不合格品控制流程图
不合格处理流程图

线长 (专门人员) 线长 课长
不良对策
水平展开
报废处理
部长
财务报告
红箱、黄箱的处理应该 由线长或专门人员进行 处理,而不是让作业者 进行
平展开
不合格品处理流程图
(红箱、黄箱处理) 信息处理
发生异常产品
生产部门 责任部门
工程异常处理规定
OK 判定 NG
退 回 产 线
作业者
不合格品
区分
作业者 系长 QRQC报告
红箱
黄箱
退 回 产 线
品质
对策指示
责任部门 (发生) 线长
先行对策
OK NG 判定
要返修
掌握不合格内 容、原因解析 和数据化
NG
1小时1次判定处理, 必须收集数据和将 现物作为样品
不合格品处理流程图红箱黄箱处理生产部门责任部门作业者作业者系长qrqc报告品质对策指示责任部门发生线长线长专门人员线长课长部长信息处理发生异常产品判定不合格品退回产线工程异常处理规定黄箱红箱判定ng退回产线ok报废处理ngok要返修区分掌握不合格内容原因解析和数据化ng财务报告先行对策水平展开不良对策1小时1次判定处理必须收集数据和将现物作为样品红箱黄箱的处理应该由线长或专门人员进行处理而不是让作业者进行
ISO9001不合格品控制程序(含流程图)
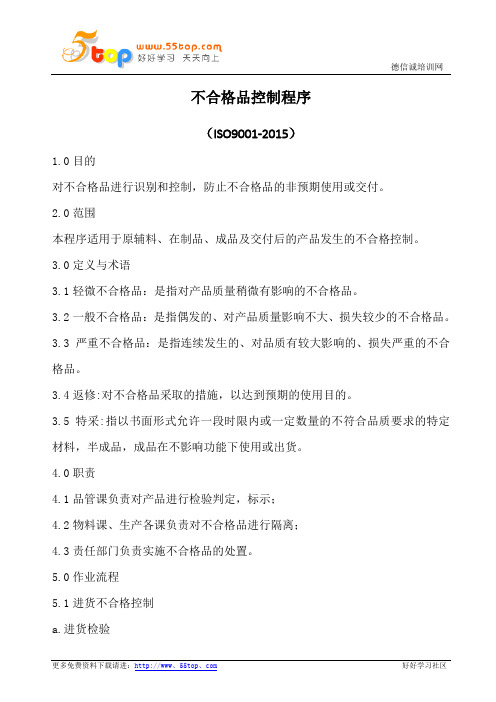
不合格品控制程序(ISO9001-2015)1.0目的对不合格品进行识别和控制,防止不合格品的非预期使用或交付。
2.0范围本程序适用于原辅料、在制品、成品及交付后的产品发生的不合格控制。
3.0定义与术语3.1轻微不合格品:是指对产品质量稍微有影响的不合格品。
3.2一般不合格品:是指偶发的、对产品质量影响不大、损失较少的不合格品。
3.3严重不合格品:是指连续发生的、对品质有较大影响的、损失严重的不合格品。
3.4返修:对不合格品采取的措施,以达到预期的使用目的。
3.5特采:指以书面形式允许一段时限内或一定数量的不符合品质要求的特定材料,半成品,成品在不影响功能下使用或出货。
4.0职责4.1品管课负责对产品进行检验判定,标示;4.2物料课、生产各课负责对不合格品进行隔离;4.3责任部门负责实施不合格品的处置。
5.0作业流程5.1进货不合格控制a.进货检验检验人员依据原物料检验标准、工程图纸、顾客要求等进行检验,判定为不合格品时开《品质异常处理单》并填写相关异常信息并附上不合格样品一并交给品管课长审核和管理部经理批准后扫描发邮件给采购课、生管课、物料课。
b.标示隔离进料不合格品由品管课检验人员进行标示,物料课人员将产品移至不合格品区域进行隔离。
c.不合格品处理1.退货:由物料课开具《退货单》,经品管、仓管确认后,经物料课长审核后通知采购课在7日内退货,若超出期限由我司自行处理。
当同一供应商因产品连续有2批因同样质量被拒收时,品管课开出《纠正和预防措施单》交采购课处理。
2.挑选使用:由采购课通知供应商,确定挑选方式:(1)由供应商进行挑选,挑选后的原物料须由品管课重新检验合格后方可入库使用;(2)由我公司安排物料课全检组人员进行挑选,挑选后的原物料须由品管课重新检验合格后方可入库使用;3.特采接收:在生产急需或紧急出货的情况下不影响安全,功能或结构的不合格品由采购课填写《品质异常处理单》交相关单位会审后由管理部经理核准后方可特采,同时品管员于该批产品上加贴“进料特采标签”;4.报废:制程中发现无法使用的来料不良品(含特采物料),由采购课与供应商沟通处理方式,物料课接收到可报废处理邮件或已扣款的财务部确认签署后开立《报废单》经资材部经理审核、副总核准后进行报废;5.不合格品的处理期限要求:采购课接单后需在24H内签回。
iatf16949不合格品控制程序(含乌龟图)
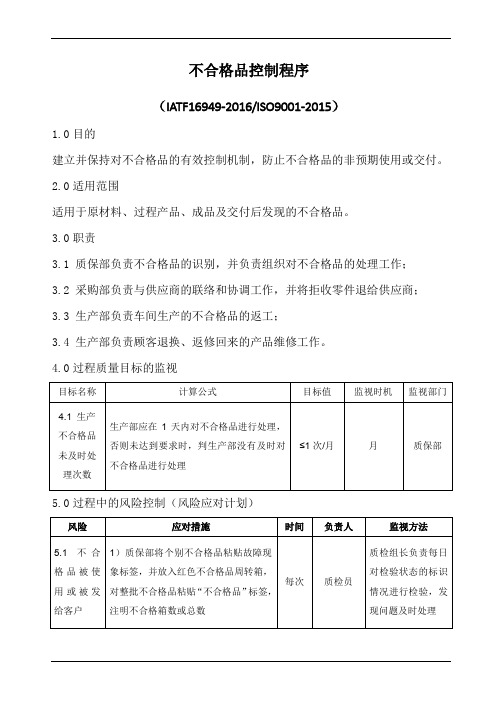
不合格品控制程序
(IATF16949-2016/ISO9001-2015)
1.0目的
建立并保持对不合格品的有效控制机制,防止不合格品的非预期使用或交付。
2.0适用范围
适用于原材料、过程产品、成品及交付后发现的不合格品。
3.0职责
3.1 质保部负责不合格品的识别,并负责组织对不合格品的处理工作;
3.2 采购部负责与供应商的联络和协调工作,并将拒收零件退给供应商;
3.3 生产部负责车间生产的不合格品的返工;
3.4 生产部负责顾客退换、返修回来的产品维修工作。
4.0过程质量目标的监视
5.0过程中的风险控制(风险应对计划)
6.0作业程序与控制要求
8.0过程流程图
8.1进料检验不合格品处理流程图
8.2过程产品检验不合格品处理流程图
8.3成品出厂检验不合格品处理流程图
8.4客户返修或退换产品处理流程图
9.0相关文件
9.1 《文件控制程序》
9.2 《纠正措施控制程序》
9.3 《过程和产品的监视和测量控制程序》
10.0相关记录
10.1 《进货检验不合格记录》
10.2 《原材料不合格品退库单》
10.3 《外部质量反馈单》
10.4 《首件检验不合格记录》
10.5 《过程不合格品及维修记录》
10.6 《纠正措施处理单》
10.7 《产品检验及维修记录》
10.8 《控制器不合格品报告及维修记录》
10.9 《报废申请单》
10.10《不合格品标签》(让步接收、不合格品、拒收、需挑选或修复等)。
不合格品控制流程图
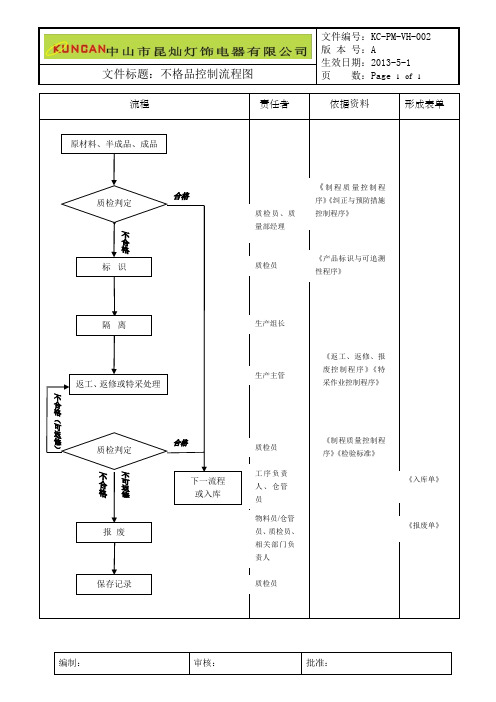
隔 离
生产组长
《返工、返修、报 生产主管 废控制程序》 特 《 采作业控制程序》
返工、 返修或物料员/仓管
《制程质量控制程 序》 《检验标准》 《入库单》
下一流程 或入库
报 废
员、 质检员、 相关部门负 责人
《报废单》
保存记录
质检员
编制:
审核:
批准:
文件标题:不格品控制流程图
流程 责任者
文件编号:KC-PM-VH-002 版 本 号:A 生效日期:2013-5-1 页 数:Page 1 of 1 依据资料 形成表单
原材料、半成品、成品
《制程质量控制程 质检判定
质检员、质 量部经理 序》 《纠正与预防措施 控制程序》
标 识
质检员
《产品标识与可追溯 性程序》
不合格品控制程序及处理流程图
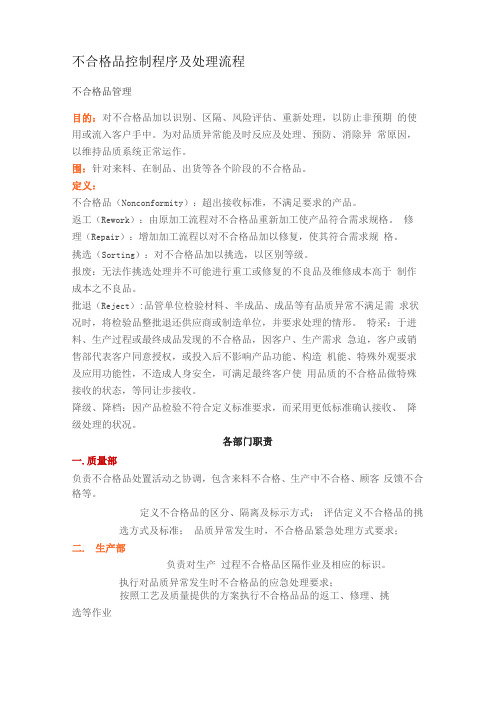
不合格品控制程序及处理流程不合格品管理目的:对不合格品加以识别、区隔、风险评估、重新处理,以防止非预期的使用或流入客户手中。
为对品质异常能及时反应及处理、预防、消除异常原因,以维持品质系统正常运作。
围:针对来料、在制品、出货等各个阶段的不合格品。
定义:不合格品(Nonconformity):超出接收标准,不满足要求的产品。
返工(Rework):由原加工流程对不合格品重新加工使产品符合需求规格。
修理(Repair):增加加工流程以对不合格品加以修复,使其符合需求规格。
挑选(Sorting):对不合格品加以挑选,以区别等级。
报废:无法作挑选处理并不可能进行重工或修复的不良品及维修成本高于制作成本之不良品。
批退(Reject):品管单位检验材料、半成品、成品等有品质异常不满足需求状况时,将检验品整批退还供应商或制造单位,并要求处理的情形。
特采:于进料、生产过程或最终成品发现的不合格品,因客户、生产需求急迫,客户或销售部代表客户同意授权,或投入后不影响产品功能、构造机能、特殊外观要求及应用功能性,不造成人身安全,可满足最终客户使用品质的不合格品做特殊接收的状态,等同让步接收。
降级、降档:因产品检验不符合定义标准要求,而采用更低标准确认接收、降级处理的状况。
各部门职责一.质量部负责不合格品处置活动之协调,包含来料不合格、生产中不合格、顾客反馈不合格等。
定义不合格品的区分、隔离及标示方式;评估定义不合格品的挑选方式及标准;品质异常发生时,不合格品紧急处理方式要求;二. 生产部负责对生产过程不合格品区隔作业及相应的标识。
执行对品质异常发生时不合格品的应急处理要求;按照工艺及质量提供的方案执行不合格品品的返工、修理、挑选等作业负责生产原因造成品质异常之分析与改善;三. 工艺部品质异常发生时之应急处理方案拟定。
对过程品质异常之分析与改善要求。
对修理、返工作业方式定义。
其他部门负责履行本部门的职责予以协助。
不合格品控制流程一. 进料品质异常控制质量部负责设计抽检方案,按照标准执行检验。
不合格品控制流程图
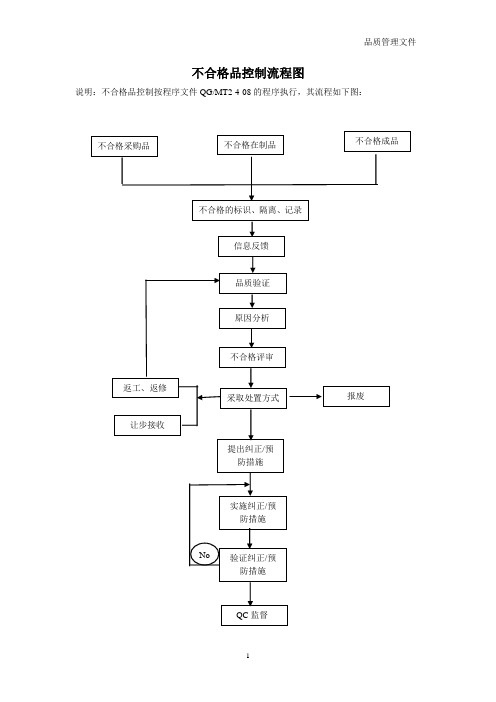
《零件不合格统计表(供应商)》
2
◆检验员应在进货检验记录上记录不合格的现象(含数据)、数量、规格、料号等信息。
◆检验员对不合格品,用不合格品标牌进行标识。
检验员
3
◆检验员通知仓库管理人员将不合格品或批次,移到不合格品区隔离。
依据检验标准分别进入“退/换货”程序或评审程序
检验员
仓库员
4
退货/换货
◆返工、返修:采购部负责组织供方或公司人员在返修区进行返工、返修,技品部负责返工、返修作业的指导和返工、返修后的重检(再次抽检),合格后标识入库。
采购部
技品部
采购部
技品部
《进货检验单》
序号
流程
工作说明
责任部门
使用表单
6
◆让步接收:技品部贴“让步接收”标识入库。
◆整批退货:由采购部负责处理退回,技品部贴“退货”标识。
◆技品部对纠正和预防措施的效果进行验证。
◆技品部对各车间的不合格品,每月进行量化分析,并跟踪和验证计划的实施效果。
生产车间
技品部
《品质异常处置单》
4、客户退货的不合格品处置流程:
序号
流程
工作说明
责任部门
使用表单
1
◆客户的退货产品到公司后,销售部通知仓管员核对退货产品型号和数量,将退货产品隔离存放并做好标识。
◆评审判定为全检由生产车间执行,经检验人员复检合格后才能出货。
◆评审判定为报废则由生产副总指定人员报废。
技品部
生产车间
5
纠正和预防措施及验证
◆属技术问题由技品部组织《品质异常处置单》的制定和实施,由车间进行跟踪验证。
◆属过程控制问题由生产车间组织《品质异常处置单》制定和实施,技品部对纠正和预防措施的效果进行验证。
汽配公司不合格品控制流程图
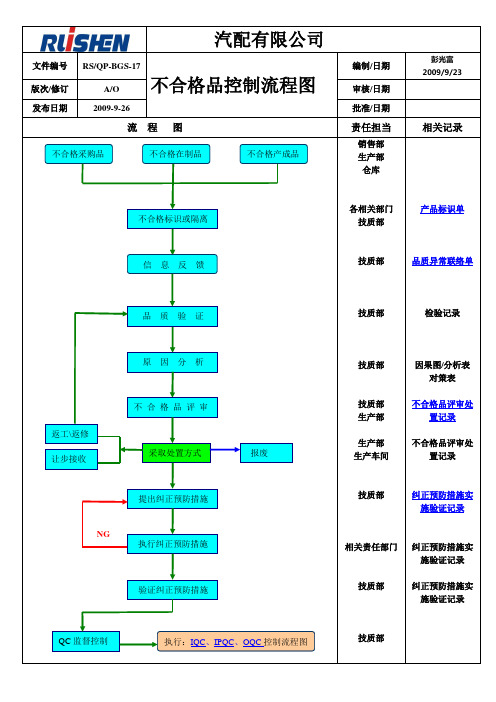
信
息 反 馈
技质部
品质异常联络单
品
质 验 证
技质部
检验记录
原
因 分 析
技质部
因果图/分析表 对策表 不合格品评审处 置记录 不合格品评审处 置记录
不 合 格 品 评 审 返工\返修 让步接收 采取处置方式 报废
技质部 生产部 生产部 生产车间
提出纠正预防措施
技质部
纠正预防措施实 施验证记录
NG 执行纠正预防措施 相关责任部门 纠正预防措施实 施验证记录 纠正预防措施实 施验证记录
汽配有限公司
文件编号 版次/修订 发布日期 RS/QP-BGS-17 A/O 2009-9-26 编制/日期
彭光富 2009/9/23
不合格品控制流程图
流 程 图
不合格产成品
审核/日期 批准/日期
责任担当
销售部 生产部 仓库
相关记录
不合格采购品
不合格在制品
不合格标识或隔离
各相关部门 技质部
产品标识单
验证纠正预防措施
பைடு நூலகம்
技质部
QC 监督控制
执行:IQC、IPQC、OQC 控制流程图
技质部
不合格品控制程序(含流程图)

5.1 品管:对不合格品标示及隔离,不合格品的确认,组织对不合格品进行评审,通知相关部门对不合格品进行处理,对返工品的重新检验;负责记录及归档不合格品处理的相关记录。
5.2采购:负责原物料特采提出及特采申请单的开立和特采物料的跟踪执行,负责来料不合格品的处理实施(退货、换货等),向供应商反馈产品的不合格信息及供应商品质改进跟踪。
文件制修订记录
NO
制/修订日期
修订编号
制/修订内容
版本
页次
1
2022-08-01
全新制订
01
制订
会审
核准
仓库
总经理
生产
人力资源
1.目的:
为使不符合要求的产品和服务处于受控状态,得到识别和控制,防止其非预期的使用或交付,确保公司产品及服务质量,特建此程序文件。
2.适用范围:
适用于本公司进料(原物料)、制程(半成品)、成品出货过程所发现的不合格品管制。
6.6特采提出时机(包括但不限于):
A、急于使用之材料,不良情形不会影响生产进程且不产生主要及致命缺点时。
B、生产过程中产生的或客户急于使用之产品,其不良状况经客户同意时。
C、客户急于使用之产品,仅为轻微之缺陷且不影响客户使用时。
6.7不合格成品降级提出时机:
A、不合格成品能实现部分或全部原设定的功能,符合法规要求,但无法进行特采或返工不经济时。
6.5不合格成品或半成品返工(数量超过100PCS)、报废及成品不合格品降级或特采,由生产填写《不合格品处理申请单》,制程(超过100PCS)或库存品的不良品报废由仓库、品管或生产填写《报废申请申》,提交相关部门会签,最后交总经理批准;对于少于100PCS的返工或少于100PCS的制程不良品报废处理,由供应链经理直接确认及安排实施(不必填写申请单)。
- 1、下载文档前请自行甄别文档内容的完整性,平台不提供额外的编辑、内容补充、找答案等附加服务。
- 2、"仅部分预览"的文档,不可在线预览部分如存在完整性等问题,可反馈申请退款(可完整预览的文档不适用该条件!)。
- 3、如文档侵犯您的权益,请联系客服反馈,我们会尽快为您处理(人工客服工作时间:9:00-18:30)。
文件编号
不合格/标识/返工管理流程图 版 本 号:A/0 第1页 共3页
不合格品控制流程图
责任人
相关表单
不合格采购品
不合格在制品
让步接收
不合格标识或隔离 信息反馈 品质验证 原因分析
不合格品评审
采取处置方式
报废
相关部门 产品标识单 质量部
质量部
不合格品评审处 置记录
质量部 检验报告
质量部
因果图/分析表/ 对策表
质量部 研发中心 生产中心
不合格品评审处 置记录
生产部
不合格品评审处 置记录
提出纠正预防措施 执行纠正预防措施
NG
验证纠正预防措施
QC 监督控制
质量部 研发中心
相关责任 纠正预防措施实
部门
施验证记录
质量中
纠正预防措施实 施验证记录
质量部
Company
文件编号
相关表单 相关记录
待返工品
返工品分类清理
生产部
统计表 产品标识单
品质异常原因分析 返工品处理
提出纠正预防措施
生产部排制单
车间安排返工作业
质量部
因果图/分析表 对策表
质量部 不合格品评审处 研发中心 置单
质量部
纠正预防措施实 施验证记录
生产车间返工
生产部
纠正预防措施实 验证记录
NG
检验员
OK
完工检验
OK
检验员 过程巡检记录
NG
检验报告
出货报告
品质异常联络单
送检单
下工序
生产车间 入库
生产部 仓管员
产品生产作业流 程单 入库单 产品标识
储存
仓管员
入库单/物料标 识卡/登记帐本
不合格/标识/返工管理流程图 版 本 号:A/0 第2页 共3页
标识和可追溯控制流程图
责任人
相关表单
编制标识规则
原辅材料
半成品、产成品
检验状态
产品名称/规 格/厂家
OK
合
格
NG
不合格
处置标识
合
格
标
让选 拒
识
步
接用 收
收
入
库
检验状态
标签
产品规格/编号/生 产班组/生产批号
NG
不 合 格
OK
合
格
※检验员对产品的状态 进行标识、各相关部门负 责所属区域内的产品的 标识区分摆放,负责对标 识的维护。品质经理和生 产经理进行监督检查
执行 不合 格品 控制 流程
贴合格标识 转序/入库 物料标识卡
领 保存所有相关记录标识
用
执行文件、记 录控制流程图
必要时进行追溯
产品交付
Company
生产过程
文件编号
不合格/标识/返工管理流程图 版 本 号:A/0 第3页 共3页
返工控制流程图
半成品
成品
客户退货
责任人 质量部 生产部 采购部 营销中心