切边模具资料
切边模开模指令规范

其他要求说明
1出2
1副(1出2)
切外形、中间孔
四柱型气液增压切边床8T型
切边模编号(作业部门压铸车间)
审核:
切外形、中间孔φ 40±0.1、硬毛刺残留允许≤0.1mm。
批准:
版本:01
客户名称: 产品名称
产品零件号 产品材料及牌号
产品信息
模具穴数 切边模数量
切边切部位
切边切设备
其他信息
ቤተ መጻሕፍቲ ባይዱ接单日期
切边模完成日期 进度要求 第一次试模日期
第二次试模日期
编制: 文件编号:
切边模开模指令规范
编号:
产品毛坯图
产品机加工图
/ 产品装配后图
/
产品编号
新产品/备模
是否汽车件
否
AlSi9Cu3(Fe)
压铸切边模具的设计及应用
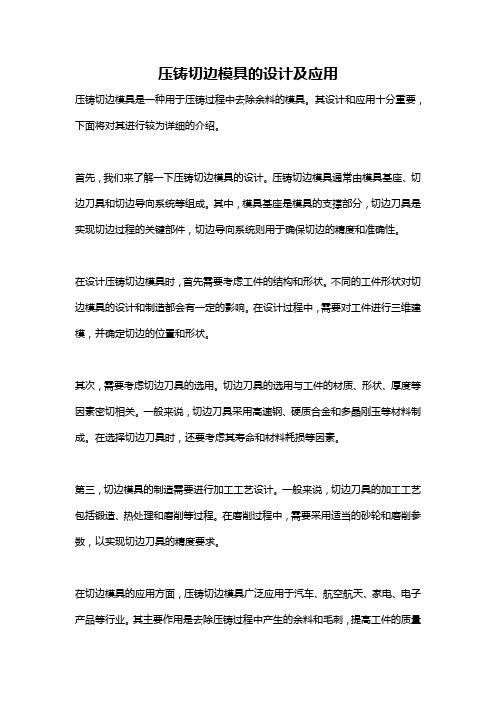
压铸切边模具的设计及应用压铸切边模具是一种用于压铸过程中去除余料的模具。
其设计和应用十分重要,下面将对其进行较为详细的介绍。
首先,我们来了解一下压铸切边模具的设计。
压铸切边模具通常由模具基座、切边刀具和切边导向系统等组成。
其中,模具基座是模具的支撑部分,切边刀具是实现切边过程的关键部件,切边导向系统则用于确保切边的精度和准确性。
在设计压铸切边模具时,首先需要考虑工件的结构和形状。
不同的工件形状对切边模具的设计和制造都会有一定的影响。
在设计过程中,需要对工件进行三维建模,并确定切边的位置和形状。
其次,需要考虑切边刀具的选用。
切边刀具的选用与工件的材质、形状、厚度等因素密切相关。
一般来说,切边刀具采用高速钢、硬质合金和多晶刚玉等材料制成。
在选择切边刀具时,还要考虑其寿命和材料耗损等因素。
第三,切边模具的制造需要进行加工工艺设计。
一般来说,切边刀具的加工工艺包括锻造、热处理和磨削等过程。
在磨削过程中,需要采用适当的砂轮和磨削参数,以实现切边刀具的精度要求。
在切边模具的应用方面,压铸切边模具广泛应用于汽车、航空航天、家电、电子产品等行业。
其主要作用是去除压铸过程中产生的余料和毛刺,提高工件的质量和外观。
在汽车行业中,压铸切边模具被广泛应用于汽车发动机缸体、变速器壳体等零部件的生产中。
通过使用切边模具,可以有效去除铸件表面的毛刺和余料,提高工件的装配精度和密封性能。
在电子产品行业中,压铸切边模具常用于手机、平板电脑、电视等产品的生产中。
通过使用切边模具,可以去除工件表面的毛刺和余料,提高产品的外观质量和用户体验。
在家电行业中,压铸切边模具常用于制造电冰箱、洗衣机、空调等产品的关键零部件。
切边模具的应用可以大幅度改善工件的质量和装配精度,提高产品的性能和可靠性。
总之,压铸切边模具是一种用于压铸过程中去除余料的重要工具。
其设计和应用对于提高工件质量和提高生产效率具有重要意义。
随着科技的不断发展,切边模具的设计和制造技术也在不断革新,将为各行业的生产带来更大的便利和效益。
切边模具资料
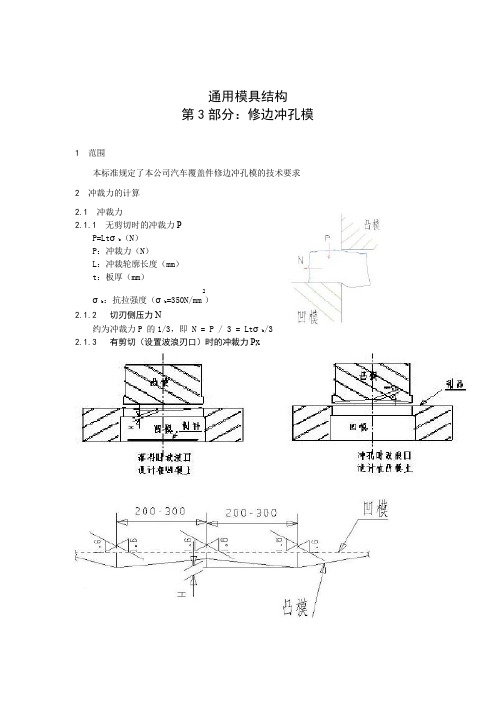
通用模具结构第3部分:修边冲孔模1范围本标准规定了本公司汽车覆盖件修边冲孔模的技术要求2冲裁力的计算2.1冲裁力2.1.1无剪切时的冲裁力PP=Ltσb(N)P:冲裁力(N)L:冲裁轮廓长度(mm)t:板厚(mm)2σb:抗拉强度(σb=350N/mm)2.1.2切刃侧压力N约为冲裁力P的1/3,即N=P/3=Ltσb/32.1.3有剪切(设置波浪刃口)时的冲裁力Px图1PPx=KP(N)Px:有剪切角时的冲裁力P:无剪切时的冲裁力H=t时,K=0.4-0.6H=2t时,K=0.2-0.4冲裁力超过冲床能力的50%时,要考虑设置波浪刃口,修边刃口长的情况下,可设计若干个波浪口。
每块镶块上尽可能取半个波浪或一个波浪;一个波浪的高点,取在镶块中间。
2.2退料力Ps退料力据板厚、形状的不同而变化,一般为冲裁力的4-20%,如间隙为板厚的10%以下时,退料力将增大。
P为冲裁力:t≤2mm:退料力Ps=0.05P(形状简单);Ps=0.06P(形状复杂)t=2~4.5mm:退料力Ps=0.07P(形状简单);Ps=0.08P(形状复杂)t≥4.6mm:退料力Ps=(0.10-0.20)P;2.3卸料力卸料力因料厚、形状等的不同而各异,一般取冲裁力的2~6%。
(常取5%)2.4常用冲压材料的抗拉强度表13冲裁间隙3.1间隙选取原则落料尺寸取决于凹模尺寸(基准侧),间隙取在凸模上;冲孔尺寸取决于凸模尺寸(基准侧),间隙取在凹模上。
3.2间隙值的选取表23.3钝角修边——30°以下钝角修边,间隙取常规的1/2。
——30~60°倾角修边,钝角刃口作出局部平台,一般为3倍料厚,但不超过5mm;间隙趋于0。
图23.4立切修边3.4.1刃口线与斜面上的最大斜线平行,允许最小θ角可参照下表,冲裁间隙按常规选用。
图3表33.4.2立切角度θ角不满足上表要求,需改造凹模刃口,并取小间隙冲裁,对于接近90°立切,冲裁间隙趋于0。
切边模具设计实用标准(上海奥托立夫方向盘有限公司管理系统)--黄铁平

前言随着公司业务的扩大,公司的客户也在不断增加,经不完全统计,近两年与我们公司有业务往来的客户都有四十多家,这些客户大多数都有自已的设计标准,要求我们按他们的要求设计制作,但有很多客户提供给我们的标准本身不是很全,有些内容在沟通过程中有修正,但客户标准没有及时修正过来,为了让工程师特别是新来的工程师能尽快熟悉客户标准,减少出错,现特对现有的客户标准做一次系统的整理。
对客户标准对最熟悉的人是具体负责这个客户的设计组长和设计工程师,只有他们才清楚客户标准哪些内容修改了,哪些内容不完善,哪些方面我们出过错,因此,起草这些客户标准的人就是这些设计组长和工程师,公司研发部标准化组在这个过程中起引导及审核的作用。
由于编制人员的水平有限以及客户要求的不断变化和模具设计制造技术的不断发展,本总结中出现不合理或过时的内容在所难免,如有发现者,欢迎通知编制人员和研发部标准化组进行修正,以使本总结更符合客户要求和生产实际情况。
另外,本标准属银宝山新公司内部资料,任何人不得随意复制。
公司研发部标准化组2009年7月20日目录第一章客户简介 (4)第二章技术文件 (5)2.1 技术文件 (5)2.2图纸文件 (5)2.3确认文件 (6)第三章模具设计 (7)3.1切边模在生产中的动作描述及最初模具设计时的要求 (7)3.2模具材料及热处理 (12)3.3模具基准及压铸骨架在切边模中的放置要求 (12)3.4切削系统(刀刃、支撑板及支撑镶件) (14)3.5顶出系统 (16)3.6排渣系统 (17)3.7奥托立夫切边模专用标准件说明 (19)3.8模具标识 (24)3.9加工要求、FIT模要求及注意事项 (25)第四章模具的使用 (26)4.1模具的吊装与搬运 (26)4.2模具的维护 (28)4.3模具的走模要求 (28)第五章模具的布局与联接 (28)5.1模具的外形尺寸与布局 (28)5.2模具的安装 (29)第六章客户工厂及模具图片 (32)6.1冲压机床图片 (32)第七章补充说明南京云海切边模设计 (39)7.1模具材料及热处理 (39)7.2顶出系统 (39)7.3排渣系统 (40)7.4 骨架在模具中的布局(41) 第一章客户简介上海奥托立夫汽车方向盘有限公司(英文简称ACW)是瑞典奥托立夫在中国的一家全资子公司,其生产的方向盘面向中国所有整车制造商,并出口到日本\韩国\美国\澳大利亚等国,预计到2010年,年产量将达到250万套,其中70%用于出口。
切边模具工作原理

切边模具工作原理
切边模具是一种常用的加工工具,用于对材料进行切边加工。
其工作原理主要包括以下几个步骤:
1. 确定切边的尺寸和形状:根据实际需求,通过设计或图纸确定切边模具的尺寸和形状。
2. 制作切边模具:根据设计要求,使用适当的材料,如工具钢,通过加工、铣削、钳工等方式制作出切边模具的具体形状。
3. 安装切边模具:将切边模具安装在切边设备上,确保模具的稳定性和合适的工作位置。
4. 材料定位:将待加工的材料,如金属板材、塑料片等,放置在切边模具的工作台上,并进行精确定位,以确保准确的加工位置。
5. 进行切边加工:启动切边设备,使切边模具以高速加工材料。
切边模具通常配备有锋利的切割刃或刀具,能够迅速而准确地切割材料边缘。
6. 完成切边加工:当切边模具完成对材料的切边任务后,切割下来的边缘将变得平整、光滑、无毛刺。
切边模具适用于各种材料的切边加工,具有高效、精准、稳定的特点。
在工业生产中,切边模具被广泛应用于各种制造行业,如汽车、电子、工程机械等,有效提高了生产效率和产品质量。
模具毕业设计83切边冲孔复合模的设计

第一章零件的工艺分析一、零件材料的分析08F钢强度、硬度很低,而塑性、韧性极高,具有良好的冷变形性和焊接性,正火后切削加工性尚可,退火后导磁率较高,剩磁较少,但淬透性、淬硬性极低。
二、零件的结构分析该零件结构简单,尺寸没有公差要求,尺寸均为自由公差,外形对称。
三、零件的工艺性分析该零件是钢料,该零件形状的基本特征是一般的有凹圆的圆筒形件,为圆筒形件底部有一个Φ10孔,内部圆周直径为Φ28,尺寸均为自由公差,因一般情况下,拉深件的尺寸精度应在IT13级以下,不宜高于IT11级。
所以将内部直径改为Φ28+00.3。
高度10+00.2为IT11-IT12级精度。
主要成形方法是冲裁、拉深、切边冲孔和弯曲。
零件的dt/d、h/d都不太大,其拉深工艺性较好。
该零件为大批量生产,零件外形简单对称。
材料为08F钢,采用冲压加工经济性较好。
零件如图:t=1mm其余R=0.4图1-1 零件图第二章确定冲压工艺方案冲压工艺方案的确定是制定冲压工艺过程的主要内容,需要综合考虑各方面的因素,有的还需要进行必要的工艺计算,因此,实际确定时通常先提出几种可能的方案。
再在此基础上进行分析、比较和择优。
从零件的结构和形状可知,所需基本工序为落料、拉深、冲孔、弯曲四种。
但工序模具生产效率低难以满足大批量生产的要求,为了提高生产效率主要采用复合冲裁或级进冲裁两种方式。
若采用级进模虽然生产效率很高,但模具的结构比较复杂,对制造精度要求较高,一般生产周期长,成本高维护也比较困难。
采用复合冲裁时,冲出的零件精度和平直度较好,生产效率也较高,模具结构较级进模简单生产成本也比级进模的低。
第一节零件毛坯的尺寸计算(1)弯曲毛坯尺寸的确定对于r<0.5t的弯曲件毛坯长度的计算公式Lz=5+4+5+0.6t=5+5+4+0.6×1=14.6(2)拉深次数的确定及尺寸计算因板料厚度t为1mm故按厚度中线尺寸计算,如图所示。
2.1.1计算坯料尺寸D=(d22+4d2H-1.72rd2-0.56r2)½=(29*29+4*29*10.5-1.72*2.5*29-0.56*2.5*2.5)½=43.94mmL1=Lz+2*2.5=19.6mmL=L1+D=63.54mm图2-12.1.2 确定拉深次数根据坯料的相对厚度t/D=1/43.94=2.28%拉伸系数m=d/D=29/43.94=0.66大于极限拉深系数[m],所以一次拉深成形。
扳手切边模具设计

为 5 6H 。 5~ 0 RC
9
图 5 下冲头
图 6 压料块
( )弹 簧的选 用应 保证 弹簧 预压 力大于 所需 提 4 供 的卸 料力 ,弹簧最 大许 可 压 缩量 大 于 弹簧 预 压量 、
工作行 程 、冲头 刃磨 量之 和 。
4 .结 语 应 用切边 模具 去除 扳 手 角部余 料 ,生 产 效率 高 , 操作方 便 ,而且 切 边 尺寸 精 度 高 、一 致性 好 ,有 效 地解决 了以往 手 工 修 边 的 各种 弊 端 。现 已推 广 应 用
边模 结构 如 图 3所 示 。为 方 便 取 放 冲件 ,选 用 了后 侧导 柱模 架 ,考 虑 到 废 料 排 除 便利 及 冲件 安 放 的稳 定性 等 因素 , 冲件 倒 置摆放 。 将 工作 时 ,将 扳手 弯 曲工 序 件 套在 下 冲头 1 上 进 1
隙不 均等 原 因 ,角 部 拉 深 成 形 后 顶 端 将会 有 不 平 齐 现象 ,因此 角部 毛坯 加 了一 定 的修 边 余 量 ,零 件 弯
H2 6Y,料 厚为 0 4 m,产 品批 量 中等 ,分 析 该 零 件 .m 形状 结构 ,可 以看 出该 零 件 成 形 属 于 弯 曲 为 主 、兼 带拉 深 的复 合 成 形 ,直 边 部 分 为 弯 曲成 形 ,圆 角 部
分属 于拉深 成 形 。
作不 便 , 刀容 易划 伤 工 人 手指 ,存 在 不安 全 因素 ; 锉
2 .切 边模 结构
图 1 扳手
所谓 切边 ,就 是 将 成 形 零 件 的边 缘 修 切 整 齐 或 切 成一 定形 状 。根 据该 扳手 零 件 形 状 特 点 ,设 计 切
在计 算该 零 件 毛坯 展 开 尺 寸 时 , 由于 零 件 角 部
切边模的设计

切边模的设计6.1 切边方式及模具类型分为冷切边和简单热切边两种方式。
1)用螺钉固定的冷切边模; 2)用压块固定的冷切边模;3)用螺钉固定的简单热切边模。
切边凹槽一般分为三块以上,一般采用这种固定方法。
6.2 切边冲孔力的计算 常有两种方法: 1)表格法切边冲孔用的压力机所需要的公称压力,通常与模锻锤有一定得配合关系。
2)计算法切边冲孔力可按照下式计算:1b F k Lt s =式中 F ——切边或冲孔力;b s ——金属在切边或冲孔温度下的抗强度,即材料的变形抗力; L ——剪切周边长度; 1t ——实际剪切厚度;1 2.5t t B =+t ——飞边桥部高度或冲孔连皮厚度;B ——锻件高度方向的正公差;k ——系数,在理想的情况下,k=0.8;考虑到切边或冲孔过程中伴有弯曲、拉伸发生,以及一些如刃口变钝等实际因数,建议取为k=1.6.6.3 切边模结构设计切边时,刃口设置在凹模上,凹模按锻件轮廓线制造,靠减小凹模尺寸获得凸凹模的间隙。
如图所示:图中间隙均取0.5mm d =,1 3.30.03tan as a-=,同时应保证凸模削平后b 值有一定得宽度:对小型锻件,b=1.5-2.5mm ;对中型锻件,b=2-3mm ,对大型锻件,b=3-5mm 。
如果锻件各部分的间隙不同,应按最小间隙作为整个凸凹模的间隙。
切边凹模有整体式、和组合式两种,前者用于中小型锻件,特别是形状简单具有对称性的锻件;后者则用于大型锻件或形状复杂的锻件。
由于油箱盖是对称性的,故选用整体式。
(1)切边凹模刃口设计切边凹模刃口轮廓形状按锻件在分模面上投影轮廓形状设计。
切边凹模刃口形式有直刃口,斜刃口和局部斜刃口。
根据分析,可采用局部斜刃口,与斜刃口相比较,减少了刃口切削加工量,便于制造。
是一种比较经济的形式。
如图所示:(2)切边凹模的分块 切边凹模的分块原则:1)分块处便于对位,又不易产生毛刺,而且能保证切边锻件质量,两端分块为好。
旋切(横向切边)模具的结构

旋切(横向切边)模具的结构
对于筒形拉深件来说,往往会涉及到修边,而修边则多采用横向切边的方式。
而如果要用模具来完成这种形式的的加工的话,在模具中就应将冲床的垂直运动转化为模具零件 刀口的水平运动,然后对工件进行剪切修边。
在这种模具中,其主要部分就是进行运动转换的凸轮机构,这也是设计的重点。
横向切边模具的典型结构如下图所示:
下图所示模具的运动过程如下:
在设计中的注意事项:下模顶内凸轮的力要大,防止在剪切过程中下打板及内凸轮倾斜,使模具的运动部分卡死;顶下打板的力不宜过大;而顶内打板的力应大一些,以方便上模的脱料;下刀口板与下定位板之间应可以产生适当的水平方向上的滑动;内、外凸轮间配合关系及内凸轮相对于外凸轮间的运动;下打板与下模板间的间隙大小。
在这种模具中,应精确控制的尺寸有:
上刀口板 与上模板 之间的高度差,这一尺寸即为原始工件的的高度,同时,这一尺寸对上下模刀口板对工件进行剪切的情况有影响,因此在
模具的组立与试模过程中,依据实际情况对这一尺寸进行修配;
下打板的厚度尺寸,这一尺寸也对上下模刀口板之间的相互运动有较大影响,同时下打板的上表面要进行研磨,以方便下定位板与下打板间的
滑动;
下内凸轮上的下刀口板固定槽尺寸,这个槽的深度与下打板的厚度,上刀口板与上模板间的高度差及刀口板的高度直接影响剪切运动及横向
剪切的断面质量,另外该尺寸还影响刀口板在下凸轮上的固定情况,因
此该的精度要求很高,应采用放电加工以保证其尺寸精度;
下定位板的外形尺寸,外定位板的外形尺寸直接影响工件的定位精度,其高度尺寸则直接影响产品的高度,因此其高度尺寸也要求准,而不允
许有较大的误差;
E.下刀口板的高度尺寸。
六角切边模生产工艺

六角切边模生产工艺【六角切边模生产工艺】一、引言其实啊,在现代工业生产中,各种各样的模具扮演着至关重要的角色。
今天咱们就来好好聊聊六角切边模生产工艺,这可是个相当有趣且实用的工艺呢!二、六角切边模生产工艺的历史1. 早期的探索在工业发展的早期阶段,对于六角形状的切边处理并没有专门的模具。
那时候,人们往往是通过手工打磨或者简单的工具来实现,效率低下不说,精度也很难保证。
说白了就是费时费力还不一定能做好。
比如早期制造六角螺母,工匠们可能得先用锉刀一点点地修整边缘,这得靠经验和耐心,一个不小心就可能前功尽弃。
2. 逐渐成型随着工业技术的不断进步,专门用于六角切边的模具开始出现。
最开始的模具可能比较简单粗糙,但已经大大提高了生产效率和精度。
就像从走路到骑自行车,速度和稳定性都有了质的提升。
3. 现代发展到了现代,六角切边模生产工艺已经相当成熟和精细。
采用了先进的材料和制造技术,能够满足各种高精度、高要求的生产需求。
如今的六角切边模,就像是一位经验丰富的大师,出手就是精品。
三、六角切边模的制作过程1. 设计规划这是第一步,也是非常关键的一步。
工程师们要根据需要切边的产品规格、材质等因素,来设计模具的结构和尺寸。
比如说要切边一个特定大小的六角螺栓,就得先精确计算出模具每个部分的尺寸和形状,就像给房子画设计图一样,得考虑方方面面。
2. 选材与加工选对材料很重要,一般会选择高强度、耐磨的材料,比如优质合金钢。
然后通过各种加工手段,如车削、铣削、磨削等,把原材料加工成模具的各个零部件。
这过程就好比雕刻一件艺术品,需要精心雕琢。
3. 组装与调试把加工好的零部件组装起来,可不是简单地拼在一起就行,还得进行调试,确保模具的各个部分能够精准配合,达到理想的切边效果。
这有点像组装一台精密的机器,每个零件都得在正确的位置发挥作用。
4. 表面处理为了提高模具的使用寿命和性能,还会进行表面处理,比如淬火、镀铬等。
这就像是给模具穿上一层坚固的铠甲,让它在工作中更耐用。
- 1、下载文档前请自行甄别文档内容的完整性,平台不提供额外的编辑、内容补充、找答案等附加服务。
- 2、"仅部分预览"的文档,不可在线预览部分如存在完整性等问题,可反馈申请退款(可完整预览的文档不适用该条件!)。
- 3、如文档侵犯您的权益,请联系客服反馈,我们会尽快为您处理(人工客服工作时间:9:00-18:30)。
通用模具结构第3部分:修边冲孔模1 范围本标准规定了本公司汽车覆盖件修边冲孔模的技术要求 2 冲裁力的计算2.1 冲裁力2.1.1 无剪切时的冲裁力PP=Lt σb (N ) P :冲裁力(N )L :冲裁轮廓长度(mm ) t :板厚(mm )σb :抗拉强度(σb =350N/mm 2) 2.1.2 切刃侧压力N约为冲裁力P 的1/3,即 N = P / 3 = Lt σb /3 2.1.3 有剪切(设置波浪刃口)时的冲裁力Px图1PPx=KP(N)Px:有剪切角时的冲裁力P:无剪切时的冲裁力 H = t 时,K = 0.4-0.6H = 2t 时,K = 0.2-0.4冲裁力超过冲床能力的50%时,要考虑设置波浪刃口,修边刃口长的情况下,可设计若干个波浪口。
每块镶块上尽可能取半个波浪或一个波浪;一个波浪的高点,取在镶块中间。
2.2 退料力Ps退料力据板厚、形状的不同而变化,一般为冲裁力的4-20% ,如间隙为板厚的10%以下时,退料力将增大。
P 为冲裁力:t≤2mm:退料力Ps=0.05P(形状简单);Ps=0.06P(形状复杂)t=2~4.5mm:退料力Ps=0.07P(形状简单);Ps=0.08P(形状复杂)t≥4.6mm:退料力Ps=(0.10-0.20)P;2.3 卸料力卸料力因料厚、形状等的不同而各异,一般取冲裁力的2~6%。
(常取5%)2.4 常用冲压材料的抗拉强度表13 冲裁间隙3.1 间隙选取原则落料尺寸取决于凹模尺寸(基准侧),间隙取在凸模上;冲孔尺寸取决于凸模尺寸(基准侧),间隙取在凹模上。
3.2 间隙值的选取表2板厚t 间隙C C/t 板厚t 间隙C C/t 板厚t 间隙C C/t 0.6 0.030 5% 1.6 0.100 6.2% 3.2 0.221 6.9% 0.7 0.035 5% 1.8 0.113 6.3% 4 0.320 8% 0.8 0.040 5% 2 0.130 6.5% 4.5 0.400 8.9%0.9 0.045 5% 2.2 0.143 6.5% 5 0.460 9.2%1.0 0.050 5%2.5 0.163 6.5% 6 0.600 10.0% 1.2 0.070 6% 2.6 0.169 6.5% 7 0.700 10.0% 1.4 0.080 6% 2.9 0.200 6.9% 8 0.800 10.0% 1.5 0.090 6% 3 0.207 6.9% 10 1.000 10.0%3.3 钝角修边——30°以下钝角修边,间隙取常规的1/2。
——30~60°倾角修边,钝角刃口作出局部平台,一般为3 倍料厚,但不超过5mm ;间隙趋于0。
图23.4 立切修边3.4.1 刃口线与斜面上的最大斜线平行,允许最小θ角可参照下表,冲裁间隙按常规选用。
图3表3t mm 0.6 0.7 0.8 0.9 1.0 1.2 1.4 1.6 1.8 2.0 θ°≥ 5.7 8.0 9.2 10.3 11.5 13.9 16.2 18.6 21.1 23.53.4.2 立切角度θ角不满足上表要求,需改造凹模刃口,并取小间隙冲裁,对于接近90°立切,冲裁间隙趋于0。
此外,注意检查压件器行程是否满足最大立切工作行程的要求。
图4 4 修边接刀基本设定原则4.1 薄板图5 4.2 厚板图65 废料处理5.1 注意事项5.1.1 必须确认废料滑到模具外还是压床工作台外。
5.1.2 废料以每一次冲裁落下为原则。
5.1.3 模具内废料滑板倾角:滑道≥25°,滚道≥15°。
5.1.4 当要求废料滑出压床工作台面时,废料滑板应为二级可拆式。
5.1.5 废料刀处必须有足够的高度,以便安装滑板。
5.1.6 废料要处理得安全,不应存在尖角,设计时要保证有足够的空间从模具里取出。
5.1.7 豆料ø30以上及对角线尺寸大于30×80的不规则豆料,不使用废料盒,应用滑板滑出。
5.1.8 废料盒容量应考虑一个班次(约500件)的冲裁量。
5.2 废料的大小要求图75.3 强制废料落下方法5.3.1 提升臂图8 5.3.2 附属气动机构图95.3.3 弹出器图105.4 大孔的废料处理5.4.1 设计成二级空刀图11 5.4.2 废料铸孔图125.4.3 倾斜面冲孔时,低处废料先接触滑板,高处铸件要空开,以防堵塞。
图13图145.5 小孔的废料处理5.5.1 一般情况按铸件选空开孔要大,但在机械加工时,按图15。
5.5.2 冲孔靠近修边时按图15图156 废料刀6.1 工作结构示意图图166.2 废料刀安装座的设计6.2.1 在下模座上,并与安装面为同一面。
图17 6.2.2 安装座设计在凸模上图186.2.3 分别设计在下模座和凸模上。
图197 废料滑板废料滑板的钢板厚t≥2.5 ㎜,采用尽可能用一块板构成,工作面不涂漆。
考虑维修、安装,采用内六角螺钉固定。
7.1 废料流出模具外图207.2 废料流到机床前侧,为确保操作者的场地,按下图处理图217.3 外围废料滑板7.3.1 前后方向图227.3.2 侧向(左右方向)图23 7.3.3 考虑模具铸件形状对废料滑板的影响。
图247.3.4 模具内的废料滑板图25 7.3.5 滑板的宽度大于废料的最大尺寸。
图267.3.6 多个废料滑出时避免干涉图277.3.7 滑板安装要方便、可靠图288 凸模8.1 凸模材质8.1.1 凸模材质的选定是依据产量、零件板厚、形状及其他条件来决定。
表4凸模的形式材质选定条件生产数量/月零件板厚零件形状、其他镶块HT + 钢镶块纵式镶块主要用于外板HT + 钢镶块横式镶块只用于内板断面变化少锻件整体钢板Cr12MnCr12MoVCH1小件断面变化少用于落料模(板材)铸造合金ZCH1(火焰淬火)其他8.1.2 凸模强度弱的部分局部镶块,以增强修边刃口强度。
图298.2 凸模分块原则8.2.1 在结构可行的情况下,凸模分块尽量少;8.2.2 凸模分块困难时,可分成若干大块;8.2.3 铸CH-1 最大铸造能力500kg。
8.3 制件定位8.3.1 当修边长度较长时,采用局部形状定位,其余部分避让图309 凹模9.1 标准断面形状 9.1.1 锻造结构B ≧ (1.2-1.5) * A图319.1.2 铸造结构凹模高度 A : 50 ≦ A ≦ 200 凹模宽度 B : B ≧ (1.2-1.5) * A 筋 位 置 : a ≦ 200; 40 ≦ b ≦ 60 A ≦ 60时不要加强筋图329.1.3 刃口部分厚度见表:表59.2 凹模的分块钢板T 一般δb ≦ 400 Mpa 40 δb = 60-80 Mpa45 δb ≧ 100 Mpa 509.2.1 分块线与刃口线夹角应在70-110°范围,尽可能垂直。
9.2.2 凹模的分块线与凸模分块线应错开5mm 以上。
图339.2.3 急剧斜面上的分块避免交角。
断面形状中 a ≦ 60°时,为避免尖角,如图所示进行分块图349.2.4 在后序伸长翻边,收缩翻边明显的地方不要分块。
图359.2.5 在平面形状的直线部位进行分块,使制造更容易。
θ和R 特别小时,在R 的终止点附近的直线部进行分块。
重量以15-20 ㎏为标准,以35kg 为最大;长度以200-300mm 标准,以500 ㎜为最大。
图369.2.6 末端部如下图所示分块。
图379.2.7 台阶镶块的分块9.2.7.1 刃口镶块的台阶原则上取水平。
图38 9.3 刃口安装螺钉(销钉)选用标准图399.3.1 t <1.5 mm: M12×40,Φ12×409.3.2 t≥1.5 mm: M16×45,Φ16×509.4 不需设销钉的情况9.4.1 镶块四个方向位置已定死,可不要销钉。
9.4.2 根据可调转刃口镶块在镶块组内的位置依键而定。
图示为螺钉位置图409.4.3 背面有挡墙时,镶块可设一个销钉。
9.4.4 三面被其它镶块围住,可设一个销钉。
9.5 吊装螺孔设置9.5.1 重量在30kg 以上时应设置吊装螺孔。
9.5.2 镶块在三面被围时应设置吊装螺孔。
9.5.3 吊装螺孔借用螺钉孔、销钉孔的情况:图41表6销孔或螺孔Φ8 Φ10 Φ12 Φ16 Φ20 M8 M10 M12 M16 吊装螺孔M10 M12 M16 M20 M24 M16 M20 M20 M3010 压件器10.1 决定行程的要素压件器的工作行程=a+b+t在凹模接触到冲压件前,压件器预压行程a=10mm以上。
斜面修边时,板厚由t0→t,垂直方向的最大工作行程t=t0/sinθ。
要考虑入模量b 因制造时的误差对行程的影响,应保证b 比b0 大。
10.2 压件器的强度10.2.1 压件器的壁厚(以灰铁为标准)图4210.2.2 强度变弱之处用钢材加强,或用QT-600 或铸钢代替HT。
θθ10.3 压件器的导向10.3.1 利用导板导向(中型和大型模具)(形状起伏较大或明显有侧向力时应采用导柱倒向)。
图4310.3.2 利用小导柱/导套导向(中小型模具)。
10.3.3 利用刃口导向(小型模具)。
10.4 压件器的避让。