設計正確設計圖十五●切去通孔零件兩端的部分可縮短頂針(型蕊)的長度. (如圖十六)錯誤設計正確設計(此設計可降低心棒受損危險性)圖十六4.加強筋●加強筋必須比注件的厚度薄一些, 防止注件表面縮水. 比較好的方法是保證加強的寬度為注件厚度的一半或更少.P8/11●同樣為避免縮水, 加強筋高度須不大於壁厚的1.5倍.●如果有必要, 可以用兩個筋位去加強注件強度用以代替一個更高的筋位的作用.這些筋位須以兩個或以上壁厚的距離分散開來.●為使注件順利地從模中取出, 加強筋必須與注件方位垂直.●由加強筋引起的縮水可以通過在其對面增加凹槽的方法加以減輕和去除. (如圖十七)蝕紋錯誤正確正確正確圖十七●加強筋的設計規則如圖十八.錯誤設計正確設計5.击台: 主要用於塑件的表面突起.●它必須有較大的半徑和圓角.●在加強筋中說明過的原則同樣適用於击台一節. 圖十九表明了固體击台的最大高度和寬度.圖十九●如果可能, 將击台做至邊角處可有助於充模時塑料的流動, 若有必要, 在做可拆裝的击台時,加個聯接筋位將有助於塑膠充模.●如果可能, 盡力避免在罐上部做击台, 因為這將會產生更多氣泡.P9/11●在击台上採用5°錐度, 其設計與加強筋相同.●如果較大的击台要用到, 那必須是中空, 且與塑件厚保持一致.6.凹槽凹槽在注塑中同樣會用到, 只是他們要用到滑動型蕊和分模方式, 凹槽可開在注件的分型線或其延長線方向上, 以避免型心的拉力作用. 凹槽可以不依靠型蕊的拉力即可較容易的脫模. 如果凹槽被移除, 則另一半模必定會保持完好. 那麼頂針(型蕊)將被用於脫模. 凹槽的一般設計尺寸如圖二十.7.螺紋設計螺紋成型盡管很複雜, 但卻是可以辦到的可使用以下三個方法:●螺紋成型後使用旋轉型蕊. 可以使模件順利地從模中取出.●令螺絲軸線與分型面一致. 這樣可避免用到旋轉型蕊, 且可以在模型間得到更好的配合以減少螺紋上的流痕. 這種方案僅用於外部螺紋制作, 且成本昂貴, 除非螺紋可以遠離分型面,而通常這也是可行的. 如果這種方法不適用, 另一種可能的方式將被要求用來移除分型面在螺紋上產生的流痕.●減少螺紋齒數, 降低螺牙高度, 零件可以直接從模腔中脫出而不須從製品中擰下來. 螺牙未端不宜延長到與垂直底面相接處, 否則易使脆性塑料件發生斷裂, 螺紋的始端均不應突然開始和結束, 而應有過渡部分. 因為它方便取出而且避免了多余的飛邊, 以致模件很難配合,甚至生成流痕. 如果是剛性螺紋, 必須使用金屬模蕊.P10/11PART 4原始設計改善設計(增強強度)有時候為了確保產品具有足夠的強度有必要修改設計方案. 防止縮水方法之一是在部件易於受影響的表面加鋸齒狀的骨位.標準的外形為模具工業的發展所需要, 因為它便宜, 且易於採購. 如果有仍何可能我們寧可用標準件, 這對於大現模生產尤其顯得重要.※擠出材料熱熔物的選擇非常重要, 特別是對一種新技術, 新產品. 高強度的苯乙烯是一種最易擠出的塑膠, 纖維與丙烯居其次, 最難擠出的材料為尼龍. 軟塑料不如硬塑料易於擠出到一個細小公差, 快速冷卻會產生內應力並導致裂紋生成. 透明材料(如: PE; 尼龍; VC和PP)常在冷水中冷卻.通過不平衡壓模ABS和PS較PE, PP料易擠出成型. 後者比前者具有更低的熔解強度和更易改變的條件(測試條件易控制).如果採用“雙料擠塑”的材料不同, (除外)那它們之間的結合可能是不完整的. 完全不同的材料連接在一起要通過凹槽. 燕尾槽或機械連接. 當要對不同的塑料作雙料擠塑時一定要考慮材料間的相容性.例如: 增型擠塑乙烯基就與PS不相容.※材料的特點:1.ABS--- 硬性好, 易出模可調任何顏色. 可塑出任何複雜外形. 公差控制水平較高. 用於房屋, 門柱手柄等.2.CA--- 價廉, 通用硬性要求高或較高產品. 顏色可任何意調製. 耐氣候性差, 須涂上防護油, 汽油和大量清潔液體. 易清洗, 斷面較薄.3.CAB--- 與2 類同,但有更好的耐熱與氣候浸蝕性氣味難聞. 顏色可隨意配製, 用於標志倍存.4.CP--- 與3相似只是沒有怪味.5.EC--- 硬性彈性好, 易出模. 公差易控制. 低溫下穩定. 用於膠管刀刃及裝飾部件.6.EV A--- 柔性好, 可配製任何顏色. 外形單調. 用於低性能小五金. 印章, 墊圈等.7.尼龍--- 體輕, 很高的延伸性, 僅用於較單一的外形產品. 對公差要求不高. 凝固速度快. 很好的吸水性. 用於膠管, 路標, 摩擦溝道等.8.PC--- 最好的整體平衡性. 用於製造標準的外形. 公差控制容易. 較貴. 須特別處理, 但其吸水性,導熱性差. 用於燈罩, 消毒櫃等.9.PE--- (高密度)比低密度的PE更加堅硬, 公差難控制. 用於皮帶, 棍棒等.10.PE--- (低密度)較軟, 難以成型. 很好的非導電性,室溫下即能溶解. 用於膠管, 手柄, 緩沖器等.11.PP--- 很輕,標準公差控制. 不適用於複雜的外形. 可調多種顏色. 用於高性能絞鏈樞扭, 滑動導架等.12.PS--- 價廉, 適用於任何顏色, 易碎, 擠塑有限製. 用於燈罩等.13.PS--- 高彈性, 堅硬, 低價. 用於複雜外形. 標準公差控制. 顏色不限. 用於滑動門的導架等.14.PVC--- (柔軟) 通用於各種硬度. 標準的複雜外形. 標準的公差控制.用於各種顏色, 常用於進氣口, 密封圈.P11/1115.PVC--- (硬) 易出模, 可用於複雜外形, 優良的非導電性特性.公差控制容易. 有顏色限製. 常用於導電體的殼和蓋.16. PN--- 可用於各種硬性可調出, 用於各種顏色. 耐磨性好, 常用於傳送帶.17. VD--與15相似. 其非導電特性比PVC(硬)更加好. 複雜的外形, 優良的公差控制特性. 可擠塑出任何顏色. 用於製做熱水管, 高溫涂藥器等.PART 5一.影響尺寸的因素:盡管模塑零件能夠保證這種變異的緊配合公差, 但是對可獲得一定精度的金屬零件之尺寸卻不能保證原因有以下幾種:1.材料收縮力, 包括材料收縮過程中的均勻和不確定性.2.塑料有高的熱膨脹系數, 因此, 如果公差定得過大或過小, 設計者就應定出溫度並采取測量措施.3.盡管有對壓力, 溫度, 時間設定作自動調節的設備, 但這些因素在從一次注塑到另一次注塑間都會有一些變化, 這些變化的結果導致模塑零件輕微的尺寸變化.4.塑料零件通常較金屬零件有較大的柔軟性.由於柔軟因素的存在使得塑膠零件的緊配合無多大必要. 裝配時, 如果有必要去確保一個好配合常可通過零件輕微的變形達到. 如有必要, 明智的設計者可利用設計塑膠零件的击台和击緣去確保與相配零件表面的對稱.與其它過程相比, 緊配合會大大的增加注塑模零件的成本, 精密(公差)模具比粗製(公差) 模具的成本更高, 正如當零額外的緊配合時就會導致加工成本的增加, 例如, 須為壓力, 溫度和循環時間增加相關過程控制, 因而也許會增加循環時間或需要膠件出模後的熱套裝置, 廢品率也更高.不同的塑料材料有不同的公差特性, 低收縮率材料能以相應公差被恆定的注塑, 玻璃或礦物填充材料的注塑比非填充材料更精確. 更多模腔數的使用導致降低所注塑零件控制尺寸的精確. 根據以往經驗, 對每個模腔在第一次啤塑之後的尺寸允差都應增加5%, 例台, 一單模腔在某一尺寸具有±0.1mm的允差;在模腔長為10應有±0.15mm (0.006in) 的允差(公差增加10x5percent=50%).表 6.2.4(略)及6.2.5(略)為不同塑料材料的尺寸公差的建儀值, 這些表格數據, 是由塑膠工業行業提供數據所歸納出的. 代表了以往和現在塑膠模工業的發展成果, 個別模廠的合同形式和協議所規定的也許有變化.。
产品结构设计-----第十一章-塑件中的嵌件

第十一章塑件中的嵌件基本设计守则塑料成型过程中所埋入的或成型后压入的螺栓、接线柱等金属或其它材质零件,统称为塑件中的嵌件.嵌件可增加制品的功能或对制品进行装饰.塑胶内的嵌件通常作为紧固件或支撑部份.此外,当产品在设计上考虑便於返修、易於更换或重复使用等要求时,嵌件是常用的一种装配方式.但无论是作为功能或装饰用途,嵌件的使用应尽量减少,因使用嵌件需要额外的工序配合,增加生产成本.嵌件通常是金属材料,其中以铜为主.嵌件的设计必须使其稳固地嵌入塑胶内,避免旋转或拉出.嵌件的设计亦不应附有尖角或封利的边缘,因为尖角或封利的边缘使塑胶件出现应力集中的情况.嵌件的模塑使操作变繁,周期加长,生产率降低〔带有自动装夹嵌件的机械手或自动线不在此列〕.11.1 嵌件的结构形式1、常见的金属嵌件〔图2-67〕2、嵌件的形状与结构要求<1> 金属嵌件采用切削或冲压加工而成,因此嵌件形状必须有良好的加工工艺性.图2-68为常用嵌件的标准形式.<2> 具有足够的机械强度〔材质、尺寸〕.<3> 嵌件与塑料基体间有足够的结合强度,使用中不拔出、不旋转.嵌件表面需有环形沟槽或交叉花纹〔参见图2-68〕;嵌件不能有尖角,避免应力集中引起的破坏;尽可能采用圆形或对称形状的嵌件,保证收缩均匀.<4> 为便于在模具中安放与定位,嵌件的外伸部分〔即安放在模具中的部分〕应设计成圆柱形,因为模具加工圆孔最容易〔图2-69〕.<5> 模塑时应能防止溢料,嵌件应有密封凸台等结构〔图2-70〕.<6> 便于模塑后嵌件的二次加工,如攻螺纹、端面切削、翻边等.图2-71a即为模塑后再翻边的嵌件结构.<7> 特殊嵌件的结构参见图2-71.3、嵌件材料铜、铝、钢、硬质异种塑件、陶瓷、玻璃等都可作为嵌件材料,其中,黄铜不生锈、耐腐蚀、易加工且价格适中,是嵌件的常用材料.11.2 嵌件在塑件中的固定<1> 为避免制品底部过薄出现波纹形缩痕而影响外观与强度,应取嵌件底面距制品壁面的最小距离T>D/6〔图2-72〕.<2> 嵌件与制品侧壁的间距不能过小,以保证模具有一定的强度〔图2-73〕.<3> 凸台中设置嵌件时,为保证嵌件结合稳定以与塑料基体的强度,嵌件应伸人到凸台的底部〔需保证最小底厚〕,嵌件头部作成圆角〔图2-74〕.<4> 小型圆柱形嵌件可用中间开槽或表面菱形滚花结构植于塑料基体之中〔图2-75〕,滚花槽深1~2mm.<5> 板、片状嵌件可用孔窗固定法固定,但薄形嵌件〔厚度小于0.5mm〕宜用切口或打弯的方法固定〔图2-76〕.<6> 杆形嵌件可用将头部打扁、冲缺、压弯、劈叉等形式固定〔图2-77〕,也可用将圆杆的中间部分压扁的方法固定〔图2-78〕.<7> 管形冲压嵌件,可在冲压时加工出膨凸部分,用以增强紧固力〔图2-79〕.11.3 嵌件在模具中的安放与定位1、嵌件的安放、定位要求<1> 不能因设备的运动或振动而松动甚至脱落.<2> 在高压塑料熔体的冲击下不产生位移和变形.<3> 嵌件与模具的配合部分应能防止溢料,避免出现毛刺,影响使用性能.2、轴类嵌件的安放定位〔图2-80〕3、孔类嵌件的安放定位〔图2-81~图2-83〕4、细长嵌件的安放定位细长嵌件的轴线与料流方向垂直时,易产生弯曲变形,需用销轴等支承,以增加其刚性〔图2-84〕.注意,附加的支承孔不应影响制件的使用.11.4 嵌件周围塑料的裂纹和联接强度1、裂纹产生的原因<1> 塑料收缩的内应力和自然老化〔图2-85〕.<2> 嵌件的结构和安放位置不合理〔图2-86〕.2、保证连接强度的必要条件——最小壁厚〔表2-25〕11.5 装配式嵌件〔制品模塑后再装入嵌件〕<1> 饭金加工〔装配〕法,如铆接〔图2-87〕、折弯〔图2-88〕.<2> 用工具将嵌件压入或旋入制品中〔图2-89、图2-90〕.<3> 热插法.热固性塑件出模时,在热态下将嵌件插入,冷却后即牢固地结合在一起〔图2-91〕.塑料收缩量应在其弹性范围内,否则塑料会裂开.<4> 其它装配方法.①粘结:热固性塑料用环氧树脂粘结,热塑性塑料用溶剂类粘结剂粘结.②超声波装配:热塑性塑料软化后压人.11.6 塑料嵌件〔嵌件的外插注射模塑〕在金属条料、卷料等已冲压零件的型孔内,模塑出小型塑料零件,使两者成为不可拆卸的组合件.这时,金属冲压件是主要零件,塑件则是嵌件.常见的塑料嵌件为齿轮、凸轮、短轴等〔图2-92〕.外插注射模塑模具为三板式或点浇口的热流道模〔图2-93〕.不同材料的设计要点POMPOM成型时,因塑料和镶入件收缩比率不同而有应力产生.渐渐在镶入件的地方发生了龟裂现象而成品破裂,以下方法可改善成品破裂现象.用温度达90℃左右的镶入件放于模腔内成型.模具内温度达90℃左右.镶入件要洁净与避免有尖角或利边.PBT镶入件通常是用以装配方便或维修容易为目的的,但亦有的是特殊用途如金属扣等.为了使镶入件在塑胶成品内减低应力和因不同物料的热膨胀系数所影响,镶入件尽量不要有尖角,防止拔出和转动的凹槽要使用简单的设计,压花的花纹面积不要太大,压花的边要和镶件边位远离,花纹的地方要放于稳藏处.镶入件表面不能有任何不相容的化学药品如润滑油等.在放入模具生产是使用80至110℃的模温来减低成型后的内应力.。
塑胶模具设计讲义.doc

塑膠模具設計講義設計流程一﹑審圖1.尺寸是否完備A.詳細審視圖面各個細部尺寸是否標註。
B.可要求製工傳圖檔,直接於檔案上測量漏標處尺寸,但仍需請製工補正確認並簽名以減少日後之爭議。
2.開模方式A.Cavity數目、模座大小、適用成型機台(Tie bar間距、最大射出能力)。
B.塑膠原料類型、可成型性及其所需之週邊設備。
乾燥桶、除濕機、模溫機(Nylon series)C.模具型式:二板或三板模;Slider or not。
除25°DIMM168 SMT type 外,其餘皆不需跑滑塊。
D. 分模線、公母模側(成品圖之Top view or bottom view為公模)。
E. 頂出方式:撥塊加頂針。
F. 模仁可加工性及機械強度:a.目前的加工能力和精度是否可達模仁設計之要求。
b.成品尺寸設計若太細微,容易造成模仁強度不足或有尖角而易損傷。
G. 公差合理性:是否具備大量製造的能力。
3.Design Review Meeting將上述有疑慮及困難的部分或須與其他零件段配合之事項於Design Review會議上提出並提供改善之建議案。
二﹑Shrinkage1.塑料縮水率(α)一般計算成型收縮率的方式是由常溫的模具尺寸D與成型品的實際尺寸M:D MD-=α在決定模具設計的實際尺寸時,依圖面所用的塑料而先查得成型縮水率,再計算出模具的尺寸。
2. Desktop Memory Socket Connector常用之塑料A. “Sumitomo LCP E6006” (ref. x:0.1%;y:0.16%;z:0.16%)B.“Polly LCP L140”C.“Toray LCP”D. “Wuno LCP ”E. “南亞、耐特、晉綸PA66”F. “Arlen PA6T ”G. “DSM PA46(F8、HF5040)”3. 可過IR 製程之塑料為“Sumitomo LCP E6006” ,而且其收縮率很小,尺寸安定性極佳,故通常以此種原料為設計基準,其他塑料則以實際射出之尺寸為該料號之圖面尺寸(目前於DIMM 168與DDR 皆採用大範圍之公差將不同原料之成品總長涵蓋,如140.9525.005.0-+;RIMM 則因為是高頻connector 且Intel 對生產製程尺寸之cpk 值要求非常嚴格,故採用E6006原料) 。
塑料模具设计课件PPT课件
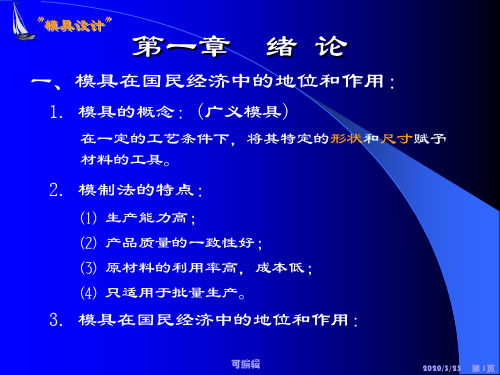
可编辑
2020/3/23 第 34页
主讲:梁 军
二、普通浇注系统的设计:
ቤተ መጻሕፍቲ ባይዱ(一) 主流道和主流道衬套(浇口套)的设计:
设计要求: 1) 进口端要与
喷嘴端密合, 不能漏料;
R=R1+1; d=d1+1
可编辑
2020/3/23 第 35页
2) 出口端要与所在面齐平;
0.2
3) 流道要有脱模斜度和足够的粗糙度;
可编辑
高度h 0.25 0.50 0.75 1.00
宽度b 0.75 1.50 2.25 3.00
2020/3/23 第 45页
h = n .t
材料 PE,PS POM,PC,PP CA,PA66,PMMA HPVC
七、塑件的圆角: 八、塑件上的螺纹:
1.螺纹的断面形状为梯形或半圆形;
2.不常拆卸的、d=2.5~6mm采用自攻螺纹;
3. 螺纹始端和末端应有圆台,螺牙始末端应用 过渡长度。 九、塑件上的嵌件: 1. 必须具有防转和防拔脱的结构;
可编辑
2020/3/23 第 19页
2. 包容的物料必须具有足够的壁厚; 3. 受力的金属嵌件一定要倒圆或倒角。
可编辑
2020/3/23 第 44页
2) 侧浇口(边缘浇口):
特点:加工修整简单、去除容
易、制件上留有明显痕
迹;
常用于 多型腔或一腔多
点进料。
适用:所有料;
板条类的大型制品。
设计:面长:小制品 0.5~0.8
~
大制品 1~2
~ ~
制品尺寸 质量 (g)
很小
0~ 5
小
5~ 40
中 40~200
- 1、下载文档前请自行甄别文档内容的完整性,平台不提供额外的编辑、内容补充、找答案等附加服务。
- 2、"仅部分预览"的文档,不可在线预览部分如存在完整性等问题,可反馈申请退款(可完整预览的文档不适用该条件!)。
- 3、如文档侵犯您的权益,请联系客服反馈,我们会尽快为您处理(人工客服工作时间:9:00-18:30)。
第十四周第一讲目的和要求:了解注射模冷却系统的组成和连通方式,初步掌握冷却系统的计算,了解加热系统的设计,熟悉模架的设计(包括其结构、标准模架及其规格和选择方法、模架的装配要求),了解注射模材料的选用(模具零件的失效形式、选用要求、种类与选用)。
重点难点:模架的设计,注射模材料的选用,冷却系统的计算。
4.11.4 冷却系统的组成及连通方式模具本身可以视为一具热交换器,将塑料熔体所含的热量经由冷却循环系统的冷却水带走。
典型的模具冷却系统如图4-317所示。
冷却系统对应不同的冷却装置有不同的零件,主要有以下几种:(1)水管接头—一般由黄铜制成,对要求不高的模具也可用一般结构钢制成。
进水和出水的接头或水嘴的安装和密封形式如图4-318所示。
图4-318a是采用55度密封管螺纹的形式联接,安装比较方便、可靠,但在螺纹加工上稍微麻烦一些。
图4-318b和c都是采用细牙螺纹的联接形式,分别在螺纹的根部和端部用型环密封的。
图4-318b是将型环嵌入模体,用螺纹压紧,使其稳定可靠。
图4-318c是将型环含在水嘴内部,其稳定密封的作用的。
(2)螺塞—主要用来构造水路,起截流作用。
要求高的模具用黄铜制作螺塞。
(3)密封圈—主要用来使冷却回路不泄漏。
”O”形密封的结构常用”O”形密封圈及装配形式,如图4-319所示。
表4-28 常用密封圈规格及装配技术要求(4)密封胶带--主要用来使螺塞或水管接头与冷却管道连接处不泄漏。
(5)软管—主要作用是连接并构制模外冷却回路。
(6)喷管—主要用在喷流式冷却系统上,最好用铜管。
(7)隔片—用在隔片导流式冷却系统上,最好用黄铜片。
(8)导热杆—用在导热式冷却系统上,主要由铍青铜制成。
另外还有模温控制单元、冷却水供应歧管、冷却水收集歧管、水泵。
4.11.5 冷却系统的计算冷却介质有冷却水和压缩空气,但用冷却水较为普遍,这是因为水的热容量大,传热系数大,成本低。
1. 冷却时间的确定在注射过程中,塑件的冷却时间,通常是指塑料熔体从充满模具型腔起到可以开模取出塑件时止的这一段时间。
这一时间标准以制品已充分固化定型而且具有一定强度和刚度为准,这段冷却时间一般约占整个注射生产周期的80%。
在生产中利用冷却时间与制品厚度关系的经验数据列表4-34,计算时可以参考。
表4-34 常用塑料制品壁厚与冷却时间的关系2. 冷却管道传热面积及管道数目的简易计算通常对于中小型模具以及对塑料制品要求不太严格时,一般可忽略空气对流、辐射以及与注射机接触传走的热量,同时也忽略高温喷嘴与模具的接触传给型腔的热量。
(1)单位时间内注入模具中的塑料熔体的总重量W(kg/h)可由下面两种方法求得方法[I]1)计算每次需要的注射量(kg)=型腔数目*单个塑件质量+浇注系统质量2)确定生产周期(t)= 注射时间(可参考所选用注射机的注射时间来确定)+冷却时间(可查表4-34)+脱模时间(根据塑件取出的难易程度确定,一般8s左右)3)求每小时可以注射的次数N=3600/t4)求每小时的注射量(kg/h)W=每小时可以注射的次数*每次需要的注射量方法[II]1)计算每次需要的注射量=型腔数目*单个塑件质量+浇注系统质量2)已知需要的生产数量N(件)3)估算总的生产时间t(h)以每月x天,每天y小时估算4)求每小时的注射量(kg/h)W=(每小时可以注射的次数*每次需要的注射量)/总的生产时间t (2)确定单位质量的塑件在凝固时所放出的热量Qs(kJ/kg)式中涉及的物理量有塑料的比热容、塑料熔体的温度、塑件在脱模前的温度及结晶型塑料结晶时放出的熔化潜热。
可查表4-35常用塑料熔体的单位热流量Qs(3)计算冷却水的体积流量qv 这里假定塑料熔体凝固和冷却过程中放出的热量全部被冷却水带走,则式中涉及的物理量有冷却水的密度、冷却水比热容、水管出口和进口的设定温度。
(4)确定冷却水路的直径d 计算出冷却水的体积流量后,可根据表4-30中所示的冷却水处于湍流状态下的流速与通道直径的关系,确定模具冷却水路的直径。
(5)冷却水在管内的流速v(m/s)与冷却水的体积流量和冷却水路的直径有关。
(6)求冷却管壁与水交界面的膜传热系数式中涉及的物理量有冷却介质在一定温度下的密度、冷却介质在圆管内的流速、水孔直径、与冷却介质温度有关的物理系数。
(7)计算冷却水通道的传热总面积A式中涉及的物理量有冷却管壁与水交界面的膜传热系数h、模具平均温度与冷却水平均温度之间的差值、每小时的注射量、塑料熔体的单位热流量Qs,即(8)计算模具所需冷却水管的总长度L 与传热总面积A和水孔直径有关。
(9)冷却水路的管道根数x 由于受模具尺寸限制,每根水路的长度由模具的尺寸决定。
射每条水路的长度为l,则冷却水路的管道根数=冷却水管的总长度L/每条水路的长度为l4.11.6 加热系统设计在一般情况下,对热固性塑件成型模具需要设计加热系统,而对于热塑性塑料注射成型时在以下四种情况也需要加热:1)对要求模具温度在80度以上的塑料成型--某些熔融粘度高,流动性差的热塑性塑料,如PC、POM、氯化聚醚、PSF、PPO等,要求有较高的模具温度,需要对模具进行加热。
如果这些塑料在成型时模温过低,则会影响塑料熔体的流动性,从而加大流动的剪切力,使塑件的内应力增大,甚至还会出现冷流痕、银丝、轮廓不清等缺陷。
2)对于大型模具的预热。
大型模具在初始成型时其模温是室温,仅靠熔融塑料的热量使其达到相应的温度是十分困难的,这时就需要在成型前对模具进行预热,才能使成型3)模具有需要加热的局部区域。
在远离浇口的模具型腔,由于模温过低可能会影响塑料熔体的流动,这时可以对该处进行局部加热。
4)热流道模具的局部加热。
热流道模具有的需要对浇注系统部分进行局部加热。
1. 模具加热方式根据加热资源不同,模具加热常常分为介质加热和电加热两大类。
(1)介质加热—利用冷却水道通入热水、热油、热空气及蒸汽的加热介质进行模具加热。
其装置和调节方法与冷却水路基本相同,结构也比较实用。
但是对于持续维持80度以上高温的模具最好不要用热水加热,因为,高温易使未经软化的水产生水垢而影响传热效率,甚至堵塞通道。
(2)电阻加热—用电热棒或电热环作为加热元件进行模具加热。
由于电加热具有清洁、简便、可随时调节温度等优点,在大型模具和热流道模具中逐渐得到广泛的应用。
2. 电阻加热的常用元件的结构、要求及计算(1)电阻加热的常用元件的结构—电阻加热的常见形式是电热棒,如图4-320所示。
根据模具体积,靠改变电热元件的功率、安装数目和输入电压来调节加热速度和温度。
电热棒一般装在通用电热板内,通常用于热固性塑料模具的加热。
如图4-321所示为常用电热板结构。
除了采用电热棒外,也可以根据模具结构的不同采用其他形式的加热元件,如电热圈等,如图4-322所示。
(2)电阻加热的基本要求1)正确合理布置加热元件,保证电热元件的加热功率。
如电热元件的功率不足,就不能达到模具要求的温度;如电热元件的功率过大,会使模具加热过快,从而出现局部过热现象。
2)对大型模具的加热板应安装两套控温仪表,用来分别控制和调节加热板中央和边缘部位的温度。
3)加热板的中央和边缘部位要分别采用不同功率的电热元件,一般在模具中央部位电热元件功率稍小,边缘部位的电热元件功率稍大。
4)加强模具的保温措施,减少热量的传导和热辐射的损失,通常在模具与压力机的上、下压板之间以及模具四周设置石棉隔热板,厚度为4-6mm。
(3)电阻加热的计算--电阻加热的计算的任务是根据模具工作的实际需要计算出所需要的电功率,并选用电热元件或设计电阻丝的规格。
要得到所需电功率的数值,须作热平衡计算,即通过单位时间内供应模具的热量与模具所消耗的热量平衡,从而求出所需电功率。
但这种计算方法太复杂,计算选用的参数不一定符合实际,所以计算结果也并不精确。
在实际生产中广泛采用简化的计算方法求得所需的电功率,并有意适当增大计算结果,通过电控装置加以控制与调节。
加热模具所需电功率可按模具质量按经验公式计算电功率= 模具质量*每千克模具维持成型温度所需要的电功率每千克模具维持成型温度所需要的电功率(W/kg),其值可查表4-36表4-36 电功率q值总的电功率算出来以后,即可根据加热板的尺寸确定电热棒的数量,进而计算每个电热棒的功率,设采用并连接法,则P每= P/n式中涉及的物理量有每个电热棒的功率、电热棒的根数。
根据P每按表4-37 可查得电热棒的外形尺寸和功率4.12.1 注射模模架的结构模架也称模体,是注射模的骨价和基体,模具的每一部分都寄生在其中,通过它将模具的各个部分有机地联系在一起。
我国市场上销售的标准模架如图4-323所示。
它一般由定模座板(或叫定模底板)、定模固定板(或叫定模板)、动模板(或叫型芯固定板)、动模垫板、垫块(或叫垫脚、模角)、动模座板(或叫动模底板)、推板(或叫推出底板)、推杆固定板、导柱、导套、复位杆等组成。
另外,根据需要还有特殊结构的模架,如点浇口模架、带脱模板的模架等。
4.12.2 标准模架的结构与形式我国的注射模架标准有两个,即《注射模中小型模架及技术条件》(GB/T 12556—1990)和《大型塑料注射模架》(GB/T 12555—1990)。
中小型模架有四种基本类型。
1. 中小型模架(1)中小型模架的四种基本类型--如图4-324所示的A1型-A4型,是中小型模架的四种基本类型,适用于W*L<=500mm*900mm的场合。
1)A1型模架定模采用两块模板,动模采用一块模板,设置推杆推出机构,适用于单分型面注射成型模具。
2)A2型模架定模、动模均采用两块模板,设置推杆推出机构,适用于直接浇口,采用斜导柱侧抽芯的注射成型模具。
3)A3型模架定模采用两块模板,动模采用一块模板,设置脱模板推出机构,适用于薄壁壳体类的成型以及脱模力大、塑件表面不允许留有推出痕迹的注射成型模。
4)A4型模架定模均采用两块模板,设置脱模板推出机构,适用范围与A3型基本相同。
(2)中小型模架的九种模架--如图4-325所示,派生型分为P1型-P9型9个品种。
1)P1型-P4型模架由基本型模架A1型-A4型对应派生而成。
结构形式的差别在于去掉了A1型-A4型定模座板上的固定螺钉,使定模一侧增加了一个分型面,成为双分型面成型模具,多用于点浇口。
其他特点和用途同A1型-A4型模架。
2)P5型模架的动、定模均由一块模板组合而成,主要适用于直接浇口、简单整体凹模结构的注射成型模具。
3)在P6型-P9型模架中,P6型与P7型、P8型与P9型是相互对应的结构,P7型和P9型相对于P6型和P8型只是去掉了定模座板上的固定螺钉。
P6型-P9型模架均适用于复杂结构的注射成型模,如定距分型自动脱落浇注系统凝料的注射模等。